DOI:
10.1039/C9RA01780A
(Paper)
RSC Adv., 2019,
9, 11476-11483
Biodegradable copolyester poly(butylene-co-isosorbide succinate) as hot-melt adhesives†
Received
8th March 2019
, Accepted 8th April 2019
First published on 11th April 2019
Abstract
We modified poly(butylene succinate) (PBS) with sugar-based monomer isosorbide to improve the bond strength between PBS and metal interfaces and thereby alleviate the environmental problems caused by nondegradable hot-melt adhesives. We analyzed the efficiency of different catalysts in the synthesis of poly(butylene-co-isosorbide succinate) (PBIS) copolyesters. The thermal stability, thermodynamic characteristics, and melting viscosity of PBIS copolyesters were systematically evaluated by characterization. The results indicate that isosorbide can greatly improve the bond strength of the interface between PBS and the iron plate when copolyesters are used as hot-melt adhesives.
Introduction
Hot-melt adhesives are a kind of adhesive which is heated melted, glued, and cured rapidly at room temperature to achieve bonding. Owing to their solvent-free, non-toxic, and tasteless characteristics, hot-melt adhesive are also referred to as “green adhesives”1 and have been widely used in various fields in recent years.2,3 Hot-melt adhesives mainly include ethylene vinyl acetate copolymer resin, polyethylene, random polypropylene, polyamide, polyester, and polyurethane.
Polyester-based hot-melt adhesives are thermoplastic adhesives with a high degree of polymerization and are based on polyester modified with several components. The polyester matrix is typically synthesized by polycondensation of aromatic acids such as terephthalic acid and isophthalic acid with diethylene glycol, butanediol, and hexanediol. When necessary, adipic acid and decanedioic acid are added to modify the polyester matrix by copolymerization to reduce the viscosity and melting point of the product, improve adhesive melting fluidity, and facilitate its processing and coating. Polyester contains polar functional groups, such as ether bonds and ester bonds, which exhibit good bonding properties with metals and non-metals. They are widely used in automotive, wood, textile, binding, building materials, and other industries.4–9
Jackson synthesized copolyester hot-melt adhesives from non-aromatic diols and terephthalic acid and applied them to bond metal products with epoxy resin coating on the surface, such as cans. Jackson also evaluated the effects of viscosity, glass transition temperature, crystallinity, and melting point of polyester hot-melt adhesives on the bond strength and toughness of polyester.10 Sturm and Bruning synthesized a low-melting-point polyester hot-melt adhesive from terephthalic acid, isophthalic acid, adipic acid, 1,4-butanediol and 1,6-hexanediol for bonding thermally sensitive materials. When the molar ratio of terephthalic acid/isophthalic acid/adipic acid was 80
:
10
:
10 and butanediol/hexanediol was 60
:
40, the glass transition temperature of the copolyester was 17 °C, and the melting point was 120 °C. Good peeling strength can be achieved for bonded fabrics.11
Although hot-melt adhesives contain no solvents and produce less direct pollution, all matrix resins of hot-melt adhesives are macromolecular compounds. They decompose very slowly in the natural environment. Owing to the increasing use of hot-melt adhesives, their cumulative impact on the environment has drawn attention. Various biodegradable hot-melt adhesives have been developed to solve environmental problems.12–19 Garry invented a biodegradable hot-melt adhesive that consists of 10–90% polylactic acid with a molecular weight of less than 20
000, 10–50% thermoplastic polyurethane or thermoplastic polyhydroxybutyric acid/valerate containing 5–35% hydroxyl valeric acid, 0–5% degradable ester plasticizer, and 0–5% stabilizer. This hot-melt adhesive can be completely biodegradable and widely used, particularly in disposable packaging and other biodegradable materials.12 Lewis also developed a fully biodegradable hot-melt adhesive formulation in which the crosslinking agent polycaprolactone is added to polylactic acid by polycondensation. This aliphatic polyester plays a toughening and coupling role in the adhesive.13
Poly(butylene succinate) (PBS) is a novel aliphatic polyester, which is widely known for its satisfactory biodegradability, excellent mechanical properties, and processability. It is one of the most cost-effective and industrialized available biodegradable polymer materials. PBS is a crystalline polymer with stable properties and a high molecular weight. It exhibits mechanical strength similar to that of polyolefin, polyethylene, and polypropylene. In addition, it meets the application requirements of general plastics. PBS is stable in a dry environment and completely biodegradable in soil, seawater, and compost; therefore, it can remain stable for a long storage and use period.20–23
In a previous study,24 we found that the introduction of isosorbide can improve the polarity of copolyesters. Compared with the biodegradable hot-melt adhesives reported,11–19 polylactic acid (PLA) and polycaprolactone (PCL) have good degradability, but their uncontrollable degradability leads to the destruction of bonding due to the degradation in the application process. For PBS, it has good stability as hot-melt adhesives in application. At present, the modification of PBS as hot-melt adhesives is mainly embodied in the introduction of rigid structures containing benzene ring such as terephthalic acid (PTA) to improve the interfacial bonding and cohesion strength, however, terephthalates are still produced in the degradation process. So isosorbide as a modifier has great advantages in improving the interfacial bonding performance and cohesion strength of PBS. Therefore, in the present study, we prepared a PBS copolyester containing a large amount of isosorbide by melting polycondensation. The copolyesters were characterized by gel permeation chromatography, 1H NMR, and differential scanning calorimetry. Moreover, it was used as a hot-melt adhesive to bond the iron plate, which showed desirable results.
Experimental
Materials
Succinic acid (SA, AR) was purchased from Feiyang Chemical Co. (Shandong, China). 1,4-Butylene glycol (BDO, AR) was purchased from Aladdin (Shanghai, China). Isosorbide (IS) was provided by Yuancheng (Wuhan, China). Tetrabutyl titanate (TBT, CP) and p-toluenesulfonic acid (TsOH·H2O, AR) were purchased from Nanjing Reagent Co. (Nanjing, China) and used without further purification. TBT was dissolved in anhydrous toluene to prepare 0.2 g mL−1 solution. The other solvent (AR) was obtained from Nanjing Reagent Co. and was used without further purification.
Synthesis of polyesters
The polyesters were synthesized on a 1 L polyester synthesis device (Scheme 1) by melt polymerization in two steps: esterification and polycondensation (Scheme 2). The molar ratio of succinic acid to diols was fixed at 1
:
1.2. For the esterification process, the succinic acid to diols (0.05 wt% TsOH·H2O based on total reactants as catalytic agent) react with a molar ratio of 1
:
1.2 at 220 °C under nitrogen atmosphere, and the pressure of the system was maintained at 350 kPa before distillation. At the end of esterification, 0.05 wt% tetrabutyl titanate catalyst (based on the total reactants) was added to the reaction system to start the polycondensation stage. After continuous reaction at 245 °C under vacuum of 20–100 Pa, PBIS was obtained. In the abbreviations of PBISx, x refers to the molar percentage (mol%) of IS units relative to the total diols.
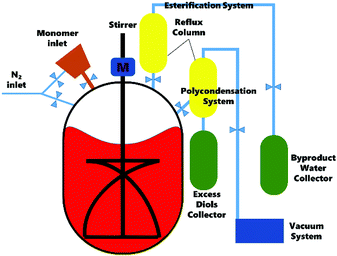 |
| Scheme 1 1 L polyester synthesis device. | |
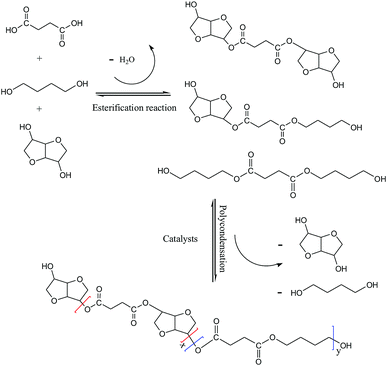 |
| Scheme 2 Synthesis process of PBIS. | |
Characterization
Molecular weight determinations were performed by GPC. Chloroform and monodisperse polystyrene were used as the eluent and standard, respectively. The concentration of sample and the flow rate of the eluent were 2.5 mg mL−1 and 1.0 mL min−1, respectively.
1H NMR was recorded using a Bruker ARX 400 NMR at 25 °C. Polyester was dissolved in chloroform, using tetramethylsilane as internal reference. The molar content of the isosorbide structural units in the copolyester was determined by the integration ratio of the proton signal peaks.
Thermogravimetric analyses were performed on TG 209 F3 (NETZSCH). The experiment was conducted under nitrogen flow at a heating rate of 10 °C min−1, within a temperature range of 30–800 °C.
Thermal behavior of polyesters were examined by DSC 200 F3 (NETZSCH). The samples were first heated to 150 °C and held at 150 °C for 5 min to eliminate the thermal history. After that, the sample was cooled to −70 °C at a cooling rate of 10 °C min−1, and finally reheated to 150 °C at heating rate of 10 °C min−1.
The attenuated total reflection infrared (ATR-IR) was measured by Fourier transform infrared spectroscopy (NicoletiS5 with ID5 accessory, ThermoFisher) from 4000 to 500 cm−1 with a resolution of 4 cm−1. The scanning frequency was 16.
The viscoelasticity of copolyesters were investigated on a Antop rheometer and temperature ranges from 110 °C to 150 °C at frequencies of 0.1 s−1.
The shear strength properties were evaluated with a universal testing machine (CMT 4204 MTS). The iron plate is first polished with sandpaper, then washed with dilute hydrochloric acid, and finally dried by nitrogen blowing. At least five measurements were conducted for each sample, and the results were reported as averages.
Results and discussion
Effect of different catalyst on polycondensation reaction
In the synthesis of polyester, the research on various catalysts has never stopped. There are many kinds of catalysts which can synthesize polyester. At present, most of the catalysts used and studied industrial production are binary element compounds: Sb and Ti. Antimony-based catalysts play a greater role in promoting polycondensation, but promoting thermal degradation reaction is smaller than that of Ti. Diantimony trioxide and ethylene glycol antimony are the most commonly used. Titanium catalysts are the most widely studied catalysis, which do not contain heavy metals and can achieve high catalytic efficiency. At present, tetrabutyl titanate is the most commonly used.
In the early work, we found that tetrabutyl titanate had the best catalytic effect on PBS synthesis, but in the process of PBIS polymerization, we found that the catalytic effect of tetrabutyl titanate became worse with the increase of isosorbide content. Therefore, we studied the synthesis of PBIS50 with three catalysts: tetrabutyl titanate, diantimony trioxide and ethylene glycol antimony. Fig. 1 has shown the reaction time consumed for each additional watt of stirring power. It can be seen that in the final stage of the polycondensation, (n-BuO)4Ti takes the longest time, and Sb2O3 takes the shortest time. We speculate that this phenomenon may be caused by the steric hindrance effect of the catalyst, so we use gauss 09 to simulate the polymer molecular chain fragments, and the results are in S1. We can found from S1 that the V-type rigid structure of isosorbide can cause the molecular chain to curl up after it is introduced into the molecular chain. In previous literatures, more researchers have report the mechanism of catalytic polycondensation. The metal in the catalyst provides the vacant orbital to coordinate with the lone pair electrons in carbonyl group, which increases the positive electricity of the carbon atom on the carbonyl, thus the oxygen atom on another carbonyl attacks the carbonyl carbon atom in the ligand and completes the polycondensation reaction. Therefore, when the molecular chain of PBIS is curled up, some carbonyl groups are wrapped in the molecular chain, which makes it difficult to coordinate with the catalyst. Moreover, a large number of molecular chains around carbonyl groups which can coordinate with catalysts also produce steric hindrance effect, which makes it difficult for catalysts with larger steric hindrance to coordinate. This corresponds to the experimental results. (n-BuO)4Ti has a large molecular configuration, and the titanium atom is located in the center of the molecule and is encapsulated by four n-butyl group. It is not easy to coordinate with carbonyl groups which have larger steric hindrance. But Sb2O3 and Sb2(OCH2CH2O)3 is different from (n-BuO)4Ti, the antimony atom of them are exposed to the outside of the molecule, which greatly enhanced the possibility of coordination with carbonyl. It can be seen from Fig. 1, that the catalytic activity of Sb2(OCH2CH2O)3 in the late stage of reaction is obviously slower than Sb2O3. This is because the molecular steric resistance of Sb2(OCH2CH2O)3 is larger than Sb2O3. Although the catalytic activity of Sb2(OCH2CH2O)3 is higher in the early stage of polycondensation, it is mainly due to the better solubility of Sb2(OCH2CH2O)3 in the system and easy to coordination in the early stage of the reaction. So we use Sb2O3 as catalyst for PBIS polymerization.
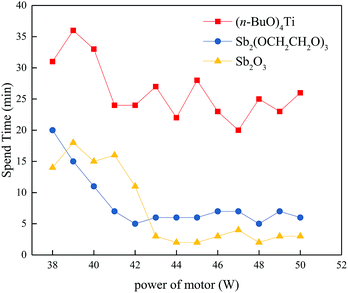 |
| Fig. 1 Reaction spend time of different catalysts for per watt. (The molar amounts of the metals are the same in polymerization of different catalysts.) | |
Structural analysis of copolyesters
PBS and PBIS were synthesized by melt polycondensation. The actual composition ratio of the copolyester largely influences its properties. Thus, the actual composition ratio of PBIS was measured by 1H NMR. The proton chemical shift peak area ratio by butylene succinate (BS) and isosorbide succinate (ISS) was intended to determine the composition ratio of the copolymer. The chemical structure of PBIS is shown in Fig. 2a. The composition ratio of PBIS was calculated by taking the 1H NMR spectrum of PBIS30 as example in Fig. 2b. The chemical shift peak Hh at 4.25 ppm and Hi at 1.73 ppm is ascribed to BDO. The high peak appearing at 2.65 ppm corresponds to the Hg protons of SA. Shifts at 5.17, 4.83, 4.47, 3.97, and 3.79 ppm belong to Hb, He, Hd, Hc, Ha, and Hf of the isosorbide unit. The results are summarized in Table 1. The actual composition of PBIS is close to that of the feed ratio when the content of isosorbide was under 50 mol%. However, when the content of isosorbide exceeds 50 mol%, the actual composition of PBIS is quite different from the feed ratio.
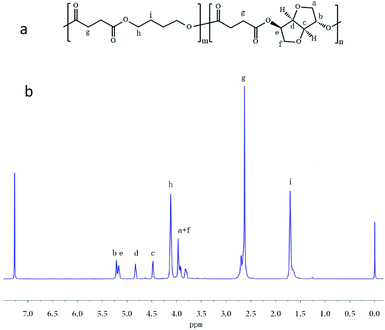 |
| Fig. 2 (a) Chemical structure of PBIS30 and (b) its 1H NMR spectrogram. | |
Table 1 Composition and molecular weight of copolyesters
Sample |
BDO/IS (feeding) |
BDO/IS (actual) |
Mn/g mol−1 |
Mw/g mol−1 |
PDI |
PBS |
100/0 |
100/0 |
88 400 |
213 400 |
2.41 |
PBIS10 |
90/10 |
91/9 |
94 500 |
201 000 |
2.12 |
PBIS20 |
80/20 |
82/18 |
85 600 |
163 000 |
1.90 |
PBIS30 |
70/30 |
72/28 |
81 500 |
132 500 |
1.62 |
PBIS40 |
60/40 |
60/40 |
77 300 |
112 300 |
1.45 |
PBIS50 |
50/50 |
52/48 |
72 100 |
107 500 |
1.49 |
PBIS60 |
40/60 |
44/56 |
70 300 |
95 400 |
1.35 |
PBIS70 |
30/70 |
35/65 |
66 900 |
87 400 |
1.30 |
PBIS80 |
20/80 |
24/76 |
63 600 |
81 000 |
1.27 |
PBIS90 |
10/90 |
16/84 |
61 200 |
75 400 |
1.23 |
For the molecular weight, the results of GPC are more accurate. It can be seen that Mn increases slightly at PBIS10 and then decreases because the isosorbide reactivity is lower than that of butanediol. When the additive amount of isosorbide is still very low, the reduction of reaction activity is not obviously; therefore the molecular weight of the copolyester showed a certain increase due the large molecular weight of isosorbide. When the additive amount increased to 10%, the decrease of reactivity became obvious, and the molecular weight of copolyester began to decrease dramatically. Furthermore, due to the low activity of isosorbide and low molecular weight, the PDI of the copolyesters gradually decreases.
Thermal properties and crystallization behaviors of copolyesters
The thermal stability of polyester is an important parameter that could avoid thermal decomposition during the processing. Fig. 3 presents the TGA of PBS and PBIS. It shows that PBS and PBIS exhibit similar thermal degradation curves under identical conditions. Figure further indicates that PBS and PBIS have no significant mass loss at 300 °C. Fig. 4 shows the parameters of the PBS and PBIS copolyester thermogravimetric curves, such as temperature at 5% weight loss (T5%) and the temperature at maximum decomposition rate (Tmax). For PBS T5% is 336 °C, and Tmax is 391 °C. For the PBIS copolyester, T5% decrease at first, then increase and finally decrease with increasing isosorbide content. Tmax is stable under 20 mol% and increases from 30 mol% to 50 mol% then remains. The reason is that isosorbide itself improves the heat resistance of the polyester and decrease the molecular weight. When the isosorbide content is under 20 mol%, because of the decreasing molecular weight and wide molecular weight distribution width, the low molecular weight part begin to decompose at lower temperature. Furthermore, the effect of improving heat resistance of isosorbide is not obvious when its content is low, resulting in a downward trend of T5% and Tmax remains non-changes. When the additional isosorbide content exceeds the threshold of 30 mol%, the increased heat resistance of isosorbide plays a major role. When the isosorbide content exceeds 60 mol%, its effect on the decreasing molecular weight of the copolyester plays a major role, both T5% and Tmax decreased slightly.
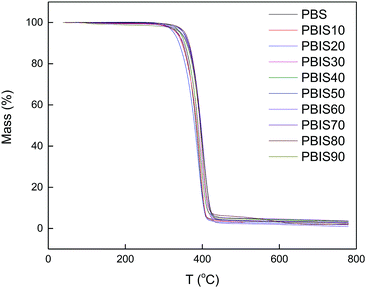 |
| Fig. 3 PBS and PBIS copolyester thermogravimetric curves. | |
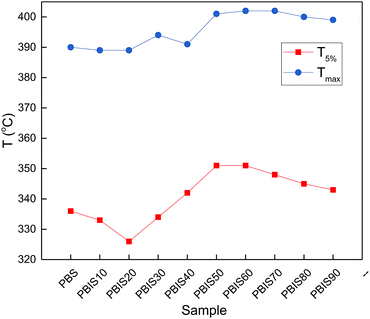 |
| Fig. 4 Parameters of the PBS and PBIS copolyester thermogravimetric curves. aT5%: temperature at which 5% weight loss was observed. bTmax: temperature for maximum degradation rate. | |
The glass transition temperature, and melting temperature of polymers are very important parameters for industrial polymer processing. Differential scanning calorimetry can intuitively express these parameters. Isosorbide is a type of diol with V-type bicyclic structure. Introducing isosorbide into the molecular chain will improve the rigidity of the copolyester, while at the same time, reducing the crystallinity of the copolyesters. Fig. 5 shows the DSC curves of PBS and copolyesters modified by isosorbide after eliminate thermal history. The curve shows PBS, PBIS10, and PBIS20 have obvious melting peak, and melting point for PBS is 114 °C and decreased with the increasing content of isosorbide for PBIS20 is 103 °C. There is no obvious melting peak in DSC curve when the content of isosorbide exceed 30%, which means polyesters become amorphous polymers. The introduction of isosorbide unit leads to increase the rigidity of molecular chain of copolyesters, which limits the ability of free movement of polymer chain. Therefore, the glass transition temperature of copolyester increases from the −28 °C for PBS to 61 °C for PBIS90.
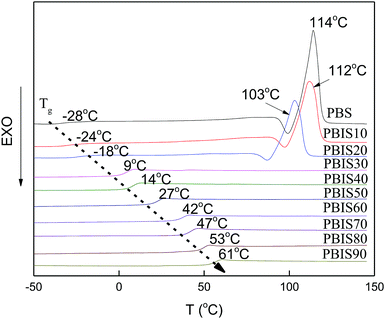 |
| Fig. 5 DSC curves of copolyesters. | |
Attenuated total reflectance infrared of copolyesters
ATR-IR can overcome the difficulties of traditional transmission spectroscopy which cannot prepare samples, or the sample preparation process is very complex, difficult and the result is not ideal. It has been widely used in structural analysis of polymer materials such as plastics, fibers, rubber, coatings, and adhesive. From the ATR-IR spectrum of Fig. 6, it can be seen that the carbonyl characteristic peaks of copolyesters are very obvious, and there are some differences among different copolyesters. When the content of isosorbide is below 20%, the copolyester is a crystalline polymer which has been proven by DSC results. Because of the tight stacking of molecular chains, the p–π conjugation of C
O bond is affected. The absorption peak of C
O shifts to low frequency at 1714 cm−1. When the content of isosorbide exceeds 30%, the copolyester changes to amorphous polymers, the steric hindrance effect of C
O bond shifting to low frequency has disappeared, and the absorption peak of C
O is 1730 cm−1. The absorption peak of C–O–C bond on isosorbide ring structure at 1092 cm−1 is increased with the increase of isosorbide content. The absorption peak of C–O in primary alcohols is at 1047 cm−1 when the isosorbide content is low, the main end group of copolyester is butanediol. While the absorption peak of C–O in secondary alcohols at 1020 cm−1 is caused by terminal group of isosorbide after the increase of isosorbide.
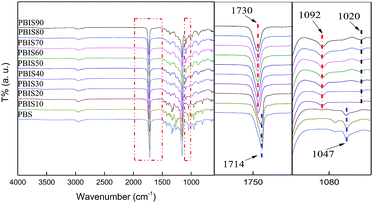 |
| Fig. 6 ATR-IR spectrum of copolyesters. | |
Rheological properties of copolyesters
Rheological analysis can provide the characteristics of viscosity and its influencing factors. Machining of macromolecule materials is usually conducted at the flowing state. Therefore, it is necessary to study the viscosity and its variation law. Rheological analysis can provide corresponding parameters for theoretical guidance. Fig. 7 shows the rheological curves of PBS and PBIS for varying temperatures. Fig. 7a shows that the viscosity of copolyesters will decrease with increasing temperature. We can found that the copolyester is a temperature sensitive material, and its viscosity decreases rapidly with the increase of the temperature. Furthermore, when the temperature exceeds 100 °C, the difference of viscosity between copolyesters becomes slight. Fig. 7b shows the magnification between 120 °C and 150 °C in Fig. 7a. The viscosity of copolyesters increases first and then decreases with the increase of isosorbide content. This is the result of the interaction between the increase rigidity of molecular chains and the decrease of the molecular weight, and the viscosity of PBIS60 is the highest at the same temperature. In terms of processing, all copolyesters can change the fluid viscosity by adjusting the temperature according to the processing equipment.
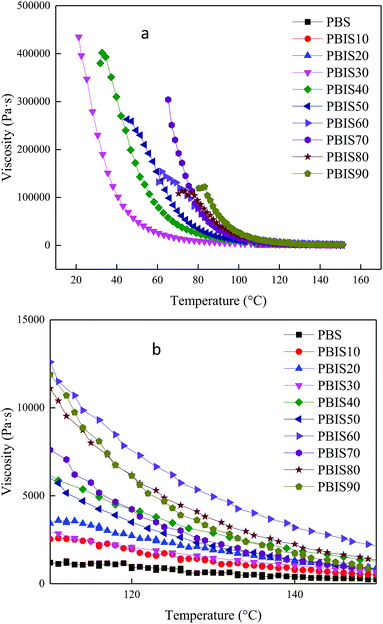 |
| Fig. 7 (a) Rheological properties of copolyesters; (b) magnification between 120 °C and 150 °C. | |
Shear strength of hot-melt adhesives
Copolyesters are applied to bond iron plates and the shear strengths of the Fe–copolyester–Fe are measured following the procedure described in the Experimental section. Fig. 8 has shown the performance properties of the PBS and PBIS hot-melt adhesive. The literature has reported isosorbide could enhance the surface polarity of the polyesters. Therefore, PBIS has better bonding performance than PBS for iron plate. We can found that the shear strength increases with the isosorbide content. However, there is a significant decline at PBIS30. This is because when isosorbide content reaches 30%, the polymer is transformed into amorphous polymer and the Tg of PBIS30 is lower than the ambient temperature when measured. At this time, the copolyester is in a rubber-like state, and the slip between the molecular chains can easily occur. Moreover, although the Tg of PBS, PBIS10 and PBIS20 is also lower than the ambient temperature, they are crystalline polymers which crystallization between molecular chains can increase the interaction fore between molecules and greatly enhance their cohesion. When the content of isosorbide exceeds 40%, the Tg of copolyesters is over the ambient temperature and it has good cohesive at the glass state. Furthermore, the main destructional forms of colloid is interface failure, which is due to the cohesion between molecules is greater than the adhesive between colloid and iron plate. When the isosorbide content reaches 80%, the shear strength is 8.0 ± 0.3 MPa reaches the maximum. The destructional forms of colloid changes from interface failure to cohesive failure. This mainly due to the decrease of molecular weight. The results indicate that isosorbide can enhance the interaction of the copolyester with the iron plate, and the copolyesters can be good used as hot-melt adhesive.
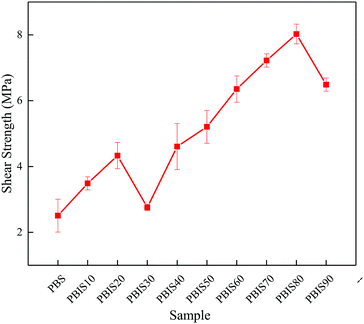 |
| Fig. 8 Shear strength of copolyesters hot-melt adhesive. | |
Biodegradation of hot-melt adhesives
We choose PBIS10 to verify the degradation of copolyesters. First, PBIS10 was pressed into a 1 mm thick film and then placed it in the natural water (Wuxi, China). The surface morphology of PBIS10 film in natural water for 0, 12 and 29 days was analyzed by scanning electron microscopy (SEM). From the Fig. 9, we can found that the PBIS10 film has a flat surface, and when it is placed in natural water for 12 days, the surface shows several volcanic protrusions and the protrusions gradually increase after 29 days, and the interior shows fragmentation. This indicates that the degradation process of PBIS10 is gradually expanding from some points on the surface. This is because bacteria and microorganisms in natural waters attach to a certain point on the surface and begin to degrade copolyesters from this point. The prominence seen in the SEM image of Fig. 9 is the attachment point of bacteria and microorganisms on the surface. Therefore, the PBIS copolyesters hot-melt adhesives can be biodegraded in nature.
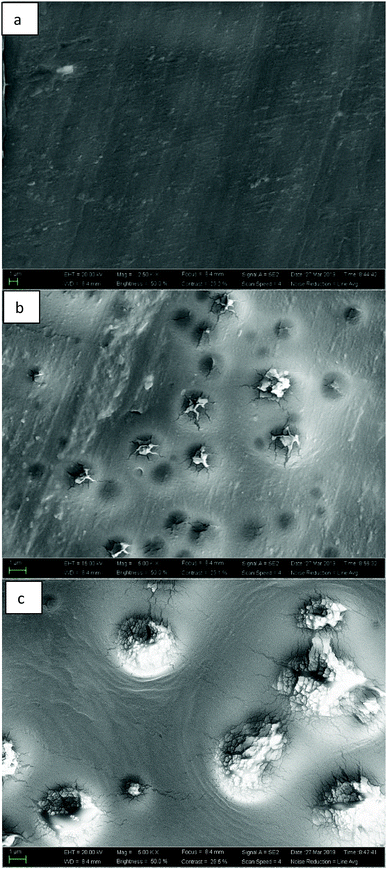 |
| Fig. 9 Surface SEM pictures of PBIS10 after biodegradation. (a) 0 day, (b) 12 days, (c) 29 days. | |
Conclusions
In this study, PBS and poly(butylene-co-isosorbide succinate) (PBIS) were prepared by melt polycondensation. Isosorbide, a sugar-based glycol containing a V-type bicyclic structure and a rigid structure, was used. On the basis of the experimental results combined with theoretical findings, antimony trioxide exerts the best catalytic effect on synthesized copolyesters. Therefore, the introduction of isosorbide can inhibit the crystallization of polyesters. When the isosorbide content reaches 30%, the copolyester translates into amorphous polymers. The higher the isosorbide content, the lower the crystallinity of polyester. With an increase in isosorbide content, the molecular weight of copolyester decreases.
The introduction of isosorbide can effectively improve the adhesion of copolyester to the interface of the iron plate. When the isosorbide content is 80%, the shear strength of the iron plate bonded with a hot-melt adhesive is 8.0 ± 0.3 MPa, and the Tg of PBIS80 is 53 °C, which indicates that it can melt at temperatures above 53 °C, and its use temperature is below 53 °C.
For PBIS copolyester hot-melt adhesive, isosorbide content can be adjusted according to the required interfacial bonding properties. It can be used for bonding in dry environment, such as splice the circuit boards and paper. At present, we have applied PBIS20 to paper bonding.
Conflicts of interest
There are no conflicts to declare.
Acknowledgements
This work was financially supported by Wuxi HIT New Material Research Institute CO., LTD (BM2017006).
Notes and references
- W. Li, L. Bouzidi and S. S. Narine, Ind. Eng. Chem. Res., 2008, 47, 7524 CrossRef CAS.
- H. Dahmane, Int. J. Adhes. Adhes., 1996, 16, 43 CrossRef CAS.
- R. Tout, Int. J. Adhes. Adhes., 2000, 20, 269 CrossRef CAS.
- M. Stolt, M. Viljanmaa and A. Södergård, J. Appl. Polym. Sci., 2004, 91, 196 CrossRef CAS.
- J. Comyn, Int. J. Adhes. Adhes., 1998, 18, 247 CrossRef CAS.
- L. Wang and F. Iida, IEEE ASME Trans. Mechatron., 2013, 18, 1397 Search PubMed.
- X. Wang, W. Lu and Y. Chen, Chem. Eng. J., 2018, 335, 82 CrossRef CAS.
- Z. Zhang, D. J. Macquarrie and J. H. Clark, RSC Adv., 2014, 4, 41947 RSC.
- X. Lu, H. Zhao and C. Feng, RSC Adv., 2017, 7, 36382 RSC.
- W. J. Jackson Jr, T. F. Gray Jr and J. R. Caldwell, J. Appl. Polym. Sci., 1970, 14, 685–698 CrossRef.
- K. G. Sturm and K. Bruning, Partially crystalline copolyesters useful as adhesives, U.S. Patent, 4,094,721, 1978-6-13.
- G. J. Edgington and C. M. Ryan, Biodegradable/compostable hot melt adhesives comprising polyester of lactic acid, U.S. Patent 5,753,724, 1998-5-19.
- D. N. Lewis, G. Schutte, H. Westerhof, et al., Environmentally degradable polymeric compounds their preparation and use as hot melt adhesive, U.S. Patent 7,465,770, 2008-12-16.
- M. Viljanmaa, A. Södergård and P. Törmälä, Int. J. Adhes. Adhes., 2002, 22, 447 CrossRef CAS.
- M. Viljanmaa, A. Södergård and P. Törmälä, Int. J. Adhes. Adhes., 2002, 22, 219 CrossRef CAS.
- M. Viljanmaa, A. Södergård and R. Mattila, Polym. Degrad. Stab., 2002, 78, 269 CrossRef CAS.
- Y. Poirier, D. E. Dennis and C. Nawrath, Adv. Mater., 1993, 5, 30 CrossRef CAS.
- S. Li and S. McCarthy, Biomaterials, 1999, 20, 35–44 CrossRef CAS PubMed.
- C. Gu, D. A. Hauge and S. J. Severtson, Ind. Eng. Chem. Res., 2014, 53, 17376–17385 CrossRef CAS.
- S. Y. Hwang, E. S. Yoo and S. S. Im, Polym. J., 2012, 44, 1179 CrossRef CAS.
- J. Xu and B. H. Guo, Biotechnol. J., 2010, 5, 1149 CrossRef CAS PubMed.
- R. T. Duan, Q. X. He, X. Dong, D. F. Li, X. L. Wang and Y. Z. Wang, ACS Sustainable Chem. Eng., 2015, 4, 350 CrossRef.
- N. Jacquel, R. Saint-Loup, J. P. Pascault, A. Rousseau and F. Fenouillot, Polymer, 2015, 59, 234 CrossRef CAS.
- D. Qu, F. Zhang and H. Gao, Chem. Res. Chin. Univ., 2019, 35, 345 CrossRef.
Footnote |
† Electronic supplementary information (ESI) available. See DOI: 10.1039/c9ra01780a |
|
This journal is © The Royal Society of Chemistry 2019 |
Click here to see how this site uses Cookies. View our privacy policy here.