DOI:
10.1039/D4DT01893A
(Paper)
Dalton Trans., 2024,
53, 14656-14664
Two-step construction of KPDMS/Al2O3 ultra-barriers for wearable sensors†
Received
30th June 2024
, Accepted 15th August 2024
First published on 22nd August 2024
Abstract
Wearable devices hold significant potential in healthcare and medical diagnostics. One major challenge in realizing this potential is the low barrier property of polymer substrates, which fail to withstand surrounding moisture and biofluids. In this work, a two-step strategy involving ALI followed by a UV-curing process is developed to fabricate a K48PDMS/Al2O3 ultra-barrier with high barrier property of 7.82 × 10−5 g m−2 day−1 under stretching strain, representing one of the highest values among current works. Moreover, the K48PDMS/Al2O3 barrier enables Ca-tested devices to exhibit extended operational lifetimes of up to 12 days in simulated rain. It also ensures the high sensitivity of strain sensors for real-time monitoring of health-related physiological signals, even when exposed to aggressive solutions such as PBS, KOH, and glucose. A clear “filling–cross-linking” mechanism is revealed, involving the filling of the void spaces within polymer chains followed by the cross-linking of polymer side chains to enhance the density of the hybrid layer. Adjusting porosity and functional group density ensures complete Al2O3 infiltration into the polymer. The cross-linking increases from 12.31% to 73.79% compared to the UV-curing process alone due to the presence of Al2O3, further enhancing the density of the hybrid layer and its barrier properties. The proposed strategy in our work shows great potential for providing highly reliable encapsulation for wearable electronics.
1. Introduction
Wearable devices can be adhered to the skin and even be implanted,1 offering significant potential in healthcare and medical diagnostics.2,3 Realizing this potential requires soft barrier substrates and encapsulation films that protect these wearable devices against moisture, biofluids, and water-based solutions from the surrounding environment.4 However, common polymer substrates have large free volumes and high chain mobility, allowing moisture to permeate them readily.5,6 Typically, these materials have a water vapor transmission rate (WVTR) that ranges from 1 to 100 g m−2 day−1, whereas practical wearable electronic devices require a much lower WVTR value of below 10−4 g m−2 day−1 to ensure their stability.7,8
Various strategies, including use of polymer nanocomposites, polymer blending, and coating, aim to enhance the barrier properties of polymer substrates. Polymer nanocomposites and blending typically achieve barrier properties of around 10−3 g m−2 day−1,9–13 which is insufficient to achieve long-term stability for wearable devices. Coating, which involves depositing thin impermeable inorganic films chemically and physically on polymer substrates, shows potential for achieving highly flexible barriers.14,15 One major challenge in achieving high barrier properties in polymer/inorganic composite structures is the interface instability caused by mismatches in modulus and CTE between the thin inorganic film and the polymer.16,17
Among the atomic-scale interface engineering methods, atomic layer infiltration (ALI) is considered one of the most effective methods to enhance interface stability through the construction of a gradient modulus structure, which comprises thin inorganic layers, hybrid layers, and a polymer layer. The thin inorganic films fabricated by ALI offer advantages such as high uniformity, conformity, precise thickness control at the sub-nanometer scale, and low-temperature deposition.18 Importantly, the hybrid layer formed by filling the free empty spaces within the polymer with oxides not only efficiently mitigates modulus and thermal mismatches at the interface but also acts as a barrier layer against moisture. Furthermore, the density of these hybrid films is positively correlated with their barrier properties. Recently, ALI has been used to modify polymers including polyethylene naphthalate (PEN), polyethylene terephthalate (PET), polyimide (PI), and polydimethylsiloxane (PDMS), demonstrating its effectiveness in creating highly stable hybrid structures with excellent barrier properties.18–22 However, maintaining the high barrier properties of polymer substrates under deformation caused by human movement and exposure to aggressive solutions like sweat remains a challenge.
Here, we present a two-step strategy by introducing a UV-curing process after the ALI process to achieve high cross-linking density of KnPDMS/Al2O3 ultra-barriers. The optimal barrier, K48PDMS/Al2O3, demonstrates its ultra-barrier ability by sustaining high barrier properties (7.82 × 10−5 g m−2 day−1) from unstrained to strain states. The K48PDMS/Al2O3 ultra-barrier can enhance the water resistance of Ca-tested devices in rainfall scenarios. Additionally, the ultra-barrier of an encapsulated wearable strain sensor maintained its resistance after being soaked in aggressive solutions such as PBS solution, KOH, and glucose for a long time. Importantly, the encapsulated strain sensor illustrates changes in sensitivity under various actions of the human body, highlighting its potential for diverse wearable electronics applications. A clear “filling–cross-linking” mechanism is revealed, supported by QCM, FTIR, and SEM analyses. This mechanism involves the filling of void spaces within polymer chains followed by the cross-linking of polymer side chains to enhance the density of the hybrid structure. Notably, a synergistic effect occurs where infiltrated Al2O3 strengthens cross-linking, increasing it from 17.08% to 74.24% compared to the UV-curing process alone.
2. Experimental methods
2.1. Materials
3-Methacryloxypropylmethyldimethoxysilane (KH571), dibutyltin dilaurate (DBTDL), and SiO2 nanoparticles (Hydrophilic-380 type) were purchased from Aladdin. Hydroxy-terminated polydimethylsiloxane (PDMS-OH) with an average molecular weight of 50
000 was purchased from Guangdong Weng Jiang Chemical Co., Ltd, China. Trimethylaluminum (TMA, 97.99999% purity) was obtained from Fornano.
2.2. Fabrication of functionalized PDMS films (KnPDMS)
Unlike the traditional fabrication method for PDMS film (Sylgard 184), which requires thermal curing at elevated temperatures (>100 °C) and a long curing time of over 120 minutes,23,24 the KPDMS substrates are synthesized via a solvent-free process by simply mixing the PDMS-OH, KH571, and SiO2 nanoparticles at room temperature under fast curing for 2 min. The mass ratio of PDMS-OH, KH571, and SiO2 is 5
:
x
:
1 (x = 1.6, 2.4, 3.2). The prepared PDMS-based films are denoted as KnPDMS, where n, which is equal to 32, 48, and 64, indicates the mass fraction of KH571. The KH571 is used as a cross-linking agent to react with PDMS-OH under the DBTL catalyst, forming the PDMS-based film,25 where no films are obtained when KH571 is absent with only PDMS-OH, SiO2, and DBTL catalyst being present in the precursor solution. The KnPDMS was applied to PVA (polyvinyl alcohol) transfer paper using a scraper, resulting in a KnPDMS film with an approximate thickness of 200 μm.
2.3. Atomic layer deposition (ALD) and atomic layer infiltration (ALI)
All the deposition processes were performed in a homemade viscous flow tube reactor. Metal–organic precursors and oxidants used in the ALD and ALI processes are trimethylaluminum (TMA) and deionized H2O, respectively. The ALI chamber pressure is set to 0.6 Torr during the process with a constant 100 sccm flow of N2 throughout to carry and purge the precursor vapors. The deposition temperature is 95 °C. The ALI process included 0.50 s of TMA pulse, 60 s of exposure time, 60 s of N2 purge time, 0.50 s of H2O pulse, 60 s of exposure time, and 60 s of purging. During the 60 s of exposure time, both the pump and gas flow are turned off, ensuring that the chamber is completely sealed. Consequently, only the initially introduced gases, including N2 and precursor gas, remain. The ALD process included 0.50 s of TMA pulse, 60 s of N2 purge time, 0.50 s of H2O pulse, and 60 s of N2 purge time.
2.4. UV-curing method
The UV-curing process is performed using a Full Features Flood UV lamp (Intelli-Ray 600, Uvitron, USA) with a UVA intensity of 150 mW cm−2. The temperature of the UV light is 40 °C. UV light exposure times of 1, 5, and 10 minutes are employed in the study. K64PDMS is used as the sample due to its higher number of functional groups.
2.5. Fabrication and encapsulation of the porous graphene sensor
The porous graphene, employed as electrode material, is fabricated on a polyimide (PI) film using a laser direct writing (LDW) process, followed by the transfer of the K48PDMS film based on differential adhesion. The K48PDMS film serves as a top layer and bottom substrate, and the porous graphene strain sensor encapsulated by the K48PDMS/Al2O3 barrier is prepared through the ALI treatment and UV-curing process.
2.6. Characterization of PDMS films
The thickness of pristine KnPDMS (n = 32, 48, 64) and KnPDMS/Al2O3 barriers are measured using an ultra-depth 3D microscope (DSX 510, Olympus) and an ellipsometer (SE, J.A. Woollam M2000). The FTIR spectra of the pristine KnPDMS and KnPDMS/Al2O3 barriers were recorded using a Nicolet iS 10 FTIR spectrometer (Thermo Fisher Scientific) with a diamond crystal ATR cell, at a resolution of 4 cm−1 over the 4000 to 400 cm−1 wavenumber range. The conversions of the double bonds of the KnPDMS/Al2O3 barriers after exposure to UV treatment are calculated as follows:
where DC is the percentage conversion of double bonds at time t, A0 is the peak area before UV treatment, and At is the peak area at time t after UV treatment.
The transparency is analyzed by UV–vis transmittance (Lambda 35, UV–Vis Spectrometer) in the range from 380 to 800 nm. The CTE is determined using a thermal-mechanical analysis (TMA, Q400) instrument under an N2 atmosphere with a fixed load of 0.05 N. The temperature range is set from 50 °C to 400 °C, with a heating rate of 5 °C min−1. The density of KnPDMS was determined using volumetric displacement, and the porosity was calculated from the bulk density (ρb) and particle density (ρp): (ε = 1 − ρb/ρp).26 The surface images of the KnPDMS/A2O3 barrier (n = 32, 48, 64) before and after stretching are characterized with the ultra-depth 3D microscope (DSX 510, Olympus). The element line analysis of the KnPDMS/Al2O3 barriers are characterized with a field emission scanning electron microscope (FE-SEM, Helios Nanolab G3 CX, FEI) equipped with an energy-dispersive X-ray (EDX) spectrometer. Mass gains are measured in situ using a quartz crystal monitor (QCM) system. A commercial stretching test machine is used to uniaxially stretch the KnPDMS/Al2O3 barriers at ambient temperature. The barrier properties of the prepared thin films are measured according to the WVTR, estimated by using a Ca test at 30 °C and 70% R.H. Utilizing the activation energy of the Al2O3 thin film (50.8 kJ mol−1)27 and the Arrhenius equation,28 an acceleration factor of 2.65 is utilized to convert the WVTR values at 30 °C and 70% RH into values under ambient conditions (25 °C and 50% RH).
3. Results and discussion
3.1. Characterization of KnPDMS substrates
A series of KnPDMS (n = 32, 48, 64) substrates with adjustable physical properties, including modulus, CTE, and density/porosity were fabricated. As shown in Fig. 1a, the modulus of KnPDMS is 1.86 MPa, 2.14 MPa and 2.71 MPa and breaking elongation is 197.6, 181.3% and 102% for K32PDMS, K48PDMS, and K64PDMS, respectively. Fig. 1b reveals a reduction in the CTE of KnPDMS with an increasing mass fraction of KH571. As shown in Fig. S1,† the FTIR spectra of the KnPDMS films display a peak at 1008 cm−1 that corresponds to Si–O–Si stretching of PDMS, and three peaks at 1202 cm−1, 1636 cm−1, and 1718 cm−1 that are attributed to the stretching vibrations of –C–O, –C
O and –C
C groups of KH571,29,30 respectively. These findings demonstrate the cross-linking reaction between KH571 and PDMS, resulting in the introduction of functional groups (C
C, C
O) into the PDMS chain. As illustrated in Fig. 1c, as the mass fraction of KH571 increases, the density of the KnPDMS substrate increases, while the porosity exhibits an inverse trend. The porosity of KnPDMS is 6.8%, 3.38%, and 1.99% for the K32PDMS, K48PDMS, and K64PDMS, respectively. Fig. 1d demonstrates that all KnPDMS substrates exhibit optical transparency in the visible region (380–780 nm), with an optical transmittance exceeding 86%. In summary, the KnPDMS substrates, which are highly stretchable and transparent through the room temperature fabrication method, demonstrate promise as soft substrates for wearable electronics; the only drawback is their low barrier property, as shown in Fig. S2.†
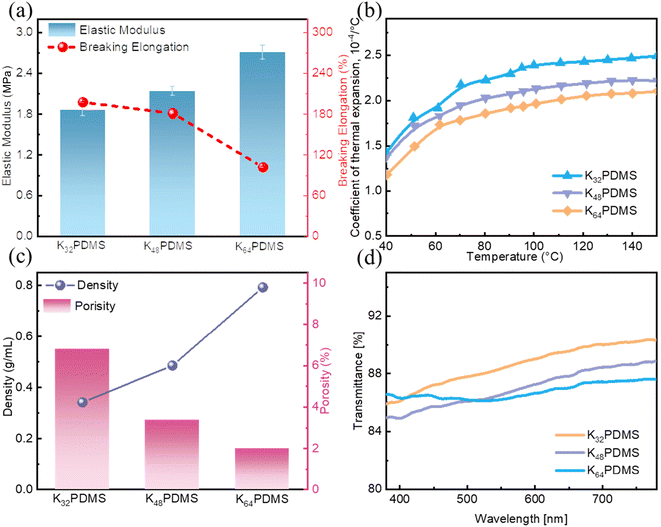 |
| Fig. 1 The KnPDMS films with engineered physical properties. (a) Elastic modulus and breaking elongation. (b) CTE. (c) Density and porosity. (d) Transmission. | |
3.2. Achieving high barrier property for KnPDMS/Al2O3 barriers
A two-step strategy involving atomic layer infiltration (ALI) followed by a UV-curing process has been developed to enhance the barrier property of the KnPDMS (n = 32, 48, 64) substrates, as illustrated in Fig. 2a. Fig. 2b demonstrates that the barrier property of KnPDMS reaches 10–3 g m−2 day−1 after the ALI treatment, and further enhancements to 10−4/10−5 g m−2 day−1 are achieved through additional UV-curing processes. Specifically, the WVTR is 1.71 × 10−4 g m−2 day−1, 1.25 × 10−4 g m−2 day−1, and 3.59 × 10−5 g m−2 day−1 for K32PDMS, K48PDMS and K64PDMS, respectively, which improved by 4 to 5 orders of magnitude the WVTR of pristine KnPDMS (∼1 g m−2 day−1). Fig. 2c shows that increasing the ALI cycles enhances the barrier properties of KnPDMS/Al2O3 (n = 32, 48) barriers, but reduces the barrier properties of the K64PDMS/Al2O3 barrier. With 130 ALI cycles, the WVTR barrier properties achieve values of 9.11 × 10−5 g m−2 day−1 for K32PDMS/Al2O3 and 7.30 × 10−5 g m−2 day−1 for K48PDMS/Al2O3. In contrast, the K64PDMS/Al2O3 barrier exhibits a WVTR of 6.04 × 10−4 g m−2 day−1. The decline after 130 cycles is due to the Al2O3 for the K64PDMS/Al2O3 barrier exceeding a critical thickness, leading to reduced tensile strength and increased stress-induced cracking.31,32 As shown in Fig. 2d, the WVTR of the K64PDMS/Al2O3 barrier first decreases and then increases with the increase of curing time, achieving optimal barrier properties with a lower WVTR of 3.59 × 10−5 g m−2 day−1 at a curing time of 1 min. Therefore, a UV-curing time of 1 minute was employed for all UV-curing experiments, unless otherwise specified.
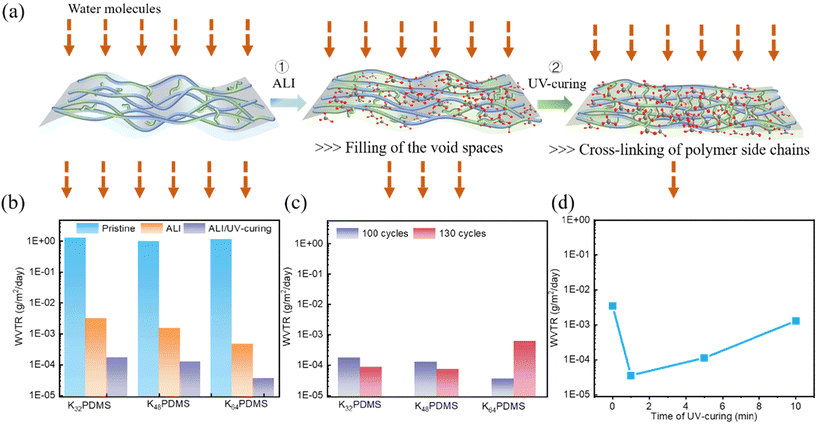 |
| Fig. 2 Achieving high barrier properties in the KnPDMS through ALI followed by UV-curing. (a) Synthetic route. (b) Process impact on barrier properties under 1 min of UV-curing time and 100 ALI cycles. (c) Effect of ALI cycle number on the barrier properties under 1 min of UV-curing time. (d) Effect of UV-curing time on the barrier properties for K64PDMS treated with 100 cycles ALI. | |
3.3. Potential of the K48PDMS/Al2O3 ultra-barrier for wearable devices
The barrier for encapsulating wearable electronics is inevitably exposed to mechanical deformations during operation, making it crucial that the stability of the barrier is maintained under conditions such as bending and stretching. Fig. 3a demonstrates the excellent flexibility of KnPDMS/Al2O3 barriers (n = 32, 48) with 130 ALI cycles. While KnPDMS with 100 ALI cycles shows good flexibility with minimal WVTR change (Fig. S3a†), it is less flexible than KnPDMS with 130 ALI cycles, as shown by the larger WVTR increase after stretching (Fig. S3b†). For KnPDMS (n = 32, 48) with both 100 and 130 ALI cycles, no cracks are observed before or after stretching, as shown in Fig. S4 and S5.† In contrast, visible cracks in K64PDMS with 130 ALI cycles after stretching (Fig. S5c†) are due to excessive thickness, correlating with the WVTR changes. In particular, the WVTR of the K48PDMS/Al2O3 optimal barrier with 130 ALI cycles and UV-curing time of 1 min remains nearly unchanged, at 7.82 × 10−5 g m−2 day−1, after 1% stretching. During stretching, the thin film extends uniformly along the stress direction, resulting in a uniform stress distribution that requires greater flexibility compared to bending deformation.33Fig. 3b and Table S1† illustrate the superior barrier properties of K48PDMS/Al2O3 while maintaining stretchability, contrasting with most other studies that focus on improving barrier properties while maintaining bendability, covering a wide range of bendable radii from 30 mm to 1.75 mm. Additionally, it demonstrates high barrier properties compared to reported stretchable barriers under the same strain.
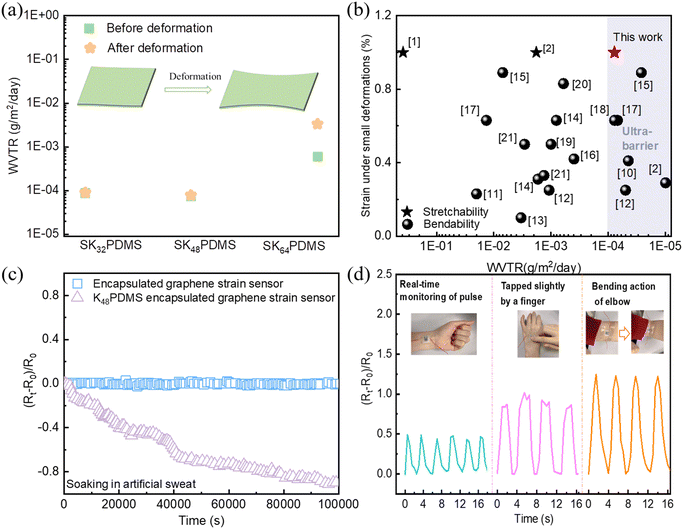 |
| Fig. 3 Potential of the K48PDMS/Al2O3 ultra-barrier for wearable electronics. (a) Deformation impact on barrier properties with 130 ALI cycles and 1 min of UV-curing time. (b) Literature summary of barrier properties and flexibility for various barriers, covering a wide range of bendable radii (30 mm to 1.75 mm). (c) Stability testing of an encapsulated strain sensor with/without PBS. (d) Real-time monitoring of pulse, slight finger tapping, and elbow bending actions. | |
The encapsulation performance of the K48PDMS/Al2O3 ultra-barrier in practical weather situations was evaluated by exposing encapsulated Ca-tested devices to intermittent water, simulating rainfall scenarios. The results, as depicted in Fig. S6,† demonstrate significant improvements in the stability of encapsulated Ca-tested devices, with an extended operational lifetime of up to 12 days compared to instant inactivation observed in unencapsulated devices. Additionally, even after being subjected to 1% stretching, K48PDMS/Al2O3 ultra-barrier-encapsulated Ca-tested devices exhibit similar decay behavior, indicating high barrier properties and flexibility, as illustrated in Fig. S7.† The K48PDMS/Al2O3 ultra-barrier ensures that 90% normalized conductance is preserved in Ca-tested devices after 16 days of operation without exposure to water. As shown in Fig. S8,† the K48PDMS/Al2O3 ultra-barrier effectively prevents PBS penetration for 115 h at pH 7.4, in contrast to the rapid color change in Ca dots encapsulated within K48PDMS. Fig. S9 and Table S2† indicate that devices encapsulated with K48PDMS/Al2O3, when soaked in PBS solution, display a longer lifetime compared to those devices encapsulated with barriers such as single thin films, nanolaminates, polymer/thin films, and polymer/nanolaminates fabricated by ALD. This demonstrates that K48PDMS/Al2O3 also effectively restricts ion diffusion.
The potential application of the K48PDMS/Al2O3 ultra-barrier in wearable electronics is demonstrated by its high stability in a carbon-based strain sensor under challenging environmental conditions. Fig. S10† shows the synthetic route of the K48PDMS/Al2O3 ultra-barrier encapsulated porous graphene sensor, and the K48PDMS/Al2O3 ultra-barrier serves as a top encapsulation thin film and bottom flexible substrate. Fig. 3c demonstrates that the strain sensor encapsulated with K48PDMS film experiences decreased resistance after soaking in PBS solution, while the sensor encapsulated with the K48PDMS/Al2O3 ultra-barrier maintains steady resistance. The encapsulated strain sensor also exhibits stability after exposure to KOH and glucose for 24 hours, as shown in Fig. S11.† Additionally, as shown in Fig. 3d, the encapsulated strain sensor possesses high sensitivity under various conditions, such as pulse signal monitoring by attaching the sensor on the radial artery of the wrist, the response to slight tapping by a finger, and the response to the bending action of the elbow. Additionally, Fig. S12† indicates the high sensitivity of the encapsulated strain sensor under different bending actions of a human finger. In summary, the K48PDMS/Al2O3 ultra-barrier maintains high barrier properties under deformation caused by human movement, ensuring the stability of wearable devices for real-time monitoring of health-related physiological signals even when exposed to aggressive solutions such as sweat, glucose, and base solutions.
3.4. Examining the roles of ALI and UV-curing in the KPDMS/Al2O3 barrier
The roles of ALI and UV-curing in enhancing the barrier property were investigated using in situ QCM, SEM, and FTIR techniques. Initially, the influence of growth behavior of Al2O3 on KnPDMS (n = 32, 48, 64) substrates in the ALI process was monitored using the in situ QCM method. As shown in Fig. 4a, the ALI growth of Al2O3 for KnPDMS can be divided into two stages based on the mass gain per cycle: the infiltration stage and the deposition stage. During the infiltration stage, the mass gain per cycle initially increases and then decreases. This initial increase corresponds to the formation and growth of Al2O3 clusters, while the subsequent decrease is attributed to the closure of internal pores by the formed Al2O3.22,34 For KnPDMS substrates, the mass gain per cycle is similar during the deposition stages, stabilizing at approximately 40 ng per cm2 per cycle. It is also found that the cycles required to achieve maximum Al2O3 infiltration differ, with K64PDMS reaching the highest infiltration in fewer cycles (4 cycles) compared to K32PDMS (7 cycles) and K48PDMS (5 cycles). This can be explained by K64PDMS having more reactive functional groups, such as carbonyl groups, which facilitate the entrapment of precursors. Additionally, the growth behavior of Al2O3 on optimal K48PDMS substrates in the ALD process was monitored using in situ QCM. As shown in Fig. S13a,† the total mass change on K48PDMS in ALI (2414.1 ng cm−2) is significantly greater than in ALD (745.89 ng cm−2). Fig. S13b† shows that the mass gain per cycle stabilizes at approximately 11.3 ng cm−2 for ALD, compared to 40 ng cm−2 for ALI. These results demonstrate that the holding time in ALI improves Al2O3 infiltration and increases nucleation sites, leading to a higher overall mass gain.
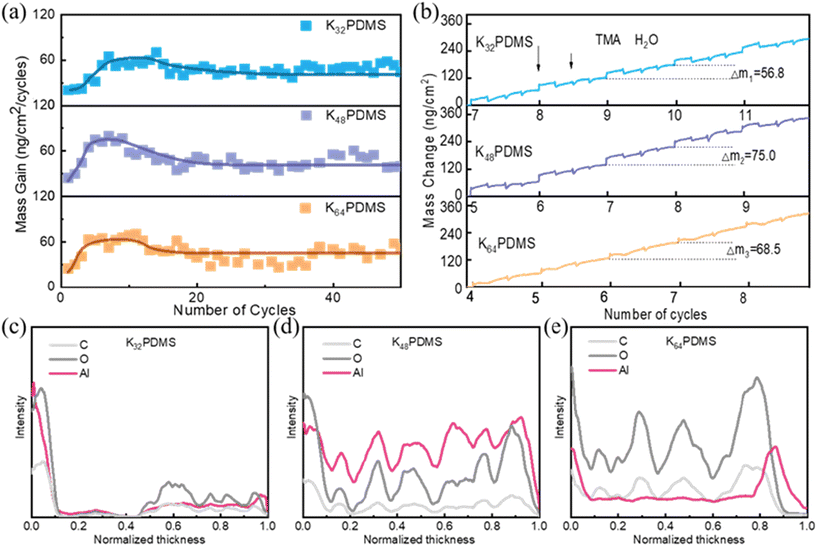 |
| Fig. 4 The enhanced mechanism of barrier property in the ALI process. (a) QCM measurement of ALI processes on KnPDMS. (b) The mass gain per cycle during the initial infiltration stage begins with the onset of maximum Al2O3 infiltration. (c–e) Element line-scan analysis of KnPDMS treated with 100 ALI cycles. | |
Fig. 4b shows the different mass gains per cycle in the initial infiltration stage, with average mass gains per cycle of 56.8 ng per cm2 per cycle, 75 ng per cm2 per cycle, and 68.5 ng per cm2 per cycle, for K32PDMS, K48PDMS and K64PDMS, respectively. The highest Al2O3 infiltration of K48PDMS enhances the density of the hybrid structure. The different Al2O3 infiltration amounts are determined by the density/porosity and functional group number of KnPDMS.35 Fig. S14† shows the elemental mapping in cross-sectional SEM images, with EDS data revealing the coexistence of Al, O, and C, demonstrating the infiltration of Al2O3 into the KnPDMS. Furthermore, the distribution of the Al element throughout the cross-section was evaluated using the line-scan method. As shown in Fig. 4(c–e) and Fig. S15,† a higher normalized intensity of the Al element is observed throughout the cross-section for K48PDMS, while for K32PDMS and K64PDMS, the Al element is only found on the surface and subsurface of the polymers. These results indicate that by adjusting the amount of KH571, full Al2O3 infiltration in K48PDMS polymer can be achieved, resulting in higher density of the hybrid layer and barrier properties.
Furthermore, the bonding mode in the ALI process and UV-curing process is evaluated through FTIR analysis. K48PDMS is selected as the representative sample due to its optimal performance. Fig. 5a shows the FTIR spectra of K48PDMS after ALI and UV-curing. It is observed that red-shifted features correspond to a decrease in the C
O peak at 1718 cm−1, and blue-shifted features of the ester C–O bond at 1202 cm−1 for the K48PDMS after the ALI process, compared to the FTIR of the pristine K48PDMS film. Additionally, two new peaks at 1558 cm−1 and 838 cm−1 are observed after the ALI process, correlated with C–O–Al and Al–O, respectively. These findings suggest that Al2O3 fills the voids within the polymer chain and reacts with C
O and C–O in polymer chains to enhance the density of the organic/inorganic hybrid layer.36 Additionally, the increase in the C–O peak area is attributed to the formation of C–O–Al–OH from the reaction between C
O and TMA.37 Notably, there is a significant decrease in the number of C
C groups, as indicated at 1646 cm−1, after UV light exposure followed by the ALI process.
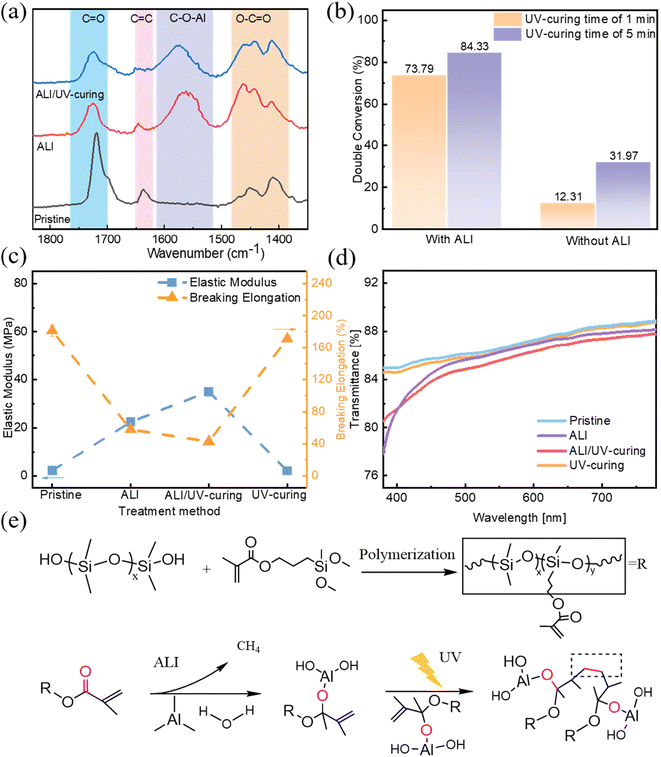 |
| Fig. 5 The enhanced mechanism during the ALI and UV-curing process. (a) Bonding mode in FTIR spectra. (b) Cross-linking of polymer side chains with and without ALI during UV-curing. (c) Enhanced mechanical property. (d) Transmittance. (e) Schematic representation of the “filling–cross-linking” mechanism. | |
FTIR spectra after the UV-curing process with or without the ALI process are illustrated in Fig. S16 and S17† and clearly highlight the effect of the ALI process. Based on the change in the C
C peak area, the conversion rates of C
C (free radical polymer rate) after UV-curing with the ALI process for 1 minute and 5 minutes are determined to be 73.79% and 84.33%, respectively, whereas those without the ALI process for 1 minute and 5 minutes are 12.31% and 31.97% respectively, as illustrated in Fig. 5b. The higher conversion rates of C
C observed after UV exposure with the ALI process compared to those without ALI are attributed to the interaction between infiltrated Al2O3 and the C
O groups, which disrupts the conjugated structure (–C
O–C
C–), leading to an increased electron density of carbon (C
C). This makes it more susceptible to the generation of free radicals under radiation.38
The difference in cross-linking after UV-curing with or without the ALI process is also evidenced to various extents by changes in mechanical properties, transmission and the barrier property. Fig. 5c reveals that the elastic modulus of K48PDMS increases from 22.45 MPa to 35.06 MPa after ALI and ALI/UV-curing, respectively, showing a 993% and 1451% increase compared to pristine K48PDMS. A similar trend is observed in KnPDMS (n = 32, 64), with an increase in elastic modulus and a decrease in breaking elongation after the ALI process, as illustrated in Fig. S18.† Conversely, the elastic modulus remains nearly unchanged after UV-curing alone compared to pristine K48PDMS. Similarly, a decrease in breaking elongation is observed after the ALI and ALI/UV-curing processes for the K48PDMS ultra-barrier, while it remains almost unchanged after UV-curing alone compared to pristine K48PDMS/Al2O3 films. As shown in Fig. 5d, there was a notable decrease in transmission after UV-curing following the ALI process compared to the almost unchanged transmission after UV-curing alone. Fig. S19† shows the barrier properties of K48PDMS before and after UV-curing, ALI treatment, and combined ALI/UV-curing. The UV-curing alone yields barrier properties similar to pristine K48PDMS, while the combined ALI and UV-curing process achieves the highest barrier property. Fig. 5e illustrates the “filling–cross-linking” reaction mechanism. Initially, KH571 doping endows PDMS with functional groups such as C
O and C
C, facilitating the infiltration of Al2O3 into the polymer voids with strong bonding via C–O–Al, forming the organic/inorganic hybrid layer. Subsequently, infiltrated Al2O3 promotes the free-radical polymerization of C
C during the UV-curing process to further enhance the density of the organic/inorganic layer, thereby exhibiting high barrier properties.
4. Conclusions
In summary, KnPDMS/Al2O3 ultra-barriers are fabricated through ALI followed by a UV-curing process. The optimal barrier, K48PDMS/Al2O3, maintains the highest barrier property with a WVTR of 10−5 g m−2 day−1 under stretching. The K48PDMS/Al2O3 ultra-barrier ensures that the wearable strain sensor maintains its high sensitivity to various health-related physiological signals even after prolonged exposure to aggressive solutions. Additionally, the K48PDMS/Al2O3 ultra-barrier extends the operational lifetime of Ca-tested devices to 12 days in water and 4 days in PBS solution (pH 7.4). Complete Al2O3 infiltration is achieved in the polymer by effectively filling void spaces within the polymer chain and facilitating cross-linking of polymer side chains, enhancing the density of the hybrid layer and barrier properties. The K48PDMS/Al2O3 ultra-barrier exhibits the highest barrier property, making it promising for applications in wearable devices in challenging environments.
Author contributions
Di Wen – conceptualization, investigation, formal analysis, writing – original draft. Ruige Yuan – validation, writing – review & editing. Fan Yang – conceptualization, writing – review & editing, supervision, funding acquisition. Rong Chen – writing – review & editing, supervision, project administration, funding acquisition.
Data availability
The data that support the findings of this study are available from the corresponding author upon reasonable request.
Conflicts of interest
The authors declare no conflict of interest.
Acknowledgements
This work was supported by the National Natural Science Foundation of China (52350349 and 52103257), the National Key R&D Program of China (2022YFF1500400), the Natural Science Foundation of Hubei Province (Grant No. 2021CFB066), and the New Cornerstone Science Foundation through the XPLORER PRIZE. We would also like to acknowledge technical support from the Analytic Testing Center and the Flexible Electronics Research Center of HUST.
References
- E. Song, C. H. Chiang, R. Li, X. Jin, J. Zhao, M. Hill, Y. Xia, L. Li, Y. Huang, S. M. Won, K. J. Yu, X. Sheng, H. Fang, M. A. Alam, Y. Huang, J. Viventi, J. K. Chang and J. A. Rogers, Proc. Natl. Acad. Sci. U. S. A., 2019, 116, 15398–15406 CrossRef CAS PubMed.
- J. Zhang, J. Li, W. Cheng, J. H. Zhang, Z. Zhou, X. Sun, L. Li, J. G. Liang, Y. Shi and L. Pan, ACS Mater. Lett., 2022, 577–599 CrossRef CAS.
- J. H. Kwon, E. G. Jeong, Y. Jeon, D. G. Kim, S. Lee and K. C. Choi, ACS Appl. Mater. Interfaces, 2019, 11, 3251–3261 CrossRef CAS PubMed.
- Y. Liu, Q. Yu, L. Yang and Y. Cui, Adv. Mater. Technol., 2023, 8, 2200853 CrossRef CAS.
- M. Mariello, K. Kim, K. Wu, S. P. Lacour and Y. Leterrier, Adv. Mater., 2022, 34, 2201129 CrossRef CAS PubMed.
- Y. Li, Y. Xiong, H. Yang, K. Cao and R. Chen, J. Mater. Res., 2020, 35, 681–700 CrossRef CAS.
- G. Dennler, C. Lungenschmied, H. Neugebauer, N. S. Sariciftci and A. Labouret, J. Mater. Res., 2005, 20, 3224–3233 CrossRef CAS.
- T. Yokota, P. Zalar, M. Kaltenbrunner, H. Jinno, N. Matsuhisa, H. Kitanosako, Y. Tachibana, W. Yukita, M. Koizumi and T. Someya, Sci. Adv., 2016, 2, 1–9 Search PubMed.
- K. Müller, E. Bugnicourt, M. Latorre, M. Jorda, Y. E. Sanz, J. M. Lagaron, O. Miesbauer, A. Bianchin, S. Hankin, U. Bölz, G. Pérez, M. Jesdinszki, M. Lindner, Z. Scheuerer, S. Castelló and M. Schmid, Nanomaterials, 2017, 7, 74 CrossRef PubMed.
- D. V. Houcke, S. Kumar and B. R. Kona, RSC Adv., 2015, 5, 63669–63690 RSC.
- D. A. Kunz, J. Schmid, P. Feicht, J. Erath, A. Fery and J. Breu, ACS Nano, 2013, 7, 4275–4280 CrossRef CAS PubMed.
- Z. Yang, H. Guo, C. Kang and L. Gao, New J. Chem., 2021, 45, 12945–12956 RSC.
- Y. Zheng, L. Michalek, Q. Liu, Y. Wu, H. Kim, P. Sayavong, W. Yu, D. Zhong, C. Zhao, Z. Yu, J. A. Chiong, H. Gong, X. Ji, D. Liu, S. Zhang, N. Prine, Z. Zhang, W. Wang, J. B.-H. Tok, X. Gu, Y. Cui, J. Kang and Z. Bao, Nat. Nanotechnol., 2023, 18, 1175–1184 CrossRef CAS PubMed.
- J. H. Han, T. Y. Kim, D. Y. Kim, H. L. Yang and J. S. Park, Dalton Trans., 2021, 50, 15841–15848 RSC.
- C. Janowitz, A. Mahmoodinezhad, M. Kot, C. Morales, F. Naumann, P. Plate, M. H. Zoellner, F. Bärwolf, D. Stolarek, C. Wenger, K. Henkel and J. I. Flege, Dalton Trans., 2022, 51, 9291–9301 RSC.
- S. H. Jen, S. M. George, R. S. McLean and P. F. Carcia, ACS Appl. Mater. Interfaces, 2013, 5, 1165–1173 CrossRef CAS PubMed.
- O. Graudejus, P. Görrn and S. Wagner, ACS Appl. Mater. Interfaces, 2010, 2, 1927–1933 CrossRef CAS PubMed.
- Y. Li, D. Wen, Y. Zhang, Y. Lin, K. Cao, F. Yang and R. Chen, Dalton Trans., 2021, 50, 16166–16175 RSC.
-
M. D. Losego and Q. Peng, Surf. Modif. Polym. Methods Appl, 2019, pp. 135–159 Search PubMed.
- E. Cianci, D. Nazzari, G. Seguini and M. Perego, Adv. Mater. Interfaces, 2018, 5, 1–10 Search PubMed.
- S. H. Kim, S. Y. Song, S. Y. Kim, M. W. Chang, H. J. Kwon, K. H. Yoon, W. Y. Sung, M. M. Sung and H. Y. Chu, npj Flexible Electron., 2022, 6, 1–6 CrossRef.
- Y. Zhang, D. Wen, M. Liu, Y. Li, Y. Lin, K. Cao, F. Yang and R. Chen, Adv. Mater. Interfaces, 2022, 9, 1–9 Search PubMed.
- B. Gong, J. C. Spagnola and G. N. Parsons, J. Vac. Sci. Technol., A, 2012, 30, 01A156-1–01A156-5 CrossRef.
- J. Huang, Y. Cai, C. Xue, J. Ge, H. Zhao and S. H. Yu, Nano Res., 2021, 14, 3636–3642 CrossRef CAS.
- C. Salazar-Hernández, M. Salazar-Hernández, R. Carrera-Cerritos, J. M. Mendoza-Miranda, E. Elorza-Rodríguez, R. Miranda-Avilés and C. D. Mocada-Sánchez, Prog. Org. Coat., 2019, 136, 105220 CrossRef.
- J. Qiu, S. Khalloufi, A. Martynenko, G. Van Dalen, M. Schutyser and C. Almeida-Rivera, Drying Technol., 2015, 33, 1681–1699 CrossRef.
- K. H. Yoon, H. S. Kim, K. S. Han, S. H. Kim, Y.-E. K. Lee, N. K. Shrestha, S. Y. Song and M. M. Sung, ACS Appl. Mater. Interfaces, 2017, 9, 5399–5408 CrossRef CAS PubMed.
- T. S. Kwon, D. Y. Moon, Y. K. Moon, W. S. Kim and J. W. Park, J. Nanosci. Nanotechnol., 2012, 12, 3696–3700 CrossRef CAS PubMed.
- D. Li, F. Xu, Z. Liu, J. Zhu, Q. Zhang and L. Shao, Appl. Surf. Sci., 2013, 266, 368–374 CrossRef CAS.
- M. A. Velazco-Medel, L. A. Camacho-Cruz and E. Bucio, Radiat. Phys. Chem., 2020, 171, 108754 CrossRef CAS.
- J. Wu, F. Fei, C. Wei, X. Chen, S. Nie, D. Zhang, W. Su and Z. Cui, RSC Adv., 2018, 8, 5721–5727 RSC.
- Y. Li, Y. Xiong, W. Cao, Q. Zhu, Y. Lin, Y. Zhang, M. Liu, F. Yang, K. Cao and R. Chen, Adv. Mater. Interfaces, 2021, 8, 1–9 CAS.
- J. Lv, G. Thangavel and P. S. Lee, Nanoscale, 2022, 15, 434–449 RSC.
- Q. Peng, Y. C. Tseng, Y. Long, A. U. Mane, S. DiDona, S. B. Darling and J. W. Elam, Langmuir, 2017, 33, 13214–13223 CrossRef CAS PubMed.
- R. A. Nye, S. Wang, S. Uhlenbrock, J. A. Smythe and G. N. Parsons, Dalton Trans., 2022, 51, 1838–1849 RSC.
- J. C. Spagnola, B. Gong, S. A. Arvidson, J. S. Jur, S. A. Khan and G. N. Parsons, J. Mater. Chem., 2010, 20, 4213–4222 RSC.
- B. Gong, Q. Peng, J. S. Jur, C. K. Devine, K. Lee and G. N. Parsons, Chem. Mater., 2011, 23, 3476–3485 CrossRef CAS.
- T. Y. Lee, T. M. Roper, E. S. Jonsson, I. Kudyakov, K. Viswanathan, C. Nason, C. A. Guymon and C. E. Hoyle, Polymer, 2003, 44, 2859–2865 CrossRef CAS.
|
This journal is © The Royal Society of Chemistry 2024 |
Click here to see how this site uses Cookies. View our privacy policy here.