Poly(ε-caprolactone) microfiber meshes for repeated oil retrieval†
Received
22nd April 2015
, Accepted 4th August 2015
First published on 5th August 2015
Abstract
Electrospun non-woven poly(ε-caprolactone) (PCL) microfiber meshes are described as biodegradable, mechanically robust, and reusable polymeric oil sorbents capable of selectively retrieving oil from simulated oil spills in both fresh and seawater scenarios. Hydrophobic PCL meshes have >99.5% (oil over water) oil selectivity and oil absorption capacities of ~10 grams of oil per gram of sorbent material, which is shown to be a volumetrically driven process. Both the oil selectivity and absorption capacity remained constant over several oil absorption and vacuum assisted retrieval cycles when removing crude oil or mechanical pump oil from deionized water or simulated seawater mixtures. Finally, when challenged with surfactant stabilized water-in-oil emulsions, the PCL meshes continued to show selective oil absorption. These studies add to the knowledge base of synthetic oil sorbents highlighting a need for biodegradable synthetic oil sorbents which balance porosity and mechanical integrity enabling reuse, allowing for the efficient recovery of oil after an accidental oil spill.
Water impact
Accidental oil spills are inevitable during the acquisition, processing, and distribution of petroleum products. Spills ranging from minor to catastrophic require environmentally friendly methods to separate oil from water, minimizing the negative long-term environmental effects. This work describes a new biodegradable and reusable polymeric microfiber absorbent which repeatedly separates oil (crude or processed) and water (deionized or seawater) mixtures.
|
Introduction
There are many industrial applications for separating low surface tension from high surface tension liquids in a robust, rapid, affordable, and environmentally conscious fashion. Current techniques to separate these immiscible liquids take advantage of density and surface tension differences to separate, absorb, or otherwise remove oil from oil and water mixtures.1–3 However, while these liquids are immiscible, they are often present as stabilized emulsions formed by surfactants naturally found within the oil or the aqueous solution causing traditional methods of separation to be lengthy, incomplete, and potentially expensive.1,2,4 The challenge of efficiently separating surfactant stabilized oil-in-water and water-in-oil emulsions is being addressed at many levels, including the use of electrically responsive membranes and energy-efficient systems based on gravity separation.5–7
For example, the petroleum industry is particularly interested in efficiently separating oil from aqueous solutions during normal petroleum acquisition and processing, and during accidental petroleum spills in rivers, lakes, and oceans.2 In the case of oil spills, the most commonly used cleanup techniques are in situ burning, mechanical methods (booms, skimming, and vacuums), chemical dispersants, and/or the use of sorbent materials.8–12 Each technique possesses advantages and disadvantage that dictate their use in various oil spill scenarios. One of the most successful, cost effective, and versatile methods is the use of porous sorbent materials to remove oil from the surface of a body of water.12 The efficiency of a sorbent material is related to its porosity, hydrophobicity, sorption capacity, sorption rate, and reusability.1 While natural oil sorbents (straw, wood, cotton, milkweed, wool, etc.) biodegrade readily, a non-trivial limitation of many natural sorbent materials is their recovery and reuse.13–18
Consequently, many novel synthetic oil sorbents are being developed to selectively adsorb low surface tension liquids while excluding high surface tension liquids such as oil and water, respectively. Tunable synthetic sorbent materials are fabricated into a variety of structures to enhance their porosity and hydrophobicity allowing for high oil sorption capacities. These materials are optimized to be highly porous (porous sponges, non-woven meshes, etc.) and hydrophobic enough to exclude water from the material and “wet” with low surface tension liquids to allow for oil removal from oil/water mixtures as a semi-solid oil-sorbent composite.19–25 The gold standard for synthetic oil sorbent materials used during oil spill cleanup today is made from polypropylene and absorbs approximately 10 grams of oil per gram of sorbent (g g−1).3 In an attempt to improve the oil removal capacity, several groups have explored polystyrene electrospun meshes with high porosity and hydrophobicity resulting in oil removal capacities ranging from 80–150 grams of oil per gram of mesh.22,26 Other groups have explored a wide variety of synthetic porous materials with similar or larger oil absorption capacities as the polystyrene meshes including: graphene functionalized polyurethane sponges or carbon nanotube aerogels, polydimethylsiloxane or polytetrafluoroethylene foams, highly porous polydivinylbenzene materials, and macroporous butyl rubber.4,27–34 More recently, efforts to develop reusable synthetic systems are being investigated to limit the amount of synthetic material required to clean large oil spills. These systems employ a variety of recovery mechanisms ranging from mechanical squeezing to magnetic aggregation allowing for oil retrieval after oil/water separation.24,29,30,35–38
While these systems show many advantages over natural sorbents and other oil recovery techniques, there are limitations that need to be addressed. First, several of these materials were tested with simple solutions containing oil (e.g., lubricating oils) and water without investigating crude oil, seawater mixtures, or mixtures in the presence of surfactants. Second, most systems favor high porosity over mechanical integrity to achieve high oil absorption capacities for a single use; however, this limits the reusability of these materials.19,39 Finally, there are currently only a few biodegradable or environmentally friendly synthetic oil sorbents reported which have the advantage of naturally degrading if they are not recovered from the ocean surface or naturally degrading when disposed of in a landfill after use and removal of the absorbed oil.19,40,41 Therefore, the design specifications for a robust synthetic oil sorbent system include selectively separating oil out of oil and water or seawater mixtures, being reusable and repurposed several times, possessing robust mechanical properties, and being composed of a biodegradable material for environmentally friendly disposal. To address the recovery, reusability, and lack of biodegradability of many synthetic sorbent materials, there is currently a push to investigate novel synthetic biodegradable systems utilizing biodegradable polymers or synthetic modifications of natural materials.40,42–44
Specifically, we describe a biodegradable electrospun poly(ε-caprolactone) (PCL) mesh that repeatedly separates lubricating oil from surfactant stabilized water-in-oil emulsions (Fig. 1). PCL (70
000–90
000 MW, Sigma) was chosen because it is a well-known biodegradable (~1 year) and biocompatible polymer used in the biomedical industry45–47 that can be produced on the ton scale for industrial uses and easily electrospun to create hydrophobic meshes with tunable fiber diameters, porosity, and mesh geometries. Microorganism accelerated decomposition of PCL in landfill conditions has been extensively studied tracking the progression of the polymer's degradation from oligomers to monomers, to carbon dioxide and methane gas resulting in a fully biodegraded system.48,49 In addition, the microorganism accelerated decomposition of crude oil has been shown to follow several aerobic and anaerobic pathways.50,51 Herein, we report the: 1) fabrication of PCL electrospun meshes with varying fiber sizes and void volumes; 2) selective absorption of oil (lubricating and light, sweet Texas crude) from oil and water mixtures and water-in-oil emulsions; 3) dependence of oil absorption capacity on mesh porosity; 4) mechanical properties of the meshes; and 5) reusability of the meshes for multiple oil recovery experiments.
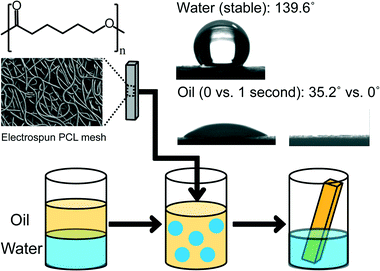 |
| Fig. 1 Schematic diagram of an electrospun hydrophobic PCL mesh that selectively removes oil from a water-in-oil emulsion. An SEM image of the mesh surface with ~6 μm in diameter fibers and ~90% porosity. The water contact angle of the PCL meshes was 139.6° and the instantaneous oil contact angle was 35.2° with complete oil wetting after 1 second. | |
Experimental
General procedure and methods
All chemicals were purchased from Sigma Aldrich and used without further purification, unless otherwise noted. The oils used within the oil absorption studies were Fisherbrand 19 mechanical pump fluid (Fisher Scientific, cat. no. 01-184-150B) and light, sweet Texas crude (Onta inc.). Deionized water was used in all oil and water mixtures except in mixtures containing simulated seawater from a diluted commercial concentrate (National Geographic liquid seawater concentrate; item #: 36-23665).
PCL mesh fabrication and characterization
Poly(ε-caprolactone) (70
000–90
000 MW, Sigma) was dissolved in 5
:
1 chloroform
:
methanol to create the weight percentages found in Table S1.† A custom made electrospinner with a rotating and translating grounded collecting cylinder was used to create 10 cm × 10 cm meshes electrospun onto tin foil. The mesh thickness was controlled by varying the electrospinning time appropriately with the polymer concentration and polymer flow rate. A syringe pump was used to flow the polymer solution through an 18 gauge blunt needle at a controlled rate. The other electrospinning parameters were modified from a previous publication and are described in Table S1.†46 The porosity of the PCL meshes was determined by calculating the volume of the mesh using calipers to measure the length and width and a calibrated microscope (Olympus IX70) to measure the thickness. The mesh was then weighted. The density of the mesh was calculated and divided by the density of PCL to give the percentage of the mesh that was PCL. The remaining volume was the void volume of the mesh. The void volume divided by the mesh volume defined the porosity of the mesh.
Oil selectivity and capacity
A 1
:
1 mixture of pump oil and water was vigorously mixed to increase the surface area of the oil to water interface. A mesh with predetermined geometry and mass was placed into the mixture and allowed to wet over 10 minutes. The mesh was then elevated above the mixture removing any loose oil or water that was adsorbed onto the mesh surface. The mesh capacity was determined by comparing the pre- and post-wetted mass. The oil selectivity was determined using thermogravimetric analysis (TGA). TGA was performed using a TA Instruments TGA Q50. A representative 10–20 mg samples was cut from each mesh and analyzed for its oil and water contents. While monitoring the mass of the sample as a percent of the initial mass, the sample was heated to 110 °C at 20 °C per minute and held at 110 °C for 5 minutes to evaporate any water within the sample. Any mass lost in this experiment can be directly related to the amount of water within the mesh sample since neither the oil nor the PCL mesh will degrade at 110 °C.
Mesh reusability
For static oil and water ratio measurements, the initial mass of an electrospun mesh was determined. The mesh was exposed to a 1
:
1 mixture of pump oil and water for 10 minutes. The mesh was then removed from the mixture and weighed. The liquid filled mesh was then exposed to a vacuum (700 mbar) through a Büchner funnel to retrieve the liquid from within the mesh and then the mesh was weighed again. For the reusability study, this process was repeated for each cycle. After the last oil exposure cycle, the liquid filled mesh was analyzed using TGA. For the reusability or cyclic studies, crude or pump oil was used for the oil phase and deionized water or seawater was used for the aqueous phase. The same oil retrieval protocol was used as for the static measurements; however, the same mixture was used across all cycles until no oil remained in the vial. The volume of the oil phase and aqueous phase was tracked via image analysis of the height of each phase using ImageJ (Fig. S4†).52
Water-in-oil emulsion
Span 80 stabilized water-in-oil emulsions were created by dissolving 0.5%, 1%, or 5% Span 80 (by weight) into the pump oil phase. This oil phase was then mixed vigorously with water at a 7
:
3 oil
:
water volume ratio to generate a water-in-oil emulsion.53 The use of pump oil enabled visualization of the emulsion. Specifically, water-in-oil emulsions were examined and photographed using a Leica DMI6000 B confocal microscope equipped with a Nipkow (CSU-X1) spinning disk (Yokogawa) and a Hamamatsu ImagEM EMCCD camera imaging through a 10× objective. The samples (100 μL) were mounted onto a glass coverslip and imaged using an excitation Coherent Sapphire laser at 488 nm and at 561 nm, and fluorescent images were captured using a Chroma ET bandpass 525/50 and a TX2 ET filter cube with a bandpass 560/40 excitation filter and a bandpass 645/75 suppression filter to capture the emitted wavelengths from the FITC-Dextran (20 kg mol−1, emission: 515 nm) in the water phase (10 μM) and nile red (emission: 605) in the oil phase (310 μM), respectively. An automated stage controlled via a μManager plugin for ImageJ (Version 1.45, NIH)52 was used to create a montage of images of the emulsion. The images were analyzed using ImageJ and the particle analysis tool.
Mesh reusability in surfactant stabilized emulsions
Span 80 stabilized emulsions were created and exposed repeatedly to 20% PCL meshes. The emulsion consisted of 700 μL of oil (with Span 80 dissolved) and 300 μL of water. Meshes with approximately 129 μL void volumes were used to remove the oil within approximately 6 cycles. After each retrieval cycle, a 700 mbar vacuum force was used to remove the liquid from the mesh before subsequent exposure to the emulsion. After 6 cycles, the remaining liquid was analyzed using confocal microscopy to visualize the remaining emulsion.
Results and discussions
Properties of PCL meshes
A set of PCL meshes were electrospun with either 20%, 15%, or 10% PCL by weight solutions to produce fiber diameters ranging from 3.1 μm to 5.6 μm, on average (see Table S1† for details). A schematic diagram of oil removal from an oil and water emulsion is presented in Fig. 1 where the fiber morphology was visualized using scanning electron microscopy and the instantaneous water and oil contact angles were determined to be 139.6° and 35.2°, respectively. The oil was selectively removed from the emulsion due to the rapid oil infiltration or “wetting” into the mesh, as illustrated by the absence of a contact angle after 1 second.
The electrospun PCL meshes were highly porous and had both micrometer (fiber diameters ≈ 3–6 μm) and nanometer (fiber texture < 100 nm) scale surface roughness (Fig. S1†). As with other highly rough surfaces, the apparent contact angles associated with oil or water droplets on the surface of the meshes were exaggerated.54–56 For example, the contact angle of pump oil on a smooth PCL film was 18.0 ± 4.8°, on the roughened mesh surface the apparent contact angle was 0° after 1 second due to the oil droplet being in the fully wetted Wenzel state. Similarly the water contact angle on a smooth PCL surface was 107.8 ± 2.9° which was enhanced to an apparent contact angle of 139.6° due to the water droplet being in the Cassie state. The PCL meshes were sufficiently rough and hydrophobic to maintain a Cassie state providing an air layer between and below the fibers which retarded water penetration or “wetting” into the mesh due to the high water contact angle, and enabled the mesh to float in water.57 In contrast, the oil contact angle was very low resulting in a rapid, fully wetted state.
The oil selectivity was determined using thermal gravimetric analysis (TGA) by quantifying the water content of meshes exposed to 1
:
1 oil and water mixtures. These mixtures were not surfactant stabilized but were vigorously shaken to disrupt the static separation of the oil and water phases, and to increase the surface area of the oil and water interface following previously published work.58 PCL meshes with varying fiber diameter and geometry (length, width, and thickness) were exposed to these mixtures for 10 minutes to allow the meshes to be saturated with liquid. A portion of the mesh was removed and analyzed using TGA by heating the sample to 110 °C for 10 minutes to evaporate any water present within the sample, and measuring the difference in mass before and after removing the water (see Fig. S2† for representative TGA plot). Each mesh had greater than 99.5% oil selectivity and removed an oil volume approximately equal to the calculated void volume of each mesh (Fig. 2). These results indicated that the meshes were completely wetted with oil, and validated that the oil removal capacity of these meshes was directly related to the empty volume within the porous PCL meshes which increases linearly as the length, width, or thickness of the mesh increases.
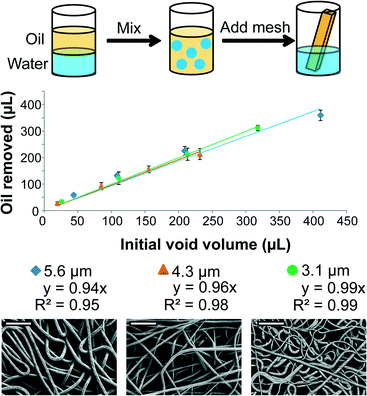 |
| Fig. 2 PCL meshes with varying fiber diameter and void volumes were used to remove oil from 1 : 1 oil : water mixtures. Fiber diameters of 5.6 ± 0.63 μm (blue diamond), 4.3 ± 0.48 μm (brown triangle), and 3.1 ± 0.78 μm (green circle) were created by electrospinning 20%, 15%, and 10% by wt PCL solutions, respectively, and analyzed using scanning electron microscopy (scale bar: 50 μm). Each mesh selectively removed oil volumes approximately equal to the mesh void volume, as indicated by the slopes of the linear regressions (n = 3; Avg ± SD). | |
This mechanism of oil removal was consistent with several previously published studies using highly porous and hydrophobic oil sorbents that absorb oil into the porous structure rather than simply allowing the oil to adsorb onto the sorbent's surface.4,19 The oil absorption capacity (grams of oil removed per gram of sorbent material) (g g−1) was volumetrically driven since the oil absorption capacity was directly related to the void volume of the substrate. Thus, more porous systems have a higher oil absorption capacity; however, highly porous systems are inherently less mechanically robust and therefore less reusable than less porous systems which contain a higher volume fraction of load bearing material.
Mesh reusability
To study the reusability of the electrospun PCL meshes, 20% PCL meshes were evaluated in static and dynamic oil and water mixture ratios composed of either pump or crude oil as well as deionized water or seawater. First, a 20% PCL mesh was exposed to a 1
:
1 pump oil and water mixture followed by a 700 mbar vacuum force.15 Five oil removal/retrieval cycles were performed and the oil absorption capacity (g g−1) of the mesh was maintained at ~9 g g−1 indicating that the void volume was wetted with pump oil and that the oil can be recovered from the mesh with a vacuum force without disrupting the porosity of the mesh (Fig. S3†). The pump oil used in these studies was composed of petroleum distillates and solvent dewaxed heavy paraffin creating a relatively viscous (0.128 Pa s @ 1 Pa and 1 Hz), and optically transparent oil phase, since it lacked impurities such as resins or asphaltenes which are commonly present in crude oil.59 To further challenge the PCL oil mesh sorbents, a sample of light (low viscosity (0.031 Pa s @ 1 Pa and 1 Hz), low density (0.827 g cm−3), and high fraction of light hydrocarbons) and sweet (low sulfur content) Texas crude oil (ONTA Inc.) was used to compare the oil sorption capacity of the meshes between the two types of oil.60 Simulated seawater and the crude oil were also used to study the efficacy of the PCL meshes in separating crude oil from seawater. In addition to removing pump oil from fixed oil and water ratios, the 20% PCL meshes showed a robust capacity to selectively remove all crude or pump oil from oil and water (deionized water or simulated seawater) mixtures leaving a “clean” aqueous sample in all cases after 12 cycles. Photographs of the mesh and oil/water mixture after cycles 1, 6, and 12 show the complete removal of 2 mL of crude oil from a 1
:
1 oil and water (deionized) mixture after 12 cycles without removing any water (Fig. 3a). Similarly, the 20% PCL meshes removed all of the pump oil and crude oil from deionized water and seawater mixtures, respectively (Fig. 3b). Based on linear fits of the data, the average oil volumes removed per cycle were 178 ± 8.3 μL, 186 ± 3.3 μL, and 194 ± 4.6 μL for the crude oil + deionized water, pump oil + deionized water, and crude oil + seawater, respectively (Fig. S5†). Despite the differences between crude oil and pump oil at 25 °C in density (0.827 g cm−3vs. 0.87 g cm−3), viscosity (0.031 vs. 0.128 Pa s) and composition, the PCL meshes removed the pump or crude oil by approximately the same volume per cycle without removing the aqueous phase.60 Finally, the mechanical properties (modulus = 2.3 MPa; yield strength = 240 kPa) and the fiber morphology of the meshes were also maintained (±5%) over at least 10 cycles (Fig. S6 and S7†). These results indicated that the porosity of the mesh was not disrupted by vacuum filtration, the fiber morphology was preserved, and the oil absorption capacity was maintained after repeated use.
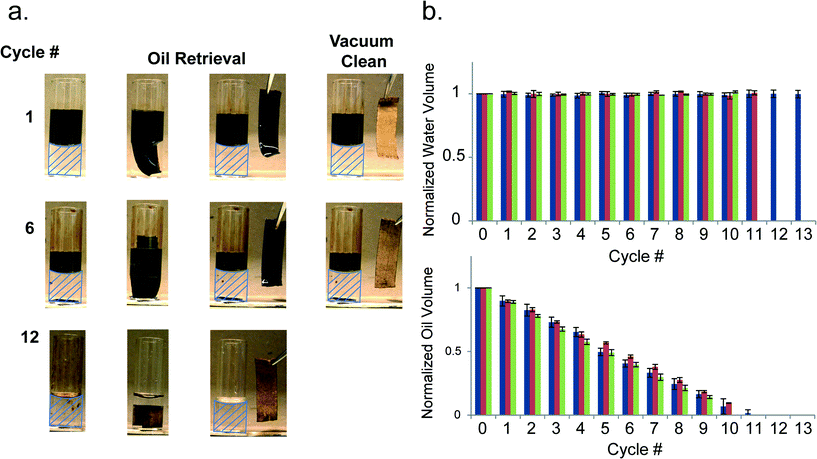 |
| Fig. 3 a) Representative photographs of a 20% PCL mesh removing Texas crude oil from a 1 : 1 oil and water mixture at cycles 1, 6, and 12. The mesh is placed into the mixture, removed with forceps, and cleaned using a vacuum force before the process is repeated (aqueous phase outlined in blue as a guide to the eye). b) Normalized water (top) and oil (bottom) volumes for the Texas crude oil + deionized water (blue), pump oil + deionized water (red), and Texas crude oil + seawater (green) over 13 reuse cycles. Approximately 180 μL of oil are removed from each mixture per cycle (Avg ± SD, n = 3) (Student's t-test: p > 0.05 for all water volumes, p < 0.05 between each cycle for each mixture). | |
Surfactant stabilized emulsions
To further challenge the oil absorption selectivity of the PCL meshes, 7
:
3 pump oil and water mixtures were stabilized by Span 80, which is a nonionic surfactant known to stabilize water-in-oil emulsions.53 Compared to oil-in-water emulsion, these mixtures contained stabilized water droplets within a bulk oil phase (Fig. 4b for confocal images of emulsions). This type of emulsion more closely mimics the emulsions formed at the surface of an oil spill in the ocean, which is often nicknamed “chocolate mousse.” These emulsions are formed by the turbulent surface conditions on the ocean and stabilized by natural surfactants within the oil or by surfactants produced as natural byproducts of oil biodegradation.2,50 In order to visualize the emulsions, these studies were conducted with pump oil rather than the crude oil due to the pump oil's optical transparency.
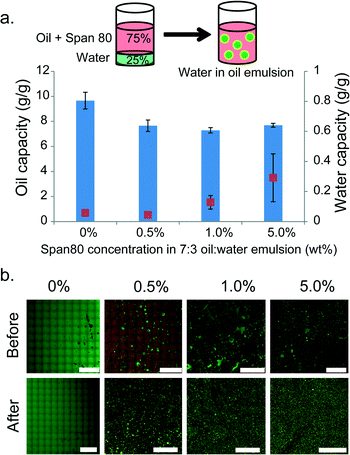 |
| Fig. 4 a) Electrospun PCL meshes selectively removed oil from water-in-oil emulsions stabilized by the non-ionic surfactant Span 80. The oil selectivity (blue) decreased slightly (not significant, t-test, p = 0.211) at higher concentrations of Span 80 as more water was able to infiltrate the mesh (red square) during the first mesh exposure (n = 3; Avg ± SD). b) Confocal microscopy of oil (red) and water (green) mixtures (0%, 0.5%, 1%, and 5% Span 80) before and after 6 oil retrieval cycles (scale bar: 1 mm). | |
The selectivity of these meshes for oil over water was evaluated by exposing the meshes to water-in-oil emulsions stabilized by different amounts of Span 80 (0.5%, 1% or 5% (by wt)). The emulsion was formed by dissolving 0.5%, 1%, or 5% by weight Span 80 into 700 μL of pump oil and then adding 300 μL of water before the sample was vigorously shaken. The resulting water-in-oil emulsions were analyzed using confocal microscopy with nile red dissolved in the oil phase (310 μM) (excitation: 488 nm emission: 515) and a 20 kg mol−1 FITC-dextran dissolved in the water phase (10 μM) (excitation: 561 emission: 605) (Fig. 4b). The average water droplet diameter before mesh exposure was ~11 μm for each emulsion (see Fig. S8† for representative analysis and Table S2† for Avg ± SD). While the mesh performed best when no surfactant was present (~10 g g−1), it continued to maintain a high oil removal capacity (~8 g g−1) when challenged with each surfactant stabilized emulsion. At the highest Span 80 concentration (5% by wt), the oil absorption selectivity, after the first exposure, was slightly reduced but not significantly (t-test between 1% and 5% Span 80 (by wt), p = 0.211) demonstrating that these electrospun PCL meshes were capable of absorbing oil over water even when challenged with surfactant stabilized emulsions. However, after repeated use the meshes exhibited a decrease in selectivity for oil over water and removed some water droplets with the bulk oil phase. This was likely due to the Span 80 adsorbing onto the mesh surface, decreasing the surface tension of the material. Contact angle analysis before and after exposure to the Span 80 stabilized emulsions showed a decrease in contact angle of water on the surface of the meshes (139.6° before and 0° after). After 6 oil retrieval cycles, the remaining liquid volume was significantly less than 300 μL for all Span 80 emulsions tested; however, qualitatively the concentration of water droplets increased as shown in Fig. 4b which suggested that while the selectivity for oil decreased, the remaining liquid was a more concentrated water-in-oil emulsion. This result indicated that a large portion of the bulk oil phase was removed.
Conclusion
A mechanically robust, reusable, and biodegradable oil sorbent system is reported using ~90% porous non-woven electrospun PCL meshes. These meshes are hydrophobic with high water contact angles and effectively 0° oil contact angles due to the micrometer and nanometer scale roughness produced by the electrospinning technique. Meshes fabricated with varying fiber diameters but similar porosities absorb the same amount of oil since the oil capacity is directly related to the mesh void volume. The mesh absorbs oil over water even when the system is challenged with absorbing crude oil or surfactant stabilized water-in-oil emulsions. Similarly, the mesh enables separation of crude oil from crude oil/seawater mixtures. The meshes possess robust mechanical properties allowing for repeated oil retrieval using a vacuum assisted technique. The oil removal capacity of the PCL electrospun mesh is similar for both pump oil and Texas crude oil and comparable to the commercial gold standard polypropylene based oil sorbents and less than other sorbent types such as graphene-based systems (Table 1). These biodegradable hydrophobic PCL electrospun meshes show promise as oil sorbents for oil spill clean-ups since they selectively absorb oil out of stable oil and water mixtures, can be cleaned and reused several times, allow for oil retrieval and collection, and will biodegrade (Table 1). Additional studies of PCL mesh biodegradation in landfills after oil exposure are necessary to understand the kinetics of the biodegradation. In addition, future improvements are necessary to maintain the oil selectivity after repeated exposure to surfactant stabilized emulsions. However, these meshes show promise as they concentrate water-in-oil emulsions by removing a large portion of the bulk oil phase. More hydrophobic polymer meshes with smaller pore sizes are likely necessary to prevent infiltration of emulsified water particles into the mesh.
Table 1 Comparison of oil sorbent materials (a comprehensive list of oil sorbent technologies can be found in several review article1,4,13,19)
Sorbent type |
Oil sorption capacity (g g−1)a |
Liquids tested |
Tested in saltwater? |
Emulsions? |
Reusable? |
Biodegradable? |
Oil sorption capacity (g g−1) indicates the mass of oil removed per gram of sorbent material on the first use.
|
Polypropylene mats3,13 |
8–12 |
Crude oil |
Yes |
No |
Yes |
No |
Aligned cotton fibers17 |
50 |
Motor oil |
No |
No |
No |
Yes |
Graphene functionalized polyurethane sponge32 |
80–160 |
Lubricating oil, olive oil, bean oil, diesel oil, pump oil, chloroform, acetone, THF, DMF, DMSO |
No |
No |
Yes |
No |
Polydimethylsiloxane (PDMS) foam30 |
4–34 |
Chloroform, cyclohexane, dichloromethane, n-hexane, toluene, aniline, acetone, methanol, petroleum ether, gasoline, diesel, crude oil, maize oil, silicone oil |
No |
No |
Yes |
No |
Polyvinyl chloride/polystyrene electrospun mesh22 |
38–146 |
Motor oil, peanut oil, diesel, and ethylene glycol |
No |
No |
No |
No |
Poly(ε-caprolactone) (PCL) electrospun mesh |
9 |
Mechanical pump oil, crude oil |
Yes |
Yes |
Yes |
Yes |
Our results support the use of biodegradable oil sorbent materials and demonstrate that: 1) materials with enhanced hydrophobicity will selectively absorb oil over water; 2) increasing sorbent porosity results in increased oil absorption capacity; 3) a balance between porosity and mechanical integrity is required for a robust and reusable oil sorbent material; and 4) long term reusability in separating surfactant stabilized emulsions requires a combination of small pore sizes and materials that repel surfactant adsorption. Continued research efforts in developing biodegradable oil sorbents will afford advances in sorbent design, capacity, selectivity, and mechanical integrity with the goal of integrating these materials into an oil retrieval system for a more effective and environmentally friendly process.
Acknowledgements
The authors gratefully acknowledge the National Institutes of Health T32 Translational research in Biomaterials grant (NIH T32EB006359), the NSF (DMR-1410450), and Boston University for support. In addition, the authors would like to thank Professor Muhammad Zaman at Boston University for access to his confocal microscope.
Notes and references
- A. A. Al-Majed, A. R. Adebayo and M. E. Hossain, J. Environ. Manage., 2012, 113, 213–227 CrossRef PubMed
.
- K. Gaaseidnes and J. Turbeville, Pure Appl. Chem., 1999, 71, 95–101 CrossRef CAS
.
- Q. Wei, R. Mather, A. Fotheringham and R. Yang, Mar. Pollut. Bull., 2003, 46, 780–783 CrossRef CAS
.
- M. O. Adebajo, R. L. Frost, J. T. Kloprogge, O. Carmody and S. Kokot, J. Porous Mater., 2003, 10, 159–170 CrossRef CAS
.
- A. K. Kota, G. Kwon, W. Choi, J. M. Mabry and A. Tuteja, Nat. Commun., 2012, 3, 1025 CrossRef PubMed
.
- G. Kwon, A. Kota, Y. Li, A. Sohani, J. M. Mabry and A. Tuteja, Adv. Mater., 2012, 24, 3666–3671 CrossRef CAS PubMed
.
- H. Yoon, S.-H. Na, J.-Y. Choi, S. S. Latthe, M. T. Swihart, S. S. Al-Deyab and S. S. Yoon, Langmuir, 2014, 30, 11761–11769 CrossRef CAS PubMed
.
-
M. Fingas and N. Laroche, Spill Technology Newsletter, 1990, vol. 15, pp. 1–11 Search PubMed.
- F. Muttin, Appl. Ocean Res., 2008, 30, 107–112 CrossRef PubMed
.
-
H. Bernard and K. Jakobson, Effectiveness of Devices for the Control And Clean up of Oil Spills, Offshore Technology Conference, 1972.
-
P. Daling and G. Indrebo, Recent improvements in optimizing use of dispersants as a cost-effective oil spill countermeasure technique, SPE Health, Safety and Environment in Oil and Gas Exploration and Production Conference, 1996.
- O. Carmody, R. Frost, Y. Xi and S. Kokot, J. Colloid Interface Sci., 2007, 305, 17–24 CrossRef CAS PubMed
.
- H. M. Choi and R. M. Cloud, Environ. Sci. Technol., 1992, 26, 772–776 CrossRef CAS
.
- M. M. Radetic, D. M. Jocic, P. M. Jovancic, Z. L. Petrovic and H. F. Thomas, Environ. Sci. Technol., 2003, 37, 1008–1012 CrossRef CAS
.
- G. Deschamps, H. Caruel, M.-E. Borredon, C. Bonnin and C. Vignoles, Environ. Sci. Technol., 2003, 37, 1013–1015 CrossRef CAS
.
- X.-F. Sun, R. Sun and J.-X. Sun, J. Agric. Food Chem., 2002, 50, 6428–6433 CrossRef CAS PubMed
.
- V. Singh, S. Jinka, K. Hake, S. Parameswaran, R. J. Kendall and S. Ramkumar, Ind. Eng. Chem. Res., 2014, 53, 11954–11961 CrossRef CAS
.
- V. Singh, R. J. Kendall, K. Hake and S. Ramkumar, Ind. Eng. Chem. Res., 2013, 52, 6277–6281 CrossRef CAS
.
- Z. Xue, Y. Cao, N. Liu, L. Feng and L. Jiang, J. Mater. Chem. A, 2014, 2, 2445–2460 CAS
.
- Q. Zhu, Q. Pan and F. Liu, J. Phys. Chem. C, 2011, 115, 17464–17470 CAS
.
- J. Wu, N. Wang, L. Wang, H. Dong, Y. Zhao and L. Jiang, ACS Appl. Mater. Interfaces, 2012, 4, 3207–3212 CAS
.
- H. Zhu, S. Qiu, W. Jiang, D. Wu and C. Zhang, Environ. Sci. Technol., 2011, 45, 4527–4531 CrossRef CAS PubMed
.
- S. Huang, ACS Appl. Mater. Interfaces, 2014, 6, 17144–17150 CAS
.
- V. H. Pham and J. H. Dickerson, ACS Appl. Mater. Interfaces, 2014, 6, 14181–14188 CAS
.
- Y. Pan, K. Shi, C. Peng, W. Wang, Z. Liu and X. Ji, ACS Appl. Mater. Interfaces, 2014, 6, 8651–8659 CAS
.
- J. Lin, B. Ding, J. Yang, J. Yu and G. Sun, Nanoscale, 2012, 4, 176–182 RSC
.
- Y. Zhang, S. Wei, F. Liu, Y. Du, S. Liu, Y. Ji, T. Yokoi, T. Tatsumi and F.-S. Xiao, Nano Today, 2009, 4, 135–142 CrossRef CAS PubMed
.
- D. Ceylan, S. Dogu, B. Karacik, S. D. Yakan, O. S. Okay and O. Okay, Environ. Sci. Technol., 2009, 43, 3846–3852 CrossRef CAS
.
- S.-J. Choi, T.-H. Kwon, H. Im, D.-I. Moon, D. J. Baek, M.-L. Seol, J. P. Duarte and Y.-K. Choi, ACS Appl. Mater. Interfaces, 2011, 3, 4552–4556 CAS
.
- A. Zhang, M. Chen, C. Du, H. Guo, H. Bai and L. Li, ACS Appl. Mater. Interfaces, 2013, 5, 10201–10206 CAS
.
- A. Rizvi, R. K. Chu, J. H. Lee and C. B. Park, ACS Appl. Mater. Interfaces, 2014, 6, 21131–21140 CAS
.
- Y. Liu, J. Ma, T. Wu, X. Wang, G. Huang, Y. Liu, H. Qiu, Y. Li, W. Wang and J. Gao, ACS Appl. Mater. Interfaces, 2013, 5, 10018–10026 CAS
.
- D. N. Tran, S. Kabiri, T. R. Sim and D. Losic, Environ. Sci.: Water Res. Technol., 2015, 1, 298–305 CAS
.
- S. Kabiri, D. N. Tran, T. Altalhi and D. Losic, Carbon, 2014, 80, 523–533 CrossRef CAS PubMed
.
- X. Gui, Z. Zeng, Z. Lin, Q. Gan, R. Xiang, Y. Zhu, A. Cao and Z. Tang, ACS Appl. Mater. Interfaces, 2013, 5, 5845–5850 CAS
.
- C.-F. Wang and S.-J. Lin, ACS Appl. Mater. Interfaces, 2013, 5, 8861–8864 CAS
.
- X. Zhou, Z. Zhang, X. Xu, X. Men and X. Zhu, Ind. Eng. Chem. Res., 2013, 52, 9411–9416 CrossRef CAS
.
- Y. Chu and Q. Pan, ACS Appl. Mater. Interfaces, 2012, 4, 2420–2425 CAS
.
- J. Lin, F. Tian, Y. Shang, F. Wang, B. Ding and J. Yu, Nanoscale, 2012, 4, 5316–5320 RSC
.
- Z. Xue, Z. Sun, Y. Cao, Y. Chen, L. Tao, K. Li, L. Feng, Q. Fu and Y. Wei, RSC Adv., 2013, 3, 23432–23437 RSC
.
- A. Prathap and K. M. Sureshan, Chem. Commun., 2012, 48, 5250–5252 RSC
.
- J. T. Korhonen, M. Kettunen, R. H. Ras and O. Ikkala, ACS Appl. Mater. Interfaces, 2011, 3, 1813–1816 CAS
.
- Z. Zhang, G. Sèbe, D. Rentsch, T. Zimmermann and P. Tingaut, Chem. Mater., 2014, 26, 2659–2668 CrossRef CAS
.
- S. T. Nguyen, J. Feng, N. T. Le, A. T. Le, N. Hoang, V. B. Tan and H. M. Duong, Ind. Eng. Chem. Res., 2013, 52, 18386–18391 CrossRef CAS
.
- M. Labet and W. Thielemans, Chem. Soc. Rev., 2009, 38, 3484–3504 RSC
.
- Q. P. Pham, U. Sharma and A. G. Mikos, Biomacromolecules, 2006, 7, 2796–2805 CrossRef CAS PubMed
.
- T. K. Dash and V. B. Konkimalla, J. Controlled Release, 2012, 158, 15–33 CrossRef CAS PubMed
.
- M. Kunioka, F. Ninomiya and M. Funabashi, Polym. Degrad. Stab., 2007, 92, 1279–1288 CrossRef CAS PubMed
.
- D.-M. Abou-Zeid, R.-J. Müller and W.-D. Deckwer, J. Biotechnol., 2001, 86, 113–126 CrossRef CAS
.
- N. E. Kimes, A. V. Callaghan, J. M. Suflita and P. J. Morris, Front. Microbiol., 2014, 5, 603 Search PubMed
.
- R. M. Atlas and T. C. Hazen, Environ. Sci. Technol., 2011, 45, 6709–6715 CrossRef CAS PubMed
.
- C. A. Schneider, W. S. Rasband and K. W. Eliceiri, Nat. Methods, 2012, 9, 671–675 CrossRef CAS PubMed
.
- M. Capdevila, A. Maestro, M. Porras and J. M. Gutiérrez, J. Colloid Interface Sci., 2010, 345, 27–33 CrossRef CAS PubMed
.
- A. Marmur, Langmuir, 2003, 19, 8343–8348 CrossRef CAS
.
- R. N. Wenzel, J. Ind. Eng. Chem., 1936, 28, 988–994 CrossRef CAS
.
- A. Cassie and S. Baxter, Trans. Faraday Soc., 1944, 40, 546–551 RSC
.
- S. T. Yohe, J. D. Freedman, E. J. Falde, Y. L. Colson and M. W. Grinstaff, Adv. Funct. Mater., 2013, 23, 3628–3637 CrossRef CAS PubMed
.
- J. Idris, G. Eyu, A. Mansor, Z. Ahmad and C. Chukwuekezie, Sci. World J., 2014, 2014 Search PubMed
.
- I. M. Head, D. M. Jones and W. F. Röling, Nat. Rev. Microbiol., 2006, 4, 173–182 CrossRef CAS PubMed
.
- EIA, Crude oils have different quality characteristics, http://www.eia.gov/todayinenergy/detail.cfm?id=7110, (accessed March 2015)
.
Footnote |
† Electronic supplementary information (ESI) available: Additional figures and experimental protocols. See DOI: 10.1039/c5ew00107b |
|
This journal is © The Royal Society of Chemistry 2015 |
Click here to see how this site uses Cookies. View our privacy policy here.