DOI:
10.1039/C7RA13605F
(Paper)
RSC Adv., 2018,
8, 5306-5311
Fouling-resistant membranes for separation of oil-in-water emulsions†
Received
23rd December 2017
, Accepted 25th January 2018
First published on 31st January 2018
Abstract
Separation by membrane technology of oily wastewater, especially emulsified oil/water mixtures, has become a topic of intensive study in recent years, and membrane fouling remains a challenge. In this work, porous polycarbonate membranes were coated with poly(diallyldimethylammonium chloride)/polystyrene sulfonate (PDDA/PSS) multilayers via the facile layer-by-layer deposition technique to improve their fouling resistance for separation of oil-in-water emulsions stabilized by ionic surfactants. The permeation flux for the virgin membrane was found to decrease by ∼90% in 10 cycles due to fouling. The membranes coated with PSS-capped PEMs were used to separate emulsions stabilized by sodium dodecyl sulfate, an anionic surfactant, whereas the ones modified with PDDA-capped PEMs were effective for separation of emulsions stabilized by cetyltrimethyl ammonium bromide, a cationic surfactant. Both retained up to 80% of their original permeation flux after 10 separation cycles. The purity of the filtrates was greater than 99.98%.
Introduction
In recent years, wastewater containing various oils, produced in many industrial processes such as petrochemical, metallurgy, coal tar, textile, steel and metal finishing, and discharged into the environment without further treatment has brought about great harm to the ecosystem we live in and raised serious concerns amongst the general public.1–6 To address this issue, the development of energy-efficient methods for oil/water separation has become an important task. These methods generally realize effective oil/water separation by either filtration or absorption of water or oils from the mixtures selectively, using materials and devices with special wetting properties.7–11 For instance, in their pioneering work, Feng and coworkers demonstrated that a mesh coated with polytetrafluoroethylene (PTFE) to make it superhydrophobic and superoleophilic can selectively permeate oils and realize oil/water separation via the “oil-removing” scheme.12 Then, in order to reduce contamination and clogging of the mesh by the oil, coated meshes with superhydrophilic and underwater-superoleophobic wetting character, operating in the “water-removing” mode where only water passes and oils do not, were developed.13 More recently, switchable mesh that can operate in both modes on demand was reported.9,10 Despite all these advances, separation of surfactant-stabilized oil/water mixtures remains a challenge, because emulsions or micro-emulsions are relatively homogeneous dispersion systems with droplets at the micrometer or nanometer scales,14 whereas the meshes mentioned above generally exhibit a pore size much larger than the emulsion droplets.1,15 In other words, traditional separation techniques for separating immiscible oil/water mixtures are not effective for emulsified oil/water mixtures,16–18 let alone surfactant-stabilized emulsions with droplet size typically below 20 μm.2,15
Recently, a breakthrough was reported by Tuteja and coworkers, using hydro-responsive membranes that are superhydrophilic and superoleophobic both in air and underwater and thus capable of separating oil-in-water and water-in-oil emulsions, with droplet size greater than 1 μm.19 Liu and coworkers developed a Janus fabric capable of breaking oil-in-water emulsions for rapid and efficient separation of oil from the emulsions.6 Jin and coworkers reported a porous superhydrophobic and superoleophilic poly(vinylidene fluoride) (PVDF) membrane2 as well as a hydrophobic–superoleophilic single-walled carbon nanotube (SWCNT) network film,15 both capable of separating water-in-oil emulsions with a droplet size ranging from micrometer to nanometer scale. However, usually the membranes employed for emulsion separation must be washed with significant quantities of alcohol or other organic solvents or water after each filtration step in order to recover their separation ability,2,15,20–24 which presumably declines due to fouling by the surfactant. Therefore, development of membranes for effective separation of surfactant-stabilized oil/water emulsions that is resistant to fouling by surfactants is a subject of interest. More recently, Jin and coworkers endowed PVDF membrane antifouling properties by introduction of zwitterionic moieties to make the membrane superhydrophilic.25
Among all surfactants commercially produced, ionic surfactants, which carry charged head groups, are produced in greater volumes than the nonionic ones and applied widely as wetting agent, dispersing agent and emulsifier. It is known that electrostatic repulsive forces existing between co-ions in the feed solution and charged surfaces would prevent the solute from depositing on the membrane surface and reduce fouling.26,27 Therefore, a charged membrane with suitable wetting character may be able to separate effectively emulsions or micro-emulsions stabilized by ionic surfactant6 and resist fouling. Polyelectrolyte multilayer (PEM) films, which can be fabricated to afford charged surfaces rapidly and effectively via layer-by-layer assembly technique on many kinds of substrate with different sizes and shapes, have emerged among others as nano-reactors and promising coatings for surface wettability manipulation.28,29 Excess charges in PEMs, located mainly at the outermost layer, can repel like-charges situated at the interface of emulsion droplets. More importantly, the type of charge carried by a PEM surface can be switched facilely by deposition of another polyelectrolyte layer. In the present work, we show that a porous polycarbonate membrane coated with a PEM can separate with high efficiency oil-in-water emulsions stabilized by ionic surfactants and resist fouling. Furthermore, the surface charge of the modified membrane can be conveniently switched between positive and negative without significant change in the wetting properties, so this membrane can process effectively oil-in-water emulsions stabilized by either anionic or cationic surfactants.
Experimental
Materials
Sodium dodecyl sulfate (SDS), cetyltrimethyl ammonium bromide (CTAB), and sodium chloride were purchased from Sinopharm Chemical Reagent Co. Ltd. Poly(diallyldimethylammonium chloride) (PDDA, 20 wt% aqueous, MW ∼ 200–350 k) and poly(sodium styrenesulfonate) (PSS, MW ∼ 70 k) were purchased from Aldrich. All chemicals were used as received without further purification. Ultrapure water (18.2 MΩ cm at 25 °C) was produced with a PGeneral GWA-UN4 system and used in all experiments. Polycarbonate membranes (diameter 47 mm, thickness 25 μm, pore size 200 nm) were purchased from Whatman, which were ultrasonically cleaned in ultrapure water for 2 min to get rid of possible surface contaminants prior to use.
PEM Deposition. A (PDDA/PSS)n film was fabricated on the polycarbonate membrane by alternatingly dipping the substrate into a PDDA (1.0 mg mL−1, with 1.0 M NaCl present) and a PSS (1.0 mg mL−1, with 1.0 M NaCl present) aqueous solution each for 15 min,29,30 with water rinsing after each dipping step. The process was repeated until a desired number of cycle n was reached, and the coating is denoted PEMn. For the PEMs terminated with a PSS layer, n = 1, 2, 3, 4, whereas for PDDA-capped PEMs, n = 0.5, 1.5, 2.5, 3.5, 4.5. The PEM-coated polycarbonate membrane was then immersed into a water bath and ultrasonicated for 0.5 min twice to remove the excess polyelectrolytes.
Preparation of oil-in-water emulsions
Anionic surfactant stabilized oil-in-water emulsion was prepared by mixing 0.020 g SDS with 90 mL water and 10 mL diesel oil. The mixture was then sonicated at a power of 2 kW for 3 h to produce a white and milky emulsion, with an apparent zeta potential of ca. −75 mV (ESI†). For cationic surfactant stabilized oil-in-water emulsion, 0.020 g CTAB and 10 mL diesel oil were added into 90 mL water, and the mixture was sonicated at a power of 2 kW for 3 h to produce a white and milky emulsion, with an apparent zeta potential of ca. +50 mV (ESI†). Excess free diesel oil liquid floating on the mixtures was removed with a pipette. The droplet size of the two emulsions prepared ranged from 100 nm to 5 μm (ESI†).
Instruments and measurements
Scanning electron micrographs (SEM) were acquired on a FEI XL30 field-emission electron microscope. Water contact angles and oil contact angles were measured on a ramé-hart 200-F1 standard goniometer at room temperature with water (5 μL) and diesel oil (5 μL) as the probing fluid, respectively. Each contact angle value reported was an average of at least five independent measurements. Optical microscopy images were taken on a Leica polarized optical microscope (POM). The purity of the filtrate was analyzed by a Thermo Scientific TRACE Gas Chromatograph Ultra AI1310 equipped with a thermal conductivity detector. Dynamic light scattering (DLS) measurements were performed on a Nano ZS zetasizer (Malvern, UK).
Results and discussion
Separation of emulsified oil/water mixture based on porous membranes is susceptible to rapid flux decline,31 which can be mainly ascribed to membrane pore clogging and surface fouling. Increasing hydrophilicity of the membrane surface is expected to increase resistance to membrane fouling because many foulants are hydrophobic in nature.27,32,33 Hydrophilic porous polycarbonate membranes are polycarbonate membranes with perpendicular round holes of a uniform pore size modified with polyvinylpyrrolidone, making the surface hydrophilic. The pore size is a critical parameter controlling the flux and separation efficiency.3 The membrane could be folded many times without cracking, indicating good flexibility and mechanical strength (ESI†). For these reasons, hydrophilic polycarbonate membranes were employed in the present study. Fig. 1A presents SEM image of the polycarbonate membrane, which shows numerous regular round pores distributing randomly in the membrane, with a pore diameter of ca. 200 nm. Contact angle measurements were carried out to examine the wetting character of the bare membrane. The surface exhibited a water contact angle and an underwater diesel oil contact angle of 53.5° and 109.6°, respectively (ESI†), displaying moderate hydrophilicity in air and oleophobicity underwater, making it suitable for separation of water from oil-in-water emulsions. After being rinsed in water for a few minutes, the polycarbonate membrane was placed onto a sand core filter plate, which was used as a support, and the assembly was mounted in a homemade filtration device (ESI†), into which a SDS stabilized diesel oil-in-water emulsion was poured and suction filtered. Once the pressure difference between the upper side and the bottom side of the membrane reached 0.1 MPa, water was observed to pass through the membrane and flow down, whereas oil droplets were retained above the membrane. The volume of filtrate collected in every 10 min (1 cycle) was recorded. This quantity is expected to decline over time if the membrane is fouled and the pores are clogged by the foulant, and the variation of this quantity with the cycle number provides a straightforward indicator for the antifouling performance of the separation membrane. Fig. 1B plots the filtrate volume as a function of the cycle number for the virgin membrane. It can be seen that the amount of filtrate decreases rapidly with increasing cycle, and little water could permeate the membrane in the tenth cycle, i.e., the membrane with weak hydrophilicity was easily fouled and the pores were quickly clogged, indicating that the hydrophilic porous polycarbonate membrane has poor antifouling ability against oil-in-water emulsion stabilized by anionic surfactants.25
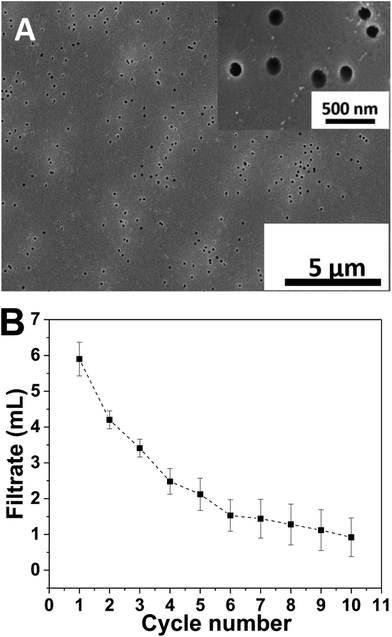 |
| Fig. 1 (A) SEM image of a virgin hydrophilic polycarbonate membrane. The inset shows a magnified view of the perpendicular pores with a diameter of ca. 200 nm in the membrane. (B) The filtration flux represented by volume of the filtrate collected in a 10 min cycle as a function of the cycle number for the virgin membrane. | |
The fouling of surfactant to the membrane may be caused by the non-specific interactions between the surfactant molecules and the membrane surface such as van der Waals interactions, hydrophobic interactions, hydrogen bonding and electrostatic interactions.34 A well-known strategy to mitigate membrane fouling is surface modification, which by altering the surface charge, hydrophilicity and smoothness may endow membrane with improved fouling resistance and preserve the flux.27 The layer-by-layer deposition provides a convenient technique for modifying the membrane surface. PEMs can be facilely fabricated on and conform a large variety of substrates of different sizes and shapes, affording charged surfaces easily, and have proved effective for surface wettability manipulation.28,30,35 Here, two typical polyelectrolytes, PDDA and PSS, were deposited on the hydrophilic porous polycarbonate membrane to form (PDDA/PSS)n PEMs in order to improve the fouling resistance of the membrane. Based on our previous research,24 the thickness of the (PDDA/PSS)4 film is ca. 8–10 nm, a small value compared to the pore diameter, so that the coating should conform the shape of the substrate and not block the pores. As seen in the SEM image (Fig. 2A), the topography of the substrate is largely preserved and the pore size remains almost the same after deposition of the (PDDA/PSS)4 film. The PEM-coated polycarbonate membrane surface was hydrophilic in air, with a water contact angle of 65.3°, and exhibited underwater oleophobicity with a contact angle of 138.1° using diesel oil as the probe fluid (ESI†). It has been demonstrated that the surface of PSS-capped PDDA/PSS multilayers is negatively charged, with a zeta potential of −30 mV.36 Therefore, the polycarbonate membrane coated with a PSS-capped PEM was employed to separate a model oil-in-water emulsion stabilized by SDS, an anionic surfactant, to assess its performance.
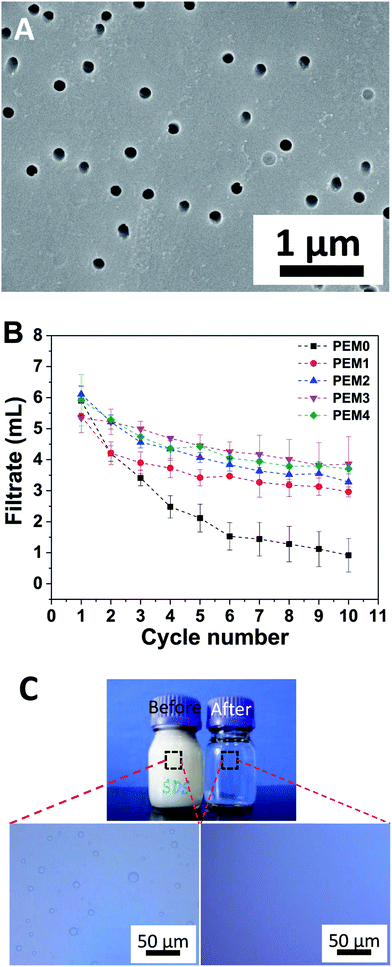 |
| Fig. 2 (A) SEM image of the PEM-coated polycarbonate membrane. (B) The filtration flux represented by volume of the filtrate collected in a 10 min cycle as a function of the cycle number for the virgin membrane and membranes coated with PSS-capped PEMn with n = 1–4 in separation of the SDS-stabilized emulsion. (C) Photograph of the SDS-stabilized oil-in-water emulsion, before and after filtration, and optical microscopy images of the emulsion feed and the filtrate. | |
Fig. 2B plots the variation of filtrate volume collected for a 10 min cycle for membranes coated with the PDDA/PSS PEM with different number of bilayers. Compared with the virgin membrane, which lost more than 80% of its permeability in 10 cycles, the PEM-coated membranes retained above 60% of their original permeation rates during the same period, showing much better antifouling performance. In particular, the membrane modified with (PDDA/PSS)3 exhibited the best improvement, retaining more than 80% of its permeation rate after 10 cycles. It should be pointed out that this was achieved without using alcohol or other organic solvent to rinse the membrane in between the cycles.
To assess the separation performance of the PEM-coated membrane, optical microscopy was employed to observe the feed emulsion and the collected filtrate, and the images are compared in Fig. 2C. Oil droplets are clearly visible in the feed, whereas no droplets are observed in the collected filtrate in the whole view. This was the case for the filtrate collected in all cycles, indicating that micrometer-sized emulsion droplets can be completely separated by the PEM-coated membrane. As discussed above, the pristine hydrophilic membrane surface is neutral and can be easily fouled by surfactants, and the pores are clogged by the adsorbed species, leading to declining flux. After coated with a PSS-capped PEM, the surface is rich in excess sulfonate groups uncompensated by the quaternary amine groups in the PDDA, rendering the surface negatively charged. The charge density is further increased in water due to orientation change of the benzenesulfonate moieties at the PEM surface.37 The hydrophilic and negatively charged surface repels the anionic surfactant molecules and the emulsion droplets carrying like charges by electrostatic repulsion, reducing their adsorption at the membrane surface, resulting in better antifouling performance. This is schematically illustrated in Scheme 1. The coating was found to be stable in the operation, as no elemental composition change was detected by XPS after 10 filtration cycles (ESI†). The flux of filtrate permeating through the PEM-coated membrane was ca. 24 L m−2 h−1 as calculated from the effective area of the membrane under a pressure difference of about 0.1 MPa. The flux observed was relatively low, which may be attributed to the low pore density of the polycarbonate membrane used in the present study, and it is conceivable that the flux can be increased proportionally by using membranes of higher pore densities.
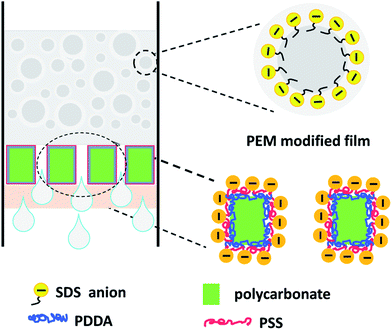 |
| Scheme 1 Schematic illustration of the negatively charged surface of the PEM-coated polycarbonate membrane and oil droplets in the emulsion stabilized by SDS. | |
The same strategy can be applied to handle oil-in-water emulsions stabilized by cationic surfactants. This time, the polycarbonate membrane was coated with a PDDA-capped PEM, and the model oil-in-water emulsion was stabilized by CTAB ESI.† Fig. 3A plots the volume of the filtrate collected in a 10 min cycle as a function of the cycle number for the virgin membrane and the membranes coated with PDDA-capped PEMs of different number of bilayers, respectively. Again, the permeability of the virgin membrane decreased by 80% in 10 cycles, showing poor antifouling ability. In addition, compared with the coated membranes, the flux in the first cycle was significantly lower, indicating that the virgin membrane is more susceptible to fouling by the CTAB-stabilized emulsion than by the SDS-stabilized one. In contrary, the PEM-modified membranes, except the one coated with a single PDDA layer (n = 0.5), all retained >80% of their permeability after 10 cycles. Apparently, the excess quaternary amine groups in the PDDA top layer uncompensated by the sulfonate groups render the surface of the modified membrane positively charged and repel the CTAB molecules and the oil droplets carrying like charges, preventing them from adsorbing to the membrane surface. In the case of n = 0.5 (membrane coated with a single PDDA layer), probably the surface coverage of PDDA was not complete and the surface charge density was low, which is typical in layer-by-layer deposition, resulting in poor fouling resistance as compared to other PEM-coated membranes. The separation performance of the membrane coated with a PDDA-capped PEM for CTAB-stabilized emulsion was assessed by optical microscopy. Fig. 3B compares the optical images of the emulsion and the filtrate, which shows that oil droplets, abundant in the emulsion, are completely absent in the filtrate, indicative of a clean separation.
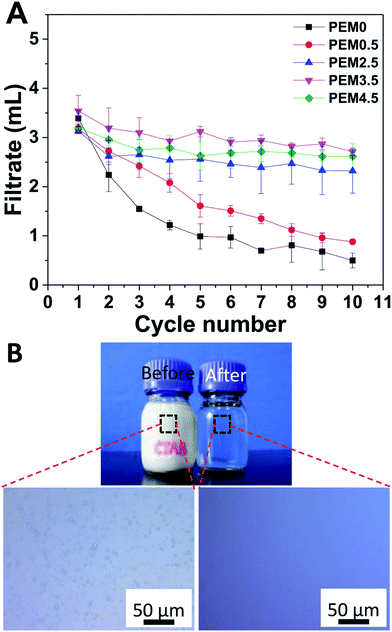 |
| Fig. 3 (A) The filtration flux represented by volume of the filtrate collected in a 10 min cycle as a function of the cycle number for the virgin membrane and membranes coated with PDDA-capped PEMn with n = 0.5, 2.5, 3.5 and 4.5, respectively, in separation of the CTAB-stabilized emulsion. (B) Photograph of the CTAB-stabilized oil-in-water emulsion, before and after filtration, and optical microscopy images of the emulsion feed and the filtrate. | |
The filtrate purity was further characterized by measuring diesel oil volume percentage in the filtrate with gas chromatography (GC). As seen in Fig. 4, the purity of filtrates (water) is above 99.98% in all cases. In contrast, the volume fraction of diesel oil in the emulsion was 10%. This result indicates extremely high separation efficiency. The purity of the water separated from the SDS-stabilized oil-in-water emulsions using membrane coated with a PSS-capped PEM was the highest. This may be attributed to stronger electrostatic repulsion between the membrane surface and the emulsion droplets due to a higher charge density at the membrane surface as discussed above and a higher charge density carried by the droplets as indicated by the greater value of the zeta-potential.
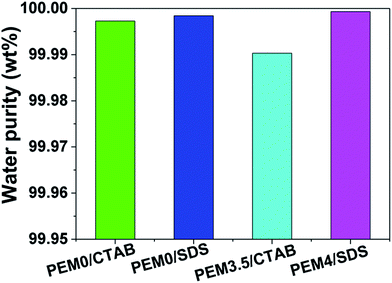 |
| Fig. 4 Purity of filtrate separated by different membranes. | |
Conclusions
In this work, porous polycarbonate membranes were coated with PDDA/PSS multilayers using the facile layer-by-layer deposition technique to produce foul-resistant membranes for separation of oil-in-water emulsions stabilized by ionic surfactants. While the virgin membrane was easily fouled by the surfactants and emulsions and the pores were quickly clogged, resulting in more than 80% decrease in flux in 10 cycles of operation, the PEM coating was found to significantly improve the foul-resistance performance of the membrane. The PSS-capped PEMs rendered the membrane surface negatively charged, making it resistant to fouling in separation of emulsions stabilized by SDS, an anionic surfactant, whereas a PDDA-capped PEM led to positive charges at the membrane surface, resulting in higher foul-resistance in separation of emulsions stabilized by CTAB, a cationic surfactant. The PEM-coated membranes retained >80% of their permeability after extended periods of operation without the need to rinse with alcohol or other organic solvents, and exhibited high separation efficiency of >99.98%. Although polycarbonate membrane was selected as the substrate in this study, the simple and versatile approach can be readily extended to other porous substrates with pore size suitable for separation of emulsions, and easily scaled up, making it a very promising method to fabricate charged membranes with antifouling capability for separation of oil-in-water emulsions in practical applications.
Conflicts of interest
There are no conflicts to declare.
Acknowledgements
This work is supported by the National Natural Science Foundation of China (21429401). Z. S. and T. S. thank the Public Foundation of Chubu Science and Technology, Japan for support.
Notes and references
- M. Tao, L. Xue, F. Liu and L. Jiang, Adv. Mater., 2014, 26, 2943–2948 CrossRef CAS PubMed.
- W. Zhang, Z. Shi, F. Zhang, X. Liu, J. Jin and L. Jiang, Adv. Mater., 2013, 25, 2071–2076 CrossRef CAS PubMed.
- Y. Z. Zhu, D. Wang, L. Jiang and J. Jin, NPG Asia Mater., 2014, 6, e101 CrossRef CAS.
- K. Liu, X. Yao and L. Jiang, Chem. Soc. Rev., 2010, 39, 3240–3255 RSC.
- B. Wang, W. Liang, Z. Guo and W. Liu, Chem. Soc. Rev., 2015, 44, 336–361 RSC.
- Z. Wang, Y. Wang and G. Liu, Angew. Chem., Int. Ed., 2016, 55, 1291–1294 CrossRef CAS PubMed.
- Q. Zhu and Q. Pan, ACS Nano, 2014, 8, 1402–1409 CrossRef CAS PubMed.
- Z. Wang, X. Jiang, X. Cheng, C. H. Lau and L. Shao, ACS Appl. Mater. Interfaces, 2015, 7, 9534–9545 CAS.
- G. Zhang, M. Li, B. Zhang, Y. Huang and Z. Su, J. Mater. Chem. A, 2014, 2, 15284–15287 CAS.
- G. J. Dunderdale, M. W. England, T. Sato, C. Urata and A. Hozumi, Macromol. Mater. Eng., 2016, 301, 1032–1036 CrossRef CAS.
- R. K. Gupta, G. J. Dunderdale, M. W. England and A. Hozumi, J. Mater. Chem. A, 2017, 5, 16025–16058 CAS.
- L. Feng, Z. Zhang, Z. Mai, Y. Ma, B. Liu, L. Jiang and D. Zhu, Angew. Chem., Int. Ed., 2004, 43, 2012–2014 CrossRef CAS PubMed.
- Z. Xue, S. Wang, L. Lin, L. Chen, M. Liu, L. Feng and L. Jiang, Adv. Mater., 2011, 23, 4270–4273 CrossRef CAS PubMed.
- C. R. Gao, Z. X. Sun, K. Li, Y. N. Chen, Y. Z. Cao, S. Y. Zhang and L. Feng, Energy Environ. Sci., 2013, 6, 1147–1151 CAS.
- Z. Shi, W. Zhang, F. Zhang, X. Liu, D. Wang, J. Jin and L. Jiang, Adv. Mater., 2013, 25, 2422–2427 CrossRef CAS PubMed.
- Y. Chen, N. Liu, Y. Cao, X. Lin, L. Xu, W. Zhang, Y. Wei and L. Feng, Sci. Rep., 2016, 6, 32540 CrossRef CAS PubMed.
- F. Zhang, W. B. Zhang, Z. Shi, D. Wang, J. Jin and L. Jiang, Adv. Mater., 2013, 25, 4192–4198 CrossRef CAS PubMed.
- N. Liu, M. Zhang, W. F. Zhang, Y. Z. Cao, Y. N. Chen, X. Lin, L. X. Xu, C. Li, L. Feng and Y. Wei, J. Mater. Chem. A, 2015, 3, 20113–20117 CAS.
- A. K. Kota, G. Kwon, W. Choi, J. M. Mabry and A. Tuteja, Nat. Commun., 2012, 3, 1025 CrossRef PubMed.
- A. L. Ahmad, M. A. Majid and B. S. Ooi, Desalination, 2011, 268, 266–269 CrossRef CAS.
- W. Zhang, Y. Zhu, X. Liu, D. Wang, J. Li, L. Jiang and J. Jin, Angew. Chem., Int. Ed., 2014, 53, 856–860 CrossRef CAS PubMed.
- J. Ju, T. Wang and Q. Wang, Colloids Surf., A, 2015, 481, 151–157 CrossRef CAS.
- X. Lin, Y. Chen, N. Liu, Y. Cao, L. Xu, W. Zhang and L. Feng, Nanoscale, 2016, 8, 8525–8529 RSC.
- M. Liu, Y. Hou, J. Li and Z. Guo, Langmuir, 2017, 33, 3702–3710 CrossRef CAS PubMed.
- Y. Zhu, W. Xie, F. Zhang, T. Xing and J. Jin, ACS Appl. Mater. Interfaces, 2017, 9, 9603–9613 CAS.
- D. Rana and T. Matsuura, Chem. Rev., 2010, 110, 2448–2471 CrossRef CAS PubMed.
- R. Kumar and A. F. Ismail, J. Appl. Polym. Sci., 2015, 132, 42042 Search PubMed.
- L. Wang, Y. Lin, B. Peng and Z. Su, Chem. Commun., 2008, 5972–5974 RSC.
- C. Chu and Z. Su, Chin. J. Appl. Chem., 2016, 33, 379–390 CAS.
- G. Zhang, X. Zhang, Y. Huang and Z. Su, ACS Appl. Mater. Interfaces, 2013, 5, 6400–6403 CAS.
- Y. Si and Z. Guo, Chem. Lett., 2015, 44, 874–883 CrossRef CAS.
- J. Lei and M. Ulbricht, J. Membr. Sci., 2014, 455, 207–218 CrossRef CAS.
- L. X. Xing, N. N. Guo, Y. T. Zhang, H. Q. Zhang and J. D. Liu, Sep. Purif. Technol., 2015, 146, 50–59 CrossRef CAS.
- R. Zhang, Y. Liu, M. He, Y. Su, X. Zhao, M. Elimelech and Z. Jiang, Chem. Soc. Rev., 2016, 45, 5888–5924 RSC.
- L. M. Wang, Y. Lin and Z. H. Su, Soft Matter, 2009, 5, 2072–2078 RSC.
- B. Wu, C. Li, H. Yang, G. Liu and G. Zhang, J. Phys. Chem. B, 2012, 116, 3106–3114 CrossRef CAS PubMed.
- X. Liu, C. Leng, L. Yu, K. He, L. J. Brown, Z. Chen, J. Cho and D. Wang, Angew. Chem., Int. Ed., 2015, 54, 4851–4856 CrossRef CAS PubMed.
Footnote |
† Electronic supplementary information (ESI) available. See DOI: 10.1039/c7ra13605f |
|
This journal is © The Royal Society of Chemistry 2018 |
Click here to see how this site uses Cookies. View our privacy policy here.