DOI:
10.1039/C9RA09893C
(Paper)
RSC Adv., 2020,
10, 4175-4188
Research into the thermal stability and mechanical properties of vitamin E diffusion modified irradiation cross-linked graphene oxide/ultra-high molecular weight polyethylene composites
Received
26th November 2019
, Accepted 7th January 2020
First published on 24th January 2020
Abstract
Recently, there has been increasing interest in modifying ultra-high molecular weight polyethylene (UHMWPE) due to glaring needs in the artificial joint replacement field. It is generally reported in the literature that irradiation cross-linking and adding graphene oxide (GO)/vitamin E (VE) can enhance the mechanical properties of UHMWPE, but this can sacrifice the oxidation stability and gel content. This paper examines how VE diffusion can influence irradiation cross-linked GO/UHMWPE composites and whether mechanical performance and oxidation resistance can be maintained simultaneously, which will provide new guidance for prolonging the longevity of UHMWPE implants. The GO/UHMWPE composites were fabricated by means of liquid ultrasonic dispersion, hot pressing and irradiation cross-linking, followed by VE diffusion and homogenization treatment. The results indicated that limited VE diffusion decreased the water absorption and wettability. The crystallinity, melting temperature, thermal stability, hardness and scratch resistance of the composites basically remain essentially the same, except in the case of pure UHMWPE. In addition, the oxidation resistance was improved significantly after incorporating VE. Furthermore, the diffusion and enhancement mechanisms were also demonstrated, respectively.
1 Introduction
As a unique polymer with outstanding physical and mechanical properties, such as chemical inertness, excellent impact resistance and self-lubricating properties, ultra-high molecular weight polyethylene (UHMWPE) has been used in orthopedics as a bearing material in total joint replacements for the past 50 years. However, osteolysis due to the wear and oxidation of the UHMWPE components has historically been one of the significant factors limiting implant longevity in the long-term. Osteolysis, as a clinical problem, has been the driving force behind the development of UHMWPE.1,2
During the last 20 years, cross-linking3–6 and filling with graphene oxide (GO)7–11 have been widely used to enhance the performance of UHMWPE. Cross-linked materials and materials with added GO have shown remarkable increases in long-term overall survival in total joint replacements around the world, due to significantly improved mechanical properties. Although a lot of effort is being spent on improving weaknesses, an effective method based on maintaining good mechanical properties and improving the oxidation resistance at the same time has yet to be developed.12 Over the course of the past few years, there has been an explosion of interest in the use of vitamin E (VE) as an antioxidant in UHMWPE due to its ability to absorb and stabilize free radicals.1,13–15 There are two ways of incorporating VE into UHMWPE, as shown in Fig. 1. One is to blend VE with UHMWPE powder prior to consolidation, followed by irradiation cross-linking. One absolute inferiority of the blending approach is considered to be the increased resistance of the material to subsequent irradiation cross-linking; the presence of VE in UHMWPE reduces the efficiency of cross-linking during irradiation, which may further influence the mechanical properties.1,16–18 An alternative method is the diffusion of VE into UHMWPE following radiation cross-linking.19,20 The degree of cross-linking is not adversely affected in this approach, since VE is not present during the irradiation process.1
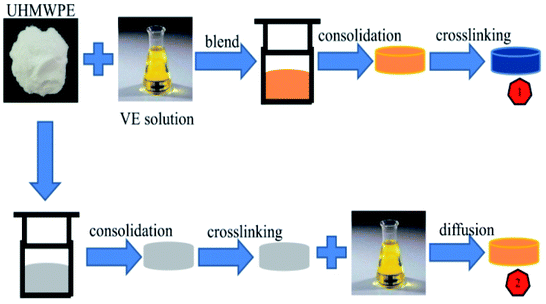 |
| Fig. 1 The two different ways of adding VE to UHMWPE. | |
The main goal of diffusing VE into radiation cross-linked GO/UHMWPE composites is to obtain enough VE throughout the joint implant components to protect the material against long-term oxidation while maintaining its mechanical properties. During the application of this method, there are several factors to be considered. For one, UHMWPE is a semi-crystalline polymer; VE can diffuse in the amorphous region freely but it is hindered by the presence of a crystal lattice in the crystallization region. Also, UHMWPE has a wide melting range, starting at 80 °C, with a peak melting point of about 135 °C. Below the melting point of the crystals, diffusion is limited to the amorphous region of the polymer, since the crystals are impermeable to a molecule as large as VE. At the same time, an increased temperature increases the surface concentration of VE at the surface of UHMWPE. However, when the melting point is exceeded, the diffusion of VE increases with a loss of crystallinity. Thus, the diffusion temperature has to be carefully determined, so as not to lose a significant amount of crystallinity.1,16–20
As discussed above, it is important not to melt the composites during the diffusion process so as to avoid a loss of crystallinity, which is closely related to the mechanical properties.1 In this paper, we focus on the diffusion of VE in irradiation cross-linked GO/UHMWPE composites and expect to obtain a material with simultaneously maximized mechanical performance and oxidation resistance. It is believed that the new materials investigated in this study can provide some guidance for improving the longevity of implants.
2 Experimental
2.1 Materials
The powdered UHMWPE used has a density of 0.93 g cm−3, an average molecular weight of five million Da, and a mean particle diameter of about 140 μm, and it was supplied by the Shanghai Research Institute of Chemical, China. High-purity graphite powder (99.9%, 325 mesh) was provided by Qingdao Jinrilai Co. Ltd, China, and was used to prepare GO. VE solution was purchased from China Pharmaceutical Group Co. Ltd. Other chemical reagents used were of analytical grade and commercially available.
2.2 Preparation of materials
GO was prepared in accordance with the modified Hummers' method.21 As shown in Fig. 2, the preparation steps for obtaining irradiation cross-linked GO/UHMWPE composites with a GO concentration of 0.5 wt% are as follows: GO (0.02 g) was placed in a beaker with alcohol solution (100 ml), then ultrasonically treated for 0.5 h to obtain a homogeneous solution. UHMWPE powder (39.8 g) was added into the beaker, followed by ultrasonic treatment for 1 h under the same conditions. After ultrasonic treatment, the homogeneous mixture was kept in a water bath at 60 °C to remove ethanol. The dried powder was then treated via high-speed ball milling at a speed of 400 rpm for 2 h. The obtained mixture powder was cold pressed at 5 MPa, and heat-treated at 200 °C for 2 h in a hot-air oven; after that, the mixture was pressed at 10 MPa until it reached room temperature. Specimens were cut into 15 mm × 10 mm × 6 mm pieces, vacuum-packed in a vacuum foil package, and then irradiated by Co60 γ-rays at a rate of 0.5 kGy h−1 at room temperature: the total irradiation dose was 100 kGy. Characterization of GO and the GO/UHMWPE composites was carried out as detailed in our preliminary study.22–30 After that, some samples and VE solution were placed in beakers, and the beakers were placed in a drying oven to soak at 120 °C for 24 h. After reaching the specified time, the samples were removed from solution and put in a drying oven at 120 °C for 24 h for homogenization treatment, followed by cooling down and wiping off the excess VE.
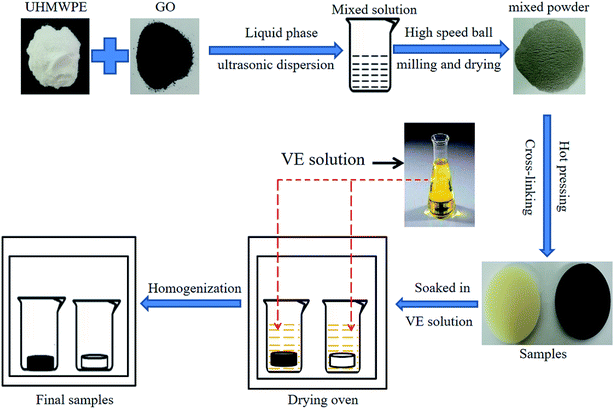 |
| Fig. 2 The preparation process of the materials. | |
2.3 Characterization
Fourier transform infrared spectrometry (FT-IR, Nicolet iS10, USA) was performed to investigate the characteristics of the composites, focusing on changes to the molecular structure.
2.4 Weight changes and diffusion depths
Weight changes (wm) were tested through measuring the mass gain using an electronic weighing balance with an accuracy of 0.1 mg. The masses of the material before and after immersion in VE solution were recorded as m1 and m2, respectively. Weight changes can be calculated according to the following equation (eqn (1)): |
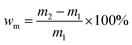 | (1) |
Diffusion depths were measured via FT-IR. Samples were sliced with a thickness of 50 μm (Leica manual slicer, PM2245, Leica, Germany). The diffusion depths of VE in different materials were studied using FT-IR based on characteristic peaks.
2.5 Crystallinity and thermal stability
Differential scanning calorimetry (DSC, TA, Q200) was applied at a scanning rate of 10 °C min−1 from 20 to 180 °C under a nitrogen atmosphere. The crystallinities of composites before and after VE doping were calculated according to the following formula: |
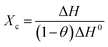 | (2) |
where θ is the filler content, ΔH is the melting enthalpy of samples and ΔH0 is the enthalpy when melting 100% crystalline UHMWPE, with a literature value of 293 J g−1.31,32
Thermal weight loss was studied by means of a thermogravimetric analyzer (TGA, TGA/1, Switzerland) over a temperature range from 50 to 800 °C at a rate of 20 °C min−1 under a nitrogen atmosphere.
2.6 Gel content
Gel content values were calculated according to ASTM D2765 guidelines using the following formula: |
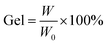 | (3) |
where W0 is the quality of the sample before testing and W is the quality of the sample after testing.
2.7 Water absorption
Water molecules can easily enter into a polymer and affect the performance of the polymer through physical or chemical action. In order to study the water absorption properties of the irradiation cross-linked composites after VE solution doping, water absorption experiments were carried out according to ASTM D570-98 guidelines. The formula for calculating water absorption is similar to eqn (1).
2.8 Wettability
The contact angle is an important polymer property, and its measurement is used as a simple surface analysis technique for evaluating the wetting behavior of a polymer surface, especially if the polymer is immersed in a biological environment. There is a key relationship between the surface properties and free energy of a material: the larger the surface energy, the easier the formation of a lubricating water film on the frictional surface. Therefore, research into the surface energy of a material can provide theoretical analysis and data support for future research into the tribological properties of a material.
The surface energy of a material can be obtained using the Owens and Wendt methods, and the calculation formulae are as follows:33
|
 | (5) |
where
θ is the contact angle;
γl is the surface tension of the liquid;
γpl is the polar force of the liquid surface tension;
γdl is the dispersive force of the liquid surface tension;
γs is the surface free energy; and
γps and
γds are the polar force and dispersive force of the surface free energy. In this paper, deionized water and glycol were used as detection liquids, and the relevant data are shown in
Table 1.
Table 1 Surface tension data and the polar and dispersive components of the liquids used
Detection liquid |
γl (mJ m−2) |
γdl (mJ m−2) |
γpl (mJ m−2) |
Deionized water |
71.50 |
28.15 |
43.35 |
Glycol |
47.46 |
31.19 |
16.27 |
2.9 Anti-oxidation properties
In order to investigate the oxidation stability after VE diffusion, an accelerated aging process was performed using an electric thermostatic drying oven (Shanghai Boxun Industry & Commerce Co., Ltd) at 80 °C for 21 days in air, according to ASTM F2003 guidelines. Oxidation resistance was measured via the oxidation index (OI), which was computed using the following equation:34 |
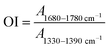 | (6) |
2.10 Hardness
The hardness values of different composites were measured (MFT-5000 tribometer) and calculated via the following equation according to the ISO2 039-73 standard: |
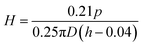 | (7) |
where H is the indentation hardness of the sample (N mm−2); p is the maximum experimental force (N); D is the diameter of the ball (mm); and h is the maximum indentation depth (mm). A schematic diagram of the ball indentation hardness test apparatus is shown in Fig. 3.
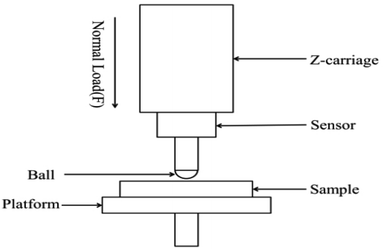 |
| Fig. 3 A schematic diagram of the hardness test apparatus. | |
2.11 Scratch resistance testing
Scratch resistance testing is also a way to evaluate the mechanical properties of a material. In this paper, scratch testing of different composites was also carried out (MFT-5000 tribometer); the scratch coefficient is calculated via the following equation: |
 | (8) |
where μ is the scratch coefficient; FT is the scratch resistance; and FN is normal pressure. A schematic diagram of the scratch test apparatus is shown in Fig. 4.
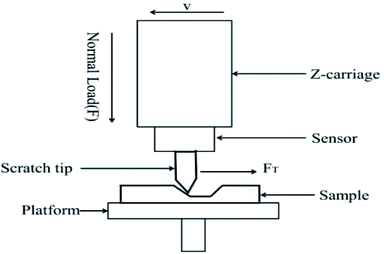 |
| Fig. 4 A schematic diagram of the scratch test apparatus. | |
Under an experimental load of 1 N, with a 12 mm scratching length at a speed of 0.2 mm s−1, the scratch morphology was also scanned (MFD-D profilometer). A schematic diagram of the parameters for scratch testing are shown in Fig. 5.
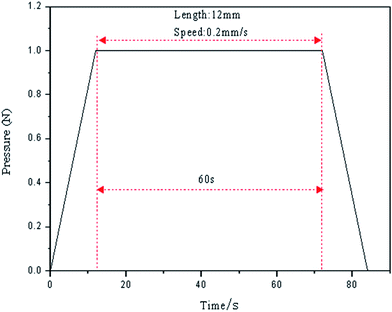 |
| Fig. 5 A schematic diagram of the parameters for scratch testing. | |
3 Results and discussion
3.1 Characterization of the composites
Fig. 6 shows the FT-IR spectra of UHMWPE, GO, VE and the soaked irradiation cross-linked composite. As can be seen, a CH2 rocking peak appears at around 720 cm−1, while a bending peak from C–H bonds is located at 1462 cm−1. Also, absorption peaks from C–H stretching are observed at 2918 cm−1 and 2840 cm−1. The spectrum of GO includes some relatively strong signals that relate to activity on the GO plane: a signal emerges at 1050 cm−1 associated with C–C vibration, the peaks at 1627 cm−1 and 1725 cm−1 are related to unoxidized sp2 C–C bonds and C
O stretching vibrations, respectively, and the signal at 3420 cm−1 is usually related to O–H stretching vibrations. The results are consistent with studies reported by Pang et al.26,27 In addition, abundant oxygen-containing functional groups can be observed in the infrared spectrum of GO. In the spectrum of VE, ether group, symmetric bending and methyl asymmetric peaks arise at 1084 cm−1, 1374 cm−1 and 1464 cm−1, respectively. Other peaks can be seen, such as an absorption peak from C–H stretching appearing at 2918 cm−1 and a C–O stretching peak from phenol appearing at 1260 cm−1. What's more, the C–O peak is a typical characteristic peak of VE, which is a way to judge the existence of VE. According to the previous research findings of our group, the FT-IR results show no significant differences after either GO filling or irradiation cross-linking has taken place, which suggests that the molecular structure of UHMWPE has not been significantly affected.22,23 Simultaneously, the typical characteristic peaks of VE can be seen in the spectra of the different materials with no other typical characteristic peaks, indicating that VE has diffused into the matrices of the composites.19,20
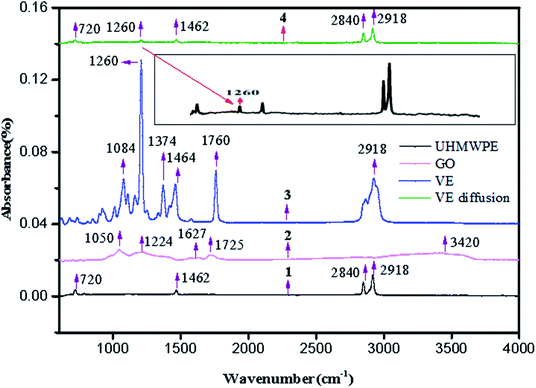 |
| Fig. 6 Infrared spectra of the composite material and its components. | |
3.2 Weight changes and diffusion depths
From Fig. 7, the obvious tendencies in the gravimetric changes of different materials after soaking in VE solution can be seen. The weight of UHMWPE increased by 5.1%, which was the largest increase among all materials. After filling with GO, the weight increase rate decreased to 3.5%. Irradiation cross-linking treatment also reduced the mass increase. When both treatments were used at the same time, however, the smallest weight change was seen. The diffusion depth data shows the same trend as the weight change data. VE has the deepest diffusion depth in UHMWPE. Adding GO or irradiation cross-linking treatment reduced the diffusion depth of VE. When used together, the diffusion depth was the shallowest. The reasons for this phenomenon can be explained from the following aspects. First of all, UHMWPE is a semi-crystalline polymer; VE can diffuse into the amorphous region freely but is hindered by the presence of the crystal lattice in the crystallization region.19,20 The melting point of UHMWPE is about 135 °C. At 100 °C, the crystalline region begins to melt, and the melting area of the crystallization zone increases as the temperature rises. After a long time in a 120 °C environment, more crystallization zones melt and the system has more energy under high temperature conditions, which is more conducive to the diffusion of VE. Therefore, the amount of VE diffusion increases significantly. However, the addition of GO hinders the diffusion of VE, as GO has a high specific surface area and its large two-dimensional planar structure hinders the diffusion of VE into UHMWPE.
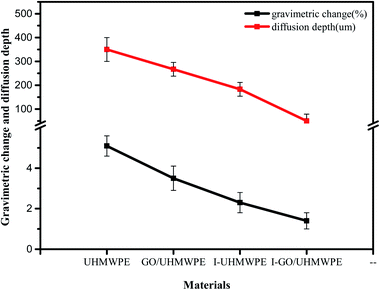 |
| Fig. 7 Weight changes and diffusion depths after VE diffusion. | |
3.3 Crystallinity analysis and thermal performance
The effects of rising temperature on UHMWPE can be divided into different stages. As shown in Fig. 8, when the temperature is below 80 °C, the longer molecular chains of UHMWPE cannot slide past each other due to insufficient energy. At temperatures higher than this, the crystallization zones begin to melt, and as the temperature increases, the melting of the crystalline zones gradually increases: the melting point is about 135 °C. If the melting point is exceeded, the material will melt completely, along with increased mobility. Fig. 9 shows the crystallinity and melting point data of materials before and after VE diffusion.
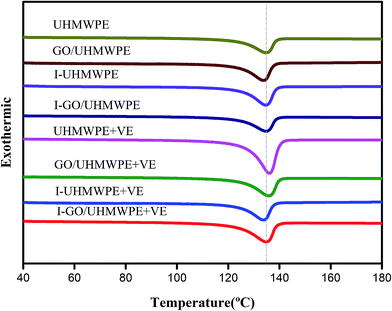 |
| Fig. 8 The DSC curves of different materials before/after VE diffusion. | |
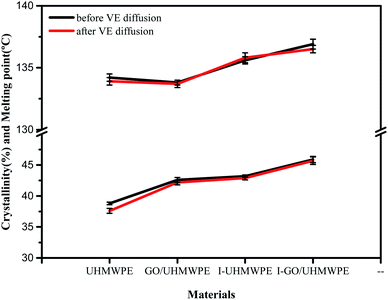 |
| Fig. 9 The crystallinity and melting point data of different materials. | |
The melting point of UHMWPE is 134.2 °C, and the addition of GO has no significant effects on the melting point of UHMWPE. In the process of irradiation cross-linking, the molecular chains in the crystal zones cross-link with each other, resulting in an increase in the melting point, so the melting point of the irradiation cross-linked composite was further increased. VE soaking and homogenization treatment seem to have no significant effects on the melting point.
The crystallinity of UHMWPE shows a value of 38.8%; this value is in accordance with previous studies.25,26,29 The addition of GO significantly increases the crystallinity of UHMWPE. Because of the large specific surface area of GO, it acts as a crystallization factor in the matrix, leading to concretion and promoting crystallization. Irradiation also increased the crystallinity. During irradiation, the molecular chains were broken and recrystallized. The structure of UHMWPE became more perfect, resulting in an increase in crystallinity. In addition, the results show that irradiation cross-linking and GO filling increased the crystallinity synergistically, bringing about the highest crystallinity. The diffusion of VE slightly reduced the crystallinity, which may be due to the fact that at high temperature, more VE diffuses into the matrix of UHMWPE, hindering the recrystallization process. The crystallinity of the other three materials show no obvious changes, mainly due to the lower diffusion of VE.37,38
Thermal stability is critical for polymers, since their properties may be affected by molding at a certain temperature during the thermoforming process. Thermogravimetric analysis (TGA) is an important method used to study the thermal stability of a composite, and the results are of great significance when analyzing the thermal stability of a polymer material. Fig. 10a shows the thermal decomposition curve of neat UHMWPE, which depicts two demarcated temperatures (T1 and T2). In TGA, the initial decomposition temperature T1 (Fig. 10b) is characterized as the temperature at which the corresponding weight loss is 5 wt%. It can be seen clearly from Fig. 10b and c that irradiation cross-linking and GO filling have distinct effects on the thermal stability of UHMWPE. The increases in T1 and T2 as a result of GO filling can be explained from the following two aspects. On the one hand, adding GO can enhance the interactions between GO and UHMWPE through van der Waals' forces and chemical bonds, thus limiting the movement of UHMWPE molecular chains. On the other hand, the lamellar structure of GO results in a large UHMWPE molecular chain free volume. These two interfering factors undergo a mutual trade-off, but the effects of interaction forces are greater than those of free space, which improves the thermal performance.25–27 The decrease in the thermal stability of the composites after irradiation cross-linking can be attributed to the decomposition of molecular chains or the decrease in molecular weight.35 The pure UHMWPE chains are relatively large, but these chains were broken into small chains and produced active radicals after irradiation. These radicals react with O2 in the air, leading to oxidative cracking reactions, so the molecular weight of the samples decreases. The addition of GO improves the thermal stability. This is because GO can be used as a scavenger for scavenging free radicals, restraining oxidative cracking reactions and improving the thermal stability.36 T1 and T2 increased slightly after adding VE, which may be due to VE diffusion increasing the liquidity of UHMWPE molecular chains.25–27 However, the effects of VE diffusion on the thermal properties are not remarkable.
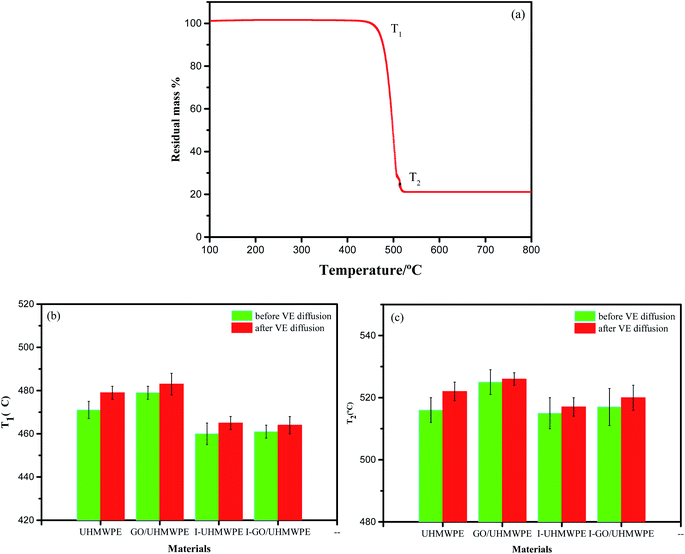 |
| Fig. 10 (a) The typical decomposition curve from thermogravimetric analysis of pure UHMWPE and (b and c) the thermal stability parameters of the composites. | |
3.4 Gel content
Due to the large amounts of free radicals generated during irradiation, the cross-linking of different free radicals led to the gel content increasing to 90.45%. After filling with GO, the gel content decreased slightly. On the one hand, the two-dimensional surface of GO limits the movement of free radicals to a certain extent, which hinders the cross-linking of free radicals. On the other hand, some GO may have been reduced to form GO radicals during high energy beam irradiation. To some extent, GO radicals reacted with UHMWPE radicals, reducing the number of cross-linked free radicals and resulting in a decrease in the gel content, as shown in Fig. 11.
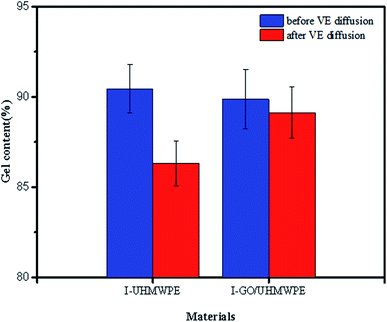 |
| Fig. 11 The gel content values of different materials. | |
Immersion in VE solution decreased the gel content. Since VE has the function of stabilizing free radicals, residual free radicals and their cross-linking were limited by the presence of VE. In addition, a large amount of VE exists on the surface of UHMWPE, which hinders the diffusion of oxygen into the matrix and reduces the reactions between free radicals and oxygen, thus reducing the gel content. The same reasons apply when explaining the reduction in the gel content of the irradiation cross-linked GO/UHMWPE composite.
3.5 Water absorption
It can be clearly seen from Fig. 12 that UHMWPE and its composites showed low levels of water absorption, with a maximum value of 0.021%. The addition of GO increases the water absorption of UHMWPE. First, it has excellent water absorption properties due to the rich oxygen-containing functional groups (such as –COOH and –OH) contained on its surfaces and edges. Second, the existence of micropores between GO and UHMWPE provides space for water molecules to penetrate into the composites. The water absorption of the composite decreased after irradiation cross-linking, mainly because cross-linking in the amorphous region of UHMWPE hindered the diffusion of water molecules into the matrix. In addition, irradiation caused the partial reduction of GO, resulting in a slight decrease in the number of oxygen containing functional groups on the surface of GO.22–24,29 Irradiation causes the chemical bonds on the GO surface to break, forming GO radicals. GO radicals and UHMWPE radicals may combine to form new ones. The chemical bonds increase the interfacial bonding force of the composite, which leads to a decrease in water absorption after the irradiation cross-linking treatment. Compared with pure UHMWPE, the water absorption of irradiated UHMWPE was slightly lower, which indicates that the increase in the cross-linking degree of UHMWPE caused by irradiation hindered the diffusion of water molecules. Soaking in VE solution reduced the water absorption, mainly due to two reasons. One is that VE is an oily hydrophobic material. The other is that during soaking and homogenization, VE can occupy the micropores in the composite and block the diffusion channels for water molecules, which hinders the diffusion of water molecules into the matrix.
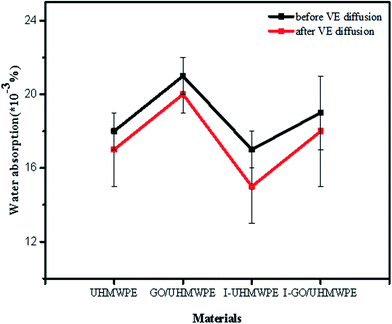 |
| Fig. 12 The water absorption properties of different materials. | |
3.6 Wettability
Wettability was investigated by testing the contact angles of the composites using different detection liquids. The results are shown in Fig. 13. Deionized water is taken as an example to explain the changes in contact angle. Using deionized water, the contact angle of pure UHMWPE is 94.87°. After soaking in VE solution, the contact angle becomes larger and the wettability decreases. This is mainly because VE is an oily fat-soluble hydrophobic substance and there is a large amount of VE on the UHMWPE surface. This results in an increase in the contact angle. The contact angle of the GO/UHMWPE composite is 85.01°, which indicates that filling with GO reduces the contact angle of the UHMWPE composite and improves its wettability, similar to the water absorption rate, because the surface of GO contains abundant oxygen-containing functional groups (–COOH and –OH), leading to excellent hydrophilicity. The contact angle increased after VE soaking, indicating that VE reduced the wettability. Irradiation cross-linking treatment reduced the contact angle of the UHMWPE material to 87.89°, indicating that irradiation cross-linking improved the wettability. The molecular chains of UHMWPE were disrupted by high-energy rays during irradiation, generating a large number of polar radicals with excellent hydrophilicity; polar radicals can easily react with O2 in the air to form substances with oxygen-containing functional groups (C
O). Due to a combination effect, the wettability of UHMWPE improved. However, it can be seen that the wettability was reduced after VE-soaking treatment. The contact angle of the irradiation cross-linked GO/UHMWPE composite shows a minimum value of 82.12°, which indicates that GO filling and irradiation cross-linking can improve the wettability. Although some GO was reduced during irradiation, resulting in a decrease in the number of oxygen-containing functional groups, it does not play a leading role. After soaking in VE, the same results are seen as for the above-mentioned materials, indicating that VE has no effects on improving the wettability of the irradiated cross-linked composites.
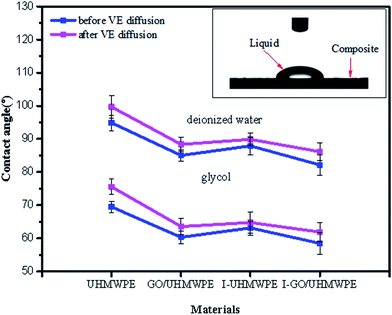 |
| Fig. 13 The contact angle values of the composites. | |
The calculated surface energies are shown in Fig. 14. It can be seen that the surface free energy of pure UHMWPE is 30.04 J m−2; irradiation increased the surface energy, mainly because of the decreased contact angle. The surface energy of the composite material was further increased after filling with GO; this is also on account of the reduced contact angle. The surface energy of the irradiation cross-linked GO/UHMWPE composite is the largest, which is similar to the wettability analysis. Meanwhile, it can be seen that the surface energy of the composite decreased after soaking in VE solution, mainly due to the hydrophobicity of VE, as the oil-soluble VE reduced the surface energy of the composite slightly.
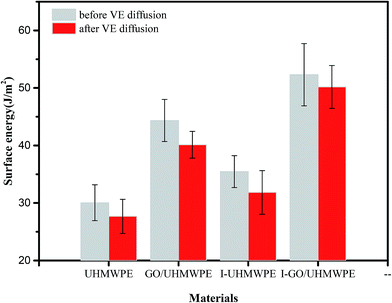 |
| Fig. 14 The surface energies of different materials. | |
3.7 Oxidation stability
Fig. 15 shows the OI values of VE-immersed irradiation cross-linked GO/UHMWPE composites before and after accelerated aging. The OI of irradiated UHMWPE after accelerated aging treatment is 2.33. Due to long-term exposure to a high-temperature air environment over the whole process, oxygen in the air continuously reacts with the free radicals inside UHMWPE, resulting in an increased OI. Irradiation cross-linked UHMWPE first immersed in VE solution and then subjected to accelerated aging treatment shows an OI value of 1.53. The significantly reduced OI value indicates the good oxidation resistance performance of VE. The OI value of the irradiated cross-linked GO/UHMWPE composite after accelerated aging treatment is 2.13. Compared with the material without GO, this is slightly decreased, indicating the weak antioxidant performance of GO. The OI of the irradiation cross-linked composite first immersed in VE solution and then subjected to accelerated aging treatment is significantly reduced, with a value of 1.49, which also shows that VE has good antioxidant properties.39–43
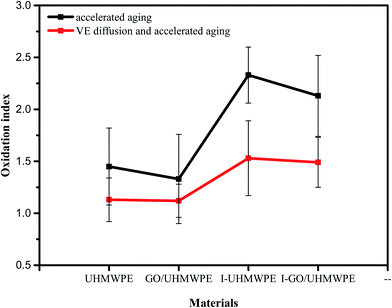 |
| Fig. 15 OI values of different materials. | |
3.8 Hardness
Fig. 16 presents the hardness properties of different composites. It can be seen that the hardness of pure UHMWPE is 22.5 MPa, and that of irradiation cross-linked UHMWPE is 24.2 MPa, which is 7.6% higher than that of the non-irradiated material. This is mainly due to the irradiation treatment leading to the generation of free radicals and their cross-linking, which improves the hardness. After filling with GO, the hardness increases obviously, mainly because the larger two-dimensional planar structure of GO has good mechanical properties and can withstand and transfer external loads. The hardness of the irradiated cross-linked composite is 37.1 MPa, indicating that GO filling and irradiation cross-linking treatments have significant effects on the hardness. The linear molecular chains of UHMWPE are disrupted during irradiation and some of the free radicals cross-linked with each other. At the same time, γ-rays with higher energy interrupted some oxygen-containing functional groups on the surface of GO and generated new free radicals. More stable functional groups (C–C) were formed, since the free radicals of UHMWPE interacted with the GO radicals.22–27,29 The interfacial binding force between GO and UHMWPE increased, resulting in an increase in hardness.
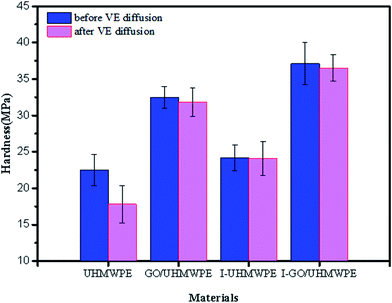 |
| Fig. 16 The hardness properties of different materials. | |
After soaking in VE solution and homogenizing, the hardness properties of the materials show no obvious changes, except in the case of UHMWPE. After immersion in VE solution, the hardness of UHMWPE decreased by 19.6%. This may be related to changes in crystallinity. High temperature is conducive to the diffusion of VE into the inner parts of the UHMWPE matrix, and more VE solution diffuses into the matrix; this hinders the recrystallization process, resulting in decreases in crystallinity and hardness. Buchanan44 showed that the hardness of UHMWPE improves with an increase in crystallinity and this report is consistent with our findings. The diffusion of VE decreased the crystallinity of UHMWPE, resulting in a decrease in hardness. The hardness of the composite remains the same after adding GO or irradiation treatment, mainly because there is no obvious influence on the crystallinity. Hardness changes in the other three materials are not obvious, mainly because of the hindrances to VE diffusion, resulting in relatively less diffusion of VE into the matrix and reducing the impact on hardness. The large two-dimensional planar structure of GO hinders the diffusion of VE into the UHMWPE matrix, and its crystallinity remains basically unchanged with little effect on the hardness. After the irradiation cross-linked GO/UHMWPE composite was immersed in VE solution, the above-mentioned observations were also valid.
3.9 Scratch resistance
Fig. 17 shows the scratched surface of UHMWPE. It can be seen that the scratch has a certain width and depth. During scratch testing, due to the movement of the probe, the material on the surface of the substrate was deposited on both sides of the scratch, and the bottom of the scratch exhibits an irregular shape due to wear debris and the internal action of the substrate.45
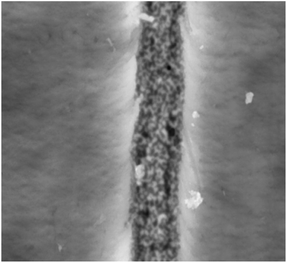 |
| Fig. 17 A scratch map of UHMWPE before VE diffusion. | |
Fig. 18 and 19 show the average scratch coefficients and scratch depths of the composites. It can be seen that the scratch coefficients of the different materials are between 0.9 and 1.2. The scratch coefficient of UHMWPE is 0.99 and this is increased by 6.1% after irradiation cross-linking, which is mainly due to the increased cross-linking degree improving the hardness. After filling with GO, the scratch coefficient increased by 11.5%. Due to the good mechanical properties of GO, the scratch coefficient increased. Meanwhile, during experiments, the probe also needs to overcome the weak van der Waals forces between GO and UHMWPE. Therefore, the resistance increased along with the scratch coefficient. The scratch coefficient showed a highest value of 1.17 when GO addition and cross-linking were both used. On the one hand, irradiation increased the cross-linking degree, leading to an increase in the hardness. On the other hand, the good mechanical properties of GO may hinder the movement of the probe inside the substrate. Finally, it may be that during the irradiation process, some of the functional groups of GO are disrupted, causing some GO to be reduced to GO radicals. The GO radicals can react with UHMWPE radicals and combine to form stronger C–C bonds. Since the bond energy of the C–C bonds is much larger than the van der Waals forces, the interfacial bonding force inside the matrix increased, which further hinders the movement of the probe inside the substrate.
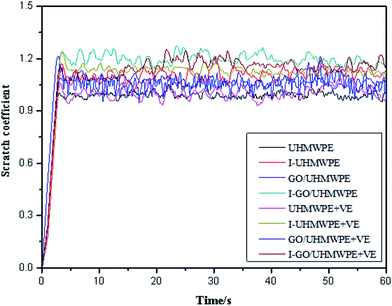 |
| Fig. 18 The scratch coefficients of the composites. | |
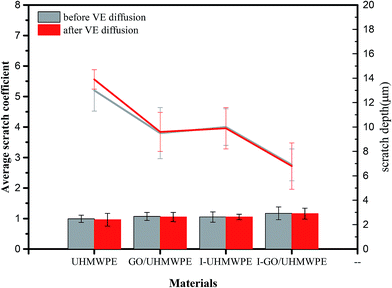 |
| Fig. 19 The average scratch coefficients (bars) and scratch depths (lines). | |
The scratch properties show the same trend as the hardness properties. After VE soaking treatment, the scratch coefficients of the materials show no significant changes, except for pure UHMWPE. This is mainly due to more VE diffusing into the UHMWPE matrix, resulting in lower crystallinity and reduced hardness and, thus, a lower scratch coefficient. The larger two-dimensional plane of GO and the cross-linking produced by irradiation hindered the diffusion of VE, and VE showed no obvious effects on the crystallinity and cross-linking degree of these materials. Therefore, the scratch coefficients show no obvious changes. The above analysis is also applicable to the changes in scratch depth. Although the diffusion of VE can reduce the crystallinity and hardness of pure UHMWPE and increase the scratch depth, the scratch depths of the other materials remain basically constant due to the synergistic action of irradiation and GO filling.
4 Mechanistic analysis
4.1 Diffusion mechanism
As described above, the generation of an increased degree of cross-linking and the two-dimensional planar structure of GO hinder the diffusion of VE into the interior of the UHMWPE matrix. What's more, during the irradiation cross-linking process, the linear molecular chains of UHMWPE are disrupted and the generated free radicals cross-link with each other to form a three-dimensional network structure; this hinders the diffusion of VE into the UHMWPE matrix. Last but not least, the high-energy rays lead to some reduction of GO and the reduced GO combines with the free radicals generated from UHMWPE to form new chemical bonds. The interfacial bonding force inside the matrix increases, hindering the diffusion of VE. Due to the combined effects of the two-dimensional planar structure of GO and cross-linking, the diffusion of VE is further decreased and, therefore, the lowest amount of VE diffusion is seen in the irradiated cross-linked GO/UHMWPE composite. The diffusion mechanism is shown in Fig. 20.
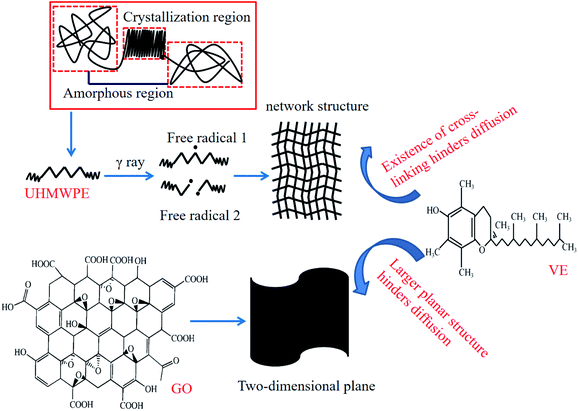 |
| Fig. 20 The diffusion mechanism of VE. | |
4.2 Enhancement mechanism
According to the preliminary work of our team, when GO addition and irradiation cross-linking are applied together to modify UHMWPE, there may be free radical and chemical bond generation.25–27,29
Gamma rays, when applied to the cross-linking process, have a mean energy some orders of magnitude higher than chemical bonds. High energy particles interact with the molecular chains of UHMWPE, leading to the scission of C–H and C–C bonds, which generates primary and secondary macro-radicals and H radicals. GO, the oxidation product of graphene, has rich oxygen-containing functional groups on its surface, such as hydroxyl groups (–OH), carbonyl groups (C
O) and carboxyl groups (O–C
O). Irradiation causes a large number of oxygen functional groups to fracture, especially the C–O bonds, and GO becomes reduced. Some of the primary and secondary macro-radicals generate H-crosslinks and Y-crosslinks. Others may react with the reduced GO, producing four different products. In the non-irradiated GO/UHMWPE composite, the interaction forces between GO and the UHMWPE matrix are van der Waals forces. Compared with van der Waals forces, the C–C chemical bonds generated after irradiation cross-linking are much stronger and the bonding force between GO and the UHMWPE matrix is obviously enhanced. Therefore, the irradiation cross-linked GO/UHMWPE composite shows superior performance. Since VE diffuses after the composites are formed, it has no significant effects on the reinforcement of the composites. This process is shown in Fig. 21 and 22.
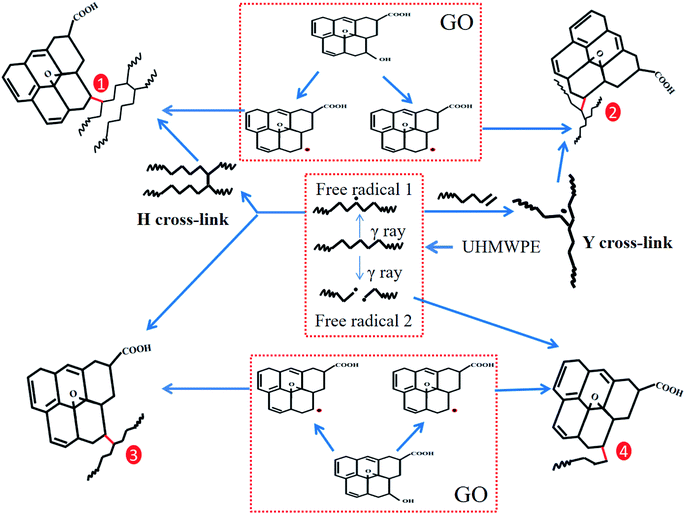 |
| Fig. 21 The mechanism explaining the enhancement of UHMWPE upon irradiation cross-linking and GO addition. | |
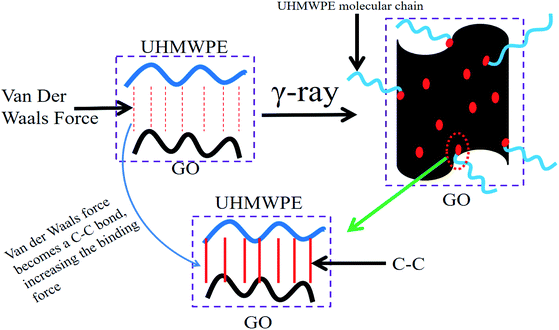 |
| Fig. 22 A schematic diagram showing C–C formation. | |
5 Conclusions
In this paper, the thermal stability and mechanical properties of irradiation cross-linked GO/UHMWPE composites were studied after incorporating VE. In addition, oxidation resistance as an important factor was also considered. The following conclusions can be drawn. (1) The existence of the two-dimensional GO layer structure and cross-linking efficiency hinder the diffusion of VE into the matrix, with a limited diffusion mass and depth observed. (2) Limited VE diffusion decreased the water absorption and wettability, as VE is an oily hydrophobic substance. (3) The crystallinity, thermal stability, hardness and scratch resistance properties of the composites basically maintain their original values, except in the case of pure UHMWPE. Since more VE diffuses into the UHMWPE surface, the recrystallization process is hindered, which slightly reduces the mechanical properties. (4) Oxidation resistance was improved significantly after incorporating VE. Therefore, the modified composites may have bright application prospects in the field of artificial joint replacement.
However, there are still some limitations to this study. For example, the fatigue strength, compression and tensile properties and wear resistance of the modified composites were not investigated. Since these are crucial performance parameters to prove artificial joint replacement suitability, they should be further studied in future studies.
Conflicts of interest
There are no conflicts to declare.
Acknowledgements
The authors gratefully acknowledge the support of the National Natural Science Foundation of China (Grant no. 51305166), and the Natural Science Foundation of Jiangsu Province, China (Grant no. BK20130143).
References
- S. M. Kurtz, Ultra High Molecular Weight Polyethylene in Total Joint, UHMWPE Biomaterials Handbook, 3rd edn, 2016 Search PubMed.
- W. Waugh and J. Charnley, The man and the hip, Spr. Sci. Bus. Med, 2012 Search PubMed.
- L. Xiong and D. Xiong, The influence of irradiation dose on mechanical properties and wear resistance of molded and extruded ultra high molecular weight polyethylene, J. Mech. Behav. Biomed. Mater., 2012, 9, 73–82 CrossRef CAS PubMed.
- S. Kayandan, B. N. Doshi, E. Oral and O. K. Muratoglu, Surface cross-linked ultrahigh molecular weight polyethylene by emulsified diffusion dicumyl peroxide, J. Biomed. Mater. Res., Part B, 2017, 106, 1–7 Search PubMed.
- R. Gul, K. Fung, B. N. Doshi, E. Oral and O. K. Muratoglu, Surface cross-linked UHMWPE Using Peroxides, J. Orthop. Res., 2017, 35, 2551–2556 CrossRef CAS.
- B. Sagbas, C. Gachot and H. Kaleli, Effect of argon plasma surface modification on tribological behavior of biopolymers, Ind. Lubr. Tribol., 2016, 68, 508–514 CrossRef.
- C. Min, P. Nie, J. Song, Z. Zhang and K. Zhao, Study of tribological properties of polyimide/graphene oxide nanocomposite films under seawater-lubricated condition, Tribol. Int., 2014, 80, 131–140 CrossRef CAS.
- G. Arash, W. Alfred and E. Nazanin, An investigation into tribological behaviour of multi-walled carbon nanotube/graphene oxide reinforced UHMWPE in water lubricated contacts, Tribol. Int., 2016, 95, 156–161 CrossRef.
- A. Chih, J. Anson and J. Pu, Frictional and mechanical behaviour of graphene/UHMWPE composite coatings, Tribol. Int., 2017, 116, 295–302 CrossRef CAS.
- S. Suner, N. Gowland, R. Craven and R. Joffe, Ultrahigh molecular weight polyethylene/graphene oxide nanocomposites: wear characterization and biological response to wear particles, J. Biomed. Mater. Res., Part B, 2018, 106, 183–190 CrossRef CAS PubMed.
- Y. Chen, Y. Qi, Z. Tai, X. Yan, F. Zhu and Q. Xue, Preparation, mechanical properties and biocompatibility of graphene oxide/ultrahigh molecular weight polyethylene composites, Eur. Polym. J., 2012, 48, 1026–1033 CrossRef CAS.
- J. M. Shah and M. Fuzail, Examination of the long-lived, oxygen-induced radicals in irradiated ultra-high molecular weight polyethylene, Nucl. Instrum. Methods Phys. Res., Sect. B, 2007, 265, 67–71 CrossRef CAS.
- B. Pierangiola and O. Ebru, Vitamin E-stabilized UHMWPE for Total Joint Implants, Clin. Orthop. Relat. Res., 2011, 469, 2286–2293 CrossRef PubMed.
- F. Jun, N. Doshi, E. Oral and O. K. Muratoglu, High temperature melted, radiation cross-linked, vitamin E stabilized oxidation resistant UHMWPE with low wear and high impact strength, Polymer, 2013, 54, 199–209 CrossRef.
- N. T. Dintcheva, R. Arrigo, C. Gambarotti, S. Carroccio, G. Filippone, F. Cicogna and M. Guenzi, a-Tocopherol-induced radical scavenging activity in carbon nanotubes for thermo-oxidation resistant ultra-high molecular weight polyethylene-based nanocomposites, Carbon, 2014, 74, 14–21 CrossRef CAS.
- M. Parth, N. Aust and K. Lederer, Studies on the effect of electron beam radiation on the molecular structure of ultra-high molecular weight polyethylene under the influence of alpha-tocopherol with respect to its application in medical implants, J. Mater. Sci., 2002, 13, 917–921 CAS.
- E. Oral, E. S. Greenbaum, A. S. Malhi, W. H. Harris and O. K. Muratoglu, Characterization of irradiated blends of alpha-tocopherol and UHMWPE, Biomaterials, 2005, 26, 6657–6663 CrossRef CAS PubMed.
- E. Oral, C. Godleski, A. S. Malhi and O. K. Muratoglu, The effects of high dose irradiation on the cross-linking of vitamin E-blended ultrahigh molecular weight polyethylene, Biomaterials, 2008, 29, 3557–3560 CrossRef CAS PubMed.
- E. Oral, K. K. Wannomae, N. E. Hawkins, W. H. Harris and O. K. Muratoglu, a-Tocopherol doped irradiated UHMWPE for high fatigue resistance and low wear, Biomaterials, 2004, 25, 5515–5522 CrossRef CAS PubMed.
- E. Oral, K. K. Wannomae, S. L. Rowell and O. K. Muratoglu, Diffusion of vitamin E in ultrahigh molecular weight polyethylene, Biomaterials, 2007, 28, 5225–5237 CrossRef CAS PubMed.
- S. H. Hummers and R. E. Offeman, Preparation of graphitic oxide, J. Am. Chem. Soc., 1958, 80, 1339 CrossRef.
- G. Huang, Z. Ni, G. Chen, W. Pang and Y. Zhao, Effects of gamma irradiation and accelerated aging on GO/UHMWPE nanocomposites, Int. J. Polym. Anal. Charact., 2016, 21, 417–427 CrossRef CAS.
- G. Huang, Z. Ni, G. Chen and Y. Zhao, The influence of irradiation and accelerated aging on the mechanical and tribological properties of the graphene oxide/ultra-high-molecular-weight polyethylene nanocomposites, Int. J. Polym. Sci., 2016, 9, 1–9 Search PubMed.
- G. Huang, Z. Ni, G. Chen, G. Li and Y. Zhao, Investigation of irradiation grapheme oxide/ultra-high-molecular-weight polyethylene nanocomposites by ESR and FTIR spectroscopy, Fullerenes, Nanotubes, Carbon Nanostruct., 2016, 24, 698–704 CrossRef CAS.
- W. Pang, Z. Ni, J. Wu and Y. Zhao, Investigation of tribological properties of graphene oxide reinforced ultrahigh molecular weight polyethylene under artificial seawater lubricating condition, Appl. Surf. Sci., 2018, 434, 273–282 CrossRef CAS.
- W. Pang, Z. Ni, G. Chen, G. Huang, H. Huang and Y. Zhao, Mechanical and thermal properties of grapheme oxide/ultrahigh molecular weight polyethylene nanocomposites, RSC Adv., 2015, 5, 63063–63072 RSC.
- W. Pang, J. Wu, Q. Zhang and G. Li, Graphene oxide enhanced, radiation cross-linked, vitamin E stabilized oxidation resistant UHMWPE with high hardness and tensile properties, RSC Adv., 2017, 7, 55536–55546 RSC.
- P. Lu, Z. Ni, G. Chen and S. Qian, The Influence of SBF on Surface Properties of Irradiated GO/UHMWPE Nanocomposites, Russ. J. Appl. Chem., 2018, 91, 1172–1178 CrossRef CAS.
- Z. Ni, W. Pang, G. Chen, P. Lu and S. Qian, The Influence of Irradiation on Thermal and Mechanical Properties of GO/UHMWPE Nanocomposites, Russ. J. Appl. Chem., 2017, 90, 1876–1882 CrossRef CAS.
- G. Chen, Z. Ni, S. Qian and Y. Zhao, Biotribological behaviour of vitamin E-blended highly cross-linked UHMWPE in a hip joint simulator, Ind. Lubr. Tribol., 2016, 68, 548–553 CrossRef.
- X. L. Xie, C. Y. Tang, K. Y. Y. Chan, X. C. Wu, C. P. Tsui and C. Y. Cheung, Wear performance of ultrahigh molecular weight polyethylene/quartz composites, Biomaterials, 2003, 24, 1889–1896 CrossRef CAS.
- B. Wunderlich, Macromolecular Physics: v.3: Crystal Melting, Academic Pr, 1980 Search PubMed.
- A. Liberknec and S. Lagan, The use of contact angle and the surface free energy as the surface characteristics of the polymers used in medicine, Polim. Med., 2014, 44, 29–37 Search PubMed.
- H. Wang, L. Xu, J. Hu, M. Wang and G. Wu, Radiation-induced oxidation of ultra-high molecular weight polyethylene (UHMWPE) powder by gamma rays and electron beams: A clear dependence of dose rate, Radiat. Phys. Chem., 2015, 115, 88–96 CrossRef CAS.
- H. Wang, L. Xu, J. Hu, M. Wang and G. Wu, Radiation-induced oxidation of ultra-high molecular weight polyethylene (UHMWPE) powder by gamma rays and electron beams: Aclear dependence of dose rate, Radiat. Phys. Chem., 2015, 115, 88–96 CrossRef CAS.
- G. Goncalves, S. Cruz, A. Ramalho and J. Gracio, Graphene oxide versus functionalized carbon nanotubes as a reinforcing agentin a PMMA/HA bone cement, Nanoscale, 2012, 4, 2937–2945 RSC.
- L. Puppulin, A. Leto, M. Hasegawa and G. Pezzotti, A comparative microstructural study of vitamin-E blended and infused highly crosslinked UHMWPE for total knee arthroplasty, J. Mech. Behav. Biomed. Mater., 2014, 39, 247–256 CrossRef CAS PubMed.
- G. Lombardo, P. Bracco, T. S. Thornhill and A. Bellare, Crystallization pathways to alter the nanostructure and tensile properties of non-irradiated and irradiated, vitamin E stabilized UHMWPE, Eur. Polym. J., 2016, 75, 354–362 CrossRef CAS.
- C. Scemama, P. Anract, V. Dumaine, A. Babinet, J. P. Courpied and M. Hamadouche, Does vitamin E-blended polyethylene reduce wear in primary total hip arthroplasty: a blinded randomised clinical trial, Int. Orthop., 2016, 41, 1113–1118 CrossRef PubMed.
- O. Popoola, K. Mimnaugh, D. A. Orozco-villasenor and M. Peiserich, Vitamin E-grafted crosslinked ultrahigh-molecular weight polyethylene (VE-HXPE) inhibits fluid absorption and has long term oxidative stability, Biotribology, 2015, 4, 12–17 CrossRef.
- K. Doudin and S. Al-Malaika, Vitamin E-stabilised UHMWPE for orthopaedic implants: quantitative determination of vitamin E and characterisation of its transformation products, Polym. Degrad. Stab., 2016, 125, 59–75 CrossRef CAS.
- S. Affatato, J. S. Mattia, P. Bracco, E. Pavoni and P. Taddei, Does cyclic stress and accelerated ageing influence the wear behavior of highly crosslinked polyethylene, J. Mech. Behav. Biomed. Mater., 2016, 59, 418–429 CrossRef CAS PubMed.
- M. S. Mehmood, T. Yasin, M. S. Jahan, B. M. Walters, M. Ahmad and M. Ikram, EPR Study of c-Irradiated UHMWPE Doped with Vitamin E: Assessment of Thermal Effects on the Organic Radicals During Vitamin E Diffusion, Appl. Magn. Reson., 2013, 44, 531–542 CrossRef CAS.
- F. J. Buchanan, J. R. White, B. Sim and S. Downes, The influence of gamma irradiation and aging on degradation mechanisms of ultra-high molecular weight polyethylene, J. Mater. Sci.: Mater. Med., 2001, 12, 29–37 CrossRef CAS PubMed.
- M. M. Shokrieh, M. R. Hosseinkhani, M. R. Naimi-Jamal and H. Tourani, Nanoindentation and nanoscratch investigations on graphene-based nanocomposites, Polym. Test., 2013, 31, 45–51 CrossRef.
|
This journal is © The Royal Society of Chemistry 2020 |
Click here to see how this site uses Cookies. View our privacy policy here.