DOI:
10.1039/D1RA08298A
(Paper)
RSC Adv., 2022,
12, 2094-2101
Waste rubber seeds as a renewable energy source: direct biodiesel production using a controlled crushing device†
Received
12th November 2021
, Accepted 4th January 2022
First published on 13th January 2022
Abstract
A multistep and high-cost biodiesel production could be simplified using the direct transesterification (DT) method. A controllable device has been developed and applied to study the effects of the ratio of rubber seeds to methanol, catalyst concentration, reaction time and rotational speed on biodiesel conversion and fatty acid (FA) yield extraction. The controllable crushing device (CCD) assisted the DT of rubber seeds and operated at ambient temperature and pressure achieved a maximum biodiesel conversion of 97.5 ± 0.6% in a reaction time of 7 minutes. The biodiesel quality estimated based on the FA extraction profile is comparable with the biodiesel standard. In terms of energy efficiency and reaction time, the CCD saved 71–98% energy consumption and reduced the reaction time up to 99%.
1. Introduction
The DT method offers a simple procedure for biodiesel production as the oil seed-bearing material is directly in contact with methanol.1,2 The DT process has been predicted to reduce 75–85% of current biodiesel production cost3–5 which therefore could increase the biodiesel competitiveness in the fuel market against petro derived fuels.6 Furthermore this methodology improves the biodiesel yield as lipid loss during the extraction step is avoided.7 The DT processes could be conducted using a catalyst or in a non-catalytic system.3 The supercritical solvent method produces a high yield and purity of biodiesel as no catalyst is involved in the reaction avoiding the neutralization process.8 However intensive energy is required to proceed the DT reaction at high temperature and pressure.9 Among catalytic DT processes, homogeneous catalysts are currently being extensively studied with promising results.3 Despite the disadvantages such as the expensive separation phase particularly for neutralization and washing products, homogeneous substances are cheap, easily accessible and have high catalytic activity.9 For example, a biodiesel conversion of 96% was achieved using NaOH as a catalyst in microwave intensified the DT of microalgal Chlorella biomass in 6 minutes reaction time.10 In contrast 70 minutes reaction time is required when using a heterogeneous substance as the catalyst.11 However a high energy input to maintain the DT reaction in reflux condition is indispensable. Martinez-Guerra et al. (2014) have predicted energy consumption of 26 MJ kg−1 biomass for microwave-intensified the DT of Chlorella sp.10
Some previous studies have shown that the DT method could be accomplished at room temperature. Application of microfluidic thin film devices in the DT of various oleaginous biomass could produce biodiesel at ambient temperature and pressure with the conversion occurring at >90% and interestingly water did not affect the transesterification reaction.12–14 Even though those processes run in a continuous system, up-scaling is a major challenge due to infrastructure constraints. In contrast, a batch-DT production system showed a promising result to apply as the current biodiesel production industry use mechanical agitation.15 A yield of 100% biodiesel conversion from the DT of soy flakes was achieved in 10 hours reaction time using NaOH as a catalyst.16 Furthermore the addition of co-solvent to the DT system increase the homogeneity of methanol and oil rendering a shorter reaction time. The diethoxymethane could intensify the DT of sunflower seeds achieving 98% biodiesel conversion in 13 minutes reaction time.17 In DT, reduction seeds particle size is the prerequisite to increase the contact reaction area and to break the cell walls18 which however decreasing biodiesel yield as some oil detected sticks to the grinder. Therefore, developing a rapid batch-DT process that combines grinding and reaction in situ is necessary to reduce biodiesel production costs.
Furthermore utilization non-edible oil for biodiesel production has gain more interest recently as the production cost is lowered than food-crops sources3,19 and to avoids fuel vs. food debate.20 Rubber seeds, a waste biomass from rubber plantation, have potency for biodiesel sources as contains 40–60% of oils.3,21 Previous published results have confirmed that biodiesel from rubber seeds oil meet the biodiesel standard and could be used as a diesel fuel.21,22
Here, the new device that could simultaneously grind and transesterify the oil is developed. The CCD (Fig. 1) is adopted from the home appliance capsule blender which is equipped with a controllable motor and a blade to crush the seeds. The influence of ratio rubber seeds to methanol (wt/v), catalyst concentration (wt/v%), reaction time (min) and rotational speed (rpm) to biodiesel conversion were systematically investigated in single-factor experiments. The CCD energy requirement was calculated and compared to other DT method and two-steps biodiesel production.
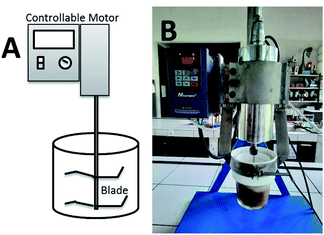 |
| Fig. 1 (A) An illustration diagram and (B) the photographic image of the CCD. | |
2. Experimental
2.1. Materials
The rubber seeds were collected from a local plantation nearby Universitas Sumatera Utara – Medan, Indonesia and used directly after being separated from the shell. Methanol (gradient grade of ≥99.9%), sodium hydroxide anhydrous pellets (reagent grade of ≥98%) and methyl heptadecanoate (C17:0) (analytical standard grade) were purchased from Sigma-Aldrich through local dealer and are used as received.
2.2. Determination of rubber seeds oil content
The Soxhlet extraction method was used to quantify oil content in the rubber seeds. Briefly, 10 grams of crushed rubber seeds were placed in a thimble and extracted using 150 mL of hexane. The extraction was conducted for 30 minutes following previous procedures.23,24 The oil was collected and separated from the solvent using the evaporation method, weighted and stored in a desiccator for lipid content analysis.
2.3. The CCD-assisted DT of waste rubber seeds to biodiesel
The direct biodiesel production from waste rubber seeds was conducted using the CCD equipped with 2 blades to disrupt the seeds and a controllable motor that has a maximum speed of 16
000 rpm. A maximum biodiesel conversion was determined by exploring parameters of ratio rubber seeds to methanol (1
:
1; 1
:
2; 1
:
3; 1
:
4 and 1
:
5, wt/v), catalyst concentration (0.5; 1; 3; 5; and 7 wt/v%), reaction time of 3, 5, 7, 10 and 15 minutes and rotational speed of 3000 to 8000 rpm with increments of 1000 rpm. For each experiment, 20 gram of rubber seeds and a prescribed amount of methanol–NaOH solution was placed in a glass reactor which connected to the CCD. Upon completion of the reaction time, the mixture was poured into a vacuum-filter to separate residual seeds from the liquid mixture followed by evaporating the methanol. A separating funnel was used to separate biodiesel from glycerol. The product was then washed with warm water to remove impurities, dried and stored in a desiccator for gas chromatography analysis.
2.4. Biodiesel confirmation and conversion determination
Confirmation and conversion determination of biodiesel products were established using spectroscopy FT-IR and GC. The PerkinElmer FT-IR 100 was set to observe biodiesel spectra in the range of 4000–400 cm−1 while the GC Shimadzu type 2010 equipped with a capillary column (length 30 m, film thickness 0.25 μm and ID 0.25 mm) and flame ionization detector (temperature of 370 °C) was used to determine biodiesel conversion. A 1 μL of biodiesel sample was injected to injection port with the injection port temperature was set to 260 °C and using helium as the gas carrier with the constant delivered flow of 30 mL min−1. The methyl heptadecanoate is used as an internal standard.
2.5. Estimation biodiesel quality
The quality of biodiesel produced from the CCD-assisted the DT of rubber seeds was determined based on the individual characteristic of FA contained. Using some reliable equations established and reported elsewhere,25–30 the values of some physicochemical properties of biodiesel such as saponification (SV) and iodine value (IV), cetane number (CN), cold (CP) and pour point (PP), density (ρ), kinematic viscosity (ν) and oxidative stability (OS) were predicted. The saponification and iodine values are calculated based on the following equations: |
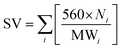 | (1) |
|
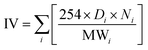 | (2) |
where MW is the molecular weight of each fatty acid ester, N is the percentage of a particular fatty acid ester and D is the number of the double bond of the fatty acid ester. The cetane number can be calculated based on the SV and IV as follow: |
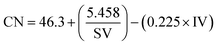 | (3) |
The parameters related to cold flow properties were predicted using eqn (4) and (5) as follows:
|
CP = (0.526 × NC16:0) − 4.992
| (4) |
|
PP = (0.571 × NC16:0) − 12.24
| (5) |
The density (g mL−1) and kinematic viscosity (mm2 s−1) of biodiesel are determined using eqn (6) and (7) as follows:
|
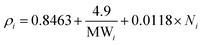 | (6) |
|
ln(νi) = −12.503 + 2.496 ln(MWi) − 0.178Ni
| (7) |
The oxidative stability of biodiesel was calculated based on the weight percentage of C18:2 and C18:3 using eqn (8).
|
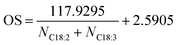 | (8) |
2.6. Statistical analysis
The significant effect of ratio seeds to methanol, catalyst concentration, reaction time and rotational speed on biodiesel conversion and fatty acid (FA) extraction yields (mol%) was determined using Statistica v13.6 software. The one-way ANOVA with the significant level set at α = 0.05 followed by Tukey post hoc analysis was used to assign the reaction condition which drove the significance.
3. Results and discussion
3.1. Oil characterization and catalyst choice
The water content of the rubber seeds assigned by Karl Fischer titration method was 10.2% which is quite high than other study that occurred 1.5%.31 The oil content determined using the Soxhlet method was 42.7% of which 58.6% were polyunsaturated fatty acid, 26% were monounsaturated fatty acid and 15.4% were saturated fatty acid. The fatty acid profile was dominated by linolenic acid with 41%, followed by oleic acid (26%) and linolenic acid (17.5%). These results are similar to other researchers' findings which obtains rubber seeds oil in the range of 40–60%.3,32 The acid value and free fatty acid (FFA) content of the rubber oil were 24.6 mg KOH per g oil and 11.5%, respectively. Due to the high amount of FFA in the rubber seeds, the CCD-assisted DT processes was conducted using sulphuric acid as catalyst in reaction condition of ratio seeds to methanol of 1
:
2 (wt/v), catalyst concentration 3 wt/v%, reaction time 7 minutes and rotational speed of 5000 rpm. Unfortunately, no biodiesel conversion was detected after the reaction was completed. This is due to the low catalytic activity of an acid catalyst which requires prolonged reaction time to complete the reaction.33 In contrast, microwave-intensified the DT of microalgal and fungi biomass using sulphuric acid as a catalyst were resulted a high biodiesel conversion in reaction times of 10 minutes.34–36 However, those results achieved in a high reaction temperature which would like to avoid due to high production cost.4,37 Therefore a homogeneous base substance was tested as a catalyst in the CCD-assisted DT of rubber seeds with the same reaction condition. The biodiesel conversion of 97.5 ± 0.6% was achieved in a short reaction time. Based on that, sodium hydroxide in methanol was used as a catalyst in this study.
3.2. The effect of ratio seeds
:
methanol (wt/v)
Due to different polarity, methanol is a poor solvent for lipids extraction.38 Soxhlet extraction of rubber seeds using methanol as solvent only yielding 7% of oils. This result in agreement with previous study which showed the extraction rate of 9% sunflower oil using methanol compared to 93% using hexane.17 However the rate was increased significantly when a catalyst was introduced to the system achieving biodiesel conversion of 98%.39 In the DT process, methanol acts as extracting and reacting agent which therefore is consumed higher than transesterification reaction.38 Moreover, a high volume of methanol is required to ensure effective agitation and cell walls destruction.3 Therefore in the present study the ratio of seeds to methanol in the range of 1
:
1 to 1
:
5 (wt/v) was investigated for biodiesel production using catalyst concentration of 3 wt/v%, a reaction time of 7 minutes and rotational speed of 5000 rpm.
As stated above, an excess volume of methanol is required to drive the penetration of the methanolic solution into the seeds. In response to that ratio of 1
:
1 (wt/v) showed the lowest biodiesel conversion of 22.9 ± 1.9% (Fig. 2A). The biodiesel conversion of ≥97 occurred for other ratios with the highest (98.5 ± 0.2%) achieved using a ratio of 1
:
3 (wt/v). This achievement is similar to the previous result of in situ transesterification microalgae Nannochloropsis gaditana biomass which observed increasing biomass yield in the increasing methanol to dry algae ratio.40 A one-way ANOVA determined a significant effect of the ratio seeds
:
methanol on biodiesel conversion. Further, Tukey post hoc analysis specify that the significance was driven by low biodiesel conversion at a ratio of 1
:
1 (wt/v).
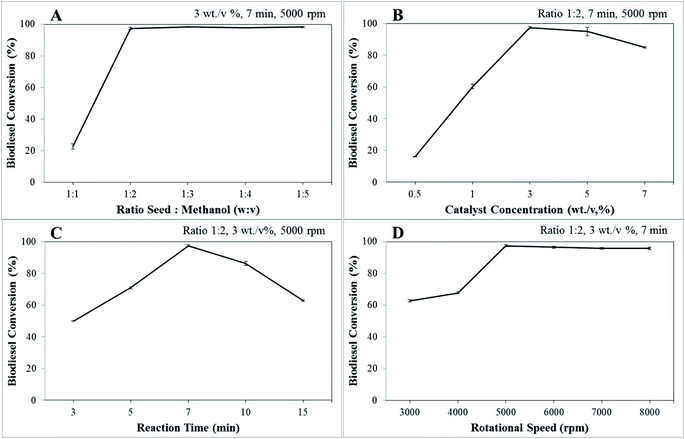 |
| Fig. 2 The effect of (A) ratio seeds : methanol; (B) catalyst concentration; (C) reaction time; and (D) rotational speed on biodiesel conversion of the CCD-assisted DT of rubber seeds. | |
Rubber seeds to methanol ratio had a significant effect on FA extraction yields (Fig. 3A) for all major FA (C16:0; C18:0; C18:1; C18:2 and C18:3) contained, showing average yields of 8.9 ± 0.2; 7.5 ± 0.6; 28.1 ± 1.6; 39.1 ± 1.6 and 15.9 ± 0.9 mol%, respectively. The highest FA extraction yields for C16:0, C18:0 and C18:1 occurred from the ratio of 1
:
4 while for C18:2 and C18:1 obtained from ratios 1
:
2 and 1
:
1, respectively. In addition, except for C18:3, the FA extraction yields derived by the CCD-assisted DT of rubber seeds were exceeded the FA yields from the Soxhlet method.
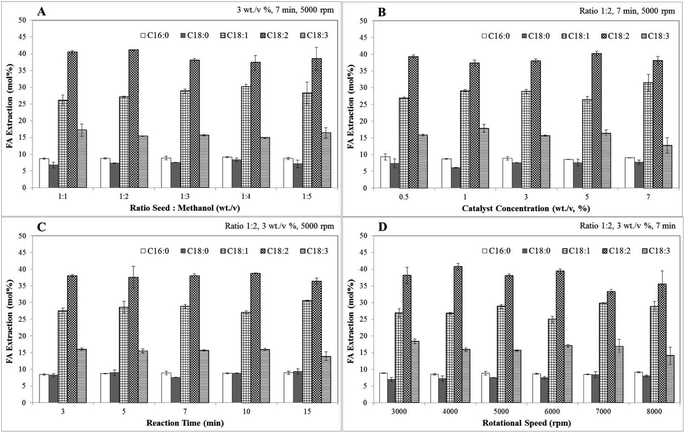 |
| Fig. 3 The effect of (A) ratio seeds : methanol; (B) catalyst concentration; (C) reaction time; and (D) rotational speed on FA extraction yield (mol%) of the CCD-assisted DT of rubber seeds. | |
3.3. The effect of catalyst concentration
Even though the rubber oil contains FFA that exceeds the minimal amount to conduct base-catalyst transesterification, the CCD-assisted DT rubber seeds could run without any saponification detected using low catalyst concentration12,14 and with high biodiesel conversion. As recorded above, the acid catalyst could not catalyse the DT in a short reaction time. The ability of homogeneous base substance to catalyse the reaction in high FFA condition presumably due to synergistic effect generated from the combination of a high shear mixing, rapid disruption seeds cell walls by fast rotation blades and methanolic solution.41 This phenomenon is also recorded in the DT of Chloroparva pannonica and Mucor plumbeus fungal which contains a high FFA. The saponification was detected in high sodium hydroxide concentration for both biomass proved by low biodiesel conversion obtained while no soap was observed when using low concentration.12,14,42,43 It is worth noting that water contained in rubber seeds did not affect the biodiesel conversion even when using a homogeneous base catalyst.12,14,44 Therefore, the effect of sodium hydroxide in methanol in the CCD-assisted DT of rubber seeds was determined at a concentration ranging from 0.5 to 7 wt/v% in reaction condition of ratio seeds
:
methanol of 1
:
2 (wt/v), reaction time of 7 minutes and rotational speed of 5000 rpm.
Biodiesel conversion increased drastically from 16.1 ± 0.1% at catalyst concentration of 0.5 wt/v% to 97.5 ± 0.6% at 3 wt/v% of catalyst (Fig. 2B). After reaching the peak, the biodiesel conversion decreased up to 12% at catalyst concentration 7 wt/v%. The decreasing possibly due to saponification occurring in excess of homogeneous base concentration.14 This result is similar to the published result in the DT of oleaginous yeast biomass which concluded that the high catalyst concentration induce soap formation.43 Other study in vortex fluidic device intensified the DT of Chloroparva pannonica observed the same phenomena.12 Further analysis of variance and Tukey test are used to examine the major contributing factors to the biodiesel conversion. The ANOVA results indicate that catalyst conversion has a significant effect on biodiesel conversion driven by low conversion obtained using a concentration of 0.5 and 1 wt/v%.
Catalyst concentrations have a significant effect on C16:0, C18:0 and C18:1 extraction with the average extraction yields exceeding the FA extraction using the Soxhlet method. Similarly, a significant effect was also observed on C18:2 and C18:3 extraction but the average extraction yields lower than the Soxhlet method. As shown in Fig. 3B, the highest FA extraction yield for C16:0 (9.3 ± 1 mol%) obtained using catalyst concentration of 0.5 wt/v% while for C18:0 and C18:1 extraction were 7.7 ± 0.6 mol% and 31.5 ± 2.5 mol% extracted using concentration of 7 wt/v%. The highest C18:2 and C18:3 extractions of 40.2 ± 0.7 mol% and 17.9 ± 1.1 mol%, respectively, were achieved at sodium hydroxide concentrations of 5 and 1 wt/v%.
3.4. Reaction time
Reaction time is a key criterion in biodiesel production as it directly affects the conversion and the upscale refineries.3,45 Initially, a small amount of conversion yield is achieved due to the penetration of the alcohol into the cell walls of the seeds followed by the dissolution of lipids.39,46 The biodiesel conversion of 50 ± 0.2% occurred at a reaction time of 3 minutes and it increase to reach the peak of 97.5 ± 0.6% at a reaction time of 7 minutes (Fig. 2C). However, after the peak, an extended time reaction does not affect the biodiesel conversion as the equilibrium reaction is reached. In this study, the biodiesel conversion of 62.9 ± 0.5% was achieved after 15 minutes reaction time. This finding is consistent with those of Laskar et al. who showed that the biodiesel yields from waste Mangifera indica were decreased after 4 hours reaction time due to ester hydrolysis rendering soap formation.47 Furthermore, another researcher found that the biodiesel yield decreases after a reaction time longer than 20 min and at 290 °C reaction temperature due to the thermal degradation of the fatty acids, particularly unsaturated fatty acids.40 The results of the reaction time study were analysed by one-way ANOVA. A statistically significant difference was indicated which further Tukey test post hoc revealed that the significance was driven by all the reaction time used.
The average extraction yields of C16:0, C18:0 and C18:1 were 8.8 ± 0.2, 8.6 ± 0.7 and 28.5 ± 1.4 mol%, respectively, which is preeminent than Soxhlet method as shown in Fig. 3C. In contrast, the average yields of C18:2 and C18:3 were lower than the Soxhlet method resulting in FA extraction yield of 37.8 ± 0.9 and 15.4 ± 0.9 mol%, respectively. The statistical analysis of the variance test reveals that there was a significant difference for all the FA. However, the comparison of means by the Tukey post hoc test could not confirm the difference.
3.5. Rotational speed
Mixing intensity plays a key role in the chemical reaction. The vigorous mixing could provide larger surface contact areas between reagents which could increase the reaction rates.48 Previous published results showed no biodiesel conversion was detected in the DT of Spirulina platensis biomass without stirring but the conversion increased significantly as an intense mixing was applied.49 Therefore the rotational speed of the CCD was varied from 3000 to 8000 rpm in increment of 1000 rpm under reaction condition of ratio seeds: methanol of 1
:
2 (wt/v), catalyst concentration of 3 wt/v% and reaction time of 7 minutes. The graph presented in Fig. 2D showed the biodiesel conversion was increased gradually over the rotational speed from 3000 rpm to 5000 rpm. At the rotational speed of 5000 rpm, the biodiesel conversion was achieved the highest conversion of 97.5 ± 0.6% and further, the conversion begins to plateau in the increasing rotational speed. This result is consistent with that for lipid extraction from black soldier fly larvae.2 Similar graph patterns also observed in the homogenizer intensified the biodiesel production from soybean oil.50 The ANOVA results indicated that rotational speed had a significant effect on biodiesel conversion. The Tukey mean comparison test further revealed that biodiesel conversions were significantly different when the CCD was conducted using a rotational speed of 3000 rpm and 4000 rpm.
The highest C18:0 and C18:1 extraction yields of 8.5 ± 0.9 mol% and 29.8 ± 0.3 mol%, respectively, were obtained from the rotational speed of 7000 rpm while C16:0 (9.2 ± 0.2 mol%), C18:2 (40.8 ± 1 mol%) and C18:3 (18.4 ± 0.7 mol%) occurred using rotational speed of 8000, 4000 and 3000 rpm, respectively (Fig. 3D). Furthermore, in comparison, all the major FA extracted was surpassing the FA extraction yields using the Soxhlet method except the average extraction yield of C18:2.
3.6. Predicting biodiesel properties
Some important biodiesel properties such as cetane number, density, viscosity, oxidative stability, pour point and cloud point is mainly affected by the fatty acid composition.52 Those properties that have been internationally regulated such as in ASTM D6751 and EN 14214 could be determined using equations that are very accurate and reliable.30,52,53 The biodiesel properties calculated from fatty acid methyl ester produced from the CCD-assisted DT of rubber seeds is presented in Table 1. As shown in Table 1, most calculated parameters meet the biodiesel international standard except for the oxidation stability which is due to the high concentration of mono and polyunsaturated fatty acid contained in the rubber seeds. This result is supported by the high value of degree unsaturation calculated from the FA profile. In contrast, the cold flow property which is critical for 4 season countries showed a good low-temperature performance. A low saturated FA contained in the sample produces biodiesel with good low-temperature properties.54 Comparison with biodiesel produced from transesterification rubber seeds oil51 showed that the calculated properties are in conformity. Therefore it can be pointed out that biodiesel produced from the CCD-assisted DT of rubber seeds meet the standard and is comparable with the properties resulting from the experiment.
Table 1 Comparison biodiesel properties
Property |
Units |
EN 14214 |
ASTM D6751 |
RSOFAME51 |
Biodiesel (this study) |
Ester content |
% |
>96.5 |
— |
|
97.5 |
Cetane number |
— |
>51 |
>47 |
54 |
Fig. 4 |
Density |
25 °C, kg m−3 |
860–900 |
— |
885 |
877 |
Viscosity |
mm2 s−1, 40 °C |
3.5–5.0 |
1.9–6.0 |
3.89 |
3.99 |
Oxidative stability |
H |
8 |
>3 |
8.54 |
4.6–5.0 |
Pour point |
°C |
Report |
Report |
−2 |
−7.1 |
Cold point |
°C |
Report |
Report |
3.2 |
0.3 |
The combustion behaviour of the fuel is determined by the ignition delay time. Diesel fuel which has a short time gap between injection and ignition is preferable.55 A higher cetane number reflect the shorter ignition delay time. As stated by EN 14214 and ASTM D6751, the minimum cetane number required to meet the standard was 51 and 47, respectively. In the present study the cetane numbers calculated based on the FA extracted yield from the CCD-assisted DT of rubber seeds were presented in Fig. 4. From these figures, it is observed that the average cetane number from all parameters was 58.8 which exceeds the minimum biodiesel standard. Furthermore, the minimum cetane number of 53.5 was achieved from reaction condition of 1
:
2 (wt/v) ratio seed to methanol, catalyst concentration of 7 wt/v%, a reaction time of 7 minutes and rotational speed of 5000 rpm also meet the standard requirement. In addition, in which the highest biodiesel conversion was achieved, the cetane number obtained was 59.6. One-way ANOVA indicated a significant difference between all tested parameters. The significance for parameter ratio seeds to methanol was particularly caused by the difference mean in ratio 1
:
3 (wt/v) and 1
:
4 (wt/v) as detected by Tukey test post hoc analysis. The difference means at a reaction time of 3 and 5 minutes has driven the significance for the parameter of reaction time while the Tukey test could not detect the main effect for the parameter of catalyst concentration and rotational speed.
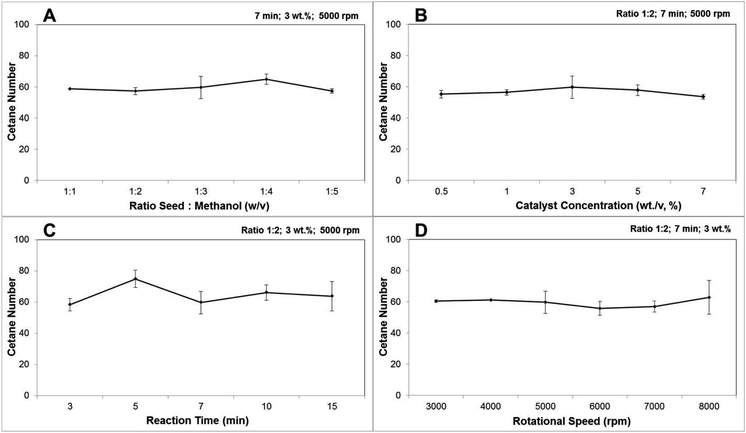 |
| Fig. 4 The effect of (A) ratio seeds : methanol; (B) catalyst concentration; (C) reaction time; and (D) rotational speed on calculated cetane number of the CCD-assisted DT of rubber seeds. | |
3.7. Energy and time consumption
The energy consumption of the reactor to conduct the reaction is important to consider for commercialization.56 Here the electricity demand for the CCD to facilitate the DT of rubber seeds was calculated roughly and compare with two-steps and other DT method (Table 2). The reflux method, which is a conventional transesterification reaction procedure, was used a regular magnetic stirrer hotplate that operates at solvent boiling point. That device consumes 600 watts per hour. The equipment used to conduct the enzymatic reaction was a shaker incubator which requires 900 watts to operate. The total energy required for processing 1 kg of rubber seeds to produce biodiesel at room temperature using the CCD was 9 kW h kg−1 equivalents to 32.4 MJ kg−1. Therefore the energy requirement to produce 1 kg biodiesel is 21.6 kW kg−1. As shown in Table 2 the energy requirement for the CCD-assisted DT of rubber seeds was lower than either two or one-step methods. Compared to the reflux method which requires 120 kW h kg−1, the CCD saves 93% of energy. Moreover, in comparison with two steps methods such as reflux and enzymatic, the energy saved by the CCD was 71% and 98%, respectively. In addition, the CCD is also time-wise as it could save reaction time by 94% compared to other published DT method and it time-save of 95.5% and 99%, respectively, compared to two steps method.
Table 2 Comparison energy (kW h kg−1) and time (min) consumption of biodiesel production from rubber seeds and rubber seeds oil
Method |
Energy consumption (kW h kg−1) |
Reaction time (min) |
References |
Two steps |
– Reflux |
31.5 |
157.5 |
51 |
– Enzymatic |
445.5 |
600 |
57 |
![[thin space (1/6-em)]](https://www.rsc.org/images/entities/char_2009.gif) |
One step |
– Reflux |
120 |
120 |
58 |
– CDT |
9 |
7 |
This study |
4. Conclusions
The CCD is a new method that simultaneously extracts and transesterify the oil from rubber seeds to biodiesel. The maximum biodiesel conversion of 97.5 ± 0.6% was obtained from reaction condition of ratio seeds to methanol of 1
:
2 (wt/v), catalyst concentration of 3 wt/v%, a reaction time of 7 minutes and rotational speed of 5000 rpm. All the parameters studied have a significant effect on biodiesel conversion. Interestingly, neither water nor FFA content affects the conversion. The predicted biodiesel quality based on the FA extracted content meet the international biodiesel standard. Compared to other published two- and one-step biodiesel production from rubber seeds, the CCD is both energy- and time-efficient. The CCD could save 71–98% energy consumption and reduces the reaction time of 94–99%.
Conflicts of interest
There are no conflicts to declare.
Acknowledgements
This research was supported by the Universitas Sumatera Utara through research grant project number: 404/UN5.2.3.1/PPM/SPP-TALENTA USU/2021.
References
- B. Kim, H. Y. Heo, J. Son, J. Yang, Y.-K. Chang, J. H. Lee and J. W. Lee, Algal Res., 2019, 41, 101557 CrossRef.
- W. Feng, H. Xiong, W. Wang, X. Duan, T. Yang, C. Wu, F. Yang, T. Wang and C. Wang, Renewable Energy, 2020, 147, 584–593 CrossRef CAS.
- E. K. Sitepu, K. Heimann, C. L. Raston and W. Zhang, Renewable Sustainable Energy Rev., 2020, 123, 109762 CrossRef CAS.
- F. Harahap, S. Silveira and D. Khatiwada, Energy, 2019, 170, 62–72 CrossRef CAS.
- M. J. Haas, A. J. McAloon, W. C. Yee and T. A. Foglia, Bioresour. Technol., 2006, 97, 671–678 CrossRef CAS PubMed.
- R. Sivaramakrishnan and A. Incharoensakdi, Fuel, 2017, 191, 363–370 CrossRef CAS.
- P. D. Patil, H. Reddy, T. Muppaneni, A. Mannarswamy, T. Schuab, F. O. Holguin, P. Lammers, N. Nirmalakhandan, P. Cooke and S. Deng, Green Chem., 2012, 14, 809–818 RSC.
- P. Andreo-Martínez, V. M. Ortiz-Martínez, N. García-Martínez, A. P. de los Ríos, F. J. Hernández-Fernández and J. Quesada-Medina, Appl. Energy, 2020, 264, 114753 CrossRef.
- K. Y. Wong, J.-H. Ng, C. T. Chong, S. S. Lam and W. T. Chong, Renewable Sustainable Energy Rev., 2019, 116, 109399 CrossRef CAS.
- E. Martinez-Guerra, V. G. Gude, A. Mondala, W. Holmes and R. Hernandez, Appl. Energy, 2014, 129, 354–363 CrossRef CAS.
- T. Dong, J. Wang, C. Miao, Y. Zheng and S. Chen, Bioresour. Technol., 2013, 136, 8–15 CrossRef CAS PubMed.
- E. K. Sitepu, K. Corbin, X. Luo, S. J. Pye, Y. Tang, S. C. Leterme, K. Heimann, C. L. Raston and W. Zhang, Bioresour. Technol., 2018, 266, 488–497 CrossRef CAS PubMed.
- E. K. Sitepu, D. B. Jones, Y. Tang, S. C. Leterme, K. Heimann, W. Zhang and C. L. Raston, Chem. Commun., 2018, 54, 12085–12088 RSC.
- E. K. Sitepu, D. B. Jones, Z. Zhang, Y. Tang, S. C. Leterme, K. Heimann, C. L. Raston and W. Zhang, Bioresour. Technol., 2019, 273, 431–438 CrossRef CAS PubMed.
- F. Visscher, J. van der Schaaf, T. A. Nijhuis and J. C. Schouten, Chem. Eng. Res. Des., 2013, 91, 1923–1940 CrossRef CAS.
- M. Haas and K. Scott, J. Am. Oil Chem. Soc., 2007, 84, 197–204 CrossRef CAS.
- J. Zeng, X. Wang, B. Zhao, J. Sun and Y. Wang, Ind. Eng. Chem. Res., 2009, 48, 850–856 CrossRef CAS.
- V. Skorupskaite, V. Makareviciene and M. Gumbyte, Fuel Process. Technol., 2016, 150, 78–87 CrossRef CAS.
- H. N. T. Le, K. Imamura, N. Watanabe, M. Furuta, N. Takenaka, L. V. Boi and Y. Maeda, Chem. Eng. Technol., 2018, 41, 1013–1018 CrossRef CAS.
- R. Dominguez-Faus, S. E. Powers, J. G. Burken and P. J. Alvarez, Environ. Sci. Technol., 2009, 43, 3005–3010 CrossRef CAS PubMed.
- W. Roschat, T. Siritanon, B. Yoosuk, T. Sudyoadsuk and V. Promarak, Renewable Energy, 2017, 101, 937–944 CrossRef CAS.
- I. Khalil, A. R. A. Aziz, S. Yusup, M. Heikal and M. El-Adawy, Biomass Convers. Biorefin., 2017, 7, 37–49 CrossRef CAS.
- Z. Al-Hamamre, S. Foerster, F. Hartmann, M. Kröger and M. Kaltschmitt, Fuel, 2012, 96, 70–76 CrossRef CAS.
- J. B. Tarigan, M. Ginting, S. N. Mubarokah, F. Sebayang, J. Karo-karo, T. T. Nguyen, J. Ginting and E. K. Sitepu, RSC Adv., 2019, 9, 35109–35116 RSC.
- K. Krisnangkura, J. Am. Oil Chem. Soc., 1986, 63, 552–553 CrossRef CAS.
- L. F. Ramírez-Verduzco, J. E. Rodríguez-Rodríguez and A. d. R. Jaramillo-Jacob, Fuel, 2012, 91, 102–111 CrossRef.
- J.-Y. Park, D.-K. Kim, J.-P. Lee, S.-C. Park, Y.-J. Kim and J.-S. Lee, Bioresour. Technol., 2008, 99, 1196–1203 CrossRef CAS PubMed.
- M. Islam, M. Magnusson, R. Brown, G. Ayoko, M. Nabi and K. Heimann, Energies, 2013, 6, 5676 CrossRef.
- M. A. Islam, G. A. Ayoko, R. Brown, D. Stuart and K. Heimann, Procedia Eng., 2013, 56, 591–596 CrossRef CAS.
- M. A. Islam, R. J. Brown, P. R. Brooks, M. I. Jahirul, H. Bockhorn and K. Heimann, Energy Convers. Manage., 2015, 98, 340–347 CrossRef CAS.
- B. A. Abdulkadir, Y. Uemura, A. Ramli, N. B. Osman, K. Kusakabe and T. Kai, J. Jpn. Inst. Energy, 2015, 94, 763–768 CrossRef.
- M. Takase, T. Zhao, M. Zhang, Y. Chen, H. Liu, L. Yang and X. Wu, Renewable Sustainable Energy Rev., 2015, 43, 495–520 CrossRef CAS.
- G. Guan, K. Kusakabe, N. Sakurai and K. Moriyama, Fuel, 2009, 88, 81–86 CrossRef CAS.
- B. D. Wahlen, R. M. Willis and L. C. Seefeldt, Bioresour. Technol., 2011, 102, 2724–2730 CrossRef CAS PubMed.
- J. Cheng, T. Yu, T. Li, J. Zhou and K. Cen, Bioresour. Technol., 2013, 131, 531–535 CrossRef CAS PubMed.
- J. Ling, S. Nip, R. A. de Toledo, Y. Tian and H. Shim, Energy, 2016, 108, 185–194 CrossRef CAS.
- Y. C. Sharma, B. Singh and S. Agrawal, Biomass Convers. Biorefin., 2012, 2, 63–71 CrossRef CAS.
- R. Zakaria and A. P. Harvey, Fuel Process. Technol., 2012, 102, 53–60 CrossRef CAS.
- J. Qian, F. Wang, S. Liu and Z. Yun, Bioresour. Technol., 2008, 99, 9009–9012 CrossRef CAS PubMed.
- S. Jazzar, P. Olivares-Carrillo, A. Pérez de los Ríos, M. N. Marzouki, F. G. Acién-Fernández, J. M. Fernández-Sevilla, E. Molina-Grima, I. Smaali and J. Quesada-Medina, Appl. Energy, 2015, 148, 210–219 CrossRef CAS.
- M. Kwak, D. Kim, S. Kim, H. Lee and Y. K. Chang, Renewable Energy, 2020, 149, 1395–1405 CrossRef CAS.
- S. B. Velasquez-Orta, J. G. M. Lee and A. Harvey, Fuel, 2012, 94, 544–550 CrossRef CAS.
- P. Thliveros, E. Uçkun Kiran and C. Webb, Bioresour. Technol., 2014, 157, 181–187 CrossRef CAS PubMed.
- C.-L. Chen, C.-C. Huang, K.-C. Ho, P.-X. Hsiao, M.-S. Wu and J.-S. Chang, Bioresour. Technol., 2015, 194, 179–186 CrossRef CAS PubMed.
- B. Freedman, E. H. Pryde and T. L. Mounts, J. Am. Oil Chem. Soc., 1984, 61, 1638–1643 CrossRef CAS.
- D. Y. C. Leung, X. Wu and M. K. H. Leung, Appl. Energy, 2010, 87, 1083–1095 CrossRef CAS.
- I. B. Laskar, R. Gupta, S. Chatterjee, C. Vanlalveni and L. Rokhum, Renewable Energy, 2020, 161, 207–220 CrossRef CAS.
- M. Sánchez-Cantú, M. Morales Téllez, L. M. Pérez-Díaz, R. Zeferino-Díaz, J. C. Hilario-Martínez and J. Sandoval-Ramírez, Renewable Energy, 2019, 130, 174–181 CrossRef.
- H. I. El-Shimi, N. K. Attia, S. T. El-Sheltawy and G. I. El-Diwani, J. Sustainable Bioenergy Syst., 2013, 3, 224–233 CrossRef CAS.
- S. Joshi, P. R. Gogate, P. F. Moreira and R. Giudici, Ultrason. Sonochem., 2017, 39, 645–653 CrossRef CAS PubMed.
- J. Ahmad, S. Yusup, A. Bokhari and R. N. M. Kamil, Energy Convers. Manage., 2014, 78, 266–275 CrossRef CAS.
- M. J. Ramos, C. M. Fernández, A. Casas, L. Rodríguez and Á. Pérez, Bioresour. Technol., 2009, 100, 261–268 CrossRef CAS PubMed.
- R. K. Bharti, R. Katiyar, D. W. Dhar, R. Prasanna and R. Tyagi, Biofuels, 2019, 1–10, DOI:10.1080/17597269.2019.1594592.
- S. K. Hoekman, A. Broch, C. Robbins, E. Ceniceros and M. Natarajan, Renewable Sustainable Energy Rev., 2012, 16, 143–169 CrossRef CAS.
- B. Sajjadi, A. A. A. Raman and H. Arandiyan, Renewable Sustainable Energy Rev., 2016, 63, 62–92 CrossRef CAS.
- M. L. N. M. Carneiro, F. Pradelle, S. L. Braga, M. S. P. Gomes, A. R. F. A. Martins, F. Turkovics and R. N. C. Pradelle, Renewable Sustainable Energy Rev., 2017, 73, 632–653 CrossRef CAS.
- A. Arumugam, D. Thulasidharan and G. B. Jegadeesan, Renewable Energy, 2018, 116, 755–761 CrossRef CAS.
- Widayat, A. D. K. Wibowo and Hadiyanto, Energy Procedia, 2013, 32, 64–73 CrossRef CAS.
Footnote |
† Electronic supplementary information (ESI) available. See DOI: 10.1039/d1ra08298a |
|
This journal is © The Royal Society of Chemistry 2022 |
Click here to see how this site uses Cookies. View our privacy policy here.