DOI:
10.1039/C8RA02103A
(Paper)
RSC Adv., 2018,
8, 20157-20165
The enhancement of photocatalytic performance of SrTiO3 nanoparticles via combining with carbon quantum dots†
Received
9th March 2018
, Accepted 17th May 2018
First published on 4th June 2018
Abstract
Carbon quantum dots were prepared by a simple chemical process using activated carbon as carbon source. The as-prepared carbon quantum dots are fine with a narrow size distribution and show excellent hydrophilicity. The carbon quantum dots were combined with SrTiO3 nanoparticles through a simple impregnation process to obtain a carbon quantum dots/SrTiO3 nanocomposite. The photocatalytic reaction rate of carbon quantum dots/SrTiO3 nanocomposite is about 5.5 times as large as that of pure SrTiO3 in the degradation of rhodamine B under sunlight irradiation. The enhanced performance in the degradation of rhodamine B may be attributed to the interfacial transfer of photogenerated electrons from SrTiO3 to carbon quantum dots, leading to effective charge separation in SrTiO3. Carbon quantum dots show potential applications in high-efficiency photocatalyst design.
1. Introduction
Carbon quantum dots (CQDs) are a new type of carbon nanomaterials and have been drawing much attention in recent years due to their unique photoluminescence (PL), high chemical inertness, good hydrophilicity, low toxicity, good biocompatibility, environmental friendliness, and high photostability.1–4 CQDs have shown promising applications in sensing,5 drug delivery,6 optoelectronic devices,7 and bioimaging.8 In addition, due to their excellent electron transfer and reservoir properties,2,9 CQDs were used to enhance the photocatalytic performance of In2S3,10 WO3,11 Bi2SiO5,12 Ag3PO4,13 BiVO4,14 Bi2MoO6,15 Fe2O3,16 and TiO2.17 Among various semiconductors, perovskite metal oxides such as SrTiO3 are promising photocatalysts because of their excellent electronic and optical properties, photochemical stability, low cost, and high catalytic efficiency.18 SrTiO3 has been extensively studied for photodegradation of organic pollutants and water splitting.19,20 However, the high electron (e−) and hole (h+) recombination efficiency of SrTiO3 results in low photocatalytic performance.21 Hence suppressing the e− and h+ recombination in SrTiO3 is the key to enhance its photocatalytic performance. Therefore, we combine CQDs with SrTiO3 to fabricate a novel CQD/SrTiO3 nanocomposite to achieve the efficient separation of the photogenerated e−–h+ pairs and to enhance the photocatalytic performance.
To date, numerous processes including acidic oxidation,22 ultrasonic treatment,23 microwave treatment,24 electrochemical exfoliation,25 laser ablation,26 thermal decomposition,27 hydrothermal treatment,28 plasma treatment,29 and high-energy ball milling30 have been developed to prepare CQDs from a variety of carbon precursors. Most of these processes suffer more or less from expensive precursor materials, complicated apparatus, harsh reaction conditions, tedious purification procedures, and high cost. Among these processes, acidic oxidation is an effective process for the large-scale preparation of carbon nanoparticles. Nevertheless, this process requires the neutralization of residual acid with a strong alkali. This results in a large amount of inorganic salt ions in the products and requires a tedious purification procedure.31,32 Here we present a simple process to prepare CQDs by acidic oxidation of activated carbon with the most affordable oxidant, nitric acid (HNO3). In our present work, the residual acid was directly evaporated rather than neutralized with a strong alkali. Thus the as-prepared CQDs contain no inorganic salt ions so that the purification procedure is simpler. Compared with other processes, our process is simple because no expensive reagents, no tedious purification procedures, no harsh reaction conditions, or no complicated apparatus are required.
The as-prepared CQDs are fine in size and have oxygen-containing functional groups (OCFGs) on their surface which endow them excellent hydrophilicity and facilitate further functionalization and applications. A novel nanocomposite photocatalyst (CQD/SrTiO3) was fabricated by combining the as-prepared CQDs with SrTiO3 nanoparticles through a simple impregnation process. Its photocatalytic performance was evaluated by degradation of Rhodamine B (RhB) under sunlight irradiation. Compared with pure SrTiO3, the CQD/SrTiO3 nanocomposite shows an excellent photocatalytic performance in the photodegradation of RhB. The photocatalytic reaction rate of the CQD/SrTiO3 nanocomposite is about 5.5 times as large as that of pure SrTiO3. Furthermore, the possible mechanism for the excellent photocatalytic performance of the CQD/SrTiO3 nanocomposite will be discussed.
2. Experimental
2.1 Materials
Nitric acid was obtained from Xilong Chemical Co. Ltd (Shantou, China). Charcoal activated and rhodamine B were from Sinopharm Chemical Reagent Co. Ltd (Shanghai, China). Strontium nitrate and citric acid were provided by Kermel Chemical Reagent Co. Ltd (Tianjin, China). Titanium isopropoxide and ethylene glycol were purchased from Li'anlong Bohua Pharmaceutical Chemical Co. Ltd (Tianjin, China). All chemical reagents used in this work were analytical grade and used without further purification.
2.2 Instrumentation
Transmission electron microscopy (TEM) observations as well as selected-area electron diffraction (SAED) analysis were performed on an FEI Tecnai G2 F30 field emission electron microscope operating at a voltage of 300 kV. X-Ray Diffraction (XRD) patterns (2θ scans) were recorded using a Rigaku D/Max-2400 X-ray diffractometer with Cu Kα radiation. Fourier transform infrared (FTIR) spectra were collected in the KBr medium on a Nicolet NEXUS 670 FTIR spectrometer. X-Ray Photoelectron Spectroscopy (XPS) measurements were performed on a Kratos Axis Ultra DLD spectrometer using Al Kα X-ray beam of 250 W as the excitation source. Scanning electron microscopy (SEM) observations and energy dispersive X-ray spectroscopy (EDS) analysis were conducted on a Hitachi S-4800 field emission scanning electron microscope working at an acceleration voltage of 20 kV. The diffuse reflectance ultraviolet-visible (UV-vis) absorption spectrum was measured using a Hitachi U-3900H spectrometer, and BaSO4 was used as a reference standard. Electrochemical impedance spectra (EIS) were recorded on a RST5200 electrochemical work station with a three-electrode system at room temperature. The PL spectra were measured using an Edinburgh Instruments FLS920 spectrometer. The total organic carbon (TOC) analysis was conducted using a Shimadzu TOC-VCPH analyzer. Centrifugation was performed on a TG 22 centrifuge with rotation speeds tunable from 100 to 22
000 revolutions per minute (rpm).
2.3 Preparation of CQDs
For a typical process, 2.0 g activated carbon was added to 250 mL HNO3 aqueous solution (3 mol L−1). After 30 min ultrasonic bath, the mixture was refluxed for 16 h. The resulting mixture was cooled to room temperature and filtered. After the residual acid was completely evaporated at 80 °C in a water bath, light brown powders were obtained. The powders were dispersed in deionized water (60 mL), yielding a suspension containing CQDs. The suspension was centrifuged at 15
000 rpm for 10 min. Finally, a transparent, light brown supernatant containing CQDs was obtained.
2.4 Preparation of SrTiO3 nanoparticles and CQD/SrTiO3 nanocomposite
SrTiO3 nanoparticles were prepared according to a reported process.19 Typically, 3.26 mL titanium isopropoxide was dissolved in 25 mL ethylene glycol for about 30 min under an Ar atmosphere at room temperature. Then 20.82 g citric acid was added into the solution and stirred until complete dissolution of the reagents. Then 5.69 g strontium nitrate was slowly added into the solution under stirring until the solution became transparent. The solution was heated to about 120 °C and kept for 5 h to promote polymerization. After heating and evaporation of the solvents, the reaction mixture gelled into a transparent brown resin. The resin was charred at 350 °C for 3 h and cooled to room temperature. Subsequently, the charred resin was ground to fine powders. The obtained powders were calcined at 800 °C for 6 h. The calcined powders were washed three times with 2 mol L−1 HNO3 aqueous solution and three times with deionized water and then dried in an oven at 80 °C for 12 h. Finally, SrTiO3 nanoparticles were obtained.
CQD/SrTiO3 nanocomposite was prepared via a simple impregnation process. In the experiments, CQD suspensions with a concentration of 0.75 mg mL−1 were obtained by suspending 15 mg CQDs in 20 mL deionized water. 0.06 g SrTiO3 nanoparticles were added into 6 mL CQD suspension and mixed by stirring for 2 h. Then the mixture was dried in a vacuum oven at 80 °C for 12 h to obtain CQD/SrTiO3 nanocomposite.
2.5 Photocatalytic measurements
In the experiments, 50 mg photocatalyst was suspended in 100 mL quartz silica glass beaker containing 50 mL RhB solution with a concentration of 10 mg L−1. A 350 W high pressure Xe lamp was used for illumination to provide an artificial sunlight. The distance between the light source and samples was about 14 cm. Before irradiation, the suspension was magnetically stirred in dark for 30 min to achieve the adsorption/desorption equilibrium between photocatalyst and RhB. Then the suspension was irradiated under the artificial sunlight with continuous stirring. To analyze the concentration change of RhB, 5 mL suspension was sampled every 20 min and centrifuged (15
000 rpm, 5 min) to remove the solid photocatalysts (SrTiO3 nanoparticles or CQD/SrTiO3 nanocomposite). The concentration of RhB was determined from the absorbance at the wavelength of 554 nm using a PERSEE TU-1810 UV-vis spectrophotometer.
3. Results and discussion
3.1 Characterizations of CQDs
The morphology and structure of the CQDs prepared from activated carbon were analyzed by TEM and FTIR. The TEM image in Fig. 1a reveals that the as-prepared CQDs are completely disperse without any agglomeration, fine in size, and nearly spherical in shape. According to their size distribution histogram in Fig. 1b, the as-prepared CQDs have a narrow size distribution between 1.5 and 4.1 nm and an average particle size of 2.7 nm. The SAED pattern in the inset of Fig. 1a shows broad diffraction halos and a faint larger one, indicating that the as-prepared CQDs are amorphous in structure. The XRD pattern of the as-prepared CQDs in Fig. 1c shows only a single diffuse halo around 23.5° (2θ) which is indicative of amorphous structure. The FTIR spectrum of the as-prepared CQDs in Fig. 1d shows the distinct absorption bands of O–H at 3422 cm−1, C–H at 2927 and 2855 cm−1, C
O at 1605 cm−1, C
C at 1433 cm−1, C–O–C asymmetric stretching vibration at 1339 cm−1, and C–O–C symmetric stretching vibration at 1129 and 1090 cm−1.33,34 The FTIR spectrum indicates the existence of OCFGs in the as-prepared CQDs. These OCFGs improve the hydrophilicity and stability of the CQDs in aqueous systems. Moreover, they help combine the CQDs with other nanomaterials because of the strong chemical interactions between the OCFGs on the CQDs and other nanomaterials.35,36
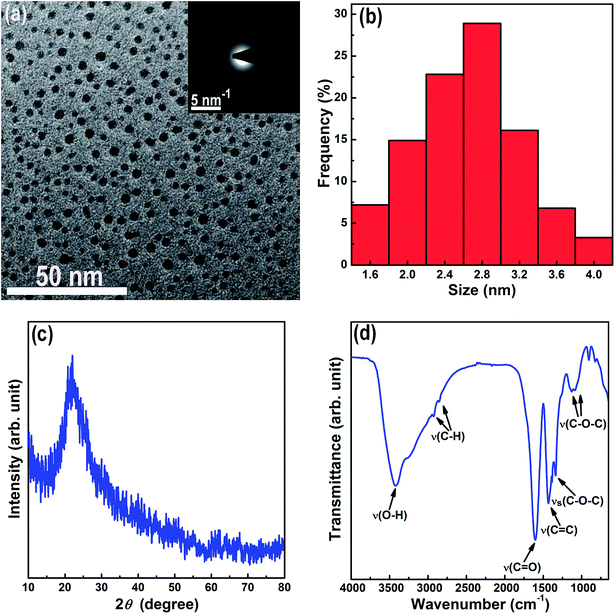 |
| Fig. 1 TEM micrograph (the inset shows the SAED pattern) (a), size distribution histogram (b), XRD pattern (c), and FTIR spectrum (d) of the CQDs. | |
3.2 Characterizations of SrTiO3 nanoparticles and CQD/SrTiO3 nanocomposite
CQD/SrTiO3 nanocomposite was prepared by combining the CQDs with SrTiO3 nanoparticles through a simple impregnation process. The structure and composition of the prepared CQD/SrTiO3 nanocomposite were analyzed by TEM, XRD, EDS, and XPS. The XRD patterns of the pure SrTiO3 nanoparticles and CQD/SrTiO3 nanocomposite (Fig. 2a) show the distinctive diffraction peaks of SrTiO3 with the perovskite structure of a cubic symmetry (JCPDS no. 79-0176),19 and no diffraction peaks from impurities such as TiO2 or Ti(OH)4 were detected. For the CQD/SrTiO3 nanocomposite, a diffuse peak at 23.5° was observed and may be attributed to the small quantity of the CQDs in the CQD/SrTiO3 nanocomposite.37 The low magnification TEM image of the pure SrTiO3 nanoparticles in Fig. 2b shows that the pure SrTiO3 nanoparticles are slightly agglomerated and 20 to 40 nm in size. After the combination with the CQDs, the low magnification TEM image of the resulting CQD/SrTiO3 nanocomposite nanoparticles in Fig. 2c reveals that the CQD/SrTiO3 nanoparticles are agglomerated and almost same in size and morphology as the SrTiO3 nanoparticles. This indicates that the introduction of the CQDs does not change the morphology and size of the SrTiO3 nanoparticles significantly. Due to the presence of hydrophilic OCFGs on the CQD/SrTiO3 nanocomposite nanoparticles, which will be confirmed by the XPS spectra, the agglomerates of the dry CQD/SrTiO3 nanocomposite nanoparticles should be soft agglomeration. The high magnification TEM image of the CQD/SrTiO3 nanocomposite in Fig. 2d reveals that a large number of fine nanoparticles (marked with white arrows) are attached to the surface of the SrTiO3 nanoparticles. The high magnification TEM image of pure SrTiO3 nanoparticles prepared in absolute ethanol in Fig. 2e shows the smooth surface of the pure SrTiO3 nanoparticles. So the fine nanoparticles on the SrTiO3 nanoparticles (Fig. 2d) should be the CQDs. This supports the formation of the CQD/SrTiO3 nanocomposite by the addition of the CQDs. The high-resolution TEM image of the CQD/SrTiO3 nanocomposite in Fig. 2f reveals lattice fringes of an SrTiO3 nanoparticle and a large number of CQDs (marked with white arrows) attached onto the surface of an SrTiO3 nanoparticle. A fringe spacing of 0.275 nm is in good agreement with the (200) interplanar spacing of SrTiO3. The EDS element mappings in Fig. 3 clearly show that the C, O, Sr, and Ti elements are uniformly distributed in the nanocomposite, confirming that the CQD/SrTiO3 nanocomposite consists of CQDs and SrTiO3. The content of CQDs in the CQD/SrTiO3 nanocomposite was estimated to be about 4.13 wt% by EDS analysis (Fig. S1 in ESI†). Such a structural feature suggests the combination of SrTiO3 with CQDs which may endow the resulting nanocomposite with a good contact between CQDs and SrTiO3. This is crucial to achieving a promoted interfacial charge transfer.
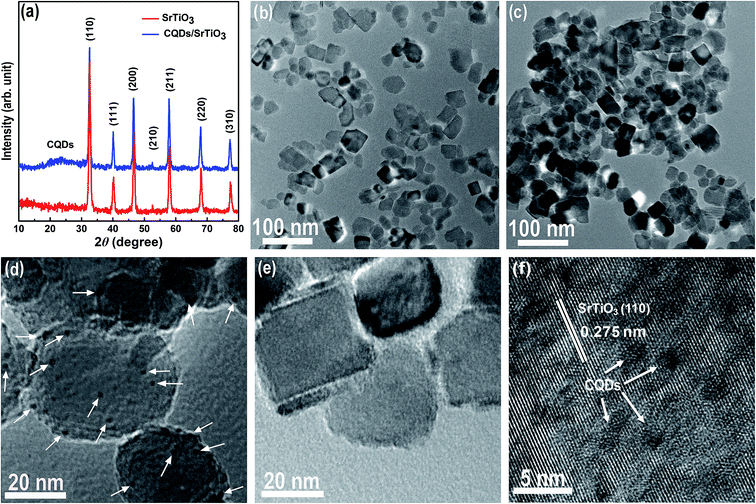 |
| Fig. 2 XRD patterns (a) of pure SrTiO3 and the CQD/SrTiO3 nanocomposite and TEM or high-resolution TEM images of pure SrTiO3 (b and e) and the CQD/SrTiO3 nanocomposite (c, d, and f). The CQDs are marked with white arrows. | |
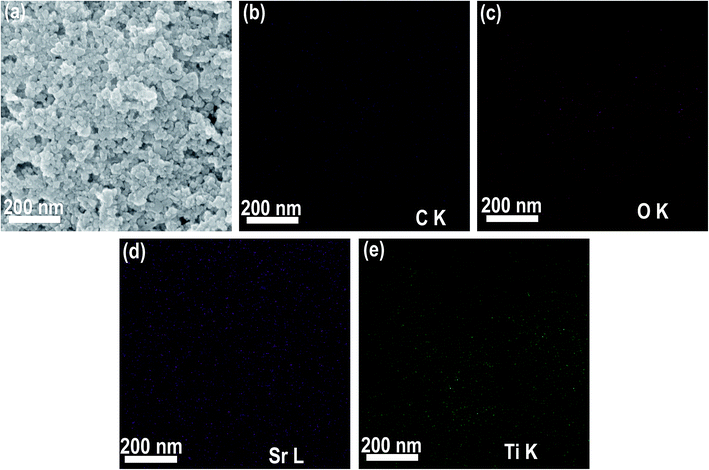 |
| Fig. 3 SEM image of the CQD/SrTiO3 nanocomposite (a) and corresponding elemental mapping images of C (b), O (c), Sr (d), and Ti (e). | |
To analyze the interactions of the CQDs with SrTiO3, XPS analysis was performed on the CQD/SrTiO3 nanocomposite. The XPS spectrum (Fig. 4a) shows the existence of C, O, Sr, and Ti in the CQD/SrTiO3 nanocomposite. The high-resolution XPS spectrum of Sr3d in Fig. 4b contains two peaks at 132.4 and 134.2 eV which can be attributed to Sr3d5/2 and Sr3d3/2, respectively.38 The high-resolution XPS spectrum of Ti2p in Fig. 4c shows two peaks at 457.8 and 463.8 eV which are assigned to Ti2p3/2 and Ti2p1/2, respectively.39 The high-resolution XPS spectrum of O1s in Fig. 4d displays three peaks at 533.1, 531.8, and 529.4 eV which are assigned to C–O, C
O, and Ti–O, respectively.39,40 The high-resolution C1s XPS spectra of the CQD/SrTiO3 nanocomposite and CQDs are shown in Fig. 4e and f, respectively. The XPS peaks of the C1s spectrum centered at the binding energies of 288.5, 286.1, and 284.5 eV are attributed to C
O, C–O, and C–C/C
C, respectively.40 A new peak at 281.5 eV in the C1s spectrum of the CQD/SrTiO3 nanocomposite appears compared to that of the CQDs. This new peak may be attributed to the chemical interaction between the CQDs and SrTiO3 in the CQD/SrTiO3 nanocomposite.39,41 The XPS analysis results reveal the presence of CQDs in the CQD/SrTiO3 and the strong interface interactions between CQDs and SrTiO3.
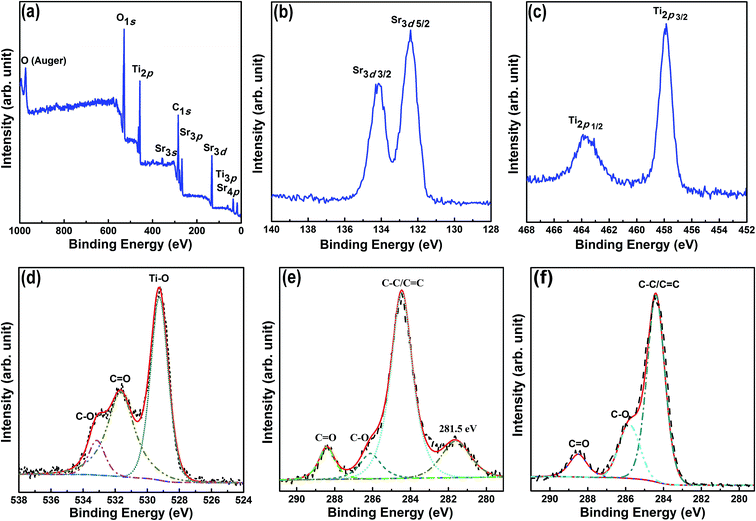 |
| Fig. 4 XPS (a) and enlarged Sr3d (b), Ti2p (c), O1s (d), and C1s (e) spectra of the CQD/SrTiO3 nanocomposite and enlarged C1s spectrum of the CQDs (f). | |
3.3 Optical properties
Photoabsorption capability is an important factor influencing the photocatalytic performance of photocatalysts and usually evaluated from UV-vis diffuse reflectance spectrum.42,43 As shown in Fig. 5a, the pure SrTiO3 nanoparticles show strong absorption in the UV region which originates from the charge transfer response of SrTiO3 from the valence band (VB) to the conduction band (CB). Compared with pure SrTiO3, the CQD/SrTiO3 nanocomposite exhibits obvious visible light absorption ranging from 400 to 600 nm besides the strong UV absorption. The enhanced light absorption of the CQD/SrTiO3 nanocomposite can be ascribed to the optical absorption of CQDs.11,15,17 The optical band gaps of the pure SrTiO3 and CQD/SrTiO3 nanocomposite can be estimated via the formula (αhν)n = A(hν − Eg), where α, h, ν, Eg, and A are the absorption coefficient, Planck constant, light frequency, band gap, and a constant, respectively, and n is an exponent determined by the nature of the electron transition during the absorption process (n = 2 for allowed direct transition and n = 1/2 for allowed indirect transition).19,44,45 Fig. 5b shows a curve of (αhν)2 versus hν from which the band gaps of SrTiO3 and CQD/SrTiO3 were estimated to be 3.16 and 3.15 eV, respectively. These results indicate that SrTiO3 and CQD/SrTiO3 have almost the same band gap energy within the experiment error. The band gap of SrTiO3 was not narrowed by combining with CQDs. Similar results were reported in literature.45,46 The UV-vis absorption spectrum of the CQDs in the range of 200–600 nm (Fig. S2 in ESI†) displays a broad absorption peak centered at 250 nm representing a typical absorption of an aromatic π system.47 Reported studies showed that the upconverted emission of CQDs was responsible for the visible-light-responding photocatalytic performance of the CQD-based composite photocatalysts.47,48 However, this is not the case of our present CQD/SrTiO3 photocatalyst. As shown in Fig. 6, the upconverted emission wavelength of the CQDs is larger than 400 nm under excitation of different wavelengths. Therefore, upconverted emission of the CQDs is not effective to excite photocatalysis of SrTiO3.
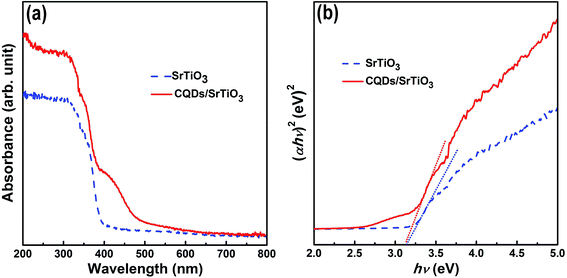 |
| Fig. 5 UV-vis diffuse reflectance spectrum (a) and (αhν)2 versus hν curve (b) of pure SrTiO3 and the CQD/SrTiO3 nanocomposite. | |
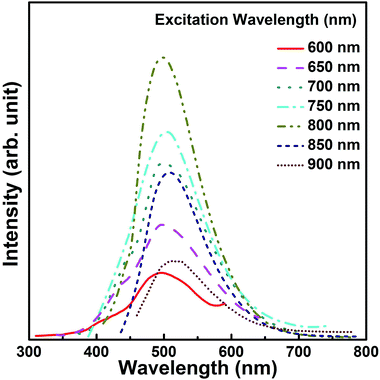 |
| Fig. 6 Upconverted PL emission spectra of the CQDs at different excitation wavelengths. | |
3.4 Photocatalytic performances
The photocatalytic performance of the CQD/SrTiO3 nanocomposite was evaluated and compared with pure SrTiO3 by the degradation of RhB under sunlight irradiation. The adsorption analysis of the catalysts in dark for RhB (Fig. S3 in ESI†) reveals that the absorption–desorption balance is achieved between the catalysts and RhB in about 30 min. About 10% and 11% of RhB was adsorbed in dark by SrTiO3 and the CQD/SrTiO3 nanocomposite, respectively, within about 30 min. This should be attributed to their different adsorption capacity. Fig. 7a plots the RhB concentration versus irradiation time under sunlight. RhB has about 7% self-degradation after irradiation for 120 min. When the CQDs were used as photocatalyst, the degradation of RhB is similar to the self-degradation of pure RhB. This manifests that the CQDs have almost no photocatalytic performance under sunlight. In contrast, the degradation of RhB in the presence of the CQD/SrTiO3 nanocomposite under sunlight reaches 73% for 120 min whereas only 22% of RhB is degraded by using pure SrTiO3. As well known, most of the photocatalytic reactions follow a pseudo-first-order kinetic equation, −ln(C/C0) = kt, where C0 and C are the equilibrium concentration of adsorption and the concentration of RhB at the irradiation time t, respectively, and k is the apparent rate constant. Fig. 7b illustrates the pseudo-first-order kinetics data for the photodegradation of RhB using pure SrTiO3 and CQD/SrTiO3 nanocomposite. The apparent rate constants are 0.01006 and 0.00183 min−1 for CQD/SrTiO3 and SrTiO3, respectively. The photocatalytic reaction rate of the CQD/SrTiO3 nanocomposite is about 5.5 times as large as that of pure SrTiO3. These results suggest that the excellent photocatalytic performance of the CQD/SrTiO3 nanocomposite may be attributed to the interaction between the CQDs and SrTiO3. In addition, the TOC analysis for the degradation of RhB by the CQD/SrTiO3 nanocomposite (Fig. S4 in ESI†) shows that after an irradiation of 2 h, about 22% TOC removal is achieved, implying that RhB degradation is accompanied by partial mineralization.
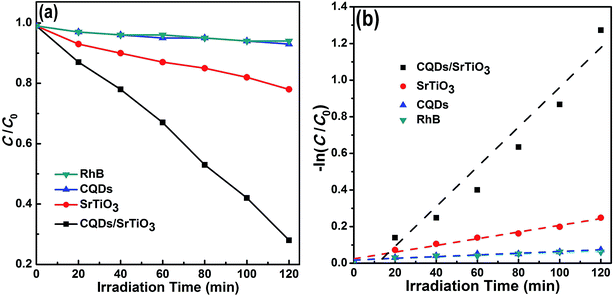 |
| Fig. 7 Photocatalytic degradation of RhB by pure SrTiO3 and CQD/SrTiO3 nanocomposite under sunlight irradiation (a) and the corresponding pseudo-first-order kinetics plot for pure SrTiO3 and CQD/SrTiO3 nanocomposite (b). | |
3.5 Photocatalytic mechanism
In order to understand the enhanced photocatalytic performance of the CQD/SrTiO3 nanocomposite, the photocatalytic mechanism of the CQD/SrTiO3 nanocomposite was analyzed using the EIS and PL spectra. The EIS measurements were usually employed to evaluate the charge transfer resistance and the separation efficiency of the photogenerated e−–h+ pairs.49 In the presence of CQDs, the CQD/SrTiO3 nanocomposite exhibits much lower charge transfer resistance than the pure SrTiO3 which is verified by the significantly reduced diameter of the Nyquist circle in the high frequency region of the EIS patterns shown in Fig. 8a. This clearly indicates that a faster interfacial charge transfer to the electron acceptor occurs and results in an effective separation of the e−–h+ pairs by the introduction of CQDs.50 This would enhance the photocatalytic performance. The CQDs may act as electron acceptor for suppressing charge recombination. In order to further confirm this mechanism, PL spectra of SrTiO3 and the CQD/SrTiO3 nanocomposite were comparatively analyzed. Because the PL emission mainly results from the recombination of free charge carriers, PL is an effective tool to analyze the transfer and recombination processes of photogenerated charge carriers in SrTiO3 and the CQD/SrTiO3 nanocomposite.51 The higher the PL intensity, the greater the probability of the charge carrier recombination.52 The comparison of the PL spectra of pure SrTiO3 and the CQD/SrTiO3 nanocomposite is shown in Fig. 8b. The PL emission intensity of the CQD/SrTiO3 nanocomposite is much lower than that of pure SrTiO3. This indicates that the recombination of the photogenerated e−–h+ pairs is strongly suppressed by the attachment of the CQDs to the SrTiO3 nanoparticles. In other words, photogenerated electrons (e−) in excited SrTiO3 nanoparticles may be injected into the CQDs. This PL analysis result is consistent with the above EIS analysis, which confirms that CQDs can accept the photogenerated e− from SrTiO3 and promote the efficient separation of photogenerated e−–h+ pairs.9,13
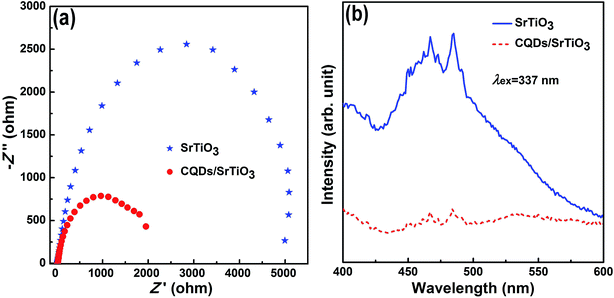 |
| Fig. 8 EIS (a) and room temperature PL (b) spectra of pure SrTiO3 and the CQD/SrTiO3 nanocomposite. | |
In order to more deeply understand the photodegradation mechanism of the CQD/SrTiO3 nanocomposite, the VB and CB edge potentials of SrTiO3 were estimated according to the equations EVB = X − Ee + 0.5 Eg and ECB = EVB − Eg, where X is the electronegativity of the semiconductor, 4.94 eV for SrTiO3,53 Ee the energy of free electrons on the hydrogen scale (about 4.5 eV), and Eg the band gap energy of the semiconductor, 3.16 eV for SrTiO3 (Fig. 5). EVB of SrTiO3 was determined to be 2.02 eV. ECB of SrTiO3 was estimated to be −1.14 eV versus normal hydrogen electrode (NHE). The VB potential of SrTiO3 (2.02 eV) is less positive than E0 (˙OH/OH−) (2.38 eV vs. NHE),54 implying that OH− cannot be oxidized to yield ˙OH by hVB+ of SrTiO3. However, the CB potential of SrTiO3 (−1.14 eV) is much less positive than E0 (O2/˙O2−) (−0.046 eV vs. NHE),55 implying that the photogenerated e− in the CB can reduce O2 to generate ˙O2−. h+ in the VB of SrTiO3 can directly oxidize RhB.56,57 The above analysis indicates that h+ and ˙O2− play an important role in the photodegradation process and ˙OH is not a main reactive species in the photodegradation.
On the basis of the above experimental results, a possible photocatalytic mechanism for the CQD/SrTiO3 nanocomposite is schematically depicted in Fig. 9. When SrTiO3 is irradiated by sunlight, electrons (e−) can be excited from the VB into the CB of SrTiO3 remaining holes (h+) in the VB. Generally, most of the photogenerated e−–h+ pairs quickly recombine and only a small fraction of e− and h+ participates in the photocatalytic reaction. However, when the SrTiO3 nanoparticles is combined with the CQDs to form the CQD/SrTiO3 nanocomposite, the photogenerated e− in the CB of SrTiO3 tend to transfer to the CQDs due to the excellent electron transfer and reservoir properties of the CQDs.2,9 These e− can be shuttled in the special conducting network of the CQDs,58 retarding the recombination of photogenerated e−–h+ pairs at the junction interface. Most e− would accumulate in the CQDs and then combine with O2 to form ˙O2−. The longer-lived h+ in the VB of SrTiO3 can oxidize RhB. So the RhB solution was degraded by the photogenerated h+ and ˙O2−.56,57 Therefore, the introduction of the CQDs (electron acceptor) to the SrTiO3 nanoparticles will facilitate the efficient separation of photogenerated e−–h+ pairs and thus enhance the photocatalytic performance.
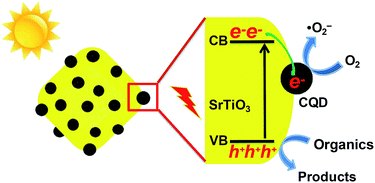 |
| Fig. 9 Schematic of a possible photocatalytic mechanism for the CQD/SrTiO3 nanocomposite under sunlight irradiation. | |
4. Conclusions
A modified acidic oxidation process for the preparation of CQDs from activated carbon was developed by direct evaporation of the residual acid. Using this process, disperse fine spherical amorphous CQDs with an average particle size of 2.7 nm were prepared. The as-prepared CQDs with OCFGs endow them excellent hydrophilicity, facilitating further functionalization and applications. A novel photocatalyst (CQD/SrTiO3) was fabricated by combining the as-prepared CQDs with SrTiO3 nanoparticles through a simple impregnation process. The photocatalytic reaction rate of the CQD/SrTiO3 nanocomposite is about 5.5 as large as that of the pure SrTiO3 nanoparticles in the degradation of RhB under sunlight. The significant enhancement of photocatalytic performance may be ascribed to the improved charge separation efficiency resulted from the presence of CQDs. RhB is degraded by the photogenerated h+ and ˙O2− reduced by the photogenerated e−. This work may open a door to the development of new CQD-based photocatalytic nanocomposites.
Conflicts of interest
There are no conflicts of interest to declare.
Acknowledgements
This work was supported by the National Natural Science Foundation of China (51272098, 51551201, and 51772137).
References
- S. N. Baker and G. A. Baker, Angewandte Chemie, 2010, 49, 6726–6744 CrossRef PubMed.
- H. Li, Z. Kang, Y. Liu and S. T. Lee, J. Mater. Chem., 2012, 22, 24230–24253 RSC.
- F. Yuan, S. Li, Z. Fan, X. Meng, L. Fan and S. Yang, Nano Today, 2016, 11, 565–586 CrossRef.
- S. Zhu, Q. Meng, L. Wang, J. Zhang, Y. Song, H. Jin, K. Zhang, H. Sun, H. Wang and B. Yang, Angewandte Chemie, 2013, 52, 3953–3957 CrossRef PubMed.
- Y. Guo, Y. Chen, F. Cao, L. Wang, Z. Wang and Y. Leng, RSC Adv., 2017, 7, 48386–48393 RSC.
- Y. Song, W. Shi, W. Chen, X. Li and H. Ma, J. Mater. Chem., 2012, 22, 12568–12573 RSC.
- X. Zhang, C. Liu, Z. Li, J. Guo, L. Shen, W. Guo, L. Zhang, S. Ruan and Y. Long, Chem. Eng. J., 2017, 315, 621–629 CrossRef.
- M. Zhang, Z. Fang, X. Zhao, Y. Niu, J. Lou, L. Zhao, Y. Wu, S. Zou, F. Du and Q. Shao, RSC Adv., 2016, 6, 104979–104984 RSC.
- J. Di, J. Xia, Y. Ge, H. Li, H. Ji, H. Xu, Q. Zhang, H. Li and M. Li, Appl. Catal., B, 2015, 168–169, 51–61 CrossRef.
- C. Huang, Y. Hong, X. Yan, L. Xiao, K. Huang, W. Gu, K. Liu and W. Shi, RSC Adv., 2016, 6, 40137–40146 RSC.
- B. Song, T. Wang, H. Sun, Q. Shao, J. Zhao, K. Song, L. Hao, L. Wang and Z. Guo, Dalton Trans., 2017, 46, 15769–15777 RSC.
- J. Di, J. Xia, Y. Huang, M. Ji, W. Fan, Z. Chen and H. Li, Chem. Eng. J., 2016, 302, 334–343 CrossRef.
- H. Zhang, H. Huang, H. Ming, H. Li, L. Zhang, Y. Liu and Z. Kang, J. Mater. Chem., 2012, 22, 10501–10506 RSC.
- D. Tang, H. Zhang, H. Huang, R. Liu, Y. Han, Y. Liu, C. Tong and Z. Kang, Dalton Trans., 2013, 42, 6285–6289 RSC.
- J. Di, J. Xia, M. Ji, H. Li, H. Xu, H. Li and R. Chen, Nanoscale, 2015, 7, 11433–11443 RSC.
- H. Zhang, H. Ming, S. Lian, H. Huang, H. Li, L. Zhang, Y. Liu, Z. Kang and S. T. Lee, Dalton Trans., 2011, 40, 10822–10825 RSC.
- X. Yu, J. Liu, Y. Yu, S. Zuo and B. Li, Carbon, 2014, 68, 718–724 CrossRef.
- H. W. Kang, S. N. Lim and S. B. Park, Int. J. Hydrogen Energy, 2012, 37, 5540–5549 CrossRef.
- S. Tonda, S. Kumar, O. Anjaneyulu and V. Shanke, Phys. Chem. Chem. Phys., 2014, 16, 23819–23828 RSC.
- L. Mu, Y. Zhao, A. Li, S. Wang, Z. Wang, J. Yang, Y. Wang, T. Liu, R. Chen, J. Zhu, F. Fan, R. Li and C. Li, Energy Environ. Sci., 2016, 9, 2463–2469 Search PubMed.
- H. Tan, Z. Zhao, W. Zhu, E. N. Coker, B. Li, M. Zheng, W. Yu, H. Fan and Z. Sun, ACS Appl. Mater. Interfaces, 2014, 6, 19184–19190 Search PubMed.
- H. Peng and J. Travas-Sejdic, Chem. Mater., 2009, 21, 5563–5565 CrossRef.
- H. Li, X. He, Y. Liu, H. Huang, S. Lian, S. T. Lee and Z. Kang, Carbon, 2011, 49, 605–609 CrossRef.
- H. Zhu, X. Wang, Y. Li, Z. Wang, F. Yang and X. Yan, Chem. Commun., 2009, 34, 5118–5120 RSC.
- J. Lu, J. Yang, J. Wang, A. Lim, S. Wang and K. P. Loh, ACS Nano, 2009, 3, 2367–2375 CrossRef PubMed.
- S. Hu, J. Liu, J. Yang, Y. Wang and S. Cao, J. Nanopart. Res., 2011, 13, 7247–7252 CrossRef.
- Y. Deng, D. Zhao, X. Chen, F. Wang, H. Song and D. Shen, Chem. Commun., 2013, 49, 5751–5753 RSC.
- Z. C. Yang, M. Wang, A. M. Yong, S. Y. Wong, X. H. Zhang, H. Tan, A. Y. Chang, X. Li and J. Wang, Chem. Commun., 2011, 47, 11615–11617 RSC.
- J. Wang, C. F. Wang and S. Chen, Angewandte Chemie, 2012, 124, 9431–9435 CrossRef.
- L. Wang, X. Chen, Y. Lu, C. Liu and W. Yang, Carbon, 2015, 94, 472–478 CrossRef.
- M. Wu, Y. Wang, W. Wu, C. Hu, X. Wang, J. Zheng, Z. Li, B. Jiang and J. Qiu, Carbon, 2014, 78, 480–489 CrossRef.
- Y. Su, M. Xie, X. Lu, H. Wei, H. Geng, Z. Yang and Y. Zhang, RSC Adv., 2014, 4, 4839–4842 RSC.
- H. Zhu, X. Wang, Y. Li, Z. Wang, F. Yang and X. Yang, Chem. Commun., 2009, 34, 5118–5120 RSC.
- Y. Liu, Y. Liu, S. J. Park, Y. Zhang, T. Kim, S. Chae, M. Park and H. Y. Kim, J. Mater. Chem. A, 2015, 3, 17747–17754 Search PubMed.
- H. Wang, J. T. Robinson, G. Diankov and H. Dai, J. Am. Chem. Soc., 2010, 132, 3270–3271 CrossRef PubMed.
- Y. Zhu, X. Ji, C. Pan, Q. Sun, W. Song, L. Fang, Q. Chen and C. E. Banks, Energy Environ. Sci., 2013, 6, 3665–3675 Search PubMed.
- H. Bozetine, Q. Wang, A. Barras, M. Li, T. Hadjersi, S. Szunerits and R. Boukherrou, J. Colloid Interface Sci., 2016, 465, 286–294 CrossRef PubMed.
- S. Fuentes, P. Muñoz, N. Barraza, E. Chávez-Ángel and C. M. S. Torres, J. Sol-Gel Sci. Technol., 2015, 75, 593–601 CrossRef.
- Y. Zhang, Z. Zhao, J. Chen, L. Cheng, J. Chang, W. Sheng, C. Hu and S. Cao, Appl. Catal., B, 2015, 165, 715–722 CrossRef.
- Y. Hu, J. Yang, L. Jia and J. S. Yu, Carbon, 2015, 93, 999–1007 CrossRef.
- B. Liu, Y. Huang, Y. Wen, L. Du, W. Zeng, Y. Shi, F. Zhang, G. Zhu, X. Xu and Y. Wang, J. Mater. Chem., 2012, 22, 7484–7491 RSC.
- W. Li, X. Jia, P. Li, B. Zhang, H. Zhang, W. Geng and Q. Zhang, ACS Sustainable Chem. Eng., 2015, 3, 1101–1110 CrossRef.
- H. Li, T. Hu, J. Liu, S. Song, N. Du, R. Zhang and W. Hou, Appl. Catal., B, 2016, 182, 431–438 CrossRef.
- G. Panomsuwan, O. Takai and N. Saito, Phys. Status Solidi A, 2013, 210, 311–319 CrossRef.
- J. Liu, Y. Liu, N. Liu, Y. Han, X. Zhang, H. Huang, Y. Lifshitz, S. T. Lee, J. Zhong and Z. Kang, Science, 2015, 347, 970–974 CrossRef PubMed.
- Y. Q. Zhang, D. K. Ma, Y. G. Zhang, W. Chen and S. M. Huang, Nano Energy, 2013, 2, 545–552 CrossRef.
- H. Li, X. He, Z. Kang, H. Huang, Y. Liu, J. Liu, S. Lian, C. H. A. Tsang, X. Yang and S. T. Lee, Angewandte Chemie, 2010, 49, 4430–4434 CrossRef PubMed.
- S. Zhuo, M. Shao and S. T. Lee, ACS Nano, 2012, 6, 1059–1064 CrossRef PubMed.
- D. Wang, X. Li, J. Chen and X. Tao, Chem. Eng. J., 2012, 198–199, 547–554 CrossRef.
- X. Cao, G. Tian, Y. Chen, J. Zhou, W. Zhou, C. Tian and H. Fu, J. Mater. Chem. A, 2014, 2, 4366–4374 Search PubMed.
- C. Zhao, W. Li, Y. Liang, Y. Tian and Q. Zhang, Appl. Catal., A, 2016, 527, 127–136 CrossRef.
- Z. Zhang, W. Wang, L. Wang and S. Sun, ACS Appl. Mater. Interfaces, 2012, 4, 593–597 Search PubMed.
- J. Zhou, L. Yin, H. Li, Z. Liu, J. Wang, K. Duan, S. Qu, J. Weng and B. Feng, Mater. Sci. Semicond. Process., 2015, 40, 107–116 CrossRef.
- J. Di, J. Xia, Y. Ge, L. Xu, H. Xu, M. He, Q. Zhang and H. Li, J. Mater. Chem. A, 2014, 2, 15864–15874 Search PubMed.
- L. Ye, J. Chen, L. Tian, J. Liu, T. Peng, K. Deng and L. Zan, Appl. Catal., B, 2013, 130–131, 1–7 Search PubMed.
- Q. X. Zeng, G. C. Xu, L. Zhang, H. Lin, Y. Lv and D. Z. Jia, New J. Chem., 2018, 42, 7016–7024 RSC.
- L. Shi, L. Liang, J. Ma, F. Wang and J. Sun, Catal. Sci. Technol., 2014, 4, 758–765 Search PubMed.
- R. Wang, K. Q. Lu, Z. R. Tang and Y. J. Xu, J. Mater. Chem. A, 2017, 5, 3717–3734 Search PubMed.
Footnote |
† Electronic supplementary information (ESI) available. See DOI: 10.1039/c8ra02103a |
|
This journal is © The Royal Society of Chemistry 2018 |
Click here to see how this site uses Cookies. View our privacy policy here.