DOI:
10.1039/D0QM00599A
(Research Article)
Mater. Chem. Front., 2021,
5, 293-303
Controllable construction of core–shell CuCo2S4@polypyrrole nanocomposites as advanced anode materials for high-performance sodium ion half/full batteries†
Received
17th August 2020
, Accepted 17th September 2020
First published on 22nd September 2020
Abstract
It is important to design and fabricate novel anode materials with stable structure and high capacity for sodium ion batteries (SIBs). Herein, core–shell CuCo2S4@polypyrrole (CS-CuCo2S4@PPy) nanocomposites were prepared by a facile solvothermal reaction and subsequent in situ chemical oxidation polymerization. The CS-CuCo2S4@PPy nanocomposites show superior electrochemical performance for half SIBs with a high reversible capacity (551.2 mA h g−1 at 0.1 A g−1 after 200 cycles), excellent rate capability (370.7 mA h g−1 at 2 A g−1), and ultra-long cycling stability (324.9 mA h g−1 at 2 A g−1 after 2000 cycles). In addition, the kinetic analysis reveals that 74.6% of charge contribution is from capacitive-controlled capacity. The Na3V2(PO4)3‖CS-CuCo2S4@PPy full cell further illustrates its practical application with a high capacity of 243.6 mA h g−1 at 0.5 A g−1 after 150 cycles. The competitive electrochemical performances of CS-CuCo2S4@PPy can be attributed to the core–shell structure and the synergistic effect of CuCo2S4 and PPy. The ternary spinel CuCo2S4 can offer rich valence constituent and active sites to achieve high capacity. The PPy layer cannot only improve the electrical conductivity but also buffer the volume variation to protect CuCo2S4 spheres from pulverization during the charge/discharge processes. This work provides a facile method to prepare conductive polymer-coated transition metal sulfide nanocomposites with stable core–shell architectures, confirming their potential application in the energy storage and conversion field.
Introduction
Sodium ion batteries (SIBs), as one of the most promising candidates to replace lithium ion batteries (LIBs) for next-generation energy storage and conversion devices, have attracted much attention from researchers worldwide due to their low cost and natural abundance.1–3 Nevertheless, the current commercial graphite anode materials for LIBs cannot satisfy the requirements of SIBs due to the large Na+ radius (1.02 Å), which limits their mobility and results in the poor diffusion kinetics of Na+ at the electrode/electrolyte interface.4–6 In addition, the large volume variation caused by the larger Na+ ion leads to serious electrode pulverization and irreversible capacity loss. Therefore, it is crucial to design and fabricate advanced anode materials with large specific surface area, increased active sites, high conductivity, and excellent structural stability.
In the past decades, ternary transition metal sulfides (TMSs), such as NiCo2S4, FeCo2S4, and ZnCo2S4, have come into the limelight as prospective candidates in the field of energy storage and conversion.7–9 In particular, CuCo2S4 and its composites, as a kind of ternary TMSs, have drawn massive attention for water splitting reactions, supercapacitors, photocatalyst, Zn–air batteries, and LIBs/SIBs due to their rich electrochemical redox/conversion reactions and synergetic effect of multiple metal species.10–15 For example, Sun's group reported the in-situ synthesis of CuCo2S4@N/S-doped graphene composites with a high reversible capacity of 453 mA h g−1 after 500 cycles at 2 A g−1 for LIBs.16 Zhao et al. synthesized CuCo2S4/reduced graphene oxide nanocomposites by the one-step solvothermal method as anode materials for SIBs.17 However, the inherent defects of ternary TMSs, such as poor electrical conductivity and large volume expansion, result in unsatisfactory cycling life and rate capability for LIBs/SIBs during the discharge/charge process.
To address the above issues, great efforts have been devoted for designing and fabricating suitable nanostructure anode materials to relieve the volume change during the electrochemical reaction. Core–shell nanostructures possess superb chemical and physical properties compared with their single-component counterparts.18 For example, Lou et al. synthesized hierarchical CuS@CoS2 double-shelled nanoboxes to relieve the volume variation and boost the sodium storage properties.19 Core–shell-structured zinc–cobalt binary metal sulfide@N-doped carbon composite (Zn–Co–S@N–C) with enhanced lithium storage was reported.20 The unique core–shell nanostructure can not only shorten the diffusion path of Li+/Na+ ions but also accommodate the volume expansion of the core to alleviate the structural strain and maintain structural integrity of the electrode, and are beneficial for the cycling stability and high rate capability of LIBs/SIBs.21
In addition, combining TMSs with carbonaceous materials (CNT, graphene, carbon fiber, and amorphous carbon) to form hybrid nanostructures is also an efficient strategy to improve the electrochemical performance.22–24 Among them, conductive polymers, such as polypyrrole (PPy), polyaniline (PANI), and polythiophene (PEDOT), have attracted great attention for improving the sodium storage performance owing to their facile synthetic process, low cost, excellent flexibility, and high conductivity.2,25 Besides, the soft conductive polymers can buffer the volume change and physically bind the active materials together to suppress the pulverization of the composite electrode during the charge/discharge process.26–28 For instance, Lou and his collaborators reported the coating of PPy on Sb2Se3 to improve the cycling performance and rate capability for SIBs by buffering the volume expansion.2 Hollow C@MoS2 were coated with PPy to enhance the structural stability of the electrode and demonstrated a long cycling life for SIBs.29 It is noted that the combination of CuCo2S4 with a conductive polymer to enhance the sodium storage properties has not been reported. In addition, recent studies have shown that the thickness of the outer conductive polymers has a great influence on the electrochemical performance. As a result, adjusting the thickness of the outer conductive layer to obtain optimal electrical conductivity and ion diffusion efficiency remains a challenge.
Herein, core–shell PPy-coated CuCo2S4 (CS-CuCo2S4@PPy) nanocomposites were successfully prepared via a two-step method. The CS-CuCo2S4@PPy exhibits excellent electrochemical performance for SIBs, including a high reversible capacity of 551.2 mA h g−1 at 0.1 A g−1 after 200 cycles and an ultra-long cycling stability of 324.9 mA h g−1 at 2 A g−1 even after 2000 cycles. In addition, the Na3V2(PO4)3(NVP)‖CS-CuCo2S4@PPy full cell exhibited excellent electrochemical performance (243.6 mA h g−1 at 0.5 A g−1 after 150 cycles). The satisfactory sodium storage ability can be attributed to the particular core–shell structure, which can not only accommodate the volume variation of the CuCo2S4 spheres so as to maintain the structural integrity for long cycling life but can also improve the contact of the electrolyte/electrode interface in order to accelerate the ionic diffusion. In addition, the PPy layer can increase the conductivity due to its conjugated π–π bond. Due to the contribution of both PPy and CuCo2S4, the CS-CuCo2S4@PPy electrode exhibits impressive sodium storage performance with an ultra-long cycling life and competitive rate capability. Based on this, our work confirms and offers a potential anode material for SIBs.
Experimental
Preparation of the CS-CuCo2S4@PPy nanocomposites
Firstly, the CuCo2S4 spheres were synthesized firstly via a simple solvothermal method according to our previous work.30 Then, 200 mg of the as-prepared CuCo2S4 spheres were dispersed in 180 mL deionized water and 20 mL ethanol by sonication for 1 h. Then, 20 mL FeCl3 aqueous solution (0.1 M) was added into the suspension as an initiator for polymerization with magnetic stirring for 1 h. Thereafter, 200 μL pyrrole was added into the suspension dropwise under vigorous stirring. The entire polymerization process was carried out in an ice bath (0–5 °C) for 6 h and the black powder was collected by high-speed centrifugation, followed by washing with deionized water and ethanol several times. Finally, the product was dried in vacuum at 60 °C. Meanwhile, in order to controllably prepare the CS-CuCo2S4@PPy nanocomposites, the polymerization time were varied in the range from 1 to 12 h.
Materials characterization
The crystallinity of the as-prepared samples was certified by X-ray diffraction (XRD, Rigaku, Japan, Cu Kα radiation). The morphologies and surface structures of the obtained samples were observed by a field-emission scanning electronic microscope (SEM, JEOL JSM-7500F) equipped with an energy-dispersive X-ray spectrometer (EDS) and a transmission electronic microscope (TEM, Hitachi HT7700). The analysis of the chemical state was done via X-ray photoelectron spectroscopy (XPS, PHI QUANTERA-II SXM). The specific surface and pore structures of the samples were analyzed by nitrogen adsorption–desorption measurements (Auto Pore IV 9510).
Electrochemical measurements
The electrochemical measurements of CS-CuCo2S4@PPy for the half and full cell were investigated by 2032-type coin cells, which were fabricated in an argon-filled glovebox with both the moisture and oxygen level less than 0.01 ppm. For the half-cell, the homogeneous slurry was made of 70 wt% active material (CS-CuCo2S4@PPy), 20 wt% conductive agent (super P), and 10 wt% sodium carboxymethyl cellulose (CMC) binder dissolved in deionized water with overnight stirring. The viscous slurry was uniformly spread out onto a copper foil and dried in vacuum at 100 °C. The dried copper foil was cut into 12 mm discs with an average loading mass of the active material of 1.0 mg cm−2, which were employed as the working electrode. Na foil and Whatman glass fiber were employed as the counter electrode and the separator, respectively. The electrolyte consisted of 1 M NaCF3SO3 dissolved in diethylene glycol ether. The cyclic voltammetry (CV) test was conducted in the range from 0.25 to 2.75 V using the electrochemical workstation (CHI-760) at a scan rate of 0.1 mV s−1. The galvanostatic discharge/charge measurement at different current densities was implemented by the Land battery-test instrument (Wuhan, China). Electrochemical impedance spectroscopy (EIS) was also carried out in the frequency range from 100 kHz to 0.01 Hz on a CHI-760 potentiostat. For comparison, the pure CuCo2S4 electrode was also tested under the same conditions for SIBs.
For sodium ion full cell assembly, NVP and CS-CuCo2S4@PPy were applied as the cathode and anode material with the same method as that for the half cell, respectively. The NVP electrodes were composed of NVP (70 wt%), Super P (20 wt%), and polyvinylidene difluoride (PVDF, 10 wt%). The preparation of NVP electrodes was same as that of the CS-CuCo2S4@PPy electrodes except that the collector and solvent were changed to Al foil and N-methyl-2-pyrrolidone (NMP), respectively. The full cells were tested in the potential window ranging from 0.25 V to 3.0 V.
Results and discussion
As shown in Fig. 1a, the CS-CuCo2S4@PPy nanocomposites were successfully prepared via the two-step method. The pure CuCo2S4 spheres were firstly prepared through the solvothermal process and then the PPy layer was coated on the surface to form a hierarchical core–shell structure. The morphologies and microstructure details of the as-prepared samples were observed using SEM and TEM. As shown in Fig. 1b and e, the pristine CuCo2S4 spheres had an average size of 300 nm with a smooth surface without aggregation. Meanwhile, Fig. 1c and d reveal that the CS-CuCo2S4@PPy nanocomposites are uniformly coated with PPy nanoparticles, which form a rough hierarchical layer on the surface of the CuCo2S4 spheres and construct a core–shell architecture, thus improving the contact area between the electrolyte and the electrode. Fig. 1f confirms the core–shell structure of CS-CuCo2S4@PPy and the thickness of the outer soft PPy layer is about 30 nm. Also, the diffraction rings of CuCo2S4 (022), (113), and (004) planes can be observed in the selected area electron diffraction (SAED) pattern inset of Fig. 1f, which illustrates the polycrystalline characteristics of CuCo2S4.31 As shown in Fig. 1g, the corresponding high-resolution TEM (HRTEM) image shows the interplanar distances of 0.545 and 0.330 nm, which are indexed to the (111) and (022) planes of spinel CuCo2S4, respectively, and the amorphous part can be attributed to the PPy layer covered on the surface of CuCo2S4.32 The microstructure and compositional distribution of the CS-CuCo2S4@PPy nanocomposites were also investigated by EDS mapping. As shown in Fig. S1 (ESI†), the corresponding elements of CS-CuCo2S4@PPy, including Cu, Co, S, C, and N, are uniformly distributed throughout the whole nanocomposite. These results demonstrate that the uniform coating of the PPy layer on the surface of the CuCo2S4 spheres forms a core–shell structure, which can not only buffer the volume variation of the CuCo2S4 spheres but can also improve the electrical conductivity due to its conjugated π–π bond.27 Thus, the CS-CuCo2S4@PPy nanocomposites can be preserved for a long cycling stability and excellent rate capability.
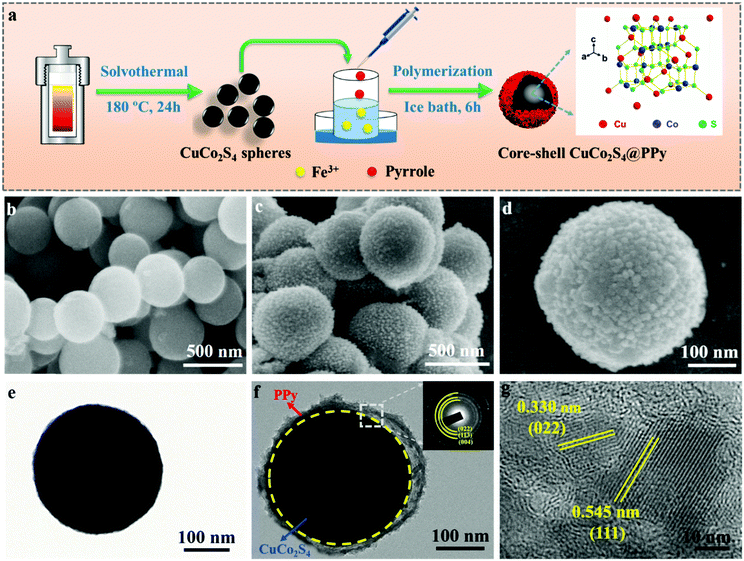 |
| Fig. 1 (a) Illustration for preparing the CS-CuCo2S4@PPy nanocomposites. (b) SEM image of CuCo2S4. (c and d) SEM images of the CS-CuCo2S4@PPy nanocomposites. (e and f) TEM images of CuCo2S4 and CS-CuCo2S4@PPy, inset of (f) is the selected area electron diffraction (SAED) pattern of CS-CuCo2S4@PPy. (g) HRTEM image of the CS-CuCo2S4@PPy nanocomposites. | |
The XRD patterns were tested to detect the crystal structure and phase purity of CuCo2S4 and CS-CuCo2S4@PPy, which ranged from 5° to 80°. As shown in Fig. 2a, the XRD pattern of CS-CuCo2S4@PPy exhibits little difference in the crystallinity compared with pure CuCo2S4 due to the coating of amorphous PPy. In addition, all the diffraction peaks of CuCo2S4 and CS-CuCo2S4@PPy can be indexed to the spinel phase of CuCo2S4 (JCPDS No. 42-1450), and there is no extra diffraction peak for CS-CuCo2S4@PPy, indicating that no impurity was produced in the preparation process. XPS was carried out to identify the elemental composition and valence state of CS-CuCo2S4@PPy, which proved the existence of Cu, Co, S, C, and N elements in the XPS survey spectrum (Fig. S2, ESI†). As shown in Fig. 2b, the spectrum of Cu 2p shows two characteristic peaks located at 952.5 eV (2p1/2) and 932.7 eV (2p3/2), and three satellite peaks, which are ascribed to Cu2+.13 In the Co 2p region (Fig. 2c), both Co 2p3/2 and Co 2p1/2 are deconvoluted into two peaks, which can be indexed to Co3+ (779.5 eV and 794.4 eV) and Co2+ (783.1 eV and 799.9 eV).33 The S 2p peaks (Fig. 2d) are split into three peaks and a satellite peak (168.5 eV). The peaks at 162.0 eV and 163.5 eV can be attributed to S 2p3/2 and S 2p1/2, respectively.10,34 The peak at 164.9 eV indicates the existence of the sulfur–metal (S–M) bond. In case of the C 1s signal (Fig. 2e), the main peak at 284.8 eV can be attributed to the C–C bond in the PPy backbone. The peak at 285.8 eV is ascribed to C–N and the characteristic peak at 288.7 eV is caused by O–C
O owing to the introduction of O2 absorbed on the surface. The N 1s spectra (Fig. 2f) can be divided into three components. The binding energies at 397.6 eV and 399.5 eV correspond to pyridinic-N and pyrrole-type N, respectively, which can create more defects and provide more active sites to improve the electrochemical performance.35–37 The peak at 402.3 eV can be ascribed to the characteristic peak of graphitic-type N.35 The results of XPS confirmed the successful formation of CS-CuCo2S4@PPy. In addition, the pore structure and specific surface area of CS-CuCo2S4@PPy and pure CuCo2S4 were tested by Brunauer–Emmett–Teller (BET) analysis. As shown in Fig. S3 (ESI†), the BET specific surface areas of CS-CuCo2S4@PPy and pure CuCo2S4 were calculated to be 47.5 and 18.6 m2 g−1, respectively. The larger specific surface area of CS-CuCo2S4@PPy can be ascribed to the core–shell structure, which can offer more contact between the electrode and the electrolyte so as to accelerate the diffusion of ions and electrons.
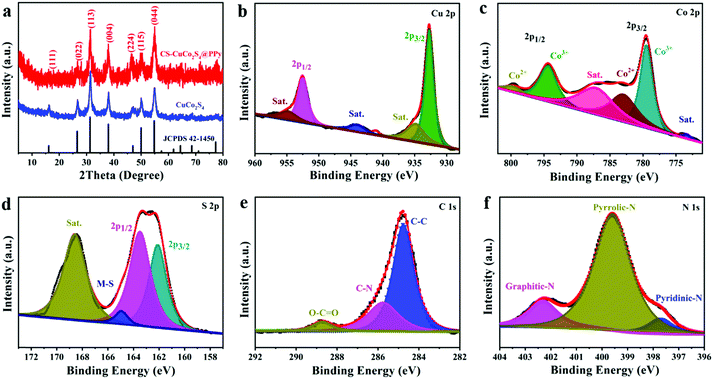 |
| Fig. 2 (a) XRD patterns of CuCo2S4 and the CS-CuCo2S4@PPy nanocomposites. (b–f) High-resolution XPS survey spectrum of Cu 2p (b), Co 2p (c), S 2p (d), C 1s, (e) and N 1s (f) for the as-prepared CS-CuCo2S4@PPy nanocomposites. | |
As is well known, the thickness of the outer conductive polymers can affect the conductivity and diffusion kinetics of Na+.38 The thickness of the PPy layer can be adjusted by controlling the polymerization time. The effect of the polymerization time on the formation of the CS-CuCo2S4@PPy nanocomposites was explored by time-dependent experiments. Fig. 3 shows the SEM and TEM images of the as-prepared samples with different polymerization times ranging from 1 to 12 h. The corresponding XRD results of the as-prepared samples with different polymerization times are illustrated in Fig. S4 (ESI†) and all the main diffraction peaks are similar to that of pure CuCo2S4 except for the crystallinity, which decreased. As shown in Fig. 3a and b, only a small part of the pyrrole monomer reacts to form PPy with the initiator of Fe3+ and adheres on the surface of the CuCo2S4 spheres when the polymerization time is 1 h. It is obvious that most of the CuCo2S4 spheres are exposed without the PPy layer coating. On prolonging the polymerization time to 6 h, PPy was uniformly coated on the surface of the CuCo2S4 spheres to form a conductive and protective layer (Fig. 3c and d). As shown in Fig. 3e and f, when the polymerization time is extended to 12 h, a large amount of the pyrrole monomer is self-polymerized to form disordered nanoparticles with obvious agglomeration except those with coating on the surface of the CuCo2S4 spheres. The agglomerated PPy layer is detrimental to the diffusion of the electrolyte and the insertion/extraction of Na+, which limits the rate capability and cycling stability of the SIBs.
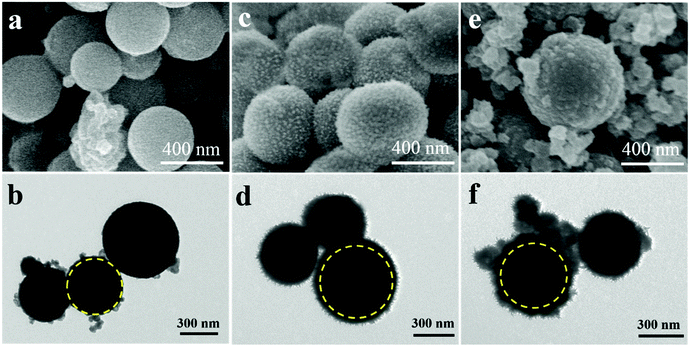 |
| Fig. 3 SEM and TEM images of the CS-CuCo2S4@PPy nanocomposites at different polymerization times. (a and b) 1 h, (c and d) 6 h, (e and f) 12 h. | |
The fundamental electrochemical performance of the as-prepared CS-CuCo2S4@PPy was investigated as an anode in SIBs. As shown in Fig. 4a and Fig. S5 (ESI†), the electrochemical reaction details were explored by cyclic voltammetry (CV) with a scan rate of 0.1 mV s−1 in the voltage window of 0.25–2.75 V (vs. Na/Na+). In the first cathodic cycle, an obvious irreversible peak at 0.75 V can be observed, which can be attributed to the reduction of CuCo2S4 to form metallic Cu and Co.39 A weak peak at 0.54 V can be assigned to the formation of the solid electrolyte interface (SEI) film.23 In the anodic cycle, there is one sharp peak at 1.72 V and four weak peaks at 1.34, 1.56, 1.97, and 2.14 V, which are caused by the involute multi-step oxidation processes of Cu and Co, thus suggesting the formation of CuS, CoS, Co3S4, and some inevitable side products.40,41 In the second cycle of the reduction process, three peaks at 1.46, 0.95, and 0.55 V are owing to the reduction of CuS, CoS, and Co3S4.17,30 In the second cycle, the CV curves are almost overlapped, demonstrating the superior cycling stability of the CS-CuCo2S4@PPy nanocomposites. The typical galvanostatic discharge/charge curves of the CS-CuCo2S4@PPy nanocomposites are displayed in Fig. 4b. In the first discharge cycle, there is a wide plateau in the voltage range from 1.0 V to 0.5 V, which is caused by the reduction of CuCo2S4 to form metallic Cu and Co. In the charge process, there are three plateaus at 1.21–1.50 V, 1.65–1.81 V, and 1.95–2.20 V owing to the multi-step oxidation processes, which are corresponding to the results of the CV test.19,42 The discharge and charge capacities of CS-CuCo2S4@PPy in the first cycle are 672 and 527.4 mA h g−1 respectively, leading to a Coulombic efficiency of 78.4%. The irreversible capacity loss can be ascribed to the formation of the SEI film and some inevitable side reactions.43
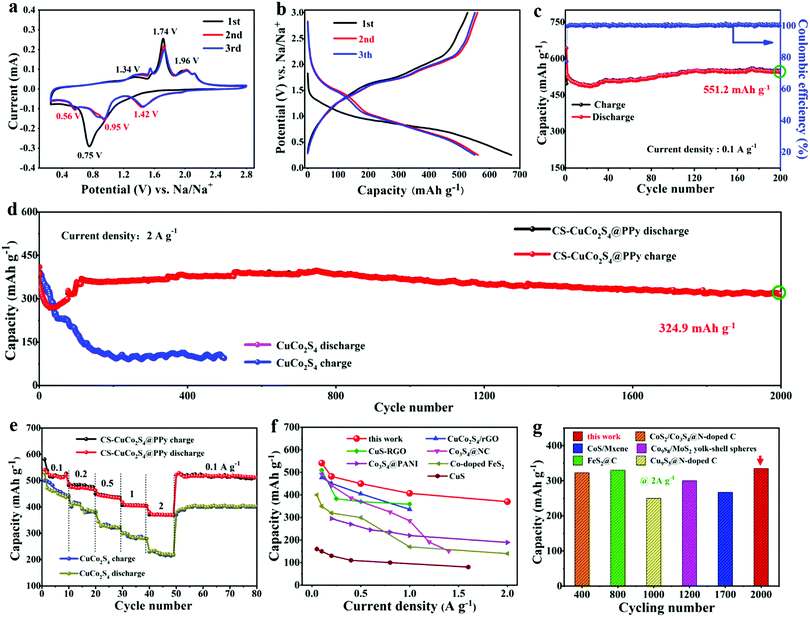 |
| Fig. 4 Na storage performance in the half cell. (a) CV curves of CS-CuCo2S4@PPy at a sweep rate of 0.1 mV s−1. (b) Galvanostatic discharge/charge curves of CS-CuCo2S4@PPy at 0.1 A g−1 during the 3 initial cycles. (c) Cycling stability of CS-CuCo2S4@PPy at 0.1 A g−1. (d) Long cycling stability of CS-CuCo2S4@PPy and pure CuCo2S4 at 2 A g−1. (e) Rate capability of CS-CuCo2S4@PPy and pure CuCo2S4. (f) Comparison of the rate capability of CS-CuCo2S4@PPy with previously reported TMSs-based anode materials. (g) Comparison of the cycling stability of CS-CuCo2S4@PPy with other TMSs-based anode materials at 2 A g−1. | |
The sodium storage performance of the CS-CuCo2S4@PPy nanocomposites was also measured at 0.1 A g−1 (Fig. 4c). The discharge specific capacity of CS-CuCo2S4@PPy in the first cycle was 642.9 mA h g−1 with a Coulombic efficiency of 77.4%. An obvious fluctuation can be observed in the first thirty cycles and then the capacity gradually tends to be stable. After 200 cycles, the CS-CuCo2S4@PPy electrode exhibits a high capacity of 551.2 mA h g−1 with a high Coulombic efficiency of 99.4%. To further confirm the stability of CS-CuCo2S4@PPy, the durable cycling performances of CS-CuCo2S4@PPy and pure CuCo2S4 were also tested at a high current density of 2 A g−1 and are illustrated in Fig. 4d. The CS-CuCo2S4@PPy electrode possesses a high discharge capacity of 409.9 mA h g−1 in the first cycle and then shows an obvious attenuation in the early stage. This phenomenon is common for metal sulfides, which may be related to the self-reconstruction of the nanomaterials and the optimization of the SEI film.23 Subsequently, the capacity of the CS-CuCo2S4@PPy electrode gradually recovers and exhibits a high reversible capacity of 324.9 mA h g−1 after 2000 cycles, while the capacity of the pure CuCo2S4 electrode declines to less than 100 mA h g−1 after 500 cycles, demonstrating an improved long cycling stability of the CS-CuCo2S4@PPy electrode. The ultra-long cycling life can be ascribed to the unique core–shell structure and the flexible PPy layer can effectively accommodate the volume expansion so as to protect CuCo2S4 from pulverization, which can be proved by the SEM and TEM images of CS-CuCo2S4@PPy and the pure CuCo2S4 electrodes after the charge/discharge processes in Fig. S6 (ESI†).
In addition, it is noted that rate capability is a crucial property for SIBs. The CS-CuCo2S4@PPy electrode was tested at a series of different current densities ranging from 0.1 to 2 A g−1. For comparison, the pure CuCo2S4 electrode was also tested under same conditions. As illustrated in Fig. 4e, the CS-CuCo2S4@PPy electrode exhibits ladder-shaped specific capacities of 541, 482.6, 450.2, 407.3, and 370.7 mA h g−1 at 0.1, 0.2, 0.5, 1, and 2 A g−1, respectively. These values are much higher than those of the pure CuCo2S4 electrode, suggesting the superior rate capability of the CS-CuCo2S4@PPy electrode. When the current density returns to 0.1 A g−1, the specific capacity of the pure CuCo2S4 electrode is only 403 mA h g−1, while the specific capacity of the CS-CuCo2S4@PPy electrode is up to 509.7 mA h g−1 with a high capacity retention rate of 94% (compared with the first cycle) after 80 cycles. Fig. 4f and g summarizes the rate capability and the cyclic performance of CS-CuCo2S4@PPy and other reported TMSs-base electrodes. As shown in Fig. 4f, compared with the previously reported TMSs-based electrodes, CS-CuCo2S4@PPy possesses a much higher rate capability.17,35,44–47 In this work, the CS-CuCo2S4@PPy electrode showed an excellent cycling stability with a high capacity of 324.9 mA h g−1 at 2 A g−1 after 2000 cycles, which is better than that of other TMSs-base electrodes (Fig. 4g).23,48–51 The excellent electrochemical performance can be attributed to the improvement in the conductivity for CS-CuCo2S4@PPy, which is caused by the introduction of the PPy layer. In addition, the core–shell structure can effectively increase the contact between the electrode and the electrolyte in order to accelerate the transfer of electrons and Na+.
As shown in Fig. 5a–d, the kinetic analysis of the CS-CuCo2S4@PPy electrodes was carried out to further unravel the capacity contribution for the SIBs. Fig. 5a displays the CV curves at different scan rates ranging from 0.4 mV s−1 to 1 mV s−1. It is obvious that the intensities of the anodic and cathodic peaks grow with increasing scan rates, suggesting the higher activity and stronger kinetics of CS-CuCo2S4@PPy. The relationship of current (i) and scan rate (v) obeys the following equations:52
where
a and
b are adjustable values. The values of
b can be calculated by the log(
i)–log(
v) plots, which reflect the control process of the electrochemical reactions. When
b = 0.5, it means that the electrochemical reaction is determined by the diffusion process. When
b = 1, the electrochemical reaction is controlled by the surface-induced capacitance process. When the value of
b is between 0.5 to 1, it indicates mixed kinetic processes.
16 As illustrated in
Fig. 5b, the calculated
b values for the cathodic anodic peak (peak 1) and cathodic peak (peak 2) are 0.78 and 0.82, respectively, which are closer to 1, suggesting that the electrochemical reaction is predominantly controlled by the capacitive kinetics. The capacitive effect and diffusion-controlled effect of total sodium storage can be quantified based on the following equation:
17The peak current (
Ip) response consists of the capacitive effect (
k1v) and the diffusion-controlled process (
k2v0.5). Also,
k1 and
k2 can be obtained by the following equation:
As shown in
Fig. 5c, the contribution ratio of the surface-induced capacitance process accounts for 74.6% at the scan rate of 0.6 mV s
−1 after calculation.
Fig. 5d demonstrates that the rates of the capacitive effect gradually increase with the values of 67.3%, 74.6%, 77.0%, and 83.2% at the scan rates of 0.4, 0.6, 0.8, and 1.0 mV s
−1, respectively. Both
b values and capacitive contribution display that the electrochemical reaction of CS-CuCo
2S
4@PPy is controlled by the capacitive process, which is caused by the introduction of the conductive PPy layer with rich pyrrole-type N.
53
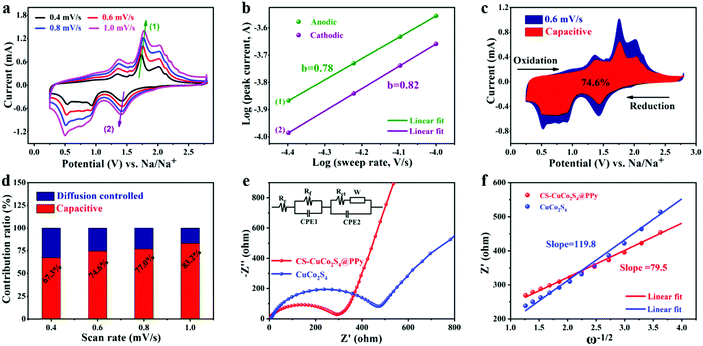 |
| Fig. 5 Kinetic analyses of the sodium storage behavior of the CS-CuCo2S4@PPy electrode in the half cell. (a) CV curves at different scan rates. (b) log(i)–log(v) plots of different peaks. (c) Separation of the contribution of capacitive and diffusion-controlled currents to the total current at 0.6 mV s−1. (d) Contribution ratio of the capacitive capacities at different scan rates. (e) EIS curves of CS-CuCo2S4@PPy and the pure CuCo2S4 electrode after 200 cycles with the inset of the corresponding equivalent circuit. (f) Relation between Z′ and ω−1/2 at the low-frequency region of the as-prepared CS-CuCo2S4@PPy and CuCo2S4 for SIBs. | |
To investigate the improved electrochemical performance, electrochemical impedance spectroscopic (EIS) measurements were also carried out (Fig. 5e and Fig. S7, ESI†). The parameters were obtained from the corresponding equivalent circuit (the inset in Fig. 5e), where Re, Rf, and Rct stand for Ohmic resistance, SEI film resistance, and charge-transfer resistance, respectively. CPE1 and CPE2 represent the constant phase elements and W is the Warburg impedance associated with the diffusion of Na+.15 As shown in Fig. 5e, the EIS curves of CS-CuCo2S4@PPy and the pure CuCo2S4 electrodes consist of a semicircle in the high frequency region and an inclined line in the middle-low frequency region, where the semicircle represents Rct and the slope of the inclined line corresponds to the sodium ion diffusion process. The Rct values of CS-CuCo2S4@PPy and pure CuCo2S4 are 298 Ω and 484 Ω after 200 cycles, respectively, where the smaller Rct demonstrates improved conductivity caused by the coating of the conductive PPy layer compared to pure CuCo2S4. It is accepted that the Na+ diffusion coefficient (DNa+) is an important parameter to investigate the kinetic behavior of the electrochemical reaction. DNa+ can be obtained by the following equation:54
| DNa+ = R2T2/2A2n4F4C2σw2 | (5) |
where
R,
T,
A,
n,
F, and
C stand for gas constant, the absolute temperature, area of electrode surface, the number of electrons, Faraday constant, and the concentration of Na
+, respectively. The
σw stands for Warburg impedance coefficient, which can be calculated according to the equation
Z′ =
Rs +
Rct +
σwω−1/2.
Fig. 5f shows the relationship between the real impedance (
Z′) and the reciprocal square-root of the frequency (
ω−1/2), and the slope values stand for the
σw values. As shown in
Fig. 5f, the
σw values for CS-CuCo
2S
4@PPy and CuCo
2S
4 are 79.5 Ω and 119.8 Ω, respectively. According the calculated results, the
DNa+ values of CS-CuCo
2S
4@PPy and CuCo
2S
4 are 9.82 × 10
−13 cm
2 s
−1 and 4.32 × 10
−13 cm
2 s
−1, respectively, which verifies the better ionic diffusion/transport kinetics for CS-CuCo
2S
4@PPy. This enhancement in the
DNa+ value for CS-CuCo
2S
4@PPy can be attributed to the unique core–shell structure with enough voids to increase the contact between the electrode and the electrolyte.
Owing to the superb electrochemical performance of CS-CuCo2S4@PPy as the sodium ion half cell, the coin-type NVP‖CS-CuCo2S4@PPy full sodium ion cell was assembled. NVP was used as the cathode material due to its suitable working voltage and slight polarization in the charge/discharge process.15 For capacity matching, the weight ratio of NVP and CS-CuCo2S4@PPy was 4
:
1 so as to ensure maximum utilization and the electrochemical performance of CS-CuCo2S4@PPy was reasonably evaluated. The schematic diagram of the full cell assembly is shown in Fig. 6a.
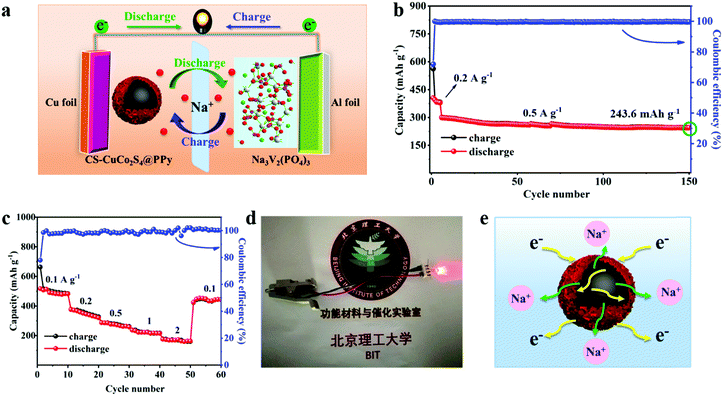 |
| Fig. 6 (a) Schematic illustration of the NVP‖CS-CuCo2S4@PPy full sodium ion cell. (b) Cycling stability of the full cell at 0.2 and 0.5 A g−1. (c) Rate performance of the full cell. (d) The digital photo of the NVP‖CS-CuCo2S4@PPy full sodium ion cell with the light red LED bulb. (e) Schematic structural features about the CS-CuCo2S4@PPy anode for Na+ and electron transport. | |
Fig. S8 (ESI†) shows the charge/discharge curves of the full cell at 0.5 A g−1 with a potential window of 0.25–3.0 V. As shown in Fig. 6b, the full cell was activated after 5 cycles at 0.2 A g−1 and then it was measured at 0.5 A g−1. The charge/discharge capacities in the first cycle are 562.5 and 405 mA h g−1, respectively, based on the anode material at 0.2 A g−1 with a Coulombic efficiency of 72%. In the following cycles, the Coulombic efficiency is gradually stabilized at about 100% and the specific capacity can maintain 243.6 mA h g−1 at 0.5 A g−1 even after 150 cycles, demonstrating the excellent cycling stability. The full cell was also tested at a series of current densities ranging from 0.1 A g−1 to 2 A g−1 so as to measure its rate capability. As shown in Fig. 6c, the full cell exhibits stepped capacities of 484, 324, 266, and 213.5 mA h g−1 at 0.1, 0.2, 0.5, and 1 A g−1, respectively. Even at a high current density of 2 A g−1, it still delivers a reversible capacity of 160.9 mA h g−1. When the current density returns to 0.1 A g−1, the capacity of 443.9 mA h g−1 is regained, which illustrates its superior rate capability. In view of evaluating its practical application, as shown in Fig. 6d, the full cell was employed to light up the red light-emitting diode lamp bead. The satisfactory electrochemical performance of CS-CuCo2S4@PPy for half and full SIBs validates that CS-CuCo2S4@PPy can be a potential anode material for sodium ion storage.
As shown in Fig. 6e, the competitive electrochemical performance of CS-CuCo2S4@PPy for half and full SIBs can be ascribed to the synergistic effect of CuCo2S4 and PPy. The CuCo2S4 spheres offer more active sites for the conversion reaction so as to improve the capacity. The flexible PPy layer can protect the CuCo2S4 spheres from pulverization, increase the conductivity, and buffer the volume change during the charge/discharge processes. Significantly, the core–shell microstructure of CS-CuCo2S4@PPy can enhance the contact between electrode and the electrolyte by making full use of the void to shorten the electrons/ions diffusion pathway and to accelerate the transfer of electrons.
Conclusions
In summary, CuCo2S4@PPy nanocomposites with a core–shell structure were successfully prepared through a two-step method, which contains a simple solvothermal method and in-situ chemical oxidation polymerization. The reaction time of polymerization has a great influence on the formation of the core–shell structure, where the CuCo2S4 can offer rich valence constituent and active sites, and the PPy layer protects CuCo2S4 from pulverization and accelerates the transfer of electrons and Na+. Benefiting from the stable core–shell microstructure and the synergistic effect of CuCo2S4 and PPy, and acting as an anode for half SIBs, CS-CuCo2S4@PPy exhibits a high reversible capacity of 551.2 mA h g−1 at 0.1 A g−1 after 200 cycles, a durable cycling performance of 324.9 mA h g−1 after 2000 cycles at a high current density of 2 A g−1, and improved rate performance, which are better thatn that of pure CuCo2S4. The kinetic analysis reveals that up to 74.6% charge contribution of CS-CuCo2S4@PPy arises from the capacitive-controlled capacity (0.6 mV s−1), resulting in excellent rate performance for SIBs. In addition, the NVP‖CS-CuCo2S4@PPy full sodium ion cell shows a superb electrochemical performance with a reversible capacity of 243.6 mA h g−1 at 0.5 A g−1 after 150 cycles. This strategy can be extended to prepare other conductive polymers-coated TMSs, which can be applied in the energy storage and conversion field.
Conflicts of interest
There are no conflicts to declare.
Acknowledgements
This work was financially supported by the Program for Innovative and Entrepreneurial team in Zhuhai (ZH01110405160007PWC). The authors also thanked Analysis & Testing Center (Beijing Institute of Technology) and Beijing Key Laboratory for Chemical Power Source and Green Catalysis.
Notes and references
- Z. Ali, M. Asif, X. Huang, T. Tang and Y. Hou, Hierarchically Porous Fe2CoSe4 Binary-Metal Selenide for Extraordinary Rate Performance and Durable Anode of Sodium-Ion Batteries, Adv. Mater., 2018, 30, 1802745 CrossRef.
- Y. Fang, X. Y. Yu and X. W. D. Lou, Formation of Polypyrrole-Coated Sb2Se3 Microclips with Enhanced Sodium-Storage Properties, Angew. Chem., Int. Ed., 2018, 57, 9859–9863 CrossRef CAS.
- Y. Wang, P. Ma, D. Cao, Z. Kang and D. Sun, SnS@C nanospheres coated with few-layer MoS2 nanosheets and nitrogen, phosphorus-codoped carbon as robust sodium ion battery anodes, Mater. Chem. Front., 2020, 4, 1212–1221 RSC.
- P. Ge, S. Li, L. Xu, K. Zou, X. Gao, X. Cao, G. Zou, H. Hou and X. Ji, Hierarchical Hollow-Microsphere Metal-Selenide@Carbon Composites with Rational Surface Engineering for Advanced Sodium Storage, Adv. Energy Mater., 2019, 9, 1803035 CrossRef.
- X. Hu, Q. Peng, T. Zeng, B. Shang, X. Jiao and G. Xi, Promotional role of nano TiO2 for pomegranate-like SnS2@C spheres toward enhanced sodium ion storage, Chem. Eng. J., 2019, 363, 213–223 CrossRef CAS.
- Y. Sun, Z. Sui, L. Zhao, M. Goktas, H. Zhou, P. Xiao, P. Adelhelm and B. Han, Synthesis and thermodynamic investigation of MnO nanoparticle anchored N-doped porous carbon as the anode for Li-ion and Na-ion batteries, Mater. Chem. Front., 2019, 3, 2728 RSC.
- Y. F. Yuan, L. W. Ye, D. Zhang, F. Chen, M. Zhu, L. N. Wang, S. M. Yin, G. S. Cai and S. Y. Guo, NiCo2S4 multi-shelled hollow polyhedrons as high-performance anode materials for lithium-ion batteries, Electrochim. Acta, 2019, 299, 289–297 CrossRef CAS.
- S. Tang, B. Zhu, X. Shi, J. Wu and X. Meng, General Controlled Sulfidation toward Achieving Novel Nanosheet-Built Porous Square-FeCo2S4-Tube Arrays for High-Performance Asymmetric All-Solid-State Pseudocapacitors, Adv. Energy Mater., 2017, 7, 1601985 CrossRef.
- D. Zhao, H. Liu and X. Wu, Bi-interface induced multi-active MCo2O4@MCo2S4@PPy (M = Ni, Zn) sandwich structure for energy storage and electrocatalysis, Nano Energy, 2019, 57, 363–370 CrossRef CAS.
- S. Czioska, J. Wang, X. Teng and Z. Chen, Hierarchically Structured CuCo2S4 Nanowire Arrays as Efficient Bifunctional Electrocatalyst for Overall Water Splitting, ACS Sustainable Chem. Eng., 2018, 6, 11877–11883 CrossRef CAS.
- Y. Huang, L. Lin, T. Shi, S. Cheng, Y. Zhong, C. Chen and Z. Tang, Graphene quantum dots-induced morphological changes in CuCo2S4 nanocomposites for supercapacitor electrodes with enhanced performance, Appl. Surf. Sci., 2019, 463, 498–503 CrossRef CAS.
- J. Lin, H. Jia, H. Liang, S. Chen, Y. Cai, J. Qi, C. Qu, J. Cao, W. Fei and J. Feng, Hierarchical CuCo2S4@NiMn-layered double hydroxide core-shell hybrid arrays as electrodes for supercapacitors, Chem. Eng. J., 2018, 336, 562–569 CrossRef CAS.
- J. Sun, T. Song, Z. Shao, N. Guo, K. Huang, F. He and Q. Wang, Interfacial Electronic Structure Modulation of Hierarchical Co(OH)F/CuCo2S4 Nanocatalyst for Enhanced Electrocatalysis and Zn-Air Batteries Performances, ACS Appl. Mater. Interfaces, 2019, 11, 37531–37540 CrossRef CAS.
- M. Chauhan, K. Soni, P. E. Karthik, K. P. Reddy, C. S. Gopinath and S. Deka, Promising visible-light driven hydrogen production from water on a highly efficient CuCo2S4 nanosheet photocatalyst, J. Mater. Chem. A, 2019, 7, 6985–6994 RSC.
- Q. Li, H. Li, W. Zhou, X. Feng, B. Qiu, Q. Shi, Y. Zheng, Y. Zhao and C. Feng, In-situ preparation of multi-layered sandwich-like CuCo2S4/rGO architectures as anode material for high-performance lithium and sodium ion batteries, J. Alloys Compd., 2020, 845, 156183 CrossRef CAS.
- P. Wang, Y. Zhang, Y. Yin, L. Fan, N. Zhang and K. Sun, In-situ synthesis of CuCo2S4@N/S doped graphene composites with pseudocapacitive properties for high performance lithium ion batteries, ACS Appl. Mater. Interfaces, 2018, 10, 11708–11714 CrossRef CAS.
- Y. Gong, J. Zhao, H. Wang and J. Xu, CuCo2S4/reduced graphene oxide nanocomposites synthesized by one-step solvothermal method as anode materials for sodium ion batteries, Electrochim. Acta, 2018, 292, 895–902 CrossRef CAS.
- W. Lu, X. Guo, Y. Luo, Q. Li, R. Zhu and H. Pang, Core-shell materials for advanced batteries, Chem. Eng. J., 2019, 355, 208–237 CrossRef CAS.
- Y. Fang, B. Guan, D. Luan and X. W. Lou, Elegant Synthesis of CuS@CoS2 Double-Shelled Nanoboxes with Enhanced Sodium Storage Properties, Angew. Chem., Int. Ed., 2019, 58, 7739–7743 CrossRef CAS.
- X. Wei, Y. Zhang, B. Zhang, Z. Lin, X. Wang, P. Hu, S. Li, X. Tan, X. Cai, W. Yang and L. Mai, Yolk-shell-structured zinc–cobalt binary metal sulfide@N-doped carbon for enhanced lithium-ion storage, Nano Energy, 2019, 64, 103899 CrossRef CAS.
- J. Gao, Y. Li, Y. Liu, S. Jiao, J. Li, G. Wang, S. Zeng and G. Zhang, The dual-function sacrificing template directed formation of MoS2/C hybrid nanotubes enabling highly stable and ultrafast sodium storage, J. Mater. Chem. A, 2019, 7, 18828–18834 RSC.
- W. Chen, X. Zhang, L. Mi, C. Liu, J. Zhang, S. Cui, X. Feng, Y. Cao and C. Shen, High-Performance Flexible Freestanding Anode with Hierarchical 3D Carbon-Networks/Fe7S8/Graphene for Applicable Sodium-Ion Batteries, Adv. Mater., 2019, 31, e1806664 CrossRef.
- C. Dong, L. Guo, H. Li, B. Zhang, X. Gao, F. Tian, Y. Qian, D. Wang and L. Xu, Rational fabrication of CoS2/Co4S3@N-doped carbon microspheres as excellent cycling performance anode for half/full sodium ion batteries, Energy Storage Mater., 2019, 25, 679–686 CrossRef.
- X. Li, K. Li, S. Zhu, K. Fan, L. Lyu, H. Yao, Y. Li, J. Hu, H. Huang, Y. W. Mai and J. B. Goodenough, Fiber-in-Tube Design of Co9S8-Carbon/Co9S8: Enabling Efficient Sodium Storage, Angew. Chem., Int. Ed., 2019, 58, 6239–6243 CrossRef CAS.
- P. Asen and S. Shahrokhian, A High Performance Supercapacitor Based on Graphene/Polypyrrole/Cu2O–Cu(OH)2 Ternary Nanocomposite Coated on Nickel Foam, J. Phys. Chem. C, 2017, 121, 6508–6519 CrossRef CAS.
- Q. Wang, Y. Ma, X. Liang, D. Zhang and M. Miao, Novel core/shell CoSe2@PPy nanoflowers for high-performance fiber asymmetric supercapacitors, J. Mater. Chem. A, 2018, 6, 10361–10369 RSC.
- Y. Zhou, Y. Li, J. Yang, J. Tian, H. Xu, J. Yang and W. Fan, Conductive Polymer-Coated VS4 Submicrospheres As Advanced Electrode Materials in Lithium-Ion Batteries, ACS Appl. Mater. Interfaces, 2016, 8, 18797–18805 CrossRef CAS.
- Q. Qu, Y. Zhu, X. Gao and Y. Wu, Core-Shell Structure of Polypyrrole Grown on V2O5 Nanoribbon as High Performance Anode Material for
Supercapacitors, Adv. Energy Mater., 2012, 2, 950–955 CrossRef CAS.
- G. Wang, X. Bi, H. Yue, R. Jin, Q. Wang, S. Gao and J. Lu, Sacrificial template synthesis of hollow C@MoS2@PPy nanocomposites as anodes for enhanced sodium storage performance, Nano Energy, 2019, 60, 362–370 CrossRef CAS.
- Q. Li, Q. Jiao, X. Feng, Y. Zhao, H. Li, C. Feng, D. Shi, H. Liu, H. Wang and X. Bai, One-Pot Synthesis of CuCo2S4 Sub-Microspheres for High-Performance Lithium-/Sodium-Ion Batteries, ChemElectroChem, 2019, 6, 1558–1566 CrossRef CAS.
- L. Kang, C. Huang, J. Zhang, M. Zhang, N. Zhang, S. Liu, Y. Ye, C. Luo, Z. Gong, C. Wang, X. Zhou, X. Wu and S. C. Jun, Effect of fluorine doping and sulfur vacancies of CuCo2S4 on its electrochemical performance in supercapacitors, Chem. Eng. J., 2020, 390, 124643 CrossRef CAS.
- N. Zang, Z. Wu, J. Wang and W. Jin, Rational design of Cu–Co thiospinel ternary sheet arrays for highly efficient electrocatalytic water splitting, J. Mater. Chem. A, 2020, 8, 1799–1807 RSC.
- M. Chauhan, K. P. Reddy, C. S. Gopinath and S. Deka, Copper Cobalt Sulfide Nanosheets Realizing a Promising Electrocatalytic Oxygen Evolution Reaction, ACS Catal., 2017, 7, 5871–5879 CrossRef CAS.
- N. Tang, H. You, M. Li, G. Z. Chen and L. Zhang, Cross-linked Ni(OH)2/CuCo2S4/Ni networks as binder-free electrodes for high performance supercapatteries, Nanoscale, 2018, 10, 20526–20532 RSC.
- Y. Jiang, G. Zou, W. Hong, Y. Zhang, Y. Zhang, H. Shuai, W. Xu, H. Hou and X. Ji, N-Rich carbon-coated Co3S4 ultrafine nanocrystals derived from ZIF-67 as an advanced anode for sodium-ion batteries, Nanoscale, 2018, 10, 18786–18794 RSC.
- L. Wu, J. Zheng, L. Wang, X. Xiong, Y. Shao, G. Wang, J. H. Wang, S. Zhong and M. Wu, PPy-encapsulated SnS2 Nanosheets Stabilized by Defects on a TiO2 Support as a Durable Anode Material for Lithium-Ion Batteries, Angew. Chem., Int. Ed., 2019, 58, 811–815 CrossRef CAS.
- D. Xie, M. Zhang, F. Cheng, H. Fan, S. Xie, P. Liu and J. Tu, Hierarchical MoS2@Polypyrrole core-shell microspheres with enhanced electrochemical performances for lithium storage, Electrochim. Acta, 2018, 269, 632–639 CrossRef CAS.
- K. Wang, S. P. Huang, Y. Wu, N. N. Cai, N. Li, Q. Xiao and Z. Sun, Critical thickness of a surface-functionalized coating for enhanced lithium storage: a case study of nanoscale polypyrrole-coated FeS2 as a cathode for Li-ion batteries, Nanoscale, 2019, 11, 16277–16283 RSC.
- R. Jin, Y. Cui, S. Gao, S. Zhang, L. Yang and G. Li, CNTs@NC@CuCo2S4 nanocomposites: An advanced electrode for high performance lithium-ion batteries and supercapacitors, Electrochim. Acta, 2018, 273, 43–52 CrossRef CAS.
- P. Wang, Y. Zhang, B. Guan, L. Fan, N. Zhang and K. Sun, Fabrication of CuCo2S4 hollow sphere @N/S doped graphene composites as high performance anode materials for lithium ion batteries, Ceram. Int., 2018, 44, 11905–11909 CrossRef CAS.
- T. Zheng, G. Li, X. Meng, S. Li and M. Ren, Porous Core-Shell CuCo2S4 Nanospheres as Anode Material for Enhanced Lithium-Ion Batteries, Chem. – Eur. J., 2018, 25, 885–891 CrossRef.
- Y. Pan, X. Cheng, L. Gong, L. Shi and H. Zhang, Nanoflower-like N-doped C/CoS2 as high-performance anode materials for Na-ion batteries, Nanoscale, 2018, 10, 20813–20820 RSC.
- Y. N. Ko and Y. C. Kang, Co9S8-carbon composite as anode materials with improved Na-storage performance, Carbon, 2015, 94, 85–90 CrossRef CAS.
- K. Zhang, M. Park, L. Zhou, G. H. Lee, J. Shin, Z. Hu, S. L. Chou, J. Chen and Y. M. Kang, Cobalt-Doped FeS2 Nanospheres with Complete Solid Solubility as a High-Performance Anode Material for Sodium-Ion Batteries, Angew. Chem., Int. Ed., 2016, 55, 12822–12826 CrossRef CAS.
- Q. Zhou, L. Liu, Z. Huang, L. Yi, X. Wang and G. Cao, Co3S4@polyaniline nanotubes as high-performance anode materials for sodium ion batteries, J. Mater. Chem. A, 2016, 4, 5505–5516 RSC.
- H. Li, Y. Wang, J. Jiang, Y. Zhang, Y. Peng and J. Zhao, CuS Microspheres as High-Performance Anode Material for Na-ion Batteries, Electrochim. Acta, 2017, 247, 851–859 CrossRef CAS.
- J. Li, D. Yan, T. Lu, W. Qin, Y. Yao and L. Pan, Significantly Improved Sodium-Ion Storage Performance of CuS Nanosheets Anchored into Reduced Graphene Oxide with Ether-Based Electrolyte, ACS Appl. Mater. Interfaces, 2017, 9, 2309–2316 CrossRef CAS.
- Y. Zhang, R. Zhan, Q. Xu, H. Liu, M. Tao, Y. Luo, S. Bao, C. Li and M. Xu, Circuit board-like CoS/MXene composite with superior performance for sodium storage, Chem. Eng. J., 2019, 357, 220–225 CrossRef CAS.
- H. Geng, J. Yang, Z. Dai, Y. Zhang, Y. Zheng, H. Yu, H. Wang, Z. Luo, Y. Guo, Y. Zhang, H. Fan, X. Wu, J. Zheng, Y. Yang, Q. Yan and H. Gu, Co9S8/MoS2 Yolk-Shell Spheres for Advanced Li/Na Storage, Small, 2017, 13, 1603490 CrossRef.
- Z. Liu, T. Lu, T. Song, X.-Y. Yu, X. W. Lou and U. Paik, Structure-designed synthesis of FeS2@C yolk–shell nanoboxes as a high-performance anode for sodium-ion batteries, Energy Environ. Sci., 2017, 10, 1576–1580 RSC.
- X. D. Lou, Bullet-like Cu9S5 Hollow Particles Coated with Nitrogen-Doped Carbon for Sodium-Ion Batteries, Angew. Chem., Int. Ed., 2019, 131, 7826–7830 CrossRef.
- Q. Guo, Y. Ma, T. Chen, Q. Xia, M. Yang, H. Xia and Y. Yu, Cobalt Sulfide Quantum Dot Embedded N/S-Doped Carbon Nanosheets with Superior Reversibility and Rate Capability for Sodium-Ion Batteries, ACS Nano, 2017, 11, 12658–12667 CrossRef CAS.
- P. Ge, H. Hou, S. Li, L. Yang and X. Ji, Tailoring Rod-Like FeSe2 Coated with Nitrogen-Doped Carbon for High-Performance Sodium Storage, Adv. Funct. Mater., 2018, 28, 1801765 CrossRef.
- R. Jin, X. Liu, L. Yang, G. Li and S. Gao, Sandwich-like Cu2-xSe@C@MoSe2 nanosheets as an improved-performance anode for lithium-ion battery, Electrochim. Acta, 2018, 259, 841–849 CrossRef CAS.
Footnote |
† Electronic supplementary information (ESI) available. See DOI: 10.1039/d0qm00599a |
|
This journal is © the Partner Organisations 2021 |
Click here to see how this site uses Cookies. View our privacy policy here.