DOI:
10.1039/D4TA08182J
(Review Article)
J. Mater. Chem. A, 2025,
13, 6895-6918
Adsorption enhanced catalytic degradation of airborne formaldehyde in bifunctional composite materials
Received
18th November 2024
, Accepted 20th January 2025
First published on 21st January 2025
Abstract
Formaldehyde (HCHO) is one of the well-known carcinogenic VOCs, which poses a serious threat to the environment and human health. Bifunctional composite materials (BFCMs) have great application prospects in the field of HCHO removal due to their impressive adsorption-promoted catalytic synergies and good catalytic stability. However, the urgency of efficient degradation of HCHO at near room temperature poses many challenges to the design of BFCMs, especially the design of components in BFCMs, such as support components (SCs) and catalytic components (CCs). In addition, the influence of multiple components in BFCMs on the degradation of HCHO is highly complex, especially the component synergies and the adsorption-promoted catalysis mechanism. To understand these effects and improve the degradation efficiency of HCHO, we first discuss the encouraging research outcomes in recent years, encompassing the design, preparation, and multilevel synergies in BFCMs (e.g. adsorption-catalytic synergies, heterogeneous synergies within SCs or CCs, structural synergies, and mass and heat transfer synergies). Subsequently, we concentrate on analysing the impacts of support component factors (e.g. types, crystal phases, particle sizes, morphologies, specific surface areas, and acidity) and catalytic component factors (e.g. shapes, morphologies, particle sizes, metal chemistry states, and loading capacities) on the HCHO removal performances. Finally, the degradation mechanism of HCHO and the catalytic stability of BFCMs are concluded.
1 Introduction
As a type of air pollutant with high carcinogenicity and mutagenicity, HCHO is found from many sources (e.g., interior decoration, organic solid waste incineration, and electronic solid waste pyrolysis), and its removal has received extensive attention.1–3 A considerable number of HCHO removal technologies has been developed, mainly including physical adsorption, chemical absorption, catalytic oxidation, plasma decomposition, and biotechnological decomposition.4–6 Among these technologies, catalytic oxidation at room temperature is regarded as the most promising HCHO removal technology.7–9 Besides, various HCHO catalysts (e.g., noble metal catalysts and transition metal oxides/TMO) for application in different humidity and temperature scenarios have been reported. Among them, most noble metal (e.g., Pd, Pt, and Au) based catalysts have been demonstrated to possess excellent HCHO degradation performance at room temperature.2 Unfortunately, they often exhibit the characteristics of low abundance, high cost, poor thermal stability, and susceptibility to toxic inactivation.10 In contrast, TMOs (e.g., MnO2, CeO2, and Co3O4) have been studied to serve as alternatives of noble metal-based catalysts due to their accessibility, competitive price, superior catalytic activity, and environmental friendliness.11 However, most TMO-based catalysts also have their own limitations for HCHO oxidation, such as low catalytic activity at room temperature.12 The possible issues mentioned above constitute a significant obstacle to the further application of catalysts in the degradation of HCHO.
To alleviate these problems, noble metals and/or TMO-based catalysts have been studied in depth, such as (i) expanding the range of noble metal species (e.g., Pt, Au, Pd, Ag, and Rh),13 (ii) modifying the particle sizes of catalysts (e.g., mm-Al2O3, μm-MnO2, and nm-Al2O3),14 (iii) investigating the bulk geometry of catalysts (e.g., pellets, monoliths and foams),2 (iv) exploring the crystalline phases of catalysts (e.g., α-MnO2, β-MnO2, γ-MnO2, and δ-MnO2),15 (v) exploring the morphologies of catalysts (e.g., α-MnO2-nanowire, α-MnO2-nanotube, α-MnO2-nanorods, and α-MnO2-nanoflower),16 (vi) exploring the mechanical mixing preparation of different components (e.g., MnOx + UiO-66, MnOx + GO, and Fe2O3 + Mn3O4),17–19 and (vii) designing and synthesizing bifunctional composite materials (BFCMs, e.g., porous carrier-based composite MnO2/UiO-66-NH220 and oxide carrier-based composite Pt/Fe2O3@SnO2).21 Among them, one of the most prominent approaches is the discovery of BFCMs (e.g., 1.5 wt% Pt/TiO2-H200, 0.887 Pt-VO-ZrO2, δ-MnOx/activated carbon, three-dimensionally ordered macroporous (3DOM)∼3 wt% Au/CeO2-Co3O4, 1 wt% MnO2/UIO-66-NH2, 3DOM∼3 wt% Au/CeO2, and GO/MnOx) (Table 1), whose alluring advantages, such as diverse components, structural design, and adjustable functions, have impelled numerous researchers to undertake horizontal and immersive longitudinal studies. Notably, BFCMs specifically refer to the materials that exhibit two or more distinct functionalities, encompassing various combinations of physical, chemical, and biological properties.64 From a transverse perspective, the influence of support components (SCs), catalytic components (CCs), and different preparation processes (e.g., solvothermal method, impregnation method, in situ deposition method, and high-temperature calcination method) on the structure and properties of BFCMs was investigated.17,31,65 Among them, the SCs encompassed various carbon materials (e.g., granular activated carbon, activated carbon fiber, and graphene oxide),12 glass fibers,26 polymers (e.g., silicone-based polymer),7 and MOF materials (such as UIO-66-NH2),20 while the CCs included noble metals, metal oxides, element-doped catalysts, and atomic substitution catalysts. Additionally, the impacts of diverse factors on the structure–activity relationship of BFCMs were investigated from a longitudinal perspective. This mainly included the type of SCs, the specific surface areas of SCs, the crystal phase of CCs/SCs (e.g., Pt/α-MnO2@L-MnO2),66 the loading capacity of CCs in BFCMs, and the doping of different elements in CCs (e.g., N-MnNxO2−x and 0.05 wt% Pt–Na/nano-Al2O3).14,67 Moreover, the enhanced degradation of HCHO was analysed to be associated with several potential factors, such as facilitating the enrichment of gas substrates (e.g., HCHO and O2), augmenting the specific surface areas of CCs, enhancing the dispersion of CCs, increasing interfacial bonding,68 and promoting electron transfer.57 Particularly, the heterogeneous interface based on the synergistic interaction of adsorption-catalytic sites significantly expedited the degradation of HCHO by establishing electron transport channels for catalytic oxidation.24
Table 1 Adsorption-catalytic removal of airborne HCHO in BFCMs at different reaction temperaturesb
BFCMs |
BFCMs quality |
T (°C) |
GHSV (h−1 or mL (g h)−1) |
[HCHO]I (ppm or V%) |
HCHO removal activity (η′/%) |
Ref. |
Coconut shell AC (40–60 mesh).
[HCHO]I (inlet HCHO concentration), η′ (HCHO conversion), and RH (relative humidity).
|
At room temperature (T ≤ 40°C)
|
0.08 wt%Pt–NC/TiO2 (Pt size of 1 nm) |
100 mg |
20 °C |
30 000 mL (g h)−1 |
100 ppm |
η′ = 100% (with 50% RH) |
22
|
F-0.08 wt%Pt/TiO2 |
300 mg |
20 °C |
50 000 mL (g h)−1 |
200 ppm |
η′ = 89% (with 19% RH) |
23
|
F-0.1 wt%Pt/TiO2 |
300 mg |
20 °C |
50 000 mL (g h)−1 |
200 ppm |
η′ = 97% (with 19% RH) |
23
|
0.51 wt%Pt-VO-ZrO2 |
100 mg |
20 °C |
600 000 mL (g h)−1 |
100 ppm |
η′ = 27% (with 30% RH) |
24
|
0.87 wt%Pt-VO-ZrO2 |
100 mg |
20 °C |
600 000 mL (g h)−1 |
100 ppm |
η′ = 95% (with 30% RH) |
24
|
1.32 wt%Pt-VO-ZrO2 |
100 mg |
20 °C |
600 000 mL (g h)−1 |
100 ppm |
η′ = 91% (with 30% RH) |
24
|
1 wt%Pt–ZrO2 |
100 mg |
20 °C |
600 000 mL (g h)−1 |
100 ppm |
η′ = 33% (with 30% RH) |
24
|
1 wt%Pd/CeO2 |
N/A |
20 °C |
120 000 mL (g h)−1 |
600 ppm |
η′ = 98% |
25
|
0.5 wt%Rh/TiO2 |
N/A |
20 °C |
30 000 mL (g h)−1 |
140 ppm |
η′ = 37% |
13
|
1 wt%Rh/TiO2 |
N/A |
20 °C |
30 000 mL (g h)−1 |
140 ppm |
η′ = 88% |
13
|
5 wt%Ag@MnO2 |
100 mg |
24 °C |
36 000 mL (g h)−1 |
420 ppm |
η′ = 100% |
26
|
0.015 wt%PtOx@BIT-72-DE |
50 mg |
25 °C |
60 000 mL (g h)−1 |
25 ppm |
η′ = 100% (with 25% RH) |
27
|
0.05 wt%Pt–Na/nano-Al2O3 |
30 mg (60 mesh) |
25 °C |
200 000 mL (g h)−1 |
120 ppm |
η′ = 100% (with 35% RH) |
28
|
0.09 wt%PtSA–MnOOH/MnO2 |
1000 mg |
25 °C |
30 000 mL (g h)−1 |
15 ppm |
98% |
29
|
0.2 wt%Pt@BEA zeolite |
50 mg |
25 °C |
360 000 mL (g h)−1 |
80 ppm |
η′ = 95% (with 10% RH) |
30
|
0.2 wt%Pt/CeO2-7 |
300 mg |
25 °C |
300 000 mL (g h)−1 |
100 ppm |
η′ = 92% (with 50% RH) |
31
|
0.5 wt%Pt/TiO2-NS |
300 mg |
25 °C |
N/A |
253 ppm |
η′ = 100% |
32
|
1.5 wt%Pt/TiO2-H200 |
10 mg |
25 °C |
600 000 mL (g h)−1 |
120 ppm |
η′ = 100% (with 50% RH) |
33
|
1.5 wt%Pt/SBT-400 |
300 mg |
25 °C |
12 600 h−1 |
100 ppm |
η′ = 100% |
34
|
1 wt%Au/γ-Al2O3 |
10 mg |
25 °C |
600 000 mL (g h)−1 |
80 ppm |
η′ = 89% (with 50% RH) |
35
|
1 wt%Au/SiO2 |
10 mg |
25 °C |
600 000 mL (g h)−1 |
80 ppm |
η′ = 80% (with 50% RH) |
35
|
1 wt%Au/HZSM-5 |
10 mg |
25 °C |
600 000 mL (g h)−1 |
80 ppm |
η′ = 43% (with 50% RH) |
35
|
1 wt%Au/CeO2 |
10 mg |
25 °C |
600 000 mL (g h)−1 |
80 ppm |
η′ = 31% (with 50% RH) |
35
|
1 wt%Au/FeOx |
10 mg |
25 °C |
600 000 mL (g h)−1 |
80 ppm |
η′ = 18% (with 50% RH) |
35
|
1 wt%Pd/KTO–NB |
50 mg |
25 °C |
20 000 h−1 |
140 ppm |
η′ = 95% (with 25% RH) |
1
|
2 wt%Na-1 wt%Pd/TiO2 |
60 mg |
25 °C |
95 000 h−1 |
140 ppm |
N/A |
36
|
3.42 V%MnOx/ACa |
100 mg |
25 °C |
60 000 mL (g h)−1 |
100 ppm |
η′ = 80.9 (with 30% RH) |
37
|
3.58 V%MnOx/AC-N1a |
100 mg |
25 °C |
60 000 mL (g h)−1 |
100 ppm |
η′ = 90.3 (with 30% RH) |
37
|
3.91 V%MnOx/AC-N2a |
100 mg |
25 °C |
60 000 mL (g h)−1 |
100 ppm |
η′ = 97.1 (with 30% RH) |
37
|
4.68 V%MnOx/AC-N3a |
100 mg |
25 °C |
60 000 mL (g h)−1 |
100 ppm |
η′ = 83.2 (with 30% RH) |
37
|
α-MnO2/GO–M2∼20 wt% |
100 mg |
25 °C |
120 000 mL (g h)−1 |
112 ppm |
η′ = 100% (with 70% RH) |
38
|
21.55 wt%MnO2@PMIA-2 |
N/A |
25 °C |
60 000 mL (g h)−1 |
100 ppm |
η′ = 71% (with 55% RH) |
39
|
23.08 wt%MnO2@PMIA-6 |
N/A |
25 °C |
60 000 mL (g h)−1 |
100 ppm |
η′ = 95.43% (with 55% RH) |
39
|
23.54 wt%MnO2@PMIA-10 |
N/A |
25 °C |
60 000 mL (g h)−1 |
100 ppm |
η′ = 78% (with 55% RH) |
39
|
δ-MnO2@GO-1 wt% |
200 mg |
25 °C |
72 000 mL (g h)−1 |
10 ppm |
η′ = 98% (with 50% RH) |
40
|
25 wt%Ce–MnOx |
300 mg |
25 °C |
N/A |
0.97–1.03 ppm |
η′ = 73% |
41
|
(CH3COO)2Co/PAN∼58.79 wt% |
100 mg |
25 °C |
60 000 mL (g h)−1 |
10–12 ppm |
η′ = 99% |
42
|
MnO2@SiO2–TiO2 |
N/A |
25 °C |
N/A |
200 ppm |
η′ = 100% (with 40% RH) |
43
|
Pt/MnOx–CeO2 (Pt–N catalyst) |
200 mg (40–60 mesh) |
25 °C |
30 000 mL (g h)−1 |
<100 ppm |
η′ = 100% |
44
|
Pt/MnOx–CeO2 (no hydrogen prereduction) |
200 mg (40–60 mesh) |
25 °C |
30 000 mL (g h)−1 |
580 ppm |
η′ = 54% |
44
|
0.1 wt%Pd/TiO2 |
60 mg |
25 °C |
120 000 mL (g h)−1 |
10 ppm |
η′ = 97% |
45
|
0.1 wt%Pt/TiO2–NS |
100 mg |
30 °C |
210 000 mL (g h)−1 |
10 ppm |
η′ > 95% (with 50% RH) |
46
|
Au@Co3O4 |
10 mg |
30 °C |
300 000 mL (g h)−1 |
100 ppm |
η′ = 92% (with 45% RH) |
47
|
0.5 wt%Pd/R-TiO2-30 |
500 mg |
30 °C |
130 000 h−1 |
20 ppm |
η′ = 94% (with 50% RH) |
48
|
1 wt%MnO2/UiO-66-NH2 |
100 mg |
30 °C |
597 134 h−1 |
100 ppm |
η′ = 88% |
20
|
8 wt%Ag/APETS/MCM-41 |
N/A |
30 °C |
9000 mL (g h)−1 |
N/A |
η′ = 6% |
49
|
2 wt%Au/CeO2-550 |
50 mg |
36 °C |
36 000 mL (g h)−1 |
220 ppm |
η′ = 100% |
50
|
3DOM∼3%Au/(2.5 : 1) CeO2–Co3O4 |
200 mg |
39 °C |
15 000 mL (g h)−1 |
8 ppm |
η′ = 100% |
51
|
3DOM∼3%Au/CeO2 |
200 mg |
39 °C |
66 000 mL (g h)−1 |
0.06 V% |
η′ = 100% |
52
|
2.30 wt%Au/CeO2 |
50 mg |
40 °C |
35 400 h−1 |
0.05 V% |
η′ = 80% |
53
|
2.22 wt%Au/TiO2 |
50 mg |
40 °C |
35 400 h−1 |
0.05 V% |
η′ = 5% |
53
|
3.52 wt%Au/Al2O3 |
50 mg |
40 °C |
35 400 h−1 |
0.05 V% |
η′ = 39% |
53
|
1.70 wt%Au/SiO2 |
50 mg |
40 °C |
35 400 h−1 |
0.05 V% |
η′ = 1% |
53
|
0.1 wt%Pd/beta zeolites |
N/A |
40 °C |
50 000 h−1 |
40 ppm |
η′ = 25% |
54
|
0.25 wt%Pd/Al2O3 |
N/A |
40 °C |
50 000 h−1 |
40 ppm |
η′ = 80% |
55
|
3 wt%Ag/MnOx–CeO2 |
N/A |
40 °C |
30 000 mL (g h)−1 |
580 ppm |
η′ = 12% |
56
|
![[thin space (1/6-em)]](https://www.rsc.org/images/entities/char_2009.gif) |
40°C < T ≤ 100°C (at relatively low temperatures)
|
Cu–Ce catalyst |
100 mg |
60 °C |
600 000 mL (g h)−1 |
58 ppm |
η′ = 95% |
57
|
MnO2–graphene |
100 mg |
65 °C |
30 000 mL (g h)−1 |
100 ppm |
η′ = 100% |
10
|
7 wt%Pt/ZrO2–GA–MOF-5 |
200 mg |
70 °C |
N/A |
50 ppm |
η′ = 95% |
58
|
9 wt%Pt/ZrO2–GA–MOF-5 |
200 mg |
70 °C |
N/A |
50 ppm |
η′ = 85% |
58
|
0.25 wt%Au/α-MnO2 |
66 mg |
75 °C |
60 000 mL (g h)−1 |
500 ppm |
η′ = 100% (with 25% RH) |
15
|
3DOM Au∼1 wt%/CeO2 (80 nm pore size) |
200 mg |
75 °C |
66 000 mL (g h)−1 |
0.06 V% |
η′ = 100% |
52
|
3DOM Au∼1 wt%/CeO2 (130 nm pore size) |
200 mg |
75 °C |
66 000 mL (g h)−1 |
0.06 V% |
η′ = 43% |
52
|
3DOM Au∼1 wt%/CeO2 (280 nm pore size) |
200 mg |
75 °C |
66 000 mL (g h)−1 |
0.06 V% |
η′ = 40% |
52
|
3DOM Au∼1 wt%/CeO2 (80 nm pore size) |
200 mg |
75 °C |
66 000 mL (g h)−1 |
0.06 V% |
η′ = 100% |
52
|
3DOM Au∼2 wt%/CeO2 (80 nm pore size) |
200 mg |
75 °C |
66 000 mL (g h)−1 |
0.06 V% |
η′ = 100% |
52
|
3DOM Au∼3 wt%/CeO2 (80 nm pore size) |
200 mg |
75 °C |
66 000 mL (g h)−1 |
0.06 V% |
η′ = 100% |
52
|
3DOM Au∼4 wt%/CeO2 (80 nm pore size) |
200 mg |
75 °C |
66 000 mL (g h)−1 |
0.06 V% |
η′ = 91% |
52
|
0.01 wt%Pt–SAC/TiO2 (Pt–SAC for single-atom catalyst) |
100 mg |
80 °C |
30 000 mL (g h)−1 |
160 ppm |
η′ = 5% (with 50% RH) |
22
|
7.10 wt%Au/Fe2O3 |
200 mg (40–60 mesh) |
80 °C |
54 000 mL (g h)−1 |
6.25 mg m−3 |
η′ = 100% |
59
|
4.85 wt%Au/Fe2O3 |
200 mg (40–60 mesh) |
80 °C |
54 000 mL (g h)−1 |
6.25 mg m−3 |
η′ = 81% |
59
|
2.52 wt%Au/Fe2O3 |
200 mg (40–60 mesh) |
80 °C |
54 000 mL (g h)−1 |
6.25 mg m−3 |
η′ = 36% |
59
|
(ε-MnO2/CeO2)@CeO2 (Ce : Mn = 1 : 4) |
100 mg |
80 °C |
100 000 mL (g h)−1 |
180 ppm |
η′ = 100% (with 50% RH) |
60
|
xMnOx–CeO2, x = Mn/(Mn + Ce) = 0.5 |
200 mg (40–60 mesh) |
90 °C |
30 000 mL (g h)−1 |
580 ppm |
η′ = 90% |
44
|
40 wt%MnO2/NCNT |
200 mg |
100 °C |
30 000 mL (g h)−1 |
100 ppm |
η′ = 100% |
61
|
40 wt%MnO2/CNTs |
200 mg |
100 °C |
30 000 mL (g h)−1 |
100 ppm |
η′ = 100% |
61
|
![[thin space (1/6-em)]](https://www.rsc.org/images/entities/char_2009.gif) |
T > 100°C (at relatively high temperatures)
|
70 wt%MnO2/CNTs |
200 mg |
150 °C |
30 000 mL (g h)−1 |
100 ppm |
η′ = 100% |
61
|
Mn0.9Ce0.1/PG∼85 wt% |
100 mg (40–60 mesh) |
160 °C |
20 000 h−1 |
300 ppm |
η′ = 100% |
62
|
Mn0.8Ce0.2/PG∼85 wt% |
100 mg (40–60 mesh) |
160 °C |
20 000 h−1 |
300 ppm |
η′ = 83% |
62
|
Mn0.7Ce0.3/PG∼85 wt% |
100 mg (40–60 mesh) |
160 °C |
20 000 h−1 |
300 ppm |
η′ = 78% |
62
|
Mn0.6Ce0.4/PG∼85 wt% |
100 mg (40–60 mesh) |
160 °C |
20 000 h−1 |
300 ppm |
η′ = 76% |
62
|
Mn0.5Ce0.5/PG∼85 wt% |
100 mg (40–60 mesh) |
160 °C |
20 000 h−1 |
300 ppm |
η′ = 62% |
62
|
Mn/PG∼85 wt% |
100 mg (40–60 mesh) |
160 °C |
20 000 h−1 |
300 ppm |
η′ = 41% |
62
|
CeO2/PG∼85 wt% |
100 mg (40–60 mesh) |
160 °C |
20 000 h−1 |
300 ppm |
η′ = 2% |
62
|
CeO2–rGO–NF |
200 mg |
170 °C |
60 000 mL (g h)−1 |
250 ppm |
η′ = 93% |
63
|
0.73 wt%Au/Fe–O |
200 mg (40–60 mesh) |
180 °C |
54 000 mL (g h)−1 |
N/A |
η′ = 11% |
59
|
Despite numerous outstanding studies being conducted on BFCMs, the intertwined interactions within or among components pose a significant challenge in determining the factors influencing the catalytic activity of HCHO and the degradation mechanism. Specifically, the following uncertainties within BFCMs might severely impact the optimization of their structure–activity relationships and the determination of HCHO degradation pathways. (i) As for SCs, aside from the adsorption capacity, various factors such as support component types, crystal phases, particle sizes, morphologies, pore sizes, specific surface areas and others may also have an impact on the removal of HCHO.69–71 (ii) As for CCs, particularly the activity of noble metal-based catalysts is prone to variation due to their own characteristics (such as loading capacities, particle sizes, dispersion, morphologies, etc.) and reaction conditions.72–74 (iii) Most crucially, the synergistic factors of SCs and CCs as well as the adsorption-catalytic mechanism in BFCMs are complex, and specifically the catalytic activity might be influenced by the decomposition rate of intermediates and the rate of product desorption.73,75,76 Therefore, it is necessary to summarize the influencing factors and synergistic mechanism of each component in BFCMs to provide a theoretical basis for researchers to design new composites for the efficient degradation of HCHO in the future.
Currently, there are hardly any review articles concerning the removal of total VOCs by adsorption/catalytic oxidation.77,78 Different from these studies, this work focuses on the multistage synergistic degradation of HCHO in composite materials from the perspective of adsorption enhanced catalytic degradation of HCHO. On this basis, the influence of various components (such as SCs and CCs) and reaction conditions on the degradation performance of HCHO is further summarized, and the recyclability and degradation paths of BFCMs are analyzed, thereby better evaluating their superiority and practical feasibility among numerous materials. A specialized review of these studies is anticipated to furnish valuable references for the design of low-cost, stable, and high-performance HCHO degrading BFCMs.
2. Recent progress on adsorption enhanced catalytic degradation of HCHO in bifunctional composite materials
Compared to single-component catalysts, BFCMs commonly exhibit several advantages, such as greater design flexibility, enhanced stability, synergistic effects, superior activity, and selectivity.79 Due to the integration of two or more functional components, BFCMs could achieve synergistic effects, enabling simultaneous or sequential execution of multiple reaction steps, thereby enhancing overall reaction efficiency and product selectivity.80 By adjusting the characteristics of SCs and CCs in BFCMs (such as species, structures, crystal phases, particle sizes, pore sizes, specific surface areas, dispersion and loading of CCs), the synergistic effect between SCs and/or CCs could be significantly intensified, thereby enhancing the adsorption and catalytic degradation ability of HCHO. These studies have not only made a breakthrough in enhancing the removal efficiency of HCHO, but also greatly improved the recycling stability, selectivity and environmental friendliness of BFCMs, providing a new direction for future research.
2.1 Design of bifunctional composite materials
To date, various highly compelling studies for HCHO removal based on multi-angle design mainly cover the following aspects. On the one hand, based on material combination innovation, different types of SCs and CCs were exquisitely combined to achieve efficient degradation of HCHO by BFCMs. This mainly encompassed the combinations of noble metals and TMOs (e.g., Pt/TiO2, Rh/TiO2, Pd/TiO2, and Au/TiO2),81 the combinations of alkali metal dopant oxides and SCs (e.g., 0.05 wt% Pt–Na/nano-Al2O3),14 or a combination of noble metals and/or TMOs with SCs (e.g., 7 wt% Pt/ZrO2–GA–MOF-5).58 On the other hand, it could be achieved through process innovation (such as in situ deposition at room temperature, chemical in situ deposition, vapor deposition, and bubble-assisted deposition precipitation),52,82–84 structural innovation (e.g., core–shell structure CeO2@LDHs,85 epitaxial structure α-MnO2@L-MnO2,66 and embedding structure MnO2/UiO-66-NH2),20 functional group modification, crystal surface exposure (e.g., {001} surface in Pt/FTiO2-NS),32 alkali metal/nitrogen atom doping (e.g., 3D-CeO2@CN), and heat/acid/base pretreatment37,86,87 to enhance the catalytic activity of BFCMs towards HCHO. All in all, the aforementioned strategies focusing on material type, structural design, element doping, and material pretreatment significantly enhance the degradation efficiency of HCHO by BFCMs.
2.2 Evaluation of degradation performance for HCHO
At low temperatures (e.g., T ≤ 40 °C), minimizing the loading capacities (e.g. <0.1 wt%) of noble metals in BFCMs or utilizing low-cost non-noble metals to effectively degrade HCHO was a desirable goal.2 In Table 1, we summarized the HCHO degradation conditions and some indices for multiple types of BFCMs based on the characteristic reaction temperature zones (e.g., T ≤ 40 °C, 40 °C < T ≤ 100 °C, and T > 100 °C). These primary conditions and indicators included the mass of BFCMs, reaction temperatures (T), gas hourly space velocity (GHSV), HCHO concentration at the inlet ([HCHO]I), HCHO removal activity (η′) under specified humidity, etc. In these reports, some studies had elaborately investigated the source/generation of HCHO involved in the evaluation process of HCHO degradation performance, the evaluation scheme of HCHO degradation, and the evaluation indicators (such as HCHO removal rate, conversion rate, and specific rate). For instance, apart from the HCHO standard gas, polluted air with a specific HCHO concentration could also be produced at a certain temperature via the polyformaldehyde layer in a U-shaped tube. To study the impact of water on catalytic efficiency, the first stream was passed through a water generator and the other through a HCHO generator, and subsequently, the two streams were merged together as feedstock gas. Additionally, while the concentration of HCHO in the stream was manually detected by using an htV-M HCHO meter, the composition of the effluent phase could be analysed online by using a gas chromatograph equipped with a methanation furnace and FID.15 In addition, the evaluation schemes of HCHO degradation ability were often classified into the static test and dynamic single test. The removal rate of HCHO and the thermal regeneration stability of BFCMs could be evaluated in the static test. The removal efficiency of HCHO and the continuous catalytic stability of BFCMs (e.g., a catalytic duration of 100 h) could be tested in a dynamic single test. Generally, the static test device could be composed of a closed glass container, circulation system, electric actuator system and HCHO monitoring system. In the dynamic single test, a HCHO standard gas bottle was connected at one end of a catalyst box, and a CO2 concentration tester and HCHO concentration tester were connected at the other end to test the real-time concentrations of HCHO and CO2 respectively. The concentration of HCHO was measured in real time with the aforementioned HCHO being utilized as the pollutant gas. The thermal regeneration stability of BFCMs could be studied by repeated static tests. Eqn (1) and (2) could be utilized to calculate the removal efficiency of HCHO and the conversion efficiency of HCHO to CO2 under the dynamic test.24 |  | (1) |
| 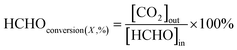 | (2) |
where [HCHO]in (ppm) and [HCHO]out were the initial equilibrium concentration of HCHO before and after the test, and [CO2]out (ppm) was the final concentration of CO2 at the end of the test. Additionally, in the course of catalytic degradation, the specific rate constituted an essential indicator for gauging the reaction rate. During the process of HCHO degradation, the specific rate (R) was computed through dynamic experimentation, and the relevant formula was listed as follows.48w |  | (3) |
here R was the specific rate, CHCHO was the inlet HCHO concentration(ppm), F was the flow rate (mL min−1), η was the HCHO conversion calculated by the generation of CO2 (%), SBET was the specific surface area of the catalyst and m was the catalyst weight.88 It should be noted that the determination and analysis of the specific rate were of great significance for comprehending the performance of catalysts and optimizing the catalytic process. However, this index had only been reported in a few literature studies.22,24,88 Therefore, the specific rate indicator is not listed in Table 1 below.
2.3 Adsorption enhanced catalytic degradation of HCHO in bifunctional composite materials
The BFCMs accomplish efficient elimination of HCHO in the same material through the combination of adsorption and catalytic functions. This synergistic effect of adsorption enhanced catalytic degradation significantly enhances the performance and application efficiency of BFCMs. Studies indicated that the synergies in BFCMs mainly include adsorption-catalytic synergies, heterogeneous synergies within SCs or CCs, structural synergies, and heat and mass transfer synergies.
2.3.1 Adsorption-catalytic synergies.
Several studies had indicated that the adsorption-catalytic synergistic effect in BFCMs could significantly promote the degradation of HCHO. In Pt/TiO2−x, the oxygen vacancies (OVs) on the surface of TiO2 were identified as the main adsorption sites for HCHO molecules, while Pt was the active site for O2 activation. The conversion of formate and dioxymethylene (DOM) intermediates to CO2 and H2O required the participation of active O substances, which proved that Pt acted as an active site for O2 activation.33 Similarly, the CeO2 surface provided adsorption sites for HCHO, and Au and Au nanoclusters provided active sites for O2 activation. CeO2 and Au collaboratively promoted the efficient degradation of HCHO on Au/CeO2-550.50 Note that the SCs in BFCMs may not be the only adsorption sites for HCHO, and cases of SCs-CCs synergistic adsorption of HCHO had also been reported. HCHO was found not only to be adsorbed and activated on the porous support component of MnO2/UiO-66-NH2, but also to be adsorbed reactively on the catalyst MnO2 and oxidized to DOM and HCOO− species.20 In addition, the usage of porous materials with functional groups (such as –OH, –NH2, and –COOH) as SCs was beneficial to enhance the adsorption of HCHO and the synergistic effect of adsorption-catalysis. For example, Pt in Pt/ZSM-5 was embedded in zeolite, and Pt NPs and its adjacent zeolite surface –OH groups not only synergically promoted the adsorption of HCHO, but also provided more opportunities to participate in DOM conversion to HCOO− and further degradation to CO2 and H2O. This maximized the atomic utilization efficiency of Pt.89 Different from promoting adsorption by –OH, the weak reducing –OH on the fiber surface in MnO2@PMIA-6 generated abundant Mn3+ near the fiber surface. These Mn3+ were coated with MnO2 crystals that grew near the fiber surface, forming BFCMs with high OV concentration. At the same time, carboxyl groups on the surface of plasma-treated PMIA could be utilized as chemical bond functional groups to anchor MnO2 nanocrystals to PMIA fibers (Fig. 1). The deep synergistic effect between MnO2 and PMIA-6 was expected to make MnO2@PMIA-6 have a better HCHO catalytic activity and washing resistance.39 In addition to –OH and –COOH, NH2 was often introduced into BFCMs to regulate the adsorption and oxidation of HCHO. The Zr atom attached to the NH2 group in MnO2/UIO-66-NH2 first adsorbed and activated HCHO and molecular oxygen species, and then degraded HCHO to carbon dioxide through intermediates such as dioxymethylene and formate. MnO2 nanoclusters acted as secondary reactive adsorption sites to facilitate the capture, activation and oxidation of HCHO molecules in the active centres of Zr. This study fully confirmed the possibility of efficient removal of HCHO by BFCMs through adsorption-catalytic synergism.20
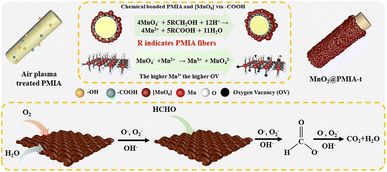 |
| Fig. 1 Systematic modulation of the specific surface area, catalytic activity, and laundering durability of fiber-based MnO2 nano-catalysts. Reproduced with permission.39 Copyright 2023, Elsevier. | |
It is worth mentioning that photo assisted adsorption-catalytic coordination was also a method to enhance the oxidation of HCHO. The pre-deposited graphene oxide on the nickel foam (NF) matrix was utilized as the photothermal conversion layer, which was conducive to the uniform and stable loading of CeO2. The addition of reduced graphene oxide increased near-infrared (NIR) light absorption, and the thermal conductivity of NF improved electron mobility, so that the oxidation of HCHO was stimulated not only by the Olatt from CeO2, but also by the photogenerated electron oxidation to produce the central point O2−. In addition, the central point O2− would reoxidize Ce3+ to Ce4+ in the OVs, accelerating the oxygen consumption and oxygen supply cycle in the lattice, and greatly improving the HCHO removal rate.63 In conclusion, the adsorption-catalytic synergy in BFCMs remarkably enhanced the catalytic performance by integrating different materials and reaction mechanisms. This synergistic effect not only boosted the capture capability of HCHO but also elevated the conversion efficiency of HCHO, offering new ideas and technical approaches for environmental governance.
2.3.2 Heterogeneous synergies among SCs or CCs.
In addition to adsorption-catalytic synergism, the secondary synergy inside the heterogeneous SCs further enhanced the degradation of BFCMs for HCHO. For example, this secondary synergy was manifested in the core–shell binding pattern and interaction of Fe2O3 and SnO2 in the heterogeneous support component in Pt/Fe2O3@SnO2. Fe2O3 in the core–shell structure was conducive to the adsorption/activation of O2, while the SnO2 shell promoted the desorption of H2O.21 In addition to core–shell binding, heterogeneous SCs could also be combined by epitaxy and coordinate with catalysts to promote the oxidation activity of HCHO. The Pt component in Pt/α-MnO2@δ-MnO2 was demonstrated to have a higher HCHO oxidation activity than the Pt component in Pt/α-MnO2 or Pt/δ-MnO2. The key reason had been found to be that the {1 0 0} surface exposed by α-MnO2 in the heteroepitaxial support component was conducive to O2 adsorption and activation, while the {0 0 1} surface exposed by layered structure δ-MnO2 was conducive to H2O desorption.66 The synergistic effect between the SCs in BFCMs could also be manifested in activating the noble metal species and accelerating the migration of surface ROS to improve the oxidation performance of HCHO.51 In addition to the above core–shell structure and epitaxy, heterogeneous SCs could also promote the degradation performance of HCHO on BFCMs by forming solid solutions. The MnOx and CeO2 components in Pt/MnOx–CeO2 formed solid solution MnOx–CeO2, which greatly improved the low temperature reducibility and oxidation activity of MnOx–CeO2 to HCHO.90 Different from the heterogeneous SCs, the secondary synergies within heterogeneous catalysts in BFCMs were also an effective way to enhance the adsorption and degradation of HCHO. In the thermal catalytic oxidation of HCHO by CuO–MnO2/GFS, although HCHO molecules were co-oxidized by copper oxide and δ-manganese dioxide in heterogeneous catalysts, the copper oxide cocatalyst also promoted the oxidation reaction of manganese semi-oxide, which significantly improved the catalytic activities of BFCMs for HCHO.91 This study revealed the mechanism of the MnO2 main catalyst and CuO co-catalyst to promote the thermal oxidation of HCHO, which provided a promising thermal catalyst for industrial waste gas purification. In addition to promoting oxidation, the secondary synergies of heterogeneous catalysts could also be enhanced by regulating the number of catalyst defects and OVs in BFCMs. The number of catalyst defects in the new core–shell (ε-MnO2/CeO2)@CeO2 and the strength of the Mn–O bond in ε-MnO2 could be regulated by process conditions (Fig. 2). More OVs on the CeO2 surface led to stronger catalyst synergies, which significantly increased the Olatt activity on the ε-MnO2 surface.60 The above-mentioned work provided a new idea for the preparation of BFCMs with excellent properties. On the basis of adsorption-catalytic synergism, the secondary synergism of heterogeneous SCs or CCs in BFCMs further improves the catalytic performance of the material through facilitating the adsorption and activation of O2, accelerating the desorption of H2O, promoting the migration of ROS on the surface, etc.
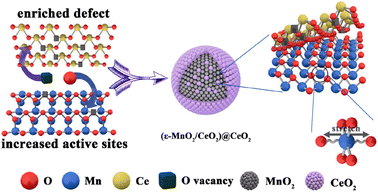 |
| Fig. 2 Schematic illustration for the synergy mechanism of the (ε-MnO2/CeO2)@CeO2 catalyst. Reproduced with permission.60 Copyright 2020, American Chemical Society. | |
2.3.3 Other synergies in bifunctional composite materials.
In addition to the synergies of adsorption and catalysis, structural synergies could also be utilized to improve the degradation performance of HCHO. For example, in 3DOM Au/CeO2, the uniform macro-porous structure in CeO2 collaborated with highly active Au nanoparticles to significantly enhance their oxidation capacity to HCHO.52 It was also possible to enhance the degradation performance of HCHO synergistically through the heat and mass transfer between SCs and catalysts. In α-MnO2/GO, the incorporation of graphene oxide not only improved the light absorption capacity and photothermal conversion efficiency, but also facilitated the heat and electron transfer between catalysts and SCs.38 It is worth mentioning that the enhancement of adsorption in BFCMs was mostly for HCHO, and may also involve O2 and other active groups (such as –OH). Homogeneous dispersion of δ-MnO2 nanorods in δ-MnO2@GO on planar GO significantly enhanced catalytic site exposure and reactant mass transfer. At these widely exposed catalytic sites, the activation of O2 and surface-adsorbed water produced abundant surface ROS and hydroxyl (–OH) groups, which synergistically promoted the activity and stability of HCHO degradation on BFCMs.40 In general, the adsorption-catalytic synergies, the secondary synergies in heterogeneous SCs or CCs, the structural synergies, and the heat and mass transfer synergies in BFCMs greatly improve the adsorption of HCHO, the adsorption and activation of O2, etc., thus improving the degradation performance of HCHO.
3. Analysis of the effects of SCs/CCs in BFCMs and reaction conditions on HCHO removal
Although single-component catalysts (such as MnOx) possess the advantages of low cost and a simple preparation process, their removal performances on HCHO are easily limited by their characteristics. More and more SCs with excellent adsorption properties or supporting ability (such as AC, MOF, etc.) are introduced to combine with CCs to form BFCMs.30,92 Nevertheless, the influence of BFCMs on the degradation performance of HCHO is rather complex, involving various factors such as the preparation process, SCs, CCs, and reaction conditions. Regarding the preparation processes of BFCMs, interested readers may refer to the synthesis methods described in these studies.93,94
3.1 Support components in bifunctional composite materials
Besides maintaining catalyst dispersion, SCs could also serve as adsorption or active sites or indirectly engage in catalytic reactions through interfaces in BFCMs.68 Specifically, SCs could affect the catalytic activity of BFCMs towards HCHO through their crystal phases,15 types,83 morphology,95 pore sizes,51 surfactant groups,39 specific surface areas,96 and stability. In practical scenarios, some of these factors might interact in a synergistic or intertwined manner, thereby complicating the determination of the factors that affect catalytic activity.
3.1.1 Types and structures of support components.
According to reports, there are various types of SCs, and common SCs in BFCMs include inorganic SCs, organic SCs (e.g., carbon and polymers), and inorganic–organic hybrid SCs (e.g., MOFs).94,97 Among them, inorganic SCs could be further subdivided into (Fig. 3): (i) reducible oxide MOx (e.g., FeOx and MnO2), (ii) non-reducible inert or acidic MOx (e.g., Al2O3, SiO2, and Nb2O5), (iii) MOx with oxygen storage capacity (e.g., CeO2), (iv) molecular MOx clusters (e.g., polyoxometalates (POM)), (v) alkaline earth metal hydroxides (e.g., Mg(OH)2 and Be(OH)2), (vi) ceramics and glass, and (vii) other non-oxide inorganic SCs (e.g., TiC and BN).98–101 Among them, the influence of reducibility, acidity and hydrophobicity of SCs on the degradation of HCHO is elaborated in Sections 3.1.7 and 3.1.8. These different types of SCs represented significant differences in HCHO degradation after loading catalysts. For example, in a variety of SCs such as SiO2, Al2O3, TiO2, CeO2, etc., the BFCMs formed by Au loading on CeO2 showed the highest reactivity. This enhancement was attributed to CeO2 surface stable cationic Au species and CeO2-promoted oxygen activation.96 The surface oxygen of these non-noble metal oxides could be activated by noble metals, promoting the migration of bulk lattice oxygen (Olatt) and forming surface reactive oxygen species (ROS), leading to the improvement of HCHO degradation performance.50 Similar studies had also demonstrated that the catalytic activity of noble metals was largely contingent upon the type of metal oxide, particularly those SCs doped with other metal oxides.98 The SCs doped with other metal oxides exhibit significantly enhanced catalytic activity upon loading noble metals, which was attributed to the synergy between different metal oxides. This synergy was revealed to activate noble metal species and facilitate the migration of reactive oxygen species on their surfaces.102–104 For instance, the synergistic effect of CeO2 and Co3O4 in 3DOM Au/CeO2–Co3O4 expedited the migration of reactive oxygen species and activated Au species on the surface of composites, resulting in 100% HCHO conversion at 39 °C.51 It is worth mentioning that the categories of SCs may also affect the active sizes of Au. The various active sizes of Au (such as single atoms, bilayers, sub-nm clusters, clusters (1–2 nm), NPs (2–5 nm), etc.) were demonstrated to be correlated closely with the type of SCs.98
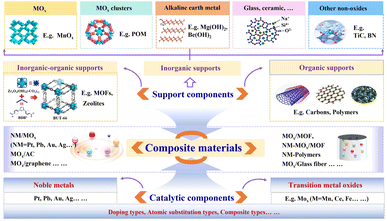 |
| Fig. 3 Types of support components and catalytic components in BFCMs. | |
Additionally, the impact of the support component structure on the catalytic performance of BFCMs encompassed some factors such as their internal structure, surface functional groups, and support component thickness. For instance, compared with powder SCs, the SCs with a 3DOM structure were utilized to load Au nanoparticles, which were more conducive to the dispersion of catalysts and the improvement of catalytic activities.51 Regarding surface functional groups, their introduction could exert an influence on the degradation route of HCHO in BFCMs. After integrating the MnO2 catalyst into graphene nanosheets, the augmented active surface and substantial amount of surface OH-matter significantly streamlined the decomposition path of HCHO without generating CO by-products.10 From the perspective of support component thickness, some developed two-dimensional materials (with thickness <5 nm) enhanced their catalytic performance through short diffusion paths, high specific surface areas, and a large number of active sites.105 For example, ultra-thin (∼4 nm thickness) Bi2WO6 nanosheets loaded with Pt showed good catalytic removal efficiency for HCHO at room temperature, with a removal rate of 93% for 200 ppm HCHO within 1 hour.90 In short, the type and structure of SCs in BFCMs may affect the degradation of HCHO to some extent through the interaction between SCs and CCs, electronic properties and the microstructure. And these factors should be taken into account to optimize the catalytic performance in the design and preparation of BFCMs.
3.1.2 Crystal phases for support components.
The degradation performances of HCHO influenced by different crystal phases for SCs in BFCMs were often ascribed to the exposure of crystal faces or their synergistic interaction with CCs in BFCMs. For instance, in Pt/α-MnO2@δ-MnO2, the {100} surface of α-MnO2 was conducive to the adsorption/activation of O2, while the {001} surface of layered MnO2 was beneficial for the desorption of H2O. The heteroepitaxy structure formed by the α-MnO2 and δ-MnO2 crystal phases in SCs integrated the exposed surfaces {100} and {001} concurrently, leading to a remarkable enhancement of HCHO oxidation activity at room temperature.66 In addition to the exposed crystal surface, the synergistic effect between MnO2 with special crystal phases and the CCs in BFCMs may also affect the improvement of degradation performances for HCHO. For example, the high removal rate of HCHO near room temperature in BFCMs formed by ε-MnO2 and Mn2V2O7 components had been analyzed to be related to the synergistic effect of the two components (Fig. 4a). Due to the similar radii, the incorporation of V5+ ions into the ε-MnO2 structure reduced the crystallinity and increased the specific surface areas of BFCMs, resulting in an increase in the number of surface OVs and adsorbed oxygen molecules, which improved the degradation ability of BFCMs to HCHO.106 Additionally, the crystal phases of SCs could also affect the removal of HCHO through unsaturated coordination atoms. Among the three ZrO2 crystal phases, namely monoclinic (m-ZrO2), tetragonal (t-ZrO2), and cubic (c-ZrO2), m-ZrO2 was structurally stable at room temperature, whereas t-ZrO2 was structurally unstable at 30 °C. Due to the special heptavalent coordination of Zr4+, the OVs of m-ZrO2 and the unsaturated coordination sites on the Zr atom could be used as the active sites for O2 activation and HCHO adsorption.107 The study of Pt-m-ZrO2 nanoparticles for HCHO catalysis at room temperature indicated that the strong metal-support interaction between Pt particles and ZrO2 could improve the catalytic performance of BFCMs.24 In addition to the crystal phases acting as SCs, the different crystal phase transformations of the same substance also provided a possibility for the construction of heterojunction BFCMs.108 In short, crystal phase selection and phase transition of SCs were the common methods to regulate the adsorption/catalytic properties of BFCMs. Selecting the crystal phases with specific crystal face exposure could optimize the surface properties of crystal phases, which was conducive to improving the catalytic performance of BFCMs.
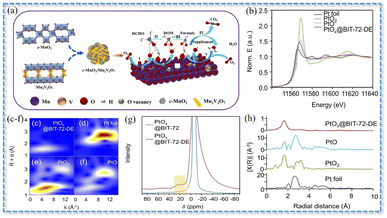 |
| Fig. 4 (a) ε-MnO2/Mn2V2O7 synergistic catalysis mechanism. Reproduced with permission.106 Copyright 2023, Elsevier. Pt L3-edge (b) XANES spectra and (c–f) EXAFS spectra. (g) WT analyses of PtOx@BIT-72-DE, PtO, PtO2, and Pt foil. (h) Al MAS NMR spectra of PtOx@BIT-72 and PtOx@BIT-72-DE. Reproduced with permission.27 Copyright 2022, Wiley. | |
3.1.3 Particle sizes and morphologies of support components.
The shapes, particle sizes and morphologies of SCs were some of the factors affecting catalytic performances, and the BFCMs with enhanced control properties of various sizes and shapes made rapid progress.109–111 Compared with bulk CeO2, the nanoparticle form of CeO2 had a larger surface area and more OVs, resulting in superior reaction and catalytic properties.112 SCs with different particle sizes may also cooperate with other components or groups to promote HCHO degradation performance. The degradation of HCHO by nano-Al2O3 and micron-Al2O3 loaded with Pt under Na doping indicated that the OH groups on the surface of Pt–Na/nAl2O3 showed stronger reaction performance than the OH groups on Pt–Na/mAl2O3.14 The reason was that a considerable amount of HO-μter in nAl2O3 was transformed into HO-μbri(Na–Al) with the aid of Na, which offered anchoring sites for Pt atoms. However, there was nearly no HO-μter on the mAl2O3 catalyst. Additionally, the distinct morphologies of nanoparticles also exerted significant influence on their catalytic performance. After the noble metal Au was deposited on the surface of CeO2 nanoparticles with various morphologies (e.g., nanorods, nanocubes, and nano-octahedra), it was discovered that the different morphologies of SCs in Au/CeO2 impacted the chemical states of Au. The reason was that the water vapor transfer reaction on the surface of CeO2 nanorods was faster than that of polyhedra and nanocubes.113 The reaction between water vapor and surface reactive oxygen species was capable of regenerating the surface hydroxyl group consumed during the oxidation process of HCHO (O2−, O− + H2O → 2-OH), and enhancing the conversion activity of HCHO in humid air.114 Moreover, the diverse morphologies of SCs also exerted an influence on the catalytic activity of BFCMs due to their distinct exposed crystal faces. Rod ceria particles exposed to the {110} and {100} surfaces had a greater catalytic activity than that of cuboidal ceria exposed to the {100} surface and polyhedral ceria exposed to the {111} and {100} surfaces.95 The reason was believed to be related to their relatively low oxygen vacancy formation energy. In brief, the particles and morphology of SCs in BFCMs exerted a profound impact on their catalytic performance. By precisely regulating these parameters, the catalytic performance of BFCMs could be optimized to attain higher efficiency and better application prospects.
3.1.4 Pore sizes of support components.
Pore volumes (Vp) and pore sizes (Dp) were closely related to the diffusion properties inside SCs.3 Too small pore sizes in SCs would affect mass transfer in catalytic applications. The common method was to utilize defect engineering to obtain larger pore sizes, promoting mass transfer and enhancing catalytic activities. For instance, the interior of an aluminum–metal–organic framework (PtOx@BIT-72-DE) after defect engineering treatment exhibited an obvious hollow structure and large pore sizes (e.g. >1 nm). This enabled it to possess good stability, efficient mass transfer, and outstanding HCHO degradation activity.27 It is worth noting that the average size of platinum oxide nanoclusters (PtOx) incorporated into BIT-72-DE within PtOx@BIT-72-DE was approximately 1 nm, and the majority of BIT-72 nanoparticle crystals were approximately 200 nm. The outcomes of X-ray absorption near edge structure (XANES) and extended X-ray absorption fine structure (EXAFS) demonstrated that the distinctive structure of PtOx@BIT-72-DE was intimately associated with the engineering defects of BIT-72-DE (Fig. 4b–h). The specific rate of PtOx@BIT-72-DE after defect engineering was 10.8 times that of PtOx@BIT-72 before defect engineering, representing that the defect engineering and pore sizes were closely related to catalytic activities.
In addition to defect engineering, SCs with large pore sizes could also be obtained through process and technological innovations. Techniques such as the colloidal crystal template method52 and bubbling-assisted deposition precipitation method51 had been developed to prepare 3DOM structures to obtain interconnected networks with adjustable pore sizes and spherical voids. In the 3DOM structure, noble metal nanoparticles were easily distributed and aggregate less, and had good catalytic activities for HCHO. However, a larger aperture was not necessarily more conducive to the improvement of catalytic activities, because the aperture may affect the specific surface areas of the samples and the distribution of noble metals. For example, studies on the catalytic activities of 3DOM Au/CeO2–Co3O4 with pore sizes of 80 nm, 130 nm and 240 nm indicated that the samples with pore sizes of 80 nm had the highest catalytic activity for HCHO oxidation. The reason was the fact that it had the largest specific surface area, smaller pore size and a more uniform distribution of Au nanoparticles.51 Similarly, 3DOM Au/CeO2 with a pore size of 80 nm showed a higher catalytic activity than the catalyst with a pore size of 130 nm. The reason was the fact that Au/CeO2 catalysts with a pore size of 80 nm had a larger surface area than catalysts with other pore sizes. However, the specific surface areas would gradually decrease with the increase in loading of Au nanoparticles.52 These BFCMs with 3DOM structures are expected to be valuable catalyst systems for HCHO removal.
3.1.5 Specific surface areas of support components.
The specific surface areas of SCs usually referred to the sum of inner surface area and outer surface area, and their impact on catalytic activity was frequently correlated with factors such as their types, shapes and pore sizes. Some individuals contended that the augmentation of specific surface areas for SCs could enhance the catalytic activity of the reaction. Studies on the degradation of HCHO by CeO2 loaded with Au indicated that compared with CeO2 with low specific surface areas (e.g., BET 37 m2 g−1), CeO2 with high specific surface areas (e.g., BET 150–270 m2 g−1) could not only provide more OVs through the nanoscale effect, but also facilitate the formation of high oxidation state Au.96 These factors greatly promoted the adsorption of HCHO. Moreover, the interfaces between Au and CeO2 with high surface area were also conducive to the formation of AuxCe1−xO2−δ solid solution, which promoted the conversion of oxygen molecules into active substances. Similarly, it was demonstrated that the co-modification of Pt atoms with the MnOOH phase significantly increased the specific surface areas of the initial MnO2 catalyst. The increased specific surface areas of MnO2 were demonstrated to facilitate the exposure of more active sites of PtSA-MnOOH/MnO2 during the catalytic process, thereby achieving better catalytic removal efficiency of HCHO.29 Besides, the high specific surface areas of SCs could also increase the stability of catalysts and the activity of the reaction by increasing the dispersion of active components.115 Another perspective is that larger specific surface areas of materials did not necessarily imply a greater contribution to the increase in their catalytic activity, particularly for microporous materials (e.g. pore sizes <2 nm). For instance, restricted by the pore sizes of the ZSM-5 molecular sieve, the adsorption and initial degradation of high molecular weight polymers mainly took place on the outer surface or pore opening. Despite the fact that zeolites possessed a high internal surface area, the active sites within these regions could not exert their catalytic activity due to the inaccessibility of these polymers.116 However, the small-sized products after degradation might enter the zeolite channel, leading to variations in product distribution and selectivity. In contrast, the majority of active sites in mesoporous materials (such as MCM-41) supported the degradation of larger-sized polymers to a greater extent. Additionally, the large specific surface areas of SCs in BFCMs typically synergized with hierarchical pores to influence the degradation performance of HCHO. The large surface area and the hierarchical pores not only facilitated the capture of HCHO and oxygen (O2), but also promoted the transfer of HCHO and intermediates.91
It was notable that the specific surface areas of BFCMs might also be influenced by the loading of CCs. Studies revealed that the specific surface areas decreased as the loading of CCs increased. For instance, the specific surface areas of MnO2/UiO-66-NH2 declined with the increase in MnO2 loading (Fig. 5a–c). When the loading capacity of MnO2 increased from 1 wt% to 20 wt%, the specific surface areas of BFCMs dropped from 883 m2 g−1 to 505 m2 g−1, and the conversion of HCHO (100 ppm) at room temperature decreased from 88% to 47% (Fig. 5d).20 The reason was that the excessive loading of MnO2 would not only clog the pores of BFCMs and restrict the access of HCHO molecules to the catalytically active sites, but also cause the catalytic sites to be buried in BFCMs instead of on the active surface. It had also been demonstrated that when the loading of TMO was substantial enough, the specific surface areas of SCs might initially decrease and then increase with the loading.61 The reason was that as the material was further oxidized, more and more MnO2 was interconnected to form porous structures. When the MnO2 loading reached 70%, the specific surface areas of MnO2/NCNT presented an increasing trend, while the average pore diameter and total pore volume also exhibited a trend of initially increasing and then decreasing. Additionally, there were certain cases where the specific surface areas would increase along with the increase in CC loading capacity. For example, the specific surface areas of MnO2@SiO2–TiO2-4, obtained through a combination of electrospinning and liquid phase synthesis, gradually increased from 4.95 to 48.59 m2 g−1 as the loading capacity of MnO2 increased with the increase in the synthesis period from 0 to 5 cycles.43 This was attributed to the fact that the layered structure of the fiber surface augmented the specific surface area of the material, thereby providing more active sites for HCHO oxidation reactions.
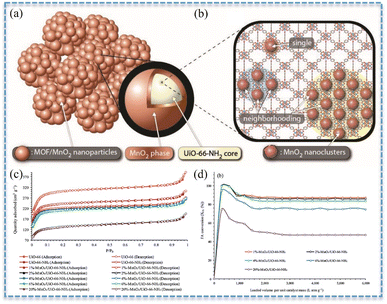 |
| Fig. 5 (a) Combined representation of the MnO2/UiO-66-NH2 phases. (b) MnO2 clusters formed in the UiO-66-NH2 pore structure. (c) N2 adsorption–desorption isotherms. (d) HCHO conversion (HCHO: 100 ppm in air, flow rate: 500 mL min−1, catalyst mass: 5 mg, GHSV: 597 134 h−1, RH: 0%, and TOS: 1 h). Reproduced with permission.20 Copyright 2022, Wiley. | |
3.1.6 Surface active groups of support components.
Existing studies indicated that common active groups (like hydroxyl, amino, etc.) played an important role in the HCHO catalytic reaction. Hydroxyl groups had been reported to assist HCHO degradation through enhanced adsorption of HCHO.76 The hydroxyl group on the surface of ZSM-5 in Pt/ZSM-5 had been demonstrated to be conducive to the adsorption of HCHO and the conversion of intermediates in the HCHO oxidation process.30 Similarly, the suitable catalytic activity of Pt/AlOOH for HCHO was partly attributed to the enhanced adsorption of HCHO resulting from the abundant hydroxyl groups on the surface of the AlOOH carrier.117 In addition, the functional group NH2 could enhance its effective adsorption of HCHO through covalent (formation of an imine/Schiff base) or non-covalent (electrostatic) interactions.118–120 For example, the –NH2 in MnO2/UiO-66-NH2 altered the catalytic process by affecting the activation of HCHO, rather than chemically reacting directly with HCHO. The HCHO–NH2 interaction should be primarily non-covalent (electrostatic), which was further demonstrated by UiO-66-NH2 FTIR spectroscopy.20 It should be mentioned that, in addition to enhancing HCHO adsorption, surface active groups in BFCMs may also directly participate in the reaction to promote HCHO oxidation. The excellent performance of DEA–MnOx–PUF for the oxidation of HCHO was due to the continuous decomposition of the intermediate by the cross-linked amino groups on its surface during the catalytic process.93 The above research provided a new way to develop BFCMs with surface active groups to efficiently remove HCHO. It is worth noting that the active groups in the aforementioned studies could be acquired through in situ synthesis and post-processing. For example, TiO2 nanosheets (TNSs) modified with F−, OH− and Cl− were prepared by hydrothermal and post-treatment methods and utilized for the adsorption and degradation of HCHO. The results indicated that although these adsorbed ions may weaken the interaction between HCHO and TNS surfaces, OH− ions could induce dissociative adsorption of HCHO by trapping an H atom from HCHO to form a formyl group and an H2O-like group.121 This study provided a new idea for the design and preparation of efficient HCHO purification materials. Besides, surface active groups could also be acquired by doping. After doping the Na component, a large amount of HO-μter in the nAl2O3 support was converted to HO–μbri(Na–Al), so that the Pt substance was dispersed at the atomic level, while there was almost no HO-μbri on mAl2O3.14
3.1.7 Reducibility of support components.
The influence of reducibility of SCs on the catalytic performance of BFCMs was a complex issue involving diverse types of CCs and SCs. In most cases, reducible oxide MOx (such as AgO, MnO2, CeO2, and FeOx) could facilitate electron transfer on the catalyst surface and enhance catalytic activity through oxygen activation and oxygen transfer via REDOX cycles among different metal valence states. For instance, the complete oxidation of HCHO by the Ag/MnOx–CeO2 catalyst at 100 °C was investigated in relation to a potential synergistic effect between the silver component, MnOx, and CeO2 in the system. That is, there was oxygen migration in the REDOX cycles of Ag+/Ag0, Mn4+/Mn3+ and Ce4+/Ce3+.56 There was also a distinct viewpoint that the reducibility of SCs had no direct influence on the activity of noble metal particles, but could affect catalytic stability.35 Studies on gold supported by reducible SC materials (like CeO2 and FeOx) and non-reducible SC materials (like γ-Al2O3, SiO2 and HZSM-5) demonstrated that reducible SCs in Au/SCs could stabilize gold via O bonds and exhibit excellent stability in the HCHO oxidation reaction. However, the scarcity of –O and –OH on the surface of non-reducible SCs in Au/SCs weakened the binding force between nano-gold and SiO2/HZSM-5, leading to the tendency of gold particles to aggregate. This study indicated that the reduction of SCs was not the crucial factor influencing the activity of the gold catalyst, but the key factor affecting the oxidation stability of Au/SCs to HCHO.35 Compared with the reducibility of SCs, it was demonstrated that the particle sizes and dispersion of noble metals in Au/SCs had a more significant effect on the oxidation reactivity of HCHO. To sum up, the influence of reducibility of SCs on the catalytic performances of BFCMs covers numerous aspects, such as material composition, electronic structure, and catalytic stability. These factors play an important role in the overall performance and application prospects of BFCMs. Therefore, these factors should be taken into consideration in the design and preparation of BFCMs to optimize the catalytic performance.
3.1.8 Hydrophobicity and acidity of support components.
The hydrophobicity of SCs is an important means to regulate the oxidation properties of BFCMs. The design and construction of SCs with good hydrophobicity are conducive to improving the oxidation capacity of HCHO. In a Pt–nanoPE membrane, Pt was hydrophilic, while PE was hydrophobic (Fig. 6). The electrolyte could spontaneously wet the Pt-coated hydrophilic surface through capillary action and stop at the Pt–PE boundary, while the hydrophobic and interconnected pores of nanoPE remained dry, thus achieving efficient HCHO transport. Together with Pt and electrolyte, hydrophobic nano-PE played a key role in three-phase HCHO catalysis.122 In addition, the hydrophobicity of SCs was often designed in conjunction with the high specific surface areas to enhance the adsorption of HCHO. For example, under the synergistic effect of high hydrophobicity and high specific surface area of reduced graphene oxide (rGO), TiO2-based BFCM (rGO/TiO2) had a better adsorption capacity for HCHO.90 In addition to being bound to the specific surface area, the hydrophobicity of SCs could also be combined with the RH of the environment to study the degradation capacity of HCHO on BFCMs. Moreover, the hydrophobicity of SCs may affect the number of recycling cycles of BFCMs and the removal rate of HCHO.39 Regarding the acidity of SCs, it was mostly in conjunction with the reaction atmosphere to jointly influence the oxidation state of the catalyst, thereby regulating the catalytic activity. The activity of catalysts often varied with the acidity of SCs, and the higher the acidity of SCs, the higher the catalytic activities of noble metal supported by SCs. The comparative study of MgO, La2O3, ZrO2, Al2O3, SiO2, and SiO2–Al2O3 supported Pt-based BFCMs in an oxidizing atmosphere indicated that the Pt on acidic SCs was less oxidized than that on basic SCs, suggesting that the increase in the acid strength of SCs was conducive to the enhancement of oxidation resistance of Pt. The increase in the acid strength of SCs in a reducing atmosphere would lead to an increase in the electron deficit for Pt.123
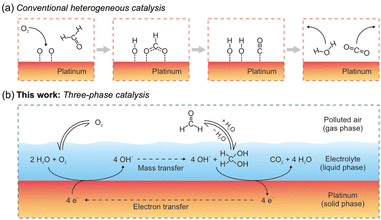 |
| Fig. 6 Reaction schemes for the oxidation of HCHO on Pt. (a) Conventional heterogeneous catalysis involves adsorption, diffusion, reaction, and desorption, constrained on a two-dimensional surface. (b) Three-phase catalysis speeds up the process by introducing a new liquid phase, with mass transfer and electron transfer facilitated by the electrolyte and Pt, respectively. Reproduced with permission.122 Copyright 2020, American Chemical Society. | |
3.2 Catalytic components in bifunctional composite materials
The efficient catalytic oxidation of HCHO at room temperature is one of the most promising technologies. The influence of catalyst components on the degradation performance of HCHO is commonly related to the types, crystal phases, morphologies, shapes, particle sizes, dispersion, metal chemical states and loading capacities of CCs.
3.2.1 Types of catalytic components.
Different types of catalysts often include noble metals, TMOs, various element doping types, atomic substitution types, and so on.124–127 Different kinds of catalysts would significantly affect the catalytically activities. The oxidation of HCHO by TiO2 loaded with different kinds of noble metals (such as Pt, Rh, Pd, and Au) indicated that the oxidation activity of HCHO was in the order of Pt/TiO2 > Rh/TiO2 > Pd/TiO2 > Au/TiO2. The reason was the fact that Pt on TiO2 had a higher dispersion than other noble metals.128 Compared with noble metals, element doping and atomic substitution was a good strategy to improve catalytic activities by regulating the electronic structure and introducing active sites. A small amount of doping tended to result in atomic or ion substitution, while excessive doping would lead to formation of clusters or local phase transformation. When a mixture of urea and α-MnO2 was calcined in a N2 atmosphere, it was found that the doping of N atoms in different sites of α-MnO2 could be regulated by the variation of urea dosage, and the catalytic decomposition performance of HCHO for α-MnO2 after doping was significantly improved. In particular, the gap N-doped α-MnO2 had better catalytic performance for HCHO, which could completely catalyze the decomposition of HCHO into carbon dioxide and water at 90 °C.129 This study explored the influence of nitrogen anion doping sites, and provided a reference for the design and preparation of HCHO purification decomposition materials.
3.2.2 Crystal phases, morphologies and shapes of catalytic components.
The corresponding morphologies and shapes of different crystalline phases for the same substance may be significantly different. Most studies on the crystalline phase of catalysts focused on metal oxides such as MnO2 and CeO2.130–132 In particular, for MnO2, among its four common crystalline phases (such as α-type, β-type, γ-type, and δ-type), δ-MnO2 was considered to have the highest catalytic activity due to its tunnel structure and easy release of Olatt.88 However, like most other non-noble metal oxides, a single δ-MnO2 phase often required a higher temperature for HCHO oxidation, and its low temperature and efficient catalytic performance still depended on the combination of different materials, noble metal doping, surface OV engineering and other technologies. The morphologies of different catalysts may affect the catalytic performance due to the difference in OV content and other factors. The catalytic decomposition of HCHO by four kinds of α-MnO2 morphologies (such as nanowires, nanotubes, nanorods and nanoflowers) assisted by mechanical vibration at room temperature indicated that the decomposition performance of nanowires > nanotubes > nanorods > nanoflowers was morphology-dependent.133 The reason was the highest Mn3+/Mn4+ molar ratio and OV content of α-MnO2 nanowires, followed by nanotubes, nanorods and nanoflowers.16 The morphology difference may also affect the mass transfer performance of catalysts. For example, the order of external diffusion properties of MnO2 for HCHO with different morphologies was nanospheres > nanorods > three-dimensional mesh structure > nanosheets > nanofibers (Fig. 7).3
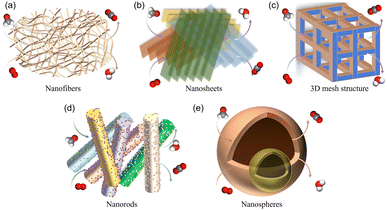 |
| Fig. 7 Schematic diagram of external diffusion of HCHO in five typical MnO2 morphologies: (a) nanofibers, (b) nanosheets, (c) three-dimensional mesh structure, (d) nanorods, and (e) nanospheres. | |
In terms of catalyst shapes, materials with ultra-thin two-dimensional nanosheet shapes presented great potential in generating surface defects. Ultra-thin two-dimensional nanosheets not only had the advantages of large specific surface areas, ultra-thin thickness, abundant active sites and a short diffusion path, but also had a large number of surface defects, including dangling bonds and coordination unsaturated atoms at the edge.46 These factors played a key role in the excellent catalytic performance and stability of catalysts. Moreover, the shape of catalysts may also vary the catalytic performance by affecting gas mass transfer, and so on. Compared with nanosheets, monolayer MnO2 made the external diffusion of HCHO on the catalyst easier, and improved the mass transfer ability and catalytic activities of HCHO. In addition, compared with bulk catalysts, powder shaped MnO2 greatly limited its scope of usage due to its easy agglomeration and tendency to result in the blockage of porous channels for SCs.
3.2.3 Particle sizes and dispersion of catalytic components.
In most cases, smaller nanoparticles have more abundant active sites, which is conducive to the dissociative adsorption of oxygen on the catalyst surface, resulting in a higher HCHO oxidation rate.1 For instance, the interfacial length of Au/CeO2 was inversely proportional to the square of the radius of Au NP nanoparticles, and the catalytic activities increased linearly with the increase in interfacial length, which proved that the particle sizes had an important influence on catalytic activities.98 It was concluded that size-related variations in catalytic activities may not depend on the number of low-coordination Au atoms, but on the number of Au atoms at the perimeter interface of BFCMs. However, there was a different viewpoint in another study. It had been suggested that the catalytic activity of Au NPs was closely related to low coordination Au atoms (such as angular atoms with coordination number 6 or lower), while the influence of perimeter Au atoms on gas oxidation was not in consideration.134 Additionally, as far as Pt was concerned, the design or selection of suitable size nanoparticles was beneficial to the improvement of activity and stability. There is a volcanic relationship between the reaction rates of HCHO and different particle sizes of Pt (like single-atom, nanocluster and nanoparticle scale) in Pt/TiO2. The results indicated that HCHO had the best degradation performance on Pt nanocluster-based composites with a size of around 1 nm.22 It is worth noting that element doping might also exert an influence on the particle sizes and dispersion of CCs, thereby influencing the catalytic activity of BFCMs. For instance, the addition of cerium could restrain the growth of manganese oxide particles in Mn1−xCex/PG. With the increase in cerium content (x = 0.1–0.5, x = Ce/(Mn + Ce)), the average particle sizes of manganese oxide particles increased from 2.87 nm to 6.86 nm. Nevertheless, if the content of Ce was properly controlled (x ≤ 2), the introduction of cerium could conspicuously enhance the dispersion of Mn–Ce oxides, giving rise to the formation of high contact interfaces and grain boundaries with MnO2. The results indicated that Mn0.9Ce0.1/PG displayed the highest catalytic activity in the oxidation of HCHO and was capable of completely removing 300 ppm of HCHO at 160 °C and 20
000 h−1 GHSV.62 In addition, there were some special cases in which the bulk shape would also provide some benefits to catalytic activities. For example, for silver, which was prone to surface oxidation, the bulk shape prevented excessive oxidation of silver inside, causing the bulk silver to exhibit higher activity than smaller silver nanoparticles. It was believed that the shell prevented the further oxidation of silver in a biphasic silver block (Ag@AgOx) composed of a metal core and oxide shell.26
In addition to particle sizes, particle dispersion would also affect catalytic activities. Stability studies of transition metal atoms (TM/MXene, TM = Au, Ag, Ru, Rh, Pt, Pd, Ti, V, Cr, Co, Ni, Cu, Zn, Cd and Hg) modified on MXene monolayers indicated that Ti/Ti3C2O2 was found to be the most stable system compared to other transition metals. The reason was that Ti atoms were more easily dispersed on the surface of Ti3C2O2 in the form of single atoms without aggregating, which significantly improved their oxidation activity to HCHO.135 In addition, studies on HCHO catalyzed by different BFCMs loaded with Au (such as Au/SiO2, Au/HZSM-5 and Au/γ-Al2O3) indicated that the reaction rate was linearly related to the Au particle sizes, indicating that the smaller the particle sizes and the higher the dispersion of Au, the higher the oxidation activity of HCHO.
3.2.4 Metal chemical states of catalytic components.
The chemical state of metals was considered to be a possible inducer of chemisorption of HCHO. For example, in a study of low temperature oxidation of HCHO by Au/CeO2, it was demonstrated that the chemisorption of HCHO molecules at high oxidation states of Au (like Au+ and Au3+) was stronger than that of low oxidation states of Au (like Au0).96 Similarly, the negatively charged Pd could enhance the electron transfer of Pd to the π* orbital of O2, further promoting the adsorption of O2 and the oxidation of HCHO.36 Moreover, different chemical states of metals could regulate the oxidation capacity of HCHO by influencing OVs. In (ε-MnO2/CeO2)@CeO2, the presence of Mn3+ would create OVs to maintain electrostatic equilibrium. Since the molar ratio (2.21) of Mn3+/Mn4+ on the surface of C-T120 was greater than 1 compared to that of C-T100, C-T120 would produce abundant OVs, which greatly improved the removal rate of HCHO (Fig. 8).60 Similarly, the presence of Ce3+ led to the creation of OVs to maintain charge balance. Moreover, the higher the Ce3+/Ce4+ ratio of the C-T120 surface, the more the OV content, and the stronger the oxidation capacity of C-T120 to HCHO. It should be mentioned that the chemical status and content of the noble metal may vary due to the variation in the surface area of SCs. The content of low oxidation state gold (Au0) decreased with the increase in CeO2 surface area, while the content of high oxidation state gold (Au+ and Au3+) increased with the increase in CeO2 surface area. The reason was the strong adsorption of HCHO molecules on high surface area catalysts, and also the formation of formic acid states, which were considered to be intermediates of HCHO oxidation. At the same time, it was suggested that enhanced chemical adsorption may also be induced by nanoscale CeO2.136
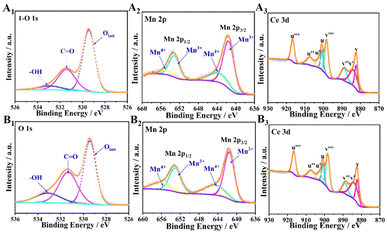 |
| Fig. 8 (1) O 1s, (2) Mn 2p, and (3) Ce 3d spectra of the catalysts: (A) C-T100 and (B) C-T120. Reproduced with permission.60 Copyright 2020, American Chemical Society. | |
The chemical state of metal could be regulated by support component-assisted electron transfer, ammonia modification, element doping, and so on. For example, manganese oxides were thought to be the catalysts with the highest HCHO oxidation activity among TMOs.137 This activity was analyzed to derive from the REDOX cycle between manganese species (Mn4+/Mn3+), resulting in a continuous oxygen activation and oxygen transfer process that promoted electron transfer on catalyst surfaces.56 Considering enhancing the electron transfer and conductivity of manganese oxide, graphene was introduced as a support component to form graphene–MnO2 nanocomposite materials. The additional interface of the hybrid region facilitated charge transfer between the different oxidation states of Mn4+/Mn3+, resulting in high reaction rates and good catalytic performance.10 Similarly, the content of Mn3+ and OV concentration in BFCMs could be adjusted by ammonia modification. A study of HCHO degradation by MnOx/AC–N2 at room temperature indicated that the excellent catalytic performance of BFCMs was attributed to the regulation of OVs by ammonia modification, while the increased Mn3+ content in catalysts led to the formation of more surface OVs to maintain electrostatic equilibrium. The existence of abundant OVs promoted the adsorption, activation and migration of O2 molecules to form more ROS.10 Different from modification, doping was another method to achieve the regulation of metal oxidation states in BFCMs. For example, the doping of Ce or Co elements could replace some Mn4+ sites to increase the content of Mn3+ and surface vacancy defects in catalysts, thereby improving the catalytic performance of materials.138 It should be noted that the oxidation state of metals in BFCMs could be varied by regulating the type of precipitants (such as NH3·H2O, KOH, NH4HCO3, K2CO3 and KHCO3).139
3.2.5 Loading capacities for catalytic components.
A remarkable disparity existed in the loading capacity of noble metals (e.g., Pt, Au, Pd, Ag, and Rh) when noble metal-based BFCMs were employed for HCHO degradation at low temperatures. The majority of Pt-based BFCMs with high HCHO oxidation activity at room temperature possessed Pt loading capacities ranging from 0.1 wt% to 2 wt%.2 In contrast to Pt-based BFCMs, the catalytic activity of most Au-based BFCMs was relatively low, and the efficient elimination of HCHO at low temperatures typically demanded considerable Au loading capacities (commonly 1 wt% to 8.0 wt%),15 such as 7.1 wt% Au/Fe2O3.59 Compared with Pt and Au, studies related to Pd-based BFCMs (e.g., 0.1 wt%Pd/beta zeolites, 0.1 wt%Pd/TiO2, 0.25 wt%Pd/γ-Al2O3, and 1 wt%Pd/CeO2) were scarcer, and the loading capacities of Pd for HCHO degradation at room temperature mainly ranged from 0.1 wt% to 1 wt% (Table 1). In contrast to Pt, Au and Pd, most Ag-based BFCMs demonstrated relatively low oxidation activity towards HCHO at room temperature (e.g., <30 wt%). Furthermore, the requisite loading capacities of Ag were relatively high (≥3 wt%), such as 3 wt%Ag/MnOx–CeO2 (ref. 56) and 8 wt%Ag/3DOM–Co3O4.55 Compared with the aforementioned noble metals, the oxidation of HCHO by rhodium (Rh) at room temperature was less reported. The reported loading capacities of Rh for HCHO degradation at room temperature were generally within the range of 0.5–1 wt%, and the activity of supported Rh catalysts seemed to be relatively low.13,128
In terms of reaction conditions and the conversion rate, the conversion rate of HCHO did not increase linearly with the increase in noble metal loading capacities. Instead, there existed an optimum loading capacity. For instance, when the loading capacity of Pt increased from 0.3 wt% to 1 wt%, the conversion of Pt/TiO2 to HCHO at room temperature escalated to 100%. Nevertheless, when the loading capacity of Pt was augmented from 1 wt% to 2 wt%, the conversion rate of HCHO remained scarcely variable. Hence, in this study, the optimal loading capacity of Pt on TiO2 was ascertained to be 1 wt%.128 The optimal loading capacity of Pt in diverse reaction systems exhibited more or fewer dissimilarities. In contrast to Pt/TiO2, the removal rates of HCHO by Pt-VO-ZrO2 with varying Pt loading capacities were in the sequence of 0.87 Pt-VO-ZrO2 > 1.32 Pt-VO-ZrO2 > 0.51 Pt-VO-ZrO2 > ZrO2.24 Before attaining the optimal loading capacity, the augmentation of noble metal content was beneficial for enhancing the activity of BFCMs. However, once this optimal loading capacity was surpassed, the continuous increase in noble metal loading capacity might result in a decline in the activity of BFCMs. The reason was that the excessive loading would probably cause adverse effects such as accumulation of active substances, specific surface reduction, and pore blockage. Compared with 1 wt% Pt/sepiolite, the overloading of Pt on 2 wt% Pt/sepiolite led to the aggregation of Pt particles and an increase in catalyst sizes, resulting in a decrease in active sites and specific surface areas of Pt nanoparticles. In addition, the pores and channels of sepiolite nanofibers may also be blocked by the aggregated Pt nanoparticles, resulting in the reduction of their specific surface areas.76 Similarly, 7 wt% Pt/ZrO2–GA–MOF-5 presented the highest activity due to its optimal loading of Pt, while the over-loading 9 wt% Pt led to a decrease in catalytic efficiency. The reason was the accumulation of Pt nanoparticles caused by excessive loading, resulting in a decrease in specific surface areas, thus reducing the catalytic effect.140
3.3 Effect of reaction conditions on HCHO degradation
In addition to the above factors, the degradation of HCHO would also be affected by a variety of reaction conditions, mainly including heat, light, electricity, the initial concentration of HCHO, relative humidity, environmental media, pH and gas flow rate. In practical applications, these parameters need to be optimized according to the conditions to improve the degradation efficiency of HCHO.
3.3.1 Heat, light and electricity.
3.3.1.1 Thermal catalysis.
In the catalytic process of HCHO, temperature was one of key factors affecting the catalytic activities and stability of BFCMs. At a lower temperature, some reaction intermediates/products adsorbed on the catalyst surface tended to block the active sites. In contrast, an increased temperature was prone to facilitate desorption of intermediates and/or products to promote the release of active sites or improve product selectivity.19 For example, while the removal efficiency of HCHO on MnOx/AC–N2 decreased slightly with increasing temperature, the CO2 selectivity increased significantly. This was attributed to the fact that the increased temperature made it easier for CO2 to release from intermediates and/or products.92 However, excessive temperature conditions would also have some adverse influence on the reaction, including increasing energy consumption or causing some other problems in the nanomaterial composite process. For example, for small-size nanoclusters with high interfacial energy and poor thermal stability, relatively high temperatures tended to cause irreversible growth and agglomeration.23 In addition, high temperature conditions also tended to lead to pore collapse and lower specific surface areas, resulting in a poor HCHO removal performance (Fig. 9e and f).141
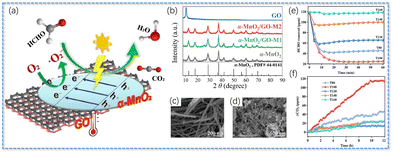 |
| Fig. 9 (a) Graphene-enhanced photothermal decomposition of carcinogenic HCHO by α-MnO2, (b) XRD patterns of different samples, (c) α-MnO2 and (d) α-MnO2/GO-M1. Reproduced with permission.38 Copyright 2022, Elsevier. HCHO removal (e) and CO2 production (f) over the MIL-88B(Fe) nanorods (sample T100) and the control samples. Reproduced with permission.141 Copyright 2021, American Chemical Society. | |
3.3.1.2 Photocatalysis and photothermal catalysis.
Owing to low energy consumption, non-toxicity, cost-effectiveness and mild reaction conditions, photocatalysis is regarded as a promising technology for HCHO degradation. However, photocatalysts were frequently affected by electron–hole recombination, significantly reducing their photocatalytic performance. To alleviate this problem, researchers had proposed various strategies. Firstly, the construction of heterogeneous structures or composite materials had been demonstrated to be an effective strategy to inhibit electron–hole pair recombination and enhance electron transport, thereby improving photocatalytic activity under visible light. For instance, the Bir/P25-2 composite exhibited a photoelectric value that was 4.59 times higher and a band gap that was 1.7 times wider than those of birnessite, leading to significantly enhanced charge separation efficiency.101 The Bir/P25-2 composite demonstrated superior photocatalytic activity, achieving the removal of 80 ppm of gaseous HCHO within 50 minutes under visible light irradiation. This enhanced performance was attributed to the increased number of OVs in Bir/P25-2 compared to birnessite, which facilitated the generation of more superoxide free radicals and hydroxyl free radicals, thereby accelerating pollutant decomposition. Secondly, the band gap of photocatalysts could be narrowed through metal ion or non-metallic element doping, extending its response range into the visible light spectrum.142 Thirdly, the usage of auxiliary catalysts or sacrificial agents could also aid in the separation of electron–hole pairs, further enhancing photocatalytic efficiency.143 Beyond their application in HCHO degradation, BFCMs (e.g. Fe–PEI–CN) based on photocatalysis exhibited significant potential for wastewater purification.144,145
In order to reduce the energy consumption caused by heating, a light-regulated photothermal catalysis technique was developed to improve the catalytic activities of HCHO.11,38,146 It is well known that manganese oxides had a strong thermal catalytic activity, but also had a generally low photocatalytic activity.147–149 Studies indicated that the incorporation of graphene oxide (GO) with strong light absorption ability and high photothermal conversion efficiency could enhance electron transport and effective separation of electrons from holes.18 The degradation rate of HCHO by the resultant nanocomposite α-MnO2/GO at room temperature and in light was as high as 100%, and its PXRD and SEM are shown in Fig. 9a–d.38 This work not only provided a new strategy for the combination of catalysts and photothermal materials to utilize solar energy, but also expanded the research on the photocatalysis of manganese oxides in HCHO.
3.3.1.3 Electrocatalysis and photoelectron catalysis.
Conventional electrocatalytic processes necessitate an external power source, which greatly restricts their commercial viability. In recent years, the electrocatalytic technology combined with the piezoelectric effect has attracted more and more attention. When subjected to mechanical stress, piezoelectric materials would generate an internal electric field that could modulate the charge migration behaviour of catalysts, thereby enhancing electrocatalytic efficiency. For instance, the piezoelectric effect could degrade HCHO by inducing polarization in two-dimensional piezoelectric material 2H–MoS2, inhibiting photogenerated electron–hole pair recombination and promoting the generation of hydroxyl radicals.150 Furthermore, self-powered triboelectric technology represents an alternative approach for achieving electrocatalytic HCHO degradation by leveraging the contact electrification effect and the principle of electrostatic induction. This method harnesses mechanical energy from the ambient environment and converts it into electrical energy for utilization. For instance, MnOx–PMMA self-powered triboelectric catalysts with a three-dimensional nanocomposite structure, driven by wind-induced friction between PMMA fibers and SSM, generated triboelectric charges that promoted reactive oxygen species (ROS) formation, thus accelerating the catalytic oxidation of HCHO and intermediates. At ambient temperature and under a 15 ppm HCHO atmosphere, this composite achieved a CO2 yield increase of 78.93% compared to MnOx catalysts.151 This study provided a new strategy for efficient, long-term, low-energy HCHO degradation at ambient temperature. On this basis, photo-electron catalysis combines the advantages of both photocatalysis and electrocatalysis, improving photogenerated carrier separation efficiency and regulating electron directional transfer via the applied voltage, thereby enhancing reaction rates and selectivity.152 A nano-catalyst Pt/TiO2–ZnO prepared using the sol–gel method and supported on a stainless steel mesh removed 74% of HCHO through photo-electron catalytic oxidation within 120 minutes.81
In short, thermal catalytic oxidation commonly necessitates elevated reaction temperatures, resulting in substantial energy consumption and rendering it unsuitable for natural environments. Nonetheless, this method retains potential in specific industrial applications, particularly where rapid treatment of large volumes of pollutants is required. In contrast, photo-catalysis may attract much attention due to its high efficiency and environmental protection, while photo-thermal catalysis and photo-electron catalysis technologies would also present important application prospects in the field of HCHO degradation due to their higher potential and flexibility.
3.3.2 Initial concentration of HCHO.
The impact of the initial HCHO concentration on its degradation is a multifaceted issue. Most studies indicated that higher initial HCHO concentrations facilitated faster diffusion of pollutant molecules to the catalyst surface, accelerating oxidative damage and enhancing removal capacity.153 However, excessively high initial concentrations may paradoxically reduce degradation rates of HCHO. For instance, as the initial HCHO concentration increased from 149 mg m−3 to 336 mg m−3, the degradation rate increased from 51% to 73%. Nevertheless, when the concentration further escalated to 660 mg m−3, the HCHO degradation rate declined to 44%.154 Another study observed that the degradation rate of HCHO diminished with increasing initial concentration. When the initial concentrations of HCHO were 0.2 ppm, 0.4 ppm and 0.6 ppm, the corresponding degradation rates of HCHO by Pt/LV over a 30 minute period were 100%, 80% and 66.7%, respectively. It was demonstrated that the composite material Pt/LV required a longer duration to degrade higher concentrations of HCHO. This phenomenon was attributed to the fact that a higher initial concentration necessitated the consumption of more O2 molecules, leading to the formation of additional H2O molecules which competed for the active sites with HCHO molecules.155 Similarly, with the increase in initial concentrations (e.g. 8.0 mg m−3, 16.0 mg m−3, 24.0 mg m−3, 32.0 mg m−3, and 40.0 mg m−3), the removal rate of HCHO by composite CoAl-LDHs decreased significantly from 72.5% to 40.3%.85 In contrast to the two aforementioned perspectives, other studies indicated that the removal efficiency of HCHO by composite materials was largely unaffected by the initial concentration of HCHO.156 This suggested that the HCHO removal rate by NPCS/Pt-4 remained consistent across varying initial concentrations (e.g. 60 ppm, 100 ppm, 200 ppm, 300 ppm, 400 ppm, and 500 ppm).
3.3.3 Relative humidity.
Relatively high or low humidity would mostly generate a negative impact on the degradation of HCHO.157–160 Relatively low humidity easily led to insufficient water adsorbed on the catalyst surface to generate surface –OH groups, which inhibited the improvement of HCHO oxidation performance. It was easy for the relatively high RH to reduce the activity and stability of catalysts for the oxidation of HCHO.161 Compared with 30% RH, the conversion rate of HCHO at 0.87Pt-VO-ZrO2 at 75% RH gradually decreased to 64%. These results suggested that the increased RH deactivated the catalysts, which should be attributed to the competitive adsorption of water and HCHO molecules at the active sites.24 Similarly, studies on the removal of HCHO by δ-MnO2@GO-RT under different RH conditions (RH = 0%, 25%, 50%, 75%, 100%) indicated that it had the best oxidation performance for HCHO at 50% RH.162 There are also control experiments with a humidity of 0 and 50%, which presented that [O]s at 50% humidity could directly react with H2O to form [OH]s, resulting in a higher catalytic activity of PtOx@BIT-72-DE than that under dry conditions.27 It is worth mentioning that a moderate increase in RH could promote the catalytic oxidation of HCHO and its intermediates. In the absence of water or RH = 0, it was easy for intermediates to accumulate on the catalyst surface, resulting in catalyst poisoning.47 With the increase in RH (RH = 4–76%), the HCHO mineralization efficiency of Au@Co3O4 increased. Similarly, the catalytic study of HCHO by Pt/SBT-400 suggested that the CO32− ions formed during the oxidation of HCHO may be adsorbed on the surface of catalysts, resulting in a decrease in the activity of Pt/SBT-400. However, the OH group formed by the conversion of water on the catalyst surface could convert CO32− ions into CO2(g), thus reducing the degree of catalyst poisoning.34
3.3.4 Environmental media and pH.
Noble metal-related BFCMs had the advantages of low temperature and high efficiency degradation of HCHO, while high cost, poor thermal stability, easy poisoning and inactivation greatly limit their application range. There were many environmental media that cause the inactivation of noble metal related BFCMs, such as fluorine, chlorine, Br−, I−, sulfur, SO2 and CO.163 It is well known that residual Cl− from Pt-related catalysts obtained from Pt precursors such as H2PtCl6 and PtCl4 could lead to inactivation by blocking the active site on Pt.44 This deactivation problem related to environmental media has affected the application of BFCMs to some extent. Fortunately, it had been found that the catalytic activities of BFCMs could be improved by treating them with alkali metal salts, as alkali metal salts (such as NaOH and Na2CO3) had been demonstrated to provide hydroxide ions (OH−) that replace the Cl− adsorbed on Pt, resulting in increased catalytic activities. Similarly, studies of fluorosis by Pt/FTiO2–NS on the oxidative decomposition of HCHO had indicated that the mechanism of F poisoning was mainly due to the strong interaction between Pt and highly electronegative F (such as Pt–F bonds) that blocked the catalytically active sites on Pt.32 The catalytic properties of BFCMs were recovered by an efficient regeneration method of NaOH washing. In other words, catalyst poisoning or competitive side reactions induced by environmental media in BFCMs would negatively affect the degradation of HCHO.164 In addition, the pH of the reaction system had more or less influence on the HCHO degradation performance of BFCMs. The degradation experiment of HCHO at MnO2@PMIA-6 at room temperature indicated that acidic conditions promoted the reaction of MnO4− with the –OH on the surface of PMIA to produce Mn2+, and a further disproportionation reaction with MnO4− to produce Mn3+. The formation of Mn3+ would promote more O atoms to escape from [MnO6] due to charge balance, resulting in the generation of more OVs, thus significantly improving the catalytic performance of nanometer-scale MnO2 at room temperature.39
3.3.5 Gas velocity.
The gas flow rate was generally regulated by using a mass flow controller. When the HCHO gas residence time was unvaried, the increase in airflow velocity was conducive to improving the external mass transfer (such as the particle gap) of catalysts and improving the catalytic efficiency.165 When the residence time was shortened, the catalytic efficiency of HCHO would decrease with the increase in airflow velocity. The Weisz-Prater criterion was commonly used to evaluate the influence of internal diffusion and reaction in heterogeneous catalytic reactions, which could be expressed as eqn (4).3Here, r′ was the observed reaction rate per unit weight of catalysts (mg gcat−1 s−1), and Rp was the catalyst radius (m). ρc was the catalyst density (g m−3), Cs was the catalyst surface reactant concentration (mg mcat−3), and De was the effective diffusion coefficient (m2 s−1). The reaction rate r′ could be calculated from eqn (5) as the total reactant consumed per unit weight of catalyst (m) (concentration difference multiplied by the flow rate G). In addition, the diffusion type was an important factor affecting the mass transfer of HCHO molecules. The Knudsen number could be used to determine the type of molecular diffusion in the pore, as shown in eqn (6).where λ represented the mean free path and r was the aperture. When Kn ≫ 1, it corresponded to Knudsen diffusion. According to the calculation, the mean free path of the HCHO molecule was 146 nm, resulting in Kn ≥ 32.44 ≫ 1. In this case, the molecular collisions were negligible, and all the momentum transfer occurred at the pore wall. However, once the aperture exceeded a certain critical length, the Knudsen coefficient tended to be constant.40 For fixed bed structures, velocity affected the residence time t and mass transfer coefficient. The residence time t could be calculated as the layer depth divided by the velocity, while the mass transfer coefficient (km) could be calculated by the correlation of Sherwood numbers (Sh), Schmidt numbers (Sc) and Reynolds numbers (Re) in eqn (7) and (8),166 where d was the equivalent diameter of catalyst particles, and D was the diffusion coefficient of HCHO molecules in air. Under experimental conditions Re was about 102. | 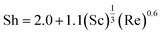 | (7) |
When the residence time was different, the catalyst efficiency decreased with the increase in flow rate, and it was closely related to the contact time between HCHO and the catalyst surface. It is worth mentioning that, unlike the contact time, the residence time was calculated as the depth of filling catalyst divided by speed. The longer the contact time, the higher the pollutant removal efficiency. The reduction of airflow speed allowed the reactant to fully come into contact with the active sites.167 In other words, the mass transfer coefficient varied with contact time, which depended on airflow speed.
3.3.6 Other factors.
In addition to the above reaction conditions, other factors (such as vibration) may also have an impact on catalytic activities. The catalytic decomposition performance of HCHO under vibration conditions was studied. The results indicated that vibration could significantly enhance the activity of α-MnO2, and the decomposition efficiency was much higher than that of vibration and catalysts alone. A low frequency vibration (e.g., 25 kHz) had a more significant effect on HCHO decomposition than a high frequency vibration (e.g., 40 kHz) because it was conducive to a higher mass transfer rate and active free radical yield. In contrast, a higher vibration power enhanced the catalytic activities of the material for HCHO decomposition by inducing vibration and friction between nanoparticles and generating heat.16
3.4 The degradation pathways of HCHO
Density functional theory (DFT) simulations were often combined with other analytical measurements to analyze the mechanisms associated with the HCHO adsorption/oxidation pathway, including in situ diffuse infrared Fourier transform spectroscopy (DRIFTS) and X-ray photoelectron spectroscopy (XPS).168–171 The adsorption behavior of reactants (O2 and HCHO) and subsequent oxidation path of HCHO could be illustrated by density functional theory (DFT) calculation and in situ diffuse infrared Fourier transform (DRIFT) spectroscopy analysis.24
By analogy with the VOC oxidation mechanism, three kinetic mechanisms of HCHO oxidation were analyzed to elucidate the reaction pathways, namely the Mars-van Krevelen (MVK) mechanism, Langmuir–Hinshelwood (L–H) mechanism, and Eley–Ridea (E–R) mechanism (Fig. 10). (i) As for the MVK mechanism, the adsorbed HCHO molecules first reacted with the Olatt on the catalyst surface to form OVs. Then, compensation of airborne oxygen or oxygen atoms in the bulk phase regenerated the reduction center.54,172,173 (ii) As for the L–H mechanism, the first step was the adsorption of oxygen and HCHO on catalysts, followed by the REDOX process. According to whether HCHO and oxygen were adsorbed at the same active site, the L–H model could be divided into the single-point L–H model and two-site L–H model.174 (iii) In the E–R mechanism, the catalytic process occurred between adsorbed oxygen and gas-phase HCHO molecules, or between adsorbed HCHO molecules and gas-phase oxygen.77,175,176
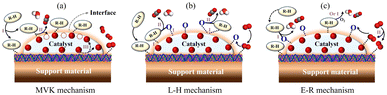 |
| Fig. 10 Kinetic model of VOC oxidation on BFCMs: the (a) MVK mechanism, (b) L–H mechanism, and (c) E–R mechanism. | |
Among the three mechanisms, most studies had indicated that the oxidation pathway of HCHO followed the MVK mechanism, in which Olatt played a key role. The main reactions involved in these studies are listed in Table 2. For example, the lattice O in Au/Fe2O3 was activated by the loaded Au and further participated in the MVK process to oxidize HCHO.177 Similarly, MnO2/UiO-66-NH2 also followed the HCHO oxidation mechanism similar to MVK. During oxidation, HCHO was first adsorbed onto the lattice by interacting with Zr in the lattice, while O2 molecules were split into O atoms at the same location, and then HCHO and O atoms react to form CO2 and H2O. Among them, there were three types of possible products which formed after the combination of HCHOads with *O2, and each type of product further reacted to produce CO2 and H2O as final products.20 In addition to surface Olatt, chemisorbed ROS (such as O2−, O− or OH) were demonstrated to play an active role in the activation of HCHO and O2, and also the oxidation of HCHO and intermediates.180 Surface oxygen preferentially located at OVs (such as the defect of MnO2) could not only activate molecular oxygen as an electron donor to form adsorbed substances lacking electrons (such as O2− and O−), but also react with H2O to form surface hydroxyl groups (O2−, O− + H2O → –OH) to assist the adsorption and degradation of HCHO.181 Among the other two possible mechanisms (i.e. L–H mechanism and E–R mechanism) of HCHO oxidation, the selection of a specific mechanism was speculated to be related to the structure of BFCMs and their surface catalytic reaction. For example, in the catalytic oxidation reaction of HCHO on the surface of FeN3-graphene, the L–H mechanism was believed to dominate the oxidation of HCHO.182 Similarly, the oxidation of HCHO catalyzed by δ-MnO2@GO mainly followed the L–H mechanism.40 By comparing the L–H and E–R oxidation mechanisms of HCHO on Ti/Ti3C2O2, it was suggested that the E–R mechanism had a lower energy barrier in the rate-limiting step. It made the huge energy release of HCHO dissociative adsorption on Ti/Ti3C2O2 with activated O2 promote the subsequent reaction steps as well as good catalytic cycle efficiency.135
Table 2 Main elementary reactions for HCHO oxidation
Equation no. |
Reaction class |
Elementary reactions |
Ref. |
1 |
ROS generation |
O2 + e− = O2− |
177
|
2H2O + 4h+ → O2 + 4H+ |
O2− + 2H+ + e− = H2O2 |
H2O2 + e− = OH− + ·OH |
OH− + h+ → ·OH |
2 |
ROS propagation |
O* + H2O → 2*OH |
24
|
HCHO + O* → *HCOOH |
*HCOO + *OH → CO2 + H2O |
3 |
ROS propagation |
O2(ads) → O2(ads)− → O(ads)− → O2(ads/lattice)− |
50
|
4 |
ROS generation, ROS propagation, and HCHO oxidation |
□ + hv → e− + h+ |
178
|
h+ + OH(ads)− or H2O(ads) → ·OH + H+ |
e− + O2(ads) → ·O2− |
HCHO + ·OH → DOM |
DOM + ·OH → HCOOH |
HCOOH + ·O2− → HCO3− + ·OH |
HCOOH + ·OH → HCOO− + H2O |
HCOO− + ·OH → CO2 + H2O |
5 |
ROS generation, ROS propagation, and HCHO oxidation |
HCHO⋯OH + H2O → H2C(OH)2 |
19
|
H2C(OH)2 + O* → H2COO⋯OH + H2O |
H2COO⋯OH + O* → HCOOH⋯OH |
HCOOH⋯OH + O* → ·CO3⋯OH + H2O |
2H+ + ·CO3⋯OH → CO2 + H2O |
6 |
HCHO oxidation |
FAads + *O2 → *O + *H2CO2 |
20
|
FAads + *O2 → *O + *HCOOH |
FAads + *O2 → *OH + *HCOO− |
7 |
HCHO oxidation |
HCHO → DOM (dioxymethylene) |
179
|
→formates → carbonates → CO2 |
8 |
HCHO oxidation |
HCHO → DOM → HCOOH/HCOO− |
46
|
→H2CO3/HCO3− → CO2 + H2O |
In practical applications, the oxidation pathway and products of HCHO may be affected by calcination temperature and RH. Taking Au/CeO2 as an example, according to the difference of pretreatment calcination temperatures (such as 350 °C, 550 °C and 750 °C), the intermediate products could be divided into three categories: (i) DOM and formate; (ii) formate, DOM and carbonate species; (iii) formate and carbonate species. On CeO2-based BFCMs, the oxidation of HCHO mainly followed the MVK mechanism, that is, it mainly oxidized HCHO to CO2 and H2O through surface Olatt.63 In addition to calcination temperature, the degradation pathway of HCHO may also vary due to an increase in ambient RH. For example, under dry conditions, [O]s reacted with HCHO to form adsorbed formate, and the separated hydrogen atoms reacted with [O]s to form [OH]s, which would further react with formate to form [H2CO3], and produced the final products CO2 and H2O. However, as the reaction occurred, the adsorbed water in the PtOx@BIT-72-DE channel gradually increased. Under wet conditions, [O]s could directly react with H2O to form [OH]s, resulting in a higher catalytic activity of PtOx@BIT-72-DE under wet conditions than that under dry conditions.27
4. Long-term stability, regeneration performance and recyclability
In addition to evaluating the influence of SCs, catalysts and reaction conditions on the catalytic performance of HCHO, it was also crucial to consider the catalytic stability and regeneration performance capability of BFCMs in practical applications.183–185
4.1 Long-term stability of bifunctional composite materials
Due to the uncertainty of RH in the surrounding environment, the study on the stability and water resistance of BFCMs was of great significance in practical applications. In order to study the reproducibility and durability of Pt-related BFCMs, the retention ratios of Pt/Fe2O3@SnO2, Pt/Fe2O3 and Pt/SnO2 to the removal capacity of HCHO were still as high as 94.40, 98.77 and 95.58%, respectively, after repeated oxidation at room temperature 5 times without any regeneration treatment. This implied that Pt-based catalysts exhibited outstanding stability and high efficiency for HCHO removal (Fig. 11).21 Similarly, when RH was 30%, the initial conversion rate of HCHO on 0.87Pt-VO-ZrO2 was 95%. The conversion rate remained at 93% after 720 min of reaction, which meant that the BFCMs had good stability.24 In addition, after the 250 min cycle test, the removal ability of MnOx/AC–N2 to HCHO did not decrease significantly, indicating that the BFCMs had good durability. The good durability of BFCMs was attributed to the stability of surface OVs as the catalytically active sites for the cyclic reaction of catalysts.92 With the increase in RH (20–50%), MnOx/AC–N2 had no significant influence on the removal rate of HCHO (97.5–87.1%), indicating that the BFCMs had a good water resistance.
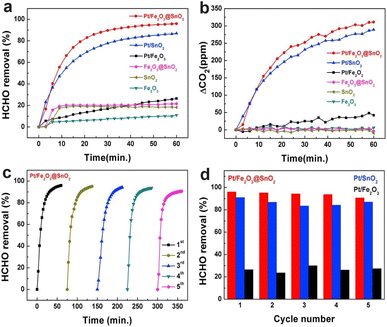 |
| Fig. 11 (a) HCHO removal capability of the samples; (b) variations of CO2 concentrations during HCHO removal; (c) consecutive 5-cycle HCHO removal treatment of Pt/Fe2O3@SnO2; (d) comparison of the reusability of the samples. Reproduced with permission.21 Copyright 2018, Elsevier. | |
4.2 Regeneration of bifunctional composite materials
In general, BFCMs suitable for large-scale applications of HCHO removal should be easy to regenerate in addition to high activity and long-term stability. The existing research indicated that there were many approaches for regeneration, such as temperature control regeneration, alkali washing regeneration, soaking regeneration and so on.
4.2.1 Thermal regeneration.
Thermal regeneration of BFCMs was a method to restore the activity of catalysts by regulating the temperature. The primary objective was to eliminate deactivating factors such as formate, carbonate, and carbon deposition on the catalyst surface, thereby restoring the original catalytic performance. Considering factors like energy consumption and structural stability, the common temperature control regeneration process was mostly implemented at a relatively low temperature.2 For example, after PtSA–MnOOH/MnO2 was kept in a drying oven at 105 °C for 15 min, static tests were performed to study its thermal regeneration stability. The results indicated that the material maintained almost the same catalytic oxidation capacity after 6 thermal regeneration-static test cycles, suggesting that it had good thermal regeneration stability.29 Likewise, MnO2@PMIA-t was kept in an air oven at 110 °C for 2 h to complete the regeneration of BFCMs. After 4 cycles of accelerated washing and 4 cycles of regeneration, the catalytic degradation efficiency of MnO2@PMIA-6 remained at 90.97% (only 4.46% loss of catalytic activity).39 MnO2/PET (polyethylene terephthalate) could be regenerated in situ and reactivated without undergoing any rinsing treatment after being heated in a 105 °C oven for 30 minutes. Besides, the sample heated at 105 °C for 30 minutes showed similar HCHO removal capabilities to the original synthetic sample. Compared with the first test, the HCHO removal efficiency of the regenerated samples did not decrease significantly after 5 repeated tests.167 It is worth mentioning that this study revealed that MnO2 nanosheets in MnO2/PET could promptly convert HCHO into formate and carbonate at room temperature. However, formate was challenging to be further oxidized to CO2, leading to its accumulation on the catalyst surface and coverage of active sites, thereby restricting the degradation activity of HCHO on MnO2/PET. After undergoing in situ heating regeneration treatment at 105 °C, the formate ester covering MnO2/PET could be further decomposed into carbonate and desorbed from the catalyst surface to release CO2.167 This straightforward thermal regeneration process enabled the rapid restoration of catalytic activity for the used MnO2/PET, rendering it a recyclable and highly efficient HCHO purification material.
In addition to low temperature heating, the regeneration of BFCMs could also be achieved through high temperature calcination. A study indicated that Fe–Mn binary metal oxides could achieve regeneration and recovery of catalytic activities after being calcined at 250 °C in air for 1 h.60 It is worth mentioning that in some cases, the degree of regeneration of BFCMs could be judged based on their adsorption isotherm. For example, if there was no significant hysteresis in the water absorption isotherm of a sample, it may mean that its regeneration process was relatively easy to achieve.186 In conclusion, the thermal regeneration of BFCMs was a sophisticated process, encompassing numerous technologies and approaches. Through rational control of temperature and other circumstances, the activity of catalysts could be effectively restored to minimize resource waste and prevent environmental pollution.
4.2.2 Alkali washing regeneration.
Alkaline washing regenerated BFCMs referred to a process where the deactivated catalyst was treated with an alkaline solution to regain its activity. Common alkaline solutions for catalyst regeneration encompass NaOH, Na2CO3, and other alkaline reagents.44 Previous studies had demonstrated that residual halogen ions (such as F−, Cl−, Br−, and I−) adhering to the surface of noble metals could cause catalyst poisoning effects, with residual concentrations reaching up to 4 mg g−2. For instance, in the composite Pt/MnOx–CeO2, the residual Cl− in the Pt-related catalyst obtained from the Pt precursor not only hindered the reduction of Pt but also migrated to the MnOx–CeO2 support and replaced the cerium oxygen vacancies by forming the CeOCl species. This rendered the Pt–Cl catalyst necessary to be reduced at a higher temperature, leading to a decline in the activity of Pt/MnOx–CeO2.44 In this case, the OH− ions furnished by alkali metal salts could effectively substitute the Cl− adsorbed on the surface, facilitating the double dehydrogenation of HCHO molecules, as well as the regeneration of Pt-based BFCMs and the activation of O2 molecules.187 Similarly, the fluorosis mechanism of Pt/FTiO2–NS in the HCHO oxidation process mainly originated from the strong interaction between Pt and the highly electronegative F, which blocked the catalytically active sites of Pt components, and inhibited the adsorption of O2 or the generation of reactive oxygen species.32 In a strongly alkaline environment, F− on TiO2–NS could be nearly completely removed by washing with NaOH solution to restore the catalytic activity of Pt/TiO2–NS. In conclusion, the aforementioned method of alkaline washing regeneration employing NaOH, Na2CO3 and other alkaline reagents could enhance the activity of BFCMs by providing hydroxide ions (OH−) to replace the halogen ions adsorbed on Pt and actualize the purpose of composite catalyst regeneration.2
4.2.3 Other regeneration approaches.
Besides thermal regeneration and alkali washing regeneration, there existed several other regeneration approaches, like reagent soaking regeneration and purging regeneration. Reagent immersion regeneration was a technique that recovered the catalyst's activity through a chemical method. The specific operation involved soaking the spent catalyst in a specific solvent to eliminate carbon deposits or other deactivated substances, thereby restoring its activity. For instance, it had been reported that Fe–Mn binary metal oxide catalysts possessed outstanding HCHO oxidation properties, with a conversion rate of up to 100% for HCHO at room temperature.19 In the catalyst regeneration experiment, after soaking the spent catalyst with 3% H2O2 for 10 minutes, the catalytic activity was restored, indicating the feasibility of material regeneration through soaking. FTIR spectroscopy demonstrated that the catalyst was reactivated by H2O2 regeneration because the intermediates covering the active surface sites (such as DOM, HCOO− and carbonate) were removed through immersion with the H2O2 reagent. Additionally, H2O2 treatment was conducive to increasing the content of active metal components (such as Mn3+ and Mn4+) and surface adsorption of oxygen, thereby accelerating the recovery of the catalyst's activity.15 It is worth mentioning that the successful regeneration of this material could also be achieved by calcination at 250 °C in air for 1 h. In conclusion, reagent soaking constituted an effective approach for chemical regeneration, and the regeneration activity and service life of the catalyst could be significantly enhanced through the judicious selection of solvents and treatment conditions. Apart from soaking regeneration, purging regeneration could also be employed to restore the catalytic activity. To recycle the catalyst, the sample δ-MnOx was purged with H2O/O2 for 1 h to attain the regeneration objective.188 In contrast to the sample prior to purging, the sample after 5 tests of H2O/O2 purging exhibited a high and stable HCHO removal efficiency (91%), while the sample S-30 without H2O/O2 purging demonstrated a gradual decline in HCHO removal efficiency from 91% to 78% after 5 tests. It was speculated that the mixed H2O in the purge gas played a crucial role in the recovery of activity. Not only could H2O form hydrogen bonds with HCHO to facilitate the adsorption of HCHO, but the adsorbed HCHO was oxidized by the structural hydroxyl group to form formate (bridging type) and carbonate (monodentate and bridging type). Most importantly, surface reactive oxygen species (e.g., O2− and O−) could react with water (O2−, O− + H2O → 2-OH) to regenerate the consumed surface –OH.
4.3 Recyclability of bifunctional composite materials
The recyclability of BFCMs constituted an important research direction, aiming at improving catalytic efficiency, prolonging the service life of catalysts, and minimizing the waste of resources. From a cost perspective, recyclability was an essential issue worthy of consideration in practical applications. If there were no significant alterations in phases, structure or crystallinity after several repeated uses, it indicated that the sample had high recyclable value. For instance, after 7 cycles of experiments, the XRD peak of ZT/GF0.2 hardly varied, and its removal rate of HCHO (94.38%) and CO2 production rate scarcely declined, indicating that this sample possessed good recyclability and significant practical application value.189 Similarly, 1.8 wt% Au/CeO2 demonstrated no significant loss of activity after 6 cycles of catalytic reaction, suggesting that the sample exhibited multiple cycles of oxidation of HCHO and recyclability.167 The spent MnO2/PET could be simply regenerated by heating at 105 °C for 30 min, indicating that MnO2/PET could be utilized as a recyclable material for the removal of toxic HCHO from indoor air. In conclusion, the recyclability of BFCMs is a multi-faceted matter, involving the structure, phase, catalytic activity of the catalyst, and specific recovery technology. Through continuous research and technological improvement, it is anticipated that more efficient and environmentally friendly BFCM recycling strategies would be achieved in the future.
5 Conclusions and future perspectives
Bifunctional composite materials have made great breakthroughs and progress with their superior synergies, becoming one of the most promising materials in the field of VOC removal. In this study, the research progress of adsorption-enhanced catalytic degradation of HCHO based on BFCMs was summarized in detail. In this paper, we first discuss the design and preparation of BFCMs, as well as the multistage synergies (such as adsorption-catalytic synergies, heterogeneous synergies within SCs or CCs, structural synergies, and heat and mass transfer synergies) in BFCMs. These synergetic effects significantly enhanced the adsorption of HCHO, increased the exposure of active sites, and accelerated mass transfer. The activation of O2 and surface adsorbed water at these sites generated an abundance of surface ROS and hydroxyl groups, which was beneficial for further enhancing the activity and stability of BFCMs to degrade HCHO. Meanwhile, to further clarify the influencing factors of HCHO degradation, the impacts of SCs, CCs, and reaction conditions (such as initial concentration of HCHO, light/heat/electricity, relative humidity, environmental media and pH) on HCHO removal in BFCMs are analyzed. Based on the conversion rate of HCHO and specific rate, the degradation performances of BFCMs are evaluated under dynamic and static circumstances, and the degradation pathways of HCHO are also analyzed in combination with DFT calculation. Finally, considering the feasibility of BFCMs in catalytic applications, the relevant issues such as long-term stability, renewability, and recyclability of BFCMs are summarized. In short, the study of adsorption enhanced catalytic degradation of airborne HCHO by BFCMs holds practical feasibility and universality. This study could offer a valuable reference for the design, development, and optimization of regulatory factors for HCHO removal materials in air.
In the future, in addition to thermal catalysis, photocatalysis, photothermal catalysis and photoelectric catalysis, ultrasonic catalysis and/or ultrasonic assisted catalysis may be utilized as an emerging environmental treatment technology for the HCHO removal. It can not only enhance the exposure of active sites on the catalyst surface, but also facilitate improved mass and heat transfer between reactants and catalysts, thereby enhancing catalytic efficiency. The integration of these technologies would provide comprehensive and efficient solutions for HCHO treatment in the future.
Data availability
No primary research results, software or code have been included and no new data were generated or analysed as part of this review.
Conflicts of interest
The authors declare that they have no known competing financial interests or personal relationships.
Acknowledgements
We acknowledge financial support from the National Key R&D Program of China (No. 2022YFC3902604), the National Natural Science Foundation of China (No. 52425004 and 22305011), the R&D Program of Beijing Municipal Education Commission (No. KM202210005009), and Beijing Natural Science Foundation (No. 2242002).
References
- L. Zhou, S. He, Y. Sang, X. Zhang, H. Liu, C. Jia and X. Xu, Catal. Commun., 2020, 142, 106034 CrossRef CAS
.
- J. Guo, C. Lin, C. Jiang and P. Zhang, Appl. Surf. Sci., 2019, 475, 237–255 CrossRef CAS
.
- J. Gong, S. Rong, X. Wang and Y. Zhou, J. Cleaner Prod., 2022, 377, 134242 CrossRef CAS
.
- Z. Zheng, C. Zhang, J. Li, D. Fang, P. Tan, Q. Fang and G. Chen, J. Hazard. Mater., 2024, 474, 134710 CrossRef CAS PubMed
.
- X. J. Zheng, Z. Jaued, C. Liu, A. Tanuir, O. Sandhu, H. R. Liu, X. G. Ji, C. Z. Xing, H. Lin and D. L. Du, J. Environ. Sci., 2024, 135, 656–668 CrossRef CAS PubMed
.
- X. Wang, J. Li, J. Xing, M. Zhang, R. Liao, C. Wang, Y. Hua and H. Ji, J. Colloid Interface Sci., 2024, 656, 104–115 CrossRef CAS PubMed
.
- S. Niu and H. Yan, J. Hazard. Mater., 2015, 287, 259–267 CrossRef CAS PubMed
.
- X. Wang, Z. Xu, J. Li, M. Zhang, K. Li, Y. Zheng and H. ji, Appl. Surf. Sci., 2023, 637, 157917 CrossRef CAS
.
- X. Wang, F. Yang, J. Yi, J. Kong, J. Gong, A. Yuan, Z. Rui and H. Ji, AIChE J., 2022, 69, e17895 CrossRef
.
- L. Lu, H. Tian, J. He and Q. Yang, J. Phys. Chem. C, 2016, 120, 23660–23668 CrossRef CAS
.
- T. He, S. Rong, D. Ding, Y. Zhou, N. Zhang and W. He, ACS Catal., 2023, 13, 8049–8062 CrossRef CAS
.
- Y. Hua, Y. Ahmadi and K.-H. Kim, Adv. Sci., 2023, 10, 2300079 CrossRef CAS PubMed
.
- X. Sun, J. Lin, H. Guan, L. Li, L. Sun, Y. Wang, S. Miao, Y. Su and X. Wang, Appl. Catal., B, 2018, 226, 575–584 CrossRef CAS
.
- Z. Zhang, G. He, Y. Li, C. Zhang, J. Ma and H. He, Environ. Sci. Technol., 2022, 56, 10916–10924 CrossRef CAS PubMed
.
- J. Chen, D. Yan, Z. Xu, X. Chen, X. Chen, W. Xu, H. Jia and J. Chen, Environ. Sci. Technol., 2018, 52, 4728–4737 CrossRef CAS PubMed
.
- T. He, D. Shao, X. Zeng and S. Rong, Chemosphere, 2020, 261, 127778 CrossRef CAS PubMed
.
- M. Zhang, B. Huang, H. Jiang and Y. Chen, Front. Chem. Sci. Eng., 2017, 11, 594–602 CrossRef CAS
.
- Z. Wang, H. Yu, L. Zhang, L. Guo and X. Dong, J. Taiwan Inst. Chem. Eng., 2020, 107, 119–128 CrossRef CAS
.
- H. Xie, X. Chen, C. Zhang, Z. Lao, X. Liu, X. Xie, R. Semiat and Z. Zhong, Environ. Sci.: Nano, 2022, 9, 767–780 RSC
.
- K. Vikrant, K. H. Kim, C. He and D. A. Giannakoudakis, Adv. Funct. Mater., 2022, 32, 2107922 CrossRef CAS
.
- T. Lv, C. Peng, H. Zhu and W. Xiao, Appl. Surf. Sci., 2018, 457, 83–92 CrossRef CAS
.
- X. Sun, J. Lin, Y. Chen, Y. Wang, L. Li, S. Miao, X. Pan and X. Wang, Commun. Chem., 2019, 2, 27 CrossRef
.
- H. Wu, Y. Liu, G. Chen, T. Li, W. Jiang, R. Jia, M. Zhang, S. Yuan, L. Shi and L. Huang, ACS Appl. Nano Mater., 2022, 5, 13100–13111 CrossRef CAS
.
- S. Peng, R. Li, Y. Huang, Y. Zhang, J.-j. Cao and S. Lee, Appl. Surf. Sci., 2022, 600, 154056 CrossRef CAS
.
- G. Li and L. Li, RSC Adv., 2015, 5, 36428–36433 RSC
.
- Z. Xu, J. Chen, S. Cai, D. Yan, X. Chen, W. Xu, J. Chen and H. Jia, Mater. Today Energy, 2019, 14, 100343 CrossRef
.
- L. Ren, Q. Ma, A. Yin, X. Feng, T. Zhang and B. Wang, ChemSusChem, 2022, 15, e202201324 CrossRef CAS PubMed
.
- G. Zhang, Z. Sun, Y. Duan, R. Ma and S. Zheng, Appl. Surf. Sci., 2017, 412, 105–112 CrossRef CAS
.
- J. Yu Zheng, K. Ling Zhou, W. Kang Zhao, Y. Wang, J. He, X. Wang, H. Wang, H. Yan and C. Bao Han, J. Colloid Interface Sci., 2022, 628, 359–370 CrossRef PubMed
.
- X. Liu, Y. Liu, Y. Wu, S. Dong, G. Qi, C. Chen, S. Xi, P. Luo, Y. Dai, Y. Han, Y. Zhou, Y. Guo and J. Wang, J. Hazard. Mater., 2023, 458, 131848 CrossRef CAS PubMed
.
- J. Xie, S. Wang and F. Wang, Appl. Surf. Sci., 2023, 644, 158709 CrossRef
.
- L. Nie, P. Zhou, J. Yu and M. Jaroniec, J. Mol. Catal. A: Chem., 2014, 390, 7–13 CrossRef CAS
.
- M. Chen, W. Wang, Y. Qiu, H. Wen, G. Li, Z. Yang and P. Wang, ACS Catal., 2022, 12, 5565–5573 CrossRef CAS
.
- M. Huang, Y. Li, M. Li, J. Zhao, Y. Zhu, C. Wang and V. K. Sharma, Environ. Sci. Technol., 2019, 53, 3610–3619 CrossRef CAS PubMed
.
- B. Chen, X. Zhu, Y. Wang, L. Yu and C. Shi, Chin. J. Catal., 2016, 37, 1729–1737 CrossRef CAS
.
- C. Zhang, Y. Li, Y. Wang and H. He, Environ. Sci. Technol., 2014, 48, 5816–5822 CrossRef CAS PubMed
.
- Y. Huang, Y. Liu, W. Wang, M. Chen, H. Li, S.-c. Lee, W. Ho, T. Huang and J. Cao, Appl. Catal., B, 2020, 278, 119294 CrossRef CAS
.
- X. Zeng, C. Shan, M. Sun, D. Ding and S. Rong, Chin. Chem. Lett., 2022, 33, 4771–4775 CrossRef CAS
.
- Z. Duan, Y. Zhou, H. Yang, D. Yan, D. Song, H. Liu, B. Deng, S. Peng and W. Xu, Chem. Eng. J., 2023, 472, 145104 CrossRef CAS
.
- Y. Li, T. Dong, P. Huang, J. Ji and H. Huang, Appl. Catal., B, 2024, 341, 123322 CrossRef CAS
.
- S. Gong, W. Wang, K. Chen, K. Xiao and Y. Yin, J. Environ. Chem. Eng., 2022, 10, 107571 CrossRef CAS
.
- Y. Jiao, C. Jing, Y. Wang, F. Yao, G. Ye, X. Wang, G. Zhao, W. Peng, H. Huang and D. Ye, Appl. Surf. Sci., 2023, 639, 158215 CrossRef CAS
.
- F. Cui, W. Han, Y. Si, W. Chen, M. Zhang, H. Y. Kim and B. Ding, Compos. Commun., 2019, 16, 61–66 CrossRef
.
- X. Tang, J. Chen, X. Huang, Y. Xu and W. Shen, Appl. Catal., B, 2008, 81, 115–121 CrossRef CAS
.
- H. Huang, X. Ye, H. Huang, L. Zhang and D. Y. C. Leung, Chem. Eng. J., 2013, 230, 73–79 CrossRef CAS
.
- S. Sun, X. Wu, Z. Huang, H. Shen, H. Zhao and G. Jing, Chem. Eng. J., 2022, 435, 135035 CrossRef CAS
.
- Q. Liu, Y. Wang, M. Wen, Y. Guo, Y. Wei, G. Li and T. An, Environ. Sci.: Nano, 2022, 9, 4162–4176 RSC
.
- M. He, J. Ji, B. Liu and H. Huang, Appl. Surf. Sci., 2019, 473, 934–942 CrossRef CAS
.
- Z. Qu, D. Chen, Y. Sun and Y. Wang, Appl. Catal., A, 2014, 487, 100–109 CrossRef CAS
.
- H. Li, S. Fang, G. Jiang and Z. Zhang, Environ. Sci.: Nano, 2023, 10, 80–91 RSC
.
- B. Liu, Y. Liu, C. Li, W. Hu, P. Jing, Q. Wang and J. Zhang, Appl. Catal., B, 2012, 127, 47–58 CrossRef CAS
.
- J. Zhang, Y. Jin, C. Li, Y. Shen, L. Han, Z. Hu, X. Di and Z. Liu, Appl. Catal., B, 2009, 91, 11–20 CrossRef CAS
.
- H. Li, X. Liu, C. Guo, T. Liu and J. Lu, Chin. J. Catal., 2009, 30, 1001–1006 CAS
.
- S. J. Park, I. Bae, I.-S. Nam, B. K. Cho, S. M. Jung and J.-H. Lee, Chem. Eng. J., 2012, 195–196, 392–402 CrossRef CAS
.
- B. Bai and J. Li, ACS Catal., 2014, 4, 2753–2762 CrossRef CAS
.
- X. Tang, J. Chen, Y. Li, Y. Li, Y. Xu and W. Shen, Chem. Eng. J., 2006, 118, 119–125 CrossRef CAS
.
- X. Zhu, X. Gao, R. Qin, Y. Zeng, R. Qu, C. Zheng and X. Tu, Appl. Catal., B, 2015, 170, 293–300 CrossRef
.
- H. Tan, D. Chen, N. Li, Q. Xu, H. Li, J. He and J. Lu, Chem.–Eur. J., 2019, 25, 16718–16724 CrossRef CAS PubMed
.
- C. Li, Y. Shen, M. Jia, S. Sheng, M. O. Adebajo and H. Zhu, Catal. Commun., 2008, 9, 355–361 CrossRef CAS
.
- S. Zhang, H. Wang, H. Si, X. Jia, Z. Wang, Q. Li, J. Kong and J. Zhang, ACS Appl. Mater. Interfaces, 2020, 12, 40285–40295 CrossRef CAS PubMed
.
- S. Peng, X. Yang, J. Strong, B. Sarkar, Q. Jiang, F. Peng, D. Liu and H. Wang, J. Hazard. Mater., 2020, 396, 122750 CrossRef CAS PubMed
.
- C. Wang, H. Liu, T. Chen, C. Qing, X. Zou, J. Xie and X. Zhang, Appl. Clay Sci., 2018, 159, 50–59 CrossRef CAS
.
- Y. Li, P. Sun, T. Liu, L. Cheng, R. Chen, X. Bi and X. Dong, Sep. Purif. Technol., 2023, 311, 123236 CrossRef CAS
.
- J. Wang, Q. Huang, W. Zhou, Y.-Y. Luo, J.-H. Shi, F.-X. Huang and J. Shi, Chem. Eng. J., 2025, 504, 158892 CrossRef CAS
.
- H. Zhiwei, G. Xiao, C. Qingqing, H. Pingping, H. Jiming, L. Junhua and T. Xingfu, Angew. Chem., Int. Ed., 2012, 57, 4198–4203 Search PubMed
.
- J. Zhou, L. Qin, W. Xiao, C. Zeng, N. Li, T. Lv and H. Zhu, Appl. Catal., B, 2017, 207, 233–243 CrossRef CAS
.
- T. He, X. Zeng and S. Rong, J. Mater. Chem. A, 2020, 8, 8383–8396 RSC
.
- C. Ma, G. Pang, G. He, Y. Li, C. He and Z. Hao, J. Environ. Sci., 2016, 39, 77–85 CrossRef CAS PubMed
.
- J. Ye, M. Zhou, Y. Le, B. Cheng and J. Yu, Appl. Catal., B, 2020, 267, 118689 CrossRef CAS
.
- L. Nie, S. Xin, C. Fang, H. Chen and Y. Yang, Chem. Eng. J., 2024, 479, 147830 CrossRef CAS
.
- M. Wang, L. Zhang, W. Huang, T. Xiu, C. Zhuang and J. Shi, Chem. Eng. J., 2017, 320, 667–676 CrossRef CAS
.
- G. Wang, B. Huang, Z. Lou, Z. Wang, X. Qin, X. Zhang and Y. Dai, Appl. Catal., B, 2016, 180, 6–12 CrossRef CAS
.
- J. Wang, G. He, C. Wang, X. Chen, X. Liu, Y. Li, W. Shan and H. He, Appl. Catal., B, 2024, 347, 123787 CrossRef CAS
.
- W. Tan, S. Xie, X. Zhang, K. Ye, M. Almousawi, D. Kim, H. Yu, Y. Cai, H. Xi, L. Ma, S. N. Ehrlich, F. Gao, L. Dong and F. Liu, ACS Appl. Mater. Interfaces, 2023, 16, 454–466 CrossRef PubMed
.
- D. C. Fang, J. Y. Zheng, C. B. Han, W. K. Zhao, Y. G. Lu, B. C. Sun, L. Sun, X. Wang and H. Yan, Appl. Catal., B, 2023, 334, 122837 CrossRef CAS
.
- Y. Ma and G. Zhang, Chem. Eng. J., 2016, 288, 70–78 CrossRef CAS
.
- C. Yang, G. Miao, Y. Pi, Q. Xia, J. Wu, Z. Li and J. Xiao, Chem. Eng. J., 2019, 370, 1128–1153 CrossRef CAS
.
- S. K. Mondal, P. Aina, A. A. Rownaghi and F. Rezaei, ChemPlusChem, 2024, 89, e202300419 CrossRef CAS PubMed
.
- Q. Yu, Y. Feng, J. Wei, X. Tang and H. Yi, Chin. Chem. Lett., 2022, 33, 3087–3090 CrossRef CAS
.
- A. Keunecke, M. Dossow, V. Dieterich, H. Spliethoff and S. Fendt, Front. Energy Res., 2024, 12, 1344179 CrossRef
.
- C. Nie, L. Liu and R. He, Sep. Purif. Technol., 2018, 206, 316–323 CrossRef CAS
.
- Y. Chen, Z. Mai, S. Fan, Y. Wang, B. Qiu, Y. Wang, J. Chen and Z. Xiao, J. Membr. Sci., 2021, 628, 119233 CrossRef CAS
.
- A. Farhad, M. Hossein, R. Mashallah, T. Shima, B. Addie, K. Frank, M. A. Tejraj, L. Jian-Rong and A. Mohammad, Prog. Mater. Sci., 2021, 125, 100904 Search PubMed
.
- Y. Shi, X. Guo, Y. Wang, F. Kong and R. Zhou, Green Energy Environ., 2023, 8, 1654–1663 CrossRef CAS
.
- S. Xia, G. Zhang, Y. Meng, C. Yang, Z. Ni and J. Hu, Appl. Catal., B, 2020, 278, 119266 CrossRef CAS
.
- T. Lv, C. Peng, H. Zhu and W. Xiao, Appl. Surf. Sci., 2018, 457, 83–92 CrossRef CAS
.
- L. Nie, J. Yu, X. Li, B. Cheng, G. Liu and M. Jaroniec, Environ. Sci. Technol., 2013, 47, 2777–2783 CrossRef CAS PubMed
.
- W. Jinlong, L. Jinge, J. Chuanjia, Z. Peng, Z. Pengyi and Y. Jiaguo, Appl. Catal., B, 2016, 204, 147–155 Search PubMed
.
- H. Chen, Z. Rui, X. Wang and H. Ji, Catal. Today, 2015, 258, 56–63 CrossRef CAS
.
- K. Vellingiri, K. Vikrant, V. Kumar and K.-H. Kim, Chem. Eng. J., 2020, 399, 125759 CrossRef CAS
.
- W.-J. Qiang, Q. Huang, J.-H. Shen, Q.-F. Ke, J.-Y. Lü and Y.-P. Guo, J. Cleaner Prod., 2022, 368, 133089 CrossRef CAS
.
- Y. Huang, Y. Liu, W. Wang, M. Chen, H. Li, S.-c. Lee, W. Ho, T. Huang and J. Cao, Appl. Catal., B, 2020, 278, 119294 CrossRef CAS
.
- G. S. Zhu, J. Y. Zheng, C. Bao Han, H. Zhang, P. Chang, W. Kang Zhao, J. He, Y. Xia, X. Song and H. Yan, ChemistrySelect, 2023, 8, 4060 Search PubMed
.
- S. Zhu, J. Zheng, S. Xin and L. Nie, Chem. Eng. J., 2022, 427, 130951 CrossRef CAS
.
- Q. Xu, W. Lei, X. Li, X. Qi, J. Yu, G. Liu, J. Wang and P. Zhang, Environ. Sci. Technol., 2014, 48, 9702–9708 CrossRef CAS PubMed
.
- H.-F. Li, N. Zhang, P. Chen, M.-F. Luo and J.-Q. Lu, Appl. Catal., B, 2011, 110, 279–285 CrossRef CAS
.
- J. He, X. Yu, X. Luan, H. Li, S. J. Shah, W. Su, Z. Jia, J. Chen, L. Zhou, J. Deng, Z. Zhao, Z. Huang and Z. Zhao, Chem. Eng. J., 2024, 479, 147828 CrossRef CAS
.
- T. Ishida, T. Murayama, A. Taketoshi and M. Haruta, Chem. Rev., 2019, 120, 464–525 CrossRef PubMed
.
- J. Liu, C. Xiong, S. Jiang, X. Wu and S. Song, Appl. Catal., B, 2019, 249, 282–291 CrossRef CAS
.
- W. Yuan, C. Wang, T. Qi, Y. Wan, S. Zhang, Y. Wu, K. Hu, G. Peng, B. Zhang and S. Shi, Appl. Catal., B, 2022, 318, 121780 CrossRef CAS
.
- C. Mang, G. Li, J. Luo, M. Rao, Z. Peng and T. Jiang, J. Environ. Chem. Eng., 2022, 10, 108740 CrossRef CAS
.
- C. Ma, D. Wang, W. Xue, B. Dou, H. Wang and Z. Hao, Environ. Sci. Technol., 2011, 45, 3628–3634 CrossRef CAS PubMed
.
- J. Gong, M. Zhang, J. Li, X. Wang, Y. Zhou, C. Yang, Y. Hua, C. Wang and A. Yuan, Appl. Surf. Sci., 2024, 669, 160513 CrossRef CAS
.
- C. Wang, X. Liu, J. Wang, Y. Li, S. Xie, F. Liu, C. Zhang, Y. Zheng, W. Shan and H. He, Chin. Chem. Lett., 2024, 35, 108739 CrossRef CAS
.
- H. Huang, Y. Xu, Q. Feng and D. Y. C. Leung, Catal. Sci. Technol., 2015, 5, 2649–2669 RSC
.
- X. Liu, J. Wu, S. Zhang, Q. Li, Z. Wu and J. Zhang, Appl. Catal., B, 2023, 320, 121994 CrossRef CAS
.
- S. Kattel, W. Yu, X. Yang, B. Yan, Y. Huang, W. Wan, P. Liu and J. G. Chen, Angew. Chem., Int. Ed., 2016, 55, 7968–7973 CrossRef CAS PubMed
.
- X. Li, M. Chen, G. Li and P. Wang, Appl. Surf. Sci., 2022, 589, 152855 CrossRef CAS
.
- D. Cericola and M. E. Spahr, Electrochim. Acta, 2016, 191, 558–566 CrossRef CAS
.
- H. Toda, H. Li, R. Batres, K. Hirayama and H. Fujihara, Acta Mater., 2023, 257, 119188 CrossRef CAS
.
- V. Viswanathan and F. Y.-F. Wang, Nanoscale, 2012, 4, 5110 RSC
.
- F. Zhang, S.-W. Chan, J. E. Spanier, E. Apak, Q. Jin, R. D. Robinson and I. P. Herman, Appl. Phys. Lett., 2002, 80, 127–129 CrossRef CAS
.
- Y. Lee, G. He, A. J. Akey, R. Si, M. Flytzani-Stephanopoulos and I. P. Herman, J. Am. Chem. Soc., 2011, 133, 12952–12955 CrossRef CAS PubMed
.
- S. Rong, P. Zhang, Y. Yang, L. Zhu, J. Wang and F. Liu, ACS Catal., 2017, 2, 1057–1067 CrossRef
.
- S. Lai, Y. Qiu and S. Wang, J. Catal., 2006, 237, 303–313 CrossRef CAS
.
- A. Marcilla, A. Gómez, S. Menargues, J. García-Martínez and D. Cazorla-Amorós, J. Anal. Appl. Pyrolysis, 2003, 68–69, 495–506 CrossRef CAS
.
- Z. Xu, J. Yu, J. Low and M. Jaroniec, ACS Appl. Mater. Interfaces, 2014, 6, 2111–2117 CrossRef CAS PubMed
.
- R. Oketani, H. Takahashi, M. Hoquante, C. Brandel, P. Cardinael and G. Coquerel, J. Mol. Struct., 2019, 1184, 36–40 CrossRef CAS
.
- L. Wang, Y. Hou, X. Zhong, J. Hu, F. Shi and H. Mi, Carbohydr. Polym., 2018, 208, 42–49 CrossRef PubMed
.
- J. Zhang, L. Xu and W.-Y. Wong, Coord. Chem. Rev., 2017, 355, 180–198 CrossRef
.
- P. Zhou, X. Zhu, J. Yu and W. Xiao, ACS Appl. Mater. Interfaces, 2013, 5, 8165–8172 CrossRef CAS PubMed
.
- J. Xu, X. Xiao, Z. Zhang, Y. Wu, D. T. Boyle, H. K. Lee, W. Huang, Y. Li, H. Wang, J. Li, Y. Zhu, B. Chen, W. Mitch and Y. Cui, Nano Lett., 2020, 20, 8719–8724 CrossRef CAS PubMed
.
- Y. Yazawa, N. Takagi, H. Yoshida, S.-i. Komai, A. Satsuma, T. Tanaka, S. Yoshida and T. Hattori, Appl. Catal., A, 2002, 233, 103–112 CrossRef CAS
.
- C. Dong, J.-J. Yang, L.-H. Xie, G. Cui, W.-H. Fang and J.-R. Li, Nat. Commun., 2022, 13, 4991 CrossRef CAS PubMed
.
- C. Dong, T. He, W. Wu, G.-R. Si, L.-H. Xie and J.-R. Li, J. Mater. Chem. A, 2024, 12, 15055–15062 RSC
.
- L. Yang, D. Lu, L. Zhu and D. Xia, J. Cleaner Prod., 2023, 413, 137462 CrossRef CAS
.
- S. K. Mondal, P. Aina, A. A. Rownaghi and F. Rezaei, ChemPlusChem, 2023, 89, e202300419 CrossRef PubMed
.
- C. Zhang, H. He and K.-i. Tanaka, Appl. Catal., B, 2006, 65, 37–43 CrossRef CAS
.
- T. He, D. Ding, Y. Zhou and S. Rong, ACS ES&T Eng., 2022, 2, 1403–1413 Search PubMed
.
- B.-T. Teng, S.-Y. Jiang, Z.-X. Yang, M.-F. Luo and Y.-Z. Lan, Surf. Sci., 2010, 604, 68–78 CrossRef CAS
.
- Y. He, Y. Zhu, J. Qian, P. Wang, Y. Zhang, K. Xu, B. Lu, Y. Liu and J. Shen, Chem. Eng. J., 2023, 474, 145737 CrossRef CAS
.
- R. F. André, G. Rousse, C. Sassoye, M. Avdeev, B. Lassalle-Kaiser, B. Baptiste and S. Carenco, Chem. Mater., 2023, 35, 5040–5048 CrossRef
.
- T. Gan, Z. Shi, Y. Deng, J. Sun and H. Wang, Electrochim. Acta, 2014, 147, 157–166 CrossRef CAS
.
- S. H. Brodersen, U. Grønbjerg, B. Hvolbæk and J. Schiøtz, J. Catal., 2011, 284, 34–41 CrossRef CAS
.
- J. Zhou, G. Liu, Q. Jiang, W. Zhao, Z. Ao and T. An, Chin. J. Catal., 2020, 41, 1633–1644 CrossRef CAS
.
- S. Carrettin, P. Concepción, A. Corma, J. M. López Nieto and V. F. Puntes, Angew. Chem., Int. Ed., 2004, 43, 2538–2540 CrossRef CAS PubMed
.
- J. Zhang, Y. Li, L. Wang, C. Zhang and H. He, Catal. Sci. Technol., 2015, 5, 2305–2313 RSC
.
- L. Zhang, S. Wang, C. Ni, M. Wang and S. Wang, Chem. Eng. Sci., 2021, 229, 116011 CrossRef CAS
.
- Z. Fan, Z. Zhang, W. Fang, X. Yao, G. Zou and W. Shangguan, Chin. J. Catal., 2016, 37, 947–954 CrossRef CAS
.
- H. Tan, D. Chen, N. Li, Q. Xu, H. Li, J. He and J. Lu, Chem.–Eur. J., 2019, 25, 16718–16724 CrossRef CAS PubMed
.
- S. Zhang, Y. Zhuo, C. I. Ezugwu, C.-c. Wang, C. Li and S. Liu, Environ. Sci. Technol., 2021, 55, 8341–8350 CrossRef CAS PubMed
.
- W. Sun and K. Yang, Mater. Chem. Front., 2020, 8, 76–80 CAS
.
- D. Kong, Y. Zheng, M. Kobielusz, Y. Wang, Z. Bai, W. Macyk, X. Wang and J. Tang, Mater. Today, 2018, 21, 897–924 CrossRef CAS
.
- Y. Bai, S. Li, B. Yin, J. Zhao and H. Li, Trans. Tianjin Univ., 2024, 30, 130–139 CrossRef CAS
.
- C. You, C. Wang, M. Cai, Y. Liu, B. Zhu and S. Li, Acta Phys.-Chim. Sin., 2024, 40, 2407014 CrossRef
.
- N. Zhang, W. He, Z. Cheng, J. Lu, Y. Zhou, D. Ding and S. Rong, Chem. Eng. J., 2023, 466, 143160 CrossRef CAS
.
- F. Yuan, R. Yang, C. Li, Y. Tan, X. Zhang, S. Zheng and Z. Sun, Build. Environ., 2022, 219, 109216 CrossRef
.
- C. Mang, J. Luo, P. Cao, X. Zhang, M. Rao, G. Li and T. Jiang, Chemosphere, 2022, 287, 132293 CrossRef CAS PubMed
.
- Y. Huang, X. Zhu, D. Wang and S. Hui, Environ. Res., 2023, 238, 117265 CrossRef CAS PubMed
.
- Y. Zhu, W. Zhao, B. Jing, J. Zhou, B. Cai, D. Li and Z. Ao, Chin. Chem. Lett., 2023, 34, 107816 CrossRef CAS
.
- W. Kang Zhao, J. Yu Zheng, C. Bao Han, J. Ruan, Y. Lu, K. Ling Zhou, T. Rui Zhai, H. Wang and H. Yan, Chem. Eng. J., 2022, 440, 135877 CrossRef
.
- S. Xu, Q. Shen, J. Zheng, Z. Wang, X. Pan, N. Yang and G. Zhao, Adv. Sci., 2022, 9, 2203941 CrossRef CAS PubMed
.
- S. Zhou, Q. Liu, Y. Zhou and Y. Li, Adv. Environ. Prot., 2022, 12, 1041–1048 CrossRef
.
- S.-Y. Zhang, Z. Li, X. Shen, J. Shan, J. Zhan, H. Zhou, X. Yi, H.-Y. Lian and Y. Liu, Environ. Res., 2023, 235, 116683 CrossRef CAS PubMed
.
- T. Cai, P. Zhang, X. Shen, E. Huang, X. Shen, J. Shi, Z. Wang and Q. Sun, ACS Appl. Mater. Interfaces, 2020, 12, 37147–37154 CrossRef CAS PubMed
.
- W. Yuan, S. Zhang, Y. Wu, X. Huang, F. Tian, S. Liu and C. Li, Appl. Catal., B, 2020, 272, 118992 CrossRef CAS
.
- M. A. Sidheswaran, H. Destaillats, D. P. Sullivan, J. Larsen and W. J. Fisk, Appl. Catal., B, 2011, 107, 34–41 CrossRef CAS
.
- B. Zhu, X.-S. Li, P. Sun, J.-L. Liu, X.-Y. Ma, X. Zhu and A.-M. Zhu, Chin. J. Catal., 2017, 38, 1759–1769 CrossRef CAS
.
- B. Zhu, L.-Y. Zhang, M. Li, Y. Yan, X.-M. Zhang and Y.-M. Zhu, Chem. Eng. J., 2020, 381, 122599 CrossRef CAS
.
- Y.-H. Liu, J.-A. Lv, M.-M. Xu, C. Dong, X.-M. Liu, J.-R. Li and L.-H. Xie, ACS Appl. Nano Mater., 2023, 6, 7794–7801 CrossRef CAS
.
- Z. Lin, X. Tong, W. Shen, J.-C. Roux and H. Xi, J. Cleaner Prod., 2020, 244, 118863 CrossRef CAS
.
- H. Huang and D. Y. C. Leung, J. Catal., 2011, 280, 60–67 CrossRef CAS
.
- X. Zhu, B. Cheng, J. Yu and W. Ho, Appl. Surf. Sci., 2016, 364, 808–814 CrossRef CAS
.
- D. Li, X. Chen, Y. Huang, G. Zhang, D. Zhou and B. Xiao, J. Hazard. Mater., 2022, 439, 129608 CrossRef CAS PubMed
.
- Z. Wang, J. Pei and J. Zhang, Build. Environ., 2013, 65, 49–57 CrossRef
.
- N. Wakao, S. Kaguei and T. Funazkri, Chem. Eng. Sci., 1979, 34, 325–336 CrossRef CAS
.
- S. Rong, P. Zhang, J. Wang, F. Liu, Y. Yang, G. Yang and S. Liu, Chem. Eng. J., 2016, 306, 1172–1179 CrossRef CAS
.
- X. Li, H. Li, Y. Huang, J. Cao, T. Huang, R. Li, Q. Zhang, S.-c. Lee and W. Ho, J. Hazard. Mater., 2022, 424, 127217 CrossRef CAS PubMed
.
- F. Liu, S. Zhang, X. Zhang, J. Shen, L. Wan, A. Bahi and F. Ko, J. Hazard. Mater., 2022, 421, 126769 CrossRef CAS PubMed
.
- L. Liu, G. Jing, C. Xu, X. Zhang, X. Zhang, L. Guo, Z. Huang, X. Wu, H. Zhao, C.-S. Yuan, H. Shen and W. Xia, Appl. Catal., B, 2024, 344, 123634 CrossRef CAS
.
- C. Mang, C. Huang, J. Luo, M. Rao, Z. Peng and G. Li, Mol. Catal., 2022, 530, 112643 CrossRef CAS
.
- J. Chen, M. Jiang, W. Xu, J. Chen, Z. Hong and H. Jia, Appl. Catal., B, 2019, 259, 118013 CrossRef CAS
.
- L. Zhao, Y. Yang, J. Liu and J. Ding, Chemosphere, 2023, 330, 138754 CrossRef CAS PubMed
.
- Y. Wang, K. Liu, J. Wu, Z. Hu, L. Huang, J. Zhou, T. Ishihara and L. Guo, ACS Catal., 2020, 10, 10021–10031 CrossRef CAS
.
- Y. Guo, M. Wen, G. Li and T. An, Appl. Catal., B, 2021, 281, 119447 CrossRef CAS
.
- Z. Zheng, C. Zhang, J. Li, D. Fang, P. Tan, Q. Fang and G. Chen, Chemosphere, 2024, 356, 142024 CrossRef CAS PubMed
.
- Z. Lan, Y. Yu, H. Li, L. Zhang and Y. Cao, Mater. Sci. Semicond. Process., 2021, 123, 105547 CrossRef CAS
.
- G. Li, C. Mang, J. Luo, M. Rao, Z. Peng and T. Jiang, J. Colloid Interface Sci., 2022, 618, 229–240 CrossRef CAS PubMed
.
- S. Rong, P. Zhang, F. Liu and Y. Yang, ACS Catal., 2018, 8, 3435–3446 CrossRef CAS
.
- R. Fang, X. Huang, X. a. Luo, Y. Sun, Z. Liu, L. Ao, F. Dong and H. Huang, J. Environ. Chem. Eng., 2023, 11, 109064 CrossRef CAS
.
- B.-B. Chen, C. Shi, M. Crocker, Y. Wang and A.-M. Zhu, Appl. Catal., B, 2013, 132–133, 245–255 CrossRef CAS
.
- Z. Liu, D. Zhang, G. Jin and W. Yang, Appl. Surf. Sci., 2020, 534, 147594 CrossRef CAS
.
- Z. Yan, Z. Xu, J. Yu and M. Jaroniec, Appl. Catal., B, 2016, 199, 458–465 CrossRef CAS
.
- H. Wang, W. Guo, Z. Jiang, R. Yang, Z. Jiang, Y. Pan and W. Shangguan, J. Catal., 2018, 361, 370–383 CrossRef CAS
.
- K. Qian, L. Du, X. Zhu, S. Liang, S. Chen, H. Kobayashi, X. Yan, M. Xu, Y. Dai and R. Li, J. Mater. Chem. A, 2019, 7, 14592–14601 RSC
.
- H. Li, X. Feng, D. Ma, M. Zhang, Y. Zhang, Y. Liu, J. Zhang and B. Wang, ACS Appl. Mater. Interfaces, 2018, 10, 3160–3163 CrossRef CAS PubMed
.
- P. Zhou, J. Yu, L. Nie and M. Jaroniec, J. Mater. Chem. A, 2015, 3, 10432–10438 RSC
.
- J. Wang, P. Zhang, J. Li, C. Jiang, R. Yunus and J. Kim, Environ. Sci. Technol., 2015, 49, 12372–12379 CrossRef CAS PubMed
.
- C. Huang, Y. Ding, Y. Chen, P. Li, S. Zhu and S. Shen, J. Environ. Sci., 2017, 60, 61–69 CrossRef CAS PubMed
.
|
This journal is © The Royal Society of Chemistry 2025 |
Click here to see how this site uses Cookies. View our privacy policy here.