The effects of SO2 impurities on CO2 electroreduction on bare silver and SiO2 coated silver in different cell geometries†
Received
8th October 2024
, Accepted 7th January 2025
First published on 10th February 2025
Abstract
Electrochemical CO2 reduction presents an opportunity to transform waste flue gas with water and renewable electricity into chemicals or fuels. However, the energy-intensive nature of purification of flue gas underscores the appeal of directly utilizing the flue gas streams containing impurities. In this study, we investigate the impact of SO2 impurities on CO2 electroreduction in two electrochemical cell geometries: an H-cell and a membrane electrode assembly (MEA) cell. We observe distinctly different behavior of the Ag on carbon black (Ag/CB) catalyst under SO2 impurities in the H-cell compared to the MEA cell, where SO2 impurities exhibit a more pronounced effect on Ag/CB catalysts in the H-cell than in the MEA cell. This difference is attributed to the higher solubility of SO2 in the electrolyte compared to CO2, resulting in an accumulation effect and causing differences in the SO2 concentration near the electrode between the H-cell and the MEA system. By depositing a very thin SiO2 coating on the outermost surface of the Ag/CB catalyst using atomic layer deposition (ALD), the impact of SO2 on the catalyst's selectivity is diminished. This is attributed to the permeability difference between CO2 and SO2 through the SiO2 coatings and results in a local SO2 concentration difference between samples with and without SiO2 coatings.
Introduction
With the ongoing rise in global CO2 emissions, there is an urgent need to develop sustainable technologies for capturing and utilizing CO2. The electrochemical reduction of CO2 offers an appealing method for transforming surplus CO2, along with water and renewable electricity, into bulk chemicals that can be directly used in the process industry or as fuels, as depicted in Fig. 1. The electrochemical reduction of CO2 to CO is particularly intriguing as this is a two-electron reduction product, resulting in significant yields from each mole of electron transfer.1 Silver (Ag) is one of the best catalysts for the electroreduction of CO2 to CO because of its high selectivity for CO during CO2 reduction and its high stability over prolonged periods of operation.2–5 However, the Ag catalyst is susceptible to poisoning and subsequent loss of activity during the reaction due to the presence of impurities in the reactants.6–9 And the CO2 streams from industry often contain a variety of pollutants, and the CO2 concentration typically is relatively low, compared to the close to 100% for carbon capture from the air or from seawater (ranging from 3 to 45% from power plants and steel manufacturing factories).10 The anticipated costs of capturing CO2 from a biomass-fueled combustion power plant range from $150 to $400 per metric ton of CO2.11 Furthermore, purification expenses for this procedure are projected to be between $70 and $275 per metric ton of CO2.11 Despite the implementation of costly purification procedures, trace amounts of contaminants persist in the gas feed.12,13 Contaminants can pose a significant challenge to the long-term operation of Ag catalysts in industrial applications. Hence, it is crucial to study the CO2 reduction reaction (CO2RR) on Ag catalysts in the presence of varying concentrations of impurities. Furthermore, it is also important to develop strategies for protecting the catalysts from exposure to impurities and alleviating the poisoning issue.
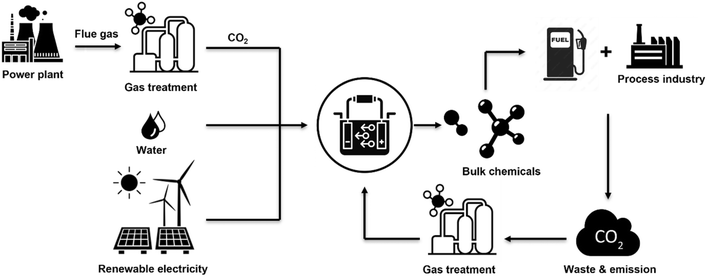 |
| Fig. 1 Schematic illustration of the concept for CO2 electroreduction in industry. | |
Unprocessed flue gas emissions contain various gaseous impurities, the concentration of each impurity significantly depends on the emission source and, hence, the type of industry. Typically, flue gas emitted from power plants contains impurities such as sulfur oxides (SOx), nitrogen oxides (NOx), oxygen, and volatile organic compounds (VOC).14,15 Hee Ko et al. have studied the impact of nitrogen oxides on electrochemical CO2RR.16 They used various NOx (including NO, NO2, and N2O) on Cu, Ag, and Sn catalysts in a flow cell and found that the presence of NOx (up to 0.83 vol%) in the CO2 feed results in a notable reduction in Faradaic efficiency (FE) during CO2 electroreduction. This reduction is attributed to the preferential electroreduction of NOx over CO2. However, despite the decrease in FE, when the pure CO2 feed is restored, the electrocatalyst maintains similar CO2 reduction capabilities. This indicates that the enduring impact of NOx on the catalytic performance of the modeled catalysts is negligible over the long term. Xu et al. found that when O2 impurities are present at typical concentrations (4 vol% of O2), most of the current was redirected from CO2RR towards the oxygen reduction reaction (ORR).17 This poses more serious issues when operating at elevated pressures. For example, 99% of the current was redirected to ORR at 15 bar. Van Daele et al. studied the stability of Ag and Bi2O3 catalysts with 198 ppm SO2 in CO2 and 213 ppm NO in CO2 over the course of 20 h.18 They found that the studied catalysts have a stable performance and high Faradaic efficiencies towards the target products over 20 h. Therefore, it seems that operating with 200 ppm of NO and SO2 in the gas feed will not have much effect on the catalyst during CO2RR. However, the presence of oxygen will significantly suppress the FE towards target products during CO2RR; with 1 vol% of O2 added to the stream, 23% of the FE towards CO2RR was lost. This likely is due to the fact that the oxygen impurity has a higher concentration than NO and SO2, and the preferential reduction of O2 compared to CO2 during the reaction. Albertini et al. found that using a passivation layer such as metallic oxides coatings can preserve catalyst's activity and improve its stability for CO2 reduction.19 Based on the aforementioned reports, we may infer that the impurities primarily affect the CO2RR through competing reactions, rather than the poisoning effects that will lead to a long-term influence on the catalysts. Moreover, these studies are all carried out in flow cell reactors, while an H-cell system may give additional insights, as it can provide additional perspectives into the intrinsic properties of the catalyst by decoupling some of the complexities introduced in flow cells.
The objective of this paper is to determine the effect of SO2 impurities on the Ag catalyst for the electrochemical reduction of CO2 in two different cell geometries: an H-cell and a membrane electrode assembly (MEA) cell. We select SO2 as the impurity for this study since it is found in most flue gases and sulfur has a pronounced poisoning effect on Ag catalysts.7–9 We find that SO2 has a more pronounced impact on Ag on carbon black (Ag/CB) catalysts in the H-cell compared to in the MEA reactor. This is attributed to the higher solubility of SO2 in the electrolyte compared to CO2, leading to an accumulation effect in the H-cell. This causes a higher SO2 concentration near the electrode surface in the H-cell system than in the MEA reactor system. We use thermal atomic layer deposition (ALD) to deposit SiO2 on Ag/CB catalyst to protect it from SO2 impurities. ALD is a gas phase coating technique based on the alternating use of two reactants, depositing a thin film on a substrate. It provides sub-nanometer precision in coating thickness, controlled by the number of deposition cycles.20 After applying 2 to 8 cycles of SiO2 ALD providing a nanocoating on the outer surface of the Ag/CB catalyst, the effect of SO2 on the selectivity of the catalyst is diminished at less negative potentials. This is attributed to the permeability difference between CO2 and SO2 through SiO2 coatings.
Experimental
Materials
Silicon tetrachloride (SiCl4, 99%) and iridium oxide (IrO2) were purchased from Alfa Aesar, isopropanol (≥98%) was purchased from Honeywell, Nafion™ perfluorinated resin solution (5 wt% in lower aliphatic alcohols and 15–20% water) was purchased from Sigma-Aldrich. Deionized water with a resistivity of 18 MΩ cm was used as the co-reactant for ALD. 20 wt% of Ag on Carbon black-Vulcan XC 72R catalyst, Carbon Black Vulcan XC 72R, and Sigracet 39BB carbon paper gas diffusion layers (GDL) pretreated with PTFE in microporous layer were purchased from FuelCell store. Glassy carbon plates were ordered from HTW Hochtemperatur-Werkstoffe GmbH (Germany). The electrolyte solution was prepared from ultrapure water (Milli-Q IQ 7000, 18.2 MΩ cm). PiperION® anion exchange membrane, 20 microns, was purchased from FuelCell store and submerged in the electrolyte overnight prior to MEA experiments. Potassium bicarbonate (KHCO3, 99.95%) was purchased from Sigma-Aldrich. Anion exchange membrane (Selemion AMV) was purchased from AGC Engineering and kept in deionized water after receiving, and used for H-cell experiments. Ag nanopowder with a particle size from 20–40 nm and without oxide layer was purchased from Thermo Fisher Scientific. All chemicals were received and used without further purification.
Electrode preparation
Electrodes used in H-cell experiments. The Ag/CB catalyst was first drop casted on the glassy carbon electrode before the ALD coating. The catalyst ink was prepared by combining 4 mg of catalyst with 800 μL of deionized water, 180 μL of isopropanol, and 20 μL of Nafion perfluorinated resin solution in a vial. The mixture was then sonicated in an ice bath for 1 hour. Following this, 25 μL of the catalyst ink was drop-cast onto the surface of the glassy carbon electrode each time and this process was repeated four times to achieve a homogeneous deposition on the electrode. The SiO2 coatings on the catalyst were then deposited in a custom-built flat substrate ALD reactor20–22 operating at atmospheric pressure. The reactor chamber comprises a metal cylinder with an inner diameter of 40 mm and a length of 190 mm, accompanied by a substrate holder with dimensions of 30 mm by 125 mm. To ensure a uniform temperature profile, the deposition temperature was monitored and regulated using two thermocouples positioned inside and outside the ALD reactor. We opted for atmospheric pressure ALD over vacuum ALD as it reduces investment costs and enhances throughput at a larger scale.21,22 Our SiO2 deposition process was adapted from literature,23 but the reaction time and precursor gas flow rate were adjusted based on our own requirements and still under the saturation conditions.24 In summary, the SiCl4 and H2O, the ALD reactants, were filled in stainless steel bubblers and kept at room temperature. Nitrogen gas, with a purity of 99.999%, served as both carrier and purging gas, flowing at a rate of 0.5 L min−1 throughout the process, parallel to the substrate surface in the reactor. Before each experiment, samples underwent air plasma pre-treatment at room temperature and 4 mbar pressure for 60 seconds using a Harrick plasma machine. The ALD reactor was heated to and maintained at 100 °C throughout the process. SiCl4 was introduced into the reactor for 15 second pulses, followed by 60 second purging with N2 and 30 second dosing of H2O vapor. A final 60 second purging with N2 completed one ALD cycle. Detailed SiO2 ALD operation conditions are available in Table S1.† Samples with varying numbers of ALD cycles were obtained by repeating the ALD cycles as needed. Upon completion of the synthesis process, the reactor was purged with N2 flow for 15 minutes and cooled to room temperature.
Electrodes used in MEA experiments. The catalyst used during the MEA experiments was synthesized using a vibrated fluidized bed reactor25–27 operating at atmospheric pressure. A vibrating table was used at a frequency of 60 Hz to fluidize the powders and create uniform fluidization inside the reactor during the reaction. A glass column with an inner diameter of 2.5 cm was used as the reactor. 0.5 g of Ag/CB catalyst (pre-dried at 80 °C for 3 hours before the experiment, to remove the moisture) was used for each synthesis batch in the reactor. The SiCl4 and H2O, the ALD reactants, were filled in stainless steel bubblers and kept at room temperature. Nitrogen gas, with a purity of 99.999%, served as both carrier and purging gas throughout the reaction. A compensation N2 stream with a flow rate of 1.5 L min−1 was employed during the SiCl4 dosing period to maintain an equal gas flow of 2 L min−1 throughout the whole ALD process and keep the fluidization of the powders inside the reactor. The ALD reactor was heated to and maintained at 100 °C throughout the process. SiCl4 was introduced into the reactor for 60 second pulses, followed by 150 second purging with N2 and 60 second dosing of H2O vapor. A final 150 second purging with N2 completed one ALD cycle. By repeating the same ALD cycles for 4 times, 4 cycles coated sample was achieved. After the synthesis procedure, the fluidized bed reactor was purged for 15 minutes with N2 flow to remove the residual reactants. Detailed SiO2 ALD operation conditions were shown in Table S1.† The 4 cycles SiO2 coated Ag/CB powders synthesized using the aforementioned method was utilized to prepare the ink that can be airbrushed on the GDL for the MEA experiments. The ink formula is very similar to the previously mentioned ink formula used for the H-cell experiments. In general, 4 mg of catalyst with 800 μL of isopropanol, 180 μL of deionized water, and 20 μL of Nafion perfluorinated resin solution were mixed in a vial. The mixture was then sonicated in an ice bath for 1 hour. After that, the ink solution was airbrushed onto the GDL using an airbrush gun and N2 flow to reach a catalyst loading of 0.2 mg cm−1.
Gas mixing steps for SO2 impurities experiments. A gas mixing apparatus (Environics® Series 4000) was employed to mix the feed gas and ensure precise control over gas proportions for the electrochemical tests. To protect against the potential corrosion induced by SO2, a precautionary measure was taken by coating the mass flow controllers and gas tubing within the testing system with SilcoNert® and sealing them with Kalrez®. The generation of varied concentrations of SO2 gas was achieved by using two standard gas cylinders containing SO2 with concentrations of 100 ppm and 10
000 ppm, balanced with CO2 from Linde Gas. The pure CO2 gas used in the experiments was also from Linde Gas with a purity of 99.999%. Detailed information regarding the gas recipes used for the electrochemical tests can be found in Table S2.†
Material characterization. X-ray photoelectron spectroscopy (XPS) analyses were conducted utilizing the Thermo Scientific™ K-alpha™ instrument from ThermoFisher™ Scientific. The instrument employed monochromatic X-ray beams of aluminum Kα radiation (1486.7 eV) with a spot size of 400 μm. For the survey scans, a pass energy of 200 eV and a step size of 1 eV were employed, while higher-resolution spectra were obtained using a pass energy of 50 eV and a step size of 0.1 eV. All peak positions were analyzed and calibrated with reference to the aliphatic C 1s peak at 284.8 eV, utilizing CasaXPS software.XPS area scan was performed with a Thermo Scientific™ K-alpha™ (ThermoFisher™ Scientific) utilizing a monochromatic X-ray of aluminum Kα radiation (1486.7 eV) and a circular area was chosen with a diameter of 12 mm. 121 points were selected and evenly distributed within the circular area. A pass energy of 153 eV and a dwell time of 0.5 s were used. The data was analyzed and plotted using the Avantage software.
Electrochemical measurements
Electrochemical measurements in H-cell. The electrochemical measurements were conducted using a H-cell setup.28 A leak-free Ag/AgCl reference electrode (sat. KCl) was employed, alongside a counter electrode consisting of IrO2-coated glassy carbon electrode. All potentials employed in this study were adjusted to the RHE scale using the following equation:29
ERHE = EAg/AgCl + 0.197 + 0.059 × pH |
A 0.1 M solution of KHCO3 served as the electrolyte in both chambers, and each chamber contains 1.8 mL of electrolyte. An anion-exchange membrane, Selemion AMV, was utilized to separate the anode and cathode chambers of the H-cell. Electrochemical measurements were conducted using a Biologic SP-200 potentiostat. Potentiostatic electrochemical impedance spectroscopy was utilized to evaluate the ohmic loss of the cell and was compensated for each experiment. Chronoamperometric measurements were carried out at different applied potentials from −0.8 to −1.2 V vs. RHE and were used to determine the FE of the catalysts. Before each experiment, the cathode electrolyte was purged with feeding gas for 15 minutes. The gas products were analyzed by an in-line gas chromatography (GC) (Compact GC4.0, Global Analyzer Solutions). Every 2 minutes the products were analyzed by the GC for quantification. The gas flow rate used during the experiments was kept at 8 sccm for every tests.
Electrochemical measurements in MEA. The electrochemical measurements were conducted using a MEA reactor purchased from Dioxide Materials. It is a 5 cm2 CO2 MEA electrolyzer cell coupled with a stainless steel flowfield plate with a serpentine channel in contact with the cathode GDE and a titanium flowfield plate with a serpentine channel in contact with the anode GDE. The reactor was assembled with 2 N*m Torque to ensure a leak-free assembly. The working electrode was prepared using the aforementioned method. The counter electrode was an IrO2 airbrushed GDE. The anion-exchange membrane used in the MEA was a PiperION® anion exchange membrane. 40 ml of 1 M KHCO3 solution was used and circulated with a flow rate of 5 ml min−1 in the anode serpentine channel. Use of 0.1 M KHCO3 electrolyte in H-cell configurations and 1 M KHCO3 electrolyte in MEA configurations are widely reported in the literature and facilitates comparisons across different studies. Employing 0.1 M KHCO3 electrolyte in the MEA configuration can result in a very high Faradaic efficiency toward H2 and a significantly low FE toward CO, thereby diminishing its relevance for CO2 reduction studies. Chronopotentiometry measurements were carried out at different current densities and were used to determine the FE of the catalysts. The current density was calculated by dividing the applied current by the geometric area of the working electrode. CV measurements were carried out from 0.2 V to −1.0 V at a scan rate of 10 mV s−1. The gas products were analyzed using the same in-line GC as described in the H-cell experiments; the gas flow rate used during the experiments was 20 sccm for every test.
Results and discussion
SO2 impurities effects on CO2 electroreduction in H-cell reactor
We first examined the effect of SO2 impurities on the Ag/CB catalyst for CO2 electroreduction in the H-cell system. A series of Ag/CB samples coated with SiO2 were synthesized using ALD with a flat substrate reactor and compared with an uncoated Ag/CB sample. As demonstrated in our previous study,30 thick SiO2 coatings can reduce the catalyst activity. Therefore, in this study, we limited the deposition to a maximum of 8 cycles to avoid compromising catalyst performance. Based on the reported growth per cycle of SiO2 using SiCl4 under the experimental conditions, which is approximately 2 Å per cycle,31,32 a very thin SiO2 layer ranging from 0.4 nm to 1.6 nm is anticipated after 2 to 8 cycles of ALD coating. To determine the actual Ag weight percentage in the original Ag/CB nanoparticles, the sample underwent characterization through thermogravimetry differential thermal analysis (TG/DTA). The TG/DTA analysis (Fig. S1†) showed that roughly 22 wt% of Ag2O residues were present after the analysis and revealed approximately 20 wt% of Ag in the original Ag/CB samples, and this number matches the metal loading specified in the documentation from the supplier. The rate of SiO2 deposition was characterized via X-ray photoelectron spectroscopy (XPS), with Fig. S2† illustrating a monotonic increase in Si atomic percentage with the number of ALD cycles. High-resolution Si 2p spectra indicated that the Si in the coated samples predominantly exists in the SiO2 state, which can be deconvoluted into Si 2p3/2 and Si 2p1/2 peaks. This demonstrated successful SiO2 deposition on the surface of Ag/CB samples, with the Si content increasing proportionally with the number of coating cycles.
The stability of the original Ag/CB catalyst was assessed in an H-cell at −1.0 V vs. RHE over a 20 hour period. Fig. 2 shows that the Faradaic efficiency (FE) of the original Ag/CB catalyst towards CO remained relatively constant at around 70% throughout the 20 hour test, with minor fluctuations. The total Faradaic efficiency falling below 100% can be attributed to incomplete product detection and electron losses resulting from parasitic processes, such as electrode corrosion and catalyst degradation. This underscores the stability of the original Ag/CB catalyst in H-cell environments, consistent with previous research, indicating the robustness of Ag catalysts under similar testing conditions.2–5 Notably, the Ag catalyst exhibited no significant deterioration in performance under neutral pH conditions. However, the selectivity of the original Ag catalyst was found to be lower than that reported in some papers.2,33,34 To further investigate the selectivity of the Ag catalyst, we also evaluated pure Ag nanoparticles drop-casted onto a glassy carbon electrode while maintaining consistent metal loading (80 μg cm−2) with our Ag/CB catalyst. As depicted in Fig. S3,† an optimal FECO of the pure Ag nanoparticles was achieved at −0.8 V vs. RHE, with a similar selectivity towards CO of around 70%. Upon mixing the Ag nanoparticles with carbon black to mimic our Ag/CB catalyst while keep the same Ag loading on the electrode, we observed that the optimal FE was achieved at −1.0 V vs. RHE, demonstrating a FECO of approximately 72%. This indicated that the low FE of the Ag catalyst was not inherent to the catalyst itself but was more associated with the used H-cell configuration. In the H-cell configuration, the availability of CO2 in the cathode compartment was restricted due to the low solubility of CO2 in the electrolyte. The low solubility of CO2 resulted in a low concentration of CO2 in the vicinity of the electrode. When the CO2 concentration near the cathode is insufficient, the FECO decreases. CO2 must then diffuse through the electrolyte to reach the cathode, and in the H-cell configuration, this diffusion is hindered by the distance between the CO2 source (e.g., the gas phase or CO2 inlet) and the cathode. The slower diffusion rate can lead to localized CO2 depletion at the electrode, further restricting CO2 reduction efficiency. Mass transfer, including the movement of CO2 to the electrode, is also limited in the H-cell configuration due to the static nature of the electrolyte and the lack of continuous flow. These limitations were more serious under high current densities, as these conditions require a higher amount of CO2 supply. Consequently, CO2 reduction in the H-cell was less efficient, resulting in lower FE towards CO. While the partial current density of the Ag nanoparticles with or without mixing with carbon black towards CO appeared comparable at all three potentials, there was a notable disparity in the H2 partial current density between the Ag nanoparticles drop casted directly on the glassy carbon electrode and those mixed with carbon black. The Ag nanoparticles mixed with carbon black consistently exhibited a lower H2 partial current density at all three potentials. We hypothesize that part of the Ag is buried beneath the carbon particles. This means that the CO2 consumption during CO2 reduction will be lower with these samples. Therefore, the samples with carbon black will have a relatively higher CO2 concentration near the electrode, which suppresses the hydrogen evolution activity.
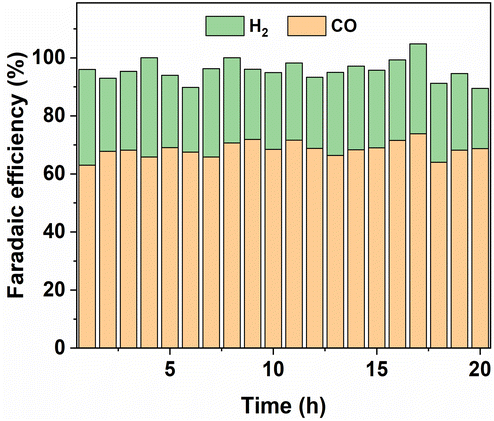 |
| Fig. 2 Faradaic efficiency toward H2 and CO of the uncoated Ag/CB catalyst during 20 h H-cell testing at −1.0 V vs. RHE using a pure CO2 gas feed and a 0.1 M KHCO3 electrolyte. | |
SO2 concentrations of 10 ppm, 100 ppm, and 1000 ppm were tested in this study, considering that the majority of flue gas emissions from power plants typically fall within an SO2 concentration range from 100 to 400 ppm.18 The gas compositions employed for the SO2 impurity experiments are listed in Table S2.† Three different CO2 gas cylinders containing 0, 100, and 10
000 ppm SO2 were utilized, and a gas mixer was employed to ensure thorough mixing of various gas streams to achieve a homogeneous gas stream flowing into the H-cell cathode chamber. The original Ag/CB catalyst (i.e., 0 cycles) and catalysts with 2, 4 and 8 cycles of SiO2 ALD coating were tested at three potentials using chronoamperometry (CA) under different gas feed compositions. As is seen from Fig. 3, the catalyst performance was first benchmarked with a pure CO2 feed and a similar selectivity toward CO was observed with and without SiO2 coating, reaching the highest FECO of 70% at −1.0 V vs. RHE. Nevertheless, when SO2 impurities were introduced into the gas stream, the FECO of the uncoated Ag/CB catalyst showed a significant decrease. A decrease in FECO to 57% with 10 ppm SO2 and 56% with 100 ppm SO2, at −1.0 V vs. RHE was observed. At the highest SO2 concentration (1000 ppm), the FECO decreased by 23%, 24%, and 14% at −0.8 V vs. RHE, −1.0 V vs. RHE, and −1.2 V vs. RHE, respectively. The SO2 poisoning effect on the Ag catalyst appears to be potential dependent, with a greater impact observed at lower potentials. This is expected due to the more favorable reduction of SO2 over CO2, since SO2 reduction has a significantly less negative reduction potential compared to CO2 reduction.35 We have conducted cyclic voltammetry tests under various gas supplies, including pure Ar, CO2 with 1000 ppm SO2 and pure CO2 to verify the CO2 reduction potential and the SO2 reduction potential. However, as shown in Fig. S4,† no distinct SO2 reduction peak was observed. This indicates that SO2 reduction occurs within a potential window similar to that of CO2 reduction and hydrogen evolution. When we calculate the loss in FECO and attribute it to SO2 reduction, we find that approximately 50 ppm SO2 is required to account for the missing FE when 1000 ppm SO2 is introduced at −0.8 V vs. RHE. This suggests that there is sufficient SO2 in the gas stream during the reaction for the indicated SO2 reduction (detailed calculation method can be found in ESI,† method to calculate the SO2 concentration required to get SO2 reduction section). Additionally, the potential poisoning of the Ag/CB catalyst during the reaction can also contribute to the performance degradation when SO2 is introduced to the gas stream, as we detected the formation of Ag2S species on the surface of the catalyst after the reaction, as shown in Fig. 4. Although the exact mechanism of the Ag2S formation process is unclear and remains an objective for future study. All of these factors combined together contribute to the decrease in FECO for the CO2 electrolysis. The decrease in CO selectivity of the Ag/CB catalyst at a high concentration of SO2 impurities was more pronounced at less negative potential (−0.8 V vs. RHE) compared to more negative potential (−1.2 V vs. RHE) indicating that the competition between SO2 reduction and CO2 reduction is potential dependent. SO2 reduction is more favored compared to CO2 reduction at less negative potentials. As the potential becomes more negative, the effectiveness of CO2 reduction increases, with the loss in FECO decreasing. The Ag/CB catalysts protected with 2–8 ALD cycles of SiO2 coating were much less affected by the SO2 contaminant. At −0.8 V vs. RHE, the FECO of the uncoated Ag/CB catalyst was 52%, 47%, and 39% with 10 ppm SO2, 100 ppm SO2, and 1000 ppm SO2, respectively. After applying 2 cycles of SiO2 coating on the surface of the catalyst, the FECO improved to 54%, 51%, and 50%, respectively. When we further increased the coating cycles to 4 cycles, the FECO of the ALD coated catalyst increased to 62%, 65%, and 66%. After 8 cycles of SiO2 coating, the FECO reached 62%, 62%, and 67%. The SiO2 coating thereby effectively reduced the SO2 poisoning effect on the Ag catalyst. When the applied potential became more negative, the SO2 effects on Ag catalyst decreased, and the coating effectiveness decreased as well. The FECO of the uncoated Ag/CB catalyst at −1.2 V vs. RHE was 50%, 43%, and 41% under 10 ppm SO2, 100 ppm SO2, and 1000 ppm SO2, respectively. After 2 cycles of coating, the FECO improved to 51%, 48%, and 46%. And after 4 cycles coating, it increased to 48%, 53%, and 52%. With 8 cycles coating, the FECO improved to 49%, 54%, and 50%. The decreased FECO, especially for the uncoated and 2 cycles coated samples under SO2 impurity, can likely be attributed to the SO2 reduction and the poisoning of the catalysts. However, due to the high solubility of the sulfur-containing anions in the electrolyte and its cross-over through the anion-exchange membrane to the anolyte, we cannot accurately detect the SO2 reduction products and quantify their Faradaic efficiency.
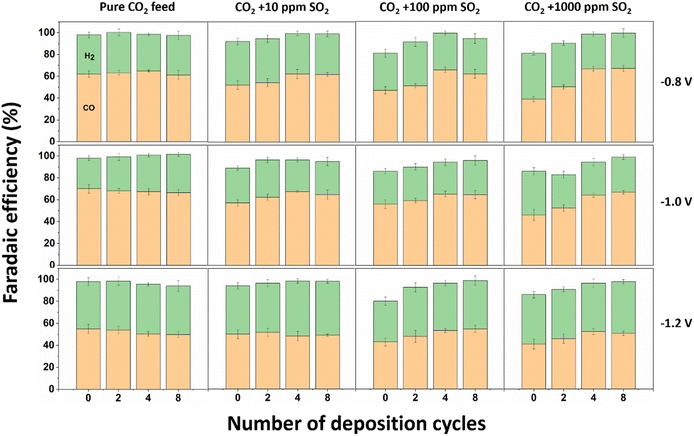 |
| Fig. 3 Faradaic efficiency of the Ag/CB catalyst with or without SiO2 coating during 1 h H-cell CA testing in a 0.1 M KHCO3 electrolyte at 3 potentials using CO2 gas feed with different concentrations of SO2 impurities. The data was collected from two independent measurements and the error bars represent the arithmetic mean. | |
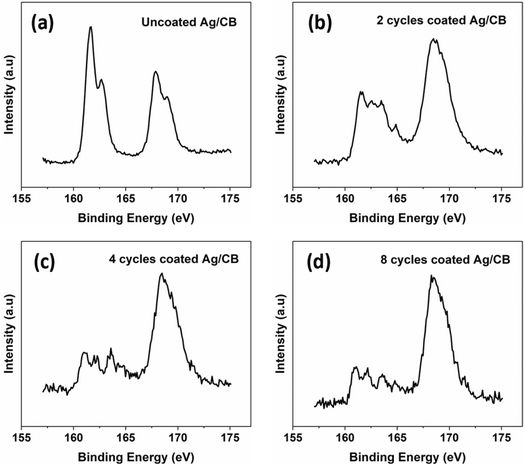 |
| Fig. 4 S 2p XPS spectrum of the Ag/CB catalyst after CO2 electrolysis with 1000 ppm SO2. (a) Ag/CB catalyst without SiO2 coating. (b) Ag/CB catalyst with 2 cycles SiO2 coating. (c) Ag/CB catalyst with 4 cycles SiO2 coating. (d) Ag/CB catalyst with 8 cycles SiO2 coating, tested at H-cell at −1.0 V vs. RHE. | |
Fig. 4 presents the XPS characterization of the Ag/CB catalyst without and with SiO2 coating following a 1 hour CA test at −1.0 V vs. RHE with 1000 ppm SO2. In all samples, an intense peak at 168.7 eV was observed in the S 2p spectrum, attributed to the sulfur-containing functional groups within the Nafion binder utilized for drop-casting the catalyst on the surface of the glassy carbon electrode, and serving as the ionomer in the catalyst. Peaks at 161.1 eV and 162.2 eV are attributed to silver sulfide (Ag2S) formation during the reaction.36 Notably, the intensity of the Ag2S peaks was notably higher in the uncoated catalyst. Upon applying 2–8 cycles of SiO2 coating, a decrease in the intensity of the Ag2S peak was observed, suggesting that SiO2 coating mitigated Ag2S formation during the reaction under high concentrations of SO2 (1000 ppm SO2) gas feed. An XPS area scan was conducted after 1 h CO2 electrolysis at −1.0 V vs. RHE with 2 kinds of gas feed. Fig. S5† shows that the uncoated Ag/CB catalyst after 1 h CO2 electrolysis with pure CO2 gas feed only has a low intensity of S peak on the electrode. For a gas feed of CO2 with 1000 ppm SO2, the uncoated Ag/CB catalyst shows a much stronger S peak on the electrode. Nevertheless, for the catalyst treated with 8 cycles of SiO2 coating, the S peak is significantly decreased on the electrode after CO2 electrolysis with 1000 ppm SO2.
In summary, we found that the Ag/CB catalyst was significantly affected by SO2 impurities in the H-cell geometry, especially for a high SO2 concentration and at a less negative potential. The SiO2 coating can be used to protect the Ag/CB catalyst from SO2 impurities and maintain the catalyst selectivity for all investigated potentials.
SO2 and CO2 permeability differences through SiO2 coating
To further illustrate the protection mechanism of SiO2 on Ag/CB catalysts against SO2 impurities, we investigated the permeability differences of SO2 and CO2 through SiO2 coatings based on existing papers. Mohd Nor et al. found that CO2 has high permeability through SiO2 modified polymer matrix membranes.37 After adding 5 wt% of SiO2 nanoparticles to the polymer matrix membranes (ENR/PVC), the CO2 gas permeability increased to approximately 6 times higher than the original membranes without SiO2 modification. Wahab et al. also found a similar phenomenon.38 They reported that CO2 gas exhibits strong interaction with SiO2 due to the presence of hydroxyl functional groups (–OH) on the SiO2 particles. This interaction enhances the solubility of CO2 within the membrane, thereby improving CO2 diffusivity and resulting in high permeability of CO2 through SiO2 filled fiber mixed matrix membrane. Meng et al. tested that the organic–inorganic hybrid SiO2 membranes exhibited a high O2 permeance that was 2.87 × 10−8 mol m−2 s−1 Pa−1 and a poor SO2 permeance of 3.9 × 10−9 mol m−2 s−1 Pa−1.39 The O2 permeance was 7.4 times higher than the SO2 permeance through the membranes. This indicates that the SO2 permeability through this organic–inorganic hybrid SiO2 membranes is very low. Yoshiura et al. also found that the 3,3,3-trifluoropropyltrimethoxysilane derived SiO2 membranes have very high SO42− ions rejection rates.40 The NaSO4 and MgSO4 rejection percentage after the liquid permeation tests was 91.0% and 98.2%, respectively. This is attributed to the dissociation of the –OH groups on the silica surface during testing and produce a negatively charged surface. The SiO2 coating on the Ag/CB catalyst was negatively charged during CO2RR as well. Hence, it can also have a repulsive effect on SO2 derived ions. Yu et al. discovered that silica–zirconia membranes with a high Si/Zr molar ratio (Si/Zr = 7/3) exhibit excellent resistance to SO3 and demonstrate gas separation of O2/SO3 selectivity ranging from 13 to 10, surpassing the Knudsen selectivity of 1.58.41 This suggests promising potential for their application in O2/SO3 separation processes and indicates that O2 has more than 10 times higher permeability through silica–zirconia membranes with a high Si/Zr molar ratio compared to SO3. Based on the preceding discussion, it can be inferred that there is a notable difference in the permeability of CO2 and SO2 through SiO2, with CO2 showing significantly higher permeability compared to SO2 or SO2 derived ions present in the electrolyte. The variation in permeability between CO2 and SO2 indicates that the concentrations of these gases outside and inside the SiO2 coating, which directly interact with the Ag/CB catalyst, are also likely to differ. The lower SO2 concentration on the inside of the coating may account for the observation that after applying 2–8 cycles of SiO2 coating, the formation of Ag2S on the electrode surface is considerably less than without SiO2 coating after CO2 electrolysis with 1000 ppm SO2 feed at −1.0 V vs. RHE. It also explains why SO2 has much less effect on the catalyst's selectivity after it has been coated with SiO2 films. The SO2 concentration near the electrode surface decreases, so the competition between the SO2 reduction and CO2 reduction is reduced, and the potential poisoning of the Ag/CB catalyst is minimized.
SO2 impurities effects on CO2 electroreduction in MEA reactor
Based on the findings from our investigation using the H-cell, we proceeded to evaluate the performance of SiO2 coated Ag/CB samples in a MEA reactor, a widely utilized flow cell structure in the field of CO2 reduction, to understand their behavior in the flow cell system. Given that the current density in the H-cell is relatively low and cannot meet industrially relevant requirements, assessing the SiO2 coated Ag/CB catalyst in a flow cell geometry such as a MEA is needed.
We applied 4 cycles of SiO2 coating on Ag/CB powders using a fluidized bed ALD reactor. This is different from the samples used in H-cell tests, in which we used a flat substrate ALD reactor and only coated the very outermost surface of the Ag/CB catalyst on the glassy carbon electrode. For these experiments, we fluidized the Ag/CB powder in a dedicated ALD reactor and coated the entire surface of the Ag/CB particles. The coated Ag/CB catalyst was airbrushed on the gas diffusion electrode and assembled in the MEA electrolyzer for the electrochemistry tests. The uncoated Ag/CB catalyst tested in MEA showed a FECO of 79% at 100 mA cm−2 with a pure CO2 gas feed (as shown in Fig. 5a). When the gas feed shifted to CO2 with 1000 ppm SO2, the FECO did not decrease significantly as in the experiments in the H-cell, but remained at a FECO of 75%. When the Ag/CB catalyst was coated with 4 cycles of SiO2, we observed that the catalyst's selectivity was inhibited to some extent. The 4 cycles SiO2 coated sample showed a FECO of 70% with pure CO2 feed, and a FECO of 71% when the gas feed was changed to CO2 combined with 1000 ppm SO2. The slight inhibition effect of the coating may stem from the SiO2 coating forming connections between catalyst particles, which could hinder electrical conductivity and ionic charge transfer between the membrane and the bulk catalyst. The water transport within the bulk catalyst might also be influenced by the SiO2 coating. All of these factors can collectively affect the catalyst's selectivity in the MEA configuration. Fig. S6† shows that the CV scan of the uncoated Ag/CB catalyst and the catalyst with 4 cycles of SiO2 coating do not have notable differences. The oxidation and reduction peaks of Ag are well defined with 4 cycles of SiO2 coating and nearly coincide with the catalyst without coating. This indicates that the obstruction caused by the SiO2 coating on the catalyst's outmost surface active sites is minimal. Fig. 5b and c shows the chronopotentiometry (CP) results of the Ag/CB catalyst tested at 100 mA cm−2. It indicates that adding 1000 ppm SO2 to the feeding gas does not change the cell potential under the same current density. Applying an SiO2 coating also did not alter the cell potential for the same current density. The XPS characterization of the catalyst before and after CO2 electrolysis with or without SO2 impurities are shown in Fig. 6. From the figure we observe that peaks at 161.1 eV and 162.2 eV, which are attributed to Ag2S, are present in all samples, even with pure CO2 feed. This is likely due to the higher Nafion loading on the GDE (218.5 μg cm−2) compared to the H-cell electrode (87.4 μg cm−2), and more importantly, the higher current density in MEA caused more reduction of sulfonic acid (–SO3H) groups in the Nafion binder during CO2 electrolysis. We can observe that the Ag2S peak becomes stronger after shifting the feed gas from pure CO2 to CO2 combined with 1000 ppm SO2 for the catalyst without SiO2 coating. Nevertheless, for the catalyst coated with 4 cycles of SiO2, the Ag2S peak remains almost identical with or without 1000 ppm SO2 in the feed gas stream. This suggests that inhibition of SO2 penetration by SiO2 is also present in the MEA experiments.
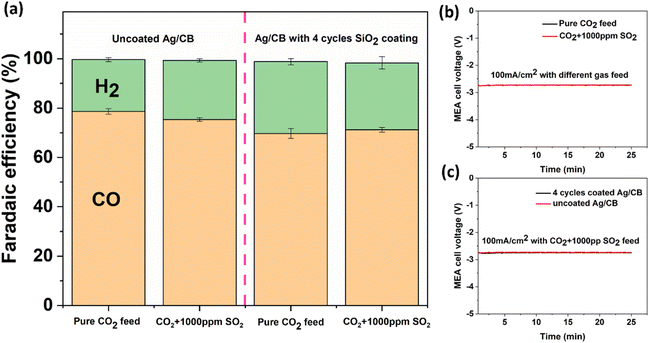 |
| Fig. 5 (a) Faradaic efficiency of the Ag/CB catalyst with or without SiO2 coating tested at MEA reactor at 100 mA cm−2 current density in a 1 M KHCO3 electrolyte with pure CO2 feed or CO2 mixed with 1000 ppm SO2. The data was collected from two independent measurements and the error bars represent the arithmetic mean. (b) CP testing of the Ag/CB catalyst at MEA reactor. Original Ag/CB catalyst tested with pure CO2 or CO2 with 1000 ppm SO2 impurities at 100 mA cm−2 current density. (c) CP testing of the Ag/CB catalyst at MEA reactor. Ag/CB catalyst with or without 4 cycles of SiO2 coating tested using CO2 with 1000 ppm SO2 impurities as gas feed at 100 mA cm−2 current density. | |
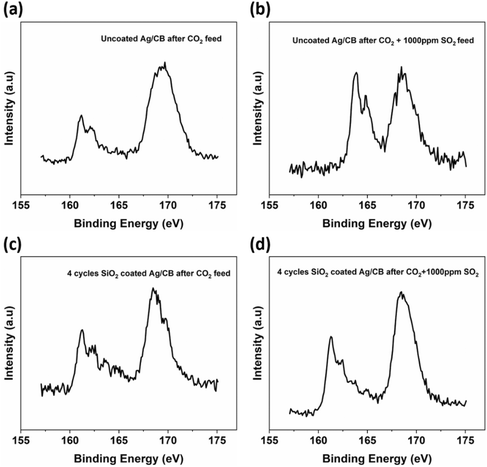 |
| Fig. 6 S 2p XPS spectrum of the Ag/CB catalyst after CO2 electrolysis tested at MEA reactor at 100 mA cm−2. (a) Ag/CB catalyst tested with CO2 feed. (b) Ag/CB catalyst tested with CO2 + 1000 ppm SO2 feed. (c) Ag/CB catalyst with 4 cycles SiO2 coating tested with CO2 feed. (d) Ag/CB catalyst with 4 cycles SiO2 coating tested with CO2 + 1000 ppm SO2 feed. | |
SO2 impurities in the CO2 feed had a stronger influence on Ag/CB catalysts within the H-cell system than in the MEA reactor under the conditions used here. We attribute this difference in behaviour to the higher solubility of SO2 in the liquid electrolyte compared to CO2, resulting in an accumulation of SO2 in the batchwise operated H-cell, but not in the MEA flow cell configuration. A visual representation of both cell geometries is provided in Fig. S7.† The solubility of CO2 in water at 20 °C is 1.7 g L−1. Under the same conditions, the solubility of SO2 is 110 g L−1, nearly 65 times higher than that of CO2 in the electrolyte. This will lead to a continuous increase of SO2 concentration in the electrolyte within the H-cell during the experiments until it reaches saturation. However, due to the high solubility of SO2 in the electrolyte and the relatively low concentration of SO2 in the feed gas stream, even with the highest concentration of SO2 used in the experiments (CO2 with 1000 ppm SO2, which means 0.1 vol% of SO2 in the CO2 stream), it would require 6.6 days of continuous dosing to reach SO2 saturation in the electrolyte. This implies that the electrolyte will never reach saturation during the H-cell experiments and the SO2 concentration in the electrolyte will keep on increasing during the experiments. Consequently, the SO2 concentration near the surface of the electrode will be much higher than in the feed gas for the H-cell experiments. On the contrary, in the MEA reactor geometry, the cathode is in direct contact with the feed gas, without the presence of electrolyte in the cathode serpentine channel. Therefore, the SO2 concentration near the cathode in the MEA system is the same as in the feed gas, which is much lower than the concentration near the cathode in the H-cell system with the same feed gas composition. This explains why the Ag/CB catalyst in the MEA system is not significantly affected by SO2 impurities and it shows that the Ag/CB catalyst can maintain its performance with 1000 ppm SO2 impurities in the MEA system within our 25 minutes testing timeframe. The long-term stability of the Ag/CB catalyst in the MEA reactor under SO2 impurities is worth investigating as well. However, after 50 minutes of CP testing, we encountered significant salt precipitation in the MEA system, resulting in a subsequent decrease in Faradaic efficiency. The first 18 minutes serve as a stabilization period, during which the reaction products are transferred to the GC. During this period, the Faradaic efficiency for both H2 and CO is lower than expected. Additionally, the FECO started to decrease after 35 minutes during CP testing with pure CO2 gas feed at 100 mA cm−2, as shown in Fig. S8.† Very obvious KHCO3 salt precipitation can be seen on the cathode serpentine channel and gas diffusion electrode after 50 minutes CP testing (as shown in Fig. S9†). Nevertheless, the cell potential was relatively stable during 50 minutes CP testing, as can be seen in Fig. S10.† The minor fluctuation was due to the gas chromatography (GC) injection during the CP testing. Salt precipitation issues prevented us from further investigating the stability of Ag/CB catalyst in the MEA system, especially in the presence of SO2 impurities. Therefore, this research question awaits further investigation in subsequent studies.
Conclusions
We have explored the performance of the Ag/CB catalyst under SO2 impurities for CO2 electrolysis in two electrochemical cell geometries: an H-cell and a MEA cell. Both systems behave differently with respect to SO2 contamination in the CO2 feed. The impact of SO2 on Ag/CB catalysts was large in the H-cell, while it was nearly absent in the MEA geometry under the relatively short testing time used in this study. This difference can be attributed to the greater solubility of SO2 in the electrolyte compared to CO2, leading to an accumulation effect and a much higher liquid phase concentration of SO2 in the H-cell. This led to a greater performance decrease of the Ag/CB catalyst in the H-cell compared to the MEA geometry, when exposed to the same concentration of SO2 impurities. An ultrathin SiO2 coating synthesized via ALD protected the Ag/CB catalyst in the H-cell against SO2 impurities under relatively less negative potentials. This is due to the SO2 and CO2 permeability differences through the SiO2 coatings. CO2 has much higher permeability compared to SO2 (or SO2 derived ions) through SiO2. This leads to a significant obstruction in the interaction of SO2 with the catalyst and might decrease the SO2 concentration after the SiO2 coatings.
Data availability
The data supporting this article have been included as part of the ESI† see DOI: https://doi.org/10.1039/D4CY01196A.
Author contributions
M. Li: conceptualization, methodology, formal analysis, validation, writing – original draft. S. Fu: methodology, validation, writing – review & editing. R. Kortlever: supervision, writing – review & editing, project administration. J. R. van Ommen: supervision, writing – review & editing, project administration, funding acquisition.
Conflicts of interest
J. R. van Ommen has a financial interest in Powall.
Acknowledgements
M. L. acknowledges the PhD scholarship awarded by the China Scholarship Council (CSC). The authors thank Saeed Saedy for doing the TG/DTA analysis, Cas Veenhoven for the assistance in the lab, Bart Boshuizen for the XPS area scan training and Baukje Terpstra for the ICP-OES analysis.
Notes and references
- C. Chen, J. F. Khosrowabadi Kotyk and S. W. Sheehan, Progress toward Commercial Application of Electrochemical Carbon Dioxide Reduction, Chem, 2018, 4(11), 2571–2586 CAS.
- M. Ma, K. Liu, J. Shen, R. Kas and W. A. Smith, In Situ Fabrication and Reactivation of Highly Selective and Stable Ag Catalysts for Electrochemical CO2 Conversion, ACS Energy Lett., 2018, 3(6), 1301–1306 CrossRef CAS PubMed.
- N. Zhang, X. Zhang, L. Tao, P. Jiang, C. Ye and R. Lin, et al. Silver Single-Atom Catalyst for Efficient Electrochemical CO2 Reduction Synthesized from Thermal Transformation and Surface Reconstruction, Angew. Chem., Int. Ed., 2021, 60(11), 6170–6176 CrossRef CAS PubMed.
- H. Wang, Z. Han, L. Zhang, C. Cui, X. Zhu and X. Liu, et al. Enhanced CO selectivity and stability for electrocatalytic reduction of CO2 on electrodeposited nanostructured porous Ag electrode, J. CO2 Util., 2016, 15, 41–49 CrossRef CAS.
- S.-Q. Liu, S.-W. Wu, M.-R. Gao, M.-S. Li, X.-Z. Fu and J.-L. Luo, Hollow Porous Ag Spherical Catalysts for Highly Efficient and Selective Electrocatalytic Reduction of CO2 to CO, ACS Sustainable Chem. Eng., 2019, 7(17), 14443–14450 CrossRef CAS.
- J. Osiewacz, M. Löffelholz, L. Weseler and T. Turek, CO poisoning of silver gas diffusion electrodes in electrochemical CO2 reduction, Electrochim. Acta, 2023, 445, 142046 CrossRef CAS.
- D. E. Doronkin, T. S. Khan, T. Bligaard, S. Fogel, P. Gabrielsson and S. Dahl, Sulfur poisoning and regeneration of the Ag/γ-Al2O3 catalyst for H2-assisted SCR of NOx by ammonia, Appl. Catal., B, 2012, 117–118, 49–58 CrossRef CAS.
- F. Gobal and L. Majari Kasmaee, Polysulfide Poisoning of Ag Electrocatalyst during L-Ascorbate Ion Electro-oxidation in Alkaline Solution, Chin. J. Catal., 2012, 33(2–3), 267–274 CrossRef CAS.
- V. Houel, P. Millington, S. Pollington, S. Poulston, R. R. Rajaram and A. Tsolakis, Chemical deactivation of Ag/Al2O3 by sulphur for the selective reduction of NOx using hydrocarbons, Catal. Today, 2006, 114(4), 334–339 CrossRef CAS.
- P. Bains, P. Psarras and J. Wilcox, CO2 capture from the industry sector, Prog. Energy Combust. Sci., 2017, 63, 146–172 CrossRef.
- T. Al-Attas, S. K. Nabil, A. S. Zeraati, H. S. Shiran, T. Alkayyali and M. Zargartalebi, et al. Permselective MOF-Based Gas Diffusion Electrode for Direct Conversion of CO2 from Quasi Flue Gas, ACS Energy Lett., 2022, 8(1), 107–115 CrossRef.
- G. Pipitone and O. Bolland, Power generation with CO2 capture: Technology for CO2 purification, Int. J. Greenhouse Gas Control, 2009, 3(5), 528–534 CrossRef CAS.
- R. T. J. Porter, M. Fairweather, M. Pourkashanian and R. M. Woolley, The range and level of impurities in CO2 streams from different carbon capture sources, Int. J. Greenhouse Gas Control, 2015, 36, 161–174 CrossRef CAS.
- D. M. D'Alessandro, B. Smit and J. R. Long, Carbon dioxide capture: prospects for new materials, Angew. Chem., Int. Ed., 2010, 49(35), 6058–6082 CrossRef PubMed.
- G. V. Last and M. T. Schmick, Identification and Selection of Major Carbon Dioxide Stream Compositions, US Department of Energy, 2011, PNNL-20493 Search PubMed.
- B. H. Ko, B. Hasa, H. Shin, E. Jeng, S. Overa and W. Chen, et al. The impact of nitrogen oxides on electrochemical carbon dioxide reduction, Nat. Commun., 2020, 11(1), 5856 CrossRef CAS PubMed.
- Y. Xu, J. P. Edwards, J. Zhong, C. P. O'Brien, C. M. Gabardo and C. McCallum, et al. Oxygen-tolerant electroproduction of C2 products from simulated flue gas, Energy
Environ. Sci., 2020, 13(2), 554–561 RSC.
- S. Van Daele, L. Hintjens, S. Hoekx, B. Bohlen, S. Neukermans and N. Daems, et al. How flue gas impurities affect the electrochemical reduction of CO2 to CO and formate, Appl. Catal., B, 2024, 341, 123345 CrossRef CAS.
- P. P. Albertini, M. A. Newton, M. Wang, O. Segura Lecina, P. B. Green and D. C. Stoian, et al. Hybrid oxide coatings generate stable Cu catalysts for CO2 electroreduction, Nat. Mater., 2024, 23(5), 680–687 CrossRef CAS PubMed.
- H. Van Bui, F. Grillo and J. R. van Ommen, Atomic and molecular layer deposition: off the beaten track, Chem. Commun., 2016, 53(1), 45–71 RSC.
- K. S. Yoo, D.-G. Kim, S. Lee, W.-B. Lee and J.-S. Park, Atmospheric pressure spatial ALD of Al2O3 thin films for flexible PEALD IGZO TFT application, Ceram. Int., 2022, 48(13), 18803–18810 CrossRef CAS.
- D. H. Levy, D. Freeman, S. F. Nelson, P. J. Cowdery-Corvan and L. M. Irving, Stable ZnO thin film transistors by fast open air atomic layer deposition, Appl. Phys. Lett., 2008, 92, 192101 CrossRef.
- D. La Zara, F. Sun, F. Zhang, F. Franek, K. Balogh Sivars and J. Horndahl, et al. Controlled Pulmonary Delivery of Carrier-Free Budesonide Dry Powder by Atomic Layer Deposition, ACS Nano, 2021, 15(4), 6684–6698 CrossRef CAS PubMed.
- J. W. Klaus and S. M. George, Atomic layer deposition of SiO2 at room temperature using NH3-catalyzed sequential surface reactions, Surf. Sci., 1999, 447(2000), 81–90 Search PubMed.
- F. Grillo, H. Van Bui, J. A. Moulijn, M. T. Kreutzer and J. R. van Ommen, Understanding and Controlling the Aggregative Growth of Platinum Nanoparticles in Atomic Layer Deposition: An Avenue to Size Selection, J. Phys. Chem. Lett., 2017, 8(5), 975–983 CrossRef CAS PubMed.
- M. Li, S. Fu, S. Saedy, A. Rajendrakumar, F. D. Tichelaar and R. Kortlever, et al. Nanostructuring Pt-Pd Bimetallic Electrocatalysts for CO2 Reduction Using Atmospheric Pressure Atomic Layer Deposition, ChemCatChem, 2022, 14, e202200949 CrossRef CAS.
- R. Kamphorst, P. Wanjari, S. Saedy, J. F. K. van Dam, A. Thijssen and P. Brüner, et al. Enhancing colloid stability of polymer microspheres in water through SiO2 coating: Effects of coating cycles and surface coverage, Surf. Interfaces, 2024, 45, 103852 CrossRef CAS.
- Y. Song and P. N. Pintauro, The electrochemical synthesis of aminonitriles I. H-cell studies with adiponitrile and azelanitrile, J. Appl. Electrochem., 1991, 21, 21–27 CrossRef CAS.
- L. Wang, C.-Y. Lee and P. Schmuki, Solar water splitting: preserving the beneficial small feature size in porous α-Fe2O3 photoelectrodes during annealing, J. Mater. Chem. A, 2013, 1(2), 212–215 RSC.
- M. Li, S. Saedy, S. Fu, T. Stellema, R. Kortlever and J. R. van Ommen, Enhancing the durability of Pt nanoparticles for water electrolysis using ultrathin SiO2 layers, Catal. Sci. Technol., 2024, 14(5), 1328–1335 RSC.
- Y. Du, X. Du and S. M. George, SiO2 film growth at low temperatures by catalyzed atomic layer deposition in a viscous flow reactor, Thin Solid Films, 2005, 491(1–2), 43–53 CrossRef CAS.
- J. W. Klaus, O. Sneh and S. M. George, Growth of SiO2 at Room Temperature with the Use of Catalyzed Sequential Half-Reactions, Science, 1997, 278(5345), 1934–1936 CrossRef CAS PubMed.
- H. Yun, J. Kim, W. Choi, M. H. Han, J. H. Park and H.-S. Oh, et al. Understanding morphological degradation of Ag nanoparticle during electrochemical CO2 reduction reaction by identical location observation, Electrochim. Acta, 2021, 371, 137795 CrossRef CAS.
- C. Kim, T. Eom, M. S. Jee, H. Jung, H. Kim and B. K. Min, et al. Insight into Electrochemical CO2 Reduction on Surface-Molecule-Mediated Ag Nanoparticles, ACS Catal., 2016, 7(1), 779–785 CrossRef.
- N. J. Harmon and H. Wang, Electrochemical CO2 Reduction in the Presence of Impurities: Influences and Mitigation Strategies, Angew. Chem., Int. Ed., 2022, 61(52), e202213782 CrossRef CAS PubMed.
- S. Ghafoor, S. Ata, N. Mahmood and S. N. Arshad, Photosensitization of TiO2 nanofibers by Ag2S with the synergistic effect of excess surface Ti3+ states for enhanced photocatalytic activity under simulated sunlight, Sci. Rep., 2017, 7(1), 255 CrossRef PubMed.
- F. M. Nor, N. H. A. Karim, I. Abdullah and R. Othaman, Permeability of carbon dioxide and nitrogen gases through SiO2 and MgO incorporated ENR/PVC membranes, J. Elastomers Plast., 2016, 48(6), 483–498 CrossRef CAS.
- M. F. A. Wahab, A. F. Ismail and S. J. Shilton, Studies on gas permeation performance of asymmetric polysulfone hollow fiber mixed matrix membranes using nanosized fumed silica as fillers, Sep. Purif. Technol., 2012, 86, 41–48 CrossRef CAS.
- L. Meng, M. Kanezashi, J. Wang and T. Tsuru, Permeation properties of BTESE–TEOS organosilica membranes and application to O2/SO2 gas separation, J. Membr. Sci., 2015, 496, 211–218 CrossRef CAS.
- J. Yoshiura, K. Ishii, Y. Saito, T. Nagataki, Y. Nagataki and A. Ikeda, et al. Permeation Properties of Ions through Inorganic Silica-Based Membranes, Membranes, 2020, 10, 27 CrossRef CAS PubMed.
- X. Yu, L. Meng, H. Nagasawa, M. Kanezashi, M. Machida and T. Tsuru, Evaluating the chemical stability of metal oxides in SO3 and applications of SiO2-based membranes to O2/SO3 separation, J. Am. Ceram. Soc., 2019, 102(11), 6946–6956 CrossRef CAS.
|
This journal is © The Royal Society of Chemistry 2025 |
Click here to see how this site uses Cookies. View our privacy policy here.