DOI:
10.1039/D3CS00898C
(Review Article)
Chem. Soc. Rev., 2024,
53, 5552-5592
Recycling of spent lithium-ion batteries for a sustainable future: recent advancements†
Received
16th October 2023
First published on 22nd April 2024
Abstract
Lithium-ion batteries (LIBs) are widely used as power storage systems in electronic devices and electric vehicles (EVs). Recycling of spent LIBs is of utmost importance from various perspectives including recovery of valuable metals (mostly Co and Li) and mitigation of environmental pollution. Recycling methods such as direct recycling, pyrometallurgy, hydrometallurgy, bio-hydrometallurgy (bioleaching) and electrometallurgy are generally used to resynthesise LIBs. These methods have their own benefits and drawbacks. This manuscript provides a critical review of recent advances in the recycling of spent LIBs, including the development of recycling processes, identification of the products obtained from recycling, and the effects of recycling methods on environmental burdens. Insights into chemical reactions, thermodynamics, kinetics, and the influence of operating parameters of each recycling technology are provided. The sustainability of recycling technologies (e.g., life cycle assessment and life cycle cost analysis) is critically evaluated. Finally, the existing challenges and future prospects are presented for further development of sustainable, highly efficient, and environmentally benign recycling of spent LIBs to contribute to the circular economy.
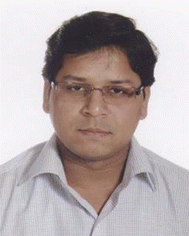
Basanta Kumar Biswal
| Dr Biswal is presently working as a Senior Research Fellow at the National University of Singapore (NUS). He obtained his PhD from McGill University, Canada in 2014. Post-PhD, he carried out his independent research at Nanyang Technological University (Singapore), Hong Kong University of Science and Technology, Korea Advanced Institute of Science and Technology, and now at NUS. He has published 43 papers in top scientific journals and 3 book chapters in reputed publishers. Dr Biswal is an Environmental Biotechnologist with expertise in topics related to antimicrobial resistance genes, biological nitrogen removal, nature-based solutions, environmental sustainability, and spent Lithium-ion battery recycling. |
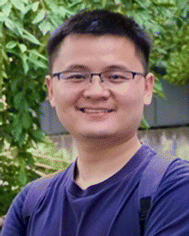
Bei Zhang
| Dr Bei Zhang received his PhD degree in Environmental Engineering from Shandong University, China, in 2019 with the guidance of Prof. Yujiang Li. He then joined Prof. Rajasekhar Balasubramanian's group as a Research Fellow at the National University of Singapore, Singapore. In 2021, he began his research at the Tokyo Institute of Technology (Japan) as a JSPS Postdoctoral Fellow in the group led by Prof. Manabu Fujii. His major research interests include thermal transformation of biomass to high-value-added materials and their environmental applications, including adsorption and advanced oxidation processes for the removal of emerging contaminants. |
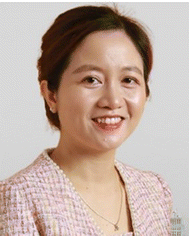
Phuong Thi Minh Tran
| Dr Phuong Tran is currently working as a Research Fellow in the Department of Civil and Environmental Engineering at the National University of Singapore (NUS). She completed her PhD under the supervision of Prof. Rajasekhar Balasubramanian from NUS in 2022. Her research interest mainly focuses on assessing indoor and outdoor air quality, investigating sustainable urban development and life cycle assessment (LCA), and conducting environmental and health risk assessments. |
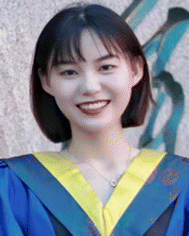
Jingjing Zhang
| Jingjing Zhang obtained her Master of Science degree in 2020 from Hunan University, China. Currently, she is pursuing her doctoral studies under the mentorship of Professor Rajasekhar Balasubramanian at the National University of Singapore (NUS). Presently, Jingjing focuses on two crucial areas. The first is centered around advancing the recycling processes for lithium-ion batteries, contributing to the sustainable management of this critical energy storage technology. Her second research domain involves the synthesis, design, and practical applications of nanostructured semiconductors, primarily for photocatalytic environmental purification. Jingjing's work aims to addressing pressing environmental challenges through cutting-edge nanomaterials and sustainable energy technologies. |
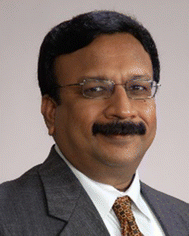
Rajasekhar Balasubramanian
| Rajasekhar Balasubramanian is Keppel Professor in Sustainability Solutions (Endowed Professorship) at NUS. He received his PhD in Atmospheric Chemistry from the University of Miami, USA, in 1991. His main research interests include air quality, climate change, and environmental sustainability. He has authored more than 250 refereed articles, which are highly cited. In recognition of his outstanding contributions in Environmental Science & Engineering, he has been honored with numerous awards including the Alan Berman Research Publication Award from the US Department of Navy (2014), Sustainable Technology Award (2015), etc. He is an elected Fellow of the Royal Society of Chemistry (2021). |
1. Introduction
In recent years, increasing attention has been paid worldwide to the development of green, sustainable and renewable energy sources to replace fossil fuels and to mitigate climate change.1,2 According to the international energy agency (IEA) report, the annual clean energy investment increased by nearly 24% from 2021 to 2023.3 Lithium-ion batteries (LIBs) are becoming a vital energy storage tool to facilitate the shift to a more renewable, sustainable, and low-carbon future. LIBs are now being upgraded with more attractive characteristics such as higher energy densities, better safety features, lower cost and longer cycle life to meet the growing energy demand.1,4,5 Compared to other conventional batteries (e.g., nickel–iron and nickel–metal hydride, and lead acid-based batteries), LIBs are highly preferred due to their low reduction potential, easy storage and fast Li ion mobility in most solid materials.4 Additionally, LIBs offer the highest volumetric energy densities (320–450 W h L−1), power output (more than 300 W kg−1) and cycling stability (nearly 2000 cycles) relative to other types of metal ion-based batteries.4,6
LIBs were initially commercially developed for use in portable consumer electronic devices. However, in recent years, they have been widely used in several other applications including electric vehicles (EVs). Among the different types of EVs, BEVs (battery EVs) dominate in the market and account for about two-thirds of new electric car registrations.7 The global LIB production capacity in 2022 was 1.57 TW h, but it is projected to increase by nearly four-fold (6.79 TW h) by 20308 (Fig. S1a, ESI†). According to a recent report on the global EV production, EV production significantly increased from 0.01 million in 2010 to 11.26 million in 20209 (Fig. S1b, ESI†). Additionally, it is anticipated that the EV production will reach 21.5 million by 2030.10 A recent report indicated that the global demand for LIBs used in EVs would increase from 110 GW h in 2020 to 6530 GW h in 2050.11 Among various countries, China (5.37 million in 2020) was the top producer of EVs followed by Europe (3.32 million in 2020) and United States (1.79 million in 2020).9 According to the IEA report, between 2013 and 2020, the global LIB market size increased from US$15.1 billion to US$40.8 billion (i.e., nearly three times increase) (Fig. S1c, ESI†), whereas the LIB production rose from 52.2 GW h to 239.9 GW h (i.e. nearly five times increase)12 (Fig. S1d, ESI†). With the rising trend of energy demand, it is estimated that between 2020 and 2030, the LIBs' global market will concurrently increase from 259 to 2500 GW h with an average growth of 25.4% per year.1
Based on the size and shape, LIBs are commonly available in four different geometries namely cylindrical, prismatic, coin and pouch cells.13 The main components of a LIB cell include an anode (negative electrode), a cathode (positive electrode), a separator, an electrolyte, casing materials, etc.10,14,15 Among the various types of LIBs developed so far using different types of cathode materials, lithium cobalt oxide (LiCoO2)-based LIBs are considered to have the most promising performance due to their superior properties such as high energy density, high voltage, mature technology, and long life span (Fig. S2, ESI†).4,16 The average life span of the LIBs is between 1 and 3 years. Thus, after the usage phase, a large number of obsolete LIBs would enter the solid waste stream.17,18 It has been predicted that up to 4 million metric tons of EV-based spent LIBs could be generated within the next 20 years.10 The overwhelming generation of end-of-life batteries brings several environmental and economic challenges. Thus, proper management of spent LIBs is needed. However, unfortunately, there is no consensus yet as to how to manage spent LIBs.19 The management options of spent LIBs include their reuse, recycling, landfilling, incineration and chemical or biological processing.20,21 At present, recycling (i.e., converting waste into wealth) is considered as the important method for the management of a huge quantity of spent LIBs.22 The recycling of LIBs reinstates the end-of-life valuable materials back into the economic cycle, avoids landfill-related environmental consequences, and promotes the circular economy.23
The recycling of spent LIBs is needed to address environmental and global sustainability challenges24 which are summarized as follows: (1) recovery of high value resources from spent LIBs, (2) reduction of environmental pollution due to the toxic components of spent LIBs, (3) achievement of sustainable mineral mining for LIB production, (4) uneven global resource distribution and production, and (5) escalation of critical materials' costs.1,25 More detailed information about the five challenges is provided in the ESI.† Due to the complex nature of spent LIBs, the use of appropriate pre-treatment technologies is necessary to enable effective downstream recycling of spent batteries. The advantages and disadvantages of different types of pre-treatment technologies are presented in Table S1 (ESI†). The key methods involved in the pre-treatment of spent LIBs include sorting, discharge/deactivation, disassembly, crushing and separation (Fig. S3, ESI†).26
To assess the present state-of-knowledge on the recycling of spent LIBs, a thorough literature search was done in the scientific database (Scopus) using different combinations of keywords in the Scopus search engine together with “spent lithium-ion batteries” namely “direct recycling”, “pyrometallurgy”, “hydrometallurgy”, “biohydrometallurgy or bioleaching”, and “electrometallurgy” (Fig. 1a). This publication profile indicates that increasing interest has emerged among scientific communities in studying various aspects of the hydrometallurgical method-based technology for recycling of spent LIBs. Additionally, the publication trend of direct recycling and electrometallurgical methods suggests that these two methods also receive competitive attention worldwide. To better understand the significance of the most recent innovations in the recycling of spent LIBs, the scientific publication trend over the last 10 years (2013–2022) was critically analyzed (Fig. 1b). It shows that there was a constant increase in the number of scientific publications specifically, between 2018 and 2022.
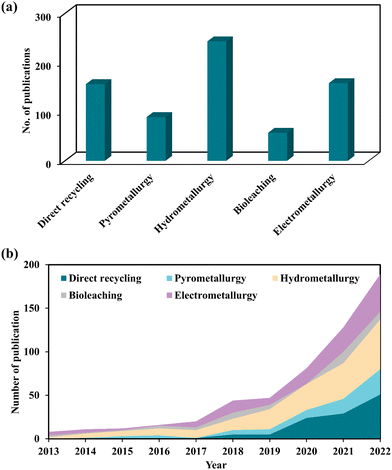 |
| Fig. 1 Total number of scientific publications resulted by searching in the Scopus database using appropriate keywords for different LIB recycling technologies (a) and the publication trend in each recycling technology in the last 10 years (2013–2022) (b). | |
The top four countries with a maximum number of scientific publications related to the recycling of spent LIBs include China, United States, India, and South Korea. This analysis suggests that these countries may be the major producers of LIBs, or end-users of LIB-based electrical and electronic products. Notably, research publications are distributed in diverse multidisciplinary subject areas including Environmental Science, Engineering, Energy, Materials Science and Chemistry. This observation suggests that interdisciplinary knowledge is needed to address the complex characteristics of spent LIBs. A stringent screening process was adopted to select the most recent and relevant articles which meet the overall objectives and scope of this review. Most of the articles included in this review are mainly peer-reviewed papers (research articles, reviews, book chapters, etc.) published in the past ten years (2013–2022). The quality of papers was checked by multiple ways including the reputation of journals, the specific contents, the number of citations received, etc. The quantitative information which is required for this review was collected by reading the abstract and/or by referring to particular sections of papers. Finally, a comprehensive analysis and comparative evaluation of the current knowledge on various LIB recycling technologies were conducted to identify key knowledge gaps and propose future research directions to develop sustainable, eco-friendly and high efficiency recycling technologies.
We further critically analyzed recent literature on the scope and objectives of previously published reviews on the recycling of spent LIBs. Our analysis reveals that most of the past reviews were mainly focused on specific LIB recycling technologies, for example, direct recycling,27,28 classical metallurgy-based methods namely pyrometallurgy29,30 and hydrometallurgy,31–34 biohydrometallurgy35–38 or a combination of pyrometallurgy, hydrometallurgy, direct recycling and/or biohydrometallurgy.39–44 To our knowledge, no critical review has been published yet on a comprehensive analysis and comparative evaluation of various aspects of major technologies used in recent years for the recycling of spent LIBs.
Additionally, to the best of our knowledge, the significance of electrometallurgy was not sufficiently discussed in previous reviews. Limited information is only available on the prospects and challenges associated with the recycling of spent LIBs having LiCoO2 as the cathode material. Specifically, the potential physicochemical methods needed for the regeneration of cathode materials from spent LIBs were not reviewed in a comprehensive manner previously. The kinetics and thermodynamics associated with specific hydrometallurgy and biohydrometallurgy processes which influence the process efficiency were not sufficiently addressed in the past reviews. A comparative evaluation of the sustainability of various recycling technologies based on the life cycle assessment (LCA) and techno-economic analysis (TEA) is found to be lacking in the past reviews. The overarching objective of this comprehensive review article is to critically analyze the recent advancements (2013–2022) in five major technologies used for the recycling of LIBs: direct recycling, pyrometallurgy, hydrometallurgy, biohydrometallurgy and electrometallurgy. This review is organized into 8 sections. Section 1 provides a broad overview of LIBs, the major challenges involved in the recycling of spent LIBs and the scope of the current review papers compared to the previous ones published in the literature. Sections 2–6 deal with the fundamental concepts of major recycling technologies namely direct recycling, pyrometallurgical, hydrometallurgical, bio-hydrometallurgical, and electrometallurgical methods with sufficient depth and breadth. Section 7 focuses on the evaluation of sustainability aspects of each technology with respect to various criteria including the environmental impact assessment (EIA), technological maturity level (TRL), economic feasibility, energy consumption, etc. Additionally, a comparative evaluation of the potential advantages and disadvantages of different recycling methods is done from the perspectives of their economic feasibility, efficiency and environmental friendliness. To make further advances in specific research areas, this review highlights major knowledge gaps and points out our own perspectives in the individual sections. Finally, Section 8 summarizes major conclusions and future research directions. The overall scope and main objectives of this comprehensive review are shown in Fig. 2. We believe that this compressive review would help to develop sustainable, environmentally friendly and highly efficient recycling technologies for optimal recovery of valuable resources (e.g., Co and Li) from spent LIBs and contribute to the circular economy.
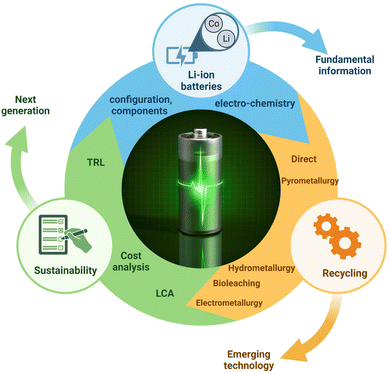 |
| Fig. 2 The overall scope and main objectives of this comprehensive review. | |
2. Direct recycling of spent LIBs
Direct recycling is one of the most promising methods for the conversion of spent LIBs into resources. This technology has received increasing attention in recent years due to its potential economic and environmental benefits.45 However, the technology has been limited to mainly the laboratory-scale, due to the lack of robustness, for example, the requirement of tedious pre-treatments which involve the use of toxic organic solvents.46 Neumann et al.47 stated that the principal idea behind the direct recycling strategy is to reactivate the active electrode materials in spent LIBs in order to reinstate the capacity and property losses over recycling, instead of initially breaking them down into their different parts and then resynthesizing them. The direct recycling of spent LIBs involves the following important steps namely discharging and dismantling, recovery of electrolytes, separation of electrode materials or metal foils, and regeneration of electrode materials (Fig. 3).48 The primary step of the direct recycling method is “discharging” which aims to eliminate any residual power in spent LIBs, followed by “dismantling” to open the LIB cell and separate different components. The second step is the “recovery of electrolytes” from spent LIBs (electrolyte extraction). The third step is the “separation of foils from electrodes”, for example, separation of copper foils from anodes and aluminium foils from cathodes (electrode/metal separation). The fourth step is the “separation of cathodes and anodes” from the separator (cathode/anode separation). The recovered electrodes can then be regenerated for the remanufacturing of batteries. An effective disassembly of LIBs offers an optimum recycling rate by the direct recycling method. In the direct recycling technology, harvesting and recovery of active components of spent LIBs after stabilization can be achieved without alternation of the original structure and chemical composition of batteries. In this strategy, the battery materials are separated using physical and magnetic separation techniques with nominal heating to evade chemical degradation of the active components like electrode materials.49 The active components recovered by disassembly can be purified (e.g., removal of deposited salts). The surface and bulk faults can then be corrected by the relithiation process or hydrothermal methods.49 The key indication of the decrease of power capacity of the battery/decay of battery performance by aging causes the loss of lithium from the layered oxide in the cathodes as well as irreversible structural transition.28,47 For regeneration of electrode materials, the purified cathode materials can be exposed to high lithium moieties.
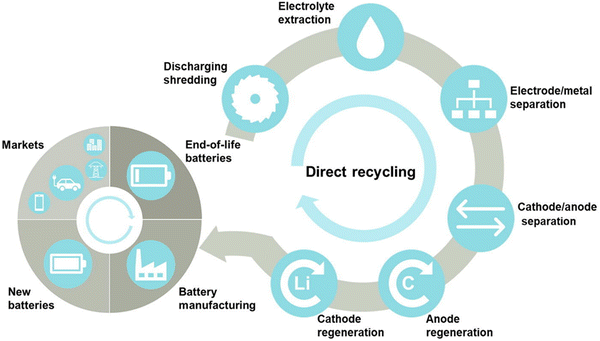 |
| Fig. 3 Key steps involved in the recycling of spent LIBs using direct recycling process. Reproduced (adapted and modified) with permission from ref. 48; Copyright 2020, Elsevier. | |
2.1 Regeneration of cathode materials
Continuous charging and discharging cycles could cause the decrease of the performance of LIBs due to changes of the chemical characteristics of electrode materials (e.g., loss of Li). The direct regeneration is an efficient approach for the restoration of the structure and composition of degraded cathodes to their original state.50 In the degraded LCO-based LIBs, in addition to Li deficiencies in the bulk crystal structure, the original layered structure is also deformed and transformed into different structures (e.g., spinal phases).51 Thus, in the regeneration process, it is essential to refill the Li shortages in the LCO crystal and carry out the transformation of the spinel phase to the original layered-based structure of cathode materials. The relithiation of degraded cathodes can be done in a solid medium or an aqueous solution with a short annealing step with an excess of Li2CO3 (nearly 5 wt%). The relithiation reactions are presented below (eqn (1) and (2)).51 |
Li1−xCoO2 + xLi+ + xe− → LiCoO2 | (1) |
|
4Co3O4 + 6Li2CO3 + O2 → 12LiCoO2 + 6CO2 | (2) |
The main regeneration methods applied to cathode materials include solid-state reactions, hydrothermal treatment, co-precipitation, the sol–gel method and carbon-thermal reduction.52,53 In the solid state regeneration method, the pre-treated precursors (cathodes) are mixed with the solid lithium sources (e.g., Li2CO3 or LiOH) at an ideal molar ratio. Then, the mixture is thermally treated/annealed in the temperature range of 800–950 °C to rectify the structural and compositional defects of the cathode.51 Zhou et al.54 used the high-temperature (1000 °C for 10 hours) solid-phase method for Li ion refilling and co-doping of Mg/Ti at the Co site for direct regeneration of the spent LCO material. The regenerated cathode material shows high-voltage performance due to improvement of structural stability, impeding of phase transformation, and increase of Li ion diffusion capability. The solid-state synthesis approach is a simple reaeration process and requires fewer steps.53 However, this process requires high energy consumption and it is difficult to remove impurities. In the hydrothermal-based regeneration method, the recycled cathodes are mixed with the solution containing Li, and then placed in a hydrothermal reactor which operates at a low temperature (120–220 °C) to synthesize new cathodes.53 Liu et al.55 employed a microwave-based hydrothermal method for regeneration of spent LCO cathode materials at 200 °C (time: 30–120 min) using 4 M lithium hydroxide solution. The regenerated cathode materials display high-capacity and high-rate properties (141.7 mA h g−1 at 5C) with a cycle retention rate of 94.5% after 100 cycles. The advantages of the hydrothermal process are that it is a low energy requirement process and the reaction time is short.53 Nevertheless, the use of specific equipment (e.g., a hydrothermal reactor) is needed to carry out the hydrothermal regeneration.
Co-precipitation is a viable method to produce homogeneous electrode materials.53 It is a multistep process that includes leaching of cathode materials using acid solution, removal of impurities from the leachate by a selective precipitation or solvent extraction method, and addition of a precipitant to the acid leaching solution to produce precursors via co-precipitation reactions. The produced precursor is then mixed with Li sources to synthesize the cathode materials. A recent study applied the co-precipitation method for regeneration of spent NCM batteries by using multiple reagents.56 Initially, spent batteries are dissolved in an equimolar (1 M) solution of H2SO4 and H2O2. Subsequently, in a tank reactor, the reclaimed leachate is mixed with Na2CO3 (2 M) and NH4OH (0.5 M) to regenerate the precursor (Ni0.5Co0.2Mn0.3CO3). The precursor is added to Li2CO3 and calcinated at different temperatures. The regenerated material demonstrates good performance. The co-precipitation method results in a high purity product and a high recovery rate. However, it is a complex process and not cost effective.53
Unlike co-precipitation, the sol–gel method used for regeneration of cathodes also involves various steps including initial leaching of the recovered cathodes using organic/inorganic acids, addition of complexing agents to induce polymerization and hydrolytic reactions to form sol, then formation of a gel with a spatial structure and finally regeneration of products by the sintering process.53 A study by Lee and Rhee57 used the sol–gel method for regeneration of LCO from spent LIBs. They used reductive leaching agents (e.g., HNO3 plus H2O2) to leach out cathode active materials (LCO). A gelatinous precursor material was then prepared by using citric acid. The precursor product was calcined at 950 °C for 24 hours to obtain high purity crystalline LCO powder. The regenerated LCO shows high cycling performance and charge–discharge capacity. The sol–gel method produces high purity products, but it is a complex process which requires high energy consumption and economically not feasible.53
The carbon-thermal reduction method is mainly applied to the regeneration of LFP cathode materials.53 In this process, the cathode material is initially leached by using acid reagents, and then thermally treated to synthesize the precursor material. The precursor product was mixed with Li and carbon sources in a specific ratio. The cathode was regenerated via a carbon-thermal reduction reaction in an inert environment (e.g., Ar or N2 environment). Yang et al.58 used the carbon-thermal reduction method for regeneration of the active cathode material from the spent LFP batteries. The discharge capacities of the re-synthesized LFP cathode materials varied from 144.2–110.5 mA h g−1 at rates of 0.1–5.0C, and meet the requirements of middle-end LFP batteries. The carbon-thermal reduction method is a simple regeneration process, but the process is energy intensive, and it is difficult to remove impurities.53 The advantages and disadvantages of different regeneration methods are presented in Table 1. Overall, the use of one type of direct regeneration method may not be fully suitable to recover and regenerate different active cathode materials, i.e., selection of a direct regeneration process may depend on the chemistry of the cathode materials.
Table 1 Comparison of advantages and disadvantages of different regeneration methods in the direct recycling of spent batteries. Reproduced with permission from ref. 53; Copyright 2020, Elsevier
Regeneration method |
Advantages |
Disadvantages |
Solid-state reaction |
Simple production process, fewer steps |
Difficult to remove impurities, uneven mixing of raw materials, high energy consumption |
Hydrothermal |
Lower energy consumption, shorter reaction time |
Strict requirements for equipment |
Sol–gel |
Make full use of the metal ions, high product purity |
Complex operation process, high energy consumption, high cost |
Co-precipitation |
High product purity, high metal recovery rate |
Complex procedure, high cost |
Carbon-thermal reduction |
Simple production process |
Difficult to remove impurities, high energy consumption |
2.2 Regeneration of anode materials
In LIBs, graphite is usually used as an anode material due to its outstanding electrochemical performance.28,51 However, with the continuous charging/discharging processes, the destruction and exfoliation of graphite occur by the repeated de-intercalation of Li ions which leads to the change of volume of graphite anode materials. Additionally, the cumulative stress progressively causes the graphite particles to disintegrate, crack and fragment into smaller particles. Prior to the repair of spent graphite anode materials, it is required to remove impurities namely polymeric binders, conductive agents and other metal sediments which can be removed through acid treatment, chemical treatment, water treatment and/or heat treatment. In recent years, synthetic graphite is explored for the production of LIBs due to its consistency in performance, high level of purity and constant supply, but it looks expensive (US$14 per kg or even higher).51 Thus, the regeneration of anode materials could contribute to sustainable development and circularity in battery technology.
Numerous methods including chemical and thermal treatment-based methods are used for the regeneration of anode materials from spent LIBs. The electrochemical properties of the recycled graphite can be improved by coating treatment or high temperature graphitization.59 Markey et al.60 used boric acid (5 wt%) pre-treatment and short annealing (750–1050 °C for 1 hour) to restore the compositional and structural defects of the degraded graphite. Moreover, the functional boron-doping on the surface of graphite particles provided high cycling stability and electrochemical performance. In a recent work, Xiao et al. explored the regeneration of spent graphite at elevated temperature with coating of the outer surface of graphite using asphalt.61 The surface modification by asphalt coating decreased the aggregation of graphite particles and improved the surface morphology to be smoother. The regenerated graphite anode materials demonstrated impressive electrochemical performance. In total, the degraded graphite can be regenerated by thermo-chemical processes. Compared to cathode regeneration, limited work has been performed on the regeneration of anode materials from spent LIBs.
2.3 Perspectives
The direct recycling of spent LIBs is an emerging technology which revives the spent electrode materials (cathodes and anodes) through non-destructive approaches. This technology has received increasing attention recently since it is an energy efficient process with lower environmentally negative effects (e.g., reduced CO2 footprint), requires a fewer recycling steps, and leads to higher economic benefits compared to the conventional recycling methods such as hydrometallurgical and pyrometallurgical processes.51,53 The direct recycling method is still at the early stage of the development with numerous technological and fundamental issues including effective separation of different components, removal of binders and recovery of electrolytes. More fundamental work is needed to understand safety issues associated with the direct recycling method as well as the purity level of products obtained from different regeneration steps which would help to scale-up the recycling process to industrial applications. Although numerous studies have been conducted on the regeneration of cathode materials from spent LIBs using direct recycling, limited information is currently available about the direct recycling of anode (graphite) materials. Since it is very hard to completely remove impurities (e.g., metallic salts or binder materials) deposited onto the surface of electrode materials, more comparative studies are needed to evaluate the changes of the electrochemical performance of the electrodes with and without impurities. The purity level of the electrode materials may change with the application of single vs. multiple regeneration methods which is worthy of investigation in future studies.
3. Recycling of spent LIBs by the pyrometallurgical process
As one of the most widely used extractive metallurgical techniques, pyrometallurgy has been extensively developed for the recovery of valuable metals from minerals and the recycling of spent LIBs.62 While employing the traditional pyrometallurgical process (e.g., direct roasting) for the recycling of spent LIBs, various components (i.e., cathodes, anodes, binders, separators and electrolytes) of LIBs are transformed into cobalt-containing alloys, slag, and gases at the operational temperature higher than 1000 °C.63 The cobalt-containing alloy is usually collected as a valuable product with disposal of the slag and gases as wastes.64 Zhou et al. proposed evolution pathways toward a closed-loop pyrometallurgical recycling of spent LIBs by direct roasting (Pyro 1.0), atmosphere-assisted roasting (Pyro 2.0), additive-assisted roasting (Pyro 3.0), and high-value utilization (Pyro 4.0), as shown in Fig. S4 (ESI†).62 Based on these evolution pathways, various emerging pyrometallurgical processes are discussed in this section including their chemical transformation, thermodynamics, kinetics, and optimization of pyrometallurgical parameters.
3.1 Chemical transformation during pyrometallurgical processes
In pyrometallurgical processes, various chemical reactions occur with the transformation of different components of spent LIBs into cobalt-containing alloys, slag, and gases (Fig. 4).62 Accordingly, this section analyzes the chemical transformations of different components of spent LIBs under different pyrometallurgical conditions.
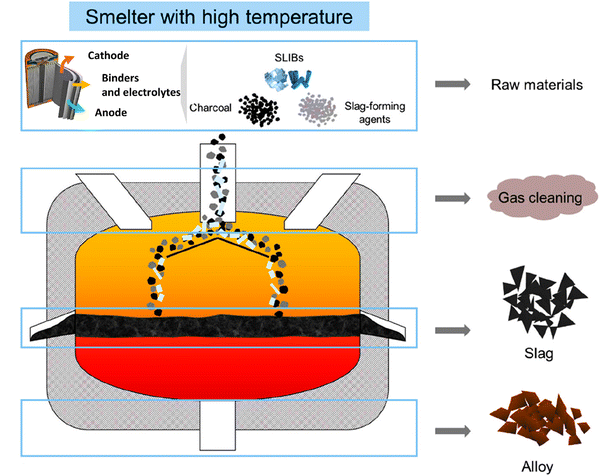 |
| Fig. 4 Typical pyrometallurgical processes of spent LIBs. Reproduced with permission from ref. 62; Copyright 2021, American Chemical Society. | |
3.1.1 Cathodes.
The direct roasting (Pyro 1.0) of spent LIBs is usually conducted to recycle cathode active materials (e.g., LiCoO2), in which carbothermic reduction and thermite reduction are the main chemical transformations during typical pyrometallurgical processes.62 To optimize the reduction and extend the recycling, atmosphere-assisted roasting (Pyro 2.0) and additive-assisted roasting (Pyro 3.0) are developed based on the extensive chemical transformations (e.g., sulfation, chlorination and nitration).62 To achieve high-value utilization (Pyro 4.0), the regeneration of the original phase of spent LIBs serves as the key chemical transformation for cathode recycling.62
(1) Carbothermic reduction.
Carbothermic reduction has been widely used to recycle cathode active materials by using reductive carbon such as the anode graphite65–67 and additives68,69 under various pyrometallurgical conditions (Fig. 5). The overall carbothermic reduction reaction (eqn (3)) involved in the traditional pyrometallurgical process occurs recovering Li2CO3 and Co.66 Specifically, the decomposition of LiCoO2, oxidation of carbon, formation of Li2CO3, and reduction of CoO (eqn (4)–(9)) occur during the different stages of the traditional pyrometallurgical processes (Fig. 5). The coupling reactions were found to decrease the decomposition temperature of LiCoO2 from 1153 °C to 900 °C.66 Li et al. clarified the reaction mechanism (Fig. 5) by increasing the temperature from 500 °C to 1000 °C.67 Notably, the decomposition of Li2CO3 (eqn (7)) occurs with an increase in temperature to 1000 °C.67 To optimize the pyrometallurgical conditions and upgrade the products, a carbothermal shock method was developed by Zhu et al. with uniform temperature distribution, high heating and cooling rates (104–105 °C s−1), high temperatures (up to ≈2200 °C), and ultrafast reaction times (≈20 s).70 As a result of the high-temperature decomposition (eqn (7)), Li2O evaporated from the inside of the calcined products and then recrystallized on the surface due to the ultrafast cooling rate and short reaction duration.70
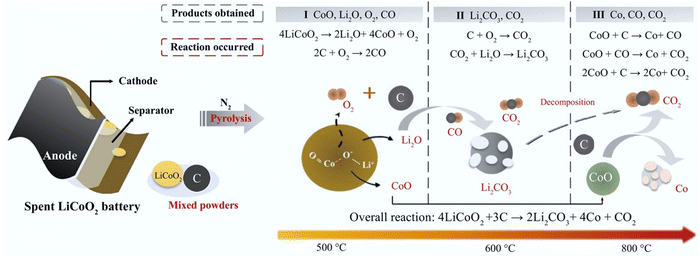 |
| Fig. 5 Schematic illustration of carbothermic reduction during pyrometallurgical processes. Reproduced with permission from ref. 71; Copyright 2020, Elsevier. | |
Overall reaction of carbothermic reduction:
|
4LiCoO2 + 3C → 2Li2CO3 + 4Co + CO2 | (3) |
Step 1. Decomposition of LiCoO2 and oxidation of carbon: |
4LiCoO2 → 2Li2O + O2 + 4CoO | (4) |
Step 2. Formation and decomposition of Li2CO3:Step 3. Reduction of CoO:Step 4. Pyrolysis gas reduction of LiCoO2 and CoO: |
Organic carbon → H2 + CO + CH4 + C2H6 | (10) |
|
2LiCoO2 + CO → Li2O + 2CoO + CO2 | (11) |
|
2LiCoO2 + H2 → Li2O + 2CoO + H2O | (12) |
|
8LiCoO2 + CH4 → 4Li2O + 8CoO + 2H2O + CO2 | (13) |
|
14LiCoO2 + C2H6 → 7Li2O + 14CoO + 3H2O + 2CO2 | (14) |
|
4CoO + CH4 → 4Co + CO2 + 2H2O | (16) |
|
7CoO + C2H6 → 7Co + 2CO2 + 3H2O | (17) |
Additionally, additive-assisted reduction reactions can be proposed to explain the formation of targeted products under optimized conditions. The pyrolysis gases (eqn (10)) produced from the organic carbon (e.g., biomass, separators, and other additives) serve as reductants for recycling the cathode materials (eqn (11)–(17)).68,69 The sustainability, economics, and efficiency for recycling cathodes are significantly improved by using pyrolysis gas, which highlights the reutilization of pyrolysis gases as a closed-loop recycling.68,69
(2) Thermite reduction.
Thermite reduction has been applied for the recovery of Li and Co from spent LIBs.72,73 The Al foil from the current collector was directly used as the reductant for thermite reduction (eqn (18)–(22)). By coupling with hydrometallurgical leaching, various products could be further collected, which will be discussed in Section 4. |
18LiCoO2 + 2Al → 9Li2O + 6Co3O4 + Al2O3 | (18) |
|
6LiCoO2 + 2Al → 3Li2O + 6CoO + Al2O3 | (19) |
|
Li2O + Al2O3 → 2LiAlO2 | (20) |
|
3Co3O4 + 2Al → 3CoO + Al2O3 | (21) |
|
3CoO + 2Al → 3Co + Al2O3 | (22) |
(3) Additive-assisted transformation.
Various additives such as inorganic acids extend the chemical transformation (e.g., sulfation, chlorination and nitration reactions) of the cathode during pyrometallurgical processes. The sulfation agents including sulfuric acid and sulfates74,75 have been used in the sulfation reaction (eqn (23)–(26)). However, the emission of SOx is not considered to be environmentally friendly during the traditional sulfation process.74,75 Consequently, a sustainable sulfation process was developed considering the principles of green chemistry with a low environmental impact and enhanced atomic efficiency of sulfur.75 The formation of sulfates (eqn (26)), instead of the SOx emission, has been controlled thoroughly.75
Sulfation reaction:
|
4LiCoO2 + 6H2SO4 + 22H2O → 2Li2SO4 + 4(CoSO47H2O) + O2 | (23) |
|
2CoSO4 + 4LiCoO2 → 2Li2SO4 + 6CoO + O2 | (24) |
|
12LiCoO2 + 6H2SO4 → 6Li2SO4 + 4Co3O4 + 6H2O + O2 | (26) |
Chlorination reaction: |
Li2O + CaCl2 → 2LiCl + CaO | (27) |
|
2Li2O + 2Cl2 → 4LiCl + O2 | (28) |
|
Li2O + 2HCl → 2LiCl + H2O | (29) |
|
6LiCoO2 + 18NH4Cl → 6CoCl2 + 6LiCl + 12H2O + N2 + 16NH3 | (30) |
|
6LiCoO2 + 2NH3 → 6CoO + 3Li2O + 3H2O + N2 | (31) |
|
CoO + HCl → CoCl2 + H2O | (32) |
|
Li2O + 2HCl → 2LiCl + H2O | (33) |
Nitration reaction: |
LiCoO2 + 4HNO3 → LiNO3 + Co(NO3)2 + NO + O2 + H2O | (34) |
The chlorination reaction initiated by the addition of CaCl2 contributes to the formation of LiCl (eqn (27)–(29)).72,76 It was found that the volatilization of LiCl was controlled by the interfacial chemical reaction, in which Li2CO3 could be subsequently collected by a precipitation process.72 Additionally, NH4Cl was used as a reductant and as a chlorination agent for the recycling of Li and Co (eqn (30)–(33)).77–79 Based on the optimization of temperature, pressure and contact area between NH4Cl and LiCoO2, nearly 100% extraction efficiency of Li and Co could be achieved, showing great potential for a scale-up chlorination process.77–79 However, the gas emissions (e.g., SOx, Cl2, and NOx) during the sulfation, chlorination and nitration (eqn (34)) processes pose safety and health risks to the instrument and environment, respectively.62,80
(4) Regeneration of cathodes.
Regeneration of cathode materials aims to not only extract Co and Li from spent LIBs, but also regenerate high value-added products.62 Zhou et al. summarized two techniques including the solid-state reaction and spray pyrolysis, in which the spent LIBs are used as precursors to synthesize targeted products.62 Notably, the structure distortion in the spent LIBs will be regained as active phases.62 However, the efficient classification and purification of spent LIBs are important to ensure the quality of the regenerated cathode.62 Most recently, Yin et al. developed an efficient, one-step, non-destructive method for the regeneration of cathodes81 (Fig. 6). The rapid Joule heating played a key role in the re-lithiation of the spent LIBs by repairing the crystal structure.81
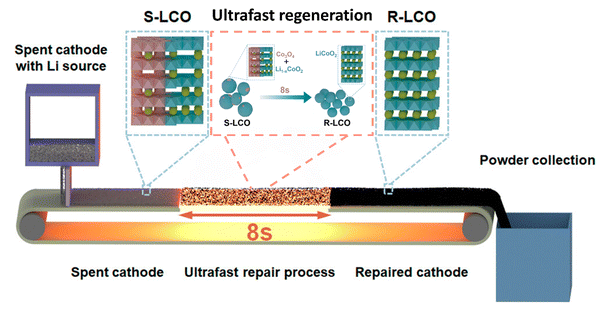 |
| Fig. 6 Rapid Joule heating process for non-destructive reconstruction of cathodes. Reproduced with permission from ref. 81; Copyright 2023, American Chemical Society. | |
3.1.2 Anodes.
Due to the large amount (12–21 wt%) and cost (10–15%) of graphite anodes in LIBs, the recycling of graphite anodes has received increasing attention.62 During the carbothermic reduction (Section (1) in 3.1.1), graphite anodes in the mixture of spent LIBs have been utilized as reductants to facilitate the recycling of cathodes. By introducing the elaborate classification and separation, the regeneration and functionalization of anodes (Fig. 7) significantly increase the recycling efficiency to produce high value-added products.82,83
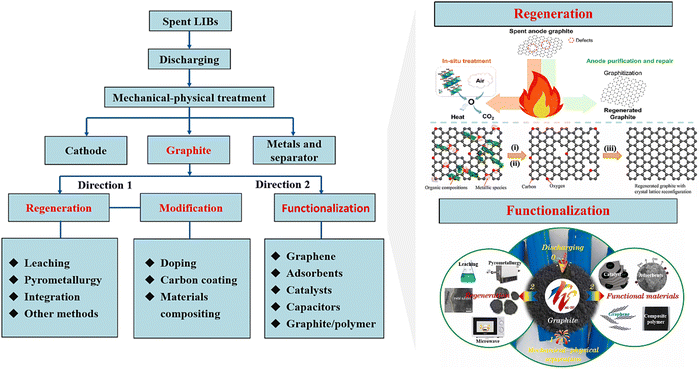 |
| Fig. 7 Schematic illustration of regeneration of functionalization of anodes. Reproduced with permission from ref. 29, 84 and 85; Copyright 2021, American Chemical Society; Copyright 2022, Elsevier; Copyright 2021, Elsevier. | |
(1) Regeneration of anodes.
The regeneration of spent graphite anodes has been developed to remove the impurities and restore the graphite crystal lattice.82 The high temperature maintained during the pyrometallurgical processes contributes to the dissociation, decomposition and separation of impurities and subsequent graphitization of spent graphite.86 It was found that the maintenance of 3000 °C during pyrometallurgy for 6 hours under a nitrogen atmosphere facilitated the graphitization effect with superior electrochemical properties.86 However, ultra-high temperature of regeneration leads to a high energy consumption. Yi et al. developed a green and facile approach for regeneration of graphite anodes at 1400 °C for 4 hours under a nitrogen atmosphere.87 Notably, the enlarged interlayer spacing of regenerated graphite was found to be used as a promising positive electrode material.88
(2) Functionalization.
The spent graphite anodes could be treated as promising carbon precursors for further functionalization including modification (e.g., doping) and composition (e.g., composite electrode).82 The defect region in the spent graphite anode provides active sites for chemical doping and other functionalization.82 Specifically, Xu et al. mixed the spent graphite anode with urea during pyrometallurgical processes.89 NH3 produced from the decomposition of urea promoted the exfoliation of graphite.89 Additionally, g-C3N4 (polymeric carbon nitride) generated from thermal transformation of urea served as an efficient nitrogen source to obtain abundant nitrogen-doping sites.89 Eventually, the nitrogen-doping product showed excellent rate performance, high capacity and fast charging performance as a regenerated anode.89 Since graphite has been widely used as a carbon source for the synthesis of carbon nanomaterials, extensive exploration has been carried out to synthesize carbon nanomaterials (e.g., graphene, carbon nanotubes, and other composites) from spent graphite.82,83 The concept of “trash to treasure” elevates the applicability of spent graphite anodes, and has been well discussed in related review papers.82,83 However, an in-depth life cycle assessment of graphite used in LIB production, needs to be conducted at various stages including production and recycling of LIBs to propose a sustainable recycling strategy to fulfil the demand of graphite in future.
3.1.3 Binders, separators, and electrolytes.
To achieve a full component recycling of spent LIBs, the transformation of binders, separators, and electrolytes has been investigated for potential recycling and upgrading. Poly(vinylidene fluoride) (PVDF) and polytetrafluoroethylene (PTFE) are commonly used as binders, whereas polyethylene (PE) and polypropylene (PPE) are used as the separators in LIBs. Moreover, the electrolyte consists of a solvent and Li-containing solute. Non-destructive recycling (Fig. 8) of binders, separators, and electrolytes has been developed including low-temperature volatilization and molten salt recovery, in which binders, separators, and electrolytes can be separated, extracted, purified and collected for recycling. In this section, we focus on the chemical transformation of binders, separators, and electrolytes by destructive treatments (Fig. 8) during pyrometallurgical processes.
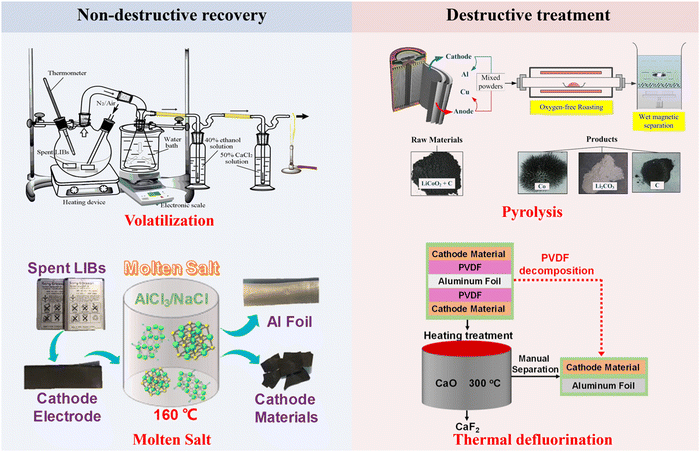 |
| Fig. 8 Schematic illustration of non-destructive and destructive treatment of binders, separators and electrolytes. Reproduced with permission from ref. 29 Copyright 2021, American Chemical Society. | |
Thermal degradation of PVDF at 500–600 °C produces F-containing gases (e.g., HF), which cause air pollution and instrumental corrosion.62,90 Accordingly, thermal defluorination techniques have been developed by adding defluorinated agents (e.g., CaO and Li salts).91,92 Specifically, CaO serves as a heat storage medium, a defluorination agent and a fluorine adsorbent during the thermal decomposition of PVDF.91 In view of the unit structure (–CH2–CF2–) of PVDF, the strong electron-withdrawing effect of the F atom in the CF2 unit makes the adjacent H in the CH2 unit active as an acidic site.91 Accordingly, the abundant basic sites of CaO can promote the elimination reaction with acidic sites of PVDF.91 The elimination reaction between CaO and PVDF induces the initial decomposition of PVDF at low temperatures (around 300 °C).91 Additionally, HF can be immediately captured by CaO to produce CaF2, avoiding the release of F-containing gases.91 By comparing five lithium salts, Ji et al. demonstrated that the LiOAc–LiNO3 (LAN) system can avoid particle morphological changes and HF release.92 The developed LAN system facilitated the decomposition of PVDF by heat transferring and removing H+ from HF when reacting with unsaturated hydrocarbons.92
The thermal decomposition of PTFE usually produces tetrafluoroethylene (TFE), RCF radicals, which promote secondary reactions to generate other fluorocarbons (e.g., carbonyl fluoride).93 During the pyrometallurgical process, C2F4, CF4, COF2, HF, hydrocarbons, and benzene have been detected as the decomposition products of PTFE along with other components from spent LIBs.62 Notably, the usage of inorganic (e.g., LiPF6 as an electrolyte) and organic (e.g., PVDF and PTFE) fluorinated substances has raised the concerns as potential sources of per- and polyfluoroalkyl substances (PFAS).94 Ultra-high temperature pyrometallurgical processes are suggested to achieve complete mineralization of PFAS.94 However, the thermal transformation of PFAS is still obscure in view of the complex types and transformation pathways.95
As discussed in Section (1) in 3.1.1 (eqn (10)), organic carbon derived from separators (i.e., PE and PPE) tends to be decomposed during pyrometallurgical processes.68 The gases produced in eqn (10) can be applied as reductants to facilitate the carbothermic reduction for the cathode recycling process.68 The thermal decomposition of PE96,97 and PPE98,99 usually generates unsaturated and saturated hydrocarbons as gaseous, liquid and solid products by free radical reactions. The main products include methane, propylene, propane, 2-methylpentane, 2,4-dimethylpentane, and 2,4-dimethylheptane.98,99 Notably, the decomposition products have been investigated as potential sources of microplastics, which need to be extensively studied in future.97
The thermal stability and transformation of electrolytes have been investigated under pyrometallurgical processes.100 Various organic solvents including dimethyl carbonate (DMC), ethyl methyl carbonate (EMC), diethyl carbonate (DEC), ethylene carbonate (EC), and propylene carbonate (PC) with LiPF6 show different thermal properties.100 It was found that DEC-LiPF6 possessed the lowest thermal stability due to the abundant –CH3CH2 groups in the DEC molecule.100 The initial decomposition of PF6− promoted the decomposition of the C–O bond in organic molecules.100 The development of characterization and recycling methods is necessary to promote the full recovery of chemical components in spent LIBs.62
3.2 Thermodynamic, kinetic and pyrometallurgical parameters
3.2.1 Thermodynamics and kinetics.
During the pyrometallurgical process, the analysis of thermodynamics contributes to the fundamental understanding of the overall properties, behavior, and equilibrium composition based on chemical transformations of the cathodes (Section 3.1). The exploration of thermodynamics and reaction mechanisms makes it possible to clarify the pyrometallurgical mechanisms during the high temperature and complex interactions. In this section, four representative chemical transformations of the cathodes are compared based on their thermodynamics.
As shown in Fig. 9,66 the coupling reactions reduced the reaction temperature according to the calculated standard molar enthalpy and entropy (discussed in Section (1) in 3.1.1). Specifically, when mixing LiCoO2 and C for the coupling reactions, the reduction of LiCoO2 and CoO could be promoted at lower temperature than that of separated reactions. The subsequent carbon thermal experiments conducted verified that the coupling reactions decreased the decomposition temperature of LiCoO2 from 1153 °C to 900 °C.66 In addition to the carbon source from graphite, the coupling reaction among pyrolysis gases and Al foil and LiCoO2 has been investigated for synergistic reduction of the cathode during pyrometallurgical processes (Fig. 10).101 Specifically, pyrolysis gases including hydrogen, methane and propylene reduced the reaction temperature with cathodes below 500 °C.101 Due to the contact of Al foil with cathodes, the coupling reaction occurred at the contact area, promoting the thermite reduction.101
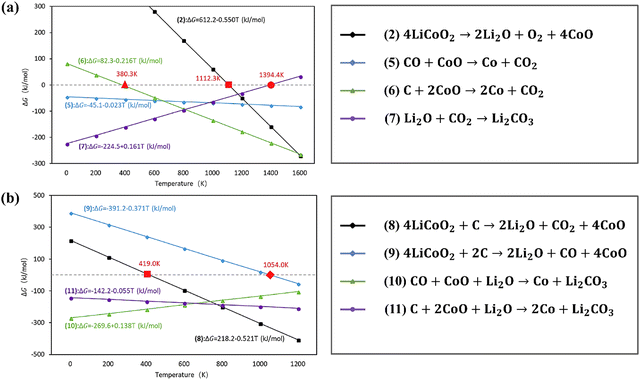 |
| Fig. 9 Thermodynamics analysis of coupling reactions for recycling of cathodes by carbothermic reduction. Reproduced with permission from ref. 102; Copyright 2018, Elsevier. | |
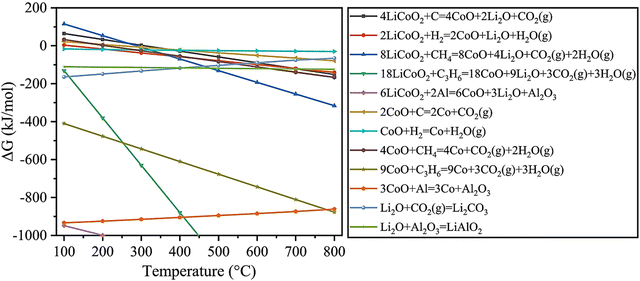 |
| Fig. 10 Thermodynamics analysis for recycling of cathodes with addition of Al foil and pyrolysis gases. Reproduced with permission from ref. 103; Copyright 2022, Elsevier. | |
Apart from the thermodynamics of carbothermic and thermite reduction reactions, Qu et al. analyzed the chlorination reaction by adding CaCl2 during pyrometallurgical processes.76 Although a high temperature above 940 °C is necessary for the reaction between Li2O and CaCl2, the decomposition products (e.g., Cl2 and HCl) can react with Li2O at lower temperatures, i.e., 520 °C and 480 °C, respectively.76 To predict and analyze the reaction between NH4Cl and cathodes (Fig. 11), the Gibbs free energies of the proposed reactions were calculated using HSC Chemistry 9.0 (Outotec, Finland).78 Accordingly, it was found that oxygen is helpful to facilitate the reaction between NH4Cl and cathodes due to the spontaneous oxidation of NH4Cl by oxygen.78 However, the practical reaction characterization is still necessary to validate the prediction by thermodynamics analysis.78
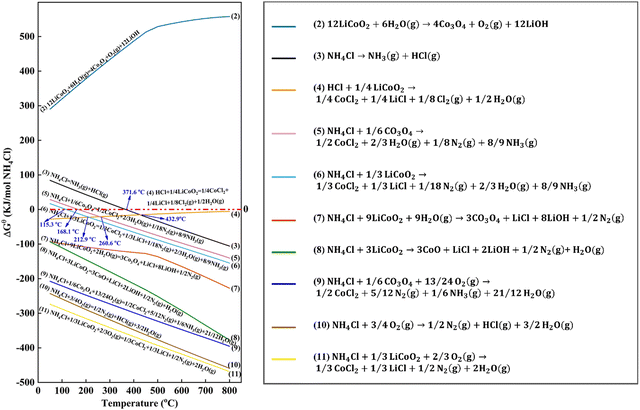 |
| Fig. 11 Thermodynamics analysis for recycling of cathodes with addition of NH4Cl. Reproduced with permission from ref. 104; Copyright 2020, American Chemical Society. | |
While thermodynamics predicts what can occur during pyrometallurgical processes, kinetics provides an indication of the occurrence of reactions on an atomic or a molecular level. The complex chemical transformation occurs during pyrometallurgical processes, and it is not possible to use simple reactions to describe the whole transformation. Therefore, kinetic analysis is needed as it contributes to a comprehensive understanding of pyrometallurgical processes.67 Li et al. firstly introduced two iso-conversion methods (i.e., the Kissinger–Akahira–Sunose model and the Flynn–Wall–Ozawa model) to investigate the kinetics during pyrometallurgical processes.67 Herein, the effects of the heating rate, activation energy, and conversion rate were included in the developed methods. However, further modification is necessary to provide insights into complex transformation products and pyrometallurgical conditions. Notably, the reaction interface is important for the promotion of kinetics, such as the gas–solid reaction.72
3.2.2 Pyrometallurgical parameters.
To promote favorable thermodynamics and kinetics during pyrometallurgical processes, the effects of various operating parameters (e.g., temperature, reaction time, atmosphere and additives) are discussed for the optimization of reaction conditions and targeted products.
High temperature is a significantly important and representative factor for pyrometallurgical processes in comparison to other recycling processes. As discussed in Section 3.2.1, various temperature regions give different thermodynamic properties with reactions. However, the balance between productivity and energy consumption during high-temperature pyrometallurgy needs to be optimized by precisely investigating the effect of temperature.30 Moreover, the increase in temperature during pyrometallurgical processes shows improvement in the recycling efficiency in typical pyrometallurgical techniques including roasting, calcination, pyrolysis, incineration, smelting and Joule heating for the recycling of electrolytes, binders, separators, cathodes and anodes.30 Based on the investigation of the effect of temperature on pyromettalurgy,30,76 two emerging directions have been proposed for the temperature optimization. Firstly, the optimization of additives to reduce the required temperature for pyrometallurgical recycling.68,69,79,101,105 The intermediates (e.g., pyrolysis gases) produced at low temperatures have been confirmed to reduce the reaction temperature for the reduction of cathodes.68,69,79,101,105 Secondly, the emerging thermal techniques including Joule heating make it possible to achieve the transformation of cathodes at ultrahigh temperatures within ultrafast reaction time.70 Additionally, the reaction time (or holding time) serves as an accompanying factor with temperature to ensure a sufficient chemical transformation of cathodes during pyrometallurgical processes.69
Atmosphere-assisted roasting (Pyro 2.0 in Fig. S4, ESI†) emphasizes the effect of the atmosphere on pyrometallurgical processes.62 Various atmospheric conditions have been investigated including air, N2, Ar, CO2 and vacuum.62 Additionally, pyrolysis gases and additives can also provide the atmosphere for sulfation, chlorination and nitration reactions in Section (3) in 3.1.1. The selection and regulation of the atmosphere under which reactions are carried out are in line with the pyrometallurgical stages for recycling different components such as cathodes, anodes, binders, separators and electrolytes.62 To promote the carbothermic reduction, the reaction atmosphere must not have oxygen to prevent the combustion of carbon.66 In contrast, air conditions are necessary if the pyrometallurgical processes aim to completely remove the organic substances for recycling metal components.62 Moreover, the vacuum atmosphere has been utilized to investigate the intermediates during pyrometallurgical processes for the clarification of transformation pathways.
Additive-assisted roasting (Pyro 3.0) and high-value utilization (Pyro 4.0) highlight the effect of additives for the production of high value-added products from spent LIBs. By adding the additives such as chlorides, sulfates, or nitrates, the sulfation, chlorination and nitration reactions could be constructed for efficient recycling of cathodes (Section (3) in 3.1.1).62 Notably, the ratios of “salt to cathode”,74,77,92 “acid to scrap”,80 and “liquid to solid”80 play a key role in the recycling efficiency during pyrometallurgical processes.
3.3 Perspectives
The key knowledge gaps and new research directions to develop sustainable, eco-friendly and high efficiency pyrometallurgy-based recycling technologies are discussed in the following paragraphs.
(1) Full recycling of each component of spent LIBs: the recycling of cathodes has been well investigated in recent years especially in terms of industrial practice. However, the additive-assisted chemical transformation of the cathodes needs to be verified in large-scale applications. Although research efforts are increasing to recycle other components of LIBs such as anodes, binders, separators and electrolytes, the full recycling of each component of spent LIBs is still far-fetched. The introduction of pretreatment in conjunction with pyrometallurgical processes is important to achieve an efficient recycling process. In addition to the regeneration of each component, modification and functionalization of the precursors and products during the recycling of spent LIBs show great potential for recycling and upgrading the spent LIBs. Specifically, a continuous pyrometallurgical process involving sequential recycling of each component at programmed temperature is vital to maximize the recycling technology with efficient energy inputs.
(2) Elimination of thermal degradation intermediates: in addition to obtaining the targeted products (e.g., valuable metals and graphite), byproducts are produced as thermal degradation intermediates during pyrometallurgical processes. Although the emission of pyrolysis gases (e.g., SOx, Cl2, and NOx) has received increasing attention, emerging pollutants have been identified among thermal degradation intermediates during pyrometallurgical processes. Currently, not all thermal degradation intermediates are well monitored, regulated and eliminated during pyrometallurgical processes. Notably, some intermediates have been identified as a source of PFAS94 and microplastics.97 The development of fluorine-free alternatives of binders will contribute to the elimination of fluorine contamination. The exhaust gas pollution has limited the application of pyrometallurgical processes considering their environmental and safety aspects.
(3) Coupling analysis of chemical reactions, thermodynamics and kinetics: the complexity of thermal reactions poses challenges in terms of tracing chemical transformations of all components of LIBs during pyrometallurgical processes. Moreover, the need to maintain high temperature and “various atmospheres” limits the real-time characterization of reaction products. Although thermodynamics makes it possible to predict the possible occurrence of reactions under complex conditions, the detection of all products is necessary to get the targeted products with a high yield. Notably, the kinetics-based advanced modeling is still a necessity by introducing the developed kinetics (rates of chemical transformations as a function of temperature) from pyrolysis experiments. Additionally, the modification of developed kinetics should be addressed with the detection of reaction products. Thus, the coupling of chemical transformations, related thermodynamics and kinetics is necessary to provide a comprehensive assessment for the optimization of pyrometallurgical processes. However, massive efforts are needed in this task. Most recently, the development of data science facilitates the handling of complex parameters. Thus, the application of machine learning tools shows great potential for the prediction of reaction pathways and optimization of operating parameters during pyrometallurgical processes.
4. Recycling of spent LIBs by the hydrometallurgical process
As one of the extractive metallurgical techniques, hydrometallurgy has been widely used to recycle valuable components of LIBs using various aqueous solutions (e.g., acid). In comparison to pyrometallurgical processes, hydrometallurgical processes have been well-developed and are more mature for the recycling of spent LIBs.63 The integration of leaching and purification processes during the hydrometallurgical process provides various practical advantages including high recycling efficiency, high selectivity, low energy consumption, and less gas emissions as compared to pyrometallurgical processes.106 Nevertheless, the utilization of strong acids and the disposal of liquid wastes pose a significant challenge from the sustainability viewpoint, encouraging the development of sustainable hydrometallurgical processes from Hydro 1.0 to Hydro 4.0 as shown in Fig. S5 (ESI†).
4.1 Chemical transformation during hydrometallurgical processes
Chemical transformation (e.g., leaching) of various components (e.g., cathodes, anodes, electrolytes, binders, shell and separators) during different hydrometallurgical processes (e.g., leaching and extraction) under various conditions (e.g., inorganic acid and alkaline leaching, organic acid leaching, alkaline leaching, and intensified leaching) is discussed in this section. Based on the schematic diagram in Fig. S5 (ESI†), the recycling of cathodes is analyzed with the proposed evolution pathway from Hydro 1.0 to Hydro 4.0 in view of recent advancements made in this area of research. Nevertheless, the limited research on the recycling of anodes, binders, separators and electrolytes impedes the development of sustainable utilization.
4.1.1 Cathodes.
(1) Inorganic acid and alkaline leaching and extraction (Hyro 1.0).
Leaching is a key step to dissolve metals and minerals in aqueous media during hydrometallurgical processes.106 In terms of the recycling of cathodes, the crystal lattice of cathode materials from spent LIBs is broken down in various leaching media.106 Inorganic acids (e.g., HCl, H2SO4, and HNO3 in eqn (35)–(37)) have been used for the leaching of cathodes since hydrogen ions can extract lithium from spent cathodes (hydro 1.0 in Fig. S5, ESI†).107 In comparison to H2SO4 and HNO3, the presence of chloride ions in HCl facilitates the dissolution of cathode components by destabilizing the formation of a surface layer.108 Notably, the addition of H2O2 as a reductant has been investigated to find out if it enhances the leaching process (eqn (38)).109 Specifically, the study confirmed that the presence of H2O2 as an additive promotes the reduction of Co3+ to Co2+, in which Co2+ possesses a higher solubility than Co3+ under the same leaching conditions.109 Accordingly, the closed-loop recycling was developed by optimizing the operation conditions using the combination of HCl and H2SO4 + H2O2 as leachants.110,111 The subsequent precipitation achieves a high efficiency for the cathode recycling.110–112 To improve the extraction efficiency and selectivity, a rotating reactor (Fig. 12) was designed to promote the interaction between the feed/extractant and the extractant/acceptor interfaces multiple times.113 Accordingly, a low extractant concentration was achieved to ensure an efficient extraction and high selectivity.113 |
2LiCoO2 + 8HCl → 2CoCl2 + Cl2 + 2LiCl + 4H2O | (35) |
|
4LiCoO2 + 6H2SO4 → 4CoSO4 + O2 + 2Li2SO4 + 6H2O | (36) |
|
4LiCoO2 + 12HNO3 → 4Co(NO3)2 + O2 + 4LiNO3 + 6H2O | (37) |
|
2LiCoO2 + 3H2SO4 + H2O2 → 2CoSO4 + O2 + Li2SO4 + 4H2O | (38) |
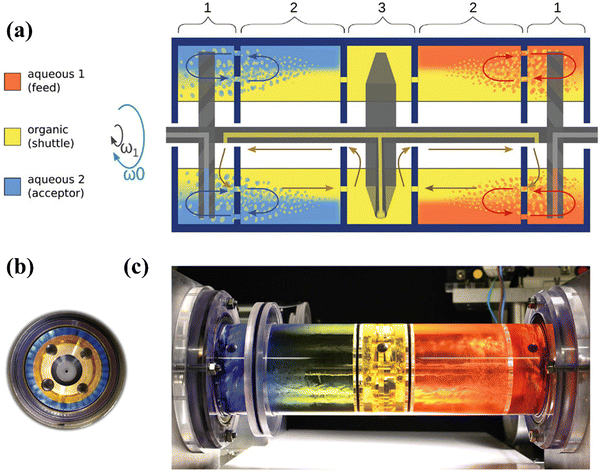 |
| Fig. 12 The rotating reactor designed to promote the interaction between feed/extractant and the extractant/acceptor interfaces multiple times. Reproduced with permission from ref. 113; Copyright 2023, Wiley. | |
The leached cathode components could be recovered through selective precipitation as metal hydroxides using NaOH.107 A complete precipitation can be achieved under alkaline conditions.107 The addition of ammonia can also promote the leaching of cathodic components by reacting with Co2+.107
(2) Leaching and extraction by organic acids and solvents (Hyro 2.0).
The use of organic acids (i.e., citric acid, aspartic acid, malic acid, oxalic acid, ascorbic acid, and glycine) as leachants provides an alternative approach to solve the problems involved in the inorganic acid-based leaching.109 Meanwhile, oxalic acid has been utilized as a reductant and leachant (eqn (39)) to improve the leaching efficiency.109 Additionally, the co-leaching with H2O2 has also been investigated to leach all the metals from cathodes.114 Apart from H2O2, glucose was selected as the reductant to facilitate the leaching efficiency with the addition of citric acid.115 Lei et al. integrated inorganic and organic acids to achieve an ultra-fast leaching of metals (within 10 min) and reduce the cost of the hydrometallurgy process by optimizing the operation conditions.116 According to quantum chemistry and thermodynamics, the synergy-coordination mechanism of both Cl− and dehydroascorbic acid contributes to the fast leaching of Li.116 |
2LiCoO2 + 4H2C2O4 → 2CoC2O4 + 2CO2 + Li2C2O4 + 4H2O | (39) |
In addition to the organic acids, deep eutectic solvents (DESs) have been employed as novel green solvents to replace inorganic acids for hydrometallurgical leaching.117 In comparison to conventional ionic liquids (ILs), DESs lead to simple synthesis, maintain high thermal stability, and promote a significant depression of the freezing point.117 Notably, the hydrogen bonding between donors and acceptors gives the DESs unique properties of low viscosity, high metal solubility as well as biodegradation compared to the inorganic and organic acids used for the leaching process.117 Luo et al. synthesized DESs from betaine hydrochloride and ethylene glycol and subsequently achieved the selective leaching and separation of Co, Mn and Ni from the cathode materials.118 Based on the DESs made from oxalic acid and choline chloride, a double closed-loop process was constructed to achieve the recycling of spent LIBs and DESs.119 Specifically, DESs can be filtered and recycled by evaporating water for reuse.119 Nevertheless, high consumption of acids, reductants and other solvents is usually involved in the hydrometallurgical leaching.
(3) Integrated leaching and extraction (Hyro 3.0).
The integration of hydrometallurgy with other technologies (e.g., hydrothermal treatment, microwave assistance, and membrane filtration) significantly extends the application of recycling processes, providing a flexible approach to solve the rigid problems and tackle the challenges of isolated hydrometallurgical processes.
The conventional hydrometallurgical process emphasizes the utilization of aqueous solutions with various solvents for the leaching of cathodic components. The physicochemical properties of water, the main solvent in the conventional hydrometallurgy, remain generally constant although the temperature involved in the hydrometallurgical process is usually higher than room temperature. In contrast, the physicochemical properties of water under hydrothermal conditions with high temperatures and pressure contribute to the hydrometallurgical leaching (Fig. 13).120,121 Under the hydrothermal conditions (200 °C for 6 hours), the chemical structure and electrochemical performance of spent LIBs can be restored with addition of the reductant.120 The promotion of ion transportation under hydrothermal conditions facilitates the regeneration of the crystal structure of LIBs.120 Under the subcritical conditions (350 °C for 30 min), a co-treatment process of recycling Co and Li and simultaneous detoxification of PVC were achieved.122 Nevertheless, the scale-up application of subcritical and critical water requires a practical and continuous assessment for the recycling and production technologies.121
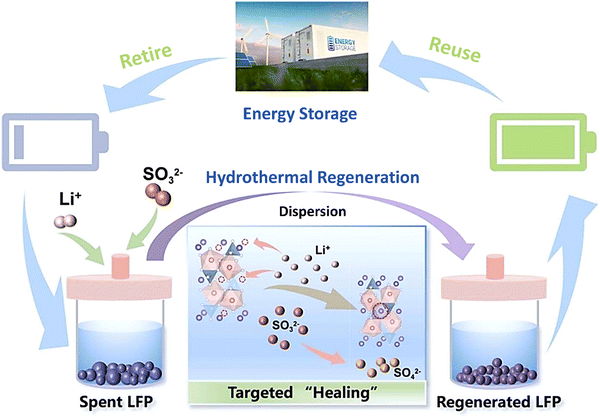 |
| Fig. 13 Hydrothermal regeneration of the spent LIBs as a closed-loop recycling. Reproduced with permission from ref. 123; Copyright 2023, Elsevier. | |
The integration of microwave with hydrometallurgy provides an environmentally friendly and time-saving leaching process.124 By using citric acid as the leaching agent and ascorbic acid as the redox agent, the microwave-assisted hydrometallurgical leaching achieved an efficient and low-energy-consumption strategy to upcycle cathodes in spent LIBs to lithium dual-ion battery anodes.124 Liu et al. combined the microwave-based method with DESs to achieve a fast leaching of Li and Co within 10 min.125 Under the microwave conditions, the free hydrogen ions in DESs combine with chloride anions to attack the original crystal structure of spent LIBs, facilitating the formation of defects and subsequent dissolution.125
The integration of the mechanical process,126 membranes,127 and additives128,129 with hydrometallurgy has been designed to promote the leaching and extraction of valuable cathodes. Notably, challenges remain in the comprehensive design of the recycling processes to introduce external technologies (e.g., mechanical and membrane processes). The complexity of the closed-loop recycling increases with the use of integrated technologies. Among the integrated technologies, bioleaching and electrometallurgy processes have received increasing attention,130 which are discussed in Sections 5 and 6, respectively.
(4) Sustainable utilization (Hyro 4.0).
The sustainable utilization (Hyro 4.0) is similar to that of Pyro 4.0, in which a closed-loop recycling can be achieved under the sustainable assessment for large-scale applications in future. The pioneering research on the sustainable utilization for hydrometallurgical recycling of cathodes is reviewed in this section.
Xu et al. designed a green and sustainable system with the configuration of “lithium-rich electrodes‖LLZTO@LiTFSI + P3HT‖LiOH” (Fig. 14), in which lithium-containing electrodes can be recycled by double-side and roll-to-roll approaches without destroying their integrity.131 The key connection of the “LLZTO@LiTFSI + P3HT” membrane solved the H+/Li+ exchange problem, resulting in high Li selectivity (97%), excellent faradaic efficiency (≥97%), and high purity of LiOH and H2.131
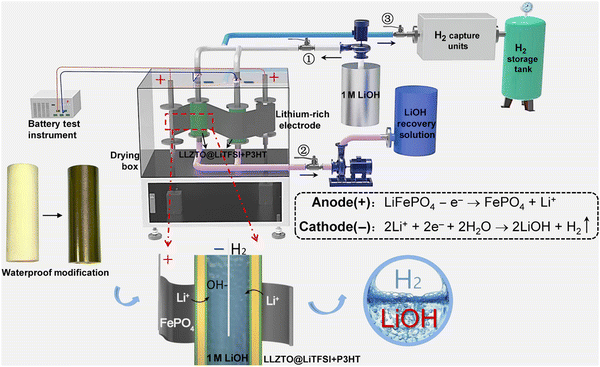 |
| Fig. 14 The green and sustainable system with the configuration of “lithium-rich electrode‖LLZTO@LiTFSI + P3HT‖LiOH”. Reproduced with permission from ref. 132; Copyright 2022, Science. | |
To promote the large-scale application of the hydrometallurgical process, Kim et al. reutilized wastewater containing highly concentrated ions by electrodialysis.133 The regenerated base served as a CO2 adsorbent to enhance the sustainability during the recycling of cathodes and wastewater.133 The economic analysis highlighted the reduction of the cost of chemicals and recycling process.133 Nevertheless, Cao et al. claimed that the co-products' recovery of anodes, additives and wastewater did not necessarily mitigate the environmental and economic trade-offs in comparison to that of the main product and recycling of cathodes.134 Specifically, co-product recycling doubled the net greenhouse gas emissions and decreased the economic gain.134 Conversely, the human health impacts were mitigated by co-product recycling.134 The detailed discussion on the sustainability of the recycling process135 is provided in Section 9. The discussion herein is intended to propose the sustainable utilization based on the achievement of the hydrometallurgical process.
4.1.2 Anodes.
The recycling of graphite anodes is important to establish a fully closed loop.136 During the pretreatment process, a manual separation of cathodes and anodes contributes to the subsequent leaching and recycling.109 However, the manual operation is not applicable for a large-scale recycling process, in which a mechanical process is conducted including crushing, sieving, magnetic separation and classification.32 The mixture of anodes and other components poses the challenge for the recycling and upcycling of graphite anodes.32 As discussed in Section 3.1.2, high-temperature thermal treatment contributes to the reconstruction of graphite anodes. Thus, the practice of combining leaching and thermal treatment has been explored to recycle graphite anodes (Fig. 15).136,137
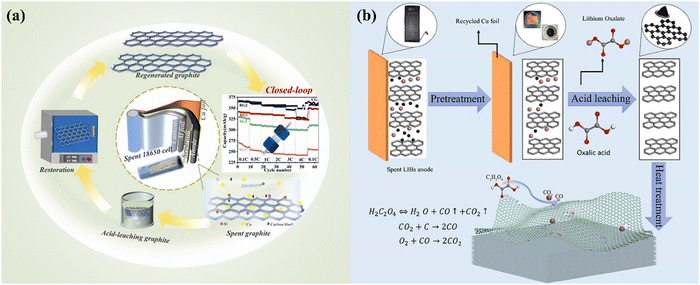 |
| Fig. 15 The combination of acid leaching and thermal treatment for the recycling of spent graphite anode as a closed-loop approach. Reproduced with permission from ref. 138 and 139; Copyright 2023, Elsevier. | |
By applying sulfuric acid and nitric acid, acid leaching graphite was prepared for subsequent thermal reconstruction (Fig. 15).137 It was found that the layer space of graphite was enlarged by the concentrated acid mixture,137 which has been confirmed by the initial intercalation of acids during the preparation of graphene oxide by Hummers' method.140 Accordingly, the migration of Li+ was promoted during the charging and discharging processes, showing an excellent regeneration performance.137 Organic acid-based leaching has also been investigated to assist the vapor phase reduction of high-density defects of graphite anodes during the thermal treatment process.136 Oxalic acid was used in the initial leaching process, in which the subsequent thermal treatment at 600 °C was conducted for the regeneration of graphite anodes.136 It was found that CO2 and CO produced from the thermal decomposition of oxalic acid contributed to the formation of nanoconfined structures with high-density defects in spent graphite.136 During the conventional regeneration of graphite anodes, the defects in the spent graphite anodes were usually eliminated by the reconstruction process. However, during the oxalic acid-based leaching process, the high-density defects produced from the thermal treatment facilitate a high electrochemical performance with enriched activated sites and mass transfer efficiency as that of lithium-ion batteries.136 The flexibility of recycling graphite promotes the exploration to upgrade the spent graphite.
4.1.3 Binders, separators and electrolytes.
The conventional pretreatment processes are designed to promote separation and disposal of binders, separators, and electrolytes for the subsequent recycling of cathodes and anodes.32 As discussed in Section 3.1.3, the thermal decomposition of binders and separators usually occurs during the pyrometallurgical process. Nevertheless, the dissolution process is applied to remove the adhered binders and separators (e.g., PVDF and Al foils) using organic solvents during the hydrometallurgical processes.32 Additionally, ultrasonic treatment has been tested to promote the separation and collection of active cathode materials. Nevertheless, the chemical stability of binders and separators such as PTFE resists the dissolution during the leaching process, showing a great challenge to recycle binders and separators. Research on the handling, disposal and recycling of binders and separators needs to be conducted to achieve a fully closed-loop recycling in future.
Since valuable contents (e.g., Li) exist in the electrolyte solution, the leaching process has been designed to extract the electrolyte during the hydrometallurgical process.109 The well-designed processes involving supercritical CO2 extraction, anion exchange deacidification, dehydration and component supplementation are utilized to recycle spent LIB electrolytes.141 Additionally, 6% H2SO4 at 80 °C was optimized to prepare lithium carbonate from lithium-rich electrolytes during the hydrometallurgical process.141
4.2 Factors influencing the recycling performance
4.2.1 Thermodynamics and kinetics.
Thermodynamics provides the information regarding chemical stability of spent LIB components and reaction viability of dissolution, leaching, extraction, precipitation and other recycling processes.142 In addition to the chemical reactions at increasing temperature (discussed in Section 3.2 on the pyrometallurgy), the influence of leaching and precipitation reactions at different temperatures and pH values on the hydrometallurgical processes is usually investigated.142
To investigate the effect of reductants on the hydrometallurgical process, Sun et al. applied the thermodynamics of leaching reactions to calculate the Gibbs free energy based on the initial and final states of the reaction system.143 However, the thermodynamically favorable leaching products should be identified carefully.143 Accordingly, the reduction of Co3+ to Co2+ by SnCl2 occurred with the oxidation of Sn2+ to Sn4+.143 It was found that the Gibbs free energy of the H2O2 leaching reaction is smaller than that of the SnCl2 leaching reaction, indicating a large range of the H2O2 leaching reaction but a feasible replacement of H2O2 leaching by SnCl2 leaching.143 By using the Van’t Hoff equation, the thermodynamics of the extraction of Co and Li was analyzed during the leaching process by ionic liquid extraction.144 Accordingly, the extraction process of Li and Co was an endothermic reaction, in which the increasing temperature contributed to the extraction of Co and Li.144 The separation factor of Co and Li was 102.11 at 60 °C showing a well separation potential for recycling Co and Li.144 In view of the limited thermodynamic data from HSC Chemistry 6.5, different calculations on the complexity of the reaction of critical metals with Cl− and dehydroascorbic acid were conducted using MATLAB and Material Studio 7.0, respectively.116 Accordingly, the reaction mechanism was proposed with quantum chemistry calculations. As shown in Fig. 16, the Eh-pH diagram showed a sharp increase in the first 3 min due to the alkaline nature of LiCoO2.116 Then, a stable pH of around 0.52 was found coupled with the diffusion-controlled mechanism.116
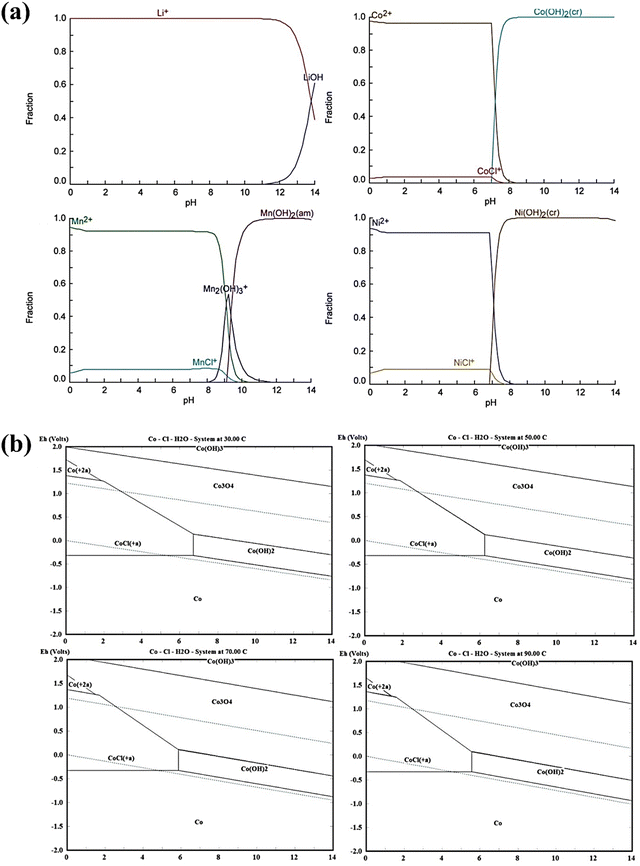 |
| Fig. 16 The Eh-pH diagram during the leaching process. Reproduced with permission from ref. 145; Copyright 2021, Elsevier. | |
To optimize the pH of precipitation, the Eh-pH diagram was usually calculated as the extension of thermodynamic analysis.146 Based on the experimental and thermodynamics analysis, He et al. demonstrated that NH4HCO3 failed to achieve the separation of Mn and Co in the water leaching system.147 In contrast, (NH4)2S2O8 can induce the oxidative precipitation of Mn at pH < 2 for the separation with Co.147 Moreover, a detailed thermodynamic prediction was carried out using Visual MINTEQ 3.0 software, which provides the simulation of thermodynamic equilibria by calculating metal speciation, solubility and sorption equilibria.148 Additionally, in another study which used a salt leaching method, thermodynamic analysis was conducted to find out a suitable pH for the recovery of valuable metals (e.g., Co, Mn, Ni, etc.) from spent batteries.149
Reaction kinetics evaluates the reaction rates of leaching, extraction and precipitation processes for recycling spent LIBs.142 The temperature and concentration are involved in the calculation of reaction kinetics.142 The surface chemical reaction and diffusion have been identified as the key parameters to control the kinetics of leaching processes.150 During the leaching process, the diffusion of the leaching agent occurs first within the liquid film surrounding the particles (e.g., active cathode materials).150 Then, the leaching agent passes the solid product layer of the particle to the surface of the inner core for the chemical reaction.150 It was found that the temperature was recognized as the most influential parameter.150 Specifically, the surface chemical reaction controlled the leaching of Co (cobalt) at a temperature lower than 45 °C.150 However, the leaching rate of Co was controlled by diffusion through the product layer at a temperature higher than 45 °C.150 It should be noted that the optimization of feasible kinetic model formulae is still in progress to precisely describe the reaction kinetics.150 Lin et al. established a multiple-factor formula to enable the prediction and the Monte Carlo simulation for the exploration of the leaching kinetics mechanisms.151 Specifically, the curve fitting results for the leaching of Li and Co showed a well fit of the chemical reaction model in the initial stage (0–10 min) and subsequently the diffusion reaction model (20–60 min).151 The abundant acid leachant in the initial stage provided a sufficient reactant for the chemical reaction.151 Then, the depleting acid had to diffuse through the product layer for the reaction, which was controlled by the diffusion reaction model.151
4.2.2 Hydrometallurgical parameters.
During the conventional hydrometallurgical processes, the solid to liquid ratio (S/L), temperature, types of acid (e.g., organic and inorganic acids), acid concentration, and additives (e.g., hydrogen peroxide concentration) serve as the key parameters for the hydrometallurgical efficiency.150 To optimize these parameters, the response surface methodology (RSM) has been utilized to achieve the maximum recycling efficiency.150 Firstly, the screening tests were designed to reduce the number of experiments according to orthogonal array L16 by the Taguchi method.150 The most influential variables were screened for the subsequent design by RSM subdivision with the Design Expert 7 software.150 Accordingly, temperature was recognized as the most influential parameter.150 The optimized conditions (e.g., S/L: 30 g L−1; temperature: 60 °C; acid concentration: 2 M; H2O2 concentration: 1.25%; leaching time: 2 hours) achieved 81% of Co and 92% of Li recovery.150 By using the same RSM optimization, the revised leaching system with gluconic and lactic acids was designed to achieve 100% recovery of Li and 97.36% recovery of Co.152 The optimized conditions included a S/L ratio of 16.3 g L−1, a temperature of 79 °C, an acid concentration of 1.52 M, a H2O2 amount of 4.84% and a leaching time of 2 hours.152 In addition to the temperature, the optimized addition of acids and additives serves as the vital parameter to maximize the recycling efficiency.152
In terms of practical applications, the optimization of leaching time and temperature is conducted with a high recovery efficiency as well as a low energy cost during the hydrometallurgical process. Around 100% recovery of all valuable metals was achieved at a temperature of 51 °C for 60 min.110 The subsequent precipitation and fabrication of new cathodes facilitated the closed-loop recycling.110 With the increasing temperature to subcritical conditions, more than 95% Co and nearly 98% Li were recovered at 350 °C for 30 min.110 Notably, PVC was completely dechlorinated without any release of toxic chlorinated organic compounds.110 By adding a DES as an efficient leachant, nearly 100% recovery of Li and Co was achieved within 10 min at 70 °C.125 Thus, the comprehensive optimization of operational parameters should be conducted in terms of the economy, effectiveness, and environmental impacts.
4.3 Perspectives
The key knowledge gaps and new research directions to develop sustainable, eco-friendly and highly efficient hydrometallurgy-based recycling technologies are discussed with the following perspectives.
(1) Elaborate pretreatment and selective leaching: an elaborate pretreatment including separation and classification of active cathode and anode materials usually helps in the subsequent leaching, extraction and precipitation processes for the recycling of spent LIBs. Most of the laboratory-scale recycling has been conducted by the manual pretreatment. Accordingly, the high recovery of specifically valuable metals was achieved with the developed hydrometallurgical methods. However, mechanical treatment is more feasible for the large-scale recycling process than manual operation.32 The complete separation and pretreatment are difficult to be achieved because of the complicated structure of spent LIBs. The recycling methods developed in the laboratory face the challenges when applied in the large-scale recycling of complicated LIBs. Accordingly, the selective leaching and extraction provide the solution to tackle this challenge, in which selective leaching and extraction have received increasing attention during the recycling of spent LIBs.153 Notably, the modified and updated methods should be investigated for the selective leaching and extraction of new components of next-generation batteries.32 A sustainable strategy should be proposed to consider the elaborate pretreatment and selective recycling when designing the next-generation batteries.
(2) Effectiveness and sustainability: the recycling effectiveness has been improved during the initial leaching stage of the Hydro 1.0 by introducing H2O2 and other intensified agents. However, the sustainability of Hydro 1.0 is criticized during the high consumption of inorganic acids and high generation of the toxic liquid phase. Thus, organic acids are applied in Hydro 2.0 considering the effectiveness and sustainability. However, the emission of pollutants is difficult to avoid during the leaching process, promoting the integration of treatment of the wastewater in Hydro 3.0 and Hydro 4.0. Additionally, the development of bio-hydrometallurgical (discussed in Section 5) and electrometallurgical (discussed in Section 6) processes shows the efforts to consider the effectiveness and sustainability. However, the recycling of spent LIBs is so urgent that we cannot dispose the spent LIBs until the full development and implementation of a well-designed recycling strategy. Meanwhile, the environmental damage caused by the toxic liquid emission is irreversible. Accordingly, a suitable recommendation is proposed to apply the modified method to improve the sustainability of currently commercial hydrometallurgy considering the effectiveness and sustainability.
(3) Integration of hydrometallurgy with other technologies as a closed-loop recycling: the integration of hydrometallurgy with other technologies as a closed-loop recycling provides a flexible approach to solve the challenge in terms of the effectiveness and sustainability. The combination of pyrometallurgical and hydrometallurgical processes has been investigated to maximize the recycling of cathodes, anodes and other valuable components in a closed-loop recycling.154 Additionally, the integration of hydrometallurgy with other technologies provides the solution to the current challenges such as toxic gas, liquid and solid emissions. Meanwhile, the integration of different technologies enhances the modularization, which helps in the upgrading of LIBs in terms of the recycling of complicated and new components of spent LIBs in future.
5. Recycling of spent LIBs by the bio-hydrometallurgical (bioleaching) process
5.1 Bacterial bioleaching for recovery of valuable metals from spent LIBs
In the bacterial-based bioleaching process, iron (e.g., IOB – iron oxidizing bacteria) and sulfur oxidizing microorganisms (e.g., SOB – sulfur oxidizing bacteria) are commonly used for recovery of valuable metals from the spent LIBs.155 The acidophilic bacteria which are used in bioleaching experiments are mainly from the following three genera namely Acidithiobacillus, Sulfobacillus and Leptospirillum.156 The IOB microbes used for bioleaching studies include Acidithiobacillus ferrooxidans, Sulfobacillus spp. and Leptospirillum ferriphilum, while Acidithiobacillus thiooxidans, Alicyclobacillus spp, and Sulfobacillus thermosulfidooxidans are the key SOB microorganisms employed for bioleaching experiments.36 In the IOB-mediated bioleaching process, IOB act as biological oxidizing agents which oxidize the ferrous ion (Fe2+) to a ferric ion (Fe3+), whereas in the SOB-mediated process, SOB oxidize sulfur by reducing S0 to SO42−.157 Sulfuric acid (H2SO4) is the main bioacid produced in the bacterial leaching system.158
In bacterial-mediated bioleaching, both mixed (e.g., IOB plus SOB)159–161 and pure cultures (IOB or SOB)158,162 are employed. However, mixed culture systems seem to be more efficient for metal recovery.163 Using mixed culture microbial systems (A. ferrooxidans (IOB) and A. thiooxidans (SOB)) using the two-step leaching method, Heydarian et al.157 obtained 50.4% Co, 99.2% Li and 89.4% Ni recovery with the experimental conditions of 36.7 g L−1 iron sulfate, 5 g L−1 sulfur and a medium pH of 1.5. Another study also applied the microbial consortia of A. ferrooxidans and A. thiooxidans for the removal of Co and Li from spent LIBs containing LCO (27.5 wt%) as the cathode material.161 The removal efficiency of Co was 67% while 80% Li recovery was achieved. In a recent study, bioleaching using ascorbic acid (0.1 M)-based mixed culture (Acidithiobacillus caldus and Sulfobacillus thermosulfidooxidans) was explored at an initial pH of 2.5 and a sulfur dose of 10 g L−1 for optimum recovery of several critical metals (mainly Co and Li) from spent LIBs at high pulp density.163 The addition of ascorbic acid showed positive effects since only 40% Co and 60% Li recovery were obtained without ascorbic acid. However, in the integrated system with ascorbic acid, the recovery of both Co and Li considerably increased to 94% and 95%, respectively, at a higher pulp density (20 g L−1).
Numerous studies have been conducted on the removal of valuable metals from the complex spent LIB residues using pure cultures of IOB or SOB. Biswal et al.158 used chemolithoautotrophic bacteria (A. thiooxidans) for the recovery of Co and Li from spent LIBs using one-step and two-step experimental methods. Between the two types of leaching conditions, the metal recovery rate of the two-step method (Co: 22.6% and Li: 66%) was higher than that of the one-step process (Co: 2.7% and Li: 22.8%). Naseri et al.164 found that the removal efficiency of three critical elements namely Co, Li and Mn from spent coin LIBs was 60%, 99% and 20%, respectively, at a pulp density of 30 g L−1. The TCLP tests showed that the bioleaching treatment was effective to reduce the metal concentrations in spent LIB residues to below the USEPA TCLP regulatory level, and the bioleached residues can be disposed safely. Another study from the same research group using A. ferrooxidans (IOB) achieved 88% Co, 100% Li and 20% Mn removal at a pulp density of 40 g L−1.165 Together, acidophilic IOB and SOB microorganisms show impressive performance for the recovery of critical metals from spent LIBs (Table 2).
Table 2 Bacterial-based bioleaching for recovery of valuable metals from spent LIBs. Adapted and modified from ref. 36
Bacteria |
Key experimental condition |
Bioleaching efficiency |
Ref. |
Co |
Li |
Other metals |
Note. A. thiooxidans: Acidithiobacillus thiooxidans. L. ferriphilum: Leptospirillum ferriphilum. Mixed culture 1: Acidithiobacillus ferrooxidans and Acidithiobacillus thiooxidans. Mixed culture 2: Acidithiobacillus caldus, Leptospirillum ferriphilum, Sulfobacillus spp. and Ferroplasma spp. Mixed culture 3: Leptospirillum ferriphilum and Sulfobacillus thermosulfidooxidans. Mixed culture 4: Acidithiobacillus thiooxidans and Leptospirillum ferriphilum. Mixed culture 5: Alicyclobacillus spp. and Sulfobacillus spp. NA: data not available. |
A. ferrooxidans
|
Pulp density: 10 g L−1 |
19.0% |
67% |
Mn: 50%, Ni: 34% |
166
|
A. ferrooxidans
|
Pulp density: 100 g L−1 |
94% |
60.30% |
NA |
162
|
A. ferrooxidans
|
Pulp density: 100 g L−1 |
82% |
89% |
Mn: 92%, Ni: 90% |
162
|
A. thiooxidans
|
Pulp density: 30 g L−1, pH: 2.0 |
60% |
99% |
Mn: 20% |
164
|
A. thiooxidans
|
Pulp density: 40 g L−1, pH: 2.0 |
88% |
100% |
Mn: 20% |
164
|
A. thiooxidans
|
Pulp desity: 0.25% (w/v), pH: 2.4 |
23% |
60% |
NA |
158
|
A. thiooxidans
|
Pulp density: 1% (w/v), pH: 1.0 |
NA |
98% |
NA |
167
|
L. ferriphilum
|
Pulp density: 1% (w/v), pH: 1.0 |
NA |
49% |
NA |
167
|
A. ferrooxidans
|
Pulp density: 1% (s/v), bacteria inoculation: 5% (v/v), pH: 1.5 |
47.60% |
NA |
NA |
168
|
A. ferrooxidans
|
Pulp density 1% (s/v) |
98.40% |
NA |
NA |
169
|
Mixed culture 1 |
Pulp density: 1% (w/v), pH: 2.0 |
99.95% |
NA |
Ni: 99.95% |
170
|
Mixed culture 2 |
Pulp density: 10 g L−1, pH: 1.8 |
99.90% |
84% |
NA |
160
|
Mixed culture 3 |
Pulp density: 5% (w/v), pH: 1.25 |
96.3% |
98.1% |
NA |
171
|
Mixed culture 1 |
Iron sulfate: 36.7 g L−1; sulfur: 5.0 g L−1, pH: 1.5 |
50.40% |
99.20% |
Ni: 89.4% |
157
|
Mixed culture 1 |
Pulp density: 10% (w/v), pH: 1.8 |
53.20% |
60.00% |
Ni: 48.7%, Mn: 81.8%, Cu: 74.4% |
155
|
Mixed culture 1 |
Pulp density: 10 g L−1, pH: 1.5 |
67% |
80% |
NA |
161
|
Mixed culture 4 |
Pulp density: 1% (w/v), pH: 1.0 |
96.0% |
92.0% |
Mn: 92%, Ni: 97% |
167
|
Mixed culture 4 |
Pulp density: 1% (w/v), pH: 1.0 |
NA |
>95% |
Mn: >95% |
167
|
Mixed culture 5 |
Pulp density: 2% (w/v), pH: 1.0 |
72.0% |
89.0% |
NA |
172
|
5.2 Fungal bioleaching for recovery of valuable metals from spent LIBs
The dominant fungi genera used in biological leaching studies include genera of Aspergillus (Aspergillus niger and Aspergillus tubingensis) and Penicillium (e.g., Penicillium simplicissimum and Penicillium chrysogenum).173,174 However, in most of the spent LIBs studies, Aspergillus niger (A. niger) is widely employed due to its high tolerance ability to the toxic environment and can grow over a broad range of pH.36,175 Fungal bioleaching is carried out using organic compounds as the source of carbon and energy, and the metabolism of organic substrates produces different types of carboxylic acid metabolites such as gluconic acid, oxalic acid, malic acid, citric acid, etc.36,158,173
Biswal et al. isolated two A. niger strains from Jatropha roots and aerosol samples, and then tested their performance for the removal of Co and Li from spent LIBs using the sucrose medium with a pulp density of 0.25% (w/v) under one-step and two-step leaching methods.158 The two A. niger isolates displayed similar bioleaching performance. Furthermore, between two types of bioleaching methods, a higher metal recovery rate was found when using the two-step method (Co: 82% and Li: 100%) than the one-step process (Co: 67% and Li: 87%). The authors have reported that citric acid (40.7–70.8 mM) was the dominant metabolite produced from the sucrose metabolism which contributed to the metal extraction from the solid spent LIB powder.136 Horeh et al.173 carried out the bioleaching of spent LIBs from mobile phones in sucrose medium using a pure culture of A. niger (PTCC 5210) with a pulp density of 1% (w/v) in three different methods (one-step, two-step and spent medium). The spent medium bioleaching tests resulted in an optimum recovery of multiple metals including Co (45%), Li (95%), Mn (70%), Ni (38%), Cu (100%) and Al (65%). Four types of bioacids including citric, oxalic, malic and gluconic acids were detected in the leaching medium. However, the concentration of citric acid (8078 mg L−1) was considerably higher than that of other organic acids (1170–2126 mg L−1). In the subsequent work from the same research group, the A. niger strain was initially adapted to heavy metals using the spent LIB powder (0.3–1.0% w/v).175 The adaption process decreased the time to reach the A. niger to the logarithmic phase as well as accelerated the production of organic acids. Notably, in the un-adapted A. niger leaching medium with sucrose as the carbon source, oxalic acid was only produced. However, oxalic, malic, citric and gluconic acids were found in the leaching medium added with adapted A. niger culture, but gluconic acid was the dominant metabolite. Higher percentage of metal removal was also observed using the adapted A. niger (Co: 38%, Li: 100%, Mn: 72%, Ni: 45%, Cu: 94% and Al: 62%). Overall, the results of these studies show that fungal bioleaching is effective for the removal of diverse metals from the spent batteries (Table 3).
Table 3 Fungal-based bioleaching for recovery of valuable metals from spent LIBs. Adapted and modified from ref. 36
Fungus |
Key experimental condition |
Bioleaching efficiency |
Ref. |
Co |
Li |
Other metals |
Note. Mixed culture 1: Aspergillus niger and Aspergillus tubingensis. NA: data not available. |
Aspergillus niger
|
Pulp density: 10% (w/v), carbon source: glucose; pH: 4.5 |
NA |
73.3% |
NA |
176
|
Penicillium chrysogenum
|
Pulp density: 10% (w/v), carbon source: glucose; pH: 4.5 |
NA |
54.6% |
NA |
176
|
Aspergillus niger
|
Pulp density: 0.25% (w/v); carbon source: sucrose; pH: 3.5 |
80–82% |
100% |
NA |
158
|
Aspergillus niger
|
Pulp density: 1% (w/v), carbon source: sucrose |
38% |
100% |
Cu: 94%, Mn: 72%, Al: 62%, Ni: 45% |
175
|
Aspergillus niger
|
Pulp density: 1–2% (w/v), carbon source: sucrose |
64% |
100% |
Cu: 100%, Mn: 77%, Al: 75%, Ni: 54% |
177
|
Aspergillus niger
|
Pulp density: 1% (w/v); pH: 6.0 |
45% |
95% |
Cu: 100%, Mn: 70%, Al: 65%, Ni: 38% |
173
|
Mixed culture 1 |
Pulp density: 1% (w/v), carbon source: sucrose, impure sucrose or vinasse |
∼60% |
∼95% |
Mn: ∼98%, Ni: ∼80%, Al: ∼82% |
174
|
5.3 Bioleaching mechanisms
The mechanisms responsible for the bioleaching of spent LIBs can be described on the basis of the nature of interactions between microorganisms and the solid particles of spent LIBs in the aqueous medium. Depending on the microbe–material interactions, the bacteria-based bioleaching mechanisms are broadly divided into (1) the direct/contact mechanism, and (2) the indirect/non-contact mechanism.156 In the direct/contact mechanism, the microorganisms attach themselves onto the surface of the spent LIB particles through electrostatic attraction or hydrophobicity, and then form a biofilm.156 The attached microorganisms oxidize the substrates (e.g., S0 and Fe2+) present in the leaching medium under an aerobic condition. The microbial oxidation of sulfur produces biogenic H2SO4. The reactions involved in the direct mechanism are presented below (eqn (40)–(43)).35,178 The microbial conversion of sulfur to sulfate is mediated by the sulfur oxidase enzyme.179 |
 | (40) |
|
H2SO4 + M(s) → MSO4(aq) + 2H+ (M: metals present in spent LIBs) | (41) |
|
 | (42) |
|
 | (43) |
In the indirect/noon-contact mechanism, the microbial cells do not directly attach themselves to the solid particles of spent batteries.156 However, the leaching is driven by the metabolites produced by the microbial agent. For example, in the IOB-based bioleaching system, Fe2+ is used as a source of energy which is oxidized to Fe3+. Reduction reactions of Fe3+ then lead to proton (H+) production that increases the metal recovery rate (eqn (44)–(47)). The microbial oxidation of Fe2+ to Fe3+ is mediated by the ferroxidase enzyme.179
|
 | (44) |
|
Fe3+ + H2O → Fe(OH)2+ + H+ | (45) |
|
Fe3+ + 2H2O → Fe(OH)2+ + 2H+ | (46) |
|
Fe3+ + 3H2O → Fe(OH)3+ + 3H+ | (47) |
The fungal bioleaching is mainly carried out by three types of mechanisms including acidolysis, complexolysis and redoxolysis which are mediated by the production of organic acids by the heterotrophic fungi using glucose, sucrose or other organic substances as the source of carbon and energy.
36,173 The dominant carboxylic acids produced by fungi through sucrose metabolism include citric acid, oxalic acid, gluconic acid and malic acid.
175 Among the various acids, oxalic acid can promote precipitation of metals (
e.g., Co and Ni), while citric acid acts as a chelating agent to dissolve metals.
180 The mechanisms responsible for the removal of metals using different types of bioacids are presented below (
eqn (48)–(62)). The different pathways for the microbial-mediated removal of metals are illustrated in
Fig. 17.
|
C12H22O11 (sucrose) + H2O → C6H12O6 (glucose) + C6H12O6 (fructose) | (48) |
|
C6H12O6 (glucose) + 1.5O2 → C6H8O7 (citric acid) + 2H2O | (49) |
|
C6H8O7 ↔ (C6H7O7)− + H+ | (50) |
|
(C6H7O7)− + M+ (metal) ↔ M[C6H7O7] (citric metallic complex) | (51) |
|
C6H12O6 (glucose) + 4.5O2 → 3C2H2O4 (oxalic acid) + 3H2O | (52) |
|
C2H2O4 ↔ (C2HO4)− + H+ | (53) |
|
(C2HO4)− + M+ (metal) ↔ M[C2HO4] (oxalic metallic complex) | (54) |
|
C6H12O6 (glucose) + O2 → C6H10O6 (gluconolactone) + H2O2 | (55) |
|
C6H10O6 (gluconolactone) + 2H2O → C6H12O7 (gluconic acid) + H2O2 | (56) |
|
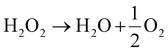 | (57) |
|
C6H12O7 ↔ (C6H11O7)− + H+ | (58) |
|
(C6H11O7)− + M+ (metal) ↔ M[C6H11O7] (gluconic metallic complex) | (59) |
|
4C6H12O6 (glucose) + 6O2 → 6C4H6O5 (malic acid) + 6H2O | (60) |
|
C4H6O5 ↔ (C4H5O5)− + H+ | (61) |
|
(C4H5O5)− + M+ (metal) ↔ M[C4H5O5] (malic metallic complex) | (62) |
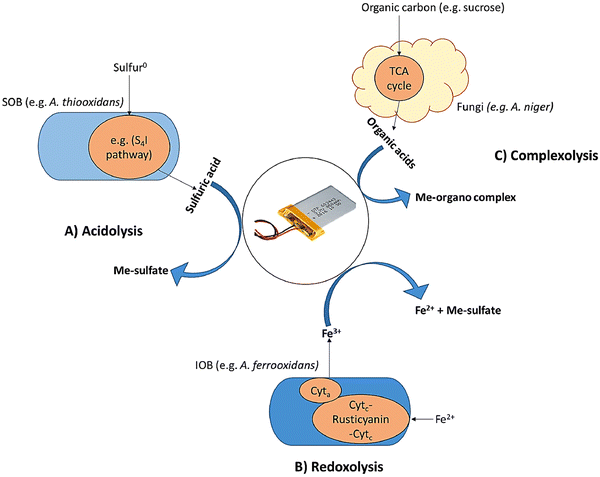 |
| Fig. 17 Different pathways of microbial-mediated metal solubilization. Reproduced with permission from ref. 37; Copyright 2021, Elsevier. | |
5.4 Bioleaching kinetics and thermodynamics
The rate of the bioleaching process is usually slower than that of the other spent LIB recycling technologies namely hydrometallurgy and pyrometallurgy.35,181 To enhance the bioleaching kinetics, several studies have been carried out using catalysis-based bioleaching with the application of metallic catalysts such as silver ions169,170 and copper ions181,182 as well as the application of ultrasonication (i.e. ultrasonic treatment).166 Different kinetic models including the shrinking sphere (Stokes regime), diffusion controlled, chemical reaction controlled and product layer diffusion models are used to evaluate the bioleaching transformation rate of different metals in spent LIBs.172 Niu et al.172 applied the above four kinetics models, and found that the bioleaching characteristics of Co (R2: 0.9731) and Li (R2: 0.9572) from spent batteries (pulp density: 2%, w/v) can be well-explained using the product layer diffusion model. A subsequent study conducted by the same research group on the spent Zn–Mn batteries using consortia of A. thiooxidans (SOB) and L. ferriphilum (IOB) as well as using Cu2+ ions as the catalyst reported that among the tested four models, the chemical reaction controlled model was the best to describe the kinetics of metal (Zn and Mn) dissolution in the catalytic bioleaching system (R2 ≥ 0.97).182 In a bacterial bioleaching system using A. thiooxidans, the kinetics data were evaluated using the diffusion and chemical reaction models.164 Among the two models, the chemical reaction model (R2 ≥ 0.92 for Co, Li and Mn) was the most suitable to explain the leaching kinetics. Thermodynamic analysis shows that the biological leaching has much higher chances to occur compared to the conventional chemical leaching process.172
5.5 Factors influencing the bioleaching performance
The major factors that influence the recycling performance of the bioleaching process include (1) the type of acidophilic microorganism (bacteria vs. fungi), (2) pH and temperature, (3) nutrients or source of energy, (4) pulp density, (5) catalyst and particle size of spent LIB powder, etc. The key recent findings are summarized here.
5.5.1 Acidophilic microorganisms.
The bioleaching-mediated recycling of spent LIBs is mainly carried out using either chemolithoautotrophic bacteria (e.g., IOB and/or SOB) or heterotrophic fungi. Bioleaching studies are conducted using the pure bacterial or fungal strains or microbial species isolated from heavy metals contaminated sites (e.g., mining site).158,167 Since bacteria and fungi use different substrates for their energy and growth, and they produce different biogenic acids (e.g., H2SO4 in bacteria, while organic acids in fungi), the metal removal efficiency could vary with the changes of types of microorganisms employed. Additionally, the metal bioleaching performance depends on the use of a single culture vs. mixed culture microbial system, and the consortia system usually demonstrates better performance for extraction of metals from waste materials.183 Biswal et al.158 compared the metal removal efficiency between bacterial and fungal leaching, and the metal extraction rate was significantly higher in fungal leaching (Co: 82% and Li: 100%) compared to the bacterial leaching system (Co: 23% and Li: 66%). A study compared the Li dissolution rate from the lepidolite mineral in the three different bioleaching systems (bacterial consortia, fungi and yeast).184 The bioleaching yield of mixed bacterial culture (8.8%) was higher than that of fungi (0.2%) and yeast (1.1%). To enhance the metal tolerance level, microorganisms can be initially exposed to the synthetic solution of metals or spent battery powder for a specific period.175,185 With initial adaption of A. niger to 1% (w/v) spent LIB powder, the adapted fungi exhibited a greater performance for the removal of various metals including Co (38%) and Li (100%).
5.5.2 pH and temperature.
Most of the bioleaching microorganisms are acidophilic and can grow in an acidic environment with pH ranging from 1.5–3.0. However, the pH range of 3.0–8.0 is most suitable for the growth of fungi.179 Apart from pH, temperature is another important parameter which controls the metal dissolution rate in the bioleaching process. A majority of the bioleaching microorganisms are mesophilic in nature with ideal temperature for their growth and metabolism ranging from 25–40 °C.179 Several fungal bioleaching studies were conducted in the temperature range of 27–30 °C.173,176,186
5.5.3 Nutrients.
The types of nutrients (N and P) and substrates (source of energy) as well as their concentrations present in the growth medium could impact the growth rate of the acidophilic microorganisms as well as the quality and quantity of the produced biogenic acids or lixiviant agents which predominantly drive the metal removal in bioleaching.37 In bacteria-based leaching (IOB and SOB), inorganic substrates like Fe2+ (e.g., ferrous sulfate, FeSO4), sulfur (e.g., elemental sulfur, S0) and pyrite (FeS2) are used as the sources of energy.35,187 To reduce the bioleaching process cost, waste materials like iron scrap can be considered as the substrate.160 Additionally, the medium is supplemented with nutrients namely ammonia, phosphate, magnesium and calcium to accelerate the bacterial growth. Thus, the adequate amount of these nutrients and substrates should be supplied to the growth medium to achieve the optimum microbial growth as well as high production of biogenic acids.
5.5.4 Pulp density.
Pulp density (also called the solid-to-liquid ratio, S/L ratio) is one of the critical parameters which impacts the bioleaching efficiency. In general, the bioleaching efficiency is reduced with the increase of pulp density due to reduction of microbial growth and metabolic activities. The increase of pulp densities causes (i) an increase of pH of the leaching medium due to consumption of protons (H+ ions) by the alkaline components of spent batteries, (ii) a decrease of oxidation reduction potential (ORP), (iii) an increase of toxicity substances like electrolytes and metals, and (iv) an increase of viscosity of the leaching medium which causes reduction of the availability of oxygen (i.e., a decrease of the oxygen transfer rate) as well as nutrients and substrates to the microorganisms.35,37 All these factors collectively contribute to the reduction of microbial activities in the leaching medium and decrease the bioleaching performance.
5.5.5 Catalyst and particle size.
To enhance the rate of bioleaching kinetics, the addition of metallic ions such as copper (e.g., Cu2+)181,182 and silver ions (Ag+)169,170 as catalysts and ultrasonication treatment166 are explored. In a bacterial leaching system with a mixed culture of IOB and SOB, the percentage of removal of Zn and Mn from spent Zn–Mn batteries (ZnMn2O4) increased from 7.7 to 62.5% and from 30.9 to 62.4%, respectively, with the rise of the Cu2+ concentration from 0 to 0.8 g L−1 at a pulp density of 10% (w/v).182 The increase of the kinetics rate was due to the formation of a copper-based intermediate product (CuMn2O4). An appropriate particle size of the spent batteries powered is required to achieve the optimum recovery of metals.36,188
5.6 Perspectives
Bioleaching technology is still limited to the laboratory-scale study which could be related to its slow metal dissolution kinetics. Thus, more studies are needed to enhance the bioleaching efficiency and achieve the selective dissolution of critical metals. Although numerous bacterial-based bioleaching studies are conducted, limited works have been carried out on spent LIB recycling using the fungal-based bioleaching system. Additionally, less research work has been done using the mixed culture systems (specifically using fungus isolates) since the bioleaching efficiency may increase due to the production of diverse biogenic acids produced by synergistic interactions between consortia microbes and spent batteries powder. At present, the performance of the bacteria and fungi is evaluated separately, but the performance of the hybrid microbial leaching system (specifically using the spent medium method) was not explored yet. A limited number of microbial isolates (IOB, SOB and fungal isolates) are currently available to use in bioleaching studies. To enhance the microbial collections, efforts should be made to isolate more microbial strains from the acidic environment and/or heavy metal contaminated sites. Synthetic biology tools can be applied to engineer the microbial genome specifically to modify the genes related to heavy metal tolerance and enzymatic-based substrate metabolism pathways to enhance the metabolite production. More mechanistic insight-based work is needed to better understand the microbe–material interactions and their effects on the bioleaching kinetics of the metal dissolution. From the sustainability and large-scale application points of view, in-depth life cycle analysis (LCA) including techno-economic analysis and environmental implications of the bioleaching technology should be carried out in future.
6. Spent LIB recycling by the electrometallurgical process
In recent years, electrometallurgy (Table 4) has received increasing attention for the recovery of critical metals from spent LIBs compared to the conventional methods including acid-based leaching or alkaline-based leaching.189 According to a recent study,190 electrometallurgy is a class of metallurgical technologies involving the use of electrolysis, electric-arc furnaces and other electrical operations, and includes four types of processes including electrowinning, electrorefining, electroplating and electroforming. The electrochemical process uses in situ generated electrons as the oxidizing or reducing agents rather than exogenous chemicals that are used in other recycling processes.191 In this process, the electrons are used as green oxidizing or reducing agents.192 The electrochemical treatment of metal-containing wastes usually involves multiple processes including oxidative leaching, reductive deposition, etc.191 The electrochemically assisted leaching is considered to be environmentally benign and more efficient than the traditional aqueous leaching method which requires a high amount of reactants, high concentrations of acids and high temperature.191 In this process, the metals can be extracted and purified, but it requires high energy consumption. In the electrolytic leaching process, an electrolytic agent such as H2SO4/CuSO4 as well as a reductant namely H2O2/Fe2+ are used.189,192,193 Numerous studies have used both the electrochemical leaching and electrodeposition together in a single electrochemical cell for the recovery of metals from spent batteries (Fig. 18).189,194 In the electrodeposition process, dissolved metal ions are reduced and deposited on the surface of electrodes with the application of current.195 Metal extraction through conventional methods namely solvent extraction or chemical precipitation produce low-quality products and cause secondary environmental pollution.195 However, efficient and selective recovery of metals based on their differences in the electrode potential (e.g., E0 for Pb2+, Ni2+, Fe2+ and Al3+ varied between −0.13 to −1.68 V, while Pb2+, Ag+, Pd2+, Pt2+ and Au+ ranged from 0.34 to 1.83 V) can be achieved by the electrodeposition method. Overall, in the electrochemical process, the electrochemical reactions take place at the electrodes, i.e., oxidation reaction at the anode, while reduction reaction occurs at the cathode (eqn (63) and (64)).196
Table 4 Performance of the electrometallurgical process for recovery of metals from spent batteries
Type of spent batteries |
Key experimental conditions |
Metal recovery efficiency |
Ref. |
Spent LIBs |
Current density −500 A m−2, Cu2+: 0.15 M, temperature: 60 °C and retention time: 60 min |
Co: 92%, Li: 97% |
189
|
Spent LIBs |
Mild leaching conditions (−0.15 V, 0.5 M H2SO4, 30C) with a low Ecell value (<1 V) |
Co: 98.16%, Li: 98.95%, Al foil: 89.61% |
197
|
Spent LIBs |
2.0–2.5 electrolyte solution pH, 90 °C temperature and current density of 200 A m−2 |
Co: 96%, Mn: 99%, Cu: 97% |
196
|
Spent LIBs |
1 M KOH solution, Fe2+ as reducing agent, pulp density: 200 g L−1 |
Co, Li, Mn, and Ni: 96% |
192
|
Spent NCM |
2.5 g L−1 (NH4)2SO4 electrolytic solution with reaction time 4–5 min at 25 V |
Li and transition metals: 98%, Al foil: 98.5% |
198
|
Spent NCM |
Electrolytic solution of 0.05 M K2SO4 with applied voltage of 2.5 V for 3 hours |
Li: 95.02%, Ni: 1.6%, Co: 0.6%, and Mn: 0.3% |
199
|
Spent LCO, LMO and NCM |
0.5 M H2SO4 electrolytic solution with application of 2.0 V for 90 min |
Co, Li, Mn, and Ni: >97% |
200
|
Scrap LMO |
Mixed electrolytic solution (1 M H2SO4 and 1 M MnSO4) with 30 A m−2 current density, 75 g L−1 of pulp density, 20 hours reaction time at 90 °C |
Li: 99%, Mn: 92% |
201
|
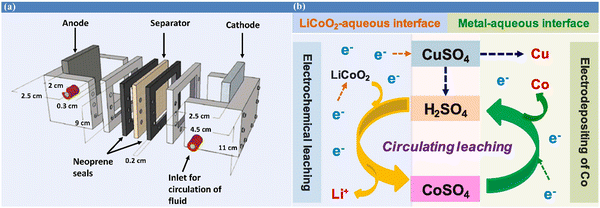 |
| Fig. 18 Schematic of the cell consisting of both electroassisted leaching and electrodeposition. Reproduced with permission from ref. 189 and 194; Copyright 2021, Elsevier; Copyright 2015, Elsevier. | |
Anode (oxidation):
Cathode (reduction):
Here, M refers to metals like Co, Cu, Ni,
etc., and
ne denotes the number of electrons/valency number.
Numerous lab-scale studies have been conducted on the recycling of spent batteries (LCO, NCM, LMO, etc. as the cathode materials) using the electrometallurgical process.189,196,199 In the electrochemical treatment, with the application of electric current to the electrochemical cell, oxidation of water occurs at the anode compartment which produces protons (H+).202 Then, the generated protons react with the cathode materials to drive the leaching of metals from spent batteries. Prabaharan et al.196 reported that the optimum conditions for the removal of various metals from spent LIBs were 2.0–2.5 electrolyte solution pH, 90 °C temperature and a current density of 200 A m−2 which resulted in about 96% Co, 99% Mn and 97% Cu removal in the electrochemical process. However in another study which was conducted with the application of 500 A m−2 current density, 0.15 M CuSO4 as an electrolytic solution, 60 °C temperature and 60 min leaching time, 92% Co and 97% Li could be removed from spent batteries in the electrochemical system.189 The different chemical reactions involved in the electrometallurgical process are presented below (eqn (65)–(67)). Hazotte et al.194 performed electro-assisted leaching and electrodeposition in a single cell for the recovery of metals from spent Ni–Cd batteries. The combined system shows high selectivity towards the removal of the major metal (e.g., Cd) by efficient electrodeposition. Since the conventional electrochemical system requires a high cell potential (Ecell) and may cause environmental problems, Kong et al.197 developed a novel electrochemical redox system for simultaneous recovery of both cathode and anode materials from spent batteries. The novel system was effective for the recovery of valuable metals from spent LIBs. Specifically, 98.16% Co and 98.95% Li recovery could be achieved under mild electrochemical leaching conditions of −0.15 V, 0.5 M H2SO4 and 30 °C temperature with a low Ecell value (<1 V). Additionally, 89.61% Al foil and graphite recovery were also achieved from spent LIBs. In a recent work, the cathode electrolysis was conducted to recover critical metals from spent LIBs.200 Using 0.5 M H2SO4 with an applied potential of 2 V and a reaction time of 90 min, more than 97% recovery of Co, Li, Mn and Ni was observed. The corresponding electrochemical reactions are shown in eqn (68)–(70).
Primary electrodeposition reaction:
|
2CuSO4 + 2H2O → 2Cu + 2H2SO4 + O2 | (65) |
Anode (acid generation):
|
2H2O → O2 + 4H+ + 4e− | (66) |
Cathode (electro-leaching):
|
LiCoO2 + 4H+ + e− → Co2+ + Li+ + 2H2O | (67) |
Cathode reaction:
|
LiCoO2 + 4H+ + e− → Li+ + Co2+ + 2H2O | (68) |
Anode reaction:
|
2H2O → O2 + 4H+ + 4e− | (69) |
Overall reaction:
|
4LiCoO2 + 6H2SO4 = 2Li2SO4 + 4CoSO4 + O2 + 6H2O | (70) |
A study using acidic Cl-based electrolyte (
i.e., electrolysis of 0.5 M NaCl at 8 V with mixed metal oxide or graphite electrodes) reported that the electrolytic solution generated using the mixed metal oxide electrode shows better performance for the removal of various metals from spent LIBs (Li: 24%, Ni: 20% and Mn: 6%).
203 The associated electrochemical reactions are shown below (
eqn (71)–(74)), Liu
et al.198 reported that with the optimized electrolysis conditions of 25 V, a temperature of 25 °C and a reaction time of 4 min using 2.5 g L
−1 (NH
4)
2SO
4 as the electrolytic agent, 98% Li and 98.5% Al foil were recovered from the spent NCM batteries. The remaining metals in the leach liquor were used to resynthesize the cathode material which showed good electrochemical performance with an initial capacity of 161 mA h g
−1 at 0.1C and 88.3% capacity retention after 200 cycles.
|
2Cl− → Cl2 + 2e− (E0 = −1.360 V) | (71) |
|
H2O → 0.5O2 + 2e− + 2H+ (E0 = −1.230 V) | (72) |
|
Cl2(g) + H2O(l) → HOCl(Aq) + HCl(Aq) | (73) |
|
2H2O + 2e− → H2 + 2OH− (E0 = −0.828 V) | (74) |
6.1 Factors influencing the spent LIB recycling performance in electrometallurgy
The major factors that influence the recycling performance of electrometallurgy include (1) current density/applied voltage, (2) electrolyte concentration, and (3) leaching time, temperature, mixing, etc. The key recent findings are summarized here.
6.1.1 Current density/applied voltage.
The current density/applied voltage is one of the important parameters which could impact the metal leaching efficiency in the electrochemical process. A recent study evaluated the influence of different current density (100–400 A m−2) on the efficiency of the electrochemical leaching of spent LIBs using 2 M H2SO4 and a reaction time of 90 min.196 The leaching rate of different metals was directly proportional to the current density.
6.1.2 Electrolyte concentration.
The leaching efficiency of metals in the electrochemical process could change with the change of the concentration of acids which are usually used as an electrolyte. Prabaharan et al.196 investigated the effects of different concentrations of H2SO4 (1.0–4.0 M) on the recovery of various metals from spent LIBs using the electrochemical leaching at a current density of 200 A m−2 and a reaction time of 150 min. The leaching efficiency for various metals (e.g., Co, Li, Mn and Ni) was enhanced with the increase of the H2SO4 concentration from 1 M (metal removal: nearly 40–58%) to 2 M (nearly 100% metal dissolution). Further increase of the acid concentration above 2 M had negative effects on the leaching performance. The decline of metal removal efficiency above 2 M H2SO4 concentration was presumably due to the saturation effects (i.e., saturation of leaching solution with the metal ions).
6.1.3 Leaching time, temperature and mixing.
The variation of leaching time/reaction time could change the electrochemical leaching efficiency. With the increase of the leaching time from 30 to 300 min, the leaching efficiency of various metals (Co, Li, Mn, Ni, and Al) from spent LIBs increased from nearly 60% (for all metals) to 78.3% for Co, 76.7% for Li, 77.2% for Mn, 81.2% for Ni and 79.1% for Al. Another study also showed that the increase in the leaching time had positive effects on the recovery of metals from spent batteries by the electrochemical process since with the increase of reaction time from 0 to 60 min, the recovery rate of two critical elements namely Co and Li increased from 0% to 92 and 97%, respectively.189 The leaching solution/environmental temperature plays a critical role in the recovery of valuable metals from spent batteries in the electrometallurgical process. A study evaluated the effects of different temperatures (30–80 °C) on the removal of Co and Li from spent LIBs at a current density of 500 A m−2 and 0.15 M CuSO4 solution.189 The metal leaching efficiency increased up to a temperature of 60 °C (86% Co and 95% Li), and then remained unchanged between 60–80 °C. The rise of leaching efficiency with the increase of temperature at the initial stage was due to the increase of the diffusion rate of metal ions in the electrolytic solution, which avoided the concentration polarization and the enhancement of the current efficiency. However, the decrease of leaching efficiency at higher temperature could be due to the reduction of hydrogen evolution overpotential and the enhancement of the hydrogen evolution reaction at the negatively changed anode compartment. The type and speed of mixing of mixing equipment could impact the leaching efficiency in the electrochemical system due to the increase of the mass transfer rate caused by mixing. A mechanical stirrer or magnetic stirrer is typically used in the electrochemical system.201
6.2 Recovery of metals from the leach liquor (electrodeposition)
Several studies have attempted to recover the valuable metals from the leach liquor using the electrodeposition process. However, the performance of the electrodeposition process depends on numerous parameters including solution pH, reaction temperature, current density, pulp density, etc.189,196 A study applied an electrolytic method for the recovery of Co and Mn from the purified leach liquor obtained from electrochemical leaching with H2SO4 as the electrolytic agent.196 In the electrolytic process, Co was deposited at the cathode material by reduction reaction while Mn was oxidized at the anode and formed electrolytic manganese dioxide. The electrolytic oxidation and reduction reactions are presented below (eqn (75)–(78)). The purity of the recovered products was very high with 99.2% for Co and 96% for MnO2. Li et al.189 reported that 93.22% Co recovery was obtained with a current efficiency of 69.36% under the following optimum electrodeposition conditions: 500 A m−2 current density, 40 min reaction time, 70 °C reaction temperature, 7.5 g L−1 pulp density, and 2.5–3.0 solution pH. In addition to Co, Cu deposition was also achieved from CuSO4 solution (eqn (79)).
At cathode (reduction):
|
Co2+ + 2e− → Co (E0 = −0.28 V) | (75) |
|
2H+ + 2e− → H2 (E0 = 0 V) | (76) |
At anode (oxidation):
|
2H2O → O2 + 4H+ + 4e− (E0 = 1.23 V) | (77) |
|
Mn2+ + 2H2O → MnO2 + 4H+ + 2e− | (78) |
Electrodeposition of Cu:
|
Cu2+ + 2e− → Cu (E0 = 0.337 V) | (79) |
6.3 Perspectives
Electrometallurgy is an important and practical method for the recycling of spent LIBs. However, limited studies have been conducted using different electrochemical conditions (e.g., current density, electrolytic solutions, reaction time, solution pH, pulp density, mixing intensity, etc.) to evaluate the performance of the electrochemical systems for the recovery of valuable metals from spent LIBs. The electrometallurgical method employed for the recycling of spent batteries is still at the state of infancy at the present time since most of the studies were carried out under the laboratory-scale experimental conditions. Therefore, more in-depth works are needed to scale-up the electrometallurgical process for large-scale industrial applications. The improvement in the performance of the electrodeposition process can be explored by using the cathode materials with better deposition characteristics, low-cost and stable electrolytic solution, increasing the mass transfer rate by using different techniques such as using a rotating electrode or turbulent flow and/or by integration of a membrane into the electrochemical system. Since the performance of the electrochemical process specifically for the selective metal leaching is highly dependent on the level of impurities present in the electrode materials of spent batteries to be recycled, an efficient pre-treatment process (e.g., disassembly and crushing) is required to obtain electrode materials with less impurity. The use of an acid-based electrolytic solution could damage the electrochemical system (e.g., due to corrosion) during the long-term continuous operation, Thus, a suitable green and environmentally friendly electrolytic agent should be developed.
7. Sustainability of recycling technologies of spent lithium-ion batteries (LIBs)
To comprehensively ascertain and appraise the advantages and drawbacks associated with the recycling of LIBs, particularly concerning sustainability, we have compiled and analyzed relevant life cycle assessment (LCA) and life cycle cost (LCC) investigations pertaining to lithium cobalt oxide (LCO) LIBs.
7.1 LCA of various recycling technologies of LIBs
7.1.1 Overview of LCA in recycling of LIBs.
LCA constitutes a systematic and practical tool that has the capability of assessing the environmental burden associated with products, processes, or activities throughout their entire life cycle, encompassing stages ranging from raw material acquisition to final disposal.204 The application of LCA allows for a comprehensive evaluation of the environmental impacts of various methods used for the recycling of spent LIBs. Specifically, insights can be gained regarding the transfer of environmental impacts across the various stages of recycling of LIBs.
LCA comprises four distinct phases: goal and scope definition, inventory analysis, impact assessment, and interpretation.204 Initiated by a well-defined goal and scope, LCA establishes the recycling methods’ depth and breadth, including the functional unit, system boundaries, and relevant assumptions and limitations. In the context of LIB recycling analysis, common functional units encompass mass-based metrics (e.g., one ton of spent LIB batteries or 1 kg of cobalt recycled) and energy-based metrics (e.g., 1 kW h of electricity capacity stored).39,205–209 The inventory analysis phase entails recording the inputs of energy and raw materials and the outputs of products, by-products, and environmental releases. Variation exists in impact categories adopted by different LCA studies, including aspects like energy consumption, greenhouse gas (GHG) emissions, acidification, gas emissions, eutrophication, toxicity, and carcinogens. Among these, global warming potential (GWP) and cumulative energy demand (CED) represent the most frequently utilized categories in LCA studies focusing on LIB recycling.39,210 The final phase, interpretation, discusses the outcomes of both life-cycle inventory and impact assessment. The conclusions derived from the interpretation offer valuable guidelines for recommendations and decision-making that align with the predefined goal and scope of the LCA study. Consequently, the LCA process provides essential insights into the environmental implications of LIB recycling, empowering stakeholders to make informed and sustainable choices.39,211
Fig. 19 illustrates generalized boundary, process and material/energy flow analysis within the context of LCA for a battery. Numerous cradle-to-gate assessments focusing on LIBs have consistently revealed that the largest environmental impacts occur during the raw material phase, encompassing materials extraction, transportation, purification, and other associated processing stages.212,213 Consequently, this emphasizes the crucial role of battery recycling in the complete life cycle of batteries, particularly its positive influence on battery production. Emphasizing the importance of sustainability, recycling LIBs yields numerous benefits, including pollution mitigation, decreased primary mineral resource consumption, and a viable alternative to mitigate dependence on fossil fuels.212,214
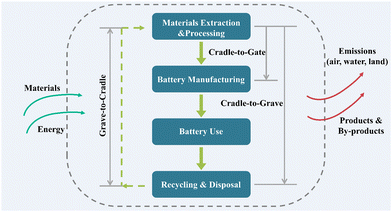 |
| Fig. 19 Generalized boundary, process and material/energy flow analysis of an LCA of a battery. Reproduced with permission from ref. 39; Copyright 2018, Royal Society of Chemistry. | |
7.1.2 Comparison of environmental impacts of different recycling technologies.
Currently, most of the LCA-based studies focus on devising recycling methodologies for the extraction of cathode materials from spent LIBs.214 This focus is justified due to the significant impact of cathode materials on life cycle emissions of environmental pollutants and recovery of value-added materials within the battery system. In general, environmental trade-offs associated with the recycling of spent LIBs that can be harnessed are highly contingent upon the use of chosen recycling techniques. In view of the long processing chain involved in the recycling process, minor changes in recycling procedures can yield substantial alterations in the final outcomes.39,209 Wu et al. reported that GHG emissions and CED exhibit considerable variability across different hydrometallurgy and pyrometallurgy recycling approaches, ranging from 67 to 286 kg of carbon dioxide equivalent (CO2eq) and 1164–4349 MJ, respectively, for the regeneration of 1 kg of LCO cathode material from recovered cobalt.209 In comparison, a direct “cathode healing” process was found to emit 21–154 kg CO2eq and consume 267–2251 MJ to regenerate 1 kg of LCO cathode material. Cao et al. conducted a comprehensive assessment of the hydrometallurgy recycling process employing inorganic leaching.210 This study revealed that GHG emissions were 33 kg CO2eq per 1 kg of cobalt obtained, with an estimated CED of 572 MJ. Additionally, the study highlighted that the recycling of co-products (such as Li2CO3, nickel, Na2SO4, and graphite) doubled the net greenhouse gas emissions. Nevertheless, it had a positive impact on human health by mitigating the environmental burdens associated with virgin co-product production. Another LCA analysis, conducted by Lin et al., assessed GHG emissions during the hydrometallurgical process while employing Organic Aqua Regia (OAR).206 The findings indicated that OAR generated lower GWP, approximately 60 kg CO2eq, in comparison to citric acid (approximately 90 kg CO2eq). OAR's GHG emissions were also found to be comparable to those generated by nitric acid during the leaching process for lithium or cobalt extraction from 1 kg of the LCO cathode material from spent LIBs.
Fig. 20 provides a comprehensive overview of the environmental impacts associated with various LIB recycling processes, utilizing a functional unit of 1 kg of recovered Co. The environmental ramifications of these recycling processes vary significantly, as evidenced by the minimum GHG emissions at 1.88 kg CO2eq, the maximum emissions peaking at 152.50 kg CO2eq, and the average emission level of 53.84 kg CO2eq. It is noteworthy that hydrometallurgical processes generally entail the substantial use and generation of acid solutions, thereby resulting in substantial environmental burdens. Conversely, pyrometallurgical processes rely heavily on inert gases, such as argon, leading to adverse effects encompassing eutrophication, ozone depletion, acidification, human carcinogenic toxicity, human noncarcinogenic toxicity, and ecotoxicity. Pyrolysis processes also result in significant environmental impacts due to their energy-intensive nature and the release of volatile organic compounds (VOCs) during thermal decomposition. These VOC emissions give rise to the formation of secondary organic aerosols characterized by small average particle diameters, which can potentially pose respiratory risks to humans upon inhalation. However, when compared to LIBs manufactured from newly mined materials, it is worth noting that hydrometallurgical approaches can yield an approximate reduction of 40% in the overall environmental impact concerning primary energy consumption and greenhouse gas emissions, as reported by Fan et al.215 In contrast, pyrometallurgy achieves a reduction of approximately 20%. These findings underscore the potential environmental benefits of recycling over primary material extraction. Considering total energy consumption, as depicted in Fig. 21, it is estimated that the adoption of direct physical recycling methods can lead to a significant reduction of up to 48% in total energy consumption.216 This reduction can be attributed to the efficient recovery of LiCoO2, copper (Cu), aluminum (Al), anode materials, and electrolytes through direct physical recycling processes. Such methods operate at lower temperatures and do not necessitate the use of additional chemicals. Hydrometallurgy, while more energy-efficient than pyrometallurgy due to its lower operating temperatures, is characterized by complex process steps, extensive reagent consumption, and the generation of substantial wastewater volumes.
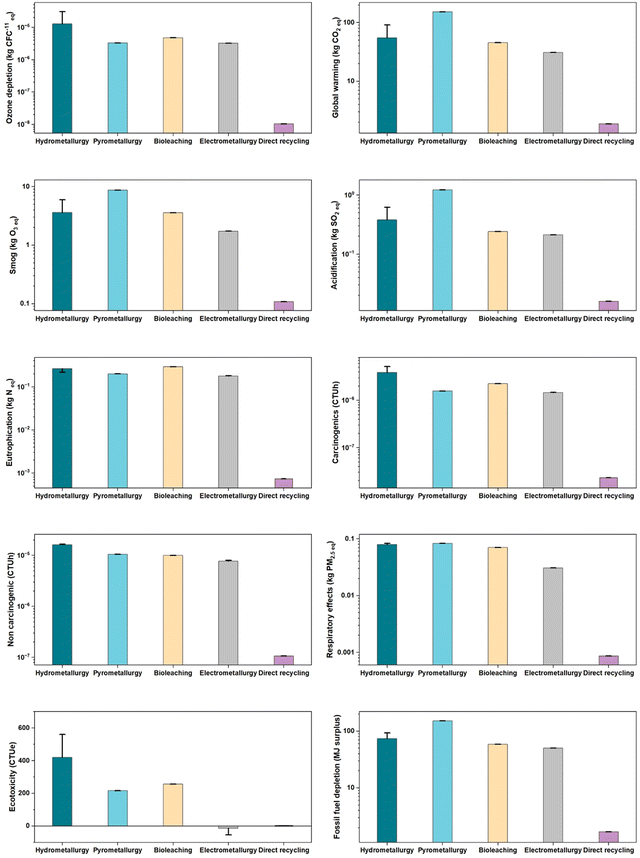 |
| Fig. 20 Environmental impacts of different LCO LIB recycling processes with the functional unit of 1 kg of Co recovered. | |
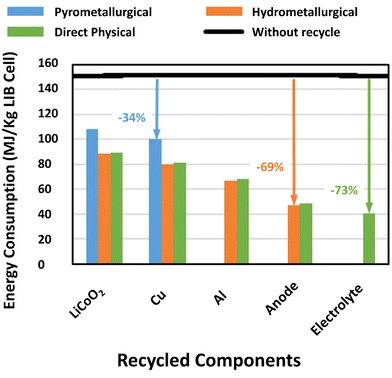 |
| Fig. 21 Reduction in cell production energy by increasing use of recycled materials. Reproduced with permission from ref. 217; Copyright 2018, Elsevier. | |
The utilization of bioleaching and electrochemical processes for the recovery of precious metals from spent LIBs has garnered increasing attention in recent times. Despite this growing interest, there remains a notable dearth of comprehensive LCA studies pertaining to these two recycling techniques. In this context, Alipanah et al. have reported findings suggesting that bioleaching, specifically employing a biolixiviant derived from corn stover by Gluconobacter oxydans bacteria, may offer a more environmentally sustainable approach when compared to alternative hydrometallurgical recovery methods, such as hydrochloric acid leaching. The former exhibited lower GWP per kilogram of recovered cobalt (16–19 kg CO2eq) in contrast to the latter (43–91 kg CO2eq).205 This environmental advantage primarily stems from reduced acid consumption inherent to the bioleaching process, relative to other chemical leaching methods. Conversely, Adhikari et al. reported that electrochemical leaching (ECL) can substantially reduce GWP by 80–87% in comparison to peroxide-based leaching. This reduction is attributed to lower acid consumption, the avoidance of hydrogen peroxide, and the regeneration of the reducing agent iron(II) sulfate.218 Furthermore, ECL exhibits superior performance in terms of CED and water consumption, consuming over 70% less energy and water across all renewable and non-renewable energy categories when compared to peroxide-based leaching. Compared to other emerging technologies like bioleaching or organic acid leaching, which yield carbon footprints ranging from 14–160 kg CO2eq, ECL stands out with a considerably lower value of 1.2–1.7 kg CO2eq. This underscores the superior environmental performance of ECL relative to other leaching methodologies.
It is important to note that LCA studies focusing on the recycling of anode materials, primarily graphite, and electrolytes have been limited. Rey et al. have contributed to this aspect by investigating various graphite recycling processes encompassing hydrometallurgical and pyrometallurgical methods.219 Their findings indicate a range of GWPs from 0.53 to 9.76 kg CO2eq per kilogram of graphite. This analysis unequivocally demonstrates the environmental competitiveness of graphite reclamation approaches when compared to the production of virgin graphite, with GWPs falling within the range of 1 to 5 kg CO2eq per kilogram of graphite.
7.1.3 Impact analysis of individual steps within a recycling process.
The assessment of a specific recycling technology is contingent upon the cumulative effects of all stages within the process. The initial pretreatment stage serves to extract valuable electrode materials from the binder, shell, and current collectors. During pretreatment, substantial energy is consumed directly in the form of electricity and heat, while the escalation of pretreatment steps results in an increased emission of exhaust gases and wastewater.212 Subsequently, various recycling technologies (i.e., pyrometallurgical, hydrometallurgical, bioleaching, and mechanochemical) are employed independently to recover metal products. Finally, the recovered metal products undergo further separation processes, such as precipitation, extraction, or electrochemical deposition, to isolate valuable metals. From the foregoing description, it becomes evident that despite efforts to mitigate the generation of secondary pollution and enhance the overall atomic economy of the recycling process, challenges still persist due to the intricate structure of LIBs and the presence of toxic substances in battery materials. To address these challenges effectively, the focus should shift towards the upstream aspects of battery design. The design of batteries should prioritize the ease of disassembly in packaging and the utilization of safer and less toxic materials. This approach will reduce the complexity of subsequent recycling processes and establish a more environmentally sustainable life cycle for LIBs.220
Numerous LCA studies in the field of LIBs have indicated electricity consumption as a primary environmental hotspot, constituting a substantial portion (e.g., 80% of total GWP) of the associated impacts.219,221 Electricity consumption also emerges as a highly sensitive parameter, with the cost of electricity playing a pivotal role in determining the profitability of the recycling process. The energy and environmental benefits of the recycling of LIBs are intricately linked to the source of electricity. It is imperative for governments to promote renewable energy sources such as photovoltaic, wind power, and biomass energy, as well as stable-output new energy sources to supplant fossil fuels. In addition to electricity, chemicals, such as acids and bases, along with ultrapure water consumption, are identified as the most energy-intensive drivers in hydrometallurgical methods.222 To enhance the sustainability of hydrometallurgical approaches, optimization of acid usage is imperative to mitigate toxicity and address mineral resource scarcity concerns. Furthermore, reducing reaction times and temperatures can effectively lower energy consumption. Pyrometallurgy, reliant on inert gases and often necessitating additional energy input, should consider transitioning to renewable energy sources and optimizing reaction times and temperatures.
In the context of the electrochemical leaching process, sulfuric acid (H2SO4) emerges as the principal environmental contributor, accounting for a substantial portion (38–90%) of the total impact across all environmental categories. Electricity consumption also plays a significant role, contributing between 4% and 46% to the overall impact.218 In bioleaching, electricity utilization in agitated leaching constitutes a predominant contributor, amounting to 80% of the total GWP. Other major contributors include iron sulfate and sodium hydroxide, with respective contributions of 5% and 4% to the total GWP, the latter being used for sodium gluconate production.205 Finally, concerning processes for recycling spent graphite, electricity remains the primary contributor in five out of seven processes, with an average contribution of 69%. When graphite is transformed into graphene oxide, chemicals exert the most substantial influence, contributing an average of 94% to the overall impact.219
7.2 Cost analysis of various recycling technologies
In addition to evaluating environmental trade-offs, the economic impact of the recycling process for spent LIBs is subject to assessment through a life cycle cost (LCC) analysis. This economic evaluation is crucial in determining the feasibility of LIB recycling and is a key consideration for industry stakeholders when designing recycling strategies. The profitability of a recycling process is contingent upon two fundamental factors: the revenue it generates and the costs it incurs, as expressed by eqn (80).210where E is the profit, R is the revenues generated from products, and CT is the total cost of the recycling process, encompassing collection and transportation expenses, water and chemical consumption, electric power usage, equipment depreciation, equipment maintenance, and labor costs.
Recycling inherently involves substantial costs due to the multi-stage operations ranging from waste collection to processing. Currently, the availability of data for production cost analysis is limited, primarily due to the relatively small-scale operations and the nascent stage of LIB recycling, resulting in a scarcity of economic data. However, several researchers have conducted economic analyses of spent LCO LIB recycling, demonstrating positive net income.220,223 For instance, a rough estimation of the profit gained from recycling 1 ton of spent LCO powders is approximately $28016.2, whether using pyrometallurgy or hydrometallurgy.215 In the case of recycling 1 kg of the main product cobalt through a hydrometallurgical process, it could yield a net income of up to $27.70. However, this net income decreases to $1.10 when the process includes co-product recycling.210 Furthermore, Alipanah et al. estimated a potential average profit margin ranging from 17% to 26% for processing 10
000 tons of black mass per year using the bioleaching process.205 The presence of positive net profit underscores the economic viability of deploying recycling technologies at scale. Such economic feasibility plays a pivotal role in enhancing the LIB recycling rate, which is currently estimated at only 5% globally.224 By addressing economic barriers, it becomes feasible to increase the recycling rate, thereby promoting sustainability in the LIB industry.
Yang et al. conducted a comparative analysis of revenue generation in processing 10
000 metric tonnes of spent LIBs with the same chemistry using various processing technologies (Fig. 22a).220 Notably, LIBs with LCO chemistry yielded the highest revenue, surpassing that of lithium iron phosphate (LFP) and lithium manganese oxide (LMO) chemistries by up to 7 and 10 times, respectively. This stark contrast arises from the elevated price of cobalt, while LFP and LMO chemistries generated lower revenues due to the comparatively lower market prices of their constituent elements such as iron, phosphate, and manganese.220,223 Furthermore, among various recycling processes, the direct regeneration of cathode materials consistently emerged as the highest revenue-generating method as compared to pyrometallurgy and hydrometallurgy for all battery chemistries. It is worth noting that despite the criticism directed towards hydrometallurgical processes for their complexity, they consistently outperformed pyrometallurgical methods in terms of revenue. This is primarily attributable to the higher purity of materials recovered and the larger quantity of materials amenable to recycling in hydrometallurgy.
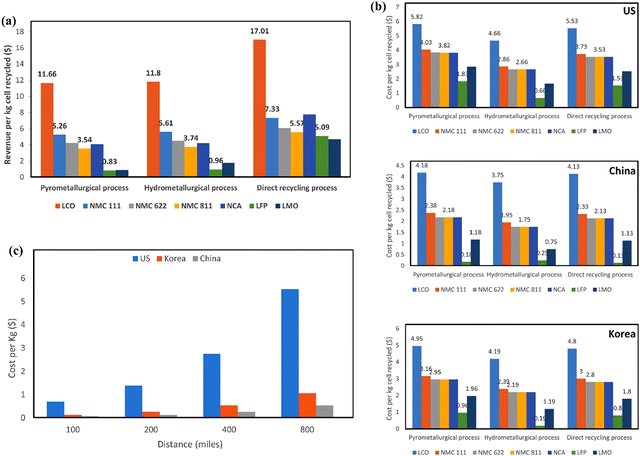 |
| Fig. 22 (a) Revenue generated per kg cell recycled; (b) cost per kg cell recycled in the US, China and South Korea; and (c) collection and transport costs for spent LIBs. Reproduced with permission from ref. 220; Copyright 2021, Elsevier. | |
The revenue generated from LIB recycling remains relatively uniform on a global scale, largely regulated by the sale of recovered materials. However, the associated costs can exhibit substantial variation depending on the location of the recycling processing plant (Fig. 22b). Yang et al. reported that recycling batteries in the United States is more expensive compared to that in China and South Korea, irrespective of the technologies employed or the battery chemistries.220 These cost disparities mainly stem from differences in labor costs and the capital investment required for establishing processing plants. Hydrometallurgical processes consistently demonstrate lower costs, ranging from $3.75 to $4.66 per kg cell recycled, despite their more extensive number of processing steps. Notably, the preprocessing and extraction phase dominates the total cost structure (Fig. 23).210 Conversely, pyrometallurgical processes face challenges associated with high initial investments, ongoing operating expenses, and substantial costs related to waste gas treatment. Direct recycling tends to exhibit lower expenses for energy and reagents, coupled with reduced fixed facility costs compared to alternative methods. In the case of bioleaching, the total cost typically falls within the range of $20 to $24 per kg of recovered cobalt.205 The primary contributors to material expenses include the purchasing cost of LIBs' black mass (accounting for 36% of the total cost) and iron sulfate (comprising 10% of the total cost). Direct recycling necessitates that LIBs are in good condition for recycling, which mandates manual classification and disassembly, significantly contributing to the overall cost. The standardization of LIB design and labeling for common applications could play a crucial role in enhancing the economic feasibility of direct recycling and reducing the overall environmental costs associated with LIB recycling.
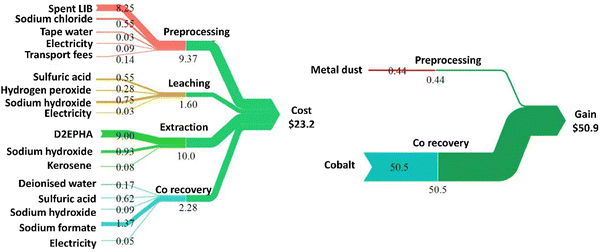 |
| Fig. 23 Economic cost and gain breakdown for spent LIB recycling with hydrometallurgy. Reproduced with permission from ref. 210; Copyright 2023, Elsevier. | |
Fig. 22c illustrates the costs associated with the collection and transportation of spent LIBs in the United States, China, and South Korea. These calculations are based on the use of a 25-ton heavy-duty truck for transporting spent batteries as hazardous waste from collection points to processing plants.220 Transport costs increase linearly with distance, and in the United States, they are five and ten times higher than those in South Korea and China, respectively. Labor costs significantly contribute to these differences, and variations in transport requirements further contribute to these disparities across countries. Regardless of the specific causes, it is evident that the profitability of LIB recycling hinges greatly on transport costs. Efforts to mitigate transport costs, such as mass transportation via rail and transporting only the active cathode materials from collection sites to processing centers, along with government policies that provide financial incentives, hold the potential to enhance profitability and the overall outcome of LIB recycling processes. The limited number of commercial-scale processing facilities for recycled LIBs worldwide underscores the need for concerted efforts to improve the commercial feasibility of LIB recycling.
7.3 Comparison of different LIB recycling technologies
Fig. 24 provides a comprehensive summary of recycling technologies for LCO LIBs. Each of these recycling methods offers distinct advantages and limitations (Table S2, ESI†). Pyrometallurgical methods boast high technical maturity and involve relatively straightforward processes that do not necessitate intensive sorting and pretreatment of spent LIBs. Consequently, pyrometallurgy has been adopted by several industrial companies. However, it has a limited capacity to recover specific metals (e.g., Co, Ni, and Fe). This approach also involves the incineration of plastics and toxic electrolytes, raising concerns about its environmental impacts. Pyrometallurgy is characterized by high energy consumption and substantial costs associated with toxic emission control. Regarding hydrometallurgy, this method enables the recovery of nearly all battery compositions with relatively high purity. Compared to pyrometallurgy, hydrometallurgy is less energy intensive. Nevertheless, it involves a series of intricate chemical processes utilizing highly corrosive chemicals, such as strong inorganic acids known for their high leaching efficiency and cost-effectiveness. This method generates significant quantities of toxic gases, landfill waste, and acidified wastewater. Currently, leaching with organic acids is of particular interest within hydrometallurgical approaches due to its environmental friendliness and considerable leaching efficiency, stemming from the reducibility and chelating properties of organic acids. However, challenges persist, including the relatively high cost, slow leaching rates, and limited capacity for widespread industrial implementation.
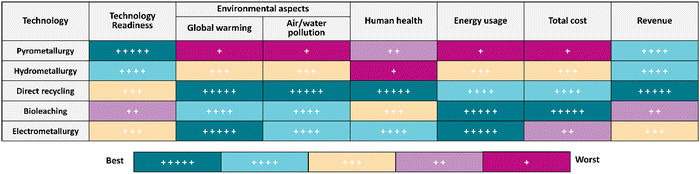 |
| Fig. 24 Comparison of different LIB recycling methods. | |
LCA and LCC analyses have suggested that direct recycling holds the potential for both economic benefits and reductions in greenhouse gas emissions. This is attributed to its low-temperature and low-energy processing compared to pyrometallurgical and hydrometallurgical processes. Nonetheless, several challenges hinder its widespread adoption, including the requirement for pre-sorting, an increased number of separation processes, and specific input material requirements, such as single material recovery and stringent degradation conditions. Currently, direct recycling remains largely at the laboratory scale. Bioleaching, while characterized by low energy consumption and favorable environmental attributes, faces limitations such as slow leaching kinetics and high potential for contamination, which restrict its practical use in industrial settings. And lastly, electrometallurgy has garnered increasing attention as an alternative method for recovering precious metals from spent LIBs. Its advantages include fast processing times, high recovery rates, and versatility in adjusting processing parameters. However, electricity consumption introduces complexity to the economic feasibility of these processes. The cost of electricity becomes a critical factor influencing profitability, and the source of electricity significantly impacts the environmental footprint of electrometallurgical methods. To enhance sustainability, it is essential to efficiently harness alternative energy sources such as solar and wind for the electrochemical metal extraction process.
7.4 Perspectives
As of now, industrial-scale recycling primarily relies on pyrometallurgy and hydrometallurgy methods, while technologies such as biohydrometallurgy, electrometallurgy, and direct recycling have not yet been widely implemented in the spent battery recovery industry, with their TRL remaining below 6.225–227 Moreover, there is a notable absence of comprehensive environmental and economic analyses regarding the cost-to-income ratios of these emerging technologies. From a sustainability standpoint, numerous cradle-to-gate assessments focusing on LIBs consistently reveal that the most significant environmental impacts and costs occur during the raw material phase. This phase encompasses activities such as materials extraction, transportation, purification, and other related processing stages. This underscores the substantial benefits, both environmentally and economically, which could be derived from closed-loop recycling practices, even though specific results may vary among different research groups. The observed variability can be attributed to variations in system boundaries, functional units, impact models, allocation criteria, and the absence of reliable data on life cycle inventories. Therefore, it is imperative to establish transparency and uniformity in LCA and LCC analyses related to LIB recycling. Systematic evaluations of existing methods under standardized conditions would facilitate cross-comparisons of the various spent LIB techniques available in the market. While energy consumption and GHG emissions currently serve as the primary assessment indicators for battery recycling, it is crucial not to overlook other relevant indicators that should be selectively assessed based on the study's specific objectives. To obtain more reliable results, there is an urgent need to update and refine data pertaining to both LIB production and recycling. Continued attention to advancements in this area and the establishment of an assessment model for economic evaluations applicable to diverse recovery technologies are vital for progress in LIB recycling. In terms of novel LIB design, the objective is to optimize these batteries for easy disassembly, part segregation, electrode material separation, and component sorting. Achieving this goal requires a sophisticated approach that integrates automated dismantling, intelligent separation techniques, and advanced characterization methods. Ongoing efforts are dedicated to reducing costs, process durations, environmental impacts, and ultimately making these processes economically viable for widespread adoption.
8. Conclusions and outlook
The key findings of our review are listed below here.
• The direct recycling process is a short recovery route in which practically all components of spent batteries including cathodes, anodes and aluminium foil can be recovered. However, the process is still in its infancy and the regeneration process is not well developed yet. Additionally, the recycled materials may not perform like the original virgin materials.
• Pyrometallurgical and hydrometallurgical processes have been developed for the recycling of spent LIBs across Pyro 1.0 to Pyro 4.0 and Hydro 1.0 to Hydro 4.0, respectively. The high efficiency and practical applicability of metallurgical (i.e., pyrometallurgy and hydrometallurgy) techniques employed for recycling spent LIBs led to the development of large-scale processes and commercial applications. However, the environmental impacts associated with these metallurgical processes have received increasing attention due to the emission of hazardous pollutants, urging the development of closed-loop recycling as a sustainable strategy in Pyro 4.0 and Hydro 4.0. Accordingly, optimized operational parameters have been developed to recycle cathodes, anodes, binders, separators, and electrolytes while using the pyrometallurgical and hydrometallurgical processes. By making use of advanced characterization tools, it is possible to gain insights into thermodynamic and kinetic aspects of recycling processes. This knowledge will in turn provide a better understanding of the mechanisms involved in the recycling process and promote the development of the next-generation sustainable recycling technologies involving pyrometallurgical and hydrometallurgical processes. Notably, during the current transition stage, the integration of pyrometallurgical and hydrometallurgical processes with developed technologies (e.g., microwave heating, Joule heating, hydrothermal treatment, bioleaching, and electrometallurgy) has great potential for the effective recycling of spent LIBs.
• Biohydrometallurgy (bioleaching) uses microbial agents such as acidophilic bacteria (IOB and SOB) and fungus (e.g., Aspergillus niger) for dissolution of critical elements such as Co and Li from the spent LIBs. Bioleaching is an environmentally benign as well as low-cost and low-energy requirement process. Nonetheless, the bioleaching technology is still in the laboratory-scale and suffers a slow metal dissolution kinetics.
• The electrometallurgical process uses electrical energy for solubilization of metals by the electrolysis. In this process, in situ generated electrons act as green agents (e.g. oxidizing and reducing agents) for the extraction of metals from the spent batteries through numerous electrochemical reactions. Additionally, critical metals such as Co, Cu and Mn can be recovered as solid products by the electrodeposition method. The process is selective and produces a high purity grade metal. However, appropriate equipment is required to improve the process efficiency that is impacted by the presence of impurities.
• From the perspective of sustainability, a number of LCA- and LCC-based studies have been conducted on LCO-based cathode LIBs. Energy consumption and greenhouse gas emissions are most frequently evaluated among different environmental impacts of LIB recycling. Our review of key publications pertaining to the LCA studies reveals that the raw material phase of LIBs' life cycle constitutes the primary source of environmental impacts, emphasizing the important role of recycling in reducing these environmental burdens and promoting sustainability. Moreover, a comparative analysis of environmental impacts across various LIB recycling technologies including hydrometallurgy, pyrometallurgy, bioleaching, electrochemical and direct recycling processes, highlights distinct variations in their environmental impacts. This review also provides insights into the economic feasibility of LIB recycling, demonstrating the potential for positive net income, while acknowledging regional disparities in LCC, influenced by factors such as labor costs and capital investments.
The significant knowledge gaps related to the various aspects of pre-treatments and recycling of spent LIBs including the sustainability assessment of different recycling methods are outlined in the respective sections. Herein, additional knowledge gaps which should be considered in future works for development of a high efficiency and sustainable recycling technology are highlighted.
• At present, the efficient recycling of spent LIBs remains a challenge due to logistical complexities, regulatory uncertainties, and evolving recycling methods. To improve recycling rates and reduce environmental impacts, effective collection and disposal systems, supported by robust regulations, are essential. Government incentives and legislative pressures encourage investments in the development of innovative recycling of LIBs, while comprehensive regulations would cover all aspects of the recycling process including its safety. Furthermore, standardized environmental and economic assessment of end-of-life LIBs could facilitate the global adoption of recycled materials.
• The critical metals such as Co and Li used for the synthesis of LIBs are usually mined from natural resources, but are mainly present in a specific country/region. The sustained supply of these critical elements may be disrupted due to many reasons including geopolitical conflicts. Therefore, research and development should be carried out for the synthesis of LIBs using other metals/materials, followed by in-depth investigations about the safety and reliable performance of LIBs during their long-term operations.
• To achieve sustainability in the LIB technology and keep up with the rapid progress in the energy sector, innovative cathode materials, anode materials, and/or electrolytes have been developed to increase the energy density of LIBs. Thus, the LIB technology is being upgraded regularly which indicates that the quantity and quality of spent LIBs to be recycled would change in future. Therefore, pre-treatment processes and recycling technologies should be modified and upgraded for efficient management of spent LIBs having complex characteristics.
• Biological processes (e.g., bioleaching) are usually environmentally benign and cost-effective due to the use of naturally abundant microorganisms and limited consumption of chemical reagents. To overcome the slow kinetic nature of the bioleaching process, more works are needed to develop innovative methods with the application of green catalysts with regeneration potential for continued use in the long-term recycling of spent LIBs.
• The recycling of spent LIBs at present is mainly focused on the recovery of valuable metals from cathode materials. As a consequence, limited information is available on the potential recycling of other components of spent LIBs (e.g., graphite in anodes, as well as Cu and Al used as the current collectors in anodes and cathodes, respectively), especially using the bioleaching method.
• Most of the recent works have evaluated the techno-economic performance of an individual spent LIB recycling technology. In-depth experimental investigations and the analysis of the benefits-to-costs ratio as well as environmental impact assessments are needed on the recycling of spent LIBs using an integrated/hybrid technology (e.g., the integrated chemical–biological method).
In view of environmental, ecological and public health risks associated with the recycling of spent LIBs, the incorporation of automation-based technologies into different stages of the recycling processes including pre-treatments (e.g., automated sorting and dismantling) could minimize the occurrence of any negative consequences and at the same time enhance the efficiency of the recycling process.
Abbreviations
Abbreviation definition
Al | Aluminum |
BEVs | Battery electric vehicles |
C6 | Graphite |
CaF2 | Calcium fluoride |
CaO | Calcium oxide |
CED | Cumulative energy demand |
Co | Cobalt |
CO | Carbon monoxide |
CO2eq | Carbon dioxide equivalent |
CoO | Cobalt(II) oxide |
CT | Total cost |
Cu | Copper |
DEC | Diethyl carbonate |
DESs | Deep eutectic solvents |
DMC | Dimethyl carbonate |
E | Profit |
EC | Ethylene carbonate |
ECL | Electrochemical leaching |
EMC | Ethyl methyl carbonate |
EU | European union |
EV | Electric vehicles |
Fe | Iron |
FeSO4 | Ferrous sulfate |
g-C3N4 | Polymeric carbon nitride |
GHG | Greenhouse gas |
GW h | Gigawatt hours |
GWP | Global warming potential |
H2O2 | Hydrogen peroxide |
H2SO4 | Sulfuric acid |
HEVs | Hybrid electric vehicles |
HF | Hydrogen fluoride |
IEA | International energy agency |
ILs | Ionic liquids |
IOB | Iron-oxidizing bacteria |
LAN | LiOAc-LiNO3 |
LCA | Life cycle assessments |
LCC | Life cycle cost |
LCO | Lithium cobalt oxide, LiCoO2 |
LFP | Lithium iron phosphate, LiFePO4 |
Li | Lithium |
Li2CO3 | Lithium carbonate |
LIBs | Lithium-ion batteries |
LiPF6 | Lithium hexafluorophosphate |
LMO | Lithium manganese oxide, LiMn2O4 |
LMP | Lithium permanganate, LiMnPO4 |
Mn | Manganese |
Na2CO3 | Sodium carbonate |
NaCl | Sodium chloride |
NaOH | Sodium hydroxide |
NCA | LiNixCoyAlzO2 |
NH4Cl | Ammonium chloride |
NH4OH | Ammonium hydroxide |
Ni | Nickel |
NMCs | LiNixCoyMn1−x−yO2 |
OAR | Organic aqua regia |
PC | Propylene carbonate |
PE | Polyethylene |
PFAS | Per- and polyfluoroalkyl substances |
PPE | Polypropylene |
PTFE | Polytetrafluoroethylene |
PVDF | Poly(vinylidene fluoride) |
R | Revenues generated from products |
RCF | Refractory ceramic mineral fibers |
S0 | Sulfur |
SHE | Standard hydrogen electrode |
SO2 | Sulfur dioxide |
SOB | Sulfur oxidizing bacteria |
TCLP | Toxicity characteristic leaching procedure |
TFE | Tetrafluoroethylene |
TRL | Technological readiness level |
TW h | Terawatt-hour |
VOCs | Volatile organic compounds |
Conflicts of interest
There are no conflicts to declare.
Acknowledgements
The Senior Research Fellow appointment of Basanta K. Biswal was supported by the National Research Foundation (NRF), Singapore, and Ministry of National Development (MND), Singapore, under its Cities of Tomorrow R&D Programme (CoT Award COT-V4-2019-6). B. Zhang thanks the assistance from Manabu Fujii and Toshihiro Isobe.
References
- X. Wu, J. Ma, J. Wang, X. Zhang, G. Zhou and Z. Liang, Glob. Challenges, 2022, 6, 2200067 CrossRef PubMed.
- B. Zhang, Y. Xu, B. Makuza, F. Zhu, H. Wang, N. Hong, Z. Long, W. Deng, G. Zou, H. Hou and X. Ji, Chem. Eng. J., 2023, 452, 139258 CrossRef CAS.
- IEA, IEA, Global energy investment in clean energy and in fossil fuels, 2015-2023, IEA, Paris https://www.iea.org/data-and-statistics/charts/global-energy-investment-in-clean-energy-and-in-fossil-fuels-2015-2023.
- F. Wu, J. Maier and Y. Yu, Chem. Soc. Rev., 2020, 49, 1569–1614 RSC.
- Y. Li, J. Yang and J. Song, Renewable Sustainable Energy Rev., 2017, 79, 1503–1512 CrossRef.
- W. Cao, J. Zhang and H. Li, Energy Storage Mater., 2020, 26, 46–55 CrossRef.
- IEA, IEA, Global electric passenger car stock, 2010-2020, IEA, Paris https://www.iea.org/data-and-statistics/charts/global-electric-passenger-car-stock-2010-2020.
- IEA, IEA, Lithium-ion battery manufacturing capacity, 2022-2030, IEA, Paris https://www.iea.org/data-and-statistics/charts/lithium-ion-battery-manufacturing-capacity-2022-2030.
- IEA, IEA, Global electric vehicle stock by region, 2010-2020, IEA, Paris https://www.iea.org/data-and-statistics/charts/global-electric-vehicle-stock-by-region-2010-2020, IEA.
- T. Or, S. W. D. Gourley, K. Kaliyappan, A. Yu and Z. Chen, Carbon Energy, 2020, 2, 6–43 CrossRef CAS.
- Y. Miao, L. Liu, Y. Zhang, Q. Tan and J. Li, J. Hazard. Mater., 2022, 425, 127900 CrossRef CAS PubMed.
- C. Shen and H. Wang, J. Phys. Conf. Ser., 2019, 1347, 12087 CrossRef CAS.
- J.-M. Tarascon and M. Armand, Nature, 2001, 414, 359–367 CrossRef CAS PubMed.
- X. Zheng, Z. Zhu, X. Lin, Y. Zhang, Y. He, H. Cao and Z. Sun, Engineering, 2018, 4, 361–370 CrossRef CAS.
- Y. Chen, Y. Kang, Y. Zhao, L. Wang, J. Liu, Y. Li, Z. Liang, X. He, X. Li, N. Tavajohi and B. Li, J. Energy Chem., 2021, 59, 83–99 CrossRef CAS.
- G. Harper, R. Sommerville, E. Kendrick, L. Driscoll, P. Slater, R. Stolkin, A. Walton, P. Christensen, O. Heidrich, S. Lambert, A. Abbott, K. Ryder, L. Gaines and P. Anderson, Nature, 2019, 575, 75–86 CrossRef CAS PubMed.
- T. Raj, K. Chandrasekhar, A. N. Kumar, P. Sharma, A. Pandey, M. Jang, B.-H. Jeon, S. Varjani and S.-H. Kim, J. Hazard. Mater., 2022, 429, 128312 CrossRef CAS PubMed.
- W. Zhang, C. Xu, W. He, G. Li and J. Huang, Waste Manage. Res., 2018, 36, 99–112 CrossRef CAS PubMed.
- W. Mrozik, M. A. Rajaeifar, O. Heidrich and P. Christensen, Energy Environ. Sci., 2021, 14, 6099–6121 RSC.
- X. Zeng, J. Li and L. Liu, Renewable Sustainable Energy Rev., 2015, 52, 1759–1767 CrossRef CAS.
- W. Mrozik, M. A. Rajaeifar, O. Heidrich and P. Christensen, Energy Environ. Sci., 2021, 14, 6099–6121 RSC.
- X. Lai, Y. Huang, H. Gu, C. Deng, X. Han, X. Feng and Y. Zheng, Energy Storage Mater., 2021, 40, 96–123 CrossRef.
- M. Iturrondobeitia, C. Vallejo, M. Berroci, O. Akizu-Gardoki, R. Minguez and E. Lizundia, ACS Sustainable Chem. Eng., 2022, 10, 9798–9810 CrossRef CAS.
- P. Zhu, Z. Jiang, W. Sun, Y. Yang, D. S. Silvester, H. Hou, C. E. Banks, J. Hu and X. Ji, Energy Environ. Sci., 2023, 16, 3564–3575 RSC.
- M. Chen, X. Ma, B. Chen, R. Arsenault, P. Karlson, N. Simon and Y. Wang, Joule, 2019, 3, 2622–2646 CrossRef CAS.
- Y. Hua, S. Zhou, Y. Huang, X. Liu, H. Ling, X. Zhou, C. Zhang and S. Yang, J. Power Sources, 2020, 478, 228753 CrossRef CAS.
- Y. Ji, E. E. Kpodzro, C. T. Jafvert and F. Zhao, Clean Technol. Recycl., 2021, 1, 124–151 Search PubMed.
- J. Wu, M. Zheng, T. Liu, Y. Wang, Y. Liu, J. Nai, L. Zhang, S. Zhang and X. Tao, Energy Storage Mater., 2023, 54, 120–134 CrossRef.
- M. Zhou, B. Li, J. Li and Z. Xu, ACS ES&T Eng, 2021, 1, 1369–1382 Search PubMed.
- B. Makuza, Q. Tian, X. Guo, K. Chattopadhyay and D. Yu, J. Power Sources, 2021, 491, 229622 CrossRef CAS.
- J. C.-Y. Jung, P.-C. Sui and J. Zhang, J. Energy Storage, 2021, 35, 102217 CrossRef.
- Y. Yao, M. Zhu, Z. Zhao, B. Tong, Y. Fan and Z. Hua, ACS Sustainable Chem. Eng., 2018, 6, 13611–13627 CrossRef CAS.
- A. Chagnes and B. Pospiech, J. Chem. Technol. Biotechnol., 2013, 88, 1191–1199 CrossRef CAS.
- E. A. Dalini, G. Karimi, S. Zandevakili and M. Goodarzi, Miner. Process. Extr. Metall. Rev., 2021, 42, 451–472 CrossRef.
- J. J. Roy, B. Cao and S. Madhavi, Chemosphere, 2021, 282, 130944 CrossRef CAS PubMed.
- B. K. Biswal and R. Balasubramanian, Front. Microbiol., 2023, 14, 1197081 CrossRef PubMed.
- M. Sethurajan and S. Gaydardzhiev, Resour. Conserv. Recycl., 2021, 165, 105225 CrossRef CAS.
- P. Moazzam, Y. Boroumand, P. Rabiei, S. S. Baghbaderani, P. Mokarian, F. Mohagheghian, L. J. Mohammed and A. Razmjou, Chemosphere, 2021, 277, 130196 CrossRef CAS PubMed.
- X. Zhang, L. Li, E. Fan, Q. Xue, Y. Bian, F. Wu and R. Chen, Chem. Soc. Rev., 2018, 47, 7239–7302 RSC.
- K. Du, E. H. Ang, X. Wu and Y. Liu, Energy Environ. Mater., 2022, 5, 1012–1036 CrossRef CAS.
- Y. Li, W. Lv, H. Huang, W. Yan, X. Li, P. Ning, H. Cao and Z. Sun, Green Chem., 2021, 23, 6139–6171 RSC.
- R. Rautela, B. R. Yadav and S. Kumar, J. Power Sources, 2023, 580, 233428 CrossRef CAS.
- P. Li, S. Luo, L. Zhang, Q. Liu, Y. Wang, Y. Lin, C. Xu, J. Guo, P. Cheali and X. Xia, J. Energy Chem., 2024, 89, 144–171 CrossRef CAS.
- Z. Dobó, T. Dinh and T. Kulcsár, Energy Rep., 2023, 9, 6362–6395 CrossRef.
- Y. Guo, C. Guo, P. Huang, Q. Han, F. Wang, H. Zhang, H. Liu, Y.-C. Cao, Y. Yao and Y. Huang, eScience, 2023, 3, 100091 CrossRef.
- V. Gupta, X. Yu, H. Gao, C. Brooks, W. Li and Z. Chen, Adv. Energy Mater., 2023, 13, 2203093 CrossRef CAS.
- J. Neumann, M. Petranikova, M. Meeus, J. D. Gamarra, R. Younesi, M. Winter and S. Nowak, Adv. Energy Mater., 2022, 12, 2102917 CrossRef CAS.
- Y. Bai, N. Muralidharan, Y.-K. Sun, S. Passerini, M. Stanley Whittingham and I. Belharouak, Mater. Today, 2020, 41, 304–315 CrossRef CAS.
- H. Ali, H. A. Khan and M. Pecht, Renewable Sustainable Energy Rev., 2022, 168, 112809 CrossRef CAS.
- G. Ji, J. Wang, Z. Liang, K. Jia, J. Ma, Z. Zhuang, G. Zhou and H.-M. Cheng, Nat. Commun., 2023, 14, 584 CrossRef CAS PubMed.
- P. Xu, D. H. S. Tan, B. Jiao, H. Gao, X. Yu and Z. Chen, Adv. Funct. Mater., 2023, 33, 2213168 CrossRef CAS.
- A. A. Pavlovskii, K. Pushnitsa, A. Kosenko, P. Novikov and A. A. Popovich, Inorganics, 2022, 10, 141 CrossRef CAS.
- Y. Zhao, X. Yuan, L. Jiang, J. Wen, H. Wang, R. Guan, J. Zhang and G. Zeng, Chem. Eng. J., 2020, 383, 123089 CrossRef CAS.
- S. Zhou, Z. Fei, Q. Meng, P. Dong, Y. Zhang and M. Zhang, ACS Appl. Energy Mater., 2021, 4, 12677–12687 CrossRef CAS.
- Y. Liu, H. Yu, Y. Wang, D. Tang, W. Qiu, W. Li and J. Li, Waste Manage., 2022, 143, 186–194 CrossRef CAS PubMed.
- X. Chen, C. Yang, Y. Yang, H. Ji and G. Yang, J. Alloys Compd., 2022, 909, 164691 CrossRef CAS.
- C. K. Lee and K.-I. Rhee, J. Power Sources, 2002, 109, 17–21 CrossRef CAS.
- C. Yang, J. Zhang, Q. Jing, Y. Liu, Y. Chen and C. Wang, Int. J. Miner. Metall. Mater., 2021, 28, 1478–1487 CrossRef CAS.
- C. Yi, L. Zhou, X. Wu, W. Sun, L. Yi and Y. Yang, Chin. J. Chem. Eng., 2021, 39, 37–50 CrossRef CAS.
- B. Markey, M. Zhang, I. Robb, P. Xu, H. Gao, D. Zhang, J. Holoubek, D. Xia, Y. Zhao, J. Guo, M. Cai, Y. S. Meng and Z. Chen, J. Electrochem. Soc., 2020, 167, 160511 CrossRef CAS.
- Y. Xiao, J. Li, W. Huang, L. Wang and J. Luo, J. Mater. Sci. Mater. Electron., 2022, 33, 16740–16752 CrossRef CAS.
- M. Zhou, B. Li, J. Li and Z. Xu, ACS ES&T Eng, 2021, 1, 1369–1382 Search PubMed.
- Y. Li, W. Lv, H. Huang, W. Yan, X. Li, P. Ning, H. Cao and Z. Sun, Green Chem., 2021, 23, 6139–6171 RSC.
- G. Harper, R. Sommerville, E. Kendrick, L. Driscoll, P. Slater, R. Stolkin, A. Walton, P. Christensen, O. Heidrich, S. Lambert, A. Abbott, K. Ryder, L. Gaines and P. Anderson, Nature, 2019, 575, 75–86 CrossRef CAS PubMed.
- J. Li, G. Wang and Z. Xu, J. Hazard. Mater., 2016, 302, 97–104 CrossRef CAS PubMed.
- J. K. Mao, J. Li and Z. Xu, J. Cleaner Prod., 2018, 205, 923–929 CrossRef CAS.
- J. Li, Y. Lai, X. Zhu, Q. Liao, A. Xia, Y. Huang and X. Zhu, J. Hazard. Mater., 2020, 398, 122955 CrossRef CAS PubMed.
- W. Hou, X. Huang, R. Tang, Y. Min, Q. Xu, Z. Hu and P. Shi, Waste Manage., 2023, 155, 129–136 CrossRef CAS PubMed.
- F. Zhou, X. Li, S. Wang, X. Qu, J. Zhao, D. Wang, Z. Chen and H. Yin, J. Hazard. Mater., 2023, 459, 132150 CrossRef CAS PubMed.
- X. Zhu, Y. Li, M. Gong, R. Mo, S. Luo, X. Yan and S. Yang, Angew. Chem., Int. Ed., 2023, 62, 1–7 Search PubMed.
- J. Li, Y. Lai, X. Zhu, Q. Liao, A. Xia, Y. Huang and X. Zhu, J. Hazard. Mater., 2020, 398, 122955 CrossRef CAS PubMed.
- G. Qu, Y. Wei, C. Liu, S. Yao, S. Zhou and B. Li, Waste Manage., 2022, 150, 66–74 CrossRef CAS PubMed.
- W. Wang, Y. Zhang, X. Liu and S. Xu, ACS Sustainable Chem. Eng., 2019, 7, 12222–12230 CAS.
- D. Wang, X. Zhang, H. Chen and J. Sun, Miner. Eng., 2018, 126, 28–35 CrossRef CAS.
- J. Lin, C. Liu, H. Cao, R. Chen, Y. Yang, L. Li and Z. Sun, Green Chem., 2019, 21, 5904–5913 RSC.
- G. Qu, B. Li and Y. Wei, Chem. Eng. J., 2023, 451, 138897 CrossRef CAS.
- J. Xiao, B. Niu and Z. Xu, J. Cleaner Prod., 2020, 277, 122718 CrossRef CAS.
- X. Qu, H. Xie, X. Chen, Y. Tang, B. Zhang, P. Xing and H. Yin, ACS Sustainable Chem. Eng., 2020, 8, 6524–6532 CrossRef CAS.
- J. Xiao, B. Niu, Q. Song, L. Zhan and Z. Xu, J. Hazard. Mater., 2021, 404, 123947 CrossRef CAS PubMed.
- C. Peng, F. Liu, Z. Wang, B. P. Wilson and M. Lundström, J. Power Sources, 2019, 415, 179–188 CrossRef CAS.
- Y.-C. Yin, C. Li, X. Hu, D. Zuo, L. Yang, L. Zhou, J. Yang and J. Wan, ACS Energy Lett., 2023, 8, 3005–3012 CrossRef CAS.
- B. Niu, J. Xiao and Z. Xu, J. Hazard. Mater., 2022, 439, 129678 CrossRef CAS PubMed.
- F. Arshad, L. Li, K. Amin, E. Fan, N. Manurkar, A. Ahmad, J. Yang, F. Wu and R. Chen, ACS Sustainable Chem. Eng., 2020, 8, 13527–13554 CrossRef CAS.
- B. Niu, J. Xiao and Z. Xu, J. Hazard. Mater., 2022, 439, 129678 CrossRef CAS PubMed.
- H. Yu, H. Dai, Y. Zhu, H. Hu, R. Zhao, B. Wu and D. Chen, J. Power Sources, 2021, 481, 229159 CrossRef CAS.
- H. Yu, H. Dai, Y. Zhu, H. Hu, R. Zhao, B. Wu and D. Chen, J. Power Sources, 2021, 481, 229159 CrossRef CAS.
- C. Yi, Y. Yang, T. Zhang, X. Wu, W. Sun and L. Yi, J. Clean. Prod., 2020, 277, 123585 CrossRef CAS.
- H. D. Pham, M. Horn, J. F. S. Fernando, R. Patil, M. Phadatare, D. Golberg, H. Olin and D. P. Dubal, Sustainable Mater. Technol., 2020, 26, e00230 CrossRef CAS.
- C. Xu, G. Ma, W. Yang, S. Che, Y. Li, Y. Jia, H. Liu, F. Chen, G. Zhang, H. Liu, N. Wu, G. Huang and Y. Li, Electrochim. Acta, 2022, 415, 1–9 CrossRef.
- M. Wang, K. Liu, J. Yu, Q. Zhang, Y. Zhang, M. Valix and D. C. W. Tsang, Glob. Challenges, 2023, 7, 2200237 CrossRef PubMed.
- M. Wang, Q. Tan, L. Liu and J. Li, ACS Sustainable Chem. Eng., 2019, 7, 12799–12806 CrossRef CAS.
- Y. Ji, C. T. Jafvert, N. N. Zyaykina and F. Zhao, J. Cleaner Prod., 2022, 367, 133112 CrossRef CAS.
- J. A. Conesa and R. Font, Polym. Eng. Sci., 2001, 41, 2137–2147 CrossRef CAS.
- A. Rensmo, E. K. Savvidou, I. T. Cousins, X. Hu, S. Schellenberger and J. P. Benskin, Environ. Sci. Process. Impacts, 2023, 1015–1030 RSC.
- J. Wang, Z. Lin, X. He, M. Song, P. Westerhoff, K. Doudrick and D. Hanigan, Environ. Sci. Technol., 2022, 56, 5355–5370 CrossRef CAS PubMed.
- J. A. Conesa, A. Marcilla, R. Font and J. A. Caballero, J. Anal. Appl. Pyrolysis, 1996, 36, 1–15 CrossRef CAS.
- E. Dümichen, A. K. Barthel, U. Braun, C. G. Bannick, K. Brand, M. Jekel and R. Senz, Water Res., 2015, 85, 451–457 CrossRef PubMed.
- J. Nisar, M. A. Khan, M. Iqbal, A. Shah, R. A. Khan, M. Sayed and T. Mahmood, Adv. Polym. Technol., 2018, 37, 1168–1175 CrossRef CAS.
- R. A. A. Nugroho, A. F. Alhikami and W. C. Wang, Energy, 2023, 277, 127707 CrossRef CAS.
- T. Gao and W. Lu, Electrochim. Acta, 2019, 323, 134791 CrossRef CAS.
- R. Tao, P. Xing, H. Li, Z. Sun and Y. Wu, Resour. Conserv. Recycl., 2022, 176, 105921 CrossRef CAS.
- J. K. Mao, J. Li and Z. Xu, J. Cleaner Prod., 2018, 205, 923–929 CrossRef CAS.
- R. Tao, P. Xing, H. Li, Z. Sun and Y. Wu, Resour. Conserv. Recycl., 2022, 176, 105921 CrossRef CAS.
- X. Qu, H. Xie, X. Chen, Y. Tang, B. Zhang, P. Xing and H. Yin, ACS Sustainable Chem. Eng., 2020, 8, 6524–6532 CrossRef CAS.
- F. Zhou, X. Qu, Y. Wu, J. Zhao, S. Gao, D. Wang and H. Yin, ACS Sustainable Chem. Eng., 2022, 10, 1287–1297 CrossRef CAS.
-
N. Bahaloo-Horeh, F. Vakilchap and S. M. Mousavi, Recycling of Spent Lithium-Ion Batteries, Springer International Publishing, Cham, 2019 Search PubMed.
- J. C. Y. Jung, P. C. Sui and J. Zhang, J. Energy Storage, 2021, 35, 102217 CrossRef.
- M. Joulié, R. Laucournet and E. Billy, J. Power Sources, 2014, 247, 551–555 CrossRef.
- W. Lv, Z. Wang, H. Cao, Y. Sun, Y. Zhang and Z. Sun, ACS Sustainable Chem. Eng., 2018, 6, 1504–1521 CrossRef CAS.
- K. H. Chan, J. Anawati, M. Malik and G. Azimi, ACS Sustainable Chem. Eng., 2021, 9, 4398–4410 CrossRef CAS.
- D. Dutta, A. Kumari, R. Panda, S. Jha, D. Gupta, S. Goel and M. K. Jha, Sep. Purif. Technol., 2018, 200, 327–334 CrossRef CAS.
- A. Aboulaich, A. Yaden, N. Elhalya, M. Tayoury, M. Aqil, L. Hdidou, M. Dahbi and J. Alami, Sustain, 2022, 14, 2552 CrossRef CAS.
- C. Quintana, O. Cybulski, B. Mikulak-Klucznik, T. Klucznik and B. A. Grzybowski, Adv. Mater., 2023, 35, 1–12 Search PubMed.
- T. Punt, G. Akdogan, S. Bradshaw and P. van Wyk, Miner. Eng., 2021, 173, 107204 CrossRef CAS.
- J. W. Choi, J. Kim, S. K. Kim and Y. S. Yun, J. Hazard. Mater., 2022, 424, 127481 CrossRef CAS PubMed.
- L. Xing, J. Bao, S. Zhou, Y. Qiu, H. Sun, S. Gu and J. Yu, Chem. Eng. J., 2021, 420, 129593 CrossRef CAS.
- B. Li, Q. Li, Q. Wang, X. Yan, M. Shi and C. Wu, Phys. Chem. Chem. Phys., 2022, 24, 19029–19051 RSC.
- Y. Luo, L. Ou and C. Yin, J. Cleaner Prod., 2023, 396, 136552 CrossRef CAS.
- Y. Luo, L. Ou and C. Yin, Sci. Total Environ., 2023, 875, 162567 CrossRef CAS PubMed.
- Y. Yang, Z. Liu, J. Zhang, Y. Chen and C. Wang, J. Alloys Compd., 2023, 947, 169660 CrossRef CAS.
- B. Zhang, B. K. Biswal, J. Zhang and R. Balasubramanian, Chem. Rev., 2023, 123, 7193–7294 CrossRef CAS PubMed.
- K. Liu and F. S. Zhang, J. Hazard. Mater., 2016, 316, 19–25 CrossRef CAS PubMed.
- Y. Yang, Z. Liu, J. Zhang, Y. Chen and C. Wang, J. Alloys Compd., 2023, 947, 169660 CrossRef CAS.
- S. Suriyakumar, B. Pattavathi, A. Jojo and M. M. Shaijumon, Adv. Sustainable Syst., 2023, 7, 1–8 Search PubMed.
- M. Liu, W. Ma, X. Zhang, Z. Liang and Q. Zhao, Mater. Chem. Phys., 2022, 289, 126466 CrossRef CAS.
- A. Porvali, S. Ojanen, B. P. Wilson, R. Serna-Guerrero and M. Lundström, J. Sustainable Metall., 2020, 6, 78–90 CrossRef.
- F. Xie, F. Lu, C. Liu, Y. Tian, Y. Gao, L. Zheng and X. Gao, Colloids Surf., A, 2023, 658, 130731 CrossRef CAS.
- A. Iqbal, M. R. Jan and J. Shah, Hydrometallurgy, 2022, 213, 105911 CrossRef CAS.
- J. Wang, X. Huo, F. Zhang, L. Wang, X. Wang, J. Li and J. Yang, Sep. Purif. Technol., 2023, 313, 123449 CrossRef CAS.
- T. Huang, L. Liu and S. Zhang, Hydrometallurgy, 2019, 188, 101–111 CrossRef CAS.
- J. Xu, Y. Jin, K. Liu, N. Lyu, Z. Zhang, B. Sun, Q. Jin, H. Lu, H. Tian, X. Guo, D. Shanmukaraj, H. Wu, M. Li, M. Armand and G. Wang, Sci. Adv., 2022, 8, eabq7948 CrossRef CAS PubMed.
- J. Xu, Y. Jin, K. Liu, N. Lyu, Z. Zhang, B. Sun, Q. Jin, H. Lu, H. Tian, X. Guo, D. Shanmukaraj, H. Wu, M. Li, M. Armand and G. Wang, Sci. Adv., 2022, 8, eabq7948 CrossRef CAS PubMed.
- J. Kim, I. Moon and J. Kim, J. Cleaner Prod., 2023, 391, 136241 CrossRef CAS.
- Y. Cao, L. Li, Y. Zhang, Z. Liu, L. Wang, F. Wu and J. You, Resour. Conserv. Recycl., 2023, 188, 106689 CrossRef CAS.
- Q. Chen, Y. Hou, X. Lai, K. Shen, H. Gu, Y. Wang, Y. Guo, L. Lu, X. Han and Y. Zheng, Sep. Purif. Technol., 2023, 311, 123277 CrossRef CAS.
- F. Arshad, L. Xu, Q. Yan, F. Zhang, Z. Hu, F. Wu, R. Chen and L. Li, Sustainable Mater. Technol., 2023, 36, e00633 CrossRef CAS.
- H. Tian, M. Graczyk-Zajac, D. M. De Carolis, C. Tian, E. Ricohermoso, Z. Yang, W. Li, M. Wilamowska-Zawlocka, J. P. Hofmann, A. Weidenkaff and R. Riedel, J. Hazard. Mater., 2023, 445, 130607 CrossRef CAS PubMed.
- H. Tian, M. Graczyk-Zajac, D. M. De Carolis, C. Tian, E. Ricohermoso, Z. Yang, W. Li, M. Wilamowska-Zawlocka, J. P. Hofmann, A. Weidenkaff and R. Riedel, J. Hazard. Mater., 2023, 445, 130607 CrossRef CAS PubMed.
- F. Arshad, L. Xu, Q. Yan, F. Zhang, Z. Hu, F. Wu, R. Chen and L. Li, Sustainable Mater. Technol., 2023, 36, e00633 CrossRef CAS.
- B. Zhang, Y. Jiang and R. Balasubramanian, J. Mater. Chem. A, 2021, 9, 24759–24802 RSC.
- W. Wang, W. Chen and H. Liu, Hydrometallurgy, 2019, 185, 88–92 CrossRef CAS.
-
M. L. Free, Hydrometallurgy, Fundemetals and Applications, 2022 Search PubMed.
- L. Sun, B. Liu, T. Wu, G. Wang, Q. Huang, Y. Su and F. Wu, Int. J. Miner. Metall. Mater., 2021, 28, 991–1000 CrossRef CAS.
- L. Xu, C. Chen and M. L. Fu, Hydrometallurgy, 2020, 197, 105439 CrossRef CAS.
- L. Xing, J. Bao, S. Zhou, Y. Qiu, H. Sun, S. Gu and J. Yu, Chem. Eng. J., 2021, 420, 129593 CrossRef CAS.
- Y. Liu, W. Lv, X. Zheng, D. Ruan, Y. Yang, H. Cao and Z. Sun, ACS Sustainable Chem. Eng., 2021, 9, 3183–3194 CrossRef CAS.
- S. He, W. Xiang, W. He, F. Yu and Z. Liu, Chem. Eng. J., 2022, 429, 132371 CrossRef CAS.
- N. Djoudi, M. Le Page Mostefa and H. Muhr, Resources, 2021, 10, 58 CrossRef.
- Y. Hua, Z. Xu, B. Zhao and Z. Zhang, Green Chem., 2022, 3723–3735 RSC.
- R. Golmohammadzadeh, F. Rashchi and E. Vahidi, Waste Manage., 2017, 64, 244–254 CrossRef CAS PubMed.
- L. Lin, Z. Lu and W. Zhang, Resour. Conserv. Recycl., 2021, 167, 105416 CrossRef CAS.
- M. Roshanfar, R. Golmohammadzadeh and F. Rashchi, J. Environ. Chem. Eng., 2019, 7, 102794 CrossRef CAS.
- A. Chagnes and B. Pospiech, J. Chem. Technol. Biotechnol., 2013, 88, 1191–1199 CrossRef CAS.
- N. Vieceli, R. Casasola, G. Lombardo, B. Ebin and M. Petranikova, Waste Manage., 2021, 125, 192–203 CrossRef CAS PubMed.
- N. J. Boxall, K. Y. Cheng, W. Bruckard and A. H. Kaksonen, J. Hazard. Mater., 2018, 360, 504–511 CrossRef CAS PubMed.
- X. Zhang, H. Shi, N. Tan, M. Zhu, W. Tan, D. Daramola and T. Gu, Bioresour. Bioprocess., 2023, 10, 19 CrossRef.
- A. Heydarian, S. M. Mousavi, F. Vakilchap and M. Baniasadi, J. Power Sources, 2018, 378, 19–30 CrossRef CAS.
- B. K. Biswal, U. U. Jadhav, M. Madhaiyan, L. Ji, E.-H. Yang and B. Cao, ACS Sustainable Chem. Eng., 2018, 6, 12343–12352 CrossRef CAS.
- B. Xin, D. Zhang, X. Zhang, Y. Xia, F. Wu, S. Chen and L. Li, Bioresour. Technol., 2009, 100, 6163–6169 CrossRef CAS PubMed.
- S. Ghassa, A. Farzanegan, M. Gharabaghi and H. Abdollahi, Hydrometallurgy, 2020, 197, 105465 CrossRef CAS.
- R. Marcincakova, J. Kadukova, A. Mrazikova, O. Velgosova, A. Luptakova and S. Ubaldini, Inżynieria Miner., 2016, R. 17, 117–120 Search PubMed.
- J. J. Roy, S. Madhavi and B. Cao, J. Cleaner Prod., 2021, 280, 124242 CrossRef CAS.
- X. Liao, M. Ye, J. Liang, S. Li, Z. Liu, Y. Deng, Z. Guan, Q. Gan, X. Fang and S. Sun, J. Cleaner Prod., 2022, 380, 134991 CrossRef CAS.
- T. Naseri, N. Bahaloo-Horeh and S. M. Mousavi, J. Environ. Manage., 2019, 235, 357–367 CrossRef CAS PubMed.
- T. Naseri, N. Bahaloo-Horeh and S. M. Mousavi, J. Cleaner Prod., 2019, 220, 483–492 CrossRef CAS.
- M. Nazerian, N. Bahaloo-Horeh and S. M. Mousavi, Korean J. Chem. Eng., 2023, 40, 584–593 CrossRef CAS.
- Y. Xin, X. Guo, S. Chen, J. Wang, F. Wu and B. Xin, J. Cleaner Prod., 2016, 116, 249–258 CrossRef CAS.
- L. Li, G. Zeng, S. Luo, X. Deng and Q. Xie, J. Korean Soc. Appl. Biol. Chem., 2013, 56, 187–192 CrossRef CAS.
- G. Zeng, S. Luo, X. Deng, L. Li and C. Au, Miner. Eng., 2013, 49, 40–44 CrossRef CAS.
- F. Noruzi, N. Nasirpour, F. Vakilchap and S. M. Mousavi, Appl. Microbiol. Biotechnol., 2022, 106, 5301–5316 CrossRef CAS PubMed.
- X. Liu, H. Liu, W. Wu, X. Zhang, T. Gu, M. Zhu and W. Tan, Front. Microbiol., 2020, 10, 3058 CrossRef PubMed.
- Z. Niu, Y. Zou, B. Xin, S. Chen, C. Liu and Y. Li, Chemosphere, 2014, 109, 92–98 CrossRef CAS PubMed.
- N. B. Horeh, S. M. Mousavi and S. A. Shojaosadati, J. Power Sources, 2016, 320, 257–266 CrossRef CAS.
- N. Alavi, K. Partovi, M. Majlessi, M. Rashidi and M. Alimohammadi, Bioresour. Technol. Reports, 2021, 15, 100768 CrossRef CAS.
- N. Bahaloo-Horeh, S. M. Mousavi and M. Baniasadi, J. Cleaner Prod., 2018, 197, 1546–1557 CrossRef CAS.
- Z. Kazemian, M. Larypoor and R. Marandi, Int. J. Environ. Anal. Chem., 2020, 103, 514–527 CrossRef.
- N. Bahaloo-Horeh and S. M. Mousavi, Waste Manage., 2017, 60, 666–679 CrossRef CAS PubMed.
- J. J. Roy, N. Zaiden, M. P. Do, B. Cao and M. Srinivasan, Joule, 2023, 7, 450–456 CrossRef.
- J. Li, H. Zhang, H. Wang and B. Zhang, Environ. Res., 2023, 238, 117145 CrossRef CAS PubMed.
- A. Naderi, F. Vakilchap, E. Motamedian and S. M. Mousavi, Appl. Microbiol. Biotechnol., 2023, 107, 7331–7346 CrossRef CAS PubMed.
- G. Zeng, X. Deng, S. Luo, X. Luo and J. Zou, J. Hazard. Mater., 2012, 199–200, 164–169 CrossRef CAS PubMed.
- Z. Niu, Q. Huang, J. Wang, Y. Yang, B. Xin and S. Chen, J. Hazard. Mater., 2015, 298, 170–177 CrossRef CAS PubMed.
- L. Dusengemungu, G. Kasali, C. Gwanama and B. Mubemba, Environ. Adv., 2021, 5, 100083 CrossRef CAS.
- J. Sedlakova-Kadukova, R. Marcincakova, A. Luptakova, M. Vojtko, M. Fujda and P. Pristas, Sci. Rep., 2020, 10, 14594 CrossRef CAS PubMed.
- A. Lobos, V. J. Harwood, K. M. Scott and J. A. Cunningham, J. Appl. Microbiol., 2021, 131, 743–755 CrossRef CAS PubMed.
- M.-J. Kim, J.-Y. Seo, Y.-S. Choi and G.-H. Kim, Waste Manage., 2016, 51, 168–173 CrossRef CAS PubMed.
- W. Wu, X. Liu, X. Zhang, X. Li, Y. Qiu, M. Zhu and W. Tan, J. Biosci. Bioeng., 2019, 128, 344–354 CrossRef CAS PubMed.
- S. Panda, S. Dembele, S. Mishra, A. Akcil, İ. Agcasulu, E. Hazrati, A. Tuncuk, P. Malavasi and S. Gaydardzhiev, J. Chem. Technol. Biotechnol., 2024, 99, 1069–1082 CrossRef CAS.
- S. Li, X. Wu, Y. Jiang, T. Zhou, Y. Zhao and X. Chen, Waste Manage., 2021, 136, 18–27 CrossRef CAS PubMed.
- M. Gavrilescu, Bioresour. Technol., 2022, 344, 126208 CrossRef CAS PubMed.
- W. Jin, Electrochim. Acta, 2021, 374, 137937 CrossRef CAS.
- L. A. Diaz, M. L. Strauss, B. Adhikari, J. R. Klaehn, J. S. McNally and T. E. Lister, Resour. Conserv. Recycl., 2020, 161, 104900 CrossRef.
- C. Lupi, M. Pasquali and A. Dell’Era, Waste Manage., 2005, 25, 215–220 CrossRef CAS PubMed.
- C. Hazotte, E. Meux, N. Leclerc and F. Lapicque, Chem. Eng. Process. Process Intensif., 2015, 96, 83–93 CrossRef CAS.
- W. Jin and Y. Zhang, ACS Sustainable Chem. Eng., 2020, 8, 4693–4707 CrossRef CAS.
- G. Prabaharan, S. P. Barik, N. Kumar and L. Kumar, Waste Manage., 2017, 68, 527–533 CrossRef CAS PubMed.
- J. Kong, S. Zhou, T. He, S. Gu and J. Yu, Green Chem., 2023, 25, 3956–3965 RSC.
- K. Liu, S. Yang, F. Lai, H. Wang, Y. Huang, F. Zheng, S. Wang, X. Zhang and Q. Li, ACS Appl. Energy Mater., 2020, 3, 4767–4776 CrossRef CAS.
- L. Yang, Z. Gao, T. Liu, M. Huang, G. Liu, Y. Feng, P. Shao and X. Luo, Environ. Sci. Technol., 2023, 57, 4591–4597 CrossRef CAS PubMed.
- J. Zhao, J. Qu, X. Qu, S. Gao, D. Wang and H. Yin, Green Chem., 2022, 24, 6179–6188 RSC.
- Z. Li, L. He, Z. Wei Zhao, D. Wang and W. Xu, ACS Sustainable Chem. Eng., 2019, 7, 16738–16746 CrossRef CAS.
- C. Hazotte, N. Leclerc, E. Meux and F. Lapicque, Hydrometallurgy, 2016, 162, 94–103 CrossRef CAS.
- N. J. Boxall, N. Adamek, K. Y. Cheng, N. Haque, W. Bruckard and A. H. Kaksonen, Waste Manage., 2018, 74, 435–445 CrossRef CAS PubMed.
- J. Pryshlakivsky and C. Searcy, J. Cleaner Prod., 2013, 57, 115–123 CrossRef.
- M. Alipanah, D. Reed, V. Thompson, Y. Fujita and H. Jin, J. Clean. Prod., 2023, 382, 135274 CrossRef CAS.
- L. Lin, Z. Lu and W. Zhang, Resour. Conserv. Recycl., 2021, 167, 105416 CrossRef CAS.
- M. Mohr, J. F. Peters, M. Baumann and M. Weil, J. Ind. Ecol., 2020, 24, 1310–1322 CrossRef CAS.
- M. Raugei and P. Winfield, J. Cleaner Prod., 2019, 213, 926–932 CrossRef CAS.
- F. Wu, L. Li, L. Crandon, Y. Cao, F. Cheng, A. Hicks, E. Y. Zeng and J. You, J. Cleaner Prod., 2022, 339, 130697 CrossRef CAS.
- Y. Cao, L. Li, Y. Zhang, Z. Liu, L. Wang, F. Wu and J. You, Resour. Conserv. Recycl., 2023, 188, 106689 CrossRef CAS.
- F. Arshad, L. Li, K. Amin, E. Fan, N. Manurkar, A. Ahmad, J. Yang, F. Wu and R. Chen, ACS Sustainable Chem. Eng., 2020, 8, 13527–13554 CrossRef CAS.
- Y. Li, W. Lv, H. Huang, W. Yan, X. Li, P. Ning, H. Cao and Z. Sun, Green Chem., 2021, 23, 6139–6171 RSC.
- A. Nordelöf, S. Poulikidou, M. Chordia, F. Bitencourt de Oliveira, J. Tivander and R. Arvidsson, Batteries, 2019, 5, 51 CrossRef.
- Z. Liang, C. Cai, G. Peng, J. Hu, H. Hou, B. Liu, S. Liang, K. Xiao, S. Yuan and J. Yang, ACS Sustainable Chem. Eng., 2021, 9, 5750–5767 CrossRef CAS.
- E. Fan, L. Li, Z. Wang, J. Lin, Y. Huang, Y. Yao, R. Chen and F. Wu, Chem. Rev., 2020, 120, 7020–7063 CrossRef CAS PubMed.
- J. B. Dunn, L. Gaines, J. C. Kelly, C. James and K. G. Gallagher, Energy Environ. Sci., 2015, 8, 158–168 RSC.
- L. Gaines, Sustainable Mater. Technol., 2018, 17, e00068 CrossRef CAS.
- B. Adhikari, N. A. Chowdhury, L. A. Diaz, H. Jin, A. K. Saha, M. Shi, J. R. Klaehn and T. E. Lister, Resour. Conserv. Recycl., 2023, 193, 106973 CrossRef CAS.
- I. Rey, C. Vallejo, G. Santiago, M. Iturrondobeitia and E. Lizundia, ACS Sustainable Chem. Eng., 2021, 9, 14488–14501 CrossRef CAS.
- Y. Yang, E. G. Okonkwo, G. Huang, S. Xu, W. Sun and Y. He, Energy Storage Mater., 2021, 36, 186–212 CrossRef.
- A. Boyden, V. K. Soo and M. Doolan, Proc. Cirp, 2016, 48, 188–193 CrossRef.
- A. Fahimi, S. Ducoli, S. Federici, G. Ye, E. Mousa, P. Frontera and E. Bontempi, J. Cleaner Prod., 2022, 338, 130493 CrossRef CAS.
- X. Wang, G. Gaustad, C. W. Babbitt and K. Richa, Resour. Conserv. Recycl., 2014, 83, 53–62 CrossRef.
- CAS, Lithium Ion Battery Recycling, CAS Science Team, https://www.cas.org/resources/cas-insights/sustainability/lithium-ion-battery-recycling#:~:text=Today%2C only 5%25 of the,8 million tons of waste.
- G. Harper, R. Sommerville, E. Kendrick, L. Driscoll, P. Slater, R. Stolkin, A. Walton, P. Christensen, O. Heidrich and S. Lambert, Nature, 2019, 575, 75–86 CrossRef CAS PubMed.
- P. Moazzam, Y. Boroumand, P. Rabiei, S. S. Baghbaderani, P. Mokarian, F. Mohagheghian, L. J. Mohammed and A. Razmjou, Chemosphere, 2021, 277, 130196 CrossRef CAS PubMed.
- R. Wagner-Wenz, A.-J. van Zuilichem, L. Göllner-Völker, K. Berberich, A. Weidenkaff and L. Schebek, MRS Energy Sustainable, 2023, 10, 1–34 CrossRef.
|
This journal is © The Royal Society of Chemistry 2024 |
Click here to see how this site uses Cookies. View our privacy policy here.