DOI:
10.1039/D5TA02391B
(Review Article)
J. Mater. Chem. A, 2025,
13, 23170-23226
From energy to intelligence: MXenes transforming triboelectric nanogenerators
Received
25th March 2025
, Accepted 12th May 2025
First published on 14th May 2025
Abstract
As a 2D functional material, MXenes have attracted increasing interest. MXenes, with their remarkable features, have redefined the performance of energy harvesting by boosting stability, efficiency, and charge transfer. Triboelectric nanogenerators (TENGs) have become an appealing technology for energy harvesting and sensing applications due to the increasing demand for self-powered and sustainable energy solutions. However, owing to the inadequate output performance of TENGs, they are still a long way from being used commercially. The use of MXenes in TENG is associated with the terminal groups (such as
O, –OH, and –F), intrinsic metallic nature, and synthetic techniques of MXenes. In this review, the recent advancements in MXene synthesis, TENG operating mechanisms, and fabrication strategies are provided. The origin, advancement, and underlying mechanism of TENG are elucidated for new researchers in this field. Furthermore, the diverse roles of MXenes in TENGs and the integration of MXene TENGs in numerous applications, including biomedical wearables, environmental sensing, sports monitoring, and soft robots, are explored thoroughly. Finally, we delve into the obstacles and future outlook of MXene-TENG research, emphasizing avenues for further advancement in the field of multifunctional sensing and energy harvesting.
 Suresh Kumar Chittibabu | Suresh Kumar Chittibabu is currently pursuing his PhD at the Center for Nanotechnology Research, Vellore Institute of Technology, Vellore, India. He received his BEng degree in the stream of Electronics and Communication from Anna University, Chennai, India, and M.Tech degree in Nanotechnology from Vellore Institute of Technology, Vellore, India. His current research focuses on advanced functional materials, with particular emphasis on MXenes, metal–organic frameworks (MOFs), energy-harvesting, triboelectric nanogenerators, wearable physical sensors, and biomedical rehabilitation devices. |
 Arunkumar Chandrasekhar | Prof. Arunkumar Chandrasekhar is currently an Associate Professor in the Department of Sensors and Biomedical Technology, Vellore Institute of Technology, Vellore, India, and he is a recipient of the VIT SEED Grant research project. He worked as a postdoctoral researcher at the Nanomaterials and Systems Lab, South Korea. He received his PhD in Mechatronics Engineering from Jeju National University, Jeju, South Korea, where he was a scholarship recipient from the Korean Government Scholarship Program. He is interested in self-healing polymers, 2D materials, wearable triboelectric nanogenerators, battery-free electronic devices, energy storage devices, MEMS, and self-powered devices. |
 Krishnamoorthi Chintagumpala | Prof. Krishnamoorthi Chintagumpala received his PhD in Physics from the Indian Institute of Technology Madras, Chennai. After graduation, he worked as a Scientist at GE Global Research and Technology Center, Bengaluru, and as a Research Fellow at the National University of Singapore, Singapore. Currently, he is working as Professor of Physics at the Center for Nanotechnology Research, Vellore Institute of Technology, Vellore, India. He has worked on magnetoresistance, magnetocaloric, magnetic hyperthermia, dilute magnetic semiconductors, electrochemical, and physical sensors. His current research interest focuses on the development of various magnetic nanomaterials and wearable physical sensors for biomedical applications. |
1. Introduction
1.1. The quest for sustainable energy
The rapid growth of multipurpose electronic devices and energy sources has transformed daily life and professional protocols. Electricity and accessibility have been crucial in technological advances.1 Today's society depends on brilliance and information technology, which require the systematic use of energy resources.2 Based on power plants (hydropower and nuclear power), conventional energy supply themes are incompatible with the present expansion of distributed electronic devices.3,4 Thus, to address the global energy scarcity and the existing state of environmental pollution, the quest for alternative energy resources with lower carbon footprints is essential for healthy evolution of human civilization.5 Abundant research has been conducted on harvesting energy from easily available sources such as human motions, ocean waves, air flow, chemical reactions, and rotational vibrations for powering several distributed portable IoT devices, such as implanted wearable biosensors,6–8 gas sensors,9,10 self-powered sensors,11,12 and wireless sensor networks.13,14 When necessary, the energy generated by these harvesters can be stored in supercapacitors or rechargeable batteries to power electronic devices.15,16 In the past decade, sophisticated technology known as nanogenerators has been quickly and successfully created to transform mechanical energy into electric energy.17,18
1.2. Why triboelectric nanogenerators? The intersection of innovation
A nanogenerator transforms mechanical and thermal energy into electricity. Based on their power-generating mechanisms, nanogenerators are divided into three categories: pyroelectric,19,20 triboelectric,21,22 and piezoelectric (PENGs).23,24 Triboelectric nanogenerator (TENG), a promising green energy innovation which is sometimes referred to as Wang generator, generates electricity by harnessing mechanical motions that exist in the surrounding environment.3,25,26 Ace. Zhong Lin Wang has discovered the TENG mechanism in 2012.27 TENG functions based on the fusion of contact triboelectrification and electrostatic induction. Triboelectrification refers to the mechanism of generating electricity through the movement of electrons from one substance that has poor electron binding capacity (+vely charged) to another substance that has superior electron binding capacity (−vely charged).28–30 This transfer occurs when a pair of non-identical materials come into contact and separate or are simply rubbed.31 TENG-based energy harvesting is considered next-generation energy harvesting technology due to its distinctive benefits, such as ease of fabrication, low cost, high voltage output, simple configuration, structural optimization, and versatile range of frictional materials.32,33 When pristine polymers are used for the fabrication of TENGs, electrons can recombine with the molecules in the air or positive charges generated on the electrode, resulting in poor performance.34,35 Thus, scientists are inclined to incorporate unique materials for the fabrication of TENGs.
1.3. 2D materials in energy harvesting: a revolutionary approach
2D materials are very appealing for use in a variety of applications, particularly energy harvesting, owing to their outstanding attributes, which include a high surface-to-volume ratio, exceptional mechanical strength, and excellent electrical and thermal conductivity.64 Notable breakthroughs have seen using 2D materials, including graphene,65 molybdenum disulfide (MoS2), hexagonal boron nitride (h-BN),66 metal–organic frameworks (MOFs),67 covalent organic frameworks (COFs),68 and black phosphorus,69 enhancing the performance of TENGs.70 Nevertheless, epoxy pastes or adhesives are always needed for adherence when integrating these 2D materials into TENGs,71 which impede the device fabrication and diminish the performance of TENGs.
1.4. MXenes: is this a future-forward material?
MXenes are two-dimensional (2D) metal carbides and nitrides comprised of two or more layers of transition metal (M) atoms, such as a honeycomb structure. The octahedral clusters within the nearest transition metal layers are occupied by layers of carbon (C) and/or nitrogen (N) (X atoms).72,73 Ternary layered MAX phases are the precursors for synthesizing MXenes. MAX phases are represented as Mn+1AXn (n = 1,2,3 or 4), where M indicates early transition metals, A is primarily group 13 to 16 elements, and X is carbon and/or nitrogen.74,75 MXenes can be synthesized by selectively etching the A element from the MAX phase. After etching, the resultant MXene is represented as Mn+1XnTx, where M can be Ti, V, Cr, Nb, Ta, Mo, W, etc., X can be C or N, or CN, and Tx implies a surface termination group such as –F, –Cl, –OH, –O, and –Br.76,77 Owing to their advantages such as superior electrical conductivity, mechanical robustness, rich surface chemistry, and electronegativity, MXenes play a vital role in enhancing the performance of TENGs.78,79 The basic theory of TENG indicates that the charge density and dielectric constant associated with materials serve as essential parameters for its performance.80 Due to the presence of surface functional groups and 2D structure in MXenes, they attract electrons and acquire charge amid interlayer sheets and polymer grids. Also, they increase the electric charge density and dielectric constant.81,82 Consequently, MXene's distinct chemical and physical attributes are favourable for TENG performance.
Initially, this comprehensive review presents the origin of triboelectricity and how it has evolved from before the Common Era (BCE) to the present 21st century. The physical principle of TENG relies on the modified Maxwell's equation, and with six operating modes of TENG, it was elaborated to reach a wider audience. The dielectric-to-dielectric, metal-to-dielectric, and deformation modes were reported to establish novel functionalities and applications with diverse materials soon. Subsequently, researchers started to explore MXenes as negative and positive triboelectric layers in a series of triboelectric materials. The thematic framework of this review, highlighting the etching strategies, operating modes of TENG, its fabrication protocols, and innovative applications of MXene TENGs, is concisely illustrated in Fig. 1. The family of MXenes, from the preparation of MAX phases via etching to advanced protocols for the synthesis of MXenes with their compositional and structural assessment, is discussed in detail. The performance of TENG can be enhanced by embedding MXenes in TENGs as electrodes, and triboelectric layers (positive and negative) were analyzed. Novel applications of MXene TENGs, such as wound healing, food spoilage detection, intelligent robots, sports monitors, and smart homes, are discussed. Finally, the present obstacles in the synthesis, oxidation, cost, and exploration of novel double-transition MXenes are presented, and how these issues can be resolved and the future evolution of MXene in TENG are summarized concisely. This review differs from the previous reviews, as it highlights the operating modes, MAX and MXene synthesis, MXene multifunctionalities in TENGs, and their unique applications.
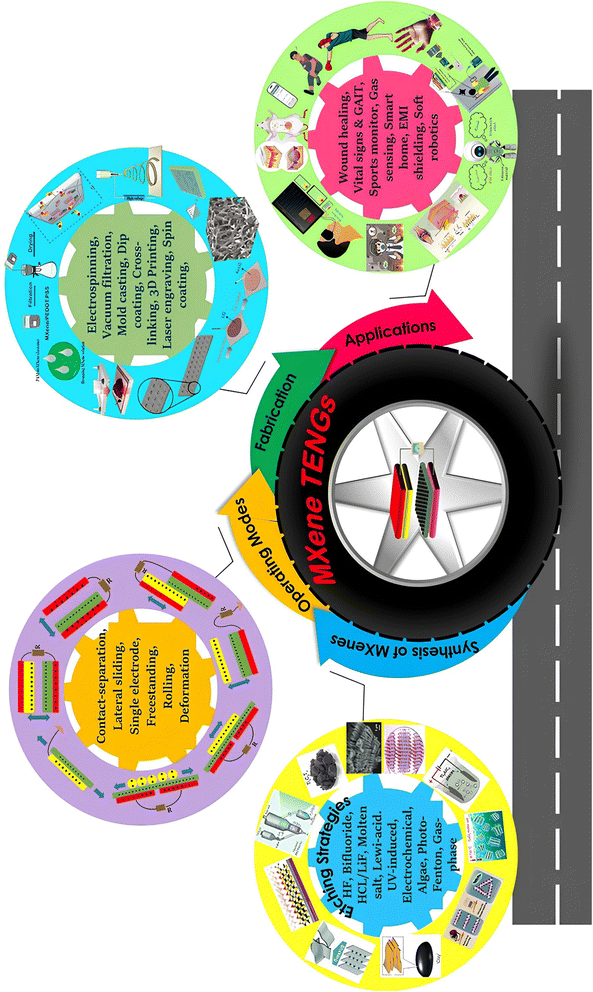 |
| Fig. 1 Visual representation of the structure of this review. Etching strategies. Reprinted with permission from ref. 36. © 2011, John Wiley & Sons. Reprinted with permission from ref. 37. © 2022, American Chemical Society. Reprinted with permission from ref. 38. © 2018, John Wiley & Sons. Reprinted with permission from ref. 39. © 2020, Nature. Reprinted with permission from ref. 40. © 2020, Elsevier. Reprinted with permission from ref. 41. © 2014, Springer Nature. Reprinted with permission from ref. 42. © 2015, Royal Society of Chemistry. Reprinted with permission from ref. 43. © 2014, American Chemical Society. Reprinted with permission from ref. 44. © 2024, Elsevier. Reprinted with permission from ref. 45. © 2020, John Wiley & Sons. Operating modes: contact-separation mode, lateral-sliding mode, single-electrode mode, freestanding mode, rolling mode, and deformation mode. Fabrication approaches. Reprinted with permission from ref. 46. © 2021, Elsevier. Reprinted with permission from ref. 47. © 2023, Elsevier. Reprinted with permission from ref. 48. © 2019, Elsevier. Reprinted with permission from ref. 49. © 2023, John Wiley & Sons. Reprinted with permission from ref. 50. © 2023, American Chemical Society. Reprinted with permission from ref. 51. © 2023, American Chemical Society. Reprinted with permission from ref. 52. © 2023, Elsevier. Reprinted with permission from ref. 53. © 2024, John Wiley & Sons. Reprinted with permission from ref. 54. © 2022, Elsevier. Applications of MXene TENGs. Reprinted with permission from ref. 55. © 2024, John Wiley & Sons. Reprinted with permission from ref. 56. © 2024, Elsevier. Reprinted with permission from ref. 57. ©2024, AIP Advances. Reprinted with permission from ref. 58. © 2024, Elsevier. Reprinted with permission from ref. 59. © 2024, American Chemical Society. Reprinted with permission from ref. 60. © 2025, Elsevier. Reprinted with permission from ref. 61. © 2024, Elsevier. Reprinted with permission from ref. 62. © 2024, Elsevier. Reprinted with permission from ref. 63. © 2024, American Chemical Society. | |
2. Unveiling the triboelectric phenomenon
2.1. History and advancement of triboelectricity
Despite its ancient origins, triboelectricity, the generation of electric charge by friction, has recently become an important topic of study.83 Around 600 BCE, the Greek philosopher Thales of Miletus became the first to identify this phenomenon. He noticed that amber attracted small items when it was rubbed with fur.84,85 Although it was not properly investigated for centuries, this observation was one of the earliest steps toward understanding static electricity.
As scientists advanced their understanding of the basics of static electricity, the study of electricity gained momentum. However, triboelectricity did not receive concentrated scientific study until the late 20th century.86,87 Researchers began to systematically study the triboelectric series to categorize materials based on their tendency to receive or lose electrons.88 Triboelectricity has gained new attention in the twenty-first century due to the development of triboelectric nanogenerators (TENGs).89,90 This development from a fascinating archaic observation to cutting-edge technology demonstrates the increasing importance of triboelectricity in modern research and engineering.
2.2. The physics behind TENGs: mechanism and their classification
Using basic physical principles, triboelectric nanogenerators (TENGs) transform mechanical energy from environmental sources into electrical energy, representing a novel approach to energy harvesting.91,92 The triboelectric effect and electrostatic induction are two fundamental physical processes that TENGs rely on to function.93 The underlying principle of TENG can be elaborated using modified Maxwell's equations, which are the basis of classical electromagnetism. To describe the current produced by the recurring contact and separation of triboelectric materials, the term “triboelectric displacement current” was established. This idea is essential to comprehend the electric field and the ensuing production of electrical power. According to the contact electrification and TENG principle, the output of TENG may be predicted and derived from Maxwell's equations as follows. The modified Maxwell's equation is presented as eqn (1), where
is the displacement current density. The energy conversion is facilitated by the displacement current, which comes from the dielectric polarization caused by a transitory electric field.
is the polarization term that emerges from the static electrostatic charges, ε0 is the permittivity of free space, and
is the electric field.94,95 |  | (1) |
The induced current produced by the fluctuating electrical field is the first component
and serves as the theoretical foundation for electromagnetic wave generation. The second component
is the current produced by the polarization field due to electrostatic charges on the material surface, which serves as the nanogenerator's primary theoretical foundation and source.96 Gaining knowledge of these concepts helps to understand how TENGs work and how they may be used in energy generation.
2.2.1. Effect of triboelectricity.
Static electric charges are created on the surfaces of two materials when they come into contact, and then separate, a phenomenon called contact electrification or the triboelectric effect.97 (i) Mechanism of charge transfer: electrons move from one material to another when two distinct materials come into contact. Higher electron affinity materials will acquire electrons and become negatively charged, whereas lower affinity materials will lose electrons and become positively charged.98–100 (ii) Surface interaction: more contact points are produced by rougher surfaces with higher asperities, which improves the charge transfer. Similarly, higher contact area conditions increase the magnitude of charge generation.101,102
2.2.2. Electrostatic induction.
Once the materials are charged via the triboelectric effect, they create an electric field in their surroundings. Electrostatic induction is the process by which this electric field induces a redistribution of charges in nearby conductive materials.103,104 (i) Induced current: when the charged materials in a TENG are separated after contact, the resulting electric field induces a potential difference across an external circuit connected to the TENG.105 This potential difference drives the flow of electrons, creating an electric current.106 (ii) AC power generation: the repetitive motion of bringing materials into contact, and then separating them generates alternating current (AC).107
2.2.3. Modes of operation in TENGs.
TENGs can be designed to operate in different modes, each leveraging the triboelectric effect and electrostatic induction in unique ways to optimize energy conversion for specific applications.
2.2.3.1 Vertical contact-separation mode.
In this mode, two materials move perpendicularly to each other, coming into contact, and then separating.108 This mode is further classified into two subdivisions of dielectric to dielectric and metal to dielectric.
2.2.3.1.1 Dielectric to dielectric.
When two dielectric films with different electron affinities come into physical contact, their surfaces become oppositely charged. The electrodes placed on the top and bottom surfaces of the two dielectric films produce a potential decrease once the two sides are separated by a certain distance. To balance the electrostatic field, the free electrons from one electrode move to the other if the two electrodes are electrically connected by a load (Fig. 2(a)(i)). The induced electrons will return after the gap is closed and the potential decrease caused by the triboelectric charges vanishes. The induced electrons move back and forth between the two electrodes as a result of the periodic contact and separation of the two material, producing an electrical signal in the external circuit.109,110
 |
| Fig. 2 Operating modes of a TENG. (a) Contact-separation mode. (i) Dielectric to dielectric. (ii) Metal to dielectric. (b) Lateral-sliding mode. (c) Single-electrode mode. (d) Freestanding mode. (e) Rolling mode. (f) Deformation mode. | |
2.2.3.1.2 Metal to dielectric.
In this mode, the metal acts as the triboelectric material and electrode, pairing opposite with the positive or negative triboelectric material. Usually, the dielectric material is pre-charged with negative charges or acquires negative charges upon interacting with the environment. When the independent metal electrode and the dielectric material (negative) come into contact and separate, the independent electrode receives and separates positive and negative charges to attain a state of electrostatic equilibrium (Fig. 2(a)(ii)). In contrast, the dielectric material receives extra negative charges. The internal electric field intensities of the electrode should be zero. As a result, positive and negative charges are simultaneously present.80,111 This simple yet effective configuration is ideal for applications where materials can be repeatedly pressed together, and then pulled apart, such as in footstep energy harvesting and pressure sensors.112,113
2.2.3.2 Lateral sliding mode.
When two triboelectric layers with opposite polarities slide horizontally, the two contact surfaces will produce an equal number of positive and negative charges. When the contact surface slides horizontally due to external mechanical action, polarization forms in that direction, and the induced charge is pushed to move, creating an induced potential difference (Fig. 2(b)). The free electrons in the circuit are pushed to neutralize the generated potential difference when an external load is connected, producing a current output. This mode is effective in scenarios involving relative sliding motions, such as in touchpads, wearable devices, and interfaces where surfaces are frequently in motion relative to each other.114–116
2.2.3.3 Single-electrode mode.
In this mode, there are no contact wires or electrodes in the free-flowing triboelectric layer. Only one electrode is connected, or it acts as a triboelectric layer on its own. Surface charge transfer takes place when the triboelectric layer and electrode are completely in contact, causing opposite charges to be induced on both surfaces without any electron flow. To balance the electric potential by exchanging charges with the ground, the induced charges on the surface of the lone electrode diminish when the two are separated (Fig. 2(c)). Electrons will move from the ground to the electrode to create equilibrium as they get closer to making contact again until both surfaces are completely in contact.117,118 This design simplifies the system by reducing the number of electrodes needed and is useful for applications where one of the materials is stationary or grounded, such as in human motion detection and environmental monitoring.119,120
2.2.3.4 Freestanding triboelectric-layer mode.
A single triboelectric layer is attached to two electrodes with a tiny space between them. One triboelectric material functions as a distinct friction layer, while the other is affixed to the two electrodes as an induction layer. Both triboelectric materials are in contact and charged in the air. The electrons are driven by an induced potential difference between the two electrodes, which is created when the independent triboelectric layer moves and alters the charge (Fig. 2(d)). An AC output is produced when the independent triboelectric layer moves periodically, causing electron transfer to occur between the two electrodes.121,122 The relative movement of the layer between the electrodes induces charge redistribution, making it suitable for energy harvesting from large-scale movements, such as ocean waves and wind energy.123
2.2.3.5 Rolling mode.
The rolling mode produces energy by using the rolling action between a triboelectric surface and a rolling element, such as a ball or cylinder. The rolling element repeatedly makes and breaks contact as it travels across the surface, resulting in cycles of charge transfer and separation. Electrons move via an external circuit due to a rapid change in electric potential (Fig. 2(e)). This model is beneficial because it converts mechanical energy from rolling motion into electrical energy with great efficiency and less wear and tear on the materials.124–126
2.2.3.6 Deformation mode.
This new mode was proposed in 2024. The two triboelectric layers are adhered together, and thus both layers are unable to slide or contact-separate. However, because the two layers have differing capacities for storing and adsorbing electrons, there is an electron balance between them. Furthermore, both layers feature excellent stretchability and flexibility. The adsorbing and storing capacities of the two layers must be altered if they deform (stretching, folding, etc.), which causes the redistribution and transfer of charge. Due to the disparity in their triboelectric characteristics, the change must be different. When the electron equilibrium is disturbed, electric signals are produced by electrons moving between layers (Fig. 2(f)). The silver wire that is attached to one layer gathers and outputs the electric signals.127 Furthermore, TENG devices operating in this mode perform exceptionally well as self-powered flexible sensors.
3. MXenes: beyond their surface
3.1. The MXene family: configuration and composition
Following the discovery of stable 2D layered graphene, 2D MXenes have attracted considerable interest from various scientific domains due to their evident configurational advantages over their bulk counterparts.128,129 The presentation of novel 2D transition metal nitride-, carbide-, and carbon nitride-based MXenes by Prof. Yury Gogotsi in 2011 marked an exciting new chapter in the ongoing hunt for more creative innovations and their prosperous application in the sciences.36
MXenes can be divided into several categories based on their number of atomic layers. Based on the transition-metal composition of MXenes, they can be further classified into two unique types. Mono-transition-metal (Mono-M) MXenes are the first group, where only one type of transition metal is present in each of the M layers (Ti3CN, Mo2C, Ta2C, etc.). The second group is double transition-metal (DTM) MXenes, where two different types of transition metals are present at the M sites (Mo2TiC2, (W2Hf2)C3, etc.).130–132 Based on their structural characteristics, DTM MXenes can also be divided into two groups of ordered MXenes and solid-solution MXenes. In-plane order and out-of-plane order are two further classifications of ordered MXenes.133–136 The transition metals in the M sites of MXenes have a close-packed hexagonal crystal structure, while the X atoms are positioned in the octahedral sites between the M atomic planes. As mentioned above, carbon, nitrogen, or both can occupy the X sites.137,138 Except for Ti2NTx and Ti4N3Tx, less research has been done on nitride MXenes owing to their difficult synthesis.139 It has been proposed that the C and N atoms in carbonitride MXenes occupy the octahedral positions at random, regardless of the carbonitride stoichiometry.140,141
The typical method for obtaining two-dimensional materials involves extracting one or a few atomic layers from a layered molecule, where the bonds between the layers are substantially weaker than that within the layers.142,143 The precursor substance for synthesizing MXene is the MAX phase. High-binding ionic and covalent bonds constitute the M–X bonds in the MAX phase, whereas the M–A bonds are primarily metallic connections with a comparatively low binding strength.144–146 Thus, employing the appropriate etchants, it is possible to remove the “A” layers from the MAX phases selectively. Selectively147 etching the A element from the MAX phase results in the formation of exfoliated multilayer MXene flakes.148 Single-layer or monolayer MXene can be obtained through intercalation and delaminating the multilayer MXene flakes.149 The family of MXenes is subdivided based on their atomic layers. The reported MXenes (M2X, M3X, M4X, and M5X) with their atomic arrangement are depicted in Fig. 3. Adding more than 100 potential components to the MXene material, there are 18 M2X (V2C, Nb2C, Cr1.3C, (Mo2/3Y1/3)2C, etc.), 12 M3X2 (Ti3C2, Zr3C2, (V2Ti)C2, (Cr2Nb)C2, etc.), 14 M4X3 (Ta4C3, (Mo2Ta2)C3, (NbTi)4C3, (V3Cr)C3, etc.), and most recently 3 M5X4 ((Mo4V)C4, (Ti2.5Ta2.5)C4, (Ti2.765Nb2.325)C4) examples of MXene configurations reported to date.150–152 The significance of this MXene family stems from the fact that M5X4 (n = 4) exhibits characteristics that are absent from other MXenes (n = 1–3). Their thermal stability was found to be the highest among MXenes to date (about 1000 °C compared to less than 800 °C for other MXenes).153 More than 130 categories have been added to the MAX phase family thus far, where the M elements have been expanded to lanthanide rare earths ((Mo, R, Nb)4C3),154 the A site has various new elements, which have lower d electrons, and more recently boron has been added to the X site (MBenes—Mo2B, V3B4, and CrFeB2).155 Surface-terminating compounds that are not native to the parent MAX phase and come from the etchant aggressively functionalize the extremely reactive M-element surfaces during the MAX to MXene etching process.156 Depending on the synthesis method and MXene composition, the surface of MXenes is covered with single or mixed terminations (T = F, Cl, Br, O, OH, NH, etc.).157 The research on the surface of MXene is challenging due to several factors such as the presence of fragile elements such as F, O, and H on their surface, together with water and precursor impurities after etching, and changes in the experimental settings complicate their systematic evaluation.153,158
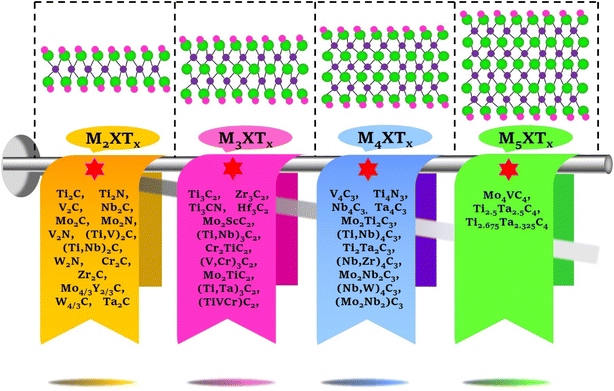 |
| Fig. 3 Atomic representations and compositions of M2X, M3X, M4X, and M5X MXenes: structural differences and reported materials. | |
Numerous experiments using first-principles computations have demonstrated the propensity for terminating at the bare MXene surface.159 Upon surface termination, MXenes exhibit a notable increase in negative formation energy, signifying the establishment of robust bonds between the terminating species and their surface M atoms. Etching the MAX phases by immersion in HF or LiF/HCl aqueous acidic solutions results in the formation of MXenes with multiple surface terminations such as F, O, Cl, and OH at different ratios.160 The synthesis of MXenes with invariable surface terminations was demanding until the development of molten salt etching with the ZnCl2 precursor. These MXenes have chlorine surface terminations (Ti3C2Cl2).161,162 This strategy was expanded to provide a generic Lewis-acidic-melt etching technique that works with a variety of systems. The broad spectrum of components seen in Lewis-acidic melts suggests that it may be possible to modify the chemistry and surface terminations of MXenes. MXenes can be synthesized with a series of terminating groups such as Br and I.163,164 The variety of MXene compositions can be further extended by exchanging these terminations with different functional groups through subsequent surface reactions.165 The surface chemistry of MXenes, specifically the nature and density of surface terminations such as –O, –OH, –F, –Cl, and –Br groups, plays a pivotal role in determining their triboelectric performance in TENG devices. These terminations impact key parameters such as electron affinity, surface conductivity, hydrophilicity, and interfacial interactions, all of which influence the charge generation, transfer, and retention capabilities of MXenes in TENG applications.166,167 By carefully tuning the surface terminations and surface roughness, MXenes can be optimized for high-efficiency TENG devices, offering great potential for energy harvesting technologies.
3.2. Triboelectric series: where do MXenes stand?
Two-dimensional (2D) transition metal carbides, nitrides, and carbonitrides, known as MXenes, are a new class of materials with special qualities such as durability, improved thermal conductivity, customizable surface chemistry, and high electrical conductivity.78,168 MXenes are relatively new in the triboelectric series, which ranks materials according to their tendency to gain or lose electrons when they come into contact with another material. Their precise place in the series can change based on their particular chemical composition and surface functionalization.169,170 Generally, MXenes are positioned towards the electronegative end of the series, indicating a propensity to gain electrons when in contact with many other materials.171
The distinct surface chemistry of MXenes enables them to display both positive and negative triboelectric properties, depending on their structure and the materials they come into contact with in triboelectric nanogenerators. The electron-donating or electron-accepting properties of MXene surfaces can be altered by the presence of different functional groups. MXenes function as a negative element when combined with materials that are more likely to give electrons, and vice versa (Fig. 4). Thus, by selecting appropriate functional groups and pairing materials, MXenes can be engineered to exhibit the desired triboelectric properties, making them versatile components in energy-harvesting devices.48,172,173 The surface functional groups on MXenes have a significant impact on their triboelectric behavior. MXenes with hydroxyl (–OH) surface terminations typically have moderate electronegativity.174,175 When in contact with less electronegative materials, they can attract electrons, but they are not as strongly electronegative as materials with other surface terminations.176 MXenes terminated with oxygen (–O) exhibit higher electronegativity.177 These MXenes are positioned lower in the triboelectric series, near materials such as polydimethylsiloxane (PDMS), which also tend to gain electrons readily.178 This makes them more effective at becoming negatively charged when interacting with other materials. Fluorine-terminated MXenes are among the most electronegative in this class due to the strong electron-withdrawing nature of fluorine.179,180 The properties and advantages of MXenes compared with conventional and advanced materials are presented in Table 1. These MXenes are positioned toward the bottom of the triboelectric series, similar to or slightly above highly electronegative materials such as polytetrafluoroethylene (PTFE).181,182
 |
| Fig. 4 Categorization of positive (electron donors) and negative (electron acceptors) materials of the triboelectric spectrum: MXene as a dual-role contender. | |
Table 1 A comprehensive comparison of conventional vs. advanced vs. MXene materials
Criteria |
Conventional materials |
Advanced materials |
MXenes |
Examples |
Polymers (PTFE, PDMS, PET, PVDF), metals (gold, silver, copper, aluminium), ceramics (BaTiO3, PLZT) |
TMDs, MOFs, h-BN, graphene, perovskites (methylammonium lead halides), black phosphorus, quantum dots |
Ti3C2, Ti2C, Nb2C, V2C, etc., with various surface terminations (–O, –F, –OH, –Cl, –Br) |
Charge generation efficiency |
Moderate |
High |
Very high under optimized conditions; influenced by surface terminations, MXene type, and the environment |
Mechanical properties |
Polymers: flexible but less strong |
Highly flexible with elevated dielectric constant but often brittle |
Excellent flexibility combined with high mechanical strength |
Metals: strong but not flexible |
Ceramics: brittle |
Surface functionalization |
Limited |
Highly tunable |
High tunable: the surface can be modified with functional groups (–O, –F, –OH) for specific triboelectric properties |
Environmental stability |
Polymers: prone to UV degradation |
Highly stable but toxic and requires protective coatings |
Moderate; MXenes are prone to oxidation |
Metals and ceramics: good stability but prone to oxidation |
Durability |
Moderate |
Good |
High potential durability; longevity depends on encapsulation and oxidation resistance |
Cost |
Low |
High |
Currently high due to complex synthesis |
Scalability |
Easy to produce on a large scale |
Still in the development stage |
Scalability is a challenge |
Design flexibility |
Limited |
High |
Very high |
MXenes are often used to form composites with polymers, metals, or other 2D materials to create hybrid structures with synergistic effects.183,184 These composites can retain the advantageous qualities of the host material, while utilizing the high charge density, mechanical strength, and flexibility of MXenes.185 For instance, high-performance TENGs with improved durability and efficiency have been created by mixing MXenes with polymers such as polydimethylsiloxane (PDMS) and polyvinylidene fluoride (PVDF).186,187 TENGs based on MXene have demonstrated promise in capturing energy from various sources, such as wind, ocean waves, and human motion. MXene composites' high output performance makes them suitable for powering portable sensors and LEDs, among other small electronic equipment, offering a renewable and sustainable energy source.188–190
3.3. Key indicators for TENG evaluation
Triboelectric nanogenerators (TENGs) are widely assessed based on a set of critical electrical parameters that represent the device efficiency and output capacity when subjected to mechanical stimuli. The critical performance indicators are short-circuit current (Isc), open-circuit voltage (Voc), output power (P), transferred charge (Q), and power density (W m−2). The maximum potential difference produced between the TENG electrodes in the absence of an external electrical load is known as the open-circuit voltage (Voc).3,89 Through contact electrification and electrostatic induction, triboelectric materials demonstrate innate capacity to produce an electric potential. When the electrodes are linked directly along the channel with zero resistance, the maximum instantaneous current that can flow is known as the short-circuit current (Isc). The total electrical charge transferred between the electrodes throughout a full mechanical actuation cycle, which usually entails a total contact and separation operation, is measured by the transferred charge (Q).191–193 To precisely monitor the low-current and high-impedance signals necessary for TENG performance evaluation, these parameters were continuously tracked using a high-sensitivity electrometer.
The maximum output power is measured by implementing an array of external resistors as a load and using the formula in eqn (2).
Furthermore, power density (P/A) is a crucial metric for evaluating the appropriateness of TENG devices of various sizes for real-world energy harvesting applications. The power density can be calculated using the formula in eqn (3).
where
A is the effective contact area of the TENG. Reliable data interpretation requires the accurate assessment of this area. The power density is particularly essential for low-frequency mechanical inputs, which are frequently found in wearable electronics, biomedical devices, and Internet of Things applications that require small and effective energy solutions.
194–196 These performance indicators offer a thorough framework for evaluating and enhancing TENG devices.
3.4. MXene magic: smart synthesis strategies
3.4.1. From atoms to layers: crafting MAX phases for MXenes.
Since their invention, numerous physical and chemical approaches have been thoroughly investigated for the synthesis of MXenes. Different synthesis procedures have been devised to create MXenes with rich configurations and distinctive properties by etching their MAX phase.197 MAX phases serve as precursors to create MXene materials with higher efficacy in various applications. Therefore, creating high-quality MXenes requires the accurate synthesis of the MAX phase and associated characterization procedures.198,199 The quality and properties of the generated MXene may be adversely affected by the presence of pollutants or phase impurities in the MAX phase precursor.200 The chemical constituents in the periodic table for the synthesis of MAX phases and MXenes are shown in Fig. 5(a). There are 342 MAX phases reported to date. Nearly half of the MAX phases were invented after 2018. MAX phases can be prepared through three techniques, which are subdivided into multiple types. These techniques include molten procedures (molten salt and infiltrating molten metal), physical vapor deposition (PVD), and solid/liquid state reactions. The synthesis of MAX phases is easy, but obtaining large yields can be challenging given that they interact with other phases such as ordered intermetallic alloys, carbides, and nitrides.201,202 Although PVD techniques yield extremely pure MAX phases, they are not appropriate for producing powder samples. The precursor MAX phases for MXene synthesis are frequently created by pressure-less (atmospheric pressure) reactive sintering in an inert atmosphere (Fig. 5(b)). This method produces porous sintered billets and makes it easier to treat them further into etching powders.203 Forming MAX phases is most commonly accomplished by liquid/solid-state reaction. To prevent their oxidation, the temperature used for synthesis normally varies from 1100 °C to 1700 °C and is carried out in a protective environment.204,205 Solid-state reactions are widely used to synthesize MAX phases. After evenly mixing the M, A, and X powders with ethanol, the particles are dried and pressed into a pellet. Then, the pellet is heated in a sealed atmosphere (>1200 °C) such as a vacuum hot press chamber for a specific period. This heating process produces an MAX phase with some intermetallic compounds. Microwave-supported heating is a unique way to achieve temperatures up to 1000 °C within minutes.206–208 The atomistic pattern of the synthesized MAX (211) phase with M and X elements divided by the A element is shown in Fig. 5(c). The distinctive layered structure of the MAX phases originates from their distinct crystal structure (Fig. 5(d–f)). The SEM image of the Ti2AlC MAX phase confirmed the formation of the MAX phase by producing a kink band, a feature of MAX phases, which is induced when the dislocations are restricted to their basal planes (Fig. 5(d)).209
 |
| Fig. 5 MAX phase—composition, synthesis, and characterization. (a) Elements in the periodic table for MAX phases and MXenes. M denotes the early transition metals (green), A indicates the group A elements (yellow), X indicates carbon, nitrogen, or carbon/nitrogen (purple), and Tx is the surface terminations of MXene after etching (rose). (b) The first step in the synthesis of the MAX phase, the usual MXene precursor, is pressure-less sintering under vacuum with the blend of M, A, and X powders. (c) Atomic arrangement of the synthesized 211 MAX phase. (d) SEM image of the synthesized 211 MAX phase. Scale 500 nm. Reprinted with permission from ref. 209. © 2020, John Wiley & Sons. (e) HR-STEM Z contrast image of the synthesized 211 MAX phase. (f) SAED pattern of the synthesized 211 MAX phase. Scale 1 nm. Reprinted with permission from ref. 210. © 2008, John Wiley & Sons. | |
To confirm the atomic-stacking sequence and phases present in the MAX precursor, high-resolution scanning transmission electron microscopy (HR-STEM) and selected area diffraction pattern (SAED) characterization were performed (Fig. 5(e and f), respectively). Fig. 5(e) shows the high-intensity Z contrast image of the 211 MAX phase (V0.5Cr0.5)2AlC. The image shows that a black layer of Al separates each of the two light layers of (V and Cr). The atomic arrangement along the [0001] direction is described as ABABAB (the letters represent the Al atom), which is a typical 211-phase structure.210 The electron beam in the SAED pattern is parallel to the 1210 direction. The SAED pattern of the 211 MAX phase confirmed its structure based on the differences in spacing for the 0001 reflections (Fig. 5(f)).210 Besides the above-mentioned the solid-state processes, the synthesis of MAX phases has also been accomplished via a sol gel-based strategy that includes several gel-promoting chemicals and water-soluble metal precursors.211
3.4.2. Synthesis and structural assessment of MXenes.
The scientific community has reported numerous synthesis processes for preparing MXene compounds based on their etchant, precursor material, and intended use. When transforming the MAX phase to MXene, the M element (transition metals) and A element are crucial in determining the etching technique.212,213 In addition to being the first MAX phase to be etched, the triadic Ti3AlC2 is still the subject of extensive research, and numerous synthesis techniques have been developed to transform it into Ti3C2Tx. Firstly, in 2011, hydrofluoric acid (HF) was used for etching the Al element from the MAX phase (Ti3AlC2) for synthesizing MXene (Ti3C2Tx). It was performed by soaking the MAX phase (Ti3AlC2) in hydrofluoric acid for a couple of hours. The resultant suspension was washed several times with DI water until the pH became neutral.214 After etching, the layers accommodated surface terminal groups such as –F, –OH, and –O. These surface terminal groups were annotated as Tx.215 The process of the HF etching is illustrated through eqn (4)–(6), as follows: | Ti3AlC2 + 3HF = AlF3 + 3/2H2 + Ti3C2 | (4) |
| Ti3C2 + 2H2O = Ti3C2(OH)2 + H2 | (5) |
| Ti3C2 + 2HF = Ti3C2F2 + H2 | (6) |
The etching time depends on the M atom. Intense etching is necessary for M atoms with more valence electrons. For instance, the stirring time for Nb2AlC is longer than that for Ti3AlC2.216 The MAX phase and MXene need to be characterized using multiple analytical techniques. Fig. 6(a) depicts the Raman spectroscopy analysis of Ti3AlC2 (MAX phase) and the etched MXene (Ti3AlC2). The Raman spectrum of the precursor Ti3AlC2 has prominent peaks in the range of 110 to 680 cm−1, which indicate its distinctive molecular vibrations. In the spectrum of MXene, the peaks at around 204 and 718 cm−1 are smooth and bent, respectively, which are comparable to the MAX phase, representing the proper removal of Al. The remaining peaks in the range of 228 to 470 cm−1 and 525 to 745 cm−1 are the vibrational modes associated with the surface functional groups (Tx) and carbon (C), respectively. Fig. 6(b) shows the XRD assessment of Ti3AlC2 (MAX phase) and the etched MXene (Ti3C2Tx). The distinctive 002 peak of the MAX phase shifted for MXene from the 2θ value to 9.7° to 6.8°, confirming an increase in the interlayer gap. The same peak 002 broadened and shifted, which were caused by the surface functional groups (Tx) replacing the Al layers owing to the appropriate exfoliation. Fig. 6(c) shows the UV-vis spectra of the MXene (Ti3C2Tx). The optical absorption of the MXene (Ti3C2Tx) with peaks at 328 and 720 nm is related to the interband conversion and plasmonic bands, respectively. These two peaks indicate the photothermal activity of MXene, particularly the second peak is due to the resonant activation at the surface of the MXene sheets.217Fig. 6(d) and (e) show the scanning electron microscopy (SEM) images of the MAX phase (Ti3AlC2) and MXene (Ti3C2Tx). Fig. 6(d) depicts the morphological feature of the stacked structure of the MAX phase at the magnification of 1 μm. Fig. 6(e) indicates the morphology of the etched MXene with a layered framework and widened gaps between the interlayers.218Fig. 6(f) shows the field emission scanning electron microscopy (FESEM) image of the MXene (Ti3C2Tx) after HF treatment. The image depicts that the MXene is etched via the nanosheets that are interleaved with each other at the magnification of 3 μm.219Fig. 6(g)–(i) show the transmission electron microscopy (TEM), high-resolution TEM (HRTEM) and SAED pattern, and the cross-sectional TEM images of the MXene (Ti3C2Tx), respectively. Fig. 6(g) shows the TEM image of the synthesized MXene, demonstrating its flawless surfaces and incredibly thin nature. Fig. 6(h) depicts the HRTEM image and SAED (inset) pattern of the MXene (magnification: 5 nm), showing its hexagonal crystal structure. Fig. 6(i) indicates that the MXene flakes are sufficiently thin to be transparent, in the range of nm. Also, the image shows that the MXene has visible 6 layers with a total thickness of 8 nm.220 Although HF etching offers multiple advantages such as absolute removal of the A element, superior morphology, and yield, the toxicity and corrosiveness of HF hinder its direct use, given that excess preventive measures and familiarity in handling HF are required. Thus, to reduce the usage of HF, various synthesis routes have been investigated.221,222
 |
| Fig. 6 Characterization of MAX phase and MXene. (a) Raman spectroscopic analysis of MAX phase (Ti3AlC2) and MXene (Ti3C2Tx). (b) XRD analysis of MAX phase (Ti3AlC2) and MXene (Ti3C2Tx). (c) UV-vis spectroscopic analysis of MXene (Ti3C2Tx). Reprinted with permission from ref. 217. © 2022, American Chemical Society. SEM analysis images. (d) MAX phase (Ti3AlC2). (e) MXene (Ti3C2Tx). Scale 1 μm. Reprinted with permission from ref. 218. © 2022 MDPI. (f) FESEM analysis image of MXene (Ti3C2Tx). Scale 3 μm. Reprinted with permission from ref. 219. © 2018, Royal Society of Chemistry. TEM analysis. (g) TEM image of MXene (Ti3C2Tx). (h) HRTEM and SAED pattern of MXene (Ti3C2Tx). (i) Cross-sectional TEM image of MXene (Ti3C2Tx). Scale 5 nm. Reprinted with permission from ref. 220. © 2018, Royal Society of Chemistry. | |
In 2014, Michael Ghidiu et al. proposed a technique of incorporating hydrochloric acid + lithium fluoride (HCl/LiF) to remove the A elements to synthesize MXene (Ti3C2Tx).41 Lithium ions persistently penetrate the MXene layer, weakening the link between M and A, eventually removing the A element from the MAX phase. This procedure also generates flammable H2 gas.223 Ammonium hydrogen bifluoride (NH4HF2) was introduced as a harmless etchant to etch the Al layers from Ti3AlC2.43 The cations present in the bifluoride salts occupy the negatively charged sites of the MXene and expand the interlayer space.224 This approach is considered to be safe compared to HF etching given that the etching occurs at room temperature. Thus, this technique is recommended for etching the Ti3AlC2 MAX phase. However, whether it will be a suitable alternative MAX phase needs to be investigated.225 The bond between Al and N in nitride MAX phases is robust and the energy required for extraction is higher than that of Al and C. Therefore, etching the A layers from nitrides and carbonitrides is largely unsuccessful when using fluoride-based water solutions. To solve this issue, other fluoride salts such as sodium fluoride (NaF, 12%), potassium fluoride (KF, 59%), and LiF (29%) were also applied for the removal of A elements for the effective synthesis of MXene.226,227 This molten-fluoride etching takes place at extremely high temperatures. It takes only 30 min for the etching process to be completed, making it an extremely efficient technique.228 In 2020, Varun Natu et al. synthesized MXene (Ti3C2Tz) without the use of water, in the presence of ammonium dihydrogen fluoride and a polar organic solvent with generous fluorine (–F) terminations.229 A comprehensive survey of MXene exfoliation techniques with their etchants, procedures, advantages, disadvantages, and safety and ecological implications is presented in Table 2.
Table 2 A comparative study of MXene exfoliation techniques: etchants, procedures, benefits, key challenges, and safety and ecological implicationsa
Exfoliation method |
Etchants |
Protocol synopsis |
Favorable aspects |
Key hindrances |
Safety and ecological implications |
References |
TMAOH: tetramethylammonium hydroxide, TBAOH: tetrabutylammonium hydroxide, Na2S: sodium sulfide, Br: bromide, LiTFSI: lithium bis(trifluoromethanesulfonyl)imide, TEGDME: tetraethylene glycol dimethyl ether, FeCl3: ferric chloride, BMIMPF6: 1-butyl-3-methylimidazolium hexafluoro-phosphate, EMIMBF4: 1-ethyl-3-methylimidazolium tetrafluoroborate.
|
Direct HF |
Hydrofluoric acid (HF) |
Direct HF etching removes A layer |
Complete etching of A layer, stable, high yield |
Presence of high fluorine contents, highly corrosive |
Highly toxic, trained persons needed to handle |
214
|
In situ HF |
HCl/LiF, LiF/NaF |
Etchants generate HF in situ, increasing interlayer spacing |
High-quality MXene, direct delamination, high-surface area |
More time to dry, interlayer spacing gets broken or reduced |
Cautious stoichiometry of precursors and solvents used, H2 gas risks |
41 and 223 |
Lewis acidic molten salt |
CuCl2/TBAOH, ZnCl2, FeCl3, CuCl2/KCl/NaCl, CrCl3 |
Salts at high temperatures remove A layers |
Binding strength, durability, stability |
High temperature, undesired byproducts, extra purification |
Expertise required for settings (etching time and temperature) |
243 and 244 |
Electrochemical |
LiCl/LiOH, KCl, NaCl, NH4Cl/TMAOH |
Bias at the anode removes A layers in electrolyte solution |
Safe and green synthesis, inexpensive, high lateral diameters |
CDC formation, structural damage, workstation required |
Electrical protection is needed, and less chemical waste |
230 and 231 |
Algae extraction |
Algae |
When exposed to algae, MAX changes into an MXene |
Low-cost, biocompatible, high-yield, and simple |
Prolonged time for etching, controlling the purity is tedious |
Algae species should be selected aptly and tested before etching |
233
|
Photochemical |
UV light |
MAX with acid exposed to UV light, an MXene is generated |
Toxic acids are not used, fine structures can be attained, and easy to reproduce |
Expensive, multiple processes, the reaction is complicated and can cause impurities |
Appropriate clothing and UV protective glass are needed, and UV intensity should be optimized |
40
|
Thermal reduction |
Inert gas (e.g., H2) |
Treating the MAX with high temperature in an inert atmosphere |
Precise structure, large-scale production, high purity, and simple |
Low yield, restricted MXene types, high energy consumption |
Inhalation hazard, handling of inert gases, high energy demand |
245
|
Hydrothermal alkali |
NaOH/Na2S, NaOH, TMAOH |
High temperature initiates the MAX phase interaction with hydroxide ions |
Fast, simple, high-purity multilayer MXenes, enhanced material stability |
Autoclave might explode, oxidation, surface defects |
Though greener, it requires waste management to reduce chemical waste |
237 and 246 |
Alkali-based |
NaOH/hydrazine, KOH, LiCl/TMAOH |
The OH ions attack the A elements of the MAX, resulting in the removal of A element |
Fluoride-free, less corrosive, control over etching |
Low quality, incomplete etching, limited surface terminations |
Caustic nature, heavy metal contamination, PPE equipment needed |
247 and 248 |
Chemical vapor deposition |
Metal foil (Ti, Zr), titanium chlorides, CH4, N2 |
Exposing the surface of the metal foil under the gas mixture diluted in Ar gas |
High-quality films, precise thickness, uniform composition, control over surface terminations |
High-cost, time-consuming, complex process, post-processing, defects |
Toxic precursors, gas leaks, chemical emissions, waste generation |
249 and 250 |
Scalable |
CO2, NH4HF2 |
Etching the MAX phase with supercritical CO2 and NH4HF2 results in MXene (–OH) |
Large-scale production, reduction in costs, high yield in a single step |
Complex setup, non-commercial, usage of hazardous chemicals (HF), problematic reactor |
Be cautious due to exothermic reaction; material disposal is crucial; gloves, face shields, and fume hoods are required |
45
|
Microwave-treated |
LiF/HCl, NaOH |
Nucleation of etchant atoms into the MAX interlayer gap in microwave causes the A elements to be removed |
Time-efficient, low etching time (30 min), less hazardous |
Limited etching depth, non-uniform temperature, non-reproducibility |
Microwave radiation exposure, impact on air quality, contaminants |
208 and 251 |
Organic base |
TMAOH, LiCl/TMAOH |
TMAOH initiates the hydrolysis of Al elements, generates Al(OH)4− ions, and leads to the formation of MXenes |
Milder etching condition, compatible with other materials, high conductivity |
Incomplete etching, surface chemistry variability, expensive |
Inhalation risk, health effects with prolonged exposure, aquatic toxicity, flammability |
252 and 253 |
Halogen + acid/halide |
I2/HCl, IBr/ICl/I2/Br2/TBAX |
Halogens lead to surface breakdown at the A element of the MAX phase, generating MXenes with halogen-terminated surfaces |
High reactivity, rapid reaction rates, good selectivity, enhanced electrical attributes |
Toxic, corrosion of equipment, high cost, limited etching depth |
Explosion hazards, bioaccumulation, generates fumes, water disposal issues |
241 and 254 |
Halide-based |
NH4Br, KBr, NaBr, LiBr, HBr |
Br ions are adsorbed, forming soluble metal halides, and the removal of A elements from the MAX |
High degree of selectivity, faster etching, simple and cost-effective process |
Risk of over-etching, only certain MXenes can be etched, low yield |
Regulatory concerns, handling risks, soil and water contamination |
255
|
Photo-Fenton |
FeCl3/sodium oxalate |
Acceleration of oxygen species weakens the M–A bonds, resulting in the formation of MXenes |
Efficient etching, reduction of structural damage, versatility, fluoride-free |
Light-dependent, iron ion contamination, pH sensitivity |
Sustainability, harmful chemical release, risk to the skin and eyes |
37
|
Gas-phase |
TiCl3, CH4 |
The precursor (TiCl3) was loaded in the reactor at 770 °C and promptly sublimated for nucleation to produce MXene (Ti2CCl2) |
Stable operation, large-production, accurate regulation for MXene synthesis |
Complex reactor, difficult to maintain constant quality in large-scale production |
Precautions required to operate the reactor, explosion risks (CH4), greenhouse gas emissions |
44
|
Li intercalation–alloying–microexplosion |
Li foil, LiTFSI, TEGDME |
Lithium intercalated into the A layer and forms Al–Ti alloys, and etched into MXene sheets |
Precise etching, single- or few-layer MXenes, high-purity, fast exfoliation |
Prolonged processing, confined to selective MAX phases, non-uniform layer thickness |
Highly reactive, ejection of particles, air pollution, demand of high energy |
256
|
Ionic-liquid (IL)-based ionothermal |
BMIMPF6, EMIMBF4, deep eutectic solvents |
Fluorine present in the etchants operates as an anion and supports the removal of A element |
Mild reaction, enduring stability, extensive tunability, enhanced dispersion, non-volatile |
Cost of IL is high, viscosity issues, pH is much higher |
Toxicity, spills or leaks can occur, reactive under high temperatures |
221
|
DC magnetron sputtering |
HF, NH4HF2 |
MAX phases were deposited on the substrate via sputtering, after which HF and NH4HF2 were used to etch the A element |
Uniform films, large-scale production, high-purity, enhanced adhesion |
Expensive, possibility of oxidation, heat generation, undesirable surface terminations |
Safety precautions since it operates under high voltage, PPE is required, and metal leakage causes habitat destruction |
43
|
Laser-based |
CH4 |
A thin film of MXene grown over the substrate in a chamber filled with ionized CH4 which produces plasma |
Enhanced layer quality, high electronic conductivity, rapid reaction kinetics |
Expensive, complex equipment, time-consuming process, undesirable carbon formation |
Harmful plasma generation, flammable methane gas, high release of carbon footprint |
257
|
All wet chemical approaches used to etch the MAX phases are intrinsically electrochemical, that is, electrons are transferred from the A elements of the MAX phases to other groups. During electrochemical etching, the anode and cathode are isolated, and the etching process is governed by the bias. Several electrolytes (NaCl and HCl) were used to etch the tightly packed MAX phases.230 Nevertheless, the MXenes formed through electrochemical etching are highly vulnerable to the excessive etching of the MAX phase. This is similar to the thorough HF etching of MXenes, which occurs by the removal of only the M element (Ti2GeC) or both the M and A elements (carbide-derived carbons (CDC)) from the MAX phase.231,232 For example, W. Sun et al. synthesized MXene (Ti2CTx) (fluorine-free) via electrochemical etching using an HCl electrolyte. In this process, Al was initially etched from the MAX phase (Ti2AlC) with only –Cl terminations and the usual –O, and OH surface functional groups. Then, the outer layer of the MXene (Ti2CTx) was again etched to CDC.231 The substantial issue of electrochemical etching is that the MXene (Ti2AlC) is exposed to a high cathodic potential, resulting in the formation of CDC. Therefore, regulation of the etching voltage, electrode assembly, and etching time is vital to attain efficient MAX phase etching.223
The synthesis of MXenes through the abovementioned techniques tends to be expensive, clumsy, and difficult. Alternatively, Shah Zada et al. established a sustainable mechanism that uses algae extract to synthesize a vanadium carbide (V2C) MXene from the parent V2AlC MAX phase.233 The unique characteristic of the algae extract etching approach is that it is biocompatible in contrast to conventional chemical procedures. Additionally, the algae can be grown under sunlight and is reasonably priced.234 The process of etching the MAX phase to synthesize MXene is illustrated in eqn (7), as follows:
| V2AlC + algae extract = V2C + Al − algae extract | (7) |
However, this etching process takes a long time and is sluggish. Furthermore, it is difficult to maintain consistency and purity during etching. Thus, this synthetic approach has rarely been used.233 To produce MXenes with a precise structure and specific morphology, Jun Mei et al. introduced a technique to synthesize a molybdenum carbide MXene (Mo2C) using UV light. This UV-induced approach is unique and effective in etching the MAX phase (Mo2Ga2C). When the MAX phase is exposed to UV light with acid, an MXene is formed. The MXenes are terminated with –OH and –Cl.40 The mechanism of etching is illustrated in eqn (8)–(10), as follows:
| Mo2Ga2C + UV light + 6HCl = Mo2C + 2GaCl3 + 3H2 | (8) |
| Mo2C + H2O = Mo2C(OH)2 + H2 | (9) |
| Mo2C + 2HCl = Mo2C(Cl)2 + H2 | (10) |
According to reports, MXenes produced using this method show encouraging outcomes when utilized as an anode material for energy-storage applications.235 MXenes with superior grade and multilayers have not been synthesized using conventional acid techniques. This can be eliminated by incorporating hydrothermal alkali etching, which produces MXenes in a short period compared to the previous approaches.236 Chao Peng et al. initially synthesized MXenes (Ti3C2 and Nb2C) using less toxic reagents (sodium borohydride (NaBH4)/HCl) via hydrothermal treatment.237 Beyond that, Tengfei Li et al. proposed a hydrothermal method to produce a fluorine-free MXene (Ti3C2Tx) using alkali (NaOH) treatment. This delivered an MXene with superior purity (above 90%) and surface terminations of –O and –OH. The proposed method is environment-friendly without the use of harmful acids. In the hydrothermal process, the MAX phase reacts with water and hydroxide ions.238 The hydrothermal activity is depicted with eqn (11) and (12), as follows:
| Ti3AlC2 + OH− + 5H2O = Ti3C2(OH)2 + Al(OH)4− + 2.5H2 | (11) |
| Ti3AlC2 + OH− + 5H2O = Ti3C2O2 + Al(OH)4− + 3.5H2 | (12) |
This hydrothermal process may be risky given that the etching occurs at high pressure and temperature. Safety precautions should be taken before the reaction to guard against blasts.239 Although there is a shortage of experimental evidence, reports have indicated that the production of MXenes may be ramped up to an industrial scale. In 2022, Christopher E. Shuck and the team from A.J. Drexel Nanomaterials Institute schemed out a chemical reactor for the mass production of MXenes. In the early stages, they prepared MXenes in two classes (1 g and 50 g) for comparison. In terms of structural morphology, they projected no discernible differences between the two classes of materials.45,78 Later, Ningjun Chen et al. synthesized large quantities (1 kg) of multiple MXenes using carbon dioxide as an etchant. The usage of carbon dioxide engages the etching of MAX phases with NH4HF2, and an –OH–terminated MXene was formed.240 This etching technique is demonstrated in eqn (13), as follows:
| Ti3AlC2 + CO2 + 3NH4HF2 = Ti3C2(OH)2 + (NH4)3AlF6 + 1.5H2 | (13) |
Preventive measures must be taken before initiating the reaction because the etching procedure employed in this method is highly exothermic. All the reported methods are expensive and complex to handle. Huanhuan Shi et al. introduced an approach for etching the MAX phase (Ti3AlC2) using iodine. Firstly, the MAX phase (Ti3AlC2) is submerged in iodine-acetonitrile (CH3CN), which forms Ti3C2Ix. Then, Ti3C2Ix is exposed to an HCl solution for delamination. After delamination, the resultant MXene is Ti3C2Tx (–OH terminated). The abovementioned process takes a longer time, and the availability of the precursor material is limited.241 An MXene was also delaminated effectively using an ion-gelation process. Here, the MXene was exposed to ions (potassium hydroxide (KOH) surroundings) to convert it into microgels. The resultant monolayer MXene (Ti3C2Tx) film was collected through vacuum filtration. This delamination occurs when the NaOH ions introduced in Ti3C2Tx.242 The process of delamination is shown in eqn (14), as follows:
| Ti3C2Tx + NaOH(aq) = monolayer MXenes | (14) |
MXenes have also been produced using several techniques, such as chemical vapour deposition (CVD), sputtering, and gas-phase (–Cl terminated) approach. Joseph Halim et al. prepared the Ti3C2Tx MXene through a magnetron sputtering procedure. Initially, a thin film (Ti3AlC2) was deposited employing a DC sputtering approach in an extreme vacuum apparatus. Then, the film was subjected to NH4HF2 for etching. After etching, an MXene (Ti3C2) film with an area of 1 × 1 cm2 was obtained.43 Sicong Liu et al. used the same sputtering technique to synthesize zirconium carbide (ZrC) above a fiber (D in shape) for the analysis of its optical attributes.258
To control the area and thickness of MXenes, Fan Zhang et al. synthesized a single crystalline Mo2C film in a large area on a sapphire substrate. This team grew a thin film via plasma-enhanced pulsed laser deposition (700 °C).257 Acid-free etching was carried out by the team of Samantha Husmann et al. They particularly etched the Al component from the MAX phases (Ti3AlC2 and Ti2AlC) adopting an ionic liquid. The ionic liquid intercalated between the layers of the MAX phases and served as an etchant. Even the interlayer spacing could be regulated through this ionic-liquid etching.259 Recently, Maoqiao Xiang and colleagues designed a reactor (fluid-based) for the synthesis of MXene (Ti2CCl2). They loaded the precursor (TiCl3) in the reactor at 770 °C and it promptly sublimated for nucleation. Ar gas was used as the gas-phase precursor for the reactor.44 The entire etching mechanism is depicted in eqn (15), as follows:
| 6TiCl3 + CH4 = Ti2CCl2 + 4TiCl4 + 2H2 | (15) |
Usually, MAX phases are etched to create MXenes. Di Wang et al. synthesized MXenes (Ti2CCl2 and Ti2NCl2) uniquely without using the parent MAX phases. They incorporated precursors such as TiCl4 or TiCl3, Ti, C or N, graphite, and methane (CH4) or nitrogen (N2) to synthesize Ti2CCl2 and Ti2NCl2 MXenes. The growth of MXenes was established by the CVD procedure (950 °C) with a knotty, unique morphology rather than a layered arrangement.250 Waterless, inexpensive, and harmless pathways for synthesizing MXene (Ti3C2) were proposed by Junbiao Wu et al. in 2020. The etching was accomplished using oxalic acid and choline chloride as the precursors, and a small amount of ammonium fluoride (NH4F) was mixed in an autoclave with the MAX phase Ti3AlC2, followed by an ionothermal reaction. These were also termed “deep eutectic solvents”, which are simple to prepare and easy to handle in the process of etching at ambient temperature.221 From 2011 to 2024, the MXene synthesis roadmap (Fig. 7) charts the significant developments in fabrication techniques, such as surface changes, precursor selection, etching procedures, and scalable production strategies.
 |
| Fig. 7 Evolution of MXene synthesis: a roadmap from 2011 to 2024. “HF etching” image: reprinted with permission from ref. 36. © 2011, John Wiley & Sons. “Intercalation (DMSO) and delamination image: reprinted with permission from ref. 260. © 2013, Springer Nature. “Bifluoride salt etching” image: reprinted with permission from ref. 43. © 2014, American Chemical Society. “HCl/LiF etching (clay technique)” image: reprinted with permission from ref. 41. © 2014, Springer Nature. “TBAOH delamination” image: reprinted with permission from ref. 42. © 2015, Royal Society of Chemistry. “Tape exfoliation” image: reprinted with permission from ref. 261. © 2015, Royal Society of Chemistry. “Molten fluoride salt etching” image: reprinted with permission from ref. 228. © 2016, Royal Society of Chemistry. “HCl/LiF etching (MILD) method” image: reprinted with permission from ref. 262. © 2016, The American Ceramic Society. “Electrochemical etching” image: reprinted with permission from ref. 38. © 2018, John Wiley & Sons. “Alkali etching” image: reprinted with permission from ref. 263. © 2018, John Wiley & Sons. “Fluoride-free molten salt etching” image: reprinted with permission from ref. 161. © 2019, American Chemical Society. “Lewis acid molten salt etching” image: reprinted with permission from ref. 39. © 2020, Nature. “UV-induced etching” image: reprinted with permission from ref. 40. © 2020, Elsevier. “Large-scale synthesis” image: reprinted with permission from ref. 45. © 2020, John Wiley & Sons. “Iodine-assisted etching” image: reprinted with permission from ref. 241. © 2021, John Wiley & Sons. “Photo-Fenton approach” image: reprinted with permission from ref. 37. © 2022, American Chemical Society. “Halide-based etching” image: reprinted with permission from ref. 255. © 2023, Elsevier. “Gas-phase synthesis” image: reprinted with permission from ref. 44. © 2024, Elsevier. | |
The hazardous chemicals utilized in the synthesis of MXene, particularly concentrated hydrofluoric acid (HF), which is extremely corrosive and presents major health and environmental risks, are intimately related to biosafety issues in research.264 HF exposure is inappropriate for large-scale or biomedical applications, wherein biosafety is a top concern given that it can result in significant tissue damage, systemic harm, and the need for stringent handling procedures. Thus, alternative etching techniques have been developed to overcome these restrictions. The LiF/HCl approach has been widely used for safer synthesis given that it produces HF in situ, greatly reducing the amount of concentrated HF that must be handled directly.41,222 Fluoride-free techniques employing chemicals such as tetramethylammonium hydroxide (TMAOH) have surfaced recently, providing a safer and more environmentally friendly path with an equivalent etching efficiency.244 In addition to improving the lab safety, these developments satisfy the increasing need for biocompatible and ecologically friendly materials for wearable and biomedical applications. To guarantee the biosafety of MXenes in real-world applications, low-toxicity synthesis techniques must be developed and adopted further.
MXenes are highly desirable for the fabrication of triboelectric nanogenerators (TENGs) due to their excellent conductivity. However, the process of oxidation impairs their performance by changing their surface charge behavior and reducing their conductivity. Exposure to the environment (moisture, oxygen) is the primary cause of oxidation, particularly at the flake edges and inadequate defect areas. Degradation is initiated by surface terminations such as –OH and –F groups, which promote the production of TiO2.265,266 Atomic defects, surface terminations, constrained water, and synthesis techniques all have a major impact on the oxidation of MXenes. Particularly, at high temperatures, the constrained water molecules entrapped between the MXene layers promote oxidation, forming TiO2 and amorphous carbon, which are more difficult to remove than surface-adsorbed water.177,267 Given that the (010) and (100) planes are more reactive and allow the quicker diffusion of oxygen than the (001) plane, oxidation mostly starts in defect-prone locations, such as the low-coordination M atoms. With time, MXene degrades into titanium oxides (such as TiO2) and disordered carbon, which results in black and white degradation byproducts that reduce their effectiveness, particularly under aqueous conditions. Similarly, it has been reported that MXenes based on Nb and Mo break down in water within days, impairing their electrical and dielectric qualities that are crucial for TENGs.268,269
Therefore, methods to improve the stability of MXenes are essential. In this case, a popular technique is polymer encapsulation, which reliably maintains the triboelectric output for days by preventing oxygen and water intrusion through hydrophilic barriers such as PVA or hydrophobic layers such as PDMS.270,271 Regulated synthesis and termination customization is another useful tactic. For instance, post-synthesis annealing can change unstable surface groups into more inert terminations, while softer etching chemicals such as LiF–HCl decrease the number of oxidation-prone sites in comparison to HF.213 Furthermore, it has been demonstrated that low-temperature preservation (−20 to −80 °C in an inert atmosphere) and solvent-assisted storage (such as in ethanol or DMSO) significantly lower the oxidation rates of MXenes.272,273 These strategies are essential for improving the long-term stability of MXenes in TENGs, where exposure to environmental conditions is unavoidable. They can be applied to a variety of MXenes beyond Ti3C2Tx. Thus, for MXenes to reach their full potential in practical energy applications, chemical, physical, and engineering solutions must be integrated.
4. Unique attributes of MXenes in TENGs
TENGs are the most effective option for capturing mechanical energy from widely accessible natural resources for harvesting electrical current. According to early TENG research, several polymers have been explored to fabricate TENGs, such as PVDF,274 PDMS,275 polytetrafluoroethylene (PTFE),276 poly(vinylidene fluoride-co-trifluoro ethylene) (PVDF-TrFE),277 polyurethane (PU),278 polyvinyl alcohol (PVA),279 and polyethylene phthalate (PET).280 The primary barrier to collecting current from TENGs is the insulating attribute of these polymers. Due to their thermal and chemical instability, an extra current-collecting material is always needed. As MXene was initially shown to be a negative triboelectric material in 2017, it has been used widely in TENGs.182,281 This section presents the benefits of MXene (Fig. 8) over other 2D and polymer materials as a multipurpose material for the fabrication of next-generation TENGs.
 |
| Fig. 8 Unique attributes of MXenes in TENG. | |
4.1. Tailorable surface terminations
Tx in the MXene representation (Mn+1XnTx) denotes the surface terminal groups present after the etching process of the MAX phase. Tx can be –O, –OH, –F, –Cl, –Br, –I, –S, etc., depending on the etchant and technique used to etch the MAX phase. These generous surface terminations equip MXenes with exceptional electronegativity, tailorable surface chemistry, and facilitating interface with the molecular dipoles of the polymers.177,282 The standard etchants (HF or LiF/HCl) used for etching the MAX phase establish the –O, –F, and –OH terminations on the MXene surface. When a high concentration of HF is used for etching, –F terminations are dominant in MXenes. In contrast, using light LiF/HCL etchants, the ratio of –O groups its higher than that of –F.283 Owing to these surface terminations, MXenes tend to act as either positive or negative triboelectric materials based on the paired material. Long Jin et al. controlled the surface terminations of an MXene (Ti3C2Tx) and analyzed the performance of TENG with an MXene and alkali-treated MXene. In the alkali-treated MXene, the fluorine terminations were reduced. Consequently, the TENG exhibited a superior performance with the MXene due to its rich fluorine groups supporting exceptional electron affinity.169 The surface terminations of MXenes, mainly fluorine groups, play a key role in the array of triboelectric materials. Besides fluorine terminations, MXenes can also act as positive triboelectric materials by altering their surface terminations.
4.2. 2D layered configuration with a large surface area
After etching, MXenes are thin nanosheets with a lamellar structure. This 2D layered configuration enhances the contact area with the other side of the triboelectric material, enabling substantial electron transfer when the two triboelectric layers are in contact.284 Also, other metal oxides285 and 2D materials such as molybdenum disulfide (MoS2),286 metal–organic frameworks (MOFs),287 graphene,288 and black phosphorus289 can be intercalated in the interlayer spacing of MXenes, preventing their oxidation, resulting in outstanding charge retention ability, and promoting superior electrical output. The efficiency of energy conversion also increases due to the combination of the conductivity and surface terminations of MXenes.290 Prolonged investigation of MXene intercalation, attention to unique surface terminations, and doping with other materials are envisioned to ignite new avenues for green energy harvesting.
4.3. Versatile fabrication and integration
MXenes show phenomenal flexibility in fabrication approaches and doping with other materials, making them ideal for multiple types of TENG designs. Due to their inherent attributes, MXenes can be prepared into numerous forms, such as films, composites, inks, and coatings.178 The processing of MXene colloidal solutions is easy given that they are hydrophilic and readily dispersed in water or solvents, which can be used for mold casting, printing, and spraying on the desired surfaces. MXenes are suitable with both traditional and modern production techniques, facilitating the economical and scalable manufacturing of TENG.291,292 The approaches for the fabrication of MXene-based TENGs (MX-TENGs) include molding,293 vacuum-filtration,46 spraying,294 spinning (electrospinning, solution blow spinning, wet spinning),295–297 chemical crosslinking,298 spin coating,299 printing (screen and 3D),300,301 and fabric framework.302 The approach for fabrication should be meticulously selected depending on the desired application and the challenge of the proposed TENG. Md Mehdi Hasan et al. introduced a thermal drawing approach for manufacturing MXene (Ti3C2Tx)/PVDF fibers with a length of 1 km in a single operation. Using textile looms, the fibers could be generated commercially and sufficiently adaptable to be knitted as fabric. Consequently, the fabric-based TENG was confirmed to show potential to capture the mechanical energy from human motions.303 In the context of (TENGs), the flexibility of MXenes in device integration is one of their notable features. MX-TENGs can be seamlessly integrated as wearable devices by integrating MXenes and polymers and simply placing them on the body to harvest energy from human activities.304 The triboelectric feature of MXene in TENG has a direct impact on the applied mechanical force. With this feature, TENG derived from MXene can be converted to a self-powered sensor for monitoring the vital signs of humans, vibrations in industries, humidity, and pressure in the environment.305 To harvest energy from numerous sources in the environment, MX-TENGs can be integrated with piezo and thermo-electric materials and function as hybrid devices.306 MX-TENGs have exceptional capability to continuously power low-energy IoT devices and wireless sensors in IoT networks for monitoring agriculture, and smart cities.196 In this area, MX-TENGs harvest energy from the environment such as wind, water waves, and vibrations from the vehicles to power the IoT devices without an external power source.307 The flexibility of MX-TENGs in fabrication and integration in multiple ways makes them perfect for extensive energy harvesting, specifically in healthcare, autonomous systems, and environmental monitoring.
4.4. Augmentation of dielectric quality
Incorporating MXene as a filler in insulting polymers (PTFE, PDMS, PVA, PVDF, etc.) significantly increases the dielectric permittivity, enhancing the surface charge density in TENGs. This enhancement is caused by the polarizability and conductivity of MXenes, elevating the charge accumulation and retention, which boosts the efficacy of TENGs. The technique of mixing conductive or ceramic materials in polymers for elevating their dielectric constant is known as dielectric modulation.308,309 Trilochan Bhatta et al. demonstrated the approach of compositing MXene into PVDF to enhance the dielectric quality of TENG for the first time in 2021. The nanofibers were prepared by electrospinning an MXene/PVDF blend to improve the dielectric constant. It was revealed that the dielectric constant of MXene/PVDF increased by 270% compared to that of the pristine PVDF nanofiber.193 Blending MXenes in the polymer molecular chains initiated the development of surface dipoles within the hydrogen atoms of the polymers and F and O atoms of the MXenes. When exposed to an external electric field, the dipoles gravitate to the direction of the electric field, increasing the dielectric constant of the material.303,310 When MXene fillers are closely spaced in the polymer chains, a fragile dielectric layer is formed in the intersection, generating a capacitor configuration. This capacitor model elevates the dielectric constant and smoothens the charge transfer in TENGs.311,312 The content of the MXene as filler must be appropriately regulated because to accommodate the closeness of the fillers it should not be too low; on the other hand, an excessive content of MXene fillers can result in tunneling charge injection and reduced charge capture capability.313 In contrast, R. L. Bulathsinghala and group incorporated a group of liquid fillers to analyze the inherent effect of the dielectric constant in TENGs. The results revealed that increasing the dielectric constant at a low load and decreasing the dielectric constant at a high load enhanced the electrical parameters of the TENG.314 The dual perspectives are not mutually exclusive, MX-TENGs may not be able to handle high loads, but they boost the other effective parameters required for superior TENGs.
4.5. Bifunctional role
MXenes can be applied as both the triboelectric layer and electrode in TENGs. Owing to the electronegative nature of MXenes, they tend to be employed as superior triboelectric negative materials in TENGs. Several forms of MXene composites have been prepared using traditional and advanced manufacturing techniques such as surface-modified films, hydrogels, 3D frameworks, and fiber mats.190 Mirza Mahmood Baig et al. analyzed the performance of a silica nanosphere-intercalated MXene (Ti3C2Tx) as a highly efficient tribonegative layer in TENGs. This intercalation eliminated the restacking of the MXene nanosheets and increased the interlayer spacing between the sheets. Also, the electronegative nature of the MXene increased through intercalation and the negative surface charges of the TENGs.315 In contrast to the above-mentioned point of view, Viet Anh Cao et al. incorporated a chemically modified Ti3C2 MXene as both the tribopositive and tribonegative friction layer simultaneously, and analyzed the performance of the fabricated TENGs. In the positive and negative triboelectric layer, the surface of the Ti3C2 MXene was terminated with NH2 and N groups using the precursor of ammonia solution for positive attributes and urea (NH2CONH2) for negative attributes. Then, the positive Ti3C2 modified with NH2 and the negative Ti3C2 modified with N were composited with nylon and PVDF-TrFE for the fabrication of TENGs. The results revealed that the mechanical performance was enhanced with superior stability and durability in 14
400 cycles.316 Likewise, Bernd Wicklein et al. demonstrated the relation of Ti3C2Tx and Ti3CNTx with sodium alginate biopolymers in TENGs. It was proposed that the MXenes can be used as either the positive or negative triboelectric material based on the other side of the contact material. They performed the analyses with different dielectric polymers and exhibited that the Ti3CNTx/sodium alginate composite acted as the positive electric layer with opposite fluorinated ethylene propylene negative layer. Also, they inferred that the Ti3CNTx composite delivered a superior triboelectric performance than the widely investigated Ti3C2Tx. The electrodes in the TENG are responsible for capturing the charges created during the contact electrification and transferring the charges to external devices.317 Thus, the appropriate choice of electrodes and patterns is crucial in enhancing the flexibility and performance of TENGs.318 Due to their attributes of superior conductivity and electrical parameters, MXenes have excelled as superior electrodes in TENGs. MXenes are widely applied as electrodes (positive or negative) in TENGs in the form of liquid, hydrogels, fabrics, and transparent materials.319 Zichao Zhang et al. incorporated a unique approach called vacuum-filtration for constructing MXene electrode-based TENGs. Firstly, they prepared an MXene/PEDOT:PSS film through vacuum filtration using a PTFE membrane as a high-conductive electrode. PTFE is a membrane with a porous pattern that directly operates as a triboelectric layer. The entire TENG was fabricated in single-step, assuring close contact between the electrode and triboelectric layer, which enabled uninterrupted charge transfer between the layers.46 Owing to their special blend of conductive and triboelectric qualities, MXenes can substantially improve TENG performance. The particular demands of the application, such as output performance, versatility, and architectural simplicity, will determine whether MXenes are used as an electrode, triboelectric layer, or both.
4.6. Intensifying robustness with exceptional conductivity
Maximizing the mechanical functionality and effective charge transfer is vital in TENG operation, as these devices are applied under frequent mechanical stress. Density functional theory (DFT) and molecular dynamics (MD) simulations revealed that the in-plane Young's modulus of MXenes was substantially greater than that of graphene with a similar thicknesses. According to DFT simulation, the Young's modulus of several carbide MXenes is larger than that of their parent MAX phases, ranging from 500 to 800 GPa.320,321 Mixing even a tiny amount of MXenes in polymers enhances the crystallinity, Young's modulus, and tensile strength of the polymer matrix.322 Kangshuai Li et al. applied an MXene to increase the mechanical performance of a TENG and used it to detect human motions and spot handwriting. Firstly, they prepared the hydrogel using hydroxypropyl methylcellulose and polyacrylamide. Then, the MXene was added to the hydrogel, which enhanced the hydrogen bonds due to the excessive hydrophilic atoms present in the MXene. The mechanical property analysis revealed that in the absence of the MXene, the hydrogel stretched to 1800% strain, whereas with the MXene-composited hydrogel, the network attained a maximum stretching of 2260% strain. It was inferred that incorporating MXenes increased the stability under multiple loading/unloading cycles, recovery rate, and strain of the hydrogel.323 The electrical conductivity of MXenes (105 S m−1) is superior to that of other materials such as metal oxides, graphene, MOFs, and conducting polymers in terms of charge transfer efficiency.324 The contact and separation of TENG devices result in the formation of charges by triboelectrification, and these charges flow through the electrode to reach the external connections. Thus, the conductivity of MXene ensures the fast and effective transfer of charges by reducing the charge decay, resistance, and energy loss. Moreover, the electron double layer is enhanced, resulting in long-term charge retention, enabling a maximum output in TENGs.325,326
Owing to their customizable surface terminations, MXenes substantially enhance TENG performance by maximizing interfacial compatibility and charge transfer. Their 2D structure and high surface-to-volume ratio optimize the active contact regions for charge production. Furthermore, their ability to improve the dielectric characteristics increases the triboelectric efficiency, while the diverse production techniques for MXenes allow their smooth incorporation into a variety of systems. Additionally, MXenes with a bifunctional role enable the fabrication of robust and flexible TENG devices. MXenes offers a revolutionary framework for creating high-performance, enduring, and scalable TENG devices for cutting-edge energy-harvesting applications.
5. Embedding MXenes in TENG devices
5.1. MXene as a next-gen electrode
In TENG, the charge transfer occurs between the electrodes during sporadic contact based on the variations in their electronegativity. The oppositely charged electrodes are separate from each another, creating an electrical potential difference akin to that of a capacitor. The voltage generated from the contact between the electrodes and the current that can be extracted from the TENG is determined by the electrical conductivity of the electrodes.327 Therefore, to extract effective electrical power from a TENG, its electrodes must be electrically conductive. Triboelectrically negative electrical conductors are extremely rare; however, triboelectrically positive electrical conductors that are classified high in the triboelectric family exist.328 Considering MXene is an excellent electrical conductor, it can be utilized as the current collector-electrode in TENGs. MXene electrodes can boost the efficiency of TENGs by lowering their internal resistance.329
Beginning with the first analysis of an MXene in a TENG device, which was published in 2017, an MXene was incorporated as electrodes in both flexible and solid TENG devices to harvest productive energy in a two-electrode design. Firstly, the Ti3C2Tx MXene solution was coated on a glass substrate, which was used as the bottom electrode, as shown in Fig. 9(a). To introduce an air gap between the top and bottom electrode, 4 insulating spacers were fixed at the corners of the substrate. Then, an ITO-coated PET film was used as the top electrode. The entire illustration of the fabricated device is shown in Fig. 9(b). Fig. 9(c) shows that the fabricated TENG device was highly flexible. To evaluate its flexibility further, the TENG device was fixed at 30° in a horizontal plane and the force of 1 N was applied to its loose end through a mandrel (Fig. 9(d)). The fabricated TENG was flexible and merged with accessories to harvest electrical energy from the movements of the body.182 To attain the maximum electrical output in a cost-effective manner and hassle-free synthesis, Shoaid Anwer et al. proposed a TENG based on an MXene negative electrode with a unique structure and enhanced stability. Initially, the Ti3C2Tx MXene was spray-coated on warm Al foil to construct the negative tribo-electrode. Then, the MXene-coated Al film (15 μm) was wrapped with a PET film for shielding. In the case of the positive tribo-electrode, PVA/NaCl was coated on an Al film using the doctor-blade approach. A thick PET film was used to anchor the triboelectric layers and to maintain the distance of 8 mm between the electrodes. The entire configuration of the fabricated TENG is shown in Fig. 9(e). This device could power 500 LEDs and precisely observe the physiological motions of humans with a durable sensing performance.330 Maximizing the simplicity of the fabrication process of TENG further, Jiacheng Fan et al. incorporated MXene as an electrode layer with enhanced flexibility and durability. The cotton fabric was submerged in an MXene/cellulose nanofiber (CNF) solution. MXene/CNF was evenly distributed on the fabric due to electrostatic absorption and used as an electrode. The friction layer was prepared by molding an Ecoflex solution and spin-coated with AgNWs. The fabricated device could detect the mass of steel objects and sustain various deformations, indicating that it can be used as a wearable to detect human motions.331 Detecting ions in humans requires pre-enzymes such as urease, DNAzymes, and glucose oxidase enzymes. These enzymes need to be modified specifically to detect the target of interest. When detecting glucose, the enzyme must be biocompatible, stable, and compatible with electrochemical systems.332 Addressing the above-mentioned limitations of glucose detection, Wei Yang et al. designed a TENG device incorporating MXene/graphene oxide (GO) as an electrode for glucose detection. The MXene/GO film was prepared by mixing the exfoliated MXene and GO through an ultrasonic approach (Fig. 9(f)) and the mixture was filtered using a vacuum-filtration technique. After drying, the MXene/GO film easily peeled off. An Ecoflex solution was spin-coated on the glass substrate and Cu tape was fixed at the back of the Ecoflex film. MXene/GO was employed as the top electrode, Cu tape as the bottom electrode, and Ecoflex as the triboelectric layer (Fig. 9(g)). To detect glucose, glucose-dissolved water was dropped on the surface of the electrode and dried at room temperature.288
 |
| Fig. 9 MXene as electrodes in TENG. (a) MXene solution was coated on a glass surface. (b) Top PET-ITO electrode and bottom MXene-coated glass electrode were divided by spacers composed of insulating glass, which was about 1 mm thick. (c) Evaluation of the flexibility of MXene TENG by manual bending. (d) MXene TENG was held at a 30° angle and flexed by a mandrel at 1 N per second. Reprinted with permission from ref. 182. © 2018, Elsevier. (e) TENG device with a spray-coated MXene shielded by PET and PVA/NaCl coated on Al foil. Reprinted with permission from ref. 330. © 2023, Elsevier. (f) Approach for the fabrication of MXene/GO electrode. (g) Schematic of TENG device with MXene/GO film as the electrode. Reprinted with permission from ref. 288. © 2023, MDPI. (h) Diagrammatic representation of the fabrication procedure of MXene/CNF liquid electrode for TENG. Reprinted with permission from ref. 335. © 2020, John Wiley & Sons. (i) Layout dimensions and architecture of the MXene/PVA hydrogel electrode-based TENG. Reprinted with permission from ref. 298. © 2021, John Wiley & Sons. (j) Diagram showing the construction of MXene/PVA TENG with hydrophobic PVDF electrode. Reprinted with permission from ref. 47. © 2023, Elsevier. (k) Structure of chitin nanocrystals. (l) Fabrication of MXene/chitin nanocrystals through vacuum-filtration approach. Reprinted with permission from ref. 339. © 2024, Elsevier. (m) Copolymerization of MXene/CNF/PAS hydrogel. (n) Schematic of single-electrode TENG. Reprinted with permission from ref. 340. © 2024, Elsevier. (o) Fabrication of TENG skin patch based on MXene/gelatin hydrogel. Photographs of (p) TENG skin patch and (q) TENG skin patch applied to treat a mouse. Reprinted with permission from ref. 341. © 2024, Elsevier. | |
Skin-mounted electronics are more likely to use single-electrode TENGs due to their potential benefits of simple structure and portability. The appropriate electrode material is the most important element in ensuring that single-electrode TENGs operate normally. In this case, liquid electrodes are considered an excellent choice for constructing efficient single-electrode TENGs.333,334 W. Cao et al. reported the fabrication of a single-electrode TENG based on an MXene composite as a deformable liquid electrode. Initially, the delaminated MXene Ti3C2Tx and naturally extracted CNF were mixed uniformly through stirring. Alternatively, liquid silicon was poured into plain PTFE and sandpaper-fixed PTFE molds separately. Then the two silicone rubbers were attached to form a capsule-like assembly. Finally, the MXene/CNF dispersion was injected into the capsule (Fig. 9(h)). A TENG was fabricated with MXene/CNF liquid as the electrode and silicone rubbers as the triboelectric and packaging layer. Employing this method, the application potential of single-electrode TENGs has been accelerated in harvesting energy and physiological signal monitoring with superior sensing properties.335 However, liquid electrodes necessitate a packaging layer to avoid leaks and are vulnerable to evaporation, non-biocompatible, less flexible, and pose chemical hazards, which can reduce their performance over time.336 Xiongxin Luo et al. fabricated a TENG device using an MXene/PVA hydrogel as an electrode to eliminate the above-mentioned drawbacks. MXene/PVA was prepared using PVA as the base solution and MXene as the crosslinking substance. Two Ecoflex layers were prepared with the same size and the prepared MXene/PVA hydrogel was encapsulated between them. The top and bottom Ecoflex layers were connected to prevent water leakage from the hydrogel (Fig. 9(i)). The MXene fillers facilitated the crosslinking of the PVA hydrogel and created microchannels within the hydrogel. This enhanced ion transport enabled the TENG to stretch about 200% from its original length.298 Triboelectric charges dissipate more quickly in hostile environments such as high humidity, biofouling, and elevated friction at the surface of the ocean, which will shorten the tribo-electrode service life. These factors significantly affect the stability and efficiency of energy harvesting and restrict the use of TENGs in the marine environment.337,338
A novel TENG with enhanced triboelectric properties at 95% humidity and an effective sterilization rate of 98.9% was fabricated by Xiao Sun et al. using MXene/PVA as electrodes. The MXene/PVA electrode was prepared by mixing PVA and MXene solutions until their dispersion and pouring the dispersion into a PTFE mold, drying, and peeling it off. The alternate electrode was prepared using a 3D-printed stainless-steel substrate and PVDF nanowires to elevate the hydrophobicity of PVDF. Then, both the MXene/PVA electrode and PVDF electrode were assembled to fabricate a TENG device. As shown in Fig. 9(j), adding MXenes enhances the number of hydrogen bonds on the surface of PVA, which fixes more water molecules there. These water molecules act as an electropositive material and contribute to the friction process. This shows that the TENG can withstand water treatment with a long life in the oceanic environment.47 Decreasing the electron affinity of MXenes enhances their charge-storing and charge-transfer capability in TENGs. Adding adhesives to MXene increases its electrical conductivity, which is highly required for its application as an electrode in TENG.342 Yunqing He et al. proposed a single-electrode TENG based on an MXene/chitin nanocrystal composite as an electrode. Chitin nanocrystals were extracted from the disposed shell of shrimp through a hydrolysis approach (Fig. 9(k)). The composite was prepared with the synthesized MXene and chitin in different ratios through vacuum filtration (Fig. 9(l)). Then, the composite was packed using PDMS to avoid the oxidation of the MXene/chitin film. Due to electrostatic attraction and hydrogen bonding, chitin stuck to the surface of the MXene nanosheets when combined in a certain ratio (Fig. 9(l)). The negative charge on the surface of the MXene nanosheets was continually neutralized as the weight ratio of chitin to MXene increased. This reduced the electron affinity and increased the conductivity and robustness of the TENG.339
The high water content in hydrogels creates a thin barrier, which often keeps hydrogels from sticking directly to the skin. During repetitive deformations in TENG, efficient electrical signal detection and transmission depend on the excellent adherence of hydrogels.343,344 A hydrogel with exceptional adhesive properties as a TENG electrode was proposed by Wei Zhang et al. using an MXene as the crosslinker, acrylic acid, 2-(methacryloyloxy)ethyldimethyl-(3-sulfopropyl)ammonium hydroxide, and acrylic acid N-hydroxysuccinimide ester were copolymerized and dissolved with CNF in water and potassium persulfate was added in a single process to create hydrogels (Fig. 9(m)). The MXene acted a multipurpose crosslinking agent that accelerated the gelation of the hydrogels, in addition to serving as the conductive filler. The TENG device was fabricated by encapsulating the MXene hydrogel electrode between two PU films (Fig. 9(n)). Even under moist conditions, the MXene hydrogel-based TENG device adapted to the surface of the skin and demonstrated advantageous self-adhesive qualities.340 Likewise, Bo-Yu Lai et al. used an MXene in a PVA/PEG hydrogel to further enhance the streaming vibration potential in TENGs. The fluorine-terminated MXenes in the hydrogel served as an ionic conductor (electrode), initiating an electrostatic mechanism, which in turn increased the effectiveness of the TENG device.345 Coupling photothermal materials with TENG devices, which combine electrical and thermal stimulation to fasten wound healing, is considered a favorable approach.346 A single-electrode mode TENG was fabricated based on an MXene/gelatin hydrogel as an electrode with strong wound-healing capability by Meiru Mao et al. The hydrogel was prepared by mixing an aqueous MXene solution and gelatin-dissolved water; afterwards, glycerol was added to the mixture (Fig. 9(o)). After vigorous stirring, the hydrogel was prepared. The TENG device was fabricated by sandwiching the hydrogel between the two Ecoflex layers and glued together with Ecoflex solution (Fig. 9(p)). The hydrogel-based TENG device was proven to accelerate wound healing in mice (Fig. 9(q)) by enhancing cell proliferation and has wide potential in other biomedical applications.341
Attaining a dual-function sensor is the most demanding in electronic devices. In this case, fiber membranes have been widely used in both TENG and strain sensors. Fiber composite membranes are prepared via the electrospinning technique.352,353 Qingsen Gao et al. fabricated a unique MXene composite membrane for both strain sensing and as an electrode in TENG for harvesting energy. First, a thermoplastic urethane conductive nanofiber film (TPU) was prepared with a TPU-dissolved solution by electrospinning. TPU was submerged in a polydopamine solution to enhance the binding force between the fiber and MXene. Then, the film was submerged in the prepared MXene/carbon black solution. After drying, a nanofibrous membrane with outstanding conductivity was obtained (Fig. 10(a)). At last, the fiber was used as a TENG electrode and strain sensor for harvesting energy and monitoring human activities.347 The nanostructure of an MXene was altered through the oxidation technique and used as a conductive filler in polyacrylamide for the preparation of a hydrogel. After etching, NaOH was added to the MXene solution to increase the number of hydroxyl groups in the MXene. The high amount of hydroxyl groups in MXene reacted with the Ti atoms, resulting in the production of TiO2 nanowires and protecting the MXene from further oxidation (Fig. 10(b)). This oxidation treatment enhanced the dispersibility, sensitivity, and transparency of the MXene.348
 |
| Fig. 10 MXene as an electrode in TENG. (a) Schematic illustration of the electrospinning process to prepare the MXene/PDA/CB/SR/TPU composite fiber. Reprinted with permission from ref. 347. © 2024, John Wiley & Sons. (b) Schematic illustration of the preparation of oxidized MXene/polyacrylamide hydrogel. Reprinted with permission from ref. 348. © 2024, Elsevier. (c) Schematic illustration of the preparation of melamine/MXene/PDA/AgNW foam. (d) Single-electrode melamine/MXene/PDA/AgNW foam-based TENG. Reprinted with permission from ref. 349. © 2024, John Wiley & Sons. (e) Schematic illustration of the MXene/PMMA electrode TENG. (f) Preparation process of MXene/PMMA composite film through vacuum-filtration. Reprinted with permission from ref. 350. © 2023, John Wiley & Sons. (g) Electrohydrodynamic printing process of PAM/CNF/MXene conductive hydrogel. Single-electrode TENG based on conductive hydrogel. (h) Graphical representation. (i) Photographic image. Reprinted with permission from ref. 351. © 2025, American Chemical Society. | |
A transparent ionic liquid-based MXene–AgNW composite was also prepared on a large scale (20 cm wide roll) as a flexible transparent electrode for electromagnetic shielding and TENG. The composite exhibited excellent stability, and durability even at elevated temperatures.354 3D foams exhibit enormous potential in TENGs for harvesting energy. Chenhui Xu et al. proposed a TENG device using MXene foam as the negative electrode. Melamine foam was dipped into a PDA solution under stirring, and then the melamine foam modified with PDA was dip-coated in an MXene/AgNW solution (Fig. 10(c)). The dried MXene/AgNW/melamine/PDA foam was used as the negative electrode and an Ecoflex layer was coated on the electrode as the friction layer (Fig. 10(d)) in a TENG for monitoring human activities.349 A versatile tile-structured MXene/polymethyl methacrylate (PMMA) film as an electrode (Fig. 10(e)) in TENG for monitoring vital signs was proposed by Huamin Chen et al. PMMA was added to the MXene solution and stirred until forming a dispersion. Using vacuum-filtration, the tile structure was assembled in the MXene/PMMA layer (Fig. 10(f)). It was shown that physiological signals in a variety of kinematic motions, including finger and elbow bending, belly breathing, and throat pronouncing, could be detected by a wireless monitoring system with the TENG.350 The conventional hydrogels are comprised of a polymer matrix with high structural voids. However, this polymer matrix exhibits low strength, resulting in inadequate mechanical attributes.355 The performance of MXene electrodes in TENGs with their triboelectric layers, fabrication approaches, electrical parameters, and corresponding applications is tabulated in Table 3.
Table 3 A brief outline of MXenes as high-performance electrodes in TENGsa
Electrode (MXene) |
Triboelectric layers |
Fabrication approach |
Mode |
Voltage |
Current |
Power or power density |
Stability (cycles) |
Application |
References |
TP: tribopositive electric layer, TN: tribonegative electric layer, CS: vertical contact-separation mode, SE: single-electrode mode.
|
Ti3C2Tx |
PET |
Spray coating |
CS & SE |
650 V |
7.5 μA |
0.65 mW |
50 000 |
Energy harvesting from muscle movements |
182
|
Ti3C2Tx |
TP-PVA/NaCl |
Spray coating |
CS |
390 V |
96 μA |
6.66 mW m−2 |
15 000 |
Detect and monitor human motions |
330
|
TN-PET |
Ti3C2Tx/CNF fabric |
TN-silicone rubber |
Dip coating |
SE |
400 V |
680 nA |
40 mW m−2 |
1500 |
Monitor human body motions and handwriting |
331
|
Ti3C2Tx/GO |
TP-Ecoflex |
Vacuum filtration |
CS |
258.8 V |
2 μA |
84.5 μW |
2400 |
Non-invasive glucose detection |
288
|
Ti3C2Tx/CNF liquid |
TN-silicone rubber |
Mold casting |
SE |
300 V |
5.5 μA |
505 mW m−2 |
6000 |
Monitor human motions |
335
|
Ti3C2Tx hydrogel |
TP-Ecoflex |
Chemical crosslinking |
SE |
230 V |
270 nA |
0.33 mW m−2 |
— |
Monitor body motions and handwriting |
298
|
TN-Kapton |
Ti3C2Tx/PVA |
TP-PVA |
Solution blending |
CS |
1056 V |
36.6 μA |
— |
50 000 |
Water treatment in an oceanic environment |
47
|
TN-PVDF |
Ti3C2Tx/chitin |
TP-glass |
Vacuum filtration |
SE |
56 V |
3.2 μA |
99.5 mW m−2 |
2000 |
Detecting joint bents and tactile sensing |
339
|
TN-PDMS |
Ti3C2Tx/CNF/PAS hydrogel |
TP-PU |
Mold casting |
SE |
143 V |
10 μA |
— |
3000 |
Detecting human motions |
340
|
TN-Kapton |
Ti3C2Tx/PVA/PEG hydrogel |
TP-silicone rubber |
Chemical crosslinking |
SE |
212 V |
1.1 μA |
3 mW m−2 |
— |
Human motion monitoring |
345
|
TN-PTFE |
Ti3C2Tx/gelatin hydrogel |
TN-Ecoflex |
Solution blending |
SE |
163.7 V |
8.1 μA |
— |
6000 |
Wound healing |
341
|
Ti3C2Tx/TPU/PDA/CB fiber |
TN-silicone rubber |
Electrospinning |
SE |
115 V |
0.8 μA |
68 mW m−2 |
10 000 |
Detect human motions |
347
|
Ti3C2Tx/PA hydrogel |
TN-Ecoflex |
Solution blending, oxidation treatment |
CS & SE |
243 V |
31 μA |
2.38 mW m−2 |
850 |
Operate in vibrations, morse code recognition |
348
|
TP-PA |
Ti3C2Tx/AgNWs foam |
TP-Ecoflex |
Vacuum-assisted dip coating |
SE |
115 V |
1.7 μA |
514.2 mW m−2 |
10 000 |
EMI shielding, sport monitoring |
349
|
TN-PVDF |
Ti3C2Tx/PMMA |
TN-PDMS |
Vacuum filtration |
CS |
37.8 V |
1.8 μA |
7.3 μW |
10 000 |
Wireless human health monitor |
350
|
Ti3C2Tx/CNF/PAM |
TP-Ecoflex |
Electrohydrodynamic printing |
SE |
67.5 V |
0.13 μA |
— |
600 |
Monitor human motions and writing recognition |
351
|
TN-Kapton |
Ti3C2Tx/GO/PAM/PDA |
TP-butyronitrile |
Chemical crosslinking |
CS |
105 V |
0.72 μA |
1 W cm−2 |
— |
E-skin and human–machine interface |
356
|
TN-PTFE |
Hongjie Zeng et al. prepared a conductive hydrogel with a dual matrix configuration, which eliminated the high gaps present in the single matrix configuration. Using polyacrylamide (PAM), MXene, and CNF, a conductive hydrogel was prepared via in situ photopolymerization aided by the electrohydrodynamic printing approach under the influence of UV light (Fig. 10(g)). Then, the hydrogel was encapsulated with Ecoflex as the negative triboelectric layer and a Kapton film was used as the positive triboelectric layer (Fig. 10(h)). A photograph of the fabricated TENG device is shown in Fig. 10(i). The fabricated TENG was not only used to detect human motions but also to transmit information.351
Considering their many benefits compared to conventional materials such as metals, polymers, and other 2D materials such as graphene and MoS2, MXenes have become promising electrode materials for TENGs.357 MXenes have metallic conductivity of over 20
000 S cm−1, which makes charge transport more effective and improves the performance overall of TENG. Conversely, MWCNT/chitosan and graphene-based electrodes usually show conductivity in the range of 10–10
000 S cm−1, whereas Ag/chitosan electrodes offer lower conductivity (∼6300 S cm−1).358 Owing to their surface groups (–OH, –F, and –O), which improve charge trapping and adherence to dielectrics, MXenes have two-dimensional layered structures that improve charge transmission. In contrast to liquid metals, they are easily shaped and produced using low-cost, scalable techniques, and they provide exceptional mechanical strength and flexibility superior to CNTs and graphene.331,359 As a result, when compared with conventional materials, MXenes offer a well-balanced combination of high conductivity, mechanical compatibility, and chemical activity, which significantly improve the performance of TENG devices.
5.2. MXene acting as an electrode and triboelectric layer concurrently
According to the working principle of TENGs, which combines contact electrification and electrostatic induction, the electrical conductivity of the electrode materials and the contact-generated voltage between the triboelectric layers determine the output performances of the resulting TENGs, which can impact the maximum energy extracted from these devices. Thus, the sensible selection of materials as the electrode and triboelectric pairs is essential in enhancing the output capabilities of TENGs. Numerous electronegative polymers such as PDMS, PI, PTFE, and FEP have been widely used as materials for the fabrication of TENGs.327 Nevertheless, their continued use as electrodes, where high electrical conductivity is required to extract the most energy from the devices, is hindered by the electrically insulating nature of the polymers or the low electrical conductivity of composites.360 Benefitting from the rich surface terminal groups, exceptional electronegativity and enhanced conductivity of MXenes, researchers have applied them as both the electrode and triboelectric layers simultaneously. This dual function of MXenes in TENGs simplifies the device structure, reduces interfacial losses, minimizes material consumption, and enhances charge transfer at a low cost.361
A TENG device was fabricated by Yuzhang Du et al. utilizing the benefits of high conductivity and electronegativity of MXenes. An MXene-polymer composite was prepared using the mold (PTFE) casting technique and the device was fabricated by dropping a Ti3C2Tx MXene solution on an MXene-polymer mold. After drying, the other MXene-polymer composite was attached to the top (Fig. 11(a)). The pristine MXene electrode (50 μm) was sandwiched between the two MXene-polymer composites (triboelectric layers) and the device operated in single-electrode mode (Fig. 11(b)), which exhibited rich EMI shielding ability with outstanding self-healing capacity.54 Reliable wearable electronics face a huge problem in developing flexible, affordable, and self-powered TENGs with a good output performance, while their potential applications are hampered by their low surface charge density.362 Xu Yang et al. proposed a TENG device based on an MXene hybrid film, which was economically fabricated in a single step. Firstly, a PEDOT solution was mixed in an Nb2CTx MXene solution, and then the CNT was added to the MXene/PEDOT solution. The solution was ultrasonicated to attain complete dispersion and filtered through vacuum filtration using a PTFE membrane (Fig. 11(c)). Two membranes were prepared similarly and assembled. In the top film, the hybrid MXene composite acts as an electrode and PTFE as a tribolayer, and in the bottom film, the MXene hybrid acted as an electrode as well as a triboelectric layer (Fig. 11(d)), and the reported device has potential for wide application in biomedical wearables.363 Surface terminations in MXenes determine the performance of TENGs and the research on MXene in TENG mainly focuses on MXene composites and synthesis.304 The influence of surface terminal groups of MXenes when applied in TENGs was analyzed and compared by Xu Cai et al. by refining the MXene synthesis with different approaches. The comparison was between the synthesis of MXene by gentle etching with various times and temperatures, bare MXene, and HF etched MXene. As shown in Fig. 11(e), the TENG device exhibited a better response with the MXene synthesized via gentle etching (48 h at 40 °C) paired with an Ecoflex triboelectric layer.364 Preserving and protecting sensitive data as universal concerns have arisen with major consequences for the armed forces, the economy, and national security.365 As a luminescence emission method, alternating current electroluminescence (ACEL) is a significant substitute for luminous data encryption owing to its extremely long lifespan, consistent luminescence, and ease of construction.366 Nevertheless, the necessity of an external high-voltage AC power source significantly limits its use in portable electronics.367 In this case, ACEL devices can be directly powered by TENG. Copper wires and other weak electrical connections are still utilized to link two distinct TENG and ACEL devices, which still have significant issues with portability and integrity.368 A self-powered EL wearable device can be implemented by sharing the electrode in both the TENG and EL devices. Siyu Zhang et al. fabricated a wearable EL device by integrating a TENG and EL sharing s common single MXene electrode, which eliminated the requirements of external wires. The electrode was prepared by spin-coating a Ti3C2Tx MXene solution on a surface-modified PET film. The TENG device was fabricated by pouring the MXene/silicon solution on a mold and covering the mixture with half of the MXene electrode (Fig. 11(f)). After drying, the TENG device with a metal wire was peeled off and operated in single-electrode mode (Fig. 11(g)). The remaining half of the electrode was used by the EL device.49
 |
| Fig. 11 MXene as an electrode and triboelectric layer in a TENG. (a) Fabrication of the TENG device by sandwiching the MXene electrode between two MXene/polymer elastomers. (b) Single-electrode operating mode of fabricated TENG. Reprinted with permission from ref. 54. © 2022, Elsevier. (c) Fabrication process of CNT/MXene/PEDOT hybrid film. (d) Simple architecture of TENG with two CNT/MXene/PEDOT hybrid films. Reprinted with permission from ref. 363. © 2022, Elsevier. (e) Graphical diagram of TENG with MXene as an electrode and triboelectric layer. Reprinted with permission from ref. 364. © 2023, John Wiley & Sons. (f) Fabrication procedure of TENG with MXene electrode and MXene/silicone elastomer as a triboelectric layer. (g) Device representation of single-electrode mode TENG. Reprinted with permission from ref. 49. © 2023, John Wiley & Sons. (h) Fabrication process of MXene/PEDOT:PSS hybrid film and simple architecture of TENG with two MXene/PEDOT:PSS hybrid films. (i) Operating procedure of TENG. Reprinted with permission from ref. 46. © 2021, Elsevier. (j) Optical image of the MXene/CNF film. (k) Device structure of MXene TENG. Reprinted with permission from ref. 370. © 2022, American Chemical Society. (l) Fabrication process of the MXene-leather coated LIG film. (m) Architecture of the TENG device. Reprinted with permission from ref. 51. © 2023, American Chemical Society. (n) Preparation process of the MXene/oxidized CNF film. (o) Device architecture with MXene/oxidized CNF film as an electrode and triboelectric layer. Reprinted with permission from ref. 371. © 2025, Elsevier. (p) Schematic diagram of TENG device driven by wind. Reprinted with permission from ref. 372. © 2024, Elsevier. | |
Finding a stable electrode-triboelectric layer interface for prompt and sustained triboelectric surface charge transfer is still very difficult.362 A unique technique for fabricating a TENG combining the electrode and tribolayer in single-step without a hybrid membrane composite was first proposed by Zichao Zhang et al. The TENG was fabricated by mixing PEDOT/PSS in a Ti3C2Tx MXene solution under stirring. Then, the solution was filtered using a vacuum-filtration assembly with a PTFE membrane. Likewise, another film was prepared and assembled to fabricate the TENG device (Fig. 11(h)). As shown in Fig. 11(i), the TENG device operated in contact-separation mode, generating charges when the upper PTFE film came into contact with the lower MXene film (tribolayer and electrode).46 Numerous researchers have incorporated MXenes as conductive fillers to increase the conductivity or dielectric permittivity of polymers. There are much less reports on high-content MXene composites with electronegative or even electropositive properties that function as efficient electrodes and tribolayer at the same time.369 A high-content MXene/CNF film with a novel spider-web architecture for attaining an enhanced performance in TENGs was proposed by Chenyang Xing et al. The MXene film was prepared by mixing a CNF solution with an MXene solution using an oscillator, and then the mixture was filtered using a vacuum-filtration approach, and a photograph of the film is shown in Fig. 11(j). The TENG device was fabricated by assembling the prepared MXene film with PTFE or nylon as the counter triboelectric layer (Fig. 11(k)). A high content denotes that the ratio of MXene starts from 20% to 80%.370
The addition of MXene to polymers not only enhances the flexibility of polymers but also increases the resistive property in the composites. Another approach to enhance the flexibility is by generating stretchable structures in the substrates.373,374 The performance of MXene as an electrode and triboelectric layer simultaneously in TENGs with their triboelectric layers, fabrication approaches, electrical parameters, and corresponding applications is presented in Table 4. Several membranes have been used such as PTFE, and cellulose ester for preparing MXene films. A genuine and steady approach for maximizing the flexibility of MXene films using natural leather as a filter membrane was reported by Shaochun Zhang et al. The Ti3C2Tx MXene film was prepared through a vacuum-filtration approach using leather as a filter membrane. PI tape was fixed at the back of the leather and treated with a laser to attain a laser-induced graphene (LIG) electrode. Then, the film was dipped into an HAuCl4 solution to coat Au on the LIG electrode (Fig. 11(l)). The TENG device was assembled by pairing the LIG electrode with triboelectric positive PU and operated in single-electrode mode (Fig. 11(m)).51 When natural cellulose was properly treated, CNF with better flexibility, stretchability, and biocompatibility was obtained. However, prior research has shown that surface modification with functional groups can influence the triboelectric charge density of CNFs.375,376 To enhance the flexibility of CNFs further, Linlin Zhou et al. oxidized CNFs with carboxylate functions. The film was prepared by mixing an oxidized CNF and 50% MXene solution under stirring, and after that the solution was filtered using vacuum-filtration (Fig. 11(n)). The TENG was fabricated using the electronegative MXene-oxidized CNF composite paired with nylon as the positive triboelectric layer. The composite film was used as the bottom electrode and dielectric, while Cu was used as the top electrode (Fig. 11(o)).371 Gaseous pollutants such as nitrogen dioxide (NO2), ammonia (NH3), and sulfur dioxide (SO2) play a significant role in aggravating the problem of chemical gas pollution, which has become one of the main causes of sickness and fatalities. Thus, the requirement for chemical gas sensors for detecting chemical gases is high, leading to the necessity of energy consumption.377,378 Dongyue Wang et al. found that the usage of MXene in interdigitated electrodes as a multi-gas sensing element powered by TENG will resolve the abovementioned issues. Four PVC sheets, each 1 mm thick, were initially attached to form the body of the TENG device. The cellulose acetate sheet was adhered to a sleek rod at one end. At last, the top and bottom of the frame were sprayed with Ti3C2Tx MXene. As shown in Fig. 11(p), the TENG was fabricated with MXene as the electrode and negative tribolayer and cellulose acetate as the positive tribolayer.372
Table 4 A brief outline of MXenes as high-performance electrodes and triboelectric layers concurrently in TENGs
Electrode (MXene) |
Triboelectric layers |
Fabrication approach |
Mode |
Voltage |
Current |
Power or power density |
Stability (cycles) |
Application |
References |
Ti3C2Tx |
TN-MXene |
Mold & drop casting |
SE |
245 V |
29 μA |
1150 mW m−2 |
— |
EMI shielding |
54
|
Nb2CTx/CNT/PEDOT |
TP-Nb2CTx/CNT/PEDOT |
Vacuum filtration |
CS |
184.1 V |
4.2 μA |
420 μW |
400 |
Detecting small human motions such as vocal cord movement and wrist bending |
363
|
TN-PTFE |
Ti3C2Tx |
TP-Ecoflex |
Vacuum filtration |
CS |
281 V |
9.7 μA |
633.24 mW m−2 |
4100 |
Wireless control over a computer game |
364
|
TN-Ti3C2Tx |
Ti3C2Tx |
TP-skin/nylon |
Spin coating & mold casting |
SE |
290 V |
24 μA |
0.9 W m−2 |
10 000 |
Decrypting and encrypting hidden information |
49
|
TN-MXene/silicone rubber |
Ti3C2Tx |
TP-MXene/PEDOT PSS, TN-PTFE |
Vacuum filtration |
CS & SE |
29.56 V |
0.07 nA |
— |
6000 |
Detecting human voices and facial expressions |
46
|
Ti3C2Tx |
TP-MXene/CNF |
Vacuum filtration |
CS |
1120 V |
24 μA |
144 mW m−2 |
7000 |
Gesture recognition |
370
|
TN-PTFE |
Ti3C2Tx |
TP-PU |
Vacuum filtration & dip coating |
SE |
199.56 V |
9.04 μA |
0.469 mW cm2 |
4000 |
Human–machine interaction |
51
|
TN-MXene |
Ti3C2Tx/TOCNF |
TP-nylon |
Vacuum filtration |
CS |
210 V |
0.84 μA |
— |
3600 |
Detecting human motions and transmission of information |
371
|
TN-MXene/TOCNF |
Ti3C2Tx |
TP-cellulose acetate |
Spray coating |
CS |
269 V |
13.2 μA |
1.2 mW |
12 500 |
Chemical gas detection |
372
|
TN-MXene |
TENGs that incorporate MXenes as both electrodes and tribolayers offer distinct benefits over conventional materials. In TENGs, MXenes can act as the tribolayer and electrode at the same time. This dual functionality simplifies the manufacturing process and device structure, which can lower costs and improve the device dependability.285,379 Alternatively, traditional materials frequently require distinct tribolayers and electrodes, making the design and production procedures more difficult. MXenes have outstanding wear resistance and mechanical strength.59 According to studies, MXene-based composites outperform other materials in durability tests due to their reduced friction and ultralow wear rates.370 Furthermore, to improve their triboelectric qualities, MXenes can be blended with a variety of compounds, including silicone, polyvinylidene fluoride (PVDF), and polydimethylsiloxane (PDMS).380 In summary, MXenes provide a special blend of strong electrical conductivity, superior mechanical strength, the ability to operate as both electrodes and tribolayers, high output performance, and material combination diversity.
5.3. MXenes as electron donor (positive) tribolayer
According to research, the triboelectric characteristics of MXenes are greatly influenced by their synthesis techniques, etchants, intercalating chemicals, and processes.172 Etching the MAX phase (Ti3AlC2) through a minimally intensive layer delamination (MILD) approach using LiF/HCl etchant results in an MXene with positive polarity. The Ti3C2Tx MXene synthesized through MILD etching was incorporated as the positive triboelectric layer and paired with PTFE as the negative tribolayer in a TENG (Fig. 12(a)). The TENG device operating in single-electrode mode could be used to detect infusion and clinical discharge procedures in real-time, lowering the workload of medical personnel.46 Extending the investigation of the MXene on positive polarity, Lin Shi et al. synthesized MXenes (Ti3C2Tx, Nb2CTx, and V2CTx) via mild etching and paired them with 9 different polymers to determine their surface potential. The MXene film was prepared via the vacuum-filtration technique using a PVDF membrane. The Ti3C2Tx, Nb2CTx, and V2CTx MXenes exhibited positive triboelectric characteristics when paired with PVC as triboelectric layers (Fig. 12(c)). Particularly, Nb2CTx showed an extremely elevated power density compared with the other two MXenes. Using Kelvin probe force microscopy (KPFM), the contact potential difference was depicted to confirm the polarity of the MXenes. Based on the contact potential difference, Nb2CTx (Fig. 12(b)(iii)) possessed a higher positive voltage compared to Ti3C2Tx. V2CTx (Fig. 12(b)(i)) exhibited a lower voltage than both the Ti3C2Tx (Fig. 12(b)(ii)) and Nb2CTx MXenes. However, all MXenes examined in this study are oriented toward the positive end of the triboelectric series, as seen in Fig. 12(d).173
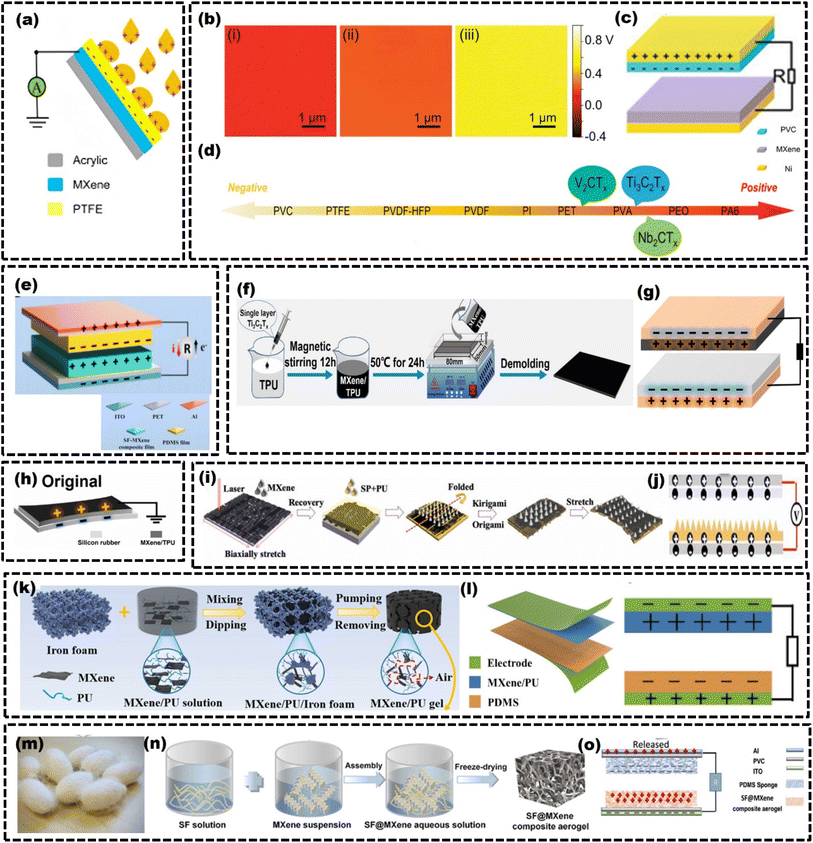 |
| Fig. 12 MXene as a positive tribolayer in TENG. (a) Schematic diagram of water droplets splashing on a single-electrode TENG. Reprinted with permission from ref. 46. © 2021, Elsevier. (b) Kelvin probe force microscopic images of MXenes. (i) V2CTx, (ii) Ti3C2Tx and (iii) Nb2CTx. (c) Schematic representation of the MXene/PVA composite TENGs. (d) Transformed triboelectric sequence of materials of the V2CTx, Ti3C2Tx, and Nb2CTx MXenes. Reprinted with permission from ref. 173. © 2024, John Wiley & Sons. (e) Schematic diagram of the MXene/silk fibroin composite-based TENG. Reprinted with permission from ref. 63. © 2024, American Chemical Society. (f) Preparation process of MXene/TPU composite film. Operating mechanism of TENG in (g) vertical contact-separation mode and (h) novel deformation mode. Reprinted with permission from ref. 127. © 2024, Elsevier. (i) Schematic diagram of kirigami spider fibroin-based microneedle patch. (j) TENG device design with kirigami spider fibroin-based microneedle patch. Reprinted with permission from ref. 61. © 2024, Elsevier. (k) Schematic illustration of the fabrication of 3D MXene/PU gel. (l) Architecture of TENG device in operation. Reprinted with permission from ref. 381. © 2024, American Chemical Society. (m) Optical image of a silkworm cocoon. (n) Fabrication procedure of 3D silk fibroin/MXene composite aerogel. (o) Fabricated TENG device with 3D silk fibroin/MXene composite aerogel as a positive triboelectric layer. Reprinted with permission from ref. 50. © 2023, American Chemical Society. | |
Recently, a 3D architecture biocompatible MXene Ti3C2Tx–silk fibroin composite as a positive triboelectric layer in TENG was proposed by Xueqiang Tan et al. The TENG was fabricated by assembling the vacuum-filtered MXene–silk fibroin composite (positive) and PDMS (negative) with ITO and Al as electrodes (Fig. 12(e)). This device was applied to detect insomnia and the quality of sleep for humans.63 Flexible sensors, particularly for the detection of significant deformation, require exceptional flexibility and stretchability. Consequently, the lack of stretchability in TENGs limits their use as self-powered sensors.362 A novel approach for increasing the flexibility of the TENG device by detaching the electrodes with Ti3C2Tx MXene/TPU as the positive tribolayer and silicon rubber as the negative tribolayer was unveiled by Jiacheng Fan et al. MXene/TPU was prepared using a mold-casting approach (Fig. 12(f)). This technique introduced a new mode in TENG known as the deformation mode. In deformation mode (Fig. 12(h)), MXene/TPU attached as the positive and silicone rubber as the negative triboelectric layers generated voltages based on stretching. However, the TENG device operated both in contact separation (Fig. 12(g)) and deformation mode.127 One of the most common causes of disability is joint injuries. Currently, their treatment focuses on oral medications and surgical procedures, which cause patients needless and serious problems. In this case, to achieve effective joint management, intelligent patches with stretchability and cognitive drug control-release capability are highly desirable.382,383 Drawing inspiration from kirigami structures, Shuhuan Li et al. created a novel TENG patch that can be applied for joint care. The kirigami-based MXene@spider fibroin patch was prepared by laser engraving on a stretched Ecoflex mold, followed by coating with a Ti3C2Tx MXene solution. Then, the prepared spider fibroin solution was added dropwise to the stretch-free mold (Fig. 12(i)). As shown in Fig. 12(j), the TENG device was fabricated by using the MXene composite as the positive and PTFE film as the negative triboelectric layer pasted with Cu foil on the top and bottom.61
The performance of MXene as a positive triboelectric layer in TENGs with their electrodes and pairing negative triboelectric layers, fabrication approaches, electrical parameters, and corresponding applications is presented in Table 5. Achieving enhanced sensitivity, a wide working range and exceptional stability is vital in pressure sensors and triboelectric nanogenerators.384 Thus, to achieve this, 3D conductive polymer composites with MXene/PU gel were prepared using an iron template approach. The 3D composite gel was prepared by mixing the Ti3C2Tx MXene and polyurethane solution and the solution was poured into a flask with the iron foam, followed by pressing until the gel was formed. Then, the 3D gel was immersed in an H2SO4 solution to remove the iron foam (Fig. 12(k)). The MXene/PU gel was washed to neutralize the pH value. The MXene/PU gel was used as the positive and PDMS as the negative triboelectric layer for the fabrication of a TENG device (Fig. 12(l)).381 The advancement of self-powered bioelectronics is aided by the rising demand for triboelectric layers composed of biocompatible and biodegradable materials for reuse and combining with biomedical electronics.385
Table 5 A brief outline of MXenes as positive triboelectric layers in TENGs
Electrode |
Triboelectric layers |
Fabrication approach |
Mode |
Voltage |
Current |
Power or power density |
Stability (cycles) |
Application |
References |
Al-positive |
TP-Ti3C2Tx/silk fibroin, TN-PDMS |
Vacuum filtration |
CS |
418 V |
11.6 μA |
9.92 W m2 |
— |
Detecting insomnia and quality of sleep |
63
|
ITO-negative |
No electrode |
TP-Ti3C2Tx/TPU |
Mold casting |
Deformation |
7.1 V |
— |
— |
— |
Detecting human motions |
127
|
TN-silicone rubber |
Copper foils |
TP-Ti3C2Tx/spider fibroin, TN-PTFE |
Laser engraving & mold casting |
CS |
4 V |
— |
— |
26 |
Joint treatment |
61
|
Copper foils |
TP-Ti3C2Tx/PU |
Iron foam template technique |
CS |
8 V |
31 nA |
— |
7800 |
Human step frequency monitoring |
381
|
TN-PDMS |
Al-positive |
TP-Ti3C2Tx/silk fibroin, TN-PDMS |
Freeze-drying |
CS |
545 V |
16.13 μA |
13.25 W m2 |
— |
Detecting asthma symptoms |
50
|
ITO-negative |
Copper tapes |
TP-Ti3C2Tx/gel/sodium lignosulphonate TN-PDMS |
Scalable one-pot |
CS |
230 V |
28 μA |
2.9 W m−2 |
1000 |
EMI shielding and sensing human motions |
386
|
A Ti3C2Tx MXene–silk fibroin aerogel-based biocompatible TENG was proposed for monitoring the respiratory rate of humans. The silk fibroin was extracted from the natural silkworm cocoons (Fig. 12(m)). The composite was prepared by intercalating the silk fibroin into the MXene sheets, resulting in the formation of a 3D bionic configuration. Then, the 3D MXene@silk fibroin was freeze-dried to form an aerogel (Fig. 12(n)). As shown in Fig. 12(o), using the aerogel as the positive tribolayer and the PDMS sponge as the negative tribolayer with Al and ITO as electrodes, a TENG is fabricated.50
To develop superior triboelectric materials for TENGs with improved performances, MXenes have been blended with other materials such as poly(vinyl alcohol) (PVA), PDMS, Ecoflex (silicone rubber), PTFE, PVDF, poly(3,4-ethylenedioxythiophene):poly (styrenesulfonate) (PEDOT:PSS), and poly(lactic acid).329 Two recent studies have shown that Ti3C2Tx films are more triboelectrically negative than PTFE,182 even when they are used as the triboelectric layer in TENGs. The second study showed that Ti3C2Tx films are more positive than PTFE.46 Subsequent investigation showed that the triboelectric characteristics of MXenes are strongly influenced by their synthesis techniques, etchants, intercalating chemicals, and processes.173 Similar to fluorine in FEP, the fluorine atoms on the MXene flakes at or just below the contact surface are probably responsible for removing electrons from the tribopositive material.317 In contrast to their typical application as tribonegative electrodes or fillers in TENGs, it can be deduced that these MXenes can act as both tribopositive and tribonegative materials.
5.4. MXene as an electron acceptor (negative) tribolayer
MXenes are potential negative triboelectric materials due to the presence of negative surface terminations –OH and –F. According to reports, MXenes are more electronegative compared to PTFE.387 In TENGs based on MXenes, their open-circuit voltage is often high owing to the strong electronegativity of MXenes, which attract electrons during triboelectrification processes. Thus, researchers have embedded or composited MXenes with polymers to enhance TENG performance. Dielectric permittivity and percolation are two impacts of MXenes in polymer films that must be balanced by the MXene proportion to achieve the optimal performance.34,167 MXene (Ti3C2Tx) as a negative friction layer was first incorporated in TENG in 2019. To enhance the flexibility, the MXene was mixed with the PVA to create nanofibers through electrospinning (Fig. 13(a)). Silk fibroin nanofiber was used as the positive friction layer. With Al foils as electrodes, a TENG was fabricated with the prepared positive and negative friction layers (Fig. 13(b)).48
 |
| Fig. 13 MXene as a negative tribolayer in TENG. (a) Preparation process of MXene/PVA nanofibers. (b) TENG device structure with MXene/PVA nanofibers. Reprinted with permission from ref. 48. © 2019, Elsevier. 3D Graphical illustration of (c) the preparation process of MXene/SRP composite through hot pressing and (d) TENG device structure with MXene/SRP composite. Reprinted with permission from ref. 53. © 2024, John Wiley & Sons. (e) Preparation process of the MXene/MWCNT/Ecoflex composite film. (f) Schematic of TENG with MXene/MWCNT/Ecoflex operating in single-electrode mode. Reprinted with permission from ref. 390. © 2025, Elsevier. (g) 3D design of the TENG device in spring design. (h) Digital image of the fabricated TENG in spring design. (i) Working structure of TENG device with MXene/PVDF composite. Reprinted with permission from ref. 391. © 2024, American Chemical Society. (j) Schematic of TENG device with MXene/PVDF-HFP nanofibers. Reprinted with permission from ref. 392. © 2024, Elsevier. (k) Peony flower for surface modification of triboelectric layer. (l) Process of preparing the surface-modified MXene/PDMS film. (m) Schematic of TENG device assembly with gelatin and MXene/PDMS films. Reprinted with permission from ref. 393. © 2024, Springer Nature. | |
After this, numerous approaches such as hydrogels, aerogels, and 3D networks were proposed employing MXenes with different polymers (PDMS, PTFE, PVDF, etc.). Fluorine has the highest electron negativity in the Periodic Table, meaning that fluoropolymers can effectively remove electrons from other materials to produce a large negative surface charge density. Nevertheless, fluoropolymers cause considerable environmental damage by leaking poly-fluoroalkyl compounds into the surroundings, leading to serious medical conditions.388,389
Thus, to alleviate this environmental issue, a sulfur-based polymer with minimal MXene (Ti3C2Tx) as a filler was used to fabricate a green and sustainable TENG. The composite was prepared by immersing the sulfur-based polymer (SRP) powder into an MXene solution under mechanical stirring. After drying, the MXene-coated SRP powder was hot-pressed with Al foil on one side (Fig. 13(c)). On the other end, Al foil was thermally coated on the substrate as a conductor and positive friction layer and assembled to create a TENG (Fig. 13(d)).53 The distinctive benefits of noncontact human–machine interfaces (HMI) of high accuracy, rigidity, and hygiene have recently attracted increasing attention. These advantages hold considerable potential for smart robots and augmented or virtual medical facilities.394,395 A novel TENG was developed using MWCNT and MXene (Ti3C2Tx) as a filler in an Ecoflex dielectric to generate an electrical signal without contact for wireless robots. The negative friction layer was prepared by blending the MXene and MWCNT into the Ecoflex solution and streamed into a glass, followed by curing in an oven (Fig. 13(e)). The array-based TENG was constructed using 8 × 8 composite matrices adhered to acrylic substrates and Cu as electrodes (Fig. 13(f)).390 MXenes, in particular, Ti3C2Tx have been the focus of much research on TENGs due to their remarkable electrical conductivity. Reports suggest that the niobium carbide (Nb2CTx) MXene possesses enhanced electrical conductivity and large surface area compared to Ti3C2Tx, but reports on its use in TENG is not common.396 Yang Tao et al. fabricated a TENG device using an Nb2CTx MXene and PVDF composite as the negative friction layer. Multiple Al electrodes were laminated in 3D to fabricate the device as a spring assembly, as shown in Fig. 13(g). The composite was prepared by pouring PVDF solution on a glass substrate and drying in an oven, and then an Nb2CTx solution was sprayed on the surface of PVDF using a spray gun. A photograph of the device is shown in Fig. 13(h). The TENG possessed 16 components for generating electricity, with polypropylene and Nb2CTx/PVDF as the positive and negative friction layers (Fig. 13(i)).391 To enhance the dielectric constant and reduce charge loss, Omar Faruk et al. incorporated the V2CTx MXene into poly(vinylidene-fluoride-co-hexafluoropropylene) (PVDF-HFP) to create nanofibers as the negative friction layer in TENGs. PEO nanofibers were used as the positive friction layer in TENG with fabric as the electrodes (Fig. 13(j)). Both the MXene/PVDF-HFP and PEO nanofibers were prepared through electrospinning.392 The development of TENG technology greatly benefits from the usage of eco-friendly friction materials.397 Zekun Wang et al. proposed a TENG device with MXene/PDMS and gelatin as the negative and positive friction layers, respectively, and Cu foil as electrodes (Fig. 13(m)). Both friction layers were surface-modified using peony petals (Fig. 13(k)) as the substrate (Fig. 13(l)). In addition to its exceptional electrical performance, gelatin is a green and eco-friendly material.393 For biosensing and antimicrobial activity, the TENG device requires the side that comes into touch with the human skin to be hydrophilic to absorb sweat. Additionally, for better self-cleaning and longer use, the exterior surface should be hydrophobic.398,399 Shanguo Zhang et al. proposed a TENG device based on bilayer MXene Ti3C2Tx composites for antibacterial activity and avoiding bacterial septicity. The negative friction bilayer was prepared by casting MXene/Ag/PVDF/cellulose acetate as the bottom layer, followed by casting the MXene/PVDF top layer on an Al plate (Fig. 14(a)). Nylon was used as the positive friction layer and conductive tape as the electrode (Fig. 14(b)). The top layer enhanced the performance of the TENG, while the bottom layer exhibited a competent shield against E. coli and S. aureus bacteria.400 The performance of MXene as a negative triboelectric layer in TENGs with their electrodes and pairing positive triboelectric layer, fabrication approaches, electrical parameters, and corresponding applications is presented in Table 6.
 |
| Fig. 14 MXene as a negative tribolayer in TENG. (a) Schematic of the preparation of MXene/Ag/PVDF/cellulose acetate composite. (b) Schematic illustration of TENG device with MXene/Ag/PVDF/cellulose acetate composite. Reprinted with permission from ref. 400. © 2024, Elsevier. (c) 3D illustration of the TENG device. (d) Schematic of TENG device with bilayer MXene/silicone composite. Reprinted with permission from ref. 401. © 2024, Elsevier. (e) Schematic of the preparation of alternating ABAB-layered MXene composite. (f) Structure of TENG device with alternating ABAB-layered MXene composite. Reprinted with permission from ref. 380. © 2021, Springer Nature. (g) Schematic of TENG device with MXene/Ecoflex composite. Reprinted with permission from ref. 404. © 2025, Springer Nature. (h) Schematic of MXene/Ecoflex composite with pyramid structure attached to fabric. (i) Photograph of the composite with a pyramid structure. (j) Schematic of the toroidal TENG device. Reprinted with permission from ref. 52. © 2023, Elsevier. (k) Unique intercalation strategy of MXene with modified silica nanospheres. Reprinted with permission from ref. 315. © 2024, John Wiley & Sons. | |
Table 6 A brief outline of MXenes as negative triboelectric layers in TENGs
Electrode |
Triboelectric layers |
Fabrication approach |
Mode |
Voltage |
Current |
Power or power density |
Stability (cycles) |
Application |
References |
Al foils |
TN-Ti3C2Tx/PVA |
Electrospinning |
CS |
117.7 V |
— |
1087.6 mW m−2 |
124 000 |
Power electrowetting on a dielectric device |
48
|
TP-silk fibroin |
Al foils |
TN-Ti3C2Tx/SRP |
Hot-pressing |
CS |
1717.7 V |
129 μA |
3.80 W m−2 |
7200 |
Power commercial electronics |
53
|
TP-Al foil |
Al foils |
TN-Nb2CTx/PVDF |
Spraying |
CS |
420 V |
33.45 μA |
619 mW m−2 |
— |
Water level monitoring |
391
|
TP-polypropylene |
Conductive fabric |
TN-V2CTx/PVDF-HFP, TP-PEO |
Electrospinning |
CS |
1240 V |
119 μA |
18.20 W m−2 |
15 000 |
Human activity and posture monitoring |
392
|
Copper foils |
TN-Ti3C2Tx/PDMS |
Drop-casting |
CS |
417.39 V |
12.01 μA |
170 μW cm−2 |
10 000 |
Foot status monitoring |
393
|
TP-gelatin |
Conductive tape |
TN (bilayer)-top-Ti3C2Tx/PVDF, bottom-Ti3C2Tx/Ag/PVDF/cellulose acetate |
Combined crystallization and diffusion |
SE |
1236 V |
70 μA |
18.55 W m−2 |
400 000 |
Protect against bacterial infections |
400
|
TP-nylon |
Copper foils |
TN (bilayer)-top-silicone, Bottom-Ti3C2Tx/silicone |
3D printed template |
CS |
1160 V |
— |
— |
1500 |
Ethanol sensing and alarm |
401
|
Al foils |
TN-Ti3C2Tx/CeO2/CNF, TP-silicone |
Electrospinning |
CS |
160 V |
— |
3485 mW m−2 |
16 000 |
Ammonia and biomarker detection |
402
|
Al foils |
TN-Ti3C2Tx/PVC |
Electrospinning |
CS |
51 V |
29.79 μA |
4.94 mW cm−2 |
1600 |
Human motion monitoring |
403
|
TP-Al foil |
Copper foils |
TN-Nb2CTx/Ti3C2Tx |
Vacuum filtration |
CS |
34.63 V |
8.06 μA |
100 μW cm−2 |
— |
Harvest energy from human motions |
380
|
TP-Nylon |
Cu–Ni polyester |
TN-Ti3C2Tx/Ecoflex |
Roll-casting |
CS |
350 V |
42 μA |
7.8 W m−2 |
— |
Energy storage |
404
|
TP-PDMS |
Conductive fabric |
TN-Ti3C2Tx/Ecoflex |
3D printed template |
SE |
19.91 V |
1.15 μA |
— |
50 000 |
Smart glove |
52
|
TP-human skin |
Al |
TN-Ti3C2Tx/modified silica nanospheres/PDMS TP-Al |
Mold casting |
CS |
461 V |
16 μA |
691.1 μW cm−2 |
>2800 |
Energy harvesting |
315
|
Copper |
TN (bilayer)-top-PDMS, bottom-Ti3C2Tx/PDMS |
Spin coating |
SE |
2016 V |
86 μA |
11.27 m W |
30 000 |
Volleyball training monitoring |
405
|
TP-Nylon |
Al |
TN-Ti3C2Tx/PVDF |
Electrospinning |
CS |
305 V |
10.6 μA |
10.91 Wm−2 |
10 000 |
Smart home |
406
|
TP-ZIF-67/PAN |
Although TENG is a powerful energy harvesting technique, it still has the drawback of poor output performance when used to create a self-powered sensing system.407 Thus, to mitigate the issue of charge dissipation in the dielectric layers with ease, a TENG device with negative dual dielectric layers was proposed by Shasha He et al. The dual dielectric layers of silicone rubber (top) and MXene (Ti3C2Tx)/silicone composite (bottom) were prepared by 3D mold casting. As shown in Fig. 14(c), employing the dual layer as the negative and nylon as the positive friction layers with copper foil as the electrodes and Kapton as substrate, a TENG was constructed and the device operated in CS mode (Fig. 14(d)).401
The agglomeration of MXenes limits the access of their –F group to nanochannels, which impairs their performance. Ti3C2Tx MXene nanosheets with a porous framework and interlayer spacing were demonstrated to fully exploit their electrochemical characteristics. The output performance of TENG has also been greatly enhanced by the addition of interlayer spacers to MXene.408,409 This layer-stacked configuration was developed to construct alternate-layered MXene films with rich –F groups and a homogeneous intrinsic microstructure. An alternating-layered composite (negative friction layer) was prepared by assembling delaminated Ti3C2Tx and Nb2CTx MXenes in an ABAB configuration via the vacuum-filtration technique (Fig. 14(e)). Adopting nylon as the positive friction layer and Nb2CTx/Ti3C2Tx as the negative friction layer with copper electrodes, a TENG device was fabricated (Fig. 14(f)).380 Determining the percolation level of MXenes is critical in attaining a stable dielectric constant for the smooth operation of TENG.410 A TENG device with a Ti3C2Tx MXene/Ecoflex composite as the negative friction layer was prepared to determine the dielectric constant of the composite. The MXene fillers enhanced the dielectric constant of Ecoflex to 19.5 from 11.2, which started to decrease when the content of MXene exceeded 3 wt%. As shown in Fig. 14(g), applying MXene/Ecoflex as the negative and PDMS as the positive friction layers, together with a Cu–Ni polyester electrode, a TENG device was fabricated.404 Even with the advancements, the field of gesture sensors can still be improved. This is because gesture sensors are invariably made smaller to fit comfortably in the finger; however, this results in a poor triboelectric output due to the size and the CS mode operation.411,412 Considering these problems and difficulties, a triboelectric toroidal device with a pyramid surface MXene/Ecoflex composite was proposed. The composite was prepared by casting an MXene/Ecoflex suspension into a 3D mold and fixing with conductive fabric. After curing, the composite was peeled off from the mold (Fig. 14(h)). A photograph of the prepared composite with a pyramid surface is shown in Fig. 14(i). A glove was fabricated by 3D printing all the components separately and assembled with copper wire connections. The TENG device (Fig. 14(j)) with MXene/Ecoflex as the negative friction layer with fabric electrode operated in SE mode.52 Despite its unique potential, MXene still has significant problems with restacking and charge blockage because of the van der Waals interaction, which makes it difficult to restrict charge transport paths. Body-penetrated charges have a high chance of recombining with opposing charges that are induced on the triboelectric electrodes.413,414 Intercalating the Ti3C2Tx MXene with altered silica nanospheres was proposed as an effective solution to the above-mentioned drawback. The modified silica nanospheres were synthesized using disposed bagasse ash from a sugar factory. The silica nanospheres were intercalated into the MXene nanosheets by mixing in water, under stirring for 2 h and the nanosheets were intercalated with silica nanospheres through hydrogen bonding and electrostatic interaction (Fig. 14(k)). Then, the resultant composite was mixed with PDMS in different concentrations, which was applied as the negative friction layer in a TENG paired with Al as the top electrode as well as tribopositive material.315 To retain the surface charges, given that a portion of the surface charges is lost during the triboelectrification process,415 a dual-layer negative friction material comprised of a sodium niobate/PDMS composite at the bottom and Ti3C2Tx MXene/PVDF composite at the top was proposed. The performance of TENG devices is greatly enhanced by this method given that it produces noticeably larger surface charges and prolongs their retention.416
As an electron acceptor material with superior triboelectric qualities, PTFE has been recognized in numerous series presented to date, which explains its widespread use in TENG applications.417,418 Research conducted in 2017 revealed that MXene behaves similarly to PTFE while resolving some of the issues with the use of PTFE, such as low conductivity.182 The combination of high electrical output, mechanical toughness, and long-term stability provided by the incorporation of MXenes as negative triboelectric layers in TENGs makes them potential materials for sophisticated energy harvesting applications.
6. MXene TENGs in action: real-time applications
6.1. Biomedical wearables
Over the past 30 years, biomedical devices have been crucial in enhancing healthcare outcomes; however, their continuous and active biomedical sensing function in daily life has been hindered by wearability constraints and limited power source access. In this case, triboelectric nanogenerators have been proven to be incredibly versatile and capable of producing wear-optimized and self-powered biomedical sensors.419,420
6.1.1. Wound healing.
The skin is a diversified microbial habitat and the body's main barrier against external touch. Accordingly, if electronic equipment is not bactericidal, it may introduce bacteria and viruses when it comes into close contact with the skin.421 Thus, the antimicrobial attributes of the bilayer triboelectric MXene/Ag/PVDF/cellulose (bottom)-MXene/PVDF layer (top) layer, PVDF/cellulose acetate, and bilayer without Ag were examined against bacteria (E. coli and S. aureus). The findings (Fig. 15(a)) indicate that the bilayer without PVDF eliminated limited bacteria, while the bilayer with PVDF completely eliminated the bacteria. By the eighth hour, neither the E. coli nor S. aureus colonies could be identified on the agar plates given that their numbers drastically declined over time (Fig. 15(b)). Microscopy images confirmed (Fig. 15(c)) that when the bilayer composite was applied to the skin on the back of a mouse for 24 h, its skin remained healthy, demonstrating the great safety and biocompatibility of the tribolayer.400 The difference in trans-epithelial potential (TEP) between the injured area and healthy skin typically promotes wound healing. To aid the healing process, the endogenous TEP produces an electric current when a wound arises, which pushes the charged Na+ and Cl− ions toward the center of the injured area. Alternatively, a poor TEP lengthens the healing period for chronic wounds.422,423 As shown in Fig. 15(d), styrene-butadiene-styrene-coated silver nanoparticle nanofibers were used to deliver induced energy to the injured location, and a TENG was made using a PET substrate, which allowed free tapping on the rat skin when it moved. The TENG was directly mounted on the injured rats in an in vivo experiment, with its AC and DC electrical performance analyzed (Fig. 15(e)) to demonstrate this. During AC and DC simulations, the positive and negative charges were transferred to the wounded area. As illustrated in Fig. 15(f), on days 3, 7, 10, and 14, pictures were taken to track the condition of the wound. The rats in the control sample were not given any treatment. The electrode was patched to contact the wound edges, allowing symmetrical wound recovery. On day 14, the reported wound closure ratio had already surpassed 95% (Fig. 15(g)).55
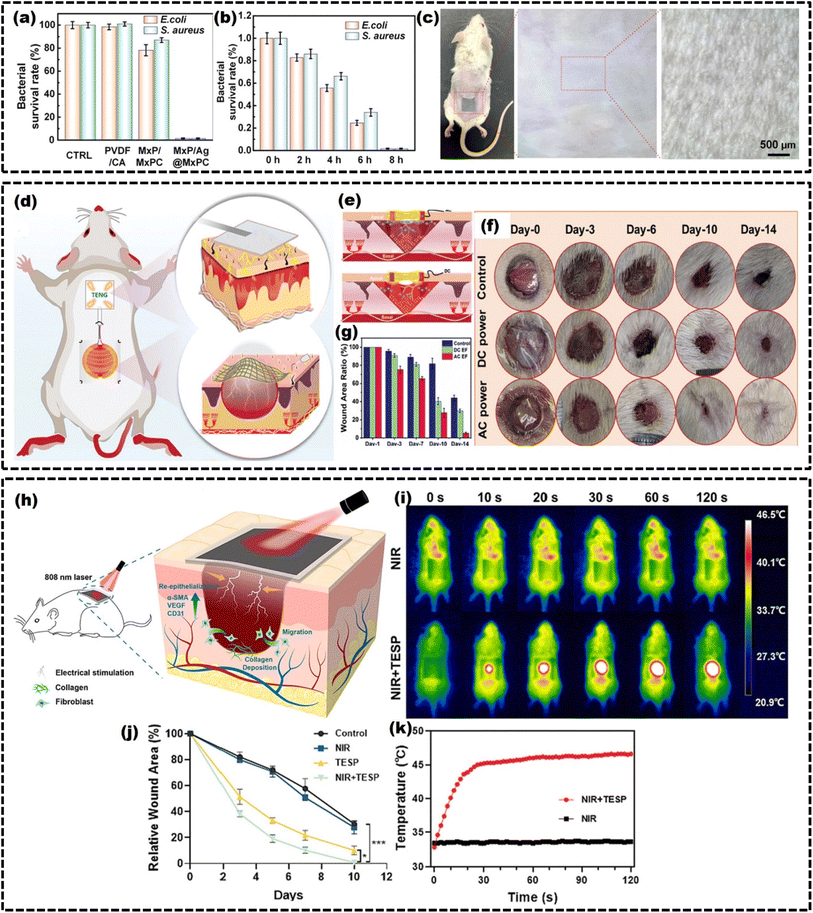 |
| Fig. 15 MXene TENG for wound healing. (a) Comparison of E. coli and S. aureus bacterial survival rates with different composites. (b) Survival rates of bacteria at different time intervals. (c) Photograph and microscopy images of the rat skin after 24-hour implantation of bilayer MXene composite. Reprinted with permission from ref. 400. © 2024, Elsevier. (d) Schematic representation of the electrical stimulation of TENG during the healing process of wounds. (e) Illustration showing the procedure of the AC and DC electrical stimulation on the injured area. (f) Rat wound skin photos were taken at different time points. (g) Recovery rate of the wound following 3, 7, 10, and 14 days of therapy. Reprinted with permission from ref. 55. © 2024, John Wiley and Sons. (h) Schematic illustration of wound healing with MXene TENG electronic skin patch that responds to NIR light. (i) Thermal images showing temperature variations in mice treated with or without a TENG patch following a 120 s exposure to NIR light. (j) Recovery rates of wound healing with multiple groups of therapy. (k) Photothermal heating curves of wounds both with and without TENG skin patch. Reprinted with permission from ref. 341. © 2024, Elsevier. | |
Furthermore, photothermal techniques can effectively speed up wound healing by producing heat. By transforming light into thermal energy, photothermal materials heat the wound site locally, promoting cellular metabolism and preventing the growth of microorganisms.424,425 A single-electrode TENG as a skin patch was proposed based on an MXene/gelatin photothermal hydrogel. The hydrogel was directly applied to a rat epidermal wound and served as an electrode. To facilitate wound healing, the TENG device gathered biophysical energy, created an electric field surrounding the injured tissues, and worked in tandem with the near-infrared photothermal effect (Fig. 15(h)). The temperature barely rose when near-infrared light was applied to the wound; however, when the TENG patch with NIR was applied, the temperature increased from 32 °C to 45 °C in just two minutes (Fig. 15(i and j)). This showed that the key to converting light energy into thermal energy in TENG is the photothermal property of MXene. After ten days, it was evident that the TENG device treatment with near-infrared light had the greatest healing impact among the groups (Fig. 15(k)).341 Incorporating MXenes into TENG enhances wound healing, utilizing both electrical stimulation and photothermal heating.
6.1.2. Health diagnostics.
An essential component of the human knee joint that keeps it stable is the anterior cruciate ligament (ACL). Using wearable technology to check for early ACL injuries lowers the risk of long-term consequences and allows prompt intervention.426,427 An MXene/PVDF-HFP-based TENG integrated with peripheral devices was proposed to diagnose early ACL injuries in mobile applications, as presented in Fig. 16(a). The peripheral device was comprised of a hardware component (filters and microcontroller) and a signal process unit, as shown in Fig. 16(b). The TENG device was positioned on the front part of the patient's wounded leg to confirm the injury. Then, the output voltage of the TENG was measured using an Anterior Drawer Test (ADT). After that, the same test was conducted with the TENG in the same location on the patient's normal leg. The comparison of signals denoted that the output voltage of the injured leg was higher than the normal leg (Fig. 16(c)). Based on the confusion matrix results, the TENG device exhibited 100% accuracy in detecting ACL injuries.56 One common sleep problem that has a significant detrimental impact on daily functioning, sleep quality, and mental and physical health is insomnia disorder.428 A TENG-based eye mask was proposed to identify the signs of insomnia and track sleep quality in real-time. Using MXene–silk fibroin and PDMS as the positive and negative friction layers, with ITO and Al electrodes, a TENG device was tightly sealed into an economical eye mask (Fig. 16(d)). As illustrated in Fig. 16(e), the TENG device offered wired and wireless (gadgets) sensing of the quality of the human sleep pattern. Based on the electroencephalography (EEG)429 technique of frequency bands, the sleep pattern of a healthy individual and insomnia patient was recorded. When recording the electrical impulses of the normal individual, the δ (0.5–4 Hz, deep sleep) wave generated an output voltage of 108 mV and the θ (4–8 Hz, entire sleep) wave produced a significant voltage of 196 mV (Fig. 16(f)). No δ wave was visible when recording the signals of the insomnia patients; only the α (8–3 Hz, half-sleep) wave generated a voltage of 76 mV and the θ wave was present (Fig. 16(g)). By comparing the frequencies of both signals, it was evident that the normal person attained deeper sleep, while the insomnia patient exhibited a disturbed sleep pattern.63 Nowadays, the main focus of joint management is using medication and surgery to slow the progression of this condition. However, regular drug use has the danger of causing acute renal impairment and gastrointestinal system damage, and injections may cause edema.430,431 These problems were addressed by the proposal of a TENG drug delivery system and microneedle patches based on kirigami spider fibroin. Employing kirigami structured-MXene/spider fibroin microneedles and PTFE as the positive and negative triboelectric layers, respectively, with copper electrodes, a TENG was fabricated (Fig. 16(h)). To assess the capacity of the TENG patch to speed up the joint treatment, 0.1 mL of drug was injected into various rats and compared with the paw thickness of the untreated rat. The microneedle-TENG-treated rat had the best healing efficacy because electrical stimulation accelerated medication release, and after six days, paw swelling virtually vanished. This indicates that the reported microneedle-TENG can be used in joint treatment.61
 |
| Fig. 16 MXene TENG for health diagnostics. (a) Schematic of TENG device for ligament injury diagnosis in mobile application. (b) Hardware assembly of the diagnosis system. (c) TENG device fixed on a volunteer to diagnose ligament injury. Reprinted with permission from ref. 56. © 2024, Elsevier. (d) Optical image of a portable MXene TENG mask for the eyes. (e) Schematic illustration of the MXene TENG mask for detecting the status of human sleep. TENG mask's output circuit voltage (Voc). (f) Detection of normal sleep patterns. (g) Detection of insomnia signs. Reprinted with permission from ref. 63. © 2024, American Chemical Society. (h) Joint treatment through spider-fibroin microneedle-based TENG patch. Reprinted with permission from ref. 61. © 2024, Elsevier. | |
An important metric for assessing the physiological well-being of the human body is the blood glucose level. However, the development of viable glucose sensors for diabetes patients is hampered by the unreliability of enzymatic glucose biosensors.432 In this case, an MXene/GO-based TENG was fabricated to detect glucose levels without the support of glucose enzymes. Common and significant chemicals, such as glucose and Na+, were examined to assess the MXene/GO TENG biosensor potential. The TENG was shielded before the analysis to prevent contamination and 0.1 mL of glucose solution was dropped on its electrode. The output voltage of the TENG with multiple glucose concentrations was recorded and the output voltage developed to 426 V for 500 μmol concentration. Thus, this MXene/GO electrode in TENG opens the door for innovative biosensors and non-invasive health monitoring.288
6.1.3. Vital sign assessment and gait analysis.
In everyday life, the ongoing monitoring of vital signs can help detect patient decline early and make the transition to home care easier. In in-patient situations, wearable sensors for constant vital sign monitoring are frequently assessed utilizing patches, mattress sensors, or more comprehensive sensors worn on the arm.433,434 For monitoring vital signs, TENGs can function as active wearable sensors that provide real-time electrical signals without an external power source.418 An MXene (Ti3C2Tx)/PVC film was prepared through electrospinning and applied as a negative friction layer in a TENG for monitoring the respiratory rate, heart rate, and gait analysis pattern (Fig. 17(a)). The TENG was fastened to a face mask for respiratory monitoring (Fig. 17(b)). It generated recurring voltage signals that represent the respiratory rate of the user. The inset demonstrates the possibility of real-time breath monitoring, which presents additional details about the single breathing cycle. Fig. 17(c) shows the heartbeat tracking before and following exercise, with noticeably stronger signals following exercise because of the elevated cardiac activity. When analyzing the gait pattern (Fig. 17(d)), running produced signals with higher amplitudes because of the increased force and frequency of motion.403 The advancement of self-powered bioelectronics is supported by the rising demand for triboelectric layers composed of biocompatible and biodegradable materials for reuse and integrating with biomedical electronics.435 A TENG mask based on an MXene (Ti3C2Tx)/silk fibroin aerogel composite and PDMS sponge as the positive and negative friction layers, respectively, was proposed to detect the respiratory rate and asthma. Air permeability is crucial in fabricating TENG to integrate with fabrics and masks. Fig. 17(e) illustrates that the MXene/silk fibroin aerogel offers an air permeability of 389 mm s−1, which is greater than the disposable medical mask and lab coat. The entire porous TENG device was integrated within a disposable medical mask owing to its exceptional air permeability (Fig. 17(f)). Fig. 17(g) shows that the output voltage was 1.3 V at 0.2 Hz and 1.9 V at 1 Hz, confirming that the entire TENG device was frequency dependent. The output voltage frequency by the TENG (Fig. 17(h)) for normal breath was much less than the frequency of asthma-related breath. Despite the lack of noticeable changes in the output voltage, it is a trustworthy indicator for detecting asthma.50 Most battery-powered wearable sensors have a short lifespan, making them unsuitable for sustainable use. Thus, it is essential to develop wireless self-powered systems for monitoring vital signs.436 Employing MXene (Ti3C2Tx)/PMMA and PDMS as the positive and negative tribolayers, respectively, for wireless breath monitoring was proposed. A tiny chip, a TENG device, a lithium-ion battery, and a mobile application were integrated for wireless transmission. The TENG was fixed to the abdomen (Fig. 17(i)) to monitor the shallow and deep breathing patterns based on the frequency and amplitude of the signal (Fig. 17(j)).437 In wearable and implanted devices, photodetectors and photoplethysmography (PPG), a non-invasive technique for health monitoring, are essential for measuring vital signs.438
 |
| Fig. 17 MXene TENG for vital sign assessment and gait analysis. (a) MXene/PVC TENG for monitoring vital signs and gait pattern. (b) TENG device was adhered to a face mask to monitor the respiratory rate. (c) Monitoring of heartbeat before and after physical activity. (d) Monitoring of gait pattern. Reprinted with permission from ref. 403. © 2025, AIP Publishing. (e) Air permeability test of usual fabrics and fabricated TENG device. (f) Optical image of a face mask integrated with a TENG. (g) Output voltage of the TENG face mask at various breathing frequencies. (h) Output voltages of the TENG device detecting usual breathing patterns and asthma signs. Reprinted with permission from ref. 50. © 2023, American Chemical Society. (i) MXene/PMMA TENG device fixed on the abdomen of a human to detect breathing patterns. (j) Output voltage of the TENG monitoring breath rate. Reprinted with permission from ref. 437. © 2023, John Wiley & Sons. (k) A wristband comprising TENG, photodetector, and LED. (l) Current versus time graph revealing the heart rate. Reprinted with permission from ref. 58. © 2024, Elsevier. (m) TENG device attached to the front and back foot for gait analysis. (n) Output voltages in all directions during walking. (o) Output voltages in all directions during running. Reprinted with permission from ref. 393. © 2024, Springer Nature. (p) Output voltages of TENG based on MXene/PAM hydrogel for detecting walking and running. Reprinted with permission from ref. 348. © 2024, Elsevier. | |
An MoS2-based photodetector powered by an MXene (Ti3C2Tx)/PDMS TENG device was proposed to track the heart rate and UV illumination (Fig. 17(k)). The systolic and diastolic phases of the heart are represented by the current peaks in the I–t diagram caused by LED light (660 nm) reflected off the fingertip onto the active area of the photodetector. When tapping the TENG device at the frequency of 1 Hz, it charged the capacitor of 220 μF in less than 2 min. The photodetector received the DC voltage that is stored in the capacitor when the tapping stopped. As shown in Fig. 17(l), heartbeats were obtained in DC mode by plotting the current versus time of the photodetector.58 GAIT ability is a crucial component in assessing the quality of life of a person and reflects their status as a healthy individual. GAIT is a complicated, unrealized motor pattern that is essential to living, enabling people to function in the human world and engage in daily activities.439,440 A TENG device based on MXene (Ti3C2Tx)/PDMS and gelatin as the negative and positive friction layers, respectively, was fabricated simply and economically. Its surface was modified using a flower petal and only 0.03 wt% of MXene was added to PDMS. The TENG device was fixed on the front part and heel of the foot to record the gait pattern (Fig. 17(m)). The output voltage of the TENG device fixed on the front foot had 3 peaks, and the negative voltage was 40 V (Fig. 17(n)), which was higher than the negative voltage of the heel-fixed TENG. The positive voltage was 60 V in running from the heel-fixed TENG (Fig. 17(o)), which was higher than the forefoot TENG positive voltage. These variations in the voltage are due to the diverse movements of the foot.393 Similarly, a hydrogel based on MXene/PAM was applied in a TENG to monitor the walking and running of humans. To enhance the dispersibility of the MXene in the hydrogel, the MXene was oxidized to alter its nanostructure. The single-electrode TENG was attached to the foot sole to track human steps. The recorded voltage and number of peaks corresponding to walking were less than running, as illustrated in Fig. 17(p).348 As a result, MXene TENGs enhance the applicability of monitoring vital signs and gait patterns in real-time.
MXene TENGs have demonstrated great potential in biomedical applications such gait analysis, vital sign monitoring, wound healing, and health diagnostics because of their remarkable electrical conductivity, mechanical flexibility, and biocompatibility. Their antibacterial qualities and potential for medication delivery further improve the therapeutic efficacy, and their capacity to produce localized electrical stimulation and photothermal impacts speeds up tissue regeneration in wound healing.341,441 MXene TENGs provide self-powered, high-sensitivity physiological signal detection, such as breathing and pulse, for health diagnostics and vital sign assessment.440,442 Their versatile form factors allow continuous, wearable monitoring. Because of their tremendous electrical output, they offer precise, real-time motion monitoring in gait analysis.393 However, issues including long-term biocompatibility, mechanical durability, environmental stability, and the requirement for scalable production must be resolved.
6.2. Gas sensing
Gas sensors transform complicated ambient biochemical data into signal data, enabling the real-time quantitative monitoring of certain gaseous targets, including hazardous components. Due to the materials and design of sensors, the majority of detecting sensors on the market are expensive and power-hungry. Therefore, creating gas detectors with a detection limit that are affordable and readily available is essential for environmental monitoring.443,444 Self-powered gas sensors rely on energy harvesting techniques to produce electrical power for gas detection, allowing them to function without an external power source.445 Integrating gas sensors with TENGs to create a revolutionary self-powered gas sensing systems was suggested based on the “impedance matching effect”.446 MXenes are becoming progressively known as exciting materials in the field of gas sensing because of their excellent ion-transmission properties and wide range of surface functional group modifications.447 A TENG device incorporating a dual-layer tungsten trioxide (WO3)/MXene–carbon quantum dots as the negative friction layer was fabricated to detect triethylamine for tracking rotten fish meat. As shown in Fig. 18(a), the response of the MXene/WO3–carbon quantum dots increased when the concentration of triethylamine increased, exhibiting the maximum response of 53%. The response rate of triethylamine with other gases is shown in Fig. 18(b). The output voltages of the fish meat followed different decay durations, and through time, the output voltage increased (Fig. 18(c)). This denotes that triethylamine reacts with the composite, exhibiting high sensitivity.448 Ammonia (NH3) monitoring is a reliable indicator of dangerous gas leaks or formation during fires because unlike the more common gases such as CO2, NH3 is not usually found in everyday situations.449 A self-powered gas sensor based on MXene/MoS2/cellulose diacetate/tetraethyl orthosilicate and (PVDF HFP)/BaTiO3 as the negative and positive friction layers, respectively, was fabricated to sense ammonia (Fig. 18(d)). The response and recovery time of the TENG for NH3 (86.1%) was 2 s and 3 s at the rate of 10 ppm, respectively (Fig. 18(e)). Through FTIR analysis, the NH3 gas was sensed, which was intentionally leaked by burning hair (Fig. 18(f)). The TENG device responded 28 s earlier than other NH3 detectors.62 Gaseous pollutants such as sulfur dioxide (SO2), nitrogen dioxide (NO2), and ammonia (NH3) are aggravating the problem of chemical gas pollution, which has become one of the main causes of disease and death. Although MXene improves gas sensor responsiveness, cross-sensitivity is still a problem when using these sensors to detect multi-component chemical gases.450,451 A multi-gas sensing array powered by a TENG integrated with a convolution neural network-gated recurrent unit neural network mode was proposed to detect the composition and forecast the concentration of 3 chemical gases (Fig. 18(g)). The TENG was driven by the wind. The effective identification of the composition of NH3–SO2–NO2 chemical gas mixtures and concentration prediction offer a general approach for more intricate multi-component gas mixture detection.372 In vegetable greenhouses, small quantities of ammonia (NH3) generated during the breakdown of organic fertilizers, urea, and ammonium bicarbonate may reach plants through their stomata, burning their tender shoots, and even causing the entire plant to perish.452,453 An Nb2AlC/Ta2O5 composite-based sensor powered by a wind-driven TENG was proposed to detect trace NH3 in greenhouses. The reported sensor could detect the presence and concentration of NH3 with alarms. This paves the way for modern agriculture.454 Regular inspection of fruit and vegetable storage warehouses is necessary to prevent the degradation of fruits and vegetables. Excessive ethanol accumulation can cause deterioration in quality, faster aging, unpleasant flavours, and a major decrease in storability.455,456 A TiO2/CuO/MXene-based sensor driven by a TENG for ethanol detection in warehouses was reported. The assembled ethanol sensor can be mounted on a moving inspection robot, and the TENG is anticipated to capture the mechanical energy produced by the robot. The electrical output of the TENG array is stored in a management circuit, which serves as the operational power source of the sensor for the ethanol concentration warning and online warehouse ethanol level monitoring.401
 |
| Fig. 18 MXene TENG for gas sensing and sports monitoring. (a) Response rate of triethylamine sensing (different concentrations) using self-powered TENG-based on MXene/carbon quantum dots/WO3 composite. (b) Selectivity test of the TENG sensor for multiple gases. (c) Optical image and voltage signal of 30 g of fish meat deteriorating after various storage times. Reprinted with permission from ref. 448. © 2025, American Chemical Society. (d) Release of ammonia gas from the environment harms human health. (e) Response and recovery time of the TENG device for multiple NH3 concentrations. (f) FTIR spectrum of burnt hair (releases ammonia). Reprinted with permission from ref. 62. © 2024, Elsevier. (g) TENG array driven by wind powering the gas sensor array for detecting multiple elements of gases. Reprinted with permission from ref. 372. © 2024, Elsevier. (h) MXene composite-based TENG was fixed at the different parts of the human body for scientific basketball training. (i) Output voltages of the TENG device when lifting the arm and jumping. Reprinted with permission from ref. 457. © 2024, AIP Publishing. (j) Bilayer MXene/PDMS TENG was fixed at different parts of the body to assist volleyball training. (k) Output voltages of the TENG device when bending the wrist and knee during play. Reprinted with permission from ref. 405. © 2024, Elsevier. (l) Schematic of a boxer throwing punches at the target. (m) Optical image of the MXene/PDMS TENG for monitoring boxing movements. (n) Output voltages of the TENG for straight fist and hook fist punches. Reprinted with permission from ref. 57. © 2024, AIP Publishing. (o) MXene/PI-based TENG was attached to a tennis bat to track batting activities. (p) Current signals of the TENG during the table tennis practice. Reprinted with permission from ref. 458. © 2025, AIP Publishing. | |
TENGs based on MXene have shown great promise for self-powered gas sensing applications because of their distinct electrical and structural characteristics. In gas detection applications, the 2D structure of MXenes improves the sensitivity by facilitating improved contact with gas molecules.363,459 The selectivity of sensors can be improved by customizing the surface functional groups of MXenes to interact with particular gas molecules.447 When incorporated in TENGs, MXenes help create completely self-powered devices that do not require external power, which makes them perfect for wearable technology or remote environmental monitoring.453,454 Their mechanical adaptability also facilitates their incorporation into stretchable and flexible systems.444 However, there are still issues that must be resolved for dependable long-term use, namely fabrication scalability, surface area reduction from sheet aggregation, and environmental instability caused by oxidation.
6.3. Sports monitoring
In sports, wearable technology has emerged as a crucial instrument that is transforming how athletes prepare, perform, and rehabilitate. These electronic devices offer real-time data on important performance indicators including heart rate, pace, distance, and muscle activity. They range from smartwatches and fitness trackers to sophisticated sensors built into clothes.460,461 Basketball stands out among the various sports as a very competitive sport where the focus is on winning and losing. Thus, the development of an athlete's competitive skills is necessary to win basketball games.462 Scientific training is the foundation for all these criteria, and a crucial part of scientific training is scientific training monitoring.463 An N-isopropylacrylamide/PDA/MXene hydrogel-based TENG was fabricated to monitor the posture of a basketballer. The device was attached to the elbows and joints of the volunteer to monitor human motions such as arm lifting and jumping (Fig. 18(h)). It was demonstrated through lifting and jumping that the TENG could distinguish between different pressure levels. The corresponding output voltages of arm lifting and jumping were 8.9 V and 17.16 V, respectively (Fig. 18(i)). Thus, the TENG device can monitor diverse human motion in sports.457 Similarly, a TENG device based on dual-layer PDMS–MXene/PDMS was reported for monitoring volleyball guidance. Monitoring different body joints is crucial to aiding training because volleyball players move their bodies in a variety of ways during practice, as illustrated in Fig. 18(j). The device was placed on the wrist and knee to monitor the motions and based on the output voltage, which could distinguish wrist and knee motions (Fig. 18(k)).405
Research on the physical demands of boxing has only been conducted on amateur fighters; studies on professional fighters have only looked at injury risk or weight loss. This implies that it is unknown what demands a professional boxer will face.464 Thus, a TENG device for developing a database comprised of the objects of professional boxers was fabricated based on MXene/PDMS film. A representation of a boxer throwing punches at a target is shown in Fig. 18(l). This graphic portrayal makes it easier to understand the experimental apparatus used to record the triboelectric signals. An actual boxing action is shown in Fig. 18(m), where a glove hits the TENG sensor, highlighting the usefulness of this device in a real-world situation. Plotting the voltage output against time (Fig. 18(n)) is done for the jab, straight fist, and hook fist punches. In contrast to the straight and hook fists, which produce noticeably greater voltages because of the increased impact force and surface area contact, the jab produces comparatively smaller voltage peaks.57 Different athlete motion abilities and task objectives result in varying table tennis motion durations, which can potentially lead to issues with motion recognition.465 Incorporating MXene/PI film, a TENG sensor was reported to track the batting activities of tennis. The TENG sensor was integrated into a tennis bat to track the batting activities (Fig. 18(o)). The current signals were produced in real-time throughout table tennis practice (Fig. 18(p)). The data showed clear peaks that correspond to each ball strike, giving specific details about how frequently and how hard the hits occur.458 Thus, TENG-based self-powered sensors can be applied in intelligent sports monitoring.
MXene triboelectric nanogenerators (TENGs) are becoming increasingly popular as cutting-edge self-powered wearable sensor components in the constantly evolving environment.466 These digital devices provide up-to-date information on critical performance metrics such as muscle activity, heart rate, pace, and distance.467 Additionally, MXene TENGs have excellent mechanical durability, continuing to function for thousands of cycles, which makes them perfect for continuous, real-time sports monitoring.403,457 Besides, their ability to create wearables that are strong, lightweight, and function effectively might completely change how athletes track their performance and avoid injuries.
6.4. Smart homes
Automation based on the Internet of Things (IoT) has been popular for years. Automation is being incorporated into every part of daily life, from consumer homes to industrial machinery.468 Smart homes have attracted significant interest because of their potential to increase the quality of life of people. Environmentally friendly, highly stable, and high-performing electrical devices are desperately needed as a key part of smart homes. Triboelectric nanogenerators (TENGs), which can transform mechanical energy into electrical outputs at low frequencies, are considered the most promising way to deal with this problem.469,470 A highly sensitive MXene/silicone film that operates in single-electrode was used for security purposes. An Arduino board was connected to an aluminium electrode attached to this triboelectric layer. Through contact electrification, a voltage pulse is produced when a human hand touches the triboelectric layer. The Arduino board then records this voltage signal, which causes the Arduino's built-in Wi-Fi module to send a security warning to a mobile device. Every time there is unwanted access, the mobile phone receives emails and SMS. Additionally, the time and date of the unauthorized access are included in email notifications (Fig. 19(a)).59
 |
| Fig. 19 MXene TENG for smart homes, EMI shielding, and soft robotics. (a) Schematic of the single-electrode MXene/silicone TENG device as an IoT touch sensor for security applications. Reprinted with permission from ref. 59. © 2024, American Chemical Society. (b) Schematic of the MXene/PVDF IoT TENG device for wireless control of multiple home appliances. Reprinted with permission from ref. 473. © 2024, American Chemical Society. (c) Schematic of the MXene/PVDF nanofiber-based TENG device attached to the multiple areas of a door for energy harvesting. Reprinted with permission from ref. 406. © 2023, John Wiley & Sons. (d) Schematic illustration of EMI shielding using an MXene/gelatin/sodium lignosulphonate composite. (e) EMI shielding performance after applying the composite with different contents of MXene. (f) EMI shielding effectiveness of the composite before and after 1000 bending cycles (MXene 50 wt%). Reprinted with permission from ref. 386. © 2025, Elsevier. (g) Schematic illustration of EMI shielding using 3D printed MXene/chitosan aerogel. (h) MXene/chitosan composite's EMI shielding effectiveness (8–12 GHz). Reprinted with permission from ref. 477. © 2025, Elsevier. (i) Schematic illustration of EMI shielding using carboxylated styrene-butadiene rubber/polydopamine-altered carbon nanotube/MXene composite. (j) EMI shielding effectiveness of the composite with multiple contents of MXene/CNT/PDA. Reprinted with permission from ref. 478. © 2025, Elsevier. (k) Schematic representation of the HMI system with TENG, Arduino board, transceivers, and robotic arm. (l) Output voltage signals of the TENG captured by the microcontroller circuits. (m) Robot arm performs 3 digital motions according to the control instructions. Reprinted with permission from ref. 390. © 2025, Elsevier. (n) Schematic of constructed intelligent gripper with multi-modal recognition. (o) Schematic of constructed intelligent gripper by coupling photo-thermoelectric and triboelectric actuators. (p) Optical images of the intelligent gripper operation under NIR light. (q) Temperature variations, PTE voltage signals, and triboelectric voltage signals of the intelligent gripper as it comes into touch with six materials exposed to NIR light. Reprinted with permission from ref. 60. © 2025, Elsevier. (r) TENG-powered MXene/CuO/TiO2 sensor as an inspection robot for ethanol alarms in vegetable warehouses. Reprinted with permission from ref. 401. © 2024, American Chemical Society. | |
The primary objective of power management is to efficiently manage the load profiles of its clients. Disruptions are prevented to maintain the stability of the main power system and lower the likelihood of issues. Reducing energy consumption and electricity costs is essential.471 Controlling home appliances remotely is a tedious task and it prevents the waste of power.472 A smart home system operating in a dual mode based on an MXene porous TENG was revealed to control multiple appliances in the home (Fig. 19(b)). The output voltages of the TENG varied based on the applied pressure. In both modes, the system compared the voltages in multiple thresholds and sent commands. Mode 1 can operate only three appliances given that only three thresholds were selected. In mode 2, the signals are transformed into digital form through a microcontroller, which enables the system to control multiple appliances.473 Global warming and other serious ecological and environmental issues are increasing the demand for alternative energy, in addition to renewable energy sources. Therefore, the development of clean, green energy collecting and storage technologies is imperative.474,475 Employing MOF/PAN and MXene/PVDF as positive and negative friction layers, respectively, a TENG device was fabricated to harvest electricity from waste mechanical motions. The TENG was attached to several places in a smart door and produced electricity when the door was opened, knocked, or tapped. After fixing the TENG on the door, the device generated a voltage of 28 V and 18 V when opening and knocking on the door (Fig. 19(c)).406 These findings show that the manufactured TENG gadget might be used in a smart home or office to regulate various appliances to save power, harvest electricity from waste physical motions, and provide security features.
MXene TENGs are showing great promise as parts of security and smart home systems because of their remarkable mechanical, electrical, and environmental characteristics.53,286 These exceptional properties make it feasible to incorporate self-powered, robust, and extremely responsive sensors into motion detection, tamper warning, and environmental monitoring systems.476 They are perfect for powering security devices without the need for external sources because of their capacity to capture mechanical energy from the surrounding environment.308,473 However, in actual application, issues including environmental sensitivity, fabrication scalability, and interaction with current systems must be resolved.
6.5. EMI shielding
Electronic waste and electromagnetic radiation are becoming increasingly dangerous, endangering public health and electronic device functionality. The growth of portable electronics and the introduction of 5G mobile network communication technologies have increased the demand for robust, portable materials with exceptional electromagnetic interference (EMI) shielding qualities.479 An MXene/gelatin/sodium lignosulphonate film-based TENG was used as an effective EMI shield with a vector network analyzer (Fig. 19(d)). The effectiveness of EMI shielding with diverse MXene contents was analyzed. As shown in Fig. 19(e), the EMI shielding effectiveness dramatically improved with an increase in the MXene (Ti3C2Tx) nanosheet content, peaking at 49 dB with 50% content. Even after 1000 bending cycles, the MXene composite film maintained exceptional EMI shielding stability and dependability because of its outstanding mechanical flexibility and stability (Fig. 19(f)).386 Porous conductive polymer nanocomposite foams and aerogels have been shown in numerous experiments to efficiently attenuate electromagnetic radiation by absorption. These thin composites act as sound-absorbing and thermal-management materials, in addition to protecting against electromagnetic radiation.480,481 An MXene (Ti3C2Tx) was solidified into a 3D-printed chitosan aerogel through a direct-ink writing approach and prepared for EMI shielding (Fig. 19(g)) and energy harvesting. The EMI shielding efficiency of the aerogels is shown in Fig. 19(h). The findings showed that increased MXene concentrations enhanced the ability of the printed aerogels to shield against electromagnetic interference. In particular, the printed aerogel with 1% MXene had a shielding effectiveness of around 10 dB, but when the MXene concentration was increased to 10%, its shielding effectiveness significantly increased to about 27 dB.477 In addition to improving their EMI shielding capabilities, composites made of a polymer matrix should be considered owing to the need for multifunctionality under challenging application circumstances.482 A multifunctional carboxylated styrene-butadiene rubber/polydopamine-altered carbon nanotube/MXene film (Fig. 19(i)) was prepared for energy harvesting, EMI shielding, and thermal management. The effectiveness of EMI shielding with different MXene contents in the composite was analyzed. When the MXene content was 50%, the EMI shielding effectiveness reached 58.8 dB from 24.2 dB (Fig. 19(j)). This composite showed certain potential applications, such as Joule heating and TENG, in addition to its good EMI shielding capability.478 Likewise, melamine/PDA/MXene/AgNW foam with multifunctional abilities was prepared. This composite exhibited excellent EMI shielding effectiveness of 48.3 dB, in addition to thermal management and energy harvesting.349 These multipurpose composites will provide scientific guidance and motivation for creating the next generation of wearable electronics that can satisfy the demands of various applications in challenging settings.
MXene films surpass many conventional materials, with EMI SE values exceeding 20 dB at thicknesses as low as approximately 40 nm.483 Composites with improved mechanical strength and EMI shielding qualities can be created by combining MXenes with polymers, carbon nanotubes, and other materials.478,484 In recent years, MXenes, promising absorbing agents, have attracted significant interest for the creation of EMI shielding or absorption materials.54 However, their incorporation in commercial EMI shielding solutions will require addressing issues associated with their stability, environmental sensitivity, and manufacturing scalability.
6.6. Intelligent soft robots
Robots are widely used in many different industries because of their uniqueness and stability. In the past, these robots were made of rigid parts that effectively completed repeated duties. Several sensor modules were used for motion direction and sensing. However, the function of robots has changed over time, moving from basic mechanical tasks to intricate interactive behaviors.485,486 The design and manufacturing of soft sensors have proven essential in unlocking complicated functionality and reducing rigid components. In the course of steady rigid-hybrid-soft evolution, soft robots have arisen with high degrees of freedom and intricate shape creations.487 Robots with TENG-based sensors are promising substitutes for traditional rigid sensors and will expand the capabilities of robotics. TENGs also encourage the creation of novel flexible structures and the inclusion of robotics.488,489 A TENG device based on a single-layer MXene/MWCNT/Ecoflex film was developed for remote robotic control without human touch (noncontact). An HMI system was assembled with a TENG, an Arduino microcontroller for generating instructions and signal processing, a couple of wireless transceiver modules for commands, and a robot arm for tracking and executing the commands (Fig. 19(k)). The robot arm, which could execute various digital gestures that correspond to various microcontroller channels, was controlled by the output voltages of the TENG units. The analog output signals were recorded and detected by the microcontroller, as seen in Fig. 19(l), depending on the TENG unit. The microcontroller then translated the identified impulses into control commands to operate the robot arm, enabling it to precisely perform the matching digital motions (e.g., “1” and “2”) (Fig. 19(m)).390 Most soft robots must include external power and sensing modules to obtain stimulus-response information because traditional light-driven actuators cannot perceive on their own. This compromises their compact size and remote actuation sensitivity.490,491 A dual-layer MXene/chitin nanofibers/PET/PEDOT:PSS film-based intelligent gripper (without external power) was created to achieve the combined benefits of light-driven actuator and multi-modal (temperature/material) recognition by concisely merging the photo-thermoelectric and the triboelectric actuator (Fig. 19(n)). Initially, the material recognition was evaluated with diverse materials and the TENG generated a significant change in the output voltage. An intelligent gripper is constructed by coupling photo-thermoelectric and triboelectric actuators (Fig. 19(o)). Under the influence of NIR light, multiple materials were adhered to a 3D-printed cube and touched by the intelligent gripper (Fig. 19(p)). The triboelectric and photo-thermoelectric actuator generated a different voltages and temperatures (Fig. 19(q)) for different materials contacted by the intelligent gripper. Based on the triboelectric and photo-thermoelectric signals, the intelligent gripper recognized the light-driven information and material without interference.60 Intelligent gas monitoring depends on installing massive sensors, which can result in significant energy waste and installation expenses. Thus, novel energy harvesting techniques to lower power consumption are needed.492,493 An MXene/TiO2/CuO-based ethanol sensor powered by a TENG array was developed as an inspection robot in warehouses to impede the spoilage of fruits and vegetables. The constructed ethanol sensor was mounted on a moving inspection robot, and the TENG was anticipated to capture the mechanical energy produced by the robot. A management circuit stored the electrical output produced by the TENG array, which served as the operational power source of the sensor to enable the concentration of ethanol alarm and online warehouse ethanol level monitoring (Fig. 19(r)).401
MXene-based triboelectric nanogenerators (TENGs) have rich surface functional groups, remarkable electrical conductivity, and mechanical flexibility, making them extremely promising for intelligent soft robots.52,293 Because of these characteristics, MXenes can operate as sensors, actuators, and energy harvesters all at once, enabling self-sufficient, multipurpose robotic systems.494 Their low-voltage actuation and high sensitivity improve energy efficiency and real-time responsiveness.390 Their incorporation into next-generation robotics is further enhanced by their interoperability with wearable human–machine interfaces.
7. Obstacles and future outlook
2D MXenes unquestionably have unique benefits and various features that are not to be undervalued. As a result, they offer numerous innovative ideas for triboelectric nanogenerators. A thorough grasp of MXenes enables the identification of areas with substantial development potential as well as the establishment of a theoretical framework for maximizing their functioning and structure. MXenes have become potential materials for enhancing TENG performance. TENG efficiency is significantly boosted by its special qualities, which include mechanical stability, tailorable surface chemistry, and high electrical conductivity. MXenes enhance the surface charge density through their surface functional groups (–OH, –F, –Cl, –O, etc.) and promote the interactions with the polymer network. These developments make MXene TENGs a viable option for self-powered systems and efficient energy harvesting. However, despite the significant progress, there are many issues that need to be resolved in the emerging field of MXenes in TENG research.
MXenes are extremely hydrophilic due to the presence of surface functional groups (–OH, –F, –O). Their high affinity for water speeds up their oxidation and hydrolysis, which eventually causes structural deterioration. Oxidation transforms MXenes into insulating metal oxides (TiO2, V2O5, and Nb2O5) and reduces the charge transfer ability in TENGs. In this case, encapsulating MXenes with polymers or depositing oxide layers prevents their oxidation by serving as a barrier against moisture. The production of MXene entails laborious procedures, including the use of extremely toxic HF solution and centrifugation to create MXene nanosheets of the proper size. The most common etchant in MXene synthesis is HF, which presents significant safety hazards for large-scale production. Thankfully, various fluorine-free etching substitutes are now available, and it has been demonstrated that large-batch synthesis preserves the product quality comparable to smaller batches. Although MXenes are classified as carbides, nitrides, or carbonitrides, only carbide MXenes (Ti3C2Tx, V2CTx, and Nb2CTx) have been widely explored in TENG. Investigations on double-transition MXenes (Mo2TiC2Tx and Nb2TiC2Tx), high-entropy MXenes (TiVNbMoC3 and TiVCrMoC3), and nitride MXenes (V2N and Mo2N) in TENGs can increase their stability and charge retention. The key developments and the future outlook on MXene TENGs are shown in Fig. 20. The presence of multi-metals in MXenes improves their durability and charge transfer efficiency, while preventing their oxidation. The restacking ability of MXenes has been found to significantly impair their stability; this issue can be resolved by creating various MXene heterostructures. This can increase their stability and assist in resolving restacking concerns.
 |
| Fig. 20 Significant advancements and prospects for MXene TENGs. | |
The long-term sonication used for delamination produces MXenes with a large number of surface defects, which may alter the properties of MXenes. Moreover, the delamination and intercalation processes use organic solvents, which are hazardous to the environment. Alternatively, MXenes can be delaminated using electrolyte solutions (LiCl and TMAOH), amino acids, natural polymers, and electrochemical intercalation. These green and sustainable approaches make MXenes more appropriate for energy harvesting applications. Understanding the dimensions and structure–property relationships of MXenes is crucial for their large-scale synthesis and for comprehending the intricate mechanism at the interface between the MXene and the deposited materials, but very few papers have paid significant attention to this topic. To fully comprehend and gain a thorough grasp of the reaction process between MXenes and foreign elements, a mix of in situ synthesis and simulation studies should be performed. Finding the ideal MXene compositions with optimum triboelectric characteristics is one of the main hurdles in MXene-based TENGs; nevertheless, Artificial Intelligence (AI)/machine learning (ML) can forecast high-performance MXenes before their synthesis. AI and ML in MXene TENGs have a bright future, allowing improvements in real-time energy management, device optimization, and material discovery. First-principles computations (discrete Fourier transform (DFT) and molecular dynamics (MD) simulations) can be processed by AI algorithms to forecast the triboelectric and bandgap characteristics of novel MXene compositions. The effects of various functional groups (–OH, –F, –Cl, and –O) on the triboelectric performance can be predicted by ML. Real-time IoT connectivity, self-optimizing storage integration, and adaptive power management can all be made possible by intelligent AI-based energy harvesting systems. These developments in AI and ML will transform MXene-TENGs into scalable, intelligent, and effective energy harvesting systems.
8. Conclusions
Triboelectric nanogenerators based on MXene have attracted significant attention because of their exceptional mechanical flexibility, structural adaptability, and electrical conductivity, making them essential components for energy harvesting in the future. In addition to describing the numerous TENG operating processes and tracing the genesis and evolution of triboelectricity, this review attempted to enhance the knowledge on the recently developed deformation mode, which presents new functional possibilities. The tunability of MXenes for optimal triboelectric performances was highlighted by examining their location in the triboelectric series, their varying compositions, and their synthesis developments between 2011 and 2024. Their versatility in various TENG configurations was highlighted by their integration as electrodes, tribolayers, and multifunctional materials. The design scope of MXene TENGs was further expanded by their capacity to operate as both positive and negative tribolayers. Their potential in wearable and smart sensing technologies was demonstrated by real-world applications such as wound treatment, sports monitoring, food spoilage detection, intelligent robotics, gait analysis, and EMI shielding. Despite the current obstacles, improving their performance will require developments in large-scale fabrication, surface engineering, and material stability. Material optimization powered by AI and ML may hasten their actual implementation. With ongoing research, MXene-based TENGs have the potential to revolutionize intelligent environmental sensing, healthcare monitoring, and self-powered electronics, spurring innovation in sustainable energy solutions.
Data availability
No primary research results, software, or code have been included, and no new data were generated or analyzed as part of this review. All figures and tables were reproduced from references with permission.
Author contributions
Conceptualization, S. K. C., A. C.; methodology, S. K. C., A. C.; formal analysis, S. K. C., A. C.; visualization, S. K. C., A. C.; investigation, A. C.; validation, A. C.; writing – original draft, S. K. C., writing – review & editing, S. K. C., A. C.; supervision, A. C., K. C.; project administration, A. C., K. C.
Conflicts of interest
The authors declare no competing interests.
Acknowledgements
No acknowledgement is necessary for this work.
References
- H. Sun, Y. Zhao, S. Jiao, C. Wang, Y. Jia, K. Dai, G. Zheng, C. Liu, P. Wan and C. Shen, Adv. Funct. Mater., 2021, 31, 2101696 CrossRef CAS.
- P. Zhu, M. Niu, S. Liang, W. Yang, Y. Zhang, K. Chen, Z. Pan and Y. Mao, Nano Res., 2025, 18, 94907301 CrossRef.
- Z. L. Wang, Adv. Energy Mater., 2020, 10, 1–6 Search PubMed.
- B. A. Gyamfi, F. F. Adedoyin, M. A. Bein, F. V. Bekun and D. Q. Agozie, J. Clean. Prod., 2021, 126373, DOI:10.1016/j.jclepro.2021.126373.
- H. Liu, K. How Koh and C. Lee, Appl. Phys. Lett., 2014, 104, 53901 CrossRef.
- C. Rodrigues, D. Nunes, D. Clemente, N. Mathias, J. M. Correia, P. Rosa-Santos, F. Taveira-Pinto, T. Morais, A. Pereira and J. Ventura, Energy Environ. Sci., 2020, 13, 2657–2683 RSC.
- Z. Wang, L. He, X. Gu, S. Yang, S. Wang, P. Wang and G. Cheng, Rev. Sci. Instrum., 2021, 92, 41501 CrossRef CAS PubMed.
- L. Lu, G. Hu, J. Liu and B. Yang, Adv. Sci., 2024, 11, 1–9 Search PubMed.
- D. Wang, D. Zhang, J. Guo, Y. Hu, Y. Yang, T. Sun, H. Zhang and X. Liu, Nano Energy, 2021, 89, 106410 CrossRef CAS.
- S. Veeralingam and S. Badhulika, Sens. Actuators, B, 2023, 380, 133346 CrossRef CAS.
- S. M. S. Rana, M. A. Zahed, M. T. Rahman, M. Salauddin, S. H. Lee, C. Park, P. Maharjan, T. Bhatta, K. Shrestha and J. Y. Park, Adv. Funct. Mater., 2021, 31, 2105110 CrossRef CAS.
- P. Ma, H. Zhu, H. Lu, Y. Zeng, N. Zheng, Z. L. Wang and X. Cao, Nano Energy, 2021, 86, 106032 CrossRef CAS.
- F. Wen, H. Wang, T. He, Q. Shi, Z. Sun, M. Zhu, Z. Zhang, Z. Cao, Y. Dai, T. Zhang and C. Lee, Nano Energy, 2020, 67, 104266 CrossRef CAS.
- S. Lu, L. Gao, X. Chen, D. Tong, W. Lei, P. Yuan, X. Mu and H. Yu, Nano Energy, 2020, 75, 104813 CrossRef CAS.
- G.-T. Hwang, V. Annapureddy, J. H. Han, D. J. Joe, C. Baek, D. Y. Park, D. H. Kim, J. H. Park, C. K. Jeong, K.-I. Park, J.-J. Choi, D. K. Kim, J. Ryu and K. J. Lee, Adv. Energy Mater., 2016, 6, 1600237 CrossRef.
- X. Dong, Y.-G. Wang and Y. Xia, Acc. Chem. Res., 2021, 54, 3883–3894 CrossRef CAS PubMed.
- X. Yu, Y. Shang, L. Zheng and K. Wang, ACS Appl. Electron. Mater., 2023, 5, 5240–5248 CrossRef CAS.
- X. Cao, Y. Xiong, J. Sun, X. Xie, Q. Sun and Z. L. Wang, Nano-Micro Lett., 2022, 15, 14 CrossRef PubMed.
- G. Prestopino, R. Pezzilli, N. J. Calavita, C. Leonardi, C. Falconi and P. G. Medaglia, Nano Energy, 2023, 118, 109017 CrossRef CAS.
- X. Li, Y. Li, Y. Li, J. Tan, J. Zhang, H. Zhang, J. Liang, T. Li, Y. Liu, H. Jiang and P. Li, ACS Appl. Mater. Interfaces, 2022, 14, 46789–46800 CrossRef CAS PubMed.
- B. Hedau, B.-C. Kang and T.-J. Ha, ACS Nano, 2022, 16, 18355–18365 CrossRef CAS PubMed.
- M. Kim, H. Park, M. H. Lee, J. W. Bae, K. Y. Lee, J. H. Lee and J.-H. Lee, Nano Energy, 2023, 107, 108159 CrossRef CAS.
- H. Khan, N. Mahmood, A. Zavabeti, A. Elbourne, M. A. Rahman, B. Y. Zhang, V. Krishnamurthi, P. Atkin, M. B. Ghasemian, J. Yang, G. Zheng, A. R. Ravindran, S. Walia, L. Wang, S. P. Russo, T. Daeneke, Y. Li and K. Kalantar-Zadeh, Nat. Commun., 2020, 11, 3449 CrossRef CAS PubMed.
- R.-C. Wang, Y.-C. Lin, H.-C. Chen and W.-Y. Lin, Nano Energy, 2021, 83, 105743 CrossRef CAS.
- Q. Zhang, J. Mu, J. Mu, X. Yang, S. Zhang, X. Han, Y. Zhao, Y. You, J. Yu and X. Chou, Energy Technol., 2021, 9, 2000962 CrossRef CAS.
- Y. Hao, J. Yang, X. Zhu, K. Hong, J. Su, Y. Qin, W. Su, H. Zhang, C. Zhang and X. Li, J. Mater. Chem. A, 2025, 13, 1853–1862 RSC.
- F.-R. Fan, Z.-Q. Tian and Z. Lin Wang, Nano Energy, 2012, 1, 328–334 CrossRef CAS.
- J. Luo, Z. Wang, L. Xu, A. C. Wang, K. Han, T. Jiang, Q. Lai, Y. Bai, W. Tang, F. R. Fan and Z. L. Wang, Nat. Commun., 2019, 10, 5147 CrossRef PubMed.
- J. Chen, Y. Huang, N. Zhang, H. Zou, R. Liu, C. Tao, X. Fan and Z. L. Wang, Nat. Energy, 2016, 1, 16138 CrossRef CAS.
- Q. Li, Y. Hu, Q. Yang, X. Li, X. Zhang, H. Yang, P. Ji, Y. Xi and Z. L. Wang, Adv. Energy Mater., 2023, 13, 2202921 CrossRef CAS.
- J. Luo, W. Gao and Z. L. Wang, Adv. Mater., 2021, 33, 2004178 CrossRef CAS PubMed.
- D. Liu, J. Liu, M. Yang, N. Cui, H. Wang, L. Gu, L. Wang and Y. Qin, Nano Energy, 2021, 88, 106303 CrossRef CAS.
- Z. Wang, Y. Wu, W. Jiang, Q. Liu, X. Wang, J. Zhang, Z. Zhou, H. Zheng, Z. Wang and Z. L. Wang, Adv. Funct. Mater., 2021, 31, 2103081 CrossRef CAS.
- M. Shanbedi, H. Ardebili and A. Karim, Prog. Polym. Sci., 2023, 144, 101723 CrossRef CAS.
- R. Wen, J. Guo, A. Yu, J. Zhai and Z. lin Wang, Adv. Funct. Mater., 2019, 29, 1807655 CrossRef.
- M. Naguib, M. Kurtoglu, V. Presser, J. Lu, J. Niu, M. Heon, L. Hultman, Y. Gogotsi and M. W. Barsoum, Adv. Mater., 2011, 23, 4248–4253 CrossRef CAS PubMed.
- L. Liang, L. Niu, T. Wu, D. Zhou and Z. Xiao, ACS Nano, 2022, 16, 7971–7981 CrossRef CAS PubMed.
- S. Yang, P. Zhang, F. Wang, A. G. Ricciardulli, M. R. Lohe, P. W. M. Blom and X. Feng, Angew. Chem., Int. Ed., 2018, 57, 15491–15495 CrossRef CAS PubMed.
- Y. Li, H. Shao, Z. Lin, J. Lu, L. Liu, B. Duployer, P. O. Å. Persson, P. Eklund, L. Hultman, M. Li, K. Chen, X.-H. Zha, S. Du, P. Rozier, Z. Chai, E. Raymundo-Piñero, P.-L. Taberna, P. Simon and Q. Huang, Nat. Mater., 2020, 19, 894–899 CrossRef CAS PubMed.
- J. Mei, G. A. Ayoko, C. Hu, J. M. Bell and Z. Sun, Sustain. Mater. Technol., 2020, 25, e00156 CAS.
- M. Ghidiu, M. R. Lukatskaya, M.-Q. Zhao, Y. Gogotsi and M. W. Barsoum, Nature, 2014, 516, 78–81 CrossRef CAS PubMed.
- M. Naguib, R. R. Unocic, B. L. Armstrong and J. Nanda, Dalton Trans., 2015, 44, 9353–9358 RSC.
- J. Halim, M. R. Lukatskaya, K. M. Cook, J. Lu, C. R. Smith, L.-Å. Näslund, S. J. May, L. Hultman, Y. Gogotsi, P. Eklund and M. W. Barsoum, Chem. Mater., 2014, 26, 2374–2381 CrossRef CAS PubMed.
- M. Xiang, Z. Shen, J. Zheng, M. Song, Q. He, Y. Yang, J. Zhu, Y. Geng, F. Yue, Q. Dong, Y. Ge, R. Wang, J. Wei, W. Wang, H. Huang, H. Zhang, Q. Zhu and C. J. Zhang, Innovation, 2024, 5, 100540 CAS.
- C. E. Shuck, A. Sarycheva, M. Anayee, A. Levitt, Y. Zhu, S. Uzun, V. Balitskiy, V. Zahorodna, O. Gogotsi and Y. Gogotsi, Adv. Eng. Mater., 2020, 1901241, DOI:10.1002/adem.201901241.
- Z. Zhang, Q. Yan, Z. Liu, X. Zhao, Z. Wang, J. Sun, Z. L. Wang, R. Wang and L. Li, Nano Energy, 2021, 88, 106257 CrossRef CAS.
- X. Sun, L. Dong, Y. Liu, X. Li, J. Liu, N. Wang, Y. Liu, X. Li, D. Wang and S. Chen, Mater. Today Nano, 2023, 24, 100410 CrossRef CAS.
- C. Jiang, C. Wu, X. Li, Y. Yao, L. Lan, F. Zhao, Z. Ye, Y. Ying and J. Ping, Nano Energy, 2019, 59, 268–276 CrossRef CAS.
- S. Zhang, Y. Zhu, Y. Xia, K. Liu, S. Li, B. Yang, M. Li, X. Zhi and X. Wang, Adv. Funct. Mater., 2023, 2307609, DOI:10.1002/adfm.202307609.
- X. Tan, S. Wang, Z. You, J. Zheng and Y. Liu, ACS Mater. Lett., 2023, 5, 1929–1937 CrossRef CAS.
- S. Zhang, Y. Xiao, H. Chen, Y. Zhang, H. Liu, C. Qu, H. Shao and Y. Xu, ACS Appl. Mater. Interfaces, 2023, 15, 13802–13812 CrossRef CAS PubMed.
- S. Zhang, S. S. Rana, T. Bhatta, G. B. Pradhan, S. Sharma, H. Song, S. Jeong and J. Y. Park, Nano Energy, 2023, 106, 108110 CrossRef CAS.
- W. Cho, S. Kim, H. Lee, N. Han, H. Kim, M. Lee, T. H. Han and J. J. Wie, Adv. Mater., 2024, 2404163, DOI:10.1002/adma.202404163.
- Y. Du, X. Wang, X. Dai, W. Lu, Y. Tang and J. Kong, J. Mater. Sci. Technol., 2022, 100, 1–11 CrossRef CAS.
- M. Venkatesan, J. Chandrasekar, Y. Hsu, T. Sun, P. Li, X. King, M. Chung, R. Chung, W. Lee, Y. Zhou, J. Lin and C. Kuo, Adv. Sci., 2024, 2404019, DOI:10.1002/advs.202404019.
- Y. Zhang, X. Dai, Y. Zhou, J. Shao, L. Zhao, T. Wang, F. Liu, X. Yan, M. Yang, P. Sun and G. Lu, Nano Energy, 2024, 132, 110372 CrossRef.
- H. Zhang, Q. Hao and H. Liu, AIP Adv., 2024, 14 DOI:10.1063/5.0238763.
- A. Mirsepah, L. Shooshtari, R. Mohammadpour, A. Esfandiar and A. Irajizad, Chem. Eng. J., 2024, 499, 155953 CrossRef CAS.
- N. Madathil, S. Potu, J. Pani, L. Bochu, A. Babu, H. Borkar, P. Kodali, U. K. Khanapuram and R. K. Rajaboina, ACS Appl. Electron. Mater., 2024, 6, 5563–5574 CAS.
- J. Zhou, H. Chen, Z. Wu, P. Zhou, M. You, C. Zheng, Q. Guo, Z. Li and M. Weng, Nano Energy, 2025, 134, 110552 CrossRef CAS.
- S. Li, S. Cao, H. Lu, B. He and B. Gao, Mater. Today Bio, 2024, 26, 101044 CrossRef CAS PubMed.
- F. Wang, S. Wang, Y. Liu, Z. Hu, S. Zhang, S. Ouyang, S. Ma, Z. Wu, Z. Zhao, M. Li, Y. Wu, L. Wang, C. Jia and J. Zhao, Nano Energy, 2024, 131, 110323 CrossRef CAS.
- X. Tan, Z. Huang, L. Chang, H. Pei, Z. Jia and J. Zheng, ACS Sens., 2024, 9, 5782–5791 CrossRef CAS PubMed.
- F. R. Fan, R. Wang, H. Zhang and W. Wu, Chem. Soc. Rev., 2021, 50, 10983–11031 RSC.
- G. Prasad, J. U. Yoon, I. Woo and J. W. Bae, Chem. Eng. J., 2023, 470, 144280 CrossRef CAS.
- B. G. Hyun, Y.-S. Jun, J.-H. Lee, M. Hamidinejad, Z. Saadatnia, S. Ghaffari-Mosanenzadeh, H. E. Naguib and C. B. Park, Compos. B Eng., 2024, 272, 111193 CrossRef CAS.
- N. P K and A. Chandrasekhar, ACS Appl. Electron. Mater., 2024, 6, 5314–5327 CrossRef CAS.
- L. Shi, V. S. Kale, Z. Tian, X. Xu, Y. Lei, S. Kandambeth, Y. Wang, P. T. Parvatkar, O. Shekhah, M. Eddaoudi and H. N. Alshareef, Adv. Funct. Mater., 2023, 33, 2212891 Search PubMed.
- R. Wang, X. Jin, Q. Wang, Q. Zhang, H. Yuan, T. Jiao, X. Cao and J. Ma, Matter, 2023, 6, 1514–1529 Search PubMed.
- T. I. Kim, I.-J. Park, S. Kang, T.-S. Kim and S.-Y. Choi, ACS Appl. Mater. Interfaces, 2021, 13, 21299–21309 CrossRef CAS PubMed.
- L. Dong, M. Wang, J. Wu, C. Zhu, J. Shi and H. Morikawa, ACS Appl. Mater. Interfaces, 2022, 14, 9126–9137 CrossRef CAS PubMed.
- A. VahidMohammadi, J. Rosen and Y. Gogotsi, Science, 2021, 372, eabf1581 CrossRef CAS PubMed.
- M. Naguib, M. W. Barsoum and Y. Gogotsi, Adv. Mater., 2021, 33, 2103393 CrossRef CAS PubMed.
- L. Chen, M. Dahlqvist, T. Lapauw, B. Tunca, F. Wang, J. Lu, R. Meshkian, K. Lambrinou, B. Blanpain, J. Vleugels and J. Rosen, Inorg. Chem., 2018, 57, 6237–6244 CrossRef CAS PubMed.
- T. S. Mathis, K. Maleski, A. Goad, A. Sarycheva, M. Anayee, A. C. Foucher, K. Hantanasirisakul, C. E. Shuck, E. A. Stach and Y. Gogotsi, ACS Nano, 2021, 15, 6420–6429 CrossRef CAS PubMed.
- Q. Yang, S. J. Eder, A. Martini and P. G. Grützmacher, npj Mater. Degrad., 2023, 7, 6 CrossRef CAS.
- B. Ul Haq, S.-H. Kim, A. Rasool Chaudhry, S. AlFaify, F. K. Butt, S. A. Tahir, R. Ahmed and A. Laref, ChemPhysChem, 2024, 25, e202300605 CrossRef CAS PubMed.
- C. E. Shuck and Y. Gogotsi, Chem. Eng. J., 2020, 401, 125786 CrossRef CAS.
- K. Huang, Z. Li, J. Lin, G. Han and P. Huang, Chem. Soc. Rev., 2018, 47, 5109–5124 RSC.
- S. Niu, S. Wang, L. Lin, Y. Liu, Y. S. Zhou, Y. Hu and Z. L. Wang, Energy Environ. Sci., 2013, 6, 3576 RSC.
- M. Hu, R. Cheng, Z. Li, T. Hu, H. Zhang, C. Shi, J. Yang, C. Cui, C. Zhang, H. Wang, B. Fan, X. Wang and Q.-H. Yang, Nanoscale, 2020, 12, 763–771 RSC.
- C. Jiang, X. Li, Y. Yao, L. Lan, Y. Shao, F. Zhao, Y. Ying and J. Ping, Nano Energy, 2019, 66, 104121 CrossRef CAS.
- Z. Wei, J. Wang, Y. Liu, J. Yuan, T. Liu, G. Du, S. Zhu and S. Nie, Adv. Funct. Mater., 2022, 32, 2208277 CrossRef CAS.
- K. Sotthewes, H. J. G. E. Gardeniers, G. Desmet and I. S. M. Jimidar, ACS Omega, 2022, 7, 41828–41839 CrossRef CAS PubMed.
- P. Iversen and D. J. Lacks, J. Electrost., 2012, 70, 309–311 CrossRef.
- R. Zhang, M. Hummelgård, J. Örtegren, M. Olsen, H. Andersson, Y. Yang, H. Zheng and H. Olin, Nano Energy, 2021, 86, 106041 CrossRef CAS.
- J. Shao, T. Jiang and Z. Wang, Sci. China Technol. Sci., 2020, 63, 1087–1109 CrossRef.
- X. Zhang, L. Chen, Y. Jiang, W. Lim and S. Soh, Chem. Mater., 2019, 31, 1473–1478 CrossRef CAS.
- W. Liu, Z. Wang and C. Hu, Mater. Today, 2021, 45, 93–119 CrossRef.
- A. Ahmed, I. Hassan, A. M. Pourrahimi, A. S. Helal, M. F. El-Kady, H. Khassaf and R. B. Kaner, Adv. Mater. Technol., 2020, 5, 2000520 CrossRef CAS.
- C. X. Lu, C. B. Han, G. Q. Gu, J. Chen, Z. W. Yang, T. Jiang, C. He and Z. L. Wang, Adv. Eng. Mater., 2017, 19, 1700275 CrossRef.
- Y. Zi, J. Wang, S. Wang, S. Li, Z. Wen, H. Guo and Z. L. Wang, Nat. Commun., 2016, 7, 10987 CrossRef CAS PubMed.
- X. Chen, Z. Ren, M. Han, J. Wan and H. Zhang, Nano Energy, 2020, 75, 104980 CrossRef CAS.
- Z. L. Wang, Mater. Today, 2022, 52, 348–363 CrossRef.
- T. Cheng, J. Shao and Z. L. Wang, Nat. Rev. Methods Primers, 2023, 3, 39 CrossRef CAS.
- Y. Li, G. Li, P. Zhang, H. Zhang, C. Ren, X. Shi, H. Cai, Y. Zhang, Y. Wang, Z. Guo, H. Li, G. Ding, H. Cai, Z. Yang, C. Zhang and Z. L. Wang, Adv. Energy Mater., 2021, 11, 2003921 CrossRef CAS.
- Z. L. Wang, Faraday Discuss., 2014, 176, 447–458 RSC.
- X. Cui and Y. Zhang, Nano Sel., 2020, 1, 461–470 CrossRef.
- D. Li, C. Wu, L. Ruan, J. Wang, Z. Qiu, K. Wang, Y. Liu, Y. Zhang, T. Guo, J. Lin and T. W. Kim, Nano Energy, 2020, 75, 104818 CrossRef CAS.
- Z.-H. Lin, Y. Xie, Y. Yang, S. Wang, G. Zhu and Z. L. Wang, ACS Nano, 2013, 7, 4554–4560 CrossRef CAS PubMed.
- J. Wen, H. He, C. Niu, M. Rong, Y. Huang and Y. Wu, Nano Energy, 2022, 96, 107070 CrossRef CAS.
- C. Kumar, J. Perris, S. Bairagi, G. Min, Y. Xu, N. Gadegaard and D. M. Mulvihill, Nano Energy, 2023, 107, 108122 CrossRef CAS.
- D. Liu, X. Yin, H. Guo, L. Zhou, X. Li, C. Zhang, J. Wang and Z. L. Wang, Sci. Adv., 2024, 5, eaav6437 CrossRef PubMed.
- J. You, J. Shao, Y. He, X. Guo, K. W. See, Z. L. Wang and X. Wang, EcoMat, 2023, 5, e12392 CrossRef.
- K. Wang, Y. Weng, G. Chen, C. Wu, J. H. Park, Z. Qiu, J. Wang, Y. Liu, Y. Zhang, X. Zhou, T. Guo and T. W. Kim, Nano Energy, 2021, 85, 105929 CrossRef CAS.
- S.-H. Chung, J. Chung, M. Song, S. Kim, D. Shin, Z.-H. Lin, B. Koo, D. Kim, J. Hong and S. Lee, Adv. Energy Mater., 2021, 11, 2100936 CrossRef CAS.
- Y. Chen, Y. Cheng, Y. Jie, X. Cao, N. Wang and Z. L. Wang, Energy Environ. Sci., 2019, 12, 2678–2684 RSC.
- R. Zhang, M. Hummelgård, J. Örtegren, M. Olsen, H. Andersson and H. Olin, Nano Energy, 2019, 57, 279–292 CrossRef CAS.
- Y. He, J. Tian, W. Peng, D. Huang, F. Li and Y. He, Nanotechnology, 2023, 295401, DOI:10.1088/1361-6528/accde5.
- T. Du, Z. Chen, F. Dong, H. Cai, Y. Zou, Y. Zhang, P. Sun and M. Xu, Adv. Funct. Mater., 2024, 34, 2313794 CrossRef CAS.
- H. Zhao, H. Wang, H. Yu, Q. Xu, X. Li, J. Guo, J. Shao, Z. L. Wang, M. Xu and W. Ding, Energy Environ. Sci., 2024, 17, 2228–2247 Search PubMed.
- D. Yan, D. Tao, D. Xu, Y. Sun, B. Deng, G. Cao, J. Fang and W. Xu, Nano Energy, 2024, 129, 110000 CrossRef CAS.
- L. Gu, L. German, T. Li, J. Li, Y. Shao, Y. Long, J. Wang and X. Wang, ACS Appl. Mater. Interfaces, 2021, 13, 5133–5141 CrossRef CAS PubMed.
- H. Zhang, C. Zhang, J. Zhang, L. Quan, H. Huang, J. Jiang, S. Dong and J. Luo, Nano Energy, 2019, 61, 442–453 CrossRef CAS.
- J. Yun, N. Jayababu and D. Kim, Nano Energy, 2020, 78, 105325 CrossRef CAS.
- S. Hu, J. Weber, S. Chang, G. Xiao, J. Lu, J. Gao, W. Jiang, Y. Zhang and Y. Tao, Adv. Mater. Technol., 2022, 7, 2200186 CrossRef CAS.
- A. R. Mule, B. Dudem, H. Patnam, S. A. Graham and J. S. Yu, ACS Sustain. Chem. Eng., 2019, 7, 16450–16458 CrossRef CAS.
- H. Zhang, D.-Z. Zhang, D.-Y. Wang, Z.-Y. Xu, Y. Yang and B. Zhang, Rare Met., 2022, 41, 3117–3128 CrossRef CAS.
- Z. Yu, Z. Zhu, Y. Wang, J. Wang, Y. Zhao, J. Zhang, Y. Qin, Q. Jiang and H. He, Cellulose, 2023, 30, 5355–5371 CrossRef CAS.
- P. Zhang, X. Bu, L. Huang, Y. Li, Z. Zhao, R. Yang, L. Yang and K. Zhang, Sustain. Energy Fuels, 2024, 8, 2743–2750 RSC.
- L. Zhang, C. Su, X. Cui, P. Li, Z. Wang, L. Gu and Z. Tang, ACS Appl. Electron. Mater., 2020, 2, 3366–3372 CrossRef CAS.
- L. Liu, X. Yang, L. Zhao, H. Hong, H. Cui, J. Duan, Q. Yang and Q. Tang, ACS Nano, 2021, 15, 9412–9421 CrossRef CAS PubMed.
- X. Zhu, X. Cao and Z. L. Wang, Adv. Mater. Technol., 2022, 7, 2200006 CrossRef.
- Z. Li, S. Zhang, H. Guo, B. Wang, Y. Gong, S. Zhong, Y. Peng, J. Zheng and X. Xiao, Nano Energy, 2023, 113, 108595 CrossRef CAS.
- X. Wang, L. Chen, Z. Xu, P. Chen, C. Ye, B. Chen, T. Jiang, Z. Hong and Z. L. Wang, Small, 2024, 20, 2310809 CrossRef CAS PubMed.
- X. Su, Y. Su, H. Yan, X. Zhang, G. Dai, X. Dong, J. Wu, X. Zhao, K. Zhao and Z. Li, Nanoscale, 2025, 17, 3370–3380 RSC.
- J. Fan, R. Yang, Y. Du, F. Wang, L. Wang, J. Yang and A. Zhou, Nano Energy, 2024, 129, 109999 CrossRef CAS.
- F. Ezzah Ab Latif, A. Numan, N. M. Mubarak, M. Khalid, E. C. Abdullah, N. A. Manaf and R. Walvekar, Coord. Chem. Rev., 2022, 471, 214755 CrossRef CAS.
- Y. Gogotsi and Q. Huang, ACS Nano, 2021, 15, 5775–5780 CrossRef CAS PubMed.
- M. Wang, M. Khazaei, Y. Kawazoe and Y. Liang, Phys. Rev. B, 2021, 103, 35433 CrossRef CAS.
- Z. Li and Y. Wu, Small, 2019, 15, 1–10 Search PubMed.
- I. Hussain, U. Sajjad, O. J. Kewate, U. Amara, F. Bibi, A. Hanan, D. Potphode, M. Ahmad, M. S. Javed, P. Rosaiah, S. Hussain, K. Khan, Z. Ajmal, S. Punniyakoti, S. S. Alarfaji, J.-H. Kang, W. Al Zoubi, S. Sahoo and K. Zhang, Mater. Today Phys., 2024, 42, 101382 CrossRef CAS.
- S. Venkateshalu, G. M. Tomboc, B. Kim, J. Li and K. Lee, ChemNanoMat, 2022, 8, e202200320 CrossRef CAS.
- Z. Jing, H. Wang, X. Feng, B. Xiao, Y. Ding, K. Wu and Y. Cheng, J. Phys. Chem. Lett., 2019, 10, 5721–5728 CrossRef CAS PubMed.
- N. M. Caffrey, J. Phys. Chem. C, 2020, 124, 18797–18804 CrossRef CAS.
- W. Hong, B. C. Wyatt, S. K. Nemani and B. Anasori, MRS Bull., 2020, 45, 850–861 CrossRef.
- Z. Fu, N. Wang, D. Legut, C. Si, Q. Zhang, S. Du, T. C. Germann, J. S. Francisco and R. Zhang, Chem. Rev., 2019, 119, 11980–12031 CrossRef CAS PubMed.
- J. D. Gouveia, F. Viñes, F. Illas and J. R. B. Gomes, Phys. Rev. Mater., 2020, 4, 54003 CrossRef CAS.
- H. Kumar, N. C. Frey, L. Dong, B. Anasori, Y. Gogotsi and V. B. Shenoy, ACS Nano, 2017, 11, 7648–7655 CrossRef CAS PubMed.
- T. Zhang, C. E. Shuck, K. Shevchuk, M. Anayee and Y. Gogotsi, J. Am. Chem. Soc., 2023, 145, 22374–22383 CrossRef CAS PubMed.
- K. Shevchuk, A. Sarycheva, C. E. Shuck and Y. Gogotsi, Chem. Mater., 2023, 35, 8239–8247 CrossRef CAS.
- A. J. Mannix, B. Kiraly, M. C. Hersam and N. P. Guisinger, Nat. Rev. Chem., 2017, 1, 14 CrossRef CAS.
- X. Xiao, H. Wang, P. Urbankowski and Y. Gogotsi, Chem. Soc. Rev., 2018, 47, 8744–8765 RSC.
- Z. Wu, T. Shang, Y. Deng, Y. Tao and Q.-H. Yang, Adv. Sci., 2020, 7, 1903077 CrossRef CAS PubMed.
- X. Hui, X. Ge, R. Zhao, Z. Li and L. Yin, Adv. Funct. Mater., 2020, 30, 2005190 CrossRef CAS.
- M. Malaki, X. Jiang, H. Wang, R. Podila, H. Zhang, P. Samorì and R. S. Varma, Chem. Eng. J., 2023, 463, 142351 Search PubMed.
- T. Su, X. Ma, J. Tong, H. Ji, Z. Qin and Z. Wu, J. Mater. Chem. A, 2022, 10, 10265–10296 Search PubMed.
- M. Benchakar, L. Loupias, C. Garnero, T. Bilyk, C. Morais, C. Canaff, N. Guignard, S. Morisset, H. Pazniak, S. Hurand, P. Chartier, J. Pacaud, V. Mauchamp, M. W. Barsoum, A. Habrioux and S. Célérier, Appl. Surf. Sci., 2020, 530, 147209 CrossRef CAS.
- M. Downes, C. E. Shuck, B. McBride, J. Busa and Y. Gogotsi, Nat. Protoc., 2024, 19, 1807–1834 CrossRef CAS PubMed.
- I. Hussain, W. U. Arifeen, S. A. Khan, S. Aftab, M. S. Javed, S. Hussain, M. Ahmad, X. Chen, J. Zhao, P. Rosaiah, K. F. Fawy, A. Younis, S. Sahoo and K. Zhang, Nano-Micro Lett., 2024, 16, 215 CrossRef CAS PubMed.
- M. Downes, C. E. Shuck, R. W. Lord, M. Anayee, M. Shekhirev, R. J. Wang, T. Hryhorchuk, M. Dahlqvist, J. Rosen and Y. Gogotsi, ACS Nano, 2023, 17, 17158–17168 CrossRef CAS PubMed.
- G. Deysher, C. E. Shuck, K. Hantanasirisakul, N. C. Frey, A. C. Foucher, K. Maleski, A. Sarycheva, V. B. Shenoy, E. A. Stach, B. Anasori and Y. Gogotsi, ACS Nano, 2020, 14, 204–217 Search PubMed.
- M. Shekhirev, C. E. Shuck, A. Sarycheva and Y. Gogotsi, Prog. Mater. Sci., 2021, 120, 100757 CrossRef CAS.
- H. Guo, X. Fu, L. Peng, C. Wang, Y. Zhuang, H. Chong, Z. Chen, W. Gong, M. Yan, Q. Wang and W. Cui, Adv. Mater., 2024, 36, 2404466 CrossRef CAS PubMed.
- X. Guo, S. Lin, J. Gu, S. Zhang, Z. Chen and S. Huang, Adv. Funct. Mater., 2021, 31, 2008056 Search PubMed.
- R. Ibragimova, P. Erhart, P. Rinke and H.-P. Komsa, J. Phys. Chem. Lett., 2021, 12, 2377–2384 Search PubMed.
- J. Björk and J. Rosen, Chem. Mater., 2021, 33, 9108–9118 Search PubMed.
- A. Djire, H. Zhang, J. Liu, E. M. Miller and N. R. Neale, ACS Appl. Mater. Interfaces, 2019, 11, 11812–11823 Search PubMed.
- J. Bekaert, C. Sevik and M. V Milošević, Nanoscale, 2020, 12, 17354–17361 Search PubMed.
- S. Kumar, Small, 2024, 20, 2308225 CrossRef CAS PubMed.
- M. Li, J. Lu, K. Luo, Y. Li, K. Chang, K. Chen, J. Zhou, J. Rosen, L. Hultman, P. Eklund, P. O. Å. Persson, S. Du, Z. Chai, Z. Huang and Q. Huang, J. Am. Chem. Soc., 2019, 141, 4730–4737 Search PubMed.
- J. Lu, I. Persson, H. Lind, J. Palisaitis, M. Li, Y. Li, K. Chen, J. Zhou, S. Du, Z. Chai, Z. Huang, L. Hultman, P. Eklund, J. Rosen, Q. Huang and P. O. Å. Persson, Nanoscale Adv., 2019, 1, 3680–3685 RSC.
- Y. Li, H. Shao, Z. Lin, J. Lu, L. Liu, B. Duployer, P. O. Å. Persson, P. Eklund, L. Hultman, M. Li, K. Chen, X.-H. Zha, S. Du, P. Rozier, Z. Chai, E. Raymundo-Piñero, P.-L. Taberna, P. Simon and Q. Huang, Nat. Mater., 2020, 19, 894–899 CrossRef CAS PubMed.
- M. Li, X. Li, G. Qin, K. Luo, J. Lu, Y. Li, G. Liang, Z. Huang, J. Zhou, L. Hultman, P. Eklund, P. O. Å. Persson, S. Du, Z. Chai, C. Zhi and Q. Huang, ACS Nano, 2021, 15, 1077–1085 CrossRef CAS PubMed.
- V. Kamysbayev, A. S. Filatov, H. Hu, X. Rui, F. Lagunas, D. Wang, R. F. Klie and D. V. Talapin, Science, 2020, 369, 979–983 CrossRef CAS PubMed.
- Y. Liu, J. Mo, Q. Fu, Y. Lu, N. Zhang, S. Wang and S. Nie, Adv. Funct. Mater., 2020, 30, 2004714 CrossRef CAS.
- B. Zhang, G. Tian, D. Xiong, T. Yang, F. Chun, S. Zhong, Z. Lin, W. Li and W. Yang, Research, 2021, 2021 DOI:10.34133/2021/7189376.
- M. Dadashi Firouzjaei, M. Karimiziarani, H. Moradkhani, M. Elliott and B. Anasori, Mater. Today Adv., 2022, 13, 100202 CrossRef CAS.
- L. Jin, Z. Li, H. Huang, X. Chu, W. Deng, J. Zhang, Y. Ao, T. Xu, G. Tian, T. Yang, L. Tang and W. Yang, Adv. Eng. Mater., 2023, 25, 2300709 CrossRef CAS.
- A. Ahmed, S. Sharma, B. Adak, M. M. Hossain, A. M. LaChance, S. Mukhopadhyay and L. Sun, InfoMat, 2022, 4, e12295 CrossRef CAS.
- R. Khanal and S. Irle, J. Chem. Phys., 2023, 158, 194701 CrossRef CAS PubMed.
- A. M. Patil, A. A. Jadhav, N. R. Chodankar, A. T. Avatare, J. Hong, S. D. Dhas, U. M. Patil and S. C. Jun, Coord. Chem. Rev., 2024, 517, 216020 CrossRef CAS.
- L. Shi, Y. Wang, T. Guo, Y. Lei, J. K. El-Demellawi, Z. Zhao and H. N. Alshareef, Adv. Funct. Mater., 2024, 2408538, DOI:10.1002/adfm.202408538.
- D. Ontiveros, F. Viñes and C. Sousa, J. Mater. Chem. A, 2023, 11, 13754–13764 RSC.
- J. D. Gouveia and J. R. B. Gomes, Mater. Today Chem., 2023, 29, 101441 CrossRef CAS.
- T. Shimada, N. Takenaka, Y. Ando, M. Otani, M. Okubo and A. Yamada, Chem. Mater., 2022, 34, 2069–2075 CrossRef CAS.
- V. Natu and M. W. Barsoum, J. Phys. Chem. C, 2023, 127, 20197–20206 CrossRef CAS.
- G. Khandelwal, N. P. Maria Joseph Raj and S.-J. Kim, Adv. Energy Mater., 2021, 11, 2101170 CrossRef CAS.
- M. M. Hasan, M. S. Bin Sadeque, I. Albasar, H. Pecenek, F. K. Dokan, M. S. Onses and M. Ordu, Small, 2023, 19, 2206107 CrossRef CAS PubMed.
- P. Pendyala, J. Lee, S. J. Kim and E.-S. Yoon, Appl. Surf. Sci., 2022, 603, 154402 CrossRef CAS.
- Y. Gao, G. Liu, T. Bu, Y. Liu, Y. Qi, Y. Xie, S. Xu, W. Deng, W. Yang and C. Zhang, Nano Res., 2021, 14, 4833–4840 CrossRef CAS.
- Y. Dong, S. S. K. Mallineni, K. Maleski, H. Behlow, V. N. Mochalin, A. M. Rao, Y. Gogotsi and R. Podila, Nano Energy, 2018, 44, 103–110 CrossRef CAS.
- X. Chen, Y. Zhao, L. Li, Y. Wang, J. Wang, J. Xiong, S. Du, P. Zhang, X. Shi and J. Yu, Polym. Rev., 2021, 61, 80–115 CrossRef CAS.
- C. B. Hatter, J. Shah, B. Anasori and Y. Gogotsi, Compos. B Eng., 2020, 182, 107603 CrossRef CAS.
- X. Zhao, M. Zhu, C. Tang, K. Quan, Q. Tong, H. Cao, J. Jiang, H. Yang and J. Zhang, J. Colloid Interface Sci., 2022, 620, 478–485 CrossRef CAS PubMed.
- J. Yun, J. Park, M. Ryoo, N. Kitchamsetti, T. S. Goh and D. Kim, Nano Energy, 2023, 105, 108018 CrossRef CAS.
- A. Babu, I. Aazem, R. Walden, S. Bairagi, D. M. Mulvihill and S. C. Pillai, Chem. Eng. J., 2023, 452, 139060 CrossRef CAS.
- R. Mohan and F. Ali, Polym. Adv. Technol., 2023, 34, 3193–3209 CrossRef CAS.
- J. A. Ajani Lakmini Jayarathna, S. Hajra, S. Panda, E. Chamanehpour, I. Sulania, M. Singh Goyat, S.-H. Hsu, H. Joon Kim, T. Treeratanaphitak and Y. Kumar Mishra, Mater. Lett., 2024, 363, 136252 CrossRef CAS.
- D. P. Pabba, M. Satthiyaraju, A. Ramasdoss, P. Sakthivel, N. Chidhambaram, S. Dhanabalan, C. V. Abarzúa, M. J. Morel, R. Udayabhaskar and R. V. Mangalaraja, Micromachines, 2023, 14(6), 1273 CrossRef PubMed.
- Y. Wang, J. Zhang, X. Jia, M. Chen, H. Wang, G. Ji, H. Zhou, Z. Fang and Z. Gao, Nano Energy, 2024, 119, 109080 CrossRef CAS.
- X. Li, G. Xu, X. Xia, J. Fu, L. Huang and Y. Zi, Nano Energy, 2019, 56, 40–55 CrossRef CAS.
- T. Bhatta, P. Maharjan, H. Cho, C. Park, S. H. Yoon, S. Sharma, M. Salauddin, M. T. Rahman, S. S. Rana and J. Y. Park, Nano Energy, 2021, 81, 105670 CrossRef CAS.
- S. Chun, I. Y. Choi, W. Son, J. Jung, S. Lee, H. S. Kim, C. Pang, W. Park and J. K. Kim, ACS Energy Lett., 2019, 4, 1748–1754 CrossRef CAS.
- Q. Zhang, C. Jiang, X. Li, S. Dai, Y. Ying and J. Ping, ACS Nano, 2021, 15, 12314–12323 CrossRef CAS PubMed.
- Q. Zhang, C. Xin, F. Shen, Y. Gong, Y. Zi, H. Guo, Z. Li, Y. Peng, Q. Zhang and Z. L. Wang, Energy Environ. Sci., 2022, 15, 3688–3721 RSC.
- T. Zhang, L. Chang and X. Xiao, Small Methods, 2023, 7, 2201530 CrossRef CAS PubMed.
- J. Wozniak, A. Jastrzębska and A. Olszyna, Mater. Technol., 2022, 37, 1639–1650 CrossRef CAS.
- H. Alnoor, A. Elsukova, J. Palisaitis, I. Persson, E. N. Tseng, J. Lu, L. Hultman and P. O. Å. Persson, Mater. Today Adv., 2021, 100123, DOI:10.1016/j.mtadv.2020.100123.
- J. Gonzalez-Julian, J. Am. Ceram. Soc., 2021, 104, 659–690 CrossRef CAS.
- M. S. Alam, M. A. Chowdhury, M. A. Kowser, M. S. Islam, M. M. Islam and T. Khandaker, Eng. Rep., 2024, 6, e12911 CrossRef.
- M. W. Barsoum and T. El-Raghy, Am. Sci., 2001, 89, 334–343 CrossRef.
- S. N. Perevislov, T. V Sokolova and V. L. Stolyarova, Mater. Chem. Phys., 2021, 267, 124625 CrossRef CAS.
- P. Eklund, M. Beckers, U. Jansson, H. Högberg and L. Hultman, Thin Solid Films, 2010, 518, 1851–1878 CrossRef CAS.
- X. Lei and N. Lin, Crit. Rev. Solid State Mater. Sci., 2022, 47, 736–771 CrossRef CAS.
- M. Sokol, V. Natu, S. Kota and M. W. Barsoum, Trends Chem., 2019, 1, 210–223 CrossRef CAS.
- M. Dahlqvist, M. W. Barsoum and J. Rosen, Mater. Today, 2024, 72, 1–24 CrossRef.
- N. Kubitza, R. Xie, I. Tarasov, C. Shen, H. Zhang, U. Wiedwald and C. S. Birkel, Chem. Mater., 2023, 35, 4427–4434 CrossRef CAS.
- J. Gonzalez-Julian, J. Am. Ceram. Soc., 2021, 104, 659–690 CrossRef CAS.
- Y. Zhou, F. Meng and J. Zhang, J. Am. Ceram. Soc., 2008, 91, 1357–1360 CrossRef CAS.
- J. P. Siebert, K. Patarakun and C. S. Birkel, Inorg. Chem., 2022, 61, 1603–1610 CrossRef CAS PubMed.
- T. Amrillah, C. A. C. Abdullah, A. Hermawan, F. N. I. Sari and V. N. Alviani, Nanomaterials, 2022, 12(23), 4280 CrossRef CAS PubMed.
- A. Iqbal, J. Hong, T. Y. Ko and C. M. Koo, Nano Convergence, 2021, 8, 9 CrossRef CAS PubMed.
- M. Naguib, M. Kurtoglu, V. Presser, J. Lu, J. Niu, M. Heon, L. Hultman, Y. Gogotsi and M. W. Barsoum, Adv. Mater., 2011, 23, 4248–4253 CrossRef CAS PubMed.
- M. Naguib, V. N. Mochalin, M. W. Barsoum and Y. Gogotsi, Adv. Mater., 2014, 26, 992–1005 CrossRef CAS PubMed.
- L. Gao, C. Li, W. Huang, S. Mei, H. Lin, Q. Ou, Y. Zhang, J. Guo, F. Zhang, S. Xu and H. Zhang, Chem. Mater., 2020, 32, 1703–1747 CrossRef CAS.
- M. Mustakeem, J. K. El-Demellawi, M. Obaid, F. Ming, H. N. Alshareef and N. Ghaffour, ACS Appl. Mater. Interfaces, 2022, 14, 5265–5274 CrossRef CAS PubMed.
- S. Zhang, M. Zhang, W. Xiong, J. Long, Y. Xu, L. Yang and W. Dai, Catalysts, 2022, 1594, DOI:10.3390/catal12121594.
- J. Li, D. Yan, S. Hou, Y. Li, T. Lu, Y. Yao and L. Pan, J. Mater. Chem. A, 2018, 6, 1234–1243 RSC.
- S. Chen, Y. Xiang, M. K. Banks, C. Peng, W. Xu and R. Wu, Nanoscale, 2018, 10, 20043–20052 RSC.
- J. Wu, Y. Wang, Y. Zhang, H. Meng, Y. Xu, Y. Han, Z. Wang, Y. Dong and X. Zhang, J. Energy Chem., 2020, 47, 203–209 CrossRef.
- C. E. Shuck, K. Ventura-Martinez, A. Goad, S. Uzun, M. Shekhirev and Y. Gogotsi, ACS Chem. Health Saf., 2021, 28, 326–338 CrossRef CAS.
- P. Lakhe, E. M. Prehn, T. Habib, J. L. Lutkenhaus, M. Radovic, M. S. Mannan and M. J. Green, Ind. Eng. Chem. Res., 2019, 58, 1570–1579 CrossRef CAS.
- C. Zhang, X. Wang, W. Wei, X. Hu, Y. Wu, N. Lv, S. Dong and L. Shen, Chemelectrochem, 2021, 8, 3804–3826 CrossRef CAS.
- A. Feng, Y. Yu, Y. Wang, F. Jiang, Y. Yu, L. Mi and L. Song, Mater. Des., 2017, 114, 161–166 CrossRef CAS.
- F. Liu, A. Zhou, J. Chen, J. Jia, W. Zhou, L. Wang and Q. Hu, Appl. Surf. Sci., 2017, 416, 781–789 CrossRef CAS.
- F. Liu, J. Zhou, S. Wang, B. Wang, C. Shen, L. Wang, Q. Hu, Q. Huang and A. Zhou, J. Electrochem. Soc., 2017, 164, A709–A713 CrossRef CAS.
- P. Urbankowski, B. Anasori, T. Makaryan, D. Er, S. Kota, P. L. Walsh, M. Zhao, V. B. Shenoy, M. W. Barsoum and Y. Gogotsi, Nanoscale, 2016, 8, 11385–11391 RSC.
- V. Natu, R. Pai, M. Sokol, M. Carey, V. Kalra and M. W. Barsoum, Chem, 2020, 6, 616–630 CAS.
- M. Zhao, M. Sedran, Z. Ling, M. R. Lukatskaya, O. Mashtalir, M. Ghidiu, B. Dyatkin, D. J. Tallman, T. Djenizian, M. W. Barsoum and Y. Gogotsi, Angew. Chem., Int. Ed., 2015, 54, 4810–4814 CrossRef CAS PubMed.
- W. Sun, S. A. Shah, Y. Chen, Z. Tan, H. Gao, T. Habib, M. Radovic and M. J. Green, J. Mater. Chem. A, 2017, 5, 21663–21668 RSC.
- M. R. Lukatskaya, J. Halim, B. Dyatkin, M. Naguib, Y. S. Buranova, M. W. Barsoum and Y. Gogotsi, Angew. Chem., 2014, 126, 4977–4980 CrossRef.
- S. Zada, W. Dai, Z. Kai, H. Lu, X. Meng, Y. Zhang, Y. Cheng, F. Yan, P. Fu, X. Zhang and H. Dong, Angew. Chem., Int. Ed., 2020, 59, 6601–6606 CrossRef CAS PubMed.
- F. Gao, C. Xue, T. Zhang, L. Zhang, G. Zhu, C. Ou, Y. Zhang and X. Dong, Adv. Mater., 2023, 2302559, DOI:10.1002/adma.202302559.
- X. Xu, L. Yang, W. Zheng, H. Zhang, F. Wu, Z. Tian, P. Zhang and Z. Sun, Mater. Rep.: Energy, 2022, 2, 100080 CAS.
- G. Li, K. Jiang, S. Zaman, J. Xuan, Z. Wang and F. Geng, Inorg. Chem., 2019, 58, 9397–9403 CrossRef CAS PubMed.
- C. Peng, P. Wei, X. Chen, Y. Zhang, F. Zhu, Y. Cao, H. Wang, H. Yu and F. Peng, Ceram. Int., 2018, 44, 18886–18893 CrossRef CAS.
- T. Li, L. Yao, Q. Liu, J. Gu, R. Luo, J. Li, X. Yan, W. Wang, P. Liu, B. Chen, W. Zhang, W. Abbas, R. Naz and D. Zhang, Angew. Chem., Int. Ed., 2018, 57, 6115–6119 CrossRef CAS PubMed.
- Y. Hai, S. Jiang, C. Zhou, P. Sun, Y. Huang and S. Niu, Dalton Trans., 2020, 49, 5803–5814 RSC.
- N. Chen, Z. Duan, W. Cai, Y. Wang, B. Pu, H. Huang, Y. Xie, Q. Tang, H. Zhang and W. Yang, Nano Energy, 2023, 107, 108147 CrossRef CAS.
- H. Shi, P. Zhang, Z. Liu, S. Park, M. R. Lohe, Y. Wu, A. Shaygan Nia, S. Yang and X. Feng, Angew. Chem., Int. Ed., 2021, 60, 8689–8693 CrossRef CAS PubMed.
- J. Wang, H. Kang, H. Ma, Y. Liu, Z. Xie, Y. Wang and Z. Fan, Eng. Sci., 2021, 15 DOI:10.30919/es8d446.
- Y. Bai, C. Liu, T. Chen, W. Li, S. Zheng, Y. Pi, Y. Luo and H. Pang, Angew. Chem., 2021, 133, 25522–25526 CrossRef.
- S. Siddique, A. Waheed, M. Iftikhar, M. T. Mehran, M. Z. Zarif, H. A. Arafat, S. Hussain and F. Shahzad, Prog. Mater. Sci., 2023, 139, 101183 CrossRef CAS.
- J. Mei, G. A. Ayoko, C. Hu and Z. Sun, Chem. Eng. J., 2020, 395, 125111 CrossRef CAS.
- B. Unnikrishnan, C.-W. Wu, A. Sangili, Y.-J. Hsu, Y.-T. Tseng, J. Shanker Pandey, H.-T. Chang and C.-C. Huang, J. Colloid Interface Sci., 2022, 628, 849–857 CrossRef CAS PubMed.
- A. Al Mayyahi, S. Sarker, B. M. Everhart, X. He and P. B. Amama, Mater. Today Commun., 2022, 32, 103835 CrossRef.
- N. Xue, X. Li, M. Zhang, L. Han, Y. Liu and X. Tao, ACS Appl. Energy Mater., 2020, 3, 10234–10241 CrossRef CAS.
- H. Zhou, Z. Chen, E. Kountoupi, A. Tsoukalou, P. M. Abdala, P. Florian, A. Fedorov and C. R. Müller, Nat. Commun., 2021, 12, 5510 CrossRef CAS PubMed.
- D. Wang, C. Zhou, A. S. Filatov, W. Cho, F. Lagunas, M. Wang, S. Vaikuntanathan, C. Liu, R. F. Klie and D. V. Talapin, Science, 2023, 379, 1242–1247 CrossRef CAS PubMed.
- A. Numan, S. Rafique, M. Khalid, H. A. Zaharin, A. Radwan, N. A. Mokri, O. P. Ching and R. Walvekar, Mater. Chem. Phys., 2022, 288, 126429 CrossRef CAS.
- H. O. Badr, T. El-Melegy, M. Carey, V. Natu, M. Q. Hassig, C. Johnson, Q. Qian, C. Y. Li, K. Kushnir, E. Colin-Ulloa, L. V. Titova, J. L. Martin, R. L. Grimm, R. Pai, V. Kalra, A. Karmakar, A. Ruffino, S. Masiuk, K. Liang, M. Naguib, O. Wilson, A. Magenau, K. Montazeri, Y. Zhu, H. Cheng, T. Torita, M. Koyanagi, A. Yanagimachi, T. Ouisse, M. Barbier, F. Wilhelm, A. Rogalev, J. Björk, P. O. Å. Persson, J. Rosen, Y.-J. Hu and M. W. Barsoum, Mater. Today, 2022, 54, 8–17 CrossRef CAS.
- F. Wang, Z. Bian, W. Zhang, L. Zheng, Y. Zhang and H. Wang, Sep. Purif. Technol., 2023, 314, 123549 CrossRef CAS.
- A. Jawaid, A. Hassan, G. Neher, D. Nepal, R. Pachter, W. J. Kennedy, S. Ramakrishnan and R. A. Vaia, ACS Nano, 2021, 15, 2771–2777 CrossRef CAS PubMed.
- F. Wang, S. Jin, Y. Du, Q. Xia, L. Wang and A. Zhou, Diam. Relat. Mater., 2023, 136, 109922 CrossRef CAS.
- Z. Sun, M. Yuan, L. Lin, H. Yang, C. Nan, H. Li, G. Sun and X. Yang, ACS Mater. Lett., 2019, 1, 628–632 CrossRef CAS.
- F. Zhang, Z. Zhang, H. Wang, C. H. Chan, N. Y. Chan, X. X. Chen and J.-Y. Dai, Phys. Rev. Mater., 2017, 1, 034002 CrossRef.
- S. Liu,
et al.
, J. Mater. Chem. C, 2021, 9, 16985–16990 RSC.
- S. Husmann, Ö. Budak, H. Shim, K. Liang, M. Aslan, A. Kruth, A. Quade, M. Naguib and V. Presser, Chem. Commun., 2020, 56, 11082–11085 RSC.
- O. Mashtalir, M. Naguib, V. N. Mochalin, Y. Dall'Agnese, M. Heon, M. W. Barsoum and Y. Gogotsi, Nat. Commun., 2013, 4, 1–7 Search PubMed.
- S. Lai, J. Jeon, S. K. Jang, J. Xu, Y. J. Choi, J.-H. Park, E. Hwang and S. Lee, Nanoscale, 2015, 7, 19390–19396 RSC.
- J. Yang, M. Naguib, M. Ghidiu, L.-M. Pan, J. Gu, J. Nanda, J. Halim, Y. Gogotsi and M. W. Barsoum, J. Am. Ceram. Soc., 2016, 99, 660–666 CrossRef CAS.
- T. Li, L. Yao, Q. Liu, J. Gu, R. Luo, J. Li, X. Yan, W. Wang, P. Liu, B. Chen, W. Zhang, W. Abbas, R. Naz and D. Zhang, Angew. Chem., Int. Ed., 2018, 57, 6115–6119 CrossRef CAS PubMed.
- M. Naguib, O. Mashtalir, J. Carle, V. Presser, J. Lu, L. Hultman, Y. Gogotsi and M. W. Barsoum, ACS Nano, 2012, 6, 1322–1331 CrossRef CAS PubMed.
- H. Fang, A. Thakur, A. Zahmatkeshsaredorahi, Z. Fang, V. Rad, A. A. Shamsabadi, C. Pereyra, M. Soroush, A. M. Rappe, X. G. Xu, B. Anasori and Z. Fakhraai, Proc. Natl. Acad. Sci. U. S. A., 2024, 121(28), e2400084121 CrossRef CAS PubMed.
- Z. Hao, S. Zhang, S. Yang, X. Li, Y. Gao, J. Peng, L. Li, L. Bao and X. Li, ACS Appl. Energy Mater., 2022, 5, 2898–2908 CrossRef CAS.
- Y. Sun, C. Zhan, P. R. C. Kent, M. Naguib, Y. Gogotsi and D. Jiang, ACS Appl. Mater. Interfaces, 2020, 12, 763–770 CrossRef CAS PubMed.
- S. Sunderiya, S. Suragtkhuu, S. Purevdorj, T. Ochirkhuyag, M. Bat-Erdene, P. Myagmarsereejid, A. D. Slattery, A. S. R. Bati, J. G. Shapter, D. Odkhuu, S. Davaasambuu and M. Batmunkh, J. Energy Chem., 2024, 88, 437–445 CrossRef CAS.
- Y. Liu, Z. Shi, T. Liang, D. Zheng, Z. Yang, Z. Wang, J. Zhou and S. Wang, InfoMat, 2024, 6, 1–14 CrossRef PubMed.
- S. Kumar, N. Kumari, T. Singh and Y. Seo, J. Mater. Chem. C, 2024, 12, 8243–8281 RSC.
- S. Kumar, S. M. Zain Mehdi, M. Taunk, S. Kumar, A. Aherwar, S. Singh and T. Singh, J. Mater. Chem. A, 2025, 11050–11113, 10.1039/d4ta08094g.
- X. Hong, Z. Xu, Z. P. Lv, Z. Lin, M. Ahmadi, L. Cui, V. Liljeström, V. Dudko, J. Sheng, X. Cui, A. P. Tsapenko, J. Breu, Z. Sun, Q. Zhang, E. Kauppinen, B. Peng and O. Ikkala, Adv. Sci., 2024, 11, 1–11 Search PubMed.
- R. A. Soomro, P. Zhang, B. Fan, Y. Wei and B. Xu, Nano-Micro Lett., 2023, 15, 108 CrossRef CAS PubMed.
- D. T. K. Ong, J. S. C. Koay, M. T. Sim, K. C. Aw, T. Nakajima, B. Chen, S. T. Tan and W. C. Gan, Nano Energy, 2023, 113, 108555 CrossRef CAS.
- K. Ke and C. Chung, Small, 2020, 16 DOI:10.1002/smll.202001209.
- A. Chandrasekhar, S. A. Basith, V. Vivekananthan, G. Khandelwal, N. P. M. Joseph Raj, Y. Purusothaman and S. J. Kim, Nano Energy, 2024, 123, 109379 CrossRef CAS.
- L. Yao, Z. Zhang, Q. Zhang, Z. Zhou, H. Yang and L. Chen, Nano Energy, 2021, 86, 106128 CrossRef CAS.
- A. A. Maamoun, A. A. Mahmoud, D. M. Naeim, M. Arafa and A. M. K. Esawi, Mater. Adv., 2024, 5, 6132–6144 RSC.
- J. Wang, Z. Xia, H. Yao, Q. Zhang and H. Yang, ACS Appl. Mater. Interfaces, 2023, 15, 47208–47220 CrossRef CAS PubMed.
- S. Roy, P. K. Maji and K.-L. Goh, Chem. Eng. J., 2021, 413, 127409 CrossRef CAS.
- A. C. Wang, C. Wu, D. Pisignano, Z. L. Wang and L. Persano, J. Appl. Polym. Sci., 2017, 45674, DOI:10.1002/app.45674.
- J. Gu, Q. Zhu, Y. Shi, H. Chen, D. Zhang, Z. Du and S. Yang, ACS Nano, 2020, 14, 891–898 CrossRef CAS PubMed.
- M. Ghidiu, J. Halim, S. Kota, D. Bish, Y. Gogotsi and M. W. Barsoum, Chem. Mater., 2016, 28, 3507–3514 CrossRef CAS.
- V. Kumar, P. Kumar, R. Deka, Z. Abbas and S. M. Mobin, Chem. Rec., 2022, e202200067, DOI:10.1002/tcr.202200067.
- S. Anwer, M. Umair Khan, A. Alazzam, B. Mohammad and E. Abu Nada, Chem. Eng. J., 2024, 502, 157985 CrossRef CAS.
- S. Sardana, V. Sharma, K. G. Beepat, D. P. Sharma, A. K. Chawla and A. Mahajan, Nanoscale, 2023, 15, 19369–19380 RSC.
- D. Wang, D. Zhang, Y. Yang, Q. Mi, J. Zhang and L. Yu, ACS Nano, 2021, 15, 2911–2919 CrossRef CAS PubMed.
- W. Yang, X. Cai, S. Guo, L. Wen, Z. Sun, R. Shang, X. Shi, J. Wang, H. Chen and Z. Li, Materials, 2023, 16, 841 CrossRef CAS PubMed.
- C. Fang, J. Han, Q. Yang, Z. Gao, D. Tan, T. Chen and B. Xu, Adv. Sci., 2024, 2408549, DOI:10.1002/advs.202408549.
- M. Y. Bhat, W. A. Adeosun, K. Prenger, Y. A. Samad, K. Liao, M. Naguib, S. Mao and A. Qurashi, Adv. Compos. Hybrid Mater., 2025, 8, 52 CrossRef CAS.
- M. A. Saeed, M. Z. Qamar, Z. Khalid, E. Chamanehpour and Y. K. Mishra, Chem. Eng. J., 2024, 490, 151600 CrossRef CAS.
- S. Abdolhosseinzadeh, X. Jiang, H. Zhang, J. Qiu and C. John Zhang, Mater. Today, 2021, 48, 214–240 CrossRef CAS.
- S. K. Ghosh, J. Kim, M. P. Kim, S. Na, J. Cho, J. J. Kim and H. Ko, ACS Nano, 2022, 16, 11415–11427 CrossRef CAS PubMed.
- W. Chen, L.-X. Liu, H.-B. Zhang and Z.-Z. Yu, ACS Nano, 2020, 14, 16643–16653 CrossRef CAS PubMed.
- P. Zhang, W. Tong, C. Liang, Y. Chen, Y. Liu, Z. Wang and Y. Zhang, J. Mater. Chem. A, 2022, 10, 24310–24319 RSC.
- H. Xu, J. Tao, Y. Liu, Y. Mo, R. Bao and C. Pan, Small, 2022, 2202477, DOI:10.1002/smll.202202477.
- L. Lan, C. Jiang, Y. Yao, J. Ping and Y. Ying, Nano Energy, 2021, 84, 105954 CrossRef CAS.
- X. Luo, L. Zhu, Y. Wang, J. Li, J. Nie and Z. L. Wang, Adv. Funct. Mater., 2021, 2104928, DOI:10.1002/adfm.202104928.
- W. He, M. Sohn, R. Ma and D. J. Kang, Nano Energy, 2020, 78, 105383 CrossRef CAS.
- B. Wang, M. Gao, X. Fu, M. Geng, Y. Liu, N. Cheng, J. Li, L. Li, Z. Zhang and Y. Song, Nano Energy, 2023, 107, 108135 CrossRef CAS.
- K. N. Kim, S. Y. Kim, S. H. Choi, M. Lee, W. Song, J. Lim, S. S. Lee and S. Myung, Adv. Electron. Mater., 2022, 2200819, DOI:10.1002/aelm.202200819.
- B. K. Deka, A. Hazarika, M.-J. Kwak, D. C. Kim, A. P. Jaiswal, H. G. Lee, J. Seo, C. Jeong, J.-H. Jang, Y.-B. Park and H. W. Park, Energy Storage Mater., 2021, 43, 402–410 CrossRef.
- M. M. Hasan, M. S. Bin Sadeque, I. Albasar, H. Pecenek, F. K. Dokan, M. S. Onses and M. Ordu, Small, 2023, 19, 2206107 CrossRef CAS PubMed.
- R. Chen, X. Jia, H. Zhou, S. Ren, D. Han, S. Li and Z. Gao, Mater. Today, 2024, 75, 359–385 CrossRef CAS.
- Y. Hao, C. Zhang, W. Su, H. Zhang, Y. Qin, Z. L. Wang and X. Li, SusMat, 2024, e244, DOI:10.1002/sus2.244.
- Y. Wang, Y. Gui, S. He and J. Yang, Compos.–A: Appl. Sci. Manuf., 2023, 173, 107692 CrossRef CAS.
- H. Jiang, X. Lv and K. Wang, APL Mater., 2024, 12 DOI:10.1063/5.0219633.
- S. M. S. Rana, M. T. Rahman, M. Salauddin, S. Sharma, P. Maharjan, T. Bhatta, H. Cho, C. Park and J. Y. Park, ACS Appl. Mater. Interfaces, 2021, 13, 4955–4967 CrossRef CAS PubMed.
- W. Li, L. Lu, F. Yan, G. Palasantzas, K. Loos and Y. Pei, Nano Energy, 2023, 114, 108629 CrossRef CAS.
- M. T. Rahman, S. M. S. Rana, M. Salauddin, M. A. Zahed, S. Lee, E.-S. Yoon and J. Y. Park, Nano Energy, 2022, 100, 107454 CrossRef CAS.
- S. Tu, Q. Jiang, X. Zhang and H. N. Alshareef, ACS Nano, 2018, 12, 3369–3377 CrossRef CAS PubMed.
- D. Wang, Y. Lin, D. Hu, P. Jiang and X. Huang, Compos.–A: Appl. Sci. Manuf., 2020, 130, 105754 CrossRef CAS.
- Y. Chen, W. Tong, X. Wang, P. Zhang, S. Wang and Y. Zhang, Colloids Surf., A, 2023, 664, 131172 CrossRef CAS.
- R. L. Bulathsinghala, A. Ravichandran, H. Zhao, W. Ding and R. D. I. G. Dharmasena, Nano Energy, 2024, 123, 109383 CrossRef CAS.
- M. M. Baig, Q. M. Saqib, M. Noman, M. Sheeraz, A. Rasheed, M. Yousuf, E. Lee, J. Kim, Y. Ko, C. S. Patil, S. R. Patil, H. Ju, S. G. Lee and J. Bae, Adv. Funct. Mater., 2024, 2408271, DOI:10.1002/adfm.202408271.
- V. A. Cao, M. Kim, S. Lee, P. C. Van, J.-R. Jeong, P. Park and J. Nah, Nano Energy, 2023, 107, 108128 CrossRef CAS.
- B. Wicklein, G. Valurouthu, H. Yoon, H. Yoo, S. Ponnan, M. Mahato, J. Kim, S. S. Ali, J. Y. Park, Y. Gogotsi and I.-K. Oh, ACS Appl. Mater. Interfaces, 2024, 23948–23959, DOI:10.1021/acsami.4c03298.
- B. Xie, Y. Guo, Y. Chen, H. Zhang, J. Xiao, M. Hou, H. Liu, L. Ma, X. Chen and C. Wong, Nano-Micro Lett., 2025, 17, 17 CrossRef CAS PubMed.
- C. Liu, Z. Feng, T. Yin, T. Wan, P. Guan, M. Li, L. Hu, C. Lin, Z. Han, H. Xu, W. Cheng, T. Wu, G. Liu, Y. Zhou, S. Peng, C. Wang and D. Chu, Adv. Mater., 2024, 2403791, DOI:10.1002/adma.202403791.
- M. Kurtoglu, M. Naguib, Y. Gogotsi and M. W. Barsoum, MRS Commun., 2012, 2, 133–137 CrossRef CAS.
- Z. Guo, J. Zhou, C. Si and Z. Sun, Phys. Chem. Chem. Phys., 2015, 17, 15348–15354 RSC.
- K. Gong, K. Zhou, X. Qian, C. Shi and B. Yu, Compos. B Eng., 2021, 217, 108867 CrossRef CAS.
- K. Li, D. Zhang, H. Zhang, D. Wang, Z. Xu, H. Cai and H. Xia, ACS Appl. Mater. Interfaces, 2023, 15, 32993–33002 CrossRef CAS PubMed.
- N. K. Chaudhari, H. Jin, B. Kim, D. San Baek, S. H. Joo and K. Lee, J. Mater. Chem. A, 2017, 5, 24564–24579 RSC.
- L. Li and M. Wu, ACS Nano, 2017, 11, 6382–6388 CrossRef CAS PubMed.
- S. Wang, H.-Q. Shao, Y. Liu, C.-Y. Tang, X. Zhao, K. Ke, R.-Y. Bao, M.-B. Yang and W. Yang, Compos. Sci. Technol., 2021, 202, 108600 CrossRef CAS.
- Z. L. Wang, ACS Nano, 2013, 7, 9533–9557 CrossRef CAS PubMed.
- S. S. K. Mallineni, Y. Dong, H. Behlow, A. M. Rao and R. Podila, Adv. Energy Mater., 2018, 1702736, DOI:10.1002/aenm.201702736.
- Y. Tian, Y. An and B. Xu, Nano Energy, 2022, 101, 107556 CrossRef CAS.
- S. Anwer, M. Umair Khan, B. Mohammad, M. Rezeq, W. Cantwell, D. Gan and L. Zheng, Chem. Eng. J., 2023, 470, 144281 CrossRef CAS.
- J. Fan, M. Yuan, L. Wang, Q. Xia, H. Zheng and A. Zhou, Nano Energy, 2023, 105, 107973 CrossRef CAS.
- I. S. Kucherenko, O. O. Soldatkin, S. V. Dzyadevych and A. P. Soldatkin, Anal. Chim. Acta, 2020, 1111, 114–131 CrossRef CAS PubMed.
- S. Wang, L. Ding, X. Fan, W. Jiang and X. Gong, Nano Energy, 2018, 53, 863–870 CrossRef CAS.
- S. Ankanahalli Shankaregowda, R. F. Sagade Muktar Ahmed, C. B. Nanjegowda, J. Wang, S. Guan, M. Puttaswamy, A. Amini, Y. Zhang, D. Kong, K. Sannathammegowda, F. Wang and C. Cheng, Nano Energy, 2019, 66, 104141 CrossRef CAS.
- W. Cao, H. Ouyang, W. Xin, S. Chao, C. Ma, Z. Li, F. Chen and M. Ma, Adv. Funct. Mater., 2020, 2004181, DOI:10.1002/adfm.202004181.
- Y. Pan, J. Song and K. Wang, ACS Appl. Electron. Mater., 2024, 1–12, DOI:10.1021/acsaelm.4c01729.
- B. Shan, T. Ai and K. Wang, Int. J. Electrochem. Sci., 2024, 19, 100694 CrossRef CAS.
- J. Shen, Z. Li, J. Yu and B. Ding, Nano Energy, 2017, 40, 282–288 CrossRef CAS.
- Y. He, L. Zhao, X. Guo, X. Yang, B. Luo and M. Liu, Chem. Eng. J., 2024, 485, 149949 Search PubMed.
- W. Zhang, P.-L. Wang, X.-X. Ji, L.-Z. Huang, D.-Q. Cao, J. Li and M.-G. Ma, Compos.–A: Appl. Sci. Manuf., 2024, 177, 107957 CrossRef CAS.
- M. Mao, J. Kong, X. Ge, Y. Sun, H. Yu, J. Liu, W. Huang, D. Y. Wang and Y. Wang, Chem. Eng. J., 2024, 482, 148949 CrossRef CAS.
- S. Jung, U. Zafar, L. S. K. Achary and C. M. Koo, EcoMat, 2023, e12395, DOI:10.1002/eom2.12395.
- C. Liu, R. Zhang, Y. Wang, C. Wei, F. Li, N. Qing and L. Tang, Mater. Horiz., 2023, 10, 3488–3498 RSC.
- X. Zou, X. Wang, M. Gou, O. Yue, Z. Bai, H. Zhang and X. Liu, J. Mater. Chem. A, 2022, 10, 14555–14567 RSC.
- B.-Y. Lai, S.-N. Lai, H.-Y. Lin and J. M. Wu, Nano Energy, 2024, 125, 109554 CrossRef CAS.
- X. Chang, Q. Wu, Y. Wu, X. Xi, J. Cao, H. Chu, Q. Liu, Y. Li, W. Wu, X. Fang and F. Chen, Nano Lett., 2022, 22, 8321–8330 CrossRef CAS PubMed.
- Q. Gao, X. Wang, D. W. Schubert and X. Liu, Macromol. Mater. Eng., 2025, 2400357, DOI:10.1002/mame.202400357.
- Y. Zhang, J. Zou, S. Wang, X. Hu, Z. Liu, P. Feng, X. Jing and Y. Liu, Compos. B Eng., 2024, 272, 111191 CrossRef CAS.
- C. Xu, Z. Li, T. Hang, Y. Chen, T. He, X. Li, J. Zheng and Z. Wu, Adv. Sci., 2024, 2403551, DOI:10.1002/advs.202403551.
- H. Chen, S. Guo, S. Zhang, Y. Xiao, W. Yang, Z. Sun, X. Cai, R. Fang, H. Wang, Y. Xu, J. Wang and Z. Li, Energy Environ. Mater., 2024, 7, e12654 CrossRef CAS.
- H. Zeng, L. Zhang, T. Wu, H. Song, Y. Wan and M. Zhang, ACS Appl. Nano Mater., 2025, 589–601, DOI:10.1021/acsanm.4c05875.
- Q. Zhang, T. Wang, R. Du, J. Zheng, H. Wei, X. Cao and X. Liu, ACS Appl. Mater. Interfaces, 2024, 16, 40069–40076 CrossRef CAS PubMed.
- J. Chen, F. Wang, G. Zhu, C. Wang, X. Cui, M. Xi, X. Chang and Y. Zhu, ACS Appl. Mater. Interfaces, 2021, 13, 51567–51577 CrossRef CAS PubMed.
- J. Yang, L. Chang, X. Zhang, Z. Cao and L. Jiang, Nano-Micro Lett., 2024, 16, 140 CrossRef CAS PubMed.
- Y. Luo, M. Yu, Y. Zhang, Y. Wang, L. Long, H. Tan, N. Li, L. Xu and J. Xu, Nano Energy, 2022, 104, 107955 CrossRef CAS.
- C. Qiu, M. He, S. Xu, A. M. Ali, L. Shen and J. Wang, Int. J. Biol. Macromol., 2024, 269, 131825 CrossRef CAS PubMed.
- R. Zhang and H. Olin, ACS Nanosci. Au, 2022, 2, 12–31 CrossRef CAS PubMed.
- S. K. Maity, U. Tyagi, A. K. Sharma, P. Bisht, S. Sirohi, K. Kumar, N. Sheoran, S. Singh and G. Kumar, Cellulose, 2025, 32, 1787–1804 CrossRef CAS.
- B. Xie, Y. Guo, Y. Chen, H. Zhang, J. Xiao, M. Hou, H. Liu, L. Ma, X. Chen and C. Wong, Nano-Micro Lett., 2024, 17, 17 CrossRef PubMed.
- Y. Wang, H.-K. Peng, T.-T. Li, B.-C. Shiu, H.-T. Ren, X. Zhang, C.-W. Lou and J.-H. Lin, Chem. Eng. J., 2021, 412, 128681 CrossRef CAS.
- W. He, S. Li, P. Bai, D. Zhang, L. Feng, L. Wang, X. Fu, H. Cui, X. Ji and R. Ma, Nano Energy, 2022, 96, 107109 CrossRef CAS.
- A. Baburaj, S. K. Naveen Kumar, A. K. Aliyana, M. Banakar, S. Bairagi and G. Stylios, Nano Energy, 2023, 118, 108983 CrossRef CAS.
- X. Yang, F. Wu, C. Xu, L. Yang and S. Yin, J. Alloys Compd., 2022, 928, 167137 CrossRef CAS.
- X. Cai, Y. Xiao, B. Zhang, Y. Yang, J. Wang, H. Chen and G. Shen, Adv. Funct. Mater., 2023, 2304456, DOI:10.1002/adfm.202304456.
- R. A. John, N. Shah, S. K. Vishwanath, S. E. Ng, B. Febriansyah, M. Jagadeeswararao, C.-H. Chang, A. Basu and N. Mathews, Nat. Commun., 2021, 12, 3681 CrossRef CAS PubMed.
- B. Lee, J.-Y. Oh, H. Cho, C. W. Joo, H. Yoon, S. Jeong, E. Oh, J. Byun, H. Kim, S. Lee, J. Seo, C. W. Park, S. Choi, N.-M. Park, S.-Y. Kang, C.-S. Hwang, S.-D. Ahn, J.-I. Lee and Y. Hong, Nat. Commun., 2020, 11, 663 CrossRef CAS PubMed.
- H. Fang, H. Tian, J. Li, Q. Li, J. Dai, T.-L. Ren, G. Dong and Q. Yan, Nano Energy, 2016, 20, 48–56 CrossRef CAS.
- M. Gu, Y. Chen, S. Gu, C. Wang, L. Chen, H. Shen, G. Chen, X. Sun, H. Huang, Y. Zhou and Z. Wen, Nano Energy, 2022, 98, 107308 CrossRef CAS.
- W. Yang, H. Chen, M. Wu, Z. Sun, M. Gao, W. Li, C. Li, H. Yu, C. Zhang, Y. Xu and J. Wang, Adv. Mater. Interfaces, 2022, 2102124, DOI:10.1002/admi.202102124.
- C. Xing, Y. Tian, Z. Yu, Z. Li, B. Meng and Z. Peng, ACS Appl. Mater. Interfaces, 2022, 14, 36741–36752 CrossRef CAS PubMed.
- L. Zhou, C. Duan, H. Liu, Z. Jia, H. Zhang, X. Han, L. Dai and S. Yu, Int. J. Biol. Macromol., 2025, 291, 139055 CrossRef PubMed.
- D. Wang, D. Zhang, H. Zhang, Z. Wang, J. Wang and G. Xi, Sens. Actuators, B, 2024, 417, 136101 CrossRef CAS.
- H. Fan, Q. Li, K. Li, C. Hou, Q. Zhang, Y. Li and H. Wang, Sci. China Mater., 2020, 63, 2582–2589 CrossRef CAS.
- W. Chen, L.-X. Liu, H.-B. Zhang and Z.-Z. Yu, ACS Nano, 2021, 15, 7668–7681 CrossRef CAS PubMed.
- K. B. R. Teodoro, R. C. Sanfelice, F. L. Migliorini, A. Pavinatto, M. H. M. Facure and D. S. Correa, ACS Sens., 2021, 6, 2473–2496 CrossRef CAS PubMed.
- M. Wu, Z. Gao, K. Yao, S. Hou, Y. Liu, D. Li, J. He, X. Huang, E. Song, J. Yu and X. Yu, Mater. Today Energy, 2021, 20, 100657 CrossRef CAS.
- D. Shindell and C. J. Smith, Nature, 2019, 573, 408–411 CrossRef CAS PubMed.
- Q. Zhou, J. Pan, S. Deng, F. Xia and T. Kim, Adv. Mater., 2021, 2008276, DOI:10.1002/adma.202008276.
- J. Zhao and Y. Shi, Adv. Funct. Mater., 2023, 2213407, DOI:10.1002/adfm.202213407.
- Y. Feng, M. He, X. Liu, W. Wang, A. Yu, L. Wan and J. Zhai, Nanoscale Res. Lett., 2021, 16, 81 CrossRef CAS PubMed.
- S. Wang, Z. Chen, H. Zhou, X. Fu, B. Chen, F. Wang, A. Liu, W. Guo and M. Ye, ACS Appl. Electron. Mater., 2024, 6, 3491–3500 CrossRef CAS.
- J. Xie, Y. Wang, L. Lu, L. Liu, X. Yu and F. Pei, Ageing Res. Rev., 2021, 70, 101413 CrossRef CAS PubMed.
- H. Yang, Z. Yu, S. Ji, J. Yan, Y. kong, Q. Huo, Z. Zhang, Y. Niu and Y. Liu, Adv. Funct. Mater., 2022, 2207637, DOI:10.1002/adfm.202207637.
- Z. Shen, Z. Zhang, N. Zhang, J. Li, P. Zhou, F. Hu, Y. Rong, B. Lu and G. Gu, Adv. Mater., 2022, 2203650, DOI:10.1002/adma.202203650.
- Z. Gao, Y. Zhou, J. Zhang, J. Foroughi, S. Peng, R. H. Baughman, Z. L. Wang and C. H. Wang, Adv. Mater., 2024, 2404492, DOI:10.1002/adma.202404492.
- X. Zhou, X.-A. Ye, X. Zhang, D. Wen, H. Wang and G.-G. Wang, Chem. Eng. J., 2025, 503, 158401 CrossRef CAS.
- Y. Liu, J. Ping and Y. Ying, Adv. Funct. Mater., 2021, 2009994, DOI:10.1002/adfm.202009994.
- S. Li, J. Nie, Y. Shi, X. Tao, F. Wang, J. Tian, S. Lin, X. Chen and Z. L. Wang, Adv. Mater., 2020, 2001307, DOI:10.1002/adma.202001307.
- R. A. Dickman and D. S. Aga, J. Hazard. Mater., 2022, 436, 129120 CrossRef CAS PubMed.
- S. Zhang, M. Guo, Y. Xia, S. Li, X. Zhi and X. Wang, Chem. Eng. J., 2025, 505, 159562 CrossRef CAS.
- Y. Tao, H. Xiang, X. Cao and N. Wang, ACS Appl. Mater. Interfaces, 2024, 16, 3406–3415 CrossRef CAS PubMed.
- O. Faruk, M. R. Islam, S. M. S. Rana, G. B. Pradhan, H. Kim, M. Asaduzzaman, T. Bhatta and J. Y. Park, Nano Energy, 2024, 127, 109787 CrossRef CAS.
- Z. Wang, C. Hao, M. Cai, J. Cui, Y. Zheng and C. Xue, Nano Res., 2024, 17, 4151–4162 CrossRef CAS.
- Y. Ma, B. Li, G. Ren, Z. Wang, S. Zhou, Q. Hu and C. Rensing, Biosens. Bioelectron., 2024, 247, 115924 CrossRef CAS PubMed.
- N. Dai, X. Guan, C. Lu, K. Zhang, S. Xu, I. M. Lei, G. Li, Q. Zhong, P. Fang and J. Zhong, ACS Nano, 2023, 17, 24814–24825 CrossRef CAS PubMed.
- Y. Yan, H. Han, Y. Dai, H. Zhu, W. Liu, X. Tang, W. Gan and H. Li, ACS Appl. Nano Mater., 2021, 4, 11763–11769 CrossRef CAS.
- C. Liu, L. Jiang, O. Yue, Y. Feng, B. Zeng, Y. Wu, Y. Wang, J. Wang, L. Zhao, X. Wang, C. Shao, Q. Wu and X. Sun, Adv. Compos. Hybrid Mater., 2023, 6, 112 CrossRef CAS.
- G. Xiao, J. Ju, M. Li, H. Wu, Y. Jian, W. Sun, W. Wang, C. M. Li, Y. Qiao and Z. Lu, Biosens. Bioelectron., 2023, 235, 115389 CrossRef CAS PubMed.
- H. Zhang, X. Gong and X. Li, J. Mater. Chem. A, 2023, 11, 24454–24481 RSC.
- S. Zhang, T. Jiang, M. Li, H. Sun, H. Wu, W. Wu, Y. Li and H. Jiang, Nano Energy, 2024, 131, 110214 CrossRef CAS.
- S. He, Y. Gui, Y. Wang, L. Cao, G. He and C. Tang, ACS Sens., 2024, 9, 1188–1198 CrossRef CAS PubMed.
- S. Sardana, P. Mahajan, A. Mishra, A. K. Chawla and A. Mahajan, Adv. Mater. Technol., 2025, 2400829, DOI:10.1002/admt.202400829.
- L. Liu, W. Zhu, H. Ma and J. Zhou, APL Mater., 2025, 13 DOI:10.1063/5.0250284.
- B. Mahanty, S. K. Ghosh and D.-W. Lee, Compos. B Eng., 2025, 291, 111995 CrossRef CAS.
- R. Yang, Heliyon, 2024, 10, e32361 CrossRef CAS PubMed.
- G. M. Rani, S. M. Ghoreishian, K. S. Ranjith, S. H. Park, M. Lee, R. Umapathi, Y. Han and Y. S. Huh, Adv. Mater. Technol., 2023, 2300685, DOI:10.1002/admt.202300685.
- J. Zhu, M. Zhu, Q. Shi, F. Wen, L. Liu, B. Dong, A. Haroun, Y. Yang, P. Vachon, X. Guo, T. He and C. Lee, EcoMat, 2020, e12058, DOI:10.1002/eom2.12058.
- B. Anasori, M. R. Lukatskaya and Y. Gogotsi, Nat. Rev. Mater., 2017, 2, 16098 CrossRef CAS.
- M. Zhao, X. Xie, C. E. Ren, T. Makaryan, B. Anasori, G. Wang and Y. Gogotsi, Adv. Mater., 2017, 1702410, DOI:10.1002/adma.201702410.
- Y. Li, Y. Luo, H. Deng, S. Shi, S. Tian, H. Wu, J. Tang, C. Zhang, X. Zhang, J. Zha and S. Xiao, Adv. Mater., 2024, 2314380, DOI:10.1002/adma.202314380.
- Y. Xiong, Z. Huo, J. Zhang, Y. Liu, D. Yue, N. Xu, R. Gu, L. Wei, L. Luo, M. Chen, C. Liu, Z. L. Wang and Q. Sun, Nano Energy, 2024, 124, 109465 CrossRef CAS.
- H. Kim, G. Zan, Y. Seo, S. Lee and C. Park, Adv. Funct. Mater., 2024, 2308703, DOI:10.1002/adfm.202308703.
- W. Li, Y. Xiang, W. Zhang, K. Loos and Y. Pei, Nano Energy, 2023, 113, 108539 CrossRef CAS.
- R. Yang, X. Chen, W. Ke and X. Wu, Nanomaterials, 2022, 12, 1907 CrossRef CAS PubMed.
- K. Li, S. Gong, S. Fu, H. Guo, C. Shan, H. Wu, J. Wang, S. Xu, G. Li, Q. Zhao, X. Wang and C. Hu, Energy Environ. Sci., 2024, 17, 8942–8953 RSC.
- A. Mondal, M. Faraz, M. Dahiya and N. Khare, ACS Appl. Mater. Interfaces, 2024, 16, 50659–50670 CrossRef CAS PubMed.
- S. Tremmel, X. Luo, B. Rothammer, A. Seynstahl, B. Wang, A. Rosenkranz, M. Marian and L. Zhu, Nano Energy, 2022, 97, 107185 CrossRef CAS.
- Y. Long, Z. Wang, F. Xu, B. Jiang, J. Xiao, J. Yang, Z. L. Wang and W. Hu, Small, 2022, 2203956, DOI:10.1002/smll.202203956.
- A. Baburaj, S. Banerjee, A. K. Aliyana, C. Shee, M. Banakar, S. Bairagi, S. K. Naveen Kumar, S. W. Ali and G. K. Stylios, Nano Energy, 2024, 127, 109785 CrossRef CAS.
- M. Azeem, M. Shahid, I. Masin and M. Petru, J. Text. Inst., 2025, 116, 80–95 CrossRef.
- Vidyasagar, R. R. Patel, S. K. Singh and M. Singh, Mater. Adv., 2023, 4, 1831–1849 RSC.
- J. Tian, R. Shi, Z. Liu, H. Ouyang, M. Yu, C. Zhao, Y. Zou, D. Jiang, J. Zhang and Z. Li, Nano Energy, 2019, 59, 705–714 CrossRef CAS.
- G. Thakral, J. LaFontaine, B. Najafi, T. K. Talal, P. Kim and L. A. Lavery, Diabet. Foot Ankle, 2013, 4, 22081 CrossRef PubMed.
- P. Zhao, Y. Zhang, X. Chen, C. Xu, J. Guo, M. Deng, X. Qu, P. Huang, Z. Feng and J. Zhang, Adv. Sci., 2023, 2206585, DOI:10.1002/advs.202206585.
- H. Fu, K. Xue, Y. Zhang, M. Xiao, K. Wu, L. Shi and C. Zhu, Adv. Sci., 2023, 2206865, DOI:10.1002/advs.202206865.
- R. Kotsifaki, V. Korakakis, E. King, O. Barbosa, D. Maree, M. Pantouveris, A. Bjerregaard, J. Luomajoki, J. Wilhelmsen and R. Whiteley, Br. J. Sports Med., 2023, 57, 500–514 CrossRef PubMed.
- T. Tan, A. A. Gatti, B. Fan, K. G. Shea, S. L. Sherman, S. D. Uhlrich, J. L. Hicks, S. L. Delp, P. B. Shull and A. S. Chaudhari, npj Digit. Med., 2023, 6, 46 CrossRef PubMed.
- H. Zhang, H. Sun, J. Li, Z. Lv, Y. Tian and X. Lei, Prog. Neuro-Psychopharmacol. Biol. Psychiatry, 2025, 136, 111209 CrossRef CAS PubMed.
- I. Hussain, M. A. Hossain, R. Jany, M. A. Bari, M. Uddin, A. R. M. Kamal, Y. Ku and J.-S. Kim, Sensors, 2022, 22, 3079 CrossRef PubMed.
- Y. Lei, X. Wang, J. Liao, J. Shen, Y. Li, Z. Cai, N. Hu, X. Luo, W. Cui and W. Huang, Bioact. Mater., 2022, 16, 472–484 CAS.
- H. Yuan, L. L. E. Mears, Y. Wang, R. Su, W. Qi, Z. He and M. Valtiner, Adv. Colloid Interface Sci., 2023, 311, 102814 CrossRef CAS PubMed.
- Y.-H. Chang, L.-Y. Chang, C.-C. Chang, Y.-S. Chiu, P. Kanokpaka, K.-C. Ho, H. Mizuguchi and M.-H. Yeh, Nano Energy, 2024, 120, 109114 CrossRef CAS.
- S. K. Chittibabu and K. Chintagumpala, Microelectron. Eng., 2023, 276, 112013 CrossRef CAS.
- M. D. Santos, C. Roman, M. A. F. Pimentel, S. Vollam, C. Areia, L. Young, P. Watkinson and L. Tarassenko, Front. Digit. Health., 2021, 630273, DOI:10.3389/fdgth.2021.630273.
- S. S. Mirbakht, A. Golparvar, M. Umar, B. A. Kuzubasoglu, F. S. Irani and M. K. Yapici, Adv. Sci., 2025, 2405988, DOI:10.1002/advs.202405988.
- H. Yu, N. Li and N. Zhao, Adv. Energy Mater., 2021, 2002646, DOI:10.1002/aenm.202002646.
- H. Chen, S. Guo, S. Zhang, Y. Xiao, W. Yang, Z. Sun, X. Cai, R. Fang, H. Wang, Y. Xu, J. Wang and Z. Li, Energy Environ. Mater., 2024, e12654, DOI:10.1002/eem2.12654.
- A. Al Fahoum, A. Al Omari, G. Al Omari and A. Zyout, Heliyon, 2024, 10, e39745 CrossRef PubMed.
- T. Ito, K. Noritake, Y. Ito, H. Tomita, J. Mizusawa, H. Sugiura, N. Matsunaga, N. Ochi and H. Sugiura, Sci. Rep., 2022, 12, 7822 CrossRef PubMed.
- H. Zhou, Y. Gui, G. Gu, H. Ren, W. Zhang, Z. Du and G. Cheng, Small, 2025, 21, 2405064 CrossRef CAS PubMed.
- A. Zarepour, N. Rafati, A. Khosravi, N. Rabiee, S. Iravani and A. Zarrabi, Nanoscale Adv., 2024, 6, 3513–3532 RSC.
- Q. Yi, X. Pei, P. Das, H. Qin, S. W. Lee and R. Esfandyarpour, Nano Energy, 2022, 107511 CrossRef CAS.
- H. Cui, M. Ran, X. Peng and G. Zhang, J. Environ. Chem. Eng., 2024, 12, 112047 CrossRef CAS.
- M. A. Belal, S. Hajra, S. Panda, K. R. Kaja, M. M. M. Abdo, A. Abd El-Moneim, D. Janas, Y. K. Mishra and H. J. Kim, J. Mater. Chem. A, 2025 Search PubMed.
- C. Cai, J. Mo, Y. Lu, N. Zhang, Z. Wu, S. Wang and S. Nie, Nano Energy, 2021, 83, 105833 CrossRef CAS.
- Z. Wen, J. Chen, M.-H. Yeh, H. Guo, Z. Li, X. Fan, T. Zhang, L. Zhu and Z. L. Wang, Nano Energy, 2015, 16, 38–46 CrossRef CAS.
- L. T. Nhiem, J. Mao, Q. T. Hoai Ta and S. Seo, Nanoscale Adv., 2025 Search PubMed.
- X. Li, X. Gong, H. Zhang, C. He, J. Ye and X. Wang, Langmuir, 2025, 41, 955–963 CrossRef CAS PubMed.
- D. Xiong, M. Luo, Q. He, X. Huang, S. Cai, S. Li, Z. Jia and Z. Gao, Talanta, 2025, 286, 127446 CrossRef CAS PubMed.
- C. Chen, G. Xie, J. Dai, W. Li, Y. Cai, J. Li, Q. Zhang, H. Tai, Y. Jiang and Y. Su, Nano Energy, 2023, 116, 108788 CrossRef CAS.
- S. J. Kim, H.-J. Koh, C. E. Ren, O. Kwon, K. Maleski, S.-Y. Cho, B. Anasori, C.-K. Kim, Y.-K. Choi, J. Kim, Y. Gogotsi and H.-T. Jung, ACS Nano, 2018, 12, 986–993 CrossRef CAS PubMed.
- M. Klimczyk, A. Siczek and L. Schimmelpfennig, Sci. Total Environ., 2021, 771, 145483 CrossRef CAS PubMed.
- X. Luo, M. Zhang, Y. Ni and G. Shen, Environ. Technol. Innov., 2025, 37, 103995 CrossRef CAS.
- J. Li, S. Xie, W. Zhu, W. Di and L. Gong, J. Environ. Chem. Eng., 2025, 13, 115294 CrossRef CAS.
- G. Li, X. Li, J. Li, Z. Lv, H. Wang, R. Gao and L. Luo, Sustain. Chem. Pharm., 2021, 24, 100516 CrossRef CAS.
- F. R. Thewes, A. Brackmann, V. Both, V. Ludwig, L. M. Wendt, F. R. Thewes and F. J. Soldateli, Postharvest Biol. Technol., 2023, 197, 112209 CrossRef CAS.
- T. Chen and X. Liang, AIP Adv., 2024, 14 DOI:10.1063/5.0191225.
- D. Xu, X. Ma and Y. Ma, AIP Adv., 2025, 15(1), 015229 CrossRef CAS.
- Z. Otgonbayar and W.-C. Oh, FlatChem, 2023, 40, 100524 CrossRef CAS.
- H. Espinosa, A. Mears, A. Stamm, Y. Ohgi and C. Coniglio, Sports Eng., 2025, 28, 4 CrossRef.
- H. Xu, Procedia Comput. Sci., 2024, 247, 752–759 CrossRef.
- X. U. Jie, Therm. Sci. Eng. Prog., 2025, 58, 103234 CrossRef.
- C. Midoglu, A. Kjæreng Winther, M. Boeker, S. Dahl Pettersen, S. Pedersen, N. Ragab, T. Kupka, S. A. Hicks, M. Bredsgaard Randers, R. Jain, H. J. Dagenborg, S. A. Pettersen, D. Johansen, M. A. Riegler and P. Halvorsen, Sci. Data, 2024, 11, 553 CrossRef PubMed.
- A. Usher and J. Babraj, Eur. J. Appl. Physiol., 2024, 124, 595–606 CrossRef PubMed.
- J. Zhang, Y. Ren, L. Lin, Y. Xing and J. Ren, Sci. Rep., 2024, 14, 3549 CrossRef CAS PubMed.
- S. Atkare, C. S. Rout and S. Jagtap, Mater. Adv., 2024, 5, 1440–1453 RSC.
- Z. Zhang and J. Cai, ChemNanoMat, 2024, 202300614 CrossRef.
- I. Lee and K. Lee, Bus. Horiz., 2015, 58, 431–440 CrossRef.
- G. Zhao, F. Qian, X. Li, Y. Tang, Y. Sheng, H. Li, J. Rao, M. V. Singh, H. Algadi, M. Niu, W. Zhang, Z. Guo, X. Peng and T. Chen, Adv. Compos. Hybrid Mater., 2023, 6, 184 CrossRef CAS.
- H. Wu, Z. Wang, B. Zhu, H. Wang, C. Lu, M. Kang, S. Kang, W. Ding, L. Yang, R. Liao, J. Wang and Z. L. Wang, Adv. Energy Mater., 2023, 13, 2300051 CrossRef CAS.
- T. Bektaş, J. F. Ehmke, H. N. Psaraftis and J. Puchinger, Eur. J. Oper. Res., 2019, 274, 807–823 CrossRef.
- A. Natarajan, V. Krishnasamy and M. Singh, Renew. Sustain. Energy Rev., 2022, 167, 112731 CrossRef.
- Y. Zhang, J. Chong, Y. Mao, X. Gao, J. He, H. Wang, S. Guo and H. Zheng, Nanoenergy Adv., 2024, 4, 97–109 CrossRef.
- S. Hajra, V. Vivekananthan, M. Sahu, G. Khandelwal, N. P. M. Joseph Raj and S.-J. Kim, Nano Energy, 2021, 85, 105964 CrossRef CAS.
- A. Ganeshkumar, K. Pazhanivel, N. Ramadoss and M. Arivanandhan, Carbon Lett., 2022, 32, 753–765 CrossRef.
- D. Tao, P. Su, A. Chen, D. Gu, M. Eginligil and W. Huang, npj Flex. Electron, 2025, 9, 4 CrossRef CAS.
- A. Jalali, T. Gupta, V. Pakharenko, Z. Ben Rejeb, M. Kheradmandkeysomi, M. Sain and C. B. Park, Carbohydr. Polym., 2025, 352, 123252 CrossRef CAS PubMed.
- Y. Yang, L. Shao, J. Wang, W. Wang, C. Su, C. Li, H. Di, J. Ma and Z. Ji, Compos. Commun., 2025, 54, 102267 CrossRef.
- C. Wang, Y. Wang, F. Zou, B. Fang, J. Zhao, H. Zhang, J. Guo, L. Jia and D. Yan, Compos. B Eng., 2025, 291, 112043 CrossRef.
- C. Li, L. Qi, J. Fei, J. Yan, Z. Wu, T. Zhang and H. Li, Carbon, 2024, 217, 118620 CrossRef CAS.
- H. Guo, H. Feng, T. Liu and T. Kuang, Polymer, 2025, 316, 127891 CrossRef CAS.
- H. Tan, J. Gou, X. Zhang, L. Ding and H. Wang, J. Membr. Sci., 2023, 675, 121560 CrossRef CAS.
- M. Han, C. E. Shuck, R. Rakhmanov, D. Parchment, B. Anasori, C. M. Koo, G. Friedman and Y. Gogotsi, ACS Nano, 2020, 14, 5008–5016 CrossRef CAS PubMed.
- Y.-R. Zhang, B.-C. Wang, S.-L. Gao, L.-P. Qiu, Q.-H. Zheng, G.-T. Cheng, W.-P. Han, S. Ramakrishna and Y.-Z. Long, ACS Appl. Nano Mater., 2022, 5, 12320–12342 CrossRef CAS.
- D. R. Yao, I. Kim, S. Yin and W. Gao, Adv. Mater., 2024, 36, 2308829 CrossRef CAS PubMed.
- C. Chen, S. Ding and J. Wang, Nat. Rev. Mater., 2024, 9, 159–172 CrossRef.
- M. A. McEvoy and N. Correll, Science, 2015, 347, 1261689 CrossRef CAS PubMed.
- Y. Fu, H. Wang, Y. Zi and X. Liang, Nano Energy, 2021, 89, 106368 CrossRef CAS.
- Y. Lee, Z. Ren, Y.-H. Hsiao, S. Kim, W. J. Song, C. Lee and Y. Chen, Nano Energy, 2024, 126, 109602 CrossRef CAS.
- M. Guo, X. Yang, J. Yan, Z. An, L. Wang, Y. Wu, C. Zhao, D. Xiang, H. Li, Z. Li and H. Zhou, J. Mater. Chem. A, 2022, 10, 16095–16105 RSC.
- P. Zhou, J. Lin, W. Zhang, Z. Luo and L. Chen, Adv. Sci., 2022, 9, 2104270 CrossRef CAS PubMed.
- X. Li, W. Wan, G. Bai, Y. Zhao, X. Shi and J. Zhu, Sci. Rep., 2025, 15, 470 CrossRef CAS PubMed.
- X. Tongqiang, L. Diao, L. Xiaolin, Y. Xin and J. G. Wang, Appl. Energy, 2024, 353, 122147 CrossRef.
- C. Jiang, X. Li, Y. Yao, L. Lan, Y. Shao, F. Zhao, Y. Ying and J. Ping, Nano Energy, 2019, 66, 104121 CrossRef CAS.
|
This journal is © The Royal Society of Chemistry 2025 |
Click here to see how this site uses Cookies. View our privacy policy here.