DOI:
10.1039/C7RA07863C
(Paper)
RSC Adv., 2017,
7, 40452-40461
Preparation of silver/reduced graphene oxide coated polyester fabric for electromagnetic interference shielding
Received
17th July 2017
, Accepted 11th August 2017
First published on 18th August 2017
Abstract
In this study, silver/reduced graphene oxide (Ag/RGO) coated polyester (PET) fabrics with dopamine as adhesive agent were prepared through an efficient chemical reduction method under microwave irradiation. The as-synthesized samples were characterized by X-ray photoelectron spectroscopy (XPS), X-ray diffraction (XRD) and scanning electron microscopy. Deposit weight, surface resistance and electromagnetic interference (EMI) shielding effectiveness (SE) of the Ag/RGO coated PET fabric were investigated. The dopamine modified PET fabric is covered with silver particles and reduced graphene oxide (RGO) sheets uniformly and densely. In addition, the Ag/RGO coated fabric possesses high electrical conductivity with low surface resistance of 0.678 Ω sq−1 and EMI SE of Ag/RGO coated fabric ranges from 58 dB to 65 dB in the range of 1–18 GHz X-band. Adhesive strength between Ag/RGO particles and PET fabric is significantly improved.
1. Introduction
Recently, electromagnetic interference has received considerable attention because of the rapid development of electronic devices, which results in great negative effects not only on sensitive electronic equipment but also on human health. Therefore, it is urgent to develop textile materials which can protect the human body from electromagnetic interference.
Generally, EMI shielding efficiency is the combination of the reflection from the material surface, the absorption of electromagnetic energy and the multiple internal reflections of electromagnetic radiation.1 Among them, reflection is the determining factor for all high frequency signal attenuation, while maximum reflection occurs with the highest conductivity materials. Thus, EMI shielding properties depend mainly on the electrical conductivity. Poor electrical conductivity results in static electricity and transparent to electromagnetic wave. In recent years, graphene has been widely used in various fields due to its high surface area, high electrical conductivity, excellent mechanical and thermal properties.2–5 To date, many research groups have reported the feasibility of graphene used in EMI shielding and high-efficiency microwave absorption.6–9 RGO, which is the derivatives of graphene, has received a great attention for functional materials. However, there are oxygen-containing functional groups on RGO because of the incomplete reduction, which causes defects and restricts electrical conductivity of RGO. Currently, introducing metals or metal oxides on RGO has been considered to be an effective method for enhancing electrical conductivity. Recently, silver particles deposited on RGO to enhance functional properties has attracted ever-growing interest, because silver possesses excellent electrical conductivity, inoxidizability and antibacterial property and the synergistic effect of combination of graphene and silver particles.10,11
Electrically conductive textile has been considered as wearable EMI shielding devices on account of its light weight, flexibility, and comfort. PET fabric has been widely used in textile industry because of its good wear resistance, high fracture strength and low production cost. However, it possesses disadvantages such as poor electrical conductivity and antistatic behavior. Hence, it is necessary of improving the electrical conductivity of PET fabric. Until now, there are a large number of researches on imparting PET fabric with high conductivity. In general, conductive polymer, metals and carbon materials are usually coated on PET fabric for enhancing electrical conductivity.12–14 In recent years, Babaahmadi and Moazami reported the synthesis of Ag/RGO composites on PET fabric for improvement of electrical conductivity through traditional chemical reduction method.15,16 However, traditional chemical reduction method is usually carried out through heat conduction, which results in uneven heating during reaction because heating mode is from outside to inside. Thus, reaction rate is slow and the heating is not uniform.
Nowadays, numerous methods have been developed for assisting synthesis of Ag/RGO hybrids such as visible-light, microwave and ultrasonic irradiation.17–19 Among them, microwave irradiation has been recently used as an important technique for assisting coating of materials on textile because microwave irradiation can offer rapid and uniform volumetric heating, high reaction rates, short reaction time, high yield production and low cost.20,21 In addition, microwave irradiation is helpful for diffusion of molecules and ion into fibers and their further reduction.
It is difficult that materials are immobilized on fabrics owing to poor adhesion of the coating on fabrics. Therefore, it is very necessary and desirable to improve durability of Ag/RGO coatings on fabrics. Recently, dopamine has been used to modify surface of various textile materials to improve adhesive strength between coatings and substrates.22–24 Dopamine is a kind of biomolecule containing catechol and amine functional groups, thus it is eco-friendly and flexible agent for surface coating of various materials. Dopamine can be spontaneously self-polymerized on a variety of substrates after being oxidized in air, which provides a facile method to immobilize desired coatings onto surface.25 However, to the best of our knowledge, it has not been reported that Ag/RGO are coated on textiles with dopamine as an adhesive agent under microwave irradiation.
In this study, Ag/RGO coated PET fabrics modified with dopamine were prepared through chemical reduction under microwave irradiation. In addition, influences of concentration of silver nitrate in chemical reduction solution on deposit weight, surface resistance and EMI SE of Ag/RGO coated PET fabrics were investigated. The coated PET fabrics were characterized by XPS, SEM and XRD. Deposition rate, surface resistance and EMI SE of the coated PET fabrics were evaluated. Additionally, adhesive strength between Ag/RGO coatings and PET fabric modified with dopamine was evaluated.
2. Experimental
2.1. Materials
Plain weave 100% PET fabric (95 g m−2) in white color was used. Multilayer GO powder (purity > 95%) was purchased from Suzhou Tanfeng Graphene Tech. Co., Ltd. Silver nitrate, trisodium citrate, tris(hydroxymethyl)aminomethane (Tris) and dopamine were purchased from Chengdu KeLong Chemical Co., Ltd. All the chemicals were of analytical grade and used without further purification.
2.2. Modification of the PET fabrics with dopamine
Dopamine (0.3 g) was dissolved in Tris buffer solution (100 mL). pH value of the solution was regulated to 8.5. PET fabrics were cut into 5 cm × 5 cm and subsequently cleaned in acetone, ethanol and deionized water under ultrasonic irradiation for 30 min, respectively. The cleaned PET fabrics were immersed into the solution with dopamine at ambient temperature for 24 h and then rinsed in deionized water.
2.3. Synthesis of GO coated PET fabrics
Aqueous dispersion of GO (1 g L−1, 100 mL) was prepared and sonicated for 60 min. The dopamine modified PET fabrics were dipped into the prepared dispersion and then exposed to microwave irradiation (domestic microwave oven, 700 W) for 20 min and turned over every two minutes to ensure the uniform coating GO nanosheets on the fabrics. The GO coated fabrics were rinsed in deionized water and finally kept in an oven at 100 °C for 60 min.
2.4. Synthesis of Ag/RGO coated PET fabrics
GO coated PET fabric was immersed into the solution of silver nitrate with different concentration of silver nitrate (1–6 g L−1, 100 mL). Trisodium citrate was added into the reaction mixture and the mixture was subjected to microwave irradiation (domestic microwave oven, 700 W) for 20 min. The fabrics were turned over every two minutes to ensure uniform coating of Ag/RGO on PET fabrics. Finally, the Ag/RGO coated fabrics were rinsed in deionized water and then dried at 100 °C for 120 min. For comparison, the RGO and Ag coated PET fabrics were prepared according to the above procedure, respectively. In addition, Ag/RGO with 6 g L−1 silver nitrate in the solutions was also coated on PET fabric without pretreatment with dopamine according to the above procedures. Additionally, Ag/RGO coated PET fabrics modified with dopamine with different silver nitrate concentration from 1 g L−1 to 6 g L−1 were labelled as Ag/RGO-D1 to Ag/RGO-D6, while Ag/RGO coated PET fabrics modified with dopamine was labelled as Ag/RGO-D. Besides, Ag/RGO coated PET fabric with silver nitrate concentration of 6 g L−1 without pretreatment with dopamine was labelled as Ag/RGO-N.
2.5. Characterization
Chemical composition of dopamine, GO and Ag/RGO coated PET fabrics was determined by XPS (Kratos XSAM800 spectrometer) using an Al Kα source (14 kV and 350 W).
Surface morphologies of original fabric and dopamine, RGO, Ag and Ag/RGO coated PET fabrics were observed by SEM (JSM-5900LV) at an acceleration voltage of 5 kV and 10 mm of working distance.
Crystal structures of original fabric, and RGO and Ag coated PET fabrics and Ag/RGO-D6 were detected by XRD (X'Pert Pro MPO) with a scan rate of 5° per minute in the angular range of 10–90°. The radiation used was Cu Kα with a wavelength of 1.5418 Å.
Surface resistances of original fabric, and dopamine, RGO, Ag and Ag/RGO coated PET fabrics were tested using a four-point probes equipment (RTS-9). Each sample was measured at least five times and the average values were calculated for the results.
EMI SE of original fabric and dopamine, RGO, Ag and Ag/RGO coated PET fabrics were evaluated on a vector network analyzer (Agilent E5063A ENA) in 1–18 GHZ X-band range. Each sample was cut into circle shape with a diameter of 110 mm for the tested. Total EMI shielding effectiveness (SE (total)) was used to evaluate ability of material to attenuate electromagnetic waves, which refers to the logarithm of the ratio of the incident wave PI to the transmitted wave PT as shown in the following equation.
|
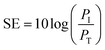 | (1) |
Ag/RGO coated PET fabrics were washed in 0.37 wt% of detergent with 10 steel balls at 40 °C for 45 min in accordance with standard AATCC 61-2003. SEM, surface resistance and EMI SE of Ag/RGO coated PET fabrics after washing were evaluated.
3. Results and discussion
3.1. Mechanism of Ag/RGO coating on PET fabrics modified with dopamine
The mechanism that Ag/RGO coatings are coated on PET fabric modified with dopamine under microwave irradiation is illustrated in Scheme 1. Dopamine was used as adhesive agent to improve the strength between coatings and textiles because it is difficult for Ag/RGO immobilized on the surface of polyester fibers. Thus, thin film of GO can be can be quickly formed on PET fibers modified with dopamine when the PET fabric is immersed into aqueous solution of GO. Moreover, GO can be easily diffused into the gap among PET yarns under microwave irradiation. GO coated on the fibers carry negative charges due to the large quantities of carboxyl (–COO−) and hydroxyl (–OH−) functional groups. Therefore, silver ions with positive charges can be easily adsorbed on the surface of GO coated fibers due to strong electrostatic force. Subsequently, silver particles and RGO sheets are formed through simultaneous in situ reduction of Ag+ and GO to Ag0 and RGO with trisodium citrate as a reducing agent under microwave irradiation, respectively. Reaction efficiency is enhanced with the help of microwave irradiation because the reaction system can be heated quickly and uniformly. Therefore, microwave irradiation is beneficial for uniform deposition of silver particles and RGO sheets on the PET fibers.
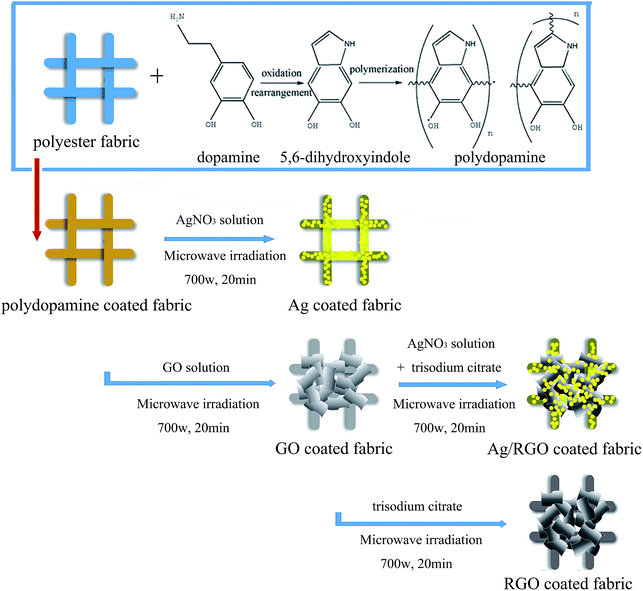 |
| Scheme 1 Mechanism of Ag/RGO coating on PET fabric modified with dopamine. | |
3.2. XPS analysis
XPS wide and narrow spectra of dopamine, GO and Ag/RGO coated PET fabrics are illustrated in Fig. 1, 2 and 3, respectively. Elements of C and O detected from the fabric modified with dopamine (Fig. 1a) are attributed to PET fabric, while N comes from dopamine. Narrow spectrum of N 1s is shown in Fig. 1b. It can be fitted into a typical peak at 402.0 eV, which is attributed to amine (–N–H).26 The result confirms that dopamine is successfully adsorbed on surface of PET fabric.
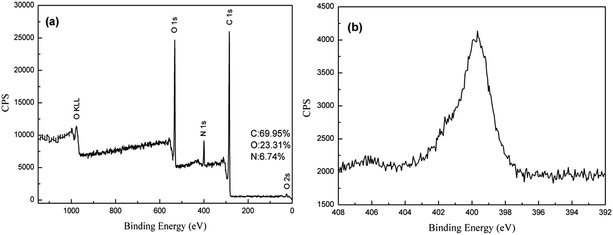 |
| Fig. 1 (a) XPS wide and narrow spectra of (b) N 1s of PET fabric modified with dopamine. | |
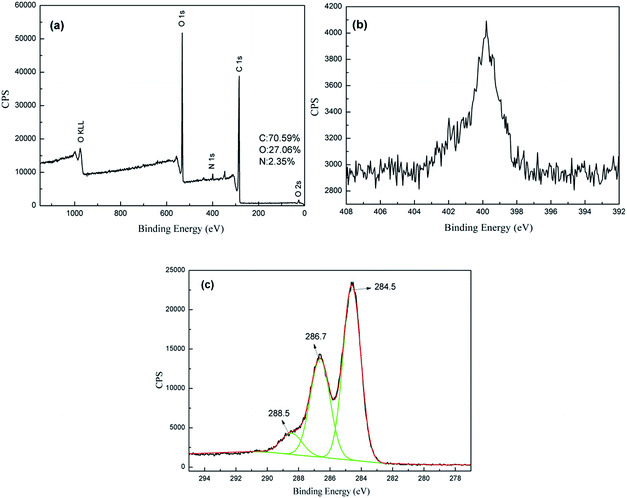 |
| Fig. 2 (a) XPS wide and narrow spectra of (b) N 1s and (c) C 1s of GO coated PET fabric. | |
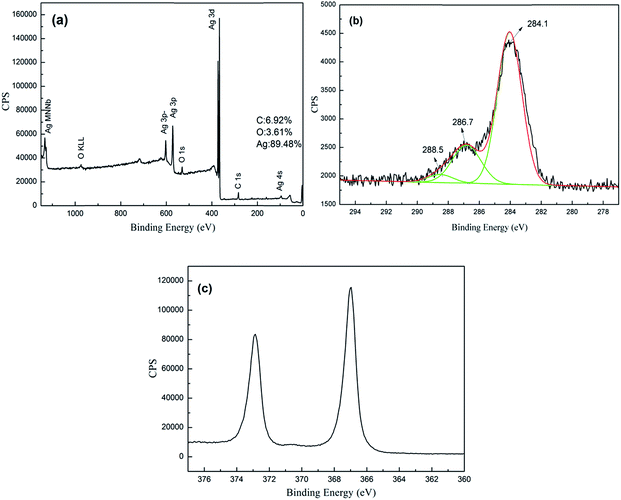 |
| Fig. 3 (a) XPS wide and narrow spectra of (b) C 1s and (c) Ag 3d of Ag/RGO coated PET fabric. | |
XPS wide and narrow spectra of the GO coated PET fabric modified with dopamine are shown in Fig. 2. It is obvious that elements of C, O and N are existed in the GO coated PET fabric modified with dopamine (Fig. 2a). It can be seen from Fig. 2c that C 1s spectrum of GO coated PET fabric can be deconvoluted into three peaks at 284.5 eV, 286.7 eV and 288.5 eV, which correspond to characteristics of bonds of C–C (unoxidized graphite carbon skeleton), C–O (hydroxyl and epoxide) and C
O (carboxyl), respectively. The result is consistent with the reported literature.11,15,27
Three prominent elements of Ag, C and O are existed in Ag/RGO coated PET fabric as shown in Fig. 3. Elements of C and O are ascribed to RGO and PET. In addition, Ag/RGO coated PET fabric mainly consists of Ag and content of Ag is 89.48 wt% (Fig. 3a). The XPS narrow spectrum in the region 275–295 eV is presented in Fig. 3b. It is obvious that peak intensity of C 1s on surface of Ag/RGO coated PET fabric at 286.7 eV and 288.5 eV are remarkably lower than that of GO coated fabric due to low content of C–O and C
O in Ag/RGO coated PET fabric. The result confirms that GO is effectively reduced to RGO with trisodium citrate as a reducing agent under microwave irradiation. In addition, the peak of carbon species (C–C) at 284.1 eV is strong. XPS narrow spectrum of Ag 3d in the region of 360–380 eV is presented in Fig. 3c. The peaks at 367.9 eV and 373.9 eV correspond to Ag 3d5/2 and Ag 3d3/2 of metallic silver, respectively. The result indicates that silver ions are reduced to Ag0 under microwave irradiation. In conclusion, Ag/RGO are successfully coated on the PET fabric.
3.3. Surface morphology
Fig. 4 shows surface morphologies of original fabric and dopamine, RGO and Ag coated PET fabrics and Ag/RGO-D6. It can be seen from Fig. 4a and b that PET fibers are cylindrical and surface is relatively smooth. The surface of PET fibers is covered with agglomerated polydopamine film (Fig. 4c and d) after dopamine modification. Fig. 4e and f show that RGO sheets are densely attached on the surface of PET fibers with slight winkles. The surface of Ag coated PET fibers is rough due to silver particles deposited on the fibers (Fig. 4g and h). Silver particles on the fibers modified with dopamine are irregularly round and the size ranges from 200 nm to 600 nm. Surface morphology of Ag/RGO-D6 are presented in Fig. 4i and j. It is obvious that the silver particles are uniformly coated on the fibers and the particle size ranges from 300 nm to 1 μm. Silver particles of Ag/RGO-D6 is obviously bigger than that of Ag coated PET fabric. The phenomenon can be explained by the fact that GO film with oxygen atoms (–COO− and –OH−) shows strong electrostatic force to Ag+. The GO coated PET fabric can efficiently prompt silver deposition from the reaction solution, which would result in fast nucleation and growth of silver. The migration and aggregation of silver particles would produce thermodynamically stable particles with bigger sizes.
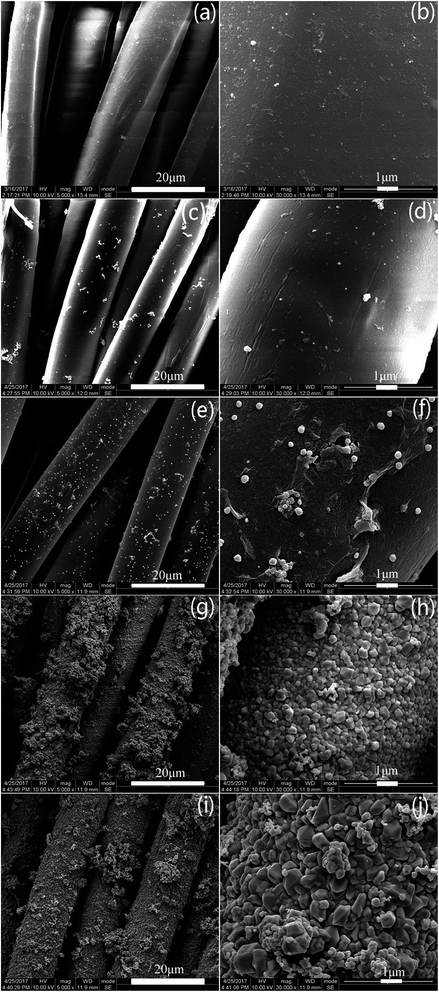 |
| Fig. 4 SEM images of (a, b) original PET fibers, (c, d) dopamine, (e, f) RGO and (g, h) Ag coated PET fibers and (i, j) Ag/RGO-D6. | |
Fig. 5 presents surface morphologies of Ag/RGO-N and Ag/RGO-D6 after washing. It is obvious that a lot of Ag/RGO coatings are peeled off from the PET fibers without dopamine pretreatment after laundering according to standard method AATCC 61 (Fig. 5a and b). However, it can be seen from Fig. 5c and d that Ag/RGO particles are still densely coated on the PET fibers modified with dopamine. Only few coatings are removed after laundering because of strong coordinate bonds and electrostatic adsorption between the coatings and fibers. Accordingly, adhesive strength between silver particles, RGO sheets and PET fibers is improved because coordinate bonds and electrostatic force between silver particles, RGO sheets and the polydopamine on the fabric are formed.
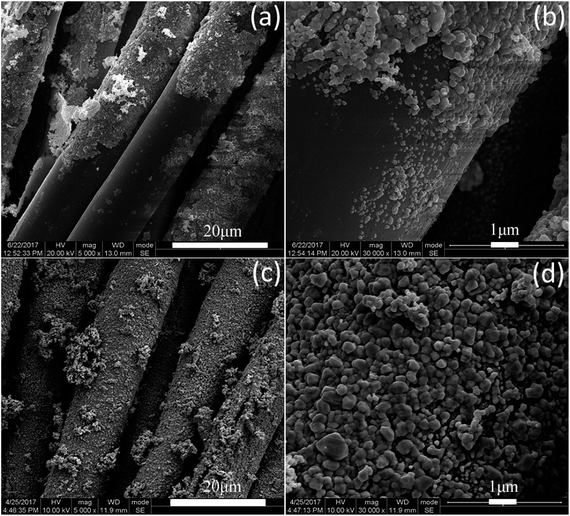 |
| Fig. 5 SEM images of (a, b) Ag/RGO-N and (c, d) Ag/RGO-D6 after washing. | |
3.4. Crystal structure
X-ray diffraction patterns of RGO and Ag and Ag/RGO coated PET fabrics are shown in Fig. 6. Weak peaks at 2θ of 17.2°, 22.3° and 25.5° are assigned to PET fibers (Fig. 6a). The characteristic peak of RGO are obviously overlapped with peaks of PET. Five diffraction peaks of Ag and Ag/RGO coated PET fabrics located at 38.1°, 44.2°, 64.3°, 77.2° and 81.5° are assigned to (111), (200), (220), (311) and (222) reflection lines of silver, respectively (Fig. 6b and c). The XRD patterns identified by the PDF card reveals that Ag and Ag/RGO coatings on PET fabrics exhibits face-centered cubic crystalline structure.
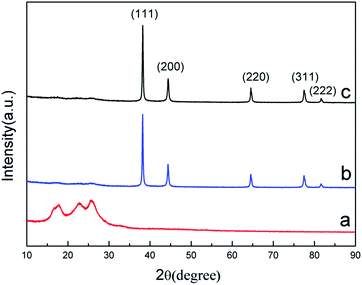 |
| Fig. 6 XRD patterns of (a) RGO and (b) Ag coated PET fabrics, and (c) Ag/RGO-D6. | |
Based on the XRD results, crystal size of Ag deposits was determined from the broadening of the diffraction peak of (111) by employing Scherrer formula as expressed by following equation.
|
 | (2) |
where
t is the crystal size;
λ is the X-ray wavelength corresponding to Cu Kα radiation (0.154056 nm);
θ is the diffraction angle;
B is the full width half maximum (FWHM) of the diffraction peak at 2
θ and
n is the Scherrer constant as 0.89. Average size of silver particles on the Ag coated PET fabric and Ag/RGO-D6 are 29.89 nm and 30.83 nm with respect to Ag (111) peak, respectively.
3.5. Deposit weight and surface resistance
Surface resistance and deposit weight of Ag coated PET fabric and Ag/RGO-D are shown in Fig. 7. As is well known, the original and dopamine coated PET fabrics show no electrical conductivity. In addition, RGO coated PET fabric also shows poor electrical conductivity because there are many functional groups in RGO including hydroxyl, epoxy and carboxyl and the structure of C–C is incomplete, which causes defects and significantly restricts its electrical conductivity. Surface resistance of Ag coated PET fabric and Ag/RGO-D6 are 0.759 Ω sq−1 and 0.678 Ω sq−1, respectively. Electrical conductivity of Ag/RGO coated PET fabric is higher than previous report.16 The result indicates that Ag coated PET fabric and Ag/RGO-D show excellent electrical conductivity. However, electrical conductivity of Ag/RGO-D6 is superior to that of Ag coated PET fabric. The phenomenon can be explained by the fact that the RGO sheets are beneficial for deposition of silver particles on the PET fabric. In addition, surface resistance of the Ag/RGO coated fabrics decreases with the rise of concentration of silver nitrate in the solution. More deposit weight results in lower surface resistance. In this study, deposit weight of coating on the fibers increases with the increase of concentration of silver nitrate, thus surface resistance of the Ag/RGO coated fabrics decreases with the rise of concentration of silver nitrate.
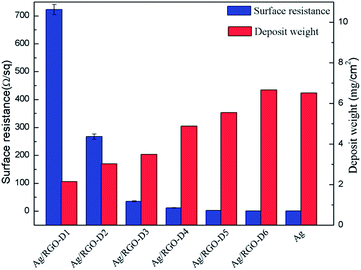 |
| Fig. 7 Surface resistance and deposit weight of original fabric and dopamine, RGO, Ag and Ag/RGO coated PET fabrics. | |
Surface resistance and deposit weight of Ag/RGO-N and Ag/RGO-D6 before and after washing are shown in Fig. 8. Ag/RGO-N after washing shows no electrical conductivity because the deposits peels from the fabric resulted from weak Van der Waals' force between Ag/RGO coating and the fabric. In addition, surface resistance of Ag/RGO-D6 after washing is 2 Ω sq−1, which is slightly higher than that before washing. It is can be explained by that there are still lots of Ag/RGO coating on the fibers due to coordinate bonds and electrostatic adsorption between the coatings and fibers. The result indicates that the Ag/RGO coated PET fabrics with dopamine possess excellent electrical conductivity and washing fastness.
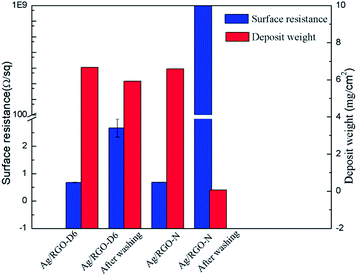 |
| Fig. 8 Deposit weight and surface resistance of Ag/RGO-N and Ag/RGO-D6 before and after washing. | |
3.6. EMI SE of Ag/RGO coated PET fabrics
Fig. 9 presents EMI SE of original fabric and dopamine, RGO, Ag and Ag/RGO coated PET fabrics. It is obvious that EMI SE of original fabric, dopamine and RGO coated PET fabrics are so low. The phenomenon can be explained by the fact that EMI SE depends on electrical conductivity of shielding material. The electrical conductivity is a key factor to EMI SE. Accordingly, poor electrical conductivity results in low EMI SE. Obviously, EMI SE of Ag/RGO coated PET fabric ranges from 58 dB to 65 dB at the frequencies from 1 GHz to 18 GHz, which is much higher than that coated with Ag or RGO due to the synergistic effects of Ag and RGO. In addition, EMI SE of Ag/RGO coated PET fabric after washing ranges from 40 dB to 45 dB, which is lower than that before washing due to an increase of surface resistance after washing. Nonetheless, EMI SE of Ag/RGO coated PET fabric after washing is still more than that of Ag coated PET fabric.
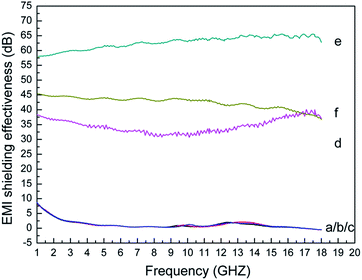 |
| Fig. 9 EMI SE of (a) original fabric and (b) dopamine, (c) RGO, (d) Ag coated PET fabrics and Ag/RGO-D6 (e) before and (f) after washing at the frequency ranging from 1 GHz to 18 GHz. | |
Fig. 10 shows that EMI SE of Ag/RGO-D1, Ag/RGO-D2, Ag/RGO-D3, Ag/RGO-D4, Ag/RGO-D5 and Ag/RGO-D6. It can be seen from Fig. 10 that EMI SE of Ag/RGO coated PET fabrics increases with rise of silver nitrate concentration. EMI SE of Ag/RGO coated PET fabrics increases from 6 dB to 65 dB at frequencies ranging from 1 GHz to 18 GHz when silver nitrate concentration increases from 1 g L−1 to 6 g L−1. The phenomenon can be explained by that better electrical conductivity results in excellent EMI SE of Ag/RGO coated PET fabrics. EMI SE of Ag/RGO coated PET fabric can reach 65 dB. Until now, it has been reported about EMI shielding textile materials through pure metal or carbon material deposition on textile.28–30 Compared with previous studies, it is affirmed that Ag/RGO coated PET fabric possesses high EMI SE property.
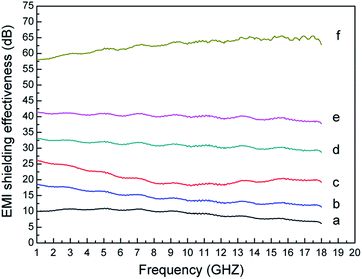 |
| Fig. 10 EMI SE of (a) Ag/RGO-D1, (b) Ag/RGO-D2, (c) Ag/RGO-D3, (d) Ag/RGO-D4, (e) Ag/RGO-D5 and (f) Ag/RGO-D6 at the frequency ranging from 1 GHz to 18 GHz. | |
As is well known, EMI shielding efficiency is the combination of the reflection, absorption and multiple internal reflections of electromagnetic radiation. In previous reports, carbon materials exhibit the efficient absorption of electromagnetic energy, which is ideal absorbers.31–34 Generally, metal materials usually show the reflection of electromagnetic energy. In this study, there are a lot of silver particles deposited on the surface of RGO sheets as shown in Fig. 4. The Ag/RGO coated PET fabric probably exhibit reflection-dominated EMI shielding property. Therefore, there is a potential application of Ag/RGO coated PET fabric modified with dopamine as lightweight and flexible EMI shielding materials.
4. Conclusions
PET fabric is successfully modified with dopamine, and then RGO sheets and silver particles are compactly coated on the dopamine modified PET fabric under microwave irradiation. Surface resistance of Ag/RGO coated PET fabrics decreases and EMI SE increases with the rise of concentration of silver nitrate in the solution. Moreover, electrical conductivity and EMI SE of Ag/RGO coated PET fabric modified with dopamine after washing are slightly lower than that before washing. However, electrical conductivity and EMI SE of Ag/RGO coated PET fabrics with dopamine is much better than that without dopamine. The result suggests that dopamine modification on PET fabric improves adhesive strength between coatings and PET fabric. Therefore, there is a potential application of Ag/RGO coated PET fabric modified with dopamine as lightweight and flexible EMI shielding materials.
Conflicts of interest
There are no conflicts to declare.
Acknowledgements
This work was financially supported by The National Natural Science Foundation of China (No. 51203099) and Chengdu Science and Technology Bureau (No. 2015-HM01-00380-SF).
References
- X. C. Luo and D. D. L. Chung, Composites, Part B, 1999, 30, 227–231 CrossRef.
- M. D. Stoller, S. Park, Y. W. Zhu, J. An and R. S. Ruoff, Nano Lett., 2008, 8, 3498–3502 CrossRef CAS PubMed.
- Y. A. Samad, Y. Li, S. M. Alhassan and K. Liao, RSC Adv., 2014, 4, 16935–16938 RSC.
- A. K. Geim, Science, 2009, 324, 1530–1534 CrossRef CAS PubMed.
- C. Lee, X. Wei, J. W. Kysar and J. Hong, Science, 2008, 321, 385–388 CrossRef CAS PubMed.
- M. S. Cao, X. X. Wang, W. Q. Cao and J. Yuan, J. Mater. Chem. C, 2015, 3, 6589–6599 RSC.
- M. Q. Cao, X. X. Wang, J. Yuan, W. Z. Wang and M. S. Cao, J. Mater. Chem. C, 2015, 3, 10017–10022 RSC.
- B. Wen, M. S. Cao, M. M. Lu, W. Q. Cao, H. L. Shi, J. Liu, X. X. Wang, H. B. Jin, X. Y. Fang, W. Z. Wang and J. Yuan, Adv. Mater., 2014, 26, 3484–3489 CrossRef CAS PubMed.
- J. Z. He, X. X. Wang, Y. L. Zhang and M. S. Cao, J. Mater. Chem. C, 2016, 4, 7130–7140 RSC.
- S. J. Wang, Y. W. Zhang, H. L. Ma, Q. L. Zhang, W. G. Xu, J. Peng, J. Q. Li, Z. Z. Yu and M. L. Zhai, Carbon, 2013, 55, 245–252 CrossRef CAS.
- G. Liu, Y. J. Wang, X. J. Pu, Y. Jiang, L. L. Cheng and Z. Jiao, Appl. Surf. Sci., 2015, 349, 570–575 CrossRef CAS.
- N. Sabetzadeh, S. S. Najar and S. H. Bahrami, J. Appl. Polym. Sci., 2013, 130, 3009–3017 CrossRef CAS.
- F. Z. Engin and I. Usta, Text. Res. J., 2014, 84, 903–912 CrossRef CAS.
- K. K. Gupta, S. M. Abbas and A. C. Abhyankar, J. Electromagn. Waves Appl., 2015, 29, 1454–1472 CrossRef.
- V. Babaahmadi, M. Montazer and W. Gao, Carbon, 2017, 118, 443–451 CrossRef CAS.
- A. Moazami, M. Montazer and M. K. Dolatabadi, Fibers Polym., 2016, 17, 1359–1370 CrossRef CAS.
- D. P. Das, R. K. Barik, J. Das, P. Mohapatra and K. M. Parida, RSC Adv., 2012, 2, 7377–7379 RSC.
- T. Long, L. Hu, H. X. Dai and X. Y. Tang, Appl. Phys. A, 2014, 116, 25–32 CrossRef CAS.
- A. Moradi Golsheikh, N. M. Huang, H. N. Lim and R. Zakaria, RSC Adv., 2014, 4, 36401–36411 RSC.
- R. H. Guo, Y. N. Li, J. W. Lan, S. X. Jiang, T. Liu and W. Q. Yan, J. Appl. Polym. Sci., 2013, 130, 3862–3868 CAS.
- V. H. T. Thi and B. K. Lee, J. Photochem. Photobiol., A, 2017, 338, 13–22 CrossRef CAS.
- W. C. Wang, W. J. Cheng, M. Tian, H. Zou, L. Li and L. Q. Zhang, Electrochim. Acta, 2016, 79, 37–45 CrossRef.
- R. K. Wang, C. H. Shin, S. Park, L. Z. Cui, D. Kim, J. S. Park and M. Ryu, Food Chem., 2015, 226, 2241 Search PubMed.
- R. Sa, Y. Yan, Z. Wei, L. Zhang, W. Wang and M. Tian, ACS Appl. Mater. Interfaces, 2014, 6, 21730–21738 CAS.
- L. H. Peng, R. H. Guo, J. W. Lan, S. X. Jiang, Y. F. He and X. M. Huang, Appl. Surf. Sci., 2016, 386, 151–159 CrossRef CAS.
- C. Xu, M. Tian, L. Liu, H. Zou, L. Zhang and W. Wang, J. Electrochem. Soc., 2012, 159, D217–D224 CrossRef CAS.
- L. Z. Li, M. X. Chen, G. B. Huang, N. A. Yang, L. Zhang, H. Wang, Y. Liu, W. Wang and J. P. Gao, J. Power Sources, 2014, 263, 13–21 CrossRef CAS.
- Y. X. Lu, S. H. Jiang and Y. M. Huang, Surf. Coat. Technol., 2010, 204, 2829–2833 CrossRef CAS.
- R. R. Bonaldi, E. Siores and T. Shah, Synth. Met., 2014, 187, 1–8 CrossRef CAS.
- L. H. Zou, C. T. Lan, X. P. Li, S. L. Zhang, Y. P. Qiu and Y. Ma, Fibers Polym., 2015, 16, 2158–2164 CrossRef CAS.
- B. Wen, M. S. Cao, Z. L. Hou, W. L. Song, L. Zhang, M. M. Lu, H. B. Jin, X. Y. Fang, W. Z. Wang and J. Yuan, Carbon, 2013, 65, 124–139 CrossRef CAS.
- J. J. Liang, Y. Wang, Y. Huang, Y. F. Ma, Z. F. Liu, J. M. Cai, C. D. Zhang, H. J. Gao and Y. S. Chen, Carbon, 2009, 47, 922–925 CrossRef CAS.
- M. S. Cao, W. L. Song, Z. L. Hou, B. Wen and J. Yuan, Carbon, 2010, 48, 788–796 CrossRef CAS.
- Z. F. Liu, G. Bai, Y. Huang, Y. F. Ma, F. Du, F. F. Li, T. Y. Guo and Y. S. Chen, Carbon, 2007, 45, 821–827 CrossRef CAS.
|
This journal is © The Royal Society of Chemistry 2017 |
Click here to see how this site uses Cookies. View our privacy policy here.