DOI:
10.1039/C8RA06984K
(Paper)
RSC Adv., 2018,
8, 31979-31983
One-pot synthesis of cup-like ZSM-5 zeolite and its excellent oxidative desulfurization performance†
Received
21st August 2018
, Accepted 7th September 2018
First published on 13th September 2018
Abstract
A one-step method to synthesize small size cup-like hollow ZSM-5 single crystals is reported in this paper. Characterization methods show that the product has a typical ZSM-5 structure and most crystals are uniform, mono dispersed crystal shells with distinct hollow structure. The average size of a single crystal is about 350 nm. Every cup-like hollow ZSM-5 crystal can act as a microreactor in the reaction, and the ZSM-5 based catalyst POM-MOF-ZSM-5 (polyoxometalates (POM), metal–organic frameworks (MOF)) shows excellent oxidative desulfurization performance of DBT (dibenzothiophene).
1 Introduction
Zeolites are widely used in industry as heterogeneous catalysts and especially in oil refining and petrochemistry as solid acid catalysts.1 However, zeolites have diffusional limitations which bring lots of problems such as decrease in reaction rate and deactivation.2,3 Decreasing the diffusion length in the zeolite crystals is a way to alleviate molecular transport problems. But their synthesis is not always easy. Therefore, to create an additional array in zeolites, fabrication of zeolite molecular sieves with mono-crystalline hollow structures attracts wide attention.4,5 In hollow structure zeolites, guest molecules only stay in the zeolites for a short amount of time, thus improving the mass transfer efficiency.6–9 In addition, small size crystal molecular sieves have larger specific surface area, shorter pore channels, abundant surface acid sites compared to big size crystal molecular sieves.7 Therefore, small size crystal molecular sieves are more stable, more active and more selective, and they have shown excellent catalytic performance in many critical catalytic reactions.9,10 Besides, the large internal cavity of hollow structure zeolites can encapsulate catalyst and be used as a micro reactor. Compared to polycrystalline hollow zeolites, hollow single crystals are generally defect-free and homogeneous, which make it perfectly adapted for the encapsulation of catalysts.11 They also have the potential application as biomedical and pharmaceutical vectors for controlled drug delivery.
Currently, there are only limited reports on hollow, single crystal ZSM-5 zeolite molecular sieves. These reports are mainly focused on MFI molecular sieves12–17 due to their excellent pore channel structure, thermo stability and thus vast potential in many catalytic reactions.
One method of synthesizing hollow ZSM-5 crystals includes two steps. Firstly, they manufactured conventional ZSM-5 molecular sieves grain crystal, and then treated the solid crystals with acidic or basic solutions for dealumination or desilication. Finally, they did recrystallization to obtain some hollow zeolite molecular sieves.12–19 Mei and colleagues20 treated 350 nm ZSM-5 molecular sieves with 0.6 M Na2CO3 to obtain small-sized hollow ZSM-5 crystal. Fodor et al.21 first synthesized nanoscale ZSM-5 molecular sieves, and obtained nanoscale hollow ZSM-5 molecular sieves by first corroding with 0.1 M sodium hydroxide and then washed with 0.1 M hydrochloric acid.
Another method to synthesize hollow ZSM-5 crystals is the addition of the hard templates or soft templates. During the synthesis, carbon nanoparticles or some polymer beads was used as hard templates.22–24 Jacobsen et al.25 used excess of a zeolite gel to grow around carbon particles of the inert matrix within the whole pore system. After the combustion in air, the carbon particles were removed and the mesoporous zeolite single crystals were obtained. Zhao et al.26 reported the fabrication of mesoporous zeolite with a hollow capsule structure by using conventional TPAOH and surfactant (CTAB) as soft micro- and mesopore generation templates through controlled hydrolysis.
The aforementioned reports regarding synthesizing hollow zeolite molecular sieves all have relatively complex synthesis process, and need further treatment to obtain somewhat hollow molecular sieves. These process is time and energy consuming, and potentially harmful for the environment. Therefore, seeking a simple, single-step method for synthesizing small crystal hollow ZSM-5 zeolite molecular sieves remains a challenge.
This article introduces a one-step, simple method for directly synthesizing hollow, small-sized single crystal ZSM-5 zeolite. It has cup-like structure and the uniform shell is dozens of nanometers. The cavity can encapsulate catalyst, and act as a microreactor. Therefore, the catalyst POM-MOF-ZSM-5 was prepared, which shows excellent oxidative desulfurization performance of DBT and huge potential in the desulfurization of the oil.
2 Results and discussion
2.1 Synthesis and characterization
We mixed sodium metaaluminate, tetraethoxysilane (TEOS), tetrapropylammonium hydroxide (TPAOH) and water in a certain order until the mixture is uniform. The mixture was put in crystallization reactor and crystallized under certain temperature for 12 to 48 hours. Then the products was filtered, washed, and dried to obtain small-sized hollow ZSM-5 molecular sieves. Finally, the sample was converted into H-ZSM-5 through ion exchanges with NH4NO3 solution at 90 °C for three times and calcinated at 550 °C for 5 h.
Both XRD and IR results show that the synthesized hollow molecular sieves (crystallization temperature 130 °C, crystallization time 48 h, OH−/SiO2 = 0.3) have the framework structure of ZSM-5 (Fig. 1). The overall graphs exhibit no impure crystal peaks and no incompletely crystallized amorphous plastic materials. The three NH3 desorption peaks of the NH3-TPD infers the existence of the three kinds of acids, weak acid, mediate strong acid and strong acid (Fig. S1†). The XPS of the catalyst gives the information about the chemical state (Fig. S2†). The binding energy peaks of C, O, Si, Al are easy to be confirmed in the survey spectrum. The nitrogen adsorption–desorption isotherms of the cup-like ZSM-5 zeolite exhibits the type II isotherms and proves the existence of the large pores (Fig. S3†).
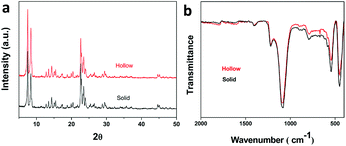 |
| Fig. 1 XRD and IR of regular solid and hollow ZSM-5 molecular sieves. (a) XRD. (b) IR. | |
Nextly, we evaluated the SEM and TEM results of the synthesized hollow ZSM-5 (Fig. 2b and d) comparing to regular, solid ZSM-5 sample (Fig. 2a and c). From SEM (Fig. 2b), it is seen that the crystals are hollow and the size of zeolite particle is about 350 nm. From TEM, ZSM-5 sample in Fig. 2c are opaque and non-transparent; whereas the crystals in Fig. 2d are transparent and thus show typical hollow cup-like structure, whose shell thickness is dozens of nanometers. Therefore, this method of synthesis yields hollow zeolite single crystals. In addition, the resulted molecular sieves have uniform shell thickness and well ordered pore channel structure. From elemental mapping images of an individual ZSM-5 crystal (Fig. 2e), the shell of the ZSM-5 crystal is mainly formed by silicon and oxygen, together with a little amount of aluminum. It is believed that the cup-like structure can be used as a microreactor in reactions.
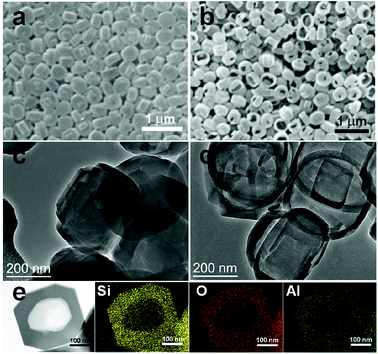 |
| Fig. 2 SEM (a and b) and TEM (c and d) of synthesized zeolites. (a and c) Regular, solid ZSM-5. (b and d) Hollow ZSM-5. (e) Elemental mapping images of an individual ZSM-5 crystal. | |
2.2 Key influence factors in synthesizing hollow ZSM-5 zeolites
2.2.1 The effect of crystallization time. Fig. 3 is the SEM image of ZSM-5 molecular sieves samplent crystallization time, while holding all other parameters constant. Clearly, crystallization time has critical influence on forming ZSM-5 molecular sieves. When crystallized for 12 h or 24 h, the resulted product was solid ZSM-5 crystal. When the crystallization time prolonged to 36 hours, some of the synthesized ZSM-5 particles became hollow. When it was crystallized for 48 hours, the resulted crystals were mostly hollow ZSM-5. Therefore, it is concluded that long crystallization time is beneficial for forming hollow ZSM-5. We further deduce that the synthesis process involves first forming solid ZSM-5 crystals, then converting to hollow crystals under the corrosion of bases present in the system.
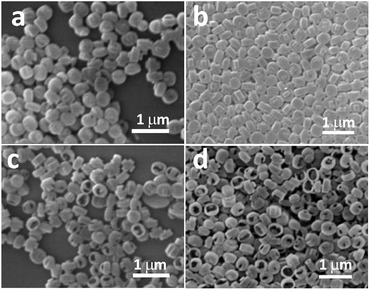 |
| Fig. 3 SEM of synthesized ZSM-5 with different crystallization time (130 °C, OH−/SiO2 = 0.3). (a) 12 h, (b) 24 h, (c) 36 h, (d) 48 h. | |
2.2.2 The effect of synthetic basicity. Fig. 4 is the SEM image of synthesized ZSM-5 with different synthetic fluid basicity. The picture shows that when the synthetic system was less basic (OH−/SiO2 = 0.17), the synthesized molecular sieves were solid ZSM-5 particles with relatively big particle diameters. When the basicity increased (OH−/SiO2 = 0.4), the resulted zeolite crystals were mostly hollow ZSM-5 with uniform particle diameters and similar shapes. Therefore, high basicity is a favorable condition for forming hollow ZSM-5 crystals.
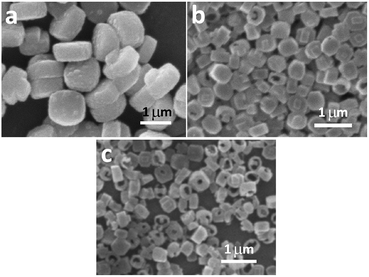 |
| Fig. 4 SEM of ZSM-5 with different basicity while crystallized for 48 h under 170 °C. (a) OH−/SiO2 = 0.17; (b) OH−/SiO2 = 0.3; (c) OH−/SiO2 = 0.4. | |
2.2.3 The effect of crystallization temperature. The SEM image of synthesized ZSM-5 with different crystallization temperature is shown in Fig. 5. There was no hollow ZAM-5 crystals when the crystallization time was 100 °C. And there was very little hollow ZSM-5 among the solid ones crystallized at 130 °C. Whereas at 170 °C, the synthesized ZSM-5 crystals were mostly hollow. Therefore, high crystallization temperature is favorable for hollow ZSM-5 formation.
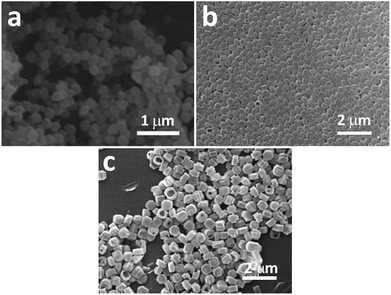 |
| Fig. 5 SEM of ZSM-5 under different crystallization temperature (OH−/SiO2 = 0.3, crystallized for 24 h). (a) 100 °C, (b) 130 °C, (c) 170 °C. | |
2.3 Discussion on the mechanism of hollow ZSM-5 formation
As discussed in the previous section, long crystallization time, high crystallization temperature and high system basicity are all favorable conditions for forming hollow ZSM-5 crystals. Therefore, we deduce that there are two steps in this synthetic process: first the crystallization of regular solid ZSM-5 crystals; then the corrosion of these solid crystals under basic conditions. As the crystallization time increases, the crystal growth slows down and the corrosion speeds up.
This deduced mechanism is consistent with our observations. When crystallized for only 24 hours, the ZSM-5 crystals were mostly solid. It is suggested that the early synthetic environment favours the formation of zeolite crystals and the corrosion is weak. When crystallized for 36 hours and even 48 hours, it was observed that the particle diameter of zeolite crystals remained constant, while more and more crystals became hollow. It is indicated that after 24 hours, the synthetic environment does not support crystal growth but favours corroding zeolite crystals.
When crystallized for a longer time (48 hours) under low system basicity (Fig. 4a), the zeolite crystals were mostly solid and the crystals have clearly grown to about 1 μm. It is indicated that low system basicity is beneficial for zeolite crystal growth, not basic corrosion of crystals.
This one-step synthetic method for single crystal hollow ZSM-5 zeolites has similar mechanism as the previously reported two-step methods.6,8,10 The key in the single-step synthesis is the coordination between different parameters. In the same synthetic system, the zeolite crystals grow in the earlier stage. Afterwards the crystals are corroded to form molecular sieves with hollow structures.
2.4 Oxidative desulfurization performance of POM-MOF-ZSM-5
In earlier report, a catalyst system was designed by a kind of hybrid material POM@MOF-199@MCM-41 (PMM). It was fabricated through a one pot and POM template self-construction of MOF-199 in the pore of MCM-41.27 This catalyst was used for the direct oxidative desulfurization process of model oil. In our work, we used hollow ZSM-5 instead of MCM-41 to obtain the catalyst, which gave excellent desulfurization performance.
ZSM-5 was added into polyoxometalates (POMs) PMo12O40·nH2O solution, then metal–organic frameworks (MOFs) MOF-199 was added in. The mixture was refluxed overnight, filtered and dried to obtain the catalyst POM-MOF-ZSM-5. We prepared POM-MOF-MCM-41 in the similar way.
DBT was dissolved in octane to obtain model diesel. The oxidative desulfurization experiment was carried out in a 100 mL three-neck flask connected with a pump to share oxygen. In every run, a certain amount of catalyst was added and stirred. Then 1 mL reactant solution was collected and centrifuged, and injected in gas chromatograph to calculate the desulfurization rate, following the equation below (η is the conversion rate, and C0 and C is the initial and final concentration of S-compounds respectively):
Desulfurization performances of different catalysts were shown in Table 1. The desulfurization rate of ZSM-5 and POM-MOF-MCM-41 was only 21.2%, 83.5% respectively, while the value of POM-MOF-ZSM-5 reached 91.2%. In Fig. 6, after 180 min, the oxidative desulfurization rate increased in the order of ZSM-5 < POM-MOF-MCM-41 < POM-MOF-ZSM-5. The reactivity of POM-MOF-ZSM-5 is the best, for the more firmly and uniformly fixation of heteropolyacid in MOF-199, after dispersed homogeneously in the hollow ZSM-5 zeolites. More detailed results will be reported later.
Table 1 Desulfurization performance of different catalysts
Catalyst |
DBT conversion (%) |
ZSM-5 |
21.2% |
POM-MOF-MCM-41 |
83.5% |
POM-MOF-ZSM-5 |
91.2% |
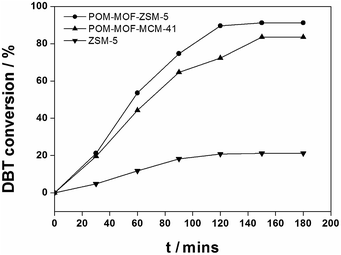 |
| Fig. 6 The desulfurization result of ZSM-5, POM-MOF-MCM-41 and POM-MOF-ZSM-5. | |
3 Conclusions
This single-step, hydrothermal synthesis method yielded highly crystallized small size cup-like ZSM-5 crystal with uniform shell thickness and well-ordered pore channels. The resulted zeolite crystals are mono dispersed, highly crystallized. These zeolite crystals have uniform particle diameters (approximately 350 nm) and no impure crystals. Long crystallization time, high crystallization temperature and high synthetic basicity are favorable conditions for forming hollow ZSM-5 molecular sieves. The synthetic process for hollow ZSM-5 molecular sieves have simple operation steps without any additives, and can yield high quality molecular sieve products. The whole process is fast, energy saving and environment protecting. The catalyst POM-MOF-ZSM-5 based on hollow ZSM-5 molecular sieves exhibits good oxidative desulfurization performance of DBT, which implies a broad application prospect.
Conflicts of interest
There are no conflicts to declare.
Acknowledgements
This work was supported by Foundation of Yanchang Petroleum (Group) Co. (No. ycsy2015ky-A-12 and ycsy2017QNJJ-b-19).
Notes and references
- M. E. Davis, Ind. Eng. Chem. Res., 1991, 30, 1675 CrossRef.
- C. Yu, J. Fan and B. Tian, et al., Adv. Mater., 2002, 14, 1742 CrossRef.
- M. Hartmann, Angew. Chem., Int. Ed., 2004, 43, 5880 CrossRef PubMed.
- F. Caruso, R. A. Caruso and H. Moöhwald, Science, 1998, 282, 1111 CrossRef PubMed.
- X. Wang, X. Zhang and Y. Wang, et al., Chem. Mater., 2011, 23, 4469 CrossRef.
- S. Van Donk, A. H. Janssen and J. H. Bitter, et al., Catal. Rev., 2003, 45, 297 CrossRef.
- R. Ravishankar, C. E. A. Kirschhock and P. P. Knops-Gerrits, et al., J. Phys. Chem. B, 1999, 103, 4960 CrossRef.
- W. Song, R. E. Justice and C. A. Jones, et al., Langmuir, 2004, 20, 8301 CrossRef PubMed.
- W. Zhang, D. Ma and X. Liu, et al., Chem. Commun., 1999, 1091 RSC.
- Y. Wang, M. Lin and A. Tuel, Microporous Mesoporous Mater., 2007, 102, 80 CrossRef.
- C. Pagis, A. R. Morgado Prates and D. Farrusseng, et al., Chem. Mater., 2016, 28, 5205 CrossRef.
- W. Song, C. Dai and Y. He, et al., Appl. Catal., A, 2012, 453, 272 Search PubMed.
- V. Valtchev, Chem. Mater., 2002, 14, 4371 CrossRef.
- Y. Wang and A. Tuel, Microporous Mesoporous Mater., 2007, 113, 286 CrossRef.
- C. Dai, A. Zhang and L. Li, et al., Chem. Mater., 2013, 25, 4197 CrossRef.
- J. C. Groen, J. C. Jansen and J. A. Moulijn, et al., J. Phys. Chem. B, 2004, 108, 13062 CrossRef.
- C. Mei, Z. Liu and P. Wen, et al., J. Mater. Chem., 2008, 18, 3496 RSC.
- J. C. Groen, T. Bach and U. Ziese, et al., J. Am. Chem. Soc., 2005, 127, 10792 CrossRef PubMed.
- Y. Wang and A. Tuel, Microporous Mesoporous Mater., 2008, 113, 286 CrossRef.
- C. Mei, Z. Liu and P. Wen, et al., J. Mater. Chem., 2008, 18, 3496 RSC.
- D. Fodor, L. Pacosová and F. Krumeich, et al., Chem. Commun., 2014, 50, 76 RSC.
- A. Zhang, Y. Zhang and N. Xing, et al., Chem. Mater., 2009, 21, 4122 CrossRef.
- J. Liu, S. Z. Qiao and S. Budi Hartono, et al., Angew. Chem., Int. Ed., 2010, 122, 5101 CrossRef.
- K. Kamata, Y. Lu and Y. Xia, J. Am. Chem. Soc., 2003, 125, 2384 CrossRef PubMed.
- C. J. H. Jacobsen, C. Madsen and J. Houzvicka, et al., J. Am. Chem. Soc., 2000, 122, 7116 CrossRef.
- J. Zhao, Z. Hua and Z. Liu, et al., Chem. Commun., 2009, 7578 RSC.
- S. W. Li, R. M. Gao and R. L. Zhang, et al., Fuel, 2016, 184, 18 CrossRef.
Footnote |
† Electronic supplementary information (ESI) available. See DOI: 10.1039/c8ra06984k |
|
This journal is © The Royal Society of Chemistry 2018 |
Click here to see how this site uses Cookies. View our privacy policy here.