DOI:
10.1039/C2RA00963C
(Paper)
RSC Adv., 2012,
2, 3410-3415
3D-hierarchical NiO–graphene nanosheet composites as anodes for lithium ion batteries with improved reversible capacity and cycle stability
Received
27th October 2011
, Accepted 26th January 2012
First published on 28th February 2012
Abstract
3D-hierarchical NiO–graphene nanosheet (GNS) composites as high performance anode materials for lithium-ion batteries (LIBs) were synthesized through a simple ultrasonic method, and characterized by X-ray diffraction, Raman spectrum, field emission scanning electron microscopy and transmission electron microscopy. The results show that the 3D-hierarchical NiO carnations with nanoplates as building blocks are homogeneously anchored onto GNS and act as spacers to reduce the stacking of GNS. Electrochemical performances reveal that the obtained 3D-hierarchical NiO–GNS composites exhibit remarkably high reversible lithium storage capacity, good rate capability and improved cycling stability, e.g. approximate 1065 mA h g−1 of reversible capacity is retained even after 50 cycles at a current density of 200 mA g−1. The remarkable improvement of electrochemical performances of the obtained composites could be attributed to the decrease of the volume expansion and contraction of NiO and the improvement of the electronic conductivity of composites during the cycling process.
Introduction
Recently, lithium-ion batteries for electric vehicles and popular consumer electronics have been under intensive investigation.1 As a commercial anode material, graphite is usually employed in LIBs because of its reversible discharge and charge under intercalation potentials with appropriate specific capacity.2,3 To further improve the capacity and energy density of the battery system, much effort has been focused on the researches of high-performance electrode materials for next-generation LIBs.2,4,5 Metal oxides, such as MnO2,6 TiO2,7 Fe2O3,8 Co3O4,9,10 NiO,11 and SnO2,12,13 have attracted extensive attention as anode materials for LIBs due to their high theoretical capacities. However, these anode materials always suffer from rapid capacity fading because of poor conductivity and the large volume expansion occurring in cycling process.14 Thus, graphitic carbons with better electrical conductivity have been widely used as matrices for metal oxides to improve their cycling performances.15,16
As one of the special structures of carbon, graphene nanosheets (GNS) consist of monolayers of sp2 hybridized carbon atoms arranged in a honeycombed network with six-membered rings.17,18 The unique structure of GNS holds great potential because of its high surface area, excellent electronic conductivity and high Li storage density.19–23 The theoretical capacity of GNS is 744 mA h g−1,24,25 twice as large as that of graphite (372 mA h g−1). Moreover, the incorporation of nanostructured metal oxides into GNS layers will generate a porous network, providing excellent electron-conducting and ion-transporting pathways.26,27 On the other hand, the nanostructured metal oxides anchored onto GNS can also act as spacers to prevent the re-stacking of GNS during cycling process. Thus some metal oxide–GNS composites were fabricated for investigation of Li-ion storage properties and to improve their cycling performance and rate capabilities.1,28
Recently, NiO–GNS composites have been prepared via a solvothermal method.1,29 However, NiO obtained in these composites is always in the form of spherical nanoparticles, and the reversible lithium storage capacities are not obviously improved, compared to that of pure NiO. Herein, we report an ultrasonic synthesis of 3D-hierarchical NiO–GNS composites with enhanced electrochemical performances as anode for LIBs. The obtained 3D-hierarchical NiO–GNS composites exhibit a high reversible lithium storage capacity (1065 mA h g−1 at a current density of 200 mA g−1), which is much higher than the theoretical capacity of NiO (718 mA h g−1).30
Experimental section
Preparation of 3D-hierarchical NiO–GNS composites
GNS was prepared via a modified Hummers method,31 and 3D-hierarchical NiO carnations were synthesized as previously reported.32 Typically, 80 mg of 3D-hierarchical NiO carnations were dispersed in 60 mL of distilled water. Then 30 mg of GNS was added into the above solution with ultrasonic treatment for 1 h. The mixed solution was immediately separated by centrifugation, washed with distilled water several times and dried in a vacuum oven at 60 °C overnight to obtain 3D-hierarchical NiO carnation–GNS composites.
Characterization
The structure and morphology of the obtained products were characterized using XRD (Shimadzu XRD-6000, Cu Kα, 40 kV, 30 mA), FESEM (JSM-7401F) and TEM (JEOL, JEM-2100). Raman spectra were recorded on a Super LabRam-II spectrometer with a holographic grating of 1800 g mm−1. Thermogravimetric (TG) analysis was carried out on a Perkin-Elmer 7 instrument to determine the weight content of GNS in the 3D-hierarchical NiO–GNS composites.
Electrochemical measurement
The electrochemical properties of the obtained products were measured using coin cells. The working electrodes were prepared by casting a slurry containing 80% active material (3D-hierarchical NiO–GNS composites), 10% acetylene black and 10% polyvinylidene fluoride (PVDF) in a volatile solvent onto a copper foil according to previous work.27 Lithium foil was used as the counter electrode. The charge–discharge performances of the fabricated cells were tested between 0.01 and 3 V vs. Li+/Li using a battery test system (LAND CT2001A model, Wuhan Jinnuo Electronics, Ltd.). Cyclic voltammetry (CV) was conducted using an electrochemical workstation (CHI660C). All tests were performed at room temperature.
Results and discussion
Characterization of 3D-hierarchical NiO carnation–GNS composites
Fig. 1a shows the X-ray diffraction pattern of the as-prepared 3D-hierarchical NiO carnation–GNS composites. All the major diffraction peaks can be indexed to NiO with a cubic structure (JCPDS CARD No. 78-0643). A broad and weak diffraction peak centered at 2θ = 23.2° is the (002) diffraction peak of GNS (d = 4.45 Å), indicating the formation of NiO–GNS composites.26,33 The representative TG analysis curve of the NiO–GNS composites is shown in Fig. 1b, the amount of NiO in the NiO–GNS composites is about 73.6 wt% according to the mass loss of GNS in the obtained composites. Raman spectroscopy is a non-destructive method that can be used to characterize graphitic materials.34,35 A broad D band (1320 cm−1) and a broad G band (1590 cm−1) appear in the obtained composites (as shown in Fig. 1c). The D peak is usually related to the k-point phonon of A1g symmetry, while the G peak represents the in-plane bond-stretching motion of the E2g phonons of Csp2 atoms,36,37 and their relative intensity provides a clue to the disordered and/or ordered crystal structures of GNS. The D/G intensity ratio of the obtained NiO–GNS composites indicates the small size of the in-plane sp2 domains of GNS.31,38
FESEM images of NiO, GNS and NiO–GNS composites are shown in Fig. 2. Pure NiO exists in the form of a carnation shape, and is built by nanoplates (Fig. 2a).32 Pure GNS is stacked and enfolded with each other, similar to crumpled paper (Fig. 2b).39 From the FESEM image of NiO–GNS composites, one can see that the 3D-hierarchical NiO with carnation shape is distributed on the surface of the curly GNS (Fig. 2c), and some NiO carnations become incomplete, and become nanoplates, which are the self-assembling units.32 The inset in Fig. 2c shows the individual NiO carnation surrounded by GNS. The above observation indicates that the ultrasound process is beneficial to exfoliate 3D-hierarchical NiO with carnation shape and to form composites with GNS. A higher magnification FESEM image (Fig. 2d) further reveals that NiO carnations are assembled from NiO nanoplates and they are surrounded by the thin, aggregated, crumpled GNS after the ultrasound process. The morphologies of the obtained 3D-hierarchical NiO carnation–GNS composites can be more clearly shown by TEM image (Fig. 3). As shown in Fig. 3a, the sheet-like products can be attributed to GNS because of its thinner structure. 3D-hierarchical NiO carnations with sizes in the range 1–2 μm are anchored onto/into the surface of the GNS layers. A higher magnification image of an individual NiO carnation also clearly reveals that the as-prepared NiO has a hollow structure with a hole in its center (Fig. 3b). The selected area electron diffraction (SAED) pattern (inset in Fig. 3b) clearly demonstrates the polycrystalline nature of these 3D-hierarchical NiO carnations.
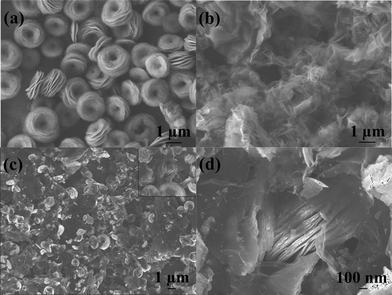 |
| Fig. 2 FESEM images of NiO carnations (a), GNS (b) and 3D-hierarchical NiO–GNS composites (c, d), the insert in (c) shows individual NiO carnation surrounded by GNS. | |
 |
| Fig. 3 (a,b) TEM images of the as-prepared 3D-hierarchical NiO–GNS composites, the insert in (b) is the corresponding SAED pattern. | |
Moreover, the ultrasound process plays an important role during the preparation of NiO–GNS composites. Firstly, the ultrasound treatment would disperse well the 3D-hierarchical NiO carnations into DI water. Secondly, GNS is highly negatively charged because the ionization of functional groups in GNS happens for the carboxylic acid and phenolic hydroxyl groups in the hydrazine hydrate reducing GO process. Thus both the well dispersed NiO and GNS would lead to well dispersed composites. On the other hand, the coordination and electrostatic interactions between the functional groups exited in GNS and Ni atoms on the surface of NiO carnations will also be beneficial for the formation of well dispersed NiO–GNS composites.
Lithium storage properties of 3D-hierarchical NiO–GNS composites
Galvanostatic charge–discharge experiments were carried out to evaluate the electrochemical performances of the as-prepared 3D-hierarchical NiO–GNS composites. For comparison, electrodes made of pure NiO carnations and pure GNS were also tested under the same electrochemical conditions. The 1st, 2nd, 10th and 30th charge–discharge curves of the 3D-hierarchical NiO–GNS composites, pure GNS and pure NiO carnations under a current density of 200 mA g−1 are presented in Fig. 4a–4c, respectively. As shown in Fig. 4a, the electrode based on 3D-hierarchical NiO–GNS composites delivers a discharge capacity of 1398 mA h g−1 and a charge capacity of 907 mA h g−1 at the 1st cycle with a coulombic efficiency of about 65%. Moreover, the efficiency rapidly increases to 97.0% in the 5th cycle, and remains in the following cycles. Furthermore, the 3D-hierarchical NiO–GNS composites still show a high reversible capacity of ∼1050 mA h g−1 after 30 discharge–charge cycles. In contrast, the first discharge and charge capacities are 1014 and 412 mA h g−1 for pure GNS, respectively. The pure GNS electrode also exhibits a comparative low efficiency at the 1st cycle (only 40.6%) and no obvious voltage plateau in the curve (Fig. 4b), which is similar to that of previous works.26,27 On the other hand, the electrode based on pure NiO carnations has a specific capacity of 1049 mA h g−1 in the first discharge step and a reversible capacity of 751 mA h g−1 in the initial charge step (Fig. 4c). However, it suffers from a fast reversible capacity fading since the 2nd cycle. In addition, the 3D-hierarchical NiO–GNS composites show that the voltage plateaus around 1.1 V, which is similar to that of pure hierarchical NiO carnations. Fig. 4d shows the cyclic performances of all electrodes at a current density of 200 mA g−1. After 50 discharge–charge cycles, the 3D-hierarchical NiO–GNS composites still maintain a capacity of 1065 mAh g−1, while pure GNS only exhibits a poor capacity of 237 mA h g−1 and the electrode based on pure NiO carnations shows a much worse capacity of 156 mA h g−1. It is worthy to note, the reversible capacity of the 3D-hierarchical NiO–GNS composites slightly increases from the 2nd cycle and reaches ∼1060 mA h g−1 after 50 cycles, which could be ascribed to the gradual activation of GNS in the composites during the first several cycles.27,40 On the other hand, GNS should also have a great contribution to the high lithium storage capacity of the obtained composites because the theoretical reversible capacity of NiO is about 718 mA h g−1.
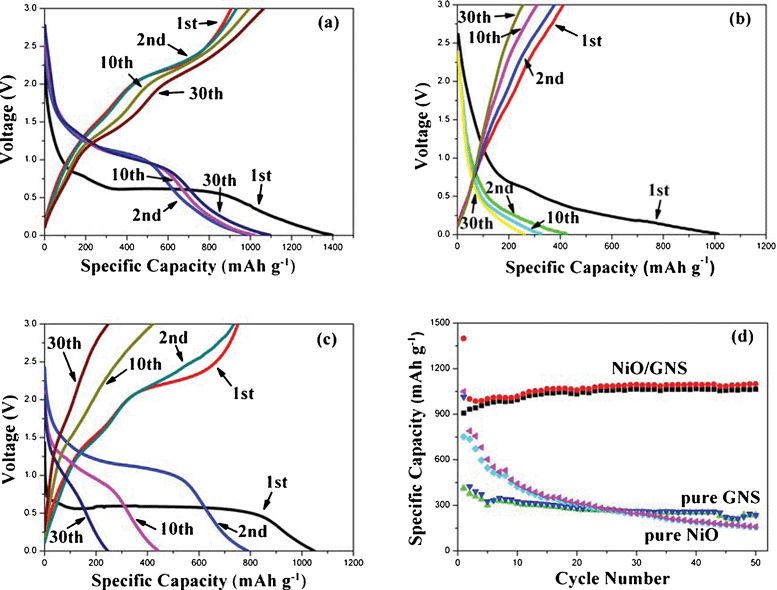 |
| Fig. 4 Typical charge–discharge curves of (a) 3D-hierarchical NiO–GNS composites, (b) GNS and (c) NiO carnations cycled at the 1st, 2nd, 10th and 30th between 0.01 V and 3.0 V. (d) The comparison of the cycling performance of composites, GNS and NiO. | |
Cyclic voltammograms (CV) further reveal the lithium storage process of the 3D-hierarchical NiO–GNS composites (Fig. 5). In the 1st cycle, the two observed cathodic peaks at 0.26 and 0.52 V can be attributed to the electrochemical reduction reaction of NiO,1 and the two anodic peaks at 1.60 and 2.39 V correspond to an oxidation reaction of NiO in the 3D-hierarchical NiO–GNS composites.31 The main reduction peak is shifted to 0.90 V for the 3D-hierarchical NiO–GNS composites since the 2nd cycle. Based on the previous reports, the capacity of GNS increases with the expansion in (002) interlayer spacing, and a Li storage capacity of 1116 mA h g−1 will be maintained when the interlayer spacing is about 4.0 Å, according to the Li2 covalent molecule model.41–43 Because the interlayer spacing of GNS in the obtained composite is about 4.45 Å, a higher lithium storage capacity of GNS (>1116 mA h g−1) could be expected, which would lead to a high lithium storage capacity of the obtained composites of 1060 mA h g−1. The integral area and peak intensity in the 3rd cycle are close to that of the 2nd cycle for the composites, indicating that the electrochemical reversibility of the obtained composites is gradually built after the 2nd cycle.
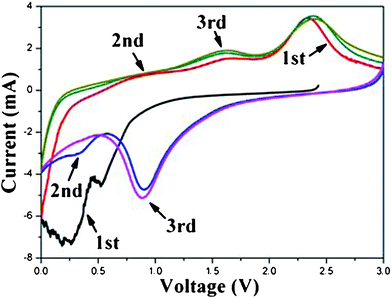 |
| Fig. 5 CV curves of electrode based on 3D-hierarchical NiO–GNS composites at a 1 mV s−1 scan rate. | |
The pure NiO anode material fabricated by Huang et al.11 only showed 540 and 210 mA h g−1 at current densities of 100 and 1000 mA g−1, respectively. Kottegoda et al.1 found that the reversible capacity of nanostructured GNS/NiO anode material remained 450 mA h g−1 after 40 cycles at a current density of 300 mA g−1. In this report, the 3D-hierarchical NiO–GNS composites exhibit much better rate capability compared to the previous results1,11 and the pure NiO carnations at various current densities from 100 to 1000 mA g−1 (Fig. 6a–6b). It is obvious that the reversible capacity of 3D-hierarchical NiO–GNS composites slightly increases and reaches to 1053 mA h g−1 after 10 cycles under a current density of 100 mA g−1, whereas that the NiO carnations electrode rapidly drops from 1049 to 603 mA h g−1. In the following cycles, the obtained 3D-hierarchical NiO–GNS composites keep a reversible capacity of 1059, 967 and 823 mA h g−1 at the current density of 200, 500 and 1000 mA g−1, respectively. However, the reversible capacity of pure NiO carnations declines quickly at the same conditions, and only 124 mA h g−1 for the 40th cycle at 1000 mA g−1 is retained, which is much lower than its original capacity (1049 mA h g−1 at 100 mA g−1). Moreover, the obtained 3D-hierarchical NiO–GNS composites recover to their original capacity or even a bit higher (1189 mA h g−1 at the 45th cycle) when the rate comes back to the initial 100 mA g−1 after 40 cycles, which could be attributed to the gradual activation of GNS in the composites in the cycling process. But the pure NiO carnations only exhibit a reversible capacity of 384 mA h g−1 for the 45th cycle and further drop under the same rate. The above results demonstrate that the electrode based on the 3D-hierarchical NiO–GNS composites shows a superior rate capability.
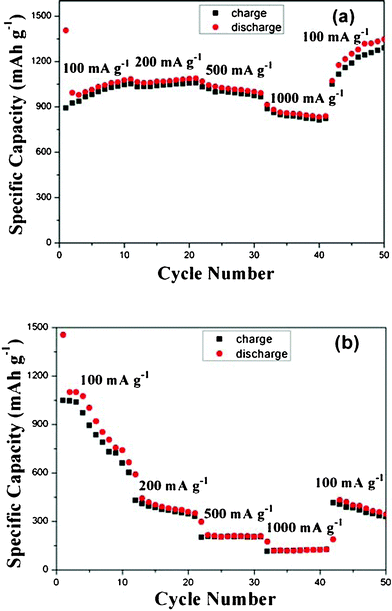 |
| Fig. 6 Rate performance of 3D-hierarchical NiO–GNS composites (a) and NiO carnations (b) at various current densities between 100 and 1000 mA g−1. | |
As illuminated in Scheme 1, the improved cycling stability, remarkably high reversible lithium storage capacity and superior rate capability of the obtained 3D-hierarchical NiO–GNS composites could be attributed to the properties of GNS and the unique structure of NiO. First, GNS can serve as the conductive channels between hierarchical NiO and improve the electronic conductivity of composites during the charge–discharge process because the excellent electronic conductivity would reduce the polarization of electrode and decrease the inner resistance of LIBs.27,44 Second, the presence of hierarchical NiO between GNS can effectively reduce the stacking degree of GNS and further keep their high active surface area. Third, the confined effects of hierarchical NiO and flexible GNS in the composites can block the physical aggregation of NiO and further avoid the rapid capacity fading of electrodes during a continuous cycling process. Thus, the obtained hierarchical NiO–GNS composites could exhibit excellent electrochemical performances.
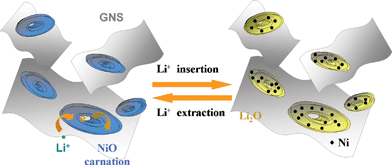 |
| Scheme 1 Schematic illustration of the 3D-hierarchical NiO–GNS composites before and after the cycling process. | |
Conclusions
In summary, 3D-hierarchical NiO–GNS composites were synthesized by a simple ultrasonic process. The obtained hierarchical NiO–GNS composites exhibit remarkable high lithium storage capacity with improved reversible cycling stability and superior rate capability, e.g. the reversible capacity of composites is much higher than the theoretical reversible capacity of 718 mA h g−1 of pure NiO (1065 mA h g−1 for the 50th cycle at a current density of 200 mA g−1) and also shows stable capacities of 1189 and 823 mA h g−1 at current densities of 100 and 1000 mA g−1, respectively. This simple method could be easily adapted to fabricate other GNS related anodes with superior electrochemical performances.
Acknowledgements
The work was supported by National Basic Research Program of China (2009CB930400 and 2007CB209705), National Natural Science Foundation of China (21071097, 20901050), Shanghai Pujiang Program (09PJ1405700) and the key project of State Key Laboratory of High Performance Ceramics and Superfine Microstructure (SKL200901SIC).
References
- I. R. M. Kottegoda, N. Hayati Idris, L. Lin, J. Z. Wang and H. K. Liu, Electrochim. Acta, 2011, 56, 5815 CrossRef CAS.
- J. M. Tarascon and M. Armand, Nature, 2011, 414, 359 CrossRef.
- Z. Du, X. Yin, M. Zhang, Q. Hao, Y. Wang and T. Wang, Mater. Lett., 2010, 64, 2076 CrossRef CAS.
- G. Wang, B. Wang, X. Wang, J. Park, S. Dou, H. Ahn and K. Kim, J. Mater. Chem., 2009, 19, 8378 RSC.
- P. G. Bruce, B. Scrosati and J. M. Tarascon, Angew. Chem., Int. Ed., 2008, 47, 2930 CrossRef CAS.
- J. Z. Zhao, Z. L. Tao, J. Liang and J. Chen, Cryst. Growth Des., 2008, 8, 2799 CAS.
- K. X. Wang, M. D. Wei, M. A. Morris, H. S. Zhou and J. D. Holmes, Adv. Mater., 2007, 19, 3016 CrossRef CAS.
- C. Z. Wu, P. Yin, X. Zhu, C. Z. OuYang and Y. Xie, J. Phys. Chem. B, 2006, 110, 17806 CrossRef CAS.
- Y. Sun, X. Y. Feng and C. H. Chen, J. Power Sources, 2011, 196, 784 CrossRef CAS.
- W. Y. Li, L. N. Xu and J. Chen, Adv. Funct. Mater., 2005, 15, 851 CrossRef CAS.
- X. H. Huang, J. P. Tu, C. Q. Zhang and F. Zhou, Electrochim. Acta, 2010, 55, 8981 CrossRef CAS.
- J. Yao, X. P. Shen, B. Wang, H. K. Liu and G. X. Wang, Electrochem. Commun., 2009, 11, 1849 CrossRef CAS.
- L. F. Cui, J. Shen, F. Y. Cheng, Z. L. Tao and J. Chen, J. Power Sources, 2011, 196, 2195 CrossRef CAS.
- S. Yang, G. Cui, S. Pang, Q. Cao, U. Kolb, X. Feng, J. Maier and K. Müllen, ChemSusChem, 2010, 3, 236 CrossRef CAS.
- G. Wang, J. Ahn, J. Yao, S. Bewlay and H. Liu, Electrochem. Commun., 2004, 6, 689 CrossRef CAS.
- S. Yang, H. Song and X. Chen, J. Power Sources, 2007, 173, 487 CrossRef CAS.
- D. Li and R. Kaner, Science, 2008, 320, 1170 CrossRef CAS.
- G. Eda and M. Chhowalla, Adv. Mater., 2010, 22, 2392 CrossRef CAS.
- M. D. Stoller, S. J. Park, Y. W. Zhu, J. An and R. S. Ruoff, Nano Lett., 2008, 8, 3498 CrossRef CAS.
- M. Burghard, H. Klauk and K. Kern, Adv. Mater., 2009, 21, 2586 CrossRef CAS.
- Y. B. Zhang, Y. W. Tan, H. L. Stormer and P. Kim, Nature, 2005, 438, 201 CrossRef CAS.
- P. Lian, X. Zhu, S. Liang, Z. Li, W. Yang and H. Wang, Electrochim. Acta, 2010, 55, 3909 CrossRef CAS.
- A. Gerouki, M. Goldner, R. Goldner, T. Haas, T. Liu and S. Slaven, J. Electrochem. Soc., 1996, 143, L262 CrossRef CAS.
- J. R. Dahn, T. Zheng, Y. H. Liu and J.S. Xue, Science, 1995, 270, 590 CAS.
- Y. H. Liu, J. S. Xue, T. Zheng and J. R. Dahn, Carbon, 1996, 34, 193 CrossRef CAS.
- H. Kim, D.-H. Seo, S.-W. Kim, J. Kim and K. Kang, Carbon, 2011, 49, 326 CrossRef CAS.
- Z. S. Wu, W. C. Ren, L. Wen, L. B. Gao, J. P. Zhao, Z. P. Chen, G. M. Zhou, F. Li and H. M. Cheng, ACS Nano, 2010, 4, 3187 CrossRef CAS.
- Y. S. He, D. W. Bai, X. W. Yang, J. Chen, X. Z. Liao and Z. F. Ma, Electrochem. Commun., 2010, 12, 570 CrossRef CAS.
- Z. Ji, J. Wu, X. Shen, H. Zhou and H. Xi, J. Mater. Sci., 2011, 46, 1190 CrossRef CAS.
- J. Zhong, X. Wang, X. Xia, C. Gu, J. Xiang, J. Zhang and J. Tu, J. Alloys Compd., 2011, 509, 3889 CrossRef CAS.
- L. H. Tang, Y. Wang, Y. M. Li, H. B. Feng, J. Lu and J. H. Li, Adv. Funct. Mater., 2009, 19, 2782 CrossRef CAS.
- L. X. Yang, Y. J. Zhu, H. Tong, Z. H. Liang and W. W. Wang, Cryst. Growth Des., 2007, 7, 2716 CAS.
- G. X. Wang, J. Yang, J. Park, X. L. Gou, B. Wang, H. Liu and J. Yao, J. Phys. Chem. C, 2008, 112, 8192 CAS.
- G. X. Wang, X. P. Shen, J. Yao and J. Park, Carbon, 2009, 47, 2049 CrossRef CAS.
- J. Yan, T. Wei, W. Qiao, B. Shao, Q. Zhao, L. Zhang and Z. Fan, Electrochim. Acta, 2010, 55, 6973 CrossRef CAS.
- A. C. Ferrari and J. Robertson, Phys. Rev. B: Condens. Matter, 2000, 61, 14095 CrossRef CAS.
- F. Tuinstra and J. L. Koenig, J. Chem. Phys., 1970, 53, 1126 CrossRef CAS.
- S. Stankovich, D. A. Dikin, R. D. Piner, K. A. Kohlhaas, A. Kleinhammes, Y. Jia, Y. Wu, S. B. T. Nguyen and R. S. Ruoff, Carbon, 2007, 45, 1558 CrossRef CAS.
- P. Guo, H. H. Song and X. H. Chen, Electrochem. Commun., 2009, 11, 1320 CrossRef CAS.
- S. K. Behera, Chem. Commun., 2011, 47, 10371 RSC.
- D. Pan, S. Wang, B. Zhao, M. Wu, H. Zhang, Y. Wang and Z. Jiao, Chem. Mater., 2009, 21, 3136 CrossRef CAS.
- Z. J. Fan, J. Yan, T. Wei, L. J. Zhi and F. Wei, ACS Nano, 2011, 5, 2787 CrossRef CAS.
- I. Lahiri, S. W. Oh, J. Y. Hwang, S. Cho, Y. K. Sun, R. Banerjee and W. Choi, ACS Nano, 2010, 4, 3440 CrossRef CAS.
- S.-M. Paek, E. Yoo and I. Honma, Nano Lett., 2009, 9, 72 CrossRef CAS.
Footnote |
† These authors contributed equally. |
|
This journal is © The Royal Society of Chemistry 2012 |
Click here to see how this site uses Cookies. View our privacy policy here.