DOI:
10.1039/D3SE00099K
(Review Article)
Sustainable Energy Fuels, 2023,
7, 2042-2062
A review of renewable hydrogen hybrid energy systems towards a sustainable energy value chain
Received
27th January 2023
, Accepted 6th April 2023
First published on 6th April 2023
Abstract
Hydrogen could be a technically feasible energy vector in many circumstances, ranging from small-scale electricity provision for remote locations to large-scale hydrogen export. Additionally, the challenge of long-term/seasonal energy storage is universal when it comes to providing electricity from renewable energy systems with high levels of availability. Renewable hydrogen energy systems are, however, complex due to the transformations involved in their production, storage, and usage. Therefore, understanding the system topographies, as well as modeling the system components is critical at the design stage. This is because all components, such as photovoltaic panels and wind turbines, electrolyzers, hydrogen storage, and fuel cells, need to interface and work together optimally. Thus, this review is presented from a system perspective, aiming to elucidate how a sustainable hybrid energy system can incorporate hydrogen generation, storage, and conversion. In addition, we examine the literature on the sizing methods of system components and discuss their integration. We also discuss opportunities and challenges for renewable hydrogen hybrid energy systems.
1 Introduction
It has long been believed that fossil fuels are energy 'sources' despite their inherent nature as natural resources. However, detailed analysis indicates fossil fuels can generally be considered photosynthesis-derived energy carriers or energy vectors. Since these energy vectors are immediately consumed globally, the reverse vector, CO2, accumulates in the atmosphere.1 This accumulation of CO2 has an adverse effect on the global climate, leading to a rise in global temperatures. Burning fossil fuels is the primary cause of this phenomenon and is a major contributor to climate change. For example, in 2013, CO2 levels surpassed 400 ppm for the first time in recorded history, indicating a strong correlation between the burning of fossil fuels and climate change.2 Therefore, it is imperative to harness sustainable energy sources and vectors in the medium to long term for the planet to flourish. Renewable energy sources, such as solar, wind, and hydropower, can provide a sustainable alternative to the burning of fossil fuels. Therefore, investing in such sources will reduce the amount of CO2 in the atmosphere and help mitigate climate change's effects. Additionally, renewable energy sources are more cost-effective in the long term, and also global energy demand is considerably less compared to renewable energy sources (mainly solar and wind), which would seem to be an attractive option as a primary energy source.3
There are tens of thousands of remote areas and villages around the globe that are off-grid because of inadequate energy supply.1 There is thus societal pressure for regulation mandating similar or equivalent energy supply reliability and availability for rural or off-grid areas compared to urban or on-grid areas. Moreover, the cost of extending the existing electric grid makes alternative energy systems necessary. Aside from environmental considerations, the transportation of fossil fuels incurs an increased cost in remote or island areas; it becomes a financial driver for using locally available renewable energy sources. Hybrid renewable energy systems could offer a sustainable and clean electrical supply to off-grid communities, along with the capability to store electricity as hydrogen. Since hydrogen is a clean fuel candidate, it is advantageous to store energy as hydrogen. Additionally, they are highly energy-efficient and flexible for future energy value chains, as well as high in energy content. As a result, there can be technical arguments in favor of hydrogen-based energy systems as long as they are based on green and environmentally friendly technologies.4,5
Typically, renewable energy sources are unpredictable and often volatile. However, by combining wind turbines (WTs) with photovoltaic (PV) panels, hybrid energy systems can improve overall efficiency because of the complementary nature of solar radiation and wind. In comparison to energy systems based on diesel and/or grid extensions, hybrid energy systems have already proven to be economically viable. Additionally, it can provide better system performance than systems that utilize a single type of energy source, especially in remote areas and areas without grids.6–10 The design of renewable hybrid energy systems is heavily influenced by ensuring a reliable power supply to the consumer under variable atmospheric conditions, as well as local energy storage. Hybrid energy systems are therefore designed and assessed according to their ability to handle power outages and lack of a reliable supply.
Since prototyping and testing each design would take a long time, modeling and simulations are essential tools for evaluating a hybrid energy system and predicting its performance, regardless of whether it is on- and/or off-grid. In addition, choosing the appropriate size of components for a hybrid energy system is crucial to achieving maximum system performance while minimizing capital costs.11–13 Selection of the appropriate technology and component sizes can be challenging. This approach usually aims to meet multiple objectives while simultaneously meeting multiple constraints. For example, it aims to minimize installation and operating costs and/or environmental impact, increase reliability, and reduce investment payback periods.
Thus, a model must accurately reflect a system's essential features in order to achieve these goals. Furthermore, reliable and comprehensive experimental data is crucial when validating a model and predicting the performance of a simulated system. Moreover, because hybrid energy systems are complex and require embedded control software, it is advantageous to use a modeling environment that can model both components as well as control algorithms.
There have been several reviews in the literature on renewable hybrid energy systems focused on system modeling, optimization, and energy management,14–18 and on control objectives, techno-economics, and storage options.19–23 As part of some reviews, it has been suggested that renewable integrated energy systems can overcome intermittency and satisfy off-grid consumers' load demands and that the absence of grid-mandated storage at a scale sufficient to meet the reliability required in supply.24–27 However, it is imperative to note that, despite the attention paid to specific renewable hybrid energy systems and their relevance to a sustainable energy value chain, no systematic analysis has been conducted on the prospects of hydrogen hybrid energy systems utilizing a full range of hydrogen technologies, as well as component sizing and their integration.
Our review focuses on renewable hybrid energy systems that combine hydrogen storage with batteries to mitigate load demand and address the issue of intermittent power generation. In order to store energy for long periods at a minimal leakage rate, such as during the monsoon season or even from season to season, hydrogen storage can be designed for a lifetime of many years with minimal leakage. While batteries only last for a few years with substantial self-discharge and need to be replaced after that.5 Thus, even if the cost of the hydrogen generation and storage is relatively high, it can potentially be economically viable because the amount required is relatively small in the context of the system. This further emphasizes the importance of system sizing. Therefore, in order to assess how system components are currently functioning in the energy system, as well as how they are sized and integrated, we will collate and review the current state. The basic premise is that energy is to be delivered as electricity to consumers with a defined requirement for supply reliability, ranging from individual dwellings to remote industries to small communities. The supply of hydrogen as a fuel, in addition to electricity, will create an opportunity for integrated energy systems based on twin electricity and hydrogen vectors. For example, connecting fast-response electrolyzers to soak up excess grid capacity and contribute to grid stabilization is also possible.28 In this article, the most significant depth of scrutiny is applied to the currently most practicable (therefore most frequently installed) technologies, with a more general consideration given to technologies that are not yet commercialized or widely installed. We discuss the steps necessary to set component sizes (energy or power capacities) and integrate them into a whole-of-system model. Finally, we consider the opportunities and challenges of hydrogen hybrid energy systems.
2 Renewable hydrogen hybrid energy system
A practical implementation of a renewable hydrogen hybrid energy system is shown in Fig. 1, which closely corresponds to some demonstration projects that have been carried out.1,29 Despite the fact that hydrogen is the primary storage modality in this energy system, short- and long-term storage of electricity is also required to accommodate brief surges in demand and prolong the life of components such as fuel cells in the energy system.4 In addition, there are batteries and supercapacitors that could be used for short-term storage.
 |
| Fig. 1 A simple implementation of a renewable hydrogen hybrid energy system. | |
For the most part, hydrogen hybrid renewable energy systems have been employed on their own in stand-alone applications. Gahleitner29 examined 48 renewable hybrid energy systems (power-to-gas) with capacities from 1.5 to 140 MW. The primary means of storing electrical energy is through lead–acid batteries. Approximately 88% of hydrogen storage projects used compressed gaseous storage, and 12% used metal hydride storage, with a storage capacity ranging from 0.2 kg to 1350 kg, for hydrogen production via alkaline electrolyzers (0.005–6.3 MW). Later, Abdin1 examined 19 renewable hydrogen hybrid energy systems with capacities ranging from 1.3 to 6.3 MW. Lead–acid batteries were primarily used to store electrical energy in these systems. The majority of hydrogen production was achieved through alkaline electrolyzers (0.8–320 kW); 74% of hydrogen storage projects employed compressed gaseous storage, while 26% relied on metal hydride storage, with hydrogen storage capacity from 0.2 kg to 450 kg.
It is crucial to develop hydrogen energy infrastructure in order to successfully implement hydrogen hybrid energy systems since it provides the necessary setting for storing and transporting fuel. However, demonstrations and pilot projects are required to gain public acceptance and obtain accurate performance data. These demonstrations and pilot projects are imperative to prove hydrogen hybrid energy systems' economic and environmental benefits. In addition, they are necessary to gain public trust in terms of safety, reliability, and cost. Demonstrations and pilot projects also provide useful data to help inform the development of the hydrogen energy infrastructure and refine the design of hydrogen hybrid energy systems. There are currently a number of renewable hydrogen hybrid energy systems in operation for supplying electricity, as listed in Table 1. Developing a more complex renewable hydrogen hybrid energy system has taken place as hydrogen becomes a critical energy vector worldwide, creating an alternative, benign and sustainable energy source.30
Table 1 Renewable hydrogen hybrid energy systems are currently in operation for supplying electricity
Resource type |
Installed power (kW p) |
Electrolyser |
Battery |
Hydrogen storage |
Fuel cell |
Project in operation (Year) |
References |
Type |
Power (kW) |
Type |
Energy capacity (kW h) |
Equivalent hrs |
Type |
Volume capacity (Nm3 H2) |
Equivalent hrs |
Type |
Power (kW) |
PV |
330 |
Alkaline |
200 |
Li-ion |
1310 |
22 |
MH, 10 bar |
1502 |
37 |
PEM |
60 |
2013 |
1
|
PV |
62 |
— |
— |
— |
— |
— |
MH |
— |
— |
PEM |
54 |
2017 |
31
|
PV-wind-microhydro |
13-50-3.2 |
Alkaline |
36 |
Lead–acid |
120 |
17 |
PT, 137 bar |
2856 |
1068 |
PEM |
7 |
2004 |
32
|
PV-wind |
1–10 |
Alkaline |
5 |
Lead–acid |
42 |
8 |
PT, 10 bar |
40 |
12 |
PEM |
5 |
2001 |
33
|
Wind |
6300 |
Alkaline |
320 |
— |
— |
— |
PT, 10 bar |
90 |
— |
— |
— |
2009 |
29
|
PV-wind |
10–3 |
PEM |
4.2 |
Lead–acid |
144 |
36 |
PT, 30 bar |
54 |
20 |
PEM |
4 |
2008 |
34
|
PV |
20 |
Alkaline |
50 |
— |
— |
— |
PT, 15 bar |
8 |
5 |
Alkaline |
2.5 |
2000 |
35
|
PV |
5 |
PEM |
3.35 |
Lead–acid |
28 |
12 |
MH, 14 bar |
5.4 |
3 |
PEM |
2.4 |
2007 |
36
|
PV |
8.6 |
PEM |
4 |
Lead–acid |
1.7 |
1.7 |
— |
— |
— |
PEM |
1 |
2009 |
37
|
3 System components
3.1 Energy generation
Stand-alone renewable hydrogen hybrid systems must emphasize generating electricity from renewable sources (i.e., solar and wind). Although it has been demonstrated that hydrogen can be generated by solar thermolysis, photocatalysis, biochemical processes, etc., there is currently no widely available technology for obtaining hydrogen from solar energy other than by electrolysis of water.38 In addition, stand-alone/independent energy systems are nearly universally required at small scales compared to centralized electricity generation for the grid, so it is unlikely that processes such as solar-driven thermochemical cycles will be economically feasible.38
The key technologies for renewable (i.e., solar and wind) electricity production are photovoltaics (generation of photocurrent) and wind turbines (mechanical power coupled to a generator).
3.1.1 Photovoltaics.
A fast-growing technology, PV has reached at least 947 GW of cumulative installed capacity as of 2021.39 This is due to its cost-effectiveness, the availability of raw materials, and its environmental benefits. Additionally, research and development in the field of PV continues to increase, leading to more efficient and cost-effective solutions. As a result, global installed PV capacity could be well over 50 TW by 2050,40,41 well above prior predictions, and could supply over 50% of global electricity demand.42 SunPower® X-Series solar panels achieved a world record efficiency of 22.8%. Compared to conventional solar panels, the SunPower panel can produce up to 70% more energy in the same space over the first 25 years.43 It is widely known that the cost of PV panels varies widely, with higher-efficiency panels typically costing more than lower-efficiency panels. Additionally, higher-efficiency PV panels require less area to generate the same amount of electricity, making them more cost-effective and having higher conversion rates, meaning they can generate more electricity with the same amount of sunlight compared to lower-efficiency panels. Because of this, they have become increasingly popular for real-time applications. Therefore, installations in the MW range are becoming common because decreasing prices and capital expenditure, particularly for modules, have increased the competitiveness of PV technologies.41 In addition, due to PV's low cost and scalable nature, renewable hydrogen hybrid energy systems overwhelmingly use PV electricity as their primary energy input.1,29
3.1.2 Wind turbine.
As of 2021, around 840 GW of WTs were installed globally; this wind power capacity helps to avoid over 1.1 billion tonnes of CO2 globally, equivalent to South America's annual carbon emissions.44 A combination of cost and performance improvements in wind power technologies and production tax credits has driven wind energy capacity additions. However, the intermittent nature of wind as an energy source makes stand-alone wind energy systems unreliable, and most renewable hybrid hydrogen energy systems also include PV energy generation.1,29
Numerous electromagnetic technologies are employed in wind generators of both DC and AC types: parallel and compound DC generators, permanent-magnet or electric-field excited, asynchronous or synchronous generators. The generator type selection is made according to load, local wind-speed profile, and the application (i.e., off-grid or grid-connected).45 The doubly-fed induction generator (DFIG) is frequently used in medium-scale energy systems, both grid-connected and stand-alone. In small stand-alone systems, asynchronous or synchronous generators have also been used, but more recently, the popularity of the permanent-magnet synchronous generator (PMSG) with power converters has increased. The details of the DFIG and PMSG have been critically discussed and reviewed in ref. 46 and 47.
3.2 Hydrogen technology
A closed energy loop can be formed when renewable energy (solar and wind) and hydrogen (an energy vector) are combined, as they are natural partners in the generation of both reverse (water) and forward (hydrogen) vectors in a sustainable manner. It has been demonstrated so far that electrolyzing water is the most commonly used method of producing hydrogen in hybrid energy systems.1 In the context of hydrogen conversion technology, a fuel cell can be utilized to help improve a system's overall reliability. This is because it can generate electricity when it is critical to meet load demands. Since then, fuel cells have become increasingly popular for generating electricity in remote areas, compared to fossil fuel engines. Furthermore, hydrogen storage can be added to hybrid energy systems. This makes the hydrogen profile independent and able to adjust to the electrical load so that power can be produced.48
3.2.1 Production.
The fundamental problem of hydrogen production is to supply the energy needed to break the bond between H and O in the case of water feedstock or H and C in the case of hydrocarbon feedstock. This energy is measured in eV per bond, requiring very high temperatures for thermal energy to achieve an apparent dissociation rate: setting kT = 1 eV implies T ≈ 104 K. On the other hand, electron-volt energies are readily supplied in electrolytic processes. Hydrogen production methods utilizing renewable energy can thus be broadly classified as either thermally driven, implying the conversion of photon energy to heat, or electrically driven, implying the conversion of photons to current. The latter approach includes the direct application of photons, with electron-volt energies throughout most of the solar spectrum, to promote dissociation. Photobiochemical processes are of this type. Water electrolysis is the dominant route for producing hydrogen using renewable energy.
Thermally-driven renewable (solar) hydrogen production methods include water thermolysis, cracking, reforming, and gasifying fossil fuels through thermochemical cycles with water or hydrocarbon feedstocks. Direct thermolysis of water has been demonstrated49 but requires an impractically high temperature. Catalyzed thermolysis requires a much lower temperature50 but is again only at the demonstration stage. Nevertheless, many thermochemical cycles suitable for large-scale hydrogen production have been proposed, analyzed, and demonstrated,50 and some of these could potentially be solar-driven.49,50
Steam reforming of natural gas is the primary method for producing hydrogen in the current energy environment. This is due to the abundance of natural gas, the relatively low cost of the process, and the relatively high efficiency of the process, which produces hydrogen with only a small amount of byproducts. Global production exceeds 50 Mt annually but contributes to greenhouse gas emissions.51 The majority of hydrogen is used in petroleum refining and fertilizer production, despite its evolving use in transportation and utilities. In a small number of cases, fuel-cell vehicles are available, primarily light vehicles that can be filled at hydrogen filling stations, with a total of 685 stations available by 2021.52 Hydrogen can be produced using renewable resources most conveniently using water electrolysis.53–55
Alkaline and proton-exchange membrane (PEM) electrolyzers are two of three types of modern electrolyzers currently in use. While solid oxide electrolyzers (SOE) are a relatively new invention and operate at temperatures ranging between 600 and 1000 °C. SOE electrolyzers offer higher efficiency and less degradation of the electrolyte, making them attractive for large-scale applications. However, due to their high operating temperatures, they require expensive materials and complex systems. Nevertheless, there is a potential advantage to high-temperature electrolysis, which can be seen when we point out that the cost of electrolysis for low-temperature electrolyzer types is largely due to the consumption of electricity, which accounts for more than two-thirds of the cost.56 Therefore, high-temperature electrolysis can potentially reduce the costs of electrolysis by reducing the amount of electricity used. This could make it more cost-effective for wider adoption in the energy industry. Among these three electrolyzer technologies, each alternative has advantages and challenges for developing and integrating renewable energy sources. SOEs have the highest potential for efficiency gains in commercial configurations.57 On the other hand, PEMs offer scalability and can be deployed in a wide range of sizes and configurations. Alkaline electrolyzers have the longest track record but are less efficient than the other two technologies. Therefore, it is important to consider the pros and cons of each technology when deciding which one to choose for a particular application.
The most mature technology is the alkaline type, with a hydrogen production rate of up to 760 Nm3 h−1 at 3.5 MW electric input.55 This makes it the most cost-effective form of water electrolysis. It is also the most widely used, accounting for nearly 80% of all electrolyzers installed worldwide. This technology has a long lifespan, with a typical operational life of 20 years. It also has the advantage of being able to operate at a wide range of temperatures and pressures. Additionally, it is capable of scaling up to large-scale industrial applications. While a review by Carmo et al.58 suggested that PEM was more suitable for low-scale (hydrogen production rate up to 30 Nm3 h−1) applications. However, research has since shown that it can be adapted for larger-scale applications. This has led to the development of more efficient and cost-effective PEM systems. In recent years, PEM systems have become increasingly popular for large-scale industrial applications. As of 2017, several manufacturers were producing PEM electrolyzers with MW electric inputs; a 10 MW (hydrogen production rate of about 2000 Nm3 h−1) had been announced,59 and it has now become a reality.60 This is a significant advancement in PEM electrolysis technology, and it has paved the way for the commercialization of renewable energy sources. Currently, PEM electrolyzers are being used in a variety of industries, from automotive to aerospace. Additionally, PEM electrolyzers are being explored for use in fuel cell systems. An analysis shows that an alkaline electrolyzer has a lower stack cost than a PEM one. Since the PEM electrolyzer uses a noble metal catalyst, manufacturing costs are higher compared to alkaline. However, as the system size increases, the complexity and cost of balance of plant (BOP) PEM decrease. Also, PEM service costs are one-third of alkaline, and the total ownership cost is lower than alkaline.61 PEM electrolyzers also have a longer lifetime and a faster start-up time than alkaline electrolyzers, making them more attractive for large-scale applications. Additionally, PEM electrolyzers are better suited to higher hydrogen production pressures.
Because of the predominance of electrolyzers for hydrogen production in installed demonstrations of renewable hybrid energy systems and the maturity of electrolysis technologies relative to those not involving solar electricity, in the following subsections, we limit the discussion to hydrogen production by electrolysis.
3.2.1.1 PEM.
The rate of technological progress in PEM electrolyzers, their simplicity relative to the alkaline type, their ability to ramp up quickly, and the high purity of the produced hydrogen (an essential consideration for PEM fuel-cell vehicles) make the PEM electrolyzer the preferred device for hydrogen production using renewable energy in both grid-connected and standalone modes.
The PEM electrolyzer has been proven to produce hydrogen with high purity, around 99.99%. In addition, the thin membrane allows for better proton conductivity, which means that higher current densities can be achieved.62 Due to this, PEM electrolyzers can operate at higher current densities than alkaline electrolyzers (over 2 A cm−2), which in turn reduces the plant's overall cost. In addition, PEM electrolyzers have a low gas crossover rate, which enables them to operate in a wide range of nominal power densities (10–100%). When it comes to the change in power input, inertia does not play a role.63
The basic construction of PEM electrolyzers has mostly stayed the same over the last 50 years of research. Because they continue to use Nafion® membranes, Ir for anodes, Pt for cathodes, and Ti for current collectors, the historical performance of PEM electrolyzers has been reviewed by Carmo et al.58
3.2.1.2 Alkaline.
The alkaline electrolyzer uses a water form of electrolytes with a concentration of about 25 to 35 wt% of KOH in the electrolytes, and the hydroxide ion (OH−) is used as a charge carrier in the electrolyzer. The alkaline electrolyzers are available in two types: monopolar and bipolar. It is primarily the cell and stack designs that differ between the two types, but the principle of operation remains the same. The electrodes of each cell in a monopolar structure are directly connected to the opposite terminal of the DC power supply in parallel. On the other hand, every electrolysis cell in a bipolar configuration is connected in series. This includes the input and output electrodes, as well as the intermediate electrodes that act as anode and cathode. Alkaline electrolyzers with zero gaps (<0.5 mm between anode and cathode) have recently gained attention from manufacturers because they could be less energy-consuming.53,55
An improved alkaline electrolyzer has a current density of 0.4 A cm−2 and reduced electricity consumption. Minimum production is 25% to 40% of the rated capacity. This lower limit prevents hydrogen and oxygen from forming a potentially dangerous mixture. Operating temperatures are between 5 °C and 120 °C while operating pressures are between 10 bar and 30 bar.55,64
3.2.1.3 SOE.
When the temperature of the SOE electrolyzer is sufficiently high, oxide anions (O2−) can be conducted through the solid ceramic electrolyte (generally yttria-stabilized zirconia). A chemical reaction occurs when an electrode is in contact with the electrolyte and gas. In spite of its high operating temperature (>600 °C),53 this electrolyzer technology uses significantly less electricity as long as the temperature is sustained.65 There are several ref. 66 and 67 that provide a comprehensive overview of SOE technologies.
3.2.1.4 In summary.
PEM electrolyzers have a shorter start-up time, lower operating temperatures, and require less maintenance than alkaline electrolyzers. SOE electrolyzers are more efficient and have a smaller footprint than PEM electrolyzers. All three of these electrolyzers offer distinct advantages but also come with their own set of challenges. Alkaline electrolyzers need more energy, while PEM electrolyzers are more prone to corrosion. SOE electrolyzers are more expensive and require careful monitoring of the electrolyte to maintain optimal efficiency. However, SOE electrolyzers are more durable, require less maintenance, and can operate at higher temperatures and pressures than the other two types of electrolyzers. They can be used for a variety of applications, but the most appropriate type of electrolyzer to use will depend on the needs of the application. Ultimately, it is important to consider the desired outcome and the cost of the different types of electrolyzers when making a decision. The right choice will depend on the specific requirements of the application. Therefore, it is important to do research and compare the different types of electrolyzers to make sure that the right one is chosen for the application. It is also important to factor in the cost of maintenance and operation to ensure that the electrolyzer is cost-effective for the application.
3.2.2 Storage.
Energy from renewable resources, such as wind and solar, is intrinsically intermittent and relies on efficient and reliable storage systems in order to provide electricity to consumers. Energy storage solves the problem of balancing the generation and consumption of power. In addition, large quantities of energy can be retained to meet short-term changes in demand when grid-connected and to ensure continuity of supply in off-grid systems. Therefore, determining the correct size (energy capacity) for an energy storage sub-system is crucial to its effective functioning. The project to build a 129 MW h short-term battery storage facility for the Australian state of South Australia,68 which relies heavily on wind power, underlines both the scale at which storage needs to be developed and its fundamental importance.
Energy storage technologies can be divided into two categories: capacity-oriented storage systems (pumped hydroelectric systems, compressed air, and hydrogen) and access-oriented storage technologies (batteries, flywheels, supercapacitors, and superconducting magnetic energy storage).69 A fundamental distinction must be made between these two types of classes. By incorporating a modular unit into a storage subsystem based on batteries or other access-oriented devices, an increase in capacity can also be achieved, in addition to an increase in power capability. It is possible to decouple storage and power ratings by utilizing capacity-driven storage. This is achieved by controlling the fuel cell size according to the load power required. This is supplied by hydrogen storage with a capacity determining how long the energy can be delivered. Gray et al.5 have demonstrated that as the storage capacity of Li-ion batteries increases, there is a convergence between storage subsystem footprints utilizing electrolyzers, metal-hydride storage, and fuel cells. Furthermore, because of the modularity of batteries, supercapacitors, and other components and the cost-saving componentry of the storage subsystem, the hydrogen-based system becomes physically smaller as the scale increases. This allows for enhanced flexibility in terms of form factor, enabling more compact designs that can be deployed in more diverse locations with less space restrictions. Furthermore, the system's scalability allows for the integration of multiple types of energy storage components, which increases efficiency and reliability.
Hydrogen hybrid energy systems can store energy in multiple forms so that it can be used at different times and for different purposes since energy demands are diverse. For example, the electrochemical storage of energy in batteries enables quick access to energy when needed, while the chemical storage of energy in hydrogen can be used for long-term storage and use over a longer period of time. Solar energy can be stored in batteries for immediate use, and excess solar energy can be stored in the form of hydrogen for use at night or during periods of low solar availability. In addition, electricity stored in supercapacitors allows for quick energy bursts. For example, supercapacitors can be used to quickly start a car, whereas hydrogen fuel cells can be used to power the car for a longer duration. Energy storage flexibility allows for more efficient energy use, leading to cost savings and reduced environmental impact. Furthermore, the ability to store and use energy in multiple forms increases energy system reliability. And so, to determine the feasibility and associated costs, mainly the levelized cost of storage, of appropriate storage technology, it is imperative to know what kind of load demands the hybrid energy system will mitigate. It is also imperative to know how it is designed. This is because understanding how the system will be used, what kind of loads it will need to meet, and how to design it correctly will help determine the size of storage technology and types as well as the levelized costs. It will also help ensure that the hybrid energy system is reliable, efficient, and cost-effective while minimizing its environmental impact.
Several options exist for electricity storage, each with its own unique characteristics. It is commonly used to classify energy storage systems based on the form of energy used, as demonstrated by Abdin and Khalilpour.31 Additionally, they discuss whether electrical energy storage technologies can be integrated into power generation and distribution systems. In addition, they provide an overview of the most advanced technologies on the market today. Hydrogen hybrid energy systems store surplus energy in 3 forms: electrochemically (in batteries), chemically (in hydrogen), or electrically (in supercapacitors). Therefore, the following sections discuss these three types of storage technologies.
3.2.2.1 Rechargeable batteries.
Lithium-ion batteries are suitable options for portable electronic applications as they feature high efficiency (over 95%), high power and energy density, fast discharge rate, and the ability to last for many cycles (over 3000 cycles at 80% depth of discharge).70 In contrast, many accidents caused by overheating indicate that this technology should be more mature since it must be able to be deployed safely in extensive installations.71 It has been demonstrated, however, that Li-ion batteries can be effectively utilized in on- and off-grid systems. Griffith University, Brisbane, Australia, installed 1 MW h Li-ion batteries in 2013 at 70% depth of discharge (DoD) to store renewable energy, primarily solar power.1 In addition, around 9 MW h of Li-ion battery storage was installed by A123 Systems for sustainable energy integration and grid stability.72 Australia's largest Li-ion battery storage (129 MW h) for storing renewable energy is operational.68 In California, USA, the Moss Landing Energy Storage Facility (1600 MW h) is the world's largest Li-ion battery energy storage system.73
For a long time, lead–acid batteries have been used, primarily for small-to medium-sized storage applications. Although lithium-ion batteries and other technologies have rapidly developed, their dominance of the total battery market has not diminished.74 Vehicles account for the majority of lead–acid batteries, but communications, stationary energy storage, and other applications are also common.75 The low cost, excellent efficiency, high reliability, and surge capability of lead–acid batteries make them a popular choice for uninterruptible power supplies, power quality, and spinning reserves.70 However, due to their short life cycle, low energy density, maintenance and safety requirements, and heating in cold conditions, they are not as effective as other energy management methods.70 Valves-regulated lead–acid batteries have overcome some of these limitations.75 However, the short lifespan of lead–acid batteries makes them relatively expensive per unit of stored energy, though they are relatively cheap to install.
Flow batteries, the newest technologies in electric energy storage, separate two liquid chemical components with membranes. Redox-flow batteries (RFBs) have been proposed for load leveling, peak shaving, uninterruptible power supplies, emergency backup, and integration with wind and photovoltaic energy systems. Unlike other batteries, a liquid reservoir allows them to decouple energy and power. Thus, vanadium redox batteries (VRBs) have reached commercial development.76,77 The VRBs range in size from 0.5 to 100 MW h, with an energy density of 15–25 W h L−1. In addition, their charge/discharge efficiency is 75–80%, their life expectancy is 10–20 years with over 10
000 cycles, and their average cost is approximately 0.001 $ per kW h.76 VRBs, therefore, have an attractively low cost per unit of energy stored over their lifetime, despite being expensive at the beginning of their commercialization.
3.2.2.2 Supercapacitors.
While having a low energy density, supercapacitors have a high power density (5–15 kW kg−1). It can be recharged and discharged up to one million times, storing energy as electricity, which may contribute to its suitability for a variety of applications.78 Zhong et al.79 provided an overview of how different types of supercapacitors have advanced, such as double-layer capacitors, pseudocapacitors, and hybrid supercapacitors. The various technologies, working principles, and materials involved in supercapacitors have been explained by González et al.80 Vangari et al.81 discussed various aspects of supercapacitors, including the development of advanced materials and fabrication methods, as well as recent developments and their implications for the future of supercapacitor technology. They can meet instantaneous variations (e.g., charge/discharge times ranging from 1 to 10 seconds) in electricity demand by combining supercapacitors with technology that has a higher energy density but a lower effective power density.31
3.2.2.3 Hydrogen.
Compared to other energy vectors, hydrogen has a significant calorific advantage owing to its lower heating value (LHV), also known as net calorific value. Hydrogen is the smallest element and, as a result, is fugacious and has a low density. For example, to store 1 kg of hydrogen, a 12 m3 storage tank is required since hydrogen has a density of 0.08 kg per m3 at ambient conditions. Fig. 2 illustrates the energy density differences between hydrogen storage technologies. The amount of hydrogen required for storage varies depending on the application, thereby affecting its levelized cost.
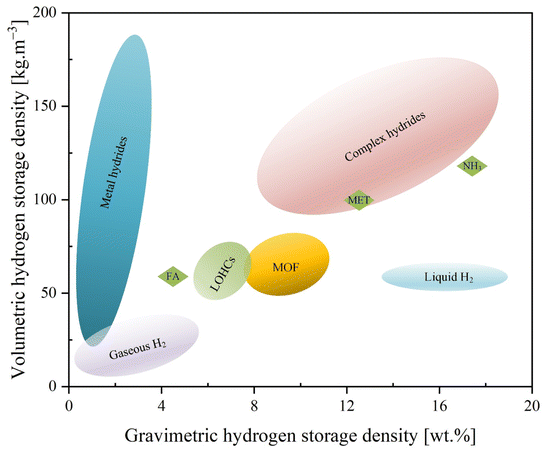 |
| Fig. 2 Volumetric and gravimetric densities (based on storage materials and storage vessels) of different hydrogen storage technologies; circular carriers: ammonia (NH3), methanol (MET), and formic acid (FA).48 | |
Compression is the most commonly used method of hydrogen storage since it is easily operated at ambient temperature and easy to store and retrieve. The hydrogen liquefaction process consumes between 25% and 45% of its energy content.48 Due to its relatively low boiling temperature (20 K), hydrogen requires bulky insulation or sophisticated cooling systems in order to remain liquid.6 Furthermore, hydrogen liquefaction faces several challenges with regard to system volume and weight, the price of tanks, and exothermic ortho–para conversion (a process through which the total nuclear spin of H2 is changed from 1 to 0).82 Increasing gas density at a given temperature is achieved through cryo-compression since the relationship between volume and pressure inverses with temperature. By lowering the tank temperature from 300 K to 77 K, the volumetric density will increase by more than 3.5 times. However, the additional materials in the cooling system decrease the system's overall volumetric and gravimetric capacities. Additionally, cryo-compression requires approximately 20% of the energy content of hydrogen in order to perform compression.83 In this article, we will not go into the details of cryo-compression, as it is still in the research and development stage.
Compressed hydrogen storage dominates renewable hydrogen energy systems because the pressurized tank is a mature technology and readily available.48 The disadvantages of compressed hydrogen storage are compressibility, safety concerns, low energy density, and transportation costs. However, despite these drawbacks, hydrogen storage is becoming a commercial reality in fuel-cell vehicles and filling stations. Compressed hydrogen storage is technically feasible in the context of providing electricity via fuel cells; however, it requires expensive compression technology, which constitutes a parasitic load on the energy system and operates at much higher pressures than conventional electro-lyzers and fuel cells.
Despite attempts to store hydrogen in liquid form in vehicles, compressed hydrogen has taken over. However, space industry experts are accustomed to cryogenic storage tanks that can store thousands of m3 of liquid hydrogen. For example, the 3800 m3 tank is located at Cape Canaveral, Florida, which holds around 245 tonnes of liquid hydrogen.84 To import pure hydrogen, Kawasaki Heavy Industry has built small hydrogen carriers capable of containing 200 tonnes.85 Economies of scale make it most suitable for centralized liquefaction plants since liquid hydrogen is likely to suffer from boil-off due to heat transfer from the exterior. However, a hydrogen hybrid energy system does not yet have a commercially viable storage system based on liquid hydrogen. This is because hydrogen liquefaction consumes 35% of its energy.86
Solid pure hydrogen has a melting point of 14.0 K at 1 atmosphere and is not considered here. However, hydrogen is adsorbed onto the surface of many porous materials in molecular form and absorbed in atomic form into the crystal structure of many materials, enabling a solid-state storage system. Owing to the relatively low heat of adsorption of H2 on most surfaces, cryogenic temperatures are required to retain an appropriate amount. To our knowledge, there are no commercially available cryo-adsorption hydrogen storage units suitable for solar/wind hybrid energy systems, so this modality is not discussed further here.
Metal hydrides (MH) encompass a wide variety of materials, including elemental metals, alloys, and nonmetallic compounds containing stoichiometric nonmetallic compounds, all of which are capable of dissociating hydrogen molecules from the surface of the material and absorbing hydrogen atoms into its crystal structure. Several studies have indicated that hydrogen can absorb and desorb by metal hydrides at a wide range of pressures and temperatures.31 Therefore, metal hydrides with relatively high hydrogen density are typically used in hydrogen hybrid energy systems. At room temperature and at pressures of up to a few bars, these can absorb and desorb hydrogen, with reaction enthalpy of between ±30 and ±40 kJ mol−1 H2.48
The benefits of metal-hydride storage include low operating pressure and high volume density, making it a useful long-term storage alternative to batteries.5 Moreover, the classic intermetallic hydride LaNi5H6 has a volumetric density of 115 kg m−3 but contains only 1.4 wt% hydrogen. In contrast, liquid hydrogen has a volumetric density of 70.8 kg m−3 at room temperature.87 Review articles and books published within the last decade provide much greater detail on the progress of solid-state hydrogen storage in terms of technology and materials. For example, ref. 88–90 and the references cited therein provide many more details.
It is also possible to store hydrogen reversibly using liquid organic molecules. They can be hydrogenated by saturating the π-bonds with hydrogen, or they can be dehydrogenated in the reverse direction. It is also possible to transport and store hydrogen using circular carriers such as ammonia and methanol. When based on gas molecules, circular carriers are liquid or liquefied under mild conditions and have similar characteristics to liquid organics. Liquid organics and circular carriers can be used to store and transport bulk hydrogen. These chemicals are widely produced, compatible with existing infrastructure, and can be delivered continuously; thus, they could be a potential candidate for hybrid energy systems. Abdin et al.48 provide more details on hydrogen storage via liquid molecules.
3.2.2.4 In summary.
All of these storage technologies offer distinct advantages but also come with their own set of challenges. For example, one of the main challenges with batteries is that their capacity and lifespan are limited. On the other hand, supercapacitors have a much higher energy density but are expensive and have a shorter lifespan. Hydrogen storage is the most promising technology, but the development of safe storage solutions has been slow due to the high flammability of hydrogen gas. In addition, hydrogen storage is difficult to scale and can be expensive to produce. This makes it challenging to implement on a large scale and limits its potential to revolutionize the energy storage industry. Moreover, these technologies significantly impact the environment if they are not properly managed. For instance, the production of battery cells and their materials, such as lithium and cobalt, require a high level of energy and water consumption, while the recycling process of batteries is still not efficient and cost-effective. They must be designed to be safe, reliable, and efficient to ensure that they do not cause any harm to the environment. Proper disposal of these technologies must also be considered to ensure that no toxins are released into the environment. Adequate recycling of these technologies is critical to reducing the amount of waste that is created. Research and development should also be conducted to identify more environmentally friendly solutions to these technologies.
3.2.3 Conversion.
Renewable hydrogen hybrid energy systems, which use hydrogen as an energy carrier for the generation of electricity, make use of fuel cells as one of the key components. Fuel cells benefit hydrogen hybrid energy systems because they are flexible, controllable, and typically located close to demand. Also, in this energy system, long-term hydrogen storage helps shift electricity from times of renewable surplus to shortfall. Fuel cell systems are gaining popularity because they deliver cheaper electricity than local utilities and allow a move away from diesel engines as an uninterruptable power supply.91 A comprehensive overview of renewable power to gas pilot plants has been provided in ref. 1 and 29. This overview also provides detailed information about the nominal power of each electricity generation device. According to this summary, the majority of electric systems are powered by fuel cells, whereas internal combustion engines or combined heat and power plants power 10% of electric systems. Thus, the discussion is limited to fuel cells.
Based on electrolyte and operating temperature, there are six types of fuel cells: alkaline fuel cells (AFCs), polymer electrolyte membrane fuel cells (PEMFCs), phosphoric acid fuel cells (PAFCs), molten carbonate fuel cells (MCFCs), solid oxide fuel cells (SOFCs) and direct methanol fuel cells (DMFCs). In ref. 92–95, a comprehensive review of hydrogen fuel cells has been conducted. Generally, solid electrolytes are used in hybrid energy systems installed in remote locations or on islands.
3.2.3.1 AFC.
The AFC is the reverse of the alkaline water electrolyzer. The operating temperature ranges up to 80 °C (low-temperature AFC) and 100 °C to 250 °C (high-temperature AFC). It has fast reaction kinetics. AFC are reliable within their lifetime and have been used in spacecraft for power generation, but they are intolerant of CO2. Generally, there is no degradation of the electrodes due to CO2, but it may cause blockage of the pores of the gas diffusion layer.96 The liquid electrolyte requires careful attention to the operating conditions to avoid flooding or drying. Both electrodes suffer from degradation because non-noble metal electrocatalysts are used. KOH electrolyte's corrosive properties limit electrocatalyst choice, affecting seals and current collectors. The low lifetime of AFC (not more than 5000 hours) is another major obstacle to large-scale commercialization.97
3.2.3.2 PEMFC.
Since the PEM fuel cell has a solid polymer membrane, it is simpler and less hazardous than an alkaline fuel cell. However, the PEM fuel cell is more complicated to manage because of the necessity of adequately hydrating the membrane.98 The PEM fuel cell can operate at temperatures ranging from 0 °C to 90 °C. In order to operate a PEM fuel cell efficiently, its membrane must be hydrated, which can only be achieved by humidifying the reactant gases. A low level of water can result in dehydration and increased membrane resistance. A large amount of water can flood the electrode pores and increase electrode resistance. Metal-hydride hydrogen storage systems are well suited to PEMs due to their sensitivity to impurities in hydrogen streams.
As for the PEM electrolyzer, the PEM fuel cell, which pre-dates its development, has become very popular for hydrogen energy systems. PEM fuel cells are now sufficiently reliable and robust to be exclusively used in fuel-cell vehicles due to zero CO2 emissions. Since about 2000, hybrid energy systems have used the PEM type almost exclusively, as reported in ref. 1 and 29. The distributed power system mainly focuses on small-scale systems, such as 50–250 kW for decentralized power and <10 kW for households.99
3.2.3.3 PAFC.
The PAFC type is a long-established technology mainly used for on-site electric power plants in the 50–250 kW range. The operating temperature is ∼200 °C. The high operating temperature compared to AFCs makes heat management more straightforward and its carbon tolerance much higher. Therefore, PAFCs are desirable in CHP applications since they operate at higher temperatures than PEMFCs.100 However, its market share has declined recently because competing technologies have become cheaper.
3.2.3.4 MCFC.
One of the fuels that can be used for MCFCs is natural gas combined with oxygen or carbon dioxide. MCFCs can be used for stationary applications over 200 kW. The high operating temperature (approximately 650 °C) makes cell efficiency higher than that of low-temperature types. However, the molten electrolyte and the need to inject carbon make this type of cell less suitable for small-scale applications, particularly those in remote locations.
3.2.3.5 SOFC.
SOFCs are the counterparts of solid-oxide electrolyzers but pre-date them in development. The SOFC has a solid oxide electrolyte and operates at temperatures from 500 to 1000 °C depending on the cell configuration. The high operating temperature leads to increased efficiency, typically 60%, making the SOFC a promising contender for hybrid energy systems, especially in CHP, when high-grade heat is needed. Using the waste heat in a steam turbine significantly increases the overall hydrogen-electricity conversion efficiency. SOFCs can use carbon-containing fuels, such as syngas, from coal gasification, so there is no need for the extensive reforming and gas clean-up required to use impure hydrogen in PEMFC systems. The SOFC is a strong candidate for stationary power generation, especially in the 1–200 kW range.99
3.2.3.6 DMFC.
The DMFC was developed to tackle the hydrogen fuel storage problem and eliminate the need for a reformer to convert methanol to hydrogen. The DMFC is classified as a PEMFC because it also uses a PEM membrane. DMFCs operate at low temperatures, usually <100 °C, and are mainly used for portable power applications below 250 W, laptops and mobile appliances, and small plants less than 5 kW.101 However, The DMFC uses methanol rather than hydrogen fuel and thus produces carbon-containing emissions. Also, the efficiency of a DMFC is less than 40%, considered the lowest among all FC technologies.102
3.2.3.7 In summary.
The different characteristics and benefits of each of these fuel cells make them suitable for various applications, depending on their intended application type. For example, AFCs have a high power density, enabling them to be ideal for producing large amounts of energy in a short period of time. On the other hand, SOFCs have high efficiency and low emissions, rendering them suitable for stationary applications. DMFCs can reach full power in a matter of seconds, making them ideal for powering devices that need a quick burst of power, such as laptops and phones. PEMFCs are suitable for mobile applications, such as electric vehicles, due to their high power and efficiency. They also provide a more consistent power output over longer periods of time and can handle sudden changes in power demand. PAFCs are the most cost-effective option, making them an appropriate choice for applications that require large amounts of energy over an extended period of time. PEMFCs and SOFCs, however, are commonly used in hydrogen hybrid energy systems as a result of their higher efficiency compared to other fuel cells. They are also ideally suited for remote applications requiring more reliable power, a longer lifespan, and high-temperature operation. For example, PEMFCs are often used in hydrogen hybrid energy systems for off-grid applications, such as powering remote homes and telecommunications sites, and SOFCs are well-suited for stationary applications, such as combined heat and power systems.
4 Component sizing and integration
In this article, the renewable hydrogen hybrid energy system is considered to be modular, assembled from components such as wind generators, batteries etc., that have specified capacities (sizes) and are interfaced with each other (integrated) and managed by a control algorithm. Control could be centralized for a complex system or decentralized for a system with few components. Specific components may operate under local control or internally in response to commands from a central controller. The concept of modules and interfaces is natural and convenient. It allows an individual component to be modeled according to its operation's scientific principles and technical details. This is done with inputs and outputs specified according to the exchange of energy, data, and commands with other components. Integration then consists of tying each component's inputs/outputs to the correct outputs/inputs of other components and specifying how and when the component is brought into action.
Integration and sizing are intertwined tasks: the optimal size of a component is determined by its usage in the system, which means the topology of its connections between components and the control approach used to manage them. As a result, sizing implies optimization, whereas integration involves physical links.
4.1 Sizing
System component sizing aims to find the most appropriate configuration according to the load, local (solar/wind) resources, technologies, and their costs. In order to properly operate the hybrid energy system and minimize building costs, the correct sizing of power and energy capacities is essential. An initial estimate can be made using global criteria like annual energy demand and time to survive without primary energy. Then, a simulation of the entire system operating according to its predetermined control algorithm should be used to refine component sizes. As a result, sizing is an iterative process when optimizing the system according to set objectives. The configuration won't be unique if optimization is limited to technical factors. This is because specific component sizes may be correlated, such that increasing one compensates for decreasing the other, e.g., PV array size and hydrogen storage capacity.5 Multi-objective optimization may, however, resolve the optimization to a unique configuration. This optimization has been discussed in detail elsewhere.16
For the purpose of developing an economically and technically optimum hybrid renewable energy system, it is possible to apply the sizing methods described in the literature (as shown in Fig. 3). To achieve the most optimal output parameters, they must, however, strike a balance between the system's reliability and its cost. The literature16,21,103–105 offers a number of optimization techniques that may be used to size components of renewable hybrid energy systems. Table 2 provides a summary of studies that have addressed sizing.
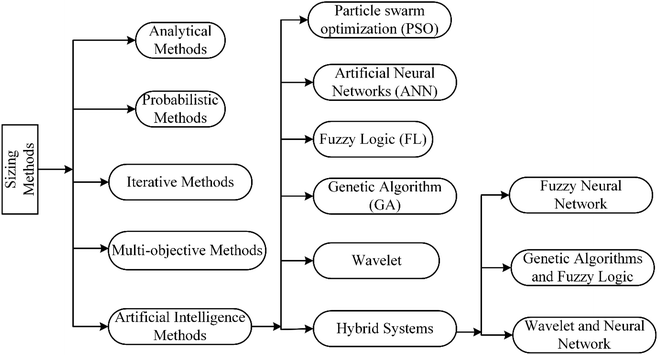 |
| Fig. 3 Existing sizing methods for hybrid energy systems. | |
Table 2 Optimization algorithms, analysis, and design constraints of sizing methods for different renewable hybrid energy systems
Approaches |
Methods |
Resource type |
Energy system |
Optimization variables |
Analysis |
Design constraints |
References |
SA for stand-alone and GC for grid-connected.
EENS for expected energy not supplied.
|
Conventional |
Probabilistic |
Wind-PV-battery |
SAa |
LPSP, SOC |
Probabilistic |
LPSP |
109
|
PV-wind-battery |
SAa |
Cost per kW h(unit cost) |
Techno-economic |
Level of autonomy |
110
|
PV-wind-diesel-battery |
SAa |
NPC |
Probabilistic |
Reliability level |
111
|
PV-wind |
SAa |
Annual total cost |
Probabilistic |
Energy index of reliability, which is directly related to EENSb and the internal rate of return |
112
|
PV-wind-battery |
SAa |
Production cost |
Probabilistic |
Expected energy supplied (EES) |
113
|
PV-wind |
SA-GCa |
Annual total cost |
Probabilistic |
Energy index of reliability (EIR), EENSb |
114
|
PV-battery |
SAa |
System cost |
Probabilistic |
LOPP |
115
|
Analytical |
PV-wind-H2 |
GCa |
NPV |
Economical |
— |
116
|
PV-wind- diesel |
SAa |
Annualized cost (AC) |
Economical |
LPSP |
117
|
PV-wind- battery-UPS |
SAa |
LCE |
Techno-economic |
LPSP |
118
|
PV-GC |
GCa |
PV electricity cost |
Techno-economic |
Fraction to load |
119
|
PV |
SAa |
Embodied energy |
Economical |
Power generation to load ratio |
120
|
PV-wind-battery |
SAa |
Capital cost |
Economical |
LPSP |
121
|
PV-wind |
SAa |
Hybrid generation cost |
Techno-economic |
Demand |
122
|
PV-wind-battery banks |
SAa |
Production cost |
Economical |
— |
123
|
Non-conventional |
Iterative |
Wind-H2-biomass |
SAa |
Capital, operations, and maintenance cost. efficiency and produced waste |
Techno-economic |
Energy stored in the H2 tanks |
124
|
PV-wind |
SAa |
Investment cost system |
Techno-economic |
Auxiliary energy unit cost and electric load |
125
|
PV-wind |
SAa |
AC |
Techno-economic |
LPSP |
126
|
PV-diesel-battery |
SAa |
COE |
Techno-economic |
SOC, generator output |
127
|
PV-diesel |
SAa |
Total net present cost |
Techno-economic |
Unmet load and battery capacity |
128
|
PV-wind |
SAa |
Total cost |
Techno-economic |
Load energy requirements |
129
|
PV-wind- hydro |
SAa |
Life cycle cost |
Techno-economic |
Resources availability and equipment |
130
|
PV-wind |
SAa |
LPSP |
Techno-economic |
LCE |
13
|
Multi-objective |
PV-wind-diesel |
SAa |
NPC, emissions |
Techno-economic and environmental |
Load profile |
131
|
PV-wind-battery |
SAa |
LCE, LPSP |
Techno-economic |
Energy storage and load profile |
132
|
PV-wind-diesel |
SAa |
LCE, Unmet load |
Techno-economic |
Specified LCE and reliability |
133
|
PV-wind-diesel-battery-FC |
SAa |
Total system cost, CO2 emissions, LOLP |
Techno-economic |
Hydrogen storage |
134
|
PV-wind-battery |
SAa |
LPSP, LCC, EE |
Techno-economic |
Number of the generator, SOC |
135
|
PV-battery |
SAa |
Voltage regulation, peak power reduction, the annual cost |
Techno-economic |
Total annual cost limit |
136
|
PV-wind-biomass-coal plant |
SA–GCa |
NPC, emission |
Techno-economic and environmental |
Biomass transport limit, generation limit, capital investment |
137
|
PV-battery-hydrogen |
SAa |
LCE, grid integration |
Techno-economic |
Energy supply rate and demand |
138
|
PV-wind-diesel-batteries-hydrogen |
SAa |
NPC |
Techno-economic |
Energy demand |
139
|
PV-battery-hydrogen |
SAa |
LCE, MDPFT |
Techno-economic |
Power consumption of the auxiliaries, aging of the components, performance degradation |
140
|
PV-battery-FC |
SAa |
Annual running cost, CO2 emissions |
Techno-economic and environmental |
Energy balance and component technical features |
141
|
Artificial intelligence |
PV-wind-diesel-biodiesel-battery |
SAa |
COE and greenhouse gas (GHG) emissions |
Economical and environmental |
Electrical load |
142
|
PV-wind-battery |
SA– GCa |
Total cost, energy index of reliability (EIR), and pollutant emissions (PEs) |
Techno-economic and environmental |
LPSP, system area |
143
|
PV-wind-diesel |
SAa |
Total net present cost and CO2 production for one year |
Techno-economic and environmental |
Unmet load and battery capacity |
131
|
PV-wind |
SAa |
Total system cost, autonomy level, and wasted energy rate |
Techno-economic |
— |
144
|
PV-wind-FC |
SAa |
Annualized cost |
Techno-economic |
Equivalent loss factor |
145
|
PV-wind-diesel-battery |
SAa,b |
LCE |
Techno-socio-economic |
Number of generators, SOC, system health state |
146
|
PV-battery |
SAa |
The capacity of the generator |
Technical |
Accumulator capacity, LOLP, and the clearness index |
147
|
PV-wind-battery |
SAa |
Total annual cost |
Technical |
Number of generators(PV panels, wind turbine, and batteries) and battery SOC |
148
|
PV-wind-battery |
SAa |
Cost efficiency |
Technical |
Energy balance |
149
|
PV-battery |
SAa |
PV area and practical accumulator capacity |
Technical |
LPSP |
150
|
PV-wind-battery |
SAa |
NPV |
Economical-ecological |
Sources capacities, SOC, and load |
151
|
PV-wind-battery |
SAa |
NPV, COE |
Techno-economic |
Number of generators, energy balance, and SOC |
152
|
PV-battery |
SAa |
PV area and functional accumulator capacity |
Technical |
LPSP |
153
|
PV-wind-battery-FC |
SAa |
LCE |
Technical |
Stochastic load and source power variations |
154
|
According to these studies, capital expenditures could be reduced by reducing the size of the components of the system. As a result of uncertainty, the system components have been oversized. Therefore, it is essential to assess the system's long-term performance to achieve the proper balance between reliability and cost. While a hybrid energy system must be able to provide a reliable supply of energy, its price remains the most significant factor to consider. A study of the relationship between the reliability and the cost of hybrid energy systems is essential to achieve the optimal solution to the problem. Furthermore, it is imperative to recognize that the size of the components of a hybrid energy system has a substantial impact on its affordability and availability. Therefore, it will be necessary to conduct a pre-feasibility analysis of the potential location to determine its feasibility. It is essential to conduct simulations to demonstrate a proposed hybrid energy system as operating, feasible, and reliable. A number of approaches to the problem are based on simulations, so it is critical to take this into consideration as we approach the problem. In addition, it is imperative to assess the cost of the proposed solutions and to analyze the potential environmental and social impacts of the proposed solutions. We need to understand the risks associated with the proposed solutions and take steps to reduce them. Finally, it is worthwhile to develop a comprehensive plan for the implementation of the suggested solutions, including an analysis of the resources and personnel needed to carry out the project.
Usually, the size of a given component depends on how it is deployed within the system under the control of a power management algorithm (PMA). This is especially true in a stand-alone system, where having an effective PMA is vital to maximizing power availability and minimizing outages. Therefore, knowledge of the intended PMA is necessary to create a detailed system model and simulate energy availability based on meteorological data106,107 and the dynamic behavior of the system components, particularly those involving hydrogen technology. In addition, an active PMA may also enhance the stability and lifetime of the system components by operating them inside their preferred operational envelopes, such as the maximum and minimum recommended state of charge (SOC) for a battery. The relatively few practical PMAs found in the literature are summarised and discussed in ref. 21,105 and 108.
4.2 Integration
At a practical level, integration requires interconnects for energy flow (electricity, hydrogen, heat) which may themselves require modeling (e.g., electrical and flow resistance), and converters which may be embedded within individual components or interposed as identified components (e.g., DC–DC converters). The connecting hardware must be sized according to the rate of energy flow through it. Monitoring and communication are necessary in the sectors of the system where energy is exchanged between components. In order for the controller to make control decisions, issue commands to the components, and receive acknowledgment and confirmation messages, the controller needs to have information on which to base control decisions. The state variables must be monitored (e.g., insolation, wind speed, temperatures at various locations, hydrogen pressure, power consumption, etc.) to know each component's current condition and the whole system. Communications between components and the controller should be standardized to a selected protocol as much as possible.
Fig. 4 illustrates the physical structure of a modular hybrid energy system with the connections necessary to integrate the components and control the system. Again, a DC-only internal electricity bus is assumed. Heat management may be necessary depending on the type of hydrogen storage adopted. For example, heat management is mandatory for metal-hydride storage owing to the enthalpy of hydrogen absorption/desorption.
 |
| Fig. 4 Example of a hybrid energy system based around a DC microbus, including heat management and monitoring. | |
In Fig. 5, the corresponding logical structure of a whole-of-system model of the system shown in Fig. 4 is sketched, along with examples of parameters measured by sensors or calculated by component models. Modules predict the behavior of the PV array and its power electronics, the wind turbine and its power electronics, and so on. They pass the required parameters to the control module. The control module uses the provided information to ascertain the system's state and deploy resources according to a PMA. This modular approach facilitates the testing of alternative components, alternative models of those components, and alternative control strategies without altering the overall model structure. In addition, specific parameters that are used within the component models, such as insolation and wind speed, are also passed to the controller model to be used in decision-making.
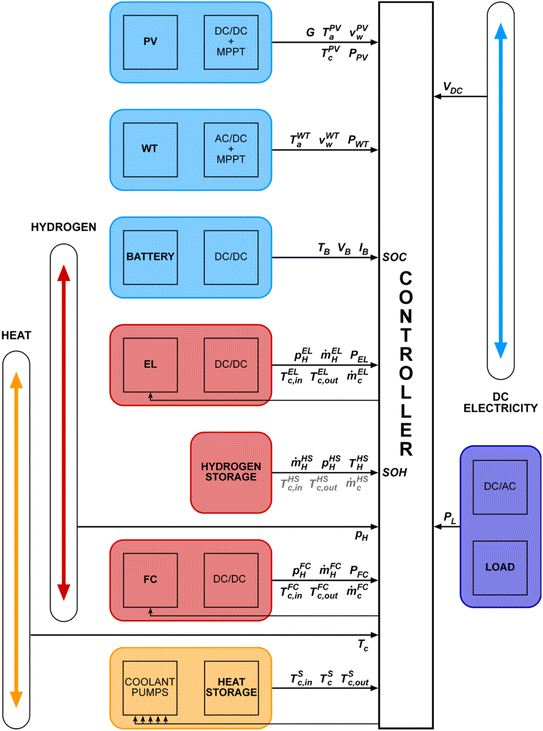 |
| Fig. 5 Skeleton of the whole-of-system model structure corresponds to Fig. 4. Parameter values are passed to the controller model, which decides how to deploy the resources according to conditions, the load, the battery state of charge (SOC), the state of hydrogen (SOH), etc. The description of these symbols can be found in the Abbreviations. | |
4.3 Opportunities and challenges
A growing number of renewable hydrogen hybrid energy systems are being installed in remote areas or places without an electrical grid. In addition, this energy system can store energy as hydrogen for extended periods of time; thus, it can be designed to emit no greenhouse gases as well as have a low maintenance cost.1,155 Since renewable energy production levels vary between seasons, it would be beneficial to use renewable hydrogen hybrid energy systems in high-latitude locations. Short-term balancing is likely to be accomplished using demand-side management technologies, such as batteries, but long-term hydrogen storage is possible.30
Fossil fuels are the primary source of power for nearly all islands and remote areas. There are, however, a number of factors that affect the long-term viability of fossil fuel-based energy systems, including high demand, global politics, as well as the rapid rise of fossil fuel prices. As a result, island communities rely primarily on diesel and petroleum products for power unless subsidized. The majority of fuel is used for transportation on islands and remote areas, while the remaining portion is utilized to generate heat and electricity.156 Therefore, energy security and reducing dependence on fossil fuels can be achieved using renewable energy resources, resulting in improved quality of life and economic growth.1
Hybrid hydrogen energy systems have been tested in both quasi-laboratories and public buildings,1,29 and the technology has also been successfully applied in remote/island settings, which means they may be feasible there as well. There are, however, several significant challenges to overcome in order to reach this goal, including:
(a) for a hydrogen hybrid energy system to be economically viable, the cost of the components must be reduced while increasing efficiency at the same time; this is generally true for hydrogen technologies as a whole. For example, significant efforts have been underway worldwide to reduce the cost of hydrogen generation. However, similar efforts also need to be made for hydrogen storage, as well as conversion technology.
(b) Due to the compromise between cost and energy availability, the renewable hydrogen hybrid energy system requires long periods of operation in harsh and varied conditions. When oversized, demand and reliability are compromised. Oversizing is a challenge. Creating a robust, flexible algorithm is one goal. This algorithm reduces energy flow through vulnerable components by maximizing energy availability and reducing energy flow fluctuations.
(c) Most hybrid system components degrade in performance over time, so it is imperative to address this issue. Further, because hydrogen energy technologies are well understood from an engineering point of view, hybrid energy systems need new and cheaper technologies (as mentioned in point (a)).
(d) More energy systems must be developed in order to demonstrate the safety and incident-free use of hydrogen. This is because hydrogen is highly combustible, and the safety risks associated with using it need to be minimized. In addition, by creating more hydrogen energy systems, we can observe and learn from any possible incidents to develop better and safer systems. This can be achieved to a certain extent,1,29 but hydrogen infrastructure in public settings is essential for future hydrogen value chains to succeed.
(e) Hybrid hydrogen energy systems, which comply with different standards and regulations, are more complex and expensive in many countries that do not have regulations regarding hydrogen energy.
5 Conclusions
Renewable hydrogen hybrid energy systems require multiple technologies to build, making them highly complex by their nature. The purpose of this study is to provide an overview of the components of hybrid energy systems. Among all available technologies, these are the most suitable and commercially accessible. Following this, we discussed methods for sizing the components of a hybrid energy system at a level of complexity that is compatible with building a whole-of-system model and simulating the entire system.
After reviewing available technologies for capturing energy, producing electricity and hydrogen, storing electricity and hydrogen, and producing electricity from hydrogen, water electrolysis is currently the only viable method of producing renewable hydrogen. In order to generate electricity, the focus has shifted to photovoltaics and wind turbines. PEM electrolyzer technology has progressed rapidly in recent years, and it is nearly universally used in today's hydrogen hybrid renewable systems as well as alkaline electrolyzers. For electricity storage, batteries and supercapacitors, as well as for hydrogen storage, compressed gas, metal hydride, and liquid molecules are the only viable hydrogen storage technologies at the present time.
Hydrogen hybrid energy systems are likely to be implemented with fuel cells since they can generate electricity from hydrogen on a scale sufficient to supply off-grid power. Furthermore, fuel-cell technology has developed rapidly, and now commercial units are available, although efficiency still needs to be improved. With advances in battery technology, hydrogen fuel cells are now cost-competitive with traditional sources of energy, making them attractive for large-scale applications. As such, fuel cells are expected to play a major role in the transition to a low-carbon economy.
Finally, approaches to sizing and managing the components of a hybrid energy system were surveyed. There has been much progress in this area in recent years, mainly through bio-inspired algorithms. However, the importance of having a practical power management algorithm, and incorporating it into the modeling at the system level, was also noted.
A mix of energy resources and energy vectors is likely to emerge in the global energy system since no single energy technology (resource or vector) has gained dominance in the energy value chain so far. This review examines hydrogen hybrid energy systems as a possible energy source for electricity supply to off-grid and remote communities. As legislation has evolved, it is increasingly expected that supply availability is equal between remote and other off-grid areas and cities. It was reiterated that hydrogen could be used to store energy for a long time to ensure a reliable electricity supply using renewable energy. When hydrogen is stored between seasons, there is little loss in energy compared to commercial batteries, which have limited energy capacity and suffer from self-discharge, so they are only suitable for short-term storage. Further research is necessary to achieve higher efficiency of the system components and reduce the system's costs, particularly in hydrogen storage and conversion.
Abbreviations
PV | Photovoltaics |
WT | Wind turbine |
SOC | State of charge |
SOH | State of hydrogen |
DoD | Depth of discharge |
SA | Stand-alone |
GC | Grid connected |
PMA | Power management algorithm |
LHV | Lower heating value |
BoP | Balance of plant |
G | Insolation |
T
PVa
| Ambient temperature at PV array |
v
PVw
| Wind speed at PV array |
T
PVc
| Average PV cell temperature |
P
PV
| Power output of PV array |
T
WTa
| Ambient temperature at WT |
v
WTw
| Wind speed at the wind turbine |
P
WT
| Power output of wind turbine |
T
B
| Battery temperature |
V
B
| Battery voltage |
I
B
| Battery charge/discharge current |
p
ELH
| Hydrogen pressure at electrolyzer (EL) |
ṁ
ELH
| Hydrogen mass flow rate from EL |
P
EL
| Power consumed by EL |
T
ELc,in
| Inlet coolant temperature to EL |
T
ELc,out
| Outlet coolant temperature from EL |
ṁ
ELc
| Coolant mass flow rate through EL |
ṁ
HSH
| Hydrogen mass flow rate to/from storage |
p
HSH
| Hydrogen pressure within storage |
T
HSH
| Hydrogen temperature within storage |
T
HSc,in
| Inlet coolant temperature to hydrogen storage |
T
HSc,out
| Outlet coolant temperature from hydrogen storage |
ṁ
HSc
| Coolant mass flow rate through hydrogen storage |
p
FCH
| Hydrogen pressure at fuel cell (FC) |
ṁ
FCH
| Hydrogen mass flow rate to FC |
P
FC
| Power supplied by FC |
T
FCc,in
| Inlet coolant temperature to FC |
T
FCc,out
| Outlet coolant temperature to FC |
ṁ
FCc
| Coolant mass flow rate through FC |
P
L
| AC power delivered to load |
V
DC
| DC electricity bus voltage |
p
H
| Hydrogen manifold pressure |
T
c
| Coolant manifold temperature |
Author contributions
Zainul Abdin: conceptualization, methodology, formal analysis, investigation, resources, visualization, writing – original draft, writing – review & editing. Nameer Al Khafaf: writing – review & editing. Brendan McGrath: writing – review & editing. Kylie Catchpole: writing – review & editing. Evan Gray: visualization, writing – review & editing.
Conflicts of interest
The authors declare that they have no known competing financial interests or personal relationships that could influence the work reported in this paper.
Acknowledgements
The authors acknowledge receiving financial support from the Victorian Higher Education State Investment Fund (VHESIF), Melbourne, Australia.
References
-
Z. Abdin, Component Models for Solar Hydrogen Hybrid Energy Systems Based on Metal Hydride Energy Storage, Griffith University, 2017 Search PubMed.
-
How Do We Know Climate Change Is Real?, accessed via https://climate.nasa.gov.
-
D. G. Smith, The Cambridge Encyclopedia of Earth Sciences, ed. D. G. Smith, Crown and Cambridge University Press, Cambridge (UK), 1981, vol. 496p. 1 Search PubMed.
- Z. Abdin and W. Mérida, Hybrid energy systems for off-grid power supply and hydrogen production based on renewable energy: A techno-economic analysis, Energy Convers. Manage., 2019, 196, 1068–1079 CrossRef.
- E. M. Gray,
et al., Hydrogen storage for off-grid power supply, Int. J. Hydrogen Energy, 2011, 36(1), 654–663 CrossRef CAS.
- S. S. Dihrab and K. Sopian, Electricity generation of hybrid PV/wind systems in Iraq, Renewable Energy, 2010, 35(6), 1303–1307 CrossRef.
- R. Dufo-López,
et al., Multi-objective optimization minimizing cost and life cycle emissions of stand-alone PV–wind–diesel systems with batteries storage, Appl. Energy, 2011, 88(11), 4033–4041 CrossRef.
- I. P. Panapakidis, D. N. Sarafianos and M. C. Alexiadis, Comparative analysis of different grid-independent hybrid power generation systems for a residential load, Renewable Sustainable Energy Rev., 2012, 16(1), 551–563 CrossRef.
- G. Giannakoudis,
et al., Optimum design and operation under uncertainty of power systems using renewable energy sources and hydrogen storage, Int. J. Hydrogen Energy, 2010, 35(3), 872–891 CrossRef CAS.
- M. H. Nehrir,
et al., An approach to evaluate the general performance of stand-alone wind/photovoltaic generating systems, IEEE Trans. Energy Convers., 2000, 15(4), 433–439 CrossRef.
- M. Santarelli, M. Cali and S. Macagno, Design and analysis of stand-alone hydrogen energy systems with different renewable sources, Int. J. Hydrogen Energy, 2004, 29(15), 1571–1586 CrossRef CAS.
- D. Nelson, M. Nehrir and C. Wang, Unit sizing and cost analysis of stand-alone hybrid wind/PV/fuel cell power generation systems, Renewable energy, 2006, 31(10), 1641–1656 CrossRef CAS.
- H. Yang, L. Lu and W. Zhou, A novel optimization sizing model for hybrid solar-wind power generation system, Sol. Energy, 2007, 81(1), 76–84 CrossRef.
- F. Vivas,
et al., A review of energy management strategies for renewable hybrid energy systems with hydrogen backup, Renewable Sustainable Energy Rev., 2018, 82, 126–155 CrossRef CAS.
- T. Khan, M. Yu and M. Waseem, Review on recent optimization strategies for hybrid renewable energy system with hydrogen technologies: State of the art, trends and future directions, Int. J. Hydrogen Energy, 2022, 47, 25155–25201 CrossRef CAS.
- E. Eriksson and E. M. Gray, Optimization and integration of hybrid renewable energy hydrogen fuel cell energy systems–A critical review, Appl. Energy, 2017, 202, 348–364 CrossRef.
- L. Olatomiwa,
et al., Energy management strategies in hybrid renewable energy systems: A review, Renewable Sustainable Energy Rev., 2016, 62, 821–835 CrossRef.
- W. Gu,
et al., Modeling, planning and optimal energy management of combined cooling, heating and power microgrid: A review, Int. J. Electr. Power Energy Syst., 2014, 54, 26–37 CrossRef.
- F. A. Khan, N. Pal and S. H. Saeed, Review of solar photovoltaic and wind hybrid energy systems for sizing strategies optimization techniques and cost analysis methodologies, Renewable Sustainable Energy Rev., 2018, 92, 937–947 CrossRef.
- T. Egeland-Eriksen, A. Hajizadeh and S. Sartori, Hydrogen-based systems for integration of renewable energy in power systems: Achievements and perspectives, Int. J. Hydrogen Energy, 2021, 46(63), 31963–31983 CrossRef CAS.
- A. Chauhan and R. P. Saini, A review on Integrated Renewable Energy System based power generation for stand-alone applications: Configurations, storage options, sizing methodologies and control, Renewable Sustainable Energy Rev., 2014, 38, 99–120 CrossRef.
- L. Meng,
et al., Microgrid supervisory controllers and energy management systems: A literature review, Renewable Sustainable Energy Rev., 2016, 60, 1263–1273 CrossRef.
- K. S. Krishna and K. S. Kumar, A review on hybrid renewable energy systems, Renewable Sustainable Energy Rev., 2015, 52, 907–916 CrossRef.
- S. Guo,
et al., A review on the utilization of hybrid renewable energy, Renewable Sustainable Energy Rev., 2018, 91, 1121–1147 CrossRef.
- V. Khare, S. Nema and P. Baredar, Solar–wind hybrid renewable energy system: A review, Renewable Sustainable Energy Rev., 2016, 58, 23–33 CrossRef.
- S. Mandelli,
et al., Off-grid systems for rural electrification in developing countries: Definitions, classification and a comprehensive literature review, Renewable Sustainable Energy Rev., 2016, 58, 1621–1646 CrossRef.
- M. S. Ismail,
et al., Effective utilization of excess energy in standalone hybrid renewable energy systems for improving comfort ability and reducing cost of energy: A review and analysis, Renewable Sustainable Energy Rev., 2015, 42, 726–734 CrossRef.
- C. Zhang,
et al., Flexible grid-based electrolysis hydrogen production for fuel cell vehicles reduces costs and greenhouse gas emissions, Appl. Energy, 2020, 278, 115651 CrossRef CAS.
- G. Gahleitner, Hydrogen from renewable electricity: An international review of power-to-gas pilot plants for stationary applications, Int. J. Hydrogen Energy, 2013, 38(5), 2039–2061 CrossRef CAS.
- Z. Abdin, K. Khalilpour and K. Catchpole, Projecting the levelized cost of large scale hydrogen storage for stationary applications, Energy Convers. Manage., 2022, 270, 116241 CrossRef CAS.
-
Z. Abdin and K. R. Khalilpour, Single and polystorage technologies for renewable-based hybrid energy systems, in Polygeneration with Polystorage for Chemical and Energy Hubs, Elsevier, 2019, pp. 77–131 Search PubMed.
-
R. Gammon, et al., HARI-hydrogen and Renewables Integration. Case Study Report, IEA Hydrogen Implementing Agreement, 2006 Search PubMed.
- K. Agbossou,
et al., Electrolytic hydrogen based renewable energy system with oxygen recovery and re-utilization, Renewable Energy, 2004, 29(8), 1305–1318 CrossRef CAS.
-
S. Voutetakis, et al., Design, Optimization and Control of Power Systems Based on Renewable Energy Sources with Hydrogen Production, Storage and Utilization, Nova Science Publishers Inc, New York, 2011 Search PubMed.
-
I. Vokony and B. Hartmann. Proposal of a novel operation and control system for a micro renewable energy farm, in 2013 4th International Youth Conference on Energy (IYCE), IEEE, 2013 Search PubMed.
- E. Cetin,
et al., Electrical analysis of a hybrid photovoltaic-hydrogen/fuel cell energy system in Denizli, Turkey, Energy Build., 2009, 41(9), 975–981 CrossRef.
- M. Brinkhaus, D. Jarosch and J. Kapischke, All year power supply with off-grid photovoltaic system and clean seasonal power storage, Sol. Energy, 2011, 85(10), 2488–2496 CrossRef.
- J. D. Holladay,
et al., An overview of hydrogen production technologies, Catal. Today, 2009, 139(4), 244–260 CrossRef CAS.
-
Photovoltaic Power Systems Programme, Snapshot, acceseed via, 2022, https://iea-pvps.org.
- N. M. Haegel,
et al., Terawatt-scale photovoltaics: Transform global energy, Science, 2019, 364(6443), 836–838 CrossRef CAS PubMed.
-
Fraunhofer Institute for Solar Energy Systems, Photovoltaics Report, 2017, accessed via https://www.ise.fraunhofer.de Search PubMed.
- M. Victoria,
et al., Solar photovoltaics is ready to power a sustainable future, Joule, 2021, 5(5), 1041–1056 CrossRef CAS.
-
SunPower® Solar Panel Again Raises the Bar in Efficiency, accessed via https://www.prnewswire.com.
-
Global Wind Report, 2021, accessed via https://gwec.net/global-wind-report-2021/.
-
N. Orlando, et al., Comparison of power converter topologies for permanent magnet small wind turbine system, in IEEE International Symposium on Industrial Electronics, ISIE 2008, IEEE, 2008 Search PubMed.
- N. A. Orlando,
et al., A survey of control issues in PMSG-based small wind-turbine systems, IEEE Trans. Ind. Inf., 2013, 9(3), 1211–1221 Search PubMed.
- R. Cardenas,
et al., Overview of control systems for the operation of DFIGs in wind energy applications, IEEE Trans. Ind. Electron., 2013, 60(7), 2776–2798 Search PubMed.
- Z. Abdin,
et al., Large-scale stationary hydrogen storage via liquid organic hydrogen carriers, Iscience, 2021, 24(9), 102966 CrossRef CAS PubMed.
- E. Bozoglan, A. Midilli and A. Hepbasli, Sustainable assessment of solar hydrogen production techniques, Energy, 2012, 46(1), 85–93 CrossRef CAS.
- C. Acar, I. Dincer and G. F. Naterer, Review of photocatalytic
water–splitting methods for sustainable hydrogen production, Int. J. Energy Res., 2016, 40(11), 1449–1473 CrossRef CAS.
-
USA, D.O.E., Report of the Hydrogen Production Expert Panel, 2013 Search PubMed.
-
GmbH, L.-B.-S., accessed via https://www.H2stations.org.
- K. Zeng and D. Zhang, Recent progress in alkaline water electrolysis for hydrogen production and applications, Prog. Energy Combust. Sci., 2010, 36(3), 307–326 CrossRef CAS.
- J. Barton and R. Gammon, The production of hydrogen fuel from renewable sources and its role in grid operations, J. Power Sources, 2010, 195(24), 8222–8235 CrossRef CAS.
- A. Ursua, L. M. Gandia and P. Sanchis, Hydrogen production from water electrolysis: current status and future trends, Proc. IEEE, 2012, 100(2), 410–426 CAS.
-
P. Millet and S. Grigoriev, Water electrolysis technologies, Renewable Hydrogen Technologies: Production, Purification, Storage, Applications and Safety, 2013, pp. 19–42 Search PubMed.
- Z. Abdin,
et al., Hydrogen as an energy vector, Renewable Sustainable Energy Rev., 2020, 120, 109620 CrossRef CAS.
- M. Carmo,
et al., A comprehensive review on PEM water electrolysis, Int. J. Hydrogen Energy, 2013, 38(12), 4901–4934 CrossRef CAS.
-
ITM Power: Energy Storage|Clean Fuel, accessed via http://www.itm-power.com.
-
A. Badgett, et al., Water Electrolyzers and Fuel Cells Supply Chain-Supply Chain Deep Dive Assessment, USDOE Office of Policy, 2022 Search PubMed.
-
M. Holst, et al., Cost Forecast for Low-Temperature Electrolysis-Technology Driven Bottom-Up Prognosis for PEM and Alkaline Water Electrolysis Systems. A Cost Analysis Study on Behalf of Clean Air Task Force. 2021 Search PubMed.
- S. Slade,
et al., Ionic conductivity of an extruded Nafion 1100 EW series of membranes, J. Electrochem. Soc., 2002, 149(12), A1556–A1564 CrossRef CAS.
- F. Barbir, PEM electrolysis for production of hydrogen from renewable energy sources, Sol. Energy, 2005, 78(5), 661–669 CrossRef CAS.
- Ø. Ulleberg, Modeling of advanced alkaline electrolyzers: a system simulation approach, Int. J. Hydrogen Energy, 2003, 28(1), 21–33 CrossRef.
- J. Sigurvinsson,
et al., Can high temperature steam electrolysis function with geothermal heat?, Int. J. Hydrogen Energy, 2007, 32(9), 1174–1182 CrossRef CAS.
- M. Ni, M. K. H. Leung and D. Y. C. Leung, Technological development of hydrogen production by solid oxide electrolyzer cell (SOEC), Int. J. Hydrogen Energy, 2008, 33(9), 2337–2354 CrossRef CAS.
- S. Y. Gómez and D. Hotza, Current developments in reversible solid oxide fuel cells, Renewable Sustainable Energy Rev., 2016, 61(Supplement C), 155–174 CrossRef.
- M. Diesendorf and B. Elliston, The feasibility of 100% renewable electricity systems: A response to critics, Renewable Sustainable Energy Rev., 2018, 93, 318–330 CrossRef.
- M. Nehrir,
et al., A review of hybrid renewable/alternative energy systems for electric power generation: Configurations, control, and applications, IEEE Trans. Sustainable Energy, 2011, 2(4), 392–403 Search PubMed.
- H. Chen,
et al., Progress in electrical energy storage system: A critical review, Prog. Nat. Sci., 2009, 19(3), 291–312 CrossRef CAS.
- W. M. Seong,
et al., Abnormal self-discharge in lithium-ion batteries, Energy Environ. Sci., 2018, 11(4), 970–978 RSC.
- J. Leadbetter and L. G. Swan, Selection of battery technology to support grid-integrated renewable electricity, J. Power Sources, 2012, 216, 376–386 CrossRef CAS.
-
D. A. Landmann, Design Guidelines for Next-Generation Sodium-Nickel-Chloride Batteries, EPFL, 2022 Search PubMed.
- J. Liu, Addressing the grand challenges in energy storage, Adv. Funct. Mater., 2013, 23(8), 924–928 CrossRef CAS.
- Y. Chang,
et al., Lead–acid battery use in the development of renewable energy systems in China, J. Power Sources, 2009, 191(1), 176–183 CrossRef CAS.
- M. Vynnycky, Analysis of a model for the operation of a vanadium redox battery, Energy, 2011, 36(4), 2242–2256 CrossRef CAS.
-
Sumitomo Electric Starts Demonstration of Storage Battery System for Power Grid in California, accessed via http://global-sei.com.
- P. Sharma and T. Bhatti, A review on electrochemical double-layer capacitors, Energy Convers. Manage., 2010, 51(12), 2901–2912 CrossRef CAS.
- C. Zhong,
et al., A review of electrolyte materials and compositions for electrochemical supercapacitors, Chem. Soc. Rev., 2015, 44(21), 7484–7539 RSC.
- A. González,
et al., Review on supercapacitors: Technologies and materials, Renewable Sustainable Energy Rev., 2016, 58(Supplement C), 1189–1206 CrossRef.
- M. Vangari, T. Pryor and L. Jiang, Supercapacitors: review of materials and fabrication methods, J. Energy Eng., 2012, 139(2), 72–79 CrossRef.
-
K. Hirose, Handbook of Hydrogen Storage: New Materials for Future Energy Storage, John Wiley & Sons, 2010 Search PubMed.
- A. Züttel, Materials for hydrogen storage, Mater. Today, 2003, 6(9), 24–33 CrossRef.
-
J. Sheffield, K. Martin, and R. Folkson, Electricity and hydrogen as energy vectors for transportation vehicles, in Alternative Fuels and Advanced Vehicle Technologies for Improved Environmental Performance, Elsevier, 2014, pp. 117–137 Search PubMed.
-
Kawasaki Hydrogen Road, accessed via http://global.kawasaki.com.
- J. Andersson and S. Grönkvist, Large-scale storage of hydrogen, Int. J. Hydrogen Energy, 2019, 44(23), 11901–11919 CrossRef CAS.
- Z. Abdin, C. J. Webb and E. M. Gray, One-dimensional metal-hydride tank model and simulation in Matlab–Simulink, Int. J. Hydrogen Energy, 2018, 43(10), 5048–5067 CrossRef CAS.
- B. Sakintuna, F. Lamari-Darkrim and M. Hirscher, Metal hydride materials for solid hydrogen storage: a review, Int. J. Hydrogen Energy, 2007, 32(9), 1121–1140 CrossRef CAS.
- C. Webb, A review of catalyst-enhanced magnesium hydride as a hydrogen storage material, J. Phys. Chem. Solids, 2015, 84, 96–106 CrossRef CAS.
- J. Ren,
et al., Current research trends and perspectives on materials-based hydrogen storage solutions: a critical review, Int. J. Hydrogen Energy, 2016 Search PubMed.
- I. Staffell,
et al., The role of hydrogen and fuel cells in the global energy system, Energy Environ. Sci., 2019, 12(2), 463–491 RSC.
- A. B. Stambouli and E. Traversa, Solid oxide fuel cells (SOFCs): a review of an environmentally clean and efficient source of energy, Renewable Sustainable Energy Rev., 2002, 6(5), 433–455 CrossRef CAS.
- O. Z. Sharaf and M. F. Orhan, An overview of fuel cell technology: Fundamentals and applications, Renewable Sustainable Energy Rev., 2014, 32, 810–853 CrossRef CAS.
-
D. Stolten, Hydrogen and Fuel Cells: Fundamentals, Technologies and Applications, John Wiley & Sons, 2010 Search PubMed.
-
R. O'hayre, et al., Fuel Cell Fundamentals, John Wiley & Sons, 2016 Search PubMed.
- G. Merle, M. Wessling and K. Nijmeijer, Anion exchange membranes for alkaline fuel cells: A review, J. Membr. Sci., 2011, 377(1), 1–35 CrossRef CAS.
- F. de Bruijn, The current status of fuel cell technology for mobile and stationary applications, Green Chem., 2005, 7(3), 132–150 RSC.
- M. Ji and Z. Wei, A review of water management in polymer electrolyte membrane fuel cells, Energies, 2009, 2(4), 1057–1106 CrossRef CAS.
- Y. Wang,
et al., A review of polymer electrolyte membrane fuel cells: Technology, applications, and needs on fundamental research, Appl. Energy, 2011, 88(4), 981–1007 CrossRef CAS.
- S. Mekhilef, R. Saidur and A. Safari, Comparative study of different fuel cell technologies, Renewable Sustainable Energy Rev., 2012, 16(1), 981–989 CrossRef CAS.
- M. A. Abdelkareem,
et al., Environmental aspects of fuel cells: A review, Sci. Total Environ., 2021, 752, 141803 CrossRef CAS PubMed.
- B. Ong, S. Kamarudin and S. Basri, Direct liquid fuel cells: A review, Int. J. Hydrogen Energy, 2017, 42(15), 10142–10157 CrossRef CAS.
- R. Luna-Rubio,
et al., Optimal sizing of renewable hybrids energy systems: A review of methodologies, Sol. Energy, 2012, 86(4), 1077–1088 CrossRef.
- M. Castañeda,
et al., Sizing optimization, dynamic modeling and energy management strategies of a stand-alone PV/hydrogen/battery-based hybrid system, Int. J. Hydrogen Energy, 2013, 38(10), 3830–3845 CrossRef.
- P. Bajpai and V. Dash, Hybrid renewable energy systems for power generation in stand-alone applications: A review, Renewable Sustainable Energy Rev., 2012, 16(5), 2926–2939 CrossRef.
-
Ø. Ulleberg, Stand-alone Power Systems for the Future: Optimal Design, Operation & Control of Solar-Hydrogen Energy Systems, NTNU, Trondheim, Norvège, 1998 Search PubMed.
- M. Kolhe,
et al., Analytical model for predicting the performance of photovoltaic array coupled with a wind turbine in a stand-alone renewable energy system based on hydrogen, Renewable Energy, 2003, 28(5), 727–742 CrossRef CAS.
- F. Zhang,
et al., Power management control for off-grid solar hydrogen production and utilisation system, Int. J. Hydrogen Energy, 2013, 38(11), 4334–4341 CrossRef CAS.
- H. Yang, L. Lu and J. Burnett, Weather data and probability analysis of hybrid photovoltaic–wind power generation systems in Hong Kong, Renewable Energy, 2003, 28(11), 1813–1824 CrossRef.
- A. N. Celik, Techno-economic analysis of autonomous PV-wind hybrid energy systems using different sizing methods, Energy Convers. Manage., 2003, 44(12), 1951–1968 CrossRef.
- J. M. Lujano-Rojas, R. Dufo-López and J. L. Bernal-Agustín, Probabilistic modelling and analysis of stand-alone hybrid power systems, Energy, 2013, 63, 19–27 CrossRef.
- G. Tina and S. Gagliano, Probabilistic analysis of weather data for a hybrid solar/wind energy system, Int. J. Energy Res., 2011, 35(3), 221–232 CrossRef.
- S. Karaki, R. Chedid and R. Ramadan, Probabilistic performance assessment of autonomous solar-wind energy conversion systems, IEEE Trans. Energy Convers., 1999, 14(3), 766–772 CrossRef.
- G. Tina, S. Gagliano and S. Raiti, Hybrid solar/wind power system probabilistic modelling for long-term performance assessment, Sol. Energy, 2006, 80(5), 578–588 CrossRef CAS.
- A. D. Bagul, Z. M. Salameh and B. Borowy, Sizing of a stand-alone hybrid wind-photovoltaic system using a three-event probability density approximation, Sol. Energy, 1996, 56(4), 323–335 CrossRef.
- R. Dufo-López, J. L. Bernal-Agustín and F. Mendoza, Design and economical analysis of hybrid PV–wind systems connected to the grid for the intermittent production of hydrogen, Energy Policy, 2009, 37(8), 3082–3095 CrossRef.
- S. Kamel and C. Dahl, The economics of hybrid power systems for sustainable desert agriculture in Egypt, Energy, 2005, 30(8), 1271–1281 CrossRef.
- S. Diaf,
et al., Design and techno-economical optimization for hybrid PV/wind system under various meteorological conditions, Appl. Energy, 2008, 85(10), 968–987 CrossRef.
- J. D. Mondol, Y. G. Yohanis and B. Norton, Optimising the economic viability of grid-connected photovoltaic systems, Appl. Energy, 2009, 86(7), 985–999 CrossRef.
- J. Kaldellis, D. Zafirakis and E. Kondili, Optimum autonomous stand-alone photovoltaic system design on the basis of energy pay-back analysis, Energy, 2009, 34(9), 1187–1198 CrossRef CAS.
- B. S. Borowy and Z. M. Salameh, Methodology for optimally sizing the combination of a battery bank and PV array in a wind/PV hybrid system, IEEE Trans. Energy Convers., 1996, 11(2), 367–375 CrossRef.
- T. Markvart, Sizing of hybrid photovoltaic-wind energy systems, Sol. Energy, 1996, 57(4), 277–281 CrossRef.
- D. K. Khatod, V. Pant and J. Sharma, Analytical approach for well-being assessment of small autonomous power systems with solar and wind energy sources, IEEE Trans. Energy Convers., 2010, 25(2), 535–545 Search PubMed.
- S. Hakimi and S. Moghaddas-Tafreshi, Optimal sizing of a stand-alone hybrid power system via particle swarm optimization for Kahnouj area in south-east of Iran, Renewable energy, 2009, 34(7), 1855–1862 CrossRef.
- B. Y. Ekren and O. Ekren, Simulation based size optimization of a PV/wind hybrid energy conversion system with battery storage under various load and auxiliary energy conditions, Appl. Energy, 2009, 86(9), 1387–1394 CrossRef.
- H. Yang, Z. Wei and L. Chengzhi, Optimal design and techno-economic analysis of a hybrid solar–wind power generation system, Appl. Energy, 2009, 86(2), 163–169 CrossRef.
- X. Zhang,
et al., Components sizing of hybrid energy systems via the optimization of power dispatch simulations, Energy, 2013, 52, 165–172 CrossRef.
- R. Dufo-Lopez and J. L. Bernal-Agustín, Design and control strategies of PV-Diesel systems using genetic algorithms, Sol. Energy, 2005, 79(1), 33–46 CrossRef CAS.
- E. Koutroulis,
et al., Methodology for optimal sizing of stand-alone photovoltaic/wind-generator systems using genetic algorithms, Sol. Energy, 2006, 80(9), 1072–1088 CrossRef.
- S. Ashok, Optimised model for community-based hybrid energy system, Renewable energy, 2007, 32(7), 1155–1164 CrossRef.
- J. L. Bernal-Agustín, R. Dufo-López and D. M. Rivas-Ascaso, Design of isolated hybrid systems minimizing costs and pollutant emissions, Renewable Energy, 2006, 31(14), 2227–2244 CrossRef.
- S. Diaf,
et al., Technical and economic assessment of hybrid photovoltaic/wind system with battery storage in Corsica island, Energy Policy, 2008, 36(2), 743–754 CrossRef.
- A. Maheri, Multi-objective design optimisation of standalone hybrid wind-PV-diesel systems under uncertainties, Renewable Energy, 2014, 66, 650–661 CrossRef.
- M. Sharafi and T. Y. ELMekkawy, Multi-objective optimal design of hybrid renewable energy systems using PSO-simulation based approach, Renewable Energy, 2014, 68, 67–79 CrossRef.
- D. Abbes, A. Martinez and G. Champenois, Life cycle cost, embodied energy and loss of power supply probability for the optimal design of hybrid power systems, Math. Comput. Simul., 2014, 98, 46–62 CrossRef.
- J. Tant,
et al., Multiobjective battery storage to improve PV integration in residential distribution grids, IEEE Trans. Sustainable Energy, 2013, 4(1), 182–191 Search PubMed.
- A. Arnette and C. W. Zobel, An optimization model for regional renewable energy development, Renewable Sustainable Energy Rev., 2012, 16(7), 4606–4615 CrossRef.
- S. Avril,
et al., Multi-objective optimization of batteries and hydrogen storage technologies for remote photovoltaic systems, Energy, 2010, 35(12), 5300–5308 CrossRef CAS.
- J. L. Bernal-Agustín and R. Dufo-López, Efficient design of hybrid renewable energy systems using evolutionary algorithms, Energy Convers. Manage., 2009, 50(3), 479–489 CrossRef.
- B. Guinot,
et al., Techno-economic study of a PV-hydrogen-battery hybrid system for off-grid power supply: Impact of performances' ageing on optimal system sizing and competitiveness, Int. J. Hydrogen Energy, 2015, 40(1), 623–632 CrossRef CAS.
- H. Ren,
et al., Optimal operation of a grid-connected hybrid PV/fuel cell/battery energy system for residential applications, Energy, 2016, 113, 702–712 CrossRef.
- Y. Katsigiannis, P. Georgilakis and E. Karapidakis, Multiobjective genetic algorithm solution to the optimum economic and environmental performance problem of small autonomous hybrid power systems with renewables, IET Renewable Power Gener., 2010, 4(5), 404–419 CrossRef.
- L. Wang and C. Singh, Multicriteria design of hybrid power generation systems based on a modified particle swarm optimization algorithm, IEEE Trans. Energy Convers., 2009, 24(1), 163–172 Search PubMed.
- J. H. Shi, X. J. Zhu and G. Y. Cao, Design and techno-economical optimization for stand-alone hybrid power systems with multi-objective evolutionary algorithms, Int. J. Energy Res., 2007, 31(3), 315–328 CrossRef.
- A. Kashefi Kaviani, G. Riahy and S. Kouhsari, Optimal design of a reliable hydrogen-based stand-alone wind/PV generating system, considering component outages, Renewable Energy, 2009, 34(11), 2380–2390 CrossRef.
- P. Paliwal, N. Patidar and R. Nema, Determination of reliability constrained optimal resource mix for an autonomous hybrid power system using Particle Swarm Optimization, Renewable Energy, 2014, 63, 194–204 CrossRef.
- L. Hontoria, J. Aguilera and P. Zufiria, A new approach for sizing stand alone photovoltaic systems based in neural networks, Sol. Energy, 2005, 78(2), 313–319 CrossRef.
- A. Askarzadeh, A discrete chaotic harmony search-based simulated annealing algorithm for optimum design of PV/wind hybrid system, Sol. Energy, 2013, 97, 93–101 CrossRef.
- A. Arabali,
et al., Genetic-algorithm-based optimization approach for energy management. Power Delivery, IEEE Trans. Sustainable Energy, 2013, 28(1), 162–170 Search PubMed.
- A. Mellit,
et al., A simplified model for generating sequences of global solar radiation data for isolated sites: Using artificial neural network and a library of Markov transition matrices approach, Sol. Energy, 2005, 79(5), 469–482 CrossRef.
- G. Merei, C. Berger and D. U. Sauer, Optimization of an off-grid hybrid PV–Wind–Diesel system with different battery technologies using genetic algorithm, Sol. Energy, 2013, 97, 460–473 CrossRef CAS.
- R. Kumar, R. Gupta and A. K. Bansal, Economic analysis and power management of a stand-alone wind/photovoltaic hybrid energy system using biogeography based optimization algorithm, Swarm Evol. Comput., 2013, 8, 33–43 CrossRef.
- A. Mellit, M. Benghanem and S. Kalogirou, Modeling and simulation of a stand-alone photovoltaic system using an adaptive artificial neural network: Proposition for a new sizing procedure, Renewable energy, 2007, 32(2), 285–313 CrossRef CAS.
- F. K. Arabul,
et al., Providing energy management of a fuel cell–battery–wind turbine–solar panel hybrid off grid smart home system, Int. J. Hydrogen Energy, 2017, 42(43), 26906–26913 CrossRef.
- B. Shabani, J. Andrews and S. Watkins, Energy and cost analysis of a solar-hydrogen combined heat and power system for remote power supply using a computer simulation, Sol. Energy, 2010, 84(1), 144–155 CrossRef CAS.
-
A. Woodruff, An Economic Assessment of Renewable Energy Options for Rural Electrification in Pacific Island Countries, SOMAC, 2007 Search PubMed.
|
This journal is © The Royal Society of Chemistry 2023 |
Click here to see how this site uses Cookies. View our privacy policy here.