DOI:
10.1039/D4PY01321B
(Paper)
Polym. Chem., 2025,
16, 979-986
Amphiphilic block-random copolymer stabilisers: extension to other monomer types†
Received
19th November 2024
, Accepted 14th January 2025
First published on 16th January 2025
Abstract
Block-random copolymers (BRCs) incorporating acrylics were synthesised using nitroxide-mediated polymerisation (NMP) to form macro-stabilisers for the preparation of polymer latexes. These hybrids of block copolymers and random copolymers are traditionally composed of a polystyrene hydrophobic block coupled with a hydrophilic random block of styrene and acrylic acid. Their aqueous dispersions exhibit unique behaviour compared to conventional block copolymers, including being responsible for a unique nucleation mechanism in emulsion polymerisation. However, all previous work has only used styrene as the hydrophobic monomer, and only styrene emulsion polymerizations have been conducted. To explore the versatility of BRCs for the polymerisation of monomers other than styrenics (e.g. acrylates, methacrylates), the BRC library was explored with the introduction of methyl methacrylate (MMA) and n-butyl acrylate (n-BuA) units as the hydrophobic monomers. With blocks composed of one or multiple monomers, all the BRCs were successfully dispersed in water at high concentrations (>100 g L−1), with similar behaviour compared to previously reported for styrene-based BRCs. Semi-batch emulsion polymerisation of styrene or acrylates latexes was also performed. A hydrophobic block consisting of a n-BuA and styrene copolymer was found to be of the most interest, showing promising stability over the range of latexes polymerised.
Introduction
The waterborne coating market reached over 81 billion dollars (USD) in 2021 and is expected to nearly double by the end of the decade.1 The acrylic sector leads this market with over 35% of revenue share. The demand in waterborne coatings is fuelled by VOC restrictions, which limit the use of organic solvents, especially in applications where workers or customers are exposed, such as the construction and automotive industries. Although aesthetics are important, the coating's primary purpose is to protect and increase the life time of the coated surface.
Polymeric surfactants have been studied for the past several decades with several industrial successes such as the non-ionic polyoxamers Pluronics®.2 Attention has also been given to polysoaps like alkali-soluble resins (ASRs), a random copolymer that show several performance-related advantages such as improved freeze–thaw stability, improved wetting, and desirable rheologic properties.3 The development of Reversible Deactivation Radical Polymerisation (RDRP) methods (ATRP, NMP, RAFT, etc.) allowed the synthesis of more controlled structures with well-defined hydrophilic/hydrophobic balances, which could greatly enhance the efficiency of polymeric stabilisers.
Among these structures, the polyelectrolyte block copolymer stabiliser family has attracted attention.4,5 These materials combine electrostatic and steric repulsion by using a polyelectrolyte water soluble block such as polystyrene sulfonate, polyacrylic acid, or polymethacrylic acid, together with a hydrophobic block, which is intended to be adsorbed (“anchored”) on the surface of the latex particle. The block copolymer technology grew to be one of the most studied technologies thanks to its unique features, such as low critical aggregation concentration, the formation of polymer seeds, and the very high area stabilised per macromolecule.6–9
Sanders et al. recently reported a new class of block-random copolymer (BRC).10 A hydrophobic block of polystyrene with a hydrophilic block of poly[styrene-r-acrylic acid] showed promising stabilisation properties for polystyrene latexes while overcoming disadvantages of conventional block copolymers. Stable latexes with high solid content (50% w/w) and small particle diameter (<100 nm) were obtained, while a pH dependence on the nucleation mechanism was observed. At high pH (>8.5), BRC aggregates act as small seeds that coagulate as the particle grows, yielding a robust nucleation mechanism largely independent from kinetic factors and process conditions termed “seeded-coagulative” nucleation. At neutral pH this mechanism shifts toward a conventional seeded process, with the BRC molecules forming larger seeds less susceptible to coagulation.11–13
While light has been shed on the dispersion properties of BRCs and their ability to stabilise emulsion polymerisations,13 previous work focussed only on polystyrene based BRCs. It is not known if styrene-based BRCs can be effective stabilisers for non-styrenic monomers (e.g. acrylics) due to compatibility concerns. For example, hydrophobic polystyrene (PS) chains are not thermodynamically miscible in more polar acrylic monomers such as n-butyl acrylate (n-BuA) or methyl methacrylate (MMA), which may prevent styrene-based BRCs from acting as anchoring blocks on the surface of acrylic latex particles.
In this context, the present publication focuses on the synthesis and uses of BRCs with styrene, MMA, and n-BuA monomers in both blocks, as they are three of the most commonly used industrial monomers. The dispersion of such polymers showed a critical aggregation concentration relatively constant from one BRC to another. When the pH kept above 8.5, the seeded-coagulative nucleation mechanism was confirmed for all the acrylic-containing BRCs. Stable polymer latexes of styrene, acrylates, or comonomer mixtures were obtained upon careful design of the BRC chain.
Experimental section
Materials
N-tert-Butyl-N-[1-diethylphosphono-(2,2-dimethylpropyl)nitroxide] (SG1, 85%) and N-(tert-butyl)-N-(1-diethylphosphono-2,2-dimethylpropyl)-O-(2-carboxylprop-2-yl) hydroxylamine (BlocBuilder™, 99%) were obtained from Arkema and used as received. Acrylic acid (anhydrous, 180–200 ppm MEHQ as an inhibitor, 99%), styrene (4-tert-butylcatechol as a stabiliser, ≥99%), methyl methacrylate (≥99%, ≤30 ppm MEHQ as inhibitor), n-butyl acrylate (≥99%, 10–60 ppm MEHQ as inhibitor), and ammonium persulfate (>98%), were supplied by Sigma-Aldrich and used as received. Methanol (99.8%), tetrahydrofuran (THF, 99%), and hexanes (98.5%) were supplied by ACP Chemicals and used as received. Sodium hydroxide (1 M in aqueous solution), 1,4-dioxane (99.9%) and hydroquinone (crystalline, laboratory grade) were purchased from Fisher Scientific and used as received. Trimethlysilyldiazomethane (2 M in hexanes) was supplied by Alfa Aesar. Deionized water used in the present study was obtained from a Millipore Synergy water purification system equipped with SynergyPak purification cartridges (18.2 MΩ cm).
Characterisation of polymers
Molecular weight measurements were carried out by means of gel permeation chromatograph (GPC) analysis in THF eluent. A Waters 2690 Separation Module with a Waters 410 Differential Refractometer with Waters Styragel HR (4.6 × 300 mm) 4, 3, 1, and 0.5 separation columns operating at 40 °C and 0.3 mL min−1 was used. The carboxylic acid groups of the copolymers were methylated prior to GPC analysis. Similar to previous methylation techniques,14,15 a slight excess of trimethlysilyldiazomethane was added to the polymer sample already dissolved in a 3
:
1 ratio of THF/methanol mixture. Calibration of the GPC was carried out using narrow molecular weight distribution polystyrene and PMMA standards supplied by Polymer Standards Service.
1H NMR spectroscopy was performed on an FT-NMR Bruker Avance 400 MHz spectrometer at room temperature. Spectra were recorded with a total of 64 scans, using a polymer concentration of 5 mg mL−1 in CDCl3. Yields and molecular weight were calculated using the integration of the proton at 5.1 ppm (1 H styrene), at 5 or 3.7 ppm (respectively 1 H and 3 H methyl methacrylate), at 4.1 ppm (2 H n-butyl acrylate) and the average of the proton peaks of acrylic acid (∼6.5 ppm).
Atomic Force Microscopy (AFM) was performed on a Bruker Dimension Icon AFM. The samples were cast on mica substrate at concentration above the critical aggregation concentration (1–10 g L−1) and dried overnight in a dry environment at room temperature. The results were recorded in tapping mode and analysed using the software Gwyddion 2.61.
All reported dynamic light scattering (DLS) measurements are an average of 30–50 sequential measurements taken on Malvern Zetasizer Nano ZS with non-invasive backscattering optics (173°) and a 4 mW He–Ne laser (633 nm). The number of latex particles (L−1) was calculated using eqn (1):
| 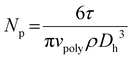 | (1) |
with
τ being the polymer content of the latex (g L
−1) determined by gravimetry,
ρ the density of the polymer,
Dh the hydrodynamic diameter of the polymer core measured by DLS, and
vpoly the volume fraction of polymer in the particles during size measurement.
Critical aggregation concentrations (CAC) of the BRCs were evaluated at pH = 9.5 and ionic strength of 0 or 100 mM (NaCl) by varying the BRC concentration and measuring the intensity of scattered light. BRCs concentrations ranged from 0.01 g L−1 to 20 g L−1. The CAC was taken at the intersections between the two linear portions of the data (Fig. S6†).
Determination of pKa values was conducted by titration using a Mettler Toledo S470 SevenExcellence Multiparameter meter fitted with an InLab Routine Pro-ISM pH probe and an InLab 741 conductivity probe. BRC dispersions were diluted to 1 g L−1 in pure water. The initial pH was adjusted to approximately 11.5 using 1 M NaOH. Additions of 10 to 20 μL of 0.1 M HCl at 30 s intervals were carried out until the pH stabilized to a value of approximately 2.5. Both conductivity and pH values were monitored throughout the titrations (Fig. S7†).
Synthesis of macroinitiator
The polystyrene macroinitiator was synthesised in bulk and reported as outlined in a previous publication by Sanders et al.10 The other macroinitiators were synthesised with an adapted protocol described in the ESI.† When indicated, purification steps were conducted with precipitation in methanol followed by successive steps of solubilisation/precipitation with THF/methanol until no traces of monomer remained, as confirmed by the absence of vinyl peaks in the 1H NMR spectra. For others, the polymerisation of the second block was started directly in the reaction medium without purification.
Chain extensions with styrene and/or n-butyl acrylate, and/or methyl methacrylate and acrylic acid
The solution polymerisation of the second block of polystyrene-based BRCs was conducted as outlined in a previous publication.10 The chains extensions were performed following an adapted protocol described in the ESI.† For BRC1 and BRC2 the addition of dioxane as solvent was needed to solubilize the acrylic acid and enhance control over the polymerisation. BRC3, BRC4 and BRC5 were polymerised in bulk to increase the reaction rate. Aliquots of the reaction medium were taken to follow the reaction by 1H-NMR. BRC1–5 were purified by precipitation in hexanes followed by successive solubilisation/precipitation with THF/hexanes. The purified copolymer was subsequently dried overnight at 50 °C under vacuum in a low-heat oven for 24 hours and characterised with GPC analysis to obtain the Mn presented in Table 1 and Fig. S2.†
Table 1 Chemical composition of BRC1–5 polymerised by NMP and characterised by 1H-NMR and GPC
Copolymer |
Anchoring block |
Stabilising block |
Overall BRC |
Monomers |
DP |
M
n(GPC)
M
n(1H–NMR) kg mol−1 |
Đ
|
Monomers |
DP |
M
n(GPC) Mn(1H–NMR) kg mol−1 |
Đ
|
% AA |
BRC1 |
Sty |
25 |
2.6/2.6 |
1.11 |
Sty/AA |
50/25 |
10.3/— |
1.16 |
25 |
BRC2 |
n-BuA |
28 |
3.0/3.6 |
1.28 |
n-BuA/AA |
39/20 |
12.0/— |
1.29 |
22 |
BRC3 |
Sty/n-BuA |
15/11 |
4.9/3.0 |
1.16 |
Sty/n-BuA/AA |
33/32/21 |
13.0/11.7 |
1.32 |
19 |
BRC4 |
Sty/MMA |
3/27 |
3.2/3.0 |
1.40 |
Sty/MMA/AA |
4/40/18 |
6.4/8.6 |
1.46 |
20 |
BRC5 |
Sty/n-BuA/MMA |
6/5/9 |
2.0/2.1 |
1.41 |
Sty/n-BuA/MMA/AA |
18/13/9/21 |
8.0/9.2 |
1.34 |
26 |
Dispersion of block-random copolymers in aqueous solution
After determination of the acid moiety content in the chain by 1H-NMR, BRCs were dispersed in the aqueous phase by dropwise addition of 1 M NaOH solution at 90 °C for PMMA and PS based BRCs, while the dispersion was performed at room temperature for PBA and P[BA-r-S] based BRCs. The pH was monitored and kept below 10 for acrylate/methacrylate based BRCs to avoid hydrolysis of the alkyl ester groups. The dispersions reached a final concentration of 200 g L−1 of BRCs.
Emulsion polymerisation procedure
A standard semi-batch emulsion polymerisation of monomers (styrene, methyl methacrylate or/and n-butyl acrylate) began by mixing deionized water and a dispersion of BRC. This mixture was sealed in a 50 mL round bottom flask and immersed in an 85 °C bath of silicone oil with a magnetic stir bar. The reactor was purged with nitrogen for 30 minutes prior to polymerisation, and a small flow of nitrogen was maintained through the reaction. The initiator (ammonium persulfate, 0.75% w/w based on monomer) was added after purging with nitrogen. The monomer was introduced using a syringe pump for a total feeding time of 120 min reaching a proportion of 20% v/v related to the water phase. The reaction in the round bottom flask was kept running for an additional 60 min to reach high conversion. The pH of the initial solution was adjusted to 9.5 and decrease upon polymerization to reach ∼7.5 after 180 min. Stabiliser and salt concentrations were varied as required. Time zero for the reaction was set as the time when the reaction mixture reached 85 °C.
Results and discussion
Synthesis of BRC1–5
The previously published BRCs used as macro-stabilisers for emulsion polymerisation were based on a polystyrene backbone (BRC1). While being a classic model monomer, styrene-based BRCs may have limitations for the polymerisation of common industrial latexes based on (meth)acrylates used in many coatings and adhesive formulations. To this end, four new BRCs based on styrene, n-butyl acrylate, methyl methacrylate and acrylic acid were synthesised and studied as macro-stabilisers. Their compositions are shown in Table 1 while details of their synthesis are provided in the ESI (Fig. S1–S5†). BRC5 is of unique composition, containing styrene, n-butyl acrylate, methyl methacrylate and acrylic acid. Its synthesis was inspired by the emulsion polymerisation results using BRC1–4.
Dispersion of BRC1–5
The critical aggregation concentration (CAC) represents a transition between a soluble state in a solvent (i.e. a solution) and a stable aggregate state (i.e. a dispersion). Narrainen et al. showed that the CAC value of a poly(2-dimethylamino)ethyl methacrylate-block-polybutyl methacrylate copolymer has little dependence on the size of the hydrophilic block, or its position within the chain (in the case of triblocks).16 The distribution of monomers along the chain is an important parameter in determining the morphology and the assembly behaviour of copolymers. Typical block copolymer CAC values range from 10−8 to 10−5 M.16,17 In contrast, ASRs exhibit a CAC which is orders of magnitude higher (∼5.10−3 M) as the random distribution of hydrophilic monomers within the chain lowers the hydrophobic interactions.18 The CACs of BRCs are expected to be somewhere in between these two values, as recently reported by Smeltzer et al. where a series of polystyrene-b-poly[styrene-r-(acrylic acid)] exhibited values between 10−4 and 3 × 10−4 M.13 In the present case, the CAC values of BRC1-BRC5 were determined by SLS in the absence and presence (100 mM) of NaCl (Table 2 and Fig. S6, 7 ESI†).
Table 2 Critical Aggregation Concentration of BRC1–5 determined by DLS in the presence or absence of added salt, at pH = 9.5, along with the pKa of each BRC measured by pH and conductimetric titration
Copolymer |
CAC mM ([NaCl] = 0 M) |
CAC mM ([NaCl] = 0.1 M) |
pKa |
BRC1 |
0.45 ± 0.01 |
0.31 ± 0.02 |
6.5 |
BRC2 |
0.13 ± 0.01 |
0.12 ± 0.01 |
7.5 |
BRC3 |
0.22 ± 0.06 |
0.11 ± 0.01 |
6.7 |
BRC4 |
0.33 ± 0.10 |
0.20 ± 0.06 |
6.7 |
BRC5 |
0.09 ± 0.01 |
0.06 ± 0.01 |
6.9 |
The salt had a moderate effect on the CAC value, with a slight decrease in CAC observed for each system when NaCl was added. This was explained by the enhanced repulsion between AA moieties at lower salt concentrations. Despite having the highest proportion of AA within the chain (26%), BRC5 exhibited the lowest CAC among the tested BRCs. As expected, the CACs of the BRCs were positioned between block copolymers and ASRs, in agreement with what we observe with PS-PAA BRCs.
We recently published the results of semi-batch emulsion polymerisation stabilised by BRC at a concentration lower than the CAC which led to low conversion. This phenomenon was explained by the fact that, in the absence of aggregates, the nucleation is homogeneous in the water phase, which is associated with slower kinetics.19 For this reason, the concentrations for the semi-batch emulsion polymerisations run in this study were always higher than the CAC.
Atomic force microscopy
The ability for BRCs to stabilise a growing latex is determined largely by their ability to form aggregates above the CAC in the water phase. In a previous publication, the impact of the pH has been investigated for the polymerisation of a PS latex stabilised by a PS-based BRC.12 Briefly, we hypothesised that at high pH (>9) the previously published seeded-coagulation nucleation mechanism occurred in both the presence and absence of added salt. However, at pH below 8.5 and in the absence of added salt, generation of larger seeds within the reactor led to a mix of both seeded and seeded-coagulative nucleation mechanisms. This effect led to an increase in both the specific surface occupied per BRC chain at the latex interface and a larger number of particles (i.e. lower final overall average size of the latex). Atomic force microscopy (AFM) was used to investigate the form of the aggregates of BRC1, BRC3, BRC4 and BRC5 at high pH and at pH = pKa (Table 2) (the low Tg of BRC2 did not allow an AFM study). All of the BRCs studied appeared to undergo a self-assembly process into spherical aggregates at pH = 9.5 which could be seen with AFM (Fig. 1). Furthermore, when pH = pKa, the aggregate diameter was larger than at pH = 9.5 (Table 3 and Fig. 3), as described in a previous study.12 The AFM technique does not allow the calculation of accurate diameters for polymer structure as deformation of the particles due to interaction with the mica substrate can occur. However, the comparison at different pH values provides evidence for a different self-assembly process occurring while lowering the pH.20 As the pH decreases the AA moieties become increasingly protonated, reducing the solubility of the BRC in water. Instead of precipitating, the small aggregates self-assembled into larger aggregates, lowering the total surface in contact with water. The exact mechanism is still under study, but this feature exhibits similarities with a self-assembly process induced by a change in the packing parameter (e.g. polymerisation-induced self-assembly).21 The affinity to water of the hydrophilic block is lowered, and hydrogen bonding between protonated acrylic acid units increases, which tends to reduce the volume occupied by this block in water. As reported previously,12 this phenomenon starts at pH ∼ pKa + 2, ∼8.5; the pH of the dispersion prior to polymerisation is hence of importance and was fixed for the rest of this study at pH = 9.5.
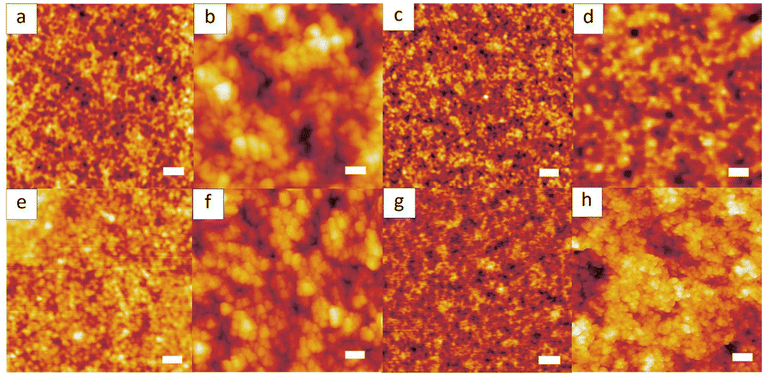 |
| Fig. 1 AFM images of films of BRC at pH = 9.5 (a, c, e and g) and pH = pKa (b, d, f and h) with BRC1 (a and b) BRC3 (c and d) BRC4 (e and f) BRC5 (g and h). Scale bar is 200 nm. | |
Table 3 Diameters of the aggregates measured by AFM. Diameters are an average of 100 measurements
Copolymer |
Diameter (nm) pH = 9.5 |
Diameter (nm) pH = pKa |
BRC1 |
42 ± 8 |
69 ± 14 |
BRC3 |
34 ± 5 |
75 ± 13 |
BRC4 |
54 ± 9 |
104 ± 18 |
BRC5 |
— |
39 ± 5 |
Semi-batch emulsion polymerisation
The ability of BRCs to stabilise semi-batch and batch styrene emulsion polymerisations has been demonstrated in previous publications.10,22 However broad application of this technology requires the ability of BRCs to stabilise other kinds of latexes, including for example acrylates and methacrylates. In this study, we compared the ability of BRCs to stabilise styrene, MMA, and a comonomer mixture of MMA and n-BuA, as an example of a common latex formulation for coating or adhesive applications.
Effect of monomer type in the emulsion polymerisation
As shown in Table 4, BRC1, BRC2 BRC3 and BRC5 successfully stabilised styrene emulsion polymerisations without the formulation of coagulum. The use of BRC4 led to 100% coagulum with styrene, with destabilisation occurring from the first minutes of monomer feeding. This unsuitability of BRC4 for the emulsion polymerisation of styrene can be explained by multiple factors, including a chemical incompatibility between styrene and BRC4 but also the significantly lower molecular weight of the chains (8.6 kDa by NMR) combined with a higher dispersity (Đ = 1.45) compared to the other BRCs. BRC4 is rich in the somewhat hydrophilic MMA (compared to PBA or PS), which is apparently unfavourable for the efficient stabilisation of styrene latexes.
Table 4 Characterisation by DLS and gravimetry of various latexes stabilised by BRC1–5 concentrated at 10% w/w based on monomer with at pH > 7.5. Dn and PDI are number average diameter and polydispersity index
Monomer |
Styrene |
BA : MMA (50/50 v/v) |
MMA |
D
h, Dn (nm) |
PDI |
Conv. (%) |
D
h, Dn (nm) |
PDI |
Conv. (%) |
D
h, Dn (nm) |
PDI |
Conv. (%) |
BRC1 |
140; 120 |
0.02 |
— |
249; 224 |
0.08 |
75 |
— |
— |
100% coagulum |
BRC2 |
296; 218 |
0.32 |
— |
175; 149 |
0.06 |
>99 |
— |
— |
100% coagulum |
BRC3 |
177; 151 |
0.03 |
— |
176; 155 |
0.04 |
>99 |
— |
— |
100% coagulum |
BRC4 |
— |
— |
— |
350; 199 |
0.33 |
|
— |
— |
100% coagulum |
BRC5 |
244; 192 |
0.16 |
89 |
179; 37 |
0.54 |
>99 |
1005; 983 |
0.22 |
31 |
MMA and n-BuA are often copolymerised in industrial latexes, with numerous process variations reported in the literature, including batch, semi-batch, and sequential polymerisation designed to yield the desired composition of the copolymer and achieve either core–shell or homogeneous particles.23,24 In the present study, semi-batch conditions were chosen with a MMA/n-BuA volume ratio of 1
:
1 without the presence of a pre-emulsion or seeds in the reactor or in the feeding syringe. Each BRC led to stable copolymer latexes without the formation of coagulum. Conversions and diameters were generally similar to those obtained with styrene. These experiments constitute a proof of concept that the BRC stabilizing technology is not limited to styrene and can be extended to other monomers if the composition of the BRC is properly tuned.
The homopolymerisation of MMA by emulsion polymerisation differs from styrene and MMA-co-n-BuA polymerisations because of the higher solubility of MMA in water and therefore its greater tendency to undergo homogeneous nucleation. In the absence of micelles, the particles are formed by precipitation of the growing chains. These small precursor particles are then stabilised by the surfactant, which diffuse from the continuous medium to the surface of the growing particle. In the present case, all the BRCs evaluated failed to provide good stabilisation to MMA homopolymerisations. Even BRC4, which has the highest proportion of MMA, did not provide efficient stabilisation. As published recently,11 the mobility of BRCs in the water phase may be too low to efficiently come in contact with a growing particle and prevent coagulum formation.
Effect of the nature of the BRC chain composition
With block copolymers, it has been shown that incompatibility (i.e. immiscibility) with the growing latex (e.g. PS-b-PAA with PMMA latex) generally reduces the stability of the emulsion and can reduce the diameter of the particles.25,26 This phenomenon is due to the phase separation within each particle, which drives the block copolymer chains to the interface, while in a latex/block copolymer miscible couple, a proportion of the block copolymer is buried within the particle. This reduced particle size effect was not observed in the present case; both BRC1 and BRC2 led to smaller particle diameters when employed to make their respective (i.e. same hydrophobic monomer in both BRC and emulsion polymerization) latexes (Table 4). Each BRC chain is hence more efficient for the stabilisation of chemically compatible latexes, which is probably a consequence of the unique mechanism of nucleation operating in these systems.10 BRC3 exhibited interesting behaviour with a final hydrodynamic diameter and number diameter equivalent for PS and PMMA-PBA latexes (Table 4). This is evidence that the chemical composition of the BRC plays an important role in the stabilisation of latexes. With the PMMA-based BRC4, the polymerisation of a styrene latex was unsuccessful, likely because of the immiscibility of the BRC with the latex, while the polymerisation of n-BuA/MMA led to a large diameter population with a high PDI of 0.33. The polymerisation of PMMA latexes led to coagulum for the reasons mentioned in the previous section. The PMMA-based BRC4 showed little ability to stabilise latexes under these conditions and was not used for the rest of this study. The polymerisation using BRC5 P(S6-r-BA5-r-MMA9)-b-P(S18-r-MMA9-r-BA13-r-AA21), was successful with the styrene and BA-MMA latexes. However, the PMMA latex prepared using BRC5 contained micron-size beads which sedimented in a few hours. The final diameters (Dh, Dn) were overall much larger when BRC5 is used compared to the other BRCs.
The rest of the study focused on BRC1–3 which all showed good stabilisation properties for both MMA/n-BuA and styrene emulsion polymerisations. In Fig. 2, latexes with an increasing proportion of (meth)acrylates in an acrylate/styrene mix were polymerised. The BRC concentration (10% w/w based on monomer), the overall solid content (200 g L−1) are constant and the mix of acrylate is composed of 50/50 in volume of MMA/n-BuA. BRC1 showed efficient stabilisation for every latex containing styrene, even at the lowest tested concentration (20 v/v %) with a very low PDI (Fig. 2), and showed a much higher Dh for 100% MMA/n-BuA. Using a polystyrene-based BRC is hence an appropriate solution for the polymerisation of latexes containing at least a small proportion of styrene. BRC2 showed good results for the acrylates latexes but exhibited higher PDI for every proportion of styrene in the mix. The polymerisation was successful without the formation of coagulation; however, this PBA-based BRC should be avoided for a precise control of the size of styrenic latexes. BRC3 showed similar results while polymerising acrylates or styrene (Table 4). In Fig. 2, it is clear that BRC3 provided a fairly consistent particle size for the studied latexes. Very few previous studies on ionic amphiphilic diblock copolymers gave attention to the polymerisation of a latex of a different chemical nature than the hydrophobic block. Heuts et al. polymerised MMA in the presence of a PS-PPEGMA block copolymer and showed that the final latexes were negatively impacted by the incompatibility of the hydrophobic phases, including irregular morphology and systematic coagulum formation.26 With the objective of bringing this technology to an industrial scale, it was of importance to demonstrate the ability of a single BRC to exhibit consistency in the polymerisation of latexes of varying composition. BRC3 demonstrated the best overall versatility by combining the ability to stabilise both PS and P(MM-co-BA) latexes efficiently. Moreover, its synthesis was done in bulk at a lower temperature than the one reported for BRC1 in the previous publication. The combination of n-BuA and styrene within the chain also allows the tailoring of the glass transition of the BRC, which will be of interest for coating applications.
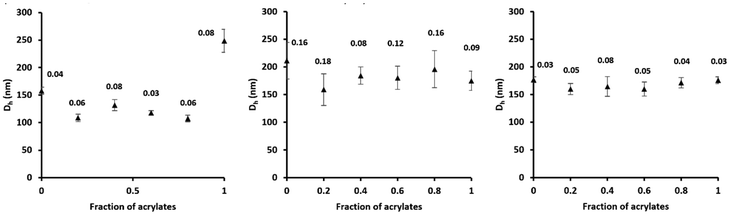 |
| Fig. 2 Evolution of the hydrodynamic diameter for latexes of styrene, acrylates (n-BuA/MMA 50/50) or a mixture of those (weight fraction), stabilised with 10% w/w of (left) BRC1, (middle) BRC2, (right) BRC3. Numbers above the data point represent the PDI of these measurements. | |
Nucleation step
The understanding of nucleation is determinant for the prediction of the number of particles Np and the diameter, hence the total particle surface area and other important specifications (e.g., interparticle spacing, percentage of coverage) that are important for the industrialisation of a stabiliser technology. Because of the unique dispersion properties and self-assembly of BRCs in water, a novel nucleation mechanism has been proposed by George et al.22 Briefly, the macro-stabiliser aggregates act as seeds, which coagulate due to insufficient stabilisation as the total particle surface area increases. In this theory, named seeded-coagulative nucleation, the number of particles Np and the stabiliser concentration [S] exhibits a cubic dependency. Np ∝ [S]α with α ≈ 3.
The determination of the α parameter for BRC1 and BRC3 was made by polymerising polystyrene latexes, while a mix of acrylates (50/50 v/v % MMA/n-BuA) was used for BRC2, in accordance with the results in the previous section. The concentration of BRC was varied while pH (9.5), initiator concentration (0.75% w/w based on monomer), and targeted final solid content (200 g L−1) were kept constant. All the monomer conversions reached at least 95%. The α parameter remains constant and equal to ∼3 for the three tested BRCs, confirming the previously published results (Fig. 3). Moreover, the evolution of Np for an acrylate latex or a polystyrene latex, both stabilised by BRC3 (10% w/w based on monomer), showed a similar evolution (Fig. 3). The same coalescence behaviour was observed with approximately the same final number of particles. These curves were compared on the same graph with a batch emulsion polymerisation (polystyrene stabilised by BRC3). The coalescence of the latex through semi-batch polymerisation is limited by the feeding; however, it is clear that the seeded-coagulative theory can be extended not only to other kinds of BRC but also to other kinds of latexes and operating modes (semi-batch vs. batch). As shown in Table 5, the PDI values of latexes stabilised by BRC2 and BRC3 were slightly higher than the ones stabilised by BRC1. The PDI may be slightly higher for BRC2 and BRC3 because of the simplified synthesis procedure (fewer purification steps) we used compared to BRC1. However, from a practical perspective, the simplified procedure is far more desirable and cost effective while having only a minimum impact on stabilisation performance. Overall, the associated data (Dh, Dn, Np, and as) showed consistency over the range of concentration evaluated, with comparable results between the three kinds of BRCs.
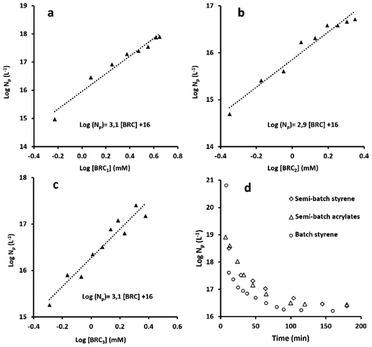 |
| Fig. 3 Evolution of Np while varying the concentration of BRC1 (a), BRC2 (b), BRC3 (c). Evolution of Np during semi-batch polymerization of styrene, semi-batch polymerization of n-BuA/MMA (50/50 v/v) and batch polymerization of styrene (d). | |
Table 5 Characterisation of latexes polymerised by BRC1 (polystyrene), BRC2 (MMA/n-BuA 50/50 v/v) and BRC3 (MMA/n-BuA 50/50 v/v) in semi-batch process
BRC |
[BRC] mM |
[BRC] BoMa % |
D
h b (nm) |
D
n b (nm) |
PDIb |
N
p c (10−15 L−1) |
a
s d (nm2 per chain) |
Based on monomer.
Determined by DLS.
Calculated from DLS data with eqn (1) based on Dh.
Calculated from Dh, assuming all the BRC chains are present at the interface.
|
BRC1 |
0.59 |
2.5 |
646 |
653 |
0.13 |
1 |
3.5 |
1.19 |
5.0 |
259 |
228 |
0.09 |
29 |
6.6 |
1.78 |
7.5 |
178 |
159 |
0.07 |
83 |
6.2 |
2.37 |
10.0 |
140 |
120 |
0.02 |
192 |
6.1 |
2.97 |
12.5 |
131 |
111 |
0.02 |
251 |
5.4 |
3.56 |
15.0 |
127 |
99 |
0.06 |
351 |
5.0 |
4.15 |
17.5 |
102 |
77 |
0.07 |
754 |
5.6 |
4.45 |
18.8 |
97 |
74 |
0.06 |
797 |
5.2 |
|
BRC2 |
0.45 |
2.0 |
756 |
607 |
0.26 |
1 |
3.3 |
0.67 |
3.0 |
474 |
406 |
0.21 |
3 |
4.5 |
0.89 |
4.0 |
422 |
379 |
0.36 |
4 |
4.2 |
1.12 |
5.0 |
247 |
219 |
0.10 |
17 |
4.8 |
1.34 |
6.0 |
233 |
200 |
0.09 |
21 |
4.3 |
1.57 |
7.0 |
227 |
207 |
0.06 |
38 |
6.5 |
1.79 |
8.0 |
233 |
178 |
0.13 |
38 |
6.0 |
2.01 |
9.0 |
205 |
180 |
0.08 |
46 |
5.0 |
2.24 |
10.0 |
175 |
149 |
0.06 |
51 |
3.7 |
|
BRC3 |
0.51 |
3.0 |
571 |
520 |
0.17 |
2 |
6.0 |
0.68 |
4.0 |
349 |
265 |
0.21 |
8 |
7.4 |
0.85 |
5.0 |
358 |
269 |
0.15 |
7 |
5.8 |
1.03 |
6.0 |
251 |
208 |
0.10 |
25 |
8.1 |
1.20 |
7.0 |
219 |
195 |
0.07 |
32 |
6.7 |
1.37 |
8.0 |
165 |
129 |
0.13 |
78 |
8.1 |
1.54 |
9.0 |
141 |
112 |
0.08 |
121 |
8.2 |
1.71 |
10.0 |
175 |
123 |
0.13 |
64 |
5.9 |
2.05 |
12.0 |
110 |
66 |
0.18 |
255 |
7.8 |
2.39 |
14.0 |
131 |
84 |
0.17 |
150 |
5.6 |
Conclusion
Block-random copolymers made of styrene, n-BuA and/or MMA with acrylic acid, were synthesised and used as stabilisers in the semi-batch emulsion polymerisation of styrene and MMA-co-n-BuA. The different BRCs showed similar CAC values and aggregate formation behaviour. The emulsion polymerisations of (meth)acrylates and styrenic latexes were successful provided the composition of the BRC was tuned to the (co)monomer composition. Polystyrene and poly(butyl acrylate) BRCs were able to stabilise most of the latexes, and the combination of those two monomers within one chain showed the best results in term of consistency as a function of emulsion polymer monomer composition. The versatility of this BRC represent an important step toward the spreading of this technology in the emulsion polymerisation field. Finally, the seeded-coagulative nucleation mechanism, first observed with styrenic based BRCs used for emulsion polymerisation of styrene, was also observed in the systems studied in this work.
Author contributions
Arthur Werner: conceptualization, data curation, formal analysis, investigation, methodology, validation, visualization, writing – original draft, writing – review & editing; Connor A. Sanders: conceptualization, formal analysis, validation, writing – review & editing; Sandra Smeltzer: conceptualization, formal analysis, validation, writing – review & editing; Sean R. George: conceptualization, funding acquisition, project administration, validation, resources, supervision, writing – review & editing; Andreas Gernandt: conceptualization, project administration, validation, resources, writing – review & editing; Bernd Reck: conceptualization, funding acquisition, project administration, validation, resources, writing – review & editing; Michael F. Cunningham: conceptualization, formal analysis, funding acquisition, project administration, resources, supervision, writing – review & editing.
Data availability
The authors confirm that the data supporting the findings of this study are available within the article and/or its ESI.†
Conflicts of interest
There are no conflicts to declare.
Acknowledgements
The authors acknowledge BASF and the Natural Sciences and Engineering Council of Canada (NSERC) for financial support.
References
- Waterborne Coatings Market Size, Trends, Growth, Report 2030, https://www.precedenceresearch.com/waterborne-coatings-market, (accessed 20 March 2023).
- T. H. Vaughn, H. R. Suter, L. G. Lundsted and M. G. Kramer, J. Am. Oil Chem. Soc., 1951, 28, 294–299 CrossRef CAS.
-
W. J. Blank and R. E. Layman, US patent, 4151143, 1979 Search PubMed.
- G. Riess, Colloids Surf., A, 1999, 153, 99–110 CrossRef CAS.
- G. Riess and C. Labbe, Macromol. Rapid Commun., 2004, 25, 401–435 CrossRef CAS.
- T. Rager, W. H. Meyer, G. Wegner, K. Mathauer, W. Mächtle, W. Schrof and D. Urban, Macromol. Chem. Phys., 1999, 200, 1681–1691 CrossRef CAS.
- H. Müller, W. Leube, K. Tauer, S. Förster and M. Antonietti, Macromolecules, 1997, 30, 2288–2293 CrossRef.
- P. Raffa, D. A. Z. Wever, F. Picchioni and A. A. Broekhuis, Chem. Rev., 2015, 115, 8504–8563 CrossRef CAS.
- K. Khougaz, Z. Gao and A. Eisenberg, Macromolecules, 1994, 27, 6341–6346 CrossRef CAS.
- C. A. Sanders, S. R. George, G. A. Deeter, J. D. Campbell, B. Reck and M. F. Cunningham, Macromolecules, 2019, 52, 4510–4519 CrossRef CAS.
- C. A. Sanders, A. Werner, S. E. Smeltzer, S. R. George, A. Gernandt, B. Reck and M. F. Cunningham, Macromolecules, 2024, 57, 3484–3495 CrossRef CAS.
- A. Werner, C. A. Sanders, S. E. Smeltzer, S. R. George, A. Gernandt, B. Reck and M. F. Cunningham, Polym. Chem., 2023, 14, 1781–1790 RSC.
- S. E. Smeltzer, C. A. Sanders, Y. Liu, S. R. George, C. Amiri, A. Gernandt, B. Reck and M. F. Cunningham, Macromolecules, 2023, 56, 1601–1614 CrossRef CAS.
- N. Hashimoto, T. Aoyama and T. Shioiri, Chem. Pharm. Bull., 1981, 29, 1475–1478 CrossRef CAS.
- L. Couvreur, C. Lefay, J. Belleney, B. Charleux, O. Guerret and S. Magnet, Macromolecules, 2003, 36, 8260–8267 CrossRef CAS.
- A. P. Narrainen, S. Pascual and D. M. Haddleton, J. Polym. Sci., Part A: Polym. Chem., 2002, 40, 439–450 CrossRef CAS.
- I. Astafieva, X. F. Zhong and A. Eisenberg, Macromolecules, 1993, 26, 7339–7352 CrossRef CAS.
- H.-D. Hwu and Y.-D. Lee, Polymer, 2000, 41, 5695–5705 CrossRef CAS.
- F. K. Hansen and J. Ugelstad, J. Polym. Sci., Polym. Chem. Ed., 1978, 16, 1953–1979 CrossRef CAS.
- S. J. Hanley, J. Giasson, J.-F. Revol and D. G. Gray, Polymer, 1992, 33, 4639–4642 CrossRef CAS.
- N. J. Warren, O. O. Mykhaylyk, D. Mahmood, A. J. Ryan and S. P. Armes, J. Am. Chem. Soc., 2014, 136, 1023–1033 CrossRef CAS PubMed.
- S. R. George, C. A. Sanders, G. A. Deeter, J. D. Campbell, B. Reck and M. F. Cunningham, Macromolecules, 2022, 55, 5279–5290 CrossRef CAS.
- C.-F. Lee, K.-R. Lin and W.-Y. Chiu, J. Appl. Polym. Sci., 1994, 51, 1621–1628 CrossRef CAS.
- H. Xu, N. Wang, T. Qu, J. Yang, Y. Yao, X. Qu and P. A. Lovell, J. Appl. Polym. Sci., 2012, 123, 1068–1078 CrossRef CAS.
- J. Zhou, L. Wang and J. Ma, Des. Monomers Polym., 2009, 12, 19–41 CrossRef CAS.
- A. Muñoz-Bonilla, S. I. Ali, A. del Campo, M. Fernández-García, A. M. van Herk and J. P. A. Heuts, Macromolecules, 2011, 44, 4282–4290 CrossRef.
|
This journal is © The Royal Society of Chemistry 2025 |
Click here to see how this site uses Cookies. View our privacy policy here.