DOI:
10.1039/D0RA03025B
(Paper)
RSC Adv., 2020,
10, 18936-18944
Rapid solidification of Portland cement/polyacrylamide hydrogel (PC/PAM) composites for diverse wastewater treatments
Received
3rd April 2020
, Accepted 11th May 2020
First published on 19th May 2020
Abstract
Cementitious solidification is an effective but time-consuming method for waste disposal, and the incorporation of polyacrylamide hydrogel in Portland cement paste is a simple way to enhance the time-efficiency of cementitious solidification. In this study, a series of Portland cement/polyacrylamide hydrogel (PC/PAM) composites suitable for the wastewater treatment were prepared by a one-pot method and their time-dependent reaction processes, mechanical properties and microstructures were tested. Based on the gelation time method, PC/PAM composites showed great solidification efficiency when treating simulated radioactive liquids, organic dye waste and solutions with strong alkalinity and acidity. At temperatures ranging from 5 °C to 40 °C, it took only a few minutes for these composites to solidify wastes. Also, PC/PAM composites containing wastes had a compressive strength that is more than 2 MPa after reacting for 3 days and were suitable for landfill or secondary treatments. The rapid gelation and sufficient strength development demonstrated that PC/PAM composites have great potential for application in solidifying multi-component wastes, especially in some emergency circumstances.
1. Introduction
In both developing and developed countries, a growing number and types of pollutants, originating from industrial, agricultural and municipal human activities, are emerging in water and doing great harm to ecosystems and human health.1,2 Such wastewaters contain a high level of microbial pathogens, toxic metals, organic matters and particles, and some technologies, such as flocculation and filtration,3,4 adsorption,5 solvent extraction,6 ion exchange,7 membrane processes8 and chemical precipitation,9 have been developed for wastewater treatment. However, their distinctive features determine the difficulty of treating wastewaters with both low-cost and energy-efficiency. Different from these above technologies, the solidification method, a process that converts the waste into a stable solid form with a low leachability and zero liquid discharge after treatment, has been acknowledged as a process with low cost, robustness and wide applicability.10,11 Various matrixes are identified as candidates for waste solidification, such as cements,12,13 ceramics,14 glasses15 and polymers.16 Due to the distinguished features of long-term stability, high waste loadings and low cost, Portland cement-based solidification has been recognized as the “best demonstrated available technology” by the US Environmental Protection Agency for land disposal of various wastes17 and has been successfully used for disposals of heavy metals,18 nuclear waste,19 alkaline chemicals,20 etc.
Contaminants can be encapsulated through physical and/or chemical means in Portland cement matrix.19 Contaminants are likely to be adsorbed inside the cement reaction products21–23 and the pores with substantial surface areas that formed during cement reaction.24 For special contaminants, they can also be bound by chemical actions through formation of insoluble complexes or hydroxides in alkaline environment,25 ion exchange between wastes and crystalline phases,26,27 or ion integration in defects of amorphous products.28,29 Though having an effective solidification, it usually takes several hours for cement to set to solidify wastes,30,31 and may be even longer when some types of wastes inhibit cement reacting with water.32–34 Therefore, cementitious solidification method sometimes is hard to be considered as a time-efficient technique and is difficult to achieve rapid solidification when emergencies occur. This necessitates the accelerating of cement setting and reaction to broaden its applicability for multi-component wastes solidification, especially in some emergency circumstances, such as severe nuclear accidents and industrial chemical leakage.
According to our preliminary laboratorial experiments, a few hydrogels can accelerate the fixation and solidification of cement particles through their gelation processes. Also, hydrogels have exhibited superior performance in the adsorptive removal of a wide range of aqueous contaminants.35,36 Therefore, combining the advantages of Portland cement and hydrogel for wastes treatment, a serials of Portland cement/polyacrylamide hydrogel (PC/PAM) composites were designed and synthesized by a one-pot method in this study, aiming at providing a new and efficient treatment for various wastewaters. To the best of our knowledge, this is the first time for this type of composite to be used for water treatment. The heat released by cement hydration accelerated polyacrylamide hydrogel gelation to form a soft network, and the network in turn fixed cement particles to form a rigid and fragile skeleton to solidify wastes. Moreover, the pore structure in polyacrylamide backbone promoted the waste adsorption. In this work, the properties of PC/PAM composites were first characterized in respect of the reaction behaviors, the time-dependent mechanical properties and the microscopic structures. Then, the gelation times of composites containing cesium ions, dye, alkali and acid were determined to study the solidification efficiency, while the early mechanical properties of solidified waste forms were measured to evaluate the stability of treated wastewaters.
2. Experimental
2.1. Raw materials
Acrylamide (AM) and ammonium persulfate (APS), with an analytical purity, were purchased from Sinopharm Chemical Reagent. N,N′-Methylene acrylamide (MBA) was brought from Energy Chemical and had a purity of 99%. A class P·II 52.5 Ordinary Portland cement (OPC) was provided by Jiangnan-Xiaoyetian Co, Ltd and its chemical and mineral compositions are listed in Table 1, which were determined by X-ray fluorescence and X-ray diffraction respectively. Cesium chloride (99.9% metals basis, Aladdin), methyl orange (IND, Nanjing Chemical Reagent), sodium hydroxide (Analytical reagent, Sinopharm Chemical Reagent) and sulfuric acid (Analytical reagent, Shanghai Lingfeng Chemical Reagent) were selected to prepare wastewater forms. Deionized water was used in this study.
Table 1 Chemical and mineral compositions of Portland cement
Oxides |
SiO2 |
Al2O3 |
Fe2O3 |
CaO |
MgO |
SO3 |
K2O |
Na2O |
TiO2 |
Loss on ignition |
wt% |
19.70 |
4.45 |
2.93 |
63.62 |
1.28 |
2.93 |
0.68 |
0.12 |
0.27 |
1.09 |
Minerals |
C3S |
C2S |
C3A |
C4AF |
Calcite |
Bassanite |
Quartz |
wt% |
59.8 |
15.4 |
7.6 |
7.1 |
5.5 |
4.2 |
0.4 |
2.2. Synthesis and characterization of PC/PAM composites without contaminants
2.2.1. One-pot process to prepare PC/PAM composites. PC/PAM composites were produced by an in situ polymerization method, and the procedure is illustrated in Fig. 1. First, the monomer AM with various concentrations and the crosslinker MBA were dissolved in two-third of total amount of water used, and the initiator APS solution was added dropwise to form the mixing-solution: AM/APS/MBA/cement/total water = (4, 8, 12) g/3 g/28 mg/(30, 60, 120) g/60 g. Then, mixed cement with mixing-solution by vortex oscillator for 30 s to prepare the composites. In the following part of this work, the symbol PCa/PAMb is used to distinguish different mix proportions. For instance, PC120/PAM8 indicates the mixture with 120 g cement and 8 g AM. Before performing the tests, all the samples were cured at 20 °C.
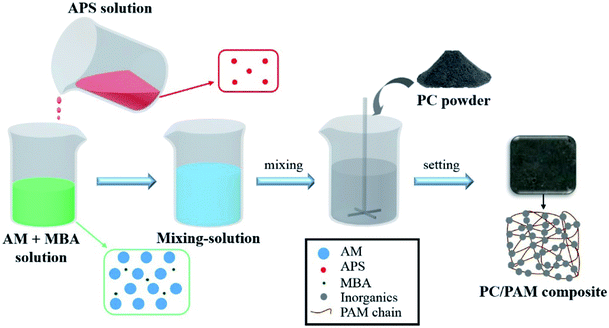 |
| Fig. 1 Synthetic procedure for the preparation of PC/PAM composites. | |
2.2.2. Properties characterization of PC/PAM composites. The solidification of waste forms is a result of the setting and reaction of cement paste, and the influence of PAM in the composites on the reaction process of cement (i.e., the reaction speed and the products composition) was investigated.The reaction of composites is an exothermic process, and the rate of heat release can reveal the speed of reaction. An 8-channel isothermal calorimeter (TAM Air, Sweden) was applied to record the heat flow data to investigate the influence of PAM hydrogel on the reaction of composites. Each fresh mixture was placed in a sealed ampoule, and the ampoule was then loaded into the calorimeter to carry out data collection under a constant temperature of 20 ± 0.01 °C. Besides PC/PAM composites, plain cement paste with a constant water to cement mass ratio (0.5) was also prepared and all the heat flow data collected were normalized by cement mass used for comparison. For the time-dependent phase composition characterization, X-ray diffractometer (Brucker D8-Discover, Germany) with Cu Kα radiation was used to conduct measurements in the 2θ range from 5° to 65°. All samples were cured in water till prescribed ages (e.g., 3 days and 7 days), then were soaked in alcohol to terminate the reactions, followed by vacuum drying, grinding and sieving at 80 μm. Corundum powder (α-Al2O3 ≥ 99.99%) was used as an internal standard in XRD tests and the phase contents were quantitatively analyzed by using TOPAS v4.0 software based on Rietveld method and the Rwp in all cases is lower than 7%.
The incorporation of PAM introduces network microstructure into the hardened composites, increasing internal specific surface areas and toughening the composites.
Scanning electron microscopy (FEI 3D, America) in secondary electron mode at an accelerating voltage of 15 kV was used to characterize the microstructure of the composites. Freeze-drying method was adopted to minimize the damage of porous network which may be induced by drying. All the samples were rapidly frozen by liquid nitrogen (−196 °C) for 15 min and then lyophilized for 2 days.
An in situ symmetrical tensile test system (Care IBTC-2000, China) was used to determine the toughened mechanical properties of the composites, i.e., tensile strength and compressive behaviors. The samples for tensile tests were of ribbon-like shape 7 mm in width and 3 mm in thickness. Tension was applied with a loading rate of 0.3 mm s−1. The samples for compression tests and cyclic compression tests were of rod-like shape 9.9 mm in diameter and 15 mm in length, and were compressed at a loading rate of 0.03 mm s−1 till the maximum force of 1800 N or maximum strain value of 60% was reached, limited by the machine.
2.3. Solidification of waste forms by PC/PAM composites
2.3.1. Preparation of wastewaters. To verify the applicability and efficiency of this cementitious solidification method, we prepared four types of simulated wastewaters. 0.1 M cesium chloride, 0.01 M methyl orange, 0.01 M sodium hydroxide and 0.005 M sulfuric acid were added into mixing-solutions (Fig. 1) to prepare wastewaters containing a relative high concentration of simulated radioactive liquids, organic dye waste and solutions with strong alkalinity and acidity respectively.
2.3.2. Performance evaluation. Gelation time method was adopted to determine the efficiencies of solidification, by using the test tube inversion method.37,38 Briefly, each fresh mixture was incubated in a vial which was then inverted every 10 s to observe the flow ability. The gelation time was defined as the time that the mixture no longer flowed anymore, i.e., the mixture did not fall when the vial was completed inverted. Experiments were designed and carried out to study the effects of cement concentration, AM concentration and temperature (5 °C, 20 °C and 40 °C) on the solidification efficiencies.The compressive strengths of solidified waste forms were investigated by an electric universal testing machine (SUNS UTM 7305, China) according to Chinese Standard GB/T 17671-1999. The incorporation of PAM changed the failure mode of composites from brittle to ductile, and the strengths of 3 days age samples were recorded when the samples were compressed till 40% deformation rather than completely squashed.
3. Results and discussion
3.1. Reaction of PC/PAM composites without contaminants
The reaction of cement with water and the polymerization of AM are all exothermic processes.39,40 As shown in Fig. 2A, a strong and narrow peak, which is attributed to the gelation of AM, existed in all the PC/PAM blends within the first hour of reaction and contributed greatly to the cumulative heat released. The shorter elapsed time when this peak appeared usually indicates a faster solidification process, so compared with plain cement paste, the incorporation of PAM strongly decreased the setting time of PC/PAM blends and the setting process could also be further accelerated when the cement concentration increased. Subsequent to that strong peak, another much weaker and broader peak appeared at about 10 h (see the inset), which mainly corresponds to the reaction of cement.41 According to the cumulative heat curves from 4 h to 24 h (Fig. 2B), plain cement paste released the highest amount of cumulative heat among all blends, indicating that a retardation of cement reaction was caused by the incorporation of PAM. This retardation could be caused by the adsorption of monomer onto cement particle surfaces to act as a barrier to cement dissolution, which phenomenon is common in cement-polymer systems.42–44 Phase analysis of PC30/PAM8, PC60/PAM8, PC120/PAM8 and cement paste are plotted in Fig. 2C and some dominant crystalline phases in the 2θ range of 5° to 65° are identified, including calcium silicate phases (alite and dicalcium silicate), aluminate phases and some reaction products such as portlandite, calcite and ettringite. Although calcium silicate hydrate is the most abundant reaction products of calcium silicate phases in blends and serves as an efficient adsorbent of wastes, it is hard to directly calculate its content based on the Rietveld refinement results due to its poorly crystallized structure and the existence of amorphous hydrogel in blends. Normally, the formation of calcium silicate hydrate is accompanied by the formation of portlandite and thus the ratio of portlandite and calcite formed from the carbonation of portlandite to alite can be served as an indicator to evaluate the reaction degree. According to the refinement results, the ratios of PC/PAM composites are much smaller than that ratio of cement paste, which means the reaction of calcium silicate phases is retarded by the incorporation of PAM at the early age and is consistent with the calorimetric results. However, the amounts of ettringite in PC/PAM composites, which potentially absorbs and immobilizes wastes through the isomorphous replacement and chemical adsorption,12 are a bit higher than that in cement paste. With the curing age extended from three days to seven days, calcium silicate phases and aluminate phases were continuously consumed to form reaction products in all blends, which enhances the solidification potential of wastes.
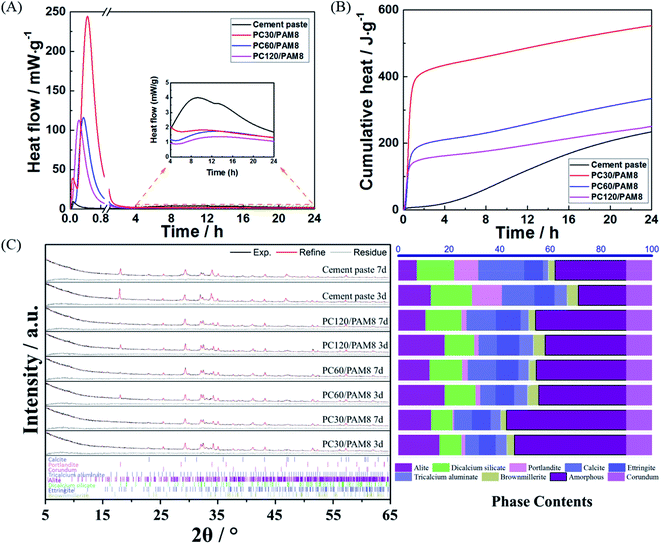 |
| Fig. 2 (A) Reaction heat development, (B) cumulative heat curves, and (C) Rietveld refinement results of PC/PAM composites and cement paste without contaminants. | |
3.2. Mechanical properties of PC/PAM composites
Mechanical properties are important indexes to distinguish unstabilized and stabilized wastes, and satisfactory mechanical properties are often required before secondary treatment or landfill.45 Hardened cementitious materials with normal strength has been proven suitable for waste solidification,19 but the incorporation of PAM toughs the composites and changes the failure mode from brittle to ductile. Therefore, to investigate the influence of PAM, mechanical tests of PC/PAM composites were conducted in this work.
Fig. 3 shows the mechanical test results of PC/PAM composites and hydrogel. Due to the limitation of testing machine, the compression of the composites was stopped at either a 60% strain or a maximum loading force of 1800 N. It is shown in Fig. 3A that the compressive strength of PC120/PAM8 can reach 21
500 kPa when the deformation was 60%. The cement concentration had a positive influence on the strength: PC60/PAM8 > PC30/PAM8 > hydrogel (without cement, 57 kPa at 60% deformation). The curves at 7 days (Fig. 3B) followed similar trends, still relatively gentle, but all had higher values. It needs to be mentioned that when reaching the maximum loading force of 1800 N, the compression of PC120/PAM8 was stopped and thus the maximum stress of 23
550 kPa obtained at the age of 7 days was considered as its strength.
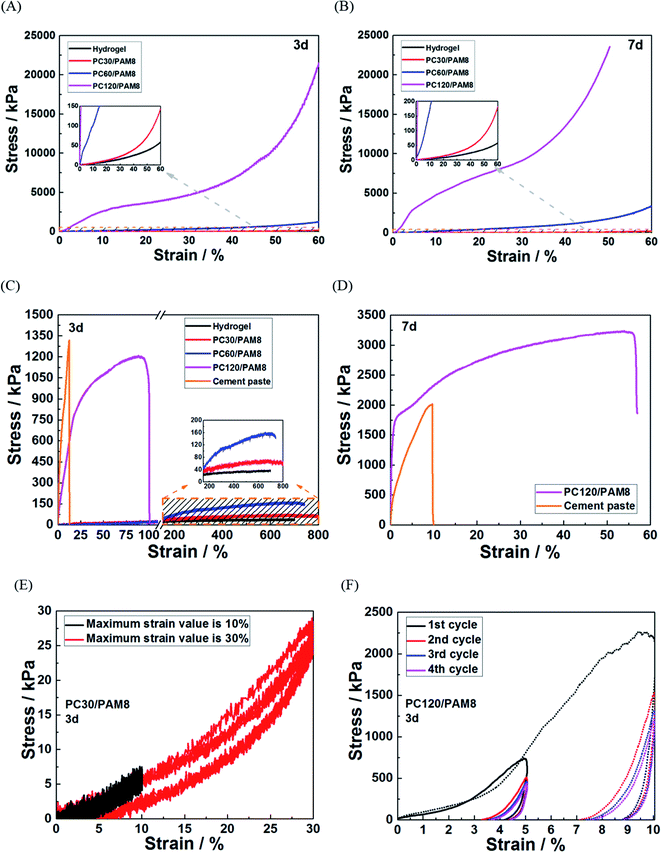 |
| Fig. 3 (A) 3 days and (B) 7 days compressive stress–strain behaviors, and (C) 3 days and (D) 7 days tensile stress–strain behaviors of PC/PAM composites without contaminants. Stress–strain behaviors curves of (E) PC30/PAM8, (F) PC120/PAM8 under cyclic loading after 3 days reaction. | |
PAM hydrogel prepared in this work had a maximum deformation about 700%, and after incorporating hydrogel with cement pastes, the ultimate elongations of PC/PAM composites were much greater than plain cement paste, though significantly shortened when comparing with hydrogel. These results in Fig. 3C and D are in agreement with the literature.40,46 Comparing to PC/PAM composites, cement paste had a higher strength (about 1320 kPa) but a poorer ductility at 3 days age. Among these PC/PAM composites, PC120/PAM8 had the highest tensile strength of 1200 kPa and an elongation of 100%, while for PC60/PAM8, the strength and elongation were 156 kPa and 740% and for PC30/PAM8, they were 70 kPa and 800%. At 7 days age, the strength of PC120/PAM8 exceeded cement paste as shown in Fig. 3D. PC/PAM composites can also be compressed, and the compressive recoverability of PC/PAM composites under cyclic compression was illustrated in Fig. 3E and F. During the four cyclic compression cycles, only PC30/PAM8 (Fig. 3E) could completely recover from either 10% or 30% deformation, and the recoverability of PC/PAM composite was reduced harshly with the increased cement concentration.
3.3. Microscopic characterization
Normally, hydrogel is much softer than cement paste and the density and the uniformity of its network structure is an important factor in determining the mechanical properties. Fig. 4 shows the scanning electron microscopy image of lyophilized hydrogel with uniform and fine microfibrils built up the internal porous structures. For PC/PAM composites, the inorganic particles can serve as crosslinker and a more rigid wall structure was built up.40,46 The pore size has been reported to be essential for the adsorption efficiency of ions.47 Also, pore diffusion is one of the common adsorption mechanisms to remove contaminants in water.48 In this study, besides the contribution on contaminant adsorption, the presence of hydrogel also plays a key role on providing places to reserve wastewaters. The structures were gradually strengthened and densified with the extension of reaction age (Fig. 5), consistent with the mechanical properties results. Take PC60/PAM8 as an example, only a few products formed at 3 days while abundant products had formed at 7 days, as shown in Fig. 5B.
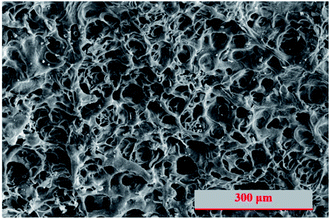 |
| Fig. 4 Morphology and microstructure of PAM hydrogel (SEM photograph). | |
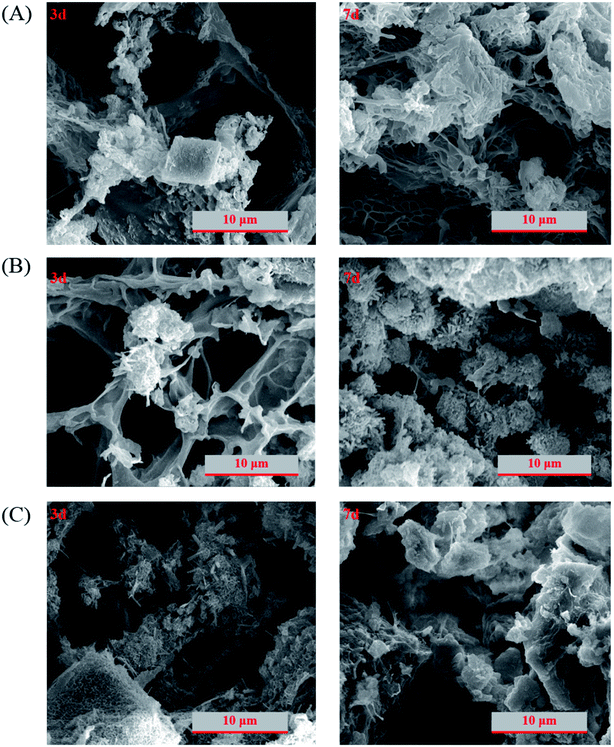 |
| Fig. 5 Morphology of (A) PC30/PAM8, (B) PC60/PAM8 and (C) PC120/PAM8 at 3 days and 7 days. | |
3.4. Solidification efficiency of simulated wastewaters
The solidification efficiency is important to determine the applicability of a given composite. Gelation time is a useful parameter to assess the efficiencies, which is equal to the time cost for a mixture to completely lose its flow ability and to be a solidified matrix (Fig. 6A-c) from the initial mixture (Fig. 6A-a). In this work, the effects of cement concentration, AM concentration and temperature on the gelation time of PC/PAM composites were studied.
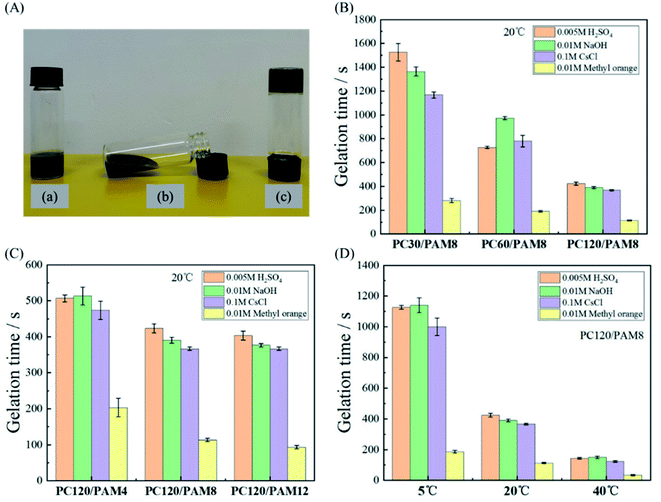 |
| Fig. 6 (A)Gelation behaviors of PC/PAM composite: (a) flowable, (b) gradually losing flow ability and (c) completely solidified PC/PAM composites. Influence of cement concentration (B), AM concentration (C) and temperature (D) on the gelation time of PC/PAM composites. | |
The standard initial setting time of Portland cement should not be less than 45 minutes according to Chinese Standard GB 175-2007. Adding wastes usually retards the setting of cement paste and prolongs its initial setting time to several hours.30,31 The retardation effect can also be amplified with an increased waste concentration.49 Comparing with plain cement paste, it is clearly seen in Fig. 6B that PC/PAM composites with relative high concentrations of contaminants had much shorter gelation times than cement paste. Interestingly, raising the cement concentration can significantly decrease the gelation time for all four simulated wastes. Among these wastes, the gelation time of methyl orange was the shortest and it took only about 110 s for PC120/PAM8 from gel to form a solid at 20 °C. This might be related to the presence of azo group in methyl orange, which can accelerate the reactions of monomers and thus azo compounds have been widely used as initiators of many polymers in the past decades.50,51 Besides methyl orange, the differences in gelation times of mixtures containing cesium chloride, sodium hydroxide and sulfuric acid were small.
The effect of AM concentration on the gelation time is shown in Fig. 6C. When the AM concentration increased from 2.1 wt% (PC120/PAM4) to 4.2 wt% (PC120/PAM8), gelation times of all the solidified waste forms reduced pronouncedly. However, such a great reduction was not observed with a further increase on AM concentration, indicating there might be an optimized concentration considering both the solidification efficiency and the cost. Given that wastewaters in real environments may have different temperatures, Fig. 6D reveals the effect of increased temperature on the gelation time of PC/PAM composites. When the temperature rose from 5 °C to 40 °C, the gelation time of PC120/PAM8 can be reduced from more than 1000 s to less than 200 s, being 80% of reduction.
Strength test data are often used as an indicator to distinguish unstabilized and stabilized wastes. Minimum compressive strength is often required to provide a guideline for solidified waste forms, e.g., a 28 day compressive strength of 0.7 MPa is required in UK52 while 0.35 MPa is required by US53 and by Spain for landfill.54 It is well known that the compressive strength of cementitious materials is dependent on their pore structure qualities, so after incorporating porous hydrogel into cement paste, the compressive strength of PC/PAM composites will be lower than normal cement paste. Due to the stretchability of PC/PAM composites, the testing samples were no longer able to be broken into fragments like common cement pastes. Therefore, 40% deformation was applied to record their strengths when some cracks started to emerged. According to Fig. 7, the 3 days age strength of PC120/PAM8 is higher than 2 MPa when containing different wastes, and is satisfactory for waste solidification. It should also be mentioned that according to the ongoing reaction, PC120/PAM8 will be continuously strengthened with time.
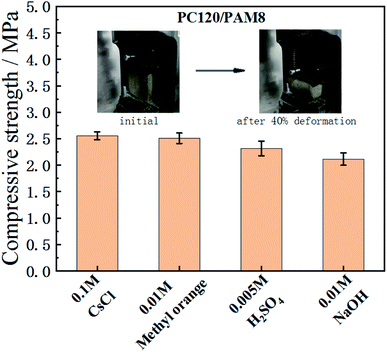 |
| Fig. 7 Compressive strength of PC120/PAM8 with contaminants after 3 days reaction. | |
4. Conclusions
Rapid cementitious solidification of wastewater in emergencies is of paramount importance to eliminate environmental pollutions and ensure safe waste treatments. In this study, a serials of PC/PAM composites were prepared by a one-pot method to rapidly solidify four types of simulated wastewaters. The properties of the composites were first investigated. The calorimetric data and the XRD results show that the reaction of these composites continuously generated products to strengthen the internal structures, and the stiffening network structure improved the mechanical properties of the composites with time. Then, the solidification efficiencies of four simulated wastewaters, including cesium chloride, methyl orange, sodium hydroxide and sulfuric acid, were assessed based on the gelation time method. The gelation times of the PC/PAM composites containing simulated wastewaters were within the range of only a few minutes, exhibiting a superior solidification performance than conventional cementitious methods. Furthermore, after solidifying different simulated wastewaters, PC120/PAM8 had a compressive strength of more than 2 MPa after 3 days reaction and met the requirement for waste solidification. In summary, PC/PAM composites provide a promising alternative for the rapid solidification of a wide range of wastewaters, particularly in emergent incidents.
Conflicts of interest
There are no conflicts to declare.
Acknowledgements
The authors would like to acknowledge the financial support by National Natural Science Foundation of China (no. 1706222, no. 51890904, no. 51708108), State Key Laboratory of High Performance Civil Engineering Materials Open Fund (no. 2018CEM001) and the Fundamental Research Funds for the Central Universities.
References
- R. P. Schwarzenbach, T. Egli, T. B. Hofstetter, U. von Gunten and B. Wehrli, Annu. Rev. Environ. Resour., 2010, 35, 109–136 CrossRef
. - V. K. Gupta, I. Ali, T. A. Saleh, A. Nayak and S. Agarwal, RSC Adv., 2012, 2, 6380–6388 RSC
. - J. Gasperi, B. Laborie and V. Rocher, Chem. Eng. J., 2012, 211, 293–301 CrossRef
. - A. Bick, G. Oron, L. Gilierman and Y. Manor, Water Sci. Technol. Water Supply, 2003, 3, 379–384 CrossRef CAS
. - Y. Kim, Y. K. Kim, S. Kim, D. Harbottle and J. W. Lee, Chem. Eng. J., 2017, 313, 1042–1050 CrossRef CAS
. - C. Xu, J. Wang and J. Chen, Solvent Extr. Ion Exch., 2012, 30, 623–650 CrossRef CAS
. - C. M. López-Ortiz, I. Sentana-Gadea, P. J. Varó-Galvañ, S. E. Maestre-Pérez and D. Prats-Rico, Chemosphere, 2018, 208, 433–440 CrossRef PubMed
. - J. R. Werber, C. O. Osuji and M. Elimelech, Nat. Rev. Mater., 2016, 1, 16018 CrossRef CAS
. - H. Ates and M. E. Argun, Water Sci. Technol., 2018, 78, 1064–1070 CrossRef CAS PubMed
. - D. Hou and A. Al-Tabbaa, Environ. Sci. Policy, 2014, 39, 25–34 CrossRef
. - D. Hou, Q. Gu, F. Ma and S. O'Connell, J. Cleaner Prod., 2016, 139, 949–956 CrossRef CAS
. - C. Fan, B. Wang and T. Zhang, Adv. Mater. Sci. Eng., 2018, 2018, 5120649 Search PubMed
. - T. Luukkonen, A. Heponiemi, H. Runtti, J. Pesonen, J. Yliniemi and U. Lassi, Rev. Environ. Sci. Biotechnol., 2019, 18, 271–297 CrossRef CAS
. - L. Wang and T. Liang, J. Adv. Ceram., 2012, 1, 194–203 CrossRef CAS
. - Z. Wang, Z. Zhao, B. Peng, D. Liu, H. Xu, Y. Chen, D. Wang, H. Liu and N. Peng, Ann. Nucl. Energy, 2019, 133, 209–215 CrossRef CAS
. - A. Bańkowska, R. Ostrysz and P. Penczek, Polimery, 2002, 47, 833–836 CrossRef
. - G. E. Voglar and D. Leštan, J. Hazard. Mater., 2010, 178, 926–933 CrossRef CAS PubMed
. - G. E. Voglar and D. Leštan, J. Hazard. Mater., 2011, 192, 753–762 CrossRef CAS PubMed
. - J. Koťátková, J. Zatloukal, P. Reiterman and K. Kolář, J. Environ. Radioact., 2017, 178, 147–155 CrossRef PubMed
. - B. Çomak, Eur. J. Environ. Civ. Eng., 2018, 22, 736–754 CrossRef
. - R. B. Kogbara and A. Al-Tabbaa, Sci. Total Environ., 2011, 409, 2325–2335 CrossRef CAS PubMed
. - N. W. Wiesława, T. Barbara and D. Sylwia, Procedia Eng., 2015, 108, 72–79 CrossRef
. - H. Chang, P. Feng, K. Lyu and J. Liu, Constr. Build. Mater., 2019, 225, 324–331 CrossRef CAS
. - L. Zampori, I. N. Sora, R. Pelosato, G. Dotelli and P. G. Stampino, J. Eur. Ceram. Soc., 2006, 26, 809–816 CrossRef CAS
. - Q. Y. Chen, M. Tyrer, C. D. Hills, X. M. Yang and P. Carey, Waste Manag., 2009, 29, 390–403 CrossRef CAS PubMed
. - S. Hajilar and B. Shafei, J. Colloid Interface Sci., 2018, 513, 104–116 CrossRef CAS PubMed
. - X. Tian, Z. Zhou, Y. Xin, L. M. Jiang, X. Zhao and Y. An, J. Hazard. Mater., 2019, 365, 572–580 CrossRef CAS PubMed
. - P. Adlercreutz, Chem. Soc. Rev., 2013, 42, 6406–6436 RSC
. - M. Vespa, R. Dähn and E. Wieland, Phys. Chem. Earth, 2014, 70, 32–38 CrossRef
. - Y. S. Wang, J. G. Dai, L. Wang, D. C. W. Tsang and C. S. Poon, Chemosphere, 2018, 190, 90–96 CrossRef CAS PubMed
. - L. Klus, V. Václavík, T. Dvorský, J. Svoboda and R. Papesch, Buildings, 2017, 7, 120 CrossRef
. - N. Jain and M. Garg, Constr. Build. Mater., 2008, 22, 1851–1856 CrossRef
. - H. Feng, H. T. N. Le, S. Wang and M. H. Zhang, Constr. Build. Mater., 2016, 129, 48–60 CrossRef CAS
. - W. Li, J. Hong, X. Zhu, D. Yang, Y. Bai, J. Liu and C. Miao, Constr. Build. Mater., 2018, 163, 714–723 CrossRef CAS
. - M. Khan and I. M. C. Lo, Water Res., 2016, 106, 259–271 CrossRef CAS PubMed
. - V. Van Tran, D. Park and Y. C. Lee, Environ. Sci. Pollut. Res., 2018, 25, 24569–24599 CrossRef CAS PubMed
. - L. S. Nair, T. Starnes, J. W. K. Ko and C. T. Laurencin, Biomacromolecules, 2007, 8, 3779–3785 CrossRef CAS PubMed
. - J. O. Buitrago, K. D. Patel, A. El-Fiqi, J. H. Lee, B. Kundu, H. H. Lee and H. W. Kim, Acta Biomater., 2018, 69, 218–233 CrossRef CAS PubMed
. - H. Taylor, Cement Chemistry, Thomas Telford, London, 2nd edn., 1997 Search PubMed
. - Y. Y. Chu, X. F. Song and H. X. Zhao, J. Appl. Polym. Sci., 2019, 136, 47905 CrossRef
. - K. L. Scrivener, P. Juilland and P. J. M. Monteiro, Cem. Concr. Res., 2015, 78, 38–56 CrossRef CAS
. - X. Kong, S. Emmerling, J. Pakusch, M. Rueckel and J. Nieberle, Cem. Concr. Res., 2015, 75, 23–41 CrossRef CAS
. - D. Han, W. Chen and S. Zhong, Adv. Cem. Res., 2018, 30, 113–122 CrossRef
. - Z. Lu, X. Kong, C. Zhang and Y. Cai, Cem. Concr. Res., 2018, 113, 140–153 CrossRef CAS
. - R. Malviya and R. Chaudhary, J. Hazard. Mater., 2006, 137, 267–276 CrossRef CAS PubMed
. - X. F. Song and Y. Y. Chu, Polym. Compos., 2019, 40, 2462–2472 CrossRef CAS
. - H. E. Abdelwahab, S. Y. Hassan, M. A. Mostafa and M. M. El Sadek, Molecules, 2016, 21, 684 CrossRef PubMed
. - Q. Peng, M. Liu, J. Zheng and C. Zhou, Microporous Mesoporous Mater., 2015, 201, 190–201 CrossRef CAS
. - M. Niu, G. Li, Y. Wang, Q. Li, L. Han and Z. Song, Constr. Build. Mater., 2018, 193, 332–343 CrossRef CAS
. - M. Erim, A. T. Erciyes, I. E. Serhatli and Y. Yağci, Polym. Bull., 1992, 27, 361–366 CrossRef CAS
. - L. Feng, J. Ye, X. Qiang and H. Zhang, J. Appl. Polym. Sci., 2011, 121, 454–461 CrossRef CAS
. - C. D. Hills and S. J. T. Pollard, J. Hazard. Mater., 1997, 52, 171–191 CrossRef CAS
. - U.S. Environmental Protection Agency, Guide to disposal of chemically stabilized and solidified wastes (EPA SW-872), 1982 Search PubMed
. - C. F. Pereira, M. Rodríguez-Piero and J. Vale, J. Hazard. Mater., 2001, 82, 183–195 CrossRef CAS
.
|
This journal is © The Royal Society of Chemistry 2020 |
Click here to see how this site uses Cookies. View our privacy policy here.