Efficient hydrogen generation from water using nanocomposite flakes based on graphene and magnesium†
Received
23rd July 2018
, Accepted 11th August 2018
First published on 16th August 2018
Abstract
Water, through a metal–water reaction, is an appealing candidate to store and release hydrogen (H2), in particular as a portable, easy to use energy storage source. However, the release of hydrogen from the reaction of water with light metals can be violent or be inhibited by the formation of an oxide layer as is the case with magnesium (Mg). For this reason, we studied the use of graphene powder (Gr) as a nano-support to control the reactivity of Mg in water. Nanofilms and nanoparticles of Mg have been grown directly on graphene sheets inducing an increase of Mg surface area and the formation of metallic nanostructures that enhance the responsiveness of metal in water. We surprisingly observed that the water–Mg/Gr reaction happens at room temperature with impressive H2 production (the Mg/Gr hydrogen gravimetric density is 3%). Therefore, the hydrogen generated from water has been successfully used in a fuel cell proving that Mg/Gr is a promising material for on-demand H2 generation.
1 Introduction
Energy is so ubiquitous in our modern society that access to energy flexibility/density is directly linked to economic growth, our quality of life, including our level of education as measured by the Human Development Index, and even our reproduction rate. The growing digitalization of our societies also requires new and advanced forms of portable energy storage systems with energy densities and capabilities beyond those of batteries in delivering electricity only. Enabling the use of hydrogen (H2) as a clean synthetic energy vector is one of the most promising approaches.1,2 H2 possesses an extremely high energy density of 142 MJ kg−1, three times higher than that of petroleum. Hydrogen can be produced from many sources and can be used in all types of engines (turbines, endothermic generators) to generate electricity (heat and work) or can be used to store thermal energy by a thermo-chemical reaction.3,4 In addition, H2 can be used to directly generate electricity in combination with a fuel cell; H2 is thus an energy vector suitable for a vast number of technologies. However, for all these applications it is very important to produce the exact amount of H2 at the right time, and therefore it is essential to produce, store, and transfer H2 in a timely controlled manner. Nowadays H2 can be stored and released using metals (metal hydrides) in which H2 dissolves forming a hydride as in magnesium5,6, and can be stored in rippled Gr,7 but the current method to store H2 is via compression in high-pressure tanks.8,9 Unfortunately, when it comes to application, safety can be an issue since H2 readily burns with atmospheric oxygen, and the lowest explosive level (LEL) of H2 is only 4% by volume.10 To reduce the risk and the cost associated with the use of H2, simplified technologies to store and produce H2 on-demand are desirable, in particular for portable devices. A suitable strategy could be the in situ generation of H2, but this requires a H2 source that is readily available everywhere, abundant, stable and low cost.11,12 H2 is not directly available from the atmosphere (its concentration is 0.5 ppm). One H2 source meeting all these requirements is water13 being composed of one oxygen and two hydrogen atoms. The more common ways to produce hydrogen from water are via electrolysis from renewable sources providing electricity to the water electrolysis process; direct photocatalytic processes are also possible and as demonstrated by several experimental results the use of graphene enhanced the solar conversion efficiency.14–24 However, sunlight and wind are not always available, and for this reason, systems to temporarily store H2 are needed.25–27 Another promising approach to generate on-demand H2 avoiding the intermittency of sunlight or other renewable energy sources is through the use of reactive metals and water, such as the magnesium (Mg)–water (H2O) reaction: | Mg + 2H2O → Mg(OH)2 + H2 | (1) |
Yavor et al. reported extensive work on the reaction of water with a wide variety of metals, aluminium, magnesium and manganese were the most effective “metallic fuels” for in situ H2 generation.28 Unfortunately, the reactivity of these metals in water at room temperature is reduced owing to their low surface area and the native protective oxide layer. Different strategies to enhance the reactivity of metals are thus needed to increase the rate of H2 production.29–31 Grosjean used ball milling and Ni as a catalyst to increase the available surface and improve the reactivity of magnesium in water using 1 M KCl as an additive to destabilise MgO and Mg(OH)2.32 Sun et al.33 studied the generation of H2 using Mg–CoCl and water for portable applications. Figen et al. studied how to enhance H2 production using Mg–Ni compounds and Marmara Sea water34 in an attempt to create a micro-galvanic cell by increasing pitting corrosion and thus hydrogen production. Uda et al. reported the generation of hydrogen using nanopowder (265 nm diameter) produced by an arc plasma method, reaching an interesting value of completeness of Mg–water reaction of 11% at room temperature.35 The low percentage of completeness of water–metal reaction, an imprecise control reaction-kinetic as well as a relatively low rate of H2 production are still limiting factors for practical purpose. The reactivity of the metal with water is intimately related to the surface area of the metal, the stability of native metal oxides and the presence of defects.32 An increase of surface area and defect density enhances the probability of direct contact of water with the metal surface, which therefore increases the rate of reaction. In contrast, the metal reactivity is readily suppressed by the presence of a stable native oxide.36,37 Recently, various authors such as Tan et al. and Ma et al. have attempted to overcome the problems related to the use of metal–water reaction for hydrogen generation, adding MgCl2 into the water solution, adding Mg2Si as a catalyser of the hydrolysis of Mg with water, or using a MgH2–LiNH2 composite.38,39 Huang et al. used a solution of water with NaCl and added MoO2, MoO, MoS2 to Mg to improve the kinetics of the metal–water reaction.40 Moreover Ouyang et al. opened new prospects for the use of sodium borohydride (NaBH4) as an excellent hydrogen-generating material introducing a new efficient method to regenerate the NaBH4.41 Hydrogen-generating materials are usually synthesized using the ball milling method, which is a simple way to reduce the dimensions of metal powder and add the catalyst to enhance the hydrogen generation.40,42,43 Even if progress has been made in hydrogen generation,44 it is crucial to explore the use of emerging materials (such as 2D materials) and develop an alternative method to synthesise metal-nanocomposites to obtain an efficient and sustainable hydrogen generation. In the present work, we report on a nanomaterial based on Mg and Gr powder that generates hydrogen from water at ambient temperature; the nanocomposite material has been synthesised by a plasma deposition process that allows fine decoration of graphene flakes instead of typically used processes such as wet chemical processes and ball milling processes.45–47
Mg is one of the most interesting solid fuels for producing hydrogen via the metal–water reaction28 thanks to its abundance and low cost, while Gr powder is known to be a material with a high surface area (>400 m2 g−1) owing to its bi-dimensional structure. In fact, in Gr all carbon atoms belong to the surface.48–50 Moreover, nanocomposites based on graphene materials have been successfully used to enhance solar energy conversion, reduce surface friction, or realize transparent conductive materials.51–53 By combining Mg and Gr, we thus aimed at developing a high surface area nanocomposite material with nano-sized Mg particles that facilitate the metal–water reaction. Gr flakes have been coated using dedicated equipment based on plasma sputtering principles equipped with a micro-vibration system to improve the homogeneity of the Mg deposition. The reactivity and efficiency of Mg/Gr powder decorated using different deposition times have been evaluated by Mass Spectroscopy and with a calibrated Pressure Cell (PC). As a proof of concept, the best Mg/Gr nanocomposite material has been tested to generate hydrogen for running a commercial Polymer Electrolyte Membrane Fuel Cell (PEMFC). In the first part of the manuscript, we report on the physical and chemical properties of the Mg deposited on Gr. The second part of the manuscript describes the results relative to the efficiency of H2 generation using Mg/Gr nanocomposites.
2 Methods
Graphene (Gr) was purchased from G Supermarket, Calverton, NY – USA. According to the manufacturer's indications, the average thickness of Gr flakes is 1.6 nm, the average width is 10 μm and the surface area is in the range of 400–800 m2 g−1. The magnesium metal-chip (99.98% mesh 4–30) used as a reference material in the pressure cell was purchased from Sigma-Aldrich. The magnesium target (99.9%) was provided by Neyco Vanves France. The Gr was decorated by plasma sputtering. The plasma was operated at a power of 40 W with a radio frequency of 13.56 MHz and at a pressure of 6 Pa with argon as the sputtering gas. To ensure homogeneous Mg deposition on all the flake surfaces, the Gr powder was continuously kept in movement (50 Hz) with a piezoelectric device controlled by a waveform generator (ESI S1†). The surface chemistry was studied by X-ray Photoelectron Spectroscopy (XPS) using an Axis DLD Ultra instrument (Kratos – Manchester, UK). Broad spectra were acquired at a pass energy of 160 eV. A higher energy resolution was used for the acquisition of the core lines, setting the pass energy at 20 eV. Core line analysis was performed using home-made software (R-XPS) based on R-platform.54 The Shirley background and Gaussian components were utilized for peak fitting. Even if the samples are handled using a Kapton sealed sample holder, the presence of traces of oxygen is possible, in particular when the samples are transferred from the glovebox to other instruments such as an XPS instrument. In the experiments, the structural properties of the Mg/Gr nanocomposite were investigated by X-ray diffraction (XRD) analysis. Powder XRD data were collected at room temperature on an Italstructures APD2000 diffractometer with conventional theta–2theta Bragg–Brentano geometry operating in reflection mode with a Cu Kα radiation source (40 kV, 30 mA) and equipped with Goebel Mirror optics and a NaI scintillation detector. XRD patterns were acquired for diffraction angles over the range 10–90° with a scanning step of 0.02° and a counting time of 10 s per step. The morphology of the materials was studied using an SM-7401f Field Emission Scanning Electron Microscope (FESEM). The percentage of H2 released was estimated by using a calibrated small cell thermalised in a water bath at 22 °C and equipped with a pressure sensor (Honeywell, PX2AG2XX002BAAAX with a pressure resolution of 2%). The system was placed in a glovebag filled with high purity nitrogen (99.99999%) to minimise the oxidation of the Mg surface during the experiment (Fig. 1). The oxygen in the glovebag was ∼2–3%. The Mg/Gr powder (∼1 mg) was loaded into the reaction cell with 1 μl of water (deionised water) to generate hydrogen following reaction 1. Measuring the variation of pressure upon hydrogen generation and knowing the weight of the Mg/Gr powder, the dimensions of the calibrated cell and the amount of water, the amount of hydrogen generated could be estimated by using the following equation: | 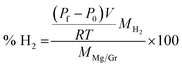 | (2) |
where % H2 is the percentage by mass of hydrogen generated for a given amount of Mg/Gr material (MMg/Gr), Pf is the final pressure reached after full hydrogen release, P0 is the initial pressure in the cell, V is the volume of the cell (without water), and MH2 is the molecular weight of hydrogen. To determine the influence of oxidation on the amount of hydrogen produced, the same experiment was also carried out in air instead of a nitrogen atmosphere. These data are reported in ESI S2.†
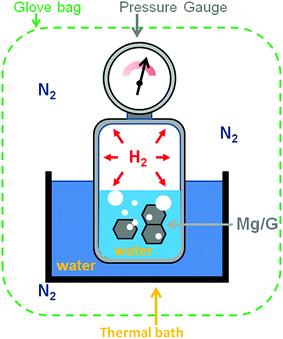 |
| Fig. 1 Schematic of the calibrated Pressure Cell (PC) used to measure the amount of H2 generated upon the reaction of water with Mg/Gr. | |
The nature of the gas produced during the reaction and its dynamic behaviour was confirmed by Mass Spectrometry (MS) by using a Proton Transfer Reaction Mass Spectrometry (PTR-MS) instrument (Kore Technology) equipped with a time-of-flight mass spectrometer and a Glow Discharge (GD) source. For PTR-MS measurements, Kr+ was used to facilitate the ionization of residual gases via charge transfer reactions,55 and the reaction of water with Mg/Gr was followed in situ. The pressure in the reaction chamber was about 0.5 mbar,56 and the amount of hydrogen measured was calibrated by using a mixture of H2 in nitrogen buffer. It should be noted that H3+ is detected and not directly H2 owing to the working principles of PTR-MS. The capability of the Mg/Gr nanocomposite to directly power a fuel cell was assessed by using a PEMFC 5053 (max 0.6 V and 360 mA, H2 flux 2.5 ml min−1), purchased from H2planet, Milano, Italy.
3 Results and discussion
3.1 Physical properties of the Mg/Gr composite material
To obtain a homogeneous composite material, the Gr powder was shaken during the deposition process of Mg by using a piezoelectric device (ESI S1†). The level of vibration depends upon the size of the objects to be vibrated. In the present case, the powder was agitated by applying a train of the square wave at a frequency of 50 Hz and an amplitude of 100 μm. Varying levels of Mg deposition have been obtained by keeping the amplitude of vibration constant while changing the deposition time.
As shown in Fig. 2, with the increase of deposition times, the amount of Mg at the surface of the Gr flakes increases. Hence, after 10 min, the deposited Mg was found to be in the form of highly dispersed nanoparticles. After 30 min, the density of nanoparticles increased (Fig. 2c), and after 60 min of deposition we observed the coalescence of the Mg particles toward the formation of a nanofilm, although not entirely uniform (Fig. 2d). This growth behaviour points toward a Volmer–Weber growth mechanism,57 indicating that the interaction between the Mg atoms is higher than in the Mg/graphene. Interestingly, both sides of flakes were uniformly covered by Mg, which further validated the approach of vibrating the Gr powder during Mg deposition (Fig. 2a red square and ESI S3†)
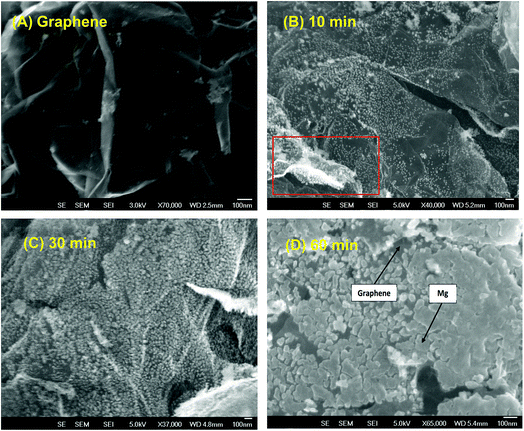 |
| Fig. 2 SEM images of Mg/Gr at varying deposition times: graphene (A), graphene after 10 min of deposition, particular showing the uniform decoration on the front and back sides of the Gr flakes (red square) (B), graphene after 30 min (C) and after 60 min of deposition (D). | |
Fig. 3a shows the experimentally obtained XRD pattern of the as-prepared Mg/Gr nanocomposite (60 min). Three diffraction peaks appeared at 36.12, 33.95 and 31.69° corresponding to the (101), (002) and (100) planes of the hexagonal phase of Mg (ICDD card #35-0821), respectively. The average Mg crystallite size calculated from the Debye–Scherrer equation, after FWHM correction for instrumental broadening, was estimated to be 21.7 ± 1.5 nm. This crystallite size corresponds to the size of the coherently diffracting domains, and it is not necessarily an indicator of the particle size. The broad peak centred at around 25° was assigned to Gr. The peaks not indicated by the black square and white square in Fig. 3 (A) and (B) are peaks due to the sample holder and adhesive tape (44.5°, 38.5°, and broadband 10° to 30°). XPS analysis confirmed the presence of Mg on the Gr surface, with core lines of Mg2p observed at 50 eV.58,59 The material also displayed XPS peaks assigned to C1s (284.5 eV) and O1s (532 eV) (Fig. S5†). Moreover, the estimated concentrations were 8.54% Mg, 73.84% C and 17.61% O. By XPS analysis, 3.5% of MgO was also estimated to be at the surface of Gr, and this was assigned to Mg bound to oxygen groups and in the form of epoxy, carbonyl and carboxyl groups or partial oxides at the surface of Gr (Table S5†). It is thus believed that the deposition of Mg at the Gr surface resulted in metallic Mg nanoparticles with an oxidised interface at the Gr surface.60 To further confirm the metallic state of Mg at the Gr surface we studied the Auger line induced by XPS at kinetic energies between 1170 and 1190 eV (Fig. 3c).61 The Auger spectra and the fit of the spectra using Gaussian components revealed a peak at 1185 eV assigned to metallic Mg (#1), and peaks at 1183.2, 1180.1, and 1178.1 eV due to non-stoichiometric MgOx (#2), MgO (#3), and MgOH (#4), respectively. The peak at 1174 eV was attributed to Mg bulk plasmon (#5).62,63 Hence, XPS and XRD analysis are in agreement with metallic Mg and Gr being the main phases of Mg/Gr.
 |
| Fig. 3 XRD spectra of Mg/Gr (after 60 min of deposition): (A) as-synthesized (black square), and (B) after the reaction with water (white square). Auger KLL spectra by XPS of Mg/Gr after 60 min of deposition: (C) as-synthesized, and (D) after reaction with water (red line). A partial oxidation of the Mg may occur during transfer to the instrument. | |
3.2 H2 generation with the Mg/Gr composite material
To check the reactivity of Mg/Gr with water, a layer of Mg/Gr was secured on sticky tape and dipped in a cuvette filled with water. By using a micro-camera, images of hydrogen evolution were recorded as shown in Fig. 4. Compared to pristine G, Mg/Gr caused turbulent gas bubbling, which was assigned to the subsequent reaction of Mg with water.1 It is noteworthy that no violent reaction occurred and the heat generated was not sufficient to trigger any flame or explosion.
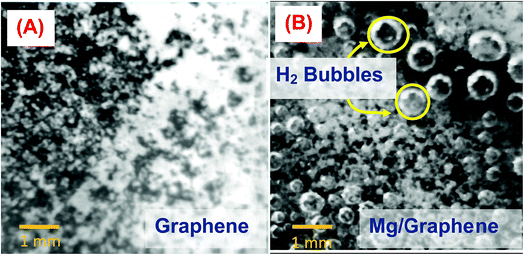 |
| Fig. 4 (A) Image of pristine Gr in water: no gas evolution was observed. (B) Image of Mg/Gr in water showing a significant evolution of gas. | |
To confirm the assumption that H2 is produced upon reaction of water with Mg/Gr, the evolving gas was analyzed by PTR-MS (Fig. 5). As shown in Fig. 5a, hydrogen was efficiently detected in the form of H3+ ions, and the release of hydrogen started as soon as water was placed in contact with Mg/Gr with a peak at 150 s. Full hydrogen release occurred in 600 s and this further indicated that the reaction is relatively fast, Fig. 5b.
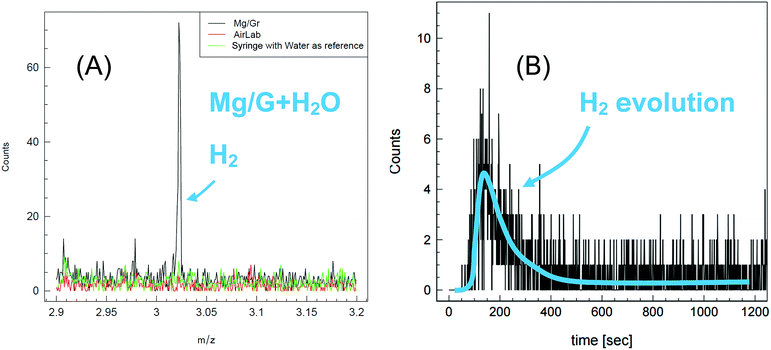 |
| Fig. 5 (A) PTR-MS spectra of H2 produced by the Mg/Gr nanocomposite reacting with water (black). The corresponding spectra of “AirLab” (red) corresponding to the analysis of the air in the laboratory environment and the water (green) used for the reaction with Mg/Gr are given as a reference. (B) Evolution of the H2 released from the reaction of Mg/Gr with water as a function of time. In this case, 3 mg of Mg/Gr powder was reacted with 15 ml of deionized water. | |
The resulting powder after the reaction was further characterized by XRD and XPS. Fig. 3b shows the XRD spectra of the Mg/Gr powder after reaction with four main peaks at 18.6°, 38.2°, 51.1° and 58.9° related to the hexagonal phase of Mg(OH)2 (ICDD card number #07-239). Similar observations were made by XPS, with peaks only due to MgOH and MgO (Fig. 3d). Hence, it can be concluded that Mg/Gr was entirely converted to magnesium oxide and hydroxide upon its reaction with water, and thus no inhibition of the reaction occurred. To quantify the amount of H2 evolved, a calibrated Pressure Cell (PC) of known volume was purposely designed (Fig. 1). As shown in Fig. 6 as the amount of Mg supported by Gr increases, more H2 is produced and this further evidenced the sole role of Mg in generating H2.
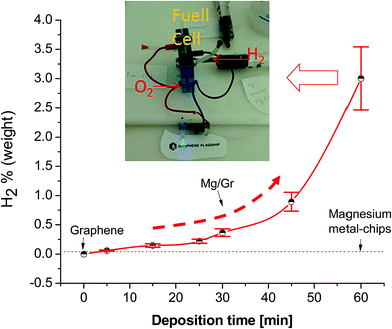 |
| Fig. 6 H2 gravimetric density produced during Mg/Gr–water reaction as a function of deposition time; the red dashed line indicates the result obtained using a commercial Mg metal-chip. The inserted picture shows the lighting of an LED (0.5 V and 7 mA) upon hydrogen production using Mg/Gr in water to power a fuel cell. A plastic syringe filled with Mg/Gr powder (7 mg) and 7 ml of water was used as the reaction vessel and directly connected to the hydrogen inlet of the fuel cell. | |
From Fig. 6, the highest production of hydrogen of 3.04 ± 0.54 wt% was achieved at a deposition time of 60 min. By gravimetric measurement, we found that the amount of Mg corresponds to 45% of the total mass of Mg/Gr powder; thus, an estimated H2 gravimetric density of 6.6 wt% can be produced through reaction (1). This value is not far from the theoretical maximum value obtainable with magnesium (7.6 wt%) and is comparable with the reference results reported in the literature for CaMg2, CaMg1.9Ni0.1 in water and a Mg-oxide composite in water with 3.5% of NaCl.40,64 The small discrepancy between the theoretical hydrogen capacity and that estimated for Mg may be due to partial oxidation of Mg/Gr during the handling of the material. Indeed, exposure of the material to oxygen in the glovebag for a few minutes oxidises the Mg nanoparticles partially at the Gr surface; therefore, lower amounts of hydrogen will be produced owing to the growth of an oxide layer at the surface (Fig. S2†). However, this does not stop the reaction from proceeding, and this result further proves the validity of the current approach in enabling the production of hydrogen through the reaction of Mg with water. Considering a gravimetric density of 2.9% wt, 1 g of Mg/Gr powder can produce more than 3.5 kJ of energy in the form of H2 and more of 5 kJ of energy as co-heat generated during the reaction (ESI S10†). Therefore, the energy density of this nanocomposite considering H2 only is 3 times higher than that of a typical lithium battery (ESI S11†). For our best sample (3% H2) we estimated a good value of hydrogen generation rate of 108 ml g−1 in 60 min. This value is similar to the hydrogen generation rate obtained recently by Tan et al. using a Mg–Mg2Si composite in water.38 The authors underline that the obtained result is encouraging but still far from the best results reported in the literature for a Mg-alloy (>400 ml g−1 in 60 min)39 and from the excellent results obtained using MgH2 (>900 ml g−1 in 40 min).39,65
3.3 The ability of the Mg/Gr composite to run a PEMFC
To verify the possibility of using this kind of Mg/Gr composite material in real applications, a small in situ H2 generator was built and connected to a PEMFC (Fig. 6). To visualize the electricity produced, the fuel cell was connected to two LEDs (Fig. 6). After a few seconds as hydrogen is produced from the reaction of water with Mg/Gr enough power was produced to light up the LEDs (Video in ESI S6†). During the experiment, we measured an output voltage of 0.5 V and a current of 7 mA. Hence, these findings prove that using Mg on graphene and water is an effective method for hydrogen generation for PEMFCs to produce energy. The possibility of generating hydrogen by simply establishing contact between water and Mg deposited on Gr is because Mg grew on Gr following the Volmer–Weber growth mode; such mode of thin film growth will induce the formation of nanostructured particles and structural defects including voids, nanopores and a significant amount of grain boundaries.57 This in conjunction with the high surface area of the Mg deposited in the form of nanoparticles/nanofilms at the surface of Gr is likely to facilitate the interaction of metal Mg and water,66 explaining the remarkable behaviour of the Mg/Gr composite at room temperature (Fig. S6†). Additional effects explaining such performance may be related to the “barrier effect” of the graphene flakes against oxygen permeation.67,68 Graphene flakes, could act as a protective blanket against the permeation of gases such as oxygen preventing the oxidation of surfaces as previously reported by Wang et al. and partially by Schriver et al.67,69–71 Moreover, the overlapping of the Mg/flakes can also reduce the diffusion of oxygen in composite materials inducing a reduction in the oxidation of the surface as reported by Tan et al.72 In Mg/Gr powder samples, the presence of flakes of pure graphene is probable, due to shadowing of the other flakes during the deposition process. These flakes and the flakes partially coated with Mg can act as a barrier against the oxidation process. The barrier effect of the flake is diminished during the immersion of Mg in water. The immersion of the Mg/Gr in water quickly disperses the powder in the liquid due to the excellent hydrophilicity of the Mg; the dispersion allowed the removal of overlapped flakes and exposed the metal directly to the water. This is partially supported by the fact that the oxygen in the glovebag used to estimate the H2 production was 2–3%; this oxygen concentration is thousand times higher than the typical oxygen concentration present in a glovebox for metal–water reaction (glovebox O2 concentration less than 10 ppm). Moreover, in some experiments conducted exposing the powder to air we observed a sensible production of hydrogen (10% of H2 compared to the same sample tested in the controlled atmosphere of glovebag S2). Both pieces of evidence indicate that the graphene flakes could partially avoid the oxidation of the Mg surface. The authors acknowledge that other experiments must be carried out to (a) understand better the effect of graphene on the reactivity of nanoscale Mg in water, (b) improve the percentage of H2 production, (c) study the barrier effect of graphene flakes, (d) estimated the apparent activation energy of Mg/Gr, and (e) understand the role of galvanic corrosion. Moreover, computational experiments are needed to study the role of graphene in the enhancement of the hydrogen generation efficiency.
However, we underline that combining a 2D material and reactive metal using plasma technology can open new prospects for H2 generation on demand; that should be of great interest for off-grid applications and a portable system based for instance on microfluidic devices.73
4 Conclusions
Mg/Gr powders were developed for the in situ generation of H2 using water as a reactant. The results show excellent control of decoration of the Gr flakes with magnesium using plasma deposition and a vibration system. The large surface area of Gr powders (>400 m2 g−1) in combination with the nano-structuration of Mg makes the Mg/Gr powder reactive with water at room temperature, avoiding the use of any acid or base solution to activate the reaction. Moreover, as a proof of concept, we demonstrated by using a simple setup that Mg/Gr composite materials were able to generate enough hydrogen to run a commercial fuel cell. This result is due to the excellent energy density of Mg/Gr, in which a 45% Mg concentration displays a gravimetric energy density three times higher than that of rechargeable Li-ion batteries. We believe that these results demonstrate the potential of 2D materials for H2 generation from water and open new perspects for the use of decorated 2D materials for energy storage and generation.
Conflicts of interest
There are no conflicts to declare.
Acknowledgements
The authors wish to thank the Autonomous Province of Trento within the project Graphene PAT (no. S116/2012-242637 and reg. deli. no. 2266) and the European Commission under the Graphene Flagship WP12 ‘Energy’, no. 696656.
References
- H. Z. Wang, D. Y. C. Leung, M. K. H. Leung and M. Ni, A review on hydrogen production using aluminum and aluminum alloys, Renewable Sustainable Energy Rev., 2009, 13(4), 845–853 CrossRef
.
- W. C. Lattin and V. P. Utgikar, Transition to hydrogen economy in the United States: a 2006 status report, Int. J. Hydrogen Energy, 2007, 32, 3230–3237 CrossRef
.
- P. Pardo, A. Deydier, Z. Anxionnaz-minvielle, S. Rougé, M. Cabassud and P. Cognet, A review on high temperature thermochemical heat energy storage, Renewable Sustainable Energy Rev., 2014, 32, 591–610 CrossRef
.
- A. Steinfeld, Solar thermochemical production of hydrogen – a review, Sol. Energy, 2005, 78, 603–615 CrossRef
.
- B. Sakintuna, F. Lamari-darkrim and M. Hirscher, Metal hydride materials for solid hydrogen storage: a review, Int. J. Hydrogen Energy, 2007, 32, 1121–1140 CrossRef
.
- M. Felderhoff, F. Schu and B. Bogdanovic, Light metal hydrides and complex hydrides for hydrogen storage, Chem. Commun., 2004, 2249–2258 Search PubMed
.
- V. D. Camiola, R. Farchioni, T. Cavallucci, A. Rossi, V. Pellegrini and V. Tozzini, Hydrogen Storage in Rippled Graphene: Perspectives from Multi-Scale Simulations, Frontiers in materials, 2015, 2, 3 CrossRef
.
- W. L. Mao and H. Mao, Hydrogen storage in molecular compounds, Proc. Natl. Acad. Sci. U. S. A., 2004, 101(3), 708–710 CrossRef PubMed
.
- T. Q. Hua, R. K. Ahluwalia, J. Peng, M. Kromer, S. Lasher and K. Mckenney,
et al., Technical assessment of compressed hydrogen storage tank systems for automotive applications, Int. J. Hydrogen Energy, 2011, 36(4), 3037–3049 CrossRef
.
- H. K. Abdel-aal, M. Sadik, M. Bassyouni and M. Shalabi, A new approach to utilize hydrogen as a safe fuel, Int. J. Hydrogen Energy, 2005, 30, 1511–1514 CrossRef
.
- Y. Kojima, K. Suzuki and Y. Kawai, Hydrogen generation by hydrolysis reaction of magnesium hydride, J. Mater. Sci., 2004, 9(2), 2227–2229 CrossRef
.
- Q. Zhao, C. Wang, Y. Liu and S. Wang, Bacterial adhesion on the metal-polymer composite coatings, Int. J. Adhes. Adhes., 2007, 27(2), 85–91 CrossRef
.
- Z. Zou, J. Ye, K. Sayama and H. Arakawa, Direct splitting of water under visible light irradiation with an oxide semiconductor photocatalyst, Nature, 2001, 414(2000), 625–627 CrossRef PubMed
.
- M. Ni, M. K. H. Leung, D. Y. C. Leung and K. Sumathy, A review and recent developments in photocatalytic water-splitting using TiO2 for hydrogen production, Renewable Sustainable Energy Rev., 2007, 11, 401–425 CrossRef
.
- M. Wang, Z. Wang, X. Gong and Z. Guo, The intensification technologies to water electrolysis for hydrogen production – a review, Renewable Sustainable Energy Rev., 2014, 29, 573–588 CrossRef
.
- Y. Hang, Y. Wang, L. Rong, H. Jun, H. Gui and C. Li, Environmental Water-soluble inorganic photocatalyst for overall water splitting, Applied Catal B, Environ., 2017, 209, 247–252 CrossRef
.
- Y. H. Hu, A Highly Efficient Photocatalyst—Hydrogenated Black TiO2 for the Photocatalytic Splitting of Water, Angew. Chem., Int. Ed., 2012, 12410–12412 CrossRef PubMed
.
- G. Xie, K. Zhang, B. Guo, Q. Liu, L. Fang and J. R. Gong, Graphene-based materials for hydrogen generation from light-driven water splitting, Adv. Mater., 2013, 25(28), 3820–3839 CrossRef PubMed
.
- K. Zhang, Q. Liu, H. Wang, R. Zhang, C. Wu and J. R. Gong, TiO2 single crystal with four-truncated-bipyramid morphology as an efficient photocatalyst for hydrogen production, Small, 2013, 9(14), 2452–2459 CrossRef PubMed
.
- J. Zhang, J. Yu, Y. Zhang, Q. Li and J. R. Gong, Visible light photocatalytic H2-production activity of CuS/ZnS porous nanosheets based on photoinduced interfacial charge transfer, Nano Lett., 2011, 11(11), 4774–4779 CrossRef PubMed
.
- Q. Li, H. Meng, P. Zhou, Y. Zheng, J. Wang and J. Yu,
et al., Zn1−xCdxS solid solutions with controlled bandgap and enhanced visible-light photocatalytic H2-production activity, ACS Catal., 2013, 3(5), 882–889 CrossRef
.
- K. Zhang, T. Dong, G. Xie, L. Guan, B. Guo and Q. Xiang,
et al., Sacrificial Interlayer for Promoting Charge Transport in Hematite Photoanode, ACS Appl Mater Interfaces, 2017, 9(49), 42723–42733 CrossRef PubMed
.
- B. Guo, A. Batool, G. Xie, R. Boddula, L. Tian and S. U. Jan,
et al., Facile Integration between Si and Catalyst for High-Performance Photoanodes by a Multifunctional Bridging Layer, Nano Lett., 2018, 18(2), 1516–1521 CrossRef PubMed
.
- K. Zhang, Y. Dai, Z. Zhou, S. Ullah Jan, L. Guo and J. R. Gong, Polarization-induced saw-tooth-like potential distribution in zincblende-wurtzite superlattice for efficient charge separation, Nano Energy, 2017, 41, 101–108, DOI:10.1016/j.nanoen.2017.09.021
.
- D. Aydin, S. P. Casey and S. Riffat, The latest advancements on thermochemical heat storage systems, Renewable Sustainable Energy Rev., 2015, 41, 356–367 CrossRef
.
- F. Schaube, L. Koch and A. Wörner, A thermodynamic and kinetic study of the de- and rehydration of Ca(OH)2 at high H2O partial pressures for thermo-chemical heat storage, Thermochim. Acta, 2012, 538, 9–20 CrossRef
.
- B. B. B. Mckeon, J. Furukawa and S. Fenstermacher, Advanced Lead – Acid Batteries and the Development of Grid-Scale Energy Storage Systems, Proc. IEEE, 2014, 102(6), 951–963 Search PubMed
.
- Y. Yavor, S. Goroshin, J. M. Bergthorson and D. L. Frost, Comparative reactivity of industrial metal powders with water for hydrogen production, Int. J. Hydrogen Energy, 2015, 40(2), 1026–1036 CrossRef
.
-
N. Giraudo, P. G. Weidler, F. Laye, M. Schwotzer, J. Lahann and C. Wo, et al., Corrosion of Concrete by Water-Induced Metal − Proton Exchange, 2016.
- Y. Kojima, K. Suzuki, K. Fukumoto, M. Sasaki, T. Yamamoto and Y. Kawai,
et al., Hydrogen generation using sodium borohydride solution and metal catalyst coated on metal oxide, Int. J. Hydrogen Energy, 2002, 27, 1029–1034 CrossRef
.
- A. Kantürk Figen, B. Coşkuner and S. Pişkin, Hydrogen generation from waste Mg based material in various saline solutions (NiCl2, CoCl2, CuCl2, FeCl3, MnCl2), Int. J. Hydrogen Energy, 2015, 40(24), 7483–7489 CrossRef
.
- M. Grosjean, M. Zidoune, L. Roue and J. Huot, Hydrogen production via hydrolysis reaction from ball-milled Mg-based materials, Int. J. Hydrogen Energy, 2006, 31(1), 109–119 CrossRef
.
- Q. Sun, M. Zou, X. Guo, R. Yang, H. Huang and P. Huang,
et al., A study of hydrogen generation by reaction of an activated Mg–CoCl2 (magnesium–cobalt chloride) composite with pure water for portable applications, Energy, 2015, 79, 310–314 CrossRef
.
- A. Kantürk Figen and B. Coşkuner Filiz, Hydrogen production by the hydrolysis of milled waste magnesium scraps in nickel chloride solutions and nickel chloride added in Marmara Sea and Aegean Sea Water, Int. J. Hydrogen Energy, 2015, 40(46), 16169–16177 CrossRef
.
- M. Uda, H. Okuyama, T. S. Suzuki and Y. Sakka, Hydrogen generation from water using Mg nanopowder produced by arc plasma method, Sci. Technol. Adv. Mater., 2012, 13, 0250091–0250097 CrossRef PubMed
.
- C. X. Shan, X. Hou and K. Choy, Corrosion resistance of TiO2 films grown on stainless steel by atomic layer deposition, Surf. Coat. Technol., 2008, 202, 2399–2402 CrossRef
.
- Y. Hsieh, M. Hofmann, K. Chang, J. G. Jhu, Y. Li and K. Y. Chen, Supplementary Material Complete Corrosion Inhibition through Graphene Defect Passivation, ACS Nano, 2014, 8(1), 443–448 CrossRef PubMed
.
- Z. Tan, L. Ouyang, J. Liu, H. Wang, H. Shao and M. Zhu, Hydrogen generation by hydrolysis of Mg-Mg2Si composite and enhanced kinetics performance from introducing of MgCl2and Si, Int. J. Hydrogen Energy, 2018, 43(5), 2903–2912, DOI:10.1016/j.ijhydene.2017.12.163
.
- M. Ma, L. Ouyang, J. Liu, H. Wang, H. Shao and M. Zhu, Air-stable hydrogen generation materials and enhanced hydrolysis performance of MgH2-LiNH2composites, J. Power Sources, 2017, 359, 427–434 CrossRef
.
- M. Huang, L. Ouyang, Z. Chen, C. Peng, X. Zhu and M. Zhu, Hydrogen production via hydrolysis of Mg-oxide composites, Int. J. Hydrogen Energy, 2017, 42(35), 22305–22311, DOI:10.1016/j.ijhydene.2016.12.099
.
- L. Ouyang, W. Chen, J. Liu, H. Felderhoff, H. Wang and M. Zhu, Enhancing the Regeneration Process of Consumed NaBH4 for Hydrogen Storage, Adv. Energy Mater., 2017, 7, 1700299 CrossRef
.
- L. Z. Ouyang, Y. J. Wen, Y. J. Xu, X. S. Yang, L. X. Sun and M. Zhu, The effect of Ni addition on hydrogeneration of Mg3La hydrides via hydrolysis, Int. J. Hydrogen Energy, 2010, 35(15), 8161–8165 CrossRef
.
- T. Si, Y. Cao, Q. Zhang, D. Sun, L. Ouyang and M. Zhu, Enhanced hydrogen storage properties of a Mg-Ag alloy with solid dissolution of indium: a comparative study, J. Mater. Chem. A, 2015, 3(16), 8581–8589, 10.1039/C5TA00292C
.
- M. Huang, L. Ouyang, J. Liu, H. Wang, H. Shao and M. Zhu, Enhanced hydrogen generation by hydrolysis of Mg doped with flower-like MoS2 for fuel cell applications, J. Power Sources, 2017, 365, 273–281, DOI:10.1016/j.jpowsour.2017.08.097
.
- Q. Li, B. Guo, J. Yu, J. Ran, B. Zhang and H. Yan,
et al., Highly efficient visible-light-driven photocatalytic hydrogen production of CdS-cluster-decorated graphene nanosheets, J. Am. Chem. Soc., 2011, 133(28), 10878–10884 CrossRef PubMed
.
- S. Orimo, G. Majer, T. Fukunaga, A. Züttel, L. Schlapbach and H. Fujii, Hydrogen in the mechanically prepared nanostructured graphite, Appl. Phys. Lett., 1999, 75(20), 3093 CrossRef
.
- W. Liu, E. Setijadi, L. Crema, R. Bartali, N. Laidani and K. F. Aguey-Zinsou,
et al., Carbon nanostructures/Mg hybrid materials for hydrogen storage, Diamond Relat. Mater., 2018, 82, 19–24 CrossRef
.
- C. Wang, L. Zhang, Z. Guo and J. Xu, A novel hydrazine electrochemical sensor based on the high specific surface area graphene, Microchim. Acta, 2010, 169, 1–6 CrossRef
.
- M. A. Bissett, I. A. Kinloch and R. A. W. Dryfe, Characterization of MoS2–Graphene Composites for High- Performance Coin Cell Supercapacitors, ACS Appl. Mater. Interfaces, 2015, 7, 17338–17398 CrossRef PubMed
.
- A. K. Geim and K. S. Novoselov, The rise of graphene, Nat. Mater., 2007, 6(3), 183–191 CrossRef PubMed
.
- G. Xie, K. Zhang, H. Fang, B. Guo, R. Wang and H. Yan,
et al., A Photoelectrochemical Investigation on the Synergetic Effect between CdS and Reduced Graphene Oxide for Solar-Energy Conversion, Chem.–Asian J., 2013, 8, 2395–2400 CrossRef PubMed
.
- M. Uysal, H. Akbulut, M. Tokur, H. Algül and T. Çetinkaya, Structural and sliding wear properties of Ag/Graphene/WC hybrid nanocomposites produced by electroless co-deposition, J. Alloys Compd., 2016, 654, 185–195 CrossRef
.
- C. Van Nguyen, R. Bartali, L. Crema and G. Speranza, Effect of glass surface treatments on the deposition of highly transparent reduced graphene oxide films by dropcasting method, Colloids Surf., A, 2016, 498, 231–238 CrossRef
.
- No Title. p. https://www.r-project.org/.
- P. Sulzer, A. Edtbauer, E. Hartungen, S. Jürschik, A. Jordan and G. Hanel,
et al., International Journal of Mass Spectrometry From conventional proton-transfer-reaction mass spectrometry (PTR-MS) to universal trace gas analysis, Int. J. Mass Spectrom., 2012, 321–322, 66–70 CrossRef
.
- A. Edtbauer, E. Hartungen, A. Jordan, G. Hanel, J. Herbig and S. Jürschik,
et al., Theory and practical examples of the quantification of CH4, CO, O2, and CO2 with an advanced (PTR/SRI-MS), Int. J. Mass Spectrom., 2014, 365–366, 10–14 CrossRef
.
- H. Z. Yu and C. V. Thompson, ScienceDirect Grain growth and complex stress evolution during Volmer–Weber growth of polycrystalline thin films, Acta Mater., 2014, 67, 189–198 CrossRef
.
- E. S. Cho, A. M. Ruminski, S. Aloni, Y.-S. Liu, J. Guo and J. J. Urban, Graphene oxide/metal nanocrystal multilaminates as the atomic limit for safe and selective hydrogen storage, Nat. Commun., 2016, 7, 10804 CrossRef PubMed
.
- L. O. Hare, B. Parbhoo and S. R. Leadley, Development of a methodology for XPS curve-fitting of the Si 2p core level of siloxane materials, Surf. Interface Anal., 2004, 36, 1427–1434 CrossRef
.
- Y. Bouvier, B. Mutel and J. Grimblot, Use of an Auger parameter for characterizing the Mg chemical state in different materials, Surf. Coat. Technol., 2004, 181, 169–173 CrossRef
.
- I. J. T. Jensen, A. Thøgersen, O. M. Løvvik, H. Schreuders and B. Dam, X-ray photoelectron spectroscopy investigation of magnetron sputtered Mg e Ti e H thin films, Int. J. Hydrogen Energy, 2013, 38(25), 10704–10715 CrossRef
.
- M. Lelis and D. Girdzevicius, Combined XRD and XPS analysis of ex situ and in situ plasma hydrogenated magnetron sputtered Mg films, J. Alloys Compd., 2015, 647, 790–796 CrossRef
.
- T. Klassen, R. Bormann and A. Ferna, Chemical and microstructural study of the oxygen passivation behaviour of nanocrystalline Mg and MgH2, ACS Appl. Mater. Interfaces, 2006, 252, 2334–2345 Search PubMed
.
- M. Ma, R. Duan, L. Ouyang, X. Zhu, Z. Chen and C. Peng,
et al., Hydrogen storage and hydrogen generation properties of CaMg2-based alloys, J. Alloys Compd., 2017, 691, 929–935, DOI:10.1016/j.jallcom.2016.08.307
.
- R. V. Lukashev, N. A. Yakovleva, S. N. Klyamkin and B. P. Tarasov, Effect of Mechanical Activation on the Reaction of Magnesium Hydride with Water, Russ. J. Inorg. Chem., 2008, 53(3), 343–349 CrossRef
.
- M.-H. Grosjean, M. Zidoune and L. Roué, Hydrogen production from highly corroding Mg-based materials elaborated by ball milling, J. Alloys Compd., 2005, 404–406, 712–715 CrossRef
.
- S. Chen, L. Brown, M. Levendorf, W. Cai, S. Ju and J. Edgeworth,
et al., Oxidation Resistance of Graphene-Coated Cu and Cu/Ni Alloy, ACS Nano, 2011, 5(2), 1321–1327 CrossRef PubMed
.
- S. P. Koenig, L. Wang, J. Pellegrino and J. S. Bunch, Selective molecular sieving through porous graphene, Nat. Nanotechnol., 2012, 7, 728–732 CrossRef PubMed
.
- B. Wang, B. V. Cunning, S.-Y. Park, M. Huang, J.-Y. Kim and R. S. Ruoff, Graphene Coatings as Barrier Layers to, ACS Nano, 2016, 10, 9797–9800 Search PubMed
.
- M. Schriver, W. Regan, W. J. Gannett, A. M. Zaniewski, M. F. Crommie and A. Zettl, Graphene as a long-term metal oxidation barrier: worse than nothing, ACS Nano, 2013, 7(7), 5763–5768 CrossRef PubMed
.
- Y. Su, V. G. Kravets, S. L. Wong, J. Waters, a K. Geim and R. R. Nair, Impermeable barrier films and protective coatings based on reduced graphene oxide, Nat. Commun., 2014, 5, 4843 CrossRef PubMed
.
- B. Tan and N. L. Thomas, A review of the water barrier properties of polymer/clay and polymer/graphene nanocomposites, J. Membr. Sci., 2016, 514, 595–612 CrossRef
.
- J. Lee and T. Kim, Micro space power system using MEMS fuel cell, Acta Astronaut., 2014, 101, 165–169 CrossRef
.
Footnote |
† Electronic supplementary information (ESI) available. See DOI: 10.1039/c8se00370j |
|
This journal is © The Royal Society of Chemistry 2018 |
Click here to see how this site uses Cookies. View our privacy policy here.