DOI:
10.1039/D1RA05307H
(Paper)
RSC Adv., 2021,
11, 28542-28549
Raw natural rubber latex-based bio-adhesive for the production of particleboard: formulation and optimization of process parameters
Received
10th July 2021
, Accepted 14th August 2021
First published on 24th August 2021
Abstract
In this study, bio-adhesives from natural rubber latex (NRL) were combined with starch and formic acid to fabricate jute stick-based particleboards (JSPs). Different blends of NRL, starch, and formic acid, i.e., 6
:
1
:
1, 2
:
1
:
1, and 2
:
3
:
3, were used to produce particleboards using a pressing temperature of 180 °C and applied pressure of 5 MPa using a 5 min pressing time. The particleboards were tested for physical, mechanical, and thermal properties according to ANSI standards. Based on initial screening, the best formula (NRL/starch/formic acid of 2
:
3
:
3) was used to optimize the temperature and pressing time for the highest board performance. The highest density, tensile strength, modulus of elasticity, and modulus of rupture were 830 g cm−3, 10.51, 2380, and 20.05 N mm−2, respectively. Thermo-gravimetric analysis indicated that thermal decomposition of samples primarily occurred in a temperature range of 265 to 399 °C, indicating good thermal performance. The measured physical and mechanical properties of the produced JSPs fulfilled the production standards. However, fulfilling the water absorption and thickness swelling criteria was a challenge. The results indicate that NRL is a promising alternative binder when blended with starch and formic acid.
1. Introduction
In recent decades, depleted resources and environmental concerns have stimulated research on renewable and recyclable components in particleboard production.1 In the development of biodegradable composites, such as fiberboards and particleboards, adhesives play a significant role in the sustainability of building and structural materials.2 The global wood-adhesive industry is supported by petrochemical-derived resins due to their superior ability to yield high performance.3,4 These formaldehyde-based resins are strongly associated with emissions of carcinogenic gases or the release of volatile organic compounds (e.g., formaldehyde) and/or other toxic compounds.2,5 Formaldehyde-bearing adhesives are linked to health and environmental risks.6,7 Therefore, attempts have been made to find novel adhesive formulae for wood from renewable resources.8,9 While many researchers are working on formaldehyde-free bio-adhesives, formaldehyde has not yet been completely phased out.7 Bio-adhesives are derived from biomass resources like starch,6,10–12 protein,13,14 lignin,15 soy flour,16 and tannin17 but the properties of these adhesives are not yet suitable for replacing synthetic-based adhesives. Among natural bio-based resins, the use of natural rubber latex (NRL) as a wood adhesive has been reported many years ago and several studies reference this raw material18,19 but it has not been studied in detail.
NRL extracted from Hevea brasiliensis Müll. Arg., is one of the most promising natural adhesives which exhibit good moisture and mold resistance with no toxicity.20,21 NRL is a milky brown fluid that contains tiny particles of rubber.22 It consists of two main parts; a hydrocarbon (1,4-cis-polyisoprene) and a mixture of other non-rubber components, mainly carbohydrates, proteins, and lipids in an aqueous serum phase.23 Its excellent flexibility, high tack and tack retention features, moderate moisture resistance, and improved strength after vulcanization24 are among the beneficial properties of NRL and aid its use in green adhesive formulae.25 Latex has been widely investigated and used to synthesize wood adhesives, especially for non-polar adherents after modification to increase its performance on polar surfaces.26 Modification of NRL to increase its bonding strength with wood has also been studied.20,21,27 However, detailed investigations on its physicochemical properties, bonding strength with wood, chemical extraction and modification, have not been performed. Its potential for wood-based industries has not yet been explored although there is a great interest in developing more sustainable adhesives.
The purpose of this study was to evaluate NRL incorporated with starch and formic acid to test its effectiveness as a bio-adhesive. The most promising adhesive formula was to be identified and used to fabricate particle board samples whose physical and mechanical properties were analysed as a function of processing parameters, i.e., time and temperature.
2. Experimental section
2.1 Materials
Crude natural rubber latex and jute stick were sourced from the rubber garden, Bangladesh Forest Industries Development Corporation (BFIDC), Chittagong, and the local market, Khulna, Bangladesh, respectively. Laboratory grade corn starch powder and reagent grade (≥95% purity) formic acid (H2CO2) and ammonium (NH4) were received from Carolina Biological Supply Company, New York City, USA, and Merck KGA, Darmstadt, Germany, respectively.
2.2 Methods
2.2.1 Preparation of raw materials. Ammonium (NH4) with a concentration of 0.8% w/w basis was added to the crude NRL to prevent coagulation. The jute sticks were air-dried at 35 °C and RH 60% for 24 h and milled, and screened using a 2 mm screen to obtain a particle size less than 2 mm. This powder was then dried in an oven (Vacuum Oven, OV-11, Korea) at 103 ± 2 °C for 24 h to a moisture content of 4% (dry basis). The oven-dried jute stick powder was stored in an airtight zip-lock bag.
2.2.2 Screening of different NRL-based bio-adhesive formula. Three different formula for NRL-based bio-adhesives were tested (Table 1). The NRL was uniformly mixed with jute stick powder, starch and formic acid using a rotary drum. Starch was added to the mixture afterward because the dispersion of starch in NRL was problematic if added earlier. Formic acid was then added to the mixture. Mats with dimensions of 310 × 310 × 7 mm were formed using a steel frame. The mats were pressed using a single daylight hot press at a temperature of 180 °C and a pressure of 5 MPa for 5 min. Three or more jute stick particleboards (JSPs) were produced with each type of adhesive formula.
Table 1 NRL-based bio-adhesive formulae used in making the three types of particleboard
Particle board |
NRL-based bio-adhesive components (% volume) |
Natural rubber latex |
Corn starch |
Formic acid (H2CO2) |
Type A |
75 |
12.5 |
12.5 |
Type B |
50 |
25.0 |
25.0 |
Type C |
25 |
37.5 |
37.5 |
2.2.3 Analysis of particleboard properties. The produced JSPs were trimmed and conditioned at 25 ± 2 °C with a relative humidity of 60 ± 2% for about three days. JSP moisture content was determined by the oven dry method. The modulus of elasticity (MOE), modulus of rupture (MOR), and tensile strength were determined according to standard methods28 using the static three-point bending and a universal testing machine (UTM) (SHIMADZU AG-50KNXplus, Japan). The particleboard density, water absorption (WA), and thickness swelling (TS) were assessed after 2 and 24 h immersion in water at room temperature.29 Differential scanning calorimetry (DSC) was used to determine the glass transition temperature (Tg). A temperature-modulated DSC (LABSys evo, Setaram Instrumentation, France) was used to measure the heat flow and reverse heat flow under nitrogen atmosphere over a temperature range of 25 to 600 °C with a heating rate of 10 °C min−1 according to ASTM. To determine the activation energy in the physical and chemical pathways, data were obtained through several kinetic non-isothermal curing experiments performed under N2 atmosphere using DSC at constant rates of heating, i.e., 5, 10, and 15 °C min−1 (constant during each test, different between tests). The activation energy was calculated following the Kissenger pathway discussed in Islam et al.12 At least five samples were tested for each mechanical property.
2.2.4 Optimization of the particleboard manufacturing process parameters.
2.2.4.1 Selection of best particleboard formula. Based on the physical, mechanical, and thermal properties of the JSPs in the NRL-based bio-adhesive formula screening experiments, type C was selected for further optimization of process temperatures and pressing times.
2.2.4.2 Fabrication of particleboards. The optimization of process parameters was performed by varying the press time and temperature according to Table 2. A total of 125 different types of particleboards, i.e., five replications for each type, were manufactured and conditioned according to the aforementioned method.
Table 2 Process parameters for optimization of the process conditions with type C bio-adhesive
Time (min) |
Temperature (°C) |
4 |
140 |
150 |
160 |
170 |
180 |
6 |
140 |
150 |
160 |
170 |
180 |
8 |
140 |
150 |
160 |
170 |
180 |
10 |
140 |
150 |
160 |
170 |
180 |
12 |
140 |
150 |
160 |
170 |
180 |
2.2.4.3 Scanning electron microscope (SEM) analysis of the particleboards. The extent of the intercalation and exfoliation of NRL-based adhesive into the matrix of the particleboard was observed with a field emission gun scanning electron microscopy (FEG-SEM) (EVO LS15, Zeiss, Germany). The fourth generation variable pressure secondary electron detector (VPSE G4) with a voltage of 17.00 kV and magnification of 69× was used for imaging. The voltage, magnification, and sensor were selected based on trial and error.
2.3 Statistical analysis
Data analysis was performed using statistical software (RStudio version 1.1.463, RStudio Team, 2008).30 The ‘psych’ package was used to analyze descriptive statistics (means, SD, SEs, etc.).31 Normality and homogeneity were tested with the ‘car’ package.32 The appropriate transformation was applied to yield normal distributions for properties. An analysis of variance (ANOVA) model and least significant difference (LSD) was used at a 5% significance level. All figures were made with the ‘ggplot2’ package (version 3.2.1).
3. Results and discussion
3.1 Screening of bio-adhesive formula
3.1.1 Physical properties. The density of type A, B, and C JSPs were 815, 857, and 861 kg m−3, respectively (Fig. 1A). Type B and C showed almost the highest density mentioned in JIS 5908 for a standard particleboard ranging from 0.4 to 0.9 g cm−3. The higher density of B and C may be due to the presence of accessible OH (hydroxyl) groups in the starch.27,33,34 Additionally, formic acid acts as a coagulant35 which helps the NRL to form into a homogenous solid. The protein molecules present in the NRL and OH groups are interlinked and, enhanced particle bonding in the matrix. Therefore, both starch and formic acid enhance particle–particle bonding. For comparison, the density of particleboards made with modified wheat and palm oil starch was reported to be 610 kg m−3.36
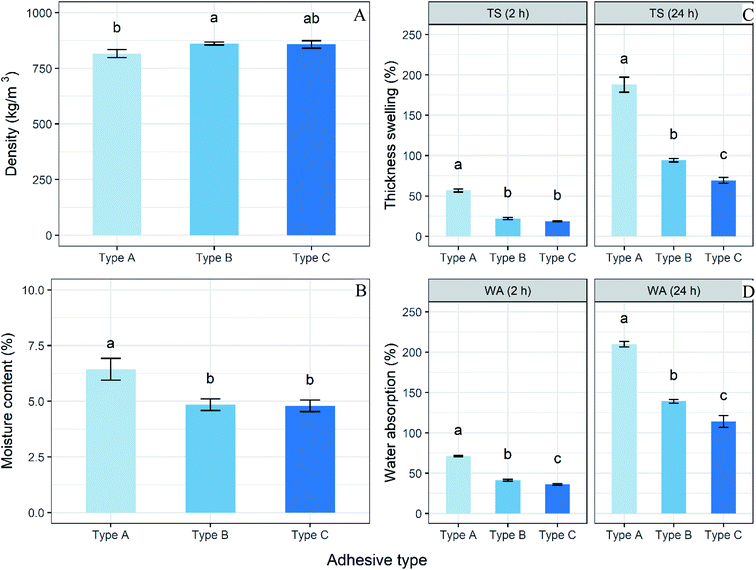 |
| Fig. 1 Density (A), moisture content (B), thickness swelling (C) and water absorption (D) of jute stick-based particleboards with different NRL-based bio-adhesive formulae (see Table 1). Analyses of variance (ANOVAs) were conducted to determine significant differences (p < 0.05); when ANOVAs were significant, the means for each value were compared with Least Significant Difference (LSD) post hoc test; means that share a lowercase letter are not statistically different, while different letters denote for statistical differences at least 95% confidence. | |
The MC of the JSPs ranged from 4.8 to 6.4% and the board density increased with decreasing MC (Fig. 1B) as the high density boards generally showed lower MC. When the bonding of interparticles in the matrix of particleboards is strong then the board density increased and, resulting in retarded water penetration. Agnantopoulou et al.37 found that the presence of starch-based materials in wood composites led to lower moisture content. Type C JSPs had the lowest WA, 36 and 114% (Fig. 1D), and the lowest TS, 18 and 69% (Fig. 1C), respectively, after 2 and 24 h water immersion. Swelling decreased with increasing NRL concentration and proportion of starch (Table 1). Previous studies have shown that the addition of starch-based materials reduces water uptake capacity in composites.37 Starch molecules and OH groups are interlinked and this accelerates particle bonding, and retards water penetration in particleboard matrix.38 This is responsible for lower MC, WA, and TS of particleboards made with an adhesive containing a lower amount of latex and a higher amount of starch. Akbari et al.27 observed a similar trend in their study. When fabricating epichlorohydrin-modified oil palm starch-based particleboards (600 kg m−3), Sulaiman et al.39 reported WA of 114 and 123%, and TS of 43% and 54% for immersion times of 2 and 24 h, respectively. However, chemical modification of NRL-based adhesives may be a viable option to improve the hydrophobicity.40
3.1.2 Mechanical properties. The observed mechanical properties of the JSPs are shown in Fig. 2. Type C particleboards had the highest MOE, MOR, and tensile strength values of 2866, 15.6, and 5.01 N mm−2, respectively. Mechanical properties were enhanced with increasing amounts of starch in the adhesive (Fig. 2). The affinity of starch to form strong adhesion is thought to be the reason for this effect20,41 as starch possesses good adhesion and film formation properties.42 The MOR of boards also tends to increase with the starch content in the NRL latex.27 This improves adhesion between the fiber matrix and the NRL.21 Moreover, as starch concentration increases, hydrogen bonding between interparticle is enhanced which increases the mechanical strength of the boards. Additionally, the dried lignocellulosic particles reduce the weaker hydrogen-bonding between water molecules. This is the primary mechanism which explains why the higher amount of starch along with latex causes higher values of MOE, MOR, and tensile strength of particleboards. All of the fabricated particleboards fulfilled the production standard requirements.28
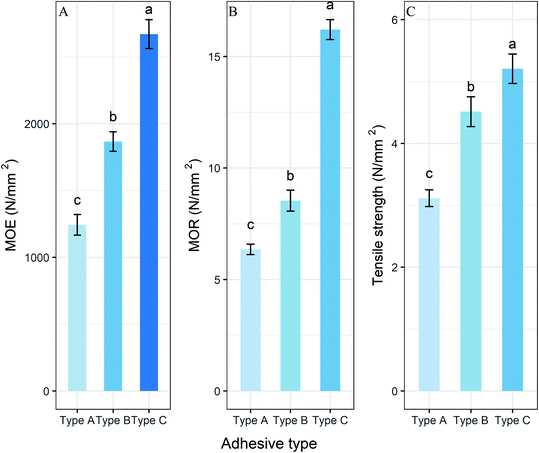 |
| Fig. 2 Modulus of elasticity (MOE) (A), modulus of rupture (MOR) (B) and tensile strength (C) of jute stick-based particleboards (JSPs) with different NRL-based bio-adhesive formulae (see Table 1). | |
3.1.3 Thermal properties. The TGA analysis shows that NRL based JSPs are likely to retain their properties even at relatively high temperatures. Fig. 3A and B show the thermogravimetric analysis (TGA) and derivative thermogravimetry (DTG) performance of produced particleboards. Particleboards of type A showed the lowest overall mass loss, whereas, type C showed the highest mass loss (Table 3). The observed mass loss can be divided into three stages. The first stage began before 100 °C when moisture was vaporized. In the second stage (100 to 250 °C), the mass did not change.43 Type A JSPs entered the third stage of significant mass loss at 250 °C, whereas this stage did not start until 300 °C for the type B and C. The blending of jute stick particles with NRL and starch appeared to cause an upward shift in the degradation temperature, i.e., from 300 to 350 °C. Similar results have been observed by other researchers.27,44
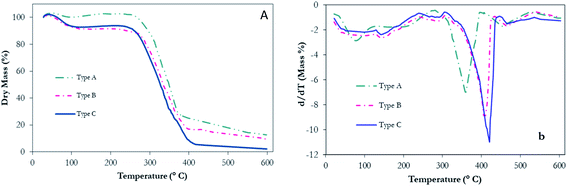 |
| Fig. 3 Thermogravimetric analysis (TGA) (A) and derivative thermogravimetry (DTG) (B) performance of the jute stick particleboards (JSPs) produced from three types (Table 1) of NRL-based bio-adhesive formula. Thermoanalysis was carried out under nitrogen atmosphere using a heating rate of 10 °C min−1 according to ASTM E1582.45 | |
Table 3 Peak decomposition temperature, activation energy and energy transformation rate of JSPs made from NRL-based bio-adhesive obtained using thermogravimetric analysisa
Adhesive |
Tp (°C) |
−(Ea/RT) |
Ea (KJ mol−1) |
Decomposition temperature |
Mass loss (%) |
R2 |
5 |
10 |
15 |
T0 (°C) |
Tp (°C) |
Te (°C) |
T0-temperature at the onset of decomposition; Tp-the peak decomposition temperature and Te-temperature at the endpoint of decomposition. |
Type A |
356.7 |
369.0 |
379.1 |
5926.7 |
49 |
320.92 |
351.79 |
366.30 |
29.3 |
0.9918 |
Type B |
386.9 |
398.0 |
410.9 |
6470.3 |
54 |
369.0 |
398.0 |
414.6 |
32.6 |
0.9617 |
Type C |
398.4 |
414.6 |
421.4 |
7238.5 |
60 |
390.76 |
419.39 |
431.74 |
37.3 |
0.9889 |
The amount of NRL in the adhesive significantly increased the rate of degradation of the sample. Sowińska et al.46 stated that the modified JSPs along with the addition of variety chemicals showed better results rather than untreated and/or NRI treated JSPs. Hossain et al.47 also observed less degradation when using okra fiber having the same chemical treatment in composite materials.
The activation energy (Ea) was consistent with the increasing mass-loss rate of different types of adhesives, and thus, the energy transformation rate (Ea/RT) had a stronger correlation with the mass loss (char residue formation) (Table 3). As a result, the higher thermal stability of composites is primarily determined by the amount and concentration of activated chemicals rather than the parent materials. Therefore, in terms of weight loss and the rate of decomposition, TGA revealed that the thermal stability of JSPs (type C) produced from NRL-based bio-adhesive was improved by the addition of higher chemical concentrations of formic acid and starch.
3.2 Optimization of process settings for type C particleboard
3.2.1 Type C physical properties. The observed physical properties of the type C JSPs are shown in Fig. 4. Board density ranged from 546 to 830 kg m−3. The highest density was obtained at 180 °C for 10 min and the lowest density at 140 °C for 4 min setting (Fig. 4D). Umemura et al.4 observed a similar trend for bio-adhesive bonded particleboard prepared at higher temperatures.
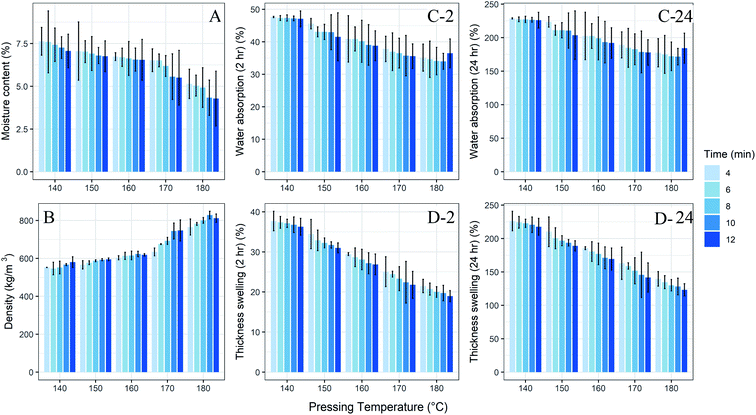 |
| Fig. 4 Moisture content (A), density (B), water absorption after two (C-2) and twenty-four (C-24) hour, and thickness swelling after two (D-2) and twenty-four (D-24) hour of type C particleboards. | |
The lowest WA at 2 and 24 h of immersion: 33% and 171%, respectively, were obtained for the 180 °C and 10 min setting (Fig. 4C), but the lowest MC and TS: 4.29 ± 2.77 and 123.22 ± 15.74%, respectively at 180 °C and 12 min (Fig. 4A and D). Umemura et al.4 observed that the TS was lower for bio-adhesive bonded particleboard prepared at higher temperature. It has previously been shown that a higher temperature increases the compactness in the matrix of particleboards, increasing the density and decreasing the MC, WA, and TS.48 The range of MC and densities of the JSPs fulfilled the ANSI standard.29 However, WA (171–228%) and TS (123–226%) for all the processed JSPs exceeded the limit of the ANSI standard29 and the measured values were higher than previously reported.3,49
3.2.2 Mechanical properties. All of the particleboards fabricated with NRL-based bio-adhesives fulfilled the ANSI standard for MOE, MOR, and TS. The highest MOE: 2380.3 ± 135 N mm−2, MOR: 20.05 ± 2 N mm−2, and tensile strength: 10.5 ± 0.21, were obtained at 180 °C and 8 min setting (Fig. 5A–C). This might be the increment of interfacial adhesion properties increasing the bonding ability in the matrix of particleboards and thus, enhances the strength properties of JSPs.48 Similar trends for bio-adhesive bonded particleboards have previously been observed.4,50,51 The crosslinking network of the NRL adhesives provided a better elasticity that is responsible for better tensile strength for the JSPs made at 180 °C and 8 min.
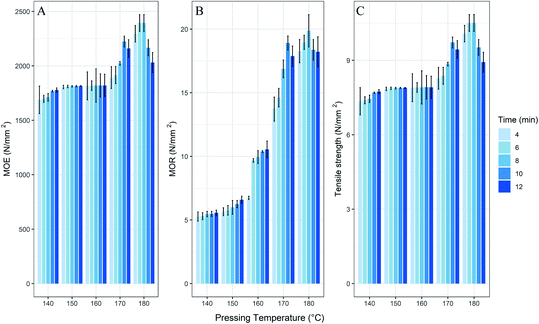 |
| Fig. 5 Modulus of elasticity (A), modulus of rupture (B) and tensile strength (C) of type C particleboards. | |
The tensile strength was also influenced by the filler fraction and interfacial adhesion between particles and the adhesive. Therefore, at a certain limit, a longer pressing time resulted in lower MOE and MOR values (180 °C and 10 and 12 min) (Fig. 5A and B). However, the best mechanical properties obtained with pressing time 8 min and temperature 180 °C are much preferred in the industrial sector.
3.2.3 Scanning electron microscopy. SEM was used to qualitatively observe the adhesion of the fabricated JSPs. Fig. 6 reveals the texture of the cross section of JSPs with type C adhesive at 180 °C for 8 min. The surface of this JSP shows a certain smoothness with no apparent lumps of adhesive. This indicates that the latex was distributed homogeneously and provided interfacial interactions between filler and matrix. As a result, this homogeneous distribution of adhesive and compactness of the matrix can distribute the load uniformly52 and can be an indication of robust interparticle bonding in the matrix.53
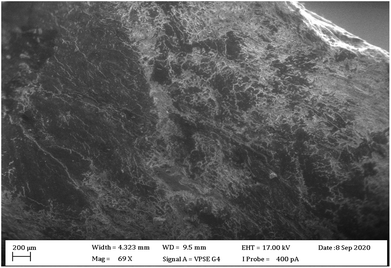 |
| Fig. 6 A SEM micrograph of the type C JSP pressing at 180 °C temperature for 8 min. | |
4. Conclusions
In this study, environmentally friendly bio-adhesives were produced from natural rubber latex (NRL), starch, and formic acid and used to fabricate jute stick particleboards (JSPs). Using different blends of these constituents, it was found that the adhesive type with the lowest NRL proportion (type C having 25% NRL, 37.5% corn starch and 37.5% formic acid) yielded JSPs with the highest strength properties. Fabrication was further optimized with this adhesive type and the most favorable pressing conditions used a pressing temperature of 180 °C and a pressing time of 8 min. Although mechanical properties were found satisfactory enough to replace urea formaldehyde (UF) based particleboards, the physical properties were not sufficient. Therefore, further studies are needed to improve the hydrophobicity of NRL.
Author contributions
Md. Nazrul Islam: conceptualization, literature review, writing – original draft, writing – review & editing, visualization; Abdullah Adib, Nabila Hasan Dana, Md Omar Faruk: data collection and analysis, writing – original draft; Atanu Kumar Das: SEM data collection and analysis, writing – review & editing, visualization, David A. Agar, Sylvia H. Larsson, Magnus Rudolfsson: SEM data collection and analysis, writing – review & editing, and Md Ashaduzzaman, Md Iftekhar Shams: writing – review & editing.
Conflicts of interest
The authors declare that they have no known competing financial interests or personal relationships that could have appeared to influence the work reported in this paper. It is here mentionable that several authors from the article author list have applied for a provisional patent (Application Number: P/BD/2018/000291) related to the research work and the final patent application is now in processing.
Acknowledgements
This research was financially supported by Bangladesh University Grants Commission (Project # ref. 6(75)/UGC/S&T/Life-27/2018/2262, date: 14/03/2019) and Khulna University Research Cell (Project # Ref.: KU/RC-04(32)/2000, date: 18/04/2019).
References
- C. R. Frihart, For. Prod. J., 2015, 65, 4–8 Search PubMed.
- F. Stoeckel, J. Konnerth and W. Gindl-Altmutter, Int. J. Adhes. Adhes., 2013, 45, 32–34 CrossRef CAS.
- A. Moubarik, A. Allal, A. Pizzi, F. Charrier and B. Charrier, Maderas: Cienc. Tecnol., 2010, 12, 189–197 CAS.
- K. Umemura, O. Sugihara and S. Kawai, J. Wood Sci., 2015, 61, 40–44 CrossRef CAS.
- H. Zhang, P. W. Liu, S. M. Musa, C. Mai and K. Zhang, ACS Sustainable Chem. Eng., 2019, 7, 10452–10459 CrossRef CAS.
- M. N. Islam, A. A. Liza, M. O. Faruk, M. A. Habib and S. Hiziroglu, Int. J. Biol. Macromol., 2020, 142, 879–888 CrossRef CAS PubMed.
- P. Navarrete, A. Pizzi, H. Pasch, K. Rode and L. Delmotte, J. Adhes. Sci. Technol., 2013, 27, 2462–2479 CrossRef CAS.
- A. K. Das, M. N. Islam, M. O. Faruk, M. Ashaduzzaman and R. Dungani, S. Afr. J. Bot., 2020, 135, 58–70 CrossRef CAS.
- N. C. Schellmann, Stud. Conserv., 2007, 52, 55–66 CrossRef.
- Y. Gu, L. Cheng, Z. Gu, Y. Hong, Z. Li and C. Li, Int. J. Biol. Macromol., 2019, 134, 247–254 CrossRef CAS.
- Z. Luo, K. Dong, M. Guo, Z. Lian, B. Zhang and W. Wei, Starch–Stärke, 2018, 70(1700211), 1–9 Search PubMed.
- M. N. Islam, M. O. Faruk, M. N. Rana, A. K. Das and A. Habib, Global Challenges, 2021, 5(2000044), 1–14 Search PubMed.
- M. N. Islam, A. K. Liza, M. L. Khatun, M. O. Faruk, A. K. Das, M. Dey and J. H. Akanda, Global Challenges, 2021,(2100002), 1–12 Search PubMed.
- P. Nordqvist, N. Nordgren, F. Khabbaz and E. Malmstrom, Ind. Crops Prod., 2013, 44, 246–252 CrossRef CAS.
- M. N. Collins, M. Nechifor, F. Tanasa, M. Zanoaga, A. McLoughlin, M. A. Strózyk, M. Culebras and C. A. Teaca, Int. J. Biol. Macromol., 2019, 131, 828–849 CrossRef CAS PubMed.
- H. Lei, G. Du, Z. Wu, X. Xi and Z. Dong, Int. J. Adhes. Adhes., 2014, 50, 199–203 CrossRef CAS.
- F. Pichelin, M. Nakatani, A. Pizzi, S. Wieland, A. Despres and S. Rigolet, For. Prod. J., 2006, 56, 31–36 CAS.
- E. Hermiati, W. Fatriasari and F. Falah, J. Ilmu dan Teknologi Kayu Tropis, 2006, 4, 33–38 Search PubMed.
- W. G. Weeraratne, M. Nadarajah, D. A. R. Eliatamby, U. P. P. Amarasinghe and N. L. Iyanage, Q. Jl. Rubb. Res. Intl. Ceylon, 1972, 49, 37–48 Search PubMed.
- J. Shey, S. H. Imam, G. M. Glenn and W. J. Orts, Ind. Crops Prod., 2006, 24, 34–40 CrossRef CAS.
- J. Thuraisingam, A. Gupta and M. Subramaniam, Aust. J. Basic Appl. Sci., 2016, 10, 101–106 CAS.
- S. Dhanania, D. Mahata, O. Prabhavale, K. Cornish, G. B. Nando and S. Chattopadhyay, Iran. Polym. J., 2018, 27, 307–318 CrossRef CAS.
- C. C. Ho, T. Kondo, N. Muramatsu and H. Ohshima, J. Colloid Interface Sci., 1996, 178, 442–445 CrossRef CAS.
- M. Nasir, A. Gupta, M. D. H. Beg, G. K. Chua and A. Kumar, Int. J. Adhes. Adhes., 2013, 44, 99–104 CrossRef CAS.
- M. I. Mugableh, in 4th ICMFE, Indonesia, 2015, p. 192 Search PubMed.
- A. Pizzi, Adhes. Age, 1977, 20, 27–29 CAS.
- S. Akbari, A. Gupta, T. A. Khan, S. S. Jamari, N. B. C. Ani and P. Poddar, J. Indian Acad. Wood Sci., 2014, 11, 109–115 CrossRef.
- American National Standards Institute, ANSI, 2016 Search PubMed.
- American National Standards Institute, ANSI A208.1, 1999 Search PubMed.
- RStudio Team, RStudio: Integrated Development for R, 2008 Search PubMed.
- W. Revelle, Psych: Procedures for Psychological, Psychometric, and Personality Research. 2017 Search PubMed.
- J. Fox and S. Weisberg, An R Companion to Applied Regression, Thousand Oaks, California, USA, 2011 Search PubMed.
- H. Onusseit, Ind. Crops Prod., 1992, 1, 141–146 CrossRef CAS.
- H. Y. Tan, Y. H. Zhang and X. L. Weng, Procedia Eng., 2011, 15, 1171–1175 CrossRef CAS.
- B. Kamm, M. Gerhardt and G. Dautzenberg, New and Future Developments in Catalysis, 2013, pp. 91–113 Search PubMed.
- K. M. Salleh, R. Hashim, O. Sulaiman, S. Hiziroglu, W. N. A. W. Nadhari, N. A. Karim, N. Jumhuri and L. Z. P. Ang, J. Adhes. Sci. Technol., 2015, 29, 319–336 CrossRef CAS.
- E. Agnantopoulou, V. Tserki, S. Marras, J. Philippou and C. Panayiotou, J. Appl. Polym. Sci., 2012, 126, E272–E280 CrossRef.
- F. Ferdosian, Z. H. Pan, G. C. Gao and B. X. Zhao, Polymers, 2017, 9(70), 1–29 Search PubMed.
- N. S. Sulaiman, R. Hashim, O. Sulaiman, N. Nasir, M. H. M. Amini and S. Hiziroglu, Int. J. Adhes. Adhes., 2018, 84, 1–8 CrossRef CAS.
- S. Hema, A. Krishnan, A. Akther, A. Suresh, S. Sambhudevan and B. Shankar, Mater. Today: Proc., 2021, 46(8), 2950–2954 CAS.
- S. Kiatkamjornwong, P. Surunchanajirasakul and P. Tasakorn, Plast., Rubber Compos., 2001, 30, 318–327 CrossRef CAS.
- A. Jonhed, C. Andersson and L. Jarnstrom, Packag. Technol. Sci., 2008, 21, 123–135 CrossRef CAS.
- Y. A. El-Shekeil, S. M. Sapuan and M. Haron, Appl. Mech. Mater., 2014, 394–399 Search PubMed.
- J. Sai Revanth, V. S. Madhav, Y. K. Sai, D. V. Krishna, K. Srividya and C. M. Sumanth, Mater. Today: Proc., 2020, 460–465 CAS.
- American Society for Testing and Materials, ASTM E1582, West Conshohocken, PA, 2017 Search PubMed.
- A. Sowińska, M. Maciejewska and A. Grajewska, Int. J. Mol. Sci., 2021, 22(3678), 1–21 Search PubMed.
- S. I. Hossain, M. Hasan, M. N. Hasan and A. Hassan, Adv. Mater. Sci. Eng., 2013, 824274, 1–6 Search PubMed.
- P. Malanit, M. C. Barbu and A. Fruhwald, J. Trop. For. Sci., 2009, 21, 361–368 Search PubMed.
- J. A. Fuwape, Bioresour. Technol., 1994, 48, 83–85 CrossRef CAS.
- A. N. Papadopoulos, G. A. Ntalos and I. Kakaras, Holz als Roh- Werkst., 2006, 64, 517–518 CrossRef CAS.
- D. H. Wang and X. Z. S. Sun, Ind. Crops Prod., 2002, 15, 43–50 CrossRef CAS.
- W. D. Callister, Ciência e Engenharia dos Materiais, São Paulo, LTC, 2002 Search PubMed.
- J. Datta and P. Parcheta, Iran. Polym. J., 2017, 26, 453–466 CrossRef CAS.
|
This journal is © The Royal Society of Chemistry 2021 |
Click here to see how this site uses Cookies. View our privacy policy here.