DOI:
10.1039/D4NA00517A
(Review Article)
Nanoscale Adv., 2024,
6, 4781-4803
Metal oxide-based photocatalysts for the efficient degradation of organic pollutants for a sustainable environment: a review
Received
23rd June 2024
, Accepted 14th August 2024
First published on 22nd August 2024
Abstract
Photocatalytic degradation is a highly efficient technique for eliminating organic pollutants such as antibiotics, organic dyes, toluene, nitrobenzene, cyclohexane, and refinery oil from the environment. The effects of operating conditions, concentrations of contaminants and catalysts, and their impact on the rate of deterioration are the key focuses of this review. This method utilizes light-activated semiconductor catalysts to generate reactive oxygen species that break down contaminants. Modified photocatalysts, such as metal oxides, doped metal oxides, and composite materials, enhance the effectiveness of photocatalytic degradation by improving light absorption and charge separation. Furthermore, operational conditions such as pH, temperature, and light intensity also play a crucial role in enhancing the degradation process. The results indicated that both high pollutant and catalyst concentrations improve the degradation rate up to a threshold, beyond which no significant benefits are observed. The optimal operational conditions were found to significantly enhance photocatalytic efficiency, with a marked increase in degradation rates under ideal settings. Antibiotics and organic dyes generally follow intricate degradation pathways, resulting in the breakdown of these substances into smaller, less detrimental compounds. On the other hand, hydrocarbons such as toluene and cyclohexane, along with nitrobenzene, may necessitate many stages to achieve complete mineralization. Several factors that affect the efficiency of degradation are the characteristics of the photocatalyst, pollutant concentration, light intensity, and the existence of co-catalysts. This approach offers a sustainable alternative for minimizing the amount of organic pollutants present in the environment, contributing to cleaner air and water. Photocatalytic degradation hence holds tremendous potential for remediation of the environment.
Introduction
Urbanization and industrialization are cornerstones of modern civilization, underpinning significant advances in economic growth, technological innovation, and improved standards of living.1 These processes have facilitated the development of cities, expanded infrastructure, and increased industrial productivity, creating myriad opportunities for societal progress.2,3 However, the rapid pace of urbanization and industrialization has also ushered in substantial environmental challenges, particularly through the generation of wastewater that contains a diverse array of organic pollutants.4–6 These pollutants are frequently hazardous, presenting significant hazards to both the environment and public health, in contrast to conventional treatment procedures.7–9 Industrial operations are major contributors to wastewater pollution, as they produce effluents laden with complex organic chemicals.10–12 These chemicals are often by-products of various industrial processes and include a wide variety of substances such as antibiotics, organic dyes, nitrobenzene, cyclohexane, phenols, toluene, biphenyls, pesticides, fertilizers, hydrocarbons, plasticizing agents, detergents, oils, greases, proteins, and carbohydrates.13–15 The environmental impact of these pollutants is profound, as they can persist in the environment, bioaccumulate in wildlife, and enter human food chains, leading to chronic health issues and ecological damage.16,17 The complexity and resilience of these organic pollutants necessitate the development of advanced treatment technologies.18,19 Traditional biological treatment methods are often inadequate for fully degrading these pollutants due to their toxicity and chemical stability. In response to this challenge, Advanced Oxidation Processes (AOPs) have been developed and are increasingly being employed for the effective degradation of hazardous organic contaminants present in wastewater.20–22 AOPs are distinguished by the production of extremely reactive species, such as hydroxyl radicals, that can indiscriminately oxidize a broad spectrum of organic pollutants. This process converts the pollutants into less dangerous chemicals or fully mineralizes them into carbon dioxide (CO2) and water (H2O).23 Among the various AOPs, photocatalytic degradation stands out as a particularly effective method.20 Photocatalysis involves the use of semiconductor materials as catalysts to accelerate chemical reactions upon exposure to light. When semiconductor materials such as zinc oxide (ZnO), iron oxide (Fe2O3), titanium dioxide (TiO2), gallium phosphide (GaP), cadmium sulfide (CdS), and zinc sulfide (ZnS) are exposed to light, they generate electron–hole pairs that can generate reactive oxygen species.24–26 These reactive species possess the very capability of breaking down complex organic pollutants into less harmful, simpler molecules and fully mineralizing them.27,28 The advantages of photocatalysis are numerous and include low operational costs, the ability to accomplish full mineralization of contaminants without generating secondary pollution, and the capability to operate at ambient temperatures and pressures.29 Among the various photocatalysts, titanium dioxide (TiO2) is the most extensively studied and broadly applied because of its exceptional chemical and photochemical stability, cost-effectiveness, low toxicity, and high activity under ultraviolet (UV) light. TiO2, with its wide band gap of approximately 3.2 eV, can mineralize a broad spectrum of organic contaminants, including herbicides, dyes, pesticides, phenolic compounds, and pharmaceuticals like tetracycline and sulfamethazine.30,31 Nevertheless, the actual utilization of TiO2 is somewhat restricted due to its dependence on UV light, which comprises just a minor portion of the solar spectral region.32 To overcome this limitation, other semiconductor materials with broader light absorption properties are being explored. Tungsten trioxide (WO3) has emerged as a promising alternative due to its capability of absorbing visible light, making it more competent for photocatalytic oxidation of volatile organic pollutants under natural sunlight.33,34 Additionally, silver nanoparticles (AgNPs) have gained significant attention as photocatalysts due to their high photostability, environmental friendliness, and catalytic properties that are dependent on their shape and size.35 The effectiveness of photocatalytic systems in degrading organic pollutants is dependent on numerous operational parameters. These factors encompass the substrate concentration, photocatalyst quantity, pH of the solution, reaction medium temperature, light irradiation duration and intensity, photocatalyst surface area, dissolved oxygen content in the reaction medium, and the characteristics of both the photocatalyst and substrate.29,36,37 Furthermore, the doping of photocatalysts with metal and non-metal ions can enhance their photocatalytic activity by modifying their electronic properties and extending their light absorption range.38 It is important to optimize these parameters to maximize the degradation kinetics and overall efficiency of photocatalytic processes.39 For instance, the proportion of the substrate to the photocatalyst must be carefully balanced to ensure that there are enough reactive sites for pollutant molecules to adsorb and react.37 The pH of the solution can affect the charge and surface properties of the photocatalyst, influencing its interaction with pollutants. Temperature and light intensity also play significant roles in determining the rate of photocatalytic reactions, with higher temperatures and light intensities generally leading to increased reaction rates.40–42 In this review, we focused on the degradation of six specific types of organic pollutants: antibiotics, organic dyes, nitrobenzene, toluene, oil, and cyclohexane. These pollutants represent a broad spectrum of chemical structures and environmental impacts, making them ideal candidates for studying the effectiveness of various photocatalysts under different operational conditions. We will delve into the various reaction parameters that are critical to achieving maximum degradation of these pollutants using different photocatalysts. This comprehensive analysis aims to provide insights into the optimal conditions and catalyst selections for effective wastewater treatment, contributing to the mitigation of environmental pollution and the protection of aquatic ecosystems.
Photocatalytic degradation of chemical pollutants (organic dyes and antibiotics)
Chemical pollutants refer to a large group of contaminants that arise from different sources, including pharmaceuticals,43 personal care items,44 pesticides,45 and other synthetic chemicals.46 Chemical pollutants, such as antibiotics and organic dyes, have significant adverse effects on the environment.47 Antibiotics, encompassing classes such as beta-lactams (e.g., penicillins, cephalosporins), macrolides (e.g., erythromycin), tetracyclines (e.g., doxycycline), aminoglycosides (e.g., gentamicin), quinolones (e.g., ciprofloxacin), sulfonamides (e.g., sulfamethoxazole), glycopeptides (e.g., vancomycin), and oxazolidinones (e.g., linezolid), are significant pharmaceutical pollutants.48 Organic dyes, including azo dyes (e.g., methyl orange), anthraquinone dyes (e.g., alizarin), phthalocyanine dyes (e.g., copper phthalocyanine), triphenylmethane dyes (e.g., malachite green), xanthene dyes (e.g., fluorescein), and indigoid dyes (e.g., indigo carmine), are prevalent industrial pollutants.49 Both types of pollutants are persistent in water bodies, posing substantial dangers to aquatic ecosystems and human health due to their toxicity, bioaccumulation potential, and the propagation of antibiotic-resistant bacteria.50,51 The persistence and toxicity of these chemical pollutants necessitate effective remediation strategies, such as photocatalytic degradation, which utilizes light-activated catalysts to break down these harmful substances into harmless by-products, ensuring cleaner water and healthier ecosystems.52
Organic dyes
A significant group of synthetic organic molecules produced by a variety of industries, including the leather, plastic, food, paper, textile, and medicinal sectors, are known as dyes.35,53 Due to their frequent application in various manufacturing sectors, dyes are inevitably accidentally released into the environment, particularly into either surface water or groundwater, where they may pose serious dangers to environmental and biological systems.54–57 Over 700
000 tons of dyes are generated globally each year; 20% of these lost dyes reach the atmosphere and create pollution throughout processing or manufacturing, accounting for about 12% of the global total of dye generation. So the degradation of these organic dyes is necessary for maintaining the ecological balance.58 Organic dyes are very detrimental to aquatic ecosystems, even at low concentrations (less than 1 ppm). Thus, it is essential and required to remove organic dyes from effluents.59 The degradation mechanism of methylene blue dye is as follows.60 | Photocatalyst + hν (photon) → Photocatalyst (ecb− + hvb+) | (1) |
| Methylene blue + ˙OH → Degradation products | (5) |
| Methylene blue + ˙O2− → Degradation products | (6) |
| Degradation products + ˙OH/O2 → CO2 + H2O + Inorganic ions | (7) |
Several metal oxides, such as ZnO, MgO, AgO, TiO2, Fe2O3, Mn2O3, CuO, and V2O5, are frequently employed as photocatalysts in wastewater treatment processes to degrade dyes.61 Zinc oxide (ZnO) is an oxidizing substance found in nature as the unusual mineral zincite. There have been attempts to use ZnO alongside other semiconductors for the photocatalytic degradation of an extensive variety of biological pollutants.62 ZnO-based photocatalysts work according to various parameter conditions. These parameters are mainly Ph, the initial concentration of dye or catalyst, the wavelength of the light & so on. The photocatalytic reaction rate at the outermost layer of the catalyst can be influenced by the initial concentration of the substrate. To prevent the dispersion of light and the concentration impact of the exposed photocatalyst surface, the ideal photocatalyst concentration ought to be unique for heterogeneous photocatalysis processes.63 Velmurugan et al. stated that the rate of degradation k dropped from 0.173 to 0.012 min−1 when the dye concentration was increased from 1 × 10−4 to 4 × 10−4 M.64 This is because many layers of adsorbed dye molecules have formed on the outermost layer of the catalyst, which prevents the photoreaction from occurring because there was not enough direct light interaction to produce hydroxyl radicals.65 The first amount of dye has a significant influence on the degradation efficiency of MB.66 Sobana et al. used ZnO that was manually combined with activated carbon (AC–ZnO) and solar irradiation to study the impact of initial Direct Blue 53 (DB53) concentration over the concentration range from 1 × 10−4 to 9 × 10−4 M.67 Its numerous functions make it extremely difficult to determine how the pH of a solution affects the efficacy of the dye photocatalytic degradation activity.68 Velmurugan et al. stated the impact of pH in the range of 3–11 upon the photocatalytic breakdown of Reactive Red 120 (RR 120) over ZnO during solar light irradiation.64 Photocatalytic breakdown of Reactive Orange 4 (RO4) and Black 5 (RB5) dyes occurs at various solution pH levels between 3 and 11.69 The pH, which regulates the adsorption of organic compounds on the outermost layer of the photocatalyst, serves as one of the most crucial factors influencing photocatalysis effectiveness.70 Electromagnetic relationships between the outermost layer of the photocatalyst and the substrate of interest can be employed to clarify how pH affects photocatalysis outcomes.27 Singh et al. stated that after exposing ZnO nanorods to UV radiation for 120 minutes, photodegradation activity levels were 7.169% and 47.63% for pH values of 4.5 and 10.5, correspondingly.71
Scientists' interest has been drawn more and more to supported TiO2 catalyst utilization over the past few years due to its prospective uses in the photocatalytic breakdown of organic contaminants such as organic dyes in air and water. Additionally, reports have it that when adsorbents are used to support TiO2, an ideal condition is created for the elimination or degradation of the compounds of interest.72,73 To enhance TiO2-based photocatalysts on organic dye in wastewater, several conditions were adjusted. These crucial elements, which included light intensity, TiO2 form and structure, target type, pH level and doping type, all had an impact on the photocatalysis method's effectiveness.58 If we want to discuss the parameters it is found that it is rather tough to comprehend how pH impacts the photodegradation process's efficacy.29 TiO2 exhibits amphoteric properties, allowing for the development of either a positive or negative charge on its outermost layer.74 Due to this, the adsorption of dye molecules over TiO2 surfaces may be affected by changes in pH.75 Bubacz et al. found that when pH is increased, so did the rate at which methylene blue was broken down photo-catalytically.76 On the other hand, Neppolian et al. showed that acidic conditions do not affect the degradation rate of the Reactive Blue 4 significantly enough.77 It has been found that organic dyes like Reactive Black 5 and Reactive Orange 4 degradation were enhanced in an acidic solution containing TiO2.69 Tanaka et al. discovered that at less acidic values, the positively charged TiO2 layer absorbed more Acid Orange 7, and greater breakdown was accomplished.78 A study has been conducted on the effects of pH on the adsorption as well as decolorization of Procion Red MX-5B (MX-5B) and Cationic Blue X-GRL (CBX). It was discovered that when the pH increased, MX-5B's adsorption was reduced.62 Another key parameter for dye degradation using a TiO2 catalyst is the dye amount or dye concentration. It has been found that the increased initial concentration of the dyes increases the degradation rate.36,79 This is because when the dye's initial concentrations rise, the dye molecules become deposited on the outermost layer of the catalyst and consume a sizable proportion of UV light instead of the TiO2 nanoparticles.80,81 Neppolian et al. investigated how the original dye concentration affected the percentage of degradation. With the best possible catalyst loading, they changed the starting concentrations of Reactive Yellow 17 (from 8.9 × 10−4 to 1.29 × 10−3 M), Reactive Red 2 (from 4.169 × 10−4 to 1.259 × 10−3 M), and Reactive Blue 4 (from 1.9 × 10−4 to 5.9 × 10−4 M).77 The dye degradation in a water-based solution utilizing a catalyst powder of TiO2 within a photocatalytic reactor is influenced by two additional parameters: the wavelength and intensity of the UV light irradiation source.82 Lower radiation wavelengths are thought to encourage the creation of electron holes, which would increase the catalyst's effectiveness.83 Ollis et al. said that at minimal light levels (0–20 mW cm−2), the rate would rise in an orderly manner as the intensity of light increased. The rate would rely on the square root of the light intensity at moderate light intensities (about 25 mW cm−2) but at intense light levels, the rate is independent of the light intensity.29,84 The degradation of Orange G was shown to be affected by light intensity in a range of 215 to 586 W cm−2. With a rise in light magnitude, Orange G's photolysis reaction rates climbed.85 Rao et al. stated that Acid Orange 7 (AO7) photocatalytically breaks down at a pace that is roughly 1.5 times faster in direct sunlight compared to that under synthetic UV radiation.86 Another significant operational parameter for the organic dye degradation is temperature range.36 The range of 40–50 °C was determined to be the ideal operating temperature range. Since desorption of the produced products happens more slowly at low temperatures than interface degradation as well as reactant adsorption, it restricts the reaction. Conversely, the limiting step becomes the dye's adsorption on TiO2 at an elevated temperature.87 A table has been added showing the photocatalytic degradation of organic pollutants (Table 1) and the process is illustrated in Fig. 1. The rate constant is lowered at elevated temperatures due to the organics' and hydrated oxygen's reduced adsorptive ability. Consequently, the ideal temperature often falls between 293 and 353 K.108,109
Table 1 Data for the photocatalytic degradation of organic dyes using various catalystsa
Pollutants |
Pollutant conc. (mg L−1) |
Catalyst |
Catalyst conc. (mg L−1) |
Operational conditions |
Lamp, power (W) |
Degradation percentage (%), time (min) |
Ref. |
MB = Methylene Blue, IC = Indigo Carmine, RhB = Rhodamine B, AR57 = Acid Red 57, CR = Congo Red, MO = Methyl Orange, AR27 = Acid Red 27, AB25 = Acid Blue 25, RO16 = Reactive Orange 16.
|
MB |
63.97 |
Mn-doped ZnO |
— |
Visible light; light intensity: 18.6 lux |
Tungsten lamp, 500 |
50%, 10 |
88
|
IC |
10 |
CA–CNT/TiO2–NH2 |
— |
UV light (315–400 nm), pH = 2, temp = 80 °C |
40 |
100%, 180 |
89
|
MB |
30 |
CA–CNT/TiO2–NH2 |
— |
UV light (315–40 nm), pH = 2, temp = 80 °C |
40 |
80%, 300 |
89
|
RhB |
6 |
Nanostructured TiO2 |
0.0001–0.0005 |
UV light, pH = around 7 |
— |
93.8%, 190 |
90
|
AR57 |
30 |
TiO2 |
0.0005 |
UV light, pH = 7.18, temp = 400 °C |
— |
90.7%, 190 |
90
|
CR |
75 |
ZnO |
0.00016 |
Solar light, pH = 6 |
— |
97%, 120 |
91
|
MB |
50 |
Cu-doped ZnO (NPs) |
— |
Visible light |
300 |
85%, 60 |
92
|
RhB |
10 |
WO3/Ag2CO3 |
— |
Visible light |
Metal halide lamp, 70 |
99.7%, 8 |
93
|
MB |
64 |
Undoped ZnO |
— |
Visible light; light intensity: 18.6 lux |
Tungsten lamp, 500 |
50%, 30 |
67
|
MO |
10 |
2% Al–2% Ni–ZnO |
500 |
Visible light |
Halogen lamp, 100 |
99%, 30 |
94
|
MB |
— |
Nano ZnO |
— |
UV light |
Mercury vapor lamp, 8 |
97.64%, 120 |
95
|
MO |
25 |
ZnO/Cu2O |
— |
UV light |
Tungsten lamp, 200 |
73%, 180 |
96
|
AR27 |
— |
Ce–ZnO |
0.004 |
Solar light, degradation steadily increased up to pH = 12 |
— |
90%, 60 |
79
|
MO |
15 |
ZnO NFs |
— |
UV light |
— |
99.46%, 50 |
97
|
MO |
— |
Natural zeolite supported TiO2 |
0.0006–0.004 |
UV light, pH = 4 |
— |
96.58%, 100 |
98
|
AB25 |
100 |
MgAl2O4 nanoparticles |
— |
UV, pH = 3 |
— |
99.86%, 35 |
99
|
MB |
50 |
ZnO NPs |
— |
UV/visible, — |
— |
100% under UV irradiation in 20 min, 91% under visible light in 60 min |
100
|
RhB |
10 |
TiO2/g-C3N4 |
— |
Solar light, temp: 350 °C |
Compact xenon lamp, 300 |
95%, 120 |
101
|
MO |
10 |
[Zn(L)(H2O)]·H2O |
— |
UV light, — |
High pressure Hg lamp, 300 |
83,8%, 120 |
102
|
MB |
5 |
ZnO nanowires |
— |
UV light, — |
High pressure Hg lamp, 50 |
96%, 120 |
103
|
IC |
10 |
TiO2–NH2 NPs |
|
UV light, pH = 2, temp: 80 °C |
UV lamp, 40 |
100%, 180 |
89
|
RhB |
0.001 |
Floral-like LaFeO3 |
— |
Visible light, — |
High pressure Hg lamp, 150 |
—, 720 |
104
|
RhB |
23.4 |
ZnO |
400 |
pH = 7 |
— |
—, 180 |
105
|
RO16 |
20–60 |
TiO2 |
90 |
UV light, pH = 7.0, temp: 25 °C |
Xenon lamp, — |
87% after 20 min, 70% after 20 min, nearly 100% after 120 min |
106
|
MO |
— |
PbBiO2Br |
— |
Visible light |
Xe arc lamp, 300 |
95%, 60 |
107
|
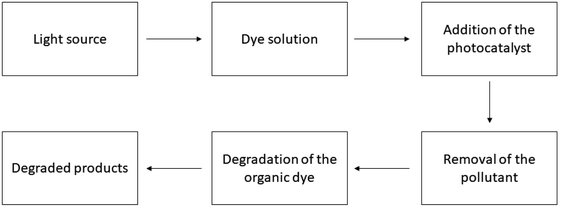 |
| Fig. 1 Working procedure of the photocatalyst for dye degradation. | |
Antibiotics
Due to their extremely stable and non-biodegradable nature, antibiotics accumulate in the ecosystem as a result of overuse and uncontrolled environmental discharge.110,111 The release of diverse antimicrobial pollutants and their varied toxicity provide a significant challenge for researchers trying to find a solution.112,113 The excessive accumulation of antibiotics in natural environments has presented a significant peril to ecological systems.114,115 Unfortunately, traditional water treatment methods such as adsorption, filtration, and biodegradation are ineffective in effectively removing antibiotics due to their significant durability and limited biodegradability. Hence, the development of novel technologies is vital to ensure the efficient elimination of antibiotics.116–119 Due to its advantageous characteristics of cost-effectiveness, environmental sustainability, and high efficacy, heterogeneous photocatalysis has become a process of great promise for wastewater treatment, which relies on the direct utilization of sunlight to effectively degrade and subsequently mineralize organic pollutants, and has emerged as a promising approach to tackle diverse environmental challenges.120–122 Furthermore, it is crucial to provide an overview of frequently utilized photocatalytic nanomaterials and their specific use in breaking down popular antibiotics. This is necessary to validate their practical superiority and efficacy as catalysts for the process of photodegradation.123–125 The degradation mechanism of ciprofloxacin antibiotic in the presence of different photocatalysts is provided.126 | Photocatalyst + hν (photon) → Photocatalyst (ecb− + hvb+) | (8) |
| hvb+ + H2O → ˙OH + H+ | (10) |
| Ciprofloxacin + ˙OH → Degradation products | (12) |
| Ciprofloxacin + ˙O2− → Degradation products | (13) |
| Degradation products + ˙OH/O2 → CO2 + H2O + Inorganic ions | (14) |
Yang et al. researched the degradation of ciprofloxacin using g-C3N4/TiO2 nanocomposites with the help of visible light irradiation utilizing a 300 W Xe visible lamp where the authors observed 88% of CIP degraded in 180 minutes.127 Verma explored the degradation of amoxicillin (AMX) by the utilization of TiO2 photocatalysis and sono-photocatalysis and achieved the highest degradation rate (80%) of AMX at a pH of 7.0 under UV irradiation at a power density of 672 W m−2.128 Zhang examined the mechanism and kinetics of photocatalytic degradation of tetracycline (TC) utilizing a supramolecular organic photocatalyst called three-dimensional network structure perylene diimide (3D-PDI).129 Fan et al. synthesized three different structures of bi-modified titanate nanomaterials (Bi-TNM) utilizing the hydrothermal technique and carefully adjusted variables to break down paracetamol (ACT). The study revealed that bi-titanate nanoribbons, when used at a concentration of 1 g L−1, had the most effective photocatalytic degradation capability, achieving a rate of 88%.130 The catalytic efficiency of NiS and NiS immobilized within the magnetite polypyrrole core/shell matrix (Fe3O4@PPY) was examined for the degradation of cephalexin. The study also examined the photocatalytic breakdown of cefalexin using the NiS-PPY-Fe3O4 photocatalyst, which was exposed to sunshine. The photocatalyst demonstrated a removal efficiency of over 80% over a 30 minute timeframe.131 Payan studied the creation of photocatalysts using Cu–TiO2@functionalized single-walled carbon nanotubes and found that sulfamethazine can be fully destroyed under solar irradiation within 300 minutes.132 R. Kumar et al. synthesized BN/CdAl2O4 composites and evaluated their photocatalytic ability to degrade cefoxitin sodium (CFT) antibiotic in an aqueous solution. The findings demonstrated that a nearly complete degradation of CFT, reaching approximately 100%, occurred within 240 minutes at a concentration of 15 mg L−1 and a pH of 7.133 A bismuth oxybromide (BiOBr) photocatalyst capped with PVP was produced by a solvothermal technique. The PVP-capped BiOBr exhibits a removal efficiency of 94% and 99.8% for the antibiotics ofloxacin (OFL) and norfloxacin (NOR) respectively, when exposed to visible light.134 Y. Gong prepared Z-scheme CdTe/TiO2 heterostructure photocatalysts decomposing 78% tetracycline hydrochloride (TC-H) within 30 min of irradiation under visible light.135 W. Wang examined the photocatalytic efficiency of BiVO4/TiO2/RGO composites for four tetracycline antibiotics. The BiVO4/TiO2/RGO photocatalyst demonstrated significant photocatalytic activity and compatibility, providing efficient separation of photo-generated carriers with oxidation capabilities and high reduction.136 N. Askari synthesized a novel heterojunction Z-scheme MnWO4/Bi2S3 using a hydrothermal technique to study the photocatalytic behavior of catalysts in the decomposition of metronidazole (MTZ) and cephalexin (CFX) under LED light exposure where a maximum degradation efficiency of 78.8% was achieved for CFX and 83.3% for MTZ.137 A. Mohammad et al. studied manufactured nanostructured photocatalysts composed of tin oxide (SnO2) and cerium oxide (CeO2). These photocatalysts were employed to degrade the antibiotic tetracycline hydrochloride (TC) under visible light. The most optimal outcome seen among the examined photocatalysts had a TC removal effectiveness of approximately 97% within a 120 minute timeframe under visible-light exposure.138 An investigation was conducted on the photocatalytic degradation of pharmaceutical micropollutants of Penicillin G (PG) in a photoreactor. The proficiency of the photocatalytic process was increased by the inclusion of persulfate sodium (PPS). The inclusion of PPS greatly enhanced the efficiency of the photolysis process, resulting in a considerable improvement of 72.72% compared to the traditional photocatalysis system, which achieved 56.71% efficiency.139 Bouyarmane synthesized TiO2-hydroxyapatite nanocomposites precipitating a re-dissolved natural phosphate mineral in ammonia using the concurrent gelation of titanium alkoxide. These nanocomposites were then subjected to degradation for drug testing in a solution under ultraviolet light. When utilizing 40TiHAp as a photocatalyst, ciprofloxacin and ofloxacin were destroyed through photodegradation in 15 minutes and 120 minutes, respectively.140 A simple solvothermal technique was employed to synthesize a novel Cu3P–ZSO–CN p–n–n heterojunction photocatalyst for the degradation of the antibiotic tetracycline (TC) under exposure to visible light. The degradation efficiency for TC was found to be 98.45%.141 M. Abdullah et al. synthesized ACT-X nanocomposites using activated carbon and TiO2 to enhance the inherent characteristics of TiO2, resulting in improved light absorption in the visible area. The ACT-4 photocatalyst has demonstrated the maximum level of photocatalytic degradation (99.6%) for the ceftriaxone (CEF) antibiotic.142 The very first 3D hierarchical ZnO/Bi2MoO6 heterojunctions were synthesized using an in situ solvothermal technique. These heterojunctions exhibited a remarkable efficiency of 100% in the photodegradation of the ofloxacin (OFL) antibiotic. This exceptional performance can be ascribed to their reduced electron–hole recombination rate and large surface area.143 A novel heterojunction photocatalyst (MoO3/g-C3N4) was synthesized using a straightforward hydrothermal calcination technique. The catalytic efficiency of this photocatalyst was assessed by measuring its ability to degrade tetracycline. The findings demonstrated that the 0D-2D MoO3/g-C3N4 Z-scheme heterojunction outperformed the original g-C3N4 and achieved an impressive 85.9% removal efficiency within 100 minutes when exposed to visible light.144 E. Gómez et al. fabricated highly efficient photocatalysts by using electrochemical deposition and thermal treatment. These photocatalysts, called nanostructured homojunction Bi2MoO6@Bi2MoO6−x, were able to effectively degrade and mineralize solutions containing various antibiotics (such as tetracycline, ciprofloxacin, and levofloxacin). After 180 minutes of radiation exposure, the photocatalysts achieved exceptionally high mineralization values (>95%) and near-complete degradation.145 P. Gholami et al. examined the photocatalytic efficacy of Zn–Co-layered double hydroxide (LDH) nanostructures containing charcoal (BC) in the breakdown of gemifloxacin (GMF), a representative pharmaceutical contaminant. The results indicate that 92.7% of GMF underwent degradation through photocatalysis in the presence of the Zn–Co-LDH catalyst. The effectiveness of BC-incorporated Zn–Co-LDH as a photocatalyst was greatly influenced by the concentration of the solute and the amount of photocatalyst used.146 Elegant Z-scheme composite hollow microspheres (CHMs) were made by sequentially controlling in situ hydrolysis and polymerization of WO3/g-C3N4. WO3/g-C3N4 CHMs are the most effective for photocatalytic degradation of CFS, with an 82% degradation efficiency after 2 hours of visible-light irradiation.147 Y. Sneha et al. conducted research on the properties of photocatalyst magnesium titanate (MgTiO3) in the presence of visible light, specifically focusing on its interaction with lomefloxacin. The study found that a concentration of 30 mg L−1 of catalyst was the most effective in breaking down 10 mg L−1 of lomefloxacin using 30 W LED irradiation for a duration of 150 minutes.148 The interaction between various surface facets of a semiconductor with suitable ratios can lead to improved performance in the degradation of photocatalytic processes. J. Wang et al. studied a material composed of bismuth called Bi4Ti3O12 and found that it showed improved degradation activity for tetracycline hydrochloride (TC-HCl) when exposed to irradiation.149 M. Shokri et al. investigated the degradation of cefazolin through exposure to immobilized and suspended TiO2 on a glass plate. A table has been added showing the photocatalytic degradation of antibiotics Table 2 and Fig. 2 shows the process. The findings indicate that the breakdown percentage of TiO2 suspension at favorable pH conditions (pH 5) is 96.47% after 60 minutes of irradiation.150
Table 2 Data for the photocatalytic degradation of antibiotics using various catalysts
Antibioticsa |
Antibiotics conc. (mg L−1) |
Catalysts |
Catalyst conc. (mg L−1) |
Operational conditions |
Lamp, power (W) |
Degradation percentage (%), time (min) |
Ref. |
CIP = ciprofloxacin, AMX = amoxicillin, TC = tetracycline, APAP = acetaminophen, CFX = cephalexin, SMZ = sulfamethoxazole, CFT = cefoxitin sodium, OFL = ofloxacin, NOR = norfloxacin, CTC = chlorotetracycline, OTC = oxytetracycline, DXC = doxycycline, MTZ = metronidazole, PG = penicillin G, CEF = cefixime, GMF = gemifloxacin, CFS = ceftazidime, SMX = sulfamethoxazole, OA = oxolinic acid.
|
CIP |
10 |
g-C3N4/TiO2 |
375 |
Visible light |
Xe, 300 |
88, 180 |
127
|
AMX |
30 |
TiO2 |
450 |
UV light, pH 7 |
672 |
80, 270 |
128
|
TC |
50 |
3D-PDI |
25 |
Visible light, pH 5 |
— |
80, 150 |
129
|
APAP |
0.7 |
BiTNMs |
1000 |
Visible light, pH 7 |
500 |
88, 180 |
130
|
CFX |
50 |
NiS-PPY-Fe3O4 |
4000 |
UV light, pH 5.5 |
Hg, 75 |
80, 30 |
131
|
SMZ |
30 |
Cu–TiO2@functionalized SWCNT |
900 |
UV-vis light, pH 7 |
— |
100, 300 |
132
|
CFT |
15 |
BN/CdAl2O4 |
330 |
UV light, pH 7 |
108 |
100, 240 |
133
|
OFL |
5 |
PVP capped BiOBr |
10 |
Visible light |
15 |
94, 240 |
134
|
NOR |
5 |
PVP capped BiOBr |
10 |
Visible light, pH 7.54 |
15 |
99.8, 240 |
134
|
TC-H |
20 |
CdTe/TiO2 |
600 |
Visible light |
300 |
78, 30 |
135
|
TC |
0.01 |
BiVO4/TiO2/RGO |
— |
Visible light, pH 3 |
Xe, 1000 |
96.2, 120 |
136
|
CTC |
0.01 |
BiVO4/TiO2/RGO |
— |
Visible light, pH 3 |
Xe, 1000 |
97.5, 120 |
136
|
OTC |
0.01 |
BiVO4/TiO2/RGO |
— |
Visible light, pH 3 |
Xe, 1000 |
98.7, 120 |
136
|
DXC |
0.01 |
BiVO4/TiO2/RGO |
— |
Visible light, pH 3 |
Xe, 1000 |
99.6, 120 |
136
|
CFX |
20 |
MnWO4/Bi2S3 |
1200 |
Visible light |
Xe, 1000 |
78.8, 180 |
137
|
MTZ |
20 |
MnWO4/Bi2S3 |
1200 |
Visible light |
Xe, 150 |
83.3, 180 |
137
|
TC |
10 |
SnO2/CeO2 |
200 |
Visible light, pH 9–10 |
500 |
97, 120 |
138
|
PG |
5 |
ZnO |
800 |
UV light, pH 6.8 |
24 |
72.72, 150 |
139
|
CIP |
20 |
40TiHAp |
2000 |
UV light, pH 6.1 |
125 |
100, 15 |
140
|
OFL |
20 |
40TiHAp |
2000 |
UV light, pH 6.1 |
125 |
100, 120 |
140
|
TC |
10 |
Cu3P/ZnSnO3/g-C3N4 |
500 |
Visible light |
Xe, 500 |
98.45, 60 |
141
|
CEF |
100 |
ACT-4 |
844 |
Visible light |
LED bulb, 50 |
99.6, 260 |
142
|
OFL |
10 |
ZnO/Bi2MoO6 |
250 |
Visible light, pH 7.54 |
Daylight lamp, 15 |
100, 240 |
143
|
TC |
10 |
MoO3/g-C3N4 |
500 |
Visible light |
— |
85, 9100 |
144
|
TC, CPX, and/or LFC solution |
60 |
Bi2MoO6@Bi2MoO6−x |
300 |
Visible light, pH 7 |
LEDs, 6.2 |
>95, 180 |
145
|
GMF |
15–35 |
Zn–Co-LDH@BC |
750 |
UV light, pH 5.5 |
10 |
92.7, 130 |
146
|
CFS |
500 |
WO3/g-C3N4 |
25 |
UV light |
Xe, 300 |
82, 120 |
147
|
Lomefloxacin |
10 |
MgTiO3 |
30 |
UV light, pH 7 |
LED light, 30 |
83, 150 |
148
|
TC–HCl |
20 |
Bi4Ti3O12 |
10 |
UV light |
Xe, 300 |
75.5, 150 |
149
|
Cefazolin |
20 |
TiO2 |
400 |
UV light, pH 5 |
15 |
96.47, 60 |
150
|
SMX |
— |
TiO2 |
0.002 |
UV light |
Xenon, 1500 |
88, 360 |
151
|
SMX |
10 |
TiO2 |
250 |
UV light, pH 4.1–5.4 |
UV, 9 |
Close to 100, 120 |
152
|
OA |
20 |
Titanium Degussa P-25 |
0.001 |
pH 7.5 |
Black light lamp |
90, 30 |
153
|
Norfloxacin |
— |
C–TiO2 |
0.0002 |
Visible light |
— |
78, 70 |
154
|
TC |
40 |
Metal ion@TiO2/HNTs |
|
Visible light |
Xenon, 500 |
76.54, — |
155
|
Chloramphenicol |
50 |
TiO2 |
0.001 |
UV light |
Osram Dulux, 9 |
90, 90 |
156
|
SMX |
100 |
TiO2 |
0.0005 |
UV light |
Xenon lamp |
80, 360 |
157
|
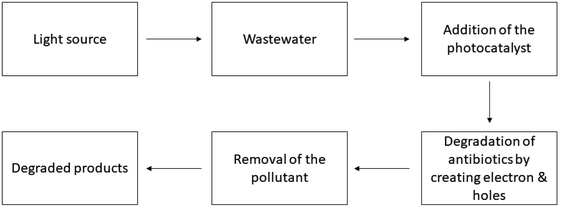 |
| Fig. 2 Working procedure of the photocatalysts for antibiotic degradation. | |
Other industrial pollutants (toluene, nitrobenzene, cyclohexane, and refinery oil)
Industrial chemical pollutants are a subgroup of chemical pollutants specifically connected with industrial operations.158 They encompass a wide spectrum of chemicals used or produced in manufacturing, refining, and other industrial processes.159 Industrial chemical pollutants, including toluene, cyclohexane, nitrobenzene, and refinery oil, pose significant environmental threats due to their widespread use and high toxicity.160,161 Toluene, an industrial solvent, pollutes air, water, and soil, causing harm to aquatic organisms and long-term environmental damage.162 Cyclohexane, used in chemical production, contributes to air and water pollution, affecting aquatic life.163 Nitrobenzene, a dye and pharmaceutical precursor, contaminates soil and water, posing toxic and carcinogenic risks.164 Refinery oil, a byproduct of petroleum refining, causes extensive damage through spills and leaks, affecting marine and terrestrial ecosystems.165 Photocatalytic degradation is crucial for mitigating these pollutants, as it offers an efficient, eco-friendly method to break down these toxic substances, preventing their persistence in the environment and safeguarding both ecosystems and human health.166
Toluene
As one of the pollutants that pose a risk to human health and the ecosystem, toluene has been classified as a priority pollutant; for this reason, emission management is required.167,168 Owing to the serious issues that toluene causes, various methods for toluene abatement have been developed.169 The rapid growth in industrialization and urbanization has played a notable role in the emergence of severe environmental issues.170,171 Toluene, a volatile organic molecule, can induce skin inflammation, respiratory ailments, chronic and acute intoxication, neurotoxicity, and reproductive toxicity.172–176 Therefore, it is necessary to enhance the efficacy of eliminating indoor toluene vapors. Methods to counteract atmospheric pollution can be classified as either chemical or physical approaches.177,178 Physical approaches include adsorption, the process of condensation, and separating membranes. Chemical approaches encompass combustion, low-temperature plasma, biological, and photocatalytic treatments.179,180 Photocatalysis is regarded as a very promising option for environmental cleaning among these techniques. Photocatalytic technologies provide the benefits of being non-toxic and cost-effective, requiring gentle reaction conditions, and producing no secondary pollutants.136,181 Almost all the hydrocarbon degrades via the following mechanism.182,183 | Photocatalyst + hν (photon) → Photocatalyst (ecb− + hvb+) | (15) |
| hvb+ + H2O → ˙OH + H+ | (17) |
| Toluene + ˙OH → Hydroxylated intermediates | (19) |
| Hydroxylated intermediates + ˙OH → Degradation products | (20) |
| Degradation products + ˙OH/O2 → CO2 + H2O + Inorganic ions | (21) |
M. Zhang et al. utilized a hydrothermal technique to synthesize In2S3 in a nanoscale form. This nanomaterial was then employed to fabricate a composite photocatalyst consisting of In2S3 and g-C3N4. The process of toluene photocatalytic decomposition was investigated, and a feasible mechanism was proposed. The In2S3/g-C3N4 heterojunctions exhibited the highest photocatalytic degradation when a 40% loading of In2S3 was used.184 B. N. R. Winayu et al. enhanced the TiO2 catalyst by introducing sulfur and nitrogen (S, N) components and reduced graphene oxide (rGO) through doping. The most efficient photocatalytic degradation of toluene was achieved using a combination of 1 wt% reduced graphene oxide (rGO) and 0.05 wt% nitrogen-doped titanium dioxide (N0.1TiO2).185 V. T. T. Ho et al. stated that the nanostructured Ir-doped TiO2 is a highly effective photocatalyst that produces a superb material for reducing the risk of gaseous toluene. The material had a large surface area and had a consistently spherical shape of 10–15 nm diameter.186 The composite of PIL (polyionic liquid)@TiO2 was formed using two different concentrations of polymerized ionic liquid (low and high). The composite was then assessed for its ability to degrade toluene. The findings indicated that the PIL(low)@TiO2 composite exhibited higher activity compared to the PIL(high)@TiO2 composites.187 Z. Sun et al. synthesized a novel hierarchical heterostructured photocatalyst consisting of TiO2/Bi/Bi2MoO6 using a solvothermal technique. On the outermost layer of flower-like Bi2MoO6 nanospheres, the TiO2 nanoparticles were evenly dispersed. The results suggest that the combination of TiO2 can greatly improve the effectiveness of the photocatalytic oxidation of toluene using the hierarchical heterostructure TiO2/Bi/Bi2MoO6.188 Y. Bi et al. used zinc chloride (ZnCl2), zinc nitrate (Zn(NO3)2), and zinc acetate (Zn(CH3COO)2) to modify activated carbon fibers (ACFs). Subsequently, titanium dioxide (TiO2) was loaded onto the modified ACFs. The study found that the photocatalytic performance and adsorption of TiO2/ACF-Ac modified by Zn(CH3COO)2 were highest for the removal of toluene.189 The presence of a three-dimensional (3D) and directed structure enables efficient absorption of photons and rapid diffusion of volatile organic compounds (VOCs), surpassing the capabilities of catalysts in powder form. The researchers successfully created uniform and free-standing nanowire (NW) arrays of p-type Cu2O by subjecting Cu(OH)2 NWs to heat treatment. The Cu2O NWs, as they are created, exhibit exceptional performance in degrading 30 ppm toluene, with a degradation rate of 99.9% achieved within 120 minutes.190 P. Mohammadi et al. used a hydrothermal technique to deposit synthesized SrTiO3 onto graphene oxide (GO). Photocatalysts that were artificially created were utilized for the process of breaking down gaseous toluene dynamically using photocatalysis while being exposed to UV radiation.191 Rostami synthesized a TiO2 and bentonite photocatalyst by a method called co-precipitation and evaluated its catalytic efficiency in degrading para-nitrotoluene (PNT).192 Oxygen vacancies (OVs) can regulate photocatalytic activity by altering their electrical and/or band structures. A wide bandgap p-block metal combination containing OVs, indium oxyhydroxide (InOOH), produced using a one-pot hydrothermal approach, was used to investigate the effect of OVs on photocatalytic decomposition and toluene ring breakage. Validated modified InOOH improves photocatalytic potency by decreasing the energy limitation of critical intermediates for reaction during toluene degradation.183 X. Zhao et al. enhanced the performance of the C–USTiO2 photocatalyst by applying it to carbon cloth and conducted a study on its ability to continuously degrade toluene under LED light exposure. The results demonstrated that the removal of the degraded toluene can exceed 80% when a large concentration of CO2 is produced, and it exhibits exceptional cycle stability lasting for over 180 minutes.193 M. Wu et al. researched the use of CeO2 nanorods for the degradation of toluene using vacuum ultraviolet (VUV) catalytic oxidation. CeO2 nanorods were utilized in a system that involved VUV-photolysis, UV-PCO, OZCO, and UVOZCO processes. Utilizing VUV light instead of ozone catalytic oxidation can significantly enhance the efficiencies, increasing them from 12.9% to 83.2% when combined with the suggested catalyst.194 An efficient electrochemical method consisting of two steps was devised to produce a nanotube array of atomically dispersed Au-loaded WO3/TiO2 for the oxidation of volatile organic compounds (VOCs). The presence of vacancies (OVs) on the surface of WO3 greatly improved the separation and movement of photogenerated carriers, as well as the adsorption of toluene. This resulted in an 85.5% mineralization and 95.4% degradation rate for the removal of toluene.195 J. Lyu et al. fabricated a hollow heterophase junction by applying a layer of amorphous TiO2 onto anatase TiO2 hollow spheres. The findings demonstrated that the application of the amorphous TiO2 coating resulted in an augmentation of fine pores and intermediate pores in the photocatalyst, leading to an improved capacity for toluene adsorption.196 By adding nanodiamonds to ZnO, the photocorrosion problem can be solved for photocatalytic degradation of gaseous toluene. A table has been added showing the photocatalytic degradation of toluene Table 3 and Fig. 3 shows the process. Nanodiamond decoration resulted in lowered photoluminescence intensity and electrochemical impedance, enhancing ZnO light absorption, charge transfer, and photocatalytic toluene oxidation efficiency.197
Table 3 Data for the photocatalytic degradation of toluene using various catalysts
Toluene conc. (ppm) |
Catalyst |
Catalyst conc. (mg L−1) |
Operational conditions |
Lamp, power (W) |
Degradation percentage (%), time (min) |
Ref. |
60 |
In2S3/g-C3N4 |
50 |
Visible light, RH 50–60% |
Xe |
89.7, 180 |
184
|
2 |
1 wt% rGO/S0.05N0.1TiO2 |
500 |
Visible light, RH 60% |
Fluorescent, 10 |
72, 480 |
185
|
1900 |
Ir doped–TiO2 |
100 |
UV light, RH 70% |
UV, 25 |
97, 8.5 |
186
|
50 |
PIL@TiO2/m-GO |
1000 |
UV, RH 40% |
UV, 8 |
97, 24 |
187
|
— |
TiO2/Bi/Bi2MoO6 |
2000 |
UV |
Xe, 320 |
26.08, 120 |
188
|
843 |
TiO2/ACF-Ac fabricated by Zn(CH3COO)2 |
151.2 |
UV, RH 40% |
Xe, 300 |
70, 2400 |
189
|
30 |
Cu2O NWs |
172.26 |
Visible, RH 74% |
Xe, 300 |
99.9, 120 |
190
|
60 |
SrTiO3/rGO |
400 |
UV light, RH 50% |
UV, 8 |
98.65 |
191
|
50 |
TiO2/Bentonite |
200 |
UV light |
UV lamp |
64, 120 |
192
|
50 |
InOOH |
400 |
UV light |
Xe, 300 |
75.8, 60 |
183
|
30 |
C–USTiO2 |
100 |
Visible light, RH 50% |
LED, 1 |
80, 180 |
193
|
30 |
CeO2 |
1000 |
VUV light, RH 50% |
VUV, 4 |
83.2, 144 |
194
|
300 |
WO3/TiO2 |
— |
LED light |
— |
95.4, 30 |
195
|
23.6 |
THS@amorphous-TiO2 |
10 |
UV light |
UV, 8 |
98.2, 240 |
196
|
50 |
TiO2/ND |
100 |
UV |
Xe, 50 |
100, 120 |
197
|
750 |
ZnAl2O4 |
— |
UV |
Black-light fluorescent lamp |
90.25, 300 |
198
|
— |
TiO2 |
— |
UV, RH 35% |
Germicidal lamp, 15 |
61.9, 180 |
199
|
160 |
TiO2 |
— |
UV, RH 25–50% |
Black lamp, 10 |
50–60, 5 |
200
|
400 |
TiO2 |
— |
UV |
Iron halogenide lamp, 500 |
52, 360 |
201
|
— |
TiO2 |
— |
UV |
Mercury lamp, 300 |
90, 120 |
202
|
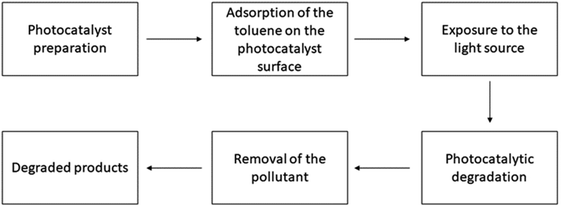 |
| Fig. 3 Working procedure of the photocatalysts for toluene degradation. | |
Nitrobenzene
Since aromatic nitro compounds are frequently employed in industrial processes (such as the production of explosives, dyes and insecticides), they are present as contaminants in a variety of liquid sources, particularly surface water, and wastewater from industries.203 Since nitrobenzene (NB) is identified as a significant contaminant, it is selected as a model pollutant. It is an extremely hazardous material and the highest permitted level of NB is 1 mg L−1 in wastewater.204,205 Numerous factors, including the presence of anions, pH, light wavelength, and others, have an impact on nitrobenzene photocatalytic degradation utilizing UV radiation.206 The degradation working mechanism of nitrobenzene in the presence of several photocatalysts is described.207,208 | Photocatalyst + hν (photon) → Photocatalyst (ecb− + hvb+) | (22) |
| Nitrobenzene → Catalyst surface | (24) |
| Nitrobenzene + ˙OH → Activated nitrobenzene | (25) |
| Activated nitrobenzene + ˙OH → Nitrophenol + Intermediate products | (26) |
| Nitrophenol + ˙OH → Degradation products | (27) |
| Degradation products + ˙OH → CO2 + H2O + Inorganic ions | (28) |
The study of the impacts of several factors, such as pH, anions, starting concentration, etc., has been done because the rate of breakdown of nitrobenzene utilizing controlled UV radiation is quite significant when compared to that utilizing solar radiation, and a small amount of TiO2 (0.05%, w/v) was used.209,210 Degussa P-25 TiO2 was utilized as the photocatalyst in the majority of the nitrobenzene photocatalytic tests. Aldrich-TiO2 (pure anatase with a BET surface area of roughly 250 m2 g−1) was used in a few tests.206 Matthews et al. used immobilized TiO2 in a spiral-shaped reactor for the photocatalytic degradation of NB and other chemicals and accomplished around 95–100% degradation at the initial concentration between 1.75 and 4.25 mg L−1.211 Degussa P-25 was applied as the catalyst in photocatalytic degradation tests, and UV lamps with lights radiating at λmax of 253 and 365 nm, respectively, were used. The two bulbs produced nearly identical deterioration.212 When it comes to 4-chlorophenol degradation, it has been discovered that utilizing pulsed photocatalysis makes little distinction in terms of TOC elimination at shorter and longer wavelengths. It should be mentioned that 387 nm is the λmin for anatase TiO2.213 The pH has an impact on the ionizable organic molecules' photocatalytic breakdown. The significance of pH on the photocatalytic destruction of NB was assessed within a pH value range of 4–10, in a solution containing 2.52 × 10−4 M of pollutants. The ideal photocatalyst concentration was determined to be 0.5 wt% Fe–TiO2 = 250 mg L−1, with an irradiation period of 60–240 minutes.214 A table has been added showing the photocatalytic degradation of nitrobenzene Table 4 and Fig. 4 shows the process. It has been discovered that, given the specified conditions, pH 7 is ideal for NB photocatalytic breakdown.205
Table 4 Data for the catalytic degradation of nitrobenzene using various catalysts
Nitrobenzene conc. (mg L−1) |
Catalyst |
Catalyst conc. (mg L−1) |
Operational conditions |
Lamp, power (W) |
Degradation percentage (%), time (min) |
Ref. |
50 |
SrFeO3−δ |
0.001 |
UV |
Mercury vapour, 125 |
99%, 360 |
215
|
50 |
P-25 |
— |
UV |
125 |
95%, 480 |
216
|
40 |
AuNPs/HPW/TiO2-NTs |
— |
Visible light |
Low-pressure mercury vapor lamp, 15 |
90%, 30 |
217
|
— |
Ag/ZnO nanoflowers |
— |
UV |
Tungsten lamp, 60 |
98%, 100 |
218
|
61.5 |
TiO2 |
— |
Visible light |
125 |
58.46%, 210 |
219
|
— |
TiO2/g-C3N4/G |
7.5 |
UV |
Xenon lamp, 300 |
97%, 240 |
220
|
25 |
H3PW12O40 supported on TiO2 |
10 |
Visible light |
Tungsten light, 500 |
88%, 390 |
221
|
50 |
|
— |
UV |
Mercury vapor lamp, 200 |
96%, 240 |
222
|
50 |
TiO2-POMs |
— |
UV |
— |
86.4%, 180 |
223
|
1900 |
TiO2-SA-Arg particles |
— |
UV |
UV lamp |
93.7%, 120 |
224
|
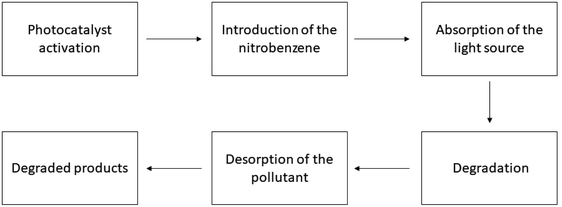 |
| Fig. 4 Working procedure of the photocatalysts for nitrobenzene degradation. | |
Cyclohexane
A common volatile organic compound (VOC) that presents significant dangers to both humans and the environment is cyclohexane.225 An extremely significant industrial procedure is the breakdown of cyclohexane to produce cyclohexanol and cyclohexanone which are utilized globally as chemical precursors for the synthesis of caprolactam and adipic acid.226,227 Photocatalytic techniques for the degradation of cyclohexane in both solid heterogeneous and homogeneous stages have received a lot of research attention in recent years.228 In heterogeneous environments, semiconductors along with oxides are being used as photocatalysts to oxidize cyclohexane. A number of semiconductors have been used, including CeO2, WO3, Sn/Sb, ZrO2, ZnO, V2O5, SnO2, Sb2O4 and mixed oxides.229 In the presence of various types of photocatalysts, cyclohexane degrades via the following mechanism.230,231 | Photocatalyst + hν (photon) → Photocatalyst (ecb− + hvb+) | (29) |
| hvb+ + H2O → ˙OH + H+ | (30) |
| Cyclohexane + ˙OH → Intermediate products | (32) |
| Intermediate products + ˙OH → Further degraded products | (33) |
| Intermediate products + ˙OH/O2 → CO2 + H2O + Inorganic ions | (34) |
Xiao et al. discussed the photocatalytic characteristics of silver nanoparticles loaded on the nanocrystals of tungsten oxide when cyclohexane was being photo-catalytically degraded.232 In standard manufacturing processes, cyclohexane is degraded at 150 °C using a homogeneous cobalt-based catalyst.228 Variations in the emitted photon flux and the irradiation wavelength during continuous irradiation result in notable variations in substance outputs and selectivity values during the photocatalytic degradation of cyclohexane by the help of TiO2 in a pure liquid organic phase.233 The photodegradation of cyclohexane proceeded with hydrogen peroxide at ambient temperature, assisted by a copper(II)-exchanged Y zeolite (CuY). A table has been added showing the photocatalytic degradation of cyclohexane Table 5 and Fig. 5 shows the process. Following 6 hours of processing, cyclohexanol and cyclohexyl hydroperoxide with 37% and 54% selectivities, respectively, were obtained as the major products.247
Table 5 Data for the catalytic degradation of cyclohexane using various catalysts
Cyclohexane conc. (mg L−1) |
Catalyst |
Catalyst conc. (mg L−1) |
Operational conditions |
Lamp, power (W) |
Degradation percentage (%), time (min) |
Ref. |
200 |
Pt/TiO2 |
— |
UV, temp: 100 °C with 0.5% Pt loading |
Osram Ultra-Vitalux lamp, 300 |
Close to 100%, — |
234
|
— |
Ti3+ self-doped TiO2 |
— |
Visible light, temp: 40 °C |
Xenon lamp |
95%, 420 |
235
|
— |
WO3/Co–Pt |
100 |
UV |
— |
93%, 720 |
236
|
— |
Degussa P-25 |
0.001 |
Visible light |
Metal halide lamp |
Around 40%, 180 |
237
|
— |
WO3–TiO2 mixed catalysts |
50 |
Visible light |
Xenon lamp, 500 |
97%, 60 |
238
|
— |
Au/TiO2 |
0.001 |
Visible light, temp: 25 °C |
Mercury lamp, 50 |
50%, — |
239
|
— |
Degussa P25 |
0.001 |
UV, temp: 650 °C |
Xenon lamp, 450 |
—, 60 |
240
|
523 |
TiO2 |
— |
UV, temp: 30 °C |
Black light lamp, 20 |
63%, 5 |
241
|
— |
TiO2 |
0.001 |
UV, — |
Mercury lamp, 50 |
—, 10 |
239
|
— |
Ag-substituted and impregnated nano-TiO2 |
0.001 |
UV, temp: below 35 °C |
A high-pressure mercury vapor lamp, 80 |
Around 10%, 6 |
242
|
— |
TiO2 |
— |
UV, temp: 140–180 °C |
A high-pressure mercury lamp, 100 |
Over 90%, — |
243
|
— |
TiO2 |
0.001 |
UV, temp: 60 °C |
Medium pressure mercury-vapor lamp, 450 |
Over 95%, — |
244
|
— |
Na4W10O32 |
0.05 |
UV, — |
Medium pressure mercury-arc lamp, 125 |
—, 3 |
245
|
— |
Fe-modified C-doped Cr2O3 |
— |
Visible light, temp: 25 °C |
Xenon lamp, 300 |
—, 5 |
246
|
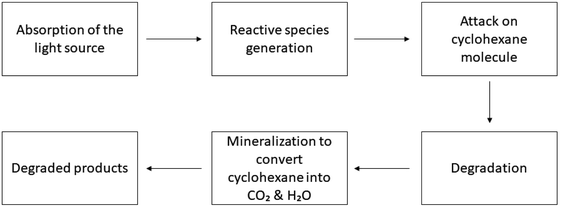 |
| Fig. 5 Working procedure of the photocatalysts for cyclohexane degradation. | |
Refinery oil
Several methods may be used for the treatment of oil refinery effluents which include adsorption, Fenton oxidation, electro-floatation–coagulation, photocatalytic degradation/oxidation, chemical flocculation–coagulation, and membrane filtration.248–253 These procedures either produce insignificant impurities or need prolonged durations to eradicate the impurities.254–256 Conventional methods like adsorption or membrane separation produce an inferior contaminant by moving the contamination from one phase to another, and the reusability of adsorbents is uncertain.257,258 Bacterial degradation requires a significant amount of time to break down pollutants and is not suitable for the majority of organic compounds found in oil refinery wastewater.259–261 Photocatalytic degradation techniques have attracted significant attention due to their ability to break down a wide range of organic compounds utilizing suitable photocatalysts.52,262,263 The degradation of pollutant chemicals is caused by the hydroxyl radical (OH), which can react with organic compounds and break them down and degrade them.264,265 The mechanism for refinery oil degradation in the presence of various photocatalysts is given.266,267 | Photocatalyst + hν (photon) → Photocatalyst (ecb− + hvb+) | (35) |
| hvb+ + H2O → ˙OH + H+ | (37) |
| Oil → Catalyst surface | (39) |
| Oil + ˙OH → Degradation products | (40) |
| Oil + ˙O2− → Degradation products | (41) |
| Degradation products + ˙OH → CO2 + H2O + Inorganic ions | (42) |
B. Ogoh-Orch et al. studied BiOI-sensitized TiO2 (BiOI/TiO2) nanocomposites with varying amounts of BiOI deposited via sequential ionic layer adsorption and reaction (SILAR) and found that they perform well in water under visible (>400 nm) irradiation for crude oil degradation. The BiOI/TiO2 heterojunction separates photogenerated charges, improving degradation efficiency.268 Actual wastewater from a refinery, containing a variety of aromatic and aliphatic organic compounds, was treated using nanoparticles (specifically TiO2 and ZnO). The degradation ability of the organic contaminants was reduced from 98.57% to 89.482% when the photocatalysts changed from TiO2 to ZnO.267 D. A. Aljuboury et al. investigated the application of ZnO/TiO2/H2O2 using visible light (1000 W m−2), to decrease the total organic carbon (TOC) content in the actual petroleum wastewater obtained from Sohar Refinery Company (SRC). The treatment efficiency for total organic carbon (TOC) at pH 5.5 increased significantly compared to that of the TiO2 procedure.269 Z. Ghasemi et al. examined the photocatalytic oxidation of organic contaminants in petroleum refinery wastewater (PRWW) utilizing synthesized nano-TiO2 incorporated into Fe-ZSM-5 zeolite and UV light. Results indicate optimal photodegradation efficiency at 3 g L−1 photocatalyst concentration, pH 4, 45 °C temperature, and 120 min UV irradiation.270 Shahrezaei investigated TiO2 photocatalysis for the primary degradation of phenol and phenolic compounds in refinery wastewater. Under optimal conditions, 90% phenol removal was achieved in 2 hours.271 The user created a composite membrane by combining polyvinylidene and titanium dioxide (PVDF/TiO2) and then treated it using the hot-pressing method. A table has been added showing the photocatalytic degradation of cyclohexane Table 6 and Fig. 6 shows the process. This treatment was done to increase the bonding between the TiO2 and the membrane surfaces, to employ the membrane to degrade oil in wastewater.
Table 6 Data for the photocatalytic degradation of refinery oil using various catalysts
Target compound |
Compound conc. (ppm) |
Photocatalyst |
Catalyst conc. (mg L−1) |
Operation conditions |
Lamp, power (W) |
Degradation percentage (%), time (min) |
Ref. |
Crude oil |
200 |
BiOI/TiO2 |
— |
Visible light |
LED, 13 |
85.62, 180 |
268
|
Refinery oil |
99.64 |
TiO2 |
100 |
UV light, pH 6 |
UV, 11 |
98.57, 120 |
267
|
Refinery oil |
99.64 |
ZnO |
100 |
UV light, pH 3 |
UV, 11 |
89.48, 120 |
267
|
Oil in petroleum wastewater |
15–22 |
TiO2/ZnO/H2O2 |
H2O2 = 850 |
Visible light, pH 5.5 |
LED, 1000 |
37, — |
269
|
ZnO = 590 |
TiO2 = 700 |
Petroleum refinery wastewater |
500 |
TiO2/Fe-ZSM-5 |
3000 |
UV light, pH 4 |
UV, 8 |
66%, 120 |
270
|
Phenol |
220 |
TiO2 |
100 |
UV light, pH 4 |
UV, 400 |
90%, 120 |
271
|
Phenol |
70 |
Degussa P25 |
0.002–0.008 |
UV light, pH 5.5 |
Fluorescent T8 backlight blue bulb, 18 |
76%, 90 |
272
|
Soap oil & grease |
480 |
Degussa P25 |
0.002–0.008 |
UV light, pH 5.5 |
Fluorescent T8 backlight blue bulb, 18 |
88%, 90 |
272
|
Refinery oil |
— |
TiO2 |
100 |
UV light, pH 3 |
UV, 400 |
93.92%, 60 |
273
|
Refinery oil |
— |
TiO2 |
0.0012 |
UV light, pH 4 |
UV, 11 |
40.68%, 120 |
274
|
Petroleum refinery wastewater |
— |
TiO2 |
100 |
UV light, pH 10 |
Mercury vapor, 6 |
TOC = 32% & TN = 67%, 90 |
275
|
Petroleum refinery wastewater |
— |
TiO2/ZnO/Degussa P25 |
0.0005–0.005 |
UV light, pH 3.5–9 |
Mercury vapor, 250 |
Phenols = 93% |
276
|
Dissolved organic carbon (DOC) = 63% |
Oil and grease (OG) = over 50%, 60 |
Petroleum refinery wastewater |
400–600 |
TiO2 |
100 |
UV light, pH 3, temp: 45 °C |
Mercury, 400 |
90%, 4 |
277
|
Petroleum refinery wastewater |
Phenol = 0.002 |
TiO2 |
0.001 |
O3/UV, pH 7.16 |
Mercury, 100 |
Phenol = 99.9% |
278
|
COD = 1954 |
COD = 31.6% |
Oil & grease = 298.8 |
Oil & grease = 5.2% |
Sulfide = 13.3 |
Sulfide = 53%, 5 |
Phenol |
10 |
TiO2 |
|
UV, pH = 5 |
|
—, 6 |
279
|
Refinery oil |
— |
TiO2 |
— |
UV light, pH 7–9 |
UV, 60 |
83%, — |
280
|
Petroleum refinery wastewater |
200–220 |
TiO2 |
100 |
UV light, pH 3, temp: 45 °C |
Mercury, 400 |
78%, 120 |
281
|
Crude oil |
0.005 |
TiO2 in zeolite |
— |
UV light, temp: 400 °C |
Mercury, 150 |
Linear alkanes = 98.66% |
282
|
Branched alkanes = 97.31% |
Cyclic alkanes = 96.04% |
Aromatic compounds = 99.54% |
Alkenes = 98.38%, 100 |
Oil emulsion in distilled/sea water |
25 |
Degussa P25 |
0.002 |
UV light, pH 4.5 |
Mercury, — |
In distilled water 92% & in artificial seawater 43%, 3 |
283
|
Petroleum refinery wastewater |
COD = 1326 |
Green nanocatalyst from the sepals of waste tomato |
0.00025 |
UV light, — |
UV, — |
99.9%, 90 |
284
|
A synthetic oil–water emulsion |
10 000 |
TiO2 |
0.002 |
UV light, — |
T8 black light blue bulb, 18 |
68%, 30 |
285
|
Refinery wastewater |
100 |
4-Chlorophenol |
178.5 |
UV light, pH 5 |
Mercury lamp, 100 |
—, 80 |
286
|
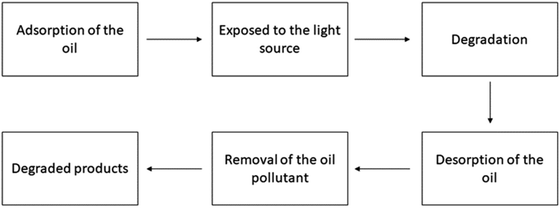 |
| Fig. 6 Working procedure of the photocatalysts for refinery oil degradation. | |
Effects of crystal size and surface area on photocatalytic degradation
Organic chemicals and the photocatalyst's surface coverage are directly correlated, and therefore surface morphology, such as crystal size and the surface area, must be taken into account during the photocatalytic degradation procedure.287,288 Since every chemical process occurs at the surface, the surface morphology of any photocatalyst is essential to its efficacy as a catalyst.289 The anatase phase with a range of 2.59 to 12.00 nm in TiO2 crystallite dimensions is visible in metal-doped TiO2 products. TiO2 has a specific surface area of between 100 and 500 m2 g−1.290,291 Sivalingam et al. used a solution combustion process where 8–10 nm pure anatase phase TiO2 with 156 m2 g−1 BET surface area was created. This TiO2 is commonly utilized for photocatalytic degradation of many dyes, including Orange G, Methylene Blue, Alizarin S, Methyl Red, and Congo Red. In this analysis, the crystal size of the photocatalyst was found to be 8 ± 2 nm.292 The photoactivity of the photocatalysts increased due to the higher surface area. It has been found that the photoactivity of the TiO2 while degrading the dye-like MB increased when the surface area of the catalyst increased from 63 m2 g−1 to 156 m2 g−1.293 For the maximum degradation of antibiotics like cefoxitin sodium, a novel BN/CdAl2O4 composite with a surface area of 14.34 m2 g−1 is used.133 Mushtaq et al. found a decrease in the degradation rate of the ofloxacin antibiotic due to the increase in the particle size and decrease in the surface area of the photocatalysts.294 The same scenario was also found during the advanced degradation of tetracycline antibiotics by graphene-ordered mesoporous silica.295 Zhou et al. used highly photoactive mesoporous anatase nanospheres that have a high specific surface area of 609 m2 g−1 for the degradation of toluene.296 The highest specific surface area (130.3 m2 g−1) of nano-sized TiO2 particles synthesized under ideal conditions is almost double that of Degussa P25 which is used for toluene degradation.297 R. J. Tayade et al. experimented with the degradation of nitrobenzene using nanocrystalline TiO2 of different surface areas, i.e. 259/199/166/124/91/2 m2 g−1.216 Photocatalytic oxidation of cyclohexane over TiO2 nanoparticles by molecular oxygen was carried out using different surface area photocatalysts ranging between 30 and 410 m2 g−1.298 TiO2 is made up of anatase and rutile with a mean particle size of 30 nm and a surface area of 50 m2 g−1 for the maximum degradation of refinery oil.285
Mechanism of photocatalytic degradation
Photocatalytic degradation is a process where light energy, typically from UV or visible light, activates a photocatalyst, such as titanium dioxide (TiO2). When the photocatalyst absorbs light, it generates electron–hole pairs. These electron–hole pairs can initiate redox reactions that produce reactive oxygen species (ROS) like hydroxyl radicals and superoxide anions. These ROS are highly reactive and can break down organic pollutants, converting them into less harmful substances like water, carbon dioxide, and inorganic ions. The overall mechanism involves light absorption, generation of electron–hole pairs, formation of ROS, and degradation of pollutants (Fig. 7).
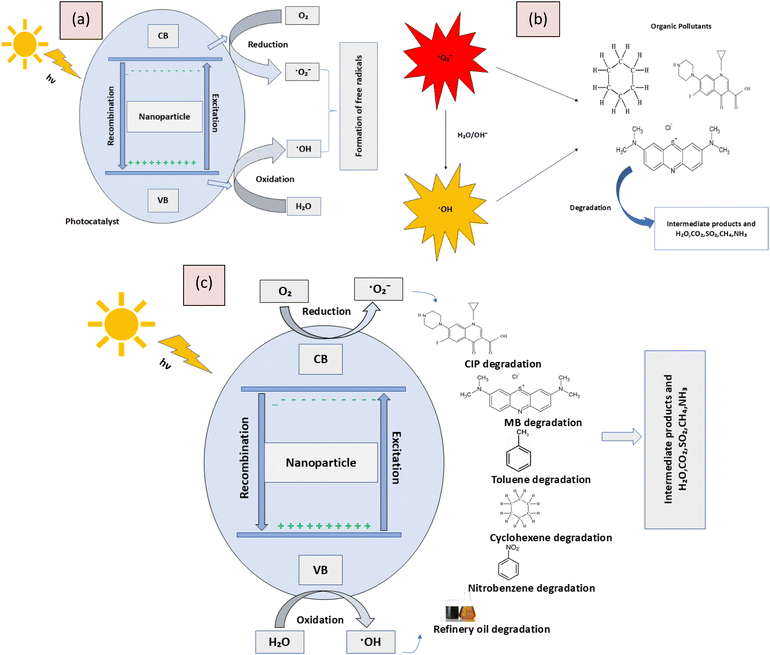 |
| Fig. 7 Illustration of (a) formation of free radicals, (b) degradation of the organic pollutants by radicals, and (c) overall photocatalytic degradation mechanism. | |
Conclusion
Various photocatalysts are used depending on the variation in organic pollutants. Titanium dioxide (TiO2) is the most broadly applied photocatalyst, known for its maximum ability, stability, and non-toxicity. It is primarily activated by UV light. Zinc oxide (ZnO) is another effective photocatalyst with properties similar to those of TiO2 but with some advantages under certain conditions. Recent research includes materials like cadmium sulfide (CdS), tungsten oxide (WO3), and various metal–organic frameworks (MOFs) as effective photocatalysts. Scientists are working on photocatalysts that are triggered by visible light in order to improve the process's applicability and reduce energy consumption in the real world. This review scrutinizes the variance in the degradation rate of organic pollutants under different conditions such as different pH levels, different concentration levels, various composites of the photocatalysts, different surface areas and sizes of the photocatalysts, and so on. This review will help to identify the optimum parameters for the maximum amount of organic pollutant degradation. The goal of this field's ongoing research and development is to broaden the use of catalytic technologies and overcome current obstacles to ensure cleaner soil and water thus leading to a more sustainable environment. Greater prospects for the use of photocatalysis in the destruction of dangerous organic pollutants may arise from a greater understanding of the process and its operating parameters.
Data availability
Data will be made available on request.
Author contributions
Abdullah Al Miad and Shassatha Paul Saikat collected the data and wrote the draft and original manuscript. Md. Sahadat Hossain conceived and designed the review, analyzed the data, and assisted in writing the manuscript. Md. Kawcher Alam assisted in collecting data. Newaz Mohammed Bahadur and Samina Ahmed supervised the findings of this work. Samina Ahmed supervised the overall work and managed the required facilities.
Conflicts of interest
There are no conflicts to declare.
Acknowledgements
The authors are grateful to the Bangladesh Council of Scientific and Industrial Research (BCSIR) authority for financial support through the R&D project (ref. no. 39.02.0000.011.14.134.2021/900; date: 30.12.2021). Abdullah Al Miad wishes to thank the Department of Applied Chemistry and Chemical Engineering, Noakhali Science and Technology University, Noakhali.
References
- J. Levec and A. Pintar, Catal. Today, 2007, 124, 172–184 CrossRef CAS.
- J. Umamaheswari and S. Shanthakumar, Rev. Environ. Sci. Biotechnol., 2016, 15, 265–284 CrossRef CAS.
- M. Molinos-Senante, R. Sala-Garrido and F. Hernández-Sancho, J. Cleaner Prod., 2016, 112, 3116–3123 CrossRef.
- B. S. Patel, B. R. Solanki and A. U. Mankad, World J. Adv. Res. Rev., 2021, 10, 323–333 CrossRef CAS.
- I. Angelidaki, A. S. Mogensen and B. K. Ahring, Biodegradation, 2000, 11, 377–383 CrossRef CAS PubMed.
- P. Kaszycki, M. Głodniok and P. Petryszak, New Biotechnol., 2021, 61, 80–89 CrossRef CAS PubMed.
- A. P. Bhat and P. R. Gogate, J. Hazard. Mater., 2021, 403, 123657 CrossRef CAS PubMed.
- B. S. Rathi, P. S. Kumar and D.-V. N. Vo, Sci. Total Environ., 2021, 797, 149134 CrossRef CAS PubMed.
- H. F. Stroo, J. Environ. Qual., 1992, 21, 167–175 CrossRef CAS.
- S. Krishnan, H. Rawindran, C. M. Sinnathambi and J. W. Lim, IOP Conf. Ser.: Mater. Sci. Eng., 2017, 206, 012089 Search PubMed.
- T. A. Kurniawan, G. Y. Chan, W.-H. Lo and S. Babel, Chem. Eng. J., 2006, 118, 83–98 CrossRef CAS.
- M. Ahmaruzzaman, Adv. Colloid Interface Sci., 2011, 166, 36–59 CrossRef CAS PubMed.
- I. Ali, M. Asim and T. A. Khan, J. Environ. Manage., 2012, 113, 170–183 CrossRef CAS PubMed.
- D. Chatterjee and S. Dasgupta, J. Photochem. Photobiol., C, 2005, 6, 186–205 CrossRef CAS.
- V. Vinayagam, K. N. Palani, S. Ganesh, S. Rajesh, V. V. Akula, R. Avoodaiappan, O. S. Kushwaha and A. Pugazhendhi, Environ. Res., 2023, 117500 Search PubMed.
-
M. M. Ali, D. Hossain, A. Al-Imran, M. S. Khan, M. Begum and M. H. Osman, Heavy Metals – Their Environmental Impacts and Mitigation, 2021, pp. 771–783 Search PubMed.
- T. Encarnação, A. A. Pais, M. G. Campos and H. D. Burrows, Sci. Prog., 2019, 102, 3–42 CrossRef PubMed.
- N. Gaur, K. Narasimhulu and Y. PydiSetty, J. Cleaner Prod., 2018, 198, 1602–1631 CrossRef CAS.
- L. Wang, D. Luo, O. Hamdaoui, Y. Vasseghian, M. Momotko, G. Boczkaj, G. Z. Kyzas and C. Wang, Sci. Total Environ., 2023, 876, 162551 CrossRef CAS PubMed.
- W. H. Glaze and J. Kang, J. AWWA, 1988, 80, 57–63 CrossRef CAS.
- W. H. Glaze, J.-W. Kang and D. H. Chapin, Ozone: Sci. Eng., 1987, 9, 335–352 CrossRef CAS.
- H. Liu, X. Li, X. Zhang, F. Coulon and C. Wang, Chemosphere, 2023, 139404 CrossRef CAS PubMed.
- A. Cesaro, V. Naddeo and V. Belgiorno, J. Biorem. Biodegrad., 2013, 4, 1–8 Search PubMed.
- K. Ayoub, E. D. Van Hullebusch, M. Cassir and A. Bermond, J. Hazard. Mater., 2010, 178, 10–28 CrossRef CAS PubMed.
- M. N. Chong, B. Jin, C. W. Chow and C. Saint, Water Res., 2010, 44, 2997–3027 CrossRef CAS PubMed.
- H. M. Coleman, C. P. Marquis, J. A. Scott, S.-S. Chin and R. Amal, Chem. Eng. J., 2005, 113, 55–63 CrossRef CAS.
- R. Comparelli, E. Fanizza, M. L. Curri, P. D. Cozzoli, G. Mascolo and A. Agostiano, Appl. Catal., B, 2005, 60, 1–11 CrossRef CAS.
- D. Zhu and Q. Zhou, Environ. Nanotechnol., Monit. Manage., 2019, 12, 100255 Search PubMed.
- K. M. Reza, A. Kurny and F. Gulshan, Appl. Water Sci., 2017, 7, 1569–1578 CrossRef CAS.
- K. Nakata and A. Fujishima, J. Photochem. Photobiol., C, 2012, 13, 169–189 CrossRef CAS.
- A. Y. Nosaka, E. Kojima, T. Fujiwara, H. Yagi, H. Akutsu and Y. Nosaka, J. Phys. Chem. B, 2003, 107, 12042–12044 CrossRef CAS.
- A. G. Agrios and P. Pichat, J. Appl. Electrochem., 2005, 35, 655–663 CrossRef CAS.
- Y. Wicaksana, S. Liu, J. Scott and R. Amal, Molecules, 2014, 19, 17747–17762 CrossRef PubMed.
- S. Ramanavičius, M. Petrulevičienė, J. Juodkazytė, A. Grigucevičienė and A. Ramanavičius, Materials, 2020, 13, 523 CrossRef PubMed.
- V. K. Vidhu and D. Philip, Micron, 2014, 56, 54–62 CrossRef CAS PubMed.
- F. Kiriakidou, D. I. Kondarides and X. E. Verykios, Catal. Today, 1999, 54, 119–130 CrossRef CAS.
- M. Umar and H. A. Aziz, Org. Pollut.: Monit., Risk Treat., 2013, 8, 196–197 Search PubMed.
- A. Bumajdad and M. Madkour, Phys. Chem. Chem. Phys., 2014, 16, 7146–7158 RSC.
- M. Sleiman, D. Vildozo, C. Ferronato and J.-M. Chovelon, Appl. Catal., B, 2007, 77, 1–11 CrossRef CAS.
- R. S. Thakur, R. Chaudhary and C. Singh, J. Renewable Sustainable Energy, 2010, 2, 42701 CrossRef.
- M. R. D. Khaki, M. S. Shafeeyan, A. A. A. Raman and W. M. A. W. Daud, J. Environ. Manage., 2017, 198, 78–94 CrossRef CAS PubMed.
- E. Rosales, M. Pazos, M. A. Longo and M. A. Sanromán, J. Environ. Sci. Health, Part A: Toxic/Hazard. Subst. Environ. Eng., 2009, 44, 1104–1110 CrossRef CAS PubMed.
- L. Corra, J. Health Pollut., 2018, 8, 180916 CrossRef PubMed.
- D. Montes-Grajales, M. Fennix-Agudelo and W. Miranda-Castro, Sci. Total Environ., 2017, 595, 601–614 CrossRef CAS PubMed.
-
K. Vassilev and V. Kambourova, in Chemicals as Intentional and Accidental Global Environmental Threats, ed. L. Simeonov and E. Chirila, Springer Netherlands, Dordrecht, 2006, pp. 173–191 Search PubMed.
- R. Naidu, B. Biswas, I. R. Willett, J. Cribb, B. K. Singh, C. P. Nathanail, F. Coulon, K. T. Semple, K. C. Jones and A. Barclay, Environ. Int., 2021, 156, 106616 CrossRef CAS PubMed.
- V. Vinayagam, K. N. Palani, S. Ganesh, S. Rajesh, V. V. Akula, R. Avoodaiappan, O. S. Kushwaha and A. Pugazhendhi, Environ. Res., 2023, 117500 Search PubMed.
- R. Gothwal and T. Shashidhar, Clean: Soil, Air, Water, 2015, 43, 479–489 CAS.
-
S. Benkhaya, S. M'rabet, H. Lgaz, A. El Bachiri and A. El Harfi, in Dye Biodegradation, Mechanisms and
Techniques, ed. S. S. Muthu and A. Khadir, Springer Singapore, Singapore, 2022, pp. 1–50 Search PubMed.
- A. Abatan, A. Obaigbena, E. D. Ugwuanyi, B. S. Jacks, U. J. Umoga, O. H. Daraojimba and O. A. Lottu, J. Eng. Sci. Technol., 2024, 5, 543–554 CrossRef.
- S. S. Shetty, S. Sonkusare, P. B. Naik and H. Madhyastha, Heliyon, 2023, 9, E19496 CrossRef CAS PubMed.
- D. Chen, Y. Cheng, N. Zhou, P. Chen, Y. Wang, K. Li, S. Huo, P. Cheng, P. Peng and R. Zhang, J. Cleaner Prod., 2020, 268, 121725 CrossRef CAS.
- A. Ucar, M. Findik, I. H. Gubbuk, N. Kocak and H. Bingol, Mater. Chem. Phys., 2017, 196, 21–28 CrossRef CAS.
- U. Kurtan, A. Baykal and H. Sözeri, J. Inorg. Organomet. Polym. Mater., 2015, 25, 921–929 CrossRef CAS.
- K. Yu, S. Yang, C. Liu, H. Chen, H. Li, C. Sun and S. A. Boyd, Environ. Sci. Technol., 2012, 46, 7318–7326 CrossRef CAS PubMed.
- M.-C. Roşu, C. Socaci, V. Floare-Avram, G. Borodi, F. Pogăcean, M. Coroş, L. Măgeruşan and S. Pruneanu, Mater. Chem. Phys., 2016, 179, 232–241 CrossRef.
- H. Kumari, S. Sonia, R. Ranga, S. Chahal, S. Devi, S. Sharma, S. Kumar, P. Kumar, S. Kumar, A. Kumar and R. Parmar, Water, Air, Soil Pollut., 2023, 234, 349 CrossRef CAS PubMed.
- J. H. B. Pinton, A. F. Oliveira, D. R. Huanca and N. D. Mohallem, Mater. Chem. Phys., 2024, 129213 CrossRef CAS.
- M. F. Lanjwani, M. Tuzen, M. Y. Khuhawar and T. A. Saleh, Inorg. Chem. Commun., 2024, 159, 111613 CrossRef CAS.
- S. Xia, L. Zhang, G. Pan, P. Qian and Z. Ni, Phys. Chem. Chem. Phys., 2015, 17, 5345–5351 RSC.
- M. K. Alam, M. S. Hossain, S. Tabassum, N. M. Bahadur and S. Ahmed, Open Ceram., 2024, 19, 100625 CrossRef CAS.
- C. Hu, C. Y. Jimmy, Z. Hao and P. K. Wong, Appl. Catal., B, 2003, 46, 35–47 CrossRef CAS.
-
J. Zhang, B. Tian, L. Wang, M. Xing and J. Lei, Photocatalysis: Fundamentals, Materials and Applications, Springer Singapore, Singapore, 2018, vol. 100, pp. 1–49 Search PubMed.
- R. Velmurugan and M. Swaminathan, Sol. Energy Mater. Sol. Cells, 2011, 95, 942–950 CrossRef CAS.
- M. H. Elsayed, T. M. Elmorsi, A. M. Abuelela, A. E. Hassan, A. Z. Alhakemy, M. F. Bakr and H.-H. Chou, J. Taiwan Inst. Chem. Eng., 2020, 115, 187–197 CrossRef CAS.
- L.-Y. Yang, S.-Y. Dong, J.-H. Sun, J.-L. Feng, Q.-H. Wu and S.-P. Sun, J. Hazard. Mater., 2010, 179, 438–443 CrossRef CAS PubMed.
- N. Sobana and M. Swaminathan, Sol. Energy Mater. Sol. Cells, 2007, 91, 727–734 CrossRef CAS.
- C. M. So, M. Y. Cheng, J. C. Yu and P. K. Wong, Chemosphere, 2002, 46, 905–912 CrossRef CAS PubMed.
- S. K. Kansal, N. Kaur and S. Singh, Nanoscale Res. Lett., 2009, 4, 709 CrossRef CAS PubMed.
- H. Liang, X. Li, Y. Yang and K. Sze, Chemosphere, 2008, 73, 805–812 CrossRef CAS PubMed.
- R. Singh and S. Dutta, Nano-Struct. Nano-Objects, 2019, 18, 100250 CrossRef CAS.
- T. Torimoto, S. Ito, S. Kuwabata and H. Yoneyama, Environ. Sci. Technol., 1996, 30, 1275–1281 CrossRef CAS.
- N. Takeda, T. Torimoto, S. Sampath, S. Kuwabata and H. Yoneyama, J. Phys. Chem., 1995, 99, 9986–9991 CrossRef CAS.
- I. Poulios, A. Avranas, E. Rekliti and A. Zouboulis, J. Chem. Technol. Biotechnol., 2000, 75, 205–212 CrossRef CAS.
- W.-Y. Wang and Y. Ku, Colloids Surf., A, 2007, 302, 261–268 CrossRef CAS.
- K. Bubacz, J. Choina, D. Dolat and A. W. Morawski, Pol. J. Environ. Stud., 2010, 19, 685–691 CAS.
- B. Neppolian, H. C. Choi, S. Sakthivel, B. Arabindoo and V. Murugesan, Chemosphere, 2002, 46, 1173–1181 CrossRef CAS PubMed.
- K. Tanaka, K. Padermpole and T. Hisanaga, Water Res., 2000, 34, 327–333 CrossRef CAS.
- N. Daneshvar, D. Salari and A. R. Khataee, J. Photochem. Photobiol., A, 2003, 157, 111–116 CrossRef CAS.
- V. Augugliaro, C. Baiocchi, A. B. Prevot, E. García-López, V. Loddo, S. Malato, G. Marcí, L. Palmisano, M. Pazzi and E. Pramauro, Chemosphere, 2002, 49, 1223–1230 CrossRef CAS PubMed.
- M. Saquib and M. Muneer, Dyes Pigm., 2003, 56, 37–49 CrossRef CAS.
- I. K. Konstantinou and T. A. Albanis, Appl. Catal., B, 2004, 49, 1–14 CrossRef CAS.
- V.-H. Nguyen, S. D. Lin, J. C.-S. Wu and H. Bai, Beilstein J. Nanotechnol., 2014, 5, 566–576 CrossRef PubMed.
- D. F. Ollis, E. Pelizzetti and N. Serpone, Environ. Sci. Technol., 1991, 25, 1522–1529 CrossRef CAS.
- C.-H. Hung and C. Yuan, J. Chin. Inst. Environ. Eng., 2000, 10, 209–216 CAS.
- K. V. S. Rao, M. Subrahmanyam and P. Boule, Appl. Catal., B, 2004, 49, 239–249 CrossRef CAS.
- E. T. Soares, M. A. Lansarin and C. C. Moro, Braz. J. Chem. Eng., 2007, 24, 29–36 CrossRef CAS.
- R. Ullah and J. Dutta, J. Hazard. Mater., 2008, 156, 194–200 CrossRef CAS PubMed.
- A. Salama, A. Mohamed, N. M. Aboamera, T. A. Osman and A. Khattab, Appl. Nanosci., 2018, 8, 155–161 CrossRef CAS.
- H. A. Kiwaan, T. M. Atwee, E. A. Azab and A. A. El-Bindary, J. Mol. Struct., 2020, 1200, 127115 CrossRef CAS.
- G. Annadurai, T. Sivakumar and S. Rajesh Babu, Bioprocess Eng., 2000, 23, 167–173 CrossRef CAS.
- S. Sriram, K. C. Lalithambika and A. Thayumanavan, Optik, 2017, 139, 299–308 CrossRef CAS.
- M. Zhou, X. Tian, H. Yu, Z. Wang, C. Ren, L. Zhou, Y.-W. Lin and L. Dou, ACS Omega, 2021, 6, 26439–26453 CrossRef CAS PubMed.
- I. N. Reddy, C. V. Reddy, J. Shim, B. Akkinepally, M. Cho, K. Yoo and D. Kim, Catal. Today, 2020, 340, 277–285 CrossRef CAS.
- R. Saravanan, H. Shankar, G. Rajasudha, A. Stephen and V. Narayanan, Int. J. Nanosci., 2011, 10, 253–257 CrossRef CAS.
- C. Xu, L. Cao, G. Su, W. Liu, H. Liu, Y. Yu and X. Qu, J. Hazard. Mater., 2010, 176, 807–813 CrossRef CAS PubMed.
- A. Mohammad, K. Kapoor and S. M. Mobin, ChemistrySelect, 2016, 1, 3483–3490 CrossRef CAS.
- F. Li, S. Sun, Y. Jiang, M. Xia, M. Sun and B. Xue, J. Hazard. Mater., 2008, 152, 1037–1044 CrossRef CAS PubMed.
- E. S. Al-Farraj, M. Khairy, F. A. Saad, R. K. Shah and E. A. Abdelrahman, Water Conserv. Sci. Eng., 2024, 9, 3 CrossRef.
- B. Haspulat Taymaz, M. Demir, H. Kamış, H. Orhan, Z. Aydoğan and A. Akıllı, Int. J. Phytorem., 2023, 25, 1306–1317 CrossRef CAS PubMed.
- N. Madima, K. K. Kefeni, S. B. Mishra and A. K. Mishra, Heliyon, 2022, 8, e10683 CrossRef CAS PubMed.
- J.-P. Dong, Z.-Z. Shi, B. Li and L.-Y. Wang, Dalton Trans., 2019, 48, 17626–17632 RSC.
- X. Xue, W. Zang, P. Deng, Q. Wang, L. Xing, Y. Zhang and Z. L. Wang, Nano Energy, 2015, 13, 414–422 CrossRef CAS.
- S. Thirumalairajan, K. Girija, V. R. Mastelaro and N. Ponpandian, New J. Chem., 2014, 38, 5480–5490 RSC.
- K. Byrappa, A. K. Subramani, S. Ananda, K. M. L. Rai, R. Dinesh and M. Yoshimura, Bull. Mater. Sci., 2006, 29, 433–438 CrossRef CAS.
- C.-Y. Chen, Water, Air, Soil Pollut., 2009, 202, 335–342 CrossRef CAS.
- Z. Shan, W. Wang, X. Lin, H. Ding and F. Huang, J. Solid State Chem., 2008, 181, 1361–1366 CrossRef CAS.
- S. Zhou and A. K. Ray, Ind. Eng. Chem. Res., 2003, 42, 6020–6033 CrossRef CAS.
- K. Mehrotra, G. S. Yablonsky and A. K. Ray, Chemosphere, 2005, 60, 1427–1436 CrossRef CAS PubMed.
- M. Sharma, D. Rajput, V. Kumar, I. Jatain, T. M. Aminabhavi, G. Mohanakrishna, R. Kumar and K. K. Dubey, Environ. Res., 2023, 231, 116132 CrossRef CAS PubMed.
- T. D. Nguyen, T. Lee, T. Van Tran, V. H. Nguyen, L. X. Nong, L. G. Bach and D.-V. N. Vo, Environ. Chem. Lett., 2023, 21, 935–980 CrossRef CAS.
- H. Khurshid, Z. Mehmood, S. Naseer, M. Aamir, F. Khurshid and M. Khan, Pak. J. Biochem. Mol. Biol., 2023, 56, 117–128 Search PubMed.
- B. Zhang, R. Xu, Y. Feng and J. Wang, Ionics, 2024, 30, 1291–1306 CrossRef CAS.
- W. Hu, Y. Zhang, B. Huang and Y. Teng, Chemosphere, 2017, 170, 183–195 CrossRef CAS PubMed.
- S. Shen, Y. Huang, A. Yuan, F. Lv, L. Liu and S. Wang, CCS Chem., 2021, 3, 129–135 CrossRef CAS.
- Z.-Y. Lu, Y.-L. Ma, J.-T. Zhang, N.-S. Fan, B.-C. Huang and R.-C. Jin, J. Water Process Eng., 2020, 38, 101681 CrossRef.
- M. S. De Ilurdoz, J. J. Sadhwani and J. V. Reboso, J. Water Process Eng., 2022, 45, 102474 CrossRef.
- B. L. Phoon, C. C. Ong, M. S. Mohamed Saheed, P.-L. Show, J.-S. Chang, T. C. Ling, S. S. Lam and J. C. Juan, J. Hazard. Mater., 2020, 400, 122961 CrossRef PubMed.
- Z. Derakhshan, M. Mokhtari, F. Babaei, R. M. Ahmadi, M. H. Ehrampoush and M. Faramarzian, J. Environ. Health Sustainable Dev., 2016, 1, 43–62 Search PubMed.
- X. Bai, W. Chen, B. Wang, T. Sun, B. Wu and Y. Wang, Int. J. Mol. Sci., 2022, 23, 8130 CrossRef CAS PubMed.
- Y. Chen, J. Yang, L. Zeng and M. Zhu, Crit. Rev. Environ. Sci. Technol., 2022, 52, 1401–1448 CrossRef CAS.
- R. Ebrahimi, A. Maleki, Y. Zandsalimi, R. Ghanbari, B. Shahmoradi, R. Rezaee, M. Safari, S. W. Joo, H. Daraei, S. Harikaranahalli Puttaiah and O. Giahi, J. Ind. Eng. Chem., 2019, 73, 297–305 CrossRef CAS.
- T. C. M. V. Do, D. Q. Nguyen, K. T. Nguyen and P. H. Le, Materials, 2019, 12, 2434 CrossRef CAS PubMed.
- K. O'Dowd, K. M. Nair and S. C. Pillai, Curr. Opin. Green Sustainable Chem., 2021, 30, 100471 CrossRef.
- K. Rokesh, M. Sakar and T.-O. Do, Nanomaterials, 2021, 11, 572 CrossRef CAS PubMed.
- X. Hu, X. Hu, Q. Peng, L. Zhou, X. Tan, L. Jiang, C. Tang, H. Wang, S. Liu and Y. Wang, Chem. Eng. J., 2020, 380, 122366 CrossRef CAS.
- Z. Yang, J. Yan, J. Lian, H. Xu, X. She and H. Li, ChemistrySelect, 2016, 1, 5679–5685 CrossRef CAS.
- M. Verma and A. K. Haritash, Environ. Technol. Innovation, 2020, 20, 101072 CrossRef CAS.
- Q. Zhang, L. Jiang, J. Wang, Y. Zhu, Y. Pu and W. Dai, Appl. Catal., B, 2020, 277, 119122 CrossRef CAS.
- G. Fan, H. Peng, J. Zhang, X. Zheng, G. Zhu, S. Wang and L. Hong, Catal. Sci. Technol., 2018, 8, 5906–5919 RSC.
- F. Torki and H. Faghihian, J. Photochem. Photobiol., A, 2017, 338, 49–59 CrossRef CAS.
- A. Payan, A. Akbar Isari and N. Gholizade, Chem. Eng. J., 2019, 361, 1121–1141 CrossRef CAS.
- R. Kumar, M. A. Barakat, B. A. Al-Mur, F. A. Alseroury and J. O. Eniola, J. Cleaner Prod., 2020, 246, 119076 CrossRef CAS.
- T. Senasu, T. Chankhanittha, K. Hemavibool and S. Nanan, Catal. Today, 2022, 384–386, 209–227 CrossRef CAS.
- Y. Gong, Y. Wu, Y. Xu, L. Li, C. Li, X. Liu and L. Niu, Chem. Eng. J., 2018, 350, 257–267 CrossRef CAS.
- W. Wang, Q. Han, Z. Zhu, L. Zhang, S. Zhong and B. Liu, Adv. Powder Technol., 2019, 30, 1882–1896 CrossRef CAS.
- N. Askari, M. Beheshti, D. Mowla and M. Farhadian, Mater. Sci. Semicond. Process., 2021, 127, 105723 CrossRef CAS.
- A. Mohammad, M. E. Khan, M. H. Cho and T. Yoon, Appl. Surf. Sci., 2021, 565, 150337 CrossRef CAS.
- M. Berkani, A. Smaali, Y. Kadmi, F. Almomani, Y. Vasseghian, N. Lakhdari and M. Alyane, J. Hazard. Mater., 2022, 421, 126719 CrossRef CAS PubMed.
- H. Bouyarmane, C. El Bekkali, J. Labrag, I. Es-saidi, O. Bouhnik, H. Abdelmoumen, A. Laghzizil, J.-M. Nunzi and D. Robert, Surf. Interfaces, 2021, 24, 101155 CrossRef CAS.
- F. Guo, X. Huang, Z. Chen, L. Cao, X. Cheng, L. Chen and W. Shi, Sep. Purif. Technol., 2021, 265, 118477 CrossRef CAS.
- M. Abdullah, J. Iqbal, M. S. Ur Rehman, U. Khalid, F. Mateen, S. N. Arshad, A. G. Al-Sehemi, H. Algarni, O. A. Al-Hartomy and T. Fazal, Chemosphere, 2023, 317, 137834 CrossRef CAS PubMed.
- T. Chankhanittha and S. Nanan, J. Colloid Interface Sci., 2021, 582, 412–427 CrossRef CAS PubMed.
- L. Liu, J. Huang, H. Yu, J. Wan, L. Liu, K. Yi, W. Zhang and C. Zhang, Chemosphere, 2021, 282, 131049 CrossRef CAS PubMed.
- E. Gómez, R. Cestaro, L. Philippe and A. Serrà, Appl. Catal., B, 2022, 317, 121703 CrossRef.
- P. Gholami, A. Khataee, R. D. C. Soltani, L. Dinpazhoh and A. Bhatnagar, J. Hazard. Mater., 2020, 382, 121070 CrossRef CAS PubMed.
- T. Xiao, Z. Tang, Y. Yang, L. Tang, Y. Zhou and Z. Zou, Appl. Catal., B, 2018, 220, 417–428 CrossRef CAS.
- Y. Sneha, S. R. Yashas, T. Thinley, S. Prabagar Jijoe and H. Puttaiah Shivaraju, Environ. Sci. Pollut. Res., 2022, 29, 67969–67980 CrossRef CAS PubMed.
- J. Wang, W. Liu, D. Zhong, Y. Ma, Q. Ma, Z. Wang and J. Pan, J. Mater. Sci., 2019, 54, 13740–13752 CrossRef CAS.
- M. Shokri, G. Isapour, M. A. Behnajady and S. Dorosti, Desalin. Water Treat., 2016, 57, 12874–12881 CrossRef CAS.
- M. N. Abellán, J. Giménez and S. Esplugas, Catal. Today, 2009, 144, 131–136 CrossRef.
- N. P. Xekoukoulotakis, C. Drosou, C. Brebou, E. Chatzisymeon, E. Hapeshi, D. Fatta-Kassinos and D. Mantzavinos, Catal. Today, 2011, 161, 163–168 CrossRef CAS.
- A. L. Giraldo, G. A. Penuela, R. A. Torres-Palma, N. J. Pino, R. A. Palominos and H. D. Mansilla, Water Res., 2010, 44, 5158–5167 CrossRef CAS PubMed.
- M. Chen and W. Chu, J. Hazard. Mater., 2012, 219, 183–189 CrossRef PubMed.
- P. Huo, X. Gao, Z. Lu, X. Liu, Y. Luo, W. Xing, J. Li and Y. Yan, Desalin. Water Treat., 2014, 52, 6985–6995 CrossRef CAS.
- A. Chatzitakis, C. Berberidou, I. Paspaltsis, G. Kyriakou, T. Sklaviadis and I. Poulios, Water Res., 2008, 42, 386–394 CrossRef CAS PubMed.
- M. N. Abellán, B. Bayarri, J. Giménez and J. Costa, Appl. Catal., B, 2007, 74, 233–241 CrossRef.
- M. Pascal, L. Pascal, M.-L. Bidondo, A. Cochet, H. Sarter, M. Stempfelet and V. Wagner, J. Environ. Public Health, 2013, 2013, 1–17 Search PubMed.
- S. N. Shah, Pak. J. Sci., 2016, 29, 701–706 CAS.
- F. A. Kuranchie, P. N. Angnunavuri, F. Attiogbe and E. N. Nerquaye-Tetteh, Cogent Environ. Sci., 2019, 5, 1603418 CrossRef.
- Y. Liu, M. Shao, L. Fu, S. Lu, L. Zeng and D. Tang, Atmos. Environ., 2008, 42, 6247–6260 CrossRef CAS.
- V. O. N. Njoku, C. Arinze, I. F. Chizoruo and E. N. Blessing, Anal. Methods Environ. Chem. J., 2021, 4, 80–106 CrossRef.
- J. E. Idomeh, O. B. Shittu, J. A. Oyedepo, B. S. Bada, S. A. Balogun, F. A. Idomeh and R. S. Ezenweani, Geomicrobiol. J., 2021, 38, 879–894 CrossRef CAS.
- C.-H. Hsu, T. Stedeford, E. Okochi-Takada, T. Ushijima, H. Noguchi, C. Muro-Cacho, J. W. Holder and M. Banasik, J. Environ. Sci. Health, Part C: Environ. Carcinog. Ecotoxicol. Rev., 2007, 25, 155–184 CrossRef CAS PubMed.
-
S. Kuppusamy, N. R. Maddela, M. Megharaj and K. Venkateswarlu, in Total Petroleum Hydrocarbons, Springer International Publishing, Cham, 2020, pp. 95–138 Search PubMed.
- R. Gusain, K. Gupta, P. Joshi and O. P. Khatri, Adv. Colloid Interface Sci., 2019, 272, 102009 CrossRef CAS PubMed.
- D. Murindababisha, A. Yusuf, Y. Sun, C. Wang, Y. Ren, J. Lv, H. Xiao, G. Z. Chen and J. He, Environ. Sci. Pollut. Res., 2021, 28, 62030–62060 CrossRef CAS PubMed.
- A. N. Ozogu, O. F. Opeoluwa, A. A. Olusegun, S. O. Adegboyega and S. O. Michael, J. Innovative Res., 2023, 1, 4–11 CrossRef.
- W. Zou, B. Gao, Y. S. Ok and L. Dong, Chemosphere, 2019, 218, 845–859 CrossRef CAS PubMed.
- X. Yang and I. Khan, Environ. Sci. Pollut. Res., 2022, 29, 4116–4127 CrossRef PubMed.
- E. Rehman and S. Rehman, Energy Rep., 2022, 8, 5430–5442 CrossRef.
-
M. D. Holmes and B. P. Murray. Toluene Toxicity, in StatPearls [Internet], StatPearls Publishing, Treasure Island (FL), 2024, Available from: https://www.ncbi.nlm.nih.gov/books/NBK599523/ Search PubMed.
-
A. Hartwig, M. Arand and M. A. K. Commission, MAK-Collection of Occupational Health and Safety, 2023, 8, 1–38 Search PubMed.
-
G. Pelletti, in Handbook of Substance Misuse and Addictions, ed. V. B. Patel and V. R. Preedy, Springer International Publishing, Cham, 2022, pp. 2591–2609 Search PubMed.
- M. V. Soares, J. Mesadri, D. F. Gonçalves, L. M. Cordeiro, A. F. da Silva, F. B. O. Baptista, R. Wagner, C. L. Dalla Corte, F. A. A. Soares and D. S. Ávila, Environ. Pollut., 2022, 298, 118856 CrossRef CAS PubMed.
- M. F. Mohammad, L. Y. Mousa, D. H. Idayyir and Z. M. Kadim, Teikyo Med. J., 2021, 44, 3345–3353 Search PubMed.
- G. Izydorczyk, K. Mikula, D. Skrzypczak, K. Moustakas, A. Witek-Krowiak and K. Chojnacka, Environ. Res., 2021, 197, 111050 CrossRef CAS PubMed.
- Y. Barwise and P. Kumar, npj Clim. Atmos. Sci., 2020, 3, 12 CrossRef CAS.
- E. Nemitz, M. Vieno, E. Carnell, A. Fitch, C. Steadman, P. Cryle, M. Holland, R. D. Morton, J. Hall and G. Mills, Philos. Trans. R. Soc., A, 2020, 378, 20190320 CrossRef CAS PubMed.
- A. Roy, A. Sharma, S. Yadav, L. T. Jule and R. Krishnaraj, Bioinorg. Chem. Appl., 2021, 10, 1764647 Search PubMed.
- J. Yang, L. Yang, M. Fang, L. Li, F. Fu, H. Xu, M. Li and X. Fan, J. Colloid Interface Sci., 2023, 631, 44–54 CrossRef CAS PubMed.
- X. Zhang, J. Chen, S. Jiang, X. Zhang, F. Bi, Y. Yang, Y. Wang and Z. Wang, J. Colloid Interface Sci., 2021, 588, 122–137 CrossRef CAS PubMed.
- J. Li, K. Li, B. Lei, M. Ran, Y. Sun, Y. Zhang, K.-H. Kim and F. Dong, Chem. Eng. J., 2021, 413, 127389 CrossRef CAS.
- M. Zhang, X. Liu, X. Zeng, M. Wang, J. Shen and R. Liu, Chem. Phys. Lett., 2020, 738, 100049 CrossRef.
- B. N. R. Winayu, W.-H. Mao and H. Chu, Sustainable Environ. Res., 2022, 32, 34 CrossRef CAS.
- V. T. T. Ho, D. H. Chau, K. Q. Bui, N. T. T. Nguyen, T. K. N. Tran, L. G. Bach and S. N. Truong, Inorganics, 2022, 10, 29 CrossRef CAS.
- S. Shajari, E. Kowsari, N. Seifvand, F. Boorboor Ajdari, A. Chinnappan, S. Ramakrishna, G. Saianand, M. Dashti Najafi, V. Haddadi-Asl and S. Abdpour, Catalysts, 2021, 11, 126 CrossRef CAS.
- Z. Sun, J. Fan, R. Feng, M. Wang, Y. Zhou and L. Zhang, J. Chem. Technol. Biotechnol., 2021, 96, 1732–1741 CrossRef CAS.
- Y. Bi, E. Sun, S. Zhang, F. Du, H. Wei, F. Liu and C. Zhao, Environ. Sci. Pollut. Res., 2021, 28, 57398–57411 CrossRef CAS PubMed.
- L. Yang, J. Guo, T. Yang, C. Guo, S. Zhang, S. Luo, W. Dai, B. Li, X. Luo and Y. Li, J. Hazard. Mater., 2021, 402, 123741 CrossRef CAS PubMed.
- P. Mohammadi, F. Ghorbani Shahna, A. Bahrami, A. A. Rafati and M. Farhadian, Int. J. Environ. Anal. Chem., 2022, 102, 222–242 CrossRef CAS.
- M. Rostami, A. Hassani Joshaghani, H. Mazaheri and A. Shokri, Int. J. Eng., 2021, 34, 756–762 Search PubMed.
- X. Zhao, Y. Zhang, M. Wu, W. Szeto, Y. Wang, W. Pan and D. Y. C. Leung, Appl. Surf. Sci., 2020, 527, 146780 CrossRef CAS.
- M. Wu, Y. Zhang, H. Huang and D. Y. C. Leung, Green Energy Environ., 2022, 7, 533–544 CrossRef CAS.
- X. Wang, H. Pan, M. Sun and Y. Zhang, J. Mater. Chem. A, 2022, 10, 6078–6085 RSC.
- J. Lyu, L. Zhou, J. Shao, Z. Zhou, J. Gao, Y. Dong, Z. Wang and J. Li, Chem. Eng. J., 2020, 391, 123602 CrossRef CAS.
- J. Liu, P. Wang, W. Qu, H. Li, L. Shi and D. Zhang, Appl. Catal., B, 2019, 257, 117880 CrossRef CAS.
- X. Li, Z. Zhu, Q. Zhao and L. Wang, J. Hazard. Mater., 2011, 186, 2089–2096 CrossRef CAS PubMed.
- W. J. Liang, J. Li and Y. Q. Jin, J. Environ. Sci. Health, Part A: Toxic/Hazard. Subst. Environ. Eng., 2010, 45, 1384–1390 CrossRef CAS PubMed.
- C. Young, T. M. Lim, K. Chiang and R. Amal, Water Sci. Technol., 2004, 50, 251–256 CrossRef CAS PubMed.
- C. L. Bianchi, S. Gatto, C. Pirola, A. Naldoni, A. Di Michele, G. Cerrato, V. Crocellà and V. Capucci, Appl. Catal., B, 2014, 146, 123–130 CrossRef.
- Y. Feng, L. Li, M. Ge, C. Guo, J. Wang and L. Liu, ACS Appl. Mater. Interfaces, 2010, 2, 3134–3140 CrossRef CAS PubMed.
- W. M. Shackelford, D. M. Cline, L. Faas and G. Kurth, Anal. Chim. Acta, 1983, 146, 15–27 CrossRef CAS.
-
R. L. Adkins, in Kirk-Othmer Encyclopedia of Chemical Technology, ed. Kirk-Othmer, Wiley, 1st edn, 2000, DOI:10.1002/0471238961.1409201801041109.a01.pub2.
- D. S. Bhatkhande, S. P. Kamble, S. B. Sawant and V. G. Pangarkar, Chem. Eng. J., 2004, 102, 283–290 CrossRef CAS.
- D. S. Bhatkhande, V. G. Pangarkar and A. A. Beenackers, Water Res., 2003, 37, 1223–1230 CrossRef CAS PubMed.
- T. Akhtar, H. Nasir, E. Sitara, S. A. B. Bukhari, S. Ullah and R. M. A. Iqbal, Environ. Sci. Pollut. Res., 2022, 29, 49925–49936 CrossRef CAS PubMed.
- D. Li, S. Yu, H. Geng, W. Zhou, D. Mu and S. Liu, Appl. Surf. Sci., 2023, 607, 154996 CrossRef CAS.
- S. P. Kamble, S. B. Sawant, J. C. Schouten and V. G. Pangarkar, J. Chem. Technol. Biotechnol., 2003, 78, 865–872 CrossRef CAS.
- S. P. Kamble, S. B. Sawant and V. G. Pangarkar, Ind. Eng. Chem. Res., 2003, 42, 6705–6713 CrossRef CAS.
- R. W. Matthews, M. Abdullah and G.-C. Low, Anal. Chim. Acta, 1990, 233, 171–179 CrossRef CAS.
- K. Hofstadler, R. Bauer, S. Novalic and G. Heisler, Environ. Sci. Technol., 1994, 28, 670–674 CrossRef CAS PubMed.
- A. Mills, R. H. Davies and D. Worsley, Chem. Soc. Rev., 1993, 22, 417–425 RSC.
- I. Nitoi, P. Oancea, M. Raileanu, M. Crisan, L. Constantin and I. Cristea, J. Ind. Eng. Chem., 2015, 21, 677–682 CrossRef CAS.
- S. Chilukoti, S. Rohit and S. Chikkadasappa, Ind. Eng. Chem. Res., 2015, 54(32), 7800–7810 CrossRef.
- R. J. Tayade, R. G. Kulkarni and R. V. Jasra, Ind. Eng. Chem. Res., 2006, 45, 922–927 CrossRef CAS.
- A. Ayati, B. Tanhaei, F. F. Bamoharram, A. Ahmadpour, P. Maydannik and M. Sillanpää, Sep. Purif. Technol., 2016, 171, 62–68 CrossRef CAS.
- G. C. J. Swarnavalli, S. Dinakaran, S. Krishnaveni and G. M. Bhalerao, Mater. Sci. Eng., B, 2019, 247, 114376 CrossRef.
- S. S. Boxi and S. Paria, RSC Adv., 2015, 5, 37657–37668 RSC.
- L. Zhang, X. He, X. Xu, C. Liu, Y. Duan, L. Hou, Q. Zhou, C. Ma, X. Yang and R. Liu, Appl. Catal., B, 2017, 203, 1–8 CrossRef CAS.
-
W. Wang, Y. Huang and S. Yang, in 2010 International Conference on Mechanic Automation and Control Engineering, IEEE, 2010, pp. 1303–1305 Search PubMed.
- W.-K. Jo, Y. Won, I. Hwang and R. J. Tayade, Ind. Eng. Chem. Res., 2014, 53, 3455–3461 CrossRef CAS.
- Z. Sun, M. Zhao, F. Li, T. Wang and L. Xu, Mater. Res. Bull., 2014, 60, 524–529 CrossRef CAS.
- S. Zhang, L. Li, Y. Liu and Q. Zhang, Chin. J. Chem. Eng., 2017, 25, 223–231 CrossRef CAS.
- Q. Liu, M. Wen, Y. Guo, S. Song, G. Li and T. An, ACS Appl. Mater. Interfaces, 2022, 14, 55503–55516 CrossRef CAS PubMed.
- R. Jevtic, P. A. Ramachandran and M. P. Dudukovic, Ind. Eng. Chem. Res., 2009, 48, 7986–7993 CrossRef CAS.
- S. K. Guha, Y. Obora, D. Ishihara, H. Matsubara, I. Ryu and Y. Ishii, Adv. Synth. Catal., 2008, 350, 1323–1330 CrossRef CAS.
- H. Li, Y. She and T. Wang, Front. Chem. Sci. Eng., 2012, 6, 356–368 CrossRef CAS.
- A. Maldotti, A. Molinari and R. Amadelli, Chem. Rev., 2002, 102, 3811–3836 CrossRef CAS PubMed.
- M. K. Estahbanati, M. Feilizadeh, A. Babin, B. Mei, G. Mul and M. C. Iliuta, Chem. Eng. J., 2020, 382, 122732 CrossRef.
- D. G. Montjoy, E. A. Wilson, H. Hou, J. D. Graves and N. A. Kotov, Nat. Commun., 2023, 14, 857 CrossRef CAS PubMed.
- Y. Xiao, J. Liu, J. Mai, C. Pan, X. Cai and Y. Fang, J. Colloid Interface Sci., 2018, 516, 172–181 CrossRef CAS PubMed.
- M. A. Brusa and M.
A. Grela, J. Phys. Chem. B, 2005, 109, 1914–1918 CrossRef CAS PubMed.
- J. J. Murcia, M. C. Hidalgo, J. A. Navío, V. Vaiano, D. Sannino and P. Ciambelli, Catal. Today, 2013, 209, 164–169 CrossRef CAS.
- P. Wen, Y. Zhang, G. Xu, D. Ma, P. Qiu and X. Zhao, J. Mater., 2019, 5, 696–701 Search PubMed.
- Y. Shiraishi, Y. Sugano, S. Ichikawa and T. Hirai, Catal. Sci. Technol., 2012, 2, 400–405 RSC.
- A. Henríquez, V. Melin, N. Moreno, H. D. Mansilla and D. Contreras, Molecules, 2019, 24, 2244 CrossRef PubMed.
- K. Ueyama, T. Hatta, A. Okemoto, K. Taniya, Y. Ichihashi and S. Nishiyama, Res. Chem. Intermed., 2018, 44, 629–638 CrossRef CAS.
- J. T. Carneiro, T. J. Savenije, J. A. Moulijn and G. Mul, J. Photochem. Photobiol., A, 2011, 217, 326–332 CrossRef CAS.
- C. B. Almquist and P. Biswas, Appl. Catal., A, 2001, 214, 259–271 CrossRef CAS.
- H. Einaga, S. Futamura and T. Ibusuki, Appl. Catal., B, 2002, 38, 215–225 CrossRef CAS.
- R. Vinu and G. Madras, Appl. Catal., A, 2009, 366, 130–140 CrossRef CAS.
- V. H. van Dijk, G. Simmelink and G. Mul, Appl. Catal., A, 2014, 470, 63–71 CrossRef CAS.
- P. Du, J. A. Moulijn and G. Mul, J. Catal., 2006, 238, 342–352 CrossRef CAS.
- E. Fornal and C. Giannotti, J. Photochem. Photobiol., A, 2007, 188, 279–286 CrossRef CAS.
- H. Wang, C. Yu, G. Xu, Y. Zhang, X. Wu and L. Cheng, Mater. Chem. Phys., 2020, 253, 123391 CrossRef CAS.
- K. Shimizu, Y. Murata and A. Satsuma, J. Phys. Chem. C, 2007, 111, 19043–19051 CrossRef CAS.
- Y. Rasouli, M. Abbasi and S. A. Hashemifard, Int. J. Environ. Sci. Technol., 2019, 16, 5595–5610 CrossRef CAS.
- H. Inan, A. Dimoglo, H. Şimşek and M. Karpuzcu, Sep. Purif. Technol., 2004, 36, 23–31 CrossRef CAS.
- O. A. Fadali, E. E. Ebrahiem, T. E. Farrag, M. S. Mahmoud and A. El-Gamil, Minia J. Eng. Technol., 2013, 32, 88–101 Search PubMed.
- M. A. Tony, P. J. Purcell and Y. Zhao, J. Environ. Sci. Health, Part A: Toxic/Hazard. Subst. Environ. Eng., 2012, 47, 435–440 CrossRef CAS PubMed.
- G. H. Ahmed, S. R. M. Kutty and M. H. Isa, Int. J. Appl., 2011, 1, 179–189 Search PubMed.
- I. Khouni, G. Louhichi, A. Ghrabi and P. Moulin, Process Saf. Environ. Prot., 2020, 135, 323–341 CrossRef CAS.
- J.-Q. Jiang, Curr. Opin. Chem. Eng., 2015, 8, 36–44 CrossRef.
- R. Asghari, M. S. Safavi and J. Khalil-Allafi, Trans. IMF, 2020, 98, 250–257 CrossRef CAS.
- L. Loredana, G. Ciobanu, S. M. Cimpeanu, O. Kotova, R. Ciocinta, D. Bucur and M. Harja, AgroLife Sci. J., 2019, 8, 139–145 Search PubMed.
- W. T. Vieira, M. B. de Farias, M. P. Spaolonzi, M. G. C. da Silva and M. G. A. Vieira, Environ. Chem. Lett., 2020, 18, 1113–1143 CrossRef CAS.
- J. F. Nure and T. T. Nkambule, J. Ind. Eng. Chem., 2023, 126, 92–114 CrossRef CAS.
- J.-S. Seo, Y.-S. Keum and Q. X. Li, Int. J. Environ. Res. Public Health, 2009, 6, 278–309 CrossRef CAS PubMed.
- R. Rauhut and G. Klug, FEMS Microbiol. Rev., 1999, 23, 353–370 CrossRef CAS PubMed.
- Z. C. Symons and N. C. Bruce, Nat. Prod. Rep., 2006, 23, 845–850 RSC.
- M. Umar and H. A. Aziz, Org. Pollut.: Monit., Risk Treat., 2013, 8, 196–197 Search PubMed.
-
R. Ameta, S. Benjamin, A. Ameta and S. C. Ameta, in Materials Science Forum, Trans Tech Publ, 2013, vol. 734, pp. 247–272 Search PubMed.
- C. S. Turchi and D. F. Ollis, J. Catal., 1990, 122, 178–192 CrossRef CAS.
- Q. Xiang, J. Yu and P. K. Wong, J. Colloid Interface Sci., 2011, 357, 163–167 CrossRef CAS PubMed.
- W. S. Koe, J. W. Lee, W. C. Chong, Y. L. Pang and L. C. Sim, Environ. Sci. Pollut. Res., 2020, 27, 2522–2565 CrossRef CAS PubMed.
- R. M. Mohammed and K. M. M. Al-zobai, Solid State Technol., 2020, 63, 5390–5404 Search PubMed.
- B. Ogoh-Orch, P. Keating and A. Ivaturi, ACS Omega, 2023, 8, 43556–43572 CrossRef CAS PubMed.
- D. A. D. A. Aljuboury and F. Shaik, S. Afr. J. Chem. Eng., 2021, 35, 69–77 Search PubMed.
- Z. Ghasemi, H. Younesi and A. A. Zinatizadeh, J. Taiwan Inst. Chem. Eng., 2016, 65, 357–366 CrossRef CAS.
- F. Shahrezaei, A. Akhbari and A. Rostami, Int. J. Energy Environ., 2012, 3, 267–274 CAS.
- E. K. Tetteh, S. Rathilal and D. B. Naidoo, Sci. Rep., 2020, 10, 8850 CrossRef CAS PubMed.
- I. Ul Haq, W. Ahmad, I. Ahmad and M. Yaseen, Water Environ. Res., 2020, 92, 2086–2094 CrossRef CAS PubMed.
- W. Z. Khan, I. Najeeb, M. Tuiyebayeva and Z. Makhtayeva, Process Saf. Environ. Prot., 2015, 94, 479–486 CrossRef CAS.
- C. P. M. de Oliveira, M. M. Viana and M. C. S. Amaral, J. Water Process Eng., 2020, 34, 101093 CrossRef.
- F. V. Santos, E. B. Azevedo and M. Dezotti, Braz. J. Chem. Eng., 2006, 23, 451–460 CrossRef CAS.
- J. Saien and H. Nejati, J. Hazard. Mater., 2007, 148, 491–495 CrossRef CAS PubMed.
- A. X. R. Corrêa, E. N. Tiepo, C. A. Somensi, R. M. Sperb and C. M. Radetski, J. Environ. Eng., 2010, 136, 40–45 CrossRef.
-
S. A. Malik, Master's thesis, King Fahd University of Petroleum and Minerals, Saudi Arabia, 2005 Search PubMed.
- P. Stepnowski, E. M. Siedlecka, P. Behrend and B. Jastorff, Water Res., 2002, 36, 2167–2172 CrossRef CAS PubMed.
- J. Saien and F. Shahrezaei, Int. J. Photoenergy, 2012, 2012, 1–5 CrossRef.
- M. D'Auria, L. Emanuele, R. Racioppi and V. Velluzzi, J. Hazard. Mater., 2009, 164, 32–38 CrossRef PubMed.
- E. A. Emam and N. A. K. Aboul-Gheit, Energy Sources, Part A, 2014, 36, 1123–1133 CrossRef CAS.
- E. H. Khader, T. J. Mohammed, T. M. Albayati, N. M. C. Saady and S. Zendehboudi, J. Mol. Struct., 2024, 1304, 137688 CrossRef CAS.
- E. K. Tetteh, B. D. Naidoo and S. Rathilal, Environ. Eng. Res., 2019, 24, 711–717 CrossRef.
- G. Alhakimi, S. Gebril and L. H. Studnicki, J. Photochem. Photobiol., A, 2003, 157, 103–109 CrossRef CAS.
- C. Kormann, D. W. Bahnemann and M. R. Hoffmann, Environ. Sci. Technol., 1988, 22, 798–806 CrossRef CAS PubMed.
- A. Kumar and G. Pandey, Mater. Sci. Eng. Int. J., 2017, 1, 1–10 Search PubMed.
- S. Ameen, H.-K. Seo, M. S. Akhtar and H. S. Shin, Chem. Eng. J., 2012, 210, 220–228 CrossRef CAS.
- J. Zhu, W. Zheng, B. He, J. Zhang and M. Anpo, J. Mol. Catal. A: Chem., 2004, 216, 35–43 CrossRef CAS.
- C. Adán, J. Carbajo, A. Bahamonde and A. Martínez-Arias, Catal. Today, 2009, 143, 247–252 CrossRef.
- G. Sivalingam, K. Nagaveni, M. S. Hegde and G. Madras, Appl. Catal., B, 2003, 45, 23–38 CrossRef CAS.
- K. Nagaveni, G. Sivalingam, M. S. Hegde and G. Madras, Appl. Catal., B, 2004, 48, 83–93 CrossRef CAS.
- K. Mushtaq, M. Saeed, W. Gul, M. Munir, A. Firdous, T. Yousaf, K. Khan, H. M. R. Sarwar, M. A. Riaz and S. Zahid, Inorg. Nano-Met. Chem., 2020, 50, 580–586 CrossRef CAS.
- A. Ali, M. Shoeb, Y. Li, B. Li and M. A. Khan, J. Mol. Liq., 2021, 324, 114696 CrossRef CAS.
- M. Zhou, J. Yu, S. Liu, P. Zhai and B. Huang, Appl. Catal., B, 2009, 89, 160–166 CrossRef CAS.
- F. He, J. Li, T. Li and G. Li, Chem. Eng. J., 2014, 237, 312–321 CrossRef CAS.
- X. Li, G. Chen, Y. Po-Lock and C. Kutal, J. Chem. Technol. Biotechnol., 2003, 78, 1246–1251 CrossRef CAS.
|
This journal is © The Royal Society of Chemistry 2024 |
Click here to see how this site uses Cookies. View our privacy policy here.