DOI:
10.1039/D0RA04189K
(Paper)
RSC Adv., 2020,
10, 23503-23509
A faster and more effective chrome tanning process assisted by microwave
Received
10th May 2020
, Accepted 25th May 2020
First published on 19th June 2020
Abstract
In leather manufacturing, microwave usually has the ability to strengthen the combination between collagen and chemicals and make the corresponding procedures faster and more effective. Although some studies clarified that tanning under microwave resulted in leather with better thermal stability, the process and leather properties of the pelt chrome tanning had not been elaborated in detail. Thus, in this study, pickled goat pelt was tanned for 5 h as a penetration procedure and then basified for another 5 h as a fixation procedure under microwave heating (MW) and water bath heating (WB); then, the changes in the pH of the chromium complexes as well as the leather chrome content were measured; finally, thermal behaviors and collagen structure of leather tanned under different methods were measured. The results indicated that microwave promoted chrome tanning agent penetration and exhaustion, consequently, chrome tanning process was faster and more effective. The leather tanned with microwave assistance had better hydrothermal and thermal stability as well as thermal decomposition resistance, indicating microwave leading to excellent tanning effect. Nevertheless, when microwave was applied in the chrome tanning process, the hierarchical structure of the leather and the collagen conformation including triple helix was not affected, and the combination pattern between ligands and chromium was also the same as that of the conventional. In brief, microwave could fasten the chrome tanning process and result in extraordinary tanning effect without damaging the leather structure; therefore, microwave might be a new method for promoting tanning efficiency and effect in future.
1. Introduction
Leather manufacturing consists of large number of chemical and mechanical processes to convert the raw hides and skins obtained from the byproduct of animal husbandry and meat production into leather, which is a useful and aesthetic natural polymer matrix. Leather manufacturing consists of three sections in general, such as beamhouse, tanning and finishing, with the tanning being the crucial procedure. Only tanning will convert raw hides and skins into leather with the characteristics of softness, fullness, durability as well as chemical and microbial resistance, which are suitable for making leather goods.1 Since chrome-tanned leather has excellent thermal stability, for which the shrinkage temperature (Ts) is usually beyond 100 °C and outstanding mechanical performance, chrome tanning is the most important and dominant process in leather making.
The frequency range of microwave, one type of electromagnetic wave, is from 300 MHz to 300 GHz. In order to prevent interfering with radar and telecommunication, the frequency of microwave for civil application is usually fixed at 2450 MHz or 915 MHz.2 Microwave could accelerate the rate of chemical reactions by several times to thousand times, resulting in high yield and better properties of the products; moreover, some reactions occurring under extreme conditions such as high temperature and high pressure could occur under milder condition via microwave assistance. Thus, microwave has been widely used in chemical synthesis.3,4 The kinetic rate,5 mechanism,6 activation energy7 and pre-exponential factor8 of the reactions under microwave are distinctively different in comparison to the traditional heating at corresponding temperature, indicating that there are special effects other than thermal in the processes, and these effects of microwave are key for the promotion of the chemical reactions.9,10
Microwave has been used in some leather making processes, such as unharing and bating,11 dyeing,12 fat liquoring13 and drying14 to make the leather making processes much faster and effective together with obtaining better performance leather in which microwave had positive effect on the improvement of the uniformity in the distribution of the chemical materials of leather and the speed of combination between the collagen and chemicals.15 In the tanning field, it has been found that the tanning effect could be promoted by microwave. Leather would have a high shrinkage temperature (Ts) and better tear strength when microwave was used to irradiate wet blue after chrome tanning agent penetrated well and evenly.16 In vegetable tanning, microwave not only improved the cross-linking to generate better thermal stability of the leather matrix but also benefited for promoting polyphenols exhaustion.17,18 In aluminum and zirconium tanning, leather with excellent thermal behaviors was obtained by microwave-assisted tanning.19,20 Furthermore, the Ts of leather tanned with the assistance of microwave could exceed 100 °C when terminal pH of the tanning liquor was only 3.3; on the contrary, the pH should be above 3.8 to reach the same Ts level in the conventional tanning system.21 With ultrasound and microwave assistance, chrome tanning could be finished within 11 min without basification.22 These evidences suggest that microwave could accelerate the tanning process and also make tanning more effective.
In general, as hides or skins have certain thickness, chrome tanning consists of two relatively independent procedures, penetration and fixation. It is necessary and important for chemicals to penetrate into the leather and distribute evenly; in this way, the relevant procedures will be carried out favorably and leather will have better performances.23 In normal chrome tanning process, pickled pelt is tanned under low pH to allow the chrome tanning agent to penetrate at first, and then alkali is added to increase the pH of the tanning system to enhance the combination between collagen and chromium. Previous studies have demonstrated that stronger tanning effect was obtained during hide powder chrome tanning process.24,25 However, chrome tanning agent easily reacts with collagen during the tanning process because the powdered tanning material is uniform and without any interwoven structure such as pelt. So far, it is unknown how the microwave affects the pelt chrome tanning process and the properties of the leather. Besides, there is no study about whether microwave would have positive effect on faster tanning process and more effective cross-linking.
In this study, microwave (MW) was used as the heating source in pelt chrome tanning process, and the tanning with water bath heating (WB) under identical conditions was used as the control. The penetration and exhaustion of the chrome tanning agent in both the processes was illustrated through pH measurement and UV-Vis spectra of the tanning effluent together with the chrome content in leather; these evidences would demonstrate whether microwave promote the tanning process or not. The thermal behaviors and leather structure were characterized to demonstrate whether microwave had positive or negative effects on the tanning process and the collagen structure of leather. This research would provide reference and practical technology for achieving faster and more effective chrome tanning process assisted by microwave.
2. Materials and methods
2.1 Materials
Pickled goat pelt with a thickness of around 1.0 mm was prepared based on normal upper shoe leather process. Chromium sulfate hexahydrate was purchased from Shanghai Aladdin Reagents Company. Sodium bicarbonate and sodium chloride were bought from Chengdu Kelong Chemical Ltd. All the chemicals were of research grade for tanning and analyzing, whereas commercial grade chemicals were used for making pelt.
2.2 Chrome tanning process
The chrome tanning liquor with 33% basicity and chromium sulfate concentration of 100 g L−1 was prepared by dissolving (191.33 ± 0.01) g chromium sulfate hexahydrate in 1400 mL of 60 g L−1 sodium chloride solution; next, (10.714 ± 0.002) g sodium bicarbonate was dissolved in a 100 mL salt solution and then the solution was dropped slowly into the chrome solution (about 30 min) under agitation; finally, the mixture was stirred for another 30 min.
About 140 g pickled goat pelt pieces (cut into 2 cm × 6 cm) were tanned in a 1000 mL beaker with 700 mL of the above-prepared chrome tanning liquor. An AMCR-3C microwave reactor (Xi'an Yuhui instrument Ltd.) was used as microwave source for MW tanning, and a DF-101S water bath heater (Wuhan Ke'er instrument Company) was applied as the heating source for WB tanning. Both the tanning processes were carried out at 40 °C under constant stirring for 10 h in which the first 5 h was regarded as the penetration procedure and the last 5 h was the fixation procedure. After the penetration procedure finished, (1.00 ± 0.002) g of sodium bicarbonate was dissolved in 20 mL water and added into the tanning system every one hour and was repeated for 5 times.
A pH-3C pH meter (Shanghai Yidian Instruments Co., Ltd.) was used for testing the pH of both the tanning liquors every 1 h. UV-Vis spectra of the tanning liquor were also measured every 1 h. Simultaneously, the chrome content in both the leathers was determined in every 1 h, and the Ts measurements were carried out after 5 h tanning and 10 h tanning.
2.3 Testing methods
2.3.1 Ts measurement. The shrinkage temperature was tested using a Shrinkage Temperature Tester (MSW-YD4, China) with the bath of a 75% glycerin solution. Each value was an average of two tests.
2.3.2 Leather chrome content measurement. 0.150 ± 0.0005 g leather dried via freeze drying was digested by 5 mL hydrogen peroxide and 10 mL nitric acid in 100 mL flask for 30 min under boiling condition until no visible particles existing in the solution. After cooling down, the digested solution was diluted to 100 mL. Optima 8000DV Inductively Coupled Plasma Atomic Emission Spectroscopy (ICP-OES, PerkinElmer, America) was used for measuring the chrome content in the diluted solution and the Cr2O3 content in leather could also be calculated.
2.3.3 UV-Vis determination. The tanning liquors were diluted ten times with distilled water and then filtrated by a 0.22 μm microporous membrane. The UV-Vis spectra of the tanning liquors were recorded on a UV1900 UV-Vis spectrometer (Beijing Puxi General Instruments Co. Ltd.) and the measuring conditions were wavelength ranging from 350 to 650 nm and at a scan rate of 120 nm min−1. R value was calculated from the formula R = A1/A2, where, A1 and A2 are the maximum absorbances of the solution at the peaks of about 420 nm and 580 nm, respectively.
2.3.4 DSC measurement. A DSC 200 PC differential scanning calorimeter (Germany NETZSCH Group) was used to measure the thermal stability of leather by placing about 0.5 mg lyophilized leather into aluminum crucibles and heating under nitrogen atmosphere at a flow rate of 100 mL min−1. The heating rate was 10 °C min−1 and the temperature range for the tests was 30 °C to 250 °C.
2.3.5 TG measurement. A NETZSCH TG 209 F1 thermal gravimetric analyzer (Germany NETZSCH Group) was used to measure the thermal decomposition resistance of leather by placing about 0.5 mg lyophilized leather into ceramic crucibles and heating under nitrogen atmosphere at a flow rate of 100 mL min−1. The heating rate was 10 °C min−1 and the temperature range for the tests was from 50 to 800 °C.
2.3.6 FT-IR measurement. Several fibers were separated from the dried leather and then ground with potassium bromide to make into a thin disc, and then a Nicolet 10 FT-IR (American Thermo Scientific Corporation) was used to scan for 32 times in the wavelength range from 500 to 4000 cm−1.
2.3.7 SEM observation. Leather histological structure was observed on a JSM-7500F scanning electron microscope (Japan Electronic Co. Ltd., Japan) at low vacuum with an accelerating voltage of 15 kV for different magnifications.
2.3.8 XRD test. The crystal structure of the leather was characterized on an EMPYREAN X-ray diffraction scanning meter (PANalytical B.V., Netherland). The leather for this test was a piece of 20 mm × 20 mm and diffraction angle (2θ) in the experiment was from 5° to 60° at a scan rate of 2° min−1 at ambient temperature and humidity.
3. Results and discussion
In the chrome tanning process, penetration and fixation are two relatively independent procedures. In the penetration procedure, since the chrome concentration in the tanning liquor is high and the pH of float is low, the chrome tanning agent trends to penetrate into the pelt dominantly. In the fixation procedure, the pH of the tanning liquor arises due to the replenishing alkaline solution, thus promoting the combination between collagen and chromium complexes. In the study, the chrome tanning process was artificially divided into penetration (from 1 h to 5 h) and fixation (from 6 h to 10 h) after the addition of sodium bicarbonate for basification. During tanning, the MW and WB were used as heating sources, and the influence of microwave irradiation and water bath heating on the chrome tanning process were studied in detail.
3.1 Influence of microwave on the chrome tanning process
As shown in Table 1, the pH values of the MW tanning liquor were always lower than those of WB under different tanning time whether in penetration or fixation procedure. As microwave could promote the hydrolysis and olation of the chrome tanning agent in one step which led to lower pH,26 it was easy to understand the reason why the tanning liquor pH of the MW sample was always lower than that of WB.
Table 1 The influence of different heating methods on the chrome tanning process
Time (h) |
WB |
Ts (°C) |
MW |
Ts (°C) |
pH |
R value |
Cr2O3 content (mg kg−1) |
pH |
R value |
Cr2O3 content (mg kg−1) |
1 |
2.66 |
1.1856 |
7.96 ± 0.38 |
|
2.64 |
1.1749 |
9.52 ± 0.35 |
|
2 |
2.72 |
1.1970 |
12.16 ± 0.44 |
|
2.70 |
1.1930 |
14.15 ± 0.51 |
|
3 |
2.68 |
1.2015 |
15.84 ± 0.81 |
|
2.65 |
1.1964 |
18.36 ± 0.66 |
|
4 |
2.66 |
1.2038 |
18.26 ± 0.51 |
|
2.62 |
1.2007 |
21.62 ± 0.94 |
|
5 |
2.65 |
1.2044 |
20.02 ± 0.81 |
73.5 ± 2.1 |
2.62 |
1.2002 |
22.66 ± 0.58 |
85.6 ± 2.8 |
6 |
2.73 |
1.2119 |
21.62 ± 1.03 |
|
2.70 |
1.2065 |
25.84 ± 0.93 |
|
7 |
2.94 |
1.2392 |
29.79 ± 0.63 |
|
2.89 |
1.2328 |
33.11 ± 0.70 |
|
8 |
3.18 |
1.2595 |
35.23 ± 0.87 |
|
3.16 |
1.2452 |
39.54 ± 1.17 |
|
9 |
3.48 |
1.2981 |
39.56 ± 1.33 |
|
3.44 |
1.2758 |
44.08 ± 1.03 |
|
10 |
3.89 |
1.2942 |
41.88 ± 0.51 |
103.0 ± 1.5 |
3.83 |
1.2872 |
47.15 ± 1.75 |
109.3 ± 2.7 |
In general, the R value larger than 1.19 signifies that there is a bridge formed between chromium and the ligands, and the value will increase if more number of bridge bonds generated.27 Simultaneously, other studies have proved that microwave could accelerate and improve the reaction between chromium(III) and ligands: the reaction time between chromium(III) and EDTA was only 3 min.28 That is to say, the R value of the MW samples should be higher because microwave promotes the coordination between chromium and the ligands, but Table 1 shows that the R values of the MW tanning liquors are always smaller than the WB samples, indicating more number of bridges formed under water bath. The better explanation for the paradox of the R value was that microwave could improve the combination between the collagen and large-sized chromium complexes, which resulted in the lower R value in the tanning liquor. It could be testified through the results that the Cr2O3 content of MW was always larger than the WB for same tanning time. Therefore, it can be deduced that microwave resulted in faster and more effective chrome tanning process by promoting the chrome penetration and exhaustion.
As for the Ts results, the value was 6.3 °C higher for the MW compared to the WB at the end of the tanning, and the Ts of the MW after penetration (5 h tanning) was 85.6 °C, while the WB at the same condition was only 73.5 °C. It might be due to the fact that microwave resulted more chromium complex penetrate into the leather and establish more cross-linking. In addition, the character of microwave which could make leather have higher Ts but finish tanning under lower terminal pH might be main cause for huge Ts difference after 5 h tanning.
As chrome complexes and collagen are polar molecules, they are affected by the microwave and generate additional movement styles caused by unforced oscillation under electromagnetic field while the system under conventional heating contained the movement caused by temperature only. Therefore, molecular movements under microwave are more turbulent and complicated; consequently, the possibility for the collision between the collagen residue and chromium complex might be higher, which benefits the faster chrome penetration and better chrome exhaustion.
3.2 Influence of microwave on leather thermal stability
Enhancement of the thermal stability is the most important function of tanning. For illustration of the influence of microwave and water bath on leather thermal behaviors during chrome tanning, DSC, TG and shrinkage temperature tests were carried out, and the results are shown in Fig. 1 and 2, and the key results of the tests are listed in Table 2.
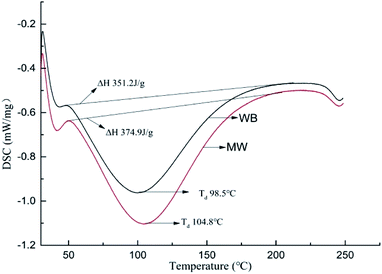 |
| Fig. 1 The influence of different heating methods on leather thermal stability. | |
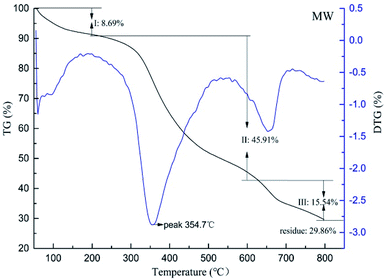 |
| Fig. 2 The influence of microwave on leather thermal decomposition resistance. | |
Table 2 The influence of different heating method on leather thermal stability
Sample |
Td (°C) |
ΔH (J g−1) |
Tmax (°C) |
Carbon residue (%) |
WB |
98.5 |
351.2 |
353.7 |
23.02 |
MW |
104.8 |
374.9 |
354.7 |
29.86 |
Fig. 1 shows the influence of different heating methods on leather thermal stability (DSC results), in which denaturation temperature (Td) and energy-consumption during denaturation (ΔH) for MW were 104.8 °C and 374.9 J g−1, and 98.5 °C and 351.2 J g−1 for WB, respectively. These results indicated that more energy was consumed during the collagen conformation change of leather tanned under microwave. Alternatively, the collagen in the leather tanned under microwave had more stable conformation.
Thermal decomposition resistance of leather could be measured via TG, and the results are shown in Fig. 2 and 3. It could be found that the maximum decomposition temperature (Tmax) and carbon residue of MW were 4.2 °C and 10.01% higher compared to the WB while weightlessness between 200 °C and 600 °C, which is attributed to the peptide decomposition during heating, was 4.43% smaller than the WB. That was to say, the collagen structures of MW were more stable than WB because of less decomposition of the collagen during pyrolysis.
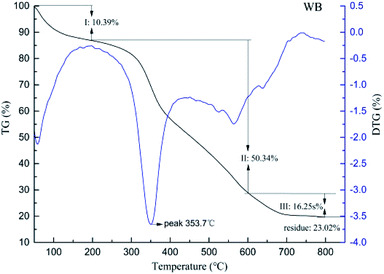 |
| Fig. 3 The influence of water bath heating on leather thermal decomposition resistance. | |
The cross-linking effect was strengthened under microwave because there would be more chromium complexes with high-positive charge and molecular-size, which had better affinity to collagen and mainly contributed to the cross-linking generated under microwave heating, and the exhaustion of these kinds of chromium complexes were higher.29 On the other hand, just as microwave could clearly promote chemical reactions, it could also make cross-linking reaction easier to occur and the efficiency might be higher under microwave compared with water bath heating. The two reasons led to better tanning effect and resulted in more stable collagen conformation, represented by higher Td, ΔH, Tmax and carbon residue. Besides, more carbon residue was not only due to the less decomposition of collagen during pyrolysis but was also the evidence for higher chrome exhaustion since chromium complexes are non-volatile. With these results, it was obvious that the microwave could strengthen the tanning effect and make cross-linking more effective to improve the thermal stability and thermal decomposition resistance of the leather; alternatively, it could use less chrome tanning agent to achieve same tanning effect under microwave assistance.
3.3 Influence of microwave on the leather structure
They are important indexes to illustrate the tanning effect through chrome exhaustion and thermal behavior, but it would be meaningless if the leather structure was damaged during the microwave assisted chrome tanning. Therefore, it is necessary to study whether the leather structure changes or not when microwave was applied in the chrome tanning process.
3.3.1 Morphologies observation. The morphologies of the leathers tanned under microwave and water bath heating were observed via SEM, and the images are shown in Fig. 4. As leather consists of hierarchical structures, different magnifications were used to observe the leather samples. It was clearly visible that both the MW and WB tanned leather had interwoven flexuous fiber bundles network when the magnification was 35 times. With the increase in magnification to 2000 times, it could be found that the leather consisted of thin and uniform fibers that were orderly packed together and there was no significant difference between the two samples. When magnification was amplified to 20
000 times, alternative brightness and darkness emerged on the collagen fibrils, attributed to the unique structure of collagen named Smith microfibril. In short, although the tanning effect improved and the tanning process was fastened by microwave, the hierarchical structure of collagen in the leather remained as normal.
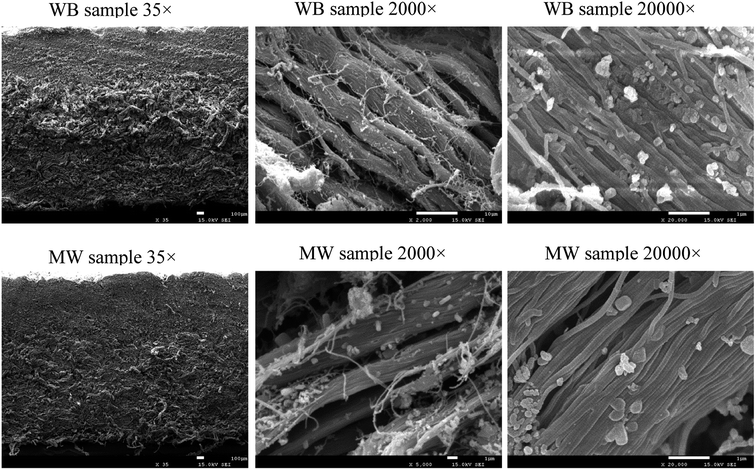 |
| Fig. 4 SEM images of leather tanned under different microwave and water bath heating. | |
3.3.2 FT-IR results. The FT-IR image of leathers tanned under different heating methods is shown in Fig. 5. The absorption bands at around 1650 cm−1, 1550 cm−1 and 1120 cm−1 are the characteristics of collagen named amide I band, amide II band and amide III band, respectively.30,31 From the figure, it is clear that the position and shape of each peaks were almost the same. In particular, the peak at around 1650 cm−1 of the MW sample was almost identical to that of WB, indicating that the triple helix structure of the collagen remained unchanged when microwave was introduced in the chrome tanning process. Moreover, there are four peaks for the two samples in the wavenumber range from 900 cm−1 to 1300 cm−1, indicating that the combination between chromium and sulfate anion in both the samples were double-point coordination.32 FT-IR results showed that the collagen secondary structure including the triple helix structure was not impacted, and the combination pattern between chromium and the ligands was maintained when microwave was used to promote the chrome tanning process.
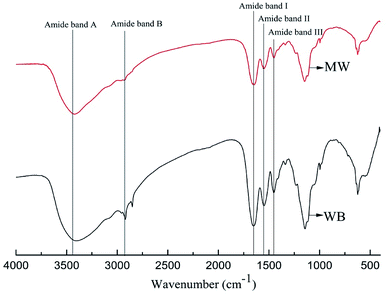 |
| Fig. 5 FT-IR images of leather tanned under microwave and water bath heating. | |
3.3.3 XRD results. The XRD results of the two leathers tanned under different heating methods are shown in Fig. 6. The peak at about 8° relates to the characteristic intermolecular lateral packing within collagen fibrils and the peak at about 20° comes from the amorphous scattering, resulting from the unordered components of the collagen fiber.33 According to a previous study, more chrome tanning agent or better tanning effect shorten the collagen intermolecular lateral packing, consequently resulting in larger 2θ at about 8°.34 In Fig. 6, it was obvious that the 2θ at about 8° of MW was larger than that of WB resulting from higher chrome exhaustion and more effective cross-linking. Also, the amorphous shapes of WB and MW were almost similar, again proving that the microwave would not damage the collagen structure.
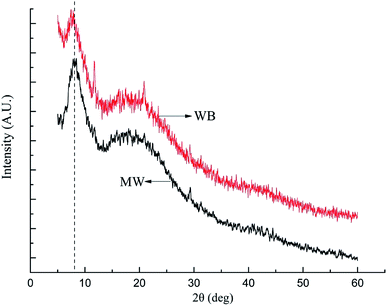 |
| Fig. 6 XRD images of leather tanned under microwave and water bath heating. | |
4. Conclusions
The influence of microwave on the intact pelt chrome tanning process as well as the leather thermal behavior and structure was studied, and the following conclusions were made: first, microwave accelerated the chrome tanning rate as a result of faster penetration and higher chrome exhaustion, hence microwave would be a potential choice for faster chrome tanning process; secondly, the microwave tanned leather had improved thermal behaviors, in other word, tanning effect and cross-linking was promoted by microwave, and thus the microwave could be used for improving the cross-linking during chrome tanning process and producing excellent performance leather and also reduce the chrome tanning agent; thirdly, although microwave resulted in a faster tanning process and more effective tanning effect, but the collagen structure and the combination mechanism between the ligands and chromium were almost the same as that of the conventional, that is, microwave did not have any negative effect on the chrome tanning process and leather properties. In brief, microwave could fasten the chrome tanning process and result in extraordinary tanning effect without damaging the leather structure; therefore, microwave might be a new method for promoting tanning efficiency and effect in future.
Conflicts of interest
There are no conflicts declare.
Acknowledgements
The authors would like to thank National Natural Science Foundation of China (No. 21576171) for providing the financial support.
References
- G. Y. Liu, R. Q. Yu, T. X. Lan, Z. Liu, P. Zhang and R. F. Liang, RSC Adv., 2019, 9, 27060–27068 RSC.
- N. N. Wang and P. Wang, Chem. Eng. J., 2016, 283, 193–214 CrossRef CAS.
- A. Diaz-Ortiz, P. Prieto and A. de la Hoz, Chem. Rec., 2019, 19, 85–97 CrossRef CAS PubMed.
- J. Asomaning, S. Haupt, M. Chae and D. C. Bressler, Renewable Sustainable Energy Rev., 2018, 92, 642–657 CrossRef CAS.
- H. Y. Gao, T. Jiang, Y. Z. Xu, J. Wen and X. X. Xue, Miner. Process. Extr. Metall. Rev., 2020, 41, 22–31 CrossRef CAS.
- G. B. Dudley, R. Richert and A. E. Stiegman, Chem. Sci., 2015, 6, 2144–2152 RSC.
- T. Aiswarya, T. V. Prasad, K. C. J. Raju and T. Vishwam, J. Mol. Liq., 2019, 293, 111506 CrossRef CAS.
- H. C. Nguyen, K. C. Huang and C. H. Su, Chem. Eng. J., 2020, 382, 122796 CrossRef CAS.
- A. Nozariasbmarz, K. Dsouza and D. Vashaee, Appl. Phys. Lett., 2018, 112, 93–103 CrossRef.
- J. Fukushima, K. Kashimura, S. Takayama, S. Motoyasu, S. Saburo, H. Yamato and T. Hirotsugu, Mater. Lett., 2013, 91, 252–254 CrossRef CAS.
- J. C. Wu, T. Sun, J. W. Zhang and W. Y. Chen, J. Soc. Leather Technol. Chem., 2018, 102, 204–209 Search PubMed.
- Y. Gong, K. Cheng, T. Zhang and W. Y. Chen, J. Am. Leather Chem. Assoc., 2011, 106, 127–132 CAS.
- Y. Gong, T. Zhang and W. Y. Chen, J. Am. Leather Chem. Assoc., 2012, 107, 60–67 CAS.
- J. W. Zhang, C. L. Zhang, J. C. Wu and W. Y. Chen, J. Am. Leather Chem. Assoc., 2017, 112, 135–139 CAS.
- J. W. Zhang, J. C. Wu and W. Y. Chen, Special review paper: applications of microwave in leather field: Further research for leather chemists and technologists, J. Am. Leather Chem. Assoc., 2017, 112, 311–318 CAS.
- H. Wang, W. Y. Chen, Y. Gong and H. B. Sun, Leather Sci. Eng., 2011, 21, 5–9 CAS.
- J. C. Wu, W. Liao, J. W. Zhang and W. Y. Chen, J. Therm. Anal. Calorim., 2019, 135, 2329–2335 CrossRef CAS.
- J. C. Wu, Z. W. Fan, J. W. Zhang, Y. Wang and W. Y. Chen, J. Soc. Leather Technol. Chem., 2018, 102, 7–11 Search PubMed.
- Y. Liu, J. W. Zhang, W. Y. Chen, D. Astruc and H. B. Gu, J. Appl. Polym. Sci., 2019, 48682, DOI:10.1002/app.48682.
- Y. T. Fang, J. W. Zhang, G. Q. Ning and W. Y. Chen, Leather Sci. Eng., 2017, 27, 12–16 Search PubMed.
- J. W. Zhang, W. Y. Chen and C. Gaidau, J. Am. Leather Chem. Assoc., 2019, 114, 287–292 CAS.
- J. W. Zhang and W. Y. Chen, J. Cleaner Prod., 2020, 247, 119425, DOI:10.1016/j.jclepro.2019.119452.
- Y. Song, S. Q. Wu, Q. Yang, H. Liu, Y. H. Zeng and B. Shi, Journal of Leather Science and Engineering, 2019, 1, 4, DOI:10.1186/s42825-019-0007-7.
- J. Chen, J. W. Zhang, N. Zhou and W. Y. Chen, Leather Sci. Eng., 2017, 27, 5–9 Search PubMed.
- J. W. Zhang, W. Y. Chen and C. Gaidau, J. Soc. Leather Technol. Chem., 2020, 104, 98–104 Search PubMed.
- J. W. Zhang, N. Cao, N. Zhou and W. Y. Chen, J. Soc. Leather Technol. Chem., 2017, 101, 1–5 CAS.
- J. C. Wu, Y. P. Gao, J. W. Zhang, Y. Wang and W. Y. Chen, Pol. J. Environ. Stud., 2018, 27, 1315–1321 CrossRef CAS.
- A. C. S. Costa, J. C. R. Assis, A. L. C. Torres, S. L. C. Ferreira, M. G. A. Korn and L. S. G. Teixeira, Química Nova, 1999, 22, 194–196 CrossRef CAS.
- J. W. Zhang, W. Y. Chen and C. Gaidau, Journal of Leather Science and Engineering, 2020, 2, 10, DOI:10.1186/s42825-020-00024-1.
- V. D. Oliveira, R. C. D. Neri, F. T. D. do Monte, N. A. Roberto, H. M. S. Costa, C. R. D. Assis, J. F. Santos, R. S. Bezerra and A. L. F. Porto, J. Mol. Struct., 2019, 1176, 751–758 CrossRef CAS.
- J. W. Zhang, N. Cao and W. Y. Chen, Spectrosc. Spectral Anal., 2018, 38, 1353–1357 CAS.
- J. W. Zhang, Y. P. Gao and W. Y. Chen, Leather and Footwear Journal, 2017, 17, 45–50 CrossRef CAS.
- S. W. Xiao, W. H. Dan and N. H. Dan, RSC Adv., 2015, 5, 88324–88330 RSC.
- B. Wu, C. D. Mu, G. Z. Zhang and W. Lin, Langmuir, 2009, 25, 11905–11910 CrossRef CAS PubMed.
|
This journal is © The Royal Society of Chemistry 2020 |
Click here to see how this site uses Cookies. View our privacy policy here.