A sequential membrane bioreactor followed by a membrane microalgal reactor for nutrient removal and algal biomass production
Received
25th September 2019
, Accepted 12th November 2019
First published on 13th November 2019
Abstract
A hybrid process combining a single compartment aerobic membrane bioreactor (MBR) and a membrane microalgal reactor (MMR) was evaluated for nutrient removal and microalgal biomass production. When operated without biomass extraction, the microalgal biomass in the MMR reached 920 mg L−1 on day 18 and then collapsed, rendering nutrient removal ineffective. Stable operation of the MMR was achieved by regular biomass extraction (i.e. 1/30 of the microalgal biomass in the reactor daily). The biomass production at steady state was approximately 26 g m−3 d−1. The NO3− and PO43− uptake values by microalgae were 4.0 ± 1.1 and 1.5 ± 0.9 g m−3 d−1, respectively. A facile flocculation and separation technique capable of recovering 98% microalgal biomass was demonstrated. Although the hybrid process can significantly enhance nutrient removal and biomass production, further research is needed to intensify the microalgal growth rate. At the current microalgal growth rate, a large MMR volume (37 times that of the MBR) is necessary for synchronous operation.
Water impact
The application of microalgae to simultaneously remove nutrients and produce valuable biomass from wastewater is a stepping stone to water sustainability. This study presents a method combining an aerobic membrane bioreactor and a membrane microalgal reactor to provide excellent nutrient removal and biomass generation. The results suggest that a synchronous operation can be achieved with high volume of the membrane microalgal reactor.
|
1. Introduction
Membrane bioreactors (MBRs) are a hybrid between biological treatment and membrane separation.1,2 In these biological reactors, microorganisms utilise dissolved organic carbon and oxygen to reproduce. The membrane then separates and retains microorganism biomass in the reactor to provide clean effluent free of suspended solids and bacteria. A simple MBR with a single aerobic stage can effectively remove dissolved organic carbon (90–95%) from wastewater,3,4 but not nitrogen and phosphorus.
To meet nutrient discharge standards, complex biological processes with multiple redox stages are necessary. For example, biological nitrogen removal involves both aerobic (for nitrification) and anoxic (for denitrification) stages to convert ammonia to nitrate and then to nitrogen gas. Yet, biological nitrogen can only achieve 75% nitrogen removal under optimum conditions.3,5 Moderate biological phosphorus removal (ca. 60–70%) is also possible under alternating aerobic and anaerobic conditions to enrich a specific microbial group called polyphosphate-accumulating organisms.5,6 Biological phosphorus removal is a complex process that is energy intensive and difficult to optimise. Indeed, many large scale MBR plants have been built and commissioned over the past few years, but the high cost of nutrient removal remains a major limitation.7–9 Additional processes, e.g. physical or chemical treatments, are often used to manage nutrients, resulting in an increase in the cost of wastewater treatment.4
Nutrients (i.e. nitrogen and phosphorus) are essential for microalgae growth. Previous studies have shown that microalgae can effectively assimilate a variety of nitrogen (e.g. ammonia, nitrate, urea and peptone)10–12 and phosphorus-bearing compounds.13–15 Microalgae have also been successfully cultivated in non-sterile environments such as wastewater13,14,16,17 with batch studies showing effective nitrogen and phosphorus removal.18,19 Microalgal biomass is also a renewable feedstock for the production of animal feed, biofuel, and a range of biochemicals.20–23 Therefore, combining the use of MBRs with microalgae cultivation is potentially an environmentally sustainable solution to (i) obtain high effluent quality without the use of complex processes or chemicals, (ii) enable beneficial reuse of residual nutrients from the effluent, and (iii) produce valuable microalgal biomass.24–26 However, to date, there have been only a few studies examining the integration of these two processes. Key technical considerations including (a) the microalgal biomass production rate and nutrient removal efficiency, (b) separation of microalgae from the final effluent and biomass harvesting, and (c) synchronization of MBR and microalgae processes have been recommended in future studies to enhance the readiness of the coupled MBR and MMR process.24,25
This study aims to assess the performance of a combined MBR and membrane microalgae reactor (MMR), focusing on answering initial questions about nutrient removal efficiency, microalgae harvesting, and reactor synchronization. The microalgal biomass growth rate in MBR effluent as well as the microalgal flocculation efficiency using cationic polyacrylamide polymers will be determined. The results of this study will provide important insights into the feasibility of incorporating microalgae into the MBR technology and wastewater treatment processes.
2. Materials and methods
2.1 Microalgae strains and growth conditions
The freshwater green algae Chlorella vulgaris (CS-41) was obtained from the Australian National Algae Culture Collection, CSIRO Microalgae Research (Hobart, TAS, and Australia). The culture was maintained in the Climate Change Cluster (C3) culture collection at the University of Technology Sydney in freshwater MLA media (Algaboost; Wallaroo, SA, Australia). Seed cultures were grown to the early stationary phase in 1 L Schott bottles, bubbled with air at ∼20 °C and ∼100 μmol photons per m2 s light intensity in a 16
:
8 hour light
:
dark cycle. C. vulgaris was selected due to its high photosynthetic efficiency and high productivity.20
2.2 Membrane bioreactor
A laboratory scale MBR system was employed in this study. The system consisted of an acrylic reactor with an active volume of 3 L, a pressure sensor, an air supply compressor, and influent and effluent pumps. A hollow fiber membrane module was made in the laboratory of Centre for Technology in Water and Wastewater, University of Technology Sydney, Australia. The module comprised 40 PVDF fibers (supplied by Evoqua Water Technologies, Australia) of 30 cm in length and 0.04 μm in pore size. The effective surface area of the membrane module was approximately 0.04 m2. The module was plotted using epoxy resin (Selleys Araldite Ultra Clear). The membrane module was submerged in the reactor and operated in 9 min suction and 1 min rest cycle mode with an average flux of 6.3 L m−2 h−1. The reactor was aerated at an air flow rate of 100 L min−1via two diffusers located at the bottom of the reactor. This resulted in a dissolved oxygen concentration of 3 to 6 mg L−1. Transmembrane pressure was continuously monitored using a high resolution pressure sensor (±0.1 kPa) (Cole-Parmer Pressure meter) to confirm that no significant membrane fouling has occurred during the experimental period. The transmembrane pressure was 35.2 kPa at the end of the experimental period, thus no membrane cleaning or backwashing was performed.
Activated sludge taken from an aeration tank of a municipal wastewater treatment plant (NSW, Australia) was used to seed the MBR. The hydraulic retention time was set at 24 h. Apart from samples for mixed liquor suspended solid analysis, no sludge was withdrawn from the MBR at any stage of this study (i.e. 150 days), and thus the sludge retention time was close to 150 days. The mixed liquor suspended solids fluctuated in the range of 2.9 to 6.3 mg L−1 (5.06 ± 1.02, n = 45). The MBR was kept at laboratory room temperature (i.e. 22–23 °C). The synthetic feed contained per liter: glucose (1.83 g), NH4Cl (30 mg), KH2PO4 (340 mg), K2HPO4 (600 mg), MgSO4 (270 mg), FeSO4 (10 mg), and 10 mL of 100× trace element solution (0.35 mg ZnSO4·7H2O, 0.21 mg MnSO4·H2O, 2.1 mg H3BO4, 1.4 mg CoCl2·2H2O, 0.07 mg CuCl2·2H20, 0.1 mg NiSO4·6H2O, and 0.21 mg Na2MoO4·2H2O) as described previously.1 The synthetic feed had an 80
:
5
:
1 ratio of COD, total nitrogen and total phosphorus (COD
:
TN
:
TP) as a representative composition of municipal wastewater. MBR effluent was collected daily into a 5 L container and pumped to the membrane microalgae reactor at a designed flow rate of 1.5 mL min−1 (section 2.3).
2.3 Membrane microalgae reactor
A laboratory scale MMR system was used. The system consisted of a glass-cylindrical tank with an active volume of 1.5 L, an air supply compressor, and influent and effluent pumps. Another membrane module (same as that described in section 2.2) was submerged in the photobioreactor. The membrane module was operated at an average flux of 3.15 L m−2 h−1. The reactor was aerated at an air flow rate of 100 L min−1via a diffuser located at the bottom of the reactor.
The MMR was started by diluting the algae culture (section 2.1) at a ratio of 1
:
50 (v/v) with the MBR permeate to a total of 1.5 L. The MMR was kept at room temperature (i.e. 22–23 °C) and illuminated on the side at ∼125 μmol photons per m2 s light intensity in a 16
:
8 hour light
:
dark cycle. The MBR permeate (1.5 L) was continuously supplied to the MMR at a flow rate of 1.5 mL min−1, resulting in a hydraulic retention time of 24 h. 50 mL of biomass solution (i.e. 1
:
30 of the biomass in the reactor) was removed from the MMR every day at midday during operation and referred to as “biomass extraction” in the text, equivalent to a cell retention time of 30 days.
2.4 Analytical methods
2.4.1 Organic carbon and nutrient measurements.
The total organic carbon (TOC) of the MBR feed and permeate and the MMR permeate was measured by using a total organic carbon analyser (Multi N/C 3100, Analytik Jena, Germany). The instrument was calibrated using potassium hydrogen phthalate at a concentration range of 1 to 100 mg L−1.
Nitrite (NO2−), nitrate (NO3−) and phosphate (PO43−) in the MBR and MMR permeate were measured by using ion chromatography (Thermo Fisher, Australia). The system was equipped with a Dionex AS-AP autosampler and a Dionex AS19 IC column (7.5 μm pore size, 4 mm diameter and 250 mm length). The sample injection volume was 10 μL. The sample was delivered in an isocratic mode with the hydroxide gradient (time [min]: concentration [mM]) (0–10: 10; 10–25: 45; 25–27: 45; 27–30: 10; 31 stop run).
2.4.2 Microalgal growth.
The optical density and dry weight of the microalgal culture were determined daily using a UV spectrophotometer (UV 6000 Shimadzu; Ermington, NSW, Australia) at a wavelength of 680 nm and by gravimetric analysis, respectively, to assess microalgal growth. For optical density analysis, 2 mL of homogeneous microalgae cell suspension was transferred into a cuvette to measure the optical density. For gravimetric analysis, 50 mL of microalgal cell suspension was filtered through a 1.1 μm pre-weighed glass fiber filter. The resulting fiber with microalgae deposition was dried at 60 °C to a constant mass over 4 h. A linear regression coefficient (R2) of 0.96 was obtained between the optical density and dry weight biomass.
2.4.3 Microalgal biomass harvesting.
Microalgal biomass was harvested by flocculation with two high charge (>80% charge) and high molecular weight (>15 megadalton) cationic polyacrylamide polymers. These polymers are BASF Zetag 3815 (SNF Pty Ltd; Corio, VIC, Australia) and Flopam FO 3808 (SZF Shanghai, China). A stock solution of the flocculant (0.4% w/v) was prepared in Milli-Q water with continuous mixing at 100 rpm for 1 h and stored at room temperature and used within 1 day of preparation.
The microalgal suspension and flocculant solution were gently mixed for one minute and then allowed to settle for another minute. An aliquot (10 mL) of the culture in the bottle was pipetted from a height of one- and two-thirds from the bottom for evaluating the flocculation performance.
The flocculation efficiency was calculated based on the change in the optical density at a wavelength of 680 nm before and after each flocculant addition, as shown in the following equation:
where ODi and ODf are the optical densities of the culture before and after flocculant addition. Each polymer dose was repeated three times.
2.4.4 Membrane microalgae reactor calculation.
The MMR system should be synchronized to remove residual nutrients in the MBR effluent. However, the uptake rate of nutrients by microalgae can be slow, requiring a larger reactor volume. This reactor volume was calculated based on the nutrient concentration of the MBR effluent and the nutrient uptake rate by the microalgae during one day of operation, as shown in the following equation:
MMR volume (L) = (C01 − C0)/U |
where, C0 is the nutrient concentration in the MBR effluent (mg L−1), C1 is the nutrient concentration in the MMR effluent (i.e. with 100% removal) and U is the nutrient uptake by microalgae per 1 L volume.
3. Results and discussion
3.1 Bulk organic removal by the MBR
The aerobic MBR system consistently removed over 99% of organic carbon, resulting in a final total organic carbon concentration in the MBR effluent of ca. 0.5–6.5 mg L−1 (Fig. 1). This result is likely due to the presence of the high biomass level (i.e. mixed liquor suspended solids of 5.06 ± 1.02 g L−1, n = 45) and aerobic conditions (i.e. dissolved oxygen of 3–7 mg L−1) in the reactor. Under aerobic conditions, activated sludge microorganisms (i.e. heterotrophs) can breakdown organic carbon for their growth and maintenance. These microorganisms oxidize a wide range of organic compounds and are essential in the removal of carbonaceous materials.3
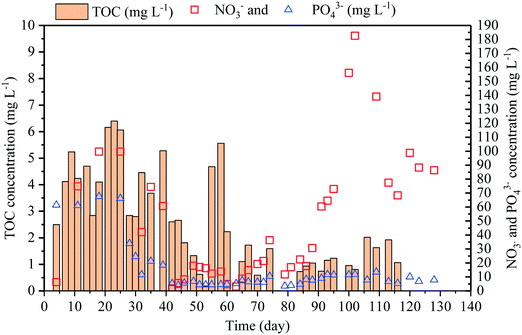 |
| Fig. 1 TOC and nutrient concentrations in MBR effluent. The MMR was coupled with the MBR i.e. MMR operated in batch mode (“without biomass extraction”) from day 40 to 75 and continuous mode (“with biomass extraction”) from day 80 to 120. | |
Efficient removal of organic carbon by the aerobic MBR limits the carbon source available for bacterial growth in the MMR. Keeping the bacterial level low in the MMR facilitates the growth of microalgae by reducing competition for nutrients and/or preventing bacterial predation on algae biomass. As such, initial removal of organic carbon and bacteria is often required for microalgae cultivation using wastewater.27 A low organic carbon content also promotes CO2 uptake by microalgae, providing additional benefit to the MMR. The aerobic MBR in this study offers a solution for both organic carbon and bacteria removal.
The effluent from the aerobic MBR system could be directly used for microalgal cultivation without any supplements (Fig. 1). During aerobic respiration, microbes in the MBR produce up to 182 mg L−1 nitrate (NO3−) and 66.3 mg L−1 phosphate (PO43−). The concentrations of ammonia and nitrite were negligible, suggesting full nitrification in the aerobic MBR. The nitrate and phosphorus concentrations fluctuated over the operation period (Fig. 1). This variation represents a realistic situation in a full-scale system, resulting in N/P ratios between 6.3 and 14.4, with the mean value of 10.3. The wastewater N/P ratio is an important parameter for microalgal growth. It has been suggested that the optimal N/P ratio for microalgae cultivation is between 7.5 and 9.6 as it represents the N/P ratio in microalgal biomass.25,28 The N/P ratio of the effluent in this study was close to the requirement for C. vulgaris16,25 and was in the optimal range for a number of microalgal species.13
3.2 MMR without biomass extraction
The growth of microalgae in the MMR was monitored over time (Fig. 2a). The initial lag-phase lasted 8 days. This long lag-phase might correspond to the adaptation of the microalgae to the new culture medium (from MLA media to MBR effluent). After this phase, microalgae grew rapidly and reached a stationary phase after 18 days of operation at a biomass concentration of 920 mg L−1. The obtained biomass concentration was similar to the reported biomass concentration from batch photobioreactor and continuous photobioreactor studies using a microalgal culture medium.14 This result confirms the feasibility of using MBR effluent for microalgal cultivation. However, prolonged operation periods resulted in the collapse of the microalgae culture. At day 20, the biomass in the MMR dropped to 800 mg L−1 and continued to decrease to 250 mg L−1 at day 27 (Fig. 2a). Reports on ecological collapse of microalgae culture in the MMR configuration are scarce in the literature. This is because most photobioreactor studies were only conducted over a short period.25,28 To address this issue, continuous operation of the MMR (noted as “MMR with biomass extraction” in this study) was investigated.
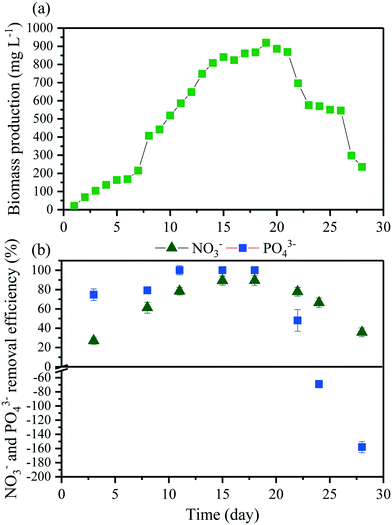 |
| Fig. 2 Biomass production (dry weight) (a) and nutrient removal efficiency (b) by the MMR without biomass extraction. Values and error bars are the mean and standard deviation of duplicate measurements. | |
NO3− and PO43− removal efficiency values of 75% and 99%, respectively, were achieved at day 11 and remained stable till day 20 (Fig. 2b). This achievement concurred with the microalgae growth phase in the reactor. The removal efficiencies correspond to uptake rates of 15.9 ± 1.6 mg L−1 for NO3− and 4.3 ± 0.9 mg L−1 for PO43− (n = 5), respectively. The uptake of nutrients through microalgal assimilation into biomass which is retained by the membrane is a major nutrient removal mechanism by the MMR. It is noted that the MF membrane in this study does not retain soluble NO3− and PO43− ions in the solution. Previous studies have also suggested that the microalgal assimilation is important for nutrient removal.14 Thus, maximizing microalgal growth is the solution to enhance nutrient removal in the MMR. In batch mode, the algal biomass has to be harvested in the late exponential, beginning of the stationary phase to avoid the release of NO3− and PO43− into the growth medium due to cell lysis.
3.3 MMR with biomass extraction
3.3.1 Biomass production and nutrient uptake.
Periodic extraction of biomass improved microalgal growth in the MMR (Fig. 3a). The biomass in the MMR rapidly increased from 60 to 730 mg L−1 within 15 days. The steep increase in biomass in the reactor is likely due to its higher production rate than that of biomass in the 50 mL microalgal culture extracted daily at this stage. There was a short lag phase of 2 days, indicating the adaptation of C. vulgaris to the MBR effluent (i.e. without adaptation, the lag phase was 8 days). After this period, the biomass production fluctuated in the range of 730–900 mg L−1. The daily biomass withdrawal could improve the growth of the remaining algae by reducing light and carbon limitations as seen with the high cell density culture.29 Overall, the average volumetric biomass productivity in the MMR was 25.8 ± 13.5 g m−3d−1 generating 1.29 ± 0.69 mg of dried biomass (i.e. from 50 mL microalgal suspension) harvested per day, using polymers with a 98% harvesting efficiency (section 3.3.2).
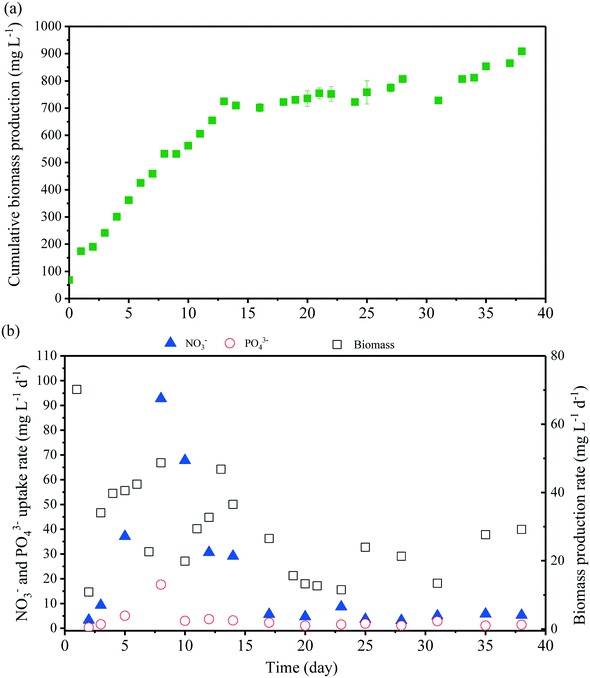 |
| Fig. 3 Cumulative biomass production in dry weight (a), nutrient removal efficiency and biomass production rate (b) by the MMR with biomass extraction. Values and error bars are the mean and standard deviation of duplicate measurements. | |
As noted in section 3.2, nutrient removal in the MMR is governed by microalgal assimilation. Accordingly, the consumption of NO3− and PO43− was high in the first 15 days and then stabilized with an uptake rate of 4.0 ± 1.1 and 1.5 ± 0.9 g m−3 d−1 (n = 8) for NO3− and PO43−, respectively. When assimilated by the cells, phosphorus is used in energy transfer and formation of cell membranes and nucleic acid metabolism.10 This process was found to be slow, affecting the nutrient uptake and removal in the MMR. Although previous studies reported the variable removal efficiency, the differences in microalgal species, cultivation time, and batch and continuous operations as well as the initial nutrient concentration make the direct comparison with literature data impossible.25,27,28 For example, Chokshi et al.30 achieved 87% removal of phosphorus by C. pyrenoidosa from dairy industrial wastewater after 10 days of batch culture. This removal was achieved in association with the increase in biomass production and cultivation time. The results from this study suggested that the nutrient uptake rate was not proportional to the increase of the nutrient supply. Therefore, the reactor volume of the MMR should be larger to meet the requirement of nutrient removal.
3.3.2 Biomass harvesting.
The microalgal biomass was effectively harvested from the reactor using flocculant cationic polyacrylamide (Fig. 4). With a flocculant dose of 24 mg g−1 dry weight, the optical density OD680 decreased by 98%. Previous studies have established 90% reduction in optical density as the benchmark for effective flocculation for microalgae harvesting.31,32 Moreover, the flocculant dose was relatively small in this study in comparison to previous reports.33–35 This is likely due to the high cationic charge density (>80%) of the polymer that supports the charge neutralization of the negatively charged microalgal cells. The efficiency of microalgal harvesting in this study allows for 98% biomass collection as well as the safe discharge of effluent (i.e. prevention of introduction of microalgal species to aquatic environments).
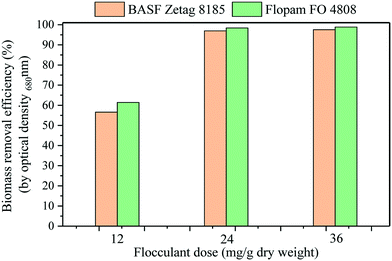 |
| Fig. 4 The effect of BASF Zetag 8185 and Flopam FO 4808 flocculant doses on the flocculation efficiency indicated by the optical density reduction at λ = 680 nm (C. vulgaris). | |
3.3.3 Synchronization of the MMR with MBR treatment.
The limitation of the nutrient uptake (i.e. slow and low level) by microalgae and the requirement of high effluent quality indicate that a large reactor volume of the MMR is required given the growth conditions tested (Fig. 5). This requires the reactor volume to be calculated using the ratio of nitrate and phosphorus concentrations in the MBR permeate and their uptake rate in the MMR (i.e. to achieve 100% removal). The volume of the MMR should be at least 37 times that of the MBR (Fig. 5) operating with a hydraulic retention time of 1 day. Large microalgae reactor volume has been suggested in the literature25,36 to facilitate light penetration, homogeneous cellular distribution, mass transfer, and others. However, having a large MMR is counterproductive to the compact design of MBRs and wastewater treatment facilities situated in urban and other space-deficient locations. In other words, having a large footprint could hinder the translation of a coupled MBR–MMR technology to the industrial-scale level. Therefore, further investigation is recommended to increase the rate of microalgal growth through optimizing key operating parameters such as the reactor shape, irradiation, and retention time to facilitate the implementation of the MMR in wastewater treatment processes.
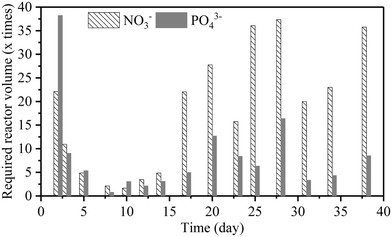 |
| Fig. 5 Required reactor volume of the MMR to compensate for the MBR permeate volume at 100% removal of nitrate and phosphorus. | |
4. Conclusions
This study demonstrated excellent NO3− and PO43− uptake rates of 4.0 ± 1.1 and 1.5 ± 0.9 g m−3 d−1, respectively, using a membrane microalgal reactor (MMR) to further remove nutrients from a conventional MBR treating synthetic municipal wastewater. Stable operation of the MMR was achieved by extracting the produced biomass (1
:
30 of microalgal biomass in the reactor, cell retention time of 30 days) on a daily basis. A facile flocculation and separation technique for microalgal biomass harvesting was also demonstrated to achieve 98% efficiency. Further research to optimize microalgal production is needed to increase the microalgal growth rate to reduce the MMR reactor volume for scaling-up and practical application of MMR in wastewater treatment.
Conflicts of interest
There are no conflicts to declare.
Acknowledgements
The authors acknowledged the funding support from the Faculty of Engineering and Information Technology, University of Technology Sydney under the Tech Lab BlueSky Project funding scheme 2019. Evoqua Water Technologies (South Windsor, NSW 2756, Australia) is thanked for the provision of membrane samples.
References
- L. N. Nguyen, F. I. Hai, J. Kang, W. E. Price and L. D. Nghiem, Removal of trace organic contaminants by a membrane bioreactor–granular activated carbon (MBR–GAC) system, Bioresour. Technol., 2012, 113, 169–173 CrossRef CAS PubMed.
- J. Ma, R. Dai, M. Chen, S. J. Khan and Z. Wang, Applications of membrane bioreactors for water reclamation: Micropollutant removal, mechanisms and perspectives, Bioresour. Technol., 2018, 269, 532–543 CrossRef CAS PubMed.
- E. Menger-Krug, J. Niederste-Hollenberg, T. Hillenbrand and H. Hiessl, Integration of Microalgae Systems at Municipal Wastewater Treatment Plants: Implications for Energy and Emission Balances, Environ. Sci. Technol., 2012, 46(21), 11505–11514 CrossRef CAS PubMed.
- S. Shao, F. Qu, H. Liang, H. Chang, H. Yu and G. Li, A pilot-scale study of a powdered activated carbon-membrane bioreactor for the treatment of water with a high concentration of ammonia, Environ. Sci.: Water Res. Technol., 2016, 2(1), 125–133 RSC.
- M. F. R. Zuthi, W. S. Guo, H. H. Ngo, L. D. Nghiem and F. I. Hai, Enhanced biological phosphorus removal and its modeling for the activated sludge and membrane bioreactor processes, Bioresour. Technol., 2013, 139, 363–374 CrossRef CAS PubMed.
- H.-L. Zhang, W. Fang, Y.-P. Wang, G.-P. Sheng, R. J. Zeng and W.-W. Li,
et al., Phosphorus Removal in an Enhanced Biological Phosphorus Removal Process: Roles of Extracellular Polymeric Substances, Environ. Sci. Technol., 2013, 47(20), 11482–11489 CrossRef CAS PubMed.
- K. Xiao, S. Liang, X. Wang, C. Chen and X. Huang, Current state and challenges of full-scale membrane bioreactor applications: A critical review, Bioresour. Technol., 2019, 271, 473–481 CrossRef CAS PubMed.
- F.-Y. Sun, X.-M. Wang and X.-Y. Li, An innovative membrane bioreactor (MBR) system for simultaneous nitrogen and phosphorus removal, Process Biochem., 2013, 48(11), 1749–1756 CrossRef CAS.
- M. D. Seib, K. J. Berg and D. H. Zitomer, Reduced energy demand for municipal wastewater recovery using an anaerobic floating filter membrane bioreactor, Environ. Sci.: Water Res. Technol., 2016, 2(2), 290–297 RSC.
- O. Perez-Garcia, F. M. E. Escalante, L. E. de-Bashan and Y. Bashan, Heterotrophic cultures of microalgae: Metabolism and potential products, Water Res., 2011, 45(1), 11–36 CrossRef CAS PubMed.
- A. S. Commault, O. Laczka, N. Siboni, B. Tamburic, J. R. Crosswell and J. R. Seymour,
et al., Electricity and biomass production in a bacteria-Chlorella based microbial fuel cell treating wastewater, J. Power Sources, 2017, 356, 299–309 CrossRef CAS.
- M. Hemalatha, J. S. Sravan, B. Min and S. Venkata Mohan, Microalgae-biorefinery with cascading resource recovery design associated to dairy wastewater treatment, Bioresour. Technol., 2019, 284, 424–429 CrossRef CAS PubMed.
- S.-Y. Chiu, C.-Y. Kao, T.-Y. Chen, Y.-B. Chang, C.-M. Kuo and C.-S. Lin, Cultivation of microalgal Chlorella for biomass and lipid production using wastewater as nutrient resource, Bioresour. Technol., 2015, 184, 179–189 CrossRef CAS PubMed.
- F. Gao, C. Li, Z.-H. Yang, G.-M. Zeng, L.-J. Feng and L. J-z,
et al., Continuous microalgae cultivation in aquaculture wastewater by a membrane photobioreactor for biomass production and nutrients removal, Ecol. Eng., 2016, 92, 55–61 CrossRef.
- K. W. Chew, S. R. Chia, P. L. Show, T. C. Ling, S. S. Arya and J.-S. Chang, Food waste compost as an organic nutrient source for the cultivation of Chlorella vulgaris, Bioresour. Technol., 2018, 267, 356–362 CrossRef CAS PubMed.
- L. Wang, M. Min, Y. Li, P. Chen, Y. Chen and Y. Liu,
et al., Cultivation of Green Algae Chlorella sp. in Different Wastewaters from Municipal Wastewater Treatment Plant, Appl. Biochem. Biotechnol., 2010, 162(4), 1174–1186 CrossRef CAS PubMed.
- J. K. Pittman, A. P. Dean and O. Osundeko, The potential of sustainable algal biofuel production using wastewater resources, Bioresour. Technol., 2011, 102(1), 17–25 CrossRef CAS PubMed.
- A. Ruiz-Martinez, N. Martin Garcia, I. Romero, A. Seco and J. Ferrer, Microalgae cultivation in wastewater: Nutrient removal from anaerobic membrane bioreactor effluent, Bioresour. Technol., 2012, 126, 247–253 CrossRef CAS PubMed.
- K. E. Dickinson, C. G. Whitney and P. J. McGinn, Nutrient remediation rates in municipal wastewater and their effect on biochemical composition of the microalga Scenedesmus sp. AMDD, Algal Res., 2013, 2(2), 127–134 CrossRef.
- P. Vo, H. H. Ngo, W. S. Guo, S. W. Chang, D. D. Nguyen and P. D. Nguyen,
et al., Can algae-based technologies be an affordable green process for biofuel production and wastewater remediation?, Bioresour. Technol., 2018, 256, 491–501 CrossRef PubMed.
- E. Jacob-Lopes, M. M. Maroneze, M. C. Deprá, R. B. Sartori, R. R. Dias and L. Q. Zepka, Bioactive food compounds from microalgae: an innovative framework on industrial biorefineries, Curr. Opin. Food Sci., 2019, 25, 1–7 CrossRef.
- D. Nagarajan, D.-J. Lee and J.-S. Chang, Integration of anaerobic digestion and microalgal cultivation for digestate bioremediation and biogas upgrading, Bioresour. Technol., 2019, 290, 121804 CrossRef PubMed.
- C.-Y. Chen, K.-L. Yeh, R. Aisyah, D.-J. Lee and J.-S. Chang, Cultivation, photobioreactor design and harvesting of microalgae for biodiesel production: A critical review, Bioresour. Technol., 2011, 102(1), 71–81 CrossRef CAS PubMed.
- S. Edmundson, M. Huesemann, R. Kruk, T. Lemmon, J. Billing and A. Schmidt,
et al., Phosphorus and nitrogen recycle following algal bio-crude production via continuous hydrothermal liquefaction, Algal Res., 2017, 26, 415–421 CrossRef.
- Y. Luo, P. Le-Clech and R. K. Henderson, Simultaneous microalgae cultivation and wastewater treatment in submerged membrane photobioreactors: A review, Algal Res., 2017, 24, 425–437 CrossRef.
- P. J. He, B. Mao, C. M. Shen, L. M. Shao, D. J. Lee and J. S. Chang, Cultivation of Chlorella vulgaris on wastewater containing high levels of ammonia for biodiesel production, Bioresour. Technol., 2013, 129, 177–181 CrossRef CAS PubMed.
- J. Lian, R. H. Wijffels, H. Smidt and D. Sipkema, The effect of the algal microbiome on industrial production of microalgae, Microb. Biotechnol., 2018, 11(5), 806–818 CrossRef PubMed.
- H. J. Choi and S. M. Lee, Effect of the N/P ratio on biomass productivity and nutrient removal from municipal wastewater, Bioprocess Biosyst. Eng., 2015, 38(4), 761–766 CrossRef CAS PubMed.
- B. Wang, C. Q. Lan and M. Horsman, Closed photobioreactors for production of microalgal biomasses, Biotechnol. Adv., 2012, 30(4), 904–912 CrossRef CAS PubMed.
- K. Chokshi, I. Pancha, A. Ghosh and S. Mishra, Microalgal biomass generation by phycoremediation of dairy industry wastewater: An integrated approach towards sustainable biofuel production, Bioresour. Technol., 2016, 221, 455–460 CrossRef CAS PubMed.
- F. Roselet, D. Vandamme, M. Roselet, K. Muylaert and P. C. Abreu, Screening of commercial natural and synthetic cationic polymers for flocculation of freshwater and marine microalgae and effects of molecular weight and charge density, Algal Res., 2015, 10, 183–188 CrossRef.
- Y. Ma, Z. Gao, Q. Wang and Y. Liu, Biodiesels from microbial oils: Opportunity and challenges, Bioresour. Technol., 2018, 263, 631–641 CrossRef CAS PubMed.
- Y. Zhou and G. V. Franks, Flocculation mechanism induced by cationic polymers investigated by light scattering, Langmuir, 2006, 22(16), 6775–6786 CrossRef CAS PubMed.
- M. R. Bilad, D. Vandamme, I. Foubert, K. Muylaert and I. F. J. Vankelecom, Harvesting microalgal biomass using submerged microfiltration membranes, Bioresour. Technol., 2012, 111, 343–352 CrossRef CAS PubMed.
- A. Augustine, A. Tanwar, R. Tremblay and S. Kumar, Flocculation processes optimization for reuse of culture medium without pH neutralization, Algal Res., 2019, 39, 101437 CrossRef.
- A. L. K. Sheng, M. R. Bilad, N. B. Osman and N. Arahman, Sequencing batch membrane photobioreactor for real secondary effluent polishing using native microalgae: Process performance and full-scale projection, J. Cleaner Prod., 2017, 168, 708–715 CrossRef CAS.
|
This journal is © The Royal Society of Chemistry 2020 |
Click here to see how this site uses Cookies. View our privacy policy here.