DOI:
10.1039/D4SC04147J
(Edge Article)
Chem. Sci., 2024,
15, 17556-17561
Controlled degradation of chemically stable poly(aryl ethers) via directing group-assisted catalysis†
Received
23rd June 2024
, Accepted 17th September 2024
First published on 7th October 2024
Abstract
To establish a sustainable society, the development of polymer materials capable of reverting into monomers on demand is crucial. Traditional methods rely on breaking labile bonds such as esters in the main chain, which limits applicability to polymers that consist of robust covalent bonds. We found that the integration of directing groups allowed the engineering of resilient polymers with built-in recyclability. Our study showcases phenylene ether-based polymers fortified with directing groups, which can be selectively disassembled under nickel catalysts via selective cleavage of carbon–oxygen bonds. Notably, these polymers exhibit exceptional chemical stability towards acids, bases, and oxidizing agents, while being degradable to well-defined, repolymerizable molecules in the presence of a catalyst. Our findings allow for the development of next-generation polymer materials that are chemically recyclable by design.
Introduction
Serious concerns about the long-term environmental impact caused by plastic pollution are prompting us to transition away from single-use plastics toward a more sustainable and circular polymer economy.1 To this end, mechanical recycling has been implemented on an industrial scale. However, the physical properties of the recycled materials are frequently compromised compared to the original ones, and mechanical recycling cannot be universally applied to all plastics.2 A more ideal approach is chemical recycling, wherein polymers are transformed back into monomers or other well-defined small molecules that could subsequently be repolymerized.3 Although this approach is appealing in principle, successful examples have primarily been limited to the polymers that contain chemically labile bonds in their main chains encompassing esters,4 acetals,5 disulfides,6 and silyl ethers7 (Fig. 1a). Polymers that consist of strong covalent bonds, such as C–C or C(aryl)–O bonds, often exhibit high robustness, which in turn makes depolymerization into monomers a challenge due to the lack of mild methods that could be used to cleave these bonds. Therefore, only a limited array of techniques has been documented for depolymerizing such polymers. For instance, polyolefins may be depolymerized by heating above the ceiling temperature (Tceiling), which is defined as the temperature at which the rates of polymerization and depolymerization of these polymers are equal. However, the Tceiling for common robust polyolefins exceeds 400 °C,8 which poses difficulties in controlling degradation into well-defined monomers. Alternatively, multi-step post-polymerization modifications9 such as C–H oxidation10 and dehydrogenation11 have been employed to promote the cleavage of C–C bonds in polymer backbones. These methods, however, also tend to yield a mixture of products that are unsuitable for repolymerization.
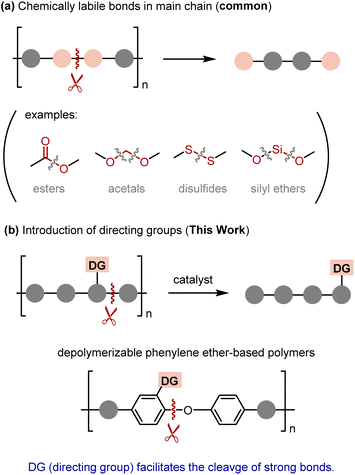 |
| Fig. 1 Strategies for the design of depolymerizable polymers. | |
Herein, we introduce a directing group (DG) that serves as a design principle for depolymerizable polymers devoid of labile chemical bonds in their main chain (Fig. 1b). DG is a heteroatom-containing functional group that coordinates to a transition metal catalyst to facilitate the cleavage of strong covalent bonds by forming a stable metallacyclic intermediate.12 DGs are strategically used to develop catalytic reactions that involve the activation of strong σ-bonds in low molecular weight compounds.13 Surprisingly, however, the DG strategy has not been exploited for the cleavage of the main chain of polymeric materials. It is noteworthy that a DG does not fundamentally alter the thermal and chemical stability of neighboring covalent bonds but rather promotes their cleavage only in the presence of a suitable catalyst. Therefore, the robust nature of parent polymers is anticipated to be preserved with the introduction of DGs.
As a proof-of-concept study, our investigation focuses on assessing the impact of a DG on the depolymerization of polymers containing a phenylene ether unit, because our group demonstrated that the cleavage of a C(aryl)–O bond can be accelerated by a DG in a nickel-catalyzed process.14 Phenylene ethers serve as crucial structural motifs in several durable polymers, notably, poly(phenylene ether)s (PPEs) and poly(ether ether ketone)s (PEEKs). While previous studies have reported the direct depolymerization of these materials using heterogeneous catalysts,15 chemical oxidation,16 or nucleophilic aromatic substitution methods,17 the resultant degraded products were obtained in forms that were unsuitable for straightforward repolymerization into the parent phenylene ether-based polymers. Herein, we demonstrate that a DG strategy enables the development of phenylene ether-based polymers capable of undergoing degradation to yield well-defined low-molecular-weight compounds, which can subsequently be repolymerized into the parent polymers.
Results and discussion
Preparation of DG-installed polymers
We initiated our studies by investigating the effect of DGs on the efficiency of the catalytic cleavage of a C(aryl)–O bond in model monomeric substrates 1 (Fig. S1†). Building upon our previous studies,14a diphenyl ether derivatives 1a–d were reacted with HSiMe(OMe)2 (reductant) in the presence of Ni(cod)2 (a catalyst precursor) and PCy3 (a ligand) in toluene at 80 °C for 18 h. Although the reaction did not occur when a substrate had no DG (Entry 1), the introduction of 2-pyridyl (Entry 2), ester (Entry 3) and amide (Entry 4) groups facilitated the reductive cleavage of C(aryl)–O bonds to form 2, with a 2-pyridyl group being the most effective. Therefore, we decided to employ a 2-pyridyl group as the DG for the development of depolymerizable polymers.
A PPE-based polymer bearing a 2-pyridyl group (DG-PPE) was synthesized by polycondensation via nucleophilic aromatic substitution (SNAr) using an initiator (Fig. 2a).18 Thus, the reaction of 4-fluorophenol derivative 3 in the presence of KH (1.0 equiv., base) and 4,4′-difluorobenzophenone (0.63 mol%, initiator) in NMP at 200 °C for 4 h afforded the desired DG-PPE in a 62% isolated yield upon reprecipitation from CHCl3/MeOH. The relatively high dispersity of DG-PPE (Đ = 3.01) compared with the value reported in Yokozawa's work (Đ = 1.1) can be attributed to the higher polymerization temperature used in our study, which induced undesired main-chain cleavage as a side reaction (see the ESI† for details). A PEEK-based polymer bearing a 2-pyridyl group (DG-PEEK1) was also synthesized using a similar method of polycondensation between hydroquinone derivative 4 and 4,4′-difluorobenzophenone derivative 5 in the presence of a catalytic amount of Cs2CO3 in NMP at 150–180 °C (Fig. 2b).19 The polycondensation of bis(phenol) derivative 6 and difluoride 5 afforded a PEEK derivative that possesses fewer 2-pyridyl groups (one pyridine ring per two ether moieties for DG-PEEK2vs. one pyridine per one ether for DG-PEEK1, Fig. 2c). All DG-installed polymers were characterized by 1H and 13C NMR and MALDI-TOF MS (see the ESI†).
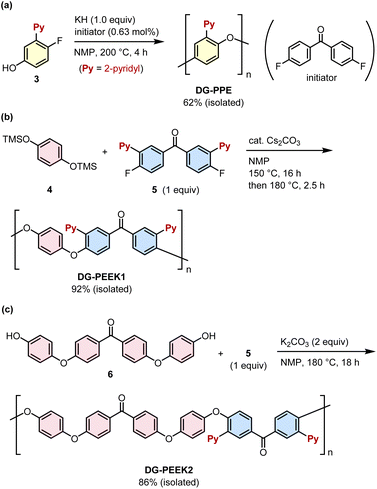 |
| Fig. 2 Synthesis of (a) DG-PPE, (b) DG-PEEK1, and (c) DG-PEEK2. | |
Properties of DG-installed polymers
The physical properties of DG-installed polymers are summarized in Table 1. All DG-installed polymers exhibited notable thermal stability with high decomposition temperatures at 5% weight loss (Td5 = 399–465 °C). The Td5 values measured under air are comparable to those measured under nitrogen. DG-PPE displayed the transition temperature (Tg) of 143 °C, which is significantly higher than that reported for a parent PPE (83 °C).20 Similarly, DG-PEEK1 exhibited a markedly higher Tg value of 182 °C, showcasing that the introduction of DGs does not compromise the exceptional heat resistance of PEEK (Tg = 143 °C). DG-PEEK2 also exhibited a comparable Tg value (172 °C), indicating that the feed ratio of DGs has minimal impact on thermal properties. None of the DG-installed polymers synthesized in this study exhibited discernible Tm values. This departure from the behavior of the parent PPE (Tm = 290 °C) and that of PEEK (Tm = 344 °C) underscores the significant influence of the DG incorporation on polymer crystallinity.
Table 1 Properties of DG-PPE, DG-PEEK1 and DG-PEEK2
Entry |
Polymer |
M
w
[kDa] |
Đ
|
T
g
[°C] |
T
d5
[°C] |
Weight average molecular weights and dispersities were determined by size-exclusion chromatography in CHCl3 by comparison with low dispersity polystyrene standards.
Glass transition temperature as determined by DSC thermogram (exo up, 10 °C min−1, second run).
Decomposition temperature at 5% weight loss as determined by TGA thermogram (10 °C min−1 under nitrogen gas flow). The values in parentheses refer to those measured under air, unless otherwise noted.
Values for poly(p-phenylene oxide), which are cited from ref. 20.
Not determined due to insolubility in organic solvents at room temperature.
Decomposition temperature at 2% weight loss that was reported in ref. 20.
Values for a sample purchased from Aldrich (Cat. No. 456640).
|
1 |
DG-PPE
|
4.98 |
3.01 |
143 |
399 (419) |
2 |
DG-PEEK1
|
27.2 |
1.81 |
182 |
465 (473) |
3 |
DG-PEEK2
|
59.0 |
2.21 |
172 |
437 (451) |
4 |
PPE
|
—e |
—e |
83 |
(390)f |
5 |
PEEK
|
—e |
—e |
143 |
576 |
The chemical stabilities of DG-PPE and DG-PEEK1 were investigated through immersion in five distinct solutions for 24 h: aqueous HCl (12 M), aqueous NaOH (10 M), aqueous H2O2 (30%), AcOH and boiling water. SEC analysis of the recovered polymeric materials after neutralization revealed no change in molecular weight after these treatments (Fig. 3a for DG-PPE; Fig. 3b for DG-PEEK1). Additionally, minimal differences were observed in the FT-IR spectra before and after exposure to the solutions (Fig. 3c for DG-PPE; Fig. 3d for DG-PEEK1), indicating the stability of these polymers towards strong acids, bases, and oxidants.
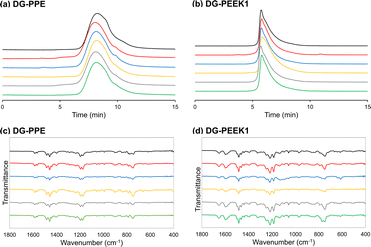 |
| Fig. 3 Chemical stability of DG-PPE and DG-PEEK1.a SEC (a and b) and FT-IR (c and d) analysis measured after neutralization for polymer samples treated with the following solutions at rt for 24 h: black, none; red, HCl (12 M); blue, NaOH (10 M); orange, H2O2 (30%); gray, AcOH; green, boiling water. | |
Controlled degradation of DG-installed polymers
Having confirmed the thermal and chemical stability of DG-introduced polymers DG-PPE, DG-PEEK1 and DG-PEEK2, we next investigated their catalytic degradation. On the basis of model studies (Fig. S1†), nickel-catalyzed reductive degradation of these polymers with hydrosilane was investigated. The reaction of DG-PPE with HSiMe(OMe)2 (2 equiv. per monomer unit) in the presence of a Ni(cod)2/PCy3 catalyst in toluene at 80 °C for 18 h afforded phenol 7 in an isolated yield of 64% (Fig. 4a). These nickel-catalyzed conditions were successfully applied to disassemble DG-PEEK1, selectively yielding hydroquinone component 8 and benzophenone component 9 in isolated yields of 78 and 87%, respectively (Fig. 4b). Similarly, DG-PEEK2 underwent degradation to afford 9 (80%) and 10 (68%) under analogous conditions (Fig. 4c). Notably, the site-selective cleavage of C(aryl)–O bonds positioned ortho to the directing group occurred, while other C(aryl)–O bonds remained intact. The resultant structurally well-defined degraded products were converted back into the parent polymers in a few chemical steps (Fig. 4d). For instance, phenol 7 was ortho-fluorinated to form 3 by palladium catalysis,21 which enabled its use in the polymerization of DG-PPE. Compound 9, which was generated from the degradation of DG-PEEK1 and DG-PEEK2, was transformed into fluorinated benzophenone 5 through oxidation and ortho-fluorination. Consequently, the straightforward recycling of DG-PEEK1 was feasible by reacting 5 with a degraded product 8. Similarly, DG-PEEK2 was chemically recycled by oxidizing degraded product 10 into ketone 6, which was followed by condensation with 5 (see the ESI†). Of particular significance is the pivotal role played by the directing group in the ortho-fluorination step, as well as its contribution to the depolymerization process. This underscores the advantageous utilization of directing groups in the strategic design of recyclable polymers.
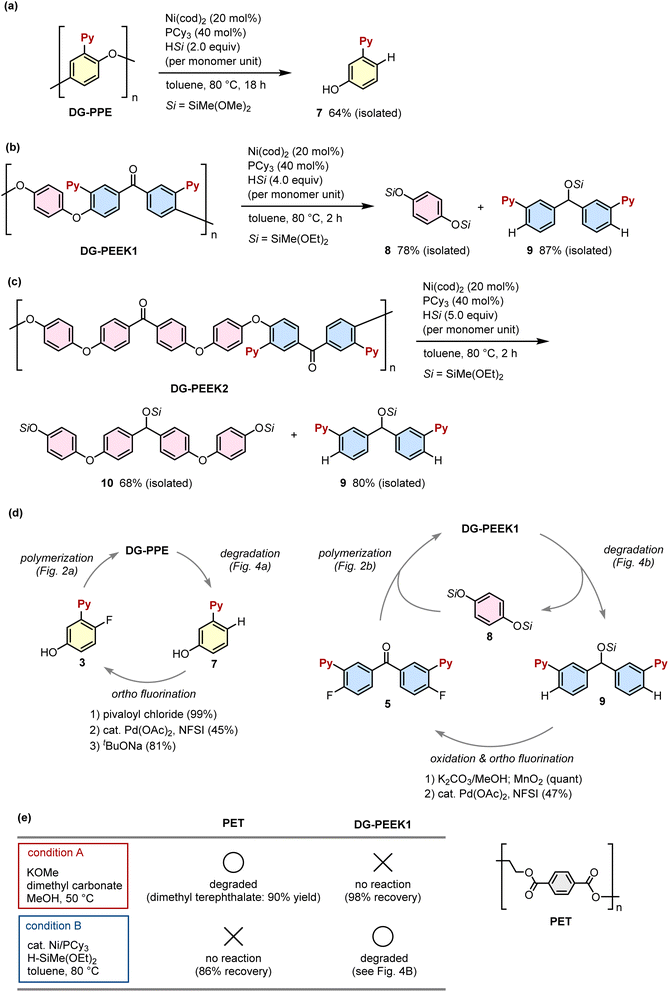 |
| Fig. 4 (a) Controlled degradation of DG-PPE. (b) Controlled degradation of DG-PEEK1. (c) Controlled degradation of DG-PEEK2. (d) Chemical recycling of DG-PPE and DG-PEEK1. (e) Orthogonal degradation of PET and DG-PEEK1. | |
The method for depolymerizing DG-installed polymers exhibits remarkable specificity, and diverges from conventional approaches used for polymers containing labile chemical bonds, such as simple acids or bases. For example, polyethylene terephthalate (PET) undergoes efficient depolymerization under basic conditions (condition A, Fig. 4e),22 whereas DG-PEEK1 remains entirely stable under these circumstances. Conversely, the nickel-catalyzed conditions utilized for DG-PEEK1 degradation (condition B, Fig. 4e) exhibit no impact on PET, underscoring the selectivity of this catalyst system toward substrates featuring DGs. This orthogonal behavior bears significant advantages for the design of chemical recycling protocols, particularly when addressing polymer mixtures.
Conclusions
While the demand for polymer materials that could be depolymerized into monomers is on the rise, current design strategies are limited mostly to the incorporation of labile covalent bonds, such as esters, into their main chains. Our work presented herein showcases a novel approach: polymers composed of strong covalent bonds can be selectively degraded into well-defined monomers by integrating the concept of a directing group. This directing group facilitates the cleavage of robust chemical bonds within the polymer's main chain through the formation of stable metallacyclic intermediates with transition metal catalysts. It is important to note that the introduction of pyridine directing groups did not compromise the chemical stability of the polymers in the absence of a catalyst, which shows promise as a potent strategy for designing robust polymers that are chemically recyclable. We are currently exploring the application of this strategy to other resilient polymers in our laboratory, which should open new avenues for the design and recycling of sustainable materials.
Data availability
All data are available in the main text or the ESI.†
Author contributions
UH and MT conceived of the work. All authors designed the experiments. SO and HM performed the experiments. All authors prepared the manuscript.
Conflicts of interest
There are no conflicts to declare.
Acknowledgements
This work was supported by JSPS KAKENHI grants JP21H04682 (M. T.), JP24H02207 (M. T.) and Japan Science and Technology Agency CREST JPMJCR22L6 (M. T.). S. O. thanks JST SPRING (JPMJSP2138) and a JSPS Research Fellowship for Young Scientists (24KJ1574). The authors thank Professors Yutaka Ie and Naoki Ando for the SEC measurements and Professor Fumitaka Ishiwari for the TGA measurements under air. We also thank the Instrumental Analysis Center, Graduate School of Engineering, Osaka University, for HRMS.
Notes and references
- I. Vollmer, M. J. F. Jenks, M. C. P. Roelands, R. J. White, T. van Harmelen, P. de Wild, G. P. van der Laan, F. Meirer, J. T. F. Keurentjes and B. M. Weckhuysen, Angew. Chem., Int. Ed., 2020, 59, 15402–15423 CrossRef CAS PubMed.
- A. Rahimi and J. M. García, Nat. Rev. Chem, 2017, 1, 0046 CrossRef.
-
(a) G. W. Coates and Y. D. Y. L. Getzler, Nat. Rev. Mater., 2020, 5, 501–516 CrossRef CAS;
(b) R. A. Clark and M. P. Shaver, Chem. Rev., 2024, 124, 2617–2650 CrossRef CAS.
-
(a) J. Payne and M. D. Jones, ChemSusChem, 2021, 14, 4041–4070 CrossRef PubMed;
(b) M. Häußler, M. Eck, D. Rothauer and S. Mecking, Nature, 2021, 590, 423–427 CrossRef;
(c) Y. Zhao, E. M. Rettner, K. L. Harry, Z. Hu, J. Miscall, N. A. Rorrer and G. M. Miyake, Science, 2023, 382, 310–314 CrossRef PubMed;
(d) J.-B. Zhu, E. M. Watson, J. Tang and E. Y.-X. Chen, Science, 2018, 360, 398–403 CrossRef PubMed;
(e) X.-L. Li, R. W. Clarke, J.-Y. Jiang, T.-Q. Xu and E. Y.-X. Chen, Nat. Chem., 2023, 15, 278–285 CrossRef PubMed.
-
(a) J. M. Williams, H.-R. Schulten, N. E. Vanderborgh and R. D. Walker, Polymer, 1992, 33, 4630–4634 CrossRef;
(b) B. A. Abel, R. L. Snyder and G. W. Coates, Science, 2021, 373, 783–789 CrossRef CAS PubMed;
(c) H. G. Hester, B. A. Abel and G. W. Coates, J. Am. Chem. Soc., 2023, 145, 8800–8804 CrossRef CAS PubMed.
-
(a) B.-S. Wang and D.-H. Qu, Chem. Lett., 2023, 52, 496–502 CrossRef CAS;
(b) Y. Deng, Q. Zhang, D.-H. Qu, H. Tian and B. L. Feringa, Angew. Chem., Int. Ed., 2022, 61, e202209100 CrossRef CAS PubMed;
(c) B.-S. Wang, Q. Zhang, Z.-Q. Wang, C.-Y. Shi, X.-Q. Gong, H. Tian and D.-H. Qu, Angew. Chem., Int. Ed., 2023, 62, e202215329 CrossRef CAS.
-
(a) A. M. Johnson and J. A. Johnson, Angew. Chem., Int. Ed., 2023, 62, e202315085 CrossRef CAS;
(b) C. Cheng, J. X. Shi, E.-H. Kang, T. F. Nelson, M. Sander, K. McNeill and J. F. Hartwig, J. Am. Chem. Soc., 2024, 146, 12645–12655 CrossRef CAS PubMed.
- M. Chu, Y. Liu, X. Lou, Q. Zhang and J. Chen, ACS Catal., 2022, 12, 4659–4679 CrossRef CAS.
- S. T. Schwab, M. Baur, T. F. Nelson and S. Mecking, Chem. Rev., 2024, 124, 2327–2351 CrossRef CAS PubMed.
-
(a) K. Parkatzidis, H. S. Wang and A. Anastasaki, Angew. Chem., Int. Ed., 2024, 63, e202402436 CrossRef CAS;
(b) Z. Huang, M. Shanmugam, Z. Liu, A. Brookfield, E. L. Bennett, R. Guan, D. E. Vega Herrera, J. A. Lopez-Sanchez, A. G. Slater, E. J. L. McInnes, X. Qi and J. Xiao, J. Am. Chem. Soc., 2022, 144, 6532–6542 CrossRef CAS;
(c) K. P. Sullivan, A. Z. Werner, K. J. Ramirez, L. D. Ellis, J. R. Bussard, B. A. Black, D. G. Brandner, F. Bratti, B. L. Buss, X. Dong, S. J. Haugen, M. A. Ingraham, M. O. Konev, W. E. Michener, J. Miscall, I. Pardo, S. P. Woodworth, A. M. Guss, Y. Román-Leshkov, S. S. Stahl and G. T. Beckham, Science, 2022, 378, 207–211 CrossRef CAS;
(d) C. Rabot, Y. Chen, S. Bijlani, Y.-M. Chiang, C. E. Oakley, B. R. Oakley, T. J. Williams and C. C. C. Wang, Angew. Chem., Int. Ed., 2023, 62, e202214609 CrossRef CAS;
(e) K. Wang, R. Jia, P. Cheng, L. Shi, X. Wang and L. Huang, Angew. Chem., Int. Ed., 2023, 62, e202301340 CrossRef CAS;
(f) S. T. Nguyen, E. A. McLoughlin, J. H. Cox, B. P. Fors and R. R. Knowles, J. Am. Chem. Soc., 2021, 143, 12268–12277 CrossRef CAS PubMed;
(g) S. T. Nguyen, L. R. Fries, J. H. Cox, Y. Ma, B. P. Fors and R. R. Knowles, J. Am. Chem. Soc., 2023, 145, 11151–11160 CrossRef CAS.
-
(a) X. Jia, C. Qin, T. Friedberger, Z. Guan and Z. Huang, Sci. Adv., 2016, 2, e1501591 CrossRef PubMed;
(b) N. M. Wang, G. Strong, V. DaSilva, L. Gao, R. Huacuja, I. A. Konstantinov, M. S. Rosen, A. J. Nett, S. Ewart, R. Geyer, S. L. Scott and D. Guironnet, J. Am. Chem. Soc., 2022, 144, 18526–18531 CrossRef CAS;
(c) R. J. Conk, S. Hanna, J. X. Shi, J. Yang, N. R. Ciccia, L. Qi, B. J. Bloomer, S. Heuvel, T. Wills, J. Su, A. T. Bell and J. F. Hartwig, Science, 2022, 377, 1561–1566 CrossRef CAS;
(d) S. M. Parke, J. C. Lopez, S. Cui, A. M. LaPointe and G. W. Coates, Angew. Chem., Int. Ed., 2023, 62, e202301927 CrossRef CAS;
(e) A. Arroyave, S. Cui, J. C. Lopez, A. L. Kocen, A. M. LaPointe, M. Delferro and G. W. Coates, J. Am. Chem. Soc., 2022, 144, 23280–23285 CrossRef CAS PubMed;
(f) D. Guironnet and B. Peters, J. Phys. Chem. A, 2020, 124, 3935–3942 CrossRef PubMed;
(g) M. Zeng, Y.-H. Lee, G. Strong, A. M. LaPointe, A. L. Kocen, Z. Qu, G. W. Coates, S. L. Scott and M. M. Abu-Omar, ACS Sustainable Chem. Eng., 2021, 9, 13926–13936 CrossRef.
- M. Albrecht, Chem. Rev., 2010, 110, 576–623 CrossRef.
- F. Kakiuchi, T. Kochi and S. Murai, Synlett, 2014, 25, 2390–2414 CrossRef.
-
(a) M. Tobisu, K. Yamakawa, T. Shimasaki and N. Chatani, Chem. Commun., 2011, 47, 2946–2948 RSC;
(b) M. Tobisu and N. Chatani, Acc. Chem. Res., 2015, 48, 1717–1726 CrossRef;
(c) B. M. Rosen, K. W. Quasdorf, D. A. Wilson, N. Zhang, A.-M. Resmerita, N. K. Garg and V. Percec, Chem. Rev., 2011, 111, 1346–1416 CrossRef;
(d) J. Cornella, C. Zarate and R. Martin, Chem. Soc. Rev., 2014, 43, 8081–8097 RSC.
-
(a) Y. Jing, Y. Wang, S. Furukawa, J. Xia, C. Sun, M. J. Hülsey, H. Wang, Y. Guo, X. Liu and N. Yan, Angew. Chem., Int. Ed., 2021, 60, 5527–5535 CrossRef PubMed;
(b) B. Feng, Y. Jing, Y. Guo, X. Liu and Y. Wang, Green Chem., 2021, 23, 9640–9645 RSC.
- Y. Shimoyama and Y. Nakajima, ChemSusChem, 2023, 16, e202300684 CrossRef.
-
(a) Y. Minami, N. Matsuyama, Y. Takeichi, R. Watanabe, S. Mathew and Y. Nakajima, Commun. Chem., 2023, 6, 14 CrossRef;
(b) Y. Minami, Y. Inagaki, T. Tsuyuki, K. Sato and Y. Nakajima, JACS Au, 2023, 3, 2323–2332 CrossRef;
(c) Y. Minami, R. Honobe, Y. Inagaki, K. Sato and M. Yoshida, Polym. J., 2024, 56, 369–377 CrossRef;
(d) Y. Minami, S. Imamura, N. Matsuyama, Y. Nakajima and M. Yoshida, Commun. Chem., 2024, 7, 37 CrossRef.
-
(a) T. Yokozawa, Y. Suzuki and S. Hiraoka, J. Am. Chem. Soc., 2001, 123, 9902–9903 CrossRef;
(b) T. Yokozawa and A. Yokoyama, Chem. Rev., 2009, 109, 5595–5619 CrossRef PubMed.
- C. Vogel and J. Meier-Haack, Open J. Polym. Chem., 2012, 2, 1–5 CrossRef.
- H. M. van Dort, C. A. M. Hoefs, E. P. Magré, A. J. Schöpf and K. Yntema, Eur. Polym. J., 1968, 4, 275–287 CrossRef.
- K. L. Hull, W. Q. Anani and M. S. Sanford, J. Am. Chem. Soc., 2006, 128, 7134–7135 CrossRef.
- S. Tanaka, J. Sato and Y. Nakajima, Green Chem., 2021, 23, 9412–9416 RSC.
|
This journal is © The Royal Society of Chemistry 2024 |
Click here to see how this site uses Cookies. View our privacy policy here.