DOI:
10.1039/C9RA01696A
(Paper)
RSC Adv., 2019,
9, 14910-14915
Removal of metallic coatings from rare-earth permanent magnets by solutions of bromine in organic solvents†
Received
6th March 2019
, Accepted 8th May 2019
First published on 14th May 2019
Abstract
Successful direct recycling routes are known for both Nd–Fe–B permanent magnets and Sm–Co permanent magnets. Often the magnets are coated by a nickel–copper–nickel coating to prevent corrosion of Nd–Fe–B magnets and chipping of Sm–Co magnets. However, this coating does not contribute to the magnetic properties and only ends up as a contamination in the recycled magnet powder, which in turn dilutes the magnet alloy and reduces the magnetic performance. One solution is the addition of virgin magnet alloy to the recycled powder, but this is not the best option from a sustainable point of view. Another option is to remove the coating prior to the magnet recycling. We developed a solvometallurgical process for removal of the metallic coating prior to direct recycling. In particular, a mixture of bromine in organic solvents was found to be very selective in the removal of the nickel–copper–nickel coating from both Nd–Fe–B permanent magnets and Sm–Co permanent magnets, without codissolution of the magnet alloy.
Introduction
The European supply of rare-earth elements (REEs) almost completely relies on imports from China. Urban mining of REEs from end-of-life permanent magnets (PMs) or from PM production scrap could partially replace primary production.1–3 Although Nd–Fe–B PMs represent the largest share of the global PM market, Sm–Co PMs are still essential for high-temperature and high-end applications.4 REE PMs can be directly recycled into new magnets which is not possible for applications, such as lamp phosphor. Compared to indirect recycling, direct recycling (magnet-to-magnet) has the advantages of short flowsheets, minimal losses of material and lower costs. Two processes, hydrogen decrepitation (HD) or hydrogen-decomposition–desorption–recombination (HDDR) have already been successfully applied at pilot scale and could be commercially feasible, especially for Nd–Fe–B magnets.5–12 However, the magnet coating partly ends up as a contamination in the decrepitated powder, dilutes the magnet alloy and deteriorates the magnetic properties of the recycled PM.9,13 Different materials are being used for coatings, depending on the application of the PMs, for instance epoxy resins, zinc, nickel–copper, and nickel–copper–nickel.14 In case of Nd–Fe–B PMs, the coating is necessary for corrosion resistance, whereas it is mainly applied to Sm–Co PMs for protection against chipping or for use in medical applications.15,16 There are three options available for removal of the coatings of PMs prior to direct recycling: mechanically, pyrometallurgically or hydrometallurgically. The latter option is preferred because it is cheaper and less labor-intensive. Nevertheless, although it is the most selective among the current three routes, hydrometallurgical pre-treatment of coated Nd–Fe–B PMs and Sm–Co PMs still causes losses of the core valuable metals by partial codissolution of the magnet alloy. No solvometallurgical treatments, in which the lixiviant is dissolved in an organic solvent, have been tested yet to dissolve metallic coating from REE PMs.17,18
In this paper, a selective solvometallurgical method is described to remove the nickel–copper–nickel coating from Sm–Co and Nd–Fe–B PMs, using a solution of elemental bromine in an organic solvent. In the literature, bromine in organic solvents such as ethyl acetate or methanol has been reported to be able to dissolve metals such as uranium, thorium, zirconium, titanium, iron, chromium and nickel.19–24 Inspired by these results, we investigated the dissolution of the nickel–copper–nickel coating of SmCo5, Sm2Co17 and Nd–Fe–B PMs in solutions of 1 vol% bromine in five organic solvents: ethylene glycol (EG), ethanol (EtOH), dimethylformamide (DMF), ethylacetate (EtOAc) and methyl acetate (MeOAc).
Experimental
Chemicals
Nickel–copper–nickel-coated SmCo5, nickel–copper–nickel-coated Sm2Co17 and nickel–copper–nickel coated Nd–Fe–B permanent magnets were kindly supplied by Magneti Ljubljana d.d. (Slovenia). The volumes of the magnets were 0.16 cm3, 0.19 cm3 and 0.12 cm3 respectively for SmCo5, Sm2Co17 and NdFeB, respectively. HNO3 65 wt% in water and ethanol (EtOH) were purchased by Fisher (Loughborough, UK). Bromine 99.6%, ethylene glycol (EG) 99.5% and dimethylformamide (DMF) 99.5% were supplied by Acros Organics (Geel, Belgium). Ethylacetate (EtOAc) ≥ 99.7% was supplied by Sigma-Aldrich (Diegem, Belgium), while methyl acetate (MeOAc) 99.0% by Janssen Chimica (Beerse, Belgium). ICP standard solutions of boron, cobalt, copper, dysprosium, iron, neodymium, nickel, praseodymium, samarium, zirconium (1000 mg L−1 in 3–5 wt% HNO3), were purchased from ChemLab (Zedelgem, Belgium). Ultrapure water with a nominal resistivity of 18.2 MΩ cm at 25 °C was used, obtained by a Millipore Milli-Q® water purification system. All chemicals were used as received without any further purification.
Dissolution experiments
All the dissolution tests were carried out by soaking a bulk SmCo5, or Sm2Co17 or Nd–Fe–B PM in a 10 mL solution of either 2 M HNO3 or 1 vol% bromine in an organic solvent. Bulk magnets were used, in order that only the coating was exposed at the starting time. The metal concentrations in solutions were measured by ICP-OES. To determine the PMs compositions, ten of each type of magnets were dissolved, separately, in 30 mL of 37 wt% HCl. Standard solutions in the concentration range of 0.1–50 mg L−1 were prepared by dilution of the metal standards in 2 vol% HNO3. All the samples were also diluted in 2 vol% HNO3 and different dilution factors were used, in the sample preparation for the ICP measurements, to detect major and minor elements. The dissolution yield, η (%), was calculated by eqn (1): |
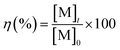 | (1) |
where [M]t and [M]0 are, respectively, the concentration of a metal M in solution at the time t of uptake and the concentration of the same metal if all the content of the coating would be dissolved in solution. As for the bromine solutions in organic solvents, solutions of 1 vol% bromine in dimethylformamide (DMF), ethanol (EtOH), ethylacetate (EtOAc), ethylene glycol (EG) and methylacetate (MeOAc) were prepared to make a screening of the best solvent in terms of both selectivity and efficiency. The screening tests were performed at room temperature for 20 minutes at 500 rpm on SmCo5 or Sm2Co17 permanent magnets. Afterwards, the dissolution rate of the metals in the best performing bromine solutions was studied by tests of 80 min at room temperature. Samples were taken at: 5, 10, 20, 30, 50 and 80 min. A solution of 2 M HNO3 was prepared by diluting properly 65 wt% HNO3 in ultrapure water. The samples of SmCo5 or Sm2Co17 in 2 M HNO3 were stirred at room temperature (RT) at 500 rpm for 210 min and samples were taken at 30, 60, 90 and 210 minutes. Metal-coated Nd–Fe–B magnets were also treated with 10 mL of the best performing bromine solutions at room temperature for 60 min with samples taken at 5, 10, 20, 30, 45 and 60 min.
Results and discussion
The solvents where chosen for their different polarity. Nickel–copper–nickel coated SmCo5, Sm2Co17 and Nd–Fe–B PMs were kindly provided by Magneti Ljubljana d.d. (Slovenia). The compositions of the magnets are reported in Table 1. The nickel–copper–nickel coating had a thickness of about 20 μm. An optical-microscope picture of its multi-layer structure is shown in Fig. 1 for SmCo5 PM. The chemical structures of the used solvents are shown in Fig. 2, together with their polarity, δ (D), and their Gutmann solvent donor number, DN (kcal mol−1), and viscosity, ν (mPa s).25,26 The DN defines the ability of a solvent to solvate cations or Lewis acids, such the metals in solution. Because of its small volume fraction, the effect of the dissolved bromine on the viscosity of the solvent was considered to be negligible. Bromine was selected because it is liquid at room temperature, thus easy to handle, and it is less toxic than chlorine gas. Screening tests were carried out on Sm–Co PMs, on which we are working with HD.5 A comparison was planned among the five 1 vol% bromine solutions in DMF, EG, EtOAc, EtOH and MeOAc, a solution of 1 vol% bromine in water and a solution of 2 M HNO3, which is a common oxidizing lixiviant in industry. However, bromine is poorly soluble in water at room temperature and this solution could not be prepared.
Table 1 Elemental composition of SmCo5, Sm2Co17 and Nd–Fe–B PMs measured by ICP-OES. For the Sm2Co17 and for the Nd–Fe–B PMs, the copper in the coating is highlighted
|
Compositiona (wt%) |
Compositions normalised to 100%. Cu in the coating, value provided by the supplier. |
Element |
SmCo5 |
Sm2Co17 |
Nd–Fe–B |
B |
0.0 |
0.0 |
1.0 |
Co |
64.9 |
49.5 |
1.0 |
Cu |
0.6 |
5.6 (0.4)b |
0.4 (0.3)b |
Dy |
0.0 |
0.0 |
2.4 |
Fe |
0.0 |
16.5 |
63.2 |
Nd |
0.0 |
0.0 |
25.3 |
Ni |
1.8 |
1.6 |
1.3 |
Pr |
0.0 |
0.0 |
5.2 |
Sm |
33.7 |
24.1 |
0.0 |
Zr |
0.0 |
2.8 |
0.0 |
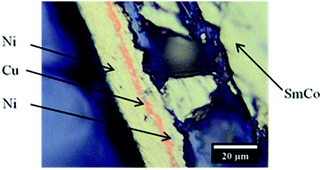 |
| Fig. 1 Optical microscopy image of the three layers of Ni, Cu and Ni coating of a SmCo5 magnet. | |
 |
| Fig. 2 Chemical structure, dipole moment δ, in D, and Gutmann's donor number DN, in kcal mol−1, of methyl acetate (MeOAc), ethyl acetate (EtOAc), ethanol (EtOH), ethylene glycol (EG) and dimethylformamide (DMF). | |
The solutions of bromine in organic solvents were regularly prepared and the tests were carried out for these and for the 2 M HNO3 solution by submerging bulk SmCo5 (0.16 cm3) and Sm2Co17 PMs (0.19 cm3) in 10 mL of each solution. The results are displayed in Fig. 3 for the solvometallurgical solutions and in Tables S1 and 2 (ESI†) for the 2 M HNO3 solution. In the case of the mineral acid, a good selectivity towards nickel over the Sm–Co alloy is shown, but it is mainly because the nickel layer is the first to be exposed to the HNO3. However, even after 210 min, no copper was detected in solution. In general, the bromine in organic solvents mixtures gave higher yields already after 20 min (Fig. 3). The poor performance of EG is surprising, despite that its chemical structure, its donor number and its polarity are very similar to those of EtOH. The contrasting results are not due to chemical differences between the solvents, but to the different physical properties, i.e. the viscosity (Fig. 2). The viscosity of EG is one order of magnitude higher than that of EtOH or DMF, which explains the lower dissolution rate of metals in the bromine–EG mixture. As for the acetates, they have a very low viscosity. Thus, the slow dissolution rate of metals in the MeOAc and EtOAc mixtures is likely attributed to the low solubility of the formed metal salts in these solvents and not to a slower diffusion rate in solution. The solubility of these metal salts is, in turn, also affected by the oxidation power of bromine in the different mixtures. Except for EG, the solvents with the highest DN interact the most strongly with the dissolved metals, Lewis acids, which explains the highest dissolution yields.27 A very high selectivity was obtained for the dissolution of coating-over-magnet-core by the developed solvometallurgical process. In fact, the magnet core was scarcely leached also when it was exposed after complete dissolution of the coating, as in case of the bromine–DMF (Fig. 3, Tables S6 and S8, ESI†). The best performing solvents were DMF and EtOH, but DMF is less preferable since it is not a green solvent.28 In fact, DMF is toxic both for the human health and the environment, but at the same time difficult to substitute, just as all other dipolar aprotic solvents.28,29
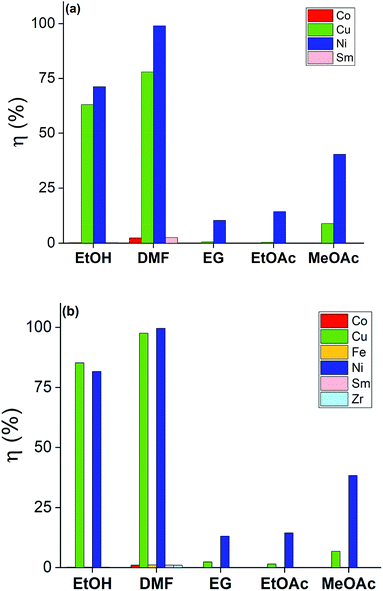 |
| Fig. 3 Screening dissolution test for the SmCo5 PMs (top) and Sm2Co17 PMs (bottom) at 20 min in 1 vol% Br2 in EG, DMF, EtOH, MeOAc and EtOAc. The recovery yields, η (%), were calculated as reported in eqn (1). | |
Next, the dissolution rate in 1 vol% bromine in EtOH and DMF was studied both for the Nd–Fe–B PMs (0.12 cm3) (Fig. 4, Tables S3 and 4 in the ESI†) and for the Sm–Co PMs (Fig. 5 and Tables S5–8 in the ESI†). In the Sm2Co17 and in the Nd–Fe–B, copper is present in both the coating and in the magnet alloy, but only the copper from the coating was considered in the calculations of the coating dissolution yields. A copper dissolution yield above 100% implied that some copper from the core started to dissolve as well. In these cases, the copper dissolution yield was rounded to 100%. The nickel–copper–nickel coating was successfully removed from all the Sm–Co PMs with a great advantage on a next HD(DR) treatment, although a η ≥ 95% would have been satisfying too. In fact, it has been reported that small amounts of impurities in the HD(DR) process do not significantly affect the magnetic properties of the recycled magnet.30 As for the Nd–Fe–B PMs, a dissolution ≥85% of the coating metals, nickel and copper, occurs in 60 min while the magnets itself is barely attacked (Tables S3 and S4, ESI†). Differently from Sm–Co PMs, the two solutions (bromine in DMF or in EtOH) did not have comparable performances. Although DMF is not a green solvent, it is the only one in which complete coating dissolution can be carried out within 60 min. The two solvents affect the stability of the metals in solution: DMF has a higher DN than EtOH and can, thus, better solvate the dissolved metals. It is worth mentioning that the dissolution proceeded slower for the Nd–Fe–B PMs than for the Sm–Co PMs. In fact, the dissolution rate is higher for the PMs with the higher volume since the solid-to-liquid ratio is higher: VSm2Co17 = 0.19 cm3 > VSmCo5 = 0.16 cm3 > VNd–Fe–B = 0.12 cm3 and ηSm2Co17 (t) > ηSmCo5 (t) > ηNd–Fe–B (t) where V is the average volume of the bulk magnets, and η(t) is the dissolution rate as function of the time, as calculated in eqn (1).
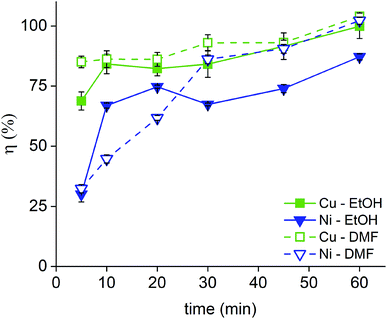 |
| Fig. 4 Dissolution rate of the Ni–Cu–Ni coating of Nd–Fe–B PMs in 1 vol% Br2 in EtOH and in 1 vol% Br2 in DMF. | |
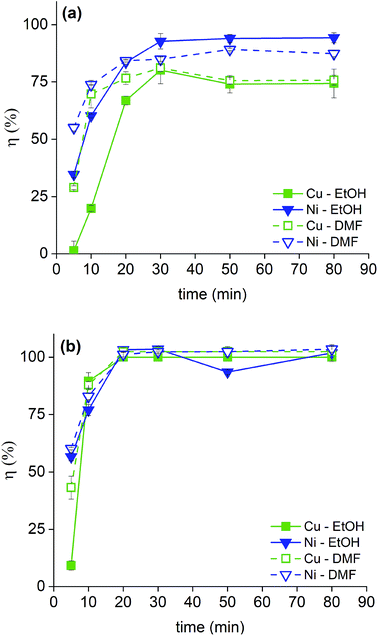 |
| Fig. 5 Dissolution rate of the Ni–Cu–Ni coating of SmCo5 PMs in 1 vol% Br2 in EtOH and in 1 vol% Br2 in DMF (a) and of the Ni–Cu–Ni coating of Sm2Co17 PMs in 1 vol% Br2 in EtOH and in 1 vol% Br2 in DMF (b). | |
As for the Sm–Co PMs, the coating metals, nickel and copper, were almost completely dissolved within just 30 min, while the alloy metals (cobalt, samarium and for the Sm2Co17 also copper, iron and zirconium) did not dissolve to more than 5 wt% of their initial content. A significant solubility of iron, but also of cobalt, in bromine solutions have been reported, but reflux conditions were applied in that case.24 Less copper than nickel dissolved in the first minutes of the process for Sm–Co PMs and this can be explained by the fact that copper is the middle layer of the coating, covered by nickel that needs to be dissolved prior to the copper dissolution. In case of Nd–Fe–B PMs, the situation was reversed: more copper than nickel dissolved in the first minutes and this might be explained with a thinner first layer of nickel for the Nd–Fe–B PMs compared to the Sm–Co PMs. The reaction between the bromine solution and the magnet core occurs as well but much slower (Tables S3–8, ESI†). A passivated layer might be formed by the oxidation of the alloy metals which impede the oxidizing dissolution of the same alloy metals underneath. A similar phenomenon has been reported in the dissolution study of metal alloys by trichloride ionic liquids.31
In Fig. 6 and 7, the progressive removal of the metallic coating from the REE PMs by bromine in organic solvents can be observed. At first, the magnet (SmCo5 or Sm2Co17, Fig. 6) is of a metallic luster because of the nickel coating, then the nickel layer starts to be attacked and the copper layer underneath becomes gradually visible, until all the nickel is dissolved. At this stage, the magnet looks of a light, shiny reddish color which clearly corresponds to the copper layer. When also the copper starts to be dissolved, the underneath nickel layer becomes visible as well. The process continues until both the copper layer and the second nickel layer are completely dissolved (in the case of EtOH and DMF). At the end, the uncoated magnet looks silver-white and dull, no longer shiny. In Fig. 7, the removal of the coating of Nd–Fe–B PMs by both 1 vol% bromine solutions in EtOH and DMF is shown as well. It is evident from this picture that the coating is fully removed after 60 min for DMF, but not for EtOH.
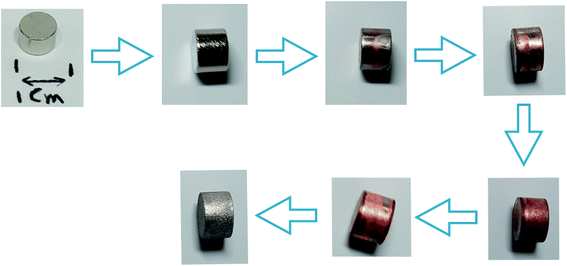 |
| Fig. 6 Progressive removal of the metallic coating from Sm–Co PMs by bromine–organic solvent mixtures. | |
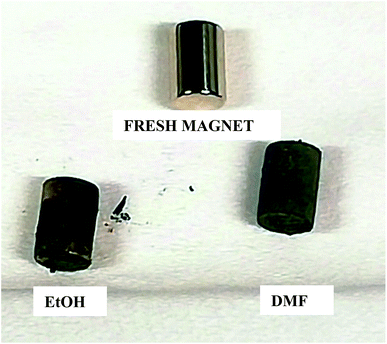 |
| Fig. 7 Progressive removal of the metallic coating from Nd–Fe–B PMs by bromine–organic solvent mixtures. | |
Conclusions
Solutions of 1 vol% bromine in EtOH and in DMF selectively remove the nickel–copper–nickel coating from both Nd–Fe–B Sm–Co PMs without leaching the magnet cores. In particular, the metallic coatings were removed in only 30 min from SmCo5 and Sm2Co17 and in 60 min from Nd–Fe–B PMs. Although the performance in 1 vol% bromine solution in DMF is the same, this last mixture is not advisable because of the higher toxicity and higher environmental impact of the DMF compared to those of EtOH. A comparison was attempted with a solution of 1 vol% bromine in water, but the bromine did not dissolve in water. Dissolution of the nickel–copper–nickel coatings in 2 M HNO3, an oxidizing lixiviant commonly used in industry, was also studied, but it did not work well. The advantages of 1 vol% bromine in organic solvents are, hence, evident: this solvometallurgical method is a fast, very selective, not labour-intensive way to remove the nickel–copper–nickel coating from Sm–Co and Nd–Fe–B, prior to PM recycling via HD. Consequently, the negative effect of the metals in the coating in the HD and HDDR processes is avoided without treating the REE PMs with high-concentrated acids or with high temperatures.
Conflicts of interest
There are no conflicts to declare.
Acknowledgements
The research leading to these results received funding from the European Community's Horizon 2020 Programme ([H2020/2014-2019]) under Grant Agreement no. 674973 (MSCA-ETN DEMETER). This publication reflects only the authors' view, exempting the Community from any liability. Project website: http://etn-demeter.eu/. The authors also want to thank Magneti Ljubljana d. d. (Slovenia) for providing the coated Sm–Co and Nd–Fe–B PMs and Dr Bieke Onghena for reviewing the manuscript.
Notes and references
- K. Binnemans, P. T. Jones, T. Müller and L. Yurramendi, J. Sustain. Met., 2018, 8, 126–146 CrossRef.
- European Commission, Directorate-General for Internal Market, Industry, Entrepreneurship and SMEs, Ad-Hoc Working Group on Defining Critical Raw Materials, 2017 list of Critical Raw Materials for the EU, Brussels, 2017 Search PubMed.
- K. Binnemans, P. T. Jones, B. Blanpain, T. Van Gerven, Y. Yang, A. Walton and M. Buchert, J. Cleaner Prod., 2013, 51, 1–22 CrossRef CAS.
- J. H. Yi, Rare Met., 2014, 33, 633–640 CrossRef CAS.
- A. Eldosouky and I. Škulj, J. Magn. Magn. Mater., 2018, 454, 249–253 CrossRef CAS.
- M. Xia, A. B. Abrahamsen, C. R. H. Bahl, B. Veluri, A. I. Søegaard and P. Bøjsøe, J. Magn. Magn. Mater., 2017, 441, 55–61 CrossRef CAS.
- A. Lixandru, I. Poenaru, K. Güth, R. Gauß and O. Gutfleisch, J. Alloys Compd., 2017, 724, 51–61 CrossRef CAS.
- M. Zakotnik and C. O. Tudor, Waste Manag., 2015, 44, 48–54 CrossRef CAS PubMed.
- A. Walton, H. Yi, N. A. Rowson, J. D. Speight, V. S. J. Mann, R. S. Sheridan, A. Bradshaw, I. R. Harris and A. J. Williams, J. Cleaner Prod., 2015, 104, 236–241 CrossRef CAS.
- I. R. Harris, A. Williams, A. Walton and J. Speight, US Pat., US 8,734,714 B2, 2014.
- M. Zakotnik, I. R. Harris and A. J. Williams, J. Alloys Compd., 2009, 469, 314–321 CrossRef CAS.
- M. Zakotnik, A. J. Williams, G. Martinek and I. R. Harris, J. Alloys Compd., 2008, 450, L1–L3 CrossRef CAS.
- M. Ueberschaar and V. S. Rotter, J. Mater. Cycles Waste Manage., 2015, 17, 266–281 CrossRef CAS.
- W. Rodewald, in Handbook of Magnetism and Advanced Magnetic Materials, John Wiley & Sons, Ltd., Hoboken, 2007 Search PubMed.
- I. Gurrappa and S. Pandian, Corros. Eng., Sci. Technol., 2006, 41, 57–61 CrossRef CAS.
- C. H. Chen, M. Q. Huang, J. E. Foster, G. Monnette, J. Middleton, A. Higgins and S. Liu, Surf. Coat. Technol., 2006, 201, 3430–3437 CrossRef CAS.
- K. Binnemans and P. T. Jones, J. Sustain. Met., 2017, 3, 570–600 CrossRef.
- Y. Marcus, Ion solvation, Wiley, New York, 1st edn, 1985 Search PubMed.
- R. P. Larsen, Anal. Chem., 1959, 31, 545–549 CrossRef CAS.
- A. R. Eberle and M. W. Lerner, Anal. Chem., 1960, 32, 1–4 CrossRef.
- G. F. Brunzie, T. R. Johnson and R. K. Steunenberg, Anal. Chem., 1961, 33, 1005–1006 CrossRef CAS.
- E. J. Violante, Anal. Chem., 1961, 33, 1600–1602 CrossRef CAS.
- R. J. Cosstick and P. C. Nancarrow, Talanta, 1978, 25, 486–488 CrossRef CAS PubMed.
- I. S. Busheina and J. B. Headridge, Analyst, 1980, 105, 600–604 RSC.
- F. Cataldo, Eur. Chem. Bull., 2015, 4, 92–97 CAS.
- D. W. Green and R. H. Perry, Perry's Chemical Engineers' Handbook, McGraw-Hill, New York, 2007 Search PubMed.
- M. Schmeisser, P. Illner, R. Puchta, A. Zahl and R. van Eldik, Chem. - Eur. J., 2012, 10969–10982 CrossRef CAS PubMed.
- K. Alfonsi, J. Colberg, P. J. Dunn, T. Fevig, S. Jennings, T. A. Johnson, H. P. Kleine, C. Knight, M. A. Nagy, D. A. Perry and M. Stefaniak, Green Chem., 2008, 10, 31–36 RSC.
- D. J. C. Constable, P. J. Dunn, J. D. Hayler, G. R. Humphrey, J. L. Leazer, R. J. Linderman, K. Lorenz, J. Manley, B. A. Pearlman, A. Wells, A. Zaks and T. Y. Zhang, Green Chem., 2007, 9, 411–420 RSC.
- A. I. Bevan, D. Zhao, I. R. Harris and A. Walton, in REPM’12 – Proceedings of the 22nd International Workshop on Rare-Earth Permanent Magnets and their Applications, Nagasaki, Japan, 2012, p. 398 Search PubMed.
- X. Li, A. Van den Bossche, T. Vander Hoogerstraete and K. Binnemans, Chem. Commun., 2018, 54, 475–478 RSC.
Footnotes |
† Electronic supplementary information (ESI) available: results of PMs dissolution rate in 2 M HNO3 and in bromine diluted in organic solvents. See DOI: 10.1039/c9ra01696a |
‡ Joint first authorship. |
|
This journal is © The Royal Society of Chemistry 2019 |
Click here to see how this site uses Cookies. View our privacy policy here.