DOI:
10.1039/C5RA24407B
(Paper)
RSC Adv., 2016,
6, 701-707
Fabrication of robust, damage-tolerant superhydrophobic coatings on naturally micro-grooved wood surfaces†
Received
18th November 2015
, Accepted 15th December 2015
First published on 17th December 2015
Abstract
Achieving durable non-wetting surfaces is extremely challenging for hydrophilic bulk materials with intrinsically heterogeneous surface structures, since the coating materials on the surface protrusions could be easily worn out, thereby exposing the underlying hydrophilic bulk materials and leading to loss of non-wettability. Herein, mechanically robust superhydrophobic surfaces were fabricated on naturally micro-grooved wood based on a two-step process, i.e., first applying a primer coating of transparent epoxy resin to cover the surface microstructures, followed by construction of superhydrophobic films using silica/epoxy resin/fluorinated alkylsilane (FAS) nanocomposites. The as-prepared superhydrophobic coatings on wood showed remarkable tolerance against mechanical damages including sandpaper abrasion, finger-wiping and knife-scratching while retaining their superhydrophobicity owing to their roughness-regenerating capability. The coated wood also exhibited excellent durability against water spray impact and ultraviolet (UV) radiation, and more importantly the wood essentially retained its original color and aesthetic appearance despite the coating treatment, highlighting its potential use in various practical applications.
Introduction
Inspired by many surfaces in nature such as lotus leaves and Nepenthes pitcher plants, a number of artificial superhydrophobic surfaces with excellent water-repellency have been developed by mimicking their surface microtextures.1–5 Such surfaces, which possess the virtue of having a large water contact angle (CA) greater than 150° and exhibiting small contact angle hysteresis, have numerous emerging applications in anti-biofouling,6 anti-icing,7,8 anti-fogging,9 non-wetting fabrics,10–12 water-oil separation13,14 and drag reduction.15 However, as the non-wetting properties rely heavily on the interplay of surface topographical patterns and low-surface-energy coatings, mechanical wear, e.g., sandpaper abrasion, finger wiping and knife scratching, could readily damage the microscopic roughness features as well as the hydrophobic material properties that are essential for superhydrophobicity, leading to permanent destruction of the non-wetting properties of the superhydrophobic surfaces. Furthermore, mechanical contact may also leave impurities and oils on the surfaces, causing organic contamination and loss of water-repellency. Indeed, the poor mechanical durability of artificial superhydrophobic surfaces seriously hinders their practical applications. Development of mechanically resilient surfaces would enable an increasingly wide range of new applications in the future.
Notably, tremendous attention has been focused exclusively on creating various types of superhydrophobic coatings themselves rather than the nature of underlying substrates. The superhydrophobic coatings that have been developed currently are mostly based on rather smooth or homogeneous substrates such as glass, paper, metal and cotton fabrics.16–19 The roughness features inherent on these substrates usually impose little impact on the wetting performance of the applied coatings. In contrast, there are also some hydrophilic bulk materials such as wood that are intrinsically heterogeneous due to the surface anatomical features and porosity. The native wood exhibits a highly-textured cellular structure with minor features (e.g., pits) decorated on the lumen surface (Fig. 2a), forming an alternating “valley” and “protrusion” configuration, which presents a naturally micro-grooved structure on wood surfaces. Although fabrication of superhydrophobic coatings on solid wood substrates has been reported extensively, the mechanical stability of the superhydrophobic surfaces is generally neglected in the literature.20–25 The challenge of this micro-grooved structure in achieving durable superhydrophobic wood surface has been demonstrated in our recent study.26 When the coated wood surface was rubbed against sandpaper, the hydrophobic coating materials were worn out from the tops of the “protrusions” but were kept intact in the “valleys”, exposing the underlying hydrophilic bulk wood. As a result, the surface became sticky towards water, resulting in an increased contact angle hysteresis, even though the Cassie state was still stable.
Unlike artificial superhydrophobic surfaces, natural plant leaves can sustain their non-wettability by regenerating their hydrophobic epicuticular wax layer after it is damaged, which is known as a self-healing function.27,28 Mimicking this self-healing ability to restore the surface functionality in artificial superhydrophobic surfaces may provide an interesting solution to tackle the problem of poor durability caused by mechanical damage. Although some bio-inspired self-healing superhydrophobic surfaces have recently been developed,29–31 the copy of a natural self-healing function that is governed by a biological growth process in lifeless artificial non-wetting surfaces is still confronted with great challenges for practical applications. Alternatively, fabricating a self-repairing topography with roughness-regenerating functionality is a new concept in designing damage-tolerant superhydrophobic surfaces.32–34 Such a bulk material would be able to regenerate the rough surface patterns upon mechanical abrasion because the low-surface-energy microstructures extend throughout its whole volume.
Herein, we report a novel method to fabricate damage-tolerant superhydrophobic coatings on naturally micro-grooved wood surfaces. Our strategy to design damage-tolerant superhydrophobic coatings is illustrated in Fig. 1. As the naturally micro-grooved structures on the wood surface are not beneficial for achieving mechanical durability of the coatings, we initially applied a primer coating of transparent epoxy resin to cover the roughness features inherent on the wood surface, thus obtaining a homogeneous and smooth surface, on which the superhydrophobic coating was constructed thereafter. To obtain mechanically durable superhydrophobic surfaces, an organic–inorganic hybrid coating solution was prepared by using fluorinated alkylsilane (FAS) functionalized silica nanoparticles dispersed in the polymer matrix of epoxy resin that also contained FAS, in which epoxy resin was expected to bind the silica particles together and anchor the particles tightly on the substrate. The as-prepared coating solution was then directly applied onto the pre-coated wood using a solution-dipping method. This procedure was repeated multiple times to enable full deposition of the silica/epoxy resin/FAS nanocomposites on the surface and to achieve an adequate coating thickness, which is believed to be essential for the mechanical robustness. The hybrid coating can sustain its roughness features and superhydrophobicity upon mechanical damages including sandpaper abrasion, finger wiping and knife scratching. The coated wood also exhibited remarkable durability against water spray and ultraviolet (UV) radiation. Importantly, the applied coating possessed good optical transparency without hiding the original color and aesthetic appearance of wood. Such mechanically resilient superhydrophobic wood surfaces highlight their great potential uses in practical applications, offering an interesting alternative to conventional wood modification systems.
 |
| Fig. 1 Sketch of the procedure to prepare superhydrophobic coatings on wood. | |
Experimental
Materials
Silica nanoparticles (10–20 nm in diameter) and 1H,1H,2H,2H-perfluorodecyltriethoxysilane (C16F17H19O3Si, FAS) was obtained from Sigma-Aldrich. Tetrahydrofuran (THF) was purchased from Sinopharm Chemical Reagent Co., Ltd (Shanghai, China). Epoxy resin and curing agent 651 were purchased from Xingchen Synthetic Material Co., Ltd (Nantong, China). All chemicals were used as received without further purification. Wood samples of Chinese white pine (Pinus armandii Franch) were cut parallel to grain direction and sawn into cubic blocks of 20 mm × 20 mm × 20 mm (radial × longitudinal × tangential), which were ultrasonically rinsed with ethanol and distilled water and then dried at 103 °C for 5 h before use.
Preparation of superhydrophobic coatings on wood
Epoxy resin (21 g) was mixed with THF (30 mL) with magnetic stirring for 20 min to form the Solution A, and the corresponding curing agent (2.8 g) was dissolved to THF (30 mL) to form the Solution B. The Solution A and B were mixed together with magnetic stirring for 30 min to obtain a primer coating solution of epoxy resin. The wood samples were dipped into the coating solution for 10 min, and then air-dried for 15 min. This procedure was repeated for 3 times. The pre-coated samples were then cured at 80 °C for 3 h.
Silica nanoparticles (0.5 g) were dispersed in THF (40 mL) with the aid of ultrasonication for 30 min. FAS (1 mL) was added to the solution in order to obtain FAS-modified hydrophobic silica particles. The reaction was allowed to continue for 1 h under constant magnetic stirring at room temperature to form the Solution C. Epoxy resin (1 g) was mixed with THF (10 mL) with magnetic stirring for 20 min to form the Solution D. The Solution C and D were mixed together, and FAS (1 mL) was added to the mixed solution. The solution was then ultrasonicated for 1 h to form the Solution E. Curing agent (0.13 g) was dissolved to THF (10 mL) to form the Solution F.
Prior to the coating treatment, the Solution E and F were mixed together with the aid of ultrasonication for 30 min at low temperature (6 °C) to form a coating solution. The epoxy resin pre-coated wood samples were dipped into the as-prepared coating solution for 10 min, and air-dried for 15 min. This procedure was repeated for 10 times to allow full deposition of the silica/epoxy resin/FAS nanocomposites on the surface and to achieve an adequate coating thickness. The coated samples were then cured at 80 °C for 3 h.
Characterization
The surface microstructure and morphology of the coated wood were examined using field-emission scanning electron microscopy (FE-SEM, Zeiss SUPRA 55, Germany) in high vacuum mode at an acceleration voltage of 5 kV. A thin aurum (Au) layer was sputtered onto the sample surfaces to improve conductivity prior to observation. The FAS-modified silica nanoparticles in the coating solution were observed by transmission electron microscopy (TEM, Tecnai G2 F30, FEI, USA). TEM samples were prepared by placing one droplet of THF dispersion of the coating solution on a copper grid and then letting it dry at room temperature. Changes in surface chemistry of the wood before and after the coating treatment were analyzed using Fourier transform infrared spectroscopy (FTIR, Nicolet Magna-IR 750, USA) equipped with an attenuated total reflection (ATR) accessory. The surface morphology and roughness of the coated wood were examined by atomic force microscopy (AFM, Dimension Icon, Bruker, Germany) with tapping mode. The scanning scale is 3 μm × 3 μm.
Measurements of water contact angle (CA) and sliding angel (SA) were carried out using a commercial contact angle meter (Shanghai Zhongchen JC2000D, China) at room temperature. A small droplet of distilled water (5 μL) was used for the measurement. The SAs were measured by tilting the sample platform equipped with a digital angle meter, and the SA values were determined by the minimum tilt angle at which a water droplet (10 μL) rolls off the surface. The CA and SA values reported represent the mean of 10 measurements.
The water dropping tests were performed to assess the water-repellency of the surfaces by dropping water droplets on them. The coated wood and pristine wood were tested for comparison. Water droplets were dyed with methylene blue to aid visualization. The transient water–surface interaction was also captured by using a Photron FASTCAM SA1.1 monochrome high-speed camera (2000 frame per s). Water droplets (∼10 μL) were dropped from a height of 50 mm (tip to surface) to the wood surface using a micro-syringe fitted with a dispensing tip.
The sandpaper abrasion test was performed according to the reported methods.17,35 As schematically depicted in Fig. 5a, under a load of 200 g weight (5 kPa), the sample surface was rubbed against the sandpaper (1500 mesh) and moved for 25 cm along the ruler with a speed of 6 cm s−1. This process is defined as one abrasion cycle, and totally ten cycles were conducted. For comparison, the fabricated wood surfaces with and without primer coatings were tested. CAs and SAs were measured after each abrasion cycle. Changes in surface morphology and chemistry of the coated wood were examined by FE-SEM and FT-IR, respectively.
Results and discussion
Surface morphology
The surface morphologies of the wood substrate before and after the coating treatment are shown in Fig. 2a–c. After primer coating with epoxy resin, the original micro-grooved structures with minor features (e.g., pits, debris) of wood surface were observed to be covered by a continuous smooth polymer film (Fig. 2b). Upon further treatment with silica/epoxy resin/FAS nanocomposites, a particulate morphology can be found on the surface (Fig. 2c). The inset high-magnification image reveals dual-scale roughness patterns consisting of exposed silica nanoparticles superimposed on random microstructures formed by the aggregation of the nanoparticles. TEM image of the hybrid coating solution also reveals that the small silica particles (10–20 nm in diameter) exhibit a tendency to aggregate with each other in the presence of epoxy resin and FAS (Fig. S1, ESI†). Cross-sectional SEM image of the coated wood surface is shown in Fig. 2d, in which different sections, i.e., pristine wood, primer coating and superhydrophobic film, were indicated by the arrows. The epoxy-resin primer coating had a thickness of ∼10 μm, which is sufficient to cover the underlying wood structures. The multiple coating cycles resulted in a superhydrophobic film of ∼6 μm in thickness. A magnified view reveals well-developed microstructures with rather high integrity (Fig. 2e). The dual-scale features with micro-scale roughness superimposed with a nanostructure can also be clearly observed in the three-dimensional AFM image with a root-mean-square (RMS) roughness of 80.8 nm (Fig. 2f).
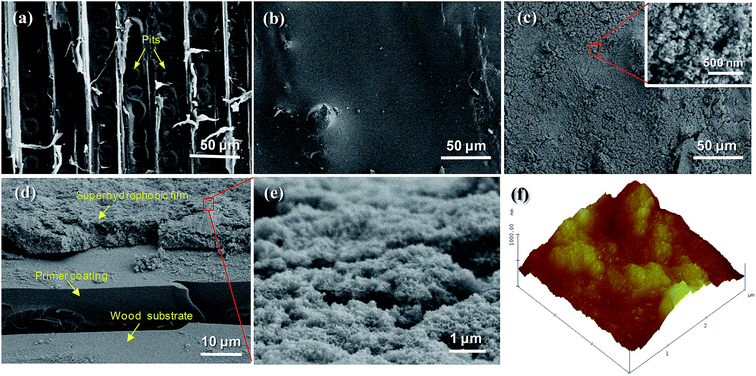 |
| Fig. 2 (a–c) Top-view SEM images of pristine (b), epoxy resin pre-coated (c), and epoxy resin/FAS/silica nanoparticles further coated (e) wood. (d) Cross-sectional SEM image of the coated wood where the magnified view of the superhydrophobic film is shown in (g). The arrows indicate different sections across the surface. (f) Three-dimensional AFM images of the superhydrophobic film. | |
FT-IR examination confirmed that the coating treatment resulted in new absorptions at 1200 and 1144 cm−1, which were assigned to the C–F stretching vibrations of FAS, contributing to the low surface energy of the surface, and the new peak at 826 cm−1 can be attributed to epoxy groups in the epoxy resin, which is believed to play a key role in the robustness of the microstructures (Fig. 3).
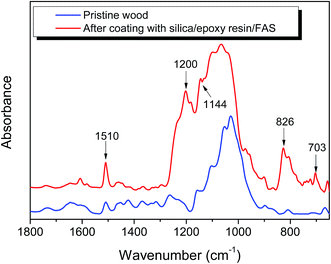 |
| Fig. 3 FTIR spectra of the wood surface before and after coating treatment. | |
Wettability
As shown in Fig. 4a, spherical water droplets (dyed in blue for clear observation) rested on the as-prepared wood surface with a static CA of 152° ± 2° and a sliding angle (SA) lower than 4°, which is in contrast to an immediate spreading of water on the pristine wood owing to its hydrophilic nature. It should be noted that the applied coating exhibited good optical transparency, and the coated wood essentially maintained its original color and aesthetic appearance, as measured using a spectrocolorimeter (Table S1, ESI†), which is of great significance to its practical applications. Upon immersion in water, the coated wood surface appeared like a silver mirror when viewed at a glancing angle (Fig. 4b), due to the light reflectance at the trapped air layer on the surface, which can effectively prevent wetting on the surface under water. The extremely low adhesion of the coated surface to water was demonstrated by the water droplets facilely bouncing and immediately rolling off upon being dropped to the surface (Movie S1, ESI†). To better visualize water–surface interaction, a high-speed camera was used to capture the transient process of water droplets (10 μL) contacting the surface in water dropping tests (Fig. 4c, Movie S2, ESI†). The water droplet was observed to rebound twice before it went through damped oscillations and finally rested on the coated surface, indicating exceptional non-wetting properties, whereas the droplet adhered tightly to the pristine wood without bouncing once it hit the surface.
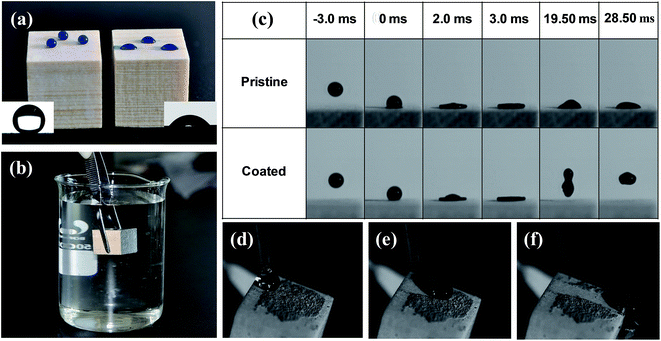 |
| Fig. 4 (a) Photograph of water droplets (dyed with methylene blue) on the coated and pristine wood. (b) Mirror-like phenomenon can be observed on the coated wood submerged in water. (c) Time-lapse photographs of water droplets (10 μL) bouncing on the coated wood in contrast to water adhesion to the pristine wood. (d–f) Time-lapse photographs of water droplet removing dirt from the coated wood, revealing a self-cleaning surface. | |
Self-cleaning effect
The as-prepared wood surface was not only superhydrophobic but also showed good self-cleaning property, which was firstly demonstrated by a dirt removal test (Movie S3, ESI†). Upon being dropped to the dye-powder dusted surfaces, water drops readily rolled off the coated surface, taking the dirt away and resulting in a dry and clean surface, whereas water drops were mixed with the dirt and stayed on the pristine wood, leading to a wet and polluted surface. The high-speed motion capture revealed the dirt removal process in great detail (Fig. 4d–f, Movie S4, ESI†). As the water droplet rolled off the surface, it picked up the dirt specks and carried them away, and the surface was thus cleaned along the path of the droplet movement. The self-cleaning ability was also tested by immersing the wood samples in the methylene blue dyed water (Movie S3, ESI†). When being withdrawn from the water, the coated wood remained clean with no trace of contamination by the dyed water, which is in sharp contrast to the fully colored and polluted pristine wood. In addition, the coated wood also exhibited remarkable repellency towards oil contamination. As shown in Movie S3 (ESI†), immersion of the coated wood in ethylene glycol (γlv = 47.3 mN m−1) resulted in a totally dry surface without any oil adhered to the surface. The low-surface-energy FAS and the well-developed roughness patterns in the coatings are believed to contribute to the formation of super-amphiphobic surfaces that repel both water and oils.
Mechanical robustness and durability
For practical applications, the microscopic roughness textures of superhydrophobic surface need to sustain various types of mechanical damages in real-life conditions. The sandpaper abrasion tests were carried out to examine the abrasion durability of the fabricated coatings on wood. With a pressure of 5 kPa exerted, the coated wood surface was rubbed against the sandpaper (1500 mesh) and moved for 25 cm along the ruler (Fig. 5a). This process is defined as one abrasion cycle, and totally ten cycles were conducted. For comparison, the fabricated wood surfaces with and without primer coatings were tested. The water CAs and SAs after each abrasion cycle are shown in Fig. 5b. It can be observed that the epoxy resin pre-coated wood still sustained the superhydrophobicity with CAs around 150° and SAs lower than 6°, after being scratched repeatedly. The mechanical abrasion resistance of the surface is also highlighted in Movie S5 (ESI†), in which one can see that water droplets can still easily roll off the surface after repeated abrasion, although a trace amount of materials was observed to be worn off from the coated surface after each abrasion cycle. It was noted that the surface microstructures with dual-scale roughness patterns were still retained upon being abraded repeatedly (Fig. 5c), and the silica/epoxy resin/FAS composition was also maintained in the coating surface after abrasion, as examined by FT-IR spectroscopy (Fig. S2, ESI†), which are essential for the mechanical durability of the surface.
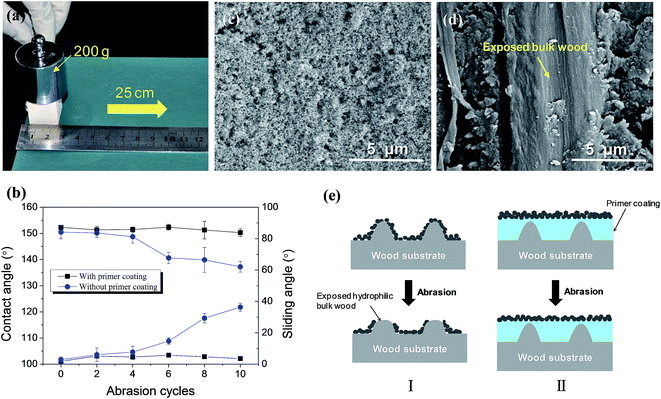 |
| Fig. 5 (a) Photograph depicting the sandpaper abrasion test. (b) CAs and SAs as a function of mechanical abrasion cycles for the treated wood with and without primer coating. (c and d) SEM images of the wood surface with (c) and without (d) primer coating after 10 cycles of abrasion. The arrow indicates the exposed bulk wood due to abrasion. (e) Sketch illustrating abrasion-induced damage to the wood surface without primer coating (I) in contrast to the surface with primer coating (II). | |
By contrast, the treated wood without a primer coating lost its superhydrophobicity with a decreased water CA of ∼140° and an increased SA of ∼40°, upon being scratched for 10 cycles (Fig. 5b), which could be attributed to the exposure of the underlying hydrophilic bulk wood due to abrasion (Fig. 5d). As schematically illustrated in Fig. 5e, the mechanical abrasion tends to remove the coating materials on top of the “protrusions” of the wood surface, exposing the underlying hydrophilic bulk wood and thus leading to sticking of water on the surface. Alternatively, with a primer coating to fill the “valleys” and cover the micro-grooved structures, the hydrophilic bulk wood is protected from direct exposure to abrasion, and more importantly, a homogeneous and smooth surface is thus generated, on which a durable coating can be relatively easily constructed. By a multiple coating procedure, a superhydrophobic film with adequate thickness is achieved, which can sustain the abrasion damage by regenerating the surface patterns as a result of the abrasion itself, since a removal of the top layer of the coating material will expose a new rough surface that is similar to the previous one. Hence, this roughness-regenerating functionality confers the fabricated wood coatings with good mechanical abrasion tolerance.
The mechanical durability of the superhydrophobic coating was also assessed by a finger-wipe test. As shown in Movie S6 (ESI†), upon being pressed by a finger, the wood surface can still exhibit silver-mirror phenomenon after immersion in water, and water drops were capable of rolling off the finger-wiped surface easily upon being withdrawn from the water. This indicates that the coating can sustain the mechanical damage by finger pressing as well as the oil and salt contaminations caused by finger contact, resulting in a finger-touchable surface. The mechanical robustness of the coating is also exhibited in a knife-scratch test (Movie S7, ESI†). Despite being scratched repeatedly by a razor blade, the wood surface retained its good water-repellency, and water drops can still roll off the damaged surface easily.
For applications in outdoor environments, the superhydrophobic wood surfaces also need to sustain the damages caused by environmental factors such as moisture, rainfall and UV light. Water spray tests were performed to assess the surface durability against water spray impact (Fig. 6a). The coated samples were impinged by a water jet at a distance of 30 cm with a water pressure of 35 kPa acting on the surface. The test consists of seven cycles, with each cycle lasting 10 s. It can be seen that the coated wood maintained the non-wetting properties with almost constant water CAs of ∼150° and SAs lower than 10°, after being impinged repeatedly by the water spray (Fig. 6b). This indicates that the well-developed microstructure of the coating is robust enough to sustain the mechanical erosion caused by water spray without impairing its water-repellency.
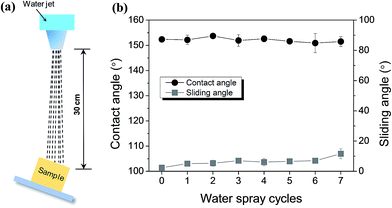 |
| Fig. 6 (a) Schematic illustration of water spray test. (b) CAs and SAs as a function of water spray cycles for the coated wood. | |
The as-prepared superhydrophobic wood also exhibited great resistance against UV radiation, which is known to be extremely harmful to wood. As shown in Fig. 7a, upon exposure to UV radiation for 80 h, the coated wood retained the superhydrophobicity with water droplets exhibiting typical spherical shapes on the surface, while water readily penetrated into the pristine wood. The coated wood sustained the non-wetting properties with large water CAs and low SAs throughout the UV radiation process (Fig. 7b). This photo-stabilizing effect could be attributed to the excellent stability of C–F bonds with a bonding energy up to 485 kJ mol−1,36 which makes the fluorinated groups in the hybrid coating difficult to be decomposed under UV radiation and thereby the low surface energy of the surface was retained. Furthermore, the coated wood almost maintained its original color with a small color change (ΔE*) of ∼5.8, which was in contrast to the obviously discolored pristine wood with a ΔE* of ∼18, due to UV radiation (Fig. 7a and S3, ESI†). The superhydrophobic coating is therefore durable enough to withstand UV-induced photodegradation while retaining the superhydrophobicity and simultaneously preserving the original wood color, which is extremely crucial for its outdoor applications.
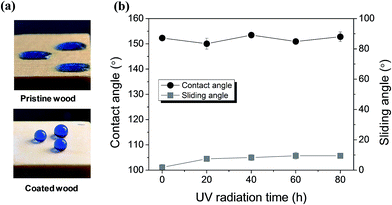 |
| Fig. 7 (a) Photographs of water droplets (dyed with methylene blue) on pristine and coated wood after exposure to UV radiation for 80 h. (b) CAs and SAs as a function of exposure time in UV radiation for the coated wood. | |
It should be noted that the newly developed organic–inorganic hybrid coatings are feasible to be incorporated into the traditional wood clear coatings since they possess good optical transparency. Further study is needed to investigate the overall performance of the hybrid coatings incorporated in wood clear coatings in terms of water-repellency, UV protection, etc.
Conclusions
In summary, we have demonstrated a novel method to fabricate robust superhydrophobic coatings on naturally micro-grooved wood surfaces based on a two-step process, consisting of initially applying a primer coating to cover the surface microstructures, followed by construction of superhydrophobic films with adequate thickness using silica/epoxy resin/FAS nanocomposites. The resulting superhydrophobic coatings on wood showed good self-cleaning properties as well as remarkable tolerance against mechanical damages including sandpaper abrasion, finger wiping and knife scratching whilst retaining their superhydrophobicity owing to their roughness-regenerating capability. The coated wood also exhibited excellent durability against water spray impact and UV radiation. Importantly, the wood retained its original color and aesthetic appearance in spite of the coating treatment. Such mechanically resilient and durable superhydrophobic wood would find many uses in outdoor applications such as garden building, fencing and flooring. In addition to wood, the approach presented here may also be applied for fabricating mechanically durable superhydrophobic coatings on other hydrophilic bulk materials with sophisticated surface structures.
Acknowledgements
This work was financially supported by the National Natural Science Foundation of China (NSFC grants 31570554 and 31170527). We thank Dr Qinwei Ma from Beijing Institute of Technology (Beijing, China) for providing high-speed motion capture system.
References
- L. Feng, S. Li, Y. Li, H. Li, L. Zhang, J. Zhai, Y. Song, B. Liu, L. Jiang and D. Zhu, Adv. Mater., 2002, 14, 1857–1860 CrossRef.
- F. Xia and L. Jiang, Adv. Mater., 2008, 20, 2842–2858 CrossRef CAS.
- J. Genzer and A. Marmur, MRS Bull., 2008, 33, 742–746 CrossRef CAS.
- B. Bhushan, Philos. Trans. R. Soc., A, 2009, 367, 1445–1486 CrossRef CAS PubMed.
- T. S. Wong, S. H. Kang, S. K. Y. Tang, E. J. Smythe, B. D. Hatton, A. Grinthal and J. Aizenberg, Nature, 2011, 477, 443–447 CrossRef CAS PubMed.
- H. Yang and P. Jiang, Langmuir, 2010, 26, 12598–12604 CrossRef CAS PubMed.
- L. Cao, A. K. Jones, V. K. Sikka, J. Wu and D. Gao, Langmuir, 2009, 25, 12444–12448 CrossRef CAS PubMed.
- Y. Wang, J. Xue, Q. Wang, Q. Chen and J. Ding, ACS Appl. Mater. Interfaces, 2013, 5, 3370–3381 CAS.
- X. Gao, X. Yan, X. Yao, L. Xu, K. Zhang, J. Zhang, B. Yang and L. Jiang, Adv. Mater., 2007, 19, 2213–2217 CrossRef CAS.
- J. Zimmermann, F. A. Reifler, G. Fortunato, L. Gerhardt and S. Seeger, Adv. Funct. Mater., 2008, 18, 3662–3669 CrossRef CAS.
- B. Deng, R. Cai, Y. Yu, H. Jiang, C. Wang, J. Li, L. Li, M. Yu, J. Li, L. Xie, Q. Huang and C. Fan, Adv. Mater., 2010, 22, 5473–5477 CrossRef CAS PubMed.
- H. Zhou, H. Wang, H. Niu, A. Gestos, X. Wang and T. Lin, Adv. Mater., 2012, 24, 2409–2412 CrossRef CAS PubMed.
- X. Zhang, Y. Guo, P. Zhang, Z. Wu and Z. Zhang, ACS Appl. Mater. Interfaces, 2012, 4, 1742–1746 CAS.
- J. Li, L. Yan, Y. Zhao, F. Zha, Q. Wang and Z. Lei, Phys. Chem. Chem. Phys., 2015, 17, 6451–6457 RSC.
- F. Shi, J. Niu, J. Liu, F. Liu, Z. Wang, X. Feng and X. Zhang, Adv. Mater., 2007, 19, 2257–2261 CrossRef CAS.
- X. Deng, L. Mammen, H. Butt and D. Vollmer, Science, 2012, 335, 67–70 CrossRef CAS PubMed.
- Y. Lu, S. Sathasivam, J. Song, C. R. Crick, C. J. Carmalt and I. P. Parkin, Science, 2015, 347, 1132–1135 CrossRef CAS PubMed.
- H. Zhou, H. Wang, H. Niu, A. Gestos and T. Lin, Adv. Funct. Mater., 2013, 23, 1664–1670 CrossRef CAS.
- S. Chen, X. Li, Y. Li and J. Sun, ACS Nano, 2015, 9, 4070–4076 CrossRef CAS PubMed.
- C. Wang, C. Piao and C. Lucas, J. Appl. Polym. Sci., 2011, 119, 1667–1672 CrossRef CAS.
- Y. Fu, H. Yu, Q. Sun, G. Li and Y. Liu, Holzforschung, 2012, 66, 739–744 CrossRef CAS.
- X. Wang, Y. Chai and J. Liu, Holzforschung, 2013, 67, 667–672 CrossRef CAS.
- X. Wang, S. Liu, H. Chang and J. Liu, Wood Fiber Sci., 2014, 46, 109–117 CAS.
- H. Chang, K. Tu, X. Wang and J. Liu, BioResources, 2015, 10, 2585–2596 CAS.
- J. Li, H. Zheng, Q. Sun, S. Han, B. Fan, Q. Yao, C. Yan and C. Jin, RSC Adv., 2015, 5, 62265–62272 RSC.
- H. Chang, K. Tu, X. Wang and J. Liu, RSC Adv., 2015, 5, 30647–30653 RSC.
- C. Neinhuis, K. Koch and W. Barthlott, Planta, 2001, 213, 427–434 CrossRef CAS PubMed.
- K. Koch, B. Bhushan, H. Ensikat and W. Barthlott, Philos. Trans. R. Soc., A, 2009, 367, 1673–1688 CrossRef PubMed.
- Y. Li, L. Li and J. Sun, Angew. Chem., Int. Ed., 2010, 49, 6129–6133 CrossRef CAS PubMed.
- H. Wang, H. Zhou, A. Gestos, J. Fang and T. Lin, ACS Appl. Mater. Interfaces, 2013, 5, 10221–10226 CAS.
- Y. Liu, Z. Liu, Y. Liu, H. Hu, Y. Li, P. Yan, B. Yu and F. Zhou, Small, 2015, 11, 426–431 CrossRef CAS PubMed.
- T. Verho, C. Bower, P. Andrew, S. Franssila, O. Ikkala and R. H. A. Ras, Adv. Mater., 2011, 23, 673–679 CrossRef CAS PubMed.
- H. Jin, X. Tian, O. Ikkala and R. H. A. Ras, ACS Appl. Mater. Interfaces, 2013, 5, 485–488 CAS.
- X. Zhang, Y. Guo, H. Chen, W. Zhu and P. Zhang, J. Mater. Chem. A, 2014, 2, 9002–9006 CAS.
- X. Zhu, Z. Zhang, X. Men, J. Yang, K. Wang, X. Xu, X. Zhou and Q. Xue, J. Mater. Chem., 2011, 21, 15793–15797 RSC.
- K. Chen, S. Zhou and L. Wu, Chem. Commun., 2014, 50, 11891–11894 RSC.
Footnote |
† Electronic supplementary information (ESI) available: Experimental details of self-cleaning tests (dirt removal, repellency towards dyed water contamination and oil repellency), mechanical robustness tests (finger-wipe, knife-scratch), water spray and UV radiation tests, supplementary Figures, Table and Movies. See DOI: 10.1039/c5ra24407b |
|
This journal is © The Royal Society of Chemistry 2016 |
Click here to see how this site uses Cookies. View our privacy policy here.