DOI:
10.1039/D0RA00525H
(Paper)
RSC Adv., 2020,
10, 9290-9298
Effect of ultrasonic application during KOH pretreatment and anaerobic process on digestion performance of wheat straw†
Received
17th January 2020
, Accepted 18th February 2020
First published on 4th March 2020
Abstract
The digester performance was enhanced by ultrasonic application during pretreatment and the anaerobic digestion (AD) process. Two setups (with and without ultrasonic application) were applied during pretreatment and AD, to untreated and potassium hydroxide (KOH) pretreated wheat straw. The results confirmed that the ultrasonic application enhanced the hydrolysis process during pretreatment. The highest total volatile fatty acid (TVFA) (3012 ± 18 mg L−1) production and overall lignin, hemicellulose, and cellulose (LHC) reductions (22.4 ± 0.5%) were obtained from ultrasonic assisted KOH pretreated (KOHU) samples, after 36 hours of pretreatment. Similarly, the SEM analysis showed obvious disruption in the outer structure of KOHU samples. However, the ultrasonic application during AD showed significant improvement in biodegradation rate, biogas and biomethane production. Obvious reduction in sonication time (76%) along with enhanced biogas (570 ± 9 mL gm−1 VS) and biomethane (306 ± 12 mL gm−1 VS) production were observed from KOH pretreated digesters, when ultrasonication was applied during AD. Moreover, the biodegradation rate reached up to 76% along with highest total solid (TS) and volatile solid (VS) reductions from digesters with single KOH pretreatment and ultrasonic influence during AD. Finally, the digester effluent ranged in between the stable values, confirming the completion of the AD process. These results suggested that ultrasonic application was more effective when applied during AD due to the higher liquid to solid ratio. The reduction in energy input can be beneficial for commercial applications and to recognize the better stage for ultrasonic application for enhanced biomethane yield.
Introduction
The dependence on alternative energy resources has increased due to limited availability of fossil fuels and their adverse environmental impact.1 Therefore, anaerobic digestion (AD) is considered as a sustainable alternative green energy resource compared to other chemical processes.2 Generally, the performance and stability of the AD process largely depends upon the characteristics of the biomass, as well as on the operational parameters such as pH, temperature, loading rate, and so on.3–5 By means of temperature conditions, two types of AD process, namely thermophilic and mesophilic conditions, are used on commercial scales. Thermophilic digesters have faster degradation, but are considered sensitive and require higher energy inputs compared to mesophilic AD processes.6 Therefore, mesophilic AD systems are more economical for biofuel production. However, lower biodegradation rates may affect the AD efficiency resulting in severe inhibition along with availability of undigested biomass in the digestate.7 This biodegradation rate is further affected, when dealing with agriculture wastes such as wheat, rice, and corn straws. The hydrophobic linkages between lignin and hemicellulose limits the access of anaerobic microbes to organic portion of the biomass resulting in reduced digestion rate.8
Various pretreatment techniques such as acid and alkali treatments, are reported to increase the biodegradation of agriculture waste by reducing the influence of lignin on effective bioconversion during AD.9,10 The alkali pretreatment shows more affinity to break the linkage between polysaccharides and lignin monomers, resulting in more release of hemicellulose structure due to saponification effects on biomass during pretreatment.10 Alkali pretreatment such as sodium hydroxide (NaOH), potassium hydroxide (KOH), are suggested more effective compared to acid pretreatment in commercial applications.11 However, high alkali concentrations may affect the digester stability and results in formation of inhabitant acids such as furfural and reducing biodegradation efficiency.12 Addition of co-pretreatment with alkali such as steam explosion, microwave, irradiation, adsorption and ultrasonication are reported for improving the disruption of lignin content.13–15 Yang et al.16 applied irradiation pretreatment on wheat straw using γ radiation to determine the effects and after effects of pretreatment and suggested effective breakdown of wheat straw structure. Similarly, Wu et al.17 reported that combination of alkalization and adsorption technique, in two step pretreatment of wheat straw was effective for enhanced hydrolysis during pretreatment.
Ultrasonic application can be helpful to get better result with lower alkali concentrations.18 The ultrasonic application during pretreatment are reported to increase structural disruption and process effectiveness for lignocellulosic biomasses, waste sludge, and many environmental processes.19–21 Specifically, combination of ultrasonic-assisted alkali pretreatment has shown significant improvements in biodegradation efficiency of digesters dealing with agricultural waste. Preeti et al.18 achieved 80% of delignification by applying ultrasonic assisted pretreatment to waste newspaper. Similarly, ultrasonication applications, during AD also revealed methane enhancement.22 Zou et al.23 suggested that application of ultrasonic pretreatment on wheat straw can increase the accessible surface during AD for enhanced methane yield. The application of low strength ultrasonication during AD can improve 40% of methane production during AD.24 However, there is limited work showing comparison of ultrasonic application during pretreatment and AD process.
Therefore, this study refers to the effectiveness of ultrasonic application by investigating its efficiency during KOH pretreatment and comparing with its application during AD. Though NaOH is considered cheaper than the KOH for pretreatment of wheat straw, but adding KOH during pretreatment will increase the value of the digestate in its application as bio-fertilizer.25 Therefore, KOH was given preference over NaOH. Parameters like pH variation, total volatile fatty acid (TVFA) production, surface morphology, and LHC reduction were determined to compare and evaluate the effects of single and ultrasonic assisted KOH pretreatment on wheat straw. However, ultrasonic addition during pretreatment may increase the energy input, resulting in increased operational cost. Therefore, digester performance was compared by applying two setups, with and without ultrasonic assisted treatment during pretreatment and AD of untreated, single KOH pretreated KOH, and ultrasonic assisted KOH pretreatment (KOHU) wheat straw. The object of this study was to minimize the ultrasonic energy input by reducing its time and increasing digester performance during AD. Moreover, system stability was also observed to confirm the benefits of enhanced biodegradation of wheat straw for digestate utilization. An appropriate stage with optimum energy can increase the potential of ultrasonic application for faster biodegradation and enhanced methane yields.
Materials and methods
Feedstock and inoculum
The wheat straw (WS) was obtained from agricultural farmland located at district Shunyi, Beijing. The WS was initially air-dried and then cut into small size (5–10 cm), with the help of paper cutter (PC500, Staida Co., Tianjin) and was further grounded to obtain a mesh size of 5–10 mm, through hammer mill (Fe130, Staida Co., Tianjin). The inoculum was an activated sludge obtained from an effluent of anaerobic digester plant of dairy manure (Nanwu biogas plant in Shunyi District, Beijing, China) operating under mesophilic conditions. The composition and properties of raw feedstock and inoculum, are shown in Table 1.
Table 1 Initial characteristics of wheat straw and inoculum
Parameter (%) |
Wheat straw |
Inoculum |
As received. On dry basis; all the values are mean ± SD (n = 3). |
Total solida |
94.31 ± 0.05 |
7.38 ± 0.09 |
Volatile solida |
89.40 ± 0.12 |
4.07 ± 0.04 |
Total carbonb |
43.55 ± 0.16 |
27.67 ± 1.65 |
Total nitrogenb |
1.43 ± 0.01 |
2.45 ± 0.03 |
Total hydrogenb |
5.46 ± 0.11 |
3.71 ± 0.28 |
Total LHCb |
80.00 ± 0.38 |
— |
Lignin contentb |
11.34 ± 0.53 |
— |
Hemicellulose contentb |
22.32 ± 0.27 |
— |
Cellulose contentb |
46.34 ± 0.21 |
— |
KOH pretreatment with and without ultrasonic application
The pretreatment was performed in 1.0 L bottles. The ratio of 1
:
0.04
:
6 (w/w) for WS
:
KOH
:
H2O was used to prepare all pretreatment bottles.26 Initially KOH solutions were prepared and left for a little time to remove any exothermic temperature increase. A 50 g TSL−1 of WS was added in each bottle containing KOH solution. 4% KOH concentrations were optimized in our preliminary experiments for effective disruption during ultrasonic assisted pretreatment technique. The WS was then mixed with KOH solution and placed under two separate conditions at ambient temperature (22 ± 1 °C); (i) with normal condition (without ultrasonic application) in sealed plastic bags, and (ii) with ultrasonic application during pretreatment. The ultrasonication treatment was applied through an ultrasonic bath (KH5200DE, Nanjing Xiao equipment company limited, China), operating at 20 kHz frequency and ambient temperature. The experimental device and operating conditions during ultrasonic pretreatment are shown in ESI (Fig. S1†). The temperature increase due to the cavitation in the bath was controlled to set point values by replacing the bath water with fresh water. The pH was used as prediction parameter for completion of the pretreatment process. After completion of pretreatment process, the portions of sample were taken and separated as solid and liquid for further analysis.
Anaerobic digestion process with and without ultrasonic application
The experimental setup and ultrasonic conditions during AD are shown in (Fig. 1). Equal amount of untreated WS (50 g TSL−1) was prepared in separate 1.0 L bottles and placed at ambient condition parallel to the pretreated bottles. Batch anaerobic digestion was applied in a bath with mesophilic temperature condition 37 ± 1 °C. A 15.0 g TSL−1 of inoculum was added in each bottle, which was based on study by Zhang and Zhang.27 The remaining working volume (80%) was obtained by adding distilled water in each digester. All the digesters were placed in the AD bath operating at mesophilic temperature (37 ± 1 °C). Two sets of each condition i.e. untreated, single KOH pretreated, and KOHU pretreated samples were prepared in triplicate. The first set remained in the AD bath throughout the digestion time, whereas second set was given ultrasonic treatment for 10 minutes on daily basis and without disturbing the mesophilic temperature (Fig. S1†). This was done by placing triplicate bottles for each condition in the ultrasonic bath (already maintained at mesophilic temperature) after measuring the daily biogas volume and removing the daily biogas produced. After ultrasonic treatment the bottles were placed back to anaerobic digestion bath. Two bottles containing only inoculum were also prepared as control for each set in triplicate.
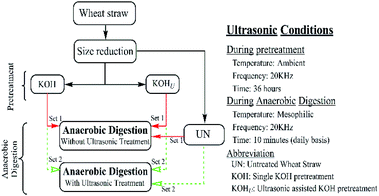 |
| Fig. 1 Experimental setup and ultrasonic conditions during pretreatment and anaerobic digestion process. | |
Kinetic model
Modified Gompertz model was applied in order to compare the experimental data with model predictions as per eqn (1).28 |
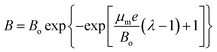 | (1) |
where B is the cumulative methane yield (CMY), Bo is the ultimate methane produced, μm is the specific methane yield rate, t is the time for AD process, λ is the phase time lag, and e is the constant value (2.72).
Biodegradability
The biodegradability was determined by using eqn (2).29 |
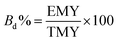 | (2) |
where TMY is the theoretical methane yield and EMY is experimental methane yield.
Analytical methods
The analysis for parameters like, total solid (TS), volatile solid (VS), alkalinity, total ammonia nitrogen (TAN) were performed as per APHA guidelines.30 Elemental composition such as total carbon and nitrogen were obtained using TC analyzer (Vario EL/micro analyzer, Germany) and the total Kjeldahl nitrogen analyzer (model KDN-2C, Shanghai), respectively. Fiber analyzer (ANKOM A2000i, country) was used to evaluate the lignin (L), hemicellulose (H), and cellulose (C) contents as per the procedure suggested by (Van Soest et al., 1991).31 Daily biogas yield were measured by water displacement method and the total sum of the daily volume was termed as cumulative yield. This volume was then calibrated to standard temperature and pressure volume by applying the ideal gas law. The gas samples were collected through rubber connections of each digester bottle (on daily basis) and the corresponding methane concentrations were determined through a gas chromatograph (GC) (HJAT, SP2100, China) equipped with detector molecular sieve packed stainless-steel column with the length and diameter of 2.0 mm × 3.0 mm (TCD) and (TDX-01) and connected to a thermal conductivity detector (TCD), and argon was used as the carrier gas. The temperature values for the injector, column, and detector were maintained at 140 °C, 150 °C, and 150 °C, respectively. For volatile fatty acid (VFA) analysis samples were first centrifuged to obtained liquid supernatants and were then filtered through 0.22 μm membrane. The concentration of VFAs in the pretreated samples and AD refuse, such as ethanol, acetic acid, propionic acid, valeric acid and butyric acid, were determined by a gas chromatograph (SHIMADZU, GC2014) equipped with a flame ionization detector (FID) and a 30 m × 0.25 mm × 0.25 μm column (Agilent, DB-WAX). Elemental analysis data was used to calculate the theoretical methane yield (TMY) of the raw wheat straw using Buswell's equation.32
Results & discussion
Effect of ultrasonic application on hydrolysis of wheat straw
The ultrasonic application during KOH pretreatment had significant effect on hydrolysis of wheat straw (Fig. 2). The pH values were determined every four hours during pretreatment, to identify the kinetics of hydrolysis process. It was observed that the pH of ultrasonic assisted KOH pretreated (KOHU) samples declined faster as compared to single KOH samples, Fig. 2(a). This was due to faster interaction of hydroxyl ions of KOH, caused by simultaneous and effective vibrations from ultrasonication process. Zhao et al.33 reported increased surface disruption and cellulose activity by cavitation from ultrasonic pretreatment on WS. The pH values of KOHU samples reached to equilibrium in 36 hours compared to the single KOH samples, which attained the similar equilibrium after 68 hours of the pretreatment process. According to previous studies, Yao et al.1 suggested 5 days of pretreatment time for wheat straw by single pretreatment with 1% urea concentration. Similarly, Zheng et al.34 suggested 3 days of pretreatment time for effective degradation of corn straw with 2% NaOH concentrations, at ambient temperature conditions and 90% moisture content. In this study, the cavitation effect caused by the ultrasonic vibrations allowed loosening of outer fiber bonding within the lignocellulosic structure of wheat straw and showed higher hydrolysis rate.33 Therefore, less pretreatment time was observed in ultrasonic influenced samples. Similar trend was observed by Xu et al.19 for ultrasonic addition during corn straw pretreatment.
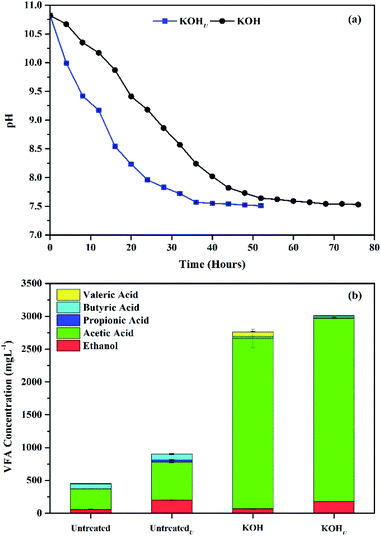 |
| Fig. 2 Effect of ultrasonic application during pretreatment of wheat straw (a) pH variation, and (b) VFA concentration. | |
Similarly, Fig. 2(b) shows the VFA concentration of untreated and KOH pretreated samples with and without ultrasonic application. Significant increase in TVFA production was observed in all samples under ultrasonic influence during pretreatment as compared to the samples without ultrasonication application. The untreatedU samples produced 903.47 ± 5.22 mg L−1 of TVFA, which was 100% more than the TVFA values of untreated WS samples without ultrasonic influence. The KOHU produced the highest TVFA (3012 ± 18 mg L−1) among all samples, with 6.6 times higher TVFAs than the untreated WS sample. However, there was very little variation in TVFA values of single KOH pretreated samples compared to KOHU. This can be explained as the ultrasonic collusions responded in structural vibrations which increased the outer surface gaps during pretreatment and the disruption was in actual due to alkali contact absorbing the organic matter from wheat straw.35 Therefore, the addition of ultrasonic treatment influenced the reaction time during hydrolysis of wheat straw and more TVFA were released in less time compared to the samples without ultrasonic contact during pretreatment process. Likewise, Zhong et al.35 also achieved enhanced saccharification (92.4%), by combining ultrasonic application with quaternary ammonium hydroxide (15% aqueous solution) pretreatment on wheat straw. The results in this study confirms the positive influence of ultrasonic application for increasing the kinetic rate of wheat straw hydrolysis, which can be helpful to treat more amount of biomass in less time.
Effect on main composition after pretreatment
Table 2 shows the individual and overall LHC reductions of untreated and KOH pretreated WS samples, after normal and ultrasonic assisted KOH pretreatment. It was observed that single ultrasonication application had no significant effect on WS for LHC reductions. This can be explained as the ultrasonication effects on the outer layer of the WS and requires organic content from WS. The lignin are phenolic compounds and has more affinity with hydroxyl ions, therefore the lignin disruption was more obvious in KOH pretreated samples with or without ultrasonic application.36 Moreover, the KOH pretreated sample with and without ultrasonic treatment showed a larger difference in the respective reduction of lignin and hemicellulose content. These results confirmed that the ultrasonic application considerably affected the outer layer of WS, which allowed deeper penetration of KOH ions. The pretreatment time for KOH and KOHU samples were also essential for demonstrating the ultrasonic influence on WS. As the time taken by KOHU samples was 52.92% less as compared to single KOH pretreated samples. These results suggested that the ultrasonic vibration successfully influenced the outer rigid surface of WS, resulting in maximum lignin removal, in less pretreatment time. Therefore, the highest LHC reductions were achieved by KOHU samples (22.38 ± 0.51%), which were 7.42 and 1.19 folds higher than the untreated and KOH sample, respectively. Similar difference in the individual LHC content reductions were also observed from KOHU samples compared to untreated and single KOH pretreatment. The hemicellulose content was most effected KOHU samples and reached to highest reduction at 29.60 ± 1.03%.
Table 2 LHC reductions of untreated and KOH pretreated wheat straw, with and without ultrasonic applicationa
Content |
LHCb (%) |
Celluloseb (%) |
Hemicellulose (%) |
Ligninb (%) |
All value are mean ± SD (n = 3). On a dry basis. |
UntreatedU |
2.53 ± 0.46 |
1.67 ± 1.08 |
2.83 ± 0.66 |
5.57 ± 0.96 |
KOH |
18.79 ± 0.39 |
16.99 ± 0.45 |
21.31 ± 1.33 |
19.58 ± 2.04 |
KOHU |
22.38 ± 0.51 |
16.71 ± 1.74 |
29.60 ± 1.03 |
26.96 ± 0.85 |
Effect on physical morphology
The SEM analysis results are shown in Fig. 3. The ultrasonic application during KOH pretreatment had great influence on the physical disruption of wheat straw. The untreated WS sample (Fig. 3(a)) showed longer, straight, and attached fibers, whereas the single KOH pretreated samples (Fig. 3(b)) were completely destroyed with clear appearance of broken backbone of the fiber. On the other hand, numerous small holes were observed throughout the surface of KOHU samples (Fig. 3(c)), indicating severe disruption. These results confirmed that the ultrasonic application totally destroyed the outer layer which is supposed to give maximum resistance to release organic content during pretreatment. However, the increased effectiveness of ultrasonic application during AD can be explained as there was more liquid to solid ratio available for ultrasonication process during AD, thereby, more effect of ultrasonic process was observed.37
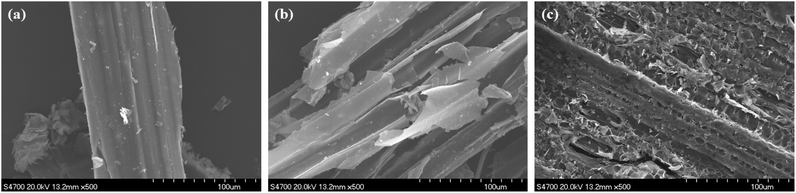 |
| Fig. 3 SEM images for untreated (a); single KOH pretreatment (b); and ultrasonic assisted KOH pretreatment (c) of wheat straw. | |
Effect on biogas and methane yield
In this work, an obvious difference in daily as well as cumulative yields of biogas and methane were observed from anaerobic digesters with ultrasonic influence (ADU), as shown in Fig. 4(a–d). There was negligible variation in biogas production during first week from all KOH pretreated digesters, with or without ultrasonic treatment during AD (Fig. 4(a and b)). This could be attributed to sufficient availability of organic content in all the KOH digesters at early stage of digestion process. The biogas and methane production was increased from second week in all ADU, indicating further release of VFAs due to ultrasonication effect.13 Additionally, a clear boost in KOH-ADU was observed from second week, which continued till the end of digestion time. The KOH-ADU reached to the highest cumulative biogas yield (CBY) with 569.89 ± 9.09 mL g−1 VSloaded in 50 days of digestion time. Similarly, the CBY from KOHU-ADU, and untreated ADU digesters reached to 475.77 ± 12.44 and 414.76 ± 12.58 mL g−1 VSloaded, respectively. The untreated, KOH, KOHU digesters without ultrasonic influence could reach only 354.44 ± 13.61, 428.92 ± 13.46 and 482.42 ± 17.12 mL g−1 VSloaded, respectively. These results indicated that addition of ultrasonication during AD was more effective as compared to the pretreatment stage. Tao Yu et al.15 also reported similar increments in the biogas production when applied microwave pretreatment on swine manure. Moreover, comparison between ultrasonic treatment during both stages (KOHU-ADU) with KOHU showed no significant difference in biogas yield.
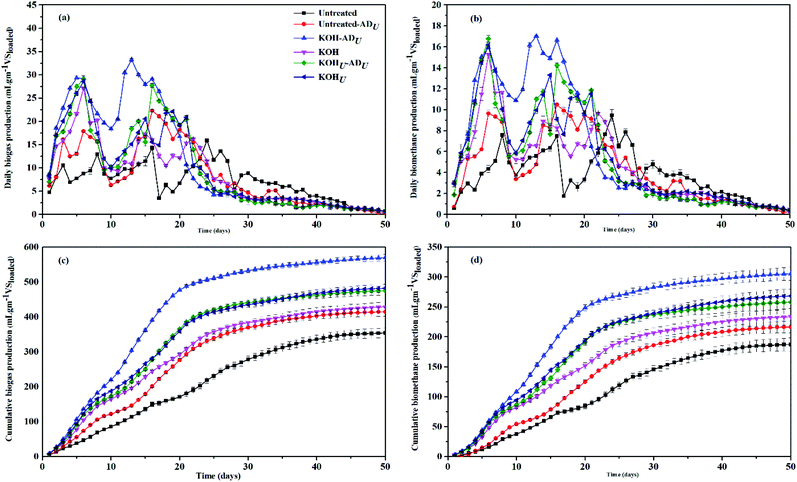 |
| Fig. 4 (a–d) Daily and cumulative biogas and biomethane productions. | |
Similarly, the daily and cumulative biomethane productions (Fig. 3(b and d)), for the digesters under ultrasonic influence ADU, remained higher throughout the digestion time. However, the relative boost in daily methane production was more obvious in ADU digesters compared to normal AD digesters. Among all digesters, KOH-ADU reached to highest values with 305.57 ± 11.71 mL g−1 VSloaded cumulative methane yield (CMY). Similarly, the CMY for untreated, untreatedU, KOH, KOHU, KOHU-ADU were at 188 ± 11, 217 ± 10, 234 ± 14, 259 ± 13 and 268 ± 12 mL g−1 VSloaded, respectively. The reason for this increased digester performance can be postulated as; (i) the simultaneous utilization of VFA produced during pretreatment of WS and production of more VFA due to ultrasonic vibrations during AD and, (ii) the ultrasonic application during AD allowed more free movement of the anaerobic microbes within the biomass, resulting in more biodegradation. These results suggest that ultrasonic addition during AD increases the digester performance along with effective increase in methane production.
However, an obvious difference in the Bd values were observed in all digesters under ultrasonic influence during AD process compared to the one with no ultrasonication. This increase in Bd values in ADU can be attributed to the high liquid to solid ratio during anaerobic digestion process which helped in increasing the effects of ultrasonication throughout the substrate.37 The another reason for this increased biodegradation can be possible VFA utilization during AD, which did not caused inhibition due to higher acidification.38,39 Thus, increased digester performance was observed in ultrasonic assisted anaerobic digester for all substrate types.
Effect on biodegradability and biodegradation rate
The biodegradability (Bd) of both untreated, KOH digesters with and without ultrasonic treatment, were calculated using eqn (2). The biodegradability results suggested that application of ultrasonic technique during AD had significantly increased in the digester performance compared to its application during pretreatment stage. The biodegradability of untreated wheat straw digester, untreated-ADU, KOH, KOH-ADU, KOHU, and KOHU-ADU digesters reached to 46.72, 53.99, 58.23, 76.15, 66.85, and 64.37%, respectively. There was no significant difference in Bd of digesters with ultrasonic application during both stages (KOHU and KOHU-ADU). This could be attributed to the fact that most of TVFAs were released during pretreatment and had no further effect on ultrasonication during AD. Similarly, T80 values were also calculated to evaluate the biodegradation rate. Lower T80 values in ultrasonic assisted anaerobic digesters, suggested faster biodegradation rates, compared to the digester without ultrasonic application during AD. The KOH-ADU reached the fastest T80 value, on 20th day of anaerobic digestion process compared to 25th day of T80 from single KOH digestion, when no ultrasonication was applied.
Similarly, the corresponding T80 values for untreated, untreated-ADU, KOHU, and KOHU-ADU, were achieved on 32nd, 27th, 24th, and 22nd day, respectively. These results suggested that the specific CMP values on the T80 were higher in ADU than the normal AD, indicating higher biodegradation rates. Moreover, the optimized time duration for ultrasonic application during pretreatment was 36 h, and the total time for ultrasonic application during AD (10 minutes on daily basis for each group) accounted 8.33 hours, only. These results confirmed that ultrasonic application was more feasible during the AD stage, due to less energy input requirement (76.9%) compared to pretreatment stage.
Kinetic model
Modified Gompertz law was applied to fit the biomethane production data, using eqn (1). Table 3 shows different parameters of modified Gompertz model for both types of anaerobic digesters of untreated, KOH, and KOHU wheat straw. The R2 values ranged in between 0.995–0.999, which reflects successful simulation of the model for this study. The Bo values predicted by model were also in agreement to the EMY. The highest EMY from KOH-ADU digesters suggested to be best combination with ultrasonic application for effective digester performance. The λ values showed no difference for both sets of digester with or without ultrasonic application. This was also in agreement to the experimental results as the difference in the ultrasonic assisted anaerobic digester was observed after first week, and all the digester had sufficient organic content at initial stage of digestion process. However, μm values observed from all ADU digesters were slight higher compared to corresponding set of digester without ultrasonic influence. This increase confirmed the hypothesis of late but higher biodegradation rate in ultrasonic assisted AD processes. However, the experimental values of μm were little higher as compared to the model prediction. The experimental μm achieved by untreated, untreatedU, KOH, KOH-ADU, KOHU, and KOHU-ADU, were 9.48 ± 0.55, 10.50 ± 0.09, 15.25 ± 0.13, 17.08 ± 0.06, 16.19 ± 0.29, and 16.78 ± 0.32 at 24th, 16th, 6th, 13th, 6th, and 6th day, respectively.
Table 3 Comparison of model prediction with experimental methane productiona
Parameter |
AD without ultrasonic application |
AD with ultrasonic application |
Untreated |
KOH |
KOHU |
Untreated |
KOH |
KOHU |
All values are mean ± SD (n = 3). |
R2 |
0.9688 |
0.9799 |
0.9805 |
0.9791 |
0.9934 |
0.9754 |
Bo |
165.34 ± 7.18 |
202.05 ± 6.48 |
235.31 ± 7.36 |
198.07 ± 6.90 |
291.15 ± 4.83 |
232.83 ± 8.02 |
μm |
7.68 ± 0.01 |
12.09 ± 0.03 |
14.77 ± 0.08 |
10.22 ± 0.02 |
18.05 ± 0.03 |
14.64 ± 0.06 |
λ |
5.74 ± 0.25 |
3.04 ± 0.14 |
3.07 ± 0.13 |
5.64 ± 0.19 |
3.45 ± 0.09 |
3.45 ± 0.15 |
EMY |
187.47 ± 10.93 |
233.66 ± 13.59 |
268.27 ± 11.87 |
216.67 ± 9.94 |
305.58 ± 11.71 |
258.30 ± 12.87 |
TS and VS reductions
Table 4 shows the TS and VS reduction after anaerobic digestion process. In consistent to biogas and biomethane results, the TS and VS reduction for ultrasonic assisted anaerobic digesters were higher compared to the conventional digesters. The change between ADU and AD digesters were also statistically significant at (∞ < 0.05). The highest TS and VS reductions were observed in KOH-ADU digester, reflecting conversion of more organic content from anaerobic microbes. This could be explained as KOH pretreatment of wheat straw partially disrupted the lignin cross linkage and ultrasonic vibrations during AD further loosen the linkage allowing microbes deeper access to more dry matter. Thus more biodegradation was observed from KOH-ADU digesters, with higher TS and VS reductions.
Table 4 TS and VS reduction after AD processa
Substrate |
AD |
ADU |
TS reduction (%) |
VS reduction (%) |
TS reduction (%) |
VS reduction (%) |
All the values are mean ± SD (n = 3). |
Untreated |
44.40 ± 0.03 |
56.70 ± 0.03 |
46.15 ± 0.09 |
65.05 ± 0.09 |
KOH |
45.58 ± 0.07 |
55.84 ± 0.07 |
64.10 ± 0.05 |
76.08 ± 0.04 |
KOHU |
48.87 ± 0.04 |
62.62 ± 0.04 |
63.42 ± 0.04 |
73.68 ± 0.05 |
Digestate characteristics
Table 5 shows the characteristics of digester refuse after anaerobic digestion process. The pH value for all digesters refuse were within the stable digester effluent range and did not required any adjustment after anaerobic digestion process.40 Similarly, the total ammonia nitrogen (TAN), value ranged between 303 to 355 mg N–NH4 L−1. These values were also in agreement with the stable ranges of digester effluents.41 TA values were high indicating sufficient buffering potential for any acidification. However, the untreated wheat straw digesters with normal AD showed, comparatively lower alkalinity values. All the values TVFA were higher than the minimum limit required for buffering the nitrification effect.42 Finally the values like TA/TVFA were also measured to identify the digester stability. The lower TVFA/TA ratio showed negative possibility for acidification and revealed that no further treatment was required to digestate.43
Table 5 Effluents characteristics after anaerobic digestiona
Parameter |
Unit |
AD without ultrasonic application |
AD with ultrasonic application |
Untreated |
KOH |
4% KOHU |
Untreated |
KOH |
KOHU |
All the values are mean ± SD (n = 3). |
Total solid |
% |
3.59 ± 0.5 |
4.10 ± 0.5 |
3.40 ± 0.2 |
3.13 ± 0.5 |
2.45 ± 0.6 |
2.45 ± 0.9 |
Volatile solid |
% |
2.66 ± 0.41 |
2.61 ± 0.24 |
2.29 ± 0.15 |
2.23 ± 0.41 |
1.67 ± 0.50 |
1.57 ± 0.69 |
Carbon |
% |
40.35 ± 1.2 |
36.27 ± 1.0 |
35.87 ± 1.0 |
37.90 ± 1.1 |
33.82 ± 1.0 |
35.86 ± 1.1 |
Nitrogen |
% |
1.90 ± 0.1 |
2.17 ± 0.2 |
2.01 ± 0.1 |
1.58 ± 0.1 |
1.63 ± 0.1 |
1.77 ± 0.1 |
Hydrogen |
% |
4.97 ± 0.2 |
4.75 ± 0.1 |
4.13 ± 0.1 |
5.18 ± 0.2 |
4.48 ± 0.1 |
4.41 ± 0.1 |
LHC content |
% |
51.9 ± 2.4 |
45.91 ± 3.4 |
42.31 ± 0.35 |
52.74 ± 2.35 |
43.65 ± 0.35 |
44.18 ± 1.35 |
Hemicellulose |
% |
15.1 ± 0.5 |
13.68 ± 1.1 |
12.62 ± 0.3 |
14.34 ± 0.1 |
12.73 ± 0.7 |
13.04 ± 0.4 |
Cellulose |
% |
19 ± 0.7 |
14.7 ± 2.0 |
12.7 ± 0.9 |
19.2 ± 2.00 |
12.5 ± 1.5 |
13.54 ± 0.8 |
Lignin |
% |
17.78 ± 0.6 |
17.55 ± 1.4 |
17.03 ± 0.7 |
19.16 ± 0.2 |
18.45 ± 1.3 |
17.60 ± 0.7 |
TAN |
mg L−1 |
359 ± 18 |
345 ± 29 |
315 ± 30 |
351 ± 7.50 |
355 ± 29 |
303 ± 37 |
Alkalinity |
g L−1 |
2.65 ± 0.2 |
6.49 ± 0.6 |
4.40 ± 0.1 |
6.04 ± 0.1 |
4.07 ± 0.5 |
4.86 ± 0.6 |
pH |
— |
7.18 ± 0.01 |
7.38 ± 0.02 |
7.15 ± 0.03 |
7.19 ± 0.02 |
7.28 ± 0.01 |
7.28 ± 0.08 |
TVFA |
mg L−1 |
85.36 ± 15.17 |
75.03 ± 4.19 |
73.21 ± 5.36 |
84.63 ± 22.71 |
85.89 ± 2.99 |
95.30 ± 9.81 |
TVFA/TA |
— |
0.03 |
0.01 |
0.02 |
0.01 |
0.02 |
0.02 |
Conclusions
The ultrasonic application is one of the effective and promising method to overcome slower biodegradation rates for lignocellulosic based substrates. The increase in hydrolysis rate during pretreatment confirmed that addition of ultrasonic application disrupted more organic content from wheat straw. As a result, pH declined faster with more TVFA release in less pretreatment time compared to normal pretreatment without ultrasonication. Similarly, highest LHC reduction was were observed from KOHU samples (22.38%) compared to untreated and single KOH pretreated wheat straw. However, the ultrasonic effects were more obvious when applied during AD. The highest biogas and methane yield was achieved by KOH-ADU (569.89 ± 0.79 and 305.58 ± 0.85 mL g−1 VSloaded respectively), which were 32.86 and 63.0% higher than the untreated digester, without ultrasonication during AD. Moreover, significant difference in energy input were also observed from ultrasonic application during pretreatment (36 h) and AD (8.33 h) reflecting 76.9% reduction in ultrasonic time. These results suggested the ultrasonic application was more beneficial during AD stage compared to pretreatment, for increasing biodegradation rate as well as biomethane yield.
Conflicts of interest
There are no conflicts to declare.
Acknowledgements
The authors are grateful to the funding supports from Pretreatment Technology Development for Anaerobic Digestion of Crops Straw, Yuan Yi Biomass S&T Company of China (No. H2015198).
Notes and references
- Y. Yao, A. D. Bergeron and M. Davaritouchaee, Renewable Energy, 2018, 115, 139–148 CrossRef CAS.
- S. K. Cho, D. H. Kim, I. S. Jeong, H. S. Shin and S. E. Oh, Bioresour. Technol., 2013, 141, 167–173 CrossRef CAS PubMed.
- S. P. Lohani and J. Havukainen, in Waste Bioremediation, Energy, Environment, and Sustainability, Springer, Singapore, 2018, pp. 343–359 Search PubMed.
- C. Mao, X. Wang, J. Xi, Y. Feng and G. Ren, Energy, 2017, 135, 352–360 CrossRef CAS.
- A. F. Soomro, Z. Ni, L. Ying and J. Liu, RSC Adv., 2019, 9, 18147–18156 RSC.
- H. Bouallagui, O. Haouari, Y. Touhami, R. Ben Cheikh, L. Marouani and M. Hamdi, Process Biochem., 2004, 39, 2143–2148 CrossRef CAS.
- N. Ülgüdür and G. N. Demirer, Water Environ. Res., 2019, 91, 259–268 CrossRef PubMed.
- C. R. Yin, D. Il Seo, M. K. Kim and S. T. Lee, Biotechnol. Lett., 2000, 22, 1531–1535 CrossRef CAS.
- Z. Song, G. Yang, X. Liu, Z. Yan, Y. Yuan and Y. Liao, PLoS One, 2014, 9, 1–8 Search PubMed.
- C. Mao, Y. Feng, X. Wang and G. Ren, Renewable Sustainable Energy Rev., 2015, 45, 540–555 CrossRef CAS.
- H. Chen, J. Liu, X. Chang, D. Chen, Y. Xue, P. Liu, H. Lin and S. Han, Fuel Process. Technol., 2017, 160, 196–206 CrossRef CAS.
- L. J. Jönsson and C. Martín, Bioresour. Technol., 2016, 199, 103–112 CrossRef PubMed.
- M. Shanthi, J. Rajesh Banu and P. Sivashanmugam, Fuel, 2019, 250, 194–202 CrossRef CAS.
- M. Wu, H. Liu and C. Yang, Int. J. Environ. Res. Public Health, 2019, 16, 205 CrossRef PubMed.
- T. Yu, Y. Deng, H. Liu, C. Yang, B. Wu, G. Zeng, L. Lu and F. Nishimura, Sci. Rep., 2017, 7, 1–8 CrossRef.
- C. Yang, Z. Shen, G. Yu and J. Wang, Bioresour. Technol., 2008, 99, 6240–6245 CrossRef CAS PubMed.
- M. Wu, H. Liu, J. Guo and C. Yang, Appl. Microbiol. Biotechnol., 2018, 102, 9831–9842 CrossRef CAS PubMed.
- P. B. Subhedar and P. R. Gogate, Ultrason. Sonochem., 2014, 21, 216–225 CrossRef CAS PubMed.
- X. Xu, R. Tu, Y. Sun, Y. Wu, E. Jiang and J. Zhen, Bioresour. Technol., 2019, 271, 427–438 CrossRef CAS PubMed.
- H. Bao, L. Jiang, C. Chen, C. Yang, Z. He, Y. Feng, W. Cai, W. Liu and A. Wang, RSC Adv., 2015, 5, 48468–48473 RSC.
- Z. Y. Xiong, Y. H. Qin, J. Y. Ma, L. Yang, Z. K. Wu, T. L. Wang, W. G. Wang and C. W. Wang, Bioresour. Technol., 2017, 227, 408–411 CrossRef CAS PubMed.
- S. K. Cho, D. H. Kim, M. H. Kim, H. S. Shin and S. E. Oh, Bioresour. Technol., 2012, 120, 84–88 CrossRef CAS PubMed.
- S. Zou, H. Wang, X. Wang, S. Zhou, X. Li and Y. Feng, Appl. Energy, 2016, 179, 191–202 CrossRef CAS.
- S. K. Cho, Y. H. Hwang, D. H. Kim, I. S. Jeong, H. S. Shin and S. E. Oh, Bioresour. Technol., 2013, 136, 66–72 CrossRef CAS PubMed.
- M. Jaffar, Y. Pang, H. Yuan, D. Zou, Y. Liu, B. Zhu, R. M. Korai and X. Li, Chin. J. Chem. Eng., 2016, 24, 404–409 CrossRef.
- M. Zheng, X. Li, L. Li, X. Yang and Y. He, Bioresour. Technol., 2009, 100, 5140–5145 CrossRef CAS PubMed.
- R. Zhang and Z. Zhang, Bioresour. Technol., 1999, 68, 235–245 CrossRef CAS.
- M. H. Zwietering, I. Jongenburger, F. M. Rombouts and K. Van't Riet, Appl. Environ. Microbiol., 1990, 56, 1875–1881 CrossRef CAS PubMed.
- E. Elbeshbishy, G. Nakhla and H. Hafez, Bioresour. Technol., 2012, 110, 18–25 CrossRef CAS PubMed.
- APHA-AWWA-WEF, Standard Methods for the Examination of Water and Wastewater, 20th edn, 1998 Search PubMed.
- P. J. Van Soest, J. B. Robertson and B. A. Lewis, J. Dairy Sci., 1991, 74, 3583–3597 CrossRef CAS PubMed.
- A. M. Buswell and H. F. Mueller, Ind. Eng. Chem., 1952, 44, 550–559 CrossRef CAS.
- S. Zou, X. Wang, Y. Chen, H. Wan and Y. Feng, Energy Convers. Manag., 2016, 112, 226–235 CrossRef CAS.
- M. Zheng, L. Li, X. Li, J. Xioang, T. Mei and G. Chen, Energy Sources, Part A Recovery, Util. Environ. Eff., 2010, 32, 1918–1925 CrossRef CAS.
- C. Zhong, H. Jia and P. Wei, Process Biochem., 2017, 53, 180–187 CrossRef CAS.
- A. U. Buranov and G. Mazza, Ind. Crops Prod., 2008, 28, 237–259 CrossRef CAS.
- X. Lu, Z. Zheng, H. Li, R. Cao, Y. Zheng, H. Yu, J. Xiao, S. Miao and B. Zheng, Ind. Crops Prod., 2017, 107, 546–557 CrossRef CAS.
- G. H. R. Braz, N. Fernandez-Gonzalez, J. M. Lema and M. Carballa, Chemosphere, 2019, 222, 323–332 CrossRef CAS PubMed.
- A. F. Soomro, I. A. Abbasi, Z. Ni, L. Ying and J. Liu, Bioresour. Technol., 2020, 304, 122980 CrossRef CAS PubMed.
- H. Zheng, M. Liu, Q. Lu, X. Wu, Y. Ma, Y. Cheng, M. Addy, Y. Liu and R. Ruan, Bioresour. Technol., 2018, 249, 479–486 CrossRef CAS PubMed.
- L. Gao, M. H. Sun, X. Z. Liu and Y. S. Che, Mycol. Res., 2007, 111, 87–92 CrossRef CAS PubMed.
- M. R. Haider, Z. Sheikh, S. Yousaf, R. N. Malik and C. Visvanathan, Bioresour. Technol., 2015, 190, 451–457 CrossRef CAS PubMed.
- X. Liu, R. Bayard, H. Benbelkacem, P. Buffière and R. Gourdon, Biomass Bioenergy, 2015, 81, 534–543 CrossRef CAS.
Footnote |
† Electronic supplementary information (ESI) available. See DOI: 10.1039/d0ra00525h |
|
This journal is © The Royal Society of Chemistry 2020 |
Click here to see how this site uses Cookies. View our privacy policy here.