DOI:
10.1039/C7RA03699J
(Paper)
RSC Adv., 2017,
7, 29806-29814
Electrospun TiO2/ZnO/PAN hybrid nanofiber membranes with efficient photocatalytic activity
Received
31st March 2017
, Accepted 1st June 2017
First published on 7th June 2017
Abstract
Electrospun polyacrylonitrile (PAN) nanofibers were decorated with TiO2, ZnO and TiO2/ZnO nanoparticles for the first time to prepare flexible multifunctional nanofibrous membranes. First, the arc-discharge process was utilized to prepare TiO2, ZnO and TiO2/ZnO nanoparticles and then the hybrid electrospun nanofibers were spun from PAN/nanoparticle colloids. X-ray diffraction, scanning electron microscopy (SEM) and transmission electron microscopy (TEM) were utilized to characterize the resulting nanoparticles and nanofiber loaded nanoparticles. The microscopic investigations revealed that the specifically TiO2 nanoparticles tend to agglomerate within the PAN nanofiber resulting increased surface roughness; however, ZnO nanorods with 1D morphology are aligned as parallel to the fiber axis. Photocatalytic activity of the hybrid nanofibers was performed by pursuing the degradation of malachite green (MG) dye under UV light irradiation. The fabricated TiO2/ZnO/PAN hybrid nanofibers showed excellent photocatalytic efficiency with at least two times higher reaction rates compared to the bare PAN nanofibers. The results suggest that the photocatalytically active TiO2/ZnO/PAN hybrid nanofibers can be considered as filtering materials for a variety of applications in the fields of wastewater systems without the need of post processing stages for separating catalysts from the liquid medium.
1. Introduction
Treatment of wastewater in the industries like pharmaceuticals, textile, leather, chemicals, and petroleum, etc. is required to decompose organic dyes.1 Different water treatment and purification methods,2–4 are often utilized to remove dyes from liquid environments due to associated serious health issues5 and environmental problems. Photocatalytic approaches are increasingly being addressed to develop less expensive,6 low energy consumption, high efficiency, and a practically advanced oxidization technique for disposal of the pollutants.7,8 Improving photocatalytic activity by modifying the catalyst has been an active research area in the past decade.9 Researchers have expressed various methods, such as doping transition metals10 and non-metals,11 and forming composite photocatalysts from different semiconductors,12 etc., to enhance the photocatalytic activity of nanocatalysts. The results reveal that nearly all composite semiconductors have higher photocatalytic activity than a single semiconductor. Zinc oxide (ZnO) is a wide bandgap semiconductor (3.37 eV) with a 60 meV exciton binding energy, which permits laser emission at room temperature. This large band gap is suitable for the use of ZnO to collect high-energy photons (UV light) as a photocatalyst in environmental cleaning.13 Titanium(IV) dioxide (titania) is an important transition metal oxide, widely used as a catalyst support, semiconductor photocatalyst, and gas and humidity sensor.14 Titania exists in three crystal forms as rutile, anatase, and brookite. Thermodynamically stable rutile phase of titania has a tetragonal structure with 3.0 eV band gap of the bulk which is smaller than anatase phase. In some cases, rutile was found to be more active for photocatalysis.15
Up until now, in most photocatalysis studies, post-treatment removal of semiconducting photocatalyst after photocatalytic reaction can be a difficult, time-consuming and costly process.16 Alternatively, the catalyst may be immobilized on a suitable solid inert support with the desired morphology, to eliminate post processes for removing the catalyst.17 Among these forms, the nanotube and nanofiber with the 1-D characteristic, which is to have one dimension many times longer than the other ones, are of particular interest. These structures provide high effective surface area and a defined flow pattern along the longer dimension, which greatly contribute to the enhanced photocatalytic efficiency in practical applications. In addition, flexibility and elasticity need to be other essential features of the next generation of photocatalysts. The electrospinning is regarded as a versatile and effective approach to prepare organic flexible nanofibrous mats with tunable diameters due to its advantages of ease of control and environmental compatibility.18,19 The electrospun polyacrylonitrile (PAN) filament forming mats, may be promising as a template polymer for the immobilization of catalytic materials due to their hydrophobic and flexible nature with too low density.20 Therefore, it easily floats on the liquid. This point would make the ability of photodegradation maximized with optimized irradiation efficiency of UV light by avoiding the hindrance of UV source penetration.21
The goal of this study to develop efficient nanofibrous membranes using a scalable process with eliminating the need for post-processing stages of separating catalysts from the liquid medium after degradation of organic dyes. Therefore, we have successfully achieved PAN based electrospun nanocomposite fibers loaded with ZnO and TiO2 nanoparticles. The electrospun fibers were utilized to decolorize an organic dye under UV light irradiation. The results showed that the obtained nanofibers with high surface area exhibit a good photocatalytic activity.
2. Materials and methods
The proposed methodology for preparation and characterization of the PAN based nanocomposite spun fiber mats contains two main fabrication processes as represented schematically in Fig. 1. In the first step, the arc discharge method was implemented to prepare ZnO, TiO2, and ZnO–TiO2 nanostructures, following, PAN-based nanocomposite fibers were spun from PAN/nanoparticle polymer solution as the second step.
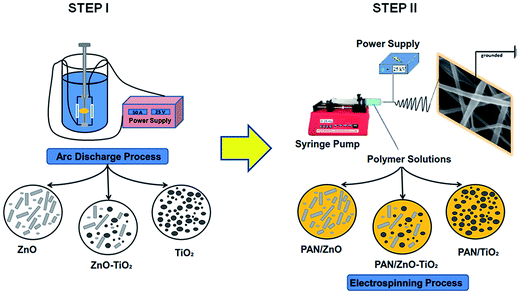 |
| Fig. 1 The methodology used to fabricate PAN based electrospun fibers modified with ZnO, TiO2 and ZnO–TiO2 nanostructures. | |
2.1 Materials
All chemicals were of analytical grade and used without further purification. High purity Zn and Ti rods (Alfa Aesar, 99.99%) were used as electrodes to synthesize ZnO, TiO2, and ZnO–TiO2 nanoparticles. Dimethylformamide (DMF) and malachite green (MG) were purchased from Merck.
2.2 Synthesis of metal oxide nanoparticles
The metal oxide nanoparticles were synthesized by an arc discharge method in de-ionized water medium as described in our previous studies.22–24 Briefly, a voltage controlled arc discharge apparatus containing vertically aligned metal electrodes was submerged in the de-ionized water-filled vessel and the arc was generated between electrodes applying a fixed current. Note that, Ti and Zn rods were directly used as electrodes to synthesize TiO2 and ZnO nanoparticles, respectively, however; Ti–Zn composite electrode was prepared to synthesize ZnO/TiO2 nanocomposite structures. Namely, a hole with the same diameter of Zn rod was drilled through the pure Ti rod and the pure Zn rod was placed within the hole to produce concentric Ti–Zn composite rod acting as an anode during arc discharge process. Discharge voltage was measured and kept constant by controlling the gap between the metal electrodes to maintain stable arc discharge during the process. Anode electrode was consumed during the process and the resulted particles dispersed within the de-ionized water medium. The vessel was kept at room temperature for 24 h to complete settling of the synthesized nanostructures. The settled particles were collected carefully by decanting and centrifuging of the suspensions, subsequently. Finally, the collected nanostructures were washed with de-ionized water and absolute ethanol and dried at 40 °C under vacuum for 24 h.
2.3 Fabrication of hybrid nanofiber
Electrospinning technique was utilized to fabricate PAN based nanocomposite fiber mats. Similar to our previous works,25,26 0.25 g of the arc discharge synthesized nanoparticles (TiO2, ZnO or TiO2/ZnO) were added into 12 mL DMF solution and the mixture was sonicated ultrasonically for 30 min. 1 g of PAN (8% w/v) was added to the homogenized mixture and mixed for 2 h at 60 °C to obtain proper viscosity for electrospinning. Then, the solution was transferred into a 10 mL syringe with a blunt-tipped 23-gauge needle. The distance between the needle tip and the square plate acting as a collector was adjusted as 15 cm. Feed rate of the polymer solution was kept constant during the spinning process as 0.15 mL h−1. The electric field occurred between the needle tip and the square plate was generated using a high voltage power supply with an applied voltage of 25 kV. PAN/ZnO, PAN/TiO2, and PAN/ZnO/TiO2 nanofibers were collected on the plate surface.
2.4 Characterization
XRD patterns of nanofibers were recorded with a Bruker Advance D8 XRD (Cu α source with 1.5406 wavelengths) in powder mode. ZeissEvo scanning electron microscope (SEM) and JEOL 2100 transmission electron microscope (TEM) were used to obtain morphological and structural properties of the nanofibers. The FTIR spectra of all materials were recorded by a Perkin Elmer 1725 spectrophotometer.
2.5 Measurement of photocatalytic activity
Malachite green (MG, C23H25N2·C2HO4·0.5C2H2O4) was used as a model dye to investigate the photocatalytic activity of electrospun PAN, PAN/TiO2, PAN/ZnO and TiO2/ZnO/PAN hybrid nanofiber. Photocatalytic decolorization of MG under UV light was carried out in a Luzchem model 4V photoreactor (Luzchem Research Inc., Canada) equipped with 2 UVC lamps with an emission at λ = 254 nm. 1.2 mg of the electrospun nanoparticles were added into a quartz tube, and 3 mL of MG aqueous solution with the concentration of 1.0 × 10−5 M was introduced. This mixture was magnetically stirred for 30 min in dark to reach the adsorption–desorption equilibrium. Then UV lamps were switched on to start the photocatalytic decolorization of MG. The photocatalytic decolorization of MG was investigated at room temperature in the presence/absence of different catalysts under irradiation/dark for given times. The concentration of the MG dye was evaluated by using the UV-vis spectroscopy method. The degradation efficiency of dye is calculated by the following equation;
where C0 is the initial concentration of dye before irradiation and C is the concentration of dye after a certain irradiation time. In general, the photocatalytic degradation of organic pollutants on the semiconducting oxide can be ascribed to a pseudo-first-order reaction which follows the simplified Langmuir–Hinshelwood model;
where C is the measured MG concentration at different intervals, C0 is the initial MG dye concentration measured after 30 min absorption and k refers to the reaction rate kinetic constant and t is the irradiation time.
3. Results and discussion
3.1 Structure and morphology
The XRD patterns of the arc discharge synthesized nanoparticles are represented in Fig. 2a. The diffraction peaks at 31.77°, 34.42°, 36.25°, 47.45°, 56.60°, and 62.86° are indicative of the typical hexagonal wurtzite ZnO phase (JCPDS no. 30-1451) while the main peaks at 27.7°, 36.1°, 41.4°, and 54.5° correspond to the XRD pattern of the rutile phase of TiO2 (JCPDS no. 88-1175). The breadth and weakness of the TiO2 peaks can be explained by the small grain sizes and amorphous/crystalline structure of the r-TiO2 nanostructures. More details on the amorphous/crystalline structure are discussed in TEM analysis. The use of Zn–Ti composite electrode as an anode during arc discharge process resulted in a nanocomposite formation of ZnO/TiO2 multiphase due to the appearance of h-ZnO and r-TiO2 peaks on the same pattern.22 No characteristic peaks other than h-ZnO and r-TiO2 crystalline phase were appeared in the XRD pattern, implying the high purity of the as-synthesized nanostructures by arc discharge method. Similarly, XRD measurements were further utilized to examine the crystal structure of the electrospun nanocomposite fibers (Fig. 2b). PAN nanofiber exhibits two wider amorphous peaks appear in the ranges of 15 and 20°, 20 and 30° with a moderate degree of crystalline order.27,28 Compared with the XRD curve of the pure PAN fibers, the hybrid electrospun nanofibers indicate crystal planes of the hexagonal wurtzite structure of ZnO and tetragonal rutile TiO2 similar to that described in the literature.29,30 The XRD curve of electrospun TiO2/ZnO/PAN nanocomposite fibers represents both of the metal oxide phases with a slight shift to higher degrees.
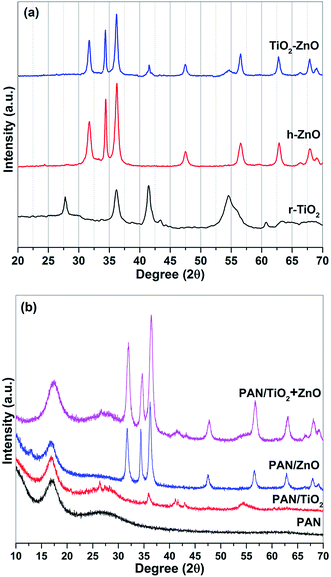 |
| Fig. 2 XRD patterns of (a) nanostructures prepared via arc-discharge method showing rutile structure of TiO2, hexagonal wurtzite structure of ZnO and TiO2–ZnO nanocomposite structures, (b) PAN based nanocomposite electrospun fibers. | |
Electron microscopy monitoring was also utilized to reveal morphologies and structures of the arc discharge synthesized nanostructures. TEM images of the ZnO, TiO2 and ZnO/TiO2 nanostructures are given in Fig. 3. The as-synthesized ZnO nanoparticles are almost in nanorod form (Fig. 3a) with diameters ranging from 10 to 30 nm and lengths range from 50 to 100 nm. The r-TiO2 nanoparticles are in well spherical shape and the diameter of the nanospheres is ranging from 5 to 50 nm (Fig. 3b). The r-TiO2 nanoparticles are in well spherical shape and the average particle size of r-TiO2 nanoparticles was about 5–70 nm (Fig. 3b). The nanoparticle morphology and size distributions can be influenced by arc-discharge parameters.31 In this case, it is quite difficult to control the continuity and stability of the arc-discharge process and therefore the process can result in nanoparticles with different size distributions.32 In contrast, it is apparent that an amorphous shell with the non-uniform thickness (less than 5 nm) was formed around the r-TiO2 nanoparticles. The structure in the shell of the present nanoparticles is different from the amorphous shell.33 We believe that the occurrence of weak and breadth peaks of the as-synthesized r-TiO2 nanospheres on the XRD spectrum directly related with this core–shell structure. Homogeneous distribution of the two phases (h-ZnO and r-TiO2) as ZnO–TiO2 nanocomposite structures was acquired using a composite anode electrode with a combination of Zn and Ti rods during arc discharge process as visualized by a TEM analysis (Fig. 3c). It can be seen from the image that the as-synthesized ZnO–TiO2 nanocomposite structure contains nanorods and nanospheres as two different nanostructure morphologies with similar sizes as observed during analysis of the individual phases.
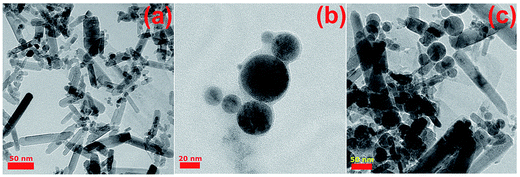 |
| Fig. 3 Representative TEM images of (a) ZnO nanoparticles (scale bar 50 nm), (b) α-TiO2 nanospheres (scale bar 20 nm), (c) ZnO + TiO2 nanocomposite structures (scale bar 50 nm). | |
Typical SEM images of the electrospun hybrid nanocomposite fibers were presented in Fig. 4. The randomly oriented PAN based nanofibers are mainly composed of well-defined smooth outer surfaces and beadles structure with lengths of several hundreds of micrometers to millimeters and diameters range from 50 to 400 nm (Fig. 4a). Incorporation of nanoparticle results in the particular coarseness and roughness of PAN nanofibers but with raised diameters compare to PAN nanofibers. Namely, the PAN nanocomposite fibers have rougher surfaces due to the presence of the TiO2, ZnO and TiO2/ZnO nanoparticles on the surface when compared to pristine PAN nanofibers (Fig. 4b–d). It is evident that the PAN/TiO2 nanocomposite fibers exhibited highest surface roughness which is primarily the result of the highest agglomeration tendency of TiO2 nanospheres due to their smaller sizes rather than ZnO nanoparticles. Moreover, the increment in diameter of nanofiber could be explained the increase in the viscosity of polymer solution due to the incorporation of the nanoparticle. As a result, the increase in polymer solution viscosity leads to an enlargeable and steady fiber diameter.34,35 The EDS mapping of SEM was utilized to explore the presence of Ti and Zn nanoparticle in the nanofibers. Here, Fig. 5 presents EDS elemental maps for PAN/TiO2, PAN/ZnO, and TiO2/ZnO/PAN hybrid nanofibers. It is revealed that C, N, O, Ti and Zn are generally exhibited a homogenous and uniform distribution throughout the nanofibers and thereby proving the presence of Ti and Zn nanoparticles in the nanofibers.
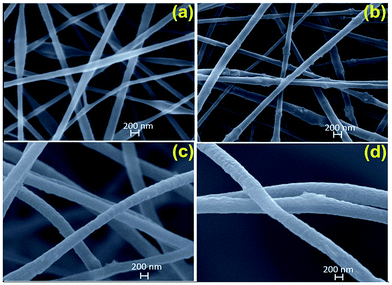 |
| Fig. 4 SEM images of (a) pristine PAN nanofiber, (b) PAN/TiO2 nanofiber, (c) PAN/ZnO and (d) TiO2/ZnO/PAN nanofibers. | |
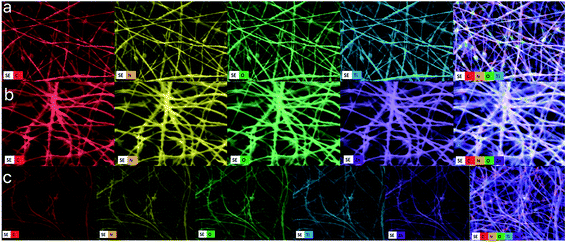 |
| Fig. 5 Elemental mapping images of (a) PAN/TiO2 nanofiber, (b) PAN/ZnO and (c) TiO2/ZnO/PAN nanofibers. | |
The detailed microstructures of the electrospun hybrid nanofibers were further examined utilizing TEM as shown in Fig. 6. PAN nanofibers represent smooth surfaces and the measured diameters consist with the SEM results (Fig. 6a). The TEM image of PAN/TiO2 nanofibers (Fig. 6b) represents a different morphology from the neat PAN nanofibers. TiO2 nanoparticles agglomerated within the PAN fiber as the light areas indicate PAN nanofibers and the dark areas show the nanoparticles. The resulted aggregation of the nanoparticles in the middle of fibers owing to electrostatic repulsion since the TiO2 with positive charges were repulsed by the positive charges on the surface of fibers and.35–37 It is easy to observe that the sizes of the TiO2 nanoparticles are about 5–50 nm, which is in good agreement with those measured by SEM above. Similarly, ZnO nanoparticles can be identified within PAN fibers as shown in Fig. 6c. It must be mentioned that the ZnO nanorods are aligned parallel to nanofiber axis, and their surfaces are relatively smoother with respect to PAN/TiO2 nanofibers. In the case of TiO2/ZnO hybrid nanoparticles were used as filler in PAN nanofibers, the agglomerated TiO2 nanoparticles are again observed on the surface of nanofibers as seen in Fig. 6d. This suggests that TiO2 nanoparticles with relatively smaller sizes agglomerated immediately after dispersion process in PAN solution and were spun as agglomerated structures due to the higher inner diameter of the needle (0.337 mm). TiO2 nanoparticles tend to enlarge on the inside and surface of the hybrid nanofibers. Therefore, TiO2 nanoparticles densely grown in the nanofiber are observed most likely due to an inhomogeneous and aggregation distribution of nanoparticle during electrospinning. Additionally, the HRTEM images of TiO2/ZnO/PAN hybrid nanofiber displays the existence of the ZnO nanorods and the TiO2 nanoparticle in the nanofibers. Note that interplanar distance of 0.26 nm is close to the d spacing of the (002) planes of the hexagonal wurtzite structured of ZnO by confirming the good crystallinity as shown in Fig. 6e. The selected area electron diffraction (SAED) pattern (the inset in the upper left) shows a single crystalline of ZnO nanorod with the growth direction along (001). For TiO2 nanoparticles, the interplanar distance of 0.32 nm is consistent with the d spacing of the (110) planes (Fig. 6f). The selected area electron diffraction (SAED) pattern (the inset in the upper left) if the TiO2 nanosphere show that the nanoparticles exhibit good single crystalline and the basal plane of the rutile crystal structure with along the (001) axis.22
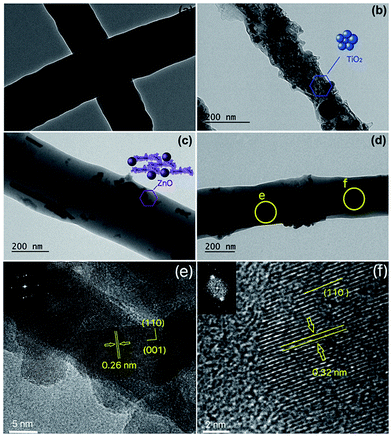 |
| Fig. 6 TEM images of (a) pristine PAN nanofiber, (b) PAN/TiO2 nanofiber, (c) PAN/ZnO and (d) TiO2/ZnO/PAN nanofibers, HR-TEM image of TiO2/ZnO/PAN hybrid nanofibers marked from yellow circle of (d) and the upper left inset the corresponding SAED pattern (e and f). | |
The presence of ZnO and TiO2 nanoparticles within the electrospun PAN nanofibers, EDX analysis of hybrid nanofiber was also performed as presented in Fig. 7. The EDX spectrum demonstrates the fabricated hybrid nanofibers are mainly composed of carbon (C) nitrogen (N), oxygen (O), titanium (Ti), zinc (Zn) elements, the Au element originates in the conductive coating of the nanofibers. Ti, Zn, and Ti–Zn peaks were apparently observed from the EDX results for the PAN–TiO2, PAN–ZnO, and TiO2/ZnO/PAN nanofibers, respectively. The EDX results confirm the presence of nanoparticles on the nanofiber surface as well as the embedding of nanoparticles in PAN nanofiber.
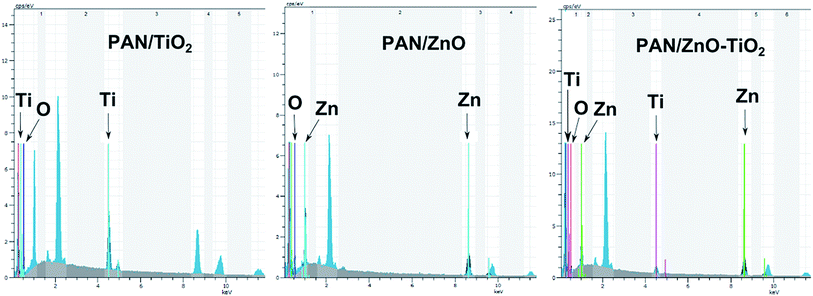 |
| Fig. 7 EDX spectra of electrospun PAN based nanofibers containing TiO2, ZnO and TiO2–ZnO. | |
FTIR analysis was also carried out to understand the structure of the electrospun hybrid nanocomposite fiber and the results are shown in Fig. 8. For the PAN electrospun nanofiber mat, the peaks at 2934 cm−1 and 2873 cm−1, 1414 cm−1, and 1093 cm−1 are assigned to the aliphatic CH group vibration of different modes in OH, CH2 and CH, respectively.38 The peaks at 2241 cm−1 and 1662 cm−1 related to the C
N stretching and C
O stretching vibrations of the acrylamide, respectively.39 Most important to the present discussion is the observation that compared with the nanoparticle-free nanofiber mats, the incorporation of nanoparticles results almost no differences of wavenumbers in the FTIR spectra but their intensities are slightly decreased. We confidently believe that the interaction between h-ZnO and r-TiO2 nanoparticles embedded in PAN matrix is physical, not chemical.40
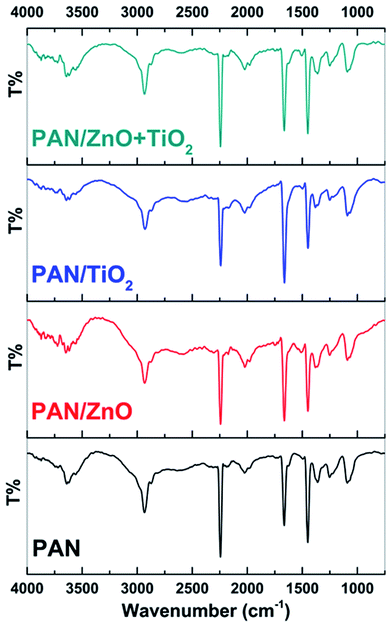 |
| Fig. 8 FTIR spectra of pristine PAN nanofiber, PAN/TiO2 nanofiber, PAN/ZnO and PAN/ZnO–TiO2 nanofibers. | |
3.2 Photocatalytic activity
Photocatalytic activities of the electrospun hybrid nanofibers were investigated by decolorization of malachite green dye solution under UV light source. Blank experiments such as without the nanofibers as the catalysts or light source indicate negligible decolorization of the dye.
The change in optical absorption spectra of MG dye by the electrospun hybrid nanofiber catalysts under UV light irradiation for different time intervals were shown in Fig. 9. It can be seen that the disappearance of the MG dye's characteristic peaks around 423 and 615 nm indicates that the MG dye has been decolorizated that the dye has been degraded gradually with advancing time by the aid of electrospun hybrid nanofibers. The decolorization efficiencies are 93% and 91% in the presence of the electrospun PAN/TiO2 and PAN/ZnO nanofibers, respectively. In the same irradiation time, the bare PAN shows only 71% decolorization efficiency. It is found from photocatalytic experiments that the electrospun TiO2/ZnO/PAN photocatalyst indicates better photocatalytic activity with 99% decolorization efficiency after 204 min. Fig. 10 shows the comparison of the decolorization rate of MG in the presence of electrospun TiO2/ZnO/PAN nanofiber, pure PAN, PAN/TiO2, and PAN/ZnO under UV light irradiation and dark conditions. Under dark conditions, MG dye was decolorized only between 6% and 11% in the presence of electrospun photocatalysts due to adsorption of the dye. After 60 min, MG dye was decolorized around 50% by using electrospun TiO2/ZnO/PAN nanofibers under UV light irradiation. However, in the same conditions, decolorization of MG dye was reached only 29% in the presence of pure PAN nanofiber. MG dye was decolorized completely by TiO2/ZnO/PAN nanofiber after 240 min.
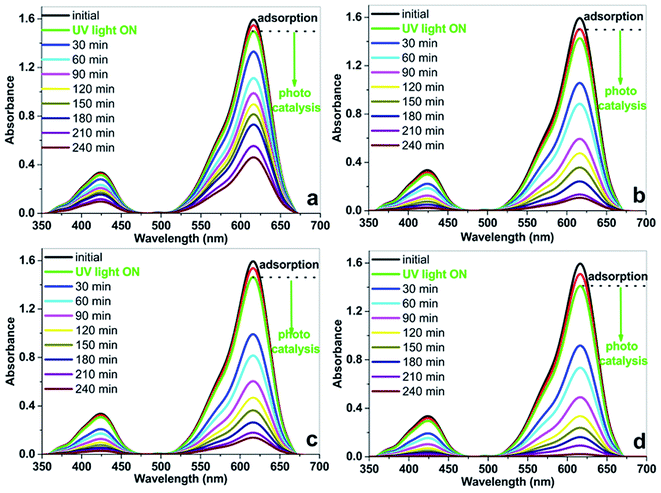 |
| Fig. 9 The change in optical absorption spectra of MG dye by the electrospun hybrid nanofiber catalysts under UV light irradiation for different time intervals. | |
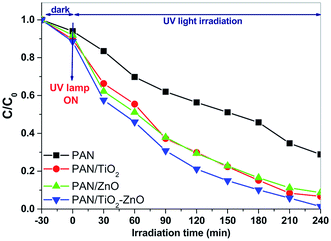 |
| Fig. 10 Decolorization comparison of the MG with respect to time intervals over electrospun PAN, PAN/TiO2, PAN/ZnO and TiO2/ZnO/PAN photocatalyst under UV light (catalyst concentration: 0.3 mg mL−1; initial concentration of dye: 1.0 × 10−5 M). | |
The reaction rate constant, k of the TiO2/ZnO/PAN photocatalyst is 0.01543 min−1 which is approximately two times higher than the reaction rate constants of the bare PAN, PAN/TiO2 and PAN/ZnO nanofibers, respectively (Fig. 11). The results show that the PAN/ZnO/TiO2 photocatalyst illustrate superior photocatalytic activity for decolorization MG dye under UV light irradiation. The activity of electrospun PAN, PAN/TiO2, PAN/ZnO and TiO2/ZnO/PAN nanofiber can be evaluated by comparing the apparent rate constants (kapp) as listed in Table 1.
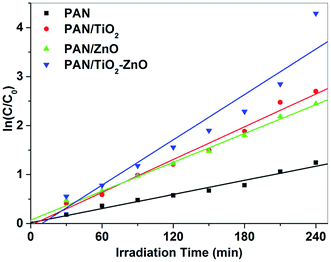 |
| Fig. 11 Comparison of the apparent rate constants of electrospun PAN, PAN/TiO2, PAN/ZnO and TiO2/ZnO/PAN photocatalysts under UV light irradiation (catalyst concentration: 0.3 mg mL−1; initial concentration of dyes: 1.0 × 10−5 M). | |
Table 1 Apparent rate constants (kapp) of dyes degradation and linear regression coefficients from plot of ln(C0/Ct) = kappt for of electrospun PAN, PAN/TiO2, PAN/ZnO and PAN/TiO2–ZnO photocatalysts under UV light irradiation after 210 min (catalyst concentration: 0.3 mg mL−1; initial concentration of dyes: 1.0 × 10−5 M)
|
kapp (min−1) |
R2 |
PAN |
0.0048 |
0.9796 |
PAN/TiO2 |
0.01117 |
0.9875 |
PAN/ZnO |
0.00982 |
0.9948 |
PAN/TiO2–ZnO |
0.01543 |
0.9352 |
The difference in photocatalytic properties between the nanofibers results from their different photocatalytic physics and photocatalytic chemistry. The photocatalytic physics mainly involves two physical factors. One is the absorption of light, and the other is the generation and recombination of the electrons and holes. The photocatalytic chemistry is mainly related to the driving force of the electrons and holes transfer. Since the energy band gaps of TiO2 and ZnO are similar, their differences in the driving forces of the electrons and holes transfer are negligible, suggesting that the photocatalytic chemistry has only fairly slight influence on their photocatalytic properties. On the other hand, numerous research endeavors have indicated that core–shell structures exhibit better photocatalytic performances by enhancing the photogenerated charge carriers.41–43 Thereby, we believe the amorphous shell structure of the r-TiO2 helps utilize the photogenerated charge carriers when it is in a form of thin shell on the crystalline r-TiO2 core. However, the highest photocatalytic activity of the TiO2/ZnO/PAN nanocomposites is attributed to presence of both phases within the PAN matrix fiber with coupled mechanisms such as reduction of electron–hole pair recombination due to the stepwise energy level structure in the composite9,44,45 and synergetic effect between hexagonal wurtzite ZnO and rutile TiO2 phases.9
4. Conclusion
In briefly, we have adapted an associated process of arc-discharge and electrospinning techniques to fabricate PAN/TiO2, PAN/ZnO, and TiO2/ZnO/PAN hybrid nanofibers. Investigation demonstrates that TiO2, ZnO, and TiO2/ZnO nanoparticles have been favorably embedded within electrospun PAN nanofiber. The hybrid nanofibers possess specific surface area as wells as being flexible in structure, resulting in a boost of photocatalytic efficiency. Also, TiO2/ZnO/PAN hybrid nanofibers have displayed better photocatalytic activity compared to the bare PAN nanofibers. Finally, we believe this strategy can be applied to remove of organic pollutants and water treatment due to their photocatalytic features with low energy consumption and flexible nature.
Acknowledgements
The authors would like to thank State Planning Organization (DPT) and Selcuk University Scientific Research Council (BAP Project No. 15101009) for their financial support. Technical support from the Selcuk University Advanced Technology Research and Application Center is much appreciated.
References
- P. Bansal and D. Sud, Sep. Purif. Technol., 2012, 85, 112–119 CrossRef CAS.
- V. K. Gupta, R. Jain and S. Varshney, J. Hazard. Mater., 2007, 142, 443–448 CrossRef CAS PubMed.
- V. K. Gupta, A. Rastogi and A. Nayak, J. Colloid Interface Sci., 2010, 342, 135–141 CrossRef CAS PubMed.
- G. H. Chen, Sep. Purif. Technol., 2004, 38, 11–41 CrossRef CAS.
- A. Mittal, L. Kurup and V. K. Gupta, J. Hazard. Mater., 2005, 117, 171–178 CrossRef CAS PubMed.
- S. H. S. Chan, T. Y. Wu, J. C. Juan and C. Y. Teh, J. Chem. Technol. Biotechnol., 2011, 86, 1130–1158 CrossRef CAS.
- D. Alibegic, S. Tsuneda and A. Hirata, Chem. Eng. Sci., 2001, 56, 6195–6203 CrossRef CAS.
- F. X. L. I. Xamena, P. Calza, C. Lamberti, C. Prestipino, A. Damin, S. Bordiga, E. Pelizzetti and A. Zecchina, J. Am. Chem. Soc., 2003, 125, 2264–2271 CrossRef PubMed.
- C. C. Pei and W. W. F. Leung, Catal. Commun., 2013, 37, 100–104 CrossRef CAS.
- N. J. Peill, L. Bourne and M. R. Hoffmann, J. Photochem. Photobiol., A, 1997, 108, 221–228 CrossRef CAS.
- S. Livraghi, K. Elghniji, A. M. Czoska, M. C. Paganini, E. Giamello and M. Ksibi, J. Photochem. Photobiol., A, 2009, 205, 93–97 CrossRef CAS.
- W. Liu, S. F. Chen, S. J. Zhang, W. Zhao, H. Y. Zhang and X. L. Yu, J. Nanopart. Res., 2010, 12, 1355–1366 CrossRef CAS.
- X. L. Ren, P. Z. Ying, Z. B. Yang, M. H. Shang, H. L. Hou and F. M. Gao, RSC Adv., 2015, 5, 16361–16367 RSC.
- A. M. Azad, S. A. Akbar, L. B. Younkman and M. A. Alim, J. Am. Ceram. Soc., 1994, 77, 3145–3152 CrossRef CAS.
- T. Ohno, K. Tokieda, S. Higashida and M. Matsumura, Appl. Catal., A, 2003, 244, 383–391 CrossRef CAS.
- H. W. Cen, X. J. Li, M. X. He, S. J. Zheng and M. Z. Feng, Chemosphere, 2006, 62, 810–816 CrossRef PubMed.
- B. Haspulat, A. Gulce and H. Gulce, J. Hazard. Mater., 2013, 260, 518–526 CrossRef CAS PubMed.
- D. Zhang, A. B. Karki, D. Rutman, D. R. Young, A. Wang, D. Cocke, T. H. Ho and Z. H. Guo, Polymer, 2009, 50, 4189–4198 CrossRef CAS.
- J. H. Zhu, S. Y. Wei, X. L. Chen, A. B. Karki, D. Rutman, D. P. Young and Z. H. Guo, J. Phys. Chem. C, 2010, 114, 8844–8850 CAS.
- C. Y. Su, Y. F. Tong, M. Y. Zhang, Y. Zhang and C. L. Shao, RSC Adv., 2013, 3, 7503–7512 RSC.
- J. S. Im, M. Il Kim and Y. S. Lee, Mater. Lett., 2008, 62, 3652–3655 CrossRef CAS.
- A. Avci, V. Eskizeybek, H. Gulce, B. Haspulat and O. S. Sahin, Appl. Phys. A: Mater. Sci. Process., 2014, 116, 1119–1125 CrossRef CAS.
- V. Eskizeybek, F. Sari, H. Gulce, A. Gulce and A. Avci, Appl. Catal., B, 2012, 119, 197–206 CrossRef.
- S. Sonmezoglu, V. Eskizeybek, A. Toumiat and A. Avci, J. Alloys Compd., 2014, 586, 593–599 CrossRef CAS.
- F. Ozel, M. Kus, A. Yar, E. Arkan, M. Can, A. Aljabour, N. M. Varal and M. Ersoz, J. Mater. Sci., 2015, 50, 777–783 CrossRef CAS.
- F. Ozel, M. Kus, A. Yar, E. Arkan, M. Z. Yigit, A. Aljabour, S. Buyukcelebi, C. Tozlu and M. Ersoz, Mater. Lett., 2015, 140, 23–26 CrossRef CAS.
- B. G. Colvin and P. Storr, Eur. Polym. J., 1974, 10, 337–340 CrossRef CAS.
- X. D. Liu and W. Ruland, Macromolecules, 1993, 26, 3030–3036 CrossRef CAS.
- Y. Y. Chen, C. C. Kuo, B. Y. Chen, P. C. Chiu and P. C. Tsai, J. Polym. Sci., Part B: Polym. Phys., 2015, 53, 262–269 CrossRef CAS.
- D. D. Lin, H. Wu, R. Zhang and W. Pan, Chem. Mater., 2009, 21, 3479–3484 CrossRef CAS.
- A. A. Ashkarran, A. I. Zad, M. M. Ahadian and S. A. M. Ardakani, Nanotechnology, 2008, 19, 195709–195715 CrossRef CAS PubMed.
- M. C. Medina, D. Rojas, P. Flores, E. Perez-Tijerina and M. F. Melendrez, J. Appl. Polym. Sci., 2016, 133, 43631–43638 CrossRef.
- X. G. Liu, Y. P. Sun, C. Feng, C. G. Jin and W. H. Li, Appl. Surf. Sci., 2013, 280, 132–137 CrossRef CAS.
- S. J. Fang, W. Wang, X. L. Yu, H. Xu, Y. Zhong, X. F. Sui, L. P. Zhang and Z. P. Mao, Mater. Lett., 2015, 143, 120–123 CrossRef CAS.
- H. C. Yu, Z. B. Jiao, H. Y. Hu, G. X. Lu, J. H. Ye and Y. P. Bi, CrystEngComm, 2013, 15, 4802–4805 RSC.
- C. Prahsarn, W. Klinsukhon and N. Roungpaisan, Mater. Lett., 2011, 65, 2498–2501 CrossRef CAS.
- C. S. Sharma, A. Sharma and M. Madou, Langmuir, 2010, 26, 2218–2222 CrossRef CAS PubMed.
- I. M. Alarifi, A. Alharbi, W. S. Khan, A. Swindle and R. Asmatulu, Materials, 2015, 8, 7017–7031 CrossRef.
- S. Dalton, F. Heatley and P. M. Budd, Polymer, 1999, 40, 5531–5543 CrossRef CAS.
- J. Shang, M. Chai and Y. F. Zhu, J. Solid State Chem., 2003, 174, 104–110 CrossRef CAS.
- S. Lee, K. Lee, W. D. Kim, S. Lee, D. J. Shin and D. C. Lee, J. Phys. Chem. C, 2014, 118, 23627–23634 CAS.
- J. Li, C. H. Liu, X. Li, Z. Q. Wang, Y. C. Shao, S. D. Wang, X. L. Sun, W. F. Pong, J. H. Guo and T. K. Sham, Chem. Mater., 2016, 28, 4467–4475 CrossRef CAS.
- Y. Q. Yang, G. Liu, J. T. S. Irvine and H. M. Cheng, Adv. Mater., 2016, 28, 5850–5856 CrossRef CAS PubMed.
- C. Karunakaran, G. Abiramasundari, P. Gomathisankar, G. Manikandan and V. Anandi, Mater. Res. Bull., 2011, 46, 1586–1592 CrossRef CAS.
- F. X. Xiao, ACS Appl. Mater. Interfaces, 2012, 4, 7054–7062 Search PubMed.
|
This journal is © The Royal Society of Chemistry 2017 |
Click here to see how this site uses Cookies. View our privacy policy here.