DOI:
10.1039/C7RA04437B
(Paper)
RSC Adv., 2017,
7, 34609-34617
MOF-derived hierarchical ZnO/ZnFe2O4 hollow cubes for enhanced acetone gas-sensing performance†
Received
20th April 2017
, Accepted 28th June 2017
First published on 11th July 2017
Abstract
ZnO/ZnFe2O4 hollow cube composites with heterogeneous structure are synthesized by a facile strategy through simple and direct pyrolysis of FeIII-modified Zn-based metal–organic frameworks. The as-synthesized ZnO/ZnFe2O4 hollow cubes have well-defined cube morphology with an ∼2 μm and multiple porous shell constructed from interpenetrated ZnO and ZnFe2O4 heterogeneous nanoparticles, providing structurally combined mesoporous channels for facilitating the diffusion and surface reaction of gas molecules. In addition, a comparative sensing performance investigation between ZnO/ZnFe2O4 hollow cubes and singular ZnO demonstrates that, in contrast with ZnO, the ZnO/ZnFe2O4 hollow cubes show significantly enhanced chemical sensing sensitivity towards low-concentration acetone. Furthermore, the ZnO/ZnFe2O4 hollow cubes exhibit good reproducibility and selectivity towards gaseous acetone. The enhanced sensing performance of the MOF-derived ZnO/ZnFe2O4 hollow cubes is ascribed to the unique hierarchical structure with high specific surface area, abundant exposed active sites with surface-adsorbed oxygen species and heterojunctions formed at the interfaces between ZnO and ZnFe2O4.
1. Introduction
Gas sensors based on metal oxide semiconductors have received widespread interest during the past decades owing to their low power consumption, easy manufacture, low cost, as well as portable characteristics in the detection of various explosives, and harmful, and toxic gases.1–3 To date, many metal oxide semiconductors such as ZnO,4 SnO2,5 In2O3,6 α-Fe2O3,7 NiO,8 and WO3 (ref. 9) have been extensively investigated for gas sensing. It is well acknowledged that the performance of sensors including increased sensitivity, enhanced selectivity, outstanding reproducibility and long-term stability strongly depend on the gas sensing materials so that great efforts have been made to enhance the sensing properties such as noble metal loading,10 designing novel material structures,11 and construction of heterojunctions.12 These efforts have indeed improved the sensing properties based on the fact that surface morphology, microstructure, crystalline size and composition could affect the sensing behaviors of the metal oxide semiconductors.13–15 Hollow micro-/nanostructures have attracted widespread interest in gas sensors because the unique structure offer large specific surface area with abundant active sites, modulative interfacial electron transfers with enhanced redox capacities compared with their singular solid building block units.16–18 The self-sacrificial template strategy based on thermolysis of solid precursors remains the most attractive one in the fabrication of hollow micro-/nanostructures and selecting the right template material is the key factor, as the self-sacrificial precursor should have the ability to be removed easily under thermal annealing condition as well as preserve the original stereoscopic shape.
Metal–organic frameworks (MOFs) are emerging as a class of very important materials offering high levels of porosity with considerable control over pore size and composition. Such properties play a crucial role in functional applications in gas adsorption,19 sensing,20 and catalysis.21 Besides, the morphology of MOFs can be easily tuned through different metal ions and organic bridging ligands under different synthesis conditions.22–26 Utilizing MOFs as templates offers a valid strategy for designing novel structure of porous carbon and metal oxides composites. For example, NiCo2O4/NiO hollow dodecahedra composite were synthesized by thermolysis of Ni containing ZIF-67 MOFs as template for enhanced lithium-ion battery.27 α-Fe2O3 porous nanorods were prepared from MIL-88A MOFs with enhanced gas sensing properties.28 MOF-5 was employed as template to fabricate hierarchical hollow ZnO nanocages with enhanced VOCs gas-sensing performance.29 Fe3C nanocrystallite embedded N-doped carbon matrix derived from MIL-88B@ZIF-8 dual-MOFs exhibit remarkable electrocatalytic activity for the ORR in a basic electrolyte.30 These great progresses were achieved due to the remarkable properties with selectable metal ion, multifunctional organic ligands, well-developed porosity and diverse morphologies of MOFs.
Among many metal oxide semiconductors, ZnO is an attractive n-type semiconductor with a direct wide bandgap (3.37 eV) as a popular gas sensing material because of its relatively high sensitivity and ease of fabrication.31 However, the sensing properties of pure ZnO are still unsatisfactory for applications in real industrial purposes due to the high operating temperature and poor selectivity.32 Recently, many reported investigations have demonstrated that the sensing performances of ZnO could be improved by the heterostructure formation techniques. For example, Qu et al. have fabricated gas sensors using ZnO/ZnCo2O4 hollow core–shell nanocages synthesized by the thermolysis of ZIF-8/Co–Zn hydroxide precursor, showing enhanced sensitivity to xylene and excellent reversibility.33 Liu et al. have synthesized ZnFe2O4 nanoparticles decorated on ZnO microflowers by a simple mild solution method, demonstrating higher response to acetone compared with single ZnO microflower.34 Although some improvements had been accomplished, there still existed some unnegligible drawbacks related to the unsatisfactory low detection limit of the sensing materials.
In this work, we show a generally applicable strategy for the synthesis of ZnO/ZnFe2O4 hollow cubes which includes the synthesis of FeIII-modified IRMOF-3 cubes nanostructure precursor and subsequent transformation to uniform ZnO/ZnFe2O4 hollow cubes by thermal annealing of the as-prepared precursor in air atmosphere. Moreover, gas sensors based on the above products were fabricated, and their gas sensing performance was investigated. It is revealed that the ZnO/ZnFe2O4 hollow cubes displayed a higher response to acetone at a lower working temperature than the singular ZnO particles. The formation of the heterojunction between ZnO and ZnFe2O4 and porous structure of ZnO/ZnFe2O4 materials are likely to be the sources of the enhancement in gas sensing properties.
2. Experimental
2.1 Materials
Zn(NO3)2·6H2O was purchased from Aladdin. Fe(acac)3 and 2-aminoterephthalic acid (H2N-BDC) were purchased from Alfa. Polyvinyl pyrrolidone (PVP, M. W. 30
000), N,N-dimethylformamide (DMF) and ethanol were purchased from Sinopharm. All chemicals were used directly without further purification. The water was made from Millipore Milli-Q water (15 MΩ cm).
2.2 Preparation of ZnO/ZnFe2O4 hollow cubes
The FeIII-modified IRMOF-3 precursor was synthesized according to the previously reported method.35 Typically, 3.34 g of Zn(NO3)2·6H2O, 4.32 g of Fe(acac)3, 0.68 g of H2N-BDC and 14.2 g of PVP were dispersed into a 480 mL of mixed solvent (DMF/ethanol = 5
:
3). The resulting solution was stirred for 1 h to obtained a uniformly dissolution of the reactants, and then refluxed at 100 °C for 8 h. The umber precipitant was washed with ethanol several times by centrifugation. As-obtained precipitant was dried at 80 °C under vacuum for 24 h. The collected powders were used as precursors to prepare ZnO/ZnFe2O4 samples by temperature-programmed thermal decomposition process with a slow rate of 1 °C min−1 from room temperature to 500 °C and kept at 500 °C for 2 h under air atmosphere. The synthesis of singular ZnO nanoparticle and singular ZnFe2O4 are presented in the ESI.†
2.3 Characterization of materials
Powder X-ray diffraction (XRD) patterns of the catalysts were measured on a Panalytical X'Pert PRO system using Cu-Kα radiation. Thermogravimetric analysis (TGA) was performance on a NETZSCH STA449F3 apparatus with a heating rate of 10 °C min−1 from 35 °C to 900 °C under air atmosphere. The N2 adsorption–desorption isotherms were measured on automatic surface analyzer (SSA-7300, China). Before the measurement, the samples were outgassed at 100 °C for 10 h. The morphology of materials were characterized by field-emission scanning electron microscopy (SEM) via an electron microscope (JEOL 2100F, operating at 15 kV) and transmission electron microscopy (TEM) with an accelerating voltage of 200 kV. The chemical compositions of the samples were measured by energy dispersive X-ray spectrometry (EDS) that was attached on TEM. Surface species of the as-prepared catalysts were determined by X-ray photoelectron spectroscopy (XPS) using an XLESCALAB 250 Xi electron spectrometer from VG Scientific with a monochromatic Al Kα radiation.
2.4 Gas sensing measurement
The gas sensing experiments were performed on a homemade tube-furnace sensor test system. The diameter of tube-furnace is 5 cm, and length is 1 m. Typically, two Pt wires were fixed on an Al2O3 substrate by silver paste (Wuhan Double bond Chemical Co., Ltd,. China). After that, a certain amount of the as-synthesized ZnO/ZnFe2O4 powders were dispersed into ethanol and then drop-coated onto the Al2O3 substrate to form a film. The obtained gas sensor was placed into the tube-furnace and kept at thermostable temperature of 300 °C over night to ensure good ohmic contacts. The ohmic contacts were confirmed by the Keithley 2601 Sourcemeter (Keither Instrument Inc., USA) with a rectangular sweep voltage (continuously set at 5 V, 2.5 V, 0 V, −2.5 V, and −5 V). The detected gases with different concentrations were obtained through mixing the synthetic air (20.9 vol% O2, 79.1 vol% N2) and standard gases (50 ppm in synthetic air for acetone, ethanol, toluene, benzene and 50 ppm in N2 for formaldehyde and ammonia, Beijing Hua Yuan Gas Chemical Industry Co., Ltd., China) in a mixer before entering into the tube furnace. The total flow velocity of gases is 600 mL min−1. The voltage bias was fixed at 5 V and the current was recorded using Keithley 2601 sourcemeter. The sensor response is defined as R = Rair/Rgas where Rair and Rgas are the sensor resistance in air and in the test gas, respectively. The response time is defined as the time required for sensor resistance reaching to 90% of the final value after exposed to the target gas. The recovery time is defined as the time required for reducing to 10% of the saturation value after exposed to clean air.
3. Result and discussion
3.1 Characterizations of materials
The crystallographic structure of the synthesized FeIII-modified IRMOF-3 precursor and ZnO/ZnFe2O4 materials were determined by XRD measurements. The detected diffraction peaks of FeIII-modified IRMOF-3 precursor in Fig. 1a are in good agreement with previously reported simulated IRMOF-3 patterns.36 It was confirmed that the crystal structure of IRMOF-3 could be maintained in the precursor even adding the Fe ions, which may be attributed to a small quantity of Fe doping.37 It should be pointed out that the intensities of diffraction peaks at 2θ = 6.9° and 9.7° in FeIII-modified IRMOF-3 precursor have been changed compared with IRMOF-3 which could be induced by Fe ions modification. Fig. 1b illustrates the XRD patterns of the final products after annealing in air which are indexed to the combined wurtzite crystal phases of ZnO (JCPDS no. 036-1451) and spinel ZnFe2O4 (JCPDS no. 077-0011), indicating co-existing of two heterogeneous phases in the synthesized products including ZnO and ZnFe2O4. It should be pointed out that the diffraction peaks of ZnFe2O4 are not obvious, probably because of the large content of ZnO or the overlap of ZnFe2O4 and ZnO peaks. But obviously, the color of ZnO/ZnFe2O4 is very different from that of bare ZnO shown in Fig. 1b, from which the heterogeneous phases get confirmed. The XRD patterns of singular ZnO and ZnFe2O4 are shown in the Fig. S1 and S2,† which is indexed to the wurtzite crystal phase of ZnO and spinel ZnFe2O4 respectively. The thermogravimetric analysis (TGA) of FeIII-modified IRMOF-3 precursor was investigated and shown in Fig. 1c. A two-step thermal decomposition process was observed includes the first weight loss of 8% from 35 °C to 150 °C which is attributed to the loss of adsorbed H2O and alcohol. While the second weight loss was about 60.1% between 150 °C to 500 °C, which most likely resulted from the decomposition of organic ligands and PVP surfactant resulting in releasing CO2, NOx and H2O. No obvious weight loss was observed after 500 °C and ZnO/ZnFe2O4 was subsequently formed. The N2 adsorption–desorption isotherms of the as-prepared ZnO/ZnFe2O4 material is presented in Fig. 1d, and feature type IV isotherm, indicating mesoporous properties of ZnO/ZnFe2O4 hollow cubes. The pore diameter of ZnO/ZnFe2O4 is about 8 nm in the inset of Fig. 1d and the BET surface area is 50 m2 g−1. Evidently, the as-prepared ZnO/ZnFe2O4 hollow cubes possess typical hierarchical structures with micro-/nanoscale particulate systems, which offer sufficiently interface and active sites for the gaseous adsorption–desorption and the chemical reaction between analyte molecules and ZnO/ZnFe2O4. The N2 adsorption–desorption isotherm of the singular ZnO and ZnFe2O4 nanoparticles are shown in Fig. S3.†
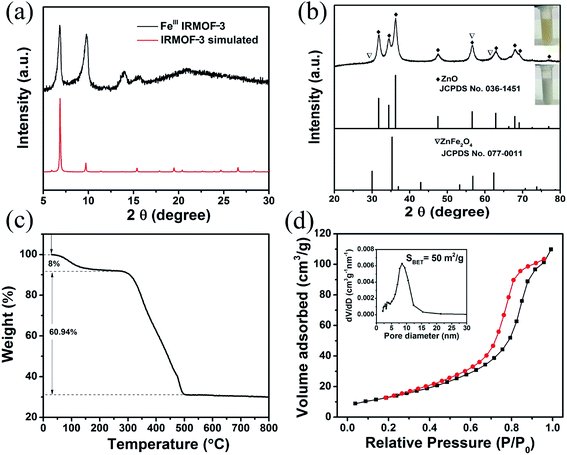 |
| Fig. 1 XRD patterns of (a) FeIII-modified IRMOF-3 precursor and (b) ZnO/ZnFe2O4 hollow cubes (the insets are the photographs of ZnO/ZnFe2O4 and singular ZnO); (c) TGA curve of FeIII-modified IRMOF-3 precursor; (d) N2 adsorption–desorption isotherm of the ZnO/ZnFe2O4 hollow cubes (the inset is the corresponding BJH pore size distribution). | |
The morphologies and microstructures of FeIII-modified IRMOF-3 precursors and their derivative ZnO/ZnFe2O4 hollow cubes are shown in Fig. 2. The FeIII-modified IRMOF-3 precursors in Fig. 2a illustrated well-defined cube morphologies with average particle sizes of about 2 μm. As shown in Fig. 2b, after calcination process at 500 °C, both the cube shape and size of the precursors remain intact except that the outside surface become little collapsing inwards indicating the hollow structure of ZnO/ZnFe2O4 cubes. The hollow structure is further confirmed from the TEM image in Fig. 2c, which shows the edge of ZnO/ZnFe2O4 composites with clearly hollow shell and the shell of individual ZnO/ZnFe2O4 hollow cubes was constructed by ultrafine interconnected nanoparticles. Moreover, the EDS mapping spectra of selected individual ZnO/ZnFe2O4 hollow cube in Fig. 3 show that the elements of Zn and Fe are uniformly dispersed within the shell, which further confirms the hollow structure of ZnO/ZnFe2O4. It should be pointed out that the Fe content is relative low (3.34 wt%) in ZnO/ZnFe2O4 sample. Fig. 2d shows the HRTEM image of selected region from Fig. 2c, indicates the ZnO–ZnFe2O4 hetero-junctions of in-shell nanoparticles with two sets of clear lattice fringes and unclear interfacial domains, indicative of crystalline detects and distortions due to two-phase transition at heterogeneous interfaces. The lattice spacings of 0.247 nm and 0.254 nm correspond to the (101) plane of the wurtzite ZnO structure and the (311) plane of the spinel ZnFe2O4 structure, respectively. The good interfacial contact between ZnO and ZnFe2O4 contribute to easy electron transfer between the two phases, which is favorable for the enhanced gas sensing performances. The TEM and SEM images of singular ZnO and ZnFe2O4 are shown in Fig. S4.†
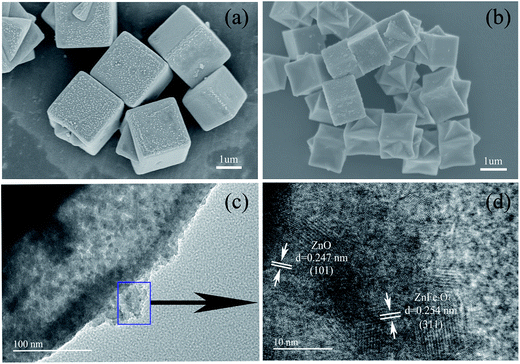 |
| Fig. 2 SEM images of (a) FeIII-modified IRMOF-3 precursor and (b) ZnO/ZnFe2O4 hollow cubes; (c) TEM image of the edge of ZnO/ZnFe2O4 hollow cubes; (d) HRTEM image taken from the frame marked region in (c). | |
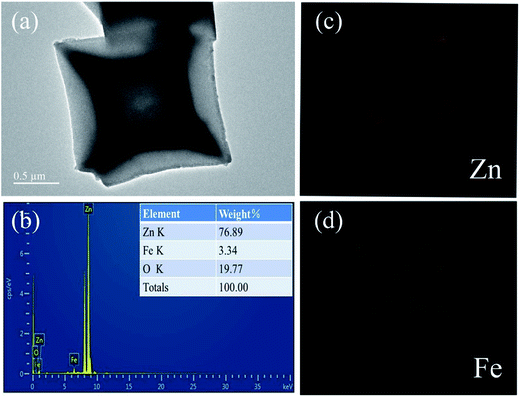 |
| Fig. 3 (a) TEM image of ZnO/ZnFe2O4 hollow cube; (b) EDS analysis of the elemental composition of ZnO/ZnFe2O4 hollow cube; (c and d) EDS mapping images of ZnO/ZnFe2O4 hollow cube. | |
XPS analysis was performed to examine the surface chemical composition and valence state of the elements of the as-synthesized ZnO/ZnFe2O4 sample, and the XPS spectra are presented in Fig. 4. Fig. 4a shows the wide spectrum of the ZnO/ZnFe2O4 sample, confirming the existence of Zn, Fe and O elements. Zn 2p spectrum in Fig. 4b displays two asymmetric peaks, corresponding to the Zn 2p1/2 and Zn 2p3/2 states of Zn 2p orbits, respectively. The fitting peaks with binding energy of 1045.1 eV and 1022.0 eV are assigned to Zn 2p1/2 and Zn 2p3/2 photoelectron responses of spinel-structural ZnFe2O4, and other two fitting peaks located at 1044.4 eV and 1021.3 eV are assigned to divalent Zn in the ZnO,38 which is also in accordance with singular ZnO sample presented in Fig. S4.† As for Fe 2p spectrum in Fig. 4c, the binding energy at 724.7 eV and 710.4 eV are ascribed to Fe 2p1/2 and Fe 2p3/2. The shake-up satellite peaks at binding energy are at range of 715.7–720.0 eV, which are characteristic of Fe3+ states in spinel ZnFe2O4 phase.39 The XPS signal of Fe 2p spectrum is weak because of the relative low content of Fe element. Besides, the asymmetrical O 1s signal can be fitted with three components: one peak at binding energy of 530.4 eV is attributed to the lattice oxygen; another peak at the medium with binding energy of 532.8 eV is assigned to the surface adsorbed oxygen and the small peak at binding energy of 533.1 eV is ascribed to the adsorbed OH groups and molecular water.40–42 It is well known that the surface-absorbed oxygen species is closely with the electron-donor oxygen vacancies, which adsorb the oxygen molecules, and ionize them into reactive surface adsorbed oxygen species (O2−, O−, O2−) which is related to the gas sensing performance of sensing material. The contents of adsorbed oxygen species in ZnO/ZnFe2O4 are clearly higher than that of singular ZnO (29.4% for ZnO/ZnFe2O4 and 23.7% for ZnO). Therefore, it is anticipated that the ZnO/ZnFe2O4 sample performs a better gas-sensing behavior than the singular ZnO counterparts.
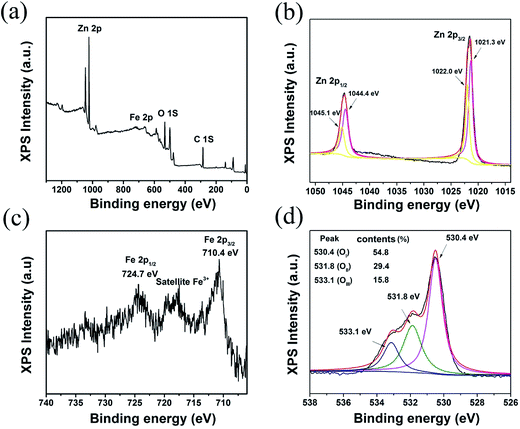 |
| Fig. 4 XPS spectra of (a) survey of the spectra; (b) Zn 2p spectra; (c) Fe 2p spectra and (d) O 1s spectra of the as-prepared ZnO/ZnFe2O4 sample. (OI: lattice oxygen; OII: surface adsorbed oxygen; OIII: adsorbed OH groups and molecular water). | |
3.2 Gas sensing performance
To demonstrate the significantly enhanced gas sensing properties of the as-prepared ZnO/ZnFe2O4 hierarchical hollow cubes with interpenetrated nanoparticles as blocking units, the singular ZnO nanoparticles were chosen as blank reference. It is well-known that the operating temperature has a great impact on the reaction between the adsorbed gas and sensing materials. Therefore, the temperature dependent properties of the as-fabricated gas sensors were measured first. As shown in Fig. 5a, the response of the two kinds of sensors increased with the increasing temperature until the value reached maximum at an optimum operating temperature, and then decreased with further increasing of the operating temperature. The optimum operating temperature ranges from 200 °C to 250 °C for the synthesized ZnO/ZnFe2O4 sample, which is lower than that of 250 °C to 300 °C for the singular ZnO counterparts. Therefore, the further measurements were performed at 250 °C. Fig. 5b provides the gas responses of the two kinds of gas sensors as a function of the concentration of acetone at 250 °C. The results showed that the gas responses of the two kinds of sensors increased with the increasing concentration of acetone and almost linear response versus concentration trend for the ZnO/ZnFe2O4 hollow cubes indicates a perfect potential in the quantitative gas analysis. It is obvious that the ZnO/ZnFe2O4 hollow cubes revealed a quite enhanced gas response compared with that of singular ZnO at each concentration of acetone. It can be observed that when the acetone concentration was as low as 0.5 ppm, it still had a response of 2.4, indicating the ultra-low detection limit of ZnO/ZnFe2O4 hollow cubes. Moreover, the response of ZnO/ZnFe2O4 hollow cubes towards 5 ppm acetone is much higher than that of singular ZnFe2O4 nanoparticles which is only 1.36 at 250 °C. The dynamic response–recovery curve of ZnO/ZnFe2O4 hollow cubes and singular ZnO towards different acetone concentrations at 250 °C are shown in Fig. 5c. The response/recover times are 5.9/7.4 min, 5.7/6.5 min, 5.8/6.3 min, 5.6/6.0 min for 0.5, 1.0, 2.0, 5.0 ppm acetone, respectively, longer than other ZnO/ZnFe2O4-based sensors towards relative high-concentration acetone. This may be ascribed to the slow surface adsorption–desorption kinetics of gaseous acetone molecules for the lower concentration acetone detection in our selected experimental conditions.43,44 Importantly, the ZnO/ZnFe2O4 hollow cubes sensor performs higher response towards acetone sensing compared with previously reported ZnO/ZnFe2O4 sensing materials with different microstructure and summarized in Table 1.
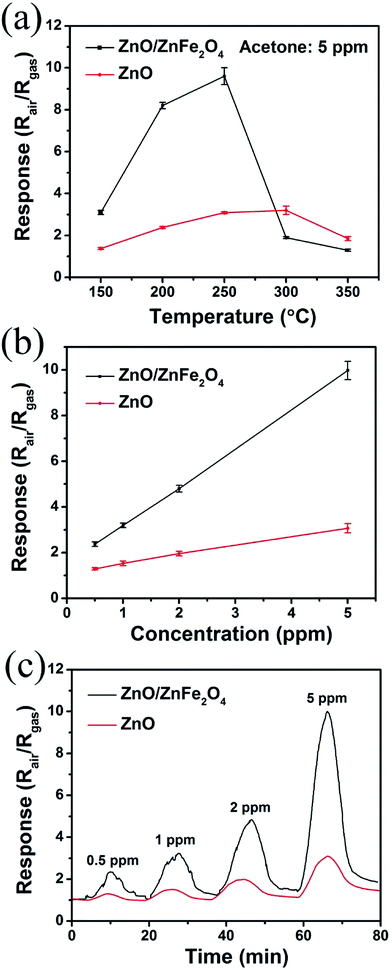 |
| Fig. 5 (a) Gas sensing response of ZnO/ZnFe2O4 hollow cubes and singular ZnO to 5 ppm acetone at different operating temperature; (b) comparison of responses between ZnO/ZnFe2O4 hollow cubes and singular ZnO operating at 250 °C; (c) the dynamic response–recovery curve of ZnO/ZnFe2O4 hollow cubes and singular ZnO towards different acetone concentration. | |
Table 1 Comparison of acetone sensing performance of gas sensors based on various ZnO/ZnFe2O4 microstructures
Materials |
Temperature (°C) |
Concentration (ppm) |
Response (Rair/Rgas) |
Reference |
ZnFe2O4/ZnO hollow microspheres |
320 |
100 |
7.5 |
45 |
ZnFe2O4/ZnO microflowers |
250 |
50 |
8.3 |
34 |
ZnFe2O4 decorated ZnO rod |
260 |
50 |
3.4 |
46 |
ZnFe2O4 nanosheets on ZnO sphere |
250 |
10 |
4.8 |
47 |
ZnO/ZnFe2O4 hollow cubes |
250 |
5 |
9.4 |
This work |
Other important gas sensing parameters including reproducibility long-term stability and selectivity were also investigated using ZnO/ZnFe2O4 hollow cubes as sensing material and shown in Fig. 6. Obviously, the ZnO/ZnFe2O4 hollow cubes illustrate good reproducibility towards 5 ppm acetone at 250 °C operating temperature after six on–off cycles, and the response value is 9.4 ± 7.1%. Moreover, ZnO/ZnFe2O4 hollow cubes based sensor to 5 ppm acetone at a constant working temperature of 250 °C during a long-term stability measurement of 14 days was conducted. The results showed that the response of the ZnO/ZnFe2O4 sensor changed a little, which confirmed good stability of ZnO/ZnFe2O4 hollow cubes. In addition, the selectivity of ZnO/ZnFe2O4 hollow cubes was also tested at 250 °C towards 5 ppm teat gases including acetone, ethanol, formaldehyde, toluene, benzene and ammonia which are common indoor gaseous contaminants. Significantly, the ZnO/ZnFe2O4 sensor possesses good selectivity to detect acetone at 250 °C, and shows low response or almost insensitive to other interference gases at the same operating temperature and shown in Fig. 6c. The good selectivity for acetone may be ascribed to the bond dissociation energy (BDE) of different gases. The BDE of H–CH2COCH3 (393 kJ mol−1) in acetone is less than that of H–OCH2CH3 (436 kJ mol−1) in ethanol, H–C6H5 (431 kJ mol−1) in benzene, but similar with CH3–C6H5 (389 kJ mol−1) in toluene. Another factor may be associated with the number of electrons released during the redox reaction at 250 °C operating temperature presented in the following equations. Therefore, the ZnO/ZnFe2O4 hollow cubes show good selectivity towards acetone with relatively lower bond dissociation energy and more released electrons. The above results demonstrate that ZnO/ZnFe2O4 hollow cubes with enhanced sensing performance having the potential for the detection of low-concentration acetone.
|
CH3COCH3 + 8O(ads)− → 3CO2 + 3H2O + 8e−
| (1) |
|
C6H6 + 15O(ads)− → 6CO2 + 3H2O + 15e−
| (2) |
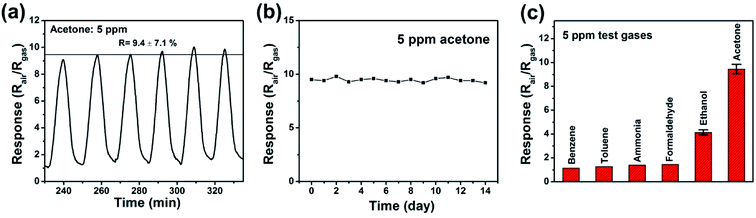 |
| Fig. 6 (a) The reproducibility of ZnO/ZnFe2O4 hollow cubes towards 5 ppm acetone at 250 °C operating temperature; (b) the long-term stability test of ZnO/ZnFe2O4 hollow cubes towards 5 ppm acetone at 250 °C; (c) the selectivity test of ZnO/ZnFe2O4 hollow cubes for 5 ppm teat gaseous acetone, ethanol, formaldehyde, toluene, benzene and ammonia at 250 °C operating temperature. | |
3.3 Gas sensing mechanism
The enhanced gas sensing performance of ZnO/ZnFe2O4 hollow cubes can mainly be attributed to the mesoporous nanostructure and formation of ZnO–ZnFe2O4 heterojunctions at the ZnO/ZnFe2O4 interfaces. First of all, the hollow cube structure with mesopores can provide a high accessible surface area, thus more surface active sites are available for the sensing reactions between teat gas molecules and adsorbed oxygen ion species, contributing to higher gas sensing performance. Besides, the sensing mechanism of n-type semiconducting metal oxides can be explained in terms of depletion layers by oxygen adsorption, which may result in change in resistance of the sensor when exposed to different gas.48,49 Fig. 7 illustrates the sensing reaction mechanism of the ZnO/ZnFe2O4 hollow cubes sensor in detecting acetone gas. When the ZnO/ZnFe2O4 expose to air, oxygen molecules can adsorb on the surface of sensing materials to form surface adsorbed oxygen (O2−, O−, O2−) by capturing electrons from the conduction band of sensing material, leading to formation of electron deletion layer in the surface regions of both ZnO and ZnFe2O4. On the other hand, the ZnO–ZnFe2O4 hetero-junctions are created in the interface regions between ZnO and ZnFe2O4, resulting in the interfacial charge separation and the increase of free electron density and plays an important role in enhancing the gas sensing properties. Since the electron depletion layer can be generated on the surface region of ZnO, ZnFe2O4 and in the vicinity of ZnO/ZnFe2O4 interfaces, a thicker electron depletion layer and a larger amount of adsorbed negatively charged oxygen ion species are formed in ZnO/ZnFe2O4 material than the singular ZnO upon exposure to air. When the sensing material is exposed to acetone, these acetone gas molecules can react with the surface adsorbed oxygen ion species to produce CO2 and H2O, and release the trapped electrons back to the conduction band, which narrows the electron depletion layer and decreases the resistance of ZnO/ZnFe2O4 nanostructure sensor. Because more trapped electrons can turn back to the conduction band of the ZnO/ZnFe2O4 nanostructure than the singular ZnO, the greater resistance change can be found, thus resulting in an enhanced response.
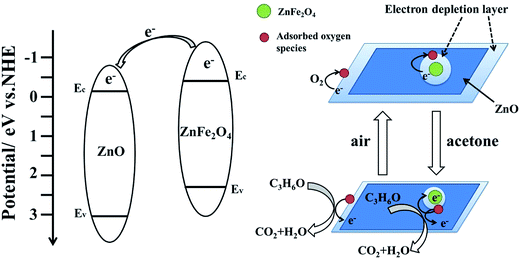 |
| Fig. 7 Schematic diagram of the sensing reaction mechanism of the ZnO/ZnFe2O4 composites sensor for detecting acetone. | |
4. Conclusions
In summary, uniform ZnO/ZnFe2O4 hollow cubes composites were synthesized by a facile strategy through simple and direct pyrolysis of FeIII-modified Zn-based metal–organic frameworks. The material composition and microstructure were examined by SEM, TEM, XRD, and XPS analysis. In particular, a comparative gas sensing investigation clearly showed that the ZnO/ZnFe2O4 material exhibited better acetone-sensing performance compared with singular ZnO nanoparticles, including higher response and good reproducibility. Besides the ZnO/ZnFe2O4 material have good selectivity to acetone, indicating its promising application as gas sensor for detecting polluting gases and selectivity to acetone. The enhanced sensing properties could be mainly attributed to the unique hierarchical structure with high specific surface area, abundant exposed active sites with surface-adsorbed oxygen species and heterojunctions formed at the interfaces between ZnO and ZnFe2O4.
Acknowledgements
The authors are grateful to the Strategic Project of Science and Technology of Chinese Academy of Science (No. XDB05050400) and the National Science and Technology support (No. 2014BAC21B00).
References
- J. H. Lee, Sens. Actuators, B, 2009, 140, 319–336 CrossRef CAS.
- D. R. Miller, S. A. Akbar and P. A. Morris, Sens. Actuators, B, 2014, 204, 250–272 CrossRef CAS.
- J. Zhang, X. H. Liu, G. Neri and N. Pinna, Adv. Mater., 2016, 28, 795–831 CrossRef CAS PubMed.
- Z. H. Jing and J. H. Zhan, Adv. Mater., 2008, 20, 4547–4551 CrossRef CAS.
- B. Wang, L. F. Zhu, Y. H. Yang, N. S. Xu and G. W. Yang, J. Phys. Chem. C, 2008, 112, 6643–6647 CAS.
- J. T. Zai, J. Zhu, R. R. Qi and X. F. Qian, J. Mater. Chem. A., 2013, 1, 735 CAS.
- C. Z. Wu, P. Yin, X. Zhu, C. Z. Ouyang and Y. Xie, J. Phys. Chem. B, 2006, 110, 17806–17812 CrossRef CAS PubMed.
- C. J. Dong, X. H. Xiao, G. Chen, H. T. Guan, Y. D. Wang and L. Djerdj, RSC Adv., 2015, 5, 4880–4885 RSC.
- R. A. Kadir, W. Zhang, Y. C. Wang, J. Z. Qu, W. Wlodarski, A. P. O'Mullane, G. Bryant, M. Taylor and K. Kalantar-zadeh, J. Mater. Chem. A., 2015, 3, 7994–8001 Search PubMed.
- K. P. Kamioth, Chem. Rev., 2008, 108, 387–399 Search PubMed.
- W. T. Koo, S. J. Choi, S. J. Kim, J. S. Jang, H. L. Tuller and I. D. Kim, J. Am. Chem. Soc., 2016, 138, 13431–13437 CrossRef CAS PubMed.
- H. L. Tian, H. Q. Fan, G. Z. Dong, L. T. Ma and J. W. Ma, RSC Adv., 2016, 6, 109091–109098 RSC.
- P. Rai, S. M. Majhi, Y. T. Yu and J. H. Lee, RSC Adv., 2015, 5, 76229–76248 RSC.
- D. P. Volanti, A. A. Felix, M. O. Orlandi, G. Whitfield, D. J. Yang, E. Longo, H. L. Tuller and J. A. Varela, Adv. Funct. Mater., 2013, 23, 1759–1766 CrossRef CAS.
- M. S. Yao, W. X. Tang, G. E. Wang, B. Nath and G. Xu, Adv. Mater., 2016, 28, 5229–5234 CrossRef CAS PubMed.
- X. Zhou, W. Feng, C. Wang, X. D. Hu, X. W. Li, P. Sun, K. Shimance, N. Yamazoe and G. Y. Lu, J. Mater. Chem. A., 2014, 2, 17683–17690 CAS.
- J. R. Huang, C. C. Shi, G. J. Fu, P. P. Sun, X. Y. Wang and C. P. Gu, Mater. Chem. Phys., 2014, 144, 343–348 CrossRef CAS.
- Z. C. Wu, K. Yu, S. D. Zhang and Y. Xie, J. Phys. Chem. C, 2008, 112, 11307–11313 CAS.
- X. Ma, H. D. Liu, W. M. Li, S. P. Peng and Y. F. Chen, RSC Adv., 2016, 6, 96997–97003 RSC.
- M. Drobek, J. H. Kim, M. Bechelany, C. Valicari, A. Julbe and S. S. Kim, ACS Appl. Mater. Interfaces, 2016, 8, 8323–8328 CAS.
- J. Song, Z. Luo, D. K. Britt, H. Furukawa, O. M. Yaghi, K. I. Hardcastle and C. I. Hill, J. Am. Chem. Soc., 2011, 113, 16839–16846 CrossRef PubMed.
- S. L. Zhao, H. J. Yin, L. Du, L. C. He, K. Zhao, L. Chang, G. P. Ying, H. J. Zhao, S. Q. Liu and Z. Y. Tang, ACS Nano, 2014, 8, 12660–12668 CrossRef CAS PubMed.
- D. Li, H. Wang, X. Zhang, H. Sun, X. P. Dai, Y. Yang, L. Ran, X. S. Li, X. Y. Ma and D. W. Gao, Cryst. Growth Des., 2014, 14, 5856–5864 CAS.
- S. Y. Zhang, H. Liu, C. C. Sun, P. F. Liu, L. C. Li, Z. H. Yang, X. Feng, F. W. Huo and X. H. Lu, J. Mater. Chem. A., 2015, 3, 5294–5298 CAS.
- L. Pan, T. Mummad, L. Ma, Z. F. Huang, S. B. Wang, L. Wang, J. J. Zou and X. W. Zhang, Appl. Catal., B, 2016, 189, 181–191 CrossRef CAS.
- Y. Bai, Y. B. Dou, L. H. Xie, W. Rutledge, J. R. Li and H. C. Zhou, Chem. Soc. Rev., 2016, 45, 2327–2367 RSC.
- C. C. Sun, J. Yang, X. H. Rui, W. N. Zhang, Q. Y. Yan, P. Chen, F. W. Huo, W. Huang and X. C. Dong, J. Mater. Chem. A., 2015, 3, 8483–8848 CAS.
- P. Y. Gao, R. Liu, H. H. Huang, X. Jia and H. B. Pan, RSC Adv., 2016, 6, 94699–94705 RSC.
- W. H. Li, X. F. Wu, N. Han, J. Y. Chen, X. H. Qian, Y. Z. Deng, W. X. Tang and Y. F. Chen, Sens. Actuators, B, 2016, 225, 158–166 CrossRef CAS.
- Y. Guan, L. Yu and X. W. Lou, Energy Environ. Sci., 2016, 9, 3092–3096 Search PubMed.
- P. Mitra, A. P. Chatterjee and H. S. Maiti, Mater. Lett., 1998, 35, 33–38 CrossRef CAS.
- N. S. Ramgir, M. Kaur, P. K. Sharma, N. Datta, S. Kailasaganapathi, S. Bhattacharya, A. K. Debnath, D. K. Aswal and S. K. Gupta, Sens. Actuators, B, 2013, 187, 313–318 CrossRef CAS.
- F. D. Qu, H. F. Jiang and M. H. Yang, Nanoscale, 2016, 8, 16349–16356 RSC.
- C. Liu, B. Q. Wang, T. S. Wang, J. Y. Liu, P. Sun, X. H. Chuai and G. Y. Lu, Sens. Actuators, B, 2017, 248, 902–909 CrossRef CAS.
- Y. J. Wu, S. L. Zhao, K. Zhao, T. X. Tu, J. H. Zheng, J. Chen, H. F. Zhou, D. J. Chen and S. X. Li, J. Power Sources, 2016, 311, 137–143 CrossRef CAS.
- M. Eddaoudi, J. Kim, N. Rosi, D. Vodak, J. Wachter, M. O'Keeffe and O. M. Yaghi, Science, 2002, 295, 469–472 CrossRef CAS PubMed.
- H. Sun, H. X. Su, X. Y. Ma, P. F. Zhang, X. Zhang, X. P. Dai, J. S. Gao, C. Chen and S. G. Sun, Electrochim. Acta, 2016, 205, 53–61 CrossRef CAS.
- L. R. Hou, L. Lian, L. H. Zhang, G. Pang, C. Z. Yuan and X. G. Zhang, Adv. Funct. Mater., 2015, 25, 238–246 CrossRef CAS.
- Y. Hou, X. Y. Li, Q. D. Zhao and G. H. Chen, Appl. Catal., B, 2013, 142, 80–88 CrossRef.
- K. Jirátová, J. Mikulová, J. Klempa, T. Grygar, Z. Bastl and F. Kovanda, Appl. Catal., A, 2009, 361, 106–116 CrossRef.
- B. Puértolas, A. Smith, I. Vázquez, A. Dejoz, A. Moragues, T. Garcia and B. Solsona, Chem. Eng., 2013, 229, 547–558 CrossRef.
- W. X. Tang, H. D. Liu, X. F. Wu and Y. F. Chen, Ozone: Sci. Eng., 2014, 36, 502–512 CrossRef CAS.
- X. W. Li, X. Zhou, H. Guo, C. Wang, J. Y. Liu, P. Sun, F. M. Liu and G. Y. Lu, ACS Appl. Mater. Interfaces, 2014, 6, 18661–18667 CAS.
- Y. Lin, W. Wei, Y. Wang, J. R. Zhou, D. M. Sun, X. D. Zhang and S. P. Ruan, J. Alloys Compd., 2015, 650, 37–44 CrossRef CAS.
- S. R. Wang, X. L. Gao, J. D. Yang, Z. Y. Zhu, H. X. Zhang and Y. S. Wang, RSC Adv., 2014, 4, 57967–57974 RSC.
- S. R. Wang, J. X. Zhang, J. D. Yang, X. L. Gao, H. X. Zhang, Y. S. Wang and Z. Y. Zhu, RSC Adv., 2015, 5, 10048–10057 RSC.
- X. W. Li, C. Wang, H. Guo, P. Sun, F. M. Liu, X. H. Liang and G. Y. Lu, ACS Appl. Mater. Interfaces, 2015, 7, 17811–17818 CAS.
- L. W. Wang, S. R. Wang, M. J. Xu, X. J. Hu, H. X. Zhang, Y. S. Wang and W. P. Huang, Phys. Chem. Chem. Phys., 2013, 15, 17179–17186 RSC.
- C. X. Wang, L. W. Yin, L. Y. Zhang, D. Xiang and R. Gao, Sensors, 2010, 10, 2088–2106 CrossRef CAS PubMed.
Footnote |
† Electronic supplementary information (ESI) available. See DOI: 10.1039/c7ra04437b |
|
This journal is © The Royal Society of Chemistry 2017 |
Click here to see how this site uses Cookies. View our privacy policy here.