DOI:
10.1039/B9NR00225A
(Paper)
Nanoscale, 2010,
2, 394-398
The effects of substitution of Cr for Mo on the mechanical properties of nanocrystalline Mo5Si3 films
Received
18th August 2009
, Accepted 29th October 2009
First published on 19th November 2009
Abstract
A series of nanocrystalline (MoxCr1−x)5Si3 films with an average grain size of 8 nm has been prepared on Ti-6A1-4V alloy substrates by glow discharge. The effect of substitution of Cr for Mo on the hardness, elastic modulus and plastic deformability of the nanocrystalline (MoxCr1−x)5Si3 film was investigated using the nanoindentation method. The results reveal that the hardness of nanocrystalline (MoxCr1−x)5Si3 films slightly decreases with increasing Cr content. In contrast, the plastic deformability significantly increases with increasing Cr content.
1. Introduction
Refractory metal silicides are of interest as high-temperature structural materials because of their ultra-high melting temperatures, and chemical stability and strength at elevated temperatures.1–3 Compared with other refractory metals, molybdenum silicide-based intermetallic compounds are one of the most attractive material systems because Mo has a lower density.4 Among the compounds of molybdenum silicides, D8m-structured Mo5Si3 is the most refractory compound having a melting point of 2180 °C, thus having great potential for structural applications in harsh environments.5–7 Unfortunately, there are still some drawbacks which have hindered their use as structural materials. Firstly, similar to most high-temperature intermetallics, Mo5Si3 is intrinsically brittle at ambient temperatures.8 Secondly, owing to its non-cubic tetragonal crystal structure, its coefficient of thermal expansion (CTE) is highly anisotropic.9 Thirdly, it suffers from severe oxidation at intermediate temperatures (around 800 °C).10 Considerable effort has been made in order to overcome these obstacles, either by substitutional alloying, or by microstructure control including in situ composites.11–13 To the best of our knowledge, there were no reports available in the literature with regard to the mechanical properties of nanocrystalline (MoxCr1−x)5Si3 either as a bulk or coating material. In our previous work,14,15 we found that the double-cathode glow discharge technique can be used to synthesize nanocrystalline Al2Mg and Cr3Si films with a grain size of <5 nm on magnesium alloy and titanium alloy, respectively. In this paper, (MoxCr1−x)5Si3 (x = 1, 0.78, 0.75, 0.64, 0.57) films with an average grain size of about 8 nm were deposited onto Ti-6A1-4V alloy substrates by glow discharge. The aim of this investigation is to explore the coupling effect of nanosize crystals and substitution of Cr for Mo on the mechanical properties of nanocrystalline Mo5Si3 films.
The nanocrystalline (MoxCr1−x)5Si3 films were deposited onto Ti-6A1-4V alloy substrates by a double-cathode glow discharge apparatus which was described in our previous papers.14 In the process of double-cathode glow discharge, one cathode is the source (target) composed of the desired sputtering materials, and the other cathode is the substrate material. When two different voltages are applied to the two cathodes, glow discharge occurs. The glow-discharge sputtering conditions are: base pressure, 4 × 10−4 Pa; target electrode bias voltage, − 900 V; substrate bias voltage, −350 V; substrate temperature, 900 °C; working pressure, 35 Pa; parallel distance between the source electrode and the substrate, 15 mm and treatment time 3 h. The sputter targets were fabricated by employing cold compacting technology under a pressure of 600 MPa from ball-milled Mo (99.99% purity), Cr (99.99% purity) and Si powders (99.99% purity). The substrates were Ti-6Al-4V alloy discs of 40 mm diameter and 3 mm thickness. The substrates were mechanically ground and progressively polished with a diamond paste. The polished substrates were then washed in acetone and ethanol using an ultrasonic washer. Five kinds of (MoxCr1−x)5Si3 (x = 1, 0.78, 0.75, 0.64, 0.57) films were deposited onto the substrate material using the double-cathode glow discharge method using five targets with different stoichiometric ratios (Mo50Si50, Mo40Cr10Si50, Mo35Cr15Si50, Mo30Cr20Si50 and Mo25Cr25Si50), respectively.
Phase composition of the as-deposited films was characterized with X-ray diffraction (XRD, D8ADVANCE) operated at 35 kV and 40 mA, respectively. X-Ray data were collected using a 0.1° step scan with a count time of 1 s. The etching of the (MoxCr1−x)5Si3 films was accomplished with the use of Kroll's reagent (10 ml HNO3, 4 mL HF and 86 mL distilled water) for 20–30 s. The cross-sectional morphology and chemical composition of the as-deposited films were studied by scanning electron microscopy (SEM, Quanta200, FEI Company) and energy-dispersive X-ray spectroscopy (EDX), respectively. Transmission electron microscopy (TEM) and high-resolution transmission electron microscopy (HRTEM) images were observed using a JEOL JEM-2010 at an accelerating voltage of 200 kV. Thin foils samples for TEM observation were cut from as-deposited film and were prepared by single-jet electropolishing from the untreated side of the substrate.
The nanohardness and the Young's modulus of as-deposited film were obtained using a nanoindentation tester (NHT) equipped with a Berkovich tip. This system, developed by CSEM Instruments, comprises two distinct components: a measuring head for performing nanoindentations and an optical microscope for selecting a specific sample site prior to indentation, and for checking the location of the imprint after indentation. The system has the load and displacement resolutions of 10 mN and 1 nm, respectively. Fused silica was used as a standard sample for the initial tip calibration. The indentation was worked by driving the indenter at a constant loading rate of 40 mN min−1 into the materials with the maximum applied load of 20 mN. The standard analysis procedure proposed by Oliver and Pharr16 was used to determine the hardness of the specimens from the unloading curve. For each indentation displacement, nanoindentation tests were conducted at five different locations to ensure the repeatability of the experimental data. After nanoindentation, the topography of the indents was immediately examined using the attached atomic force microscope (AFM).
3. Results
3.1 Microstructures and phase analysis
The X-ray diffraction patterns of the five kinds of sputter-deposited (MoxCr1−x)5Si3(x = 1, 0.78, 0.75, 0.64, 0.57) films are presented in Fig. 1(a). The diffraction patterns are characterized by a set of broad peaks indexed as the D8m-structured Mo5Si3 phase (JCPDS Card No.76-1578), indicating that all the sputter-deposited films consist of a single phase of (MoxCr1−x)5Si3, and phase composition of the as-deposited films is independent of the substitution of Cr for Mo. This is due to the fact that the chemical bonding of Cr atoms in the D8m system is considered to be similar to that of Mo atoms. Thereby, the formation of second phases never occurs with the substitution of Cr for Mo in Mo5Si3. Furthermore, it is noticed that only some changes of main peak positions are observed. With the increasing addition of Cr to Mo5Si3, the (MoxCr1−x)5Si3 peaks are incessantly shifted to higher Bragg angles, compared with the powder diffraction file (PDF) data for Mo5Si3, resulting from the difference of lattice parameters between Mo5Si3 and Cr5Si3. This is in accordance with the results reported in ref. 17. Meanwhile, when as value of x decreases, the lattice constants of (MoxCr1−x)5Si3 are found to simultaneously decrease in both c- and a-directions as does the a/c axial ratio, as shown in Fig. 1(b). Because the microstructural characteristics of the five kinds of (MoxCr1−x)5Si3 films bear a strong resemblance, only those of Mo5Si3 films are illuminated for the sake of space in the paper. Fig. 2(a) shows the SEM cross-sectional morphology of a sputter-deposited Mo5Si3 film formed on Ti-6Al-4V alloy. Clearly, the film is free of cracks and appears compact and quite well adhered to the Ti-6Al-4V alloy substrate. The microstructure of the film can be classified into three different sublayers. Curve 2 in Fig. 1(a) is the typical X-ray diffraction (XRD) pattern of a sample that has been removed from a film for understanding the phase composition of the diffusion layer of the underlying film. A comparison between curve 1 and curve 2 shows that the diffusion layer of the underlying film is a composite of β-Ti, α′′ and α′ phases. Because the dominant diffusion element in the Mo5Si3 phase is Mo,18 Mo atoms diffuses inwards to the interface between the outer layer and substrate, leading to the phase transformation β → α′′ → α′, occurring from outside to inside for the different Mo content in the diffusion layer.19 Combining the XRD results and EDX analysis, conclusions can be made that the outer deposition layer with thickness about 13 μm consists of a single Mo5Si3 phase with a Mo:Si atomic ratio approaching 1.66 and that, according to the different Mo content, the Mo diffusion layer may be subdivided into a β-phase layer with high Mo content (>10 wt%) and an α′′/α′ layer with low Mo content (10 wt%), as shown in Fig. 2(a). Fig. 2(b) shows a typical HRTEM image and selected-area diffraction (SAED) pattern of a Mo5Si3 film. As can be seen from Fig. 2(b), the microstructure is composed of randomly oriented spherical crystallites with average grain size ∼8 nm. The space of the lattice fringes of the nanocrystalline film marked A and B can be calculated as 0.211 nm and 0.168 nm, which correspond to the spacing of the (411) and (521) planes of D8m-structured Mo5Si3, respectively. The diffraction rings of the SAED pattern [inset in Fig. 2(b)] correspond to the (220), (310), (411), (431) and (521) planes of the D8m crystal structure of Mo5Si3, respectively.
![(a) XRD pattern of the sputter-deposited (MoxCr1−x)5Si3 films; (b) lattice parameters and a/c axial ratio [upper right-hand inset in Fig. 1(b)] as a function of the content of Cr in the as-deposited films.](/image/article/2010/NR/b9nr00225a/b9nr00225a-f1.gif) |
| Fig. 1 (a) XRD pattern of the sputter-deposited (MoxCr1−x)5Si3 films; (b) lattice parameters and a/c axial ratio [upper right-hand inset in Fig. 1(b)] as a function of the content of Cr in the as-deposited films. | |
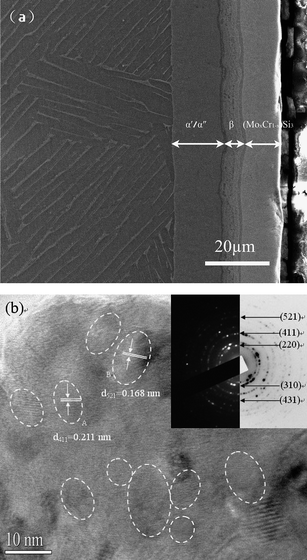 |
| Fig. 2 (a) SEM observation of the nanocrystalline Mo5Si3 film formed on Ti–6Al–4V alloy; (b) HRTEM image and the corresponding SAED pattern of the nanocrystalline Mo5Si3 film. Some of the nanocrystallites are circled for easier recognition. The space of the lattice fringes of the nanocrystalline film marked A and B can be calculated as 0.211 nm and 0.168 nm, which correspond to the spacing of the (411) and (521) planes of D8m-structured Mo5Si3, respectively. | |
3.2 Nanoindentation test
Fig. 3 shows the representative load-displacement (P–h) curves and their corresponding AFM images of indentation impressions obtained from the five kinds of nanocrystalline (MoxCr1−x)5Si3(x = 1, 0.78, 0.75, 0.64, 0.57) films under a maximum load of 20 mN. It must be additionally ensured that the indentation depth is notably lower than 10% of the film thickness in order that the contribution to mechanical properties from its substrate is negligible. Two noteworthy features can be extracted from these load-displacement (P–h) curves, i.e. pop-in and pile-up phenomena. In Fig. 3(a), multiple pop-in events, which are characterized by a distinct displacement discontinuity/jump in the loading curve, have been clearly observed in localized and enlarged load–displacement plots of Mo5Si3 films. The pop-in phenomenon is usually ascribed to onset of phase transition,20 pile-up phenomenon21 and microcracking.22 No evidence of pile-up is substantiated by Athe FM morphology and cross-profile of the impression mark [in Fig. 3(b)]. In addition, Mo5Si3 has high thermal stability with no phase transformation from room temperature to its melting point. Therefore, in the case of Mo5Si3 film, pop-in events are likely to be the result of microcracking appearing during the nanoindentation. For nanocrystalline (MoxCr1−x)5Si3 (x = 0.78, 0.75, 0.64, 0.57) films, the load–displacement curves exhibit a substantial continuity without pop-in events. Note that a significant pile-up of Cr alloy nanocrystalline films in the area surrounding the indentation is observed by AFM, and the cross-profile [in Fig. 3(b)], suggesting that localized plastic deformation has taken place during the process of nanoindentation. The pile-up height increases with increasing Cr content in the (MoxCr1−x)5Si3 films, especially for the (Mo0.57Cr0.43)5Si3 film. The occurrence of pile-up relies on the work-hardening characteristic of the materials. The work of Das et al.23 suggested that the materials with high yield ratio and low work-hardening rate, exhibit prominent pile-up. To quantify the energy dissipation involved in the plastic deformability of (MoxCr1−x)5Si3 films, the plastic work of indentation (Wp) can be assessed from the area enclosed by the loading and unloading curves.24 The calculated results clearly indicate that the plastic work value is highest for nanocrystalline (Mo0.57Cr0.43)5Si3 films (0.63 nJ) and lowest for Mo5Si3 films (0.57 nJ), indicating the least resistance to plastic deformation for (Mo0.57Cr0.43)5Si3 films and the most for Mo5Si3 films [see Fig. 3(c)]. The hardness and elastic modulus of (MoxCr1−x)5Si3(x = 1, 0.78, 0.75, 0.64, 0.57) films [Fig. 3(d)] decrease with increasing Cr addition. It is worth mentioning here that the nanocrystalline (MoxCr1−x)5Si3(x = 1, 0.78, 0.75, 0.64, 0.57) films show higher values of hardness and elastic modulus than the coarse grain Mo5Si3 reported in the literature (H = 11.48 GPa, E = 260 GPa).25 Similar findings were also observed in our previous work.15 The influences of pile-up on the accuracy of hardness and elastic modulus calculated using the Oliver–Pharr method correlate with the ratio of the final indentation depth to the maximum indentation depth (hf/hmax). When the ratio is less than 0.7, the Oliver–Pharr method is valid for estimating the hardness and elastic modulus.26 In the case of (MoxCr1−x)5Si3(x = 0.78, 0.75, 0.64, 0.57) films, the ratio values are much lower than 0.7 and thus pile-up should not have a considerable effect on the accuracy of hardness and elastic modulus values of the tested films in the present study.
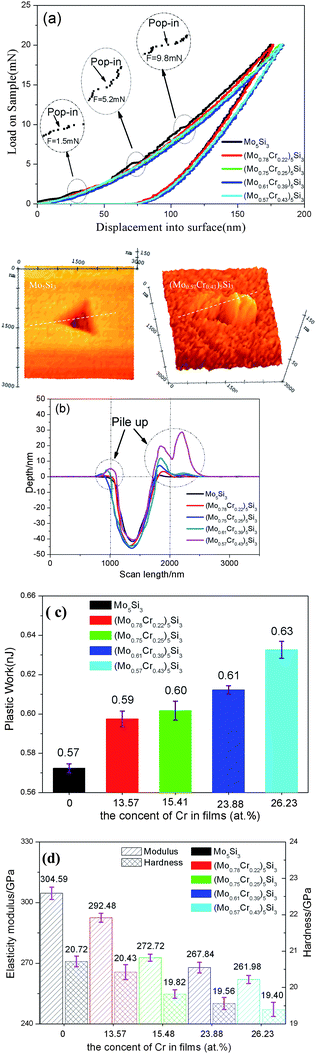 |
| Fig. 3 (a) Load–displacement curves of the nanocrystalline (MoxCr1−x)5Si3 (x = 1, 0.78, 0.75, 0.61, 0.57) films. Three middle insets show enlarged portions of load–displacement curves highlighting the details of the pop-in events. (b) Cross-profiles of the indents after nanoindentation for nanocrystalline (MoxCr1−x)5Si3 films and typical AFM morphologies of nanoindentation imprints for nanocrystalline Mo5Si3 films (upper left-hand corner) and nanocrystalline (Mo0.57Cr0.43)5Si3 films (upper right-hand corner). (c) Plastic work of the nanocrystalline (MoxCr1−x)5Si3 films. (d) Hardness and plastic work of nanocrystalline (MoxCr1−x)5Si3 films. | |
4. Discussion
4.1 Grain-boundary-mediated deformation mechanisms
A number of studies have proven that the changes in deformation mechanism from dislocation-mediated to GB-based give rise to the crossover from the “normal” Hall–Petch effect to the “inverse” one, when the grain size is reduced to below a critical value ranging from 10 nm to 50 nm.27,28 Apparently, the grain size of the nanocrystalline (MoxCr1−x)5Si3 films in the present study is below the critical grain size reported in literature. Furthermore, the nanocrystalline (MoxCr1−x)5Si3 films with randomly distributed grains and grain orientations can facilitate grain-boundary accommodation mechanisms. The intrinsic ductility properties of a nanocrystalline material remain unanswered. In recent atomic level simulations on crack propagation mechanisms in nanocrystalline Ni with mean grain sizes of 5 and 8 nm respectively, Farkas showed that grain-boundary sliding also plays an important role in the crack blunting observed in these materials.29
4.2 Effect of Cr alloying on mechanical properties
Some experimental observations have shown that nanocrystalline metals are very brittle with little tensile ductility compared with their coarser-grained counterparts.30,31 It should be noted that most simulations are performed on fully dense materials. In fact, the artefacts from processing, including flaws, contamination and residual stress, are known to be detrimental to the ductility of nanocrystalline materials.32,33 According to our results, both the nanocrystalline Mo5Si3 film with an average grain size of 8 nm and the Cr-alloyed nanocrystalline Mo5Si3 films with the same size have a positive impact on the ductility of nanocrystalline films. Owing to a high anisotropy of its coefficients of thermal expansion, a lot of microcracks are commonly observed in polycrystalline Mo5Si3 prepared by drop-casting.34 Chu et al. reported that due to thermal mismatch between different grains, significantly large residual thermal stresses (up to 1.8 GPa) can develop in Mo5Si3 in the solidification process, which are obviously higher than the compression and tension strength, causing grain-boundary cracking in polycrystalline materials.4 Although the CTE(c)/CTE(a) ratio was reduced from 2.0 to 1.55 as the Cr content increases to 25 at%, microcracks were still found in these Cr-alloyed Mo5Si3 alloys.34 Metallographic observations indicate that five kinds of nanocrystalline (MoxCr1−x)5Si3 films are free of microcracks, which suggests that thermal stresses are relieved to a certain extent. It is generally true that the smaller the grain size, the more homogeneous the deformation. Thus, crack propagation is required to have higher stress intensities with the reduction of grain sizes. As further proof, the Vickers indentation results clearly show that there is no evidence of cracks in the five kinds of nanocrystalline (MoxCr1−x)5Si3 films at an applied load of 1000 g (Fig. 4). However, since polycrystalline Mo5Si3 is intrinsically brittle at room temperature, the cracks were generated at the four corners of the indent impression at applied load of 1000 g.4,25 The nanoindentation results show that the plastic deformability of nanocrystalline (MoxCr1−x)5Si3 films is relevant to the content of Cr. As a possible explanation of this phenomenon, we speculate that the residual thermal stresses along with a superimposition of indentation stress masks the inherent mechanical properties of nanocrystalline (MoxCr1−x)5Si3 films. Because Cr has a smaller size than Mo, the “effective” interatomic distance along the [001] atom chains is increased by replacing the Mo atoms with Cr and accordingly, anharmonicity along the c-axis is reduced.34 Higher content of Cr results in lower residual thermal stresses, corresponding to the higher plastic deformability of nanocrystalline (MoxCr1−x)5Si3 films. In other words, the higher content of Cr will all the more reveal the intrinsic mechanical properties of nanocrystalline (MoxCr1−x)5Si3 films. Under indention load, the plastic deformation by grain-boundary plasticity mechanisms is preferred over cleavage fracture of nanocrystalline (MoxCr1−x)5Si3 films and thus the ductility of nanocrystalline (MoxCr1−x)5Si3 films is improved.
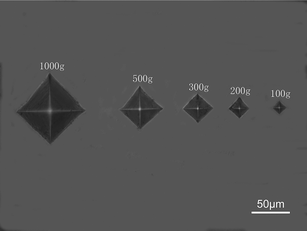 |
| Fig. 4
Optical micrograph of Vickers indentation sites in nanocrystalline Mo5Si3 films with different applied loads. | |
4.3 Elastic modulus
It may also be worthwhile to remark that elastic modulus of nanocrystalline Mo5Si3 is higher than that of coarse-grained Mo5Si3, implying a more compact topological structure for nanocrystalline Mo5Si3. This result is not consistent with the results reported in the literature, where the elastic modulus of nanocrystalline materials is obviously lower than that of their coarse-grained counterpart materials.29,35 In contrast with the conventional synthesis methods of nanocrystalline materials, such as electrodeposition, the double-cathode glow discharge process provides a new avenue for preparing nanocrystalline films with higher deposition temperature, which is conducive to preparing fully dense nanocrystalline films.
5. Conclusions
In summary, the mechanical behavior of a series of nanocrystalline (MoxCr1−x)5Si3 films, with an average grain size of 8 nm, were studied. The grain size of the nanocrystalline (MoxCr1−x)5Si3 films in the present study is the grain size of the region where it is often reported that the classical H–P relationship breaks down. Experimental results show that the hardness and elastic modulus of nanocrystalline (MoxCr1−x)5Si3 (x = 1, 0.78, 0.75, 0.64, 0.57) films decrease with increasing Cr content. In contrast, the plastic deformability of nanocrystalline (MoxCr1−x)5Si3 films increases with increasing Cr content. The effect of Cr content on the ductility of nanocrystalline (MoxCr1−x)5Si3 films is judiciously attributable to the decrease of residual thermal stresses. These valuable experimental results not only help to understand the intrinsic ductility properties of nanocrystalline materials but also provide new avenues to improve the ductility of intermetallics at lower temperatures.
Acknowledgements
The authors gratefully acknowledge the support of the Aeronautics Science Foundation of China under project No.2009ZE52047.
References
- C. L. Yeh and W. H. Chen, J. Alloys Compd., 2007, 439, 59–66 CrossRef CAS.
- C. L. Yeh and H. J. Wang, Intermetallics, 2007, 15, 1277–1284 CrossRef CAS.
- Z. Chen and Y. W. Yan, J. Alloys Compd., 2006, 413, 73–76 CrossRef CAS.
- F. Chu, D. J. Thoma, K. J. McClellan and P. Peralta, Mater. Sci. Eng., A, 1999, 261, 44–52 CrossRef.
- E. Ström, S. Eriksson, H. Rundlöf and J. Zhang, Acta Mater., 2005, 53, 357–365 CrossRef.
- E. Ström, Mater. Charact., 2005, 55, 402–411 CrossRef.
- D. P. Mason and D. C. Van Aken, Acta Metall. Mater., 1995, 43, 1201 CrossRef CAS.
- K. Yoshimi, M. H. Yoo, A. A. Wereszczak, S. M. Borowicz, E. P. George, E. Miura and S. Hanada, Mater. Sci. Eng., A, 2002, 329–331, 228–234 CrossRef.
- H. Shaked, J. D. Jorgensen, S. Short, O. Chmaissem, S. I. Ikeda and Y. Maeno, Phys. Rev. B: Condens. Matter Mater. Phys., 2000, 62, 8725 CrossRef CAS.
- S. V. Raj, Mater. Sci. Eng., A, 1995, 192–193, 583 CrossRef.
- J. H. Schneibel, C. J. Rawn, T. R. Watkins and E. A. Payzant, Phys. Rev. B: Condens. Matter Mater. Phys., 2002, 65, 134112 CrossRef.
- S. V. Raj, Mater. Sci. Eng., A, 1995, 201, 229 CrossRef.
- T. Dasgupta and A. M. Umarji, Intermetallics, 2008, 16, 739–744 CrossRef CAS.
- J. Xu, Z. Xu, J. Tao, Z. L. Liu, Z. Y. Chen and W. H. Zhu, Scr. Mater., 2007, 57, 587–90 CrossRef CAS.
- J. Xu, J. Sun and S. Y. Jiang, Mater. Lett., 2009, 63, 1082–1084 CrossRef CAS.
- W. C. Oliver and G. M. Pharr, J. Mater. Res., 1992, 7, 1564 CrossRef CAS.
- E. Ström, J. Zhang, S. Eriksson, C. H. Li and D. Feng, Mater. Sci. Eng., A, 2002, 329–331, 289–294 CrossRef.
- A. R. Cox and R. Brown, J. Less Common Met., 1964, 6, 51 CrossRef CAS.
- X. M. Peng, C. Q. Xia, Y. Y. Liu and J. H. Wang, Surf. Coat. Technol., 2009, 203, 3306–3311 CrossRef CAS.
- L. Chang and L. C. Zhang, Mater. Sci. Eng., A, 2009, 506, 125–129 CrossRef.
- S. Saber-Samandari and K. A. Gross, Acta Biomater., 2009, 5, 2206–2212 CrossRef CAS.
- D. Lorenz, A. Zeckzer, U. Hilpert, P. Grau, H. Johansen and H. S. Leipner, Phys. Rev. B: Condens. Matter Mater. Phys., 2003, 67, 172101 CrossRef.
- G. Das, Sabita Ghosh, Sukomal Ghosh and R. N. Ghosh, Mater. Sci. Eng., A, 2005, 408, 158–164 CrossRef.
- A. E. Giannakopoulos and S. Suresh, Scr. Mater., 1999, 40, 1191–1198 CrossRef CAS.
- A. Misra, J. J. Petrovic and T. E. Mitchell, Scr. Mater., 1998, 40, 191–196 CrossRef.
- A. Bolshakov and G. M. Pharr, J. Mater. Res., 1998, 13, 1049–1058 CrossRef CAS.
- Z. W. Shan, E. A. Stach, J. M. K. Wiezorek, J. A. Knapp, D. M. Follstaedt and S. X. Mao, Science, 2004, 305, 654 CrossRef CAS.
- I. A. Ovid'ko, Science, 2002, 295, 2386 CrossRef CAS.
- D. Farkas, Metall. Mater. Trans. A, 2007, 38, 2168–2173 Search PubMed.
- M. Legros, B. R. Elliot, M. N. Rittner, J. R. Weertman and K. J. Hemker, Philos. Mag., 2000, 80, 1017 Search PubMed.
- C. J. Youngdahl, P. G. Sanders, J. A. Eastman and J. R. Weertman, Scr. Mater., 1997, 37, 809 CrossRef CAS.
- C. C. Koch, D. G. Morris, K. Lu and A. Inoue, MRS Bull., 1999, 24, 54–58 CAS.
- L. Lu, L. B. Wang, B. Z. Ding and K. J. Lu, J. Mater. Res., 1999, 15, 270–2733 CrossRef.
- J. H. Schneibel, C. J. Rawn, E. A. Payzant and C. L. Fu, Intermetallics, 2004, 12, 845–850 CrossRef CAS.
- Y. Zhou, U. Erb, K. T. Aust and G. Palumbo, Scr. Mater., 2003, 48, 825–830 CrossRef CAS.
|
This journal is © The Royal Society of Chemistry 2010 |
Click here to see how this site uses Cookies. View our privacy policy here.