DOI:
10.1039/D4TA06000H
(Review Article)
J. Mater. Chem. A, 2025,
13, 6866-6894
The synergistic effect of MOF and biomass achieving dual breakthroughs in material structure and performance
Received
24th August 2024
, Accepted 24th November 2024
First published on 3rd December 2024
Abstract
In order to cope with the environmental crisis and the depletion of non-renewable resources, the combination of metal–organic framework (MOF) and biomass materials has become an important breakthrough in sustainable materials science. With its unique pore structure and adjustable performance, MOF significantly improves the thermal stability and mechanical strength of biomass materials, and broadens its application in energy, material manufacturing and other fields. MOF–biomass composites show excellent properties in carbon capture, water treatment and biomedicine, which is of great significance to environmental protection and green chemical industry. This paper summarizes the latest research progress of MOF–biomass composites, including their application in wastewater treatment, air purification, food packaging and other fields, and discusses the green synthesis method, biological interface integration strategy and its potential in biocatalysis, sensing and medical fields. The development and application of MOF–biomass composites provide a new way to solve environmental problems and promote sustainable development. Furthermore, we critically analyze the key challenges and future directions. Our sincere hope is that this review will stimulate greater research interest in applications of biomass/MOF composites, and offer valuable insights for their design and utilization strategies.
1. Introduction
In the midst of growing environmental concerns and the depletion of non-renewable energy sources, there is an urgent global need for sustainable materials. Biomass, as a renewable and biodegradable resource, is at the vanguard of this quest, presenting a multitude of applications spanning from energy generation to material fabrication.1 Biomass encompasses a wide range of materials, including lignocellulosic biomass (such as wood, agricultural residues, and energy crops), algae, and waste materials from the forestry and agricultural sectors. Each type of biomass possesses unique properties and applications, from energy generation to material fabrication. Biomass, as a renewable and environmentally friendly material, is characterized by low cost and abundant reserves, reducing reliance on fossil fuels, decreasing greenhouse gas emissions, and being more environmentally friendly. However, the inherent limitations of biomass, such as its modest thermal stability and inadequate mechanical resilience, often restrict its broader utility. MOFs are a class of sophisticated porous materials constituted by metal ions or clusters interconnected with organic linkers. MOFs' distinct characteristics, namely their expansive surface area, adaptable pore dimensions, and modularity in synthesis,2 position them as prime enhancers for biomass composites, overcoming the inherent drawbacks of biomass.3,4
MOF and biomass materials occupy distinct yet synergistic niches within the realm of materials science. Biomass materials inherently possess high porosity and large surface areas, characteristics that are also found in MOFs. The combination of the two can enhance these properties, representing one aspect of their synergistic effects. Furthermore, biomass materials contain various functional groups that can be modified and utilized, with MOFs capable of binding to specific functional groups, leading to a more uniform distribution of MOFs. Additionally, biomass materials exhibit excellent biodegradability and biocompatibility, while MOFs can be designed with specific functions. The integration of these materials allows for the creation of environmentally friendly functional materials. The fusion of these two realms through MOF–biomass composites introduces a potent strategy to elevate the performance and utility of biomass materials across a spectrum of applications. These are also the places where biomass carriers are more attractive than other carriers.
The combination of MOFs with biomass not only retains the advantages of each but also enhances overall performance through synergistic effects. In particular, they can facilitate the creation of superior adsorbents for carbon capture and sequestration, a pivotal strategy in combating climate change.5–8 Moreover, these composite materials act as catalysts in the transformation of biomass into high-value chemicals, thereby harnessing renewable resources for a more sustainable chemical industry.9–11 The integration of MOF within biomaterials for drug delivery systems and tissue engineering not only pushes the boundaries of biomedicine but also underscores the potential for producing more robust, chemically stable, and multifunctional biomaterials.12 The unique properties of MOF–biomass composites extend their potential to fields such as flexible electronics, biosensing, and environmental remediation. These materials exhibit high conductivity, mechanical flexibility, and biocompatibility, making them ideal for the development of next-generation electronic devices that are both technologically advanced and environmentally responsible. Additionally, their high adsorption capacity and selectivity for pollutants make them effective solutions for water purification and air pollution control. This reciprocal relationship sees MOFs enhancing the physical properties of biomass, while biomass serves as a sustainable and economical feedstock for MOF production.
In essence, the merging of MOFs and biomass materials paves the way for the creation of eco-friendly and biocompatible materials that hold promise in biomedicine, energy production, and environmental remediation.6,13,14 We will discuss the green synthesis methods, biological interface integration strategies, and potential applications in biocatalysis, sensing, and medical fields. By critically analyzing the key challenges and future directions, we hope to stimulate greater research interest and offer valuable insights for the design and utilization of MOF–biomass composites. These materials hold the potential to address pressing environmental issues and promote sustainable development, making them a transformative force for the 21st century (Fig. 1).
 |
| Fig. 1 Timeline of MOF–biomass composite materials. (Reproduced with permission from ref. 15–30, copyright 2015 American Chemical Society, copyright 2016 Wiley, copyright 2017 American Chemical Society, copyright 2018 Elsevier, copyright 2019 American Chemical Society, copyright 2019 Elsevier, copyright 2020 Elsevier, copyright 2020 Wiley, copyright 2021 Elsevier, copyright 2021 Wiley, copyright 2022 Elsevier, copyright 2023 Elsevier, copyright 2023 Elsevier, copyright 2023 American Chemical Society, copyright 2023 Elsevier, copyright 2024 Springer Nature, copyright 2024 Nature.) | |
2. Properties and synthesis of MOFs with biomaterial matrices
2.1 Key factors influencing MOF stability
MOFs have emerged as a class of materials with exceptional potential for various applications, especially when integrated with biomass materials.6 Their stability, a critical aspect for practical implementation, is influenced by several key factors, including the choice of metal ions, organic linkers, and the synthesis conditions.31–33 For example, the use of zirconium or titanium ions can lead to highly robust MOFs, such as UiO-66 and MIL-125, which are known for their excellent chemical and thermal stability.3 The choice of organic linkers can affect the pore size and functionality of the framework. For instance, the use of bipyridine-based linkers can introduce redox-active sites within the MOF structure, which can be beneficial for catalytic applications.34
One of the key factors that influence the stability of MOFs under operational conditions is the strength of the coordination bonds between the metal ions and the organic ligands. MOFs with strong coordination bonds are more stable and less likely to undergo degradation or structural collapse. The choice of metal ions and organic ligands can also affect the stability of MOFs.35 Walton proposed several guidelines that may be useful in the selection of further chemically stable MOFs based on this criterion. The Irving–Williams series describes the relative stability of first row transition series bivalent metal ions (Mn < Fe < Co < Ni < Cu > Zn) with a wide variety of ligands and can therefore be used as a guiding tool in the synthesis of stable structures.36 Xiong et al.37 also revealed that MOFs based on Cu2+ are more stable than their Co2+ and Zn2+ analogues, and that the N-oxide ligand endows the MOFs with a higher affinity for CO2. In addition, the use of functionalized organic ligands, such as those containing carboxylic, amino, or hydroxyl groups, can enhance the stability of MOFs by increasing the number of coordination sites and the strength of the interactions between the ligands and the metal ions.35
In addition to stability, the properties of MOFs, such as pore size, surface area, and chemical functionality, can be tuned by varying the metal ions and organic ligands used in their synthesis.15,38–40 This makes MOFs highly versatile and adaptable to a wide range of applications. For example, MOFs with large pore sizes and high surface areas are ideal for use in gas storage and separation,41,42 while those with specific chemical functionalities are useful for catalysis and drug delivery.43
2.2 Synthesis techniques for MOF–biomass composites
To harness the synergy of MOFs with biomass, innovative synthesis methods are employed:
Solvothermal/hydrothermal synthesis is the most widely used method for the synthesis of MOFs. This method involves the reaction of metal ions and organic ligands in a solvent, such as water,16 ethanol, and DMF, at elevated temperatures and pressures, as a result of high yield and uniform particle size distribution. The use of biomaterials, such as cellulose and chitosan, as templates or supports for the synthesis of MOFs can significantly improve the mechanical strength and stability of the resulting MOF–biomass composites. These composites exhibit high surface area and tunable porosity, making them ideal for applications in pollution control, such as air and water purification. They also show promise in energy storage, with potential use in the development of advanced battery materials and supercapacitors due to their excellent electrochemical properties. Furthermore, the controlled morphology and high surface area enhance catalytic efficiency, making these composites suitable for various chemical reactions.
There are two strategies for solvothermal synthesis. The first strategy is to synthesize the MOF separately and then mix it with the biomass matrix. As shown in Fig. 2a, MIL-101 was solvothermally synthesized after mixing Fe3+ and terephthalic acid, and then a mixed solution of MIL-101 and chitosan was used to form MIL-101/CS sponge.44 The advantage is that the synthesis conditions of the MOF, such as temperature, time and solvent type, can be accurately controlled, so as to obtain a MOF with a specific structure and properties. In addition, this method can further improve the performance of MOFs through post-synthesis modification, such as constructing bifunctional MOF catalysts through post-synthesis modification of organic ligands and unsaturated metal sites.48 This method can accurately control the properties of MOFs, but it may increase the synthesis steps and costs.
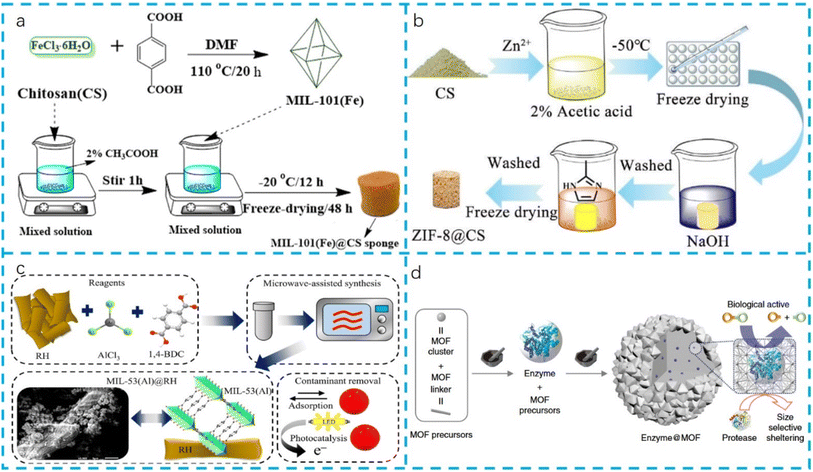 |
| Fig. 2 Preparation of MOF–biomass composite materials via various methods: (a) solvothermal (reproduced from ref. 44 with permission from Elsevier, copyright 2020); (b) in situ growth (reproduced from ref. 45 with permission from RSC, copyright 2020); (c) microwave-assisted synthesis (reproduced from ref. 46 with permission from Elsevier, copyright 2023); (d) mechanochemical process (reproduced from ref. 47 with permission from Nature, copyright 2019). | |
The second strategy is to directly mix the reactant with the biomass matrix in the process of synthesizing the MOF. The advantage of this method is that it can simplify the synthesis process, reduce the steps and possibly introduce new physical and chemical properties into the MOF. For example, a solution containing metal ions (Co(NO3)2, NiCl2, and terephthalic acid) is prepared with a specific molar ratio. This solution is then mixed with a CMC aerogel in a Teflon-lined stainless steel autoclave and heated at 120 °C for 14 hours to allow for the in situ growth of the MOF on the CMC aerogel. The resulting precursor is then washed with DMF and methanol and freeze-dried to obtain the final MOF–CMC aerogel composite.49 This method can also take advantage of the renewability and environmental friendliness of biomass matrices, providing a new way for the sustainable development of MOFs, but it may be difficult to accurately control the properties of MOFs, because the complexity of biomass matrices may affect the crystal structure and properties of MOFs. Niu et al.50 reported the synthesis of a chitosan-supported MOF composite using the solvothermal method. The resulting Zn-MOF/chitosan composite had high adsorption capacity for chromium(VI) and methyl orange through electrostatic attraction and non-electrostatic action respectively. According to Nasser Abdelhamid's research,51 the 3D printed Cellulose-ZIF8 (CelloZIF-8) composite material begins with the formulation of a thixotropic ink using SiO2-based materials and TOCNF (Tall Oil Carboxylate Nanofibers). This ink is then used to 3D print the desired structures using a 3D printer. After printing, the structures are subjected to a hydrothermal treatment to induce the in situ growth of ZIF-8 crystals on the 3D printed framework. The materials are then tested for their adsorption and catalytic properties, showing high efficiency in dye removal and CO2 adsorption. The process is binder-free and does not require additional chemical reagents, making it cost-effective and environmentally friendly.
In situ growth of MOFs in biomass composites is an innovative strategy combining MOFs with biomass materials, which are usually used to prepare continuous MOF films. It ensures strong interface adhesion between the MOF and the biomass substrate, leading to better mechanical stability and durability of the composite materials. This is crucial for applications where the material's integrity under stress is essential. The method allows for customizable properties by adjusting the growth conditions, such as temperature and pH. This flexibility enables the fine-tuning of the composite's properties to meet specific application requirements. The versatility of in situ growth means it can be applied to a wide range of biomass substrates, including cellulose fibers and polymer matrices, expanding the scope of potential applications in biomedical, sensors and food packaging. In situ growth of MOFs can effectively utilize the natural advantages of biomass, such as renewability, biocompatibility and environmental friendliness, and at the same time endow materials with new functional characteristics. By growing MOFs on the surface or inside of biomass, composite materials with excellent mechanical strength, stability and biocompatibility can be prepared, which is of great significance for developing new environmental protection materials and sustainable development materials. As shown in Fig. 2b, the ZIF-8@CS composite sponge is prepared using a modified in situ method.45 The process involves dissolving chitosan and Zn(CH3COOH)2·6H2O in acetic acid solution, followed by vacuum freeze-drying to obtain the primary Zn2+@CS sponges. These sponges are then immersed in a solution containing 2-methylimidazole for the in situ growth of ZIF-8 crystals. After washing and another round of vacuum freeze-drying, the white ZIF-8@CS sponges are obtained. Table 1 shows more MOF–biomass composites prepared by the in situ growth method.
Table 1 MOF biomaterial composites for water purification during the past five years
Adsorbent |
Preparation route |
MOF types |
Metal core |
Linker |
Pollutant |
Adsorption capacity (mg g−1) |
pH |
Reusability |
Mechanism |
Ref. |
ZIF-8@chitosan/PVA nanofiber |
Rest for 24 hours; electrospinning |
ZIF-8 |
Zn |
2-Methylimidazole |
Malachite green |
1000 |
6 |
5, 90% |
Langmuir isotherm model |
52
|
Zn-MOF/chitosan (ZnBDC/CSC) composite |
Solvothermal method |
Zn-MOF |
Zn |
1,4-Benzenedicarboxylic acid |
Cr(VI)) methyl orange (MO) |
225 |
5 |
5, 84% |
Langmuir isotherm model |
50
|
202 |
Nano-MIL-101(Fe)@chitosan (CS) hybrid sponge |
Solvothermal method |
MIL-101 |
Fe |
Terephthalic acid |
Acid red 94 |
4518 |
— |
3, 87% |
Langmuir isotherm |
44
|
Chitosan/UiO-66 composite porous monolith |
Solvothermal method; ice-templating |
UiO-66 |
Zr |
Benzene-1,4-dicarboxylate |
Congo red (CR) |
246.21 |
7 |
4, 90% |
Langmuir and Freundlich models |
53
|
ZIF-67/BC/CH aerogel |
In situ growth |
ZIF-67 |
Co |
2-Methylimidazole |
Cu2+ |
200.6 |
6 |
5, 72% |
Pseudo-second-order kinetic model |
18
|
Cr6+ |
152.1 |
5, 81% |
ZIF-67 MOF@aminated chitosan composite bead |
Solvothermal method |
ZIF-67 |
Co |
2-Methylimidazole |
Cr(VI) |
119.05 |
2 |
7, 60% |
Langmuir, Freundlich, Temkin, and Dubinin–Radushkevich (D–R) |
54
|
Chitosan-ZIF-8 composite beads |
Room temperature growth |
ZIF-8 |
Zn |
2-Methylimidazole |
Cu(II) |
165.7 |
5 |
5 |
Langmuir and Freundlich isotherm models |
55
|
Pb(II) |
131.4 |
Chitosan-g-PNVCL/ZIF-8 composite nanofibers |
Stirring for 6 hours |
ZIF-8 |
Zn |
2-Methylimidazole |
Cr(VI) |
269.2 |
3 |
3, a slight decrease |
Redlich-Peterson isotherm model |
56
|
As(V) |
258.5 |
Phenol |
152.3 |
MIL-100(Fe)-nano-modified chitosan |
Solvothermal method |
MIL-100(Fe) |
Fe |
1,3,5-Benzenetricarboxylic acid |
Sb(III) |
52.91 |
11 |
|
Freundlich model |
57
|
Chitosan-GO/ZIF (GCZ8A) foam |
Reaction at 25 °C for 4 hours |
ZIF-8-Ag |
Zn |
2-Methylimidazole |
Uranium(VI) |
361.01 |
7 |
5, 33.7% |
Freundlich model |
58
|
MOF-808/chitosan |
Solvothermal process |
MOF-808 |
Zr |
1,3,5-Benzenetricarboxylic acid |
Cr(VI) |
320 |
5 |
6 |
Langmuir isotherm model |
59
|
MIL-53(Fe)/chitosan composite hydrogel spheres |
Solvothermal method |
MIL-53(Fe) |
Fe |
Terephthalate |
CR |
590.8 |
Neutral |
3, 85% |
Pseudo-first-order model; Langmuir model |
60
|
UiO-66/CB |
Stirring for 2 hours |
UiO-66 |
Zr |
BDC |
As(III) |
88.6 |
7 |
5, 86.9% |
Freundlich model |
61
|
UiO-66-NH2-modified chitosan composite |
Solvothermal method |
UiO-66-NH2 |
Zr |
2-Aminoterephthalic acid |
Hg(II) |
896.8 |
6 |
5 |
Langmuir isotherm model |
62
|
TIF-A1/chitosan composite beads |
Secondary growth method |
TIF-A1 |
Zn |
Adenine isonicotinic acid |
Pb(II) |
397.3 |
|
5, 99% |
Langmuir model |
63
|
ZIF8–ZnO–cotton fiber |
Solvothermal reaction |
ZIF-8 |
Zn |
2-Methylimidazole |
As(V) |
52.5 |
7 |
— |
|
64
|
BC@ZIF-8 composite aerogel |
In-situ growth |
ZIF-8 |
Zn |
2-Methylimidazole |
Pb2+ and Cd2+ |
390 and 220 |
5.5 ± 0.5 |
|
Pseudo-second-order kinetic model |
22
|
ZIF-8@CNF@cellulose foam |
Solvothermal method |
ZIF-8 |
Zn |
2-Methylimidazole |
Rhodamine B |
24.6 |
|
|
|
23
|
Cr(VI) |
35.6 |
DMF |
45.2 g g−1 |
UiO-66-NH2 grafted onto cellulose fibers |
One-pot synthesis |
UiO-66-NH2 |
Zr |
2-Amino-1,4,7-triazacyclononane |
Cr(VI) |
78.2% |
|
|
|
65
|
MO |
84.5% |
UiO-66 and UiO-66-NH2@cellulose aerogels |
In situ growth |
UiO-66 and UiO-66-NH2 |
Zr |
2-Aminoterephthalic acid |
Pb2+ |
89.4 |
|
5 |
Pseudo-second-order kinetic model |
66
|
Cu2+ |
31.23 |
NH2-MIL-53/WC hybrid membrane |
Self-sacrificial template strategy |
|
Al |
2-Aminoterephthalic acid |
Pb2+ |
223.4 |
6 |
|
Langmuir isotherm model |
67
|
HKUST-1/cellulose/chitosan composite aerogel |
In situ growth method |
HKUST-1 |
Zn |
2,3,5,6-Tetrafluorophenyl |
Methylene blue (MB) |
526.3 |
7.5 |
Desorption with HCl solution; 90% |
The Freundlich model |
68
|
HKUST-1/PANNs/RC composite aerogel |
In-situ growth and solvothermal methods |
HKUST-1 |
Cu |
1,3,5-Benzenetricarboxylate |
MB |
522.01 |
|
5, 92% |
|
69
|
Cu-BTC@cellulose acetate membrane |
In-situ immobilization |
|
Cu |
BTC |
Dimethoate |
321.9 |
|
5, 77.5% |
Langmuir isotherm model |
70
|
MIL-53@PC |
Sonicate |
MIL-53 |
Fe |
2-Hydroxybenzaldehyde |
MO |
936.5 |
2 |
|
Pseudo-first-order (PFO) and pseudo-second-order (PSO) models |
71
|
3D printed cellulose-ZIF8 |
In-situ growth |
ZIF-8 |
Zn |
Imidazolate |
Cu2+ |
101.2 |
|
|
|
51
|
Co2+ |
33.5 |
Co-MOF-cellulose based composite |
In situ growth method |
ZIF-8 and ZIF-67 |
Zn and Co |
2-Methylimidazole |
Cr(VI) |
145 |
Neutral |
5, 90% |
Langmuir and pseudo-second-order model |
72
|
Fluorescent bacterial cellulose@Zr-MOF |
Solvothermal method |
Zr-MOF |
Zr |
1,3,5-Tri(4-carboxyphenyl)benzene |
Cr(VI) |
90 |
3 to 9 |
|
|
73
|
Fe/ZIF-8@cellulose bioadsorbent |
In-situ growth |
ZIF-8 |
Fe Zn |
2-Methylimidazole |
Tetracycline |
1359.2 |
|
5, 63.5% |
Langmuir isotherm model |
74
|
MIL-100(Fe)/cellulose |
Stirred at ambient temperature for 24 h |
MIL-100(Fe) |
Fe |
Benzene-1,3,5-tricarboxylic acid |
MB |
384.615 |
6.5 |
5, without significant loss |
Langmuir model |
75
|
MIL-88(Fe)cellulose-based filter |
Solvothermal method |
MIL-88(Fe) |
Fe |
Terephthalic acid |
MB |
602 |
Neutral |
5, 82.29% |
Langmuir isotherm |
76
|
Ni/Co-MOF-CMC aerogel |
Solvothermal reaction |
|
Ni Co |
Terephthalic acid |
Cu2+ |
233.99 |
2 to 5 |
|
Langmuir isotherm model |
49
|
Cellulose cotton-based UiO-66 MOF |
Solvothermal process |
UiO-66 |
Zr |
p-Phthalic acid |
Rhodamine B |
68.5 |
|
10 |
Langmuir model |
77
|
Pb(II) |
65 |
SA/CMC/Cu-BDC composite beads |
Solvothermal method |
|
Cu |
Terephthalic acid |
Tetracycline |
180.5 |
7 |
3 |
Langmuir isotherm model |
78
|
UiO-66-NH2 incorporated PVA/cellulose nanofiber composite aerogel |
Solvothermal reaction |
UiO-66-NH2 |
Zr |
2-Aminoterephthalic acid |
Formaldehyde |
Decreases from 12.85 to 11.12 mg g−1 |
|
5 |
|
79
|
TMPA@MOF-801 aerogel |
Solvothermal process |
MOF-801 |
Zr |
Fumarate |
Cr(VI) |
350.64 |
2 |
6, 88% |
Pseudo-second-order model and Langmuir model |
80
|
MIL@TH@FP composite |
— |
MIL-125-NH2 |
Ti |
|
Hg2+ |
182.8 |
6.8 |
5 |
Langmuir and pseudo-second-order models |
81
|
Cr3+ |
109.7 |
Cu2+ |
134.1 |
EC/ZIF-67 and EC/MIL-88A nanocomposites |
Green synthesis routes in water at room temperature and atmospheric pressure |
ZIF-67 |
Zr |
2-Methyl imidazole |
CR |
99.80% |
7 |
5 |
Freundlich model |
82
|
MIL-88A |
Fe |
Fumaric acid |
90.90% |
SCC-CuMOF |
Solvothermal method |
CuMOF |
Cu |
Trimesic acid |
Pb2+ |
531.38 |
|
5 |
Langmuir model |
83
|
Aminated ZIF-8 composite cellulose aerogel |
Stirring at room temperature |
ZIF-8 |
Zn |
2-Methylimidazole |
Mo(VI) |
872.39 |
3 |
5, 80% |
Langmuir and pseudo-second-order model |
84
|
Ni-MOF-74 lignin-based nanofiber materials |
Solvothermal reaction |
Ni-MOF-74 |
Ni |
2,5-Dihydroxyterephthalic acid |
Chlorobenzene |
58 490 |
|
|
Langmuir model |
85
|
NH2-UIO@L |
Solvothermal method |
UIO |
Zr |
2-Amino terephthalic acid |
MO |
214.13 |
3–10 |
6, 97.66% |
Dubinin–Radushkevich and pseudo-second-order models |
86
|
MB |
243.31 |
11–12 |
6, 99.15% |
Temkin and pseudo-second-order models |
NH2-MIL@L |
One-step hydrothermal method |
MIL |
Fe |
Phenolated lignin |
MO |
195.31 |
|
6, 91.2% |
Temkin model and pseudo-second-order kinetics |
87
|
MB |
481.34 |
6, 93.4% |
Dubinin–Radushkevich model and pseudo-second-order kinetics |
UIO-g-NL |
Solvothermal reaction; Schiff base reaction |
UIO-66-NH2 |
Zr |
Aminated lignin |
MO |
961.54 |
|
6, >90% |
Pseudo-second-order kinetic and Freundlich isotherm models |
88
|
MB |
1120.7 |
Selective adsorption of both dyes (MO and MB) is pH-dependent |
PdNPs/UiO-66-NH2/LP |
Solvothermal method |
UiO-66-NH2 |
Zr |
2-Aminoterephthalic acid |
Cr6+ |
Efficient removal of Cr6+ in 10 min |
|
4, >50% |
First-order kinetics |
89
|
Microwave-assisted synthesis is a rapid and efficient method for the synthesis of MOFs,90–92 offering significant advantages of energy efficiency and uniform heating over traditional methods. This method involves the use of microwave radiation to heat the reaction mixture, resulting in faster reaction rates and shorter synthesis times. The ability to reduce reaction times makes microwave-assisted synthesis particularly suitable for large-scale production, highlighting its advantage in terms of rapid synthesis. The use of microwave-assisted synthesis for the synthesis of MOFs with biomaterial matrices can improve the homogeneity and dispersion of the MOFs in the biomaterial matrices.46 Kevin et al.46 reported the design of MOF@Biomass layered hybrids through in situ growth from rice husk (RH) and microwave-assisted synthesized MIL-53(Al) particles that enable the reduction of reaction times, as shown in Fig. 2c. Couzon et al.93 discussed the development of a new synthesis method for MOF–textile composites using microwave irradiation. This method allows for the direct integration of MOFs onto textiles, which could enhance the protective capabilities of the material against chemical and nuclear hazards.
A mechanochemical approach provides a rapid and efficient route to MOFs directly from a metal oxide and without bulk solvent,94,95 which not only speeds up the process but also minimizes the use of organic solvents and strong acids, aligning with environmentally friendly practices. In the pharmaceutical industry, the improved enzyme stability and activity make these composites suitable for controlled drug delivery systems and topical medications, potentially improving the efficacy and safety of such treatments. Noorian96 reported a novel approach to encapsulating bioactive molecules within MOFs using a simple mechanochemical method. The focus is on developing controlled topical drug delivery systems, which could potentially improve the efficacy and safety of topical medications. By encapsulating enzymes within MOFs using this method, their stability and activity are enhanced, even under harsh conditions. This is particularly important for applications where the enzymes need to maintain their functionality in challenging environments. Fig. 2d provides the preparation process of encapsulating enzymes within MOFs using a ball milling strategy. The method is rapid, green, and minimizes the use of organic solvents and strong acids. Enzymes such as β-glucosidase, invertase, β-galactosidase, and catalase are encapsulated in ZIF-8, UiO-66-NH2, or Zn-MOF-74. The process is initiated by adding MOF precursors and the lyophilized enzyme into a zirconia grinding jar and grinding at a frequency of 8 Hz for 5 minutes. The resulting powder is then collected, washed, and stored for further use. The synthesis time is optimized to 5 minutes for industrial applicability. The amount of enzyme loading is controlled, and the encapsulation efficiency and bioactivity are evaluated. The method is shown to be general and can be applied to various enzymes and MOF, demonstrating improved enzyme stability and activity even under harsh conditions. Additionally, the encapsulation of biomolecules within MOFs can improve the sensitivity and selectivity of biosensors for detecting various analytes, making them more reliable and efficient.
Electrospinning is a versatile and scalable method for the synthesis of nanofibers and nanofiber-based composites. This method involves the use of an electric field to draw a polymer solution or melt into a thin fiber. This makes it an ideal method for industrial applications where mass production is required. The resulting nanofiber structure also improves the mechanical properties of the composites, making them suitable for structural applications that demand strength and durability. It can incorporate various functional materials into the nanofibers to enhance the multifunctionality of the composites, allowing them to perform multiple roles within a single material system. The use of electrospinning for the synthesis of MOF–biomass composites can improve the mechanical properties and functionality of the resulting composites.17 Laurila et al.97 reported the in situ crystal growth of HKUST-1 on electrospun cellulose nanofibers. And Li98 showed another in situ growth of HKUST-1 on a composite material consisting of electrospun polyacrylonitrile nanofibers and regenerated cellulose aerogel. In contrast, Bahmani et al.99 discussed the synthesis and characterization of electrospun polyacrylonitrile/cellulose acetate/MIL-125/TiO2 composite nanofibers. These nanofibers are designed to function as efficient photocatalysts and as a system for delivering anticancer drugs.
The synthesis of MOF–biomass composites employs diverse techniques to capitalize on the unique properties of both components, yielding materials with enhanced performance. Methods such as solvothermal/hydrothermal reactions, microwave-assisted synthesis, electrospinning, and mechanochemical approaches facilitate the creation of composites with improved stability, adsorption capabilities, and functional properties. These composites show promise in areas like pollution control, protective gear enhancement, and drug delivery systems, showcasing the potential of MOF–biomass integration across multiple industries.
2.3 Properties of MOFs with different metal ions and organic linkers
MOF–biomass composites represent an innovative class of hybrid materials that integrate the unique characteristics of MOFs with the natural abundance and functionality of biomass derivatives. These composites exhibit a suite of properties that transcend those of their individual components, offering enhanced performance and versatility across various applications.18,67,100
2.3.1 Porosity and surface area: enhancing adsorption capacities.
The marriage of MOFs with biomass materials yields composites with unparalleled porosity and vast surface areas. MOFs, renowned for their tunable porous architecture, can provide a surface area up to several thousand square meters per gram, which is pivotal for gas storage,42 catalytic reactions,101–103 and drug encapsulation.104–106 Tu et al.19 synthesized a ZIF-8/beech composite by an in situ growth strategy, which had a complex network structure, including macropores, mesopores and micropores, and its specific surface area was 130 times higher than that of native beech. The test of carbon dioxide adsorption capacity shows that the adsorption capacity of ZIF-8 can be maintained even after being embedded in the composite. Most importantly, the composite shows excellent mechanical properties, with compressive strength and ultimate tensile stress reaching 100 MPa and 74 MPa respectively, far exceeding those of the existing polymer-derived composites, as shown in Fig. 3c and d. Hu et al.107 prepared a CS-g-UiO-66-NH2 composite by an in situ growth strategy, which had unique structural characteristics, including macroporous, mesoporous and microporous networks. Compared with the unmodified matrix, the specific surface area of this composite significantly increased, and its adsorption performance greatly improved. The theoretical maximum adsorption capacity of UiO-66-NH2 for Cu(II) and Pb(II) reached 364.96 mg g−1 and 555.56 mg g−1, respectively, which showed its high efficiency in removing heavy metal ions in wastewater treatment.
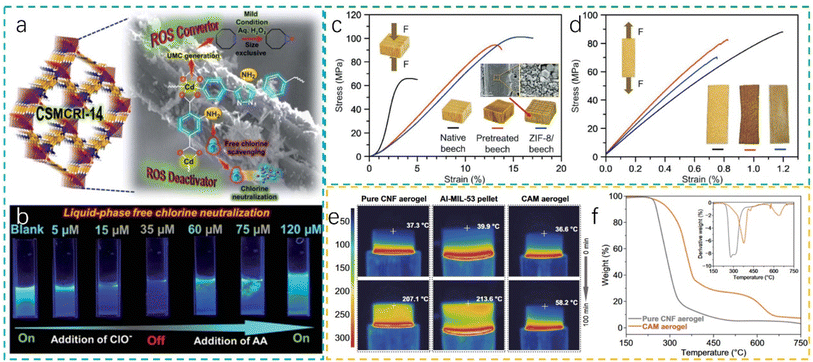 |
| Fig. 3 (a) Graphical representation of the applications carried out using CSMCRI-14 and (b) stepwise liquid-phase free chlorine neutralization via addition of AA in the aqueous phase dispersion of CSMCRI-14 (reproduced from ref. 15 with permission from RSC, copyright 2022); (c and d) compressive and tensile stress–strain curves of native beech, pretreated beech and ZIF-8/beech composite (reproduced from ref. 19 with permission from Wiley, copyright 2020); (e) infrared side-view images of the pure CNF aerogel, the pure Al-MIL-53 pellet, and the CAM aerogel, with the temperature of the top surfaces and (f) TGA analysis curves of the pure CNF and CAM aerogels under air flow (reproduced from ref. 13 with permission from Springer, copyright 2020). | |
2.3.2 Mechanical strength: reinforcing structural integrity.
Biomass polymers like cellulose, chitin, and lignin act as natural reinforcements in MOF–biomass composites, bolstering their mechanical resilience. The CS-g-UiO-66-NH2 composite prepared by Hu et al. not only showed excellent metal ion adsorption, but also excellent mechanical properties.107 Wang et al.9 successfully developed a foam-like composite material composed of highly mesoporous wood and MOF by an in situ growth strategy, which was used to capture carbon dioxide efficiently. The composite TO-wood/Cu3(BTC)2 shows high specific surface area (471 m2 g−1) and high carbon dioxide adsorption capacity (1.46 mmol g−1 at 25 °C and atmospheric pressure). In addition, this composite material was light in weight and extremely strong, which was embodied in the compression test with an elastic modulus of 3034 kN m kg−1 and a yield strength of 68 kN m kg−1. Zeng et al.108 designed a chitosan composite scaffold for both tumor therapy and bone repair. It was found that the strength and compression modulus of CS/Ti-MOF in the longitudinal direction were significantly higher than those of CS, and the compression modulus of CS/Ti-MOF (20%, w/w) increased by 450% compared to CS, which demonstrate that the addition of Ti-MOF significantly enhanced the structural strength and mechanical properties of CS.
2.3.3 Biocompatibility and biodegradability: advancing biomedical solutions.
The incorporation of biomass components, which are inherently biocompatible and biodegradable, broadens the biomedical applications of MOF–biomass hybrids.43,105,109,110 A chitosan composite scaffold (CS/DOX@Ti-MOF) utilizing an in situ growth technique, integrating doxorubicin (DOX) and amino-functionalized titanium-based MOF (NH2-MIL-125(Ti), Ti-MOF) to address postoperative bone tumor management and bone restoration was developed.108 This innovative material boasts a high specific surface area of 1116 m2 g−1, significantly outperforming conventional biomaterials, and exhibits superior biocompatibility. Remarkably, the Ti-MOF can effectively load 322 ± 21 mg g−1 of DOX, showcasing its potent antitumor capabilities. Moreover, the incorporation of DOX@Ti-MOF into the composite scaffold not only enhances its physical and mechanical attributes but also creates a rough surface that facilitates cellular adhesion and proliferation. Consequently, this multifunctional biomaterial is capable of responding to the tumor microenvironment by eliminating residual tumor cells and subsequently promoting bone regeneration by providing a conducive environment for cell attachment, growth, and differentiation.
2.3.4 Functional groups and surface chemistry: tailoring reactivity.
MOFs can be readily functionalized with specific groups to confer tailored chemical properties.105,111 In MOF–biomass systems, the synergy between the MOFs' functional groups and biomass components, such as the interaction of hydroxyl groups in cellulose with metal nodes in MOFs, can lead to the creation of composites with altered hydrophilicity and reactivity.39 This has been exploited in the design of a biosensor platform where a MOF–polysaccharide composite was functionalized to selectively bind and detect heavy metals in water, demonstrating the power of surface chemistry modification for environmental monitoring.112,113 Kayhan et al.114 introduced a cellulose-based probe (Cel-Nap) designed for the selective and sensitive detection of Cr(VI) ions, achieving an LOD of 1.07 μM. The probe was encapsulated within two different MOFs, UiO-66 and ZIF-8, to investigate their antimicrobial properties. Their antimicrobial activity, especially in the presence of Ag+ ions, was significantly enhanced, with ZIF-8-based materials showing superior performance. The study concludes that Cel-Nap could be a valuable tool for detecting toxic Cr(VI) ions and that MOF encapsulation can improve the antimicrobial properties of the materials, potentially reducing the impact of disease-causing microorganisms.
2.3.5 Thermal stability: balancing performance and sustainability.
The thermal stability of MOF–biomass composites is a critical parameter, especially for high-temperature applications. Researchers have used lignin's inherent thermal stability to counterbalance the potentially detrimental effect of some biomass components on MOFs' stability. Djahaniani et al.115 comparing the decomposition onsets of HKUST-1 and MOF segments in L/HKUST-1 (349.60 °C and 359.22 °C, respectively) indicated that lignin improved the thermal stability of the MOF structure by 10 °C. Zhou et al.13 presented the development of a novel nanocomposite material known as CNF@Al-MIL-53 aerogels, which were hybrids of cellulose nanofibers (CNFs) and an aluminum-based MOF. The unique core–shell structure of the CNFs coated with MOF nanolayers contributes to the excellent thermal stability and low thermal conductivity. After CNF@Al-MIL-53 aerogel was placed on a heating table at 300 °C for 30 minutes, the temperature of its top surface only slightly increased to 50 °C, and the temperature remained almost unchanged after 60 minutes, as shown in Fig. 3e and f. The thermal decomposition temperature of the CNF@Al-MIL-53 aerogel is 375 °C, while the thermal decomposition temperature of pure CNF aerogel is 275 °C. Furthermore, β-CD-MOF, developed as a new type of food-acceptable multiporous material, showed better thermal stability, with an initial thermal degradation temperature of 253 °C.116
2.3.6 Optical and magnetic properties: expanding application horizons.
The integration of specific metal ions and strategic design of MOFs, combined with the inherent or modified optical and magnetic properties of biomass, enables MOF–biomass composites to exhibit novel functionalities.117 Jiang et al.73 successfully synthesized a fluorescent bacterial cellulose@Zr-MOF composite via an in situ growth method. This composite possesses a remarkably high specific surface area of 1116 m2 g−1, which is substantially greater than that of Zr-MOF particles alone. Moreover, the composite exhibits strong fluorescence emission and exceptional pH stability. As shown in Fig. 3a and b, Goswami et al.15 fabricated a MOF–cellulose composite via in situ growth, which featured a fluoroswitchable bi-phasic tweezers mechanism for detoxifying free chlorine and selectively catalyzing the insertion of aqueous hydrogen peroxide (Fig. 3a and b). Omer et al.54 fabricated Fe3O4/ZIF-67@AmCs composite beads through a facile method, featuring a hierarchical pore structure and magnetic properties. This structure boasts a Brunauer–Emmett–Teller (BET) surface area of 220.76 m2 g−1 for pristine beads, significantly higher than those of typical polymer-based adsorbents. These characteristics make the Fe3O4/ZIF-67@AmCs composite beads a promising material for the efficient removal of Cr(VI) from aqueous solutions, surpassing many previously reported adsorbents in terms of adsorption capacity and reusability. The combination of magnetic Fe3O4 and chitin not only enhances the stability and adsorption capacity of the adsorbent, but also facilitates solid–liquid separation.118 Mohamed et al.119 presented the synthesis and characterization of a novel nanocomposite, NFe3O4@Zn(GA)/starch–hydrogel, designed for the efficient removal of fluvastatin from water. The composite was created by encapsulating MOFs (Zn(GA)) into starch hydrogel matrices and doping them with magnetic iron oxide nanoparticles using microwave irradiation. The material exhibited a high swelling ratio of 1000.0% under optimal conditions (pH 10, 180 minutes, 25 °C) and achieved equilibrium adsorption of fluvastatin at 782.05 mg g−1 within 30 minutes. The Langmuir isotherm and pseudo-second-order kinetic models best described the adsorption process, and the composite showed excellent regeneration ability over five cycles, demonstrating its potential for practical applications in water treatment.
2.3.7 Synthesis and optimization strategies: innovation for efficiency.
Innovative synthesis techniques, such as green chemistry approaches120 and bioinspired self-assembly,121 are being employed to optimize the fabrication of MOF–biomass composites. Using bio-based solvents in the synthesis process reduces environmental impact and enhances the sustainability profile of the final product, such as hydrothermal method, which is much “greener” than the solvothermal method. By using a one-step hydrothermal process in an acidic environment, a unique Ag-MOF/chitosan composite sponge (Ag-MOF/CSC composite sponge) was effectively created.122 Furthermore, post-synthetic modifications, such as plasma treatment,123 have been shown to enhance the surface properties of composites for specific applications, like improving the wettability for enhanced catalytic performance.
In conclusion, MOF–biomass composites, with their multifaceted properties and application versatility, stand at the forefront of material innovation. As research progresses, these composites are poised to revolutionize fields ranging from sustainable energy storage to precision medicine, underscoring the importance of continuous exploration and optimization of these remarkable hybrid materials.
2.4 Interaction of MOFs with biomass-derived materials and biological molecules
The realm of MOFs in conjunction with biomass-derived materials and biological molecules has sparked significant interest due to the unique synergies that emerge from these interactions. These associations not only underscore the versatility of MOFs in interfacing with natural systems but also pave the way for novel applications in biotechnology, medical science, and environmental remediation.124,125 By delving into the intricate mechanisms governing these interactions, we unravel the potential for designing advanced materials tailored for specific functions within biological contexts.
2.4.1 Fundamentals of interaction: from physical adsorption to chemical bonding.
At the core of MOF–biomass and MOF–biological molecule interactions lie fundamental processes of physical adsorption and chemical bonding. MOFs, with their tunable pore sizes and chemically active surfaces, offer a platform for selective adsorption of biomolecules like proteins, DNA, and enzymes.126 For instance, the hydrophobic cavities in certain MOFs have been exploited to selectively trap and concentrate hydrophobic drugs, demonstrating the potential for controlled drug delivery systems.126
The pore size of MOFs is an important factor affecting their interaction with biomolecules. By adjusting the pore size of MOFs, the selective adsorption of biomolecules with specific size can be realized.127 In addition, the functionalization of MOF surface is also a key factor to regulate their interaction with biomolecules. By introducing specific functional groups (as shown in Fig. 4),62 the interaction between MOFs and biomolecules can be enhanced, thus improving the adsorption efficiency and selectivity.129,130 Some interesting phenomena have been found in the study of the interaction between MOFs and biomolecules. For example, by using specific organic ligands and metal sources, MOFs with specific pore structure and surface functionalization can be synthesized, and these MOFs can effectively adsorb and separate organic dyes44,131,132 and heavy metal ions.107,111,113 In addition, some studies show that MOFs can also be used as drug carriers, and effective drug loading and controlled release can be achieved by adjusting the structure and functionalization of MOFs.133,134
 |
| Fig. 4 The interaction between MOFs and biomolecules. (a) Possible prepared processes and adsorption mechanism of UNCS (Reproduced with permission from ref. 62, Copyright 2023 Elsevier); (b) schematic of the growth mechanism of ZIF-8 and ZIF-67 MOF on CM cotton fabric (Reproduced with permission from ref. 128, Copyright 2021 Elsevier); (c) possible interactions between MOF and CNF in CNF@c-MOF hybrid nanofibers (Reproduced with permission from ref. 20, Copyright 2019 American Chemical Society); (d) possible interactions between MOF and chitosan in the composite (Reproduced with permission from ref. 59, Copyright 2022 Elsevier). | |
2.4.2 Influence of biomass-derived components on MOF interactions.
Biomass derivatives, such as cellulose, hemicellulose, and lignin, when integrated into MOFs, can significantly modulate these interactions, which occur at the interface between the MOF and the biomass component or within the pore channels of the MOF. Cellulose, with its abundance of hydroxyl groups, can facilitate hydrogen bonding with guest molecules, enhancing the affinity of MOFs for polar compounds.135,136 Lignin, a complex biopolymer found in plant cell walls, can be functionalized with specific groups that form strong coordination bonds with metal ions in MOFs,110,137 as shown in Fig. 5. This results in improved interfacial adhesion between the MOF and lignin, enhancing the mechanical properties of the composite material.10,140 In the context of environmental remediation, lignin-MOF67,141 and chitosan-MOF73,130 composites have shown promise in adsorbing toxic dyes and heavy metals from aqueous solutions, demonstrating the value of biomass-derived materials in tuning the selectivity and capacity of MOFs.
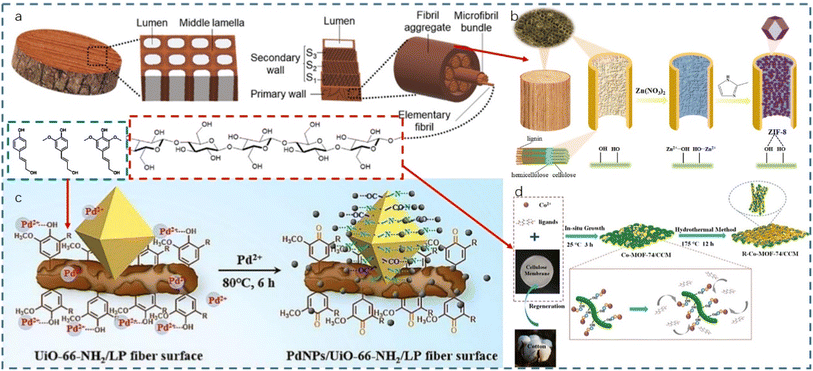 |
| Fig. 5 Chemical structure of wood (a) (reproduced from ref. 138 with permission from RSC, copyright 2022); schematic of the preparation of ZIF-8/wood composites (b) (reproduced from ref. 139 with permission from Elsevier, copyright 2021); binding mechanism of UiO-66NH2 and PdNPs with lignin (c) (reproduced from ref. 89 with permission from Elsevier, copyright 2024); in situ growth of Co-MOF-74 on cellulose (d) (reproduced from ref. 135 with permission from Elsevier, copyright 2021). | |
2.4.3 Linker considerations: bio-degradability and functionality.
The choice of organic linkers also plays a pivotal role in MOF biocompatibility. Linkers derived from bio-renewable resources, such as those based on lignin or cellulose derivatives,87,88 not only reduce environmental impact but also offer tunability for targeted degradation in vivo. Research is focusing on designing linkers that can be enzymatically cleaved, ensuring minimal residual toxicity post-application. There are also some small molecules from biomass reported as linkers, such as cyclodextrin (as shown in Fig. 6A),142,144,145 glutamate,146 and gallic acid.16,104 Abazari et al.147 developed a novel copper-based bio-MOF (bio-MOF(Cu), adenine as the linker)/graphene oxide (GO) nanocomposite with Lewis basic sites, specifically NH2, pyrimidine, and C
O groups, which serve as active centers for CO2 fixation into cyclic carbonates and Knoevenagel condensation reactions. The bio-MOF(Cu)/GO demonstrates exceptional performance in CO2 conversion under mild conditions, achieving over 99.9% conversion with a turnover number (TON) of 525 in a solvent-free reaction at 1 bar CO2 pressure.
 |
| Fig. 6 (A) Schematic diagram of the fabrication of CA/PM/EUG. (Reproduced from ref. 142 with permission from Elsevier, copyright 2024.) (B) Schematic illustration of the preparation of FeTPt@CCM and its capability of synergistic chemotherapy, PDT, and ferroptosis therapy. (a) The design of the multi-bioinspired “Trojan Horse” drug vehicle. (b) The preparation processes of FeTPt through microfluidics, and the generation of FeTPt@CCM through CCM coating. (Reproduced from ref. 143 with permission from Wiley, copyright 2023.) | |
2.4.4 Dynamic interactions and smart material design.
The dynamic nature of MOF–biomolecule interactions opens doors to the design of stimuli-responsive materials. By integrating responsive elements into the MOF structure, researchers can engineer materials that change their properties in response to specific biological cues. pH-responsive MOFs,115,148 for instance, can release encapsulated drugs in acidic tumor microenvironments, highlighting their potential in targeted chemotherapy. Zhang et al.143 detailed the development of a novel multi-bioinspired MOF drug delivery system for multimodal tumor therapy, as shown in Fig. 6B. The system, named FeTPt@CCM, integrates microfluidics technology and cancer cell membrane (CCM) coating to enhance drug delivery efficacy. It contains Fe3+ and meso-tetra(4-carboxyphenyl)porphine (TCPP), and is loaded with oxaliplatin prodrug. The CCM coating improves tumor targeting and stability. The FeTPt@CCM system exhibits the ability to induce ferroptosis, perform photodynamic therapy (PDT), and provide chemotherapeutic activity.
The interface between MOF and biomass-derived materials and biological molecules presents a fertile ground for innovation, pushing the boundaries of materials science towards more sustainable, biocompatible, and intelligent solutions. As our understanding of these interactions deepens and new synthesis strategies emerge, we edge closer to a future where MOF-based materials play a pivotal role in energy, catalysis, advancing healthcare, environmental protection, and beyond. The intricate dance between MOF and biological entities underscores the potential for transformative technologies that harmoniously integrate synthetic and natural systems.
3. Applications of MOFs in biomass materials
The synergy of MOFs with biomass aims to create a new generation of materials with enhanced properties for a multitude of applications, including but not limited to, catalysis,11,100,149 adsorption,19,21,118 energy storage,20,32,150 and environmental remediation.120 This comprehensive exploration delves into the intricate world of MOF–biomass composites, illuminating their potential, advantages, challenges, and the scientific advancements driving this exciting frontier.
3.1 Enhancing biomass properties with MOFs
3.1.1 Tailoring pore size for selective adsorption.
One of the most compelling features of MOFs is their ability to be synthesized with precisely controlled pore sizes, ranging from less than a nanometer to over a hundred nanometers.151–153 This characteristic is crucial in the context of biomass modification, where selective adsorption can significantly improve the efficiency of processes such as gas storage or the removal of contaminants. Abdelhameed et al.70 focused on the development of a highly adsorptive porous membrane made of MOF integrated with cellulose acetate (Cu-BTC@CA) for selectively removing the pesticide dimethoate from wastewater. The micro-crystals of Cu-BTC were effectively immobilized in the macroporous CA membrane with pore diameters between 112.6 and 496.0 nanometers, resulting in a 2.1-fold increase in dimethoate adsorption.
3.1.2 Surface area optimization for enhanced catalytic activity.
The vast surface area of MOFs, often reaching thousands of square meters per gram, plays a pivotal role in enhancing the catalytic activity of biomass composites.6,124,154 MOF-based catalysts, when dispersed uniformly within a biomass matrix, can significantly improve reaction kinetics and selectivity.138,155 Wood, with its natural porosity and structural order, serves as an ideal substrate for synthesizing MOF–wood composites. A recent study by Spieß et al.138 has detailed straightforward wood functionalization techniques employing maleic anhydride (MA) and (3-aminopropyl)triethoxysilane (APTES) to significantly increase the in situ loading of MOFs onto wood substrates. The maleate anchor from MA facilitates the attachment of carboxylate-based MOFs like MIL-53(Al), while the amine group of APTES anchors imidazolate MOFs such as ZIF-8, achieving MOF loadings up to 13 wt%. The performance of these composites was evaluated in the Knoevenagel condensation reaction for catalysis, demonstrating the potential of MOF–wood composites for use in catalytic processes.
3.2 Biomedical applications
3.2.1 Drug delivery systems (DDS).
Extensive scholarly focus has been placed on the development of sophisticated MOFs for the purpose of drug absorption and the establishment of systems that release medication in a controlled manner.156–158 However, the conventional synthesis of MOFs often requires harsh conditions such as high temperatures and pressures, and the use of hazardous solvents, which can restrict their practical use in drug delivery systems (DDSs).143 In the past few years, a novel strategy has been proposed to mitigate the issue of the “burst effect,” which is characterized by the sudden and unregulated release of drugs from the carrier. This strategy entails the combination of porous materials with organic polymers to form hybrid composites.159 As per a comprehensive review of the literature, the integration of polymers or biopolymers into the system can enhance the controlled release characteristics of the drug delivery system.141,160,161 The MOF component provides a porous structure for drug loading, while the biomass component enhances biocompatibility and targeting capabilities. A novel antibacterial agent has been developed through the synthesis of vancomycin-incorporated MOF-modified lignin nanocomposites, demonstrating high performance against drug-resistant bacteria.141 This innovative approach combines the properties of lignin and MOFs to create a synergistic effect that enhances the efficacy of vancomycin. The resulting composite, Lig-Van-MOF, exhibits a six-fold reduction in minimum inhibitory concentration (MIC) compared to free vancomycin and Van-MOF, showing potent antibacterial activity against Staphylococcus aureus and Escherichia coli strains, both sensitive and resistant. Xu et al.162 explored the utilization of a hyaluronic acid-rehabilitated nanoscale MOF containing Fe2+ ions to induce ferroptosis in breast cancer cells effectively and in a biocompatible manner. The research addresses the need to mitigate the side effects of conventional cancer treatments, such as cardiac toxicity associated with anthracycline therapy and cisplatin-induced nephrotoxicity and ototoxicity, by proposing a safer alternative with reduced systemic toxicity. Another drug delivery system using DOX-ZIF-8@Fe3O4/CMC nanoparticles has been developed for enhanced cancer therapy.163 These nanoparticles leverage the Fenton reaction to generate hydroxyl radicals and release doxorubicin in a pH-responsive manner, targeting cancer cells and inducing ferroptosis via the JNK signaling pathway. The therapy shows high efficacy with minimal toxicity in both in vitro and in vivo studies in Pooresmaeil's study.146 Bio-MOF with glutamic acid and copper were synthesized and combined with citric acid-based graphene quantum dots (GQDs) to form GQDs@Bio-MOF(Cu). Naproxen, a nonsteroidal anti-inflammatory drug, was loaded onto the GQDs@Bio-MOF(Cu) with a loading capacity of about 53.1%. To achieve controlled intestinal delivery, the drug-loaded system was coated with carboxymethyl starch (CMS) and chitosan (CS). The resulting CMS@CS/(NAP@GQDs@Bio-MOF(Cu)) demonstrated desirable properties for targeted drug delivery, including gastric protection, biodegradability, biocompatibility, and antibacterial activity, suggesting its potential as an effective pharmaceutical carrier for naproxen. Luo et al.16 presented a study on a novel treatment approach for periodontitis using a combination of a MOF and intelligent responsive hydrogel systems, as shown in Fig. 7a. The MOF, specifically Mg-GA, was synthesized using a hydrothermal method and combined with a smart hydrogel system containing Carboxymethyl Chitosan (CMCS), Dextran (DEX), and 4-formylphenylboronic acid (4-FPBA). This system is designed to respond to the microenvironment of periodontitis by releasing drugs in a controlled manner. When the hydrogel comes into contact with the high pH and ROS levels present in periodontal lesions, the crosslinking network is altered, leading to a change in the hydrogel's structure. This change allows for the controlled and sustained release of the encapsulated therapeutic agents, such as the MOF of Mg-GA. The study demonstrates that this treatment method has strong antibacterial effects, can inhibit the expression of inflammatory genes and proteins, and promotes the regeneration of periodontal bone tissue.
 |
| Fig. 7 (a) The schematic illustration of the preparation, application and bone regeneration promotion mechanism of CSBDX@MOF (reproduced from ref. 16 with permission from Springer Nature, copyright 2024); (b) bio-inspired synergistic antibacterial hydrogel for synergistic antibacterial and whole-process promotion of wound healing (reproduced from ref. 164 with permission from Elsevier, copyright 2023) and (c) the antifouling mechanism (reproduced from ref. 165 with permission from Elsevier, copyright 2023). | |
3.2.2 Tissue engineering.
MOF–biomass composites have been successfully used in tissue engineering applications due to their biocompatibility, mechanical properties, and ability to support cell adhesion and proliferation.166–168 The MOF component provides a scaffold for cell growth, while the biomass component enhances biocompatibility and mechanical stability. Telgerd et al.169 engineered zinc (Zn) and copper (Cu) embedded imidazole-based MOF nanoparticles, which were subsequently deposited onto poly-L-lactic acid (PLLA) nanofiber matrices for applications in bone tissue regeneration. The osteogenic differentiation capacity of the PLLA@MOF composite far surpassed that of both the unmodified PLLA scaffolds and tricalcium phosphate (TCP). This indicates that the integration of the Zn–Cu imidazole MOF onto the PLLA scaffold exerts a pronounced positive influence on the osteogenic potential of mesenchymal stem cells (MSCs). In Barjasteh's study,170 a novel silver-based MOF (SOF) was synthesized and incorporated into chitosan/bacterial cellulose (CS/BC) fibrous composites to create a hybrid antibacterial nanocomposite. The CS/BC-SOF nanocomposites showed uniform distribution of nanoparticles, and good biocompatibility with cell viability of around 94%. They also demonstrated effective antibacterial activity against E. coli and S. aureus, and promoted wound healing and tissue regeneration in animal models, suggesting their potential as advanced wound dressing materials. Wang et al.164 presented the development of a bio-inspired synergistic antibacterial hydrogel (GEL-MOF-rPDA) designed to enhance wound healing through multiple functionalities (Fig. 7b). The chitosan-starch hydrogel was inspired by the natural behavior of spiders and incorporated reduced polydopamine nanoparticles (rPDA) and copper-based MOF (Cu-MOF) to mimic the web-capturing and venom-killing mechanisms of spiders. The rPDA provided antioxidant and antibacterial properties, while Cu-MOF offered additional antibacterial effects and promoted tissue repair. The hydrogel exhibited excellent biocompatibility, hemostatic properties, and the ability to adhere to skin, making it a promising candidate for wound healing applications. In vitro and in vivo studies demonstrated the hydrogel's significant antibacterial activity and its ability to accelerate the healing process, with the potential for clinical use in treating skin wounds.
3.3 Environmental remediation
3.3.1 Water purification.
MOF–biomass composites have established themselves as promising materials extensively utilized in water purification applications, attributed to their superior properties that enable efficient contaminant removal from water.138,139,171Table 1 showcases the notable achievements in research on MOF–biomass composites for adsorbing water pollutants over the past five years. These composites skillfully merge the distinctive attributes of two disparate components: MOF and biomass.172–174
The high porosity and extensive surface area characteristic of MOFs' network structures are pivotal for adsorption processes. They provide a vast surface for the adsorption of various pollutants, encompassing heavy metals(Cr6+,50,54,59 Cu2+,18,49,55 Pb2+,22,63,67,83 As5+,56,64 As3+,61 Hg2+,62,81 Sb3+,57 U6+,58 Co2+ (ref. 51)), dyes (malachite green,52 congo red,45,53,60,82 rhodamine B,23,77 methyl orange,65,71,86,87 methylene blue,75,76,88 acid red44), and organic compounds (dimethoate,70 tetracycline,74,78 formaldehyde,79 chlorobenzene85). The remarkable surface area of MOF//////// facilitates a higher number of binding sites, thereby augmenting total adsorption capacity and efficiency. However, most MOF is in powder form, and it will be difficult to recover if it is directly used for water pollution treatment.
Conversely, biomass, sourced naturally from plant materials, agricultural residues, or microorganisms, significantly contributes to the enhanced stability and biocompatibility of these composites.175 Biomass materials are typically replete with functional groups such as hydroxyls, carboxyls, and amines, which can engage in interactions with both the MOF and the pollutants present in water. This interaction not only bolsters the composite's stability but also facilitates the selective adsorption of specific contaminants. For example, researchers report the development of a novel ZIF-8/wood composite for the removal of water pollutants, specifically focusing on the in situ growth of ZIF-8 within the aligned channels of natural balsa wood.176 This method creates a hierarchical structure with a high surface area, which facilitates efficient and rapid water filtration. The composite displays an excellent affinity and compatibility between the ZIF-8 coating and the wood's lumen, allowing for high-speed water transport. Tested with a 7.9 wt% loading of ZIF-8, a three-layered ZIF-8/wood filter (ZW-2) effectively treated 800 mL of a 10 mg L−1 Cu2+ solution.
Furthermore, incorporating biomass into MOF composites mitigates potential toxicity concerns associated with pristine MOF.152 Certain MOF may harbor heavy metals or other potentially hazardous constituents that could leach out during usage, posing threats to human health and the environment. By amalgamating MOF with biomass, the leaching of these toxic elements can be substantially reduced, rendering the composites safer for environmental applications.
Beyond their high adsorption capacity and enhanced stability, MOF–biomass composites exhibit commendable reusability – as shown in Table 1 – a critical attribute for practical water treatment technologies. Post-contaminant adsorption, these composites can often be regenerated and reused multiple times without a significant decline in performance, curtailing the costs and waste associated with water purification processes.
In summary, the synergistic integration of MOF and biomass within composites furnishes a sustainable and efficacious solution for water purification, tackling the challenge of removing a diverse array of contaminants while maintaining high efficiency, stability, and safety. This innovative approach holds immense promise for the future of water treatment technologies, particularly in addressing global concerns regarding water scarcity and pollution.
3.3.2 Air pollution control.
MOF–biomass composites have been used for air pollution control due to their high adsorption capacity and selectivity for pollutants.128,177,178 The MOF component provides a large surface area for adsorption, while the biomass component enhances stability and reduces toxicity. MOFs, especially ZIFs like ZIF-8 and ZIF-67, have been successfully utilized to functionalize cotton fabric, creating smart textiles capable of adsorbing hazardous organic pollutants from the air. By chemically modifying cotton to incorporate carboxymethyl groups (CM Cotton), researchers have grown ZIF nanoparticles directly onto the fabric's surface using an environmentally friendly technique.128 The resultant MOF-coated textiles have shown remarkable durability during washing and a large surface area that facilitates the adsorption of aromatic pollutants such as aniline, benzene, and styrene. Importantly, these fabrics can be regenerated and reused multiple times without losing their adsorption capacity. The ZIF-8@cellulose fiber filters achieved high filtration efficiencies of 98.36% and 99.94% for 0.3 μm and 0.5 μm particles respectively, under a 134 Pa pressure drop.179 These filters also showed nitrogen adsorption capacities 20 times greater than pure cellulose filters. Furthermore, Ag-MOF@cellulose fibers exhibited potent antimicrobial activity against E. coli with a 20.8 mm inhibition zone diameter. Chen et al.180 detailed the fabrication and application of hierarchically porous HKUST-1@NFC composite membranes for the efficient removal of formaldehyde from indoor air. The membranes are prepared using a green, room-temperature method without DMF and exhibit excellent flexibility and foldability due to their nanofibrillated cellulose (NFC) support. The adsorption capacity of the composite membranes for formaldehyde is attributed to their hierarchical porous structure, which exposes more active sites of HKUST-1 when simultaneously anchored inside and outside the NFC membrane. The results confirm the stability and effectiveness of the HKUST-1 in the adsorption process.
3.4 Energy storage and conversion
3.4.1 Lithium batteries.
The inefficient chemical stability and conductivity restrict the application of MOF materials. At present, the activity and conductivity of MOF materials can be enhanced by adjusting the structure of MOF materials. There are many studies on multifunctional catalytic materials derived from bimetallic MOFs. MOF–biomass composites have been used in energy storage applications due to their high specific surface area, porosity, and conductivity.181,182 MOFs with porous structures, which provide a direct path for ions, promote the rapid migration of ions.183,184 In addition, by adjusting the pore size of MOFs, the movement of ions in nanopores can be effectively controlled, which in turn affects the conductivity and ion transport properties of materials.185 Chao Xu and colleagues150 have developed flexible and foldable electrodes for energy storage devices by weaving together MOF-templated Co–Ni layered double hydroxide (LDH) nanocages, nanocellulose, and carbon nanotubes (CNTs), which exhibit a high areal capacitance of up to 1979 mF cm−2 at a scan rate of 1 mV s−1. Zhang et al.186 developed a high-performance composite membrane composed of a ZIF-8@bacterial cellulose (ZIF-8@BC) matrix and aramid nanofibers (ANFs) filler as the LIB separator via the facile in situ synthesis and subsequent filtration process. The ZIF-8@BC/30%ANF composite separator exhibited good electrolyte wettability and high electrolyte uptake (267.8%), which brought about superior ionic conductivity (1.60 mS cm−1) as shown in Fig. 8a and b. These synergistic advantages eventually endowed the battery with excellent rate capability and cycling performance.
 |
| Fig. 8 (a) Schematic illustration for the preparation of the ZIF-8@BC/ANF composite membrane and its critical role as an LIB separator; (b) microstructure design and strengthening mechanism of the ZIF-8@BC/30%ANF composite separator (reproduced from ref. 186 with permission from Elsevier, copyright 2022). (c) Schematic diagram of the preparation process of the LC@UiO-66-NH2 separator; (d) the Zn deposition process with the LC@UiO-66-NH2 separator; (e) cycling performance of Zn//AC ZHSs with different separators at 1 A g−1 (reproduced from ref. 187 with permission from Wiley, copyright 2023). | |
The MOF exhibits good application prospects in lithium batteries because the efficient ionic sieve can realize selective passage of Li+ and prevent the LiPSs from shuttling to the anode.188–190 The battery separator can be obtained by loading the MOF to the biomass membrane.191 Yan's research explores the use of monodispersed metal–organic framework (MOF)-modified nanofibers as versatile building blocks for constructing separators and composite polymer electrolytes in safe lithium–sulfur batteries.24 The study demonstrates that these nanofibers, derived from bacterial cellulose (BC), exhibit excellent thermal stability and mechanical properties, effectively adsorb lithium polysulfides (LiPSs), and enhance lithium-ion (Li+) transfer and uniform deposition. The resulting BCSZ membrane separator maintains a stable potential for 2500 hours and significantly improves the rate performance and capacity retention of lithium–sulfur batteries. When used as fillers in composite polymer electrolytes, the ionic conductivity and Li+ transference number are enhanced, leading to a stable quasi-solid-state lithium symmetric battery for 3000 hours and a low capacity decay rate of 0.038% per cycle over 800 cycles. This approach shows promising potential for achieving high-performance and safe lithium–sulfur batteries. Ma et al.192 also presented a novel method for preparing multifunctional and flexible composite aerogels by in situ growth of MOF nanoparticles on bacterial cellulose. The composite aerogels, BC@ZIF-8 and BC@UiO-66, exhibit excellent performance in heavy metal ion adsorption and as intermediate layers in high-performance lithium–sulfur batteries, demonstrating low capacity decay rates and effective suppression of polysulfide shuttling.
The electrolyte is designed to address the challenges of uneven magnesium deposition and dendrite formation, which are common issues in LMBs.193 Wang et al.194 presented a study on the preparation and application of a novel 3D-on-1D MOF@cellulose acetate (HCA) gel polymer electrolyte (GPE) in lithium–magnesium hybrid batteries (LMBs). The MOF@HCA GPE is synthesized using a metal ion pre-anchored strategy, which ensures uniform distribution of Mg2+ ions and improves ionic conductivity. MOFs are capable of adsorbing anions, which helps to inhibit their transportation, thus promoting a more homogeneous ion flux and preventing the formation of Mg dendrites. The study demonstrates that this electrolyte significantly enhances the cycling stability and efficiency of LMBs, with a capacity retention of 96% after 600 cycles at 30 °C. The research confirms that the MOF@HCA GPE offers a promising strategy for the design of functional bio-based GPEs and improves the performance of LMBs.
3.4.2 Zinc ion batteries.
Aqueous zinc ion batteries (AZIBs) with cost-effectiveness, intrinsic safety, environmental benignity, easy manufacturing and high specific and volumetric capacity are considered one of the most prospective alternatives for next-generation secondary batteries.195 However, current AZIBs still find it difficult to meet largescale commercial applications, constrained by major challenges from the cathode, electrolyte and zinc anode. Recently, due to the flourishing porous structure, abundant active sites, and versatile functionalization, MOF/MOF-derived nanomaterials have been extensively investigated in cathodes,196–198 anodes199–202 and electrolytes203–205 of AZIBs. As the combination of MOF materials with adjustable channels and flexible polymeric matrix, MOF/nanofiber composite separators enable controllable ion transport behavior, which offers promising candidates for developing novel battery separators.206 Ma et al.187 discussed the development of a novel thin-film separator for aqueous zinc-ion batteries (AZBs), which was composed of an amino-functionalized Zr-based MOF (UiO-66-NH2) and lignocellulose (LC), as shown in Fig. 8c–e. This novel separator, with an ultra-thin thickness of 20 μm, maintained high mechanical strength (47.4 MPa), excellent flexibility, good hydrophilicity, and ionic conductivity of 17.2 mS cm−1. These properties enabled it to effectively prevent the formation of zinc dendrites and reduce parasitic reactions, significantly improving the cycling stability of batteries. In experiments, zinc//zinc batteries using this separator achieved over 2000 hours of stable cycling at a current density of 2 mA cm−2 and a capacity of 2 mA h cm−2, and still maintained dendrite-free characteristics at an ultra-large area capacity of 25 mA h cm−2. Additionally, zinc//MnO2 batteries with this separator showed superior rate performance and cycle life. This work also confirms through theoretical calculations and experimental validation that the channels within UiO-66-NH2 can function as effective desolvation sieves, promoting the transport of zinc ions while blocking larger species, thereby enhancing the efficiency and lifespan of the battery.
3.5 Agriculture
3.5.1 Fertilizers.
MOF–biomass composites have emerged as innovative materials for agricultural applications, particularly as slow-release fertilizers.207,208 The primary advantage of using MOF–biomass composites as slow-release fertilizers lies in their capacity to regulate the release of essential nutrients, such as nitrogen, phosphorus, and potassium, over extended periods. This controlled release mechanism ensures that plants receive a steady supply of nutrients, which can significantly enhance crop growth and yield while minimizing nutrient loss through leaching. Moreover, the integration of biomass into these composites not only enhances their biodegradability and environmental friendliness but also provides additional benefits such as improved soil structure and increased microbial activity. The synergistic effects between MOF and biomass components result in a material that is not only efficient in nutrient delivery but also contributes positively to overall soil health. The MOF component provides a porous structure for nutrient storage, while the biomass component enhances biocompatibility and mechanical stability. A pH-responsive hydrogel was synthesized by integrating cellulose, sodium alginate, and MIL-100(Fe).207 As shown in Fig. 9, a slow-release fertilizer, U-CAM, was developed from this hydrogel, demonstrating controlled urea release that was notably slower at pH 11 compared to pH 3. This makes it suitable for arid environments. The hydrogel enhanced soil water retention, delaying moisture loss. When applied to wheat cultivation, U-CAM improved crop growth and nitrogen accumulation, with the best results seen at a 10% MOF content. The controlled release of nutrients synchronized with plant needs, improving urea utilization efficiency. The hydrogel's interconnected channels and network structure restrained nutrient diffusion, moderating the release rate.
 |
| Fig. 9 Fertilizer: the simplified scheme of the preparation of the U-CAM and its application in the slow release of the urea (reproduced from ref. 207 with permission from Elsevier, copyright 2023); pesticide: schematic diagram for the formation of PYR@UiO-66@HPC and mechanism of PYR release triggered by plant infestation by pathogenic bacteria (reproduced from ref. 209 with permission from Elsevier, copyright 2021). | |
3.5.2 Pesticides.
MOFs, porous, crystalline materials assembled from metal ions and organic linkers, were used to encapsulate and stabilize the active ingredients of pesticides, ensuring their efficacy was maintained over extended periods.210 The encapsulation process involved the trapping of pesticide molecules within the porous structure of MOFs, providing a protective barrier against environmental factors that could otherwise degrade the active compounds. This stabilization is crucial, as it prevents premature degradation of pesticides, which can lead to reduced effectiveness and increased environmental contamination.211,212 By maintaining the integrity of the active ingredients, MOF–biomass composites ensure that pesticides remain potent until they are released under controlled conditions. The controlled release aspect of these composites is achieved through a carefully engineered mechanism that governs the rate at which the pesticide is released into the environment. This can be tailored to match the specific needs of different crops and pests, optimizing the timing and amount of pesticide exposure. For instance, the release can be designed to coincide with peak pest activity periods, thereby maximizing the effectiveness of the treatment while minimizing the total amount of pesticide required. Equally, the incorporation of biomass into the MOF matrix adds an eco-friendly dimension to these composites, reduceing potential long-term environmental impacts associated with synthetic materials. Song et al.213 reported a pH responsive PDS by using a carboxymethyl cellulose (CMC) modified Zr-based MOF (UiO-66-NH2) as the nanocarrier for acetamiprid (ATP). UiO-66-NH2-CMC possesses a large surface area and abundant pores, which can effectively load ATP, and the loading rate is as high as 90.79%. The ATP@UiO-66-NH2-CMC nanopesticide exhibits pH responsive controlled release behavior, and the pesticide ATP can sustained release to the simulated medium. Another pH/cellulase dual-responsive controlled-release pesticide formulation (PYR@UiO-66@HPC), encapsulating pyraclostrobin (PYR) and coated with hydroxypropyl cellulose (HPC) inside a UiO-66 MOF, was developed.209Fig. 9 shows that PYR@UiO-66@HPC releases PYR effectively under acidic and cellulase-rich conditions akin to Rhizoctonia solani infection. It outperforms commercial microcapsules in fungicidal efficacy while showing reduced toxicity to non-target organisms, notably Daphnia magna, with a 4.6-fold decrease in toxicity compared to PYR-TC after 48 hours. The formulation supports rice growth without harming soil microbes and exhibits minimal cytotoxicity in LO2 cells, highlighting its biocompatibility and enhanced human safety. This innovation offers a smart, environmentally friendly approach to managing plant diseases sustainably.
3.6 Food industry
3.6.1 Food packaging.
In order to solve the problem of food spoilage, many researchers have prepared films214,215 and coatings216,217 with various antibacterial agents to prevent the invasion of microorganisms. MOF–biomass composites have emerged as a revolutionary material in the field of food packaging, offering superior barrier properties against gases, moisture, and light. Their intricate porous architecture acts as a physical barrier, effectively preventing the permeation of gases such as oxygen and carbon dioxide, which can cause food spoilage and oxidation. Similarly, MOFs hinder moisture transmission, maintaining the desired texture and freshness of food products for extended periods.25,218,219 As shown in Fig. 10a, through phosphate stimulation, the structure of HKUST-1@CMCS is gradually destroyed, and the intelligent release of antibacterial agents is realized, which can effectively extend the shelf life of foods such as strawberries.219 Another novel cellulose nanocrystal/MOF composite (MC) was developed as a stabilizer for alkenyl succinic anhydride (ASA) pickering emulsions, demonstrating remarkable sizing performance and antimicrobial properties for advanced food packaging applications,220 which is shown in Fig. 10b. The MC-ASA sized paper showed excellent food preservation efficacy, maintaining the freshness of strawberries for up to seven days, compared to ASA-sized paper without MCs. According to Tavassoli's research,221 composite biopolymer films consisting of methylcellulose (MC) and chitosan nanofibers (ChNF) were fabricated, which contained lactoferrin (LAC)-loaded silver-MOF (Ag-MOF) nanoparticles. The Ag-MOFLAC2% films also exhibited strong and long-lasting antibacterial activity against E. coli (19.8 ± 5.2 mm) and S. aureus (20.1 ± 3.2 mm), which was attributed to the slow release of antimicrobial LAC from the films. The composite films were shown to maintain the fresh appearance of apples for at least seven days, which was attributed to their antimicrobial and antioxidant activities. Additionally, the synergy between MOF and biomass results in a material that can be tailored to meet specific packaging requirements. The porosity of MOF can be fine-tuned to achieve desired barrier properties, while the biomass component can be varied to improve mechanical strength or introduce additional functionalities such as antimicrobial properties. Pang et al.142 reported the development of an intelligent active colorimetric film made of cellulose acetate, purple sweet potato anthocyanins, cyclodextrin MOF, and eugenol, designed for pork preservation. The film, which incorporates purple sweet potato anthocyanins (PSPAs) into a cyclodextrin MOF (CD-MOF) and eugenol, enhances the photothermal colorimetric stability of the smart films, allowing for sensitive and reversible color changes in response to pH stimuli. The film also exhibits antioxidant and antibacterial properties, particularly against Escherichia coli and Staphylococcus aureus. The application of the film in pork freshness monitoring and shelf-life extension has been demonstrated to be effective, with the potential to extend the shelf-life of pork by 100% at 25 °C. Khan et al.218 investigateed the effects of a carbon dot-doped Ti-MOF (CD@Ti-MOF) on the properties of CMC/agar films and their application in active packaging for fruit preservation. The CD@Ti-MOF was synthesized via a solvothermal-assisted mechanical stirring method and incorporated into CMC/agar films. The results showed that the addition of CD@Ti-MOF significantly enhanced the mechanical strength, antioxidant activity, water vapor permeability, oxygen permeability, and UV-blocking properties of the films. The films also exhibited strong antibacterial activity against Escherichia coli and Listeria monocytogenes. Additionally, the CMC/agar/CD@Ti-MOF films were tested for their effectiveness in preserving cherry tomatoes at 4 °C for 24 days, demonstrating improved quality retention and extended shelf life.
 |
| Fig. 10 (a) Schematic description of the preparation of HKUST-1@CMCS, the regeneration of HKUST-1@CMCS, phosphate-stimulated drug release without Cu(II) ion residues, and antimicrobial activities and food preservation of dimethyl fumarate-loaded HKUST-1@CMCS film (reproduced from ref. 219 with permission from Elsevier, copyright 2020). (b) A novel cellulose nanocrystal/MOF composite (MC) developed as a stabilizer for alkenyl succinic anhydride (ASA) pickering emulsions for advanced food packaging applications (reproduced from ref. 220 with permission from Elsevier, copyright 2024). | |
3.7 Electronics and sensors
3.7.1 Flexible electronics.
MOF–biomass composites have garnered considerable interest in the field of flexible electronics due to their unique combination of properties that cater to the evolving demands of this advanced technology sector. These composites harness the intrinsic qualities of MOFs, which are known for their structural tunability and large surface areas, alongside the natural benefits of biomass materials, resulting in a versatile class of materials with significant potential for cutting-edge electronic devices.
One of the key attributes that make MOF–biomass composites particularly appealing for flexible electronics is their high conductivity.222 Although MOF themselves may not inherently possess high electrical conductivity, the addition of conductive fillers or the modification of the organic linkers can significantly enhance this property.223–225 When combined with conductive biomass derivatives, such as carbon nanotubes or graphene extracted from plant fibers, the composites exhibit remarkable electrical conductivity, enabling the efficient flow of current even when the material is subjected to deformation. Mechanical flexibility is another critical factor for flexible electronics, and MOF–biomass composites excel in this domain as well. The porous nature of MOFs allows for the accommodation of strain without compromising structural integrity, while the inherent flexibility of biomass components, especially those derived from plant sources, contributes to the overall pliability of the composite.226,227 Wang et al.228 presented a study on the in situ growth of electrically conductive MOFs (EC-MOF) on a wood cellulose scaffold to create flexible, robust, and hydrophobic membranes for use in wearable supercapacitors, as shown in Fig. 11a–c. The research, involves incorporating EC-MOF (NiCAT or CuCAT) onto a porous TEMPO-oxidized wood (TOW) scaffold using electrostatic forces, followed by room-temperature densification to produce ultrathin membranes. These membranes exhibit exceptional mechanical properties, high electrical conductivity, and hydrophobicity, with the potential for improved electrochemical performance over traditional EC-MOF powder electrodes.
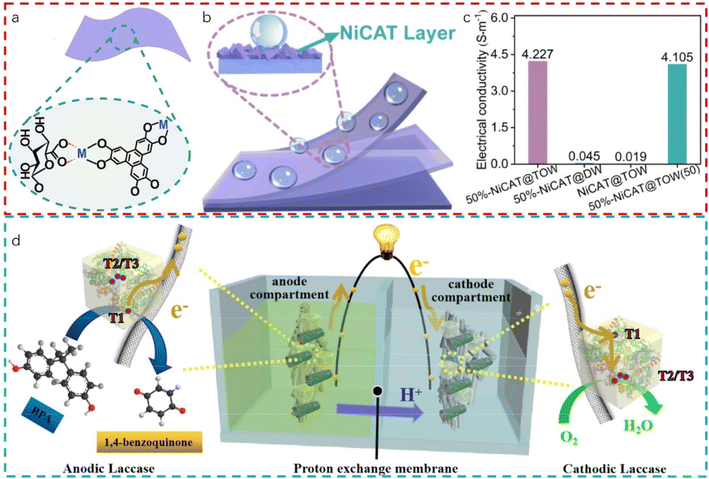 |
| Fig. 11 (a) Schematic illustration of 50%-NiCAT@TOW membrane; (b) schematic diagram of the hydrophobic mechanism of the 50%-NiCAT@TOW membrane; (c) comparison of the electrical conductivity results of 50%-NiCAT@TOW, 50%-NiCAT@DW, NiCAT@TOW membrane and 50%-NiCAT@TOW membrane after 50 times bending with an angle of ∼120 °C (reproduced from ref. 228 with permission from Elsevier, copyright 2024). (d) Schematic of the single-LAC biofuel cell with BPA as fuel and O2 as the final electron acceptor (reproduced from ref. 229 with permission from Elsevier, copyright 2020). | |
Biocompatibility is yet another distinguishing feature of MOF–biomass composites, which is particularly advantageous for applications where direct contact with human skin or biological tissues is involved, such as in biomedical sensors and implants. Researchers have developed conductive metal–organic framework (c-MOF) nanolayers on cellulose nanofibers (CNFs) to create high-performance flexible supercapacitors.20 The authors successfully fabricated CNF@c-MOF hybrid nanofibers through interfacial synthesis, resulting in freestanding nanopapers with high conductivity, hierarchical porosity, mechanical strength, and flexibility. These properties facilitate efficient charge transfer and electrolyte transport, leading to excellent electrochemical performance. The CNF@c-MOF nanopapers exhibit significantly higher conductivity and capacitance compared to pure c-MOF powders and CNF-c-MOF papers, attributed to the continuous c-MOF nanolayers on CNFs. The assembled symmetric supercapacitor based on CNF@Ni-HITP nanopapers demonstrates high stability, mechanical flexibility, and superior electrochemical performance, making it suitable for flexible electronic devices. Moreover, the biodegradability of biomass components in these composites offers an eco-friendly edge, aligning with the growing global push towards sustainable manufacturing practices. This is particularly important in the context of electronic waste management, where the disposal of traditional electronic devices poses significant environmental challenges.230
In summary, the integration of MOFs with biomass materials in composites has opened up new avenues for the development of flexible electronics. These composites, characterized by high conductivity, mechanical flexibility, and biocompatibility, hold great promise for the creation of next-generation electronic devices that are not only technologically advanced but also environmentally responsible. As research progresses, we can expect to see a wider array of applications for MOF–biomass composites in fields ranging from consumer electronics to biomedicine, reflecting their status as a transformative material for the 21st century.
3.7.2 Biosensors.
MOF–biomass composites have become increasingly prevalent in the domain of biosensing technologies, owing to their superior properties that facilitate enhanced detection capabilities.231 These composites are meticulously engineered to combine the distinctive features of MOFs, which are renowned for their high porosity and tunable structures, with the inherent advantages of biomass materials, such as biocompatibility and stability. The amalgamation of these components yields a novel class of materials that exhibits exceptional sensitivity, selectivity, and stability, making them highly suitable for biosensor applications. The MOF component of the composite serves as a scaffold, providing a vast network of pores and cavities that act as binding sites for analytes—the substances of interest in biosensing.232 This porous structure increases the surface area available for interaction, leading to a higher density of binding sites and, consequently, greater sensitivity in detecting low concentrations of analytes. Furthermore, the tunable chemistry of MOF allows for the customization of binding sites to achieve high selectivity, meaning that these composites can be designed to specifically interact with particular biomolecules, such as glucose,233 proteins, or DNA,234,235 while minimizing interference from other substances. On the other hand, the inclusion of biomass in these composites plays a pivotal role in enhancing biocompatibility and stability. This document details the development of an amino-functionalized iron-based MOF, NH2-MIL-88B, for the efficient extraction and ultra-sensitive colorimetric detection of tetracycline (TC) in milk. The material is synthesized using a solvothermal method and incorporates amino groups that enhance the material's binding and catalytic properties towards TC. The resulting sensor demonstrates a low limit of detection (LOD) and high selectivity for TC, with the potential for rapid, on-site detection using a combination of NH2-MIL-88B and TMB anchored in cellulose acetate (CA) membranes. A solid phase extraction method was developed for the simultaneous detection of lead(II) and cadmium(II) ions in food samples using a chitosan/thiol-functionalized MOF composite (CS/MOF-SH) as an adsorbent.236 The method, followed by graphite furnace atomic absorption spectrometry, achieved detection limits of 0.033 μg L−1 for Pb(II) and 0.008 μg L−1 for Cd(II). CS/MOF-SH offered superior adsorption performance and ease of handling. The technique was validated with high accuracy for monitoring trace levels of these heavy metal ions in certified reference materials such as rice, wheat, and tea, showcasing its potential for routine monitoring in real food samples. Li et al.229 encapsulated laccase enzyme within a MOF (ZIF-8) to create a stable biocatalyst (Fig. 11d). This biocatalyst was utilized in a single-enzyme biofuel cell to construct a self-powered biosensor for detecting bisphenol A (BPA). The encapsulation process significantly enhanced the enzyme's stability and enabled the biosensor to exhibit high sensitivity towards BPA.
The integration of MOFs with biomass materials presents a fertile ground for innovation, pushing the boundaries of what is achievable with sustainable materials. As research continues to unravel the complexities of MOF–biomass interactions and refine synthesis techniques, the potential for developing materials with unparalleled performance, sustainability, and functionality becomes increasingly tangible. From catalysis to environmental remediation, the future of MOF–biomass composites promises a transformative impact across multiple industries. As we embark on this journey, addressing the existing challenges and capitalizing on the unique attributes of MOF will be pivotal in realizing a sustainable materials future.
4. Challenges and future perspectives
While MOF–biomass composites have shown significant potential in various applications, there are still several challenges that need to be addressed for their widespread adoption and commercialization. In this section, we will discuss the main challenges and outline the future perspectives for MOF–biomass composites' research.
4.1 Challenges
(1) Scalability and cost-effectiveness: current synthesis methods for MOF–biomass composites often involve complex and time-consuming processes that limit their scalability and economic viability. Developing efficient and cost-effective synthesis routes is crucial for the commercialization of these materials. Currently, the synthesis of MOF–biomass composites using hydrothermal or solvothermal methods is often time-consuming, with processes lasting from several hours to multiple days. This extended duration raises the cost of synthesis. Additionally, the substantial use of solvents in these methods exerts environmental pressure due to the potential for solvent waste and its associated environmental impact.
(2) Stability and durability: MOF–biomass composites may face issues related to stability and durability under various environmental conditions, especially in harsh or dynamic environments. Ensuring the long-term stability and durability of these materials is essential for their practical applications.
(3) Toxicity and biocompatibility: although MOF–biomass composites generally exhibit good biocompatibility, concerns regarding their toxicity, especially for biomedical applications, must be thoroughly investigated. Comprehensive toxicity assessments are required to ensure their safe use in various applications.
(4) Mechanical properties: the mechanical properties of MOF–biomass composites can be limited due to the brittle nature of MOFs. Improving the mechanical properties, such as flexibility and toughness, is necessary for applications requiring robust materials.
(5) Functionalization and tunability: while MOF–biomass composites can be functionalized for specific applications, achieving precise control over their properties remains challenging. Developing methods for fine-tuning the properties of these materials is critical for their optimal performance in various applications.
4.2 Future perspectives
(1) Advanced synthesis techniques: developing innovative synthesis techniques that enable the large-scale production of MOF–biomass composites while maintaining their properties is a key area for future research. This includes exploring one-pot synthesis methods, continuous flow processes, and green chemistry approaches. For instance, Li et al.26 prepared scalable multifunctional MOF–textiles with excellent ultraviolet (UV) resistance, organic contamination degradation, antibacterial activity, self-cleaning, antifouling, and oil-water separation performances.
(2) Enhanced stability and durability: research efforts should focus on improving the stability and durability of MOF–biomass composites under various environmental conditions. This can be achieved by modifying the MOF structure, optimizing the composite composition, and incorporating protective coatings. This can involve the introduction of more robust metal nodes or the use of stronger organic linkers, which can significantly bolster the composite's resilience. The ratio of biomass to MOF components should be fine-tuned to achieve a balance between biodegradability and long-term performance. The incorporation of additives or cross-linking agents can also reinforce the composite, making it more resistant to environmental stressors such as moisture, temperature fluctuations, and chemical exposure.80 The application of protective coatings can provide an additional layer of defense against environmental factors that might compromise the integrity of the composite. These coatings can be designed to be resistant to UV radiation, water, and microbial attack, thereby extending the service life of the MOF–biomass composites.
(3) Comprehensive toxicity assessments: conducting thorough toxicity assessments, including long-term studies and in vivo evaluations, is essential to ensure the safe use of MOF–biomass composites in various applications, particularly in biomedical and food-related areas. Long-term studies provide insights into the chronic effects of these composites, which are crucial for understanding their potential impacts over extended periods of exposure. In vivo evaluations, on the other hand, offer a direct assessment of the composites' toxicity within living organisms, allowing researchers to observe biological responses and potential adverse effects in real-time. These assessments are vital for ensuring that MOF–biomass composites do not pose a threat to human health or the environment.162 By conducting these thorough evaluations, researchers can develop guidelines for safe usage and establish a foundation for the responsible integration of MOF–biomass composites into various applications, thereby supporting both innovation and safety in materials science.
(4) Tunable and functional materials: advancing the functionalization and tunability of MOF–biomass composites through the use of smart materials, responsive linkers, and stimuli-responsive properties will enable their customization for specific applications. Smart materials, known for their ability to mimic biological behavior and respond to external stimuli such as temperature, humidity, and pressure, can be integrated into MOF–biomass composites to create intelligent, responsive materials that adapt to their environment. This integration allows for the development of composites that can change their properties in response to specific triggers, enhancing their versatility and efficiency in targeted applications. The incorporation of stimuli-responsive properties into MOF–biomass composites enables them to exhibit changes in their structure or chemical composition when exposed to specific stimuli. This can lead to the development of materials that are self-healing, self-cleaning, or that can actively respond to pollutants in the environment, making them highly customizable for a wide range of applications.16
(5) Sustainable development: focusing on the sustainable production and disposal of MOF–biomass composites is essential for minimizing their environmental impact. This includes utilizing renewable resources, developing biodegradable composites, and implementing circular economy principles. Harnessing renewable resources like agricultural byproducts and plant residues for MOF–biomass composites not only cuts reliance on fossil fuels but also sustains agricultural and forest ecosystems. These biomass-derived materials are a greener, cost-effective substitute for petroleum-based polymers in materials science. The creation of biodegradable MOF–biomass composites is pivotal for curbing environmental pollution. Unlike synthetic materials that linger and pollute, biomass materials can be broken down by natural microorganisms, turning into harmless natural byproducts. This makes them ideal for disposable items and packaging, reducing plastic dependence and pollution.218 Incorporating circular economy principles into MOF–biomass composites' lifecycle is crucial for sustainability. This includes recycling bio-based components, a key aspect of a circular economy. Innovative recycling technologies and the use of novel biocomposites can decrease waste and environmental impact, aligning biocomposite development with a circular model for eco-friendly production.
5. Conclusion
In conclusion, the integration of MOF with biomass materials offers a promising approach for the development of novel composites with enhanced properties and functionalities. The tunable properties of MOFs allow for precise control over the modification effects, while the sustainable nature of biomass materials provides cost-effective and renewable sources for the production of these composites. However, several challenges remain to be addressed for the widespread application of MOF–biomass composites, including optimizing the synthesis conditions, improving the compatibility between MOF and biomass matrixes, and developing green and sustainable synthesis methods.
Future research should focus on addressing these challenges and exploring the potential applications of MOF–biomass composites in emerging fields such as energy, catalysis, and biomedicine. The development of novel MOF structures and compositions, as well as hierarchical and composite MOF structures, will further enhance the performance of these materials and expand their applications. Ultimately, the integration of MOF with biomass materials has the potential to revolutionize various industries and contribute to the development of a more sustainable and environmentally friendly future.
Data availability
Data sharing is not applicable to this article as no datasets were generated or analyzed during the current study.
Conflicts of interest
The authors declare that they have no known competing financial interests or personal relationships that could have appeared to influence the work reported in this paper.
Acknowledgements
This work was supported by the Natural Science Foundation of Fujian Province (2021J01107) and China Postdoctoral Science Foundation (2020M682603).
References
- A. Saravanakumar, P. Vijayakumar, A. T. Hoang, E. E. Kwon and W.-H. Chen, Bioresour. Technol., 2023, 370, 128562 CrossRef CAS PubMed.
- Z. Cheng, X. Li, L. Zhang, Z. Yuan, H. Zheng, H. Guo, X. Zhao, J. Chen, Y. Pan, X. Chen, Y. Feng, Z. Luo, G. Tang, X. Jin and J. He, Chem. Eng. J., 2023, 475, 145912 CrossRef CAS.
- Y. Lu, C. Liu, C. Mei, J. Sun, J. Lee, Q. Wu, M. A. Hubbe and M.-C. Li, Coord. Chem. Rev., 2022, 461, 214496 CrossRef CAS.
- H. N. Abdelhamid and A. P. Mathew, Coord. Chem. Rev., 2022, 451, 214263 CrossRef CAS.
- V. Atiroğlu, A. Atiroğlu and M. Özacar, Food Chem., 2021, 349, 129127 CrossRef PubMed.
- Y. H. Cheung, K. Ma, M. C. Wasson, X. Wang, K. B. Idrees, T. Islamoglu, J. Mahle, G. W. Peterson, J. H. Xin and O. K. Farha, Angew. Chem., Int. Ed., 2022, 61, e202202207 CrossRef CAS PubMed.
- G. W. Peterson, D. T. Lee, H. F. Barton, T. H. Epps and G. N. Parsons, Nat. Rev. Mater., 2021, 6, 605–621 CrossRef CAS.
- H. Kim, S. Yang, S. R. Rao, S. Narayanan, E. A. Kapustin, H. Furukawa, A. S. Umans, O. M. Yaghi and E. N. Wang, Science, 2017, 356, 430–434 CrossRef CAS PubMed.
- S. Wang, C. Wang and Q. Zhou, ACS Appl. Mater. Interfaces, 2021, 13, 29949–29959 CrossRef CAS PubMed.
- J. Su, X. Yang, H. Shi, S. Yao and M. Zhou, J. Colloid Interface Sci., 2024, 669, 336–348 CrossRef CAS PubMed.
- V. V. Karve, D. T. Sun, O. Trukhina, S. Yang, E. Oveisi, J. Luterbacher and W. L. Queen, Green Chem., 2020, 22, 368–378 RSC.
- S. Javanbakht, M. Pooresmaeil, H. Hashemi and H. Namazi, Int. J. Biol. Macromol., 2018, 119, 588–596 CrossRef CAS PubMed.
- S. Zhou, V. Apostolopoulou-Kalkavoura, M. V. Tavares Da Costa, L. Bergström, M. Strømme and C. Xu, Nano-Micro Lett., 2020, 12, 9 CrossRef PubMed.
- G. W. Peterson, D. T. Lee, H. F. Barton, T. H. Epps and G. N. Parsons, Nat. Rev. Mater., 2021, 6, 605–621 CrossRef CAS.
- R. Goswami, B. D. Bankar, S. Rajput, N. Seal, R. S. Pillai, A. V. Biradar and S. Neogi, J. Mater. Chem. A, 2022, 10, 4316–4332 RSC.
- Q. Luo, Y. Yang, C. Ho, Z. Li, W. Chiu, A. Li, Y. Dai, W. Li and X. Zhang, J. Nanobiotechnol., 2024, 22, 287 CrossRef CAS PubMed.
- W. Lu, C. Duan, Y. Zhang, K. Gao, L. Dai, M. Shen, W. Wang, J. Wang and Y. Ni, Carbohydr. Polym., 2021, 258, 117676 CrossRef CAS PubMed.
- D. Li, X. Tian, Z. Wang, Z. Guan, X. Li, H. Qiao, H. Ke, L. Luo and Q. Wei, Chem. Eng. J., 2020, 383, 123127 CrossRef CAS.
- K. Tu, B. Puértolas, M. Adobes-Vidal, Y. Wang, J. Sun, J. Traber, I. Burgert, J. Pérez-Ramírez and T. Keplinger, Adv. Sci., 2020, 7, 1902897 CrossRef CAS PubMed.
- S. Zhou, X. Kong, B. Zheng, F. Huo, M. Strømme and C. Xu, ACS Nano, 2019, 13, 9578–9586 CrossRef CAS PubMed.
- T. Saeed, A. Naeem, I. U. Din, M. Farooq, I. W. Khan, M. Hamayun and T. Malik, J. Hazard. Mater., 2022, 427, 127902 CrossRef CAS PubMed.
- N. Wang, X.-K. Ouyang, L.-Y. Yang and A. M. Omer, ACS Sustainable Chem. Eng., 2017, 5, 10447–10458 CrossRef CAS.
- S. Ma, M. Zhang, J. Nie, J. Tan, S. Song and Y. Luo, Carbohydr. Polym., 2019, 208, 328–335 CrossRef CAS PubMed.
- K. Yan, C. Shen, H. Wang, F. Tao, C. Zhou, C. Dong, G. Zhang, X. Chen, L. Zhang, Y. Luo and X. Xu, ACS Appl. Mater. Interfaces, 2023, 15, 29094–29101 CrossRef CAS PubMed.
- S. Feng, Q. Tang, Z. Xu, K. Huang, H. Li and Z. Zou, Food Hydrocolloids, 2023, 135, 108193 CrossRef CAS.
- W. Li, Z. Yu, Y. Zhang, C. Lv, X. He, S. Wang, Z. Wang, B. He, S. Yuan, J. Xin, Y. Liu, T. Zhou, Z. Li, S. C. Tan and L. Wei, Nat. Commun., 2024, 15, 5297 CrossRef CAS PubMed.
- Y. Song, H. Li, T. Shan, P. Yang, S. Li, Z. Liu, C. Liu and C. Shen, Carbohydr. Polym., 2023, 302, 120377 CrossRef CAS PubMed.
- L. E. Lange and S. K. Obendorf, ACS Appl. Mater. Interfaces, 2015, 7, 3974–3980 CrossRef CAS PubMed.
- H. Zhu, X. Yang, E. D. Cranston and S. Zhu, Adv. Mater., 2016, 28, 7652–7657 CrossRef CAS PubMed.
- J. Ko, S. K. Kim, Y. Yoon, K. H. Cho, W. Song, T.-H. Kim, S. Myung, S. S. Lee, Y. K. Hwang, S.-W. Kim and K.-S. An, Mater. Today Energy, 2018, 9, 11–18 CrossRef.
- Z. Kang, L. Fan and D. Sun, J. Mater. Chem. A, 2017, 5, 10073–10091 RSC.
- K. Tu, Y. Ding and T. Keplinger, Carbohydr. Polym., 2022, 291, 119539 CrossRef CAS PubMed.
- F. S. Arghavan, T. J. Al-Musawi, G. A. Rumman, R. Pelalak, A. Khataee and N. Nasseh, J. Environ. Chem. Eng., 2021, 9, 105619 CrossRef CAS.
- R. Fang, A. Dhakshinamoorthy, Y. Li and H. Garcia, Chem. Soc. Rev., 2020, 49, 3638–3687 RSC.
- A. Herbst and C. Janiak, Crystengcomm, 2017, 19, 4092–4117 RSC.
- N. C. Burtch, H. Jasuja and K. S. Walton, Chem. Rev., 2014, 114, 10575–10612 CrossRef CAS PubMed.
- Y. Xiong, Y. Fan, D. Damasceno Borges, C. Chen, Z. Wei, H. Wang, M. Pan, J. Jiang, G. Maurin and C. Su, Chem.–A Euro. J., 2016, 22, 16147–16156 CrossRef CAS PubMed.
- Z. Kang, L. Fan and D. Sun, J. Mater. Chem. A, 2017, 5, 10073–10091 RSC.
- X.-F. Zhang, Z. Wang, M. Ding, Y. Feng and J. Yao, J. Mater. Chem. A, 2021, 9, 23353–23363 RSC.
- G. Khandelwal, N. P. Maria Joseph Raj and S.-J. Kim, J. Mater. Chem. A, 2020, 8, 17817–17825 RSC.
- D. E. Jaramillo, D. A. Reed, H. Z. H. Jiang, J. Oktawiec, M. W. Mara, A. C. Forse, D. J. Lussier, R. A. Murphy, M. Cunningham, V. Colombo, D. K. Shuh, J. A. Reimer and J. R. Long, Nat. Mater., 2020, 19, 517–521 CrossRef CAS PubMed.
- H. Li, L. Li, R.-B. Lin, W. Zhou, Z. Zhang, S. Xiang and B. Chen, EnergyChem, 2019, 1, 100006 CrossRef PubMed.
- M. Wu and Y. Yang, Adv. Mater., 2017, 29, 1606134 CrossRef PubMed.
- Y. Wang, K. Wang, J. Lin, L. Xiao and X. Wang, Int. J. Biol. Macromol., 2020, 165, 2684–2692 CrossRef CAS PubMed.
- L. Liu, Y. Ma, W. Yang, C. Chen, M. Li, D. Lin and Q. Pan, New J. Chem., 2020, 44, 15459–15466 RSC.
- K. J. Fernández-Andrade, A. A. Fernández-Andrade, L. Á. Zambrano-Intriago, L. E. Arteaga-Perez, S. Alejandro-Martin, R. J. Baquerizo-Crespo, R. Luque and J. M. Rodríguez-Díaz, Chemosphere, 2023, 314, 137664 CrossRef PubMed.
- T.-H. Wei, S.-H. Wu, Y.-D. Huang, W.-S. Lo, B. P. Williams, S.-Y. Chen, H.-C. Yang, Y.-S. Hsu, Z.-Y. Lin, X.-H. Chen, P.-E. Kuo, L.-Y. Chou, C.-K. Tsung and F.-K. Shieh, Nat. Commun., 2019, 10, 5002 CrossRef PubMed.
- B. Li, Y. Zhang, D. Ma, L. Li, G. Li, G. Li, Z. Shi and S. Feng, Chem. Commun., 2012, 48, 6151 RSC.
- Q. Kong, H. Zhang, P. Wang, Y. Lan, W. Ma and X. Shi, Int. J. Biol. Macromol., 2023, 244, 125169 CrossRef CAS PubMed.
- C. Niu, N. Zhang, C. Hu, C. Zhang, H. Zhang and Y. Xing, Carbohydr. Polym., 2021, 258, 117644 CrossRef CAS PubMed.
- H. Nasser Abdelhamid, S. Sultan and A. P. Mathew, Chem. Eng. J., 2023, 468, 143567 CrossRef CAS.
- N. M. Mahmoodi, M. Oveisi, A. Taghizadeh and M. Taghizadeh, Carbohydr. Polym., 2020, 227, 115364 CrossRef CAS PubMed.
- L. Wen, X. Chen, C. Chen, R. Yang, M. Gong, Y. Zhang and Q. Fu, Arabian J. Chem., 2020, 13, 5669–5678 CrossRef CAS.
- A. M. Omer, E. M. Abd El-Monaem, M. M. Abd El-Latif, G. M. El-Subruiti and A. S. Eltaweil, Carbohydr. Polym., 2021, 265, 118084 CrossRef CAS PubMed.
- C. Wang, Q. Sun, L. Zhang, T. Su and Y. Yang, J. Environ. Chem. Eng., 2022, 10, 107911 CrossRef CAS.
- E. Bahmani, S. Koushkbaghi, M. Darabi, A. ZabihiSahebi, A. Askari and M. Irani, Carbohydr. Polym., 2019, 224, 115148 CrossRef CAS PubMed.
- N. Xiong, P. Wan, G. Zhu, F. Xie, S. Xu, C. Zhu and A. S. Hursthouse, Sep. Purif. Technol., 2020, 236, 116266 CrossRef CAS.
- X. Guo, H. Yang, Q. Liu, J. Liu, R. Chen, H. Zhang, J. Yu, M. Zhang, R. Li and J. Wang, Chem. Eng. J., 2020, 382, 122850 CrossRef CAS.
- F. M. Valadi, S. Shahsavari, E. Akbarzadeh and M. R. Gholami, Carbohydr. Polym., 2022, 288, 119383 CrossRef CAS PubMed.
- Y. Jin, Y. Li, Q. Du, B. Chen, K. Chen, Y. Zhang, M. Wang, Y. Sun, S. Zhao, Z. Jing, J. Wang, X. Pi and Y. Wang, Microporous Mesoporous Mater., 2023, 348, 112404 CrossRef CAS.
- Y. Wei, R. Zou, Y. Xia, Z. Wang, W. Yang, J. Luo and C. Liu, Mater. Today Chem., 2022, 26, 101091 CrossRef CAS.
- X. Yan and H. Ge, Int. J. Biol. Macromol., 2023, 232, 123329 CrossRef CAS PubMed.
- Y. Ma, D. You, Y. Fang, J. Luo, Q. Pan, Y. Liu, F. Wang and W. Yang, Sep. Purif. Technol., 2022, 294, 121223 CrossRef CAS.
- M. Schelling, M. Kim, E. Otal, M. Aguirre and J. P. Hinestroza, Cellulose, 2020, 27, 6399–6410 CrossRef CAS.
- T. Hashem, A. H. Ibrahim, C. Wöll and M. H. Alkordi, ACS Appl. Nano Mater., 2019, 2, 5804–5808 CrossRef CAS.
- C. Lei, J. Gao, W. Ren, Y. Xie, S. Y. H. Abdalkarim, S. Wang, Q. Ni and J. Yao, Carbohydr. Polym., 2019, 205, 35–41 CrossRef CAS PubMed.
- Y. Gu, Y. Wang, H. Li, W. Qin, H. Zhang, G. Wang, Y. Zhang and H. Zhao, Chem. Eng. J., 2020, 387, 124141 CrossRef CAS.
- Q. Liu, H. Yu, F. Zeng, X. Li, J. Sun, C. Li, H. Lin and Z. Su, Carbohydr. Polym., 2021, 255, 117402 CrossRef CAS PubMed.
- X. Li, L. Wang, S. Li, S. Yu, Z. Liu, Q. Liu and X. Dong, Int. J. Biol. Macromol., 2024, 274, 133381 CrossRef CAS PubMed.
- R. M. Abdelhameed, H. Abdel-Gawad and H. E. Emam, J. Environ. Chem. Eng., 2021, 9, 105121 CrossRef CAS.
- Z. Yuan, F. Li, X. Zhang, M.-C. Li, Y. Chen, C. F. D. Hoop, J. Qi and X. Huang, Environ. Res., 2024, 248, 118263 CrossRef CAS PubMed.
- Y. Lin, Q. Wang, Y. Huang, J. Du, Y. Cheng, J. Lu, Y. Tao and H. Wang, Int. J. Biol. Macromol., 2023, 247, 125559 CrossRef CAS PubMed.
- S. Jiang, Z. Yan, Y. Deng, W. Deng, H. Xiao and W. Wu, Int. J. Biol. Macromol., 2024, 262, 129854 CrossRef CAS PubMed.
- A. Liu, J. Liu, S. He, J. Zhang and W. Shao, Int. J. Biol. Macromol., 2023, 225, 40–50 CrossRef CAS PubMed.
- S. Abbasi, Sci. Rep., 2024, 14, 14497 CrossRef CAS PubMed.
- S. V. Kamath, J. R. Attokkaran, A. S. Maraddi, A. Samage, G. B. D'Souza, H. Yoon and S. K. Nataraj, Chem. Eng. J., 2024, 479, 147805 CrossRef CAS.
- H. Yang, P. Zhang, Q. Zheng, M. U. Hameed and S. Raza, Int. J. Biol. Macromol., 2023, 253, 126986 CrossRef CAS PubMed.
- A. Ehsani, H. Aghdasinia, M. E. Farshchi, S. Rostamnia and A. Khataee, Surf. Interfaces, 2023, 36, 102506 CrossRef CAS.
- W. Qu, Z. Wang, M. Qin, X. Yang, F. Zhang, Z. Wang, D. Ji and D. Yu, Sep. Purif. Technol., 2023, 325, 124673 CrossRef CAS.
- J. Zhao, J. He, L. Liu, S. Shi, H. Guo, L. Xie, X. Chai, K. Xu, G. Du and L. Zhang, Sep. Purif. Technol., 2023, 327, 124942 CrossRef CAS.
- A. M. Munshi, N. A. Alamrani, H. Alessa, M. Aljohani, S. F. Ibarhiam, F. A. Saad, S. D. Al-Qahtani and N. M. El-Metwaly, Cellulose, 2023, 30, 7235–7250 CrossRef CAS.
- F. Aghaei, S. Tangestaninejad, M. Bahadori, M. Moghadam, V. Mirkhani, I. Mohammadpoor−Baltork, M. Khalaji and V. Asadi, J. Colloid Interface Sci., 2023, 648, 78–89 CrossRef CAS PubMed.
- H. Zhao, J. Sun, Y. Du, M. Zhang, Z. Yang, J. Su, X. Peng, X. Liu, G. Sun and Y. Cui, J. Solid State Chem., 2023, 322, 123928 CrossRef CAS.
- Z. Qiu, F. Gao, Y. Zhang, J. Li, Y. You, X. Lv and J. Dang, Sep. Purif. Technol., 2024, 338, 126478 CrossRef CAS.
- Y. Hu, Y. Zhou, Z. Yang, F. Ren, Z. Chen, Y. Fu, R. Dong, L. Wang, Q. Zhou and H. Qin, J. Mater. Sci., 2022, 57, 1536–1544 CrossRef CAS.
- C. Wang, C. Xing, X. Feng, S. Shang, H. Liu, Z. Song and H. Zhang, Int. J. Biol. Macromol., 2023, 250, 126092 CrossRef CAS PubMed.
- C. Wang, X. Feng, Y. Tian, X. Huang, S. Shang, H. Liu, Z. Song and H. Zhang, Environ. Res., 2024, 251, 118651 CrossRef CAS PubMed.
- C. Wang, X. Feng, S. Shang, H. Liu, Z. Song and H. Zhang, Bioresour. Technol., 2023, 388, 129781 CrossRef CAS PubMed.
- L. Zhang, Y. Huang, J. Zhang, E. Zhu, J. Ma and Z. Wang, Int. J. Biol. Macromol., 2024, 255, 128187 CrossRef CAS PubMed.
- H.-T. T. Nguyen, K.-N. T. Tran, L. Van Tan, V. A. Tran, V.-D. Doan, T. Lee and T. D. Nguyen, Mater. Chem. Phys., 2021, 272, 125040 CrossRef CAS.
- Z. Zhao, H. Li, K. Zhao, L. Wang and X. Gao, Chem. Eng. J., 2022, 428, 131006 CrossRef CAS.
- R. Vakili, S. Xu, N. Al-Janabi, P. Gorgojo, S. M. Holmes and X. Fan, Microporous Mesoporous Mater., 2018, 260, 45–53 CrossRef CAS.
- N. Couzon, M. Ferreira, S. Duval, A. El-Achari, C. Campagne, T. Loiseau and C. Volkringer, ACS Appl. Mater. Interfaces, 2022, 14, 21497–21508 CrossRef CAS PubMed.
- G. Kaur, A. Anthwal, P. Kandwal and D. Sud, Inorg. Chim. Acta, 2023, 545, 121248 CrossRef CAS.
- P. A. Julien, K. Užarević, A. D. Katsenis, S. A. J. Kimber, T. Wang, O. K. Farha, Y. Zhang, J. Casaban, L. S. Germann, M. Etter, R. E. Dinnebier, S. L. James, I. Halasz and T. Friščić, J. Am. Chem. Soc., 2016, 138, 2929–2932 CrossRef CAS PubMed.
- S. A. Noorian, N. Hemmatinejad and J. A. R. Navarro, Microporous Mesoporous Mater., 2020, 302, 110199 CrossRef CAS.
- E. Laurila, J. Thunberg, S. P. Argent, N. R. Champness, S. Zacharias, G. Westman and L. Öhrström, Adv. Eng. Mater., 2015, 17, 1282–1286 CrossRef CAS.
- X. Li, L. Wang, S. Li, S. Yu, Z. Liu, Q. Liu and X. Dong, Int. J. Biol. Macromol., 2024, 274, 133381 CrossRef CAS PubMed.
- E. Bahmani, H. Seyyed Zonouzi, S. Koushkbaghi, F. Keyvani Hafshejani, A. Fassadi Chimeh and M. Irani, Cellulose, 2020, 27, 10029–10045 CrossRef CAS.
- R. M. Abdelhameed, M. El-Shahat and H. E. Emam, Carbohydr. Polym., 2020, 247, 116695 CrossRef CAS PubMed.
- M. Yousefian and Z. Rafiee, Carbohydr. Polym., 2020, 228, 115393 CrossRef PubMed.
- X. Shen, C. Zhang, B. Han and F. Wang, Chem. Soc. Rev., 2022, 51, 1608–1628 RSC.
- Y. Wang, Z. Tang, M. Chen, J. Zhang, J. Shi, C. Wang, Z. Yang and J. Wang, Energy Convers. Manage., 2020, 222, 113227 CrossRef CAS.
- H. Hamedi, S. Javanbakht and R. Mohammadi, J. Ind. Eng. Chem., 2024, 133, 454–463 CrossRef CAS.
- Y. Hassanpouraghdam, M. Pooresmaeil and H. Namazi, Int. J. Biol. Macromol., 2022, 221, 256–267 CrossRef CAS PubMed.
- M. Kim, L. K. Njaramba, Y. Yoon, M. Jang and C. M. Park, Carbohydr. Polym., 2024, 324, 121436 CrossRef CAS PubMed.
- S. Hu, T. Huang, N. Zhang, Y. Lei and Y. Wang, Carbohydr. Polym., 2022, 277, 118809 CrossRef CAS PubMed.
- Y. Zeng, J. Yuan, Z. Ran, X. Zhan, X. Li, H. Ye, J. Dong, G. Cao, Z. Pan, Y. Bao, J. Tang, X. Liu and Y. He, Int. J. Biol. Macromol., 2024, 263, 130368 CrossRef CAS PubMed.
- Z. Ansari-Asl, Z. Shahvali, R. Sacourbaravi, E. Hoveizi and E. Darabpour, Microporous Mesoporous Mater., 2022, 336, 111866 CrossRef CAS.
- R. Li, D. Huang, L. Lei, S. Chen, Y. Chen, G. Wang, L. Du, W. Zhou, J. Tao and H. Chen, J. Mater. Chem. A, 2023, 11, 2595–2617 RSC.
- P. Shi, X. Hu and M. Duan, J. Cleaner Prod., 2021, 290, 125794 CrossRef CAS.
- H. M. Nassef, G. A. A. M. Al-Hazmi, A. A. Alayyafi, M. G. El-Desouky and A. A. El-Bindary, J. Mol. Liq., 2024, 394, 123741 CrossRef CAS.
- N. A. Al-Dhabi, G. A. Esmail and M. Valan Arasu, J. Cleaner Prod., 2020, 277, 124252 CrossRef CAS.
- E. Y. Kayhan, A. Yildirim, M. B. Kocer, A. Uysal and M. Yilmaz, Int. J. Biol. Macromol., 2023, 240, 124426 CrossRef CAS PubMed.
- H. Djahaniani, N. Ghavidel and H. Kazemian, Int. J. Biol. Macromol., 2023, 242, 124627 CrossRef CAS PubMed.
- Z. Hu, S. Li, S. Wang, B. Zhang and Q. Huang, Food Chem., 2021, 338, 127839 CrossRef CAS PubMed.
- H. Wang, X. Qian, X. An and Z. Chang, Int. J. Biol. Macromol., 2024, 270, 132151 CrossRef CAS PubMed.
- Z. Huang, C. Xiong, L. Ying, W. Wang, S. Wang, J. Ding and J. Lu, Chem. Eng. J., 2022, 449, 137722 CrossRef CAS.
- A. K. Mohamed and M. E. Mahmoud, Carbohydr. Polym., 2020, 245, 116438 CrossRef CAS PubMed.
- S. Kumar, S. Jain, M. Nehra, N. Dilbaghi, G. Marrazza and K.-H. Kim, Coord. Chem. Rev., 2020, 420, 213407 CrossRef CAS.
- Z. Wang, T. Liu, M. Asif, Y. Yu, W. Wang, H. Wang, F. Xiao and H. Liu, ACS Appl. Mater. Interfaces, 2018, 10, 27936–27946 CrossRef CAS PubMed.
- H. M. Nassef, G. A. A. M. Al-Hazmi, A. A. Alayyafi, M. G. El-Desouky and A. A. El-Bindary, J. Mol. Liq., 2024, 394, 123741 CrossRef CAS.
- Q. Wei, S. Xue, W. Wu, S. Liu, S. Li, C. Zhang and S. Jiang, Chem. Rec., 2023, 23, e202200263 CrossRef CAS PubMed.
- J. Liu, J. Liang, J. Xue and K. Liang, Small, 2021, 17, 2100300 CrossRef CAS PubMed.
- C. Doonan, R. Riccò, K. Liang, D. Bradshaw and P. Falcaro, Acc. Chem. Res., 2017, 50, 1423–1432 CrossRef CAS PubMed.
- Y. Pan, H. Li, J. Farmakes, F. Xiao, B. Chen, S. Ma and Z. Yang, J. Am. Chem. Soc., 2018, 140, 16032–16036 CrossRef CAS PubMed.
- R. Anderson, J. Rodgers, E. Argueta, A. Biong and D. A. Gómez-Gualdrón, Chem. Mater., 2018, 30, 6325–6337 CrossRef CAS.
- H. S. Jhinjer, A. Singh, S. Bhattacharya, M. Jassal and A. K. Agrawal, J. Hazard. Mater., 2021, 411, 125056 CrossRef CAS PubMed.
- Y. Li, R. Wang, X. Liu, K. Li and Q. Xu, Nanotechnology, 2023, 34, 202002 CrossRef CAS PubMed.
- P. Pachfule, Y. Chen, J. Jiang and R. Banerjee, J. Mater. Chem., 2011, 21, 17737 RSC.
- C. Wang, C. Xing, X. Feng, S. Shang, H. Liu, Z. Song and H. Zhang, Int. J. Biol. Macromol., 2023, 250, 126092 CrossRef CAS PubMed.
- C. Wang, X. Feng, Y. Tian, X. Huang, S. Shang, H. Liu, Z. Song and H. Zhang, Environ. Res., 2024, 251, 118651 CrossRef CAS PubMed.
- P.-H. Tong, L. Zhu, Y. Zang, J. Li, X.-P. He and T. D. James, Chem. Commun., 2021, 57, 12098–12110 RSC.
- S. Tarasi, A. Ramazani, A. Morsali, M.-L. Hu, S. Ghafghazi, R. Tarasi and Y. Ahmadi, Inorg. Chem., 2022, 61, 13125–13132 CrossRef CAS PubMed.
- C. Hou, L. Fu, Y. Wang, W. Chen, F. Chen, S. Zhang and J. Wang, Carbohydr. Polym., 2021, 273, 118548 CrossRef CAS PubMed.
- J. Zhou, M. Song, X. Hu, W. Zhang and Z. Deng, Crit. Rev. Environ. Sci. Technol., 2023, 53, 1586–1612 CrossRef CAS.
- Y. Zhang, S. Ni, X. Wang, W. Zhang, L. Lagerquist, M. Qin, S. Willför, C. Xu and P. Fatehi, Chem. Eng. J., 2019, 372, 82–91 CrossRef CAS.
- A. Spieß, J. Wiebe, E. Iwaschko, D. Woschko and C. Janiak, Mol. Syst. Des. Eng., 2022, 7, 1682–1696 RSC.
- X.-F. Zhang, Z. Wang, L. Song and J. Yao, Sep. Purif. Technol., 2021, 266, 118527 CrossRef CAS.
- J. Su, H. Xia, F. Ge, X. Yang, M. Zhou and J. Jiang, Fuel Process. Technol., 2023, 247, 107764 CrossRef CAS.
- S. Perveen, R. Zhai, X. Chen, T. Kanwal, M. R. Shah, M. Lu, B. Ding and M. Jin, Int. J. Biol. Macromol., 2024, 274, 133339 CrossRef CAS PubMed.
- H. Pang, Y. Wu, Q. Tao, Y. Xiao, W. Ji, L. Li and H. Wang, Int. J. Biol. Macromol., 2024, 263, 130523 CrossRef CAS PubMed.
- Q. Zhang, G. Kuang, H. Wang, Y. Zhao, J. Wei and L. Shang, Adv. Sci., 2023, 10, 2303818 CrossRef CAS PubMed.
- D. Lv, W. He, W. Liu, Y. Cheng, Y. Cui, X. Zhou, Y. Xue, S. Yu, N. Zhang, H. Meng, Y. Guan, J.-H. Sun and X.-M. Shi, Biomacromolecules, 2024, 25(7), 4449–4468 CrossRef CAS PubMed.
- L. Chen, W. Huang, M. Hao, F. Yang, H. Shen, S. Yu and L. Wang, Int. J. Biol. Macromol., 2023, 242, 124881 CrossRef CAS PubMed.
- M. Pooresmaeil, Y. Hassanpouraghdam and H. Namazi, Eur. Polym. J., 2023, 184, 111802 CrossRef CAS.
- R. Abazari, N. Ghorbani, J. Shariati, R. S. Varma and J. Qian, Inorg. Chem., 2024, 63, 12667–12680 CrossRef CAS PubMed.
- M. Chen, R. Dong, J. Zhang, H. Tang, Q. Li, H. Shao and X. Jiang, ACS Appl. Mater. Interfaces, 2021, 13, 18554–18562 CrossRef CAS PubMed.
- Y. Pan, H. Li, M. Lenertz, Y. Han, A. Ugrinov, D. Kilin, B. Chen and Z. Yang, Green Chem., 2021, 23, 4466–4476 RSC.
- C. Xu, X. Kong, S. Zhou, B. Zheng, F. Huo and M. Strømme, J. Mater. Chem. A, 2018, 6, 24050–24057 RSC.
- K. Li, J. Yang and J. Gu, Acc. Chem. Res., 2022, 55, 2235–2247 CrossRef CAS PubMed.
- H. Furukawa, K. E. Cordova, M. O'Keeffe and O. M. Yaghi, Science, 2013, 341, 1230444 CrossRef PubMed.
- M. Eddaoudi, J. Kim, N. Rosi, D. Vodak, J. Wachter, M. O'Keeffe and O. M. Yaghi, Science, 2002, 295, 469–472 CrossRef CAS PubMed.
- W. Zou, H. Li, M. Liu and Y. Lv, Appl. Catal., A, 2023, 656, 119120 CrossRef CAS.
- W. Gao, Y. Li, X. Zhang, M. Qiao, Y. Ji, J. Zheng, L. Gao, S. Yuan and H. Huang, Nano Lett., 2024, 24, 3404–3412 CrossRef CAS PubMed.
- H. Nabipour, F. Aliakbari, K. Volkening, M. J. Strong and S. Rohani, Int. J. Biol. Macromol., 2024, 259, 128875 CrossRef CAS PubMed.
- Y. Sun, S. Ding, X. Zhao, D. Sun, Y. Yang, M. Chen, C. Zhu, B. Jiang, Q. Gu, H. Liu and M. Zhang, Adv. Mater., 2024, 2401094 CrossRef CAS PubMed.
- X. Zeng, P. Li, S. Yan and B.-F. Liu, Chem. Eng. J., 2023, 452, 139517 CrossRef CAS.
- X. Huang and C. S. Brazel, J. Controlled Release, 2001, 73, 121–136 CrossRef CAS PubMed.
- Q. Sun, H. Bi, Z. Wang, C. Li, X. Wang, J. Xu, H. Zhu, R. Zhao, F. He, S. Gai and P. Yang, Biomaterials, 2019, 223, 119473 CrossRef CAS PubMed.
- F. Xiong, Z. Qin, H. Chen, Q. Lan, Z. Wang, N. Lan, Y. Yang, L. Zheng, J. Zhao and D. Kai, J. Nanobiotechnol., 2020, 18, 139 CrossRef CAS PubMed.
- X. Xu, Y. Chen, Y. Zhang, Y. Yao and P. Ji, J. Mater. Chem. B, 2020, 8, 9129–9138 RSC.
- Y. Xu, S. Wang, J. Xiong, P. Zheng, H. Zhang, S. Chen, Q. Ma, J. Shen, T. Velkov, C. Dai and H. Jiang, Adv. Healthcare Mater., 2024, 13, 2303839 CrossRef CAS PubMed.
- Y. Wang, W. Qi, Z. Mao, J. Wang, R. C. Zhao and H. Chen, Mater. Today Nano, 2023, 23, 100363 CrossRef CAS.
- H. Zheng, M. Zhu, D. Wang, Y. Zhou, X. Sun, S. Jiang, M. Li, C. Xiao, D. Zhang and L. Zhang, Sep. Purif. Technol., 2023, 306, 122599 CrossRef CAS.
- Y. Wang, W. Qi, Z. Mao, J. Wang, R. C. Zhao and H. Chen, Mater. Today Nano, 2023, 23, 100363 CrossRef CAS.
- M. Shyngys, J. Ren, X. Liang, J. Miao, A. Blocki and S. Beyer, Front. Bioeng. Biotechnol., 2021, 9, 603608 CrossRef PubMed.
- C. Liu, X. Xu, W. Cui and H. Zhang, Eng. Regener., 2021, 2, 105–108 Search PubMed.
- M. D. Telgerd, M. Sadeghinia, G. Birhanu, M. P. Daryasari, A. Zandi-Karimi, A. Sadeghinia, H. Akbarijavar, M. H. Karami and E. Seyedjafari, J. Biomed. Mater. Res., Part A, 2019, 107, 1841–1848 CrossRef CAS PubMed.
- M. Barjasteh, S. M. Dehnavi, S. Ahmadi Seyedkhani, S. Y. Rahnamaee and M. Golizadeh, Surf. Interfaces, 2023, 36, 102631 CrossRef CAS.
- W. Zhu, M. Han, D. Kim, Y. Zhang, G. Kwon, J. You, C. Jia and J. Kim, Environ. Res., 2022, 205, 112417 CrossRef CAS PubMed.
- Q. Miao, L. Jiang, J. Yang, T. Hu, S. Shan, H. Su and F. Wu, J. Water Process Eng., 2022, 50, 103348 CrossRef.
- M. Khajavian, E. Salehi and V. Vatanpour, Carbohydr. Polym., 2020, 247, 116693 CrossRef CAS PubMed.
- M. Jamali and A. Akbari, J. Environ. Chem. Eng., 2021, 9, 105175 CrossRef CAS.
- J. Jiang, Y. Shi, M. Wu, M. Rezakazemi, T. M. Aminabhavi, R. Huang, C. Jia and S. Ge, Chem. Eng. J., 2024, 494, 152932 CrossRef CAS.
- X.-F. Zhang, Z. Wang, L. Song and J. Yao, Sep. Purif. Technol., 2021, 266, 118527 CrossRef CAS.
- Z. Wang, F. Yin, X.-F. Zhang, T. Zheng and J. Yao, Sep. Purif. Technol., 2022, 293, 121095 CrossRef CAS.
- S. Ma, M. Zhang, J. Nie, J. Tan, B. Yang and S. Song, Carbohydr. Polym., 2019, 203, 415–422 CrossRef CAS PubMed.
- S. Ma, M. Zhang, J. Nie, B. Yang, S. Song and P. Lu, Cellulose, 2018, 25, 5999–6010 CrossRef CAS.
- Z. Chen, X. He, J. Ge, G. Fan, L. Zhang, A. M. Parvez and G. Wang, Ind. Crops Prod., 2022, 186, 115269 CrossRef CAS.
- Q. Huang, C. Zhao and X. Li, Cellulose, 2021, 28, 3097–3112 CrossRef CAS.
- Y. Ma, Y. Zhu, Y. Lei, Y. Yang, L. Li, Q. Zhu and W. Zhang, J. Alloys Compd., 2023, 946, 169365 CrossRef CAS.
- R. Du, Y. Wu, Y. Yang, T. Zhai, T. Zhou, Q. Shang, L. Zhu, C. Shang and Z. Guo, Adv. Energy Mater., 2021, 11, 2100154 CrossRef CAS.
- L. Du, B. Zhang, W. Deng, Y. Cheng, L. Xu and L. Mai, Adv. Energy Mater., 2022, 12, 2200501 CrossRef CAS.
- Z. Zhang, M. Liu, C. Li, W. Wenzel and L. Heinke, Small, 2022, 18, 2200602 CrossRef CAS PubMed.
- S. Zhang, J. Luo, F. Zhang, M. Du, H. Hui, F. Zhao, X. He and Z. Sun, J. Membr. Sci., 2022, 652, 120461 CrossRef CAS.
- H. Ma, J. Yu, M. Chen, X. Han, J. Chen, B. Liu and S. Shi, Adv. Funct. Mater., 2023, 33, 2307384 CrossRef CAS.
- H. Zhu, S. Dong, J. Xiong, P. Wan, X. Jin, S. Lu, Y. Zhang and H. Fan, J. Colloid Interface Sci., 2023, 641, 942–949 CrossRef CAS PubMed.
- Y. Yang, S. Ma, M. Xia, Y. Guo, Y. Zhang, L. Liu, C. Zhou, G. Chen, X. Wang, Q. Wu, L. Yang and Z. Hu, Mater. Today Phys., 2023, 35, 101112 CrossRef CAS.
- R. Razaq, M. M. U. Din, D. R. Småbråten, V. Eyupoglu, S. Janakiram, T. O. Sunde, N. Allahgoli, D. Rettenwander and L. Deng, Adv. Energy Mater., 2024, 14, 2302897 CrossRef CAS.
- L. Zhou, H. Pan, G. Yin, Y. Xiang, P. Tan, X. Li, Y. Jiang, M. Xu and X. Zhang, Adv. Funct. Mater., 2024, 34, 2314246 CrossRef CAS.
- X. Ma, Y. Lou, X.-B. Chen, Z. Shi and Y. Xu, Chem. Eng. J., 2019, 356, 227–235 CrossRef CAS.
- R. Davidson, A. Verma, D. Santos, F. Hao, C. Fincher, S. Xiang, J. Van Buskirk, K. Xie, M. Pharr, P. P. Mukherjee and S. Banerjee, ACS Energy Lett., 2019, 4, 375–376 CrossRef CAS.
- Y. Wang, Y. Huang and Y. Fu, Carbohydr. Polym., 2023, 314, 120919 CrossRef CAS PubMed.
- T. Zhao, H. Wu, X. Wen, J. Zhang, H. Tang, Y. Deng, S. Liao and X. Tian, Coord. Chem. Rev., 2022, 468, 214642 CrossRef CAS.
- M. Mao, X. Wu, Y. Hu, Q. Yuan, Y.-B. He and F. Kang, J. Energy Chem., 2021, 52, 277–283 CrossRef CAS.
- X. Pu, B. Jiang, X. Wang, W. Liu, L. Dong, F. Kang and C. Xu, Nano-Micro Lett., 2020, 12, 152 CrossRef CAS PubMed.
- C. Yin, C. Pan, X. Liao, Y. Pan and L. Yuan, ACS Appl. Mater. Interfaces, 2021, 13, 35837–35847 CrossRef CAS PubMed.
- Z. Cao, H. Zhang, B. Song, D. Xiong, S. Tao, W. Deng, J. Hu, H. Hou, G. Zou and X. Ji, Adv. Funct. Mater., 2023, 33, 2300339 CrossRef CAS.
- Y. Wang, Y. Liu, H. Wang, S. Dou, W. Gan, L. Ci, Y. Huang and Q. Yuan, J. Mater. Chem. A, 2022, 10, 4366–4375 RSC.
- X. Liu, F. Yang, W. Xu, Y. Zeng, J. He and X. Lu, Adv. Sci., 2020, 7, 2002173 CrossRef CAS PubMed.
- X. Zeng, J. Zhao, Z. Wan, W. Jiang, M. Ling, L. Yan and C. Liang, J. Phys. Chem. Lett., 2021, 12, 9055–9059 CrossRef CAS PubMed.
- Z. Wang, J. Hu, L. Han, Z. Wang, H. Wang, Q. Zhao, J. Liu and F. Pan, Nano Energy, 2019, 56, 92–99 CrossRef CAS.
- H. Yang, Z. Chang, Y. Qiao, H. Deng, X. Mu, P. He and H. Zhou, Angew. Chem., Int. Ed., 2020, 59, 9377–9381 CrossRef CAS PubMed.
- L. Cao, D. Li, T. Deng, Q. Li and C. Wang, Angew. Chem., Int. Ed., 2020, 59, 19292–19296 CrossRef CAS PubMed.
- C.-Y. Liu, Y.-D. Wang, H. Liu, Q. Chen, X. Jiang, H. Jia and J.-P. Lang, Composites, Part B, 2024, 272, 111227 CrossRef CAS.
- Y. Wang, H. Shaghaleh, Y. A. Hamoud, S. Zhang, P. Li, X. Xu and H. Liu, Int. J. Biol. Macromol., 2021, 187, 262–271 CrossRef CAS PubMed.
- X. Lin, L. Guo, H. Shaghaleh, Y. A. Hamoud, X. Xu and H. Liu, Int. J. Biol. Macromol., 2021, 191, 483–491 CrossRef CAS PubMed.
- Y. Ma, M. Yu, Y. Wang, S. Pan, X. Sun, R. Zhao, Z. Sun, R. Gao, X. Guo, Y. Xu and X. Wu, Chem. Eng. J., 2023, 462, 142190 CrossRef CAS.
- S. Pezhhanfar, M. A. Farajzadeh, S. A. Hosseini-Yazdi and M. R. A. Mogaddam, J. Food Compos. Anal., 2023, 123, 105578 CrossRef CAS.
- W. Meng, Z. Tian, P. Yao, X. Fang, T. Wu, J. Cheng and A. Zou, Colloids Surf., A, 2020, 604, 125266 CrossRef CAS.
- Y. Shan, C. Xu, H. Zhang, H. Chen, M. Bilal, S. Niu, L. Cao and Q. Huang, Nanomaterials, 2020, 10, 2000 CrossRef CAS PubMed.
- S. Song, M. Wan, W. Feng, Y. Tian, X. Jiang, Y. Luo and J. Shen, Langmuir, 2022, 38, 10867–10874 CrossRef CAS PubMed.
- P. Ananthi, K. Hemkumar and A. Pius, ACS Food Sci. Technol., 2024, 4, 1462–1471 CrossRef CAS.
- D.-Y. Zhang, J.-X. Yang, E.-J. Liu, R.-Z. Hu, X.-H. Yao, T. Chen, W.-G. Zhao, L. Liu and Y.-J. Fu, Int. J. Biol. Macromol., 2022, 211, 470–480 CrossRef CAS PubMed.
- J. Wang, S. Zhou, F. Lu, S. Wang and Q. Deng, Food Chem., 2024, 451, 139451 CrossRef CAS PubMed.
- S. Ribes, A. Fuentes, P. Talens and J. M. Barat, Food Chem., 2018, 239, 704–711 CrossRef CAS PubMed.
- A. Khan, Z. Riahi, J. T. Kim and J.-W. Rhim, Food Chem., 2024, 455, 139911 CrossRef CAS PubMed.
- G. Huang, Y. Li, Z. Qin, Q. Liang, C. Xu and B. Lin, Carbohydr. Polym., 2020, 233, 115848 CrossRef CAS PubMed.
- Z. Rui, D. Yu and F. Zhang, Ind. Crops Prod., 2024, 207, 117771 CrossRef CAS.
- M. Tavassoli, A. Khezerlou, M. A. Sani, M. Hashemi, S. Firoozy, A. Ehsani, F. Khodaiyan, S. Adibi, S. M. A. Noori and D. J. McClements, Int. J. Biol. Macromol., 2024, 259, 129182 CrossRef CAS PubMed.
- S. Behboudikhiavi, G. Chanteux, B. Babu, S. Faniel, F. Marlec, K. Robert, D. Magnin, F. Lucaccioni, J. O. Omale, P. Apostol, L. Piraux, C. Lethien and A. Vlad, Small, 2024, 2401509 CrossRef CAS PubMed.
- K. Yuan, K. Tao, T. Song, Y. Zhang, T. Zhang, F. Wang, S. Duan, Z. Chen, L. Li, X. Zhang, D. Zhong, Z. Tang, T.-B. Lu and W. Hu, J. Am. Chem. Soc., 2024, 146, 6893–6904 CrossRef CAS PubMed.
- Q. Zhang, S. Jiang, T. Lv, Y. Peng and H. Pang, Adv. Mater., 2023, 35, 2305532 CrossRef CAS PubMed.
- C. Huang, W. Sun, Y. Jin, Q. Guo, D. Mücke, X. Chu, Z. Liao, N. Chandrasekhar, X. Huang, Y. Lu, G. Chen, M. Wang, J. Liu, G. Zhang, M. Yu, H. Qi, U. Kaiser, G. Xu, X. Feng and R. Dong, Angew. Chem., Int. Ed., 2024, 63, e202313591 CrossRef CAS PubMed.
- C. Yan, J. Wei, J. Guan, Z. Shao and S. Lv, Carbon, 2023, 213, 118187 CrossRef CAS.
- J. Qiao, Q. Song, X. Zhang, S. Zhao, J. Liu, G. Nyström and Z. Zeng, Adv. Sci., 2024, 11, 2400403 CrossRef CAS PubMed.
- Z. Wang, B. Sun, J. Liao, S. Cao, L. Li, Q. Wang and C. Guo, Int. J. Biol. Macromol., 2024, 255, 127989 CrossRef CAS PubMed.
- X. Li, D. Li, Y. Zhang, P. Lv, Q. Feng and Q. Wei, Nano Energy, 2020, 68, 104308 CrossRef CAS.
- F. O. Ongondo, I. D. Williams and T. J. Cherrett, Waste Manage., 2011, 31, 714–730 CrossRef CAS PubMed.
- M. Miao, L. Mu, S. Cao, Y. Yang and X. Feng, Carbohydr. Polym., 2022, 291, 119587 CrossRef CAS PubMed.
- Q. Lu, T. Su, Z. Shang, D. Jin, Y. Shu, Q. Xu and X. Hu, Biosens. Bioelectron., 2021, 184, 113229 CrossRef CAS PubMed.
- Y. Shu, T. Su, Q. Lu, Z. Shang, Q. Xu and X. Hu, Anal. Chem., 2021, 93, 16222–16230 CrossRef CAS PubMed.
- A. Afzalinia and M. Mirzaee, ACS Appl. Mater. Interfaces, 2020, 12, 16076–16087 CrossRef CAS PubMed.
- X. Li, X. Li, D. Li, M. Zhao, H. Wu, B. Shen, P. Liu and S. Ding, Biosens. Bioelectron., 2020, 168, 112554 CrossRef CAS PubMed.
- L. Huang, W. Huang, R. Shen and Q. Shuai, Food Chem., 2020, 330, 127212 CrossRef CAS PubMed.
Footnote |
† Xian Wang: Joint first author. |
|
This journal is © The Royal Society of Chemistry 2025 |
Click here to see how this site uses Cookies. View our privacy policy here.