DOI:
10.1039/D3LF00126A
(Review Article)
RSC Appl. Interfaces, 2024,
1, 43-69
Recent advances in semiconductor heterojunctions: a detailed review of the fundamentals of photocatalysis, charge transfer mechanism and materials
Received
5th August 2023
, Accepted 26th September 2023
First published on 27th September 2023
Abstract
Photocatalysis, due to its operability under sustainable and green energy conditions, is one of the cardinal branches of the environmental remediation domain. To date, a significant amount of work has been carried out in the design and development of various photocatalysts for applications such as dye degradation, CO2 and NOx reduction, organic transformation and hydrogen generation. Among several factors leading to enhancement of the photocatalytic activity, decreasing the electron–hole (exciton) recombination is regarded as one of the prime factors. Typically, the lifetime of the excitons can be increased by combining two or more semiconductors via forming a heterojunction. Various types of heterojunctions, such as the Schottky barrier, p–n (or non-p–n), van der Waals and facet heterojunctions, can be fabricated depending on specific applications. Each type of heterojunction has its advantages and limitations; hence, proper choice of heterojunction is essential. Almost all classes of semiconductor materials, for instance, metal oxide, perovskites, chalcogenides, metal–organic frameworks (MOFs), covalent organic frameworks (COFs) and MXenes, with a suitable band gap, have been studied for photocatalysis. This review details different classes of materials and types of heterojunctions from the recent literature to provide the reader with a deeper understanding of the same. Initially, the fundamentals of photocatalysis and its basic mechanism are discussed, followed by a detailed discussion on the various types of heterojunctions based on the charge transfer mechanism, such as types I, II and III, with representative examples from recent reports. This panoramic review attempts to encourage a rational design of heterojunctions by choosing the proper candidates to push the process efficiency to its limit.
Introduction
The expanding population and industrial establishments, which have paved the way for rapid developments and, consequently, increased the energy requirements, have contributed to the obliterating level of air, water and soil pollution. These factors have led to an increased awareness and, thereby, further exploration of possible approaches toward environmental remediation.1–3
Photocatalysis—a process that employs the combination of a semiconductor and an appropriate light source—has recently emerged as one of the promising technologies contributing to the generation of renewable energy sources, as well as water decontamination.4,5 In 1969, Muller discovered the photocatalytic degradation of isopropanol by ZnO.6 Following that, in 1972, researchers K. Honda and A. Fujishima discovered the water-splitting mechanism by employing TiO2.7 Since then TiO2 has remained a popular choice of photocatalyst in several domains, owing to its beneficial characteristics, such as chemical stability, non-toxicity and high reactivity.8,9 Due to the wide band gap in these materials, in the past, photocatalysis was mainly performed using ultraviolet radiation-based processes. Recently, there has been a surge of interest in utilizing solar energy for these purposes due to its abundant availability. It has been estimated that the amount of solar energy striking the Earth's surface in an hour is much higher than the global annual energy consumption. While the world's primary energy demand is expected to grow to the tune of 30% by 2040, the share of renewable energy does not exceed 40% by 2040.10 These facts highlight the necessity to substantiate the research efforts to increase the share of renewable energy for future needs.
In a typical photocatalytic process, the movement of electrons from the valence band (VB) to the conduction band (CB) occurs, creating a hole in the VB. This phenomenon is triggered by the irradiation of a photon with an energy equal to or greater than the band gap of the semiconductor. Such photogenerated electrons and holes are the active species that are primarily responsible for various photocatalytic activities. Most of the photogenerated electrons and holes recombine, a process that is detrimental to photocatalytic performance. The minimization of the electron–hole (exciton) recombination, as indicated by its increased lifetime, was realized as an efficient strategy to enhance the overall process efficiency. Since the discovery of interparticle electron transfer by Serpone et al. in 1984, combining two semiconductors to avert the charge combination has become a popular strategy.11 A decade later, the interparticle hole transfer was also affirmed, and since then, combining the two semiconductors for heterojunction formation has been a monstrously investigated zone in photocatalysis.12
As opposed to the conventional catalytic process, semiconductor catalysis relies mainly on the excitons for the various redox reactions.13–16 The major drawback in single-component catalysts is the high recombination rate, resulting in poor photocatalytic activity. The recombination rate can be addressed by the formation of a heterojunction, which is one of the driving forces for the extensive ongoing work in the development of heterojunction catalysts. Additionally, it can offer greater selectivity due to the specific redox potential of the excitons due to their various types of heterojunctions.
The number of publications regarding heterojunction in photocatalysis published between the years 1999 and 2022 is shown in the graph (Fig. 1(a)). In photocatalysis, certain discoveries have been proven to be pivotal for the development of the domain, as shown in Fig. 1(b).
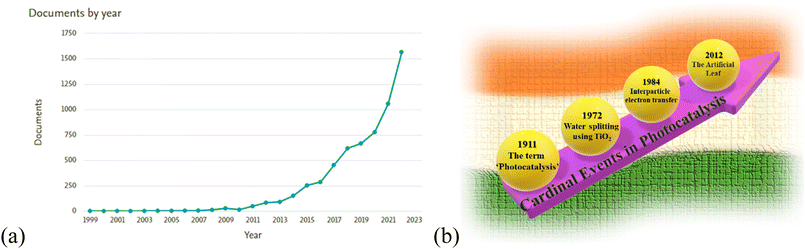 |
| Fig. 1 (a) The trend in the number of publications obtained from ‘Scopus’ with the keyword ‘heterojunction photocatalysis’ accessed on January 3, 2023. (b) Important milestones in the field of photocatalysis. | |
This panoramic review gives a nitty-gritty discourse on the various perspectives of heterojunction photocatalysis. It covers the fundamental principles of photocatalysis and presents a detailed discussion on various types of heterojunctions based on the electron–hole hopping pathway, such as type I, type II, type III, type B, Z-scheme, and S-scheme. Various heterojunctions from recent reports, such as the Schottky barrier, p–n, and non-p–n semiconductor, van der Waals, organic, and facet heterojunctions, are also discussed.
All sorts of semiconducting materials, such as MXenes, metal–organic frameworks (MOFs), covalent organic frameworks (COFs), metal oxides, perovskites, etc., with appropriate band gaps, are deployed for the heterojunction fabrication, and hence representative reports are discussed under the ‘Library of materials used for heterojunction formation in photocatalysis’ section.
A list of the selected recent heterojunction photocatalysts is represented in the tables based on the type of the heterojunction fabricated, such as type I, type II, Z-scheme, and S-scheme. Various parameters like synthetic protocol, reaction rate, experimental conditions, light source, etc., are given and future perspectives are discussed.
Fundamentals in photocatalysis
Before going further, the reader is encouraged to consult the review by Schneider et al. on the mechanisms of TiO2 photocatalysis, which discusses the processes under dark and light conditions, causing band bending and flattening.8 Band bending was first discussed by Schottky and Mott and occurs at the metal–semiconductor junction. The energy band edges in the semiconductor are shifted due to the charge transfer at the metal–semiconductor junction and this is termed band bending. The upward bend is observed when the work function of the metal is greater than that of the semiconductor. However, when the semiconductor work function is greater than the metal work function, downward band bending is observed. Apart from this, band bending of the band edges of the semiconductor can be observed due to an applied external field, adsorption on the semiconductor surface and surface states. The flat energy band (zero space charge in the semiconductor) is observed when there is zero bias voltage between the metal and the semiconductor.17
A typical photocatalytic mineralization process involves several steps, including the generation of excitons, their separation, and the production of reactive oxygen species (ROS). The salient mechanistic steps in the photodegradation of an organic pollutant are listed below.
| Photoexcitation: Photocatalyst + hν → eCB− + hVB+ | (1) |
| Electron–hole recombination: eCB− + hVB+ → heat/light | (2) |
| Formation of hydroxyl radical: −OH + hVB+ → ˙OH | (3) |
| Formation of superoxide anion radical: (O2)Ads + eCB− → −O2˙ | (4) |
| Formation of hydrogen peroxide: −O2˙ + H+ → ˙O2H | (5) |
| Photodegradation: Organic pollutant + ROS → Fragments/CO2 + H2O | (8) |
| Organic pollutant + h+ → Fragments/CO2 + H2O | (9) |
Depending on the duration of illumination, either fragments or complete mineralization of the organic pollutants can be achieved.
18–24 For further details on ROS generation mechanisms and detection methods, the reader is encouraged to review the comprehensive survey by Nosaka
et al.25
What is a heterojunction?
As mentioned earlier, to enhance the lifetime of excitons, two different semiconductors, or a semiconductor and a metal, or a semiconductor and a carbonaceous compound, are coupled to decrease electron–hole recombination. Such a combination of materials with dissimilar band diagrams results in a new electronic structure after hybridization. The band bending is created at the interface of the two semiconductors/components, resulting in a potential difference between the two semiconductor regions. The interface, therefore, induces an electric field within the space charge region that is useful for the spatial separation of the photogenerated excitons, which is termed a ‘heterojunction’.26
Due to the low dielectric constant in organic semiconductors, charge separation is inefficient. It results in coulombically bound excitons as opposed to inorganic semiconductors. Hence, various heterojunctions have been prepared for organic semiconductors to enhance the charge separation efficacy. Moreover, heterojunctions are fabricated for inorganic semiconductors as well to improve the charge separation efficiency and light absorption characteristics.27
Factors affecting heterojunctions
The efficacy of the heterojunction is controlled by several factors. The intimate contact between the components is the primary condition for effective charge separation and the formation of an inbuilt electric field at the interface. The positions of the CB and VB play a critical role in the effective transfer of the electrons and holes and depend on the type of heterojunction achieved. The built-in electric field and potential barriers at the heterojunction interface also depend on other factors such as semiconductivity (n type or p type), work function, and Fermi level.28
Besides the above factors, one may need to consider the orientation between the two components forming the heterojunction. For instance, Xiong et al. fabricated three heterojunction interfaces consisting of α-Fe2O3/Bi2O3 in “ring-to-face”, “face-to-face”, and “rod-to-face” orientations. It was found that the face-to-face model showed the highest photocatalytic activity owing to sufficient interfacial contact and adequate channels for efficient charge transfer.29
Types of heterojunctions based on structural or compositional aspects
Depending on the structural or compositional aspects, photocatalysts can be classified into Schottky barrier, p–n (or non-p–n), van der Waals, and facet heterojunctions, which are briefly discussed below (Fig. 2).
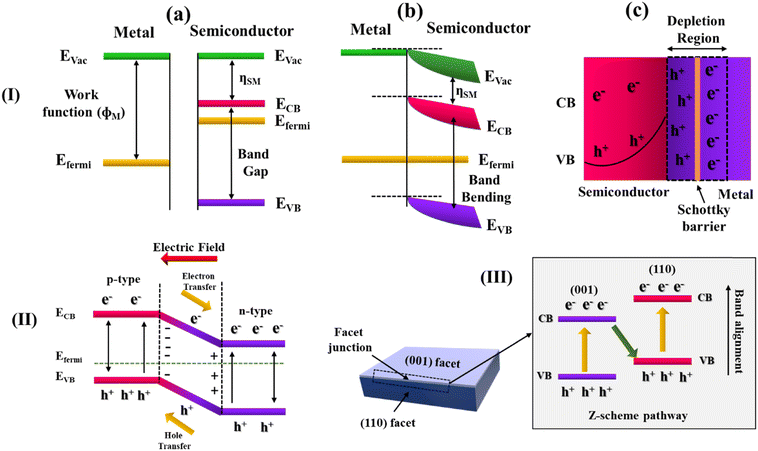 |
| Fig. 2 Schematic diagram depicting the band structure along with the charge recombination processes in the (I) Schottky barrier, (II) p–n heterojunction and (III) facet junction. In (I), panels (a)–(c) represent the steps before contact, after contact and the creation of a Schottky-like barrier, respectively. The diagrams and notations in (I)–(III) were re-drawn/reproduced from ref. 30–32, respectively. | |
Schottky barrier heterojunctions
Depending on the work function between two components, either an Ohmic contact or a Schottky barrier is generated at the interface between a semiconductor and a conductor. An Ohmic junction is formed when the work function of the semiconductor is higher than the conducting component. Ohmic contact facilitates the flow of electrons between the metal and semiconductor materials in both forward and reverse-biased directions. This results in poor charge separation and photoresponse. When the work function of the semiconductor is smaller than the conducting component, it forms the Schottky barrier. The Schottky barrier facilitates the unilateral flow of electrons in the forward-biased direction, resulting in efficient charge separation.30
The facet engineering at the interface of TiO2 and Au and its impact on the Schottky contact barrier height have been explored by Wang et al. The lowering of the Schottky barrier in Au/TiO2 (101), as compared to Au/TiO2 (001), was found to facilitate the transfer of a photogenerated electron from the CB of TiO2 to Au while encouraging the hot electron injections in the reverse direction. Such a process was reported to improve the photocatalytic activity of Au/TiO2 (101) toward the generation of CO and CH4.33 Pd nanocubes with {100} exposed facets and Pd nano-octahedrons with {111} exposed facets have been anchored on two-dimensional TiO2 nanosheets by Lu et al. Pd with exposed facet {111} has demonstrated a greater rate of photocatalytic hydrogenation of nitroarenes. Their investigation revealed that Pd with the {111} exposed facet has a higher Schottky barrier as opposed to Pd with the {100} facet exposed. The higher Schottky barrier results in efficient interfacial charge separation and lower recombination of the photoexcited charge pairs.34 Li et al. synthesized a MXene-based ternary system, CdS@Au/Ti3−xC2Ty, which was found to possess a high hydrogen production rate of 5371 μmol g−1 h−1 under visible light irradiation. The enhancement in the activity was attributed to the ‘dual Schottky barrier’ formed at the interface of the ternary system.35
p–n and non-p–n semiconductor heterojunctions
Depending on the type of semiconductors employed, there are two different forms of semiconductor–semiconductor heterojunction. The term ‘p–n heterojunction’ refers to the contact formed by p and n-type semiconductors. A ‘non-p–n junction’ is one in which there are two semiconductors, either n- or p-type, often possessing staggered band positions. For charge separation and collection, the p–n junction is an efficient architecture. At the interface, due to the diffusion of the holes and electrons, the p–n junction forms a space charge region, which creates an in-built electrical potential that directs the electrons and holes to travel in opposite directions.31
Metal–organic framework (MOF)-derived indium oxide/bismuth oxyiodide was employed by Sun et al. to create a p–n junction photocatalyst. The as-synthesized photocatalyst has shown robust activity against phenolic pollutants, which is attributed to the interfacial charge transfer and increased quantum efficiency at the p–n junction.21 Liang et al. reported the enhancement in the TiO2/NiO p–n junction efficiency by incorporating a Pt co-catalyst that resulted in higher photocatalytic hydrogen evolution activity and stability.36 Li et al. synthesized an NH2-UiO-66/CoFe2O4/CdIn2S4 composite material to construct a double p–n junction exhibiting dual-carrier transfer channels, which was found to have a higher efficiency towards photocatalytic hydrogen evolution.37 Tian et al. fabricated a facet-charge-induced coupling-dependent BiOI/g-C3N4 p–n junction, in which the catalyst with the {001} BiOI exposed facet was found to have a much higher photocatalytic activity towards industrial pollutants and antibiotic degradation than the catalyst having BiOI with the {110} facet.38
In the non-p–n junction, two semiconductors are generally coupled with the staggering band gap, which can be a type II heterojunction (vide infra).
van der Waals heterojunctions
After the discovery of graphene by Novoselov et al. in 2004, heterojunctions based on 2D sheet stacks of two different materials or multiple materials held by van der Waals forces were developed to enhance the performance of the individual components.39,40 Jia et al. synthesized the g-C3N4/BiLuWO6 heterojunction and investigated it in detail using theoretical studies.41 The theoretical and experimental studies confirmed the van der Waals heterojunction between the g-C3N4 and BiLuWO6. A Z-scheme served as the charge transfer mechanism (vide infra). The photodegradation of Rhodamine B and methylene blue was faster by the g-C3N4/BiLuWO6 van der Waals heterojunction than the individual phases (Fig. 3(A1–A5)).
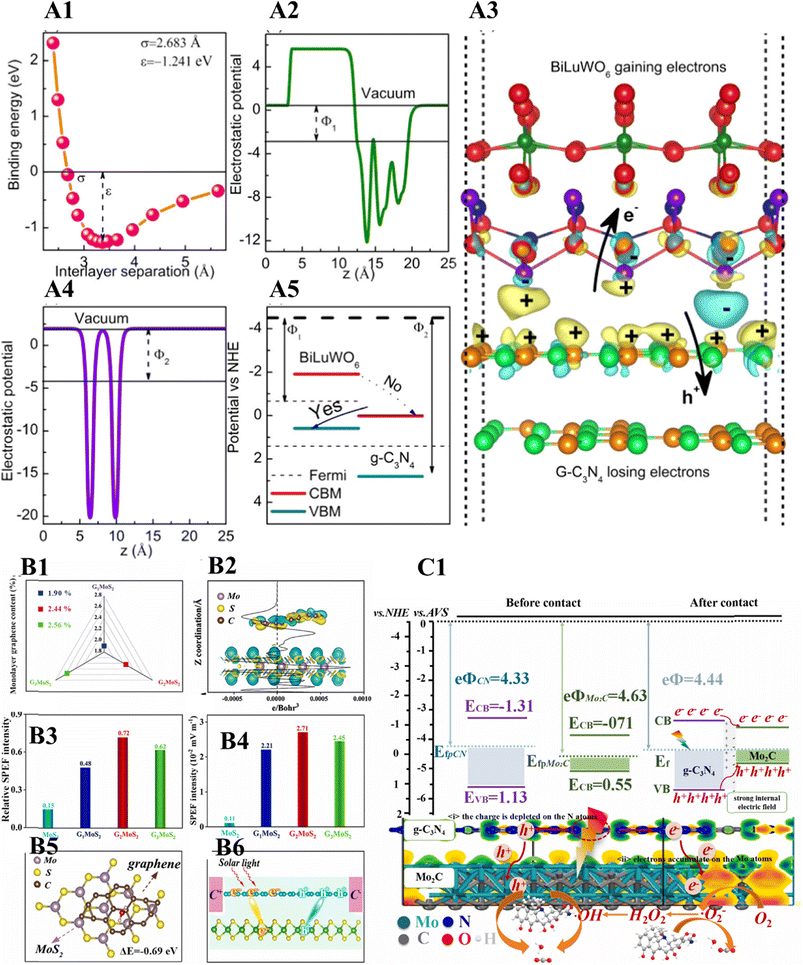 |
| Fig. 3 Binding energies (A1), electrostatic potentials (A2 and A4) of BiLuWO6 and g-C3N4, resulting Z-scheme (A5), charge density difference (with an isosurface value of 0.005 e bohr−3) and flow of excitons in the van der Waals heterojunction (A3). Reproduced with permission from ref. 41. Copyright 2021 American Chemical Society. Graphene contents (B1), differential and planar-average charge density (B2), relative SPEF intensity (B3), SPEF intensity (B4). H2O molecule adsorption on GmoS2 (top view, B5), migration and separation of excitons on GmoS2 (B6). Reproduced with permission from ref. 43. Copyright 2022 Elsevier B.V. 2D Mo2C/2Dg-C3N4 photocatalytic mechanism and charge transfer (C1). Reproduced with permission from ref. 42. Copyright 2021 Elsevier B.V. | |
Zhou et al. fabricated a 2D Mo2C/2Dg-C3N4 van der Waals heterojunction (see Fig. 3(C1)),42 which facilitated the interlayer electron transfer, building an internal electric field stimulating the photogenerated charge kinetics. The as-synthesized catalyst showed better activity for degrading waste pharmaceuticals and personal care products. Yao et al. fabricated a spin-polarized graphene monolayer-based van der Waals heterojunction on two-dimensional MoS2 (see Fig. 3(B1–B6)).43 The theoretical and experimental investigation confirmed that the photogenerated electrons and holes were separated and directionally transferred from MoS2 to the opposite regions of the monolayer graphene to form an ‘electric field’ via the van der Waals heterojunction. The as-synthesized heterojunction showed better results for overall water splitting. Xu et al. developed a simple protocol for fabricating Bi3O4Cl/g-C3N4 van der Waals heterostructures for effective CO2 photoreduction.44 A review article devoted to the theoretical studies on 2D van der Waals heterostructures for functional material and devices was reported by Hu et al.45
Facet heterojunction
Heterojunctions are also created within the same material but between two different facets. A study by Zhao et al. reported a decrease in charge recombination by forming a heterojunction between the {110} and {001} facets of BiOCl nanoplates.32 It was found that the facet ratio was crucial in determining photocatalytic activity.
By anchoring AgBr-Ag nanoparticles to the exposed {010} facets of BiVO4 microplates (Fig. 4(A1–A12)), a facet heterojunction was prepared, which showed an improved photocatalytic bacterial inactivation.46
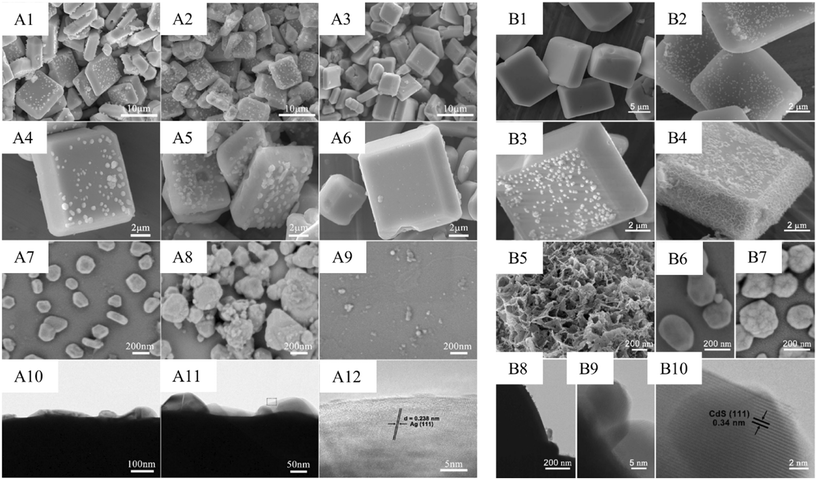 |
| Fig. 4 SEM images of Ag-BiVO4{010} (A1 and A4), AgBr-Ag-BiVO4{010} (A2 and A5), and Ag-BiVO4{010} (Na2S2O3 treated) (A3 and A6). FE-SEM images of Ag-BiVO4{010} (A7), AgBr-Ag-BiVO4{010} (A8), and Ag-BiVO4{010} (Na2S2O3 treated) (A9). HR-TEM images of AgBr-Ag-BiVO4 (A10–A12). Reproduced with permission from ref. 46. Copyright 2020 American Chemical Society. SEM images of BiVO4 (B1), Au-{010}BiVO4 (B2), CdS-Au-{010}BiVO4 (B3), CdS-Au-{010}BiVO4{110}-MnOx (B4), FE-SEM images of MnOx on {110} facet of CdS-Au-{010}BiVO4{110}-MnOx (B5), FE-SEM images of Au NPs on {010} facet of Au-{010}BiVO4 (B6). FE-SEM images of CdS-Au NPs on {010} facet of CdS-Au-{010}BiVO4{110}-MnOx (B7). HR-TEM images of CdS-Au-{010}BiVO4{110}-MnOx (B8–B10). Reproduced with permission from ref. 47. Copyright 2022 Elsevier B.V. | |
Luo et al. fabricated a facet heterojunction photothermocatalyst, CdS-Au-{010}BiVO4{110}-MnOx, for toluene degradation (see Fig. 4(B1–B10)).47 This was obtained by the selective deposition of CdS-Au and MnOx over the {010} and {110} facets of BiVO4 crystals, respectively. An adjustable {312}/{004} facet heterojunction was created by Gao et al. using multi-walled carbon nanotubes (MWCNTs) and Bi5O7I.48 Ofloxacin, a typical antibiotic, was degraded well when exposed to light due to the enhancement of charge separation by the S-scheme (vide infra). Zhang et al. deployed the directional loading of Cu2O on the [100] facet of BiOCl to create the facet heterojunction.49 Upon irradiation, electrons generated in Cu2O were transmitted to the [100] facet of BiOCl through the Z-scheme to result in the highly efficient photocatalytic synthesis of ammonia.
Types of heterojunctions based on the charge separation mechanism
Heterojunctions are also classified based on the band positions and charge transfer mechanism, which are discussed in this section.
Based on the position of the CB and VB, there are three major types of heterojunctions: type I (straddling gap), type II (staggering gap), and type III (broken gap), as shown in Fig. 5.
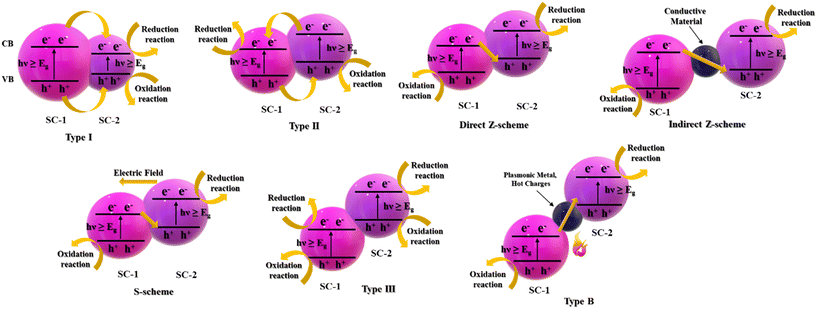 |
| Fig. 5 A composite schematic diagram depicting different types of heterojunctions classified based on the charge transfer mechanism. | |
Type I
In the type I heterojunction, a semiconductor component having a smaller bandgap is interfaced with a second semiconductor such that the CB and VB levels of the former lie between those of the latter, thus resulting in a straddling band alignment. Upon light irradiation with suitable energy, the photogenerated charge carriers of the second component (higher bandgap) hop to the first component (lower bandgap). This phenomenon causes charge accumulation in the component with the lower bandgap. It is generally regarded that the charge separation efficiency is relatively low in type I heterojunctions since all the charge accumulation occurs in one of the components.26,50 Nevertheless, the right choice of materials has shown better behaviour in the type I heterojunction systems when compared to the individual components. Zhao et al. fabricated ZnS@ZnIn2S4 core–shell cages with the type I heterojunction configuration, which resulted in the high absorption of the incident photons and effective separation of the photogenerated excitons, and thereby higher CO2 photoreduction activity.51 Another study reported a similar configuration in the CuO/BaTiO3 system, wherein the built-in potential at the nanointerface showed enhanced activity for methyl orange degradation and CO2 sensing properties. The enhancement was attributed to the compatible type I p/n heterojunction.52 Challagulla et al. reported a system comprised of a TiO2 shell supported over a Fe3O4 core, in which Fe2O3 formation was observed at the interface during the synthesis. While the Fe3O4 core facilitated the magnetic recovery and reusability of the photocatalyst, the type I heterojunction formed between TiO2 and Fe2O3 enhanced the photocatalytic Cr(VI) reduction under an aerobic atmosphere as compared to the individual components.53
Type II
The type II heterojunction is considered more effective than the type I counterpart. Due to the staggering band edge potentials, the charge carriers flow in opposite directions, resulting in effective charge separation. Consequently, many type II heterojunctions are reported in the literature due to the higher charge separation efficiency, resulting in improved photocatalytic activity.26,50 Zhang et al. prepared a type II heterojunction consisting of tin sulphide and the indium(III) sulphide, SnS2/In2S3, by deploying a one-pot hydrothermal synthesis method.54 This type II heterojunction between SnS2 and In2S3 resulted in the effective separation of the excitons, with 99.2 and 15.3 times higher photodegradation activity in Rhodamine B than the respective individual components. The same study reported the enhancement in the activity against tetracycline as 118.8 and 12.8-fold that of the SnS2 and In2S3, respectively. Liu et al. synthesized the BiVO4/Bi25VO40 composite material via an alkali-mediated dissolution–recrystallization strategy to achieve the intimate type II heterojunction with close interfacial contact. The obtained heterojunction facilitated effective charge transfer and spatial separation of the carriers, resulting in enhanced photocatalytic activity towards tetracycline.55 Huang et al. fabricated the type II heterostructure using a zirconium-based MOF and tungsten oxide (UiO-66-NH2@WO3) on a carbon cloth. They could remove 100% tetracycline from water within 60 min under visible light irradiation.20 Recently, Li et al. developed a ferroelectric Ag10Si4O13/TiO2 type II heterojunction and studied the methylene blue degradation under visible light irradiation.56 Various type II heterojunctions of g-C3N4 with different components were listed by Ong et al.26 The type II heterojunction has a drawback from a thermodynamics perspective, i.e., the improved charge separation is achieved at the expense of reduced redox potential. As the electron moves from the higher potential semiconductor component to a lower potential one, it will have a weak reduction potential, and similarly, a hole will have a weak oxidation potential with such a hopping process.57 Subsequent studies identified several strategies to overcome this issue, which were then recognized as the sub-types of type-II heterojunctions and termed as ‘Z-scheme’ and ‘S-scheme’ based on the charge transfer mechanism.
The concept of the Z-scheme photocatalytic system was initially proposed by Bard in 1979.58–60 The Z-scheme was inspired by the natural photosynthesis in green plants where 700 and 680 nm photons are harvested using photosystems I and II (PS-I and PS-II), respectively, oxidizing H2O to O2 under sunlight with a quantum yield close to unity.61 This system combines two different photocatalysts through a shuttle redox mediator.
In the Z-scheme, there is electron–hole recombination between the CB and VB levels that lie at the intermittent positions. Such a scenario makes the electron and hole occupying the respective higher CB and lower VB levels available for ROS generation. This heterojunction is preferable to the type II heterojunction in that it preserves the strong reductive and oxidative abilities of the electron and the hole, respectively.62 A Z-scheme comprising vanadium-substituted phosphomolybdic acid clusters/g-C3N4 nanosheets with effective charge separation and strong redox potentials was developed by Xing et al. and was utilized for the upcycling of polyethylene, which is an unusual and crucial application.63 The squandering of plastic is a potential threat to nature and explains the eminence of the heterojunction photocatalyst in this work. The Z-scheme is further divided into two types: ‘indirect Z-scheme’, in which the Z-type charge transfer is achieved through an electron mediator (conductors), and ‘direct Z-scheme’, in which no such electron mediator is employed.64
Several helpful review articles related to the Z-scheme charge transfer are available. Low et al. presented the Z-scheme evolution road map for photocatalytic systems from the first to third generations.59 Comprehensive details of the direct Z-scheme and various charge transfer mechanisms, such as internal electric field, interfacial defect-induced charge transfer, and facet-induced charge transfer, have been discussed in detail by Li et al.62 Zhang et al. summarized various Z-schemes dedicated to CO2 reduction reactions.64 Maeda described the historical development of photocatalytic water splitting driven by the Z-scheme.61 Zhou et al. provided a concise overview of all-solid-state Z-scheme photocatalytic systems, including composition, construction, optimization, and applications.65 Di et al. summarized the research progress in sulphide-based direct Z-scheme photocatalysts.66 A review by Ng et al. described the fundamental rationales in Z-scheme water splitting and challenges in the scaling up of the process,67 and several studies have deployed the Z-scheme for the high photocatalytic activity.68–71
Despite several advancements, the unwanted recombination of electrons and holes between the higher CB and lower VB levels was not fully avoided. Hence, a further sub-type, called the ‘S-scheme’, was introduced, in which an oxidation photocatalyst is coupled with a reduction photocatalyst. The oxidation photocatalyst has a higher oxidation potential, and the reduction photocatalyst has a higher reduction potential. The electron transfer in the S-scheme is like a ‘step’ from the macroscopic viewpoint and resembles the letter ‘N’ from the microscopic view. This novel S-scheme was discussed in detail by the synthesis of the ultrathin 2D/2D WO3/g-C3N4 by Fu et al.72 The interfacial charge transfer mechanism was investigated using ex situ and in situ irradiated X-ray photoelectron spectroscopy (XPS), electron paramagnetic resonance (EPR), and atomic force microscopy (AFM) employed in the potential mode.57 Xia et al. fabricated an S-scheme consisting of CeO2 quantum dots and polymeric carbon nitride (PCN).73 Charge transfer via the S-scheme was validated by XPS, and EPR experimental studies, which was further supported by the density functional theory (DFT) calculations. Higher antibacterial activity toward Staphylococcus aureus was seen under illumination as a result of the improved charge transfer.
Li et al. recently fabricated the TaON/Bi2MoO6 core–shell S-scheme and found that the material had high photocatalytic activity towards levofloxacin removal and Cr(VI) reduction.74 The enhancement in the activity is attributed to the S-scheme heterojunction resulting in the higher charge separation efficiency and, thereby, the higher redox potential of the photogenerated charges. TiO2/CsPbBr3 hybrids were fabricated by Xu et al. for CO2 photoreduction. The enhanced CO2 photoreduction results were attributed to the formation of the S-scheme heterojunction. DFT calculations and the experimental results confirmed the existence of the internal electric field (IEF) going from CsPbBr3 to TiO2. Upon irradiation, the IEF drives back the electrons from TiO2 to CsPbBr3, which was confirmed by in situ XPS experiments.75 By coupling inorganic and organic semiconductors, Cheng et al. created the S-scheme. They synthesized pyrene-alt-triphenylamine (PT) decorated with CdS nanocrystals, which showed robust hydrogen evolution activity. The charge transfer mechanism was probed in detail by the photoirradiated Kelvin probe measurement and in situ-irradiated XPS analyses.76
The selected recently published literature based on type I, II, Z-scheme, and S-scheme are presented in Tables 1–4.
Table 1 Representative literature on the type I heterojunction photocatalysts
Catalyst |
Band gap (optimal catalyst, eV) |
Catalyst loading |
Synthesis protocol |
Light source |
Pollutant/activity |
Pollutant/dye (conc.) |
Rate constant |
Ref. |
NA – not available. |
Fe2+-doped ZnFe2O4/ZnO |
1.78 |
1 g L−1 |
Two-step microwave-assisted solvothermal |
Sunlight |
RhB |
10 μM |
0.111 min−1 |
81
|
NixP/Mn3O4/g-C3N4/RP |
1.96 |
5 mg |
Two-step photochemical deposition |
300 W xenon lamp (with an AM 1.5G filter) |
Hydrogen generation |
10 mL of 20 vol% triethanolamine (TEOA) solution |
5851.3 mmol g−1 h−1 |
82
|
α-Ag2WO4/Ag3PO4 |
NA |
50 mg |
Coprecipitation method |
Visible light |
RhB |
50 mL, 10 mg L−1 |
0.504 min−1 |
83
|
P-doped g-C3N4/O-doped g-C3N4 |
NA |
50 mg |
Solid state synthesis |
300 W xenon lamp, 420 nm cut-off filter |
H2O2 production |
EtOH (5 mL) + water (45 mL) |
179 μM h−1 |
84
|
NiS/ZnIn2S4/g-C3N4 |
NA |
100 mg |
Solid state synthesis, solvothermal |
300 W xenon-arc lamp intensity: 120 mW m−2 |
H2 generation |
100 mL (80 mL deionized water and 20 mL TEOA) |
5.02 mmol g−1 h−1 |
85
|
BP QD/S doped g-C3N4 |
NA |
20 mg (AAP) |
Hard template-assisted solid state synthesis, ultrasound-assisted |
300 W Xe lamp 420 nm cut-off filter |
Amino acid production H2 evolution |
Amino acid production: 100 mL (100 mmol of lactic acid, 20 mL of 25 wt% ammonia solution, and deionized water), 45 °C under 1 bar N2 |
0.643 mmol h−1 (amino acid production) |
86
|
100 mg (H2 evo.) |
IR radiation: 300 W xenon lamp with 800 nm cutoff filter |
H
2
evolution: 100 mL of the aqueous solution of 10 vol% triethanolamine (TEOA) as a sacrificial agent |
102 μmol h−1 (H2 production) |
Ag2O–KNbO3 |
NA |
30 mg |
Hydrothermal, in situ deposition method |
Visible light irradiation |
Sulfamethoxazole (SMZ) degradation |
SMZ (5 ppm) aqueous solution |
0.0603 min−1 |
87
|
g-C3N4 quantum dots@SnS2 |
2.13 |
50 mg |
Hydrothermal, solid state synthesis |
500 W Xe lamp |
Bisphenol A (BPA) |
50 mL of BPA solution (10−5 M) |
0.472 h−1 |
88
|
O-doped g-C3N4/red P |
NA |
10 mg |
Solid-state synthesis, mechanical griding |
Xenon 300 W lamp |
Malachite green (MG) |
50 mL of MG aqueous solution (20 mg L−1) |
0.116 min−1 |
89
|
β-Ga2O3–TiO2–SiO2 |
2.95 |
4.0 g L−1 |
High temp. calcination, precipitation method, ball milling |
1. UV source, 2. Visible light |
p-Nitrophenol (PNP) |
25 mL, 25 mg L−1 |
0.62 mg g−1 min−1 (UV source) and 0.53 mg g−1 min−1 (visible light) |
90
|
PMPTA coated MIL-125(Ti) |
2.9 |
30 mg |
Solvothermal, solid state synthesis |
5.0 W 420 nm LED |
Selective oxidation of fluorene to fluorenone |
NHPI: 0.03 mmol, acetonitrile: 6 mL, fluorene: 0.3 mmol |
>99% conversion |
91
|
Boron nitride coupled Bi2MoO6 |
2.52 |
NA |
Solid-state synthesis, solvothermal, impregnation method |
Visible light |
Iohexol (IOH) degradation |
NA |
0.0160 min−1 |
92
|
2D/2D MoS2/CdS |
NA |
10 mg |
Precipitation–exfoliation process, ultrasonication |
300 W Xe lamp, cut-off filter (≥420 nm) |
H2 generation |
20 ml deionized water and 5 ml lactic acid |
18.43 mmol h−1 g−1 |
93
|
CdIn2S4/g-C3N4 |
2.4 |
NA |
Solid-state synthesis, hydrothermal synthesis, green wet-impregnation method |
300 W Xe lamp, 420 nm cutoff filter |
Reactive blue 19 (RB19) |
250 mL, 20 mg L−1 |
0.07357 min−1 |
94
|
2D BP/MAPbI3 |
NA |
30 mg |
Wet chemical synthesis, electrostatic adsorption |
300 mW cm−2 Xe lamp (λ ≥ 420 nm) |
H2 generation |
10 ml saturated HI solution containing 20 vol% H3PO2 |
3742 μmol h−1 g−1 |
95
|
CuO/BaTiO3 |
NA |
20 mg |
Hydrothermal synthesis, impregnation |
Rayonet RMR-3000, 300 nm, 4 W each with 6 in. in length |
Methyl orange (MO) |
1 × 10−5 M, 20 mL |
7.895 × 10−2 min−1 |
52
|
(2D/3D) metal-free (vdW) heterostructures based on triazine (C3N3) linkers |
1.91 |
10 mg |
Copper plate-based wet chemical synthesis |
300 W Xe lamp (L.O.T.-Quantum design) equipped with a cutoff filter of 395 nm |
H2 evolution |
18 mL, water : acetonitrile mixture (1 : 1) at room temperature, 2 mL triethanolamine is the sacrificial electron donor |
34 μmol h−1 g−1 |
|
ZnS@ZnIn2S4 |
2.65 |
5 mg |
Multistep wet chemical synthesis, hydrothermal |
300 W Xe lamp |
CO2 photoreduction |
NA |
CO production rate 87.43 μmol h−1 g−1 |
51
|
Table 2 Representative literature on the type II heterojunction photocatalysts
Catalyst |
Band gap (optimal catalyst, eV) |
Catalyst loading |
Synthesis protocol |
Light source |
Pollutant/activity |
Pollutant/dye (conc.) |
Rate constant |
Ref. |
Melem Nanorectangular prism-modified {Mo72Fe30} nanocapsule |
3.18 eV |
8 mg |
Acidic depolymerization, wet chemical synthesis, modified incipient-wetness procedure |
18 W full spectrum reptile light (LT) lamp |
H2O2 dismutation |
10 ml of an acetate buffer (0.1 M, pH = 3.0) containing 20.0 mM H2O2 (20 μL) |
17 mg L−1 O2 evolution in 3 h |
96
|
g-C3N4/Bi2MoO6 |
NA |
50 mg |
High-energy ball-milling process and corona poling post-treatment |
300 W xenon lamp, λ > 420 nm |
TC degradation |
50 ml of TC solution with a concentration of 20 mg L−1 |
0.0045 min−1 |
97
|
Ag/starched functionalized-Co3O4/NiFe2O4 |
NA |
2 mg (H2O2 production) |
Hydrothermal synthesis, co-precipitation method, wet chemical synthesis |
Cool white LED (1070 W m−2) light |
H2O2 production |
H
2
O
2
production: 600 μL suspension (from 5 mL DI water + 2 mg catalyst) + 5 mL DI water |
H2O2 produced 1660 μmol g1 h−1 |
98
|
2 mg (TC degradation) |
TC degradation |
TC degradation: 600 μL suspension (from 5 mL DI water + 2 mg catalyst) + 5 mL 10 ppm tetracycline solution |
TC rate is NA |
Carbon nanotube (CNT)-modified SrTiO3/Fe2TiO5 |
2.82 eV |
1.32 g L−1 |
Co-precipitation method |
Visible light |
MB, MO, RhB |
13.2 mg L−1 |
Degradation in 71 min |
99
|
MB 97% |
RhB 89% |
MO 64% |
Double-shell SnIn4S8/TiO2 |
NA |
20 mg |
Hydrothermal reaction of anhydrous glucose |
250 W xenon lamp (λ > 400 nm) |
MO, Cr(VI) photoreduction |
Cr(VI) solution (60 mL, 20 mg L−1) |
Degradation in 60 min |
100
|
Hydrolysis of TBT and calcination |
MO solution (60 mL, 15 mg L−1) |
MO (90.08%) 0.03005 min−1 |
In situ hydrothermal |
|
Cr(VI) (94.44%) 0.04628 min−1 |
UiO-66-NH2–WO3 |
NA |
3 cm × 5 cm |
Hydrothermal, solvothermal |
300 W Xe lamp, λ > 400 nm |
TC degradation |
100 mL, 20 mg L−1 |
0.0402 min−1 |
20
|
SnS2/In2S3 |
1.99 eV |
5 mg |
One-step hydrothermal |
Visible light, 300 W Xe lamp, UV cutoff >420 nm filter |
RhB, TC degradation |
50 mL RhB/TC (10 mg L−1) |
0.11716 min−1 (RhB) |
54
|
0.04280 min−1 (TC) |
BiVO4/Bi25VO40 |
NA |
0.1 g |
Hydrothermal synthesis, alkali treatment |
300 W Xe lamp, λ > 420 nm |
TC degradation |
100 mL TC, 30 mg L−1 |
0.01071 min−1 |
55
|
Nb2O5/g-C3N4 |
2.64 eV |
30 mg |
Multistep synthesis |
300 W Xe lamp |
Hydrogen generation |
80 mL of a 10 vol% TEOA aqueous solution containing H2PtCl6 |
2.07 ± 0.03 mmol g−1 h−1 |
101
|
CdS/ZnO |
NA |
0.1 g |
Wet chemical synthesis and hydrothermal |
Ultrasonic vibration, 40 kHz, 120 W |
RhB |
100 mL, 10 ppm |
0.067 min−1 |
102
|
I/BiOIO3/[Bi6O6(OH)3](NO3)3·1.5H2O (I/BiOIO3/BHN) |
NA |
50 mg |
Two step synthesis, solvothermal |
300 W Xe lamp |
RhB, MO, phenol, bisphenol A, bisphenol B, bisphenol Z |
RhB (5 mg L−1, 50 mL), MO (10 mg L−1, 50 mL), phenol (10 mg L−1, 50 mL) and bisphenols (10 mg L−1, 50 mL) |
0.1606 min−1 |
103
|
Magnetic 3-D ZnFe2O4/ZnO aerogel |
1.9 eV |
50 mg |
Aerogel formation, calcination |
300 W xenon lamp (PLS-SXE300/300UV) with a 400 nm cut-off filter |
Cr(VI) reduction |
100 mL Cr(VI) solution with the initial Cr(VI) concentration value of 100 mg L−1. 1 mL HCOOH, as the hole trapping agent, pH 2 |
87.0 × 10−3 h−1 |
104
|
Ag10Si4O13/TiO2 |
NA |
20 ppm of ASO/TO (2 : 1) catalyst |
Hybridization sol–gel method |
300 W xenon lamp, with an ultraviolet filter (λ > 420 nm) |
MB degradation |
5 ppm |
0.1147 min−1 |
56
|
Co-doped 3D petal-like ZnIn2S4/GaN |
NA |
Thin film (15 × 30 mm) |
MOCVD (metal–organic chemical vapor deposition), hydrothermal |
300 W Xe lamp, filter to cut off the light below 400 nm |
Chlortetracycline degradation |
50 mL, 20 mg L−1 |
0.00503 min−1 |
105
|
h-BN/flower-ring g-C3N4 |
NA |
20 mg |
Thermal polymerization |
300 W xenon lamp and filtered by a 420 nm filter |
TC degradation |
100 mL, 20 mg L−1 |
0.0703 min−1 |
106
|
SnS2/Bi2WO6 |
NA |
120 mg |
Hydrothermal, ultrasonication and thermal treatment route |
44 W LED, 5.3 mW cm−2, λ > 400 nm |
Glyphosate degradation tests |
300 mL of 10−4 mol L−1 |
0.0065 min−1 |
107
|
Bi@H-TiO2/B-C3N4 |
NA |
20 mg |
Solvothermal, calcination, thermal polymerization |
300 W Xe lamp covered by cutoff filter |
H2 production |
30 mL of triethanolamine aqueous solution (20 vol%, sacrificial agent) |
λ > 300 nm irradiation: 223.08 μmol g−1 h−1 under visible light (λ > 400 nm): 18.84 μmol g−1 h−1 |
108
|
CeO2/MIL-101(Fe) |
NA |
30 mg |
Hydrothermal calcination, solvothermal |
300 W xenon lamp with a 420 nm cut-off filter |
TC degradation |
100 mL, 20 mg L−1 |
TC degradation: 83.5%, 120 min |
109
|
CeOx/In2O3 |
2.43 eV |
50 mg |
Hydrothermal, wet impregnation |
500 W xenon arc lamp |
CO2 photoreduction |
CO2 (99.999%) and CH4 (99.995%), 0.3 bar above atmospheric pressure, the feed ratio of CO2 and CH4 was maintained at 1.0 |
CO and H2 produced 79 and 158 μmol gcat−1 in 5 h |
110
|
CdS/Cd-MOF |
2.29 eV |
10 mg |
Solvothermal |
Xenon lamp irradiation (200 W, λ = 320–1100 nm) |
MB degradation |
100 mL MB (20 mg L−1) |
0.023 min−1 |
111
|
ZnWO4/SnS2 |
2.37 eV |
Cr(VI) 50 mg |
Hydrothermal synthesis |
Under sunlight exposure |
MB, TC, Cr(VI) reduction |
100 mL of Cr(VI) (50 mg L−1), pH 2.5 |
Cr(VI): 0.061 min−1 |
112
|
TC 30 mg |
50 mL of TC (20 mg L−1) |
TC: 0.023 min−1 |
MB 30 mg |
50 mL of MB (20 mg L−1) |
MB: 0.055 min−1 |
Table 3 Representative literature on the Z-scheme type photocatalysts
Catalyst |
Band gap (optimal catalyst, eV) |
Catalyst loading |
Synthesis protocol |
Light source |
Pollutant/activity |
Pollutant/dye (conc.) |
Rate constant |
Ref. |
ZnS/ZnO nanosheets |
2.17 eV |
50 mg |
Solvothermal synthesis, heat treatment |
UV light |
Cr(VI) reduction, H2 generation |
Cr VI (Pot. dichromate 100 mg L−1) |
500 μmol h−1 g−1, Cr(VI) reduction 0.0078 min−1 |
113
|
NiO/α-MoO3 |
NA |
0.01 g |
Hydrothermal synthesis |
500 W Xe lamp |
MB degradation |
100 mL, 10 mg L−1 |
0.02685 min−1 |
114
|
AgInS2/AgIn5S8 QDs |
2.05 eV |
0.05 mg mL−1 |
Hydrothermal synthesis |
300 W Xe light, λ > 400 nm |
Cr(VI) reduction |
25 mL, 10 mg mL−1 |
2.01908 min−1 mol−1 |
115
|
CaTiO3/Cu/TiO2 |
3.37 eV |
30 mg |
Two step hydrothermal |
300 W Xe lamp, 300–1100 nm |
Hydrogen generation |
30 mL solution of 20 vol% MeOH, 80 vol% DW |
23.550 mmol g−1 h−1 |
116
|
CoTiO3/Zn0.5Cd0.5S |
2.33 eV |
10 mg, 25 mg (H2 production integrated with biomass derivative oxidation study) |
Multistep synthesis |
LED 3 × 30 W bulb, lambda max 450 nm |
Hydrogen generation |
40 mL aqueous solution of sacrificial electron donor (15 vol% lactic acid or 0.25 M Na2S/0.35 M Na2SO3) furfuryl alcohol (2 mg mL−1), 20 mL DI water |
1929 μmol g−1 h−1 |
117
|
g-C3N4/MoO3−x |
NA |
0.05 g |
Hydrothermal, two-step calcination |
300 W Xe lamp |
Hydrogen generation |
100 mL of 10 vol% TEOA aqueous solution |
209.2 μmol h−1 |
118
|
Ag/WO3/g-C3N4 |
NA |
40 mg L−1 |
Multistep synthesis, hydrothermal, calcination, photoreduction |
500 W Xe lamp, 420–800 nm |
Oxytetracycline hydrochloride |
10 mg L−1 |
0.1164 min−1 |
119
|
TiO2@C/g-C3N4 |
2.69 eV |
0.2 g |
One step calcination |
500 W Xe lamp, 420 nm cut-off filter |
NO removal |
100 ppm NO, 8% N2/air balance, 200 mL min−1 |
NA |
120
|
V-substituted phosphomolybdic acid/g-C3N4 |
NA |
10 mg |
Self-assembly strategy |
300 W Xe lamp, 420 nm cut-off optical filter |
Upcycling of various plastic wastes into high-value-added formic acid |
10 mL acetonitrile, 20 mg of polyethylene |
24.66 μmol g−1 h−1 |
63
|
Carbon dot decorated g-C3N4/TiO2 |
2.70 eV |
50 mg |
Simple burning, hydrothermal, |
Four LED lamps (3 W, 420 nm) |
Hydrogen generation |
80 mL triethanolamine aqueous solution (10 vol%), 34 μL H2PtCl6, pH 11 |
580 μmol h−1 g−1 |
121
|
Bi2WO6/InVO4 |
NA |
0.1 g |
Hydrothermal synthesis |
300 W xenon arc lamp with a 420 nm cut-off filter λ > 420 nm |
CO2 reduction |
5 mL deionized water, high-purity CO2 with a steady flow |
CO evolution rate: 17.97 μmol g− 1 h−1, CH4 production rate: 1.13 μmol g−1 h−1 |
122
|
Oxygen-doped carbon nitride/nitrogen-doped carbon dots/bismuth tetroxide |
NA |
0.05 g |
Hydrothermal synthesis, solid state synthesis |
300 W Xe lamp equipped with a UV cut-off filter |
TC, MO |
100 mL of TC or MO (10 mg L−1) |
TC 0.07 min−1 |
123
|
MO 0.304 min−1 |
Ag–ZnO/Bi2Sn2O7 |
NA |
50 mg |
Hydrothermal synthesis, ultrasonication, photodeposition |
300 W Xe lamp with a 420 nm UV-cutoff filter |
TC |
10 mg L−1 |
0.023 min−1 |
124
|
CQD/Bi12O17Cl2/NiAl-LDH |
3.14 eV |
50 mg |
Hydrothermal, precipitation |
300 W xenon arc lamp and a 3 AM 1.5 G filter |
CO2 reduction |
100 mL of deionized water, saturation with pure CO2 at 100 kPa for 30 min |
CO yield: 16.4 μmol g−1 h−1 |
125
|
Bi12O15Cl6/InVO4 |
NA |
40 mg |
Hydrothermal, calcination |
LED 450 nm |
TC, RhB |
100 mL, RhB (10 mg L−1) or tetracycline TC (20 mg L−1) |
TC: 0.01929 min−1 |
126
|
RhB: 0.03712 min−1 |
MnIn2S4 nanosheets/rods-like β-MnO2 |
NA |
15 mg |
Hydrothermal, in situ wet chemical synthesis |
350 W xenon lamp λ > 420 nm |
Cr(VI) |
20 mL Cr(VI) containing solution (50 mg L−1, pH = 5.6 ± 0.1) |
0.05814 min−1 |
127
|
Table 4 Representative literature on the S-scheme type photocatalysts
Catalyst |
Band gap (optimal catalyst) |
Catalyst loading |
Synthesis protocol |
Light source |
Pollutant/dye |
Pollutant/dye (conc.) |
Rate constant |
Ref. |
SnS2/RGO/g-C3N4 |
NA |
10 mg |
Photoassisted self-assembly |
300 W Xe lamp, cutoff filter: 420 nm < λ < 780 nm |
RhB, H2 generation |
50 mL, 10 mg L−1 |
0.55 min−1 |
128
|
CdS QDs/Bi2WO6 |
NA |
0.2 g |
Hydrothermal synthesis |
PLS-SXE 300 Xe-lamp |
Ethylene |
50 μL |
0.384 min−1 |
129
|
Co9S8/In2O3 |
NA |
10 mg |
Solution synthesis, high-pressure reactor, hydrothermal synthesis |
5 W white light, 420 nm or above |
Hydrogen generation |
20 mg Eosin Y, 30 mL sacrificial reagent aqueous solution (15 vol% TEOA) |
277.77 μmol in 5 h |
130
|
NH2-UiO-66/SiC |
NA |
20 mg |
Microwave synthesis |
300 W Xe lamp, λ > 420 nm |
CO2 reduction |
0.084 g NaHCO3, 0.3 mL H2SO4 (aq 2 M) |
7.30 μmol g−1 h−1 |
131
|
CdS QDs/Bi2MoO6 |
NA |
0.2 g |
Hydrothermal synthesis |
Xe lamp |
Ethene |
50 μL |
0.06036 min−1 |
132
|
In4SnS8/Cs3Bi2Br9 |
NA |
10 mg |
Wet chemical synthesis, in situ hydrothermal |
300 W argon lamp (λ > 420 nm) |
CO2 reduction |
99.999% pure CO2 gas inside the vessel at 80 kPa |
CO yield: 9.55 μmol g−1 h−1 |
133
|
NiIn LDH/In2S3 |
1.36 eV |
5 mg |
Wet chemical synthesis, hydrothermal |
300 W Xe lamp |
CO2 reduction |
Ultra-pure CO2 (>99.999%) |
CO yield: 29.43 μmol g−1 h−1 |
134
|
Co2P/PC-b-TiO2 |
3.07 eV |
50 mg |
Hydrothermal synthesis, calcination |
300 W Xe lamp, with a standard AM 1.5 filter |
Hydrogen generation |
100 mL of a mixed solution containing distilled water and TEOA with volume ratio of 9 : 1 |
1.53 mmol g−1 h−1 |
135
|
O-doped g-C3N4/N-doped Nb2O5 |
2.81 eV |
NA |
One-step polymerization, hydrothermal synthesis, surface charge-induced hetero-aggregation |
300 W xenon lamp |
CO2 reduction |
0.12 g of NaHCO3, 0.35 M HCl for the in situ production of CO2 and H2O gas |
Production rates CO: 253.34 μmol g−1 h−1 CH4: 68.11 μmol g−1 h−1 |
136
|
0D/3D Bi3TaO7/ZnIn2S4 |
NA |
50 mg |
Hydrothermal, two-step solvothermal method |
300 W Xe lamp with a 420 nm cut-off filter (λ > 420) |
TC degradation, simultaneous H2 generation |
100 mL TC solution (10 mg L−1) |
TOC removal efficiency of 36% after 180 min |
137
|
H2 evolution: 13.7 μmol g−1 h−1 |
ZnIn2S4–NiSe2/Ti3C2 |
NA |
2 mg |
Hydrothermal synthesis, wet chemical synthesis |
Xe lamp (300 W, λ > 420 nm) with a 420 nm cut-off filter |
Hydrogen generation |
80 mL ascorbic acid aqueous solution (80 mL, 1.73 wt%) anaerobic environment |
23.51 mmol g−1 h−1 |
138
|
Hexameric AgBr/Zn–Al MMO |
NA |
20 mg |
Wet chemical synthesis, in situ co-precipitation |
Xenon lamp (Perfect Light, Microsolar300, 320–780 nm, 100 mW cm−2 equipped with a UVIR cut 420 quartz coated filter) |
TC, MO, MB |
100 mL TC solution (10 mg L−1) |
TC removal rate 95% within 60 min |
139
|
Zn3In2S6/Bi2O3 |
NA |
50 mg |
Hydrothermal synthesis |
300 W Xe lamp (λ > 400 nm) |
Metronidazole, Cr(VI) |
10 mg L−1, pH 5 |
Metronidazole 0.0389 min−1, Cr(VI) 0.05409 min−1 |
140
|
TiO2–X/BiOI |
NA |
0.05 g |
Sol–gel, solvothermal, solid state synthesis |
PLS-SXE300C xenon lamp using AM 1.5 (λ = 300–800 nm) |
H2 generation |
100 mL of 15 vol% aqueous methanol, 1 wt% Pt by in situ photo deposition |
804.30 μmol g−1 h−1 |
141
|
ZnO/COF |
NA |
0.5 g L−1 |
Precipitation reaction, wet chemical synthesis, electrostatic self-assembly |
300 W xenon lamp (AM 1.5, 45 mW cm−2) |
H2O2 production |
Aqueous ethanol (10 vol%) as an electron donor |
2443 μmol g−1 h−1 |
142
|
Type III
The type III heterojunction resembles the type II heterojunction in several ways, except that the CB and VB levels are positioned so that the band gaps of the semiconductor components do not intersect. Consequently, a stronger driving force is required for the charge transfer.26,77 To circumvent this, the researchers employed a unique strategy of interfacing two semiconductors through metal nanoparticles to facilitate charge transfer by bridging the two components. Such a sub-type configuration was termed a ‘Type B’ heterojunction. Li et al. employed the ‘Type B’ heterojunction by introducing Ag nanoparticles (Ag NPs) into the Ag3PO4/GdCrO3 type III heterojunction to enable the photothermal plasmonic resonance-assisted transfer (PTPRT) process. The study found that Ag3PO4/Ag/GdCrO3 exhibited a 22-fold higher photothermocatalytic degradation rate of toluene as compared to Ag3PO4/GdCrO3, besides high efficiency towards volatile organic compound degradation and CO2 reduction. The substantial temperature and local surface plasmon resonance (LSPR) from silver nanoparticles were attributed to facilitating the ballistic transport of electrons across the PTPRT channel, leading to higher efficiency.78 In a different investigation, the same group reported a series of type B heterojunctions, namely, CuWO4/Ag/GdCrO3, WO3/Ag/GdCrO3, and Bi2WO6−xF2x/Ag/GdCrO3, wherein WO3/Ag/GdCrO3 was found to exhibit more photothermocatalytic toluene degradation and CO2 reduction as compared to the WO3/GdCrO3 type III heterojunction.79 A recent study by the same group reported the formation of defect sites at the interface of WO3−x and GdCrO3 to create a type B heterojunction, which enabled storage, secondary excitation, and interband transfer of the photothermal-induced charges. The as-developed defect band bridge exhibited excellent photothermocatalytic performance for CO2 reduction and volatile organic compound degradation.80
In a nutshell, the various heterojunctions discussed so far have several advantages and disadvantages. Depending on these factors, they can be employed for suitable applications with the wise choice and combination of various materials discussed in the ‘Library of materials used for heterojunction formation in photocatalysis’ section. A Schottky barrier can be deployed where the unilateral flow of electrons in a forward-biased direction is required, resulting in efficient charge separation. However, in ohmic contacts, the electron flow in forward and reverse-biased directions can be obtained, eventually resulting in poor charge separation and photoresponse. In this scenario, p–n junctions can offer efficient charge separation and collection.
van der Waals heterojunction can provide interlayer electron transfer in 2D materials for improved photocatalytic activity. Moreover, photogenerated charge kinetics can be stimulated by building an internal electric field in 2D materials. The facet heterojunction is a relatively different form of heterojunction; usually, in heterojunctions, two components are involved but with facet heterojunctions, a single component with two different facets with a suitable energy match can be deployed to form the heterojunction as discussed earlier. The type I heterojunction has several disadvantages such as low charge separation and a lower band gap component, which will have charge accumulation and a compromised redox potential. Compared to the type I heterojunctions, the type II heterojunctions are superior due to effective charge separation and uniform charge distribution in both components; however, there will be a compromise in terms of the redox potential of the excitons. For a high redox potential, the Z-scheme is a suitable alternative; however, charge recombination is not completely averted, so the S-scheme is the preferred option with enhanced separation efficiency and light absorption. The higher efficiency due to the photothermal plasmonic resonance-assisted transfer (PTPRT) process can be achieved using a type III heterojunction.
The detailed charge transfer mechanism is of utmost importance for the effective fabrication of the heterojunction and can be studied in detail using ultrafast transient absorption microscopy, as discussed in the following section.
Detection of carrier transport across heterojunctions
The heterojunction is widely used in photocatalysis, as discussed above, and is an essential phenomenon in catalysis and optoelectronic devices. The understanding of the charge and energy transport across the semiconductor heterojunction is of great importance for the effective application of heterojunctions in catalysis and various optoelectronic devices. The charge dynamics and transport across the heterojunction can be investigated using ‘ultrafast transient absorption microscopy (TAM)’. By deploying such techniques, the carrier diffusion of the individual material through the interface can be visualized. TAM investigation can directly quantify charge transmission through heterostructures. Such investigations have revealed that around 20% of the carrier population is lost due to interfacial energy barriers and defect recombination. Detailed investigations of various reported heterojunctions using TAM can give information on the efficiency of the heterojunction.143–145 Moreover, an in situ dynamic study can reveal critical parameters such as the lifetime of the excited state, hole trapping and interfacial electron transfer.146
Library of materials used for heterojunction formation in photocatalysis
The recent trends in materials used to create heterojunctions for photocatalysis are detailed below. Various classes of materials are briefly addressed with illustrative instances, while their categorization by the mechanistic heterojunction is provided in Tables 1–4.
Metal oxides
After the pioneering works by Muller, Honda, and Fujishima, various photocatalytic systems based on TiO2 and several other oxides were developed.7,8,147–152 AEROXIDE TiO2 P25 is often considered the ‘gold standard’ in photocatalysis, which possesses a heterojunction between anatase and rutile polymorphs. The marketed anatase to rutile weight ratio is 80
:
20.153,154 Since then, metal oxides have been front liners in photocatalysis owing to their high chemical stability and non-toxicity. Several oxides such as Fe2O3, WO3, CuO, Bi2O3, SnO, ZrO2, V2O5, and Ni2O3 are frequently used in photocatalysis.4,155–163 Kannan et al. provided a brief historical overview of nanostructured metal oxides and their composites used in photocatalytic and biological applications.164 A detailed discussion on the regulation of the physiochemical properties of metal oxide nanomaterials was given by Chen et al.165
Perovskites
Perovskites (ABX3) are another class of materials that are routinely deployed for photocatalytic applications. The commonly used perovskites for photocatalysis are LaFeO3, LaMnO3, LaCoO3, SrTiO3, BaTiO3, BiFeO3, CaTiO3, etc.166–168 More details regarding the perovskites for photocatalysis are given by Schanze et al.169 Due to their superior performance in solar cells and LED devices, metal halide perovskites have recently gained a lot of attention as a novel class of material. Various organic–inorganic and all-inorganic metal halide perovskites, such as CH3NH3PbX3 and CsPbX3, (X = Cl, Br, I), have emerged as potential candidates for different photocatalytic reactions. The exciting features of the metal halide perovskite are the redox potentials of the photogenerated holes and electrons, which can be tuned by changing the halogens. Moreover, when the size of the metal halide perovskite is smaller than the Bohr radius, it shows the multiexciton generation effect and hence supplies adequate charge carriers for multielectron redox reactions. Wang et al. provided a comprehensive review of the metal halide perovskites employed for photocatalytic H2 evolution, CO2 reduction, organic transformation, and organic pollutant degradation.170
Chalcogenides
Chalcogenides are widely recognized for their small band gap energy and are composed of at least one chalcogen (S2−, Se2−, or Te2−). Due to their non-toxicity, biocompatibility, affordability, and ease of synthesis, they have received much research attention. Depending on the number of elements in the composition, the chalcogens are generally classified broadly as binary (e.g., ZnS, CuS, Cu2Se, Ag2Se, etc.), ternary (e.g., Zn0.5Cd0.5S, Ba2ZnSe3, BaAu2S2, CuFeS2, etc.) and quaternary (e.g., Cu2FeSnS4, Cu2ZnSnSe4, etc.). Various heterostructures have been reported for photocatalytic activity (Ag/Ag2S/CuS, Ag2S/AgInS2, AgInS2 quantum dots/In2S3, etc.). The review by Rahman et al. discusses recently discovered chalcogenides for photocatalysis.171 The progress on the wide band gap chalcogenide (band gap, Eg > 2 eV) was summarized in detail by Woods-Robinson et al.172
Besides the abatement of organic pollutants, the field of organic transformations employing photocatalysis is also a fascinating avenue.173 Using the commercially available CdSe photocatalyst, Muralirajan et al. demonstrated the highly selective trifluoromethylation of (hetero) arenes and alkenes. The theoretical simulation predicts that Janus XMMX' monolayers of group III chalcogenides are suitable for photocatalytic water splitting. Among them, SGa2Te, SeGa2Te, SIn2Te, and SeIn2Te monolayers are direct gap semiconductors, with the band gap ranging from 1.54 to 1.91 eV. These monolayers exhibit better visible light absorption and suitable band edge positions for photocatalytic water splitting.174 The review by Chen et al. provides a thorough overview of multinary metal chalcogenides with tetrahedral structures and their uses in photocatalysis, photovoltaics, and second-order nonlinear optical applications.175
The compounds with the MQX stoichiometry, where M = As, Sb, and Bi; Q = O, S, Se, and Te; and X = F, Cl, Br, and I, are known as heavy pnictogen chalcohalides. Pnictogen chalcohalides are a family of compounds with a wide band gap and a layered or chain-like structure. They are synthesized by a straightforward synthetic process and are stable. Their electrical and optical properties can be tuned by halogen or chalcogen exchange. The chalcopyrites, kesterites, and chalcohalides are relatively less explored as compared to the perovskites but their structure and properties are well-suited for photocatalysis and other applications.176
MOFs and COFs
MOFs are a class of crystalline, extremely porous organic–inorganic hybrid materials. By selecting the appropriate metal node and organic linker, the MOF's framework structure, functionality, and porosity may be adjusted. With their straightforward amalgamation of metal nodes and organic linkers, MOFs exhibit extraordinary characteristics. As a result, they are frequently employed in a variety of biological and energy-related applications, as well as in adsorption and separation processes.177 Currently, researchers are showing interest in creating MOFs with two metal ions, which provide additional functionality. The bimetallic MOFs utilized for various purposes have been outlined by Manan Ahmed.178 Similar to MOFs, COFs have also been gaining popularity in recent times. They form a three-dimensional network and are majorly governed by both covalent and non-covalent interactions; covalent bonds control the primary-order chain structure, and non-covalent forces create the morphology in the system. The reader is encouraged to go through the extensive assessment of COFs by Geng et al.179
The available synthetic methods for the fabrication of the MOF/graphene heterojunction for electrocatalysis and photocatalysis have been summarized by Wang et al.,180 and g-C3N4/MOF-based heterojunctions are outlined by Zhang et al.181 MOFs deployed for photocatalysis under visible light illumination have been summarized by Wang et al.182 The versatile synthesis of MOF-based coatings for broad applications was reviewed by Meng et al.183
Several properties of the MOFs and COFs, such as high surface area, a defined pore structure, and several adsorption sites, make MOFs and COFs ideal components for adsorption control in photocatalysis. Moreover, several organic ligands are highly useful for the various functionalizations to control light harvesting properties in the region of interest of the entire light spectrum. These make MOFs and COFs ideal candidates for photocatalysis.184
Many physical and chemical properties shown by the metal ions are of immense importance for various applications. Since COFs do not exhibit such characteristics, metalated COFs are often fabricated to induce the desired properties. All the aspects of such metalated COFs can be found in the review by Guan et al.185 Comprehensive reviews of various COF catalysts deployed for photocatalytic and electrocatalytic carbon dioxide reduction are available in the literature.186,187 Considerable reviews in the field of COFs are available for energy and environmental applications.179,188–196
MOF/COF heterostructures have better properties than solo MOFs and COFs because of synergism. As a result, MOF/COF-based hybrids have seen rapid advancement and have been attracting growing attention in recent years. The design principles, synthetic methods, assembly procedures, and applications of the MOF/COF-based hybrids have been thoroughly reviewed by Guo et al.197 Various composites of the COF, such as COF/MOF, COF/g-C3N4, and COF/metal–semiconductors, have been studied by Hu et al.198
MXenes
Since their discovery, MXenes have been widely studied for various applications.199 Exceptional properties such as thermal and electrical conductivity and a large surface area make MXenes suitable for different applications, including bioapplications and heterojunction formation. The preferred notation for MXenes is Mn+1XnTx, where ‘M’ stands for early transition metals (Ti, Sc, Zr, Hf, etc.), ‘X’ for carbon or nitrogen, and ‘Tx’ represents the terminal groups like F, Br, O, S, and OH. To date, a variety of MXenes have been fabricated, including Ti3C2, Ti2C, and Nb2C.200,201
The large specific surface area and suitable optical and electronic characteristics make MXenes the most promising emerging materials in the field of photocatalysis. Moreover, good conductivity due to conducting nuclei in multilayer structures and various terminating functional groups makes MXenes promising photocatalysts.202
Comprehensive details on MXene-based photocatalysts have been reported by You et al.203 Jin et al. have reviewed the various heterostructures of MXenes and transition metal chalcogenides such as SnS, NiS, MoS2, FeS2, and NiSe2 with special emphasis on surface/heterointerface engineering for various applications such as batteries, supercapacitors, electrocatalysis, and photocatalysis.204 Several 2D and 3D MXenes have been explored and summarized in multiple reviews.205–210
Carbides and nitrides
Binary and ternary phases of metal carbides and nitrides are intriguing for catalytic applications. They are frequently discussed together due to their structural resemblance. The binary phases can generally be described by the location of C or N within the interstitial sites of close-packed metal lattices. It is claimed that carbides and nitrides are more resistant to poisoning, though not always, as compared to noble metals.211 Zhang et al. reported the recovery of SiC from a silicon waste slurry and found that it mainly consisted of 3C-SiC and 6H-SiC, with the surface primarily consisting of silicon oxycarbides.212 The as-recovered SiC was proved to be a promising photocatalyst for hydrogen production. The carbides of molybdenum, such as Mo2C, MoC2, MoC, etc., are important candidates due to their similar electronic structure to the noble metal platinum, which is highly useful for photocatalytic hydrogen production. Moreover, molybdenum carbides show remarkable properties such as adsorption, desorption, activation, and the ability to transfer hydrogen. Mo2C forms an effective heterojunction with CdS and promotes the charge separation, resulting in the enhancement in the photocatalytic activity.213 Porous silicon carbide has been used widely as summarized by Tuci et al.214 Other carbides such as niobium carbide,215 boron carbide,216 tungsten carbide,217–221 silicon carbide,222–227 vanadium carbide,228 and titanium carbide229 have also been reported for photocatalytic applications.
Almost all metals can combine to form a binary nitride, except for noble metals and alkali metals other than lithium. There are several known ternary and quaternary inorganic nitrides, which are considered “synthetic” materials since they do not exist in nature due to their thermodynamic instability towards oxidation. Co2N was used as a co-catalyst in the Co2N/BiOBr system by Di et al. towards photocatalytic CO2 reduction.230 It was shown that Co2N could interact strongly with BiOBr electrically, promoting the efficient flow of electrons from BiOBr to Co2N and to the surface. Liu et al. fabricated one-dimensional Co4N–WNx–CdS composites by a simple yet efficient electrostatic self-assembly. The resulting catalyst showed high conductivity and was enriched with active sites, resulting in a high rate of photocatalytic hydrogen evolution (14.42 mmol g−1 h−1) under vacuum conditions.231 Rao et al. discussed the overview of the nanostructured metal nitrides for photocatalytic H2 generation and CO2 reduction.232 Cheng et al. summarized recent research on transition metal nitrides.233 Numerous nitrides have been used in photocatalytic applications with success.234–242 GaN has been extensively studied for light-emitting device applications; however, it is now amply explored for photocatalysis as well.243–250 Apart from the inorganic semiconductors, a polymeric nitride material, graphitic carbon nitride (g-C3N4), has been highly explored for photocatalysis and heterojunction formation.251–258
Phosphides
The comprehensive synthetic strategy for various metal phosphides and their catalytic applications can be found in the review by Li et al.259 Callejas et al. demonstrated that iron phosphide (FeP) with a uniform hollow morphology exhibited high-efficiency for the hydrogen evolution reaction both electrocatalytically and photocatalytically.260 Under UV illumination in both acidic and neutral conditions, such FeP nanoparticles deposited over TiO2 were found to exhibit H2 production at rates and amounts comparable to that of Pt/TiO2. Ni2P and Ni12P5 were synthesized via a hydrothermal route, and the phases were controlled by varying the reaction conditions. It was observed that Ni2P possessed high photocatalytic activity as opposed to Ni12P5.261 The excellent synergism between ternary metal phosphides NixCo1−xP and Zn0.5Cd0.5S nanorods resulted in effective photocatalytic hydrogen production. The effective charge separation and transfer were achieved due to the coordination bonds formed on the surface of the optimized composition of Zn0.5Cd0.5S and Ni0.1Co0.9P.262 The Schottky heterojunction in the MoP–Cu3P system was reported to yield high photocatalytic activity in hydrogen generation with a production rate of 855 μmol h−1 g−1.263 Apart from these, several other phosphides have been explored for photocatalytic applications and used as co-catalysts.264–274
Layered double hydroxides (LDHs)
Layered double hydroxides (LDHs) or hydrotalcite-like compounds are a prominent family of 2D anionic clay materials that can be represented by the general formula [M1−x2+Mx3+(OH)2]x+[Ax/n]n−·mH2O. They are composed of brucite-like layers in which the fraction of the divalent cations (e.g., Mg2+, Fe2+, Co2+, Cu2+, Ni2+, or Zn2+) are coordinated octahedrally by hydroxyl groups. The divalent cations have been replaced isomorphously by the trivalent ones (e.g., Al3+, Cr3+, Ga3+, In3+, Mn3+, or Fe3+), giving rise to positively charged layers. The value of x is the molar ratio of M2+/(M2+ + M3+) and will be in the range of 0.2–0.33. The LDH can be synthesized via a simple, well-established protocol such as co-precipitation and homogeneous precipitation by urea hydrolysis.275
LDHs are 2D materials with various scopes for modification due to their unique layered structures. Their high adsorption capacity, tunable band gap, superior cation–anion exchange capacity and separate oxidation and reduction sites make them potential photocatalysts.276
Zhao et al. detailed the tailoring of the electronic properties of LDH through the introduction of surface defects for the enhancement of photocatalytic properties.277 Highly informative review articles on LDH-based photocatalysts are available in the literature.276,278–285
Other methods of fabricating heterojunctions
In general, a heterojunction architecture can be either a core–shell286–288 or a uniform blend.289–291 Depending on the dimensions of the morphology of individual components, various 0D/1D,292–296 0D/2D,297–300 0D/3D,301–304 1D/1D,305 1D/2D,306–308 1D/3D,309 2D/2D,310–312 and 3D/2D313 heterojunctions have been reported (Fig. 6). Apart from the aforementioned methods, several other methods have been reported for synthesizing intimately mixed semiconductor-based heterojunctions, and a few representative ones from our group are presented herein.
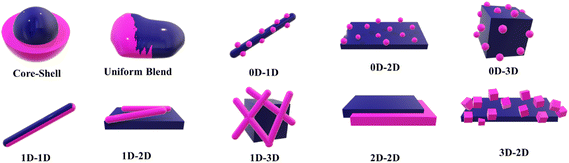 |
| Fig. 6 A schematic depiction of various heterojunction structures based on morphology. | |
Our group has recently developed a few synthetic strategies for obtaining intimately mixed composite materials to achieve effective heterojunctions. Composites of g-C3N4/AgBr are known to exhibit good photocatalytic properties; however, the conventional synthetic procedure involves a solution-based adsorption/precipitation method that results in the particle size of AgBr in the range of 5 to 50 nm. We devised a novel single-step synthesis in which melamine (precursor of g-C3N4) was intimately mixed with a tetraoctylammonium bromide–Ag complex (AgBr precursor). This solid-state approach utilized the thermal decomposition of the physically grounded precursor mixtures to obtain g-C3N4/AgBr composites, wherein highly-dispersed AgBr having a size of ∼1 nm in the g-C3N4 matrix exhibited efficient photocatalytic disinfection characteristics under both dark and light conditions.290 The high dispersion of the AgBr was attributed to the surfactant-based precursor that dramatically reduced the interfacial tension during the process. In another study, g-C3N4/Ag2S nanocomposites were synthesized by physically mixing melamine and silver amyl xanthate (Ag2S precursor) and subjecting the resultant mixture to a one-step calcination process.291 In this method, a significantly lower loading of Ag2S than the theoretical estimate was observed, a factor that was attributed to the sublimation tendency of the sulphide. As a result, a two-step method was also explored, in which the Ag2S precursor was physically mixed thoroughly over a pre-formed g-C3N4, which was then subjected to calcination. The nanocomposites obtained through the two-step method were found to result in an effective heterojunction that was proven by the enhancement in the density of states and minimization of the electron–hole recombination. These nanocomposites exhibited remarkable bactericidal efficacy under dark and visible light irradiation conditions.
Our group also fabricated a core–shell architecture via a solid-state synthesis, in which melamine was physically mixed with a pre-formed ZnO core.314 The thermolysis of the obtained blend resulted in the formation of a nitrogen-deficient g-C3N4 shell, which formed an effective heterojunction with the ZnO core and was found to be responsible for the higher photocatalytic activity. In another study, by employing a customized sol–gel synthesis, we reported the formation of a heterojunction between the three polymorphs of TiO2, namely, anatase, rutile, and brookite.315 All three polymorphs and the phase composition were controlled through the thermal pretreatment of the gel. The enhancement in the photocatalytic activity of the triphasic TiO2 was attributed to the effective heterojunction between the three polymorphs. Francis et al. reported the formation of the MOF-derived CuO/AgX (X = Cl, Br, I) nanocomposite to obtain a type I heterojunction. Calcination of silver halide-loaded Cu-BTC MOF was found to yield intimately mixed CuO/AgX nanocomposites, which showed high photocatalytic activity attributed to the effective type-I heterojunction formed.316
Applications of heterojunction catalysis
Advancements in heterojunction catalysis allow for the precise tuning of catalyst characteristics, such as surface area, adsorption, functionalization, light absorption in UV, IR, or visible regions, and exciton redox potential, to suit various applications. Heterojunction catalysts have proven effective in diverse applications, including dye degradation, CO2 reduction, NOx manipulation, organic transformation and hydrogen generation (Fig. 7).317,318 Organic transformation over heterojunction photocatalysis is also a promising avenue, considering the generation of waste to value-added products.319
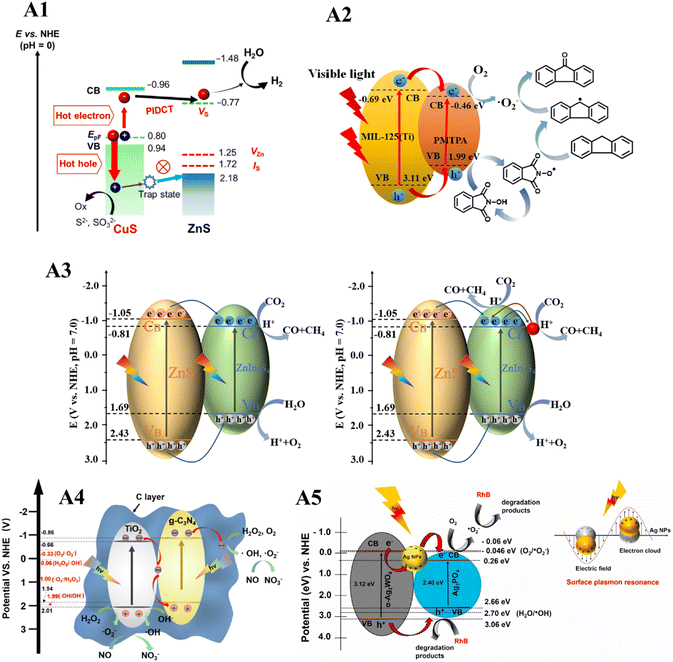 |
| Fig. 7 Various applications of heterojunction catalysts. Plasmon-induced defect-mediated carrier transfer in CuS@ZnS core@shell nanocrystals for IR light responsive photocatalytic reaction (A1). Reproduced with permission from ref. 145. Copyright 2023 American Chemical Society. Fluorene photo-oxidation over MP-30 and N-hydroxyphthalimide (NHPI) (A2). Reproduced with permission from ref. 91. Copyright 2021 Elsevier B.V. CO2 photoreduction over 3-ZnS@ZnIn2S4 core–shell cages (left), and 3-ZnS@ZnIn2S4/Au core–shell cages (right) (A3). Reproduced with permission from ref. 51. Copyright 2021 Elsevier Inc. Activation of hydrogen peroxide for NO removal over Z-scheme heterojunction catalyst TiO2@C/g-C3N4 (A4). Reproduced with permission from ref. 120. Copyright 2021 Elsevier B.V. RhB degradation using developed heterojunction catalyst α-Ag2WO4/Ag3PO4 (A5). Reproduced with permission from ref. 83. Copyright 2022 Elsevier B.V. | |
Tables 1–4 provide a comprehensive list of applications, including the type of heterojunction used, kinetic data of the reaction and other relevant reaction parameters employed.
Conclusions and future outlook
The field of heterojunction photocatalysis has evolved with the advent of various spectroscopic techniques and recent advances in simulations, which have facilitated the understanding of the plausible charge transfer mechanism(s) between the coupled semiconductors. As a result, several effective heterojunctions have been developed for various applications such as organic pollutant abatement, water splitting, organic transformations, and CO2 & NOx reduction.
Following are a few excerpts from the various types of heterojunctions based on the charge transfer mechanisms mentioned in the review.
Type I: Enhances the charge separation, and the charge density is greater in the component with a narrow band gap, compromising with the redox potential.
Type II: Enhances the charge separation and light absorption with a near-uniform distribution of charges in both components, but compromises with the redox potential.
Z-scheme: Enhances the separation efficiency, improving light absorption and maintaining strong redox ability. However, the recombination of charges from the overall higher CB and lower VB is not completely averted.
S-scheme: Enhances the separation efficiency and light absorption while maintaining the high redox capability of the electrons and holes and providing an electric field at the interface for the recombination of charges with lower redox potential.
Type III: No/inefficient charge separation owing to broken gap band positions, which can be circumvented efficiently by adding a conducting component as the source of the hot charge transfer, i.e., converting to a type B heterojunction.
Looking to the future, a few prominent challenges and opportunities are listed below:
(i) One of the major challenges faced in photocatalysis is deciphering the complex charge transfer mechanism. The mechanisms in many of the existing material compositions are not conclusive enough, which is otherwise significant, as some heterojunction categories vary marginally.
(ii) The current trend shows a diversity in the material selection, which is expected to bring out much more efficient photocatalytic heterojunction compositions by making complex architectures like ternary and multicomponent systems.
(iii) Within a given material composition, the synthetic methodology plays a vital role in deciding the performance. Hence, efficient synthetic strategies that result in tight heterojunction formation to facilitate a high degree of charge separation are required.
(iv) Several opportunities exist in developing various material compositions and synthetic strategies that possess cumulative non-toxic, cost-effective, scalable, and industrially adaptable characteristics.
Conflicts of interest
The authors declare no competing interests.
References
- A. K. Atri, S. Singh, I. Qadir, S. Sharma, U. Manhas and D. Singh, New J. Chem., 2023, 47, 12955–12972 RSC
.
- M. Qiu, W. Xu, S. Chen, Z. Jia, Y. Li, J. He, L. Wang, J. Lei, C. Liu and J. Liu, J. Taiwan Inst. Chem. Eng., 2023, 143, 104674 CrossRef CAS
.
- A. Sheikhzadeh Takabi and A. Mouradzadegun, Photochem. Photobiol. Sci., 2023, 22, 837–855 CrossRef CAS PubMed
.
- B. T. Son, N. V. Long and N. T. N. Hang, RSC Adv., 2021, 11, 30805–30826 RSC
.
- P. V. Kamat, ACS Energy Lett., 2018, 3, 1394–1395 CrossRef CAS
.
- H. D. Muller and F. Steinbach, Nature, 1970, 225, 728–729 CrossRef CAS
.
- A. Fujishima and K. Honda, Nature, 1972, 238, 37–38 CrossRef CAS PubMed
.
- J. Schneider, M. Matsuoka, M. Takeuchi, J. Zhang, Y. Horiuchi, M. Anpo and D. W. Bahnemann, Chem. Rev., 2014, 114, 9919–9986 CrossRef CAS
.
- M. H. Barzegar, M. M. Sabzehmeidani, M. Ghaedi, V. M. Avargani, Z. Moradi, V. A. L. Roy and H. Heidari, Chem. Eng. Res. Des., 2021, 174, 307–318 CrossRef CAS
.
- E. Dupont, R. Koppelaar and H. Jeanmart, Appl. Energy, 2020, 257, 113968 CrossRef
.
- N. Serpone, E. Borgarello and M. Grätzel, J. Chem. Soc., Chem. Commun., 1984, 342–344 RSC
.
- I. Bedja and P. V. Kamat, J. Phys. Chem., 2002, 99, 9182–9188 CrossRef
.
- S. Ozkar, Dalton Trans., 2021, 50, 12349–12364 RSC
.
- J. Wang, Y. Yu, W. Xu, H. Yu, W. Zhang, H. Huang, G. R. Zhang and D. Mei, J. Catal., 2022, 411, 72–83 CrossRef CAS
.
- C. Yuksel Alpaydın, S. K. Gulbay and C. Ozgur Colpan, Int. J. Hydrogen Energy, 2020, 45, 3414–3434 CrossRef
.
- D. Patra, R. Ganesan and B. Gopalan, Int. J. Hydrogen Energy, 2021, 46, 25486–25499 CrossRef CAS
.
- Z. Zhang and J. T. J. Yates, Chem. Rev., 2012, 112, 5520–5551 CrossRef CAS PubMed
.
- L. Wang, H. Yin, S. Wang, J. Wang and S. Ai, Appl. Catal., B, 2022, 305, 121039 CrossRef CAS
.
- M. Murugalakshmi, G. Mamba, S. A. Ansari, V. Muthuraj and T. I. T. Nkambule, Colloids Surf., A, 2022, 634, 127969 CrossRef CAS
.
- J. Huang, P. Xue, S. Wang, S. Han, L. Lin, X. Chen and Z. Wang, J. Colloid Interface Sci., 2022, 606, 1509–1523 CrossRef CAS
.
- M. Sun, F. Li, F. Zhao, T. Wu, T. Yan, B. Du and D. Li, J. Colloid Interface Sci., 2022, 606, 1261–1273 CrossRef CAS PubMed
.
- Y. Zhu, J. Xu and M. Chen, Sep. Purif. Technol., 2022, 282, 120004 CrossRef CAS
.
- K. Qin, Q. Zhao, H. Yu, X. Xia, J. Li, S. He, L. Wei and T. An, Environ. Res., 2021, 199, 111360 CrossRef CAS
.
- K. Girija, S. Thirumalairajan, V. R. Mastelaro and D. Mangalaraj, J. Mater. Chem. A, 2015, 3, 2617–2627 RSC
.
- Y. Nosaka and A. Y. Nosaka, Chem. Rev., 2017, 117, 11302–11336 CrossRef CAS PubMed
.
- W. J. Ong, L. L. Tan, Y. H. Ng, S. T. Yong and S. P. Chai, Chem. Rev., 2016, 116, 7159–7329 CrossRef CAS PubMed
.
- A. Wadsworth, Z. Hamid, J. Kosco, N. Gasparini and I. McCulloch, Adv. Mater., 2020, 32, 2001763 CrossRef CAS PubMed
.
- H. Yang, Mater. Res. Bull., 2021, 142, 111406 CrossRef CAS
.
- Z. Xiong, Q. Liu, Z. Gao, J. Yang, X. Zhang, Q. Yang and C. Hao, Inorg. Chem., 2021, 60, 5063–5070 CrossRef CAS PubMed
.
- P. Kumari, N. Bahadur, L. Kong, L. A. O'Dell, A. Merenda and L. Dumee, Mater. Adv., 2022, 2309–2323 RSC
.
- H. Wang, L. Zhang, Z. Chen, J. Hu, S. Li, Z. Wang, J. Liu and X. Wang, Chem. Soc. Rev., 2014, 43, 5234–5244 RSC
.
- H. Zhao, X. Liu, Y. Dong, Y. Xia, H. Wang and X. Zhu, ACS Appl. Mater. Interfaces, 2020, 12, 31532–31541 CrossRef CAS
.
- A. Wang, S. Wu, J. Dong, R. Wang, J. Wang, J. Zhang, S. Zhong and S. Bai, Chem. Eng. J., 2021, 404, 127145 CrossRef CAS
.
- S. Lu, B. Weng, A. Chen, X. Li, H. Huang, X. Sun, W. Feng, Y. Lei, Q. Qian and M.-Q. Yang, ACS Appl. Mater. Interfaces, 2021, 13, 13044–13054 CrossRef CAS PubMed
.
- Z. Li, W. Huang, J. Liu, K. Lv and Q. Li, ACS Catal., 2021, 11, 8510–8520 CrossRef CAS
.
- Z. Liang, B. Ouyang, T. Wang, X. Liu, H. Huo, D. Liu, H. Feng, J. Ma, K. Deng, A. Li and others, Int. J. Hydrogen Energy, 2022, 47, 10868–10876 CrossRef CAS
.
- C. Li, G. Ding, X. Liu, P. Huo, Y. Yan, Y. Yan and G. Liao, Chem. Eng. J., 2022, 435, 134740 CrossRef CAS
.
- N. Tian, H. Huang, S. Wang, T. Zhang, X. Du and Y. Zhang, Appl. Catal., B, 2020, 267, 118697 CrossRef CAS
.
- K. S. Novoselov, A. K. Geim, S. V. Morozov, D. Jiang, Y. Zhang, S. V. Dubonos, I. V. Grigorieva and A. A. Firsov, Science, 2004, 306, 666–669 CrossRef CAS PubMed
.
- X. Chen, W. Pan, R. Guo, X. Hu, Z. Bi and J. Wang, J. Mater. Chem. A, 2022, 10, 7604–7625 RSC
.
- W. Jia, B. Ding, X. Qian, Y. Yang, L. Mao, X. Cai, S. Guo and J. Zhang, J. Phys. Chem. C, 2021, 125, 19763–19772 CrossRef CAS
.
- Y. Zhou, C. Zhang, D. Huang, W. Wang, Y. Zhai, Q. Liang, Y. Yang, S. Tian, H. Luo and D. Qin, Appl. Catal., B, 2022, 301, 120749 CrossRef CAS
.
- G. Yao, S. Yang, S. Jiang, C. Sun and S. Song, Appl. Catal., B, 2022, 121569 CrossRef CAS
.
- Y. Xu, X. Jin, T. Ge, H. Xie, R. Sun, F. Su, X. Li and L. Ye, Chem. Eng. J., 2021, 409, 128178 CrossRef CAS
.
- W. Hu and J. Yang, J. Mater. Chem. C, 2017, 5, 12289–12297 RSC
.
- S. Bao, Z. Wang, J. Zhang and B. Tian, ACS Appl. Nano Mater., 2020, 3, 8604–8617 CrossRef CAS
.
- Y. Luo, G. Sun, B. Tian and J. Zhang, Chem. Eng. J., 2022, 442, 135835 CrossRef CAS
.
- P. Gao, S. Huang, K. Tao, Z. Li, L. Feng, Y. Liu and L. Zhang, J. Hazard. Mater., 2022, 129374 CrossRef CAS PubMed
.
- L. Zhang, Y. Meng, H. Shen, J. Li, C. Yang, B. Xie and S. Xia, Inorg. Chem., 2022, 61, 6045–6055 CrossRef CAS PubMed
.
- J. Low, J. Yu, M. Jaroniec, S. Wageh and A. A. Al-Ghamdi, Adv. Mater., 2017, 29, 1601694 CrossRef PubMed
.
- Y. Zhao, Y. Chen, L. Du, Q. Wang, X. Liu, L. Li and G. Tian, J. Colloid Interface Sci., 2022, 605, 253–262 CrossRef CAS PubMed
.
- S. Joshi, R. K. Canjeevaram Balasubramanyam, S. J. Ippolito, Y. M. Sabri, A. E. Kandjani, S. K. Bhargava and M. V. Sunkara, ACS Appl. Nano Mater., 2018, 1, 3375–3388 CrossRef CAS
.
- S. Challagulla, R. Nagarjuna, R. Ganesan and S. Roy, ACS Sustainable Chem. Eng., 2016, 4, 974–982 CrossRef CAS
.
- L. Zhang, X. Dong, Y. Wang, N. Zheng, H. Ma and X. Zhang, Appl. Surf. Sci., 2022, 579, 152088 CrossRef CAS
.
- X. Liu, Y. Liu, T. Liu, Y. Jia, H. Deng, W. Wang and F. Zhang, Chem. Eng. J., 2022, 431, 134181 CrossRef CAS
.
- C. Li, H. Sun, H. Jin, W. Li, J. L. Liu and S. Bashir, Catal. Today, 2022, 400, 146–158 CrossRef
.
- Q. Xu, L. Zhang, B. Cheng, J. Fan and J. Yu, Chem, 2020, 6, 1543–1559 CAS
.
- A. J. Bard, J. Photochem., 1979, 10, 59–75 CrossRef CAS
.
- J. Low, C. Jiang, B. Cheng, S. Wageh, A. A. Al-Ghamdi and J. Yu, Small Methods, 2017, 1, 1700080 CrossRef
.
- Q. Xu, L. Zhang, J. Yu, S. Wageh, A. A. Al-Ghamdi and M. Jaroniec, Mater. Today, 2018, 21, 1042–1063 CrossRef CAS
.
- K. Maeda, ACS Catal., 2013, 3, 1486–1503 CrossRef CAS
.
- X. Li, C. Garlisi, Q. Guan, S. Anwer, K. Al-Ali, G. Palmisano and L. Zheng, Mater. Today, 2021, 47, 75–107 CrossRef CAS
.
- C. Xing, G. Yu, J. Zhou, Q. Liu, T. Chen, H. Liu and X. Li, Appl. Catal., B, 2022, 121496 CrossRef CAS
.
- W. Zhang, A. R. Mohamed and W.-J. Ong, Angew. Chem., Int. Ed., 2020, 59, 22894–22915 CrossRef CAS
.
- P. Zhou, J. Yu and M. Jaroniec, Adv. Mater., 2014, 26, 4920–4935 CrossRef CAS
.
- T. Di, Q. Xu, W. Ho, H. Tang, Q. Xiang and J. Yu, ChemCatChem, 2019, 11, 1394–1411 CrossRef CAS
.
- B. J. Ng, L. K. Putri, X. Y. Kong, Y. W. Teh, P. Pasbakhsh and S. P. Chai, Adv. Sci., 2020, 7, 1903171 CrossRef CAS
.
- Y. Xue, W. Tang, C. Si, Q. Lu, E. Guo, M. Wei and Y. Pang, Opt. Mater., 2022, 128, 112400 CrossRef CAS
.
- S. Pu, Y. Chen, D. Wang, Y. Zhang, Y. Li, W. Feng and Y. Sun, Opt. Mater., 2023, 141, 113888 CrossRef CAS
.
- M. He, J. Chen, Y. Yang, X. Hu, Z. Jiang, Y. Yan, J. Sun, L. Fu, J. Wei and T. Yang, Opt. Mater., 2023, 137, 113554 CrossRef CAS
.
- Y. Wang, S. Feng, C. Ma, Y. Zhou, Z. Ye, X. Dai and X. Cao, Opt. Mater., 2023, 135, 113087 CrossRef CAS
.
- J. Fu, Q. Xu, J. Low, C. Jiang and J. Yu, Appl. Catal., B, 2019, 243, 556–565 CrossRef CAS
.
- P. Xia, S. Cao, B. Zhu, M. Liu, M. Shi, J. Yu and Y. Zhang, Angew. Chem., Int. Ed., 2020, 59, 5218–5225 CrossRef CAS PubMed
.
- S. Li, C. Wang, M. Cai, F. Yang, Y. Liu, J. Chen, P. Zhang, X. Li and X. Chen, Chem. Eng. J., 2022, 428, 131158 CrossRef CAS
.
- F. Xu, K. Meng, B. Cheng, S. Wang, J. Xu and J. Yu, Nat. Commun., 2020, 11, 1–9 CrossRef PubMed
.
- C. Cheng, B. He, J. Fan, B. Cheng, S. Cao and J. Yu, Adv. Mater., 2021, 33, 2100317 CrossRef CAS PubMed
.
- S. J. A. Moniz, S. A. Shevlin, D. J. Martin, Z. X. Guo and J. Tang, Energy Environ. Sci., 2015, 8, 731–759 RSC
.
- J. Li, X. Yang, C. Ma, Y. Lei, Z. Cheng and Z. Rui, Appl. Catal., B, 2021, 291, 120053 CrossRef CAS
.
- J. Li, J. Chen, H. Fang, X. Guo and Z. Rui, Ind. Eng. Chem. Res., 2021, 60, 8420–8429 CrossRef CAS
.
- J. Li, J. Feng, X. Guo, H. Fang, J. Chen, C. Ma, R. Li, Y. Wang and Z. Rui, Appl. Catal., B, 2022, 309, 121248 CrossRef CAS
.
- A. D. Lopis, K. S. Choudhari, R. Sai, K. S. Kanakikodi, S. P. Maradur, S. A. Shivashankar and S. D. Kulkarni, Sol. Energy, 2022, 240, 57–68 CrossRef CAS
.
- Q. Mao, D. Li and Y. Dong, New J. Chem., 2022, 46, 6267–6273 RSC
.
- A. B. Trench, R. Alvarez, V. Teodoro, L. G. da Trindade, T. R. Machado, M. M. Teixeira, D. de Souza, I. M. Pinatti, A. Z. Simões, Y. G. Gobato and others, Mater. Chem. Phys., 2022, 280, 125710 CrossRef CAS
.
- J. Li, Y. Mei, S. Ma, Q. Yang, B. Jiang, B. Xin, T. Yao and J. Wu, J. Colloid Interface Sci., 2022, 608, 2075–2087 CrossRef CAS PubMed
.
- X. Ji, R. Guo, J. Tang, Z. Lin, Y. Yuan, L. Hong and W. Pan, J. Colloid Interface Sci., 2022, 618, 300–310 CrossRef CAS PubMed
.
- L. Zhang, Z. Q. Wang, J. Liao, X. Zhang, D. Feng, H. Deng and C. Ge, Chem. Eng. J., 2022, 431, 133453 CrossRef CAS
.
- C. Liu, J. Xu, X. Du, Q. Li, Y. Fu and M. Chen, Opt. Mater., 2021, 112, 110742 CrossRef CAS
.
- S. Q. Guo, H. Zhang, Z. Hu, M. Zhen, B. Yang, B. Shen and F. Dong, Nano Res., 2021, 14, 4188–4196 CrossRef CAS
.
- W. Guo, J. Li, Y. Yang, M. Zhang, Y. Zhai, D. Li, H. Zhao and Y. Liu, Mater. Chem. Phys., 2021, 264, 124440 CrossRef CAS
.
- S. A. Younis, E. Amdeha and R. A. El-Salamony, J. Environ. Chem. Eng., 2021, 9, 104619 CrossRef CAS
.
- Z. Wu, K. Zhang, X. Li, G. Hai, X. Huang and G. Wang, Appl. Surf. Sci., 2021, 555, 149732 CrossRef CAS
.
- H. He, W. Wang, C. Xu, S. Yang, C. Sun, X. Wang, Y. Yao, N. Mi, W. Xiang, S. Li and others, Sci. Total Environ., 2020, 730, 139100 CrossRef CAS PubMed
.
- M. Xiong, J. Yan, B. Chai, G. Fan and G. Song, J. Mater. Sci. Technol., 2020, 56, 179–188 CrossRef CAS
.
- Y. Li, X. Wang, H. Huo, Z. Li and J. Shi, Colloids Surf., A, 2020, 587, 124322 CrossRef CAS
.
- R. Li, X. Li, J. Wu, X. Lv, Y. Z. Zheng, Z. Zhao, X. Ding, X. Tao and J. F. Chen, Appl. Catal., B, 2019, 259, 118075 CrossRef CAS
.
- M. Nikookar, A. Rezaeifard, K. V. Grzhegorzhevskii, M. Jafarpour and R. Khani, ACS Appl. Nano Mater., 2022, 7917–7931 CrossRef CAS
.
- M. Li, Y. Wang, N. Tian and H. Huang, Appl. Surf. Sci., 2022, 587, 152852 CrossRef CAS
.
- U. Kumar, J. Kuntail, A. Kumar, R. Prakash, M. R. Pai and I. Sinha, Appl. Surf. Sci., 2022, 589, 153013 CrossRef CAS
.
- E. Alimohammadi, V. Mahdikhah and S. Sheibani, Appl. Surf. Sci., 2022, 598, 153816 CrossRef CAS
.
- J. Wang, B. Wang, W. Zhang, Y. Xiao, H. Xu, Y. Liu, Z. Liu, J. Zhang and Y. Jiang, Appl. Surf. Sci., 2022, 587, 152867 CrossRef CAS
.
- Q. Dong, Z. Chen, B. Zhao, Y. Zhang, Z. Lu, X. Wang, J. Li and W. Chen, J. Colloid Interface Sci., 2022, 608, 1951–1959 CrossRef CAS PubMed
.
- X. Li, J. Wang, J. Zhang, C. Zhao, Y. Wu and Y. He, J. Colloid Interface Sci., 2022, 607, 412–422 CrossRef CAS PubMed
.
- X. Zhang, X. Yang, B. Liu, G. Zhu and J. Fan, J. Environ. Chem. Eng., 2022, 10, 107068 CrossRef CAS
.
- X. Wu, J. Lu, S. Huang, X. Shen, S. Cui and X. Chen, Appl. Surf. Sci., 2022, 594, 153486 CrossRef CAS
.
- Y. He, J. Shi, Q. Yang, Y. Tong, Z. Ma, L. B. Junior and B. Yao, Chem. Eng. J., 2022, 137355 CrossRef CAS
.
- L. Sun, W. Wang, C. Zhang, M. Cheng, Y. Zhou, Y. Yang, H. Luo, D. Qin, C. Huang and Z. Ouyang, Chem. Eng. J., 2022, 137027 CrossRef CAS
.
- Y. R. Lv, Z. L. Wang, Y. X. Yang, Y. Luo, S. Y. Yang and Y. H. Xu, J. Hazard. Mater., 2022, 432, 128665 CrossRef CAS PubMed
.
- J. Yang, Y. Wu, Y. Dong, H. Cui, C. Shi, H. Sun and S. Yin, J. Ind. Eng. Chem., 2022, 509–518 CrossRef CAS
.
- F. Chen, K. Bian, H. Li, Y. Tang, C. Hao and W. Shi, J. Chem. Technol. Biotechnol., 2022, 97, 1884–1892 CrossRef CAS
.
- T. Kulandaivalu, A. R. Mohamed, K. A. Ali and S. Kulandaivalu, J. CO2 Util., 2022, 63, 102115 CrossRef CAS
.
- C. Jing, Y. Zhang, J. Zheng, S. Ge, J. Lin, D. Pan, N. Naik and Z. Guo, Particuology, 2022, 69, 111–122 CrossRef CAS
.
- G. Kumar, J. Kumar, M. Bag and R. K. Dutta, Sep. Purif. Technol., 2022, 292, 121040 CrossRef CAS
.
- V. Poliukhova, S. Khan, Z. Qiaohong, J. Zhang, D. Kim, S. Kim and S. H. Cho, Appl. Surf. Sci., 2022, 575, 151773 CrossRef CAS
.
- J. Li, H. Liu, Z. Liu, D. Yang, M. Zhang, L. Gao, Y. Zhou and C. Lu, Arabian J. Chem., 2022, 15, 103513 CrossRef CAS
.
- C. Lan, L. Meng and N. Xu, Colloids Surf., A, 2022, 632, 127762 CrossRef CAS
.
- J. Yang, C. Shi, Y. Dong, H. Su, H. Sun, Y. Guo and S. Yin, J. Colloid
Interface Sci., 2022, 605, 373–384 CrossRef CAS PubMed
.
- S. Dhingra, M. Sharma, V. Krishnan and C. M. Nagaraja, J. Colloid Interface Sci., 2022, 608, 1040–1050 CrossRef CAS PubMed
.
- Z. Huang, J. Liu, S. Zong, X. Wang, K. Chen, L. Liu and Y. Fang, J. Colloid Interface Sci., 2022, 606, 848–859 CrossRef CAS PubMed
.
- K. Ouyang, B. Xu, C. Yang, H. Wang, P. Zhan and S. Xie, Mater. Sci. Semicond. Process., 2022, 137, 106168 CrossRef CAS
.
- T. Wang, W. Yang, L. Chang, H. Wang, H. Wu, J. Cao, H. Fan, J. Wang, H. Liu, Y. Hou and others, Sep. Purif. Technol., 2022, 285, 120329 CrossRef CAS
.
- Z. Hu, D. Shi, G. Wang, T. Gao, J. Wang, L. Lu and J. Li, Appl. Surf. Sci., 2022, 154167 CrossRef CAS
.
- J. Li, F. Wei, Z. Xiu and X. Han, Chem. Eng. J., 2022, 137129 CrossRef CAS
.
- H. Yu, Y. Xue, S. Liang and X. Wang, J. Photochem. Photobiol., A, 2022, 114077 CrossRef CAS
.
- C. Wu, Q. Shen, J. Liu, L. Jiang, J. Sheng, Y. Li and H. Yang, J. Photochem. Photobiol., A, 2022, 114142 CrossRef CAS
.
- R. Guo, Z. Bi, Z. Lin, X. Hu, J. Wang, X. Chen and W. Pan, J. Colloid Interface Sci., 2022, 627, 343–354 CrossRef CAS PubMed
.
- J. Yao, L. Huang, Y. Li, J. Liu, J. Liu, S. Shu, L. Huang and Z. Zhang, J. Colloid Interface Sci., 2022, 627, 224–237 CrossRef CAS PubMed
.
- Y. Wang, Y. Liu, F. Tian, S. Bao, C. Sun, W. Yang and Y. Yu, J. Colloid Interface Sci., 2022, 264–277 CrossRef CAS PubMed
.
- N. Lu, X. Jing, J. Zhang, P. Zhang, Q. Qiao and Z. Zhang, Chem. Eng. J., 2022, 431, 134001 CrossRef CAS
.
- Y. Su, X. Xu, R. Li, X. Luo, H. Yao, S. Fang, K. P. Homewood, Z. Huang, Y. Gao and X. Chen, Chem. Eng. J., 2022, 429, 132241 CrossRef CAS
.
- Z. Jin, X. Jiang and X. Guo, Int. J. Hydrogen Energy, 2022, 47, 1669–1682 CrossRef CAS
.
- S. Xiao, Y. Guan, H. Shang, H. Li, Z. Tian, S. Liu, W. Chen and J. Yang, J. CO2 Util., 2022, 55, 101806 CrossRef CAS
.
- X. Xu, Y. Su, Y. Dong, X. Luo, S. Wang, W. Zhou, R. Li, K. P. Homewood, X. Xia, Y. Gao and others, J. Hazard. Mater., 2022, 424, 127685 CrossRef CAS PubMed
.
- Z. Zhang, M. Wang, Z. Chi, W. Li, H. Yu, N. Yang and H. Yu, Appl. Catal., B, 2022, 313, 121426 CrossRef CAS
.
- X. Han, B. Lu, X. Huang, C. Liu, S. Chen, J. Chen, Z. Zeng, S. Deng and J. Wang, Appl. Catal., B, 2022, 121587 CrossRef CAS
.
- L. Chen, X. L. Song, J. T. Ren and Z. Y. Yuan, Appl. Catal., B, 2022, 315, 121546 CrossRef CAS
.
- F. A. Qaraah, S. A. Mahyoub, A. Hezam, A. Qaraah, F. Xin and G. Xiu, Appl. Catal., B, 2022, 121585 CrossRef CAS
.
- K. Wang, X. Shao, K. Zhang, J. Wang, X. Wu and H. Wang, Appl. Surf. Sci., 2022, 596, 153444 CrossRef CAS
.
- J. Bai, W. Chen, L. Hao, R. Shen, P. Zhang, N. Li and X. Li, Chem. Eng. J., 2022, 447, 137488 CrossRef CAS
.
- J. Zheng, C. Fan, X. Li, Q. Yang, D. Wang, A. Duan, J. Ding, S. Rong, Z. Chen, J. Luo and others, Chem. Eng. J., 2022, 137371 CrossRef CAS
.
- C. Wang, H. Liu, G. Wang, H. Fang, X. Yuan and C. Lu, Chem. Eng. J., 2022, 450, 138167 CrossRef CAS
.
- B. Zhang, D. Wang, S. Jiao, Z. Xu, Y. Liu, C. Zhao, J. Pan, D. Liu, G. Liu, B. Jiang and others, Chem. Eng. J., 2022, 137138 CrossRef CAS
.
- Y. Zhang, J. Qiu, B. Zhu, M. V. Fedin, B. Cheng, J. Yu and L. Zhang, Chem. Eng. J., 2022, 444, 136584 CrossRef CAS
.
- D. D. Blach, W. Zheng, H. Liu, A. Pan and L. Huang, J. Phys. Chem. C, 2020, 124, 11325–11332 CrossRef CAS
.
- A. Iqbal, A. Kafizas, C. Sotelo-Vazquez, R. Wilson, M. Ling, A. Taylor, C. Blackman, K. Bevan, I. Parkin and R. Quesada-Cabrera, ACS Appl. Mater. Interfaces, 2021, 13, 9781–9793 CrossRef CAS PubMed
.
- Z. Lian, F. Wu, J. Zi, G. Li, W. Wang and H. Li, J. Am. Chem. Soc., 2023, 145, 15482–15487 CrossRef CAS PubMed
.
- W. Wang, Y. Tao, J. Fan, Z. Yan, H. Shang, D. L. Phillips, M. Chen and G. Li, Adv. Funct. Mater., 2022, 32, 2201357 CrossRef CAS
.
- G. N. Schrauzer and T. D. Guth, J. Am. Chem. Soc., 1977, 99, 7189–7193 CrossRef CAS
.
- R. Nagarjuna, S. Roy and R. Ganesan, Microporous Mesoporous Mater., 2015, 211, 1–8 CrossRef CAS
.
- R. Nagarjuna, S. Challagulla, N. Alla, R. Ganesan and S. Roy, Mater. Des., 2015, 86, 621–626 CrossRef CAS
.
- S. Challagulla, K. Tarafder, R. Ganesan and S. Roy, J. Phys. Chem. C, 2017, 121, 27406–27416 CrossRef CAS
.
- S. Challagulla, K. Tarafder, R. Ganesan and S. Roy, Sci. Rep., 2017, 7, 1–11 CrossRef CAS PubMed
.
- J. Wu, Y. Tao, C. Zhang, Q. Zhu, D. Zhang and G. Li, J. Hazard. Mater., 2023, 443, 130363 CrossRef CAS PubMed
.
- Evonik, AEROXIDE, AERODISP and AEROPERL, Titanium Dioxide as Photocatalyst, Technical Information 1243, Evonik Industries, 2015, pp. 4–11 Search PubMed.
- A. M. Pennington, A. I. Okonmah, D. T. Munoz, G. Tsilomelekis and F. E. Celik, J. Phys. Chem. C, 2018, 122, 5093–5104 CrossRef CAS
.
- D. Zhang, Z. Liu and R. Mou, Inorg. Chem. Commun., 2022, 109667 CrossRef CAS
.
- V. Dutta, S. Sharma, P. Raizada, V. K. Thakur, A. A. P. Khan, V. Saini, A. M. Asiri and P. Singh, J. Environ. Chem. Eng., 2021, 9, 105018 CrossRef CAS
.
- S. Ali, A. Razzaq, H. Kim and S. I. In, Chem. Eng. J., 2022, 429, 131579 CrossRef CAS
.
- A. H. Zahid and Q. Han, Nanoscale, 2021, 17687–17724 RSC
.
- A. Ghenaatgar, R. M. A. Tehrani and A. Khadir, J. Water Process Eng., 2019, 32, 100969 CrossRef
.
- R. Nagarjuna, S. Challagulla, R. Ganesan and S. Roy, Chem. Eng. J., 2017, 308, 59–66 CrossRef CAS
.
- R. Nagarjuna, S. Challagulla, P. Sahu, S. Roy and R. Ganesan, Adv. Powder Technol., 2017, 28, 3265–3273 CrossRef CAS
.
- M. Galedari, M. M. Ghazi and S. R. Mirmasoomi, Chem. Eng. Res. Des., 2021, 170, 248–255 CrossRef CAS
.
- P. H. Palharim, M. C. D. Caira, C. de Araujo Gusmao, B. Ramos, G. T. dos Santos, O. Rodrigues Jr and A. C. S. C. Teixeira, Chem. Eng. Res. Des., 2022, 188, 935–953 CrossRef CAS
.
- K. Kannan, D. Radhika, K. K. Sadasivuni, K. R. Reddy and A. V. Raghu, Adv. Colloid Interface Sci., 2020, 281, 102178 CrossRef CAS PubMed
.
- L. Chen, Z. Liu, Z. Guo and X. J. Huang, J. Mater. Chem. A, 2020, 8, 17326–17359 RSC
.
- H. Mai, D. Chen, Y. Tachibana, H. Suzuki, R. Abe and R. A. Caruso, Chem. Soc. Rev., 2021, 50, 13692–13729 RSC
.
- K. Wei, Y. Faraj, G. Yao, R. Xie and B. Lai, Chem. Eng. J., 2021, 414, 128783 CrossRef CAS
.
- O. B. Olgun, B. Palas, S. Atalay and G. Ersoz, Chem. Eng. Res. Des., 2021, 171, 421–432 CrossRef
.
- K. S. Schanze, P. V. Kamat, P. Yang and J. Bisquert, ACS Energy Lett., 2020, 8, 2602–2604 CrossRef
.
- J. Wang, J. Liu, Z. Du and Z. Li, J. Energy Chem., 2021, 54, 770–785 CrossRef CAS
.
- A. Rahman and M. M. Khan, New J. Chem., 2021, 19622–19635 RSC
.
- R. Woods-Robinson, Y. Han, H. Zhang, T. Ablekim, I. Khan, K. A. Persson and A. Zakutayev, Chem. Rev., 2020, 120, 4007–4055 CrossRef CAS PubMed
.
- K. Muralirajan, R. Kancherla, J. A. Bau, M. R. Taksande, M. Qureshi, K. Takanabe and M. Rueping, ACS Catal., 2021, 11, 14772–14780 CrossRef CAS
.
- Y. Bai, Q. Zhang, N. Xu, K. Deng and E. Kan, Appl.
Surf. Sci., 2019, 478, 522–531 CrossRef CAS
.
- M. M. Chen, H. G. Xue and S. P. Guo, Coord. Chem. Rev., 2018, 368, 115–133 CrossRef CAS
.
- E. Wlazlak, A. Blachecki, M. Bisztyga-Szklarz, S. Klejna, T. Mazur, K. Mech, K. Pilarczyk, D. Przyczyna, M. Suchecki, P. Zawal and others, Chem. Commun., 2018, 54, 12133–12162 RSC
.
- G. Cai, P. Yan, L. Zhang, H. C. Zhou and H. L. Jiang, Chem. Rev., 2021, 121, 12278–12326 CrossRef CAS PubMed
.
- M. Ahmed, Inorg. Chem. Front., 2022, 3003–3033 RSC
.
- K. Geng, T. He, R. Liu, S. Dalapati, K. T. Tan, Z. Li, S. Tao, Y. Gong, Q. Jiang and D. Jiang, Chem. Rev., 2020, 120, 8814–8933 CrossRef CAS PubMed
.
- Z. Wang, J. Huang, J. Mao, Q. Guo, Z. Chen and Y. Lai, J. Mater. Chem. A, 2020, 8, 2934–2961 RSC
.
- G. Zhang, D. Huang, M. Cheng, L. Lei, S. Chen, R. Wang, W. Xue, Y. Liu, Y. Chen and Z. Li, J. Mater. Chem. A, 2020, 8, 17883–17906 RSC
.
- Q. Wang, Q. Gao, A. M. Al-Enizi, A. Nafady and S. Ma, Inorg. Chem. Front., 2020, 7, 300–339 RSC
.
- J. Meng, X. Liu, C. Niu, Q. Pang, J. Li, F. Liu, Z. Liu and L. Mai, Chem. Soc. Rev., 2020, 49, 3142–3186 RSC
.
- C. Du, Z. Zhang, G. Yu, H. Wu, H. Chen, L. Zhou, Y. Zhang, Y. Su, S. Tan, L. Yang, J. Song and S. Wang, Chemosphere, 2021, 272, 129501 CrossRef CAS PubMed
.
- Q. Guan, L. L. Zhou and Y. B. Dong, Chem. Soc. Rev., 2022, 6307–6416 RSC
.
- Z. He, J. Goulas, E. Parker, Y. Sun, X. Zhou and L. Fei, Catal. Today, 2023, 409, 103–118 CrossRef CAS
.
- J. Li, D. Zhao, J. Liu, A. Liu and D. Ma, Molecules, 2020, 25, 2425 CrossRef CAS PubMed
.
- R. Liu, K. T. Tan, Y. Gong, Y. Chen, Z. Li, S. Xie, T. He, Z. Lu, H. Yang and D. Jiang, Chem. Soc. Rev., 2021, 50, 120–242 RSC
.
- C. Xia, K. O. Kirlikovali, T. H. C. Nguyen, X. C. Nguyen, Q. B. Tran, M. K. Duong, M. T. N. Dinh, D. L. T. Nguyen, P. Singh, P. Raizada and others, Coord. Chem. Rev., 2021, 446, 214117 CrossRef CAS
.
- J. You, Y. Zhao, L. Wang and W. Bao, J. Cleaner Prod., 2021, 291, 125822 CrossRef CAS
.
- D. G. Wang, T. Qiu, W. Guo, Z. Liang, H. Tabassum, D. Xia and R. Zou, Energy Environ. Sci., 2021, 14, 688–728 RSC
.
- N. Keller and T. Bein, Chem. Soc. Rev., 2021, 50, 1813–1845 RSC
.
- G. B. Wang, S. Li, C. X. Yan, F. C. Zhu, Q. Q. Lin, K. H. Xie, Y. Geng and Y.-B. Dong, J. Mater. Chem. A, 2020, 8, 6957–6983 RSC
.
- H. Wang, H. Wang, Z. Wang, L. Tang, G. Zeng, P. Xu, M. Chen, T. Xiong, C. Zhou, X. Li and others, Chem. Soc. Rev., 2020, 49, 4135–4165 RSC
.
- Q. Yang, M. Luo, K. Liu, H. Cao and H. Yan, Appl. Catal., B, 2020, 276, 119174 CrossRef CAS
.
- T. Banerjee, K. Gottschling, G. Savasci, C. Ochsenfeld and B. V. Lotsch, ACS Energy Lett., 2018, 3, 400–409 CrossRef CAS PubMed
.
- C. Guo, F. Duan, S. Zhang, L. He, M. Wang, J. Chen, J. Zhang, Q. Jia, Z. Zhang and M. Du, J. Mater. Chem. A, 2022, 10, 475–507 RSC
.
- S. Y. Hu, Y. N. Sun, Z. W. Feng, F. O. Wang and Y. Lv, Chemosphere, 2022, 286, 131646 CrossRef CAS PubMed
.
- M. Naguib, M. Kurtoglu, V. Presser, J. Lu, J. Niu, M. Heon, L. Hultman, Y. Gogotsi and M. W. Barsoum, Adv. Mater., 2011, 23, 4248–4253 CrossRef CAS PubMed
.
- A. A. Fadahunsi, C. Li, M. I. Khan and W. Ding, J. Mater. Chem. B, 2022, 4331–4345 RSC
.
- T. Su, X. Ma, J. Tong, H. Ji, Z. Z. Qin and Z. Wu, J. Mater. Chem. A, 2022, 10265–10296 RSC
.
- N. H. Solangi, R. R. Karri, S. A. Mazari, N. M. Mubarak, A. S. Jatoi, G. Malafaia and A. K. Azad, Coord. Chem. Rev., 2023, 477, 214965 CrossRef CAS
.
- Z. You, Y. Liao, X. Li, J. Fan and Q. Xiang, Nanoscale, 2021, 13, 9463–9504 RSC
.
- J. Jin, T. Xiao, Y. Zhang, H. Zheng, H. Wang, R. Wang, Y. Gong, B. He, X. Liu and K. Zhou, Nanoscale, 2021, 13, 19740–19770 RSC
.
- S. Ponnada, M. S. Kiai, D. B. Gorle, R. Venkatachalam, B. Saini, K. Murugavel, A. Nowduri, R. Singhal, F. Marken, A. M. Kulandainathan and others, Catal. Sci. Technol., 2022, 4413–4441 RSC
.
- X. Chen, Z. Shi, Y. Tian, P. Lin, D. Wu, X. Li, B. Dong, W. Xu and X. Fang, Mater. Horiz., 2021, 8, 2929–2963 RSC
.
- J. Xu, T. Peng, X. Qin, Q. Zhang, T. Liu, W. Dai, B. Chen, H. Yu and S. Shi, J. Mater. Chem. A, 2021, 9, 14147–14171 RSC
.
- A. D. Handoko, S. N. Steinmann and Z. W. Seh, Nanoscale
Horiz., 2019, 4, 809–827 RSC
.
- J. Pang, R. G. Mendes, A. Bachmatiuk, L. Zhao, H. Q. Ta, T. Gemming, H. Liu, Z. Liu and M. H. Rummeli, Chem. Soc. Rev., 2019, 48, 72–133 RSC
.
- F. Song, G. Li, Y. Zhu, Z. Wu, X. Xie and N. Zhang, J. Mater. Chem. A, 2020, 8, 18538–18559 RSC
.
- A. M. Alexander and J. S. J. Hargreaves, Chem. Soc. Rev., 2010, 39, 4388–4401 RSC
.
- Y. Zhang, Y. Hu, H. Zeng, L. Zhong, K. Liu, H. Cao, W. Li and H. Yan, J. Hazard. Mater., 2017, 329, 22–29 CrossRef CAS PubMed
.
- B. Ma, D. Li, X. Wang and K. Lin, ChemSusChem, 2018, 11, 3871–3881 CrossRef CAS PubMed
.
- G. Tuci, Y. Liu, A. Rossin, X. Guo, C. Pham, G. Giambastiani and C. Pham-Huu, Chem. Rev., 2021, 121, 10559–10665 CrossRef CAS PubMed
.
- Y. Chen, H. Zhang, J. Zhang, J. Ma, L. Wang, H. Ye, G. Qian and Y. Ye, Adv. Powder Technol., 2013, 24, 207–211 CrossRef CAS
.
- J. Liu, S. Wen, Y. Hou, F. Zuo, G. J. O. Beran and P. Feng, Angew. Chem., 2013, 125, 3323–3327 CrossRef
.
- A. T. Garcia-Esparza, D. Cha, Y. Ou, J. Kubota, K. Domen and K. Takanabe, ChemSusChem, 2013, 6, 168–181 CrossRef CAS PubMed
.
- Y. Pan, T. Zhou, J. Han, J. Hong, Y. Wang, W. Zhang and R. Xu, Catal. Sci. Technol., 2016, 6, 2206–2213 RSC
.
- Y. X. Pan, H. Q. Zhuang, H. Ma, J. Cheng and J. Song, Chem. Eng. Sci., 2019, 194, 71–77 CrossRef CAS
.
- Y. Lei, K. H. Ng, Y. Zhang, Z. Li, S. Xu, J. Huang and Y. Lai, Chem. Eng. J., 2022, 434, 134689 CrossRef CAS
.
- B. P. Mabuea, H. C. Swart and E. Erasmus, ACS Omega, 2022, 7, 23401–23411 CrossRef CAS PubMed
.
- Y. Zhang, T. Xia, P. Wallenmeyer, C. X. Harris, A. A. Peterson, G. A. Corsiglia, J. Murowchick and X. Chen, Energy Technol., 2014, 2, 183–187 CrossRef CAS
.
- B. Wang, Y. Wang, Y. Lei, N. Wu, Y. Gou, C. Han, S. Xie and D. Fang, Nano Res., 2016, 9, 886–898 CrossRef CAS
.
- J. Hong, S. S. Meysami, V. Babenko, C. Huang, S. Luanwuthi, J. Acapulco, P. Holdway, P. S. Grant and N. Grobert, Appl. Catal., B, 2017, 218, 267–276 CrossRef CAS
.
- F. Chang, J. Zheng, X. Wang, Q. Xu, B. Deng, X. Hu and X. Liu, Mater. Sci. Semicond. Process., 2018, 75, 183–192 CrossRef CAS
.
- O. Koysuren, J. Appl. Polym. Sci., 2020, 137, 48524 CrossRef CAS
.
- H. Li and J. Sun, ACS Appl. Mater. Interfaces, 2021, 13, 5073–5078 CrossRef CAS PubMed
.
- L. Tian, S. Min and F. Wang, Appl. Catal., B, 2019, 259, 118029 CrossRef CAS
.
- C. Lai, Z. An, H. Yi, X. Huo, L. Qin, X. Liu, B. Li, M. Zhang, S. Liu, L. Li and others, J. Colloid Interface Sci., 2021, 600, 161–173 CrossRef CAS PubMed
.
- J. Di, C. Chen, C. Zhu, P. Song, M. Duan, J. Xiong, R. Long, M. Xu, L. Kang, S. Guo and others, Nano Energy, 2021, 79, 105429 CrossRef CAS
.
- S. Liu, W. Kuang, X. Meng, W. Qi, S. Adimi, H. Guo, X. Guo, E. Pervaiz, Y. Zhu, D. Xue and others, Chem. Eng. J., 2021, 416, 129116 CrossRef CAS
.
- T. Rao, W. Cai, H. Zhang and W. Liao, J. Mater. Chem. C, 2021, 9, 5323–5342 RSC
.
- Z. Cheng, W. Qi, C. H. Pang, T. Thomas, T. Wu, S. Liu and M. Yang, Adv. Funct. Mater., 2021, 31, 2100553 CrossRef CAS
.
- Y. Inoue, Energy Environ. Sci., 2009, 2, 364–386 RSC
.
- K. Maeda, K. Teramura, N. Saito, Y. Inoue, H. Kobayashi and K. Domen, Pure Appl. Chem., 2006, 78, 2267–2276 CrossRef CAS
.
- L. Yuliati, J. H. Yang, X. Wang, K. Maeda, T. Takata, M. Antonietti and K. Domen, J. Mater. Chem., 2010, 20, 4295–4298 RSC
.
- Y. Moriya, T. Takata and K. Domen, Coord. Chem. Rev., 2013, 257, 1957–1969 CrossRef CAS
.
- M. Ahmed and G. Xinxin, Inorg. Chem. Front., 2016, 3, 578–590 RSC
.
- M. G. Kibria and Z. Mi, J. Mater. Chem. A, 2016, 4, 2801–2820 RSC
.
- Y. Jiang, P. Liu, Y. Chen, Z. Zhou, H. Yang, Y. Hong, F. Li, L. Ni, Y. Yan and D. H. Gregory, Appl. Surf. Sci., 2017, 391, 392–403 CrossRef CAS
.
- A. Kumar, P. R. Thakur, G. Sharma, M. Naushad, A. Rana, G. T. Mola and F. J. Stadler, Environ. Chem. Lett., 2019, 17, 655–682 CrossRef CAS
.
- X. Meng, W. Qi, W. Kuang, S. Adimi, H. Guo, T. Thomas, S. Liu, Z. Wang and M. Yang, J. Mater. Chem. A, 2020, 8, 15774–15781 RSC
.
- H. S. Jung, Y. J. Hong, Y. Li, J. Cho, Y. J. Kim and G. C. Yi, ACS Nano, 2008, 2, 637–642 CrossRef CAS PubMed
.
- D. Wang, A. Pierre, M. G. Kibria, K. Cui, X. Han, K. H. Bevan, H. Guo, S. Paradis, A. R. Hakima and Z. Mi, Nano Lett., 2011, 11, 2353–2357 CrossRef CAS PubMed
.
- Z. Zhang, Q. Qian, B. Li and K. J. Chen, ACS Appl. Mater. Interfaces, 2018, 10, 17419–17426 CrossRef CAS PubMed
.
- Z. Li, L. Zhang, Y. Liu, C. Shao, Y. Gao, F. Fan, J. Wang, J. Li, J. Yan, R. Li and others, Angew. Chem., 2020, 132, 945–952 CrossRef
.
- J. Winnerl, M. Kraut, S. Artmeier and M. Stutzmann, Nanoscale, 2019, 11, 4578–4584 RSC
.
- J. Li, W. Yang, A. Wu, X. Zhang, T. Xu and B. Liu, ACS Appl. Mater. Interfaces, 2020, 12, 8583–8591 CrossRef CAS PubMed
.
- M. Idrees, C. V. Nguyen, H. D. Bui, I. Ahmad and B. Amin, Phys. Chem. Chem. Phys., 2020, 22, 20704–20711 RSC
.
- R. Li, W. H. Cheng, M. H. Richter, J. S. Du Chene, W. Tian, C. Li and H. A. Atwater, ACS Energy Lett., 2021, 6, 1849–1856 CrossRef CAS
.
- L. Zhou, H. Zhang, H. Sun, S. Liu, M. O. Tade, S. Wang and W. Jin, Catal. Sci. Technol., 2016, 6, 7002–7023 RSC
.
- G. Liao, Y. Gong, L. Zhang, H. Gao, G.-J. Yang and B. Fang, Energy Environ. Sci., 2019, 12, 2080–2147 RSC
.
- S. K. Verma, R. Verma, Y. R. Girish, F. Xue, L. Yan, S. Verma, M. Singh, Y. Vaishnav, A. B. Shaik, R. R. Bhandare and others, Green Chem., 2022, 24, 438–479 RSC
.
- M. Zhang, Y. Yang, X. An and L. Hou, Chem. Eng. J., 2021, 412, 128663 CrossRef CAS
.
- A. Mishra, A. Mehta, S. Basu, N. P. Shetti, K. R. Reddy and T. M. Aminabhavi, Carbon, 2019, 149, 693–721 CrossRef CAS
.
- S. Patnaik, D. P. Sahoo and K. Parida, Carbon, 2021, 172, 682–711 CrossRef CAS
.
- H. S. Gujral, G. Singh, A. V. Baskar, X. Guan, X. Geng, A. V. Kotkondawar, S. Rayalu, P. Kumar, A. Karakoti and A. Vinu, Sci. Technol. Adv. Mater., 2022, 23, 76–119 CrossRef CAS PubMed
.
- X. Wang, K. Maeda, A. Thomas, K. Takanabe, G. Xin, J. M. Carlsson, K. Domen and M. Antonietti, Nat. Mater., 2009, 8, 76–80 CrossRef CAS PubMed
.
- S. H. Li, M. Y. Qi, Z. R. Tang and Y. J. Xu, Chem. Soc. Rev., 2021, 50, 7539–7586 RSC
.
- J. F. Callejas, J. M. McEnaney, C. G. Read, J. C. Crompton, A. J. Biacchi, E. J. Popczun, T. R. Gordon, N. S. Lewis and R. E. Schaak, ACS Nano, 2014, 8, 11101–11107 CrossRef CAS PubMed
.
- Y. Ni, L. Jin and J. Hong, Nanoscale, 2011, 3, 196–200 RSC
.
- S. Li, L. Wang, N. Xiao, A. Wang, X. Li, Y. Gao, N. Li, W. Song, L. Ge and J. Liu, Chem. Eng. J., 2019, 378, 122220 CrossRef CAS
.
- Y. Song, X. Xin, S. Guo, Y. Zhang, L. Yang, B. Wang and X. Li, Chem. Eng. J., 2020, 384, 123337 CrossRef CAS
.
- S. Cao, Y. Chen, C. J. Wang, X. J. Lv and W. F. Fu, Chem. Commun., 2015, 51, 8708–8711 RSC
.
- S. Cao, C. J. Wang, W. F. Fu and Y. Chen, ChemSusChem, 2017, 10, 4306–4323 CrossRef CAS PubMed
.
- Y. Han, Y. Chen, R. Fan, Z. Li and Z. Zou, EcoMat, 2021, 3, e12097 CrossRef CAS
.
- Z. Hu, Z. Shen and C. Y. Jimmy, Green Chem., 2017, 19, 588–613 RSC
.
- X. Yue, S. Yi, R. Wang, Z. Zhang and S. Qiu, Small, 2017, 13, 1603301 CrossRef PubMed
.
- P. Wang, S. Zhan, H. Wang, Y. Xia, Q. Hou, Q. Zhou, Y. Li and R. R. Kumar, Appl. Catal., B, 2018, 230, 210–219 CrossRef CAS
.
- J. Wang, J. Chen, P. Wang, J. Hou, C. Wang and Y. Ao, Appl. Catal., B, 2018, 239, 578–585 CrossRef CAS
.
- Z. Sun, M. Zhu, X. Lv, Y. Liu, C. Shi, Y. Dai, A. Wang and T. Majima, Appl. Catal., B, 2019, 246, 330–336 CrossRef CAS
.
- L. Hong, R. Guo, Y. Yuan, X. Ji, Z. Lin, Z. Li and W. Pan, ChemSusChem, 2021, 14, 539–557 CrossRef CAS PubMed
.
- H. Zhou, R. Chen, C. Han, P. Wang, Z. Tong, B. Tan, Y. Huang and Z. Liu, J. Colloid Interface Sci., 2022, 610, 126–135 CrossRef CAS
.
- R. Liang, Y. Wang, C. Qin, X. Chen, Z. Ye and L. Zhu, Langmuir, 2021, 37, 3321–3330 CrossRef CAS PubMed
.
- G. Fan, F. Li, D. G. Evans and X. Duan, Chem. Soc. Rev., 2014, 43, 7040–7066 RSC
.
- H. Boumeriame, E. S. Da Silva, A. S. Cherevan, T. Chafik, J. L. Faria and D. Eder, J. Energy Chem., 2022, 64, 406–431 CrossRef CAS
.
- Y. Zhao, X. Jia, G. I. N. Waterhouse, L. Z. Wu, C. H. Tung, D. O'Hare and T. Zhang, Adv. Energy Mater., 2016, 6, 1501974 CrossRef
.
- L. Mohapatra and K. Parida, J. Mater. Chem. A, 2016, 4, 10744–10766 RSC
.
- M. J. Wu, J. Z. Wu, J. Zhang, H. Chen, J. Z. Zhou, G. R. Qian, Z. P. Xu, Z. Du and Q. L. Rao, Catal. Sci. Technol., 2018, 8, 1207–1228 RSC
.
- C. Prasad, H. Tang, Q. Q. Liu, S. Zulfiqar, S. Shah and I. Bahadur, J. Mol. Liq., 2019, 289, 111114 CrossRef CAS
.
- G. Arrabito, A. Bonasera, G. Prestopino, A. Orsini, A. Mattoccia, E. Martinelli, B. Pignataro and P. G. Medaglia, Crystals, 2019, 9, 361 CrossRef CAS
.
- A. Sherryna, M. Tahir and W. Nabgan, Int. J. Hydrogen Energy, 2021, 47, 862–901 CrossRef
.
- A. Razzaq, S. Ali, M. Asif and S. I. In, Catalysts, 2020, 10, 1185 CrossRef
.
- M. P. Jerome, F. A. Abdulkarim, M. T. Salem and M. Tahir, J. Environ. Chem. Eng., 2022, 108151 CrossRef CAS
.
- Z. Yang, F. Wang, C. Zhang, G. Zeng, X. Tan, Z. Yu, Y. Zhong, H. Wang and F. Cui, RSC Adv., 2016, 6, 79415–79436 RSC
.
- T. Cheng, H. Gao, G. Liu, Z. Pu, S. Wang, Z. Yi, X. Wu and H. Yang, Colloids Surf., A, 2022, 633, 127918 CrossRef CAS
.
- Y. Wu, X. Li, H. Zhao, F. Yao, J. Cao, Z. Chen, D. Wang and Q. Yang, Chem. Eng. J., 2021, 426, 131255 CrossRef CAS
.
- S. He, C. Yan, X. Z. Chen, Z. Wang, T. Ouyang, M. L. Guo and Z. Q. Liu, Appl. Catal., B, 2020, 276, 119138 CrossRef CAS
.
- S. Guo, L. Yang, Y. Zhang, Z. Huang, X. Ren, E. I. Wei and X. Li, J. Alloys Compd., 2018, 749, 473–480 CrossRef CAS
.
- A. Balapure, Y. Nikhariya, N. S. Sriteja Boppudi, R. Ganesan and J. Ray Dutta, ACS Appl. Mater. Interfaces, 2020, 12, 21481–21493 CrossRef CAS PubMed
.
- A. Balapure, H. Mude, P. Tata, J. R. Dutta and R. Ganesan, J. Environ. Chem. Eng., 2021, 9, 106065 CrossRef CAS
.
- B. Li, Z. Cao, S. Wang, Q. Wei and Z. Shen, Dalton Trans., 2018, 47, 10288–10298 RSC
.
- Q. Chen, M. Zhang, J. Li, G. Zhang, Y. Xin and C. Chai, Chem. Eng. J., 2020, 389, 124476 CrossRef CAS
.
- B. Wang, C. Chen, Y. Jiang, P. Ni, C. Zhang, Y. Yang, Y. Lu and P. Liu, Chem. Eng. J., 2021, 412, 128690 CrossRef CAS
.
- L. Wang, G. Tang, S. Liu, H. Dong, Q. Liu, J. Sun and H. Tang, Chem. Eng. J., 2022, 428, 131338 CrossRef CAS
.
- A. Bahadoran, S. Ramakrishna, S. Masudy-Panah, J. R. De Lile, J. Gu, Q. Liu and Y. K. Mishra, Ind. Eng. Chem. Res., 2022, 61, 10931–10944 CrossRef CAS
.
- Z. Guan, Z. Xu, Q. Li, P. Wang, G. Li and J. Yang, Appl. Catal., B, 2018, 227, 512–518 CrossRef CAS
.
- M. Zhang, C. Lai, B. Li, F. Xu, D. Huang, S. Liu, L. Qin, Y. Fu, X. Liu and H. Yi, Chem. Eng. J., 2020, 396, 125343 CrossRef CAS
.
- X. Liu, C. Bie, B. He, B. Zhu, L. Zhang and B. Cheng, Appl. Surf. Sci., 2021, 554, 149622 CrossRef CAS
.
- Y. Jiang, Z. Sun, Q. Chen, C. Cao, Y. Zhao, W. Yang, L. Zeng and L. Huang, Appl. Surf. Sci., 2022, 571, 151287 CrossRef CAS
.
- D. Kong, X. Ruan, J. Geng, Y. Zhao, D. Zhang, X. Pu, S. Yao and C. Su, Int. J. Hydrogen Energy, 2021, 46, 28043–28052 CrossRef CAS
.
- L. Zhu, H. Li, Z. Liu, P. Xia, Y. Xie and D. Xiong, J. Phys. Chem. C, 2018, 122, 9531–9539 CrossRef CAS
.
- Y. Sun, X. Wang, Q. Fu and C. Pan, Appl. Surf. Sci., 2021, 564, 150379 CrossRef CAS
.
- C. Hao, Y. Tang, W. Shi, F. Chen and F. Guo, Chem. Eng. J., 2021, 409, 128168 CrossRef CAS
.
- B. Tahir and M. Tahir, Appl. Surf. Sci., 2020, 506, 145034 CrossRef CAS
.
- Z. Kong, J. Zhang, H. Wang, B. Cui, J. Zeng, X. Chen, P. Tian, G. Huang, J. Xi and Z. Ji, Int. J. Energy Res., 2020, 44, 1205–1217 CrossRef CAS
.
- H. Hou and X. Zhang, Chem. Eng. J., 2020, 395, 125030 CrossRef CAS
.
- R. Xiao, C. Zhao, Z. Zou, Z. Chen, L. Tian, H. Xu, H. Tang, Q. Liu, Z. Lin and X. Yang, Appl. Catal., B, 2020, 268, 118382 CrossRef CAS
.
- Q. Wang, H. Zhu and B. Li, Chem. Eng. J., 2019, 378, 122072 CrossRef CAS
.
- M. Wang, M. Shen, L. Zhang, J. Tian, X. Jin, Y. Zhou and J. Shi, Carbon, 2017, 120, 23–31 CrossRef CAS
.
- M. Z. Qin, W. X. Fu, H. Guo, C. G. Niu, D. W. Huang, C. Liang, Y. Y. Yang, H. Y. Liu, N. Tang and Q. Q. Fan, Adv. Colloid Interface Sci., 2021, 297, 102540 CrossRef CAS
.
- B. Zhu, B. Cheng, J. Fan, W. Ho and J. Yu, Small Struct., 2021, 2, 2100086 CrossRef CAS
.
- Q. Zhu, Y. Sun, S. Xu, Y. Li, X. Lin and Y. Qin, J. Hazard. Mater., 2020, 382, 121098 CrossRef CAS
.
- A. Balapure, M. M. Francis, H. Mude, P. A. Maroju, J. R. Dutta and R. Ganesan, Carbon Trends, 2021, 5, 100118 CrossRef CAS
.
- A. Balapure and R. Ganesan, J. Colloid Interface Sci., 2021, 581, 205–217 CrossRef CAS
.
- M. M. Francis, A. Thakur, A. Balapure, J. R. Dutta and R. Ganesan, Chem. Eng. J., 2022, 446, 137363 CrossRef
.
- S. Li, H. Shang, Y. Tao, P. Li, H. Pan, Q. Wang, S. Zhang, H. Jia, H. Zhang, J. Cao, B. Zhang, R. Zhang, G. Li, Y. Zhang, D. Zhang and H. Li, Angew. Chem., Int. Ed., 2023, 62, e202305538 CrossRef CAS PubMed
.
- Y. Tao, Z. Ma, W. Wang, C. Zhang, L. Fu, Q. Zhu, Y. Li, G. Li and D. Zhang, Adv. Funct. Mater., 2023, 33, 2211169 CrossRef CAS
.
- A. Akhundi, A. Badiei, G. M. Ziarani, A. Habibi Yangjeh, M. J. Munoz-Batista and R. Luque, Mol. Catal., 2020, 488, 110902 CrossRef CAS
.
|
This journal is © The Royal Society of Chemistry 2024 |
Click here to see how this site uses Cookies. View our privacy policy here.