DOI:
10.1039/D1RA03270D
(Paper)
RSC Adv., 2021,
11, 22426-22432
Separation and recovery of arsenic from As, Cu, and Zn rich leaching liquor using a reduction-crystallization approach
Received
27th April 2021
, Accepted 20th June 2021
First published on 28th June 2021
Abstract
As, Cu, and Zn rich leaching liquor is generated in the leaching process of copper dust, which contains various metals with high recovery value. Herein, an approach for the direct separation and recovery of arsenic from As, Cu, and Zn rich leaching liquor was proposed. The approach includes two steps, namely SO2 reduction and arsenic crystallization. The factors affecting the reduction of As(V) to As(III) were investigated, including the pH, SO2 dosage, and reduction temperature. In the crystallization stage, the impacts of sulfuric acid consumption and temperature on the crystallization of arsenic (As2O3) were studied. The results show that the optimal H+ concentration, temperature, and SO2 input for the arsenic reduction were 3.95 mol L−1, 45 °C, and 1.14 L g−1 As(V), respectively. While the optimal temperature and sulfuric acid dosage in As recovery process were 5 °C and 0.1 L L−1 leaching liquor, respectively. Under these conditions, the As2O3 recovery percentage reached 96.53%, and the losses of Cu and Zn were only 3.12% and 0.75%, respectively. The precipitate contained 96.72% of As2O3, 0.83% of Cu, and 0.13% Zn. Compared with the traditional technologies, this new method can improve the recovery efficiency of As2O3 and reduce the loss percentage of other valuable metals (Cu and Zn).
Introduction
As2O3 is one of the important compounds of As, which has been widely used in the pharmaceutical, antiseptic, leather, and glass industries.1–4 However, it is also a toxic substance that can cause serious environmental pollution.5–9 Naturally, arsenic coexists with copper and zinc, and it can be enriched in the dust during the production of copper via pyrometallurgical process.10–16 The dust is usually leached by H2SO4,17–20 generating a large amount of As, Cu, and Zn rich leaching liquor. As, Cu and Zn have decent economic values and are widely used in various fields. Hence, recovery of these valuable metals is of great significance, not only for economic benefit but also for environmental protection.21
Recently, various methods have been proposed for the recovery of As from arsenic solution, including sulfide precipitation,22,23 calcium–arsenic coprecipitation,24 iron–arsenic coprecipitation,25–28 ionic adsorption,29,30 microbe treatment methods,31 reduction method32 and so on.33,34 Among these methods, the sulfur dioxide reduction, evaporation, and crystallization methods entail to reduce As(V) to As(III), and then, evaporate and concentrate the leaching liquor to precipitate As2O3 crystals.35,36 This process results in co-precipitation of other valuable metals in the arsenic-containing solution with As2O3 crystals and greatly increases the concentration of Zn, Cu, and inorganic salts in the arsenic-removal solution. The other methods for recovering As necessitate the addition of new reagents into the arsenic-containing solution to precipitate As at a certain pH. As-containing materials produced by these methods are still hazardous solid wastes and are not conducive for the sustainable ecological environment because they can only be stored or landfilled. Also, arsenic recovery by these methods can increase the concentration of impurities in the arsenic-removal solution, which causes problems in the recovery of valuable metals (such as Zn, Cu, etc.) from the arsenic-removal solution. Thus, a clean and effective method is urgently required to separate and recover the arsenic and valuable metals.
Herein, a new method for As2O3 recovery from As, Cu, and Zn rich leaching liquor was proposed. The process involves two steps, namely reduction of As(V) to As(III) by injecting SO2 gas, and followed by direct cooling crystallization of As(III) in the form of As2O3. Compared to other processes for arsenic recovery, this approach only involves in the addition of H2SO4 and SO2 without introducing any impurities, which makes it easier to subsequently recover other valuable metals from the leaching liquor. The factors affecting the separation and recovery of As, including SO2 input, [H+] concentration, and reduction temperature during the conversion of As(V) into As(III), and sulfuric acid concentration and cooling temperature during As2O3 crystallization, were systematically explored. This work provides a process for the recovery of arsenic from As, Cu, and Zn rich leaching liquor.
Experimental
Materials
The As, Cu, and Zn rich leaching liquor was obtained as follows. The copper dust with high As, Cu, and Zn contents was circulating leached and filtered using sulfuric acid and hydrogen peroxide solution at the ambient temperature and pressure.37 Hydrogen peroxide was used to oxidize As(III) to As(V). The copper dust was the secondary dust produced in the smelting process of copper concentrate (obtained from a copper smelting company), which contained 12.51% As, 3.02% Cu, 11.59% Zn, 0.12% Fe, 2.87% Bi, and 16.06% Pb (w/w). The XRD patterns of copper dust are shown in Fig. 1a. Since the copper dust contained negligible Fe, while Pb and Bi species were retained in the solid phase after sulfuric acid leaching due to the formation of insoluble anglesite (PbSO4) and bismuth sulphate (Bi2(SO4)3), respectively, the main constituents in the leaching liquor were As(III), As(V), Cu, and Zn, and their concentrations are listed in Table 1. All reagents were of analytical grade (>98%). Sulfuric acid was obtained from Chengdu Cologne Chemical Co., Ltd. and sulfur dioxide was provided by Hengyang Jiantao Chemical Co., Ltd.
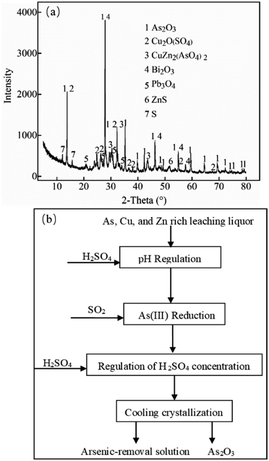 |
| Fig. 1 (a) XRD patterns of the copper dust. (b) The process of arsenic recovery from As, Cu, and Zn rich leaching liquor. | |
Table 1 The concentrations of the main constituents in the As, Cu, and Zn rich leaching liquor (mol L−1)
As |
As(III) |
As(V) |
Cu |
Zn |
1.068 |
0.135 |
0.933 |
0.315 |
0.928 |
Apparatus and procedure
The process of arsenic recovery from As, Cu, and Zn rich leaching liquor is displayed in Fig. 1b. 200 mL leaching liquor was added into a three-port conical flask (500 mL). The left interface of the conical flask was connected with a small tank of SO2. The middle interface was connected to a separating funnel with valve and the joint was sealed with a rubber, while the right interface was connected to the piston. Then, the flask was fixed into a bath heater with a magnetic stirrer. Sulfuric acid was added into the separating funnel.
The initial concentration of H+ in the leaching liquor was 0.6 mol L−1. The pH was adjusted to a certain value using sulfuric acid. SO2 was introduced into the solution to reduce As(V) to As(III), as shown in eqn (1)–(3),38 and prevent As(III) from forming Cu(AsO2)2 precipitates with Cu2+. The flow rate of SO2 was adjusted using a switch valve.
The oxidation half-reaction:
|
SO2 + 2H2O − 2e− = 4H+ + SO42−
| (1) |
The reduction half-reaction:
|
HAsO3 + 2H+ + 2e− = HAsO2 + H2O
| (2) |
Total redox reaction:
|
HAsO3 + H2O + SO2 = HAsO2 + H2SO4
| (3) |
After As(V) was completely transformed into As(III), sulfuric acid was added into the leaching liquor to adjust the [H+] concentration. Then, ice-water bath was applied to cool the solution to crystallize As(III) in the form of As2O3 through eqn (4).
The recovery percentage of As2O3 and the precipitation percentage of Cu and Zn were calculated using eqn (5)–(7):
|
 | (5) |
|
ηAs2O3 = (m × WAs/V × CAs) × 100%
| (6) |
|
 | (7) |
where
ηAs(III) is the conversion efficiency of As(
III),
ηAs2O3 1is the recovery percentage of As
2O
3,
ηi is the precipitation rate of Cu and Zn,
V is the initial volume of the leaching liquor,
V′ is the solution volume of As(
V) deoxidizing As(
III),
Vi is the volume of filtration solution after the precipitation of As
2O
3.
CAs and
CAs(III) are the initial concentrations of As and As(
III), respectively, while

is the concentration of As(
III) in the transformed solution.
Ci is the concentration of Cu and Zn in the precipitation and filtration solution of As
2O
3,
m is the weight of As
2O
3, and
WAs is the content of As in As
2O
3.
Analytical methods
The concentrations of Cu, Zn, and As in the leaching liquor were determined via inductively coupled plasma-optical emission spectroscopy (ICP-OES). The [H+] was measured via acid–base titration. The solid sample was dissolved by HNO3 and HCl, and then the elemental contents were determined by ICP-OES. The phase compositions of the residues were obtained via X-ray diffraction (XRD, D/max 2500v/pc, Cu Kα radiation). The particle size of the precipitates was determined by the laser particle size analyzer (Malvern Instruments, MS200). Before particle size measurement, the precipitates were ultrasonically dispersed. The content of As(III) was determined with the cerous sulfate–potassium bromate titration, while that of As(V) was obtained by subtracting the As(III) from total As concentration.
Results and discussion
Thermodynamics studies
The thermodynamic Gibbs free energies of the main reactions in the system are listed in Table 2. The relationship between potential and pH for each chemical reactions can be expressed as follows:39 |
aOx + nH+ + ze = bRed
| (8) |
|
 | (9) |
where Ox and Red are the oxidized and reduced states of species, a, b, n, and z are the number of oxidized species, hydrogen ions, electrons, and reduced species participated in the equation, respectively, and F is the Faraday constant.
Table 2 The Gibbs free energies (ΔrGθ) of main chemical reactions
Equilibrium reaction |
ΔrGθ (kJ mol−1) |
25 °C |
65 °C |
H2AsO4− + H+ = H3AsO4 |
−12.79 |
−15.82 |
HAsO42− + H+ = H2AsO4− |
−38.63 |
−43.84 |
H3AsO4 + 2H+ + 2e = H3AsO3 + H2O |
−110.78 |
−108.64 |
H2AsO4− + 3H+ + 2e = H3AsO3 + H2O |
−123.66 |
−124.46 |
HAsO42− + 4H+ + 2e = H3AsO3 + H2O |
−162.29 |
−168.31 |
HAsO42− + 3H+ + 2e = H2AsO3− + H2O |
−109.60 |
−112.22 |
H3AsO3 = HAsO2 + H2O |
−0.32 |
−0.60 |
AsO43− + 4H+ + 2e = H2AsO3− + H2O |
−175.81 |
−185.53 |
AsO43− + 8H+ + 5e = As + 4H2O |
−300.34 |
−308.18 |
H3AsO3 + 3H+ + 3e = As + 3H2O |
−71.85 |
−66.56 |
H2AsO3− + 4H+ + 3e = As + 3H2O |
−124.54 |
−122.65 |
As + 3H+ + 3e = AsH3 |
60.71 |
64.13 |
SO2 + H2O = H2SO3 |
−0.64 |
3.10 |
H2SO3 + H2O − 2e = HSO4− + 3H+ |
19.68 |
21.33 |
HSO4− = H+ + SO42− |
10.93 |
16.11 |
3Cu2+ + 2HAsO4− = Cu3(AsO4)2 + 2H+ |
−82.18 |
−107.62 |
Cu2+ + 2HAsO2 = Cu(AsO2)2 + 2H+ |
−7.38 |
−8.00 |
The Eh–pH diagrams of Cu–As–S–O–H2O system at different temperatures are displayed in Fig. 2. Under different pH and Eh values, As(III) had different forms in the solution. At 25 °C (see Fig. 2a), when pH was in the range of −0.5–2 and Eh lower than 0.45 V, As and Cu in the leaching liquor co-precipitated in the form of Cu(AsO2)2 or Cu3As. When Eh <0.5 V, HAsO3 transformed into HAsO2 as the Eh value decreased continuously. When Eh <0.35 V, As and Cu also co-precipitated in the form of Cu3As. Therefore, for the reduction of As(V) to As(III), the solution pH value should be lower than −0.5, and Eh should be strictly controlled so that it is not too low to cause co-precipitation of As and Cu in the form of Cu3As.
 |
| Fig. 2 Eh–pH diagrams of the Cu–As–S–O–H2O system at (a) 25 °C and (b) 65 °C. Figures were drawn by the HSC Chemistry Software (Version 6.0, Outokumpu Research Oy, Finland). The initial concentrations were CAs = 1.068 mol L−1, CS = 3.218 mol L−1, CCu = 0.315 mol L−1, and CZn = 0.928 mol L−1. | |
Comparing Fig. 2a with 2b, the Eh–pH region for Cu(AsO2)2 formation varied at different temperatures, which was enlarged at a higher temperature. This indicate that the temperature may have a significant influence on the reduction of As(V) to As(III).
Factors on As(V) to As(III) conversion and Cu/Zn precipitation
To explore the feasibility and effectiveness of arsenic recovery from the As, Cu, and Zn rich leaching liquor by the reduction-cooling crystallization approach, the effects of SO2 input, H+ concentration, and temperature on the conversion of As(V) to As(III) and Cu/Zn precipitation were studied.
Effect of SO2 input. As presented in Fig. 3, under different SO2 dosages and initial acidities, the conversion percentage of As(V) to As(III) and precipitation percentages of Cu and Zn were quite different. As shown in Fig. 3a, both the SO2 injection and initial H+ concentration had significant impact on the As(V) to As(III) conversion percentage. Under the same initial concentration of H+, as the SO2 injection volume increased gradually, the conversion percentage of As(V) to As(III) increased. Addition of SO2 resulted in a decrease in the redox potential in the liquor, which was beneficial for the reduction of As(V) to As(III).35 Moreover, when the SO2 injection volume was fixed, with a gradual rise in initial H+ concentration, the solubility of Cu(AsO2)2 increased. Thus, the As(V) to As(III) conversion percentage increased.
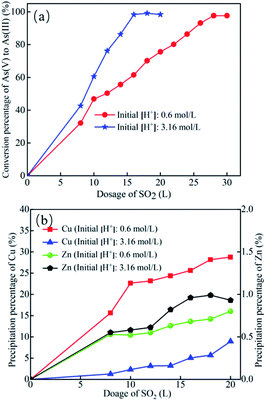 |
| Fig. 3 Effect of SO2 injection on (a) As(V) to As(III) conversion percentage and (b) the precipitation percentages of Cu and Zn (Temperature: 40 °C; SO2 input speed: 50 mL min−1). | |
With the injection of SO2, the final concentration of H+ in the liquor increased naturally (eqn (3)), which led to a rise in the solubility product of Cu(AsO2)2 and CuAs3 and a gradual decrease in Cu2+ precipitation percentage. When SO2 injection reached a certain volume, the final [H+] and solubility of Cu(AsO2)2 and Cu3As increased. Therefore, the Cu precipitation percentage decreased. Since Zn ions would not bind with Cu and As ions to form precipitate, SO2 injection had no effect on the precipitation of Zn(II) ion. Thus, Zn ions were precipitated via physical entrainment of a small amount of Zn ions into the As2O3, Cu(AsO2)2, and Cu3As precipitates.
As shown in Fig. 3a and b, when the initial concentration of H+ was 0.6 mol L−1 and SO2 injection volume was 28 L, the conversion rate of As(III) reached 97.62% while the precipitation percentage of Cu ion was higher than 25%. This result suggests that the Cu(II) ions in the leaching liquor suffered a considerable loss. When H+ concentration was 3.16 mol L−1 and SO2 input was 16 L, the conversion percentage of As(III) was 98.32%, while the precipitation percentages of Cu and Zn were 5.06% and 0.96%, respectively. Considering the cost, As2O3 quality, and loss of Cu and Zn ions, the optimal SO2 input for As(III) conversion was 16 L/14 g (1.14 L g−1 As(V)).
Effect of H+ concentration. As shown in Fig. 4a, H+ concentration had a significant impact on the conversion of As(V) to As(III). When H+ concentration was 0.6 mol L−1, the conversion percentage was only 65.13%, while the precipitation percentage of Cu ions reached 30.61%. This indicates that the sole addition of SO2 was not enough to decrease the redox potential of the liquor for As(V) reduction. Moreover, under such low [H+], As(III) species easily co-precipitated with Cu2+ to form Cu(AsO2)2, as evidenced by the XRD result of the Cu–As co-precipitation in Fig. 4b. So, increasing the H+ concentration is advantageous for avoiding the precipitation of Cu(AsO2)2. When H+ concentration was 3.16 mol L−1, the conversion rate of As(III) increased to 98.32%, while the precipitation percentage of Cu ion dropped to 5.06%. When H+ concentration increased to 3.95 mol L−1, the precipitation percentage of Cu ion continuously decreased to 2.77%, while that of As tended to reach an equilibrium. In comparison, the precipitation percentage of Zn was negligible, which was mainly attributed to the entrainment of precipitates. Thus, the optimal concentration of H+ was 3.95 mol L−1.
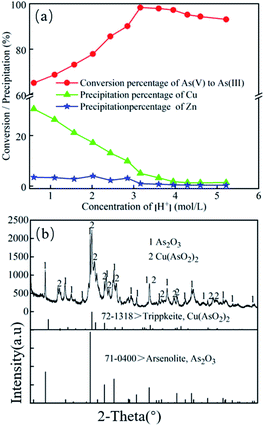 |
| Fig. 4 (a) Effect of H+ concentration on the conversion percentage of As(V) to As(III) and the precipitation percentage of Cu and Zn. (b) XRD result of the precipitate. Experimental condition: temperature 40 °C, SO2 input 16 L, SO2 input speed 50 mL min−1. | |
Effect of temperature. As shown in Fig. 5, the conversion percentage of As(V) to As(III) increased from 92% to 98.99% when the temperature increased from 15 °C to 45 °C. At this stage, the increase of temperature can promote the reduction of As(V) to As(III). However, it is not conducive to the dissolution of SO2 at high temperatures.40 Therefore, further increasing the temperature from 45 °C to 60 °C resulted in a decrease in the conversion percentage of As(V) to As(III) due to the decrease of SO2 solubility. In comparison, the temperature had a slight effect on the precipitation of Cu and Zn ions in the leaching liquor in the range of 15–65 °C; thus, the precipitation percentage changed slightly. These results suggested that the optimum temperature of As(V) to As(III) conversion was 45 °C.
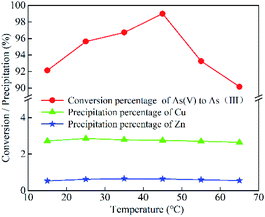 |
| Fig. 5 Effect of temperature on the conversion of As(V) to As(III) and Cu/Zn precipitation (the initial [H]: 3.95 mol L; SO2 input: 16 L; SO2 input speed: 50 mL min−1). | |
Under the optimal condition (3.95 mol L−1 [H+], temperature of 45 °C, and SO2 input of 1.14 L g−1 As(V)), the conversion efficiency of As(V) to As(III) can reach up about 98.99%, while the precipitation of Cu and Zn were kept below 2.77% and 0.64%, respectively. Therefore, the losses of Cu and Zn were well controlled, which laid the foundation for the follow up recovery of Cu and Zn.
Factors affecting As2O3 crystallization
As the concentration of sulfuric acid and temperature may affect the solubility of As2O3 crystallization, their effects on the As2O3 crystallization percentage were further investigated.
As shown in Fig. 6a, when solution temperature decreased from 65 °C to 5 °C, the crystallization (recovery) percentage of As increased significantly. The crystallization of As2O3 is an exothermic process, and the degree of supersaturation is the main driver of crystallization.3 When sulfuric acid concentration is determined, the solubility of As2O3 decreases when lowering the temperature, which is beneficial for As2O3 crystallization. When temperature was fixed, the recovery percentage of As2O3 increased with the dosage of sulfuric acid increasing from 5 to 20 mL/200 mL, and then displayed a gradual decrease with further increase in sulfuric acid concentration. Generally, the solubility of As2O3 decreases with the increasing acidity, but excess [H+] may result in reverse dissolution of As2O3.41 Therefore, the recovery percentage of As2O3 showed an initial increase and then gradually decreased with elevated sulfuric acid dosage.
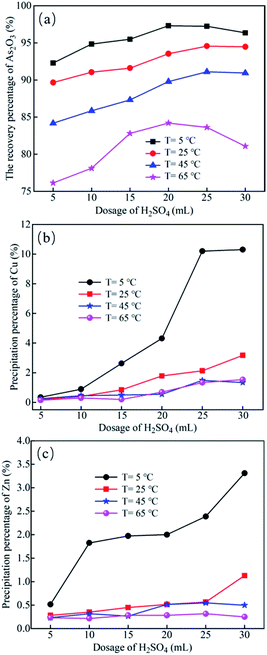 |
| Fig. 6 Effects of sulfuric acid dosage on the recovery of As2O3 (a) and the precipitation of Cu (b) and Zn (c). Volume of the leaching liquor: 200 mL. | |
The impacts of H2SO4 concentration and temperature on Cu and Zn precipitation were also studied for comparison. As shown in Fig. 6b and c, as the dosage of sulfuric acid increased at a certain temperature, the precipitation percentage of CuSO4 and ZnSO4 increased slightly. As the temperature decreased at a certain dosage of sulfuric acid, the precipitation percentage of Cu and Zn ions gradually increased.
In combination with the results in Fig. 6b and c, the optimum dosage of sulfuric acid for As2O3 crystallization was 20 mL/200 mL (0.1 L L−1) leaching liquor, while the suitable temperature was 5 °C.
Under the optimal condition, i.e., temperature of 5 °C and sulfuric acid dosage 0.1 L L−1 leaching liquor, most arsenic were crystallized in the form of As2O3 from the liquor with an recovery efficiency of 96.72%, while the losses of Cu and Zn in the system were only 0.83% and 0.13%, respectively. Conventional evaporation crystallization process inevitably results in co-precipitation of copper and zinc with arsenic under such high concentrations.40 Through precisely controlling the sulfuric acid concentration and temperature, the co-precipitation of copper and zinc can be avoided. Therefore, high purity As2O3 crystals can be obtained for arsenic recovery through this approach, and the As-removed liquor can be further processed to recover Cu and Zn resources.
Characterization of leaching residues
The crystallization composition is listed in Table 3. The XRD pattern is presented in Fig. 7a, while SEM images are presented in Fig. 7b and c. From Table 3 and Fig. 7, the constituents of precipitates were Cu, Zn, and S elements apart from the As2O3 phase, among which the content of As2O3 was 96.72%. The particle size of As2O3 precipitates was about 100 nm. The as-crystallized As2O3 can be used as the raw material for the extraction of arsenic metal. The solution after As2O3 crystallization and filtration contained some valuable elements, including Cu and Zn. The constituent analysis result of the solution is presented in Table 4. The As-removed liquor can be used for the subsequent recovery of Cu and Zn ions.
Table 3 The main component analysis of As2O3 crystal products (w/w, %)
Elements |
As |
Cu |
Zn |
S |
Content |
73.94 |
0.83 |
0.13 |
0.92 |
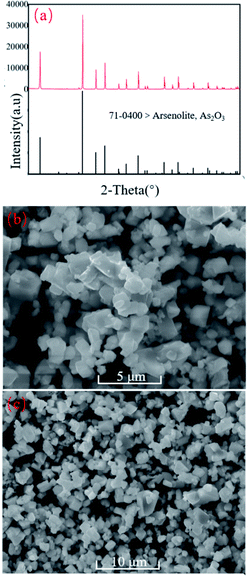 |
| Fig. 7 XRD (a) and SEM images (b and c) of As2O3 crystal products. Experimental condition: temperature 5 °C and sulfuric acid dosage 0.1 L L−1 leaching liquor. | |
Table 4 The elemental analysis of Cu–Zn-containing solution (mol L−1)
Elements |
As |
Cu |
Zn |
[H+] |
Content |
0.034 |
0.305 |
0.926 |
7.05 |
Conclusions
In this work, a reduction-cooling crystallization approach was proposed for the separation and recovery of arsenic from As, Cu, and Zn rich leaching liquor. In the reduction step, 98.99% of As(V) was successfully converted to As(III), while the precipitation of Cu and Zn were kept low (2.77% and 0.64%) under the condition of 3.95 mol L−1 [H+], temperature of 45 °C, and SO2 input of 1.14 L g−1 As(V). In the cooling crystallization step, As(III) was separated and recovered in the form of As2O3 from the leaching liquor, and the highest recovery efficiency (96.53%) can be obtained under the optimal condition: temperature of 5 °C and sulfuric acid dosage 0.1 L L−1 leaching liquor. In the whole process, only sulfuric acid and SO2 were used without introducing any impurities, and most Cu and Zn were retained in the leaching liquor, which simplified the subsequent recovery of valuable metals (Cu and Zn). This work may offer a new insight in the separation and recovery of the valuable arsenic elements from As, Cu, and Zn rich leaching liquor, and provide a prerequisite for the recovery of Cu and Zn in the subsequent process.
Author contributions
Erjun Zhang: conceptualization, data curation, validation, writing – review & editing, Kanggen Zhou: conceptualization, writing – original draft, supervision, Xuekai Zhang: investigation, data curation, Changhong Peng: supervision, resources, methodology, Wei Chen: conceptualization, writing – review & editing, funding acquisition, Dewen He: supervision, resources.
Conflicts of interest
The authors declare that they have no known competing financial interests or personal relationships that could have appeared to influence the work reported in this paper.
Acknowledgements
This work was financially supported by the Fundamental Research Funds for the Central Universities of Central South University.
References
- B. Mandal, Talanta, 2002, 58, 201–235 CrossRef CAS PubMed.
- P. Ramesh Babu, R. Vijay, S. Brammaiah, G. Naga Raju and D. Krishna Rao, Mater. Today: Proc., 2018, 5, 26356–26364 CAS.
- H. Long, Y. Zheng, Y. Peng, G. Jin, W. Deng, S. Zhang and H. He, Miner. Eng., 2020, 153, 106379 CrossRef CAS.
- N. Priyadarshni, P. Nath, Nagahanumaiah and N. Chanda, ACS Sustainable Chem. Eng., 2018, 6, 6264–6272 CrossRef CAS.
- Y. C. K. F. J. N. Magori, Sep. Sci. Technol., 2020 DOI:10.1080/01496395.2020.1837877.
- J. Guo, S. Luo, Z. Liu and T. Luo, J. Chem. Eng. Data, 2020, 65, 2938–2946 CrossRef CAS.
- A. Ghosh, S. Kanrar, D. Nandi, P. Sasikumar, K. Biswas and U. Chand Ghosh, J. Chem. Eng. Data, 2019, 65, 885–895 CrossRef.
- L. Hao, M. Liu, N. Wang and G. Li, RSC Adv., 2018, 8, 33956–39545 Search PubMed.
- X. Qi, Y. Li, L. Wei, F. Hao, X. Zhu, Y. Wei, K. Li and H. Wang, RSC Adv., 2019, 1, 29–42 Search PubMed.
- A. Jarošíková, V. Ettler, M. Mihaljevič, P. Drahota, A. Culka and M. Racek, J. Environ. Manage., 2018, 209, 71–80 CrossRef PubMed.
- A. Wikedzi and S. A. Awe, Journal of Sustainable Metallurgy, 2017, 3, 362–374 CrossRef.
- E. Prasetyo and C. Anderson, Journal of Sustainable Metallurgy, 2020, 6, 612–621 CrossRef.
- S. Y. Tshipeng, A. TshamalaKaniki and M. Kime, Journal of Sustainable Metallurgy, 2017, 3, 823–828 CrossRef.
- X. Li, D. Liu, J. Wang and J. Song, Sep. Sci. Technol., 2020, 55, 88–97 CrossRef CAS.
- G. A. Flores, C. Risopatron and J. Pease, JOM, 2020, 72, 3447–3461 CrossRef CAS PubMed.
- J. A. Tamayo, A. M. Meléndez and J. A. Calderón, Hydrometallurgy, 2019, 184, 9–21 CrossRef CAS.
- W. Liu, X. Fu, T. Yang, D. Zhang and L. Chen, Trans. Nonferrous Met. Soc. China, 2018, 28, 1854–1861 CrossRef CAS.
- Y. Wang, X. Fang, P. Deng, Z. Rong, X. Tang and S. Cao, J. Mater. Res. Technol., 2020, 9, 3208–3218 CrossRef CAS.
- D. K. Louie, Handbook of sulphuric acid manufacturing, Ontario, Canada, DKL Engineering, 2nd edn, 2005 Search PubMed.
- M. AG, A method for processing copper smelting materials and the like containing high percentages of arsenic and/or antimony, Germany pat., DE4122895C1, 1992 Search PubMed.
- J. A. Barragan, C. Ponce De León, J. R. Alemán Castro, A. Peregrina-Lucano, F. Gómez-Zamudio and E. R. Larios-Durán, ACS Omega, 2020, 5, 12355–12363 CrossRef CAS PubMed.
- B. Hu, T. Yang, W. Liu, D. Zhang and L. Chen, Trans. Nonferrous Met. Soc. China, 2019, 29, 2411–2421 CrossRef CAS.
- A. M. Nazari, R. Radzinski and A. Ghahreman, Hydrometallurgy, 2017, 174, 258–281 CrossRef CAS.
- J. Lei, B. Peng, Y. Liang, X. Min, L. Chai, Y. Ke and Y. You, Hydrometallurgy, 2018, 177, 123–131 CrossRef CAS.
- D. Halder, J. Lin, J. Essilfie-Dughan, S. Das, J. Robertson and M. J. Hendry, Appl. Geochem., 2018, 98, 367–376 CrossRef CAS.
- S. H. Ahoranta, M. E. Kokko, S. Papirio, B. Özkaya and J. A. Puhakka, J. Hazard. Mater., 2016, 306, 124–132 CrossRef CAS PubMed.
- A. Ahmad, S. Rutten, L. de Waal, P. Vollaard, C. van Genuchten, H. Bruning, E. Cornelissen and A. van der Wal, Sep. Purif. Technol., 2020, 241, 116644 CrossRef CAS.
- T. Nur, P. Loganathan, M. B. Ahmed, M. A. H. Johir, T. V. Nguyen and S. Vigneswaran, Chemosphere, 2019, 226, 431–438 CrossRef CAS PubMed.
- T. K. Das, T. S. Sakthivel, A. Jeyaranjan, S. Seal and A. N. Bezbaruah, Chemosphere, 2020, 253, 126702 CrossRef CAS PubMed.
- N. Jantunen, S. Virolainen, P. Latostenmaa, J. Salminen, M. Haapalainen and T. Sainio, Hydrometallurgy, 2019, 187, 101–112 CrossRef CAS.
- T. Luo, Z. Huang, X. Li and Y. Zhang, Sci. Total Environ., 2020, 727, 138630 CrossRef CAS PubMed.
- V. Kaushik, Y. Duan, B. Jung, B. Batchelor and A. Abdel-Wahab, Journal of Water Process Engineering, 2018, 23, 314–319 CrossRef.
- Y. Chen, T. Liao, G. Li, B. Chen and X. Shi, Miner. Eng., 2012, 39, 23–28 CrossRef CAS.
- A. Wang, K. Zhou, X. Zhang, D. Zhou, C. Peng and W. Chen, Chemosphere, 2020, 238, 124675 CrossRef CAS PubMed.
- H. Long, X. Huang, Y. Zheng, Y. Peng and H. He, Process Saf. Environ. Prot., 2020, 139, 201–209 CrossRef CAS.
- Q. Tian, G. Li, Y. Xin, X. Lv, X. Lv, W. Yu and K. Yan, Hydrometallurgy, 2020, 195, 105366 CrossRef CAS.
- E. Zhang, K. Zhou, W. Chen, X. Zhang and C. Peng, Chin. J. Chem. Eng., 2021, 33, 125–131 CrossRef.
- Y. Zheng, Y. Peng, L. Ke and W. Chen, Trans. Nonferrous Met. Soc. China, 2013, 23, 2166–2173 CrossRef CAS.
- H. G. Li, Metallurgical principle, Science press, Beijing, China, 12th edn, 2005 Search PubMed.
- W. Zhou, Y. Peng, Y. Zheng, Y. Ma and T. Cui, Trans. Nonferrous Met. Soc. China, 2011, 21, 2772–2777 CrossRef CAS.
- F. Dalewski, JOM, 1999, 51(9), 24–26 CrossRef CAS.
|
This journal is © The Royal Society of Chemistry 2021 |
Click here to see how this site uses Cookies. View our privacy policy here.