DOI:
10.1039/C8RA02713G
(Paper)
RSC Adv., 2018,
8, 16013-16018
Preparation of a palygorskite supported KF/CaO catalyst and its application for biodiesel production via transesterification
Received
29th March 2018
, Accepted 23rd April 2018
First published on 30th April 2018
Abstract
This study aimed to explore base catalysts with high transesterification efficiencies to be used for heterogeneous biodiesel production. Palygorskite, a promising low-cost clay mineral, served as a support for KF/CaO to prepare a base catalyst. The base catalyst was prepared via a facile impregnation method and characterized using X-ray diffraction (XRD), scanning electron microscopy (SEM) with energy dispersive spectroscopy (EDS), and N2 adsorption. Subsequently, the prepared catalyst was used for producing biodiesel via the transesterification of commercial soybean oil with methanol. The effects of the catalyst preparation conditions as well as the transesterification parameters, such as the loading amount of KF, calcination temperature, catalyst amount, methanol to oil molar ratio, reaction temperature and water content, on the biodiesel yield were investigated. Results showed that the metal oxide species dispersed on the surface of palygorskite, and the formed KCaF3 was the main active component for the activity of the catalyst. A maximum biodiesel yield of 97.9% was obtained under the optimal conditions. The separated catalyst could be directly used in the next round of reactions and gave a satisfactory yield. The biodiesel yields decreased from 97.9% to 91.3% from the first to the tenth use of the catalyst particles.
Introduction
Due to the exhaustion of fossil resources and the increasing emission of pollutants, many studies are now being directed towards the exploitation of alternative renewable fuel.1 Biodiesel, defined as the monoalkyl esters of fatty acids, has been receiving great attention in recent years as a renewable resource.2,3 The general method for the preparation of biodiesel is the transesterification reaction of vegetable oil or animal fat with methanol or ethanol in the presence of a catalyst.4,5 Conventionally, the transesterification has been carried out with homogeneous bases as the catalysts, such as potassium methoxide and potassium hydroxide, because of their high activity.6–8 However, the use of homogeneous catalysts has many shortcomings, such as the difficulty in product isolation, requirement of large quantities of water, time-consuming nature of the process and environmental pollution from the liquid waste.9–11
In order to circumvent the difficulties with homogeneous catalysts, many studies have been conducted in search of ideal solid catalysts which can be separated from liquid products and reused with or without regeneration.12–14 Recently, some loaded composite catalysts have been developed using supports such as Al2O3,15,16 Fe3O4,17 mesoporous silica,18,19 cinder20 and activated carbon.21,22 Additionally, different kinds of clay, such as zeolite,23 montmorillonite,24 kaolin25 and hydrotalcite,26 have been employed as heterogeneous catalysts or catalyst supports in biodiesel production. To obtain higher conversion, high temperatures or long reaction times, and even high pressures, were needed for the reaction. Therefore, exploring a high efficiency solid base catalyst that achieves a high biodiesel yield in a short time, has a good tolerance for water, and can be used in heterogeneous biodiesel production is still a challenge. In the present paper, one of our aims was to investigate a solid base catalyst which can catalyze transesterification with a high biodiesel yield at a moderate temperature and with a shorter time. Among the solid catalysts, KF/CaO nanocatalysts showed not only high catalytic ability but also high reusability.27,28 It was also demonstrated that the formation of KCaF3 was the main reason for the enhancement of catalytic activity.29–31 This paper aimed to investigate KF/CaO on a natural clay mineral (palygorskite) to prepare solid catalyst particles with high catalytic ability and reusability.
Palygorskite (Pal, formerly called attapulgite, with an ideal formula of (Mg, Al)5Si8O20(OH)2(H2O)4·4H2O) is a form of crystalline hydrated magnesium aluminum silicate mineral with a unique three-dimensional structure, presenting a fibrous morphology with exchangeable cations and reactive –OH groups on its surface.32 Palygorskite is widely used as a catalyst carrier because of its unique structure, special adsorptivity and excellent mechanical resistance. Its natural origin and the low cost make it more attractive.33,34
Here, solid base catalysts were prepared by loading KF and CaO on palygorskite (KCa/Pal) via an impregnation method and this was characterized using X-ray diffraction (XRD), scanning electron microscopy (SEM) with energy dispersive spectroscopy (EDS), and N2 adsorption. Subsequently, the prepared catalyst was used for producing biodiesel via the transesterification of commercial soybean oil with methanol. The effects of the loading amount of KF, calcination temperature, catalyst amount, methanol to oil molar ratio, reaction temperature and water content on the biodiesel yield were investigated to optimize the transesterification conditions. The reusability and stability of the solid catalyst were evaluated using batch experiments.
Experimental
Preparation of the palygorskite-based KF/CaO catalyst
The clay supported catalyst was prepared via a wet impregnation method. 1.0 g CaO and 1.0 g Pal (200 mesh) were immersed in 10 mL KF solution of 0.01–0.05 g mL−1, and this was then magnetically stirred continuously at 25 °C for 3 h and dried at 80 °C for 24 h. After grinding, the resulting product was calcined in a muffle furnace at 300–700 °C for 5 h. The prepared catalyst is denoted KCa/Pal-m (m = 10, 20, 30, 40 and 50), where m represents the mass percent of KF for the total amount of Pal and CaO, and Ca/Pal denotes the sample without KF.35
Characterization of the as-prepared catalyst
X-ray diffraction (XRD) patterns of the catalysts were obtained using a Rigaku ULTIMA IV diffractometer with high-intensity Cu/Kα radiation and a step scan technique at 2θ angles of 5–90°. The surface morphology of the catalyst was investigated using a JEOL JEM-2100 scanning electron microscope (SEM). Energy dispersive spectroscopy (EDS) was used to conduct the elemental analysis. The Brunauer–Emmett–Teller (BET) method was utilized to measure the specific surface area and pore volume of the catalysts by means of Accelerated Surface Area and Porosity (ASAP 2010, Micromeritics). The pore-size distribution was assessed using the adsorption branch of the isotherm with the Barrett–Joyner–Halenda (BJH) method.
Transesterification reaction
The transesterification reactions were carried out in a 250 mL three-necked flask. The reaction procedure was as follows: first, the soybean oil was added to the flask. Methanol and the catalyst were mixed and then added to the flask. A reflux reaction was performed at the indicated temperature. After that, the catalyst and glycerol were isolated. Methanol was isolated from the biodiesel using a rotary evaporator. The concentrated biodiesel was collected for chromatographic analysis with a heating speed of 10 °C min−1, initial temperature of 160 °C, ultimate temperature of 230 °C, injector temperature of 250 °C and detector temperature of 250 °C.36 The biodiesel yield was obtained according to the reported method.37
Results and discussion
X-ray diffraction of the samples
Fig. 1 depicts the XRD patterns of Pal, Ca/Pal and KCa/Pa-x calcined at 500 °C. As shown in Fig. 1a, for Pal, the reflections positioned at 8.3°, 13.9°, 19.9° and 24.5° correspond to crystalline Pal and those at 20.8° and 26.5° are assigned to crystalline quartz.38 Fig. 1b shows the XRD patterns of Ca/Pal and the diffraction peaks of Pal are still present. The peaks at 17.9°, 29.1°, 36.3°, 47.1° and 54.8° are assigned to the diffraction peaks of Ca(OH)2.39 The peaks at 32.3°, 37.4° and 53.9° imply that there was the crystal phase of CaO present.40 Fig. 1c–g show the XRD patterns of KCa/Pa-x with different KF load ratios to CaO. Accompanied with the increasing mass ratio of KF, the peaks at 20.7°, 29.0°, 35.1°, 41.2°, 46.7°, 54.8° and 59.5° emerged and were enhanced while the characteristic peaks of Ca(OH)2 and CaO declined. Compared with the standard patterns, the new peaks should belong to the phase of KCaF3.41 In conclusion, the addition of KF led to the formation of KCaF3, which can improve the activity of the catalyst, and increase the ability to resist the saponification reaction.42,43 However, when the loading amount of KF was 50 wt%, a diffraction peak at 34.1° corresponding to KF was clearly observed, which may have resulted from excess KF dispersing on the surface of the catalyst.44
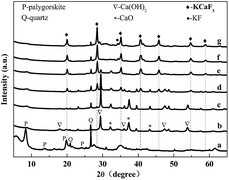 |
| Fig. 1 XRD patterns of Pal (a), Ca/Pal (b), and KCa/Pal-m (c–g), where m = 10, 20, 30, 40 and 50, respectively. | |
Surface morphology of the samples
The morphologies of Pal and KCa/Pal-40, characterized using SEM, are shown in Fig. 2. It can be clearly seen from Fig. 2a that Pal exhibits a fibrous structure and some fibers form straight parallel aggregates. The SEM image of KCa/Pal-40 in Fig. 2b is obviously different to that of Pal. After loading CaO and KF, the surface of the KCa/Pal composite was rugged and full of many fragment-like protruding objects. Combined with the results of XRD, the fragments could be ascribed to the crystals of KCaF3. Moreover, the corresponding EDS spectrum of the KCa/Pal-40 composite is displayed in Fig. 2c, showing that the detectable elements include K, Ca and F, indicating that K, Ca and F were successfully deposited on Pal under these synthesis conditions.
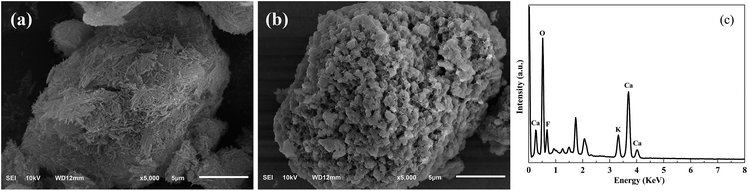 |
| Fig. 2 SEM images of Pal (a) and KCa/Pal-40 (b), and an EDS spectrum of KCa/Pal-40 (c). | |
N2 adsorption–desorption
The nitrogen adsorption/desorption isotherms for Pal and KCa/Pal-40 are shown in Fig. 3. Both samples are found to have typical IV isotherm curves which contain a hysteresis between the adsorption and desorption curves at relative pressures (P/P0) ranging from 0.4 to 0.9, suggesting that mesopores exist in Pal and KCa/Pal-40. The BET surface area, pore volume, and average pore size of Pal and KCa/Pal-40 are summarized in Table 1. Pal had a BET surface area of 107.2 m2 g−1, while after composite formation with KF and CaO, the BET surface area fell to 5.59 m2 g−1. The pore volumes of Pal and the KCa/Pal-40 composite are 0.34 m3 g−1 and 0.03 m3 g−1, respectively. The main pore size distribution centers at 13.47 nm for the Pal sample and 20.37 nm for KCa/Pal-40. The decrease of the specific surface area and pore volume as well as the increase of the average pore size is clearly visible, indicating the clay is successfully covered with the introduced metal oxide species and the micropores are partially blocked.45 Meanwhile, the large mesopores and surface area of Pal are beneficial to the formation of active sites, providing good catalytic activity for biodiesel synthesis.
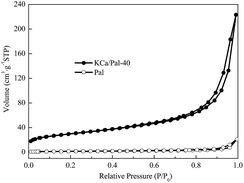 |
| Fig. 3 N2 adsorption–desorption isotherms of Pal and KCa/Pal-40. | |
Table 1 Physical properties of Pal and KCa/Pal-40
Sample |
BET surface area (m2 g−1) |
Total pore volume (m3 g−1) |
Average pore size (nm) |
Pal |
107.2 |
0.34 |
13.47 |
KCa/Pal-40 |
5.59 |
0.03 |
20.37 |
Transesterification
Influence of preparation conditions on catalytic activity
To investigate the influence of KF loading on the catalytic activity, a series of catalysts were prepared with different KF loadings (all samples were calcined at 500 °C for 5 h). Table 2 shows the results regarding the effect of KF loading on the catalytic activity. The biodiesel yield is improved from 51.3% to 95.7% when the KF loading increases from 10 wt% to 40 wt%. It can be assumed from these results that the number of active sites on the catalyst surface increases with increasing the loading of KF. When the KF loading is beyond 40 wt%, however, the activity of the catalyst decreased with increased loading of KF, and the biodiesel yield is only 84.3% at 50 wt% KF loading. This is probably due to the fact that the excessive KF covers the active sites of the catalyst surface, resulting in the decrease of catalytic activity.46 Therefore, the optimum loading of KF is 40 wt% in this study.
Table 2 Effect of the mass percent of KF on the biodiesel yielda
Catalyst |
Basicity (mmol g−1) |
Biodiesel (%) |
Transesterification conditions: a molar ratio of methanol to oil of 12 : 1, the catalyst 3 wt% of the oil, a temperature of 65 °C, a reaction time of 2.5 h and the water 2.5 wt% of the oil. |
KCa/Pal-10 |
0.34 |
51.3 |
KCa/Pal-20 |
0.41 |
78.2 |
KCa/Pal-30 |
0.57 |
84.5 |
KCa/Pal-40 |
0.71 |
95.7 |
KCa/Pal-50 |
0.62 |
82.1 |
Another important parameter to be optimized is the calcination temperature. In the preparation process for the catalyst, calcination treatment of the catalyst at a high temperature is favorable for the interaction between the support and active ingredient, which generates new active sites for the catalyst. Therefore, the calcination temperature is crucial for increasing the catalytic activity. Fig. 4 shows the results concerning the influence of the calcination temperature on the catalytic activity of KCa/Pal-40. Clearly, the biodiesel yield initially increases with the increase of calcination temperature. Then, the yield reaches a maximum value at a calcination temperature of 500 °C. However, the biodiesel yield decreases gradually with further increase of the calcination temperature. This is probably due to the fact that overheating results in surface sintering and a reduction of the specific surface area, which in turn leads to a decrease in the catalytic activity.42 The current results indicate that the optimal calcination temperature is 500 °C.
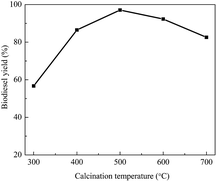 |
| Fig. 4 Effect of calcination temperature on biodiesel yield. Transesterification conditions: a molar ratio of methanol to oil of 12 : 1, the catalyst 3 wt% of the oil, a temperature of 65 °C, a reaction time of 2.5 h and the water 2.5 wt% of the oil. | |
Influence of reaction parameters on the biodiesel yield
The effect of the molar ratio of methanol to soybean oil on the transesterification was investigated. As illustrated in Fig. 5, with an increase in the methanol/oil molar ratio, the biodiesel yield increased rapidly and reached a high value at a methanol/oil molar ratio of 12
:
1. When the methanol/oil molar ratio was more than 12
:
1, the increase of the biodiesel yield was not significant. Therefore, to guarantee the biodiesel quality, the optimal methanol/oil molar ratio of 12
:
1 was selected for the further research.
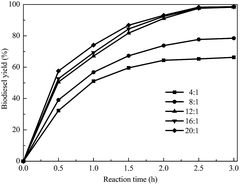 |
| Fig. 5 Effect of molar ratio of methanol to soybean oil. Transesterification conditions: the catalyst 3 wt% of the oil, a temperature of 65 °C, a reaction time of 2.5 h and the water 2.5 wt% of the oil. | |
The usage of the catalyst can be beneficial to obtain a high product yield in a relatively short reaction time. However, an excessive amount of catalyst leads to an increase of the viscosity of the reaction system and causes a problem with mixing as well as a demand for higher power consumption for adequate stirring. To overcome this kind of problem, the appropriate amount of catalyst had to be investigated. As shown in Fig. 6, the biodiesel yield was greatly increased by increasing the amount of catalyst from 1 to 3 wt% by weight of oil. However, as the catalyst dosage was continuously increased, the biodiesel yield improved slightly. This means that an excess amount of catalyst could not further promote the yield because the reaction had reached equilibrium. So, the amount of catalyst was chosen to be 3 wt% by weight of oil for our studies.
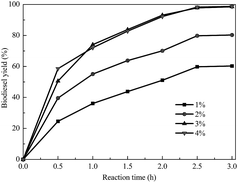 |
| Fig. 6 Effect of catalyst usage on biodiesel yield. Transesterification conditions: a molar ratio of methanol to oil of 12 : 1, a temperature of 65 °C, a reaction time of 2.5 h and the water 2.5 wt% of the oil. | |
In addition, the effect of temperature on biodiesel yield was examined. Fig. 7 shows that the biodiesel yield significantly increased from 50 °C to 65 °C. From Fig. 7, it can be seen that the biodiesel yield significantly increased from 50 °C to 65 °C, and the highest yield was at 65 °C. However, the yield decreased when the temperature was higher than 65 °C. This is mainly because the evaporation of methanol reduces the contact time between methanol and oil, resulting in a lower biodiesel yield.47
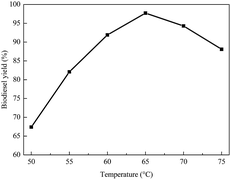 |
| Fig. 7 Effect of reaction temperature on biodiesel yield. Transesterification conditions: a molar ratio of methanol to oil of 12 : 1, the catalyst 3 wt% of the oil, a reaction time of 2.5 h and the water 2.5 wt% of the oil. | |
In the transesterification of soybean oil to biodiesel catalyzed by a solid base, the biodiesel yield is greatly affected by water. Fig. 8 shows the application of soybean oils containing various amounts of water for biodiesel synthesis catalyzed by KCa/Pal-40. The yield of biodiesel is increased from 89.3% to 97.9% when the water content increases from 0 to 2.5 wt% of soybean oil. This is probably due to the fact that water molecules are adsorbed first on the surface of the catalyst to form OH−. Then, the surface OH− abstracts a proton from methanol to generate CH3O−. Certainly, the catalyst can also abstract H+ from methanol to form CH3O−. But OH− is more easily adsorbed on the catalyst surface than CH3O−.37 When the water content is beyond 2.5 wt%, the biodiesel yield decreases with the increase of water content. Therefore, the water content in oil should be kept under 2.5 wt% to prevent catalyst deterioration and biodiesel hydrolysis.
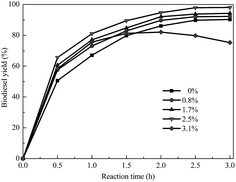 |
| Fig. 8 Effect of water content on biodiesel yield. Transesterification conditions: a molar ratio of methanol to oil of 12 : 1, the catalyst 3 wt% of the oil, a temperature of 65 °C and a reaction time of 2.5 h. | |
Reusability of the catalyst
From an economic point of view, the reusability of the catalyst is of great importance for industrial applications. After the reaction had completed, the catalyst was separated from the reaction mixture using only simple centrifugation or filtration to investigate its lifetime and stability. Prior to each reaction, the same amount of fresh commercial soybean oil and methanol were added, and the same reaction conditions were used. Fig. 9 shows the effect of repeated use of the KCa/Pal-40 and KF/CaO catalysts on the transesterification reaction. It is found that the biodiesel yield for the reaction catalyzed with KF/CaO was 75.6% after 10 cycles of reuse. However, the KCa/Pal-40 catalyzed synthesis of biodiesel still produced a yield in excess of 91.3% after being reused for the same number of times. Therefore, KCa/Pal-40 can contribute much to decreasing the cost of biodiesel production due to its long catalyst lifetime and short reaction time.
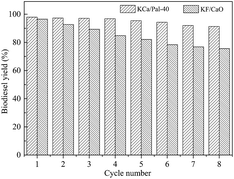 |
| Fig. 9 Reusability and recovery of KCa/Pal-40 and KF/CaO. Transesterification conditions: a molar ratio of methanol to oil of 12 : 1, the catalyst 3 wt% of the oil, a temperature of 65 °C, a reaction time of 2.5 h and the water 2.5 wt% of the oil. | |
Conclusion
In the present work, a solid basic catalyst, KCa/Pal, was used to catalyze the transesterification of soybean oil with methanol to produce biodiesel. It is demonstrated that the KCa/Pal catalyst exhibits high catalytic activity in the transesterification reaction. When the reaction was carried out under reflux with methanol, with a molar ratio of methanol to soybean oil of 12
:
1, the biodiesel yield catalyzed by 3% catalyst (based on the weight of soybean oil) reached 97.9% in 2.5 h at 65 °C. The catalyst is promising for use in the continuous production of biodiesel. According to the results of catalyst characterization, the formed KCaF3 should be the main active component for the catalytic activity. Meanwhile, the catalyst exhibited relatively good reusability. The biodiesel yield remained at 91.3% over the 10 times the catalyst was used.
Conflicts of interest
There are no conflicts to declare.
Acknowledgements
We acknowledge the support of the Scientific Research Foundation for Doctoral Teachers of Nantong College of Science and Technology (NTKY-Dr2015002) and Qing Lan Project of Jiangsu Province (2017).
Notes and references
- C. C. C. M. Silva, N. F. P. Ribeiro, M. M. V. M. Souza and D. A. G. Aranda, Fuel Process. Technol., 2010, 2, 205–210 CrossRef.
- A. Datta and B. K. Mandal, Renew. Sustain. Energy Rev., 2016, 57, 799–821 CrossRef CAS.
- Y. C. Sharma, B. Singh and S. N. Upadhyay, Fuel, 2008, 12, 2355–2373 CrossRef.
- S. T. Keera, S. M. E. Sabagh and A. R. Taman, Fuel, 2011, 1, 42–47 CrossRef.
- E. Anderson, M. Addy, Q. Xie, H. Ma, Y. Liu and Y. Cheng, Bioresour. Technol., 2016, 200, 153–160 CrossRef CAS PubMed.
- K. G. Georgogianni, A. K. Katsoulidis, P. J. Pomonis, G. Manos and M. G. Kontominas, Fuel Process. Technol., 2009, 7–8, 1016–1022 CrossRef.
- M. Agarwal, G. Chauhan, S. P. Chaurasia and K. Singh, J. Taiwan Inst. Chem. Eng., 2012, 1, 89–94 CrossRef.
- A. Aliyu, E. Lomsahaka and A. Hamza, Adv. Appl. Sci. Res., 2012, 1, 615–618 Search PubMed.
- J. Zhang, S. Chen, Y. Rui and Y. Yan, Fuel, 2010, 10, 2939–2944 CrossRef.
- M. Kouzu and J. S. Hidaka, Fuel, 2012, 1, 1–12 CrossRef.
- L. Cui, G. Xiao, X. Bo and G. Teng, Energy Fuels, 2007, 6, 3740–3743 Search PubMed.
- W. Li, D. Ma, S. Yao, Y. Gao and N. Yan, Green Chem., 2015, 17(15), 4198–4205 RSC.
- K. Sun, A. R. Wilson, S. T. Thompson and H. H. Lamb, ACS Catal., 2015, 5(16), 1939–1948 CrossRef CAS.
- J. A. Botas, D. P. Serrano, A. García and R. Ramos, Appl. Catal., B, 2014, 145, 205–215 CrossRef CAS.
- Y. Tang, H. Ren, F. Chang, X. Gu and J. Zhang, RSC Adv., 2017, 10, 5694–5700 RSC.
- D. M. Marinkovic, J. M. Avranović, M. V. Stanković, O. S. Stamenković, D. M. Jovanović and V. B. Veljković, Energy Convers. Manage., 2017, 144, 399–413 CrossRef CAS.
- A. M. Tamilmagan and A. G. Priyabijesh, Int. J. ChemTech Res., 2015, 5, 90–96 Search PubMed.
- Y. Chen, J. Han and H. Zhang, Appl. Surf. Sci., 2008, 18, 5967–5974 CrossRef.
- C. Samart, C. Chaiya and P. Reubroycharoen, Energy Convers. Manage., 2010, 7, 1428–1431 CrossRef.
- H. Liu, L. Su, F. Liu, C. Li and U. U. Solomon, Appl. Catal., B, 2011, 3, 550–558 CrossRef.
- A. Buasri, B. Ksapabutr, M. Panapoy and N. Chaiyut, Korean J. Chem. Eng., 2012, 12, 1708–1712 CrossRef.
- S. Baroutian, M. K. Aroua, A. A. Raman and N. M. Sulaiman, Bioresour. Technol., 2011, 2, 1095–1102 CrossRef PubMed.
- H. Wu, J. Zhang, Q. Wei, J. Zheng and J. Zhang, Fuel Process. Technol., 2013, 9, 13–18 CrossRef.
- M. A. F. Othman, BMC Cell Biol., 2015, 6, 759 Search PubMed.
- T. H. Dang, B. H. Chen and L. Duujong, Bioresour. Technol., 2013, 4, 175–181 CrossRef PubMed.
- G. Lee, Y. K. Ji, Y. Ning, Y. W. Suh and C. J. Ji, J. Mol. Catal. A: Chem., 2016, 423(27), 347–355 CrossRef CAS.
- W. Yun, S. Y. Hu, Y. P. Guan, L. B. Wen and H. Y. Han, Catal. Lett., 2009, 3–4, 574–578 Search PubMed.
- S. Hu, L. Wen, Y. Wang, X. Zheng and H. Han, Bioresour. Technol., 2012, 3, 413–418 CrossRef PubMed.
- L. Gao, G. Teng, G. Xiao and R. Wei, Biomass Bioenergy, 2010, 9, 1283–1288 CrossRef.
- H. Liu, L. Su, Y. Shao and L. Zou, Fuel, 2012, 7, 651–657 CrossRef.
- J. Chen, L. Jia, X. Guo, L. Xiang and S. Lou, RSC Adv., 2014, 104, 60025–60033 RSC.
- Y. Li, J. C. Hu and P. F. Han, Chin. J. Chem. Eng., 2015, 5, 822–826 CrossRef.
- A. Xue, S. Zhou, Y. Zhao, X. Lu and P. Han, J. Hazard. Mater., 2011, 5, 7–14 CrossRef PubMed.
- J. Huang, Y. Liu and X. Wang, J. Mol. Catal. B: Enzym., 2009, 1, 10–15 CrossRef.
- L. Jia, Y. Li, J. Chen, X. Guo, S. Lou and H. Duan, Res. Chem. Intermed., 2015, 3, 1–17 Search PubMed.
- X. Chen, W. W. Qian, X. P. Lu and P. F. Han, Nat. Prod. Res., 2012, 13, 1249–1256 CrossRef PubMed.
- X. Liu, H. He, Y. Wang, S. Zhu and X. Piao, Fuel, 2008, 2, 216–221 CrossRef.
- K. C. M. Xavier, M. D. S. F. D. Santos, M. R. M. C. Santos, M. E. R. Oliveira, M. W. N. C. Carvalho, J. A. Osajima, E. C. D. Silva Filho, J. A. Osajima and E. C. D. Silva Filho, Mater. Res., 2014, 8, 3–8 CrossRef.
- N. Asikin Mijan, H. V. Lee and Y. H. Taufiq Yap, Chem. Eng. Res. Des., 2015, 102, 368–377 CrossRef CAS.
- G. Moradi, M. Mohadesi and Z. Hojabri, React. Kinet. Mech. Catal., 2014, 1, 169–186 CrossRef.
- M. Kaur and A. Ali, Eur. J. Lipid Sci. Technol., 2014, 1, 80–88 CrossRef.
- S. Hu, Y. Guan, Y. Wang and H. Han, Appl. Energy, 2011, 8, 2685–2690 CrossRef.
- M. Kouzu, T. Kasuno, M. Tajika, Y. Sugimoto, S. Yamanaka and J. Hidaka, Fuel, 2008, 12, 2798–2806 CrossRef.
- L. Gao, X. Bo, G. Xiao and J. Lv, Energy Fuels, 2008, 5, 3531–3535 CrossRef.
- J. J. Li, Z. Mu, X. Y. Xu, H. Tian, M. H. Duan and L. D. Li, Microporous Mesoporous Mater., 2008, 1, 214–221 CrossRef.
- C. Sun, F. Qiu, D. Yang and B. Ye, Fuel Process. Technol., 2011, 126, 383–391 CrossRef.
- L. Wen, Y. Wang, D. Lu, S. Hu and H. Han, Fuel, 2010, 9, 2267–2271 CrossRef.
|
This journal is © The Royal Society of Chemistry 2018 |
Click here to see how this site uses Cookies. View our privacy policy here.