DOI:
10.1039/D1NR06058A
(Minireview)
Nanoscale, 2021,
13, 19828-19839
Artificial interphase engineering to stabilize aqueous zinc metal anodes
Received
14th September 2021
, Accepted 10th November 2021
First published on 11th November 2021
Abstract
Aqueous Zn-ion system combining the advantages of energy density, intrinsic safety, and environmental benignity, has been regarded as a promising power source for future electronics. Besides cathodes and electrolytes, more attention should be paid to stabilizing zinc metal anodes since the main challenges in current aqueous Zn-ion batteries are still the hydrogen evolution and dendrite growth of the zinc anode. Thereupon, artificial interphase engineering that integrates the highly tunable, selectable, and controllable characteristics becomes one of the most effective ways to stabilize zinc anodes. In this mini-review, state-of-the-art knowledge on the rational interphase engineering of aqueous zinc metal anodes in the functional layer coating and in situ solid electrolyte interphase formation are covered. The main focus of this work is to summarize the most recent development of artificial interphases in chemical composition, structure, and function. The potential issues and perspectives regarding materials and methods are presented.
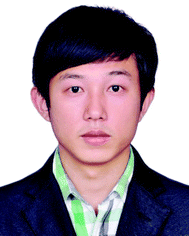 Zichao Yan | Zichao Yan received his PhD degree in the Institute for Superconducting and Electronic Materials, University of Wollongong, Australia in 2020. He is currently an Assistant Professor at Hunan University, China. His research has been focused on energy storage materials for battery applications, especially on novel composite materials and new electrolytes for sodium/zinc-based storage systems. |
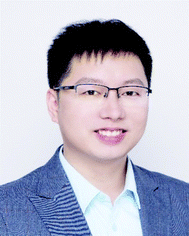 Zhiqiang Zhu | Zhiqiang Zhu is a Full Professor at the College of Chemistry and Chemical Engineering at Hunan University, China. He received his B.S. (2010) and Ph.D. (2015) from Nankai University under the supervision of Prof. Jun Chen. After working as a research fellow at Prof. Xiaodong Chen's group at Nanyang Technological University, he started his independent research career as a Full Professor at Hunan University in December 2019. His current research interests focus on functional materials for rechargeable batteries. |
1. Introduction
The development of energy storage devices with high energy density and addressing safety issues is a constant topic that people have pursued all the time.1–4 In recent years, battery fires resulting from flammable organic electrolytes and highly active alkalis metal anodes (Li and Na) have further stimulated the research interests in safer batteries.5–8,63,64 To meet the goal, batteries that are assembled in aqueous electrolytes and can be utilized for a long period of time without safety and reliability issues, will be of broad interest to society.9 Aqueous Zn-ion batteries (AZIBs) that consist of nonflammable electrolyte (water) and stable anode (metallic zinc) are promising for large-scale energy storage owing to their intrinsic safety, low cost, and environmental benignity. Undoubtedly, the utilization of metallic zinc (Zn) with high specific capacity (820 mA h g−1) and low redox potential (−0.76 V vs. the standard hydrogen electrode) can realize a competitive energy density. However, the main challenges in current AZIBs are still the hydrogen evolution and dendrite growth of the zinc anode, which could result in low Coulombic efficiency (CE) and a short lifespan.10 To address the above concerns, the following suggestions have been proposed: (i) the zinc anode should have a stable electrode/electrolyte interphase, which represents their abilities for prolonging the cycle life and the practical requirements of rechargeable batteries.11 (ii) The irreversible by-products on the Zn surface, such as ZnO and Zn4(OH)6SO4·xH2O should be minimized, which would promote zinc dendrite growth and corrosion.1 More specifically, the generated inactive by-products, passivating the zinc anode surface, would further block the transport of Zn2+. (iii) The electrolyte compatibility of the Zn anode should be considered. The huge charge transfer resistance during the plating and stripping processes of Zn2+ would cause energy consumption and poor rate performance.12 Experimentally, regulating the interface between the electrolyte and Zn anode by functional electrolyte additives or solid electrolyte interphase engineering may aid in reducing resistance.13 (iv) The failure of batteries in different application scenarios is different from one to another.14–16 For instance, water molecules that evaporate under high temperatures may accelerate the dehydration process, leading to the deterioration of electrochemical performance. At subzero temperatures, water would freeze and inhibit the ion transportation of an aqueous electrolyte.17 Therefore, all components inside, or outside the battery, including working conditions (temperature, current, voltage) and cathode systems (the additives may have side effects on the cathode) should be considered before discussing their performance.
The strategy of artificial interphase engineering integrates the highly tunable, selectable, and controllable characteristics, which becomes one of the simplest and most effective ways to improve the stability of Zn anodes.18,19 Compared to other strategies such as electrolyte regulating and host materials design, artificial interphase engineering aims to directly tailor the anode/electrolyte interphase to suppress severe interfacial reactions, showing great potential towards practical applications.11,20 Thus, a comprehensive summary and outlook of recent progress for interphase engineering of Zn anode are of great importance for the development of AZIBs. Although the introduction of the artificial interphase engineering of zinc anode has been briefly discussed elsewhere,9–11 a detailed discussion on the classification, functions, and design principles of the artificial interphases is lacking. This mini-review presents a comprehensive summary of the state-of-the-art knowledge on the rational interphase design to stabilize aqueous zinc metal anodes. The chemical composition, structure, functions, design principles, and methods of artificial interphases will be discussed in detail (Fig. 1).
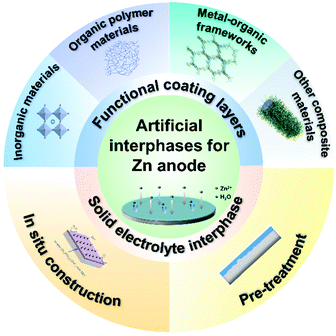 |
| Fig. 1 Schematic of strategies for artificial interphases such as functional coating layers and solid electrolyte interphases by means of materials design and interface engineering. | |
2. Functions of artificial interphases
Despite the high safety and low cost of AZIBs, the undesired side reactions associated with hydrogen evolution reaction (HER), dendrite growth, surface corrosion, and by-products formation, are still occurring at the Zn surface.21 Even worse, those complicated side reactions would further accelerate each other, leading to low CE and poor cycle life. For example, HER (eqn (1)) inevitably occurs during the zinc plating process, since the standard electrode potential of H+/H2 (0 V vs. SHE) is higher than that of Zn2+/Zn.22 |
2H2O + 2e− → 2OH− + H2↑ | (1) |
The previous research has proved that the local content of OH− ions near the anode surface increases as the HER progresses, which would accelerate the formation of the passivating layer (such as Zn hydroxides) on the Zn surface.23 Upon the by-products accumulating, the insulative passivate layer can act as a barrier to prevent the deposition and dissolution of zinc anodes, resulting in the consumption of active Zn2+ and the formation of “dead” Zn.24 Thermodynamically, nucleation of Zn2+ ions favours the sites with a lower energy barrier, while, the uneven surface corrosion by the above-mentioned side reactions would further trigger the “tip effect”, causing wild growth of zinc dendrites.25
Apparently, the side reactions are closely relevant and generally occur at the Zn/electrolyte interphase, therefore, artificially regulating the interphases would be of great help in improving the performance of AZIBs. Firstly, the construction of artificial interphase with high Zn affinity could solve the problem of Zn2+ ions deposition.26 While, its value should not be too high or too low. If the Zn affinity is too high, the plated Zn dendrites tend to grow vertically, causing the battery failure. It cannot be too low as well, which is a key criterion to judge its applicability. Actually, the value of Zn affinity is a comparative value in different reference systems and situations, the conductivity of the designed interfacial layers should be discussed, especially for high Zn affinity layers. Secondly, the hydrophily of the interfacial layer is a key factor for the interfacial impedance, polarization, and reaction kinetics.27 The unwelcome water molecules can be blocked by the hydrophobic interfacial layer, while the increased interfacial impedance and polarization would cause sluggish kinetics. Thus, the thickness and ion-conductivity of the interfacial layer should be considered for the hydrophobic interfacial layer. Similarly, proper hydrophilicity of artificial interphase can easily access electrolyte ions to the anode surface, thus improving reaction kinetics, while the side reaction resulting from water molecules would cause the battery failure. Therefore, the porous or dense characteristics of the interfacial layer should be discussed in the hydrophilic interfacial layer. Anyway, artificial interphase as the electrochemically and mechanically stable interface layer could effectively isolate both H2O molecules and electrolyte anions to suppress corrosion reaction, promoting Zn2+ transport and reaction kinetics.28 Thus, designing artificial interphases with favourable functions, including adjusting interfacial electric field, isolating bulk electrolyte, conducting zinc ions, and regulating crystal orientation, has been regarded as one of the best strategies to improve the stability of zinc anodes.
3. Artificial interphases for Zn anode
In the past decade, research efforts in Zn batteries are mainly focused on the development of high-performance cathode materials which undoubtedly helped to optimize the electrochemical performance, but it is not the only determinant of performance in practical applications.29,61,62 The Zn anode serving as the source of Zn2+ also plays a non-negligible role in AZIBs. Looking back to the history of lithium–sulfur batteries, the research interests are generally moved from cathode to anode, since scientists realized that Li dendrites are the major obstacle for practical applications.30 Similar to lithium–sulfur batteries, although recent advances in cathode materials have improved the electrochemical performance of AZIBs, the unstable anode/electrolyte interphase-caused parasitic reactions will eventually affect its applications in the long run. In view of the consequences, the construction of robust artificial interphase to generate a moderate chemical environment for uniform Zn plating/stripping is essentially needed for practical AZIBs. Generally, functional layers coating and in situ SEI formation are the main strategies to build chemically and electrochemically stable, mechanically robust artificial interphases.
3.1 Functional coating layers
In an aqueous electrolyte, the construction of an effective surface coating layer is an efficient way to stabilize the active metal anodes.11 In the case of AZIBs, the coating layer acts as a buffer interphase to avoid direct contact of Zn metal with the aqueous electrolyte, thus it can make full use of the high specific capacity of metal anodes, and suppress the dendrite growth and parasitic reactions. Coating layers directly coated on the Zn metal surface with the thickness of micrometres may not fit for the pouch cell design due to high resistance and polarization. While the ex situ designed interfacial materials have only the protective effect for the anode, thus it can apply to match most of the cathode systems. The functions of coating layers variously depend on their chemical composition and structure. For example, the Zn2+ ions conductivity of the coating layer has responded directly to the fast-charging capability of AZIBs.31 The g-C3N4 modulating interface with the uniform nucleating electron field (the rich N species) and fast electron transport (3D porous structure and innately rich structural defects) prompted the formation of strong Zn–N transient states to capture Zn2+, which induce the stabilization and uniformity of Zn distribution to further control the dendrite growth.32 This mechanism can also be applied to other interfacial layers with strong electronegative atoms, which could offer a lower energy barrier and more homogeneously charged distribution to facilitate highly reversible Zn plating/stripping. Due to the high correlation between the structure and function of coating layers, various materials in different functions, including inorganics, organic polymers, metal–organic frameworks, and other composites, have been utilized in designing stable coating layers for Zn anode.
3.1.1 Inorganic materials.
Inorganic materials, benefiting from their high mechanical intensity, good chemical stability, and stable corrosion resistance, are widely studied as coating layers to stabilize aqueous Zn metal anodes. Compared to bare Zn anode, zinc chalcogenides that feature strong electronegativity and intrinsically low electrical conductivity are generally assumed to be tightly bound with Zn2+ by the anions of zinc chalcogenides, thus enabling long-term Zn dendrite-free plating/stripping and preventing the Zn anode from side reactions of HER and Zn corrosion.33 In this respect, Cao et al.31 proved that the zinc phosphorus coated on Zn foil (Zn@ZnP) could stabilize the Zn stripping/plating processes, mainly due to the fast ion transfer and electrochemical activation energy reducing capabilities of phosphorus atoms in the coating layer. In particular, the formed ZnP solid solution alloy further expanded the interplanar spacing of the (002) and (101) facet of Zn anode by entering the P atom to the Zn lattice, resulting in excellent high-rate performance in both the Zn/Zn symmetric cell and Zn/MnO2 full cell (Fig. 2a–c). Compared to atom entering, Ma et al.34 found that the F atoms of the ZnF2 layer could form tight electrovalent bonds with Zn atoms, giving the credit the charge migration between Zn and F atoms and charge redistribution. The Zn nucleation sites for the ZnF2 layer can be attributed to the electronegative F atoms, which could greatly limit electron delocalization, providing Zn nucleation sites with lower nucleation overpotential. With high ionic conductivity and improved H2O-resistant properties of the ZnF2 layer (Fig. 2d), the Zn@ZnF2 anode offered a 2500 h cycling performance in the symmetric cell at a current density of 5 mA cm−2 with an areal capacity of 1 mA h cm−2 (Fig. 2e). In addition to the dense zinc chalcogenides, coating layers with porous structures are also believed to have a high impact to suppress the electrolyte-induced side reactions. The artificial interphases consisting of nanoscale materials are of broad interest the researchers since their advantages in building porous protecting layers, uniforming the nucleation sites, constructing highly ordered nanochannels, and adjusting interfacial electric fields, etc. Kang et al.35 coated a porous nano-CaCO3 protection layer on the Zn anode surface to improve the stability of the Zn anode during the plating/stripping. Unlike the dense layer function in isolating electrolytes, the porous nano-CaCO3 coating layer aimed to guide uniform electrolyte flux and confined Zn plating reactions at the surface region of the Zn anode, thus suppressing the dendrite growth (Fig. 3a and b). Therefore, the porous nano-CaCO3 coated Zn cell worked well within a test period of 836 h, with only a very gradual and small polarization increment from 80 to 105 mV, which was far better than the 55 h lifespan of bare Zn cell (Fig. 3c). It is well known that the formation of Zn dendrite can be specified into nucleation and growth. The nucleation process is the initial stage of Zn deposition, its uniformity is driven by the electric field, energy barrier, and surface condition. Based on this point, Liang et al.36 prepared a highly reversible Zn anode by coating Zn2+ transportable nanoparticles, which could provide uniform nucleation sites through the favourable Maxwell–Wagner polarization of the nanoparticles (Fig. 3d). Benefiting from the high dielectric constant of the ZrO2 coating layer, the induced Maxwell–Wagner polarization not only decreased the interface impedance but also provided more controllable nucleation sites, leading to uniform Zn plating/stripping and fast reaction kinetics. Consequently, the low polarization (24 mV at 0.25 mA cm−2), high CE (99.36% at 20 mA cm−2), and long cycle life (over 3800 h at 0.25 mA cm−2) were obtained for the ZrO2-coated Zn anode (Fig. 3e and f).
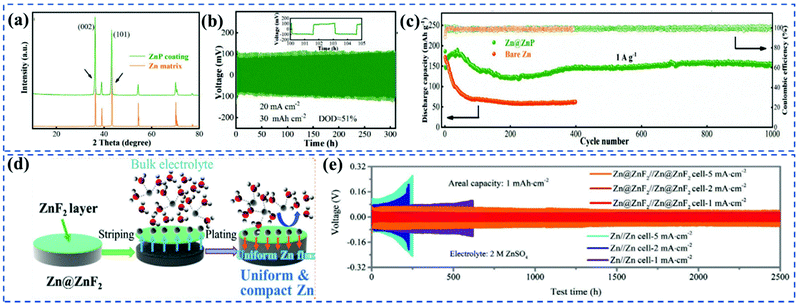 |
| Fig. 2 (a) Grazing incidence XRD (GIXRD) of ZnP coating and Zn matrix. (b) Cycling performance of symmetries cell with Zn@ZnP anode at 20 mA cm−2/30 mA h cm−2. (c) long-term cycling performance at 1 A g−1. Adapted from ref. 31, with permission from Wiley © 2021. (d) Schematic illustration of Zn deposition on Zn@ZnF2 foil; the ZnF2 layer endows a dense and dendrite-free Zn deposition by regulating Zn2+ diffusion, controlling nucleation, and prohibiting the permeation of H2O and O2. (e) Comparison of cycling stability of bare Zn∥Zn symmetric cells and Zn@ZnF2∥Zn@ZnF2 symmetric cells at 1, 2, and 5 mA cm−2 with a capacity of 1 mA h cm−2. Adapted from ref. 34, with permission from Wiley © 2021. | |
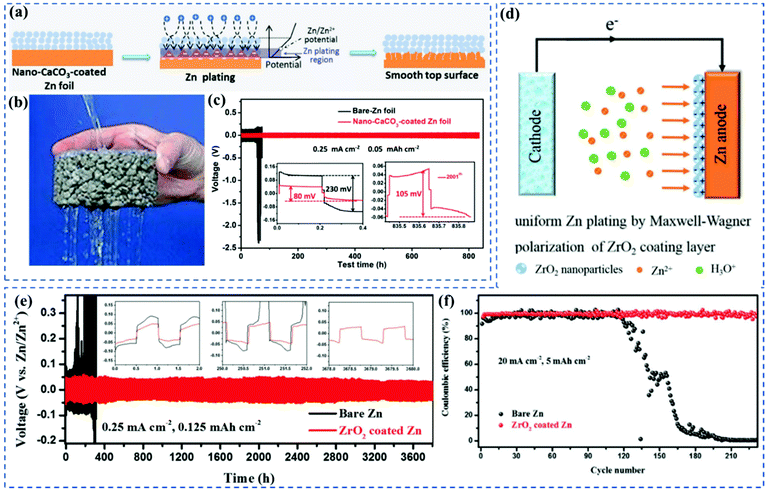 |
| Fig. 3 (a) Schematic illustrations of morphology evolution for bare and nano-CaCO3-coated Zn foils during Zn stripping/plating cycling. (b) The pores in filter papers should act as “highways” for electrolyte transport, similar to the role played by pores in water-permeable bricks. (c) Typical GCD profiles of Zn|ZnSO4 + MnSO4|Zn symmetric cells with bare (black) and nano-CaCO3-coated (red) Zn electrodes at a current density of 0.25 mA cm−2. The amount of Zn deposited in each cycle is 0.05 mA h cm−2. Insets, the first (left inset) and the last (2001th, right inset) detailed voltage profiles of cells with bare (black) and nano-CaCO3-coated (red) Zn electrodes. Adapted from ref. 35, with permission from Wiley © 2018. (d) In these cells, filter papers were employed as separators. Schematic the stripping/plating processes of the ZrO2-coated Zn anode. (e) Voltage profiles of the metallic Zn plating/stripping in Zn symmetric full-cell and ZrO2-coated Zn symmetric full-cell at 0.25 mA cm−2 for 0.125 mA h cm−2. (f) CE of Zn plating/stripping in the Zn∥Ti half-cell and the ZrO2-coated Zn∥Ti half-cell at 20 mA cm−2 with 5 mA h cm−2. Adapted from ref. 36, with permission from Wiley © 2020. | |
Lately, the inorganic coating layers with high ionic conductivity and low electrochemical activity are showing great benefits for high-rate and long-life Zn metal anodes. For example, NaTi2(PO4)3 (NTP), a typical fast ion conductor, has been demonstrated to improve the internal transport/mobility of Zn2+ due to its capability of “ion passable fence”, enabling the highly reversible Zn deposition in a Zn/MnO2 cell even at 10 C (105 mA h g−1 with a CE nearly 100% after 10
000 cycles).37 Zn affinity is an important parameter that affects the electrochemical performance of aqueous batteries. Considering the effects of crystal orientation in adjusting Zn affinity, Zhang et al.38 revealed that the (0 0 1) faceted TiO2 with −0.63 eV binding energy of Zn2+ showed a relatively low Zn affinity than the (1 0 0) facet of TiO2 (−0.95 eV), which effectively prevented Zn dendrites from growing vertically and thus realized homogeneous zinc deposition. Besides, inorganic materials with layered structures also showed good mobility and transportation toward Zn2+. The layered structure of kaolin with sieve-element function (selective channel of Zn2+) and uniform-pore distribution (≈3.0 nm) has been proposed to modulate the transference of Zn2+ while isolating bulk electrolyte from the metal Zn, alleviating the dendritic growth and corrosion.39 Later, montmorillonite was used to protect the Zn anode, ensuring a high Zn2+ transference number (t+ ≈ 0.82) and ionic conductivity (σ ≈ 3.93 mS cm−1) during the electrochemical process.40 Similar to the above-layered structure, Yang et al.41 presented that the Zn-ion diffusion channels for fast Zn2+ diffusion and stable Zn2+ flux between the electrode/electrolyte interface could also be achieved using an Mg–Al layered double hydroxide (LDH) coating layer.
3.1.2 Organic polymer materials.
Apart from designing inorganic coating layers, polymer coating as one of the widespread anti-corrosion technique has been utilized to prohibit the contact of Zn with the corrosive electrolytes.42,43 Owing to the high viscoelasticity, decent flexibility, and possession of intrinsic amide groups, polyamide was chosen as the coating layer to elevate the nucleation barrier and restrict the 2D diffusion of Zn2+.20 It has been proved that the finer size and high density of nucleus seeds of the polyamide coating layer effectively regulated the aqueous Zn deposition behavior, thus providing a 60-fold enhancement in the cycle life (over 8000 hours) compared to the polyamide-free anode. To further understand the mechanism of zinc plating/stripping in the polyimide coating layer, Zhu et al.44 prepared a polyimide-coated Zn anode that resolved the above doubts. The reason behind this was confirmed from the electrostatic potential calculation and X-ray photoelectron spectroscopy of the polyimide (Fig. 4a–d). The negative parts concentrating on the carbonyl oxygen atoms of polyimide acted as electron-donating sites were available for coordinating with Zn ions in the electrolyte, which could minimize the concentration gradient, offering fast reaction kinetics and low overpotential for Zn2+ plating and stripping (Fig. 4e and f). Considering the water-repellent capability of polymers, another new class of coating layers, the ionic liquid (IL) skinny gels, were reported to stabilize the anode/electrolyte interphase (Fig. 4g).22 Boosted by the IL solvent, Zn salts, and thiol–ene polymer compliant skeleton, the Zn/Zn symmetric cell presented a stable and sustainable cycling performance over 1000 h, as well as the Zn/MnO2 full cell (capacity retention ≈95.7% after 600 cycles) (Fig. 4h and i), indicating that the coating layer not only avoided the access of water molecules but also enabled fast and stable Zn2+ conduction.
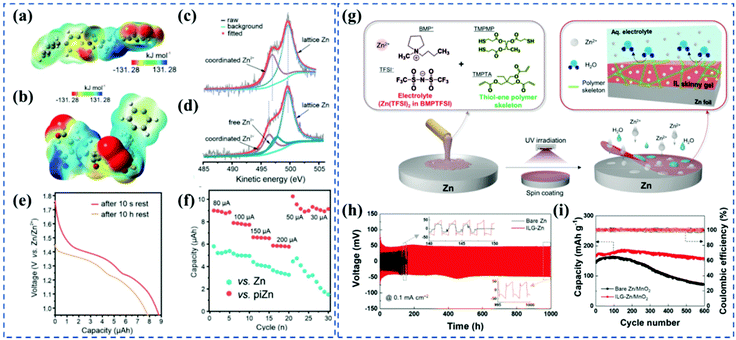 |
| Fig. 4 (a) ESP of the polyimide. (b) ESP of the cycled polyimide. (c) Zn LMM Auger spectrum of piZn before cycling. (d) Zn LMM Auger spectrum of piZn after cycling. (e) Discharge curves of a fresh piZn microbattery and that after the rest of 10 h at the fully charged state. (f) Comparisons of rate performance of the Zn and piZn microbattery. Adapted from ref. 44, with permission from Wiley © 2021. (g) Schematic illustration depicting the fabrication of an IL skinny gel on a Zn anode, along with its chemical structure and role as a water-repellent ion-conducting protective layer. (h) Galvanostatic Zn plating/stripping cyclability of the AE-containing Zn/Zn symmetric cells (ILG-Zn vs. bare Zn) at an areal capacity of 0.1 mA h cm−2 and a current density of 0.1 mA cm−2. (i) Charge/discharge cycling performance (bare Zn vs. ILG-Zn) at a current density of 2 C. Adapted from ref. 22, with permission from Wiley © 2021. | |
3.1.3 Metal–organic frameworks.
The most recently reported metal–organic frameworks (MOFs) with spatial confinement effects are introduced as functional layers to effectively modulate the diffusion, nucleation, and deposition of Zn2+.9,45 The highly ordered nanochannels and N species of the zeolitic imidazolate framework-8 (ZIF-8) have been proven to be effective protection layers in homogenizing Zn2+ flux distribution and modulating the plating/stripping rate.46 Consequently, the ZIFs coated Zn anode showed a 1200 h lifespan with a low polarization at 2 mA cm−2 in the symmetric cell, and outstanding cycling performance of 10
000 cycles in the LaVO4//Zn@ZIF full cell (Fig. 5a and b). To form an intimate ZIF-8 layer, Yuksel et al.47 built an etchable ZnO layer on the Zn surface, by etching, which then produced Zn2+ ions that were able to coordinate with the 2-methylimidazole, in situ forming the ZIF-8 layer. Additionally, they revealed that pyrolyzation of the coating layer under a gas flow of H2/Ar could achieve a hydrophilic and porous surface (Fig. 5c and d). Actually, the contact angle measurement revealed that the coating layer is not 100% hydrophilic, which is a comparative value between different decorates, thus facilitating Zn2+ ion diffusion and the production of a uniform charge distribution. This is consistent with Wang's work that the porous structure, trace amount of zinc in the framework, and high over-potential for hydrogen evolution of the annealed ZIF-8 were the reasons behind the dendrite-free Zn plating and stripping.48
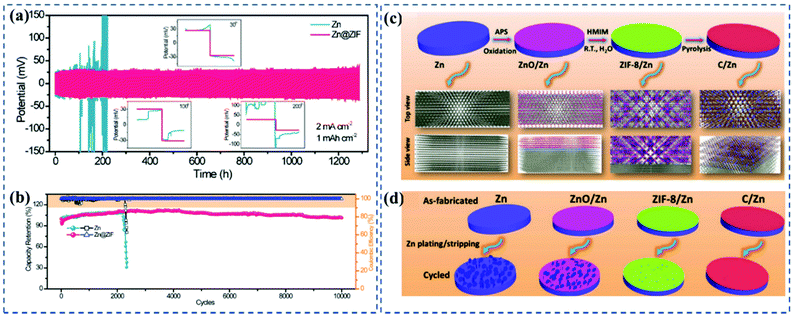 |
| Fig. 5 (a) Voltage profiles of symmetric cells based on bare Zn foil and Zn@ZIF anodes at 2 mA cm−2 with a capacity of 1 mA h cm−2. (b) Cycling performance and CE tested at 10 mA cm−2 for 10 000 cycles of the LaVO4∥Zn and LaVO4∥Zn@ZIF batteries. Adapted from ref. 46, with permission from Wiley © 2020. (c) Schematic of the Zn anode fabrication process and the predicted top and side views of the structures. (d) Schematic of dendritic Zn flake formation on Zn anodes during Zn plating–stripping. Adapted from ref. 47, with permission from Wiley © 2020. | |
3.1.4 Other composite materials.
The design of composite layers that integrate the merits of various materials has been recognized as a highly efficient way to suppress dendrite growth. So, Zhao et al.49 constructed a composited matrix, integrating the virtues of TiO2 nanoparticles and polyvinylidene fluoride, which could not only effectively assist in uniform Zn electrodeposition but also block H2O/O2 corrosion, resulting in improved electrodeposition consistency and thermodynamic stability of the Zn anode. Additionally, Cui et al.50 combined the benefits of organic and inorganic structures to design a hybrid protection layer by integrating Zn–X zeolite nanoparticles with Nafion, which shifted ion transport from channel transport in Nafion to a hopping mechanism in the composited interface. With the development of functional materials in the anode coating, more and more new functions and mechanisms by complexing organic–inorganic, organic-organic, or inorganic-inorganic materials will be revealed and broaden the interest of the researchers.51–53
In addition to the functions of coating layers in suppressing dendrites and side reactions, the high polarization value caused by the coating strategy, which is a common type of battery failure, should also be taken into account. For example, the resistance of the polyimide coating layer is estimated to be 1500 Ω, much higher than the transfer resistance at the Zn/electrolyte interface,44 which could probably result in low CE of Zn plating/stripping and low Zn utilization in long-term cycling. Considering the increased internal impedance/polarization arising from the barrier effect of the protective layers, future research works focused on the coating layers with nano-thick features and high ionic conductivity are highly emphasized to reduce the overpotential of the Zn plating/stripping, kinetically. Besides, the physical coating is hard to form even interphase for Zn deposition, thereby chemically bonding the coating layer and Zn metal at the atomic level are strongly recommended in future work, which would fundamentally lower the energy barrier of Zn2+ transferring between the protective layer and Zn anode.
3.2 Solid electrolyte interphase
Since the dense Zn2+ conductive SEI film is absent in AZIBs, the unstable anode/electrolyte interphase usually causes a series of undesired interfacial reactions.54 Inspired by the batteries operated under organic electrolytes, artificially forming a stable SEI film would dramatically aid the development of high-rate and long-life AZIBs.
The properties of SEI films are highly associated with the synthesis methods, which are generally classified into surface pre-treatment and in situ construction types. For surface pre-treatment, Hao et al.55 built an artificial ZnS interphase on the Zn surface by a vapor–solid strategy to enhance the reversibility of Zn plating/stripping (Fig. 6a). The charge distribution on ZnS not only enhanced the Zn2+ diffusion at the ZnS@Zn interphase but also increased the adhesion of the ZnS film to the Zn surface, providing a smaller voltage polarization and longer lifespan of the symmetrical cell for >1100 h at 2 mA h cm−2 compared to the bare Zn cells (Fig. 6b). The vapor–solid strategy could easily adjust the thickness and homogeneity of the SEI film, offering an in-depth study of Zn metal surface chemistry. Similarly, ZnSe film was also fabricated by exposing Zn foil in a vapored Se atmosphere (Fig. 6c).56 It has been reported that the anticorrosion and HER suppressing capabilities of the ZnSe film provided a notable rate of performance and cycling stability (1500 h) even at 10 mA cm−2 with 5 mA h cm−2 (Fig. 6d and e). In addition to the vapor–solid strategy, Xu et al.57 simply immersed a Zn plate into CuSO4 solution for a short period of time to form a uniform and robust SEI layer (Zn4SO4(OH)6·5H2O/Cu2O), which homogenized the electric field distribution and controlled the dendrite growth, leading to a long lifespan of more than 1400 h and a high average CE of 99.2% at 2.0 mA cm−2 and 2.0 mA h cm−2.
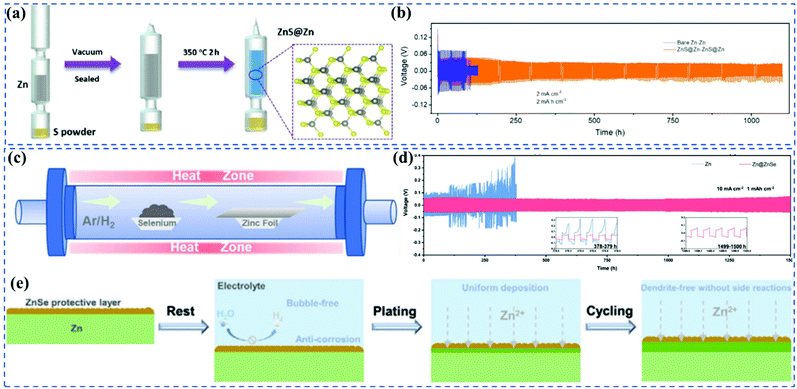 |
| Fig. 6 (a) Introducing the ZnS layer on the surface of Zn metal substrate by an in situ strategy. (b) Comparison of the cycling stability of bare Zn symmetric cell and ZnS@Zn-350 symmetric cell at 2 mA cm−2 with the capacity of 2 mA h cm−2. Adapted from ref. 55, with permission from Wiley © 2020. (c) Illustration of synthesis of Zn@ZnSe. (d) Long-term cycling test at a high rate of 10 mA cm−2 with 1 mA h cm−2 for the bare Zn and Zn@ZnSe cells. (e) Schematic illustration of the side reactions and Zn plating behaviours of the Zn@ZnSe in their whole lifecycle. Adapted from ref. 56, with permission from Wiley © 2021. | |
Even the pre-treated SEI films maintained a stable cycling performance, the lack of self-repairability is still a problem in the long run.24 Therefore, the strategy of in situ construction, adding functional additives to assist the in situ formation of stable SEI films, is a good choice for uniform Zn plating and dense zincophobic SEI growth. Cao et al.24in situ synthesized a zincophilic–zincophobic (Sn/Zn5(OH)8Cl2·H2O) SEI film by using a eutectic 7.6 m ZnCl2 aqueous electrolyte with 0.05 m SnCl2 additive. It is worth noting that the in situ produced zincophilic Sn could tightly anchor Zn foil, and further facilitate the formation of a zincophobic Zn5(OH)8Cl2·H2O film, suppressing Zn dendrite growth and water decomposition (Fig. 7a and b). With the special design, the Zn/VOPO4 full cells showed >95% capacity with a CE of >99.9% for 200 cycles at −50 °C, and retained 30% capacity at −70 °C of that at 20 °C (Fig. 7c–e). Besides, Li et al.25 found that the above robust SEI films could also be achieved at a low-concentration bi-salt Zn(OTF)2–Zn(NO3)2 electrolyte. They revealed that the self-terminated chemical reaction of NO3− with Zn2+ and OH− generated via HER could guide the formation of a conducting Zn5(CO3)2(OH)6 layer, which in turn promoted the generation of ZnF2 layer, thus forming the bi-layer SEI film (Fig. 7f). Besides inorganic additives, Cao et al.23 revealed that the decomposition of dimethyl sulfoxide (DMSO) in ZnCl2–H2O electrolyte could form Zn12(SO4)3Cl3(OH)15·5H2O, ZnSO3, and ZnS enriched SEI, which could prevent Zn dendrite and further restrain water decomposition. Later, the alkylammonium salt has also been developed to assist the formation of a robust, Zn2+-conducting, and waterproof SEI.2 The alkylammonium salt engendered the in situ formation of fluorinated and hydrophobic interphase that effectively inhibited the hydrogen evolution reaction. Specifically, this type of SEI not only showed a homogeneous thin film of 64 nm but also enabled strong compatibility with both Zn2+-conducting and waterproof components. However, the hydrophobic interphase formed in an aqueous electrolyte would increase the energy barrier for Zn nucleation/dissolution, thus increasing interfacial impedance and polarization.
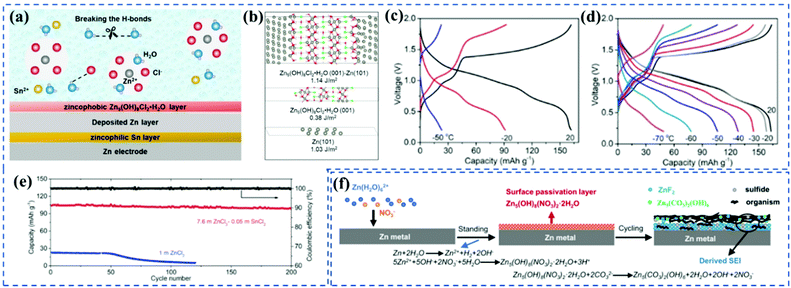 |
| Fig. 7 (a) Scheme of the electrolyte and electrolyte-electrode-interphase structure. (b) Atomic structures and related surface/interfacial energies of Zn5(OH)8Cl2·H2O surface, Zn surface, Zn5(OH)8Cl2·H2O(001)|Zn(101) interface. Electrochemical performance of VOPO4∥Zn cells using different electrolytes at different temperatures. Charge/Discharge profiles of VOPO4∥Zn cells using. (c) 1 m and (d) 7.6 m ZnCl2–0.05 m SnCl2 electrolytes. (e) Cycling performance of VOPO4∥Zn cells using different electrolytes at −50 °C with a charge/discharge current density of 1/3C. Adapted from ref. 20 with permission from the Royal Society of Chemistry © 2019. (f) ZnF2-Zn5(CO3)2(OH)6-organic SEI formation mechanism. The presence of NO3− promotes the formation of electrically and ionically insulating Zn5(OH)8(NO3)2·2H2O layer (red), which subsequently transforms into an electrically insulating but ionically conductive SEI with ZnF2-Zn5(CO3)2(OH)6 inner part coated by the organic outer part. Adapted from ref. 21 with permission from the Royal Society of Chemistry © 2020. | |
Indeed, the in situ synthesis of SEI films during the plating and stripping processes of Zn2+ would undoubtedly improve its self-repairability, this does not mean that interphase issues, such as hydrogen evolution reaction, dendrite growth, surface corrosion, and by-products formation, have been effectively addressed. Electrolyte additives are normally involved in in situ synthesis of the thin SEI films. The thin films with self-repairability have great potential for high-rate cell design due to good kinetics and reasonable resistance. While the synthesis mechanism for SEI films during the electrochemical process is sophisticated, the performance is closely related to the compatibility of all components inside, or outside the battery, including working conditions (temperature, current, voltage) and cathode systems (the additives may have side effects on the cathode). The choice of cathode systems available for the battery with in situ synthesized SEI films is limited. As we can see, the performances of SEI-protected AZIBs are far from the expectation. Therefore, selecting more suitable additives and applying more advanced in situ/ex situ techniques, including transmission electron microscopy (TEM), atomic force microscopy (AFM), secondary ion mass spectroscopy (SIMS), etc., are encouraged to provide more solid evidence to understand the microstructure, composition, thickness, and working mechanism of the in situ formed SEI films. In the meantime, some electrolyte additives can also suppress HER and dendrites without the formation of specific SEI films.58,59 Those additives can regulate the Zn2+ solvation structure to break the H-bond network and eliminate water participation.60 For that reason, the mechanism and function of selected electrolyte additives should be explained before performing the above characterizations. To better compare the relationship between properties and electrochemical performance of artificial Interphases, the interfacial materials, types, characteristics, major functions, testing conditions, and electrochemical performances of different materials relevant to artificial interphases are summarized in Table 1.
Table 1 Summary of properties and electrochemical performance of artificial interphases for AZIBs
Interfacial materials |
Types |
Characteristics |
Major functions |
Current density (mA cm−2), capacity (mA h cm−2) |
Life span (h) |
Ref. |
In |
Functional coating layer |
Corrosion inhibitor; nucleating agent |
Suppressing Zn corrosion and dendrite growth |
0.2, 0.2 |
1500 |
12
|
1, 1 |
>500 |
Sn |
Functional coating layer |
Interconnected 3D nano-channel |
Suppressing dendrite growth |
1, 1 |
800 |
16
|
Ag |
Functional coating layer |
Nucleation agent |
Guiding uniform Zn nucleation |
0.2, 0.2 |
>1400 |
18
|
2, 2 |
150 |
CNG |
Functional coating layer |
Strong tensile force; negative surface charges |
suppressing Zn corrosion |
0.25, 0.5 |
5500 |
28
|
1, 0.5 |
2956 |
g-C3N4 |
Functional coating layer |
Zincophilic interphase |
Reducing Zn2+ diffusion energy barrier; homogeneous charge distribution |
2, 2 |
500 |
32
|
10, 5 |
120 |
ZnF2 |
Functional coating layer |
Electronical insulation; Zn2+ ion conductive |
Suppressing side reactions; harmonizing Zn2+ migration |
1, 1 |
2500 |
35
|
10, 10 |
590 |
ZrO2 |
Functional coating layer |
High dielectric constant |
Enhancing Zn2+ transport kinetics; guiding uniform nucleation |
0.25, 0.125 |
>3800 |
36
|
5, 1 |
>2100 |
F-TiO2 |
Functional coating layer |
Zincophilic |
Suppressing dendrite growth; harmonizing Zn2+ migration |
1, 1 |
460 |
38
|
2, 2 |
280 |
CaCO3 |
Functional coating layer |
Porous structure |
Harmonizing Zn2+ migration; reducing Zn2+ plating rate |
0.25, 0.05 |
>800 |
35
|
MMT-Zn |
Functional coating layer |
Zn2+ ion conductive |
Suppressing Zn corrosion, passivation, and dendrites growth |
1, 0.25 |
>1000 |
26
|
10, 45 |
>1000 |
BTO |
Functional coating layer |
Ion-pumping effect |
Enhancing Zn2+ transport kinetics |
1, 1 |
4100 |
40
|
10, 5 |
720 |
HsGDY |
Functional coating layer |
Zn-ion diffusion channels; robust chemical stability |
Harmonizing Zn2+ migration |
0.5 0.5 |
2400 |
42
|
2, 2 |
2400 |
PA |
Functional coating layer |
Unique hydrogen-bonding network; strong coordination ability |
Harmonizing Zn2+ migration; suppressing Zn corrosion |
0.5, 0.25 |
8000 |
20
|
10, 10 |
70 |
COP-CMC |
Functional coating layer |
Hydrophilic layer |
Enhancing Zn2+ transport kinetics; guiding uniform nucleation; suppressing Zn corrosion and hydrogen evolution reaction |
0.25, 0.05 |
>4000 |
43
|
5, 3 |
>2000 |
Polyimide |
Functional coating layer |
Strong polar oxygen atoms |
Enhancing Zn2+ transport kinetics; reducing nucleation overpotential |
4, 2 |
300 |
44
|
ZIF-8 |
Functional coating layer |
Well-ordered nano channels and N species |
Uniforming Zn plating; enhancing Zn2+ transport kinetics |
2, 1 |
1200 |
46
|
2, 2 |
700 |
TiO2&PVDF |
Functional coating layer |
Corrosion-inhibition and electrodeposition-redirection |
Uniforming Zn plating; suppressing Zn corrosion |
0.885, 0.885 |
2000 |
49
|
8.85, 8.85 |
250 |
IL skinny gel |
Functional coating layer |
Water-repellent |
Suppressing side reactions |
0.1, 0.1 |
1000 |
22
|
0.5 1.8 |
400 |
Nafion-Zn–X |
Functional coating layer |
Ion transport channel |
Suppressing dendrite growth and side reactions |
1, 0.5 |
1000 |
50
|
1, 10 |
>1000 |
ZnF2 |
Solid electrolyte interphase |
Zn2+ conducting; waterproof SEI |
Suppressing Zn corrosion and dendrite growth |
0.5 0.25 |
>3000 |
2
|
Zn3(PO4)2·4H2O |
Solid electrolyte interphase |
Dense, stable, and Zn2+-conductive |
Suppressing side reactions |
1, 1 |
1200 |
13
|
1, 5 |
800 |
Zn12(SO4)3Cl3(OH)15·5H2O/ZnSO3/ZnS |
Solid electrolyte interphase |
Dense and self-repaired interphase |
Suppressing hydrogen evolution reaction |
0.5, 0.5 |
1000 |
23
|
ZnF2-Zn5(CO3)2(OH)6-organic |
Solid electrolyte interphase |
Electrically insulating but ionically conductive SEI |
Promoting Zn2+ diffusion; suppressing hydrogen evolution reaction |
0.5, 0.5 |
1200 |
25
|
ZnS |
Solid electrolyte interphase |
Regulable interphase |
Suppressing Zn corrosion and dendrite growth |
2.0, 2.0 |
1100 |
55
|
ZnSe |
Solid electrolyte interphase |
Low polarization voltage |
Suppressing Zn corrosion; zincophobic |
1.0, 1.0 |
1500 |
56
|
10, 1.0 |
1500 |
ZCO |
Solid electrolyte interphase |
Electrical insulation but ion conductive SEI |
Promoting electric field distribution; inhibiting dendrite growth |
1.0, 1.0 |
1400 |
57
|
2.0, 2.0 |
1400 |
4. Conclusion and perspectives
Different from the mechanism of traditional batteries operated in organic electrolytes, in which the metallic anodes are protected by the self-produced SEI film, the AZIBs operated in aqueous electrolytes are suffering from severe hydrogen evolution reactions and metallic dendrites because of the absence of an efficient SEI film. Therefore, artificially regulating the Zn/electrolyte interphase has become increasingly important. Functional layer coating and in situ solid electrolyte interphase formation could be promising solutions to the undesired dendrites and parasitic reactions on the Zn anode. A growing body of research has revealed that using artificial interphase engineering to stabilize aqueous zinc metal anodes could realize the stable Zn plating/stripping under high power and high capacity. Despite the growing interest in artificial interphase engineering in recent years, there are many potential issues and perspectives to be discussed. For functional coating layers, there are a variety of potential materials in different functions, which imply more possibilities to solve the above issues of the Zn anode. Indeed, the coating layers with multi-functions that act as buffer interphase can avoid the direct contact of Zn metal within the aqueous electrolyte. However, the physical coating is hard to form an even interphase for Zn deposition. Tightly bonding the coating layer and Zn metal at the atomic level by the chemical bond is strongly recommended to bridge the gap between the protective layer and Zn anode. Besides, the external coating strategy with poor self-repairability and loose contacts to Zn anode will be a problem for the stability of long-term cycling. Therefore, more research interest should focus on improving reaction kinetics and interphase stability in electrolyte/coating layer/Zn anode, with respects to ionic conductivity, thickness, the energy barrier of Zn2+ transferring between the protective layer and Zn anode, which would fundamentally aid the development of functional coating layers. For solid electrolyte interphase, the strategy of in situ synthesis of assisted stable SEI films, which are tightly bonded to the Zn anode is a good choice for uniform Zn plating and self-repairable SEI growth in the long run. While the formation and growth processes of SEI involved in multiple chemical reactions are sophisticated and lacking in characterization. It would be necessary to do more fundamental works that focus on mechanisms, composition, formation, and function. On the basis of developing the practically viable AZIBs, we believe that the in-depth understanding of artificial interphases in mechanism and interphase stability is the key to shed light on its future development.
Conflicts of interest
There are no conflicts to declare.
Acknowledgements
The authors are grateful for financial support from the Fundamental Research Funds for the Central Universities (531118010111; 531118010633) and National Natural Science Foundation of China (52103313; 22109041).
References
- Z. Yi, G. Chen, F. Hou, L. Wang and J. Liang, Adv. Energy Mater., 2020, 11, 2003065 CrossRef.
- L. Cao, D. Li, T. Pollard, T. Deng, B. Zhang, C. Yang, L. Chen, J. Vatamanu, E. Hu, M. J. Hourwitz, L. Ma, M. Ding, Q. Li, S. Hou, K. Gaskell, J. T. Fourkas, X. Q. Yang, K. Xu, O. Borodin and C. Wang, Nat. Nanotechnol., 2021, 16, 902–910 CrossRef CAS PubMed.
- S. Chu and A. Majumdar, Nature, 2012, 488, 294–303 CrossRef CAS PubMed.
- J. Ma, S. Zheng, P. Das, P. Lu, Y. Yu and Z.-S. Wu, Small Struct., 2020, 1, 2000053 CrossRef.
- S. F. Ye, L. F. Wang, F. F. Liu, P. C. Shi and Y. Yu, eScience, 2021 DOI:10.1016/j.esci.2021.09.003.
- D. Wang, Y. Liu, G. Li, C. Qin, L. Huang and Y. Wu, Adv. Funct. Mater., 2021, 31, 2106740 CrossRef CAS.
- Z. Zhu, Y. Tang, W. Leow, H. Xia, Z. Lv, J. Wei, X. Ge, S. Cao, Y. Zhang, W. Zhang, H. Zhang, S. Xi, Y. Du and X. Chen, Angew. Chem., Int. Ed., 2019, 58, 3521–3526 CrossRef CAS PubMed.
- Z. Yan, Q. Tian, Y. Liang, L. Jing, Z. Hu, W. Hua, A. Tayal, W. Lai, W. Wang, J. Peng, Y.-X. Wang, J. Liu, S.-L. Chou, G.-Q. Lu, H. Liu and S.-X. Dou, Cell Rep. Phys. Sci., 2021, 2, 100539 CrossRef.
- W. Lu, C. Zhang, H. Zhang and X. Li, ACS Energy Lett., 2021, 6, 2765–2785 CrossRef CAS.
- V. Verma, S. Kumar, W. Manalastas and M. Srinivasan, ACS Energy Lett., 2021, 6, 1773–1785 CrossRef CAS.
- H. Wang, R. Tan, Z. Yang, Y. Feng, X. Duan and J. Ma, Adv. Energy Mater., 2020, 11, 2000962 CrossRef.
- D. Han, S. Wu, S. Zhang, Y. Deng, C. Cui, L. Zhang, Y. Long, H. Li, Y. Tao, Z. Weng, Q.-H. Yang and F. Kang, Small, 2020, 16, 2001736 CrossRef CAS PubMed.
- X. Zeng, J. Mao, J. Hao, J. Liu, S. Liu, Z. Wang, Y. Wang, S. Zhang, T. Zheng, J. Liu, P. Rao and Z. Guo, Adv. Mater., 2021, 33, 2007416 CrossRef CAS PubMed.
- Q. Li, Y. Zhao, F. Mo, D. Wang, Q. Yang, Z. Huang, G. Liang, A. Chen and C. Zhi, EcoMat, 2020, 2, e12035 CAS.
- X. Wang and Z.-S. Wu, EcoMat, 2020, 2, e12042 CAS.
- Z. Miao, M. Du, H. Li, F. Zhang, H. Jiang, Y. Sang, Q. Li, H. Liu and S. Wang, EcoMat, 2021, 3, e12125 CrossRef CAS.
- F. Mo, G. Liang, D. Wang, Z. Tang, H. Li and C. Zhi, EcoMat, 2019, 1, e12008 CrossRef CAS.
- Q. Lu, C. Liu, Y. Du, X. Wang, L. Ding, A. Omar and D. Mikhailova, ACS Appl. Mater. Interfaces, 2021, 13, 16869–16875 CrossRef CAS PubMed.
- Y. Chu, S. Zhang, S. Wu, Z. Hu, G. Cui and J. Luo, Energy Environ. Sci., 2021, 14, 3609–3620 RSC.
- Z. Zhao, J. Zhao, Z. Hu, J. Li, J. Li, Y. Zhang, C. Wang and G. Cui, Energy Environ. Sci., 2019, 12, 1938–1949 RSC.
- H. He and J. Liu, J. Mater. Chem. A, 2020, 8, 22100–22110 RSC.
- D. Lee, H.-I. Kim, W.-Y. Kim, S.-K. Cho, K. Baek, K. Jeong, D. B. Ahn, S. Park, S. J. Kang and S.-Y. Lee, Adv. Funct. Mater., 2021, 31, 2103850 CrossRef CAS.
- L. Cao, D. Li, E. Hu, J. Xu, T. Deng, L. Ma, Y. Wang, X.-Q. Yang and C. Wang, J. Am. Chem. Soc., 2020, 142, 21404–21409 CrossRef CAS PubMed.
- L. Cao, D. Li, F. A. Soto, V. Ponce, B. Zhang, L. Ma, T. Deng, J. M. Seminario, E. Hu, X.-Q. Yang, P. B. Balbuena and C. Wang, Angew. Chem., Int. Ed., 2021, 60, 18845–18851 CrossRef CAS PubMed.
- D. Li, L. Cao, T. Deng, S. Liu and C. Wang, Angew. Chem., Int. Ed., 2021, 60, 13035–13041 CrossRef CAS PubMed.
- H. Yan, S. Li, Y. Nan, S. Yang and B. Li, Adv. Energy Mater., 2021, 11, 2100186 CrossRef CAS.
- Z. Zhu, Y. Tang, Z. Lv, J. Wei, Y. Zhang, R. Wang, W. Zhang, H. Xia, M. Ge and X. Chen, Angew. Chem., Int. Ed., 2018, 57, 3656–3660 CrossRef CAS PubMed.
- X. Zhang, J. Li, D. Liu, M. Liu, T. Zhou, K. Qi, L. Shi, Y. Zhu and Y. Qian, Energy Environ. Sci., 2021, 14, 3120–3129 RSC.
- G. Liang and C. Zhi, Nat. Nanotechnol., 2021, 16, 854–855 CrossRef CAS PubMed.
- Q. Jin, X. Zhang, H. Gao and Z. Zhang, J. Mater. Chem. A, 2020, 8, 8979–8988 RSC.
- P. Cao, X. Zhou, A. Wei, Q. Meng, H. Ye, W. Liu, J. Tang and J. Yang, Adv. Funct. Mater., 2021, 31, 2100398 CrossRef CAS.
- P. Liu, Z. Zhang, R. Hao, Y. Huang, W. Liu, Y. Tan, P. Li, J. Yan and K. Liu, Chem. Eng. J., 2021, 403, 126425 CrossRef CAS.
- Q. Zhang, J. Luan, Y. Tang, X. Ji and H. Wang, Angew. Chem., Int. Ed., 2020, 59, 13180–13191 CrossRef CAS PubMed.
- L. Ma, Q. Li, Y. Ying, F. Ma, S. Chen, Y. Li, H. Huang and C. Zhi, Adv. Mater., 2021, 33, 2007406 CrossRef CAS PubMed.
- L. Kang, M. Cui, F. Jiang, Y. Gao, H. Luo, J. Liu, W. Liang and C. Zhi, Adv. Energy Mater., 2018, 8, 1801090 CrossRef.
- P. Liang, J. Yi, X. Liu, K. Wu, Z. Wang, J. Cui, Y. Liu, Y. Wang, Y. Xia and J. Zhang, Adv. Funct. Mater., 2020, 30, 1908528 CrossRef CAS.
- M. Liu, J. Cai, H. Ao, Z. Hou, Y. Zhu and Y. Qian, Adv. Funct. Mater., 2020, 30, 2004885 CrossRef CAS.
- Q. Zhang, J. Luan, X. Huang, Q. Wang, D. Sun, Y. Tang, X. Ji and H. Wang, Nat. Commun., 2020, 11, 3961 CrossRef CAS PubMed.
- C. Deng, X. Xie, J. Han, Y. Tang, J. Gao, C. Liu, X. Shi, J. Zhou and S. Liang, Adv. Funct. Mater., 2020, 30, 2000599 CrossRef CAS.
- H. Yan, S. Li, Y. Nan, S. Yang and B. Li, Adv. Energy Mater., 2021, 11, 2100186 CrossRef CAS.
- Y. Yang, C. Liu, Z. Lv, H. Yang, X. Cheng, S. Zhang, M. Ye, Y. Zhang, L. Chen, J. Zhao and C. C. Li, Energy Storage Mater., 2021, 41, 230–239 CrossRef.
- Q. Yang, Y. Guo, B. Yan, C. Wang, Z. Liu, Z. Huang, Y. Wang, Y. Li, H. Li, L. Song, J. Fan and C. Zhi, Adv. Mater., 2020, 32, 2001755 CrossRef CAS PubMed.
- J. Ding, Y. Liu, S. Huang, X. Wang, J. Yang, L. Wang, M. Xue, X. Zhang and J. Chen, ACS Appl. Mater. Interfaces, 2021, 13, 29746–29754 CrossRef CAS PubMed.
- M. Zhu, J. Hu, Q. Lu, H. Dong, D. D. Karnaushenko, C. Becker, D. Karnaushenko, Y. Li, H. Tang, Z. Qu, J. Ge and O. G. Schmidt, Adv. Mater., 2021, 33, 2007497 CrossRef CAS PubMed.
- X. Pu, B. Jiang, X. Wang, W. Liu, L. Dong, F. Kang and C. Xu, Nano-Micro Lett., 2020, 12, 152 CrossRef CAS PubMed.
- X. Liu, F. Yang, W. Xu, Y. Zeng, J. He and X. Lu, Adv. Sci., 2020, 7, 2002173 CrossRef CAS PubMed.
- R. Yuksel, O. Buyukcakir, W. K. Seong and R. S. Ruoff, Adv. Energy Mater., 2020, 10, 1904215 CrossRef CAS.
- Z. Wang, J. Huang, Z. Guo, X. Dong, Y. Liu, Y. Wang and Y. Xia, Joule, 2019, 3, 1289–1300 CrossRef CAS.
- R. Zhao, Y. Yang, G. Liu, R. Zhu, J. Huang, Z. Chen, Z. Gao, X. Chen and L. Qie, Adv. Funct. Mater., 2021, 31, 2001867 CrossRef CAS.
- Y. Cui, Q. Zhao, X. Wu, X. Chen, J. Yang, Y. Wang, R. Qin, S. Ding, Y. Song, J. Wu, K. Yang, Z. Wang, Z. Mei, Z. Song, H. Wu, Z. Jiang, G. Qian, L. Yang and F. Pan, Angew. Chem., Int. Ed., 2020, 59, 16594–16601 CrossRef CAS PubMed.
- H. He, H. Qin, J. Wu, X. Chen, R. Huang, F. Shen, Z. Wu, G. Chen, S. Yin and J. Liu, Energy Storage Mater., 2021, 43, 317–336 CrossRef.
- F. Tao, Y. Liu, X. Ren, J. Wang, Y. Zhou, Y. Miao, F. Ren, S. Wei and J. Ma, J. Energy Chem., 2022, 66, 397–412 CrossRef.
- G. Liang, F. Mo, Q. Yang, Z. Huang, X. Li, D. Wang, Z. Liu, H. Li, Q. Zhang and C. Zhi, Adv. Mater., 2019, 31, 1905873 CrossRef CAS PubMed.
- J. Shin, J. Lee, Y. Park and J. W. Choi, Chem. Sci., 2020, 11, 2028–2044 RSC.
- J. Hao, B. Li, X. Li, X. Zeng, S. Zhang, F. Yang, S. Liu, D. Li, C. Wu and Z. Guo, Adv. Mater., 2020, 32, 2003021 CrossRef CAS PubMed.
- L. Zhang, B. Zhang, T. Zhang, T. Li, T. Shi, W. Li, T. Shen, X. Huang, J. Xu, X. Zhang, Z. Wang and Y. Hou, Adv. Funct. Mater., 2021, 31, 2100186 CrossRef CAS.
- X. Xu, Y. Chen, D. Zheng, P. Ruan, Y. Cai, X. Dai, X. Niu, C. Pei, W. Shi, W. Liu, F. Wu, Z. Pan, H. Li and X. Cao, Small, 2021, 17, 2101901 CrossRef CAS PubMed.
- Z. Hou, Z. Lu, Q. Chen and B. Zhang, Energy Storage Mater., 2021, 42, 517–525 CrossRef.
- A. Naveed, H. Yang, J. Yang, Y. Nuli and J. Wang, Angew. Chem., Int. Ed., 2019, 58, 2760–2764 CrossRef CAS PubMed.
- Q. Zhang, Y. Ma, Y. Lu, X. Zhou, L. Lin, Z. Yan, Q. Zhao, K. Zhang and J. Chen, Angew. Chem., Int. Ed., 2021, 60, 23357–23364 CrossRef CAS PubMed.
- W. Xin, L. Miao, L. Zhang, H. Peng, Z. Yan and Z. Zhu, ACS Mater. Lett., 2021, 3, 1819–1825 CrossRef.
- L. Zhang, L. Miao, W. Xin, H. Peng, Z. Yan and Z. Zhu, Energy Storage Mater., 2022, 44, 408–415 CrossRef.
- P. Li, H. Kim, J. Ming, H.-G. Jung, I. Belharouak and Y.-K. Sun, eScience, 2021 DOI:10.1016/j.esci.2021.10.002.
- S. Ye, L. Wang, F. Liu, P. Shi and Y. Yu, eScience, 2021 DOI:10.1016/j.esci.2021.09.003.
|
This journal is © The Royal Society of Chemistry 2021 |
Click here to see how this site uses Cookies. View our privacy policy here.