DOI:
10.1039/C7QM00497D
(Research Article)
Mater. Chem. Front., 2018,
2, 355-361
Highly sensitive, durable and stretchable plastic strain sensors using sandwich structures of PEDOT:PSS and an elastomer†
Received
26th October 2017
, Accepted 14th December 2017
First published on 15th December 2017
Abstract
Thin-film “plastic” strain sensors can be mounted closely on textile clothing or human skin comfortably to detect human activities without any harm to the human body. However, it is a grand challenge to prepare highly sensitive and durable plastic strain sensors. Herein, we report a high-performance plastic strain sensor with a sandwich structure of poly(3,4-ethylenedioxythiophene):poly(styrenesulfonate) doped with poly(vinyl alcohol) (PVA–PEDOT:PSS)/highly conductive PEDOT:PSS/polydimethylsiloxane elastomer. The strain sensor exhibited not only high sensitivities but also good durability at large strains owing to its robust structure integration and strong recoverability in conductance. More importantly, our plastic strain sensors are successfully used to monitor a series of human activities including joint/muscle motions, arterial pulsation and voice vibration, and distinguish some complex and diverse bending motions, demonstrating great potential in practical applications.
1. Introduction
In recent years, wearable strain gauges have attracted much research interest for their broad applications in electronic skins, health monitors, soft robotics and various medical devices.1–6 Strain sensors are commonly composed of a stretchable conductor and two metal electrodes on their surface. The stretchable conductor plays an essential role of sensing external stimulation and can generate output resistance signals. A thin-film stretchable conductor is a typical item in a strain gauge,3,7,8 which can be attached to a target object for high-quality monitoring. The stretchable conductor can also be integrated with flexible electronics and used as not only a strain gauge but also as a flexible electrode or a channel.9–11 Considering the potential applications, high-performance strain sensors should meet the following requirements:7,8,12–19 (i) high sensitivity (gauge factor, GF); (ii) high mechanical durability that enables a stable resistance response to the tensile strains; (iii) high conductance for low power consumption with high optical transparency; (iv) a simple and printing/solution manufacture process; and (v) being comfortable without allergic irritation to human skin. Although lots of efforts had been devoted to strain gauges by using metal nanowires,7,12–14 metal nanoparticles,15 carbon nanotubes,16–18 carbonized cotton fabrics,19 graphene,4,6,20–22 conducting polymers,8,23etc., new strategies are required to meet the above requirements for high-performance strain gauges.
Poly(3,4-ethylenedioxythiophene):poly(styrenesulfonate) (PEDOT:PSS) has been widely employed in wearable or flexible electronic devices, such as pressure/strain sensors, flexible solar cells, light emitting diodes, and transistors, due to many advantages including solution processability, high conductivity (σ) with high optical transparency (T), good bending flexibility, excellent thermal stability and biocompatibility.24–29 However, normal PEDOT:PSS films on flexible substrates exhibited small resistance changes and low sensitivity under tensile strains.23,27 For example, typical PEDOT:PSS films doped with dimethylsulfoxide (DMSO) prepared on polydimethylsiloxane (PDMS)23 and polyethylene terephthalate (PET) substrates27 were used as strain gauges with a sensitivity of 5.5 and 2.5 at 20% strain, respectively. Our group developed a plastic strain gauge using the strong acid-treated PEDOT:PSS films embedded into PDMS8 that demonstrated a modest sensitivity of 22 at 20% strain, which was mostly attributed to the formation of PEDOT and PDMS composites at the interfaces.8 However, a structural collapse of the composite film occurred in cyclic stretching tests, leading to limited mechanical durability and a limited strain sensing region. Recently, numerous efforts have been devoted to highly stretchable and durable conductors by blending elastomers such as soft polymers,30 Zonyl FS 300 fluorosurfactant (Zonyl),23 X-triton,31 PDMS,32 and ionic liquids33,34 into PEDOT:PSS. Unfortunately, almost all the blended films are unsuitable for fabricating sensitive strain sensors because of a small change in resistance in loading tests, which suggests a low value of sensitivity. For example, Wang et al. reported a stretchable polymer conductor of PEDOT:PSS via ionic liquids and acid doping.34 Their recipe is an innovative method that endows the polymer conductors with giant conductivity and stretchability. However, the stretchable conductors failed to sense tensile strains.34 Therefore, it is a challenge to prepare highly sensitive, stretchable and durable plastic strain sensors.
Here, we demonstrate a new strategy of fabricating highly sensitive and durable plastic strain sensors via sandwich structure engineering. In the devices, a highly conductive PEDOT:PSS film is embedded between a PDMS elastomer and a PEDOT:PSS film doped with poly(vinyl alcohol) (PVA) and Zonyl. The plastic strain sensor demonstrates high sensitivity (e.g., GF ≈ 14 at 5% strain and ≈110 at 30% strain), a stable strain sensitive region of 5–30%, and good durability in stretchable-releasing tests for hundreds of cycles and long-time loading tests. The high sensitivity originates from a large resistance change (ΔR/R0), which is mainly induced by the formation of fine cracks in the PEDOT:PSS films by tensile strains and a subsequent connection between the cracks when the films were relaxed, whereas the good durability of the devices results from the mechanically robust integration of the sandwich structure. Therefore, high sensitivity, durability and a broad strain-sensing region are simultaneously achieved in the plastic strain sensors, which satisfies the basic requirements of monitoring human daily activities such as the joint/muscle activities. The plastic strain sensors clearly distinguish the complex bending motions at diverse bending angles via alternate signals, providing more functions to plastic strain gauges.
2. Experimental method
Preparation of the sandwiched stretchable conductor
A common aqueous solution of PEDOT:PSS (Clevios PH 1000) was firstly filtered through a 0.45 μm syringe filter and then was spin-coated on glass substrates (2.5 × 7.6 cm2) to form a pristine film. Upon thermal annealing, the dried pristine film was treated with 8.0 M methanesulfonic acid at high temperature of up to 160 °C. Strong acid residuals were washed out by deionized water and isopropyl alcohol followed by thermal annealing at 120 °C. Subsequently, liquid PDMS (SYLGARD 184 SILICONE ELASTOMER from Dow Corning) was dip coated on the highly conductive films (40 nm-thickness) followed by curing at 80 °C for 2 hours to obtain the PEDOT:PSS/PDMS films. The films were peeled from the donor glass substrates. Next, a blend film was spin-coated on the films placed on a glass slide using the aqueous solutions (Clevios PH 1000, blended with 2 wt% PVA (molecular weight: 146k–186k), 1 vol% Zonyl and 6 vol% DMSO). Here, 1 wt% of Zonyl was added into the solutions to enhance the wettability of the PEDOT:PSS droplets on the surfaces of the underlying layers. Finally, thermal annealing at 120 °C for 30 min was conducted.
Fabrication and characteristics of plastic strain sensors
(1) Measurement of sensitivity and durability. First, the sandwich films (length: 7.0 cm, width: 2.2 cm, and height: 0.3–1.0 mm) were prepared. Two ITO-coated glass substrates were placed on a desk platform (one slide was fixed on the platform and the other could be moved in the horizontal direction. The initial distance of both the substrates was about 2.0 cm). The ITO side was flipped by our stretchable films followed by mechanical fixation using adhesive tapes. By moving the other slide of ITO along the horizontal direction, the resistance behavior of plastic strain sensors was recorded. Here, the operating voltage was set to 0.1 V. (2) Application of plastic strain sensors. The stretchable conductor with sandwich structures was flipped and Ag wires were attached to the ends of the stretchable conductor by Ag paste. Then, the metal electrodes were glued by liquid PDMS followed by curing at 80 °C for about 2 hours, which ensured robust contact between the stretchable conductor and metal electrodes for the next monitoring.
Characterization
The transmission spectrum was measured using a Hitachi U-3010 UV-visible spectrophotometer. Film thickness was characterized using a surface profile-meter (Talysurf Series II). Electrical contacts were made by Ag paste and indium at four points of samples. Electrical conductivity was measured using the van der Pauw four-point probe method. Film morphology was investigated by optical microscopy (Nikon, Japan). Composition analysis of the films was examined by X-ray photo-electron spectroscopy (XPS, XSAM800). Resistance response to strain was characterized using a Keithley 2400 source meter.
3. Results and discussion
3.1 Structure and electrical properties of strain sensors
Fig. 1a and b show the schematic diagram and the picture of a stretchable conductor with a sandwich structure, respectively. The preparation process of the plastic strain sensor based on the sandwiched film is illustrated clearly in Fig. S1 (ESI†). Notably, methanesulfonic acid (MSA) can react with PEDOT:PSS and generate visible smoke, which is key for the achievement of the high conductivity (≈3100 S cm−1) PEDOT:PSS films. The high temperature acid treatment not only enabled the maximum removal of insulating and viscous PSS from the matrix, but also induced very weak van der Waals forces between PEDOT:PSS and glass slides for a feasible peeling. After peeling the films from glass slides, the PVA, Zonyl and DMSO blended PEDOT:PSS films with a modest conductivity of 460 S cm−1 were spin-coated on the surfaces of PEDOT:PSS/PDMS. To explain the difference in the conductivity of both the films, the S 2p XPS of the acid–PEDOT:PSS films and the blend PEDOT:PSS films are shown in Fig. 1c. The figure shows that the strong acid is more effective than the secondary solvent of DMSO in removing PSS, leading to a significant increase in film conductivity. In addition, compared with the acid–PEDOT:PSS films, the PVA–PEDOT:PSS films became more viscous and stretchable. Finally, the PVA–PEDOT:PSS/acid–PEDOT:PSS/PDMS films exhibited a transparency (T) of 75% at λ = 550 nm (see Fig. 1d), indicating a potential application in transparent or semitransparent sensing devices.
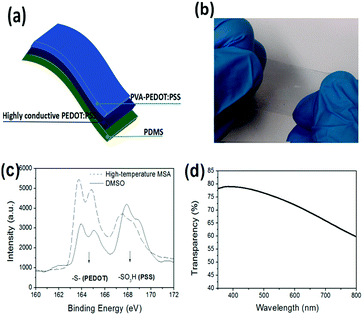 |
| Fig. 1 (a) Schematic diagram and (b) picture of the sandwiched stretchable conductor. (c) S 2p XPS of the PEDOT:PSS films by DMSO treatments and by strong acid treatments, respectively. (d) UV-visible transparency spectrum of the stretchable conductor. | |
3.2 Durability and sensitivity of strain sensors
The mechanical repeatability of the sandwiched films is first investigated in 400-cycle stretchable-releasing tests at 10%, 20% and 30% strain, respectively, as shown in Fig. 2. We found that the resistance of the films returned to the initial value (R0 ≈ 220 Ω) in the repeated loading tests at 10% and 20% strains. Meanwhile, the sandwiched films under each strain state have no remarkable variation in resistance, demonstrating outstanding mechanical repeatability and stability thanks to the robust structural integration of PDMS, acid–PEDOT:PSS and PVA–PEDOT:PSS. After the stretching–relaxing test at a strain up to 30%, the sandwiched films exhibit a slight increase in resistance (from 300 to 550 Ω), which probably resulted from the viscoelasticity of PDMS8 and slight abrasion of PEDOT:PSS in the harsh and repeated tests. Furthermore, long-time durability tests are conducted at the strains of 10–30%, as shown in Fig. 2d. Although the sandwiched films are subjected to the sustained tensile strains as long as over 120 s, they still exhibit a stable resistance response under the strains and a fast recoverability in conductance when the films are relaxed.
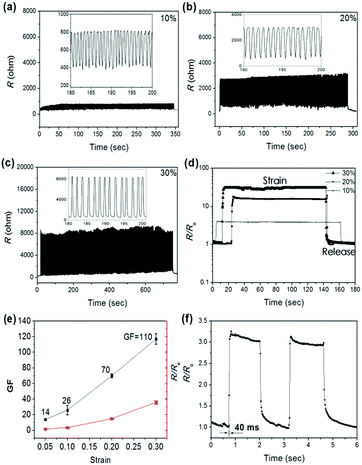 |
| Fig. 2 Resistance responses of sandwiched films in 400-cycle stretching–relaxing tests at strains of 10% (a), 20% (b) and 30% (c). (d) Resistance response in long-time loading tests. (e) Sensitivity and R/R0 as a function of strain. (f) Response time of a strain sensor in a test at about 8% strain. | |
For comparison, the repeatability and long-time durability of the reference films with the simple structure of PEDOT:PSS/PDMS are also investigated (see Fig. S2, ESI†). Obviously, an irreversible and abrupt increase in resistance was shown in the 400-cycle strain/release tests. The resistance increases irreversibly up to 2400 Ω upon the repeated loading test at 20% strain, suggesting large-domain damage of the films by the 400-cycle mechanical test. Lee et al. reported that an abrupt increase in resistance was originated from some cracks or defects generated by applied strain, which led to physical discontinuities between regions of PEDOT:PSS films.33 To confirm the discontinuity region that causes the increase in resistance, the long-time loading tests are carried out, as shown in Fig. S2b (ESI†). The reference films just afford a strain as small as 10%. With the increase of the strain up to 20%, the resistance does not recover to its initial values, whereas up to 30% strain, a large breakdown in conductance occurs, suggesting the generation of large-domain cracks and a severe discontinuity between regions of the reference films. Our results demonstrate that the sandwiched films are superior to the reference films with PEDDOT:PSS/PDMS in repeatability, long-time durability, and recoverability.
The sensitivities of the strain sensors at the strains of 5–30% are then investigated. GF is defined as (ΔR/R0)/ε, where ΔR/R0 is the relative change in resistance of the strain sensors and ε is the applied strain. It is notable that the PVA doping content plays a significant role of determining the sensitivity of the strain gauges. With the increase of PVA doping from 2 to 10 wt%, the strain sensors show lower sensitivity. And 10 wt% PVA doping causes some large aggregation of PEDOT:PSS and a following precipitate that is a challenge to filter. Therefore, 2 wt% PVA doping is selected as the optimized content in this work. Fig. 2e illustrates the calculated GF values at the strains of 5–30% and the corresponding change of R/R0, according to Fig. S3 (ESI†). The value of GF is 14 for 5% strain, 26 for 10% strain, 70 for 20% strain, and 110 for 30% strain, respectively, demonstrating the high linearity and repeatability of GF values in the strain/release tests. In addition, the response times of the strain sensors are as short as 40 ms in quick tensile strain motions (see Fig. 2f), demonstrating a fast response without obvious delays to the strain behaviors. Therefore, our sandwiched strain sensors can offer promising applications with high sensitivity, reproduction and fast response under tensile strains.
3.3 Mechanism of good durability with stable resistance response
To understand the effect of the tensile strains on the mechanical durability of the films, we investigated the micro-morphology of the PEDOT:PSS films using an optical microscope. Fig. 3a shows the morphology of the pristine sandwiched films (a) and the sandwiched films in the 400-cycle stretching–releasing tests at 20%, 30% and 40% strain. None of buckled structures or cracks appeared in the pristine sandwiched films. However, with the 400-cycle loading treatments at 20% strain, the films show buckled structures without obvious fractures, which are perhaps induced by the relaxation of the soft PDMS elastomer23 by the repeated loading, suggesting a reliable integration of the stretchable films. Upon the 400-cycle loading test at 30% strain, fine cracks with a density of 14 mm−1 are generated, resulting in a slight increase in the resistance of the sandwiched films.
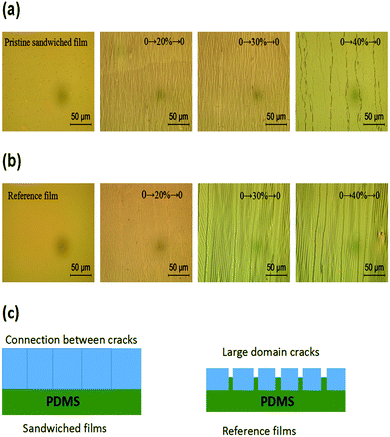 |
| Fig. 3 Micro-morphology comparison of the sandwiched films (a) and the reference films (b) with PEDOT:PSS/PDMS. (c) Schematic diagrams of crack features of sandwiched films and reference films (blue domains represent PEDOT:PSS). | |
The resistance of the sandwiched films is the sum total of the initial resistance and the generated resistance caused by the geometric distortion of the films and the crack propagation. We found that there is a relationship between R and ε as follows (see details in Fig. S4, ESI†):
| R = [1 + 1.46(e536(L−L0) − 1)]R0 | (1) |
Here,
ε =
L −
L0, where
L0 is the initial length (
i.e., 2.0 cm) of the films and
L is the tensile length. Fig. S4b (ESI
†) shows the relationship between
R/
R0 and
ε. In Fig. S4b (ESI
†), the results were obtained from the above equation and our experimental data. Obviously, the fitted curves from the equation can match well with our experimental data, demonstrating the accuracy and universality of the equation in the strain region.
When the strain increases up to 40%, severe cracks (≈35 mm−1) appear and cannot be connected when the films are released, leading to discontinuous conducting pathways that cause an irreversible increase in the resistance of the sandwiched films. In comparison, we also investigate the micro-morphology of the reference films of PEDOT:PSS/PDMS (see Fig. 3b). It shows that the crack propagation (≈25 mm−1) becomes visible upon the repeated loading tests at 20% strain and cannot be connected when the films are relaxed. With the increase of the strain up to 30%, severe cracks (≈50 mm−1) appear in relaxed PEDOT:PSS films, leading to a large increase of the electrical resistance of the films under released states. Compared with the reference films, the robust sandwich structures enable the generated cracks to be connected (or be close to each other) under the relaxed condition, leading to the plastic strain sensors with enhanced durability and stable resistance response in each cycle of strain/release. Fig. 3c illustrates the schematic diagram of crack connection and separation of the sandwiched films and the reference films after loading tests.
3.4 Application of strain sensors
3.4.1 Wearable strain sensors for sensing human motions.
The highly sensitive and durable strain sensors have a promising application for detecting human daily activities. Here, the wearable plastic strain sensors are attached on sweat trousers, jackets and rubber gloves. They provide a precise monitoring of numerous human motions including knee, elbow, finger and palm joints, as shown in Fig. 4. Fig. 4a presents the resistance response to the motions of human knees at different frequencies (f). The faster the bending-releasing of the motion, the higher the f of the output signals. With the increase of the tensile strains of the trousers caused by knee motions, the signals become sharper step by step. It is noteworthy that the resistance of the strain gauge can be recovered when the knees are relaxed fully, demonstrating a precise and stable detection of mechanical deformation. Moreover, the wearable strain sensors can monitor finger, elbow and palm activities, as shown in Fig. 4b–d. In brief, via the output signals, the detailed joint/muscle information including frequency, strength and the dynamic process can be recorded in real time and effectively.
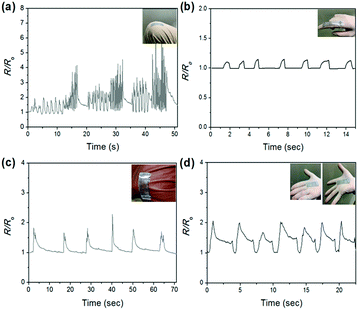 |
| Fig. 4 Real-time recording of human joint motions: (a) knee, (b) finger, (c) elbow, and (d) palm. | |
3.4.2 Bodily strain sensors as electronic skins and sound signal collectors.
Thanks to the ultra-flexibility, smoothness and thinness of the plastic strain gauge, the strain gauge can be attached well on human skin to monitor the movements of the cervical artery, muscle and even to detect the information of human sounding. It is found that no changes of resistance appeared in the films under the normal condition without bending and stretching, as shown in Fig. 5a. When the bodily sensor is attached on the epidermis of the cervical artery, a remarkable variation in resistance to the pulses of the cervical artery is displayed. The bodily devices recorded 13 obvious peaks in a span of about 11 s, reading out 70 beats per minute of pulse rate. Therefore, the strain sensors have some potential medical applications, such as evaluating the pulmonary respiratory function and improving the swallowing function of patients. Cough is one symptom of the pulmonary respiratory diseases, and many patients with lung cancer die from asphyxiation after pulmonary surgery. Our device read out the consistent cough information which resulted from throat expansion, as shown in Fig. 5c. So it helps people to record the cough information to reduce the risk of suffocating. Besides, the strain gauges are beneficial for improving the swallowing function of the patients with dysphagia. Fig. 5d shows the response of resistance to swallowing motions. The consistent signals are generated in 12 swallowing motions; it probably helps people to monitor and evaluate their swallowing function via the frequency and strength of the output signals.
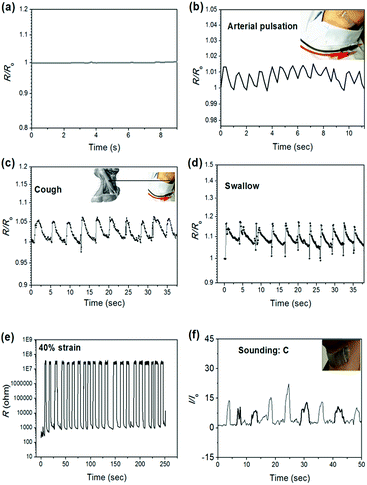 |
| Fig. 5 (a) No resistance response under normal conditions. Resistance responses of the bodily sensor to “arterial pulsation” (b), “cough” (c), “swallow” (d), respectively. (e) Stable responses in the resistance of the sensors in 21-cycle stretchable-relaxing tests at 40% strain. (f) A recorded signal that shows the characteristics in pronunciation: smoothness and continuity, and infinitesimal pause (bold curves). | |
In addition, a sandwiched film is stretched up to 40% strain to generate severe crack propagation that endows the devices with the capacity of detecting very tiny and weak vibration such as human voicing. Fig. 5e shows the resistance response of the strain sensor to the repeated stretching–relaxing at 40% strain. The resistance values are very stable (≈2.5 × 107 Ω) under 21-cycle strain. The conductance of the device could be restored reversibly to the value of 850 Ω when it is relaxed, demonstrating excellent reproducibility and repeatability. Based on pre-stretched films, the strain gauges can detect sounding vibration (i.e., speaking “C”) when attached onto the human throats. As seen in Fig. 5f, the strain sensor can distinguish the smooth pronunciation and the disturbance of voice fluency (see the bold curves in Fig. 5f) in sounding processes. The high pronunciation recognition of the devices paves a promising pathway toward the applications in human/robot pronunciation rehabilitation exercise in the future.
3.4.3 Monitoring complex bending motions.
Bending is one of the most common activities of human beings. Actually, it involves many complex motions (i.e., bending up and down) with diverse bending angles (θ, defined in Fig. 6a). To the best of our knowledge, there are few strain gauges that can distinguish complex bending motions owing to the limits of sensing performance of devices. In this work, our strain sensors by pre-stretching to 40% strain have the capability of detecting complex motions thanks to the formation of large-domain cracks in the sandwiched films. Fig. 6b shows the real-time signals of R/R0 generated by human hand bending. It should be mentioned that the strain sensor is integrated on a plastic substrate for a precise control of the bending angles. Actually, the motions of bending up and down induce the tension and compression of the cracks and the films, respectively, leading to a lower R under the tension model and a higher R under the compression model than R0. Therefore, an alternate signal is generated that is the underlying mechanism of distinguishing bending motions.
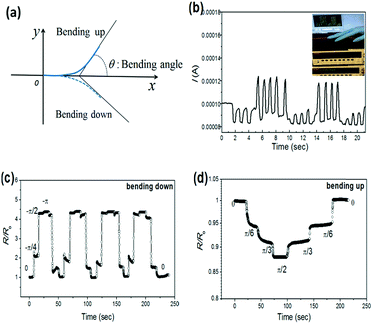 |
| Fig. 6 (a) Schematic illustration of the motions of bending up and bending down. (b) Real-time recording of the bending of the back of human hands. The inset photograph is the signals of real-time data. Response in resistance to the motions of bending down (c) and bending up (d) with different bending angles. | |
Furthermore, the strain sensor can detect diverse bending angles of bending motions. Fig. 6c shows the relative resistance change (R/R0) as a function of θ in the motion of bending down. With the decrease of θ (0 → −π/4 → −π/2 → −π), the strain of the sandwiched film became larger, increasing R/R0 to 1.80, 4.25 and 4.40, and with the increase of θ (−π → −π/2 → −π/4 → 0), the value of R/R0 recovered to 4.20, 1.50 and 0. Similar trends of resistance variation were observed in 4-cycle bending-releasing tests, demonstrating a stable and repeatable response of the plastic devices to bending. In addition, the device is capable of sensing the bending degrees of bending up, as shown in Fig. 6d. The motion of bending up is accompanied by the compression of the films and the cracks, leading to decreased resistances. It distinctly detects the bending angle (θ = 0, π/6, π/3 and π/2) via the decreased values of R/R0. On the basis of the above results, our plastic strain sensors are capable of distinguishing the complex bending motions with θ from −π to π/2.
4. Conclusion
In summary, we have fabricated a type of plastic strain sensor with high performance. The durability of the strain gauge is largely enhanced using the sandwich structure of PVA–PEDOT:PSS/acid–PEDOT:PSS/PDMS elastomer, which is contributed by the robust integration of the composites. The plastic strain sensor exhibits high sensitivity and stable resistance response both in repeated stretching–relaxing tests and in long-time loading tests due to the fine crack propagation of the sandwiched films and the connections between cracks soldered by PVA–PEDOT:PSS when the devices are relaxed. Furthermore, wearable and bodily strain sensors are integrated, which can clearly monitor a great deal of human joint/muscle activities and distinctly distinguish some complex bending motions. We believe that the new type of plastic and multifunctional strain sensors pave a promising pathway toward the bright applications due to the high sensitivity and enhanced durability.
Conflicts of interest
There are no conflicts to declare.
Notes and references
- Z. Liu, S. Fang, F. Moura, J. Ding, N. Jiang, J. Di, M. Zhang, X. Lepro, D. Galvao, C. Haines, N. Yuan, S. Yin, D. Lee, R. Wang, H. Y. Wang, W. Lv, C. Dong, R. Zhang, M. Chen, Q. Yin, Y. Chong, R. Zhang, X. Wang, M. Lima, R. Ovalle-Robles, D. Qian, H. Lu and R. H. Baughman, Science, 2015, 349, 400 CrossRef CAS PubMed.
- H. Park, Y. M. Shi and J. Kong, Nanoscale, 2013, 5, 8934 RSC.
- Y. Y. Lee, H. Y. Kang, S. H. Gwon, G. M. Choi, S. M. Lim, J. Y. Sun and Y. C. Joo, Adv. Mater., 2016, 28, 1636 CrossRef CAS PubMed.
- Y. R. Jeong, H. Park, S. W. Jin, S. Y. Hong, S.-S. Lee and J. S. Ha, Adv. Funct. Mater., 2015, 25, 4228 CrossRef CAS.
- M. Zhang, C. Wang, H. Wang, M. Jian, X. Hao and Y. Zhang, Adv. Funct. Mater., 2017, 27, 1604795 CrossRef.
- Y. Y. Qin, Q. Y. Peng, Y. J. Ding, Z. S. Lin, C. H. Wang, Y. Li, F. Xu, J. J. Li, Y. Yuan, X. D. He and Y. B. Li, ACS Nano, 2015, 9, 8933 CrossRef CAS PubMed.
- M. Amjadi, A. Pichitpajongkit, S. Lee, S. Ryu and I. Park, ACS Nano, 2014, 8, 5154 CrossRef CAS PubMed.
- X. Fan, B. Xu, N. X. Wang, J. Z. Wang, S. H. Liu, H. Wang and F. Yan, Adv. Electron. Mater., 2017, 3(5), 1600471 CrossRef.
- K. S. Kim, Y. Zhao, H. Jang, S. Y. Lee, J. M. Kim, K. S. Kim, J. H. Ahn, P. Kim, J. Y. Choi and B. H. Hong, Nature, 2009, 457(7230), 706 CrossRef CAS PubMed.
- X. Fan, B. Xu, S. Liu, C. Cui, J. Wang and F. Yan, ACS Appl. Mater. Interfaces, 2016, 8, 14029 CAS.
- C. Liao, C. Mak, M. Zhang, H. L. W. Chan and F. Yan, Adv. Mater., 2015, 27, 676 CrossRef CAS PubMed.
- M. Park, J. Im, M. Shin, Y. Min, J. Park, H. Cho, S. Park, M.-B. Shim, S. Jeon, D.-Y. Chung, J. Bae, J. Park, U. Jeong and K. Kim, Nat. Nanotechnol., 2012, 7(12), 803 CrossRef CAS PubMed.
- S. Gong and W. L. Cheng, Adv. Electron. Mater., 2017, 3(3), 1600314 CrossRef.
- S. Gong, D. T. H. Lai, B. Su, K. J. Si, Z. Ma, L. W. Yap, P. Z. Guo and W. L. Cheng, Adv. Electron. Mater., 2015, 1(4), 1400063 CrossRef.
- C. Z. Luo, J. J. Jia, Y. N. Gong, Z. C. Wang, Q. Fu and C. X. Pan, ACS Appl. Mater. Interfaces, 2017, 9, 19955 CAS.
- T. Yamada, Y. Hayamizu, Y. Yamamoto, Y. Yomogida, A. IzadiNajafabadi, D. N. Futaba and K. Hata, Nat. Nanotechnol., 2011, 6(5), 296 CrossRef CAS PubMed.
- D. J. Lipomi, M. Vosgueritchian, B. C. K. Tee, S. L. Hellstrom, J. A. Lee, C. H. Fox and Z. Bao, Nat. Nanotechnol., 2011, 6(12), 788 CrossRef CAS PubMed.
- K. Suzuki, H. Yataka, Y. Okumiya, S. Sakakibara, K. Sako, H. Mimura and Y. Inoue, ACS Sens., 2016, 1, 817 CrossRef CAS.
- M. Zhang, C. Wang, H. Wang, M. Jian, X. Hao and Y. Zhang, Adv. Funct. Mater., 2017, 27, 1604795 CrossRef.
- S. H. Bae, Y. Lee, B. K. Sharma, H. J. Lee, J. H. Kim and J. H. Ahn, Carbon, 2013, 51, 236 CrossRef CAS.
- S. Wu, R. B. Ladani, J. Zhang, K. Ghorbani, X. Zhang, A. P. Mouritz, A. J. Kinloch and C. H. Wang, ACS Appl. Mater. Interfaces, 2016, 8, 24853 CAS.
- S. Chen, Y. Wei, X. Yuan, Y. Lin and L. Liu, J. Mater. Chem. C, 2016, 4, 4304 RSC.
- S. Savagatrup, E. Chan, S. M. Renteria-Garcia, A. D. Printz, A. V. Zaretski, T. F. O’Connor, D. Rodriquez, E. Valle and D. J. Lipomi, Adv. Funct. Mater., 2015, 25, 427 CrossRef CAS.
- S. I. Na, S. S. Kim, J. Jo and D. Y. Kim, Adv. Mater., 2008, 20, 4061 CrossRef CAS.
- Y. Xia, K. Sun and J. Ouyang, Adv. Mater., 2012, 24, 2436 CrossRef CAS PubMed.
- N. Kim, S. Kee, S. H. Lee, B. H. Lee, Y. H. Kahng, Y. R. Jo, B. J. Kim and K. Lee, Adv. Mater., 2014, 26, 2268 CrossRef CAS PubMed.
- J. G. Tait, B. J. Worfolk, S. A. Maloney, T. C. Hauger, A. L. Elias, J. M. Buriak and K. D. Harris, Sol. Energy Mater. Sol. Cells, 2013, 110, 98 CrossRef CAS.
- X. Y. Liu, L. Ye, W. C. Zhao, S. Q. Zhang, S. S. Li, G. M. Su, C. Wang, H. Ade and J. H. Hou, Mater. Chem. Front., 2017, 1, 2057 RSC.
- Y. Tian, Y. C. Ling, Y. Shu, C. K. Zhou, T. Besara, T. Siegrist, H. W. Gao and B. W. Ma, Adv. Electron. Mater., 2016, 2(7), 1600165 CrossRef.
- P. Li, K. Sun and J. Ouyang, ACS Appl. Mater. Interfaces, 2015, 7(33), 18415 CAS.
- J. Y. Oh, S. Kim, H.-K. Baik and U. Jeong, Adv. Mater., 2016, 28(22), 4455 CrossRef CAS PubMed.
- T. S. Hansen, K. West, O. Hassager and N. B. Larsen, Adv. Funct. Mater., 2007, 17(16), 3069 CrossRef CAS.
- M. Y. Teo, N. Kim, S. Kee, B. S. Kim, G. Kim, S. Hong, S. Jung and K. Lee, ACS Appl. Mater. Interfaces, 2017, 9, 819 CAS.
- Y. Wang, C. X. Zhu, R. Pfattner, H. P. Yan, L. H. Jin, S. C. Chen, F. Molina-Lopez, F. Lissel, J. Liu, N. I. Rabiah, Z. Chen, J. W. Chung, C. Linder, M. F. Toney, B. Murmann and Z. N. Bao, Sci. Adv., 2017, 3(3), e1602076 CrossRef PubMed.
Footnote |
† Electronic supplementary information (ESI) available. See DOI: 10.1039/c7qm00497d |
|
This journal is © the Partner Organisations 2018 |
Click here to see how this site uses Cookies. View our privacy policy here.