DOI:
10.1039/D1RA05810J
(Review Article)
RSC Adv., 2021,
11, 31884-31922
On the diatomite-based nanostructure-preserving material synthesis for energy applications
Received
30th July 2021
, Accepted 6th September 2021
First published on 28th September 2021
Abstract
The present article overviews the current state-of-the-art and future prospects for the use of diatomaceous earth (DE) in the continuously expanding sector of energy science and technology. An eco-friendly direct source of silica and the production of silicon, diatomaceous earth possesses a desirable nano- to micro-structure that offers inherent advantages for optimum performance in existing and new applications in electrochemistry, catalysis, optoelectronics, and biomedical engineering. Silica, silicon and silicon-based materials have proven useful for energy harvesting and storage applications. However, they often encounter setbacks to their commercialization due to the limited capability for the production of materials possessing fascinating microstructures to deliver optimum performance. Despite many current research trends focusing on the means to create the required nano- to micro-structures, the high cost and complex, potentially environmentally harmful chemical synthesis techniques remain a considerable challenge. The present review examines the advances made using diatomaceous earth as a source of silica, silicon-based materials and templates for energy related applications. The main synthesis routes aimed at preserving the highly desirable naturally formed neat nanostructure of diatomaceous earth are assessed in this review that culminates with the discussion of recently developed pathways to achieving the best properties. The trend analysis establishes a clear roadmap for diatomaceous earth as a source material of choice for current and future energy applications.
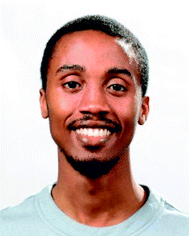 Patrick Aggrey | Patrick Aggrey is a PhD student in Materials Science and Engineering at Skoltech. Patrick's research work aims at understanding the effects of transformations within the silicon oxygen system on the structure and properties of nanostructured silicon and silica-based energy materials and designing cost effective and environmentally friendly synthesis routes to produce them. Some of his results have been recently published. At present his main focus of research is centered on hierarchically structured silica and silicon-based anode materials obtained from naturally occurring diatomaceous earth for applications in energy harvesting and storage. |
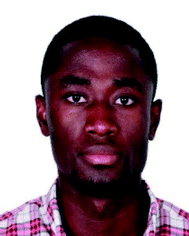 Martinson Nartey | Dr. Martinson Nartey recently received his PhD from the Zhejiang University, Hangzhou, China and joined the Materials Engineering Department of KNUST, Ghana as a lecturer. His research spans advanced composites, functional alloy development and finding alternative materials for sustainable development. Currently, Dr Nartey is working on diatomaceous earth as potential materials for energy sector applications, building industry as partial replacement of cement and wastewater treatment. |
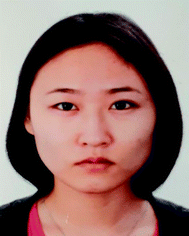 Yuliya Kan | Yuliya Kan graduated Master's degree in Material Science from Tomsk Polytechnic University in 2018. Her thesis was focused on the glass–ceramic interlayer of the coating and alumina ceramic composite for biomedical applications. In the 2nd year of her Master's degree, she participated in the academic exchange program at Technical University in Dresden. At Skoltech she keeps working with the hierarchical nanostructures for biomaterial application. |
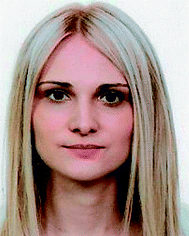 Julijana Cvjetinovic | Julijana Cvjetinovic received her M. S. in Condensed Matter Physics from National University of Science and Technology “MISiS”, Moscow, Russia and currently a PhD student at the Center for Photonics and Quantum Materials at Skolkovo Institute of Science and Technology. During her Master's degree studies she worked on development of hybrid materials based on natural and synthetic polymers for reconstructive surgery. Her current research is focused on using different photonic and bioimaging techniques to study composite multifunctional nanostructured particles for application in medicine and dentistry. Julijana's research interests include bioimaging, photoacoustic and fluorescence visualization, spectroscopy and analysis of compounds, unicellular microalgae, nanoparticles, drug delivery systems. |
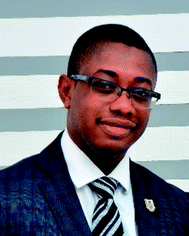 Anthony Andrews | Anthony Andrews is an Associate Professor in the Department of Materials Engineering, in the College of Engineering, Kwame Nkrumah University of Science and Technology, Kumasi – Ghana. His research interest is in materials synthesis and development of ceramic-based composites using both traditional and advanced processing routes. His current research activities include surface modification, corrosion, tribology, and ceramic processing. He has over 30 publications in reputable journals. |
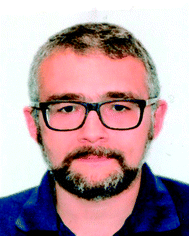 Alexey I. Salimon | Alexey Salimon is senior research engineer in the field of hierarchically structured materials having energy, biomedical and structural applications. He received a Candidate of Science (PhD) degree from the Department of Physical Materials Science of NUST MISiS (1997). His doctoral thesis was devoted to the investigation of the structure changes in metal powders under high-energy mechanical activation and alloying. Dr Alexey Salimon for more than 20 years works in the field of new materials and technologies: nanostructured metals and alloys, quasicrystalline intermetallics (University of Newcastle, UK, 1997–1998), bulk metallic glasses, composites, elastomers resistant to explosion decompression. In 2002–2004 Dr Salimon developed the expert system for the finding of application for new materials under Professor M.F. Ashby leadership in INPG (Grenoble, France). |
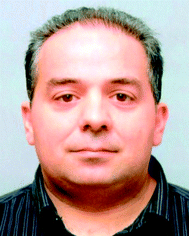 Kalin I. Dragnevski | Kalin Dragnevski obtained his MSc from the University of Chemical Technology & Metallurgy, Sofia, Bulgaria & his PhD from the Institute of Materials at Leeds University. Following a short spell in industry, he took a research position in the Cavendish Laboratory at the University of Cambridge. Kalin joined the Engineering Science Department at the University of Oxford in 2008, where he established & leads the Laboratory for In situ Microscopy & Analysis (LIMA). His research is aimed at developing methodologies for better understanding the structure–property–composition relationship in advanced materials systems on a micro- & nano-scale using novel in situ micromechanical testing techniques. His work recently received the prestigious DR Harting Award for best paper of the year given by the Society of Experimental Mechanics. |
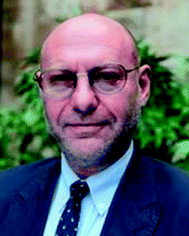 Alexander M. Korsunsky | Alexander M. Korsunsky is a leading expert in engineering microscopy of materials for optimisation of design, durability and performance. He is Fellow of the Institute of Physics, London, UK, and Editor-in-Chief of Materials & Design. Prof. Korsunsky's research interests concern improved understanding of engineered and natural structures and systems, from high-performance metallic alloys to polycrystalline ceramics to natural hard tissue such as seashell nacre and human enamel, the subject of a major research project he leads on the understanding and combatting human dental Caries. He co-authored books on fracture mechanics (Springer), elasticity (CUP) and residual stress (Elsevier), and published ∼500 articles in scholarly periodicals on subjects ranging from multi-modal ‘live’ microscopy, neutron and synchrotron X-ray analysis, contact mechanics and structural integrity to micro-cantilever biosensors, and size effects. |
1. Diatomaceous earth
Advances in scientific imaging have enabled researchers to unveil the intricate structural details of nature's own hierarchically structured materials. The use of imaging techniques based on light and electron beams have progressively revealed the micro- to nano-structures of both natural and engineered materials down to the atomic scale that could not be seen previously. Indeed, the majority of naturally occurring materials possess multi-scale, hierarchical organization that to date remains an area of keen interest for researchers. One such naturally occurring material is diatomaceous earth (DE), which is formed following the build-up of amorphous silica cell walls of dead diatoms in marine sediments.1 Originally discovered by a German peasant Peter Kasten in 1836,2 diatomaceous earth, also known as diatomite, has for some time now been mined in close to thirty countries globally.3 Presently, the leading producer of diatomite is the United States, accounting for close to 35% of the total world production.3 DE is characterized by unique properties such as high porosity, light weight, small particle size and high surface area, chemical inertness and low thermal conductivity3 thus paving the way for numerous applications. It normally has the appearance of a pale-colored powder. The typical particle size range reported for DE is about 10–200 μm.3 Diatomite, regardless of the source, contains SiO2 as the main phase. Other phases present in DE are CaO, MgO, Fe2O3, and Al2O3. Lately, the number of literature reports dedicated to DE has increased, but the fundamental requirement for the powder to be classed as DE remains unresolved, creating significant inconsistency with the term Diatomaceous Earth. However, in a study by Zahajská et al.,4 an approach to resolving these issues has been presented. In the report, a classification of sediment containing diatoms into diatomite and diatomaceous ooze is reported. This work was carried out to address the inconsistency in the use of terms ‘diatomite’ and ‘diatomaceous ooze’ in previous studies.5–14 Fig. 1 illustrates the classification system proposed by Zahajská et al.4 to group the powders into diatomite and diatomaceous ooze. From their system, a powder is considered as diatomite when consolidated siliceous/opaline sediment contains more than 80% diatom SiO2 by weight and porosity higher than 70%. It is worth noting that while other forms of diatomite are available per the classification of Zahajská et al.4 it remains a difficult task to distinguish between the diatomite precursors used in the current literature. This is due to the lack of detail provided by the authors regarding the precursors used. For this reason, the definition of diatomite given by Zahajská et al.4 cannot be applied strictly in the discussion of the existing reports, so that all reports related to diatom silica, diatomite, diatomaceous earth, diatom frustules, diatom algae, diatom earth and biosilica diatomite will be included in the scope of this review paper. It is however important that full details of precursors be used in future to establish a clearer roadmap to advanced technology use.
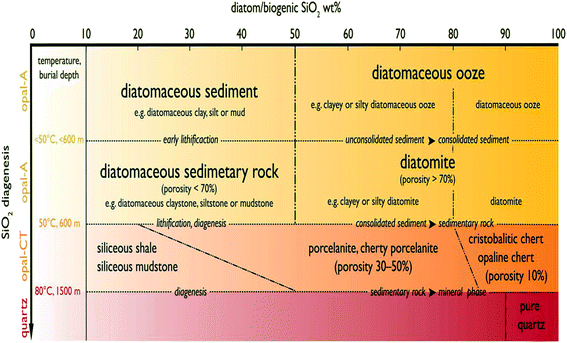 |
| Fig. 1 Classification system of diatom based sediments proposed by Zahajská et al.4 The x-axis showing the weight percentage (wt%) of diatom/biogenic SiO2 contained in sediments and their corresponding transformations as a function of burial depth on the y-axis. | |
The use of diatomite dates as far back as 2000 years ago. It is reported that the Greeks used diatomite in pottery and bricks.2 Conventionally, DE finds applications as filter aids, functional additives, absorbents, natural insecticide, and materials for soil improvement.15–19 Recently, diatomite has attracted significant attention in the scientific community. DE provides a unique way to mimic nature by using it as both template and precursor for materials with desirable nanostructures. Most of today's materials are expected to possess nano to micro-structures to meet several functionalities of specific applications. Often, materials exhibiting desirable properties at the macro-scale suffer setbacks arising from chemical, thermal, electronic or mechanical processes at the nano and micro-scale. One notable example is the potential use of silicon as an anode material in lithium-ion batteries. This area has been well studied, continues to be studied and remains a potential game changer in battery technology.20–26 Silicon is known to have a theoretical capacity an order of magnitude higher than graphite. Coupled with the aforementioned advantages of silicon as a suitable anode material, it is highly abundant and non-toxic. Nevertheless, silicon has not found commercial use as an anode material due to the low cycling stability. Volume changes (up to about 300%) during lithiation have been reported to lead to internal stresses, electrode pulverization, loss of electrical contact between the active material and the current collector, all of which eventually led to poor reversibility and rapid decline in capacity.22,27 These setbacks are peculiar to bulk silicon, particularly ball-milled Si obtained from bulk silicon. This is because the structure of bulk silicon is unable to meet a combination of functionalities required at the nanoscale. For this reason, several attempts have focused on nanostructuring silicon-based anodes to harness the full potential of silicon in battery technology.28–34 This new approach to nanostructuring Si based anodes has been reported to offer a better response to volume changes from the surface to center as shown in Fig. 2.35 As shown in Fig. 2, the ball-milled Si particle disintegrates during the lithiation process while the porous Si powder accommodates the volume changes during lithiation. Another observation of the same kind has been reported in the potential use of bulk silicon as a thermoelectric material.36 Here also, bulk silicon has not found huge applications due to the difficulty in generating a temperature gap across it. As a semiconductor made up of covalent bonds, heat at one end is almost entirely transferred to the other end by lattice vibrations. Without a temperature gradient, it is difficult to generate a significant voltage in thermoelectrics. Again, nano-structuration of silicon has been studied as a way to resolve issues related to its potential use in thermoelectric energy generation.36 Another case is the use of bulk silicon, which is widely used in photovoltaic applications. In spite of gaining commercial attention, a number of drawbacks are still persistent. Notable among these drawbacks is the high surface reflectivity of bulk silicon based solar cells.37–39 A lot of progress has been made in this area, prompting a number of review papers40–42 on the improved surface reflectance of silicon based solar cells with a nanostructured surface. All these reports point to the importance and role of silicon nano-structuration in energy related science. Most importantly, it reveals the potential of siliceous materials with desirable nanostructures and for that matter diatomaceous earth.
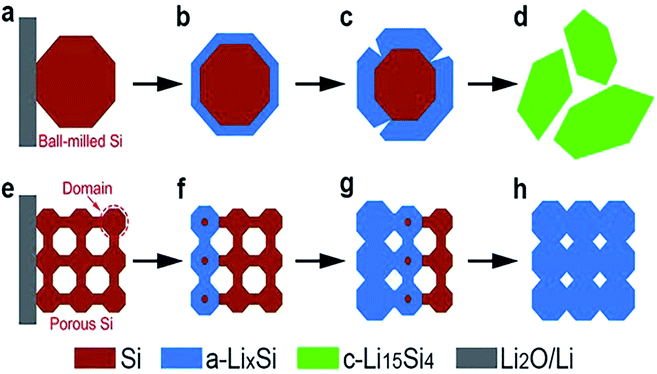 |
| Fig. 2 Lithiation manners presented in ball-milled Si and porous Si nanoparticles. (a–d) Response pattern of ball-milled Si from the surface-to-center during lithiation. (e–h) Response pattern of porous Si particle from the surface-to-center during lithiation.35 | |
The attention towards DE has produced a lot of interesting results43–53 based on which a number of excellent reviews on the application of diatomite in energy harvesting and storage have been reported.54–57 Nevertheless, these excellent reviews do not fully elaborate on the processing routes and their translation into desired properties. Thanks to a recent review by Ragni et al.58 a detailed description of some of the processes used in synthesizing nanostructured materials from diatom microalgae was presented. As DE continues to gain more attention in energy applications, it is essential to provide a comprehensive report of the major synthesis used in DE related studies for energy application which is not fully addressed in the previous reviews. This review seeks to expand and cover all the major processing routes as far as diatomite in energy applications are concerned. Also, quite a lot of progress has been made in this area since the publication of these reviews36,59–63 and for that matter we present a report of the current progress made with biosilica diatomite for potential energy application while focusing deeply on the main synthesis routes common to most of the reports. Considering the fast progress in this area, we also report on unexplored areas related to energy research.
2. Nano-scale morphology of diatomaceous earth
The structure of DE has been studied over the years using state-of-the-art scientific equipment including Scanning/Transmission Electron Microscopy (SEM and TEM),64 Atomic Force Microscopy (AFM),65 X-ray Photoelectron Microscopy,66 Fourier Transform Infrared Spectroscopy (FTIR)67 and Small Angle X-ray Scattering (SAXS).68 Individual diatom frustules within a diatomite powder are characterized by a silica cell wall consisting of two overlapping thecae (epitheca as the larger part and hypotheca, the smaller), each consisting of a valve. These valves are separated by an accompanying series of girdle bands.55 Frustules are characterized by a row of pores known as interstriae. Between the interstriae are ribs, called striae. The interstriae are mainly responsible for the uptake of nutrients.69 The frustules vary greatly, so there is no simple summary of the morphology. In Fig. 3, the SEM images of different diatoms collected from Lake Baikal, Arabian Sea and Skolkovo Pool clearly show diatoms with different shapes and structures.70 However, frustules have been traditionally classified into two groups namely; centric diatoms (Centrales) and pennate diatoms (Pennales). The centric diatom frustules have surface features arranged around a point while the pennate frustules have major features at right angles to the striae. In a classification by round and Crawford diatoms have been classified into three groups.69 They are the centric diatoms (Coscinodiscophyceae), pennate diatoms without a raphe (Fragilariophyceae), and pennate diatoms with a raphe (Bacillariophyceae).
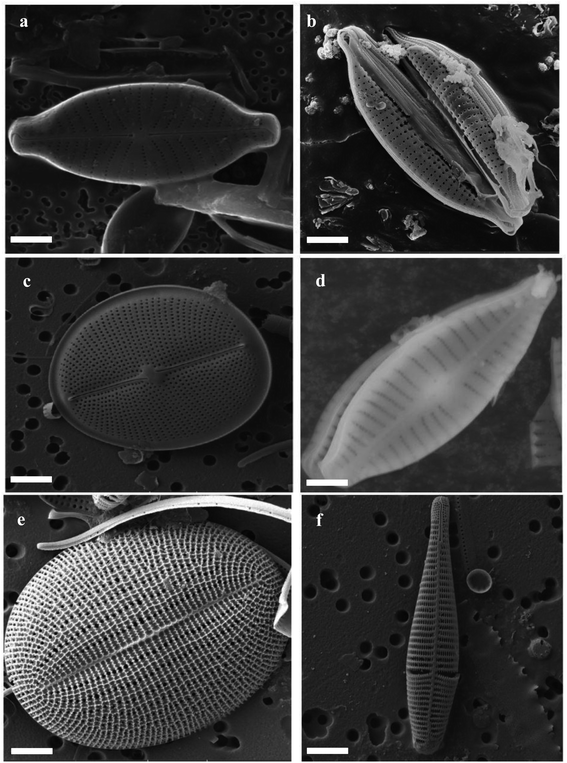 |
| Fig. 3 Different shapes and structure of diatoms (a–f) SEM images of different marine diatoms (source: Lake Baikal, Arabian Sea, and Skolkovo Pool) scale bar: 5 μm.70 | |
3. Classification of the role of DE
Diatomite plays different roles in experimental research. These roles are classified under three main groups with regards to energy related studies. These groups have been created based on the state of diatomite in particular experimental works. The three groups, namely, synthesis involving the use of raw DE, the use of DE frustules as a sacrificial material (template), and DE as a precursor for silicon-based materials are shown in Fig. 4. The main motivation behind the use of DE is to preserve and translate the nanoscale morphology of diatomite into new functional materials, either as a precursor or template. This is quite different for some studies that require the use of raw diatomite as a supporting material to host the active material especially in thermal energy storage applications. All the groups have some reports using pre-treatments, mostly thermal and mechanical. The prospect of the entire diatom macrocosm in the energy industry is further showcased in an isolated report by Chen et al.71 A rather unconventional approach with respect to most reported DE based materials for energy applications saw Chen et al.71 exploring the optical properties of a chlorophyll extract from diatom algae for solar energy harvesting. Diatom algae are known to be one of the most photosynthetic organisms. It is reported to contribute about 40% of the aquatic primary production using chlorophyll a [chl-a] component. Other important light absorption components found in diatoms are chlorophyll c [chl-c] and fucoxanthin. In their work, Chen et al.71 studied the anti-reflective property of diatom extract obtained via a facile process where the diatom extract contained chlorophyll a as the primary active component for photon energy conversion suitable for blue to red photon conversion. As expected, the diatom extract reduced the surface reflectance of Si over the entire light spectrum (350–1100 nm) up to 13%. Apart from its anti-reflective (AR) properties, the extract showed strong photon down-conversion effect where the blue light portion of light is converted to red. Both properties were credited for the enhanced short circuit current and power conversion efficiency (PCE) of the Si solar cell. Most importantly Chen et al.71 confirmed the thermal stability of the diatom extract up to 90 °C without changes in neither the optical properties nor the color.
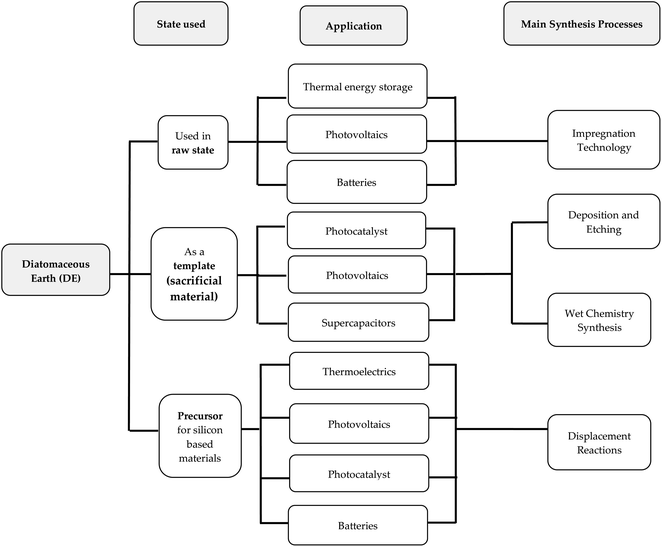 |
| Fig. 4 Schematic representation of the relationship between the state of DE, intended applications and main synthesis. | |
3.1 Raw DE for energy applications
Energy applications involving the use of raw diatomaceous earth without further chemical synthesis, capable of dissolving it or transforming it to silicon-based materials, have been majorly associated with thermal energy storage (TES)72–82 although recent isolated applications in Li-ion63 and Li–sulphur83 batteries and polymer solar cells84 have been reported as presented in Fig. 4. Diatomaceous earth normally serves as a supporting material and no form of templating or chemical reduction is required. Rather, facile processes such as mixing and impregnation are normally used to form a composite with the active material. Even though DE is applied in its raw state, pre-heat treatments such as vacuum drying, microwave heating, and calcination are sometimes performed.85–90 Thermal energy storage has long been seen as an eco-friendly approach to sustainable energy for future energy demands.91 Using phase change materials (PCMs), latent heat can be effectively used to store thermal energy. Over the years of studies, modifications with PCMs have been reported to result in substantial increase in desired properties. Notable among these modifications is the use of diatomaceous earth. DE assumes the role of a supporting material in the modification of PCMs. It is known that the higher the mass ratio of the PCM in DE, the greater the latent heat of the composite PCM.91,92 Thermal energy storage is realized through three routes namely, sensible heat, latent heat, thermochemical or a combination of these.91 Among the possible thermal energy storage routes, latent heat storage is known to be the most attractive due to its ability to provide a higher energy storage density and to store heat at a constant temperature corresponding to the phase transition temperature of PCM. In latent heat storage, a storage material undergoes a phase change from solid to liquid or liquid to gas or vice versa upon the absorption or release of heat.91 PCMs are available in three forms. They are organic, inorganic and eutectic PCMs.91 Recently, raw diatomite was studied as a potential negative electrode for Li-ion batteries and a polysulfur absorbent for Li–S batteries. In another isolated study,84 raw DE was used in a polymer solar cell to improve light trapping. In all these reports,72–82 diatomite is used in its raw state without complex chemical reactions to dissolve, precipitate or reduce silica to silicon-based compounds and does not involve templating.
3.2 DE as sacrificial material for energy applications
Inspired by the neat nanostructured patterns in diatom frustules, newly engineered structured materials/composites have been produced with similar patterns using diatom frustules as templates.93–105 Ever since Losic et al.93 reported on the fabrication of nanostructured gold using diatom frustule as a template, a number of advances pertaining to the application of this fabrication route for new engineered materials have been reported94–105 mostly for energy applications. Specifically, these materials have been found useful for photovoltaics,95,97 supercapacitors99–101 and photocatalysts98 which is shown in Fig. 4. Apart from the dissolution process often executed at the end of the synthesis protocol to dissolve DE, there is mostly no chemical reaction involving DE prior to the dissolution process. The main synthesis processes used are deposition techniques and wet chemistry routes, however, some pre-treatments such as vacuum drying and calcination are sometimes applied as a means to free the pores of all impurities.
3.3 Precursor for silicon based materials for energy applications
Pure elemental silicon, silicon oxide and other silicon-based materials have found diverse applications in energy related applications to date.106–109 Bulk silicon is widely known for its application in photovoltaics, existing as monocrystalline and polycrystalline silicon based solar cells.106 With the advent of nanotechnology, nanostructured silicon-based materials have paved the way for novel applications in batteries and thermoelectrics.22,36,109 The desire for facile and cost-effective ways of producing nanostructured silicon-based materials has led the attention of the scientific community towards diatomite, as a precursor for silicon-based materials. Diatomite happens to be the only siliceous material exhibiting a neatly formed nanoporous structure, at least to the best knowledge of the authors. It must be noted that, while the primary focus is as a silica precursor, DE eventually serves as a template for the silicon-based materials formed. There appears to be a narrow margin of difference between this category and the previous section (4.2). Here, the chemistry of DE is altered through chemical reduction reactions best known as displacement reactions, discussed in subsequent sections, but no such chemical reactions are reported for diatoms used as a template (4.2). Interestingly, some studies have combined both approaches and notable among them is a report by Le et al.110 In their work, DE initially served as a precursor for nanostructured Si. The nanostructured Si possessing the framework of the precursor DE, subsequently played the role of a template for MnO2, therefore obtaining a nanocomposite for supercapacitor applications. Potential energy applications involving the use of diatomite as a precursor for silicon-based materials are mostly batteries44,49,59,60,111, photovoltaics,112 supercapacitors110 and thermoelectrics36 as shown in Fig. 4. Widely reported materials obtained from diatomite are mostly elemental Si, Si/SiO2, Si/MgO, SiC, SiGe, and Mg2Si.
4. Synthesis routes for energy applications
The most crucial aspect of synthesis involving diatomite is the ability to preserve the nanoscale structure and translate it into the new material. For that matter, all efforts to preserve the structure are vital in research. The processing routes used in diatomite related studies are numerous,58 however, a number of these processing routes are peculiar to energy related reports. Herein, the major synthesis routes and their respective field of application are addressed. While these synthesis routes are reported as the primary process, the majority of these studies involved pre-treatments of DE, thermal or mechanically driven.
4.1 Pre-treatments of diatomaceous earth
DE pre-processing techniques have become popular when synthesizing DE-based energy materials. In most cases, these treatments were thermally or mechanically motivated. Thermal pre-treatment such as calcination,36,44,45,51,52,59,73,74,113 drying43,45,49,52,59,61,72 and microwave heating87,88 have been widely used. Mechanical milling has also been reported.49,63,113 Among the two, thermal pre-treatments have received more attention in energy related studies. Prior heat treatments are reported to cause changes in the powder characteristics of DE including the color, particle size, specific surface area, pore size and volume, crystalline state and crystallite size.63,114 Diatomite is usually dried in vacuum between 80–100 °C prior to further synthesis. This is usually done to reduce the moisture content of the powder.115 In some isolated cases, microwave heating was applied prior to further synthesis, and this affected the porous structure to some extent,87,88 notably particle size increment and an unclogged pore structure. To the best of our knowledge, no further changes are reported for vacuum drying and microwave heating of diatomite unlike other prior heat treatments. As far as diatomite is concerned, calcination involves a controlled high temperature (500–1200 °C) treatment under controlled environment. Calcination of diatomite is mostly preceded by vacuum drying. Unlike low vacuum drying and microwave heating, calcination causes a wide range of changes in the powder characteristics including color changes,114 phase composition,36,114,116 crystallite size114 and particle size.114 Clearly, calcination has serious consequences on the powder characteristics of diatomite, yet the selection of the right precursor remains a concern for some intended applications. In most reports, either a raw (dried powder) DE is used or a calcined powder (dried and calcined), particularly reports in battery, supercapacitor, and thermoelectric applications.36,44,49,50,99,117 Choosing the right DE precursor for such applications is quite a challenge as far as these reports are concerned since either raw or calcined DE powders have different consequences on the final properties. Thanks to some reports where both raw diatomite (only dried) and calcined diatomite (dried and calcined) are compared, we have some guidelines to help select the right DE precursor for specific applications. These reports, especially in filtration,118 cement production,119 thermal energy storage73,89 and photocatalyst120 carried out a comparative study of the performance of both calcined and uncalcined DE powders in a single work, providing some insight into the right candidate for these applications. This particular issue not given much attention was recently raised by Korsunsky et al.,121 where the importance of choosing the right DE precursor (calcined or raw), specifically for silica to silicon-based materials synthesis was addressed. Raw diatomite is amorphous while the calcined counterpart is crystalline (cristobalite). Understanding their individual reaction kinetics may be crucial for selecting the right precursor as well as controllable synthesis parameters. Even though both calcined and raw DE powders have successfully been reduced to silicon-based materials, it is still unclear the ideal state of the DE precursor for silicon-based material conversion.
Mechanical pre-treatments of DE normally involve high energy ball milling. In some recent studies high energy ball milling was performed on DE prior to the main synthesis process.63,122,123 Like some thermal pre-treatments, ball-milled DE normally shows significant changes in the particle size, pore size and specific surface area. Powder characteristics such as crystallinity, phase composition and color changes are not affected by ball milling. Although ball milling of DE has not received much attention like thermal processes, recent reports show it is a crucial step for some intended applications. A study by Blanco et al.63 reported the effects of ball milling of DE on the electrochemical properties of the negative electrode produced. In that work, the ball milled DE powder showed an increase in specific surface area from 1.2 m2 g−1 (pristine DE) to 17.3 m2 g−1. Additionally, the mean particle size of the ball-milled DE powder was significantly lower (470 nm) than the pristine DE (17 μm). They also reported an increased presence of mesopores in the ball-milled powder compared to the pristine powder. Blanco et al.63 indicated that although the mesopores could have been present in the pristine powder, they became accessible after ball milling. The powder characteristics reported for the ball-milled powder subsequently influenced the electrochemical performance of the DE-based negative electrode. As evidenced in Fig. 5,63 the DE based negative electrode prepared from the milled powder showed a higher capacity of 750 mA h g−1 (milled) than the pristine powder (550 mA h g−1). This was attributed to the shortening of the Li-ion diffusion path and the increased surface area of the powders achieved through particle size reduction. Ball milling offers a cheap and simple way to alter the powder characteristics of DE for intended applications, especially in silicon-based anode materials. The right combination of both mechanically and thermally motivated pre-treatments may lead to a range of functionalities for new materials.
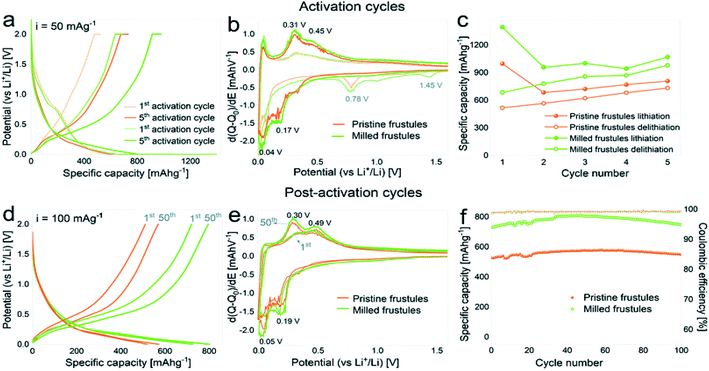 |
| Fig. 5 The electrochemical performance of the milled and pristine DE-based negative electrodes: (a and d) voltage profile curves, (b and e) differential capacity plots, (c and f) specific capacity against cycle number for activation (a–c) and post-activation (d–f) curves (green points: milled DE) and (orange points: pristine DE).63 | |
4.2 Impregnation technology
The impregnation technology is a well-known manufacturing process which has been widely used in the synthesis of nanocatalyst, composite materials, foundry technology, energy materials and eco-efficient construction.124–129 In advanced composite manufacture, impregnation is used in making the starting material, prepreg, which comprises the resin and reinforcement. Recently, impregnation technology has become a useful process for the synthesis of nanocatalyst.124 The impregnation technology has been utilized in the protection of wooden structures from destruction.129 Herein, the combustibility of constructions made from wooden structures are reduced by the impregnation of fire-retardant solutions. In the impregnation technology, a solution (impregnant) is infused to fill the invisible pores in a material. The impregnation technology comes in two forms: dry/incipient-wetness technology and wet impregnation.130,131 In dry/incipient-wetness technology, the volume of the impregnate matches exactly the pore volume of the support while in wet impregnation, an excess volume of impregnate is used.130 The impregnation technology has widely been used in the production of nanocomposite phase change materials (nPCMs) based on diatomaceous earth for TES. The principle behind this synthesis is identical to the ones presented above. Diatomaceous earth, as a supporting material in this area, offers the ability to load sufficient PCM without leakage due to their attractive sorption ability.43 Based on accounts provided in existing reports on DE-based materials prepared by impregnation technology, the wet impregnation method was mostly used. Impregnation technology is further categorized as direct or vacuum impregnation, both widely reported in recent studies.
4.2.1 Direct impregnation. Quite a number of reports on DE based nPCMs employed the impregnation technology without vacuum, well known as the direct impregnation technology.73,75,86,89 This type of impregnation process appears to provide a simple and low-cost set-up for synthesis unlike the vacuum-assisted type. In the direct impregnation process, the PCM (impregnate) is mixed with the porous powder (supporting material) at a specific melting temperature of the PCM, without prior air suction. Konuklu et al.75 showed the effectiveness of using the direct impregnation process to synthesize a DE based nPCM, with paraffin as the PCM. They reported a maximum paraffin absorption of 32%, obtained from a mixing ratio of 40
:
60 (paraffin
:
DE) as compared to other mixing ratios; 16% for 20
:
80 and 24% for 30
:
70. Their nPCM with the highest absorption showed very good thermal stability and successfully passed the leakage test performed at 95 °C. This test is carried out at high temperatures, especially in the vicinity of the PCMs melting point, as a quality check to confirm the active materials does not leak out. DE pre-treatments have received considerable attention in the preparation of nPCMs.73,87–89 As far as the impregnation method is concerned, an improved sorption ability of DE can accommodate for more PCM.91,92 Xu et al.74 studied the potential application of calcined DE as a supporting material for a nPCM based on paraffin using a direct impregnation method. In their work, they recorded an optimum paraffin absorption of 47.44% obtained from a mixing ratio of 0.9
:
1.0 (paraffin
:
DE). As expected, the nPCM with the optimum absorption capacity showed superior TES properties compared to powders with different mixing ratios. In another study showing the effects of pre-treatments on the absorption capacity of DE, microwave heating was utilized.91 Konuklu et al.,88 prepared nPCMs fabricated via the direct impregnation method using microwave modified diatomite, using lauric acid (LA). In that study, the microwave modification of diatomite led to an increased absorption of the PCM on its surface and thus showed an increase in the TES capacity as compared to nPCM without microwave modification. They also reported an optimum microwave heating time of 1 minute, beyond which TES properties deteriorated. To better predict the right DE precursor for nPCMs, a number of studies focused on both calcined and uncalcined DE powders.73,89 Sun et al.73 prepared nPCMs made from both raw and calcined opal using a direct impregnation process. Here, nPCMs made from calcined opal showed optimum absorption of the binary paraffin blends than the raw opal sample. The highest absorption obtained were 39% and 36% for the calcined and raw powders respectively. The superior absorption (39%) of the calcined opal was attributed to the increase in pore size and increased specific surface area (61.56 to 84.79 m2 g−1). The nPCM based on calcined opal showed greater latent heat than the one based on the raw opal. Other previous and recent reports that utilized the direct impregnation method in the preparation of DE based nPCMs are by Liu et al.132,133 and Jia et al.,134 which are presented in Table 1. It must be emphasized that in all these reports, the interaction between the PCMs and the diatomite was confirmed to be physical, without any chemical interaction from FTIR measurements. The direct impregnation method is a facile, cheap and eco-friendly route to commercially produce nPCMs based on DE. Regardless of these attractive attributes, some researchers use vacuum impregnation towards expecting considerable improvements in the TES capacity of prepared nPCMs. A study by Nomura et al.,77 however, alleged that a trivial difference in the latent heat was obtained for both direct and vacuum impregnation making the direct impregnation method a cost-effective route to prepare DE based nPCMs. Diatomaceous earth undergoes no chemical transformation when subjected to an impregnation process, whether directly or using vacuum. Away from thermal energy storage, Li et al.83 reported on the use of raw diatomite as a polysulfur absorbent for lithium–sulfur batteries. In their work, the sulfur–diatomite–acetylene black composite was prepared via the direct impregnation technology. The calculated adsorption capacity of diatomite was 6.14 × 10−3 g g−1, proving to be a better absorbent compared to acetylene black (5.31 × 10−2 g g−1). Schematically shown in their work and presented in Fig. 6,83 a diatomite-based sulfur electrode is seen to suppress the polysulfide diffusion significantly.
Table 1 Studies on diatomite based nPCMs synthesized via the impregnation technologya
PCM |
State of DE |
Optimum quantity of impregnant |
Type of impregnation |
Reference |
GHL = galactitol hexa laurate; GHM = galactitol hexa myristate. |
Polyethylene glycol |
Raw |
50 wt% |
Vacuum impregnation |
43 |
GHL and GHM |
Raw |
55 wt% |
Vacuum impregnation |
81 |
Binary forms of (n-octadecane, paraffin wax and liquid paraffin) |
Raw and calcined |
36 wt% and 39 wt% |
Direct impregnation |
73 |
Paraffin |
Raw and calcined |
47.37 wt% and 52.63 wt% |
Direct impregnation |
74 |
Fatty acids |
Raw |
40 wt% |
Fusion adsorption/direct impregnation |
78 |
Hexadecane, octadecane, and paraffin |
Raw |
80 wt% |
Vacuum impregnation |
72 |
Lauric–stearic acid |
Microwave modified |
n/a |
Vacuum impregnation |
87 |
Lauric acid |
Microwave modified |
n/a |
Direct impregnation |
88 |
Methyl stearate |
Dried at 120 °C for 24 hours |
51.3 wt% |
Direct impregnation |
86 |
Capric acid |
Raw diatomite |
50 wt% |
Direct impregnation |
132 |
Palmitic acid |
Dried at 120 °C for 8 hours |
55 wt% |
Direct impregnation |
134 |
Stearic–palmitic acid |
Dried at 105 °C for 1 hours |
65.2 wt% |
Vacuum impregnation |
139 |
Capric–lauric acid |
Raw |
53.6 wt% |
Vacuum impregnation |
80 |
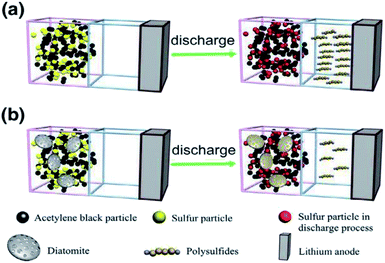 |
| Fig. 6 Polysulfide suppression behaviour schematically illustrated for (a) sulfur electrode without DE (b) sulfur electrode with DE.83 | |
4.2.2 Vacuum impregnation. Although vacuum impregnation comes with a complex set-up and relatively high cost, this impregnation process has interesting applications.135,136 The vacuum-assisted impregnation/vacuum impregnation could allow for shorter synthesis time coupled with void-free systems due to the absence of obstruction posed by impurities trapped within the pores. Herein, air is sucked out of the porous powder using a vacuum system prior to the loading process. Potentially, the entire porosity of the supporting DE material could be utilized to obtain optimum mass ratio of the PCMs for optimum TES capacity. In a report by Karaman et al.,43 a PEG/diatomite composite PCM was prepared using vacuum impregnation. Herein, they reported that air was initially evacuated from the pores on the surface of the diatomite sample followed by injection with the liquid PEG. In their work, they reported a complete dispersion of PEG into diatomite pores. This, they claim, provided mechanical stability to the composite, hence preventing seepage of melted PEG until a threshold of about 50% PEG in diatomite. Additionally, there was no chemical interaction between PEG and diatomite composite prepared using vacuum impregnation as confirmed by FTIR analysis. Physical forces including capillary and surface tension forces were observed between the functional groups of PEG and diatomite, preventing leakage and retaining PEG molecules within the diatomite pores. Sarı et al.81 reported on the use of vacuum impregnation for the synthesis of galactitol hexa-myristate (GHM)/diatomite and galactitol hexa laurate (GHL)/diatomite nPCMs. In their work, they also reported that the porous structure of the supporting material provided good mechanical properties to the composite. The maximum mass percentage of GHM and GHL confined in diatomite were 52 and 51 wt% respectively. Sarı et al.81 also attributed the leakage behavior of the PCM to the capillary and surface tension forces addressed earlier, made possible through vacuum impregnation. Like the nPCM reported by Karaman et al.,43 Sarı et al.81 also reported no chemical interaction between the components of their nPCMs. In both reports discussed above, raw (uncalcined) diatomite and the impregnation process involved the use of vacuum. Efforts to improve the sorption ability are crucial for enhanced TES application of DE based nPCMs. Growing attention given to pre-treatments especially microwave heating has received equal consideration prior to the vacuum impregnation process.87 Microwave heating is known to provide a uniform and rapid heating compared to traditional heating methods.137,138 Li et al.87 recently reported an improvement in the loading capacity of diatomite after microwave-acid treatment compared to raw diatomite using the vacuum impregnation method. As reported, a certain amount of DE was mixed with 8% HCl solution and irradiated at 700 W for 5 minutes in a microwave oven. Subsequently, air was sucked from the pores using vacuum and loaded with LA–SA composition (lauric acid–stearic acid). Prior treatment of diatomite via the microwave-acid route led to the removal of impurities which blocked the pores, hence significantly improving loading capacity. Albeit clear evidence of the role conditions such as vacuum, in enhancing the absorption properties of DE, detailed information about the effects of all the processing parameters like vacuum level, time and temperature on the structure and absorption properties of DE remains lacking. A study by Qian et al.139 investigated the effects of immersion time and temperature variations on the absorption capacity of DE. Their work illustrated in Fig. 7 showed that PEG absorption increased significantly within the first 60 minutes, but remained almost unaffected beyond 60 minutes. It was also demonstrated that an increase in temperature to 90 °C at immersion times (10 and 30 minutes) resulted in significant increase in PEG absorption. But after 60 minutes, they observed almost no further increase in PEG absorption with increasing temperature, thus proposing the optimal conditions as 60 minutes immersion time and maximum temperature of 90 °C. To fully appreciate the effects of vacuum on the immersion process, they repeated the protocol without vacuum and found that the nPCMs prepared via the vacuum impregnation process had a higher PEG ratio than the direct impregnation process. Another work by Zong et al.,140 explored the effects of vacuum level, soaking time, and temperature on the content of their PCM (stearic acid) in DE. Like Qian et al.,139 Zong et al.140 reported a significant increase in the amount of PCM in DE with increasing temperatures until 80 °C, where it begins to reduce. Increasing temperature improved the viscosity of the PCM and made it easy for it to occupy the internal pores of DE. The downside however is that further increase in temperature promotes the volatilization of the PCM, subsequently leading to a dramatic drop in its content in the supporting material. Another important parameter, immersion time, proved to be very crucial for the impregnation technology. Similar to the report by Qian et al.,139 Zong et al.140 also observed a gradual increase in the absorption capacity with increasing time till a limiting time of 2 hours, beyond which no further changes were observed. The inconsistency between the reported peak times depends on a lot of other synthesis parameters such as, the PCM used, the state of the DE powder and the presence of vacuum or direct immersion. Regardless of these parameters, allowing enough time has the likelihood of yielding optimum PCM amount in the supporting material. Having identified the optimal time and temperature, Zong et al. further analyzed the effects of vacuum levels on the absorption capacity of DE in their nPCM using the pre-established conditions. They observed an increase in the absorption capacity when vacuum level increase from 0.01 to 0.03 MPa. Beyond 0.03 MPa, the absorption capacity remained unchanged. It is without doubt that DE, as a supporting material is ideal for TES, as such finding optimal parameters to synergistically improve the impregnation of PCMs is of the highest demand. It must however be noted that, these conditions may differ for different systems, considering the different characteristics of various PCMs. A number of recent studies reported successes in preparing DE based nPCMs using the vacuum impregnation method72,80,141 as shown in Table 1.
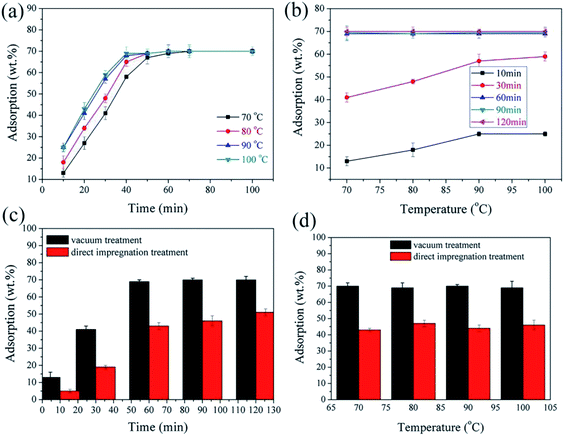 |
| Fig. 7 (a and b) Adsorption capacity of diatomite as a function of temperature and time (c and d) adsorption capacity of diatomite in vacuum and direct impregnation.139 | |
4.3 Deposition and etching
As a highly porous 3D structure with unique properties, diatomite represents a promising carrier and template for synthesizing various composite materials for energy storage applications. However, diatomite's primary limitations are its high resistivity and low conductivity, making it not favorable for energy conversion and other applications. Therefore, in the last decade, significant research has been devoted to functionalizing and modifying diatom silica by different materials to obtain novel composite structures with more efficient optical and electrical properties using several strategies such as chemical vapor deposition, atomic layer deposition and some wet chemistry approaches. Deposition techniques enable the coating of diatomite with metal nanoparticles, semiconductors, carbon, polymers, and other materials while preserving the 3D micro- and nanostructure and porosity. In most cases,101,102 where the focus is placed on the newly structured products, the active component of interest is deposited on diatomite and subsequent acid washing (etching) is done to get rid of the DE. Elsewhere,105 acid washing (etching) is not utilized since they mostly focus on preparing DE based nanocomposites.
One material that is widely used for the decoration of diatomite is graphene. Despite the excellent physical, mechanical, optical and electronic properties of graphene and the achievements in advancing its use as a supercapacitor electrode and electrocatalyst, there is still a need to improve capacitive performance and electrocatalytic efficiency.101 This improvement can be achieved through hybridization with, for example, porous diatomite and transition metal oxides such as manganese dioxides MnO2, due to their non-toxicity, low fabrication cost, good catalytic activity, abundant availability and high specific capacitance.142 A small-methane-flow chemical vapor deposition process was used by Chen et al.102 for growth of hierarchical biomorphic graphene (HBG) on diatomite. A pre-cleaned diatomite powder was held under a mixed gas flow of H2/Ar and methane to support the growth of the graphene layer whose thickness can be changed by varying the concentration of methane gas. Diatomite template was removed by immersing it in a hydrofluoric acid (HF) (molar ratio of HF
:
H2O
:
EtOH (ethanol) is 6.7
:
27.8
:
5.1) at room temperature. Afterwards, the graphene powder was obtained by freeze-drying at – 90 °C and reduced pressure. This new approach utilizes diatomite as the growth template so that the derived HBG sample is highly crystallized, retains the porous structure of diatomite and contains fewer impurities. Flexible graphene films made by adding graphene powder to an ethanol/terpineol solution containing ethyl cellulose (EC) had much higher conductivity and good bending resistance compared to reduced graphene oxide and liquid-phase layered graphene, which opens the way for applications in flexible transparent electrodes, polymer composites, conductive inks, and printed electronics.
In a recent study by Le et al.,101 natural diatomite was used as the bio-template for the chemical vapor deposition (CVD) growth of 3D graphene structure subsequently doped with nitrogen and deposited on MnO2 nanosheets. The prepared bifunctional material can be used as a high-performance supercapacitor and oxygen reduction reaction catalyst. The CVD method consisted of several stages: placing diatomite into an Al2O3 boat and a CVD system, reducing the pressure, heating to 1050 °C, and annealing in an Ar gas flow at a pressure of 26.5 kPa. The growth of graphene started with the introduction of H2 and CH4 into the system. The next step was etching the diatomite template by mixing the resulting composite with a KOH solution in an autoclave at 80 °C for 16 h. After etching, 3D graphene was doped with nitrogen (3D N-G) using a hydrothermal reaction to improve the electrochemical properties of the obtained porous graphene structure. Finally, N-doped graphene was mixed with KMnO4 and ultrasonically treated to obtain a MnO2 decorated (3D N-G) labelled as N-doped 3D graphene@MnO2. Four different N-doped 3D graphene@MnO2 hybrid systems were obtained depending on how long the mixture was autoclaved (1, 3, 5, 7 h). SEM and TEM images illustrated that graphene retained the diatomite's porous structure and morphology after removing the template. Moreover, hierarchical channels and pores that penetrate through the graphene walls can facilitate contact between the electrode and the electrolyte and improve ion/electron transfer so that redox reaction can occur at high current density without the loss of capacitance. Uniformly deposited MnO2 nanosheets, the size and density of which are directly dependent on the reaction time, improved the electrochemical characteristics. N-doped graphene@MnO2 has proven to be an effective electrocatalyst in the oxygen reduction (ORR) reaction due to the more active surface area and accelerated O2 diffusion and electron transfer. The results obtained in this article clearly show that such hybrid structures are very promising for use in ORR catalysts and supercapacitor electrodes.
Another recently published study105 found that manganese oxide deposited onto carbon nanotubes (CNTs)/graphene/diatomite substrate exhibits high specific capacitance, good rate capability, and excellent cyclic stability and therefore has great potential for energy storage applications. In this work, graphene was deposited on diatomite through the CVD process. At the same time, the carbon nanotube seeds were uniformly grown by bimetal seeds deposition and subsequent CVD on the surface of the prepared graphene/diatomite. In the final stage, MnO2 nanosheets were attached to the surface of the CNTs/graphene structure via a one-pot hydrothermal method. The preparation process of the MnO2@CNTs/G/diatomite composite is illustrated in Fig. 8.105 An interconnected network of CNTs with a diameter of around 10–50 nm and 3D porous graphene facilitates the electron transfer rate and increases active surface area whereas uniformly encapsulated porous MnO2 nanosheets provide the infiltration of electrolyte and decreased ion diffusion path. The authors also investigated the asymmetric supercapacitor (ACS) based on MnO2@CNTs/G/diatomite and microwave exfoliated graphite oxide (a-MEGO) as positive and negative electrodes. The ACS capacitor revealed high energy density (64.4 W h kg−1 at a power density of 451.5 W kg−1) and power density of 19.8 kW kg−1 (at an energy density of 6.7 W h kg−1).
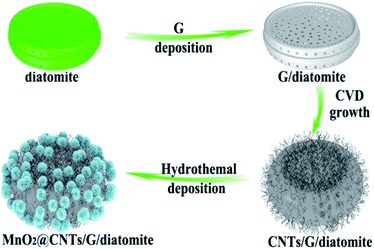 |
| Fig. 8 Illustration of the MnO2@CNTs/G/diatomite composite fabrication.105 | |
The studies mentioned above have shown that diatomite can be used as a template for the fabrication of three-dimensional newly structured/hybrid materials with improved photocatalytic and electrochemical performances through a deposition process often followed by etching of the template. Deposition techniques, although reliable come with a lot of complexities and high cost, raising a lot of concerns about potential commercialization. As mentioned earlier, depositing new materials on diatom silica can equally be achieved via facile wet chemistry routes which are discussed in the subsequent section.
4.4 Wet chemistry synthesis
For energy storage applications, the large surface area and highly porous network structure of diatomite provides the opportunity to maximize electrochemical reactions. Earlier sections have confirmed the prohibitively high synthesis cost and the ‘ungreen’ nature of some processing techniques as a major limitation to the commercialization of processes that offer alternate materials for energy storage applications. Wet chemistry synthesis shows high potential in enhancing the usability of diatomite for energy applications with the hydrothermal method receiving quite an attention in the past years. Hydrothermal synthesis is a process that produces single crystals that depend on the solubility of minerals in hot aqueous medium under high pressure.143
Jiang et al.104 dissolved purified diatomite and other inorganic compounds in an aqueous solution under magnetic stirring and later utilized Teflon-lined stainless steel autoclave at a 180 °C for 24 hours to achieve the hot medium–high pressure step of the hydrothermal synthesis after which subsequent washing was carried out. Through this approach, the inner and outer surfaces of diatomite were successfully decorated with η-Fe2O3 to form 3D porous structure that enhanced the specific capacitance of η-Fe2O3 nanospheres/diatomite composites. Similarly, Jing et al.144 used the hydrothermal synthesis to form a Ni–Co LDH@diatomite composite which exhibited capacitance retention of 94.2% after the 5000-cycle test at a current density of 2 A g−1. Yang et al.,100 employed diatomite as a template in the preparation of a MoS2/amorphous carbon composite for supercapacitor applications. After the hydrothermal synthesis, the diatomite was removed by using a 40% HF solution for 12 hours. The retention of the diatomite structure after the HF soaking ensured a unique microstructure of the MoS2/amorphous carbon composite which is shown in Fig. 9.100 This led to improved electrochemical properties with 93.2% capacitance retention after 1000 cycles. Li et al.145 used a two-step hydrothermal synthesis followed by an in situ polymerization route to form a D@FeOOH@PPy complex which showed enhanced electrochemical performance and potential for electrode material for energy storage.
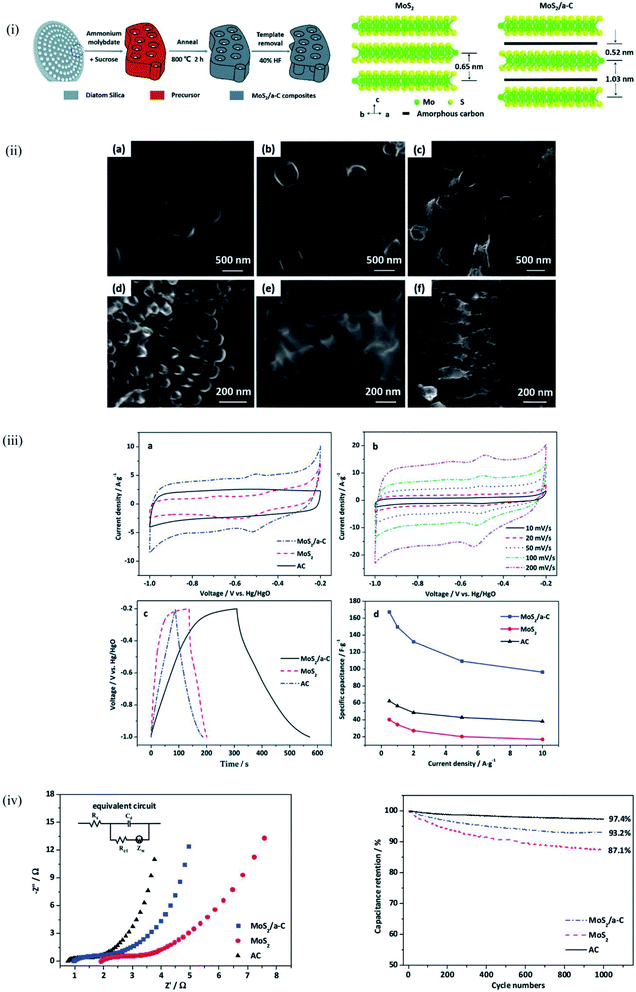 |
| Fig. 9 MoS2/a-C composite prepared using DE templating (i) schematic representation of the synthesis process (ii) schematic representation of the microstructure of MoS2 and MoS2/a-C composite (a and d) AC, (b and e) MoS2, and (c and f) MoS2/a-C composite (iii) and (iv) electrochemical performance of MoS2/a-C, MoS2, and AC.100 | |
Li et al.103 studied the MnO2 nanostructures replicated from diatoms using a simple hydrothermal process for applications in high-performance capacitors. Their study showed that MnO2 diatom replicas exhibit high specific capacitance, good cyclability and rate capability, which depend on the diatoms' shape. Guo et al.51 demonstrated a new and facile approach for the fabrication of supercapacitors based on hollow diatom silica structures coated with TiO2 nanospheres and MnO2 mesoporous nanosheets (diatomite@TiO2@MnO2). The fabrication route of the complex composite included three steps: purification of diatomite to obtain hollow silica microshells, the deposition of the TiO2 nanospheres layer by hydrolysis, and metathetic reaction using TiF4 precursor, followed by deposition of the MnO2 nanosheets using hydrothermal decomposition of KMnO4. It was shown that the diatomite@TiO2@MnO2 electrode exhibits larger specific capacitance, better rate capability, lower resistance, as well as long cyclic stability, and a high coulombic efficiency in comparison with literature data on MnO2 capacitors. This is because the deposition of TiO2 on porous diatomite represents the appropriate highly aligned substrate with open-pore channels for improved electronic transport of MnO2, thus increasing the specific surface area and enhancing the electrical conductivity of diatomite. At the same time, MnO2 ensures a high surface for contact with ions in the electrolyte.
Diatom coated nanocomposite materials have been widely studied for potential applications as photocatalysts.48,53,98,120,146–149 Among the many materials reported, diatomite coated with nanosized semiconducting TiO2 particles has been extensively used as a photocatalyst. In the study by Jia et al.,146 TiO2 was deposited onto the diatomite by employing layer-by-layer (LbL) assembly method, which is based on the electrostatic interactions between oppositely charged surfaces. The pre-calcined diatomite was firstly immersed into a colloidal solution of TiO2, followed by filtration and rinsing with distilled water and then the immersion of the derived product in phytic acid, which served as a molecular binder which was subsequently removed by thermal treatment at 400 °C. The obtained results demonstrated the uniform distribution of TiO2 nanocrystals with a size of ca. 5–10 nm. The surface area and volume of mesopores increased with an increasing amount of the deposited TiO2 which strongly depends on the number of deposition cycles. The TiO2–diatomite hybrid structure prepared by the LbL method represents promising candidature of such a route for photocatalytic applications.
He et al.147 used HCl-treated diatom cells as a template to obtain TiO2-coated SiO2 photocatalyst. In this study, titania-coated diatom frustules were prepared by immersing cleaned frustules in a vessel containing 5% titanium tetraisopropoxide (TTIP) in isopropanol for 24 h with subsequent calcination treatment at 773 K in air to remove residual organic parts. X-ray fluorescence (XRF) measurements confirmed the preservation of SiO2 and carbon contained in diatom cells which was self-doped into this structure upon treatment with the calculated molar ratio of Ti, Si, and C 8
:
1
:
4. According to the FTIR spectra, diatom-templated TiO2 consists of matrix-isolated TiO2 layers on silica frustules' surface while TEM images revealed the fine hierarchical structure of such a composite, where the diameter of a titania nanoparticle was approximately 10 nm. Due to biomorphic hierarchical structures, TiO2 coating, and carbon doping, a higher absorbance in the visible region and an improved photocatalytic efficiency was obtained for the photodegradation of rhodamine B under visible-light irradiation in comparison with the commercial Degussa P25 TiO2.
Another approach for preparing TiO2/diatomite composites for photocatalytic applications is demonstrated by Wang et al.148 TiO2 was immobilized on diatomite by adding dropwise tetrabutyl titanate (TBOT) as a precursor into the diatomite suspension under stirring. The subsequent addition of ethanol–water solution led to the hydrolysis of the TBOT at a moderate rate followed by stirring for 12 h, oven drying at 105 °C and calcination at 450–950 °C for two hours in the air. XRD results showed an increase in crystallite size and content of the rutile phase with the increase in calcination temperature. TiO2 nanoparticles with an average size in the region of 15–30 nm were uniformly distributed on the diatomite surface. TiO2/diatomite composites with a 90/10 mixing ratio of anatase/rutile phase, calcined at 750 °C for two hours, showed the best results of the photocatalytic degradation of Rhodamine B under UV-light. The photoactivity of the catalyst is mostly affected by calcination temperature but also depends on the crystalline size and anatase/rutile ratio.
The photocatalytic performance of TiO2-functionalized diatom samples for indoor air purification was evaluated by Ouwehand and colleagues.149 Acid-treated and calcined diatom frustules were added to the dissolved titanium(IV) oxysulfate–sulfuric acid hydrate, and the mixture was stirred and heated until all the liquid evaporated followed by calcination in air at 500, 550, 600, and 650 °C for 3 or 6 h using different precursor ratios. XRD analysis showed that the only crystalline phase present in the calcined samples is anatase with no rutile phase observed at calcination temperatures of 550–650 °C. It was also demonstrated that the silica substrate limited the nanoparticle growth and effectively thermally stabilized the TiO2. The sample with 18.2 wt% titania loading, calcined at 550 °C for three hours showed 2.5 times higher catalytic activity in the decomposition of gaseous acetaldehyde in comparison with the P25 TiO2 due to a smaller particle size of the active anatase phase and a stabilization of the titania particles on the silica surface. Titania-functionalized samples showed promising results in realistic conditions for the purification of indoor air as well.
The Cu2O–ZnO/diatomite composite was also reported as a potential photocatalyst in the treatment of red water from TNT manufacturing.150 The sulfuric acid-treated diatomite was added to the mixture of zinc chloride solution with different concentrations (0.05 M, 0.1 M, 0.2 M, and 0.3 M), 1 M sodium potassium tartrate, and 5% (w/v) polyvinyl pyrrolidone. Zinc oxide was deposited on the diatomite surface upon heating of this mixture to 95 °C. The next step was immobilization of cuprous oxide by adding 0.5 M copper sulfate and 1 M reductant glucose, stirring, and heating with subsequent drying of the precipitates. According to the results, the photocatalytic performance of such composites depends on the concentration of zinc oxide. The optimal optical properties and photocatalytic activity were achieved in the sample with the molar ratios of ZnO versus Cu2O 4
:
2.5 since the degradation rate of red water was 72.8% after illumination by visible light for 4 h.
Fang et al.151 investigated a highly efficient solar vapor generator obtained by the deposition of Ag nanoparticles on diatomite using a chemical plating process. Diatomite treated with a mixture of concentrated H2SO4, and H2O2 was added into a 2.3 wt% SnCl2. After stirring and rinsing with distilled water, the sample was mixed with silver–ammonia solution and C4H4O6KNa·4H2O to finish the chemical plating process. Ag/diatomite composite combined with a filter paper, an air-laid paper, and a polystyrene foam showed excellent vapor generation performance under one-sun illumination at room temperature due to the synergy of the localized surface plasmon resonance (LSPR) effect of Ag nanoparticles and the confinement effect in porous micrometer sized diatomite.
Wet chemistry syntheses are efficient ways to structure new materials and prepare hybrid products using diatomite as the base component. These wet chemistry processes end up depositing a material on diatomite just like the deposition method discussed earlier. These techniques have shown that the processes efficiently yield positive outcomes. Also, they are quite straightforward and environmentally friendly. Future works that may consider these techniques could focus on processing parameters such temperature and time on the overall properties. Note here that the DE samples used in these works were in purified form.
4.5 Displacement reactions
The quest to produce nanostructured materials has witnessed a number of new synthesis techniques.152–156 Among the many interesting techniques, metallothermic reduction reaction (MRR), a type of displacement reaction has gained a lot of attention. A mini review by Xing et al. provides a historical view of the process and highlights current trends using this technique.157 This displacement reaction type employs highly reactive metals to produce a wide range of products from stable compounds such as oxides, sulfides and halides.158–161 Materials obtained from MRR are metals, alloys and composites.157 Typical reactive elements used in MRR are lithium, sodium, magnesium, aluminum and intermetallics like Mg2Si for the reduction of oxides and sulfides.158–161 Aside MRR, a number of reduction methods are known to the scientific community. Most popular among them are the carbothermal process and the electrolytic process.162,163 It is through one of these routes (carbothermal process) that the metallurgical grade of silicon is produced. This technique involves the use of a carbon source where reaction temperatures can go as high as 2200 °C.164 Although useful for commercial production of high purity silicon, the carbothermal process is not highly regarded as the best approach to achieve silicon nanostructuration. This high temperature process poses a huge concern for silicon-based materials with nano-scale morphology. At high temperatures, particles may agglomerate and pores may disappear. For these reasons, MRR is highly touted as an appropriate route to reduce diatomite to nanostructured silicon-based materials for energy applications. In recent times, a number of different modifications to this technique have been reported, giving rise to a conventional and non-conventional MRR.
4.5.1 Conventional MRR. Ever since Sandhage et al.165 reported on the use of Mg vapor to reduce diatom frustules to porous silicon, several groups have also reported on the synthesis of silicon nanostructures such as nanocrystals,166 nanoporous films,167 porous silicon168 and 1D nanostructures169,170 from the same metallothermic reduction reaction. Most of these publications have focused on magnesiothermic reduction reaction, often referred to as MRR. Apart from magnesiothermic reduction reaction, other potentially interesting processes are aluminothermic reduction reaction and silicothermic reduction reactions.171–179 Metallothermic reduction reactions, based on the reductant, offer a rather lower synthesis temperature to producing new materials and high purity products. The criteria for selecting a particular processing route when it comes to diatomite are always influenced by the ability to preserve the morphology. This definitely makes MRR a better candidate over carbothermal reduction. Even though MRR is suitable, a number of factors are crucial for effective control of the morphology. In an excellent review by Entwistle et al.,180 the parameters which affect the size and structure of the silicon-based material were addressed, although very little attention was given to pre-treatments such as calcination and ball-milling. In their review, the following reaction conditions were reviewed; reaction temperature, reaction time, crystallite size, ramping rate, reaction ratio, powder mixing and heat scavengers. The summary of their study is presented in Fig. 10 (ref. 180) and shows the critical reaction conditions at various stages of the synthesis process. Lately, a new trend in MRR181 used purposely for structural control has caught the attention of many.182–185 Albeit MRR being suitable over the conventional carbothermal reduction process, structural control is not a guarantee. The amount of heat released in this highly exothermic reaction raises the temperature of the system to temperatures significantly higher than the actual experimental temperature. This poses another concern which was recently tackled through the use of inorganic salts. The pioneering work of Batchelor et al.181 revealed the role of salt as a thermal moderator in the highly exothermic reduction reaction using magnesium vapor. Following this great lead, a number of works centered on diatomite made use of inorganic salts to complement the already favored MRR process.36,112,182–185 In all these reports, the reductant used was magnesium. The ready availability, low cost, low toxicity and low melting temperature make magnesium the most preferred reductant among the lot. On the contrary, a recent study by Lai et al.175 showed huge structural changes and damage to morphology with the use of Mg even though it proved to be an effective reducing agent below its melting point. Aluminum, however, was an effective reducing agent at its melting point or above and offered a better structural and morphological control as compared to Mg. The improved structural control was attributed to the presence of alumina, which enhances the mechanical properties of the product silicon. It was also reported that calcium was an ineffective reducing agent for silica. Due to this, Lai et al.175 suggested a reducing mixture of 70% Mg and 30% Al which could offer the least amount of morphological damage and present a lower temperature than that required when using Mg or Al individually. This recommendation coupled with thermal moderators in the form of inorganic salts could help address the challenges faced with MRR. MRR is well-known in diatomite nanotechnology as a means to obtain pure elemental silicon or other silicon-based materials. Applications where MRR was selected as the synthesis route include both energy harvesting and storage technologies. These are battery anodes, thermoelectric generators, nano-Si coating on Si based solar cells and design of electrodes for supercapacitors. In a study by Shen et al.,186 Si was synthesized from diatomite using the MRR route. A porous Si powder with pore size identical to that of the precursor diatomite powder was obtained after magnesiothermically reducing the precursor powder at 650 °C for 6 hours as shown in eqn (1). The centric diatom frustule described in their work as a sunflower was damaged after the MRR and subsequent HCl washing while the powder particle size decreased from 25 μm to 10 μm for both precursor diatomite and obtained porous silicon respectively. Also, an increase in the surface area of the diatom-based silicon (96 m2 g−1) and original DE with surface area of 6 m2 g−1, a requirement for most energy applications was reported. In addition to the native nanopores inherent to the precursor diatomite, mesopores were found in the porous silicon powder. This, they attributed to the formation of MgO and the subsequent washing with HCl varied significantly. Albeit the sunflower shape of the frustule not being preserved, the porous structure remained almost the same, suggesting MRR as an efficient approach to retain the porous structure of DE. To obtain pure silicon after the MRR, HCl is frequently used to dissolve MgO and further rinsing with deionized water. In quite a number of works,36,112,182,183 HF was used following HCl washing to dissolve all unreacted silica as a way to obtain pure Si. In the work of Shen et al.186 only HCl was reported, suggesting an eco-friendlier approach but also accounting for the traces of unreacted silica in the porous silicon powder as detected by Raman spectroscopy. However, in a later work,187 the possibility to fully reduce diatomite to silicon was demonstrated. The protocol used was almost the same with the exception of an adequate powder mixing made possible through ball milling. The powders prior to the MRR process were ball milled at 350 rpm for 5 hours to decrease the particle size of diatomite and obtain a homogenous mixture. This additional step may have provided more reaction sites, promoting full reduction of diatomite to silicon. The high purity silicon obtained possessed a high specific surface area (131 m2 g−1) compared to the as-purchased diatomite (1 m2 g−1) due to the small particles size (less than 2 μm) and porous structure (10–70 nm). In a similar work by Wang et al.,44 a porous silicon powder was obtained after magnesiothermically reducing a purified diatomite powder. This diatomite powder was purified prior to the MRR process. Apart from the purification process, the protocol was almost the same as reported by Shen et al.186 Aside the retained mesopores and macropores retained from the diatomite powder in the product silicon powder, there was an increase in micropores after the MRR process. The use of an inorganic salt for scavenging excess heat produced from the MRR of diatomite was reported by Luo et al.182 In their work, the use of NaCl resulted in a product silicon with cylindrical architectural features retained from the precursor diatomite. This particular trend has been reported in a number of studies,36,112,183–185 suggesting an effective way to control the overall temperature in the MRR. This high purity silicon had a rough surface occupied with ultrafine Si particles (⋍10 nm). In a more recent work by Zhang et al.,60 a Si/SiO2 composite was synthesized via MRR. Here, the effect of the reaction time during MRR on the phase composition of the reaction product was explored. Reduced reaction time is reported to lead to optimal ratio between the formed silicon and DE based silica. Most importantly, aside from the possibility to create a Si/SiO2 composite, Zhang et al.60 report that increasing reduction time had significant effects on the specific surface area of the diatomite-silicon sample (D-Si). The specific surface area increased from 78 (D-Si-2 h) to 14 8 m2 g−1 (D-Si-6 h) when the reaction time was increased from 2 to 6 hours which could be attributed to the removal of organic moieties and a subsequent creation of mesopores during the reduction reaction. On the other hand, a decline in the specific surface area was observed after further increase in reaction time to 10 hours. D-Si samples reduced for 10 hours had a specific surface area of 85 m2 g−1. This decline was attributed to an increase in the crystalline silicon domain and a possible collapse/widening of the pores after a prolonged reduction. D-Si-6 h (diatomite-silicon-reaction time of 6 h) sample showed an optimal ratio of crystalline Si domains embedded within
the amorphous SiO2 matrix. All the D-Si samples synthesized in their work showed small (≈10 nm) and large pores (≈30 nm), signifying a hierarchical structure. The D-Si-6 anode showed almost the same morphology as the precursor diatomite which had the potential to enhance electrolyte diffusion inside the bulk electrode and as well limiting the volume changes in Si during charge/discharge cycles. Interestingly, as the Si domains provide lithium storage capacity, the amorphous SiO2 matrix provides stability. This synthesis approach by Zhang et al.60 offers greater control of the outcome of MRR, leading to the development of other potentially applicable anode composites. Not only has conventional MRR dominated the scientific headlines, it has also led to the introduction of other facile synthesis routes, also referred to as non-conventional MRR.
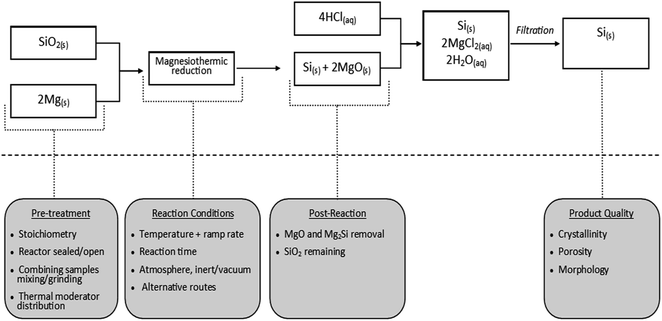 |
| Fig. 10 Flowchart of the magnesiothermic reduction reaction and the key design parameters at specific stages.180 | |
4.5.2 Non-conventional MRR. A number of non-conventional MRR have been reported.188,189 In a study by Wu et al.,188 SiOx was produced via the magnesio-mechanochemical reduction reaction of diatomite. The partial reduction by magnesium was induced by high powder milling which led to a highly porous SiOx powder after HCl purification. Wu et al.188 demonstrated the possibility to use mechanical milling to promote MRR in the presence of magnesium termed as Magnesio-Mechanochemical Reduction process (MMR). Unlike the aforementioned displacement reactions which require somewhat high reaction temperatures (650–900 °C), this approach did not require an external heat source. As compared to the majority of the previously reported MRR routes, the MMR process reported by Wu et al.188 offers the easiest, cheapest and simplest synthesis route to produce silicon-based anode materials from diatomite. The resulting diatomite-based anode (MMRD_Si indicating magnesio-milling reduced diatomite_Si) exhibited desirable powder characteristics for optimum batteries, markedly an enlarged Brunauer–Emmett–Teller (BET) surface area (from 25 m2 g−1 for the DE to 134 m2 g−1 for MMRD_Si) and a simultaneous increase in pore volume in the likewise manner (0.02 cm3 g−1 to 0.10 cm3 g−1). The MMRD_Si anode, identical to the SiO2/Si network reported by Zhang60 consisted of SiO2 nanodomains with highly crystalline Si domains in the ratio 51.4%, 48.6% respectively. Such a system, otherwise known as SiOx, has been identified as a better candidate than pure silicon. The highly desired silicon oxide (SiOx) is best described as nano-sized clusters of SiO2 and Si with suboxide-type interface190 and reportedly show the smallest volume changes (160%) in comparison with SiO2 and Si191 upon lithiation. The derived MMRD_Si anode without C-coating, showed excellent cycling stability up to 2000 cycles with a capacity retention of 71.3% after cycling at 4 A g−1. Wu et al.188 attributed the exceptional electrochemical performance of the anode to factors including the presence of both nano-sized Si domains and retained SiO2 at the nanoscale and the intrinsic porous structure, all of which contribute synergistically to the properties of MMRD_Si anode. Another type of a non-conventional reduction process was demonstrated by Liang et al.189 Described as deep reduction and partial oxidation, this process relies on the use of excess Mg which favors the formation of otherwise unwanted by-product (Mg2Si) as the main product as depicted in the reaction in eqn (2), with by-product MgO and unreacted Mg. The product Mg2Si is further oxidized, yielding both Si and MgO is shown in eqn (3). This synthesis route ensures a full reduction of the starting silica powder and thus requires no HF purification to wash unreacted DE. This could potentially increase the silicon yield. Aside from the yield, a silicon product with nanostructure identical to the parent DE was formed. A major concern for this approach is the in situ oxidation of silicon produced from Mg2Si. According to Liang et al.189 via a controlled annealing temperature, no significant formation of SiO2 was observed. Even though the oxidation rate of Si by O2 at the partial oxidation process is slow, a thin layer of SiOx was formed around the product silicon. |
4Mg + SiO2 → Mg2Si + MgO + unreacted Mg
| (2) |
|
Mg2Si + O2 + Mg → Si + MgO
| (3) |
Even though the conventional and non-conventional MRR appear somewhat less expensive to use and eco-friendly compared to other complex synthesis routes, they still have not reached a full scale commercialization due to issues such as yield and less control over outcome of synthesis. Diatomite has seen extensive research involving displacement reactions because it is the most suitable, cheapest and eco-friendliest precursor for silicon-based materials with nanoscale morphologies. Undoubtedly, displacement reactions lead to a wide range of possibilities and significant modifications in this area could potentially bridge the gap between current state of progress and commercialization. Tuning the parameters of MRR has also shown incredible results. Crucial among the list of tunable parameters are the reaction time and molar ratio as reported by Liang189 and Zhang et al.60 Further studies of these approaches could lead to a more controllable synthesis process.
Although synthesis processes delivered interesting DE-based materials that led to significant breakthroughs in their respective areas of application, a number of challenges remain that require further attention and improvement. The advantages and disadvantages of these synthesis processes are summarized in Table 2.
Table 2 Merits and Demerits of the main synthesis processes
Main synthesis process |
Merits |
Demerits |
Impregnation technology |
1. Eco-friendly, low cost and facile synthesis |
1. Requires unclogged and undamaged frustules |
2. Purely physical interaction between precursors maintains a high purity PCM |
2. Extra vacuum system may be required to achieve maximum encapsulation |
3. Suitable for a wide range of PCMs |
Deposition and etching |
1. Less time required for large scale production |
1. Requires a complex set-up and expertise |
2. Uniform and homogeneous coatings of new material produced |
2. Could require high synthesis temperatures |
3. High purity DE-templated materials produced after etching |
3. High cost of synthesis |
4. Unbroken frustules needed |
Wet chemistry synthesis |
1. Fast and facile approach to immobilizing new materials on DE |
1. Unbroken frustules needed |
2. No complex set-up required for synthesis |
2. Large scale synthesis may require more time |
3. Relatively low synthesis temperatures |
3. Relatively low quality coating compared to vapour deposition routes |
Displacement reactions |
1. Relatively lower synthesis temperature as compared to carbothermal reduction of SiO2 |
1. Highly exothermic reaction could raise the local temperature beyond the set temperature and offer less control over reaction outcome |
2. A wide range of products and composites possible; Si, Si/SiO2, Mg2Si, Si/Mg2Si and MgO when Mg is the reductant |
2. Contamination of product such as Si due to difficulty etching or rinsing by-products (mostly Mg2Si and MgO) |
3. Reductant such as Mg and Al are cheap and readily available |
3. Low structural control |
5. Energy storage applications
The potential application of diatomite in the energy industry covers a broad spectrum of energy storage systems. Here, a summary of previous and current progress made with the use of diatomite in energy storage systems are briefly discussed.
5.1 Thermal energy storage (TES)
Following the thorough review of processing techniques to preserve the highly porous and desirable structure of DE, this section provides up-to-date review of literature that incorporates DE as a supporting material for PCMs. In earlier sections, latent heat storage derived through PCMs was determined to be highly efficient amongst the categories of TES where the effectiveness of such TES with PCM has been attributed to the large storage density and narrow temperature variation during the charge–discharge process. Thus, PCMs play a critical role in thermal energy storage capacity where earlier works have classified PCMs as organic or inorganic.192 Albeit PCMs being effective instruments for thermal energy storage, the works of Sarier et al.192 and Zhang et al.193 have shown leakage during solid–liquid phase changes as a major hindrance that limits the applications of PCMs. To overcome this, several approaches have been used to generate composite PCMs. Not too long ago, Jeong et al.194 proposed the incorporation of porous diatom silica as an alternate approach to realizing light-weight and economical PCMs for thermal energy storage.
Following this proposal, Xu and Li89,195 prepared paraffin/diatom; paraffin/diatom/MWCNT and Li et al.76 prepared diatom/paraffin composite PCMs which showed enhanced performance. In the case of the paraffin/diatom/MWCNT PCM, a melting temperature of about 27.12 °C and a latent heat of 89.4 J g−1 were realized. Through a vacuum impregnation route, Jeong et al.72,194 successfully formed PCM/diatom composites and obtained a latent heat storage of 61.96 J g−1 at 54.2 °C. Sun et al.73 obtained a latent heat storage of 89.54 J g−1 at a transition temperature of 33.04 °C for a paraffin/diatom composite PCM. Xu and co-workers also successfully produced paraffin/diatomite composite PCM which had a melting temperature of 41.11 °C and latent heat storage of 70.51 J g−1.74 Li et al.76 formed a form-stable diatomite/paraffin PCM for energy storage using different grades of diatomite particles. So far, the few studies that have considered composite PCMs based on paraffin/diatom have shown great potential. Recently, Zhang et al.,90 used an oleophobic surface modification on diatomite in a paraffin/diatomite composite PCM and reported an enhancement in the latent storage capacity as well as the melting temperature (Table 3). They reported an encapsulation ratio of 84.5% for the paraffin/diatomite composite, suggesting a high efficiency in the impregnation of paraffin into diatomite. However, a noted trend for all the studies undertaken suggests that high phase change temperature/melting temperature results in lower latent heat storage capacity. Furthermore, paraffin has proven to be a major component for PCMs based on paraffin/diatoms but the arduous processes involved in their preparation continues to remain a concern especially when such methods are only applicable at the laboratory scale. In an attempt to overcome the challenge of laboratory scale production, Konuklu et al.75 proposed a direct impregnation method that required no pre-treatment of diatoms and capable of being fabricated on a large scale. Their work showed that for the preparation of PCM nanocomposites based on diatom/paraffin, the direct impregnation method yielded positive results without any chemical reaction between the diatomite and paraffin. It was also shown that the PCM filled the pores of frustules with phase changes occurring within the nanopores. Further studies could concentrate on finding a blend of high storage capacity at high temperatures and also explore the potential of other processing routes.
Table 3 Thermal properties of reported PCMs based on diatomite and other material constituentsa
PCM |
Melting temperature (°C) |
Latent heat storage (J g−1) |
Reference |
LA = lauric acid; SA = stearic acid; PA = palmitic acid, CA = capric acid; EG = expanded graphite; CNT = carbon nanotube; GnP = graphene nanoparticle; MWCNT = multi wall carbon nanotube, Dm = microwave-acid treated diatomite. |
n-Hexadecane/diatomite |
23.68 |
120.1 |
192 |
n-Octadecane/diatomite |
31.29 |
116.8 |
192 |
Paraffin wax/diatomite |
54.24 |
61.96 |
192 |
Hexadecane/diatomite/xGnP |
22.09 |
120.8 |
72 |
Octadecane/diatomite/xGnP |
30.2 |
126.1 |
72 |
Paraffin wax/diatomite/xGnP |
54.87 |
63.77 |
72 |
Paraffin/diatom/MWCNT |
27.12 |
89.4 |
89 |
Paraffin/calcined diatomite |
33.04 |
89.54 |
73 |
Paraffin/diatomite |
36.55 |
53.1 |
75 |
Paraffin/diatomite |
45.70 |
114.21 |
90 |
(Liquid paraffin + n-octadecane)/Opal |
24.91 |
59.04 |
82 |
Paraffin/diatomite particle |
41.11 |
70.51 |
74 |
Polyethylene glycol/diatomite |
27.7 |
87.09 |
43 |
LA-SA/Dm/EG |
31.17 |
117.3 |
87 |
Methyl stearate/diatomite |
36.5 |
111.8 |
86 |
Capric acid/diatomite |
34.9 |
89.2 |
132 |
Palmitic acid/diatomite |
63 |
88 |
134 |
(SA + PA)/diatomite |
52.93 |
106.7 |
139 |
CA-LA/diatomite |
23.61 |
87.33 |
80 |
CA/diatomite/CNT |
31.38 |
79.09 |
133 |
In other works, the potential of other forms of diatomite based PCM composites have been explored. Nomura et al.77 used erythritol/diatomite and obtained a latent heat of up to 70% of the theoretical value. Li et al.78,79 fabricated shape-stable fatty acid/diatomite composite PCMs for thermal energy storage. The study revealed that the latent heat of capric–lauric acid/diatomite PCM decreased by 57% relative to the latent heat of capric–lauric acid while a slight increase in phase transition temperature was recorded. The drop in latent heat was attributed to the reduction in percentage of capric–lauric acid. Sarı and Biçer81 studied the potential of fatty acid ester/building material as potential form-stable PCMs. By infusing galactitol hexa myristate (GHM) and galactitol hexa laurate (GHL) esters into porous networks of diatomite, perlite and vermiculite, they were able to optimize the thermal durability above the working temperature range of the monolithic materials. Karaman et al.43 used polyethylene glycol (PEG)/diatomite to make PCMs. They obtained a latent heat storage of 87.09 J g−1 at a melting temperature of 27.7 °C. Qian et al.139 prepared PEG/diatomite composites via vacuum impregnation and obtained the highest impregnation of PEG into diatomite. For a diatomite pre-treatment using NaOH leaching, a 70 wt% impregnation was recorded while for nano-silica decorated pre-treatment an impregnation ratio of 66 wt% was obtained. Subsequently, latent heat storage and melting temperatures were 127.0 J g−1 at 58.75 °C and 120.2 J g−1 at 57.96 °C respectively.
Through microwave-acid treatment of diatomite and the introduction of expanded graphite, Li et al.87 simultaneously enhanced the volume of lauric acid–stearic acid (LA–SA) content impregnated into diatomite matrix and the thermal conductivity of the composite PCM. Comparing the LA-SA/Dm/EG to LA-SA/Dm and LA-SA/D, a 54% and 98.6% increase in the latent heat storage was respectively recorded. Here, Dm denotes microwave-acid treated diatomite while D denotes raw diatomite. Konuklu et al.88 also reported improvement in storage capacity after modifying diatomite by subjecting the diatomite to microwave radiations in a home-style microwave at 700 W. A recent work by Huang et al.196 which used an artificial culture method to generate PEG/diatomite composites exhibited high latent heat values. For the melting and crystallization processes, 121.54 J g−1 and 127.20 J g−1 were respectively obtained for the latent storage of PEG/sintered-diatom composite with an improved enthalpy efficiency of about 98.1%. The enhancement in latent storage was attributed to the high absorption and improved phase interface.
Table 3 summarizes reported properties of PCMs based on paraffin and other materials. As evident from the work of,72,194 it is observed that the incorporation of nanoparticles into already existing composite PCMs results in no significant property enhancement while PCMs containing higher constituent volume result in pronounced decline in the melting temperature. Thus, to ensure effective diatomite based PCMs, the composite constituents, method of production and volume fractions are key parameters to be considered. It is seen from these reports that the PCM composites with fatty acids compared to paraffin based PCMs possess high latent storage density but the rather high melting temperature limits their applications in buildings. Thus, for full potential of fatty acid based PCMs, future works must concentrate on lowering the melting temperature hence sustaining the high latent storage ability.
The 3-D network structure offered by DE has proven to be an effective template/building block for the optimization of thermal energy storage capacity. However, with the increasing demand for high performing energy materials, it can be inferred from the presented literature that the full potential of the DE is yet to be realized. Thus, to reap the full benefits, future works need to focus on process optimization, powder/particle size effect as well as further stabilization of properties.
5.2 Supercapacitors
Considered as the next-generation energy saving technology, supercapacitors have been widely studied.45,50,51,99–101,103 Supercapacitors offer a high energy density, a sustainable cycling life, excellent cycling stability and fast charging/discharging rates. Transition metal oxides (TMO), studied in recent times due to their superior specific capacitance over counterpart carbonaceous materials and conducting polymers have a number of setbacks stalling their commercialization. Typical among these setbacks are low electronic conductivity, low ionic diffusion constant, and structural susceptibility.197,198 Among the many transition metal oxides studied (CuO, TiO2, MnO2, RuO2, NiO, NiCo, Fe2O3, FeOOH, MoO3, V2O5, MoS2 and Co3O4),100,144,199–202 MnO2 is reported to be the most promising due to their low fabrication cost, high specific capacitance (theoretical capacity is 1370 F g−1), abundant availability, environmental compatibility, and a high cyclic stability in alkaline/neutral media.203,204 Highly porous templates have been identified as a solution to these setbacks,57,205 most especially DE, due to the recent attention it has received. The first attempt to create diatom frustule inspired MnO2 was made by Zhang et al.45 Apart from MnO2, diatom frustule templated NiO have also been studied due to their chemical/thermal stability, high specific capacitance, lower cost, eco-friendly nature and ready availability.206,207 Despite these competitive properties, the full implementation of NiO as a material for supercapacitors is stalled by their low ionic diffusion constant and structural instability.208,209 In a comprehensive review by Sun et al.57 and a chapter by Zhang et al.205 earlier reports of modifications of MnO2 and NiO have been discussed in full details. In recent times, a lot of progress has been made with templating new materials especially TMO. Yang et al.,100 for the first time applied diatom frustule templating to synthesize a porous MoS2/a-C (amorphous carbon) composite. The MoS2/a-C composite showed high specific capacitance (167.3 F g−1 at 0.5 A g−1), high-rate capability (96.4 F g−1 at 10 A g−1) and excellent cycling stability (93.2% retention after 1000 cycles) as shown in Fig. 9.100 These great results were partially due to the well-defined microstructure inspired by the diatomite frustules, with the amorphous carbon playing an equally important role. It is reported that a combination of pores of different sizes for ion-buffering reservoirs causes an increase in the diffusion rate of ions within the porous electrode material. Undoubtedly, the high surface area of diatomite also inspired a specific surface area and nanoscale size of MoS2. This eventually leads to a substantial decrease in the diffusion lengths for ions and electrons which ultimately improves the capacitive performance. A cost effective and facile one-step hydrothermal process of synthesizing 3D porous structures of NiCo layered double hydroxide (NiCo LDH@DE) was reported by Jing et al.144 Common to most of the reports is the ability of DE to provide a nanoscale morphology suitable for the prevention of agglomerates and reduced volume changes during cycling. Apart from diatomite proving crucial in the overall performance of NiCo LDH@DE, the molar ratio is reported to have a huge impact on the structure of NiCo LDH on diatomite. Jing et al.144 reported that based on the molar ratio used, the morphology of the NiCo LDH could change from nanowires to nanosheets, thus eventually improving the electrochemical performance due to an enlarged surface area. The nanosheet morphology was obtained by increasing the Ni2+ concentration, since higher concentrations of Co favors the formation of nanowires. The porous Ni3Co1 LDH@DE reportedly showed ultrahigh specific capacitance of 514 F g−1 and an excellent capacitance retention (94.2%) after 5000 cycling tests. The combined effect of the porous structure and the nanosheets were credited for the impressive electrochemical properties of NiCo LDH@DE. Another interesting work involving the use of diatomite was reported by Jiang et al.104 Their as-synthesized η-Fe2O3/diatomite composite showed good capacitance retention of 73.92% after 1000 cycles. Their composite also showed good cycling stability coupled with a high reversibility during a repetitive charge–discharge cycling. These properties were attributed to the unique morphology of the composite characterized by a high surface area and a high porosity.104 The as-formed η-Fe2O3 decorated both the outer and inner surface of diatomite and this could have potentially led to more active sites to enhance electrochemical reaction. In a more recent work focusing on MnO2, Le et al.101 demonstrated the use of diatomite as a bio-template for the production of three-dimensional (3D) porous graphene for both supercapacitors and oxygen reduction reaction catalysts. After further doping and deposition of the porous graphene with nitrogen and MnO2 nanosheets respectively, a hybrid N-doped 3D graphene@MnO2 (N-G@MnO2) was obtained. The porous N-G@MnO2 showed a high specific capacitance (411.5 F g−1) coupled with a good cycling performance (88.3%) after 4000 charge and discharge cycles. The excellent results were partly due to the N-doped graphene, MnO2 nanosheets and the porous structure triggered by diatomite. Indeed, the porous structure was reported to provide a good contact between the electrode and the electrolyte, resulting in an improved ion transfer and decrease in the contact resistance. Additionally, the porous structure of the N-doped graphene ensured a uniform distribution of the MnO2 nanosheets on the surface. This prohibits aggregation during charging/discharging reactions. Hu et al.105 recently reported the progress made using diatomite template to create a MnO2@CNTs/G/diatomite hybrid. Their hybrid exhibited a high specific capacitance (264.0 F g−1) and excellent cyclic stability partly due to the enlarged surface area of the 3D framework provided by DE for the optimum loading of MnO2 without compromising the electrolyte infiltration and diffusion and thus having no adverse effects on electron and ion transfer. Also, DE primarily provided a platform to form 3D porous graphene. This porous graphene inspired by diatomite allowed for the immobilization of the metallic seeds used for the decomposition and in situ growth of the vertically aligned CNT. This eventually resulted in a conductive network which was reported to enhance electron transfer and increase active surface area. Li et al.145 demonstrated the effectiveness of diatomite templating in the supercapacitive properties of diatomite@FeOOH/conductive polypyrrole (D@FeOOH/PPy). In their work, a double shell FeOOH/PPy on DE was synthesized via two-step hydrothermal method and in situ polymerization routes. Although the improved electrochemical properties of D@FeOOH/PPy compared with D@FeOOH were hugely attributed to PPy nanoparticles, the use of diatomite played a crucial role for the latter to excel. Already stated from previous reports,100,101,104,105,144 DE primarily provided a highly porous structure which sufficiently exposed the PPy nanoparticles. This led to shortened ionic transport path and diffusion time, thus accelerating the electrolyte ion transport during charging/discharging cycles. The as-synthesized D@FeOOH/PPy electrode showed a high specific capacitance (417.8 F g−1) and a good capacitance retention (80.6%). The inclusion of DE in the electrode materials for supercapacitors have demonstrated huge potentials to improve the efficiency of already existing electrode material and most importantly allow for a cost effective and eco-friendly way to optimize electrode materials. To fully realize this, facile synthesis processes, with the ability to synthesis in large yields need to be developed.
5.3 Battery technology
Battery materials, especially anodic components have attracted the most attention involving the incorporation of diatomite in their synthesis. Over the past few years, a number of researchers working with silicon-based anode materials have included this silica type in their synthesis protocols.49,59,60,62,63,111 The choice of this siliceous component is justified by earlier recommendations to produce silicon-based anodes with nanoscale morphologies capable of remedying setbacks with their bulk counterparts.22,210 As the only naturally occurring siliceous material with attractive nanoscale morphology, DE presents a pathway to obtain nanostructured silicon based anodic materials or templates for other potential ones. Such anode types are highly preferred over carbon-based materials, transition metal oxides and other alloys due to a combination of superior electrochemical properties, cost and environmental factors.211 These interesting characteristics have not translated into rapid commercialization due to the large volume changes (up to about 300%) during charging/discharging cycles observed for silicon-based anodes from bulk silicon.22,27 Such volume changes cause strain-induced crumbling and eventually lead to discontinuities rendering the anode ineffective in carrying charges to current collectors. Ever since this setback was identified, several silicon nanostructures have been reported including silicon nanosheets,212 nanowires,22 nanospheres213 and nanotubes214 which have birthed several comprehensive reviews.215–217 Recently, a large number of groups have focused on DE, as it provides a ready nanoscale morphology for the synthesis of nanostructured silicon-based materials. The increasing number of reports in this area has in the recent past prompted excellent reviews by Sun et al.57 and Jeffryes et al.55 In both reviews, a detailed report of previous successes obtained for mostly silicon and titanium-based anode materials via diatomite addition is given. Since these reviews, some progress has been recorded in DE-based anode materials for battery applications. Recently, a diatomite-derived hierarchical porous crystalline and amorphous Si-based network for battery anodes was magnesiothermically produced by Zhang et al.60
By adjusting the MRR time (2–10 h, with interval of 2 hours), Si/SiO2 composites of varying characteristics were produced with 10–30 nm crystalline Si domains distributed within an amorphous SiO2 matrix. A Si/SiO2 composite denoted as D-Si-6 (reaction time of 6 h) showed the highest capacity retention (≈80%) after 200 cycles when coupled with a LiNi0.8Co0.1Mn0.1O2 cathode material in a full cell. Also, their D-Si-6 anode showed high discharge capacity (≈1000 mA h g−1), about three times that of commercial graphite anode at 0.2 C without significant capacity decay after 200 charge/discharge cycles. The superior electrochemical properties of their D-Si-6 anode, comparable to reported silicon-based anode materials218–220 was attributed to the heterogeneous (crystalline Si/amorphous SiO2) network as well as the porous structure.
The potential of using “fresh” diatom earth as an anode material was recently reported by Blanco et al.63 In their work, they investigated the electrochemical properties of both carbon (C) coated and uncoated milled diatomite powders. Additionally, the electrochemical properties of pristine diatomite were investigated. It was reported that the uncoated milled diatomite powder (470 nm particle size) showed a higher specific capacity (740 mA g−1) than the pristine diatomite with particle size of 17 μm (575 mA h g−1 after 100 cycles). After a facile carbon coating process, the C-coated milled diatomite showed the highest specific capacity (840 mA h g−1 after 100 cycles). It is almost certain that C-coating will improve the electrochemical properties of milled diatomite due to increased electronic conductivity, however different electrochemical properties observed in the pristine and milled diatomite originate from the increased surface area of the milled diatomite. The milling of diatomite produces powders with ultra-small particle size (470 nm), thus increasing the surface area and eventually reducing the Li-ion diffusion length for optimum electrochemical performance. This places a lot of importance on particle size of materials intended for use as negative electrodes for batteries such as Si, SiGe, SiO2, SiC, Mg2Si, Mg2Si/C etc. It must be noted that even though majority of the published reports have focused on liquid or polymer-based Li-ion batteries, not only these battery types are subjects of studies, a growing interest in all solid state batteries drew attention to diatomite-based anodes for such batteries. In a recent report by Zhou et al.,59 a hierarchical hybrid anode material synthesized from diatomite for an all-solid state lithium metal battery is reported. Their hierarchical hybrid (PEO-SPE/Li–Si) was based on a combination of suitable materials for all-solid state batteries namely; polyethylene oxide (PEO) based solid polymer electrolyte (SPE), lithium metal and silicon obtained from diatomite framework. Lithium metal, even though boasting of superior electrochemical properties is not applicable in liquid or polymer electrolyte-based batteries, due to the flammability of liquid electrolytes and the instability of alkali elements. All-solid state batteries provide the perfect opportunity to use Li metal, allowing for the fabrication of stable solid-state batteries exhibiting superior electrochemical properties. Solid polymer electrolytes combined with Li ion salts enable intimate interface contact and reduce interfacial resistance by providing better flexibility and wettability with Li metal than counterparts inorganic solid electrolytes (ISE).221–223 Moreover, the use of a diatomite framework is to provide a nature inspired hierarchical structure capable of accommodating volume changes and inhibiting dendrite formation. For these reasons, their hybrid anode showed stable Li stripping/plating performance over 1000 h with average overpotential lower than 100 mV without any short circuit. Coupled with a lithium iron phosphate cathode in a full cell, an excellent cycling stability (0.04% capacity decay rate for 500 cycles at 0.5 C) and high rate capability (65 mA h g−1 at 5 C) were obtained. The superior electrochemical performance compared to a lithium foil as demonstrated in Fig. 11,59 was attributed particularly to the 3D Li+ ion-conductive framework provided by diatomite inspired-silicon.
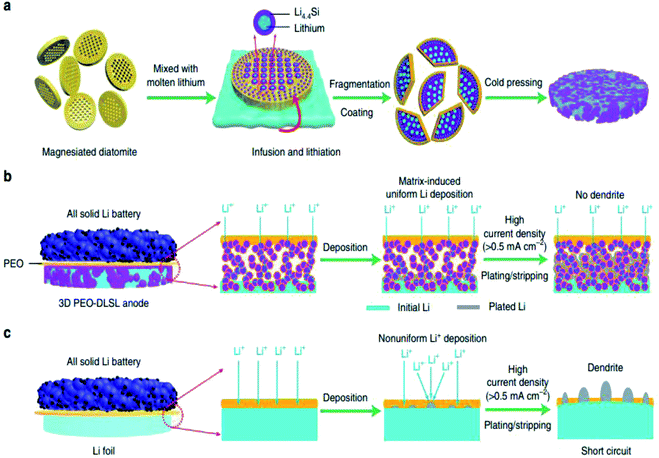 |
| Fig. 11 (a) Flowchart of PEO-DLSL fabrication process and (b and c) mode of lithium stripping/plating in all-solid-state Li metal battery with PEO-DLSL anode and planar Li-foil anode.59 | |
Aside from their use in anode material for batteries, diatomite has recently been studied as a key material in the design of other battery parts, specifically as part of the cathode for lithium sulfur batteries by Li et al.83 Lithium sulfur batteries have been identified as promising candidates for energy applications due to attractive electrochemical properties (theoretical specific capacity 1672 mA h g−1 of sulfur and energy density 2500 W h kg−1), low cost, natural abundance and eco-friendly nature of sulfur.224,225 Nevertheless, there are a number of reported shortcomings,83 and notable among them is the shuttling of soluble polysulfides (Li2Sn, 4 ≤ n ≤ 8) which undermines battery performance over time.226,227 Even though some progress has been reported in this area,83 these solutions are known to be expensive and require complex processing routes. Naturally abundant diatomite presents a good approach to reduce the shuttling rate of the polysulfides due to their excellent chemical stability and sorption ability.228,229 In their work, two composite cathodes were prepared (S-DM-AB) and (S-AB), where sulfur (S), diatomite (DM), and acetylene black (AB) as shown in Fig. 6. The composite cathode with diatomite (S-DM-AB) showed better electrochemical performance (discharge capacity of 531.4 mA h g−1 after 300 cycles at 2 C and a capacity retention of 51.6%) than the cathode without diatomite (capacity of 196.9 mA h g−1 and capacity retention of 18.6% under the same conditions). Prior to the electrochemical measurements the adsorption capability of diatomite and acetylene black for Li2S6 was investigated, with quantitative results showing that diatomite has a higher adsorption capacity (5.31 × 10−2 g g−1) than acetylene black (6.14 × 10−3 g g−1). The addition of diatomite is justified through a significant decline in the diffusion of polysulfides into the electrolyte thus improving the cycling performance. This preliminary result suggests that prior modification of the sorption capability of diatomite via pre-treatments such as calcination, roasting and drying may result in improved adsorption ability for optimum electrochemical performance of lithium sulfur batteries. DE has shown tremendous ability to be fully incorporated in the design of new battery cathode and anode materials and this could be fully realized with the combination of suitable pre-treatments.
6. Energy harvesting applications
The study of diatomite for energy harvesting has equally seen tremendous progress rising from very keen interest by researchers. In this section, a brief summary of recent and previous reports are presented.
6.1 Thermoelectric energy harvesting
Complementing their applications in thermal energy storage, diatomite has recently been studied for their potential applications in thermal energy harvesting (thermoelectrics). Based on the same knowledge of their neat nanoporous structure, diatomite could potentially contribute immensely in developing new materials for thermoelectrics. This area of application has not been addressed in previous reviews54–57 and deserves to be included in the current timeline of diatomite energy related applications. The major classes of materials studied for applications in thermoelectric generators (TEG) are chalcogenide, clathrate, skutterudite, half-Heusler, silicide, and oxide.230 Bismuth telluride and lead telluride, belonging to the chalcogenide, are the most prominent of thermoelectric materials. Chalcogenides in general have a long history of applications as thermoelectrics.230 The desire for low cost and abundant material has led to the recent attention on new material for improved and sustainable thermoelectric energy harvesting. Among these, silicides have received a lot of attention due to their availability and low.230 In order to fully realize the potential of these prospective materials, nanostructuration has been identified as key in their processing.231–235 The requirement for improved thermoelectric properties through this approach places more importance on the versatility of naturally occurring and readily available diatomaceous earth. One material which emphasizes the importance of nanoscale morphologies for thermoelectrics is Si. Silicon, well known for its applications in semiconductors, offers competitive advantages ranging from low cost, easy integration with systems, abundance and low toxicity.236 Even though it is tempting to use bulk silicon as a thermoelectric material, the very high thermal conductivity of silicon remains a concern. Efforts have been made to account for this problem with the likes of silicon nanowires237,238 and nanocrystalline bulk silicon obtained via ball milling.239 Although these efforts present positive results, they are limited by their inability to be integrated on the industrial scale and a high energy consumption. In recent times, porous structures have also been identified as a means to enhance phonon scattering, leading to reduced heat loss through lattice vibrations.240,241 Even though porous silicon produced via anodic etching appears to be a suitable option, porous Si is limited to the micrometer scale and does not affect the bulk silicon material. Based on the requirements for nanocrystalline and nanoporous materials, Zong et al.36 magnesiothermically reduced diatomite to doped silicon for thermoelectric applications. The Sb and B doped nanoporous Si otherwise denoted as n-Si and p-Si bulk after the spark plasma sintering (SPS), showed considerable reduction in the lattice thermal conductivity, 2 orders of magnitude compared to single crystal silicon. This drastic decrease in lattice thermal conductivity was attributed to effective phonon scattering by the nanograins (40 nm) and nanopores (100 nm) with sizes close to the mean free path of phonons. In the case of both doped silicon samples, the p-Si showed a rather higher lattice thermal conductivity compared to the n-Si sample. This was attributed to the incomplete doping of Sb in n-Si, which forms precipitates and contributes to phonon scattering. Apart from the differences in thermal conductivity as a result of the different dopant, the electrical conductivity and carrier mobility of the dopant varied as well. The maximum power output for both n-Si and p-Si were 1.14 and 1.81 W m−2 respectively under a temperature difference of 40 K. Additionally, a study of the effects of porosity and the pore size on the bulk lattice thermal conductivity showed a decrease in the thermal conductivity when porosity increased and pore size decreased. This suggests that an increase in porosity and reduction in pore size cause significant drop in the thermal conductivity. It goes on to outline the importance of selecting the right diatomite precursor. The figure of merit for both n and p-Si were found to increase with increasing temperature, suggesting a medium to high temperature application. However, the highest zT (thermoelectric dimensionless figure of merit) obtained shows it has not reached a practical level yet and could be increased via the choice of dopant in the n-Si type. In another related study by Szczech et al.,117 Mg2Si was magnesiothermically produced from diatomite and potential application in thermoelectrics analyzed. Silicides have already been tipped to be potential candidates for thermoelectric materials as mentioned earlier. In their study, an estimated Mg2Si grain size of 20–36 nm suggests a potential increase in zT of the thermoelectric material, based on an earlier report.242 In this report,242 nanostructures less than 10 nm cause significant decrease in thermal conductivity. Interestingly, nanostructures with relatively big grain sizes (up to 150 nm) could also cause significant decrease in the thermal conductivity, thus suggesting an expected increase in the zT of diatomite based Mg2Si.
6.2 Solar energy harvesting
The use of solar energy covers a broad spectrum of applications, ranging from direct conversion of solar energy to electricity and for photocatalysis. The latter is an area where the potential use of diatomite has received great interest.
6.2.1 Dye sensitized solar cells. The interaction of diatom frustules with light is fascinating and has been adequately studied.243–247 The interesting optical properties observed are the main motivations for the interest in diatoms for potential applications in solar energy harvesting technologies. It is reported that diatoms are efficient light harvesting organisms, and this is further backed by their ability to produce their own food like plants do with chlorophyll.248,249 This suggests the potential to channel such light trapping properties into energy harvesting based on solar energy technologies. Harnessing energy from the sun is one of the eco-friendliest ways of producing energy. A number of materials find applications in this field, but one that has seen massive commercialization is silicon based solar cells. Silicon is cheap, less toxic and offers tunable optical and electronic properties.57 Albeit these advantages, the high surface reflectance of silicon based solar cells remains a huge setback in their entire efficiency, which has over the years inspired the introduction of some promising solar energy harvesting. These are dye sensitized solar cells (DSSC), organic based solar cells, quantum solar cells and several others.250–253 Among the above-mentioned technologies, DSSC have received a lot of attention as far as diatomite application is concerned. Aside from this, DSSC has attracted widespread interest in the scientific community due to the prospects of efficiently harnessing solar energy at a low cost.56 Previous progress made in this field is fully discussed in excellent reviews by Sun et al.57 and Jeffryes et al.55 From the introduction of DSSC, an efficiency of 7% was reported,254 but this has further been increased to 10%.255 DSSC is mostly based on nanocrystalline anatase titania (TiO2) due to their competitive optical, electrical and biological properties as compared to other reported oxides like ZnO, SnO2, Nb2O5.57 Despite its suitability, there is a limitation with the surface area of TiO2. As reported,256 TiO2 does not offer very high surface areas provided by nanoparticles. Incorporating DE in the design of TiO2 based DSSC provides a high specific surface area capable of promoting the solar cell efficiency.57 Naturally occurring diatomite is known to have a refractive index of 1.43,243 and porous anatase titania thin films have a refractive index between 1.7 and 2.5.257 A combination of diatomite and porous anatase titania results in layers with high dielectric constant and light scattering within the pore array.57 With improved light scattering, there is a possibility to use less dye or reduce the photoanode layer, resulting in further reduction in production cost.55 Aside from the opportunity to reduce the cost, a reduced photoanode layer improves the efficiency significantly by decreasing the electron diffusion distance between the dye and the conductive glass electrode. This eventually leads to a decreased electron-electrolyte recombination, leading to the increased efficiency of the DSSC. A recent study based on this same approach was reported by Bandara et al.258 In their study, they incorporated DE in the preparation of the TiO2 based photoelectrode and reported an enhanced efficiency (35%) and improved short current density (39%), which were attributed to the enhanced light harvesting ability provided by DE. The incorporation of diatomite into DSSC presents an eco-friendly and more importantly an effective way to improve the interaction of light with the dye.
6.2.2 Photocatalyst. Chemical reactions facilitated through photoelectrochemical processes have seen tremendous admiration in recent times and this has seen widespread application in environmental waste treatment and hydrogen evolution via water splitting in fuel cells.259–264 The possibility of using solar energy to accelerate chemical reactions is an interesting area of research and this is made possible with the help of semiconductor photocatalysts. Although promising progress has been made in these areas, efforts are still being undertaken to improve overall efficiency of photocatalysts. The most widely known photocatalyst is TiO2, and reasons for its widespread use in solar energy harvesting have been presented earlier. Aside from the conventional use in DSSC, TiO2 is also used as a semiconductor photocatalyst. However, setbacks addressed with its applications in DSSC are no different for applications as photocatalyst.256 In addition to the setback mentioned earlier, the use of TiO2 is limited by its wide bandgap, 3.2 eV, which implies irradiation only in the ultraviolet range of the electromagnetic spectrum. This seriously limits their efficiency to 4–5%.265 Based on their interesting matter–light interaction, diatomite has seen huge attention as a way to improve the efficiency of semiconductor photocatalysts. It is worth noting that in the related reports, diatomite was the supporting material. In previous years a number of nanocomposites based on TiO2,46,48,52,53,98,120,145 Bi2MoO6,266 BiOCl,267 Bi2S3,268 Ag3PO4,269,270 Fe–Mn binary oxide,271 ZnO272–274 and Cu2O–ZnO150 etc. as precursor materials and diatomite as a supporting material have been reported. In one such report by Zhang et al.,48 a photocatalyst based on precursor TiO2 and diatomite as a supporting material was reported. The TiO2/diatomite photocatalyst was more effective in degrading gaseous formaldehyde than pristine TiO2 under UV radiation. This difference in photocatalytic performance between the composite photocatalyst and TiO2 was attributed to the potential of diatomite to accelerate a good dispersion of TiO2 nanoparticles and a strong absorption capacity for formaldehyde. Other works focusing on materials apart from the well-known TiO2 include a report by Cai et al.,266 where a facile approach to synthesize nano-sized Bi2MoO6/diatomite composite as a high performance photocatalyst under visible light irradiation was demonstrated. Their as-synthesized nano-sized Bi2MoO6/diatomite composite had significantly higher photocatalytic efficiency for Rhodamine B (RhB) degradation than the pristine Bi2MoO6 under visible light illumination. The high surface area of diatomite promotes the formations of composites with nanostructures suitable for efficient photocatalytic activities. In their work, the synthesized nano-sized Bi2MoO6/diatomite composite had Bi2MoO6 nanoflakes homogeneously attached to the surface of diatomite, unlike as-prepared pure Bi2MoO6. In the pure Bi2MoO6 sample, agglomerates were formed and such morphologies are reported to limit the overall photocatalytic activity due to the reduction of the active sites for photocatalysis. The degradation efficiency of the prepared nanocomposite increased with increasing Bi2MoO6. However, further increase to 80% Bi2MoO6 to diatomite ratio resulted in a significant drop in the photocatalytic activity of the nanocomposite due to the formation of aggregates of Bi2MoO6 on the surface of the nanocomposite. In another work by Xiao et al.,268 a semiconductor photocatalyst based diatomite and Bi2S3 was reported. In their work, the nanocomposite DE-Bi2S3 showed better photocatalytic activity than the pure Bi2S3 towards the degradation of Cr(IV), a bioaccumulated pollutant in wastewater. The improved photocatalytic activity was attributed to the ability of diatomite to prevent the aggregation of Bi2S3 monomers. Diatomite is reported to monodisperse Bi2S3 and also facilitates the absorption of Cr(IV) on its surface, thus enhancing the photocatalytic activity. Another promising nanocomposite based on a Cu2O–ZnO system immobilized on diatomite was reported by Zhu et al.150 Diatomaceous earth, playing the role of the supporting material, enhanced the photocatalytic activity of the hybrid towards the degradation of red water produced from TNT production. Natural DE used in their work played the same role as reports presented above. The high surface area of diatomite provided a bigger contact surface between the photocatalyst and the liquid due to the improved dispersion of Cu2O–ZnO on its surface. It should be noted that in all the literature addressed, the authors report of a stable nanocomposite photocatalyst which can be reused. The micro–nano structure of diatomite appears to inspire morphologies suitable for catalytic activity in almost all the works reported.
6.2.3 Silicon and polymer based solar cells. The application of diatomite in solar energy harvesting has been extended to silicon and polymer based solar cells.71,84,112 In silicon based solar cells, solar energy is directly converted to electrical energy. In these reported applications, diatomite derived materials served as an anti-reflective coating, causing a significant reduction in the surface reflectance of silicon based solar cells. One major setback of silicon based solar cells is their high surface reflectivity, which affects the overall efficiency of this solar cell type. A huge part of the electromagnetic radiation from the sun is not accounted for due to this high surface reflectivity. The measured surface reflectivity of polished silicon are given as 54, 35 and 31% for the UV range (300–400 nm), visible (400–800 nm) and near-IR (1200–2000 nm) respectively.275 To reduce the surface reflectivity, a number of approaches are employed including the use of anti-reflective coating, and surface modification of wafer surface resulting in what is best known as black silicon (BSi).71,275 Although these solutions offer improved surface properties, they are often complex, require non-eco-friendly processing and costly.71,112 In a study by Chen et al.71 a spin-coated chlorophyll extract from diatom algae caused a significant reduction of the surface reflectivity of silicon wafer to 13% (350–1100 nm). Another approach using diatomite to reduce the surface reflectivity of silicon was demonstrated by Aggrey et al.112 In their work, a black silicon-like coating, referred to in their work as “silicon nanoflakes”, was formed on the wafer surface after an in situ magnesiothermic reduction of diatomite on the surface. The silicon nanoflakes coating caused a significant drop in the surface reflectivity to 15% (1520–1620 nm). The two strategies reported have been summarized in Fig. 12,71,112 both significant in another related work, McMillon-Brown et al.84 enhanced the light trapping ability of their polymer based solar cell. Organic photovoltaics (OPV), although attractive for several reasons like being lightweight, flexible and transparent, have a huge setback. The highest power conversion efficiency (PCE) to be reported is 11.5%.276 The PCE of organic solar cells are known to be dependent on the thickness of the active layer.84 Even though an increase in the thickness of the active layer provides more absorption, charge extraction for thick active layers is limited by the low charge mobility of the organic semiconducting blend. For this reason, the thickness of the active layer is normally restricted between 100 and 300 nm. In order to improve the active-layer absorption a number of approaches have been suggested to redirect and improve light trapping, but most of them require complex and expensive processes.277–280 It is reported that DE improves the light absorption of active materials when in close proximity and this is quite expected because the interesting optical DE exhibits.246 As such, the incorporation of DE into the design of OPVs could improve the active layer absorption through improved light scattering. Through the addition of DE to their active layer, they obtained the same PCE as standard thickness cells with 36% thinner active layer. This confirms DE inclusion in OPV can help optimize them by tackling the issues with thickness limitations. In these reports the potential use of diatomite to complement bulk silicon and polymer based solar are analyzed and may be crucial for improved solar cell performance. The fascinating optical properties obviously enhance light absorption of these solar cell types and could go a long way to improve their efficiency.
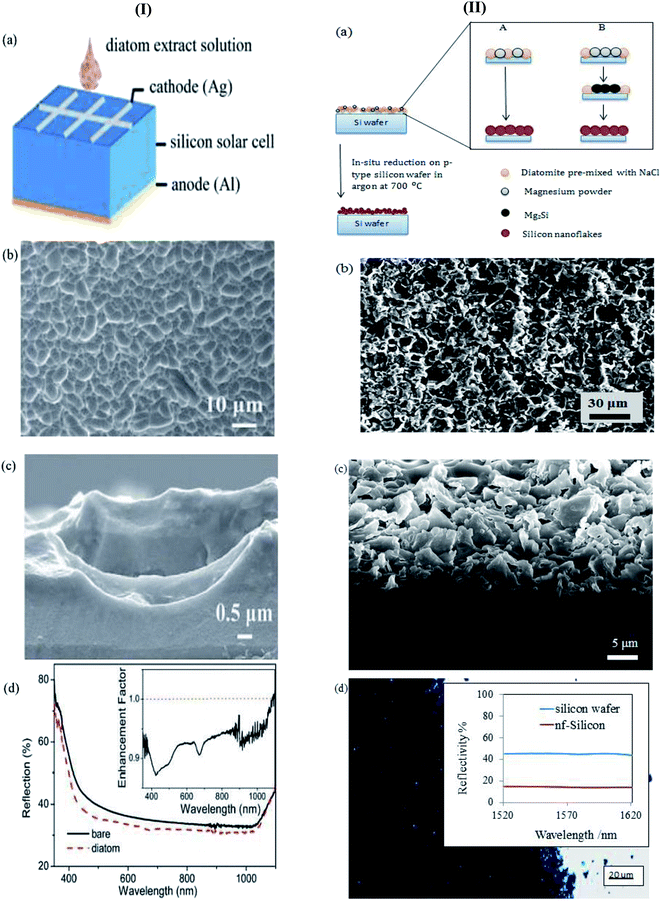 |
| Fig. 12 Schematic illustration of the 2 approaches reported to suppress surface reflectivity of silicon based solar cell (I) (a) schematic illustration of synthesis process (b and c) SEM images diatom extract (d) surface reflectivity of diatom extract71 and (II) (a) schematic illustration of synthesis process (b and c) SEM images of silicon nanoflakes (d) surface reflectivity of silicon nanoflakes.112 | |
7. Other potential energy applications
The target to increase the efficiency of green energy technologies comes with a lot of stiff criteria for energy materials. Already, notable breakthroughs have been reported about the use of diatomite in some energy harvesting and storage applications such as solar energy applications,46,52,71,84,98,112,258,268 thermal energy storage,72,76,89,195 thermoelectrics36,117 and electrical energy storage systems (batteries and supercapacitors).45,49,59,60,62,63,100,144 The successes attained to date will certainly serve as a catalyst to foster DE studies in energy applications. The widespread potential applications of DE can be attributed to a combination of factors. Diatomite is an attractive silica precursor, a workable template for new materials and most importantly possesses a naturally formed nanoporous structure highly desired and required in new energy materials. Much more can be expected from the use of diatomite as a template for electrodes of batteries based on Na, K, Mg, Al etc. and other battery types as research is still on-going in these areas. Current energy materials are expected to possess nanostructures suitable for typically functional applications in energy systems and concurrently exhibit good structural stability. It is not surprising that DE has gained such huge attention for the replacement of existing silica precursors used for outstandingly good yet structurally poor Si based anode materials. DE may receive a lot more attention as researchers continue to find ways of nanostructuring electrode materials and separators for electrochemical devices. Another potential area, currently unexplored to the best of our knowledge, is the use of DE as a precursor for the growth and formation of quartz for piezoelectric applications. As a naturally occurring siliceous material, DE qualifies to be used as a precursor for quartz formation. This gap in the potential of DE was previously addressed by Korsunsky et al.121 Using a nanostructured silica precursor for the growth and formation of nanostructured piezo quartz could allow for a simple and straightforward synthesis route unlike the protocols reported in previous studies.281,282 Nanostructured quartz films on silicon substrates have been synthesized via wet chemistry in recent studies.283,284 Currently, the electronic grade of quartz is produced via a long hydrothermal process developed by Spezia, where the large crystals are cut and polished.285 Subsequent processes such as shaping and integration are performed in order to obtain thinner oscillators with higher resonance frequencies.286 The existing process is complex and expensive and has triggered a lot of interest in cheap and straightforward routes such as sol–gel chemistry, chemical solution deposition and hydrothermal synthesis.287–291 Different silica precursors like amorphous silica colloids, tetraethoxysilane silica (TEOS), and dry amorphous silica have been used in these reports.281–284 Earlier studies emphasized the importance of synthesis conditions such as the silica precursor, catalyst, humidity and thermal treatment.292–296 As far as the silica precursor is concerned, there is yet to be a work on nanostructured quartz synthesized using DE. DE is naturally abundant, eco-friendly, cheap and most importantly possesses nanoscale morphologies which make it a suitable candidate as a silica precursor for quartz formation. Improving existing and developing future energy materials could see a more substantive approach towards DE as long as the search for cheaper and eco-friendlier ways to produce reliable and efficient energy materials stays on.
8. Conclusion
Diatomaceous earth has been explored in several forms for different energy applications. Regardless of their state of application, DE has shown promising results thus prompting further interest amongst scientists. Indeed, the fascinating naturally formed nanostructure of DE is paramount in their contributions reported to date. Using DE as a template and precursor for new energy materials seems to offer cheaper, simpler and eco-friendlier synthesis protocols compared to most protocols carried out without it. The reported synthesis routes: impregnation technology, displacement reactions, wet chemistry and deposition and etching are well established processes. In general, these synthesis routes seek to utilize or preserve the nanoporous structure of DE.
• The impregnation technology makes use of the nanoporous structure of DE to form nanocomposites by impregnating DE with the active material. DE serves as a supporting material in this process. The impregnation technology comes with a simple set-up and is normally performed at low temperatures.
• In displacement reactions, the main objective is to preserve the nanostructure of DE in Si based material after reduction reactions at relatively higher temperatures than in the impregnation technology. DE plays the role of a precursor and a template for the new material produced using the displacement reaction.
• Deposition techniques and wet chemistry routes provide platforms to produce new materials and hybrid systems by covering the surface and sometimes internal pores of DE. In the deposition and wet chemistry routes, DE plays the role of a template and in some cases both a template and supporting material.
Among these synthesis routes, further studies and modifications of displacement reactions have led to the introduction of notable non-conventional methods, which offer somewhat better control over the outcome of the typical silica to silicon conversion that takes place in this process. A better control over the outcome of displacement reactions means a better chance to control the nanoscale morphology of silicon-based materials produced from DE. Another important aspect of these synthesis processes is the role that some prior treatments performed on DE play on the nanostructure and properties of the final products. Prior treatments, mainly mechanical and thermal, affect the powder properties of DE prior to the main synthesis processes. Prior treatments such as calcination, mechanical milling, microwave heating and vacuum drying are all crucial for the full implementation of DE as the next generation energy material. DE is obviously an ideal and near perfect material for emerging energy materials, but this expectation relies heavily on the right combination of synthesis processes. The preference for DE over other siliceous materials is related to the neat naturally formed nanostructure of the former. The goal of almost all principal synthesis processes is to preserve this structure for intended applications. As far as synthesis is concerned, the main threat to the nanoscale morphology of DE comes from the high temperature and extreme mechanical treatments. Apart from displacement reactions with rather high temperatures used, the other main synthesis processes require relatively low temperatures, although pre-treatments may involve high temperature treatment. The quest to preserve the nanostructure has benefited from several ideas such as the use of inorganic salts. Inorganic salts represent a means of scavenging the enormous heat evolved in displacement reactions and thus may help preserve the nanostructure to some extent. Achieving further improvement places greater demands on the understanding of the kinetics and thermodynamics of silica to silicon transformations mostly facilitated by Mg and Al in DE-related studies. A better understanding of the reaction kinetics will inform the search for best reaction parameters which could complement inorganic salts to improve nanostructure preservation. Even though particle size reduction is reportedly beneficial for battery applications, this may not be suitable treatment for applications where high porosity is required and most importantly for bio-templating purposes, since the individual frustules end up badly fragmented. It is extremely important to find the right balance between particle size reduction and the preservation of nanoscale morphology of DE in order to obtain powders with suitable free surface characteristics for intended applications. For bio-templating purposes, it is imperative for frustules to be free from impurities blocking the pores. Thermal pre-treatment via microwave heating is reported to be effective in eliminating impurities from the pores. The ideal DE precursor with empty pores, suitable particle size and unbroken frustules may be achievable only through laboratory cultivation of diatoms which is not very economical, thus exploiting a synergy between different pre-treatments and synthesis process to obtain workable precursors is much desired. As far as applications are concerned, the prospects of DE in the ever increasing and demanding energy sector applications are indisputable based on accounts provided in the reviewed literature. In thermal energy storage, DE has been successfully incorporated together with active materials to form shape-stable phase change materials that deliver enhanced performance due to the high degree of encapsulation or impregnation of PCMs. So far, the available literature shows that DE-based nPCMs offer a high phase change temperature but this occurs at the expense of the latent heat storage ability. Thus, future works could concentrate on optimizing phase change temperatures in order to further improve the storage capability of PCMs. Incorporating DE in the design of supercapacitor electrodes has shown enormous increase in supercapacitor performance such as high specific capacitance and excellent cycling stability. This has been partly attributed to the nanoscale morphology of DE that is able to prevent agglomeration and large volume changes during cycling. Properties such as high reversibility and good cycling during charge–discharge have been ascribed to the high surface area and porosity offered by DE. Developing facile and highly efficient synthesis processes remain a crucial step in the realization of DE as supporting material or template for electrode material for supercapacitors. In battery development, DE has seen tremendous interest as a precursor for silica and silicon-based anode materials for Li-ion batteries, where significant successes have been widely reported. DE based anodes have delivered superior electrochemical performance due to their heterogeneous network and porous structure. Additionally, further application of carbon coating has been reported to optimize the electrochemical performance of these anodes to offer a higher specific capacity due to decreased diffusion length owing to the high surface area of the treated DE and the contribution from carbon. Here, other forms of conductive coatings can be investigated in varying structures in order to optimize further the electrochemical performance while also looking at other forms of treatment of the diatoms. The development of solid-state batteries, the potential battery of the future could necessitate the use of DE as a template and supporting material for the design of battery electrodes considering the recent successes reported for this battery type, where huge volume changes and dendrite formation were minimized by DE incorporation into the design of the electrode. Quite some progress has been made in reducing the shuttling effect of polysulfides in Li–S batteries by preparing a DE-based composite electrode. The improved battery stability after using DE in Li–S batteries presents a path to design composite electrode materials where DE is a competitive candidate as a supporting material. The possibility and temptation to use Si as a thermoelectric material could be realized in the nearest future following early success reported in preparing nanoporous Si thermoelectric generators, where promising results were obtained. Alongside nanoporous Si, a rather well-known thermoelectric material based on Mg and Si (Mg2Si) with interesting nanoscale morphologies could be developed from DE, to offer outstanding zT. Indeed, the realization of these possibilities hinges critically on the proper synthesis processes, which have the potential of preserving the hierarchical nanostructure of DE for the intended applications. Solar energy harvesting is another area which has seen tremendous interest in potential DE implementation, not only because they act as template for active materials but due to the interesting optical properties they possess. Dye sensitized solar cells (DSSC) and photocatalysis are areas of solar energy harvesting technology that received a lot of attention as far as the use of diatomite is concerned, although isolated cases in silicon and polymer based solar cells have been reported recently. DE has been successfully incorporated into TiO2 systems of solar cells to improve efficiency where the enhancement has been attributed to the high surface area of the diatomite contribution. Also, the low band width of TiO2 which limits irradiation to only the UV range of the electromagnetic spectrum has been improved by using DE as supporting material for systems in the past. It is worth noting that though the incorporation of DE in such systems results in improvement in properties, the present state only uses DE as supporting material and not the main active material. Capitalizing on these strengths could pave the way for full implementation of DE in DSSC and photocatalysis where minimal quantities of the active materials may be required, thus reducing the cost. Thus far, DE offered an alternative approach to enhancing energy performance of materials in an eco-friendlier and cost-effective manner. While all these studies suggest the undeniable depth of usefulness DE would yield in the energy industry, the full potential of DE could remain untapped. At present, to the best of our knowledge there is no comparative study of different DE cultures and their performance in applications. It would be interesting to synthesize DE-based energy materials based on different individual cultures and to understand the relationship between their nanoscale structure and performance. Of course, the task is challenging and time consuming, but any study dedicated to this will help realize the full potential of DE. Potentially, specific cultures may be found to be suitable for particular applications.
Conflicts of interest
There are no conflicts to declare.
Acknowledgements
The authors wish to acknowledge the support from the Royal Society of London under projects IEC/R2/170223 and IEC/R2/202254.
References
- R. Calvert, Diatomaceous earth, J. Chem. Educ., 1930 Dec, 7(12), 2829 Search PubMed.
- M. M. Ghobara, M. M. Ghobara, M. M. Ghobara and A. Mohamed, Diatomite in Use: Nature, Modifications, Commercial Applications and Prospective Trends, Diatoms: Fundamentals and Applications, 2019 Jun 28, 471–509 Search PubMed.
- T. D. Kelly, G. R. Matos, D. A. Buckingham, C. A. DiFrancesco, K. E. Porter and C. Berry, Historical statistics for mineral and material commodities in the United States, US Geological Survey data series. 2010 Feb;vol. 140, pp. 01–06 Search PubMed.
- P. Zahajská, S. Opfergelt, S. C. Fritz, J. Stadmark and D. J. Conley, What is diatomite?, Quat. Res., 2020 Jul, 96, 48–52 Search PubMed.
- J. Murray and A. F. Renard. Report on deep-sea deposits based on the specimens collected during the voyage of HMS Challenger in the years 1872 to 1876, HM Stationery Office, 1891 Search PubMed.
- P. S. Conger, Accumulation of diatomaceous deposits, J. Sediment. Res., 1942, 12(2), 55–66 Search PubMed.
- G. K. Pedersen, Anoxic events during sedimentation of a Palaeogene diatomite in Denmark, Sedimentology, 1981 Aug, 28(4), 487–504 Search PubMed.
- F. L. Kadey Jr, Diatomite. Industrial Rocks and Minerals. 1983, vol. 1, pp. 677–708 Search PubMed.
- W. E. Dean, M. Leinen and D. A. Stow, Classification of deep-sea, fine-grained sediments, J. Sediment. Res., 1985 Mar 1, 55(2), 250–256 Search PubMed.
- K. Minoura, T. Susaki and K. Horiuchi, Lithification of biogenic siliceous sediments: Evidence from Neogene diatomaceous sequences of northeast Japan, Sediment. Geol., 1996 Dec 1, 107(1–2), 45–59 Search PubMed.
- S. D. Inglethorpe. Industrial minerals laboratory manual: diatomite. British Geological Survey; 1993 Search PubMed.
- S. Akin, J. M. Schembre, S. K. Bhat and A. R. Kovscek, Spontaneous imbibition characteristics of diatomite, J. Pet. Sci. Eng., 2000 Mar 1, 25(3–4), 149–165 Search PubMed.
- R. B. Owen, Sedimentological characteristics and origins of diatomaceous deposits in the East African Rift System, Sedimentation in Continental Rifts, 2002, pp.233–246 Search PubMed.
- P. R. Moyle and T. P. Dolley, U.S. Geological Survey Chapter D, With or Without Salt-a Comparison of Marine and Continental-Lacustrine Diatomite Deposits, 2003 Search PubMed.
- S. Martinovic, M. Vlahovic, T. Boljanac and L. Pavlovic, Preparation of filter aids based on diatomites, Int. J. Miner. Process., 2006 Sep 1, 80(2–4), 255–260 Search PubMed.
- B. Yılmaz and N. Ediz, The use of raw and calcined diatomite in cement production, Cem. Concr. Compos., 2008 Mar 1, 30(3), 202–211 Search PubMed.
- X. Qi, M. Liu, Z. Chen and R. Liang, Preparation and properties of diatomite composite superabsorbent, Polym. Adv. Technol., 2007 Mar, 18(3), 184–193 Search PubMed.
- A. NIKPAY, Diatomaceous earths as alternatives to chemical insecticides in stored grain, Insect Sci., 2006 Dec, 13(6), 421–429 Search PubMed.
- D. Li, Y. K. Joo, N. E. Christians and D. D. Minner, Inorganic soil amendment effects on sand-based sports turf media, Crop Sci., 2000 Jul, 40(4), 1121–1125 Search PubMed.
- M. Green, E. Fielder, B. Scrosati, M. Wachtler and J. S. Moreno, Structured silicon anodes for lithium battery applications, Electrochem. Solid State Lett., 2003 Mar 5, 6(5), A75 Search PubMed.
- J. Rong, C. Masarapu, J. Ni, Z. Zhang and B. Wei, Tandem structure of porous silicon film on single-walled carbon nanotube macrofilms for lithium-ion battery applications, ACS Nano, 2010 Aug 24, 4(8), 4683–4690 Search PubMed.
- C. K. Chan, H. Peng, G. Liu, K. McIlwrath, X. F. Zhang, R. A. Huggins and Y. Cui, High-performance lithium battery anodes using silicon nanowires, Nat. Nanotechnol., 2008 Jan, 3(1), 31–35 Search PubMed.
- T. Song, J. Xia, J. H. Lee, D. H. Lee, M. S. Kwon, J. M. Choi, J. Wu, S. K. Doo, H. Chang, W. I. Park and D. S. Zang, Arrays of sealed silicon nanotubes as anodes for lithium ion batteries, Nano Lett., 2010 May 12, 10(5), 1710–1716 Search PubMed.
- X. Chen, K. Gerasopoulos, J. Guo, A. Brown, C. Wang, R. Ghodssi and J. N. Culver, Virus-enabled silicon anode for lithium-ion batteries, ACS Nano, 2010 Sep 28, 4(9), 5366–5372 Search PubMed.
- L. F. Cui, L. Hu, J. W. Choi and Y. Cui, Light-weight free-standing carbon nanotube-silicon films for anodes of lithium ion batteries, ACS Nano, 2010 Jul 27, 4(7), 3671–3678 Search PubMed.
- T. Takamura, M. Uehara, J. Suzuki, K. Sekine and K. Tamura, High capacity and long cycle life silicon anode for Li-ion battery, J. Power Sources, 2006 Aug 25, 158(2), 1401–1404 Search PubMed.
- U. Kasavajjula, C. Wang and A. J. Appleby, Nano-and bulk-silicon-based insertion anodes for lithium-ion secondary cells, J. Power Sources, 2007 Jan 1, 163(2), 1003–1039 Search PubMed.
- H. Kim, M. Seo, M. H. Park and J. Cho, A critical size of silicon nano-anodes for lithium rechargeable batteries, Angew. Chem., Int. Ed., 2010 Mar 15, 49(12), 2146–2149 Search PubMed.
- N. Liu, H. Wu, M. T. McDowell, Y. Yao, C. Wang and Y. Cui, A yolk-shell design for stabilized and scalable Li-ion battery alloy anodes, Nano Lett., 2012 Jun 13, 12(6), 3315–3321 Search PubMed.
- N. Liu, Z. Lu, J. Zhao, M. T. McDowell, H. W. Lee, W. Zhao and Y. Cui, A pomegranate-inspired nanoscale design for large-volume-change lithium battery anodes, Nat. Nanotechnol., 2014 Mar, 9(3), 187–192 Search PubMed.
- R. Yi, F. Dai, M. L. Gordin, S. Chen and D. Wang, Micro-sized Si-C composite with interconnected nanoscale building blocks as high-performance anodes for practical application in lithium-ion batteries, Adv. Energy Mater., 2013 Mar, 3(3), 295–300 Search PubMed.
- N. Liu, K. Huo, M. T. McDowell, J. Zhao and Y. Cui, Rice husks as a sustainable source of nanostructured silicon for high performance Li-ion battery anodes, Sci. Rep., 2013 May 29, 3(1), 1–7 Search PubMed.
- J. Song, S. Chen, M. Zhou, T. Xu, D. Lv, M. L. Gordin, T. Long, M. Melnyk and D. Wang, Micro-sized silicon–carbon composites composed of carbon-coated sub-10 nm Si primary particles as high-performance anode materials for lithium-ion batteries, J. Mater. Chem. A, 2014, 2(5), 1257–1262 RSC.
- M. Wu, J. E. Sabisch, X. Song, A. M. Minor, V. S. Battaglia and G. Liu, In situ formed Si nanoparticle network with micron-sized Si particles for lithium-ion battery anodes, Nano Lett., 2013 Nov 13, 13(11), 5397–5402 Search PubMed.
- C. Shen, M. Ge, L. Luo, X. Fang, Y. Liu, A. Zhang, J. Rong, C. Wang and C. Zhou, In situ and ex situ TEM study of lithiation behaviours of porous silicon nanostructures, Sci. Rep., 2016 Aug 30, 6(1), 1 Search PubMed.
- P. A. Zong, D. Makino, W. Pan, S. Yin, C. Sun, P. Zhang, C. Wan and K. Koumoto, Converting natural diatomite into nanoporous silicon for eco-friendly thermoelectric energy conversion, Mater. Des., 2018 Sep 15, 154, 246–253 Search PubMed.
- Y. Nishimoto and K. Namba, Investigation of texturization for crystalline silicon solar cells with sodium carbonate solutions, Sol. Energy Mater. Sol. Cells, 2000 Apr 1, 61(4), 393–402 Search PubMed.
- J. Yoo, Reactive ion etching (RIE) technique for application in crystalline silicon solar cells, Sol. Energy, 2010 Apr 1, 84(4), 730–734 Search PubMed.
- D. Z. Dimitrov and C. H. Du, Crystalline silicon solar cells with micro/nano texture, Appl. Surf. Sci., 2013 Feb 1, 266, 1–4 Search PubMed.
- X. Liu, P. R. Coxon, M. Peters, B. Hoex, J. M. Cole and D. J. Fray, Black silicon: fabrication methods, properties and solar energy applications, Energy Environ. Sci., 2014, 7(10), 3223–3263 RSC.
- M. Otto, M. Algasinger, H. Branz, B. Gesemann, T. Gimpel, K. Füchsel, T. Käsebier, S. Kontermann, S. Koynov, X. Li and V. Naumann, Black silicon photovoltaics, Adv. Opt. Mater., 2015 Feb, 3(2), 147–164 Search PubMed.
- J. Lv, T. Zhang, P. Zhang, Y. Zhao and S. Li, Review application of nanostructured black silicon, Nanoscale Res. Lett., 2018 Dec, 13(1), 1–10 Search PubMed.
- S. Karaman, A. Karaipekli, A. Sarı and A. Bicer, Polyethylene glycol (PEG)/diatomite composite as a novel form-stable phase change material for thermal energy storage, Sol. Energy Mater. Sol. Cells, 2011 Jul 1, 95(7), 1647–1653 Search PubMed.
- M. S. Wang, L. Z. Fan, M. Huang, J. Li and X. Qu, Conversion of diatomite to porous Si/C composites as promising anode materials for lithium-ion batteries, J. Power Sources, 2012 Dec 1, 219, 29–35 Search PubMed.
- Y. X. Zhang, M. Huang, F. Li, X. L. Wang and Z. Q. Wen, One-pot synthesis of hierarchical MnO2-modified diatomites for electrochemical capacitor electrodes, J. Power Sources, 2014 Jan 15, 246, 449–456 Search PubMed.
- Y. Chen, Q. Wu, C. Zhou and Q. T. Jin, Enhanced photocatalytic activity of La and N co-doped TiO2/diatomite composite, Powder Technol., 2017, 322, 296–300 CrossRef CAS.
- D. R. Huang, Y. J. Jiang, R. L. Liou, C. H. Chen, Y. A. Chen and C. H. Tsai, Enhancing the efficiency of dye-sensitized solar cells by adding diatom frustules into TiO2 working electrodes, Appl. Surf. Sci., 2015 Aug 30, 347, 64–72 Search PubMed.
- G. Zhang, Z. Sun, Y. Duan, R. Ma and S. Zheng, Synthesis of nano-TiO2/diatomite composite and its photocatalytic degradation of gaseous formaldehyde, Appl. Surf. Sci., 2017 Aug 1, 412, 105–112 Search PubMed.
- B. Campbell, R. Ionescu, M. Tolchin, K. Ahmed, Z. Favors, K. N. Bozhilov, C. S. Ozkan and M. Ozkan, Carbon-coated, diatomite-derived nanosilicon as a high rate capable Li-ion battery anode, Sci. Rep., 2016 Oct 7, 6(1), 1–9 Search PubMed.
- Y. X. Zhang, F. Li, M. Huang, Y. Xing, X. Gao, B. Li, Z. Y. Guo and Y. M. Guan, Hierarchical NiO moss decorated diatomites via facile and templated method for high performance supercapacitors, Mater. Lett., 2014 Apr 1, 120, 263–266 Search PubMed.
- X. L. Guo, M. Kuang, F. Li, X. Y. Liu, Y. X. Zhang, F. Dong and D. Losic, Engineering of three dimensional (3-D) diatom@ TiO2@ MnO2 composites with enhanced supercapacitor performance, Electrochim. Acta, 2016 Feb 1, 190, 159–167 Search PubMed.
- Y. Chen and K. Liu, Preparation and characterization of nitrogen-doped TiO2/diatomite integrated photocatalytic pellet for the adsorption-degradation of tetracycline hydrochloride using visible light, Chem. Eng. J., 2016 Oct 15, 302, 682–696 Search PubMed.
- R. Zuo, G. Du, W. Zhang, L. Liu, Y. Liu, L. Mei and Z. Li, Photocatalytic degradation of methylene blue using TiO2 impregnated diatomite, Adv. Mater. Sci. Eng., 2014 Jan 1, 2014, 170148 Search PubMed.
- D. Losic, J. G. Mitchell and N. H. Voelcker, Diatomaceous lessons in nanotechnology and advanced materials, Adv. Mater., 2009 Aug 7, 21(29), 2947–2958 Search PubMed.
- C. Jeffryes, J. Campbell, H. Li, J. Jiao and G. Rorrer, The potential of diatom nanobiotechnology for applications in solar cells, batteries, and electroluminescent devices, Energy Environ. Sci., 2011, 4(10), 3930–3941 RSC.
- Y. Wang, J. Cai, Y. Jiang, X. Jiang and D. Zhang, Preparation of biosilica structures from frustules of diatoms and their applications: current state and perspectives, Appl. Microbiol. Biotechnol., 2013 Jan, 97(2), 453–460 Search PubMed.
- X. W. Sun, Y. X. Zhang and D. Losic, Diatom silica, an emerging biomaterial for energy conversion and storage, J. Mater. Chem. A, 2017, 5(19), 8847–8859 RSC.
- R. Ragni, S. R. Cicco, D. Vona and G. M. Farinola, Multiple routes to smart nanostructured materials from diatom microalgae: a chemical perspective, Adv. Mater., 2018 May, 30(19), 1704289 Search PubMed.
- F. Zhou, Z. Li, Y. Y. Lu, B. Shen, Y. Guan, X. X. Wang, Y. C. Yin, B. S. Zhu, L. L. Lu, Y. Ni and Y. Cui, Diatomite derived hierarchical hybrid anode for high performance all-solid-state lithium metal batteries, Nat. Commun., 2019 Jun 6, 10(1), 1 Search PubMed.
- Y. Zhang, R. Zhang, S. Chen, H. Gao, M. Li, X. Song, H. L. Xin and Z. Chen, Diatomite-Derived Hierarchical Porous Crystalline-AmorphousNetwork for High-Performance and Sustainable Si Anodes, Adv. Funct. Mater., 2020 Dec, 30(50), 2005956 Search PubMed.
- J. Li, J. Xu, Z. Xie, X. Gao, J. Zhou, Y. Xiong, C. Chen, J. Zhang and Z. Liu, Diatomite-Templated Synthesis of Freestanding 3D Graphdiyne for Energy Storage and Catalysis Application, Adv. Mater., 2018 May, 30(20), 1800548 Search PubMed.
- Z. Wang, J. Zhao, S. Liu, F. Cui, J. Luo, Y. Wang, S. Zhang, C. Zhang and X. Yang, Cultured Diatoms Suitable for the Advanced Anode of Lithium Ion Batteries, ACS Sustainable Chem. Eng., 2021 Jan 7, 9(2), 844–852 Search PubMed.
- M. V. Blanco, V. Renman, F. Vullum-Bruer and A. M. Svensson, Nanostructured diatom earth SiO 2 negative electrodes with superior electrochemical performance for lithium ion batteries, RSC Adv., 2020, 10(55), 33490–33498 RSC.
- M. De Stefano, W. H. Kooistra and D. Marino, morphology of the diatom genus campyloneis (bacillariophyceae, bacillariophyta), with a description of campyloneis juliae sp. nov. and an evaluation of the function of the valvocopulae 1, J. Phycol., 2003 Aug, 39(4), 735–753 Search PubMed.
- D. Losic, R. J. Pillar, T. Dilger, J. G. Mitchell and N. H. Voelcker, Atomic force microscopy (AFM) characterisation of the porous silica nanostructure of two centric diatoms, J. Porous Mater., 2007 Mar 1, 14(1), 61–69 Search PubMed.
- B. Tesson, M. J. Genet, V. Fernandez, S. Degand, P. G. Rouxhet and V. Martin-Jezequel, Surface chemical composition of diatoms, ChemBioChem, 2009 Aug 2011, 17(12), 10 Search PubMed.
- E. Kiefer, L. Sigg and P. Schosseler, Chemical and spectroscopic characterization of algae surfaces, Environ. Sci. Technol., 1997 Feb 27, 31(3), 759–764 Search PubMed.
- E. G. Vrieling, T. P. Beelen, Q. Sun, S. Hazelaar, R. A. van Santen and W. W. Gieskes, Ultrasmall, small, and wide angle X-ray scattering analysis of diatom biosilica: interspecific differences in fractal properties, J. Mater. Chem., 2004, 14(13), 1970–1975 RSC.
- F. E. Round, R. M. Crawford and D. G. Mann, Diatoms: biology and morphology of the genera, Cambridge university press, 1990 May 25 Search PubMed.
- A. I. Salimon, P. V. Sapozhnikov, J. Everaerts, O. Y. Kalinina, C. Besnard, C. Papadaki, J. Cvjetinovic, E. S. Statnik, Y. Kan, P. Aggrey and V. Kalyaev, A Mini-Atlas of diatom frustule electron microscopy images at different magnifications. Materials Today:, Proceedings, 2020 Jan 1, 33, 1924–1933 Search PubMed.
- C. T. Chen, F. C. Hsu, J. Y. Huang, C. Y. Chang, T. Y. Chang, H. M. Lin, T. Y. Lin and Y. F. Chen, Effects of a thermally stable chlorophyll extract from diatom algae on surface textured Si solar cells, RSC Adv., 2015, 5(44), 35302–35306 RSC.
- S. G. Jeong, J. Jeon, O. Chung, S. Kim and S. Kim, Evaluation of PCM/diatomite composites using exfoliated graphite nanoplatelets (xGnP) to improve thermal properties, J. Therm. Anal. Calorim., 2013 Nov, 114(2), 689–698 Search PubMed.
- Z. Sun, Y. Zhang, S. Zheng, Y. Park and R. L. Frost, Preparation and thermal energy storage properties of paraffin/calcined diatomite composites as form-stable phase change materials, Thermochim. Acta, 2013 Apr 20, 558, 16–21 Search PubMed.
- B. Xu and Z. Li, Paraffin/diatomite composite phase change material incorporated cement-based composite for thermal energy storage, Appl. Energy, 2013 May 1, 105, 229–237 Search PubMed.
- Y. Konuklu, O. Ersoy and O. Gokce, Easy and industrially applicable impregnation process for preparation of diatomite-based phase change material nanocomposites for thermal energy storage, Appl. Therm. Eng., 2015 Dec 5, 91, 759–766 Search PubMed.
- X. Li, J. G. Sanjayan and J. L. Wilson, Fabrication and stability of form-stable diatomite/paraffin phase change material composites, Energy Build., 2014 Jun 1, 76, 284–294 Search PubMed.
- T. Nomura, N. Okinaka and T. Akiyama, Impregnation of porous material with phase change material for thermal energy storage, Mater. Chem. Phys., 2009 Jun 15, 115(2–3), 846–850 Search PubMed.
- M. Li, Z. Wu and H. Kao, Study on preparation and thermal properties of binary fatty acid/diatomite shape-stabilized phase change materials, Sol. Energy Mater. Sol. Cells, 2011 Aug 1, 95(8), 2412–2416 Search PubMed.
- M. Li, H. Kao, Z. Wu and J. Tan, Study on preparation and thermal property of binary fatty acid and the binary fatty acids/diatomite composite phase change materials, Appl. Energy, 2011 May 1, 88(5), 1606–1612 Search PubMed.
- R. Wen, X. Zhang, Z. Huang, M. Fang, Y. Liu, X. Wu, X. Min, W. Gao and S. Huang, Preparation and thermal properties of fatty acid/diatomite form-stable composite phase change material for thermal energy storage, Sol. Energy Mater. Sol. Cells, 2018 May 1, 178, 273–279 Search PubMed.
- A. Sarı and A. Biçer, Thermal energy storage properties and thermal reliability of some fatty acid esters/building material composites as novel form-stable PCMs, Sol. Energy Mater. Sol. Cell., 2012 Jun 1, 101, 114–122 Search PubMed.
- Z. Sun, W. Kong, S. Zheng and R. L. Frost, Study on preparation and thermal energy storage properties of binary paraffin blends/opal shape-stabilized phase change materials, Sol. Energy Mater. Sol. Cell., 2013 Oct 1, 117, 400–407 Search PubMed.
- Z. Li, N. Zhang, Y. Sun, H. Ke and H. Cheng, Application of diatomite as an effective polysulfides adsorbent for lithium-sulfur batteries, J. Energy Chem., 2017 Nov 1, 26(6), 1267–1275 Search PubMed.
- L. McMillon-Brown, M. Mariano, Y. L. Lin, J. Li, S. M. Hashmi, A. Semichaevsky, B. P. Rand and A. D. Taylor, Light-trapping in polymer solar cells by processing with nanostructured diatomaceous earth, Org. Electron., 2017 Dec 1, 51, 422–427 Search PubMed.
- G. Wu, S. Ma, Y. Bai and H. Zhang, The surface modification of diatomite, thermal, and mechanical properties of poly (vinyl chloride)/diatomite composites, J. Vinyl Addit. Technol., 2019 Mar, 25(s2), E39–E47 Search PubMed.
- M. J. Abden, Z. Tao, Z. Pan, L. George and R. Wuhrer, Inclusion of methyl stearate/diatomite composite in gypsum board ceiling for building energy conservation, Appl. Energy, 2020 Feb 1, 259, 114113 Search PubMed.
- C. Li, M. Wang, B. Xie, H. Ma and J. Chen, Enhanced properties of diatomite-based composite phase change materials for thermal energy storage, Renewable Energy, 2020 Mar 1, 147, 265–274 Search PubMed.
- Y. Konuklu, O. Ersoy, F. Erzin and T. YÖ, Experimental study on preparation of lauric acid/microwave-modified diatomite phase change material composites, Sol. Energy Mater. Sol. Cells, 2019 Jun 1, 194, 89–94 Search PubMed.
- B. Xu and Z. Li, Paraffin/diatomite/multi-wall carbon nanotubes composite phase change material tailor-made for thermal energy storage cement-based composites, Energy, 2014 Aug 1, 72, 371–380 Search PubMed.
- P. Zhang, Y. Cui, K. Zhang, S. Wu, D. Chen and Y. Gao, Enhanced thermal storage capacity of paraffin/diatomite composite using oleophobic modification, J. Clean. Prod., 2021 Jan 10, 279, 123211 Search PubMed.
- A. Sharma, V. V. Tyagi, C. R. Chen and D. Buddhi, Review on thermal energy storage with phase change materials and applications, Renew. Sustain. Energy Rev., 2009 Feb 1, 13(2), 318–345 Search PubMed.
- M. M. Kenisarin and K. M. Kenisarina, Form-stable phase change materials for thermal energy storage, Renew. Sustain. Energy Rev., 2012 May 1, 16(4), 1999–2040 Search PubMed.
- D. Losic, J. G. Mitchell and N. H. Voelcker, Complex gold nanostructures derived by templating from diatom frustules, Chem. Commun., 2005,(39), 4905–4907 RSC.
- D. Losic, J. G. Mitchell, R. Lal and N. H. Voelcker, Rapid fabrication of micro-and nanoscale patterns by replica molding from diatom biosilica, Adv. Funct. Mater., 2007 Sep 24, 17(14), 2439–2446 Search PubMed.
- H. Li, C. Jeffryes, T. Gutu and J. Jiao, Peptide-mediated deposition of nanostructured TiO2 into the periodic structure of diatom biosilica and its integration into the fabrication of a dye-sensitized solar cell device, Materials Research Society Online Proceedings Library (OPL), 2009, p. 1189 Search PubMed.
- Y. Yu, J. Addai-Mensah and D. Losic, Synthesis of self-supporting gold microstructures with three-dimensional morphologies by direct replication of diatom templates, Langmuir, 2010 Sep 7, 26(17), 14068–14072 Search PubMed.
- J. Toster, K. S. Iyer, W. Xiang, F. Rosei, L. Spiccia and C. L. Raston, Diatom frustules as light traps enhance DSSC efficiency, Nanoscale, 2013, 5(3), 873–876 RSC.
- D. Liu, W. Yuan, P. Yuan, W. Yu, D. Tan, H. Liu and H. He, Physical activation of diatomite-templated carbons and its effect on the adsorption of methylene blue (MB), Appl. Surf. Sci., 2013 Oct 1, 282, 838–843 Search PubMed.
- K. Li, X. Liu, T. Zheng, D. Jiang, Z. Zhou, C. Liu, X. Zhang, Y. Zhang and D. Losic, Tuning MnO2 to FeOOH replicas with bio-template 3D morphology as electrodes for high performance asymmetric supercapacitors, Chem. Eng. J., 2019 Aug 15, 370, 136–147 Search PubMed.
- Y. Yang, A. Li, X. Cao, F. Liu, S. Cheng and X. Chuan, Use of a diatomite template to prepare a MoS2/amorphous carbon composite and exploration of its electrochemical properties as a supercapacitor, RSC Adv., 2018, 8(62), 35672–35680 RSC.
- Q. J. Le, M. Huang, T. Wang, X. Y. Liu, L. Sun, X. L. Guo, D. B. Jiang, J. Wang, F. Dong and Y. X. Zhang, Biotemplate derived three dimensional nitrogen doped graphene@ MnO2 as bifunctional material for supercapacitor and oxygen reduction reaction catalyst, J. Colloid Interface Sci., 2019 May 15, 544, 155–163 Search PubMed.
- K. Chen, C. Li, L. Shi, T. Gao, X. Song, A. Bachmatiuk, Z. Zou, B. Deng, Q. Ji, D. Ma and H. Peng, Growing three-dimensional biomorphic graphene powders using naturally abundant diatomite templates towards high solution processability, Nat. Commun., 2016 Nov 7, 7(1), 1–9 Search PubMed.
- F. Li, Y. Xing, M. Huang, K. L. Li, T. T. Yu, Y. X. Zhang and D. Losic, MnO 2 nanostructures with three-dimensional (3D) morphology replicated from diatoms for high-performance supercapacitors, J. Mater. Chem. A, 2015, 3(15), 7855–7861 RSC.
- D. B. Jiang, B. Y. Zhang, T. X. Zheng, Y. X. Zhang and X. Xu, One-pot synthesis of η-Fe2O3 nanospheres/diatomite composites for electrochemical capacitor electrodes, Mater. Lett., 2018 Mar 15, 215, 23–26 Search PubMed.
- Z. Hu, K. Ma, W. Tian, F. Wang, H. Zhang, J. He, K. Deng, Y. X. Zhang, H. Yue and J. Ji, Manganese dioxide anchored on hierarchical carbon nanotubes/graphene/diatomite conductive architecture for high performance asymmetric supercapacitor, Appl. Surf. Sci., 2020 Apr 1, 508, 144777 Search PubMed.
- K. Masuko, M. Shigematsu, T. Hashiguchi, D. Fujishima, M. Kai, N. Yoshimura, T. Yamaguchi, Y. Ichihashi, T. Mishima, N. Matsubara and T. Yamanishi, Achievement of more than 25% conversion efficiency with crystalline silicon heterojunction solar cell, IEEE J. Photovolt., 2014 Sep 10, 4(6), 1433–1435 Search PubMed.
- Applications of piezoelectric quartz crystal microbalances, ed. Lu C and Czanderna AW, Elsevier; 2012 Dec 2 Search PubMed.
- N. Neophytou, Prospects of low-dimensional and nanostructured silicon-based thermoelectric materials: findings from theory and simulation, Eur. Phys. J. B, 2015 Apr, 88(4), 1–2 Search PubMed.
- A. Morata, M. Pacios, G. Gadea, C. Flox, D. Cadavid, A. Cabot and A. Tarancón, Large-area and adaptable electrospun silicon-based thermoelectric nanomaterials with high energy conversion efficiencies, Nat. Commun., 2018 Nov 12, 9(1), 1–8 Search PubMed.
- Q. J. Le, T. Wang, D. N. Tran, F. Dong, Y. X. Zhang and D. Losic, Morphology-controlled MnO 2 modified silicon diatoms for high-performance asymmetric supercapacitors, J. Mater. Chem. A, 2017, 5(22), 10856–10865 RSC.
- L. F. Guo, S. Y. Zhang, J. Xie, D. Zhen, Y. Jin, K. Y. Wan, D. G. Zhuang, W. Q. Zheng and X. B. Zhao, Controlled synthesis of nanosized Si by magnesiothermic reduction from diatomite as anode material for Li-ion batteries. International Journal of Minerals, J. Mater. Metall., 2020 Apr, 27(4), 515–525 Search PubMed.
- P. Aggrey, B. Abdusatorov, Y. Kan, I. A. Salimon, S. A. Lipovskikh, S. Luchkin, D. M. Zhigunov, A. I. Salimon and A. M. Korsunsky, In situ formation of nanoporous silicon on a silicon wafer via the magnesiothermic reduction reaction (MRR) of diatomaceous earth, Nanomaterials, 2020 Apr, 10(4), 601 Search PubMed.
- G. Leng, G. Qiao, Z. Jiang, G. Xu, Y. Qin, C. Chang and Y. Ding, Micro encapsulated & form-stable phase change materials for high temperature thermal energy storage, Appl. Energy, 2018 May 1, 217, 212–220 Search PubMed.
- P. Aggrey, A. I. Salimon, B. Abdusatorov, S. S. Fedotov and A. M. Korsunsky, The structure and phase composition of nano-silicon as a function of calcination conditions of diatomaceous earth, Mater. Today: Proc., 2020 Jan 1, 33, 1884–1892 Search PubMed.
- S. Martinovic, M. Vlahovic, T. Boljanac and L. Pavlovic, Preparation of filter aids based on diatomites, Int. J. Miner. Process., 2006 Sep 1, 80(2–4), 255–260 Search PubMed.
- R. Zheng, Z. Ren, H. Gao, A. Zhang and Z. Bian, Effects of calcination on silica phase transition in diatomite, J. Alloys Compd., 2018 Aug 15, 757, 364–371 Search PubMed.
- J. R. Szczech and S. Jin, Mg2Si nanocomposite converted from diatomaceous earth as a potential thermoelectric nanomaterial, J. Solid State Chem., 2008 Jul 1, 181(7), 1565–1570 Search PubMed.
- N. Ediz, İ. Bentli and İ. Tatar, Improvement in filtration characteristics of diatomite by calcination, Int. J. Miner. Process., 2010 Apr 28, 94(3–4), 129–134 Search PubMed.
- B. Yılmaz and N. Ediz, The use of raw and calcined diatomite in cement production, Cem. Concr. Compos., 2008 Mar 1, 30(3), 202–211 Search PubMed.
- Y. Xia, F. Li, Y. Jiang, M. Xia, B. Xue and Y. Li, Interface actions between TiO2 and porous diatomite on the structure and photocatalytic activity of TiO2-diatomite, Appl. Surf. Sci., 2014 Jun 1, 303, 290–296 Search PubMed.
- A. M. Korsunsky, Y. D. Bedoshvili, J. Cvjetinovic, P. Aggrey, K. I. Dragnevski, D. A. Gorin, A. I. Salimon and Y. V. Likhoshway, Siliceous diatom frustules–A smart nanotechnology platform, Mater. Today: Proc., 2020 Jan 1, 33, 2032–2040 Search PubMed.
- X. Tang, G. Wen and Y. Song, Novel scalable synthesis of porous silicon/carbon composite as anode material for superior lithium-ion batteries, J. Alloys Compd., 2018 Mar 30, 739, 510–517 Search PubMed.
- J. Wang, D. H. Liu, Y. Y. Wang, B. H. Hou, J. P. Zhang, R. S. Wang and X. L. Wu, Dual-carbon enhanced silicon-based composite as superior anode material for lithium ion batteries, J. Power Sources, 2016 Mar 1, 307, 738–745 Search PubMed.
- D. Lončarević and Ž. Čupić The perspective of using nanocatalysts in the environmental requirements and energy needs of industry. in Industrial Applications of Nanomaterials, Elsevier, 2019 Jan 1, pp. 91–122 Search PubMed.
- K. Schulte and F. R. L. VonF, High-density polyethylene fiber/polyethylene matrix composites, Compr. Compos. Mater. II, 2000, 231–248 Search PubMed.
- M. D. Wakeman and C. D. Rudd, Compression molding of thermoplastic composites, Compr. Compos. Mater. II, 2000, 915–963 Search PubMed.
- J. I. A. Pei-ying, Application of impregnation technology in the die castings [J], China National Knowledge Infrastructure, Shaanxi Coal, 2006, p. 4 Search PubMed.
- H. Nazir, M. Batool, F. J. Osorio, M. Isaza-Ruiz, X. Xu, K. Vignarooban, P. Phelan and A. M. Kannan, Recent developments in phase change materials for energy storage applications: A review, Int. J. Heat Mass Transfer, 2019 Feb 1, 129, 491–523 Search PubMed.
- L. N. Vakhitova. Fire retardant nanocoating for wood protection. in Nanotechnology in Eco-efficient Construction, Woodhead Publishing, 2019 Jan 1, pp. 361–391 Search PubMed.
- F. Rodríguez-Reinoso and A. Sepúlveda-Escribano. Porous carbons in adsorption and catalysis. in Handbook of surfaces and interfaces of materials, Academic Press, 2001 Jan 1, pp. 309–355 Search PubMed.
- V. P. Lehto and J. Riikonen. Drug loading and characterization of porous silicon materials, in Porous silicon for biomedical applications, Woodhead Publishing, 2014 Jan 1, pp. 337–355 Search PubMed.
- P. Liu, X. Gu, L. Bian, L. Peng and H. He, Capric acid/intercalated diatomite as form-stable composite phase change material for thermal energy storage, J. Therm. Anal. Calorim., 2019 Oct, 138(1), 359–368 Search PubMed.
- P. Liu, X. Gu, L. Bian, X. Cheng, L. Peng and H. He, Thermal properties and enhanced thermal conductivity of capric acid/diatomite/carbon nanotube composites as form-stable phase change materials for thermal energy storage, ACS Omega, 2019 Feb 11, 4(2), 2964–2972 Search PubMed.
- W. Jia, C. Wang, T. Wang, Z. Cai and K. Chen, Preparation and performances of palmitic acid/diatomite form-stable composite phase change materials, Int. J. Energy Res., 2020 May, 44(6), 4298–4308 Search PubMed.
- T. Weege. Basic impregnation techniques [for windings]. InProceedings: Electrical Insulation Conference and Electrical Manufacturing and Coil Winding Conference, IEEE, 1997 Sep 25, pp. 709–715 Search PubMed.
- Y. Zhao and J. Xie, Practical applications of vacuum impregnation in fruit and vegetable processing, Trends Food Sci. Technol., 2004 Sep 1, 15(9), 434–451 Search PubMed.
- U. Sabu, G. Logesh, M. Rashad, A. Joy and M. Balasubramanian, Microwave assisted synthesis of biomorphic hydroxyapatite, Ceram. Int., 2019 Apr 15, 45(6), 6718–6722 Search PubMed.
- N. Amini, V. S. Haritos and A. Tanksale, Microwave assisted pretreatment of eucalyptus sawdust enhances enzymatic saccharification and maximizes fermentable sugar yield, Renewable energy, 2018 Nov 1, 127, 653–660 Search PubMed.
- T. Qian, J. Li and Y. Deng, Pore structure modified diatomite-supported PEG composites for thermal energy storage, Sci. Rep., 2016 Sep 1, 6(1), 1–4 Search PubMed.
- J. Zong, D. Wang, Y. Jin, X. Gao and X. Wang. Preparation of Stearic acid/Diatomite Composite Phase Change Material, in E3S Web of Conferences 2021, EDP Sciences, vol. 245, p. 03070 Search PubMed.
- J. Jin, L. Liu, R. Liu, H. Wei, G. Qian, J. Zheng, W. Xie, F. Lin and J. Xie, Preparation and thermal performance of binary fatty acid with diatomite as form-stable composite phase change material for cooling asphalt pavements, Constr. Build. Mater., 2019 Nov 30, 226, 616–624 Search PubMed.
- T. Wang, Q. Le, J. Zhang, Y. Zhang and W. Li, Carbon cloth@ T-Nb2O5@ MnO2: A rational exploration of manganese oxide for high performance supercapacitor, Electrochim. Acta, 2017 Nov 1, 253, 311–318 Search PubMed.
- S. Feng and R. Xu, New materials in hydrothermal synthesis, Acc. Chem. Res., 2001 Mar 20, 34(3), 239–247 Search PubMed.
- C. Jing, X. Liu, X. Liu, D. Jiang, B. Dong, F. Dong, J. Wang, N. Li, T. Lan and Y. Zhang, Crystal morphology evolution of Ni–Co layered double hydroxide nanostructure towards high-performance biotemplate asymmetric supercapacitors, CrystEngComm, 2018, 20(46), 7428–7434 RSC.
- K. Li, S. Feng, C. Jing, Y. Chen, X. Liu, Y. Zhang and L. Zhou, Assembling a double shell on a diatomite skeleton ternary complex with conductive polypyrrole for the enhancement of supercapacitors, Chem. Commun., 2019, 55(91), 13773–13776 RSC.
- Y. Jia, W. Han, G. Xiong and W. Yang, Layer-by-layer assembly of TiO2 colloids onto diatomite to build hierarchical porous materials, J. Colloid Interface Sci., 2008 Jul 15, 323(2), 326–331 Search PubMed.
- J. He, D. Chen, Y. Li, J. Shao, J. Xie, Y. Sun, Z. Yan and J. Wang, Diatom-templated TiO2 with enhanced photocatalytic activity: biomimetics of photonic crystals, Appl. Phys. A, 2013 Nov, 113(2), 327–332 Search PubMed.
- B. Wang, F. C. de Godoi, Z. Sun, Q. Zeng, S. Zheng and R. L. Frost, Synthesis, characterization and activity of an immobilized photocatalyst: natural porous diatomite supported titania nanoparticles, J. Colloid Interface Sci., 2015 Jan 15, 438, 204–211 Search PubMed.
- J. Ouwehand, E. Van Eynde, E. De Canck, S. Lenaerts, A. Verberckmoes and P. Van Der Voort, Titania-functionalized diatom frustules as photocatalyst for indoor air purification, Applied Catalysis B: Environmental, 2018 Jun 15, 226, 303–310 Search PubMed.
- Q. Zhu, Y. Zhang, F. Zhou, F. Lv, Z. Ye, F. Fan and P. K. Chu, Preparation and characterization of Cu2O–ZnO immobilized on diatomite for photocatalytic treatment of red water produced from manufacturing of TNT, Chem. Eng. J., 2011 Jun 15, 171(1), 61–68 Search PubMed.
- J. Fang, Q. Liu, W. Zhang, J. Gu, Y. Su, H. Su, C. Guo and D. Zhang, Ag/diatomite for highly efficient solar vapor generation under one-sun irradiation, J. Mater. Chem. A, 2017, 5(34), 17817–17821 RSC.
- F. A. Khan, Synthesis of Nanomaterials: Methods & Technology. In Applications of Nanomaterials in Human Health, Springer, Singapore, 2020, pp. 15–21 Search PubMed.
- Nanomaterials: Synthesis, characterization, and applications, ed. Haghi AK, Zachariah AK and Kalariakkal N, CRC Press, 2013 Mar 11 Search PubMed.
- Y. B. Pottathara, Y. Grohens, V. Kokol, N. Kalarikkal and S. Thomas. Synthesis and processing of emerging two-dimensional nanomaterials, in Nanomaterials Synthesis, Elsevier, 2019 Jan 1, pp. 1–25 Search PubMed.
- R. J. Varghese, S. Parani, S. Thomas, O. S. Oluwafemi and J. Wu. Introduction to nanomaterials: synthesis and applications, in Nanomaterials for Solar Cell Applications, 2019 Jan 1, pp. 75–95, Elsevier Search PubMed.
- T. C. Mokhena, M. J. John, M. A. Sibeko, V. C. Agbakoba, M. J. Mochane, A. Mtibe, T. H. Mokhothu, T. S. Motsoeneng, M. M. Phiri, M. J. Phiri and P. S. Hlangothi. Nanomaterials: Types, synthesis and characterization, in Nanomaterials in Biofuels Research, Springer, Singapore, 2020, pp. 115–141 Search PubMed.
- Z. Xing, J. Lu and X. Ji, A brief review of metallothermic reduction reactions for materials preparation, Small Methods, 2018 Dec, 2(12), 1800062 Search PubMed.
- A. Bogacz, S. Rumianowski, W. Szymanski and W. Szklarski. Technology of light lanthanide metals production, in Advances in Molten Salts, Begell House, 1999 Jan 1 Search PubMed.
- U. B. Pal, D. E. Woolley and G. B. Kenney, Emerging SOM technology for the green synthesis of metals from oxides, Jom, 2001 Oct, 53(10), 32–35 Search PubMed.
- K. Yasuda, K. Saegusa and T. H. Okabe, Aluminum subhalide as a reductant for metallothermic reduction, High Temp. Mater. Processes, 2011 Aug 1, 30(4), 411–423 Search PubMed.
- M. A. Rhamdhani, M. A. Dewan, G. A. Brooks, B. J. Monaghan and L. Prentice, Alternative Al production methods: Part 1–a review of indirect carbothermal routes, Miner. Process. Extr. Metall., 2013 Jun 1, 122(2), 87–104 Search PubMed.
- H. P. Martin, R. Ecke and E. Müller, Synthesis of nanocrystalline silicon carbide powder by carbothermal reduction, J. Eur. Ceram. Soc., 1998 Nov 1, 18(12), 1737–1742 Search PubMed.
- D. J. Fray, Emerging molten salt technologies for metals production, JOM, 2001 Oct, 53(10), 27–31 Search PubMed.
- Z. Xing, N. Gao, Y. Qi, X. Ji and H. Liu, Influence of enhanced carbon crystallinity of nanoporous graphite on the cathode performance of microbial fuel cells, Carbon, 2017 May 1, 115, 271–278 Search PubMed.
- Z. Bao, M. R. Weatherspoon, S. Shian, Y. Cai, P. D. Graham, S. M. Allan, G. Ahmad, M. B. Dickerson, B. C. Church, Z. Kang and H. W. Abernathy Iii, Chemical reduction of three-dimensional silica micro-assemblies into microporous silicon replicas, Nature, 2007 Mar, 446(7132), 172–175 Search PubMed.
- F. Gallego-Gómez, M. Ibisate, D. Golmayo, F. J. Palomares, M. Herrera, J. Hernández, S. I. Molina and L. C. Blanco Á, Light emission from nanocrystalline Si inverse opals and controlled passivation by atomic layer deposited Al2O3, Adv. Mater., 2011 Nov 23, 23(44), 5219–5223 Search PubMed.
- E. K. Richman, C. B. Kang, T. Brezesinski and S. H. Tolbert, Ordered mesoporous silicon through magnesium reduction of polymer templated silica thin films, Nano Lett., 2008 Sep 10, 8(9), 3075–3079 Search PubMed.
- C. Y. Khripin, D. Pristinski, D. R. Dunphy, C. J. Brinker and B. Kaehr, Protein-directed assembly of arbitrary three-dimensional nanoporous silica architectures, ACS Nano, 2011 Feb 22, 5(2), 1401–1409 Search PubMed.
- Y. Zhang and J. Huang, Hierarchical nanofibrous silicon as replica of natural cellulose substance, J. Mater. Chem., 2011, 21(20), 7161–7165 RSC.
- J. K. Yoo, J. Kim, Y. S. Jung and K. Kang, Scalable fabrication of silicon nanotubes and their application to energy storage, Adv. Mater., 2012 Oct 23, 24(40), 5452–5456 Search PubMed.
- W. Deqing and S. Ziyuan, Aluminothermic reduction of silica for the synthesis of alumina-aluminum-silicon composite, J. Mater. Synth. Process., 2001 Sep, 9(5), 241–246 Search PubMed.
- J. Cui, Y. Cui, S. Li, H. Sun, Z. Wen and J. Sun, Microsized porous SiO x@ C composites synthesized through aluminothermic reduction from rice husks and used as anode for lithium-ion batteries, ACS Appl. Mater. Interfaces, 2016 Nov 9, 8(44), 30239–30247 Search PubMed.
- N. Lin, Y. Han, J. Zhou, K. Zhang, T. Xu, Y. Zhu and Y. Qian, A low temperature molten salt process for aluminothermic reduction of silicon oxides to crystalline Si for Li-ion batteries, Energy Environ. Sci., 2015, 8(11), 3187–3191 RSC.
- Z. W. Zhou, Y. T. Liu, X. M. Xie and X. Y. Ye, Aluminothermic reduction enabled synthesis of silicon hollow microspheres from commercialized silica nanoparticles for superior lithium storage, Chem. Commun., 2016, 52(54), 8401–8404 RSC.
- Y. Lai, J. R. Thompson and M. Dasog, Metallothermic reduction of silica nanoparticles to porous silicon for drug delivery using new and existing reductants, Chem. - Eur. J., 2018 Jun 4, 24(31), 7913–7920 Search PubMed.
- I. M. Morsi, K. E. Barawy, M. B. Morsi and S. R. Abdel-Gawad, Silicothermic reduction of dolomite ore under inert atmosphere, Can. Metall. Q., 2002 Jan 1, 41(1), 15–28 Search PubMed.
- J. Zhou, H. Zhao, N. Lin, T. Li, Y. Li, S. Jiang, J. Tian and Y. Qian, Silicothermic reduction reaction for fabricating interconnected Si–Ge nanocrystals with fast and stable Li-storage, J. Mater. Chem. A, 2020, 8(14), 6597–6606 RSC.
- G. D. Sun and G. H. Zhang, Study on the preparation of molybdenum silicides by the silicothermic reduction of MoS2, J. Alloys Compd., 2017 Dec 25, 728, 295–306 Search PubMed.
- M. Li, C. Ke and J. Zhang, Synthesis of ZrB2 powders by molten-salt participating silicothermic reduction, J. Alloys Compd., 2020 Sep 5, 834, 155062 Search PubMed.
- J. Entwistle, A. Rennie and S. Patwardhan, A review of magnesiothermic reduction of silica to porous silicon for lithium-ion battery applications and beyond, J. Mater. Chem. A, 2018, 6(38), 18344–18356 RSC.
- L. Batchelor, A. Loni, L. T. Canham, M. Hasan and J. L. Coffer, Manufacture of mesoporous silicon from living plants and agricultural waste: an environmentally friendly and scalable process, Silicon, 2012 Oct, 4(4), 259–266 Search PubMed.
- W. Luo, X. Wang, C. Meyers, N. Wannenmacher, W. Sirisaksoontorn, M. M. Lerner and X. Ji, Efficient fabrication of nanoporous Si and Si/Ge enabled by a heat scavenger in magnesiothermic reactions, Sci. Rep., 2013 Jul 17, 3(1), 1–7 Search PubMed.
- Z. Favors, W. Wang, H. H. Bay, Z. Mutlu, K. Ahmed, C. Liu, M. Ozkan and C. S. Ozkan, Scalable synthesis of nano-silicon from beach sand for long cycle life Li-ion batteries, Sci. Rep., 2014 Jul 8, 4(1), 1–7 Search PubMed.
- W. Wang, Z. Favors, R. Ionescu, R. Ye, H. H. Bay, M. Ozkan and C. S. Ozkan, Monodisperse porous silicon spheres as anode materials for lithium ion batteries, Sci. Rep., 2015 Mar 5, 5(1), 1–6 Search PubMed.
- C. Li, C. Liu, W. Wang, Z. Mutlu, J. Bell, K. Ahmed, R. Ye, M. Ozkan and C. S. Ozkan, Silicon derived from glass bottles as anode materials for lithium ion full cell batteries, Sci. Rep., 2017 Apr 19, 7(1), 1 Search PubMed.
- L. Shen, X. Guo, X. Fang, Z. Wang and L. Chen, Magnesiothermically reduced diatomaceous earth as a porous silicon anode material for lithium ion batteries, J. Power Sources, 2012 Sep 1, 213, 229–232 Search PubMed.
- L. Shen, Z. Wang and L. Chen, Carbon-coated hierarchically porous silicon as anode material for lithium ion batteries, RSC Adv., 2014, 4(29), 15314–15318 RSC.
- W. Wu, M. Wang, R. Wang, D. Xu, H. Zeng, C. Wang, Y. Cao and Y. Deng, Magnesio-mechanochemical reduced SiOx for high-performance lithium ion batteries, J. Power Sources, 2018 Dec 15, 407, 112–122 Search PubMed.
- J. Liang, X. Li, Z. Hou, W. Zhang, Y. Zhu and Y. Qian, A deep reduction and partial oxidation strategy for fabrication of mesoporous Si anode for lithium ion batteries, ACS Nano, 2016 Feb 23, 10(2), 2295–2304 Search PubMed.
- T. Chen, J. Wu, Q. Zhang and X. Su, Recent advancement of SiOx based anodes for lithium-ion batteries, J. Power Sources, 2017 Sep 30, 363, 126–144 Search PubMed.
- W. Luo, X. Chen, Y. Xia, M. Chen, L. Wang, Q. Wang, W. Li and J. Yang, Surface and interface engineering of silicon-based anode materials for lithium-ion batteries, Adv. Energy Mater., 2017 Dec, 7(24), 1701083 Search PubMed.
- N. Sarier and E. Onder, Organic phase change materials and their textile applications: an overview, Thermochim. Acta, 2012 Jul 20, 540, 7–60 Search PubMed.
- Z. Zhang, G. Shi, S. Wang, X. Fang and X. Liu, Thermal energy storage cement mortar containing n-octadecane/expanded graphite composite phase change material, Renewable energy, 2013 Feb 1, 50, 670–675 Search PubMed.
- S. G. Jeong, J. Jeon, J. H. Lee and S. Kim, Optimal preparation of PCM/diatomite composites for enhancing thermal properties, Int. J. Heat Mass Transfer, 2013 Jul 1, 62, 711–717 Search PubMed.
- B. Xu and Z. Li, Performance of novel thermal energy storage engineered cementitious composites incorporating a paraffin/diatomite composite phase change material, Appl. Energy, 2014 May 15, 121, 114–122 Search PubMed.
- J. Huang, B. Wu, S. Lyu, T. Li, H. Han, D. Li, J. K. Wang, J. Zhang, X. Lu and D. Sun, Improving the thermal energy storage capability of diatom-based biomass/polyethylene glycol composites phase change materials by artificial culture methods, Sol. Energy Mater. Sol. Cells, 2021 Jan 1, 219, 110797 Search PubMed.
- G. Xiong, K. P. Hembram, R. G. Reifenberger and T. S. Fisher, MnO2-coated graphitic petals for supercapacitor electrodes, J. Power Sources, 2013 Apr 1, 227, 254–259 Search PubMed.
- Q. Wu, Y. Liu and Z. Hu, Flower-like NiO microspheres prepared by facile method as supercapacitor electrodes, J. Solid State Electrochem., 2013 Jun 1, 17(6), 1711–1716 Search PubMed.
- G. Wang, L. Zhang and J. Zhang, A review of electrode materials for electrochemical supercapacitors, Chem. Soc. Rev., 2012, 41(2), 797–828 RSC.
- Z. Wang, C. Ma, H. Wang, Z. Liu and Z. Hao, Facilely synthesized Fe2O3–graphene nanocomposite as novel electrode materials for supercapacitors with high performance, J. Alloys Compd., 2013 Mar 5, 552, 486–491 Search PubMed.
- R. Liang, H. Cao and D. Qian, MoO 3 nanowires as electrochemical pseudocapacitor materials, Chem. Commun., 2011, 47(37), 10305–10307 RSC.
- Q. Liao and C. Wang, Amorphous FeOOH nanorods and Co 3 O 4 nanoflakes as binder-free electrodes for high-performance all-solid-state asymmetric supercapacitors, CrystEngComm, 2019, 21(4), 662–672 RSC.
- W. Wei, X. Cui, W. Chen and D. G. Ivey, Manganese oxide-based materials as electrochemical supercapacitor electrodes, Chem. Soc. Rev., 2011, 40(3), 1697–1721 RSC.
- L. Peng, X. Peng, B. Liu, C. Wu, Y. Xie and G. Yu, Ultrathin two-dimensional MnO2/graphene hybrid nanostructures for high-performance, flexible planar supercapacitors, Nano Lett., 2013 May 8, 13(5), 2151–2157 Search PubMed.
- Y. X. Zhang, W. Huo, K. Li, Q. Sun and T. Cao, Supercapacitor nanomaterials, Advanced Nanomaterials for Electrochemical-Based Energy Conversion and Storage, Elsevier, 2020, pp. 295–324 Search PubMed.
- L. Hu, B. Qu, L. Chen and Q. Li, Low-temperature preparation of ultrathin nanoflakes assembled tremella-like NiO hierarchical nanostructures for high-performance lithium-ion batteries, Mater. Lett., 2013 Oct 1, 108, 92–95 Search PubMed.
- Y. J. Mai, J. P. Tu, X. H. Xia, C. D. Gu and X. L. Wang, Co-doped NiO nanoflake arrays toward superior anode materials for lithium ion batteries, J. Power Sources, 2011 Aug 1, 196(15), 6388–6393 Search PubMed.
- Q. Wu, Z. Hu and Y. Liu, A novel electrode material of NiO prepared by facile hydrothermal method for electrochemical capacitor application, J. Mater. Eng. Perform., 2013 Aug, 22(8), 2398–2402 Search PubMed.
- L. Marcinauskas, Ž. Kavaliauskas and V. Valinčius, Carbon and nickel oxide/carbon composites as electrodes for supercapacitors, J. Mater. Sci. Technol., 2012 Oct 1, 28(10), 931–936 Search PubMed.
- A. S. Arico, P. Bruce, B. Scrosati, J. M. Tarascon and W. Van Schalkwijk, Nanostructured materials for advanced energy conversion and storage devices, Mater. Sustainable Energy Appl., 2011, 148–159 Search PubMed.
- W. Qi, J. G. Shapter, Q. Wu, T. Yin, G. Gao and D. Cui, Nanostructured anode materials for lithium-ion batteries: principle, recent progress and future perspectives, J. Mater. Chem. A, 2017, 5(37), 19521–19540 RSC.
- W. S. Kim, Y. Hwa, J. H. Shin, M. Yang, H. J. Sohn and S. H. Hong, Scalable synthesis of silicon nanosheets from sand as an anode for Li-ion batteries, Nanoscale, 2014, 6(8), 4297–4302 RSC.
- Y. Yao, M. T. McDowell, I. Ryu, H. Wu, N. Liu, L. Hu, W. D. Nix and Y. Cui, Interconnected silicon hollow nanospheres for lithium-ion battery anodes with long cycle life, Nano Lett., 2011 Jul 13, 11(7), 2949–2954 Search PubMed.
- T. H. Hwang, Y. M. Lee, B. S. Kong, J.
S. Seo and J. W. Choi, Electrospun core–shell fibers for robust silicon nanoparticle-based lithium ion battery anodes, Nano Lett., 2012 Feb 8, 12(2), 802–807 Search PubMed.
- M. Ashuri, Q. He and L. L. Shaw, Silicon as a potential anode material for Li-ion batteries: where size, geometry and structure matter, Nanoscale, 2016, 8(1), 74–103 RSC.
- H. K. Liu, Z. P. Guo, J. Z. Wang and K. Konstantinov, Si-based anode materials for lithium rechargeable batteries, J. Mater. Chem., 2010, 20(45), 10055–10057 RSC.
- P. Li, G. Zhao, X. Zheng, X. Xu, C. Yao, W. Sun and S. X. Dou, Recent progress on silicon-based anode materials for practical lithium-ion battery applications, Energy Storage Mater., 2018 Nov 1, 15, 422–446 Search PubMed.
- X. Li, M. Gu, S. Hu, R. Kennard, P. Yan, X. Chen, C. Wang, M. J. Sailor, J. G. Zhang and J. Liu, Mesoporous silicon sponge as an anti-pulverization structure for high-performance lithium-ion battery anodes, Nat. Commun., 2014 Jul 8, 5(1), 1–7 Search PubMed.
- P. Li, J. Y. Hwang and Y. K. Sun, Nano/microstructured silicon–graphite composite anode for high-energy-density Li-ion battery, ACS Nano, 2019 Feb 13, 13(2), 2624–2633 Search PubMed.
- X. Ding, X. Liu, Y. Huang, X. Zhang, Q. Zhao, X. Xiang, G. Li, P. He, Z. Wen, J. Li and Y. Huang, Enhanced electrochemical performance promoted by monolayer graphene and void space in silicon composite anode materials, Nano Energy, 2016 Sep 1, 27, 647–657 Search PubMed.
- X. Tao, Y. Liu, W. Liu, G. Zhou, J. Zhao, D. Lin, C. Zu, O. Sheng, W. Zhang, H. W. Lee and Y. Cui, Solid-state lithium–sulfur batteries operated at 37 C with composites of nanostructured Li7La3Zr2O12/carbon foam and polymer, Nano Lett., 2017 May 10, 17(5), 2967–2972 Search PubMed.
- R. Bouchet, S. Maria, R. Meziane, A. Aboulaich, L. Lienafa, J. P. Bonnet, T. N. Phan, D. Bertin, D. Gigmes, D. Devaux and R. Denoyel, Single-ion BAB triblock copolymers as highly efficient electrolytes for lithium-metal batteries, Nat. Mater., 2013 May, 12(5), 452–457 Search PubMed.
- Z. Xue, D. He and X. Xie, Poly (ethylene oxide)-based electrolytes for lithium-ion batteries, J. Mater. Chem. A, 2015, 3(38), 19218–19253 RSC.
- A. Manthiram, Y. Fu, S. H. Chung, C. Zu and Y. S. Su, Rechargeable lithium–sulfur batteries, Chem. Rev., 2014 Dec 10, 114(23), 11751–11787 Search PubMed.
- L. Chen and L. L. Shaw, Recent advances in lithium–sulfur batteries, J. Power Sources, 2014 Dec 1, 267, 770–783 Search PubMed.
- A. Manthiram, S. H. Chung and C. Zu, Lithium–sulfur batteries: progress and prospects, Adv. Mater., 2015 Mar, 27(12), 1980–2006 Search PubMed.
- Z. W. Seh, Y. Sun, Q. Zhang and Y. Cui, Designing high-energy lithium–sulfur batteries, Chem. Soc. Rev., 2016, 45(20), 5605–5634 RSC.
- P. Cong, S. Chen and H. Chen, Effects of diatomite on the properties of asphalt binder, Constr. Build. Mater., 2012 May 1, 30, 495–499 Search PubMed.
- L. Xu, X. Gao, Z. Li and C. Gao, Removal of fluoride by nature diatomite from high-fluorine water: an appropriate pretreatment for nanofiltration process, Desalination, 2015 Aug 3, 369, 97–104 Search PubMed.
- S. LeBlanc, Thermoelectric generators: Linking material properties and systems engineering for waste heat recovery applications, Sustainable Mater. Technol., 2014 Dec 1, 1, 26–35 Search PubMed.
- K. Biswas, J. He, I. D. Blum, C. I. Wu, T. P. Hogan, D. N. Seidman, V. P. Dravid and M. G. Kanatzidis, High-performance bulk thermoelectrics with all-scale hierarchical architectures, Nature, 2012 Sep, 489(7416), 414–418 Search PubMed.
- Z. Chen, X. Zhang and Y. Pei, Manipulation of phonon transport in thermoelectrics, Adv. Mater., 2018 Apr, 30(17), 1705617 Search PubMed.
- P. A. Zong, R. Hanus, M. Dylla, Y. Tang, J. Liao, Q. Zhang, G. J. Snyder and L. Chen, Skutterudite with graphene-modified grain-boundary complexion enhances zT enabling high-efficiency thermoelectric device, Energy Environ. Sci., 2017, 10(1), 183–191 RSC.
- Q. Zhang, Z. Zhou, M. Dylla, M. T. Agne, Y. Pei, L. Wang, Y. Tang, J. Liao, J. Li, S. Bai and W. Jiang, Realizing high-performance thermoelectric power generation through grain boundary engineering of skutterudite-based nanocomposites, Nano Energy, 2017 Nov 1, 41, 501–510 Search PubMed.
- G. Schierning, Silicon nanostructures for thermoelectric devices: A review of the current state of the art, Phys. Status Solidi A, 2014 Jun, 211(6), 1235–1249 Search PubMed.
- C. B. Vining, Desperately seeking silicon, Nature, 2008 Jan, 451(7175), 132–133 Search PubMed.
- A. I. Boukai, Y. Bunimovich, J. Tahir-Kheli, J. K. Yu, W. A. Goddard Iii and J. R. Heath, Silicon nanowires as efficient thermoelectric materials, nature, 2008 Jan, 451(7175), 168–171 Search PubMed.
- A. I. Hochbaum, R. Chen, R. D. Delgado, W. Liang, E. C. Garnett, M. Najarian, A. Majumdar and P. Yang, Enhanced thermoelectric performance of rough silicon nanowires, Nature, 2008 Jan, 451(7175), 163–167 Search PubMed.
- S. K. Bux, R. G. Blair, P. K. Gogna, H. Lee, G. Chen, M. S. Dresselhaus, R. B. Kaner and J. P. Fleurial, Nanostructured bulk silicon as an effective thermoelectric material, Adv. Funct. Mater., 2009 Aug 10, 19(15), 2445–2452 Search PubMed.
- V. Lysenko, S. Perichon, B. Remaki and D. Barbier, Thermal isolation in microsystems with porous silicon, Sens. Actuators, A, 2002 Apr 30, 99(1–2), 13–24 Search PubMed.
- G. Gesele, J. Linsmeier, V. Drach, J. Fricke and R. Arens-Fischer, Temperature-dependent thermal conductivity of porous silicon, J. Phys. D: Appl. Phys., 1997 Nov 7, 30(21), 2911 Search PubMed.
- M. S. Dresselhaus, G. Chen, M. Y. Tang, R. G. Yang, H. Lee, D. Z. Wang, Z. F. Ren, J. P. Fleurial and P. Gogna, New directions for low-dimensional thermoelectric materials, Adv. Mater., 2007 Apr 20, 19(8), 1043–1053 Search PubMed.
- T. Fuhrmann, S. Landwehr, M. El Rharbi-Kucki and M. Sumper, Diatoms as living photonic crystals, Appl. Phys. B: Lasers Opt., 2004 Feb, 78(3), 257–260 Search PubMed.
- S. Yamanaka, R. Yano, H. Usami, N. Hayashida, M. Ohguchi, H. Takeda and K. Yoshino, Optical properties of diatom silica frustule with special reference to blue light, J. Appl. Phys., 2008 Apr 1, 103(7), 074701 Search PubMed.
- J. Noyes, M. Sumper and P. Vukusic, Light manipulation in a marine diatom, J. Mater. Res., 2008 Dec, 23(12), 3229–3235 Search PubMed.
- X. Chen, C. Wang, E. Baker and C. Sun, Numerical and experimental investigation of light trapping effect of nanostructured diatom frustules, Sci. Rep., 2015 Jul 9, 5(1), 1–9 Search PubMed.
- J. Romann, J. C. Valmalette, A. Røyset and M. A. Einarsrud, Optical properties of single diatom frustules revealed by confocal microspectroscopy, Opt. Lett., 2015 Mar 1, 40(5), 740–743 Search PubMed.
- W. H. Kooistra, R. Gersonde, L. K. Medlin and D. G. Mann. The origin and evolution of the diatoms: their adaptation to a planktonic existence. Evolution of primary producers in the sea. 2007 Jan 1, pp. 207–49 Search PubMed.
- E. V. Armbrust, The life of diatoms in the world's oceans, Nature, 2009 May, 459(7244), 185–192 Search PubMed.
- F. Gaspari and S. Quaranta, 2.5 PV Materials, Elsevier Ltd., 2018, vol. 2 Search PubMed.
- J. Baxter, Z. Bian, G. Chen, D. Danielson, M. S. Dresselhaus, A. G. Fedorov, T. S. Fisher, C. W. Jones, E. Maginn, U. Kortshagen and A. Manthiram, Nanoscale design to enable the revolution in renewable energy, Energy Environ. Sci., 2009, 2(6), 559–588 RSC.
- C. Z. Hotz. Quantum Dots, in Molecular Biomethods Handbook, Humana Press, 2008, pp. 697–710 Search PubMed.
- D. Wöhrle and D. Meissner, Organic solar cells, Adv. Mater., 1991 Mar, 3(3), 129–138 Search PubMed.
- B. O'regan and M. Grätzel, A low-cost, high-efficiency solar cell based on dye-sensitized colloidal TiO 2 films, Nature, 1991 Oct, 353(6346), 737–740 Search PubMed.
- M. K. Nazeeruddin, A. Kay, I. Rodicio, R. Humphry-Baker, E. Müller, P. Liska, N. Vlachopoulos and M. Grätzel, Conversion of light to electricity by cis-X2bis (2, 2'-bipyridyl-4, 4'-dicarboxylate) ruthenium (II) charge-transfer sensitizers (X= Cl-, Br-, I-, CN-, and SCN-) on nanocrystalline titanium dioxide electrodes, J. Am. Chem. Soc., 1993 Jul, 115(14), 6382–6390 Search PubMed.
- D. Losic, G. Triani, P. J. Evans, A. Atanacio, J. G. Mitchell and N. H. Voelcker, Controlled pore structure modification of diatoms by atomic layer deposition of TiO 2, J. Mater. Chem., 2006, 16(41), 4029–4034 RSC.
- Y. Tachibana, H. Y. Akiyama and S. Kuwabata, Optical simulation of transmittance into a nanocrystalline anatase TiO2 film for solar cell applications, Sol. Energy Mater. Sol. Cell., 2007 Jan 23, 91(2–3), 201–206 Search PubMed.
- T. M. Bandara, M. Furlani, I. Albinsson, A. Wulff and B. E. Mellander, Diatom frustules enhancing the efficiency of gel polymer electrolyte based dye-sensitized solar cells with multilayer photoelectrodes, Nanoscale Adv., 2020, 2(1), 199–209 RSC.
- K. Maeda, K. Teramura, D. Lu, T. Takata, N. Saito, Y. Inoue and K. Domen, Photocatalyst releasing hydrogen from water, Nature, 2006 Mar, 440(7082), 295 Search PubMed.
- S. Y. Lee and S. J. Park, TiO2 photocatalyst for water treatment applications, J. Ind. Eng. Chem., 2013 Nov 25, 19(6), 1761–1769 Search PubMed.
- A. Kudo and Y. Miseki, Heterogeneous photocatalyst materials for water splitting, Chem. Soc. Rev., 2009, 38(1), 253–278 RSC.
- A. Kudo, Development of photocatalyst materials for water splitting, Int. J. Hydrogen Energy, 2006 Feb 1, 31(2), 197–202 Search PubMed.
- A. Primo, A. Corma and H. García, Titania supported gold nanoparticles as photocatalyst, Phys. Chem. Chem. Phys., 2011, 13(3), 886–910 RSC.
- K. M. Lee, C. W. Lai, K. S. Ngai and J. C. Juan, Recent developments of zinc oxide based photocatalyst in water treatment technology: a review, Water Res., 2016 Jan 1, 88, 428–448 Search PubMed.
- W. Choi, A. Termin and M. R. Hoffmann, The role of metal ion dopants in quantum-sized TiO2: correlation between photoreactivity and charge carrier recombination dynamics, J. Phys. Chem., 2002 May 1, 98(51), 13669–13679 Search PubMed.
- L. Cai, J. Gong, J. Liu, H. Zhang, W. Song and L. Ji, Facile preparation of nano-Bi2MoO6/diatomite composite for enhancing photocatalytic performance under visible light irradiation, Materials, 2018 Feb, 11(2), 267 Search PubMed.
- Z. Jia, T. Li, Z. Zheng, J. Zhang, J. Liu, R. Li, Y. Wang, X. Zhang, Y. Wang and C. Fan, The BiOCl/diatomite composites for rapid photocatalytic degradation of ciprofloxacin: Efficiency, toxicity evaluation, mechanisms and pathways, Chem. Eng. J., 2020 Jan 15, 380, 122422 Search PubMed.
- L. Xiao, X. Zhang and G. Yan, Diatomite-Bi2S3 composite photocatalyst: enhanced photocatalytic performance for visible light reduction of Cr (VI), Mater. Res. Express, 2019 Mar 6, 6(6), 065902 Search PubMed.
- P. Zhu, Y. Chen, M. Duan, M. Liu and P. Zou, Structure and properties of Ag3PO4/diatomite photocatalysts for the degradation of organic dyes under visible light irradiation, Powder Technol., 2018 Aug 1, 336, 230–239 Search PubMed.
- H. B. Fan, Q. F. Ren, S. L. Wang, Z. Jin and Y. Ding, Synthesis of the Ag/Ag3PO4/diatomite composites and their enhanced photocatalytic activity driven by visible light, J. Alloys Compd., 2019 Feb 15, 775, 845–852 Search PubMed.
- J. Pang, F. Fu, W. Li, L. Zhu and B. Tang, Fe-Mn binary oxide decorated diatomite for rapid decolorization of methylene blue with H2O2, Appl. Surf. Sci., 2019 Jun 1, 478, 54–61 Search PubMed.
- P. Tanniratt, T. Wasanapiarnpong, C. Mongkolkachit and P. Sujaridworakun, Utilization of industrial wastes for preparation of high performance ZnO/diatomite hybrid photocatalyst, Ceram. Int., 2016 Nov 15, 42(15), 17605–17609 Search PubMed.
- R. D. Soltani, A. Khataee, M. Mashayekhi and M. Safari, Photocatalysis of formaldehyde in the aqueous phase over ZnO/diatomite nanocomposite, Turk. J. Chem., 2016 May 17, 40(3), 402–411 Search PubMed.
- R. D. Soltani and Z. Haghighat, Visible light photocatalysis of a textile dye over ZnO nanostructures covered on natural diatomite, Turk. J. Chem., 2016 May 17, 40(3), 454–466 Search PubMed.
- S. J. Cho, T. An and G. Lim, Three-dimensionally designed anti-reflective silicon surfaces for perfect absorption of light, Chem. Commun., 2014, 50(99), 15710–15713 RSC.
- J. Zhao, Y. Li, G. Yang, K. Jiang, H. Lin, H. Ade, W. Ma and H. Yan, Efficient organic solar cells processed from hydrocarbon solvents, Nat. Energy, 2016 Jan 25, 1(2), 1–7 Search PubMed.
- J. Kong, M. M. Beromi, M. Mariano, T. Goh, F. Antonio, N. Hazari and A. D. Taylor, Colorful polymer solar cells employing an energy transfer dye molecule, Nano Energy, 2017 Aug 1, 38, 36–42 Search PubMed.
- H. A. Atwater and A. Polman, Plasmonics for improved photovoltaic devices, Mater. Sustainable Energy Appl., 2011, 1 Search PubMed.
- R. Betancur, P. Romero-Gomez, A. Martinez-Otero, X. Elias, M. Maymó and J. Martorell, Transparent polymer solar cells employing a layered light-trapping architecture, Nat. Photonics, 2013 Dec, 7(12), 995–1000 Search PubMed.
- Y. Liu, C. Kirsch, A. Gadisa, M. Aryal, S. Mitran, E. T. Samulski and R. Lopez, Effects of nano-patterned versus simple flat active layers in upright organic photovoltaic devices, J. Phys. D: Appl. Phys., 2012 Dec 17, 46(2), 024008 Search PubMed.
- J. F. Bertone, J. Cizeron, R. K. Wahi, J. K. Bosworth and V. L. Colvin, Hydrothermal synthesis of quartz nanocrystals, Nano Lett., 2003 May 14, 3(5), 655–659 Search PubMed.
- X. Jiang, Y. B. Jiang and C. J. Brinker, Hydrothermal synthesis of monodisperse single-crystalline alpha-quartz nanospheres, Chem. Commun., 2011, 47(26), 7524–7526 RSC.
- A. Carretero-Genevrier, M. Gich, L. Picas, J. Gazquez, G. L. Drisko, C. Boissiere, D. Grosso, J. Rodriguez-Carvajal and C. Sanchez, Soft-chemistry–based routes to epitaxial α-quartz thin films with tunable textures, Science, 2013 May 17, 340(6134), 827–831 Search PubMed.
- A. Carretero-Genevrier and M. Gich, Preparation of macroporous epitaxial quartz films on silicon by chemical solution deposition, J. Visualized Exp., 2015,(106), e53543 Search PubMed.
- F. Iwasaki and H. Iwasaki, Historical review of quartz crystal growth, J. Cryst. Growth, 2002 Apr 1, 237, 820–827 Search PubMed.
- A. Laschitsch and D. Johannsmann, High frequency tribological investigations on quartz resonator surfaces, J. Appl. Phys., 1999 Apr 1, 85(7), 3759–3765 Search PubMed.
- Y. Xia and G. M. Whitesides, Soft lithography, Annu. Rev. Mater. Sci., 1998 Aug, 28(1), 153–184 Search PubMed.
- C. Boissiere, D. Grosso, A. Chaumonnot, L. Nicole and C. Sanchez, Aerosol route to functional nanostructured inorganic and hybrid porous materials, Adv. Mater., 2011 Feb 1, 23(5), 599–623 Search PubMed.
- C. Sanchez, C. Boissiere, D. Grosso, C. Laberty and L. Nicole, Design, synthesis, and properties of inorganic and hybrid thin films having periodically organized nanoporosity, Chem. Mater., 2008 Feb 12, 20(3), 682–737 Search PubMed.
- C. J. Brinker and G. W. Scherer, Sol-gel science: the physics and chemistry of sol-gel processing, Academic press, San Diego, 1990.
- D. Grosso, How to exploit the full potential of the dip-coating process to better control film formation, J. Mater. Chem., 2011, 21(43), 17033–17038 RSC.
- X. Jiang, L. Bao, Y. S. Cheng, D. R. Dunphy, X. Li and C. J. Brinker, Aerosol-assisted synthesis of monodisperse single-crystalline α-cristobalite nanospheres, Chem. Commun., 2012, 48(9), 1293–1295 RSC.
- P. Bruhns and R. X. Fischer, Crystallization of cristobalite and tridymite in the presence of vanadium, Eur. J. Mineral., 2000 May 1, 12(3), 615–624 Search PubMed.
- A. M. Venezia, V. La Parola, A. Longo and A. Martorana, Effect of alkali ions on the amorphous to crystalline phase transition of silica, J. Solid State Chem., 2001 Nov 1, 161(2), 373–378 Search PubMed.
- V. G. Pol, A. Gedanken and J. Calderon-Moreno, Deposition of gold nanoparticles on silica spheres: a sonochemical approach, Chem. Mater., 2003 Mar 11, 15(5), 1111–1118 Search PubMed.
- D. C. Altamirano-Juárez, C. Carrera-Figueiras, M. G. Garnica-Romo, M. L. Mendoza-Lopez, M. B. Ortuno-Lopez, M. E. Pérez-Ramos, A. Ramos-Mendoza, C. Rivera-Rodríguez, H. Tototzintle-Huitle, J. J. Valenzuela-Jauregi and M. A. Vidales-Hurtado, Effects of metals on the structure of heat-treated sol-gel SiO2 glasses, J. Phys. Chem. Solids, 2001 Nov 1, 62(11), 1911–1917 Search PubMed.
|
This journal is © The Royal Society of Chemistry 2021 |
Click here to see how this site uses Cookies. View our privacy policy here.