DOI:
10.1039/D1RA09196D
(Review Article)
RSC Adv., 2022,
12, 4891-4912
Chemocatalytic value addition of glucose without carbon–carbon bond cleavage/formation reactions: an overview
Received
20th December 2021
, Accepted 2nd February 2022
First published on 9th February 2022
Abstract
As the monomeric unit of the abundant biopolymer cellulose, glucose is considered a sustainable feedstock for producing carbon-based transportation fuels, chemicals, and polymers. The chemocatalytic value addition of glucose can be broadly classified into those involving C–C bond cleavage/formation reactions and those without. The C6 products obtained from glucose are particularly satisfying because their syntheses enjoy a 100% carbon economy. Although multiple derivatives of glucose retaining all six carbon atoms in their moiety are well-documented, they are somewhat dispersed in the literature and never delineated coherently from the perspective of their carbon skeleton. The glucose-derived chemical intermediates discussed in this review include polyols like sorbitol and sorbitan, diols like isosorbide, furanic compounds like 5-(hydroxymethyl)furfural, and carboxylic acids like gluconic acid. Recent advances in producing the intermediates mentioned above from glucose following chemocatalytic routes have been elaborated, and their derivative chemistry highlighted. This review aims to comprehensively understand the prospects and challenges associated with the catalytic synthesis of C6 molecules from glucose.
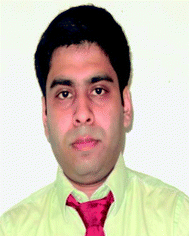 Saikat Dutta | Saikat Dutta received his PhD degree from the Department of Chemistry, University of Iowa, Iowa City, USA, in 2010. He then worked as a post-doctoral researcher at the University of California Davis, USA, till 2014. He is presently working as an assistant professor in the Department of Chemistry, National Institute of Technology Karnataka (NITK), Surathkal, India, since 2015. His research interests include synthetic organic chemistry, green chemistry, and catalysis. |
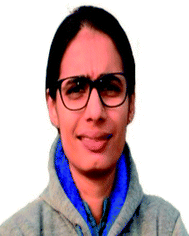 Navya Subray Bhat | Navya Subray Bhat received her Masters' degree in chemistry from Karnatak University, Dharwad, India, in 2017. She is currently pursuing her doctoral degree under the supervision of Dr Saikat Dutta. Her research interests include the chemistry of renewables, catalysis, and materials science. |
1. Introduction
As a renewable feedstock to produce carbon-based transportation fuels, chemicals, and polymers, cellulosic biomasses fit seamlessly in many futuristic depictions of a biobased economy.1 The primary motivation behind an integrated biorefinery is to access renewable chemicals by adopting environmentally acceptable processes without compromising their affordability and performance.2 Interestingly, biomass was the primary source of energy and fuels until the widespread adoption of petroleum in the second half of the 19th century.3 The primary challenges for biomass value addition in a biorefinery setup include identifying commercially tenable biomass feedstocks and developing proficient technologies for their synthetic upgrading with minimal stress on the environment.4 In this regard, cellulose is the single most abundant biopolymer available in nature, and only a small fraction of the nearly 150 billion tons of cellulose produced annually worldwide is utilized.5 Cellulose, typically found in terrestrial lignocellulose, algal biomass, and various end-user waste products, is a linear polymer made of glucose units stitched together by the β-1,4-glycosidic linkage.6 The extensive hydrogen-bonding network between the neighboring chains of cellulose fiber is responsible for its high crystallinity and chemical recalcitrance.7 Nevertheless, cellulose can be depolymerized into glucose by the saccharification process following chemocatalytic or enzymatic pathways.8,9 Glucose is present as sucrose in fruits and starch in various food grains, but these sources are more costly starting materials than cellulose. Besides, diverting sucrose or starch in producing fuels and chemicals could be disastrous for food security in many parts of the world.10 Therefore, from both economic and environmental perspectives, glucose derived from cellulosic biomasses is preferred for synthesizing biofuels and biochemicals. Over the past several years, there have been significant research breakthroughs in the selective, high-yielding synthesis of small molecules and polymers from glucose/cellulose with specific sets of functionalities and properties.11 The reagents and catalysts required for the chemical transformations are often selected by revering the green chemistry principles and commercial feasibilities, such as non-toxicity and bulk availability.12
The starting materials used in the petrorefineries and biorefineries are disparate at the molecular level.13 Molecules with specific structural and functional characteristics (e.g., monomers, pharmaceuticals) are produced by introducing heteroatoms (e.g., oxygen-containing functionalities) selectively in the petroleum-derived hydrocarbons.14 On the contrary, excessive oxygen-containing functionalities in the biomass-derived feedstocks (e.g., glucose) are selectively eliminated/tailored to produce molecules with desired structural traits.15 The primary task in a biorefinery is identifying efficient reagents and catalysts to effect selective chemical transformations. Enzymatic catalysis can produce many of these derivatives in high selectivity under ambient conditions.16 However, the process is slow (ca. days) and often requires genetically altered live organisms, expensive enzymes, and nutrients. The biocatalysts typically have a low turnover number (TON), less tolerance to feedstock flexibility, lengthy process development time, and must comply with strict regulatory requirements.17 In contrast, the chemical catalysts can be developed by a high throughput screening process, have a high TON and faster kinetics, adjust to feedstock modifications, possess a better understood structure–activity correlation, and be integrated into existing petrorefinery infrastructure.18 Primary challenges before the chemocatalytic processes are to compete with high selectivity of the enzymatic processes, perform under energy-efficient conditions, and efficient recycling of the precious catalysts.19 Many of the existing catalysts used in the petrorefinery have been repurposed, and a new library of robust, selective, inexpensive, and eco-friendly catalysts have been developed for biorefinery operations.20 Noble metals and non-noble metal-based heterogeneous solids, ionic liquids, ion-exchange resins, metal–organic frameworks, zeolites, and polyoxometalates are frequently used catalysts in biorefinery operations.21 Nanocatalysts and single-atom catalysts (SACs) are also increasingly being administered in the chemical-catalytic value addition of biomass due to their high activity and selectivity compared to traditional heterogeneous catalysts.22 The preparation of many high-value chemicals from glucose/cellulose involves C–C bond breaking/forming reactions.23–26 Selective catalysts and precise reaction conditions are being developed for C–C breaking or formation reactions forming high-value chemicals from glucose. However, from the atom economy and carbon economy perspective, preserving all the carbon atoms of glucose in the product is warranted. The processes avoid waste formation, do not release carbon into the environment, and produce C6 molecules containing diverse carbon skeletal systems. Therefore, the present review focuses on preparing value-added products sourced from cellulose and glucose with a 100% carbon economy.27,28 This work will help the readers to comprehend recent developments in this field, appreciate the prospects, identify the challenges, and prescribe improvements.
2. Direct value addition of glucose/cellulose
Cellulose remains one of the most widely used natural fibers throughout human history and is extensively used in the textile, paper, animal feed, cosmetic, and pharmaceutical industries.29 Various high-value derivatives of cellulose have been prepared by keeping its polymeric core structure and the carbon skeleton unperturbed. The direct applications of glucose and cellulose without significantly altering their core structure include human and animal feed, wood and paper, fibers and clothes, cosmetics, packaging, and an excipient in the pharmaceutical industries.30,31 The crystallinity of native cellulose is moderated by disrupting the hydrogen bonds formed between the secondary and primary hydroxyl groups of the glucose units between the polymeric chains. Ethyl cellulose, cellulose acetate, and hydroxypropyl cellulose are prepared by converting some of the free hydroxyl groups in cellulose into ethyl ether, acetate group, and 2-hydroxypropyl group, respectively.32–34 Other important derivatives of cellulose include cellulose nitrate and cellulose sulfate. Cellulose nitrate (mono-, di-, and tri-nitro esters of cellulose produced by reacting cellulose with HNO3) has a long history of being used as explosive and lacquer.35 Cellulose sulfate, a water-soluble derivative of cellulose, is prepared by treating cellulose with conc. H2SO4 at low temperature (ca. −10 °C) in an alcoholic (e.g., ethanol) medium.36 Cellulose fiber is used as reinforcement for natural and synthetic polymer matrices due to its low density, non-toxicity, and good mechanical properties.37 The cellulose derivatives such as cellulose acetate have also been applied as filler or polymer matrix for various composite materials.38 Nanocellulose in the form of cellulose nanocrystals and cellulose nanofibers has excellent mechanical properties and is used as a reinforcing material across multiple polymer nanocomposites.39 Nanocellulose is sourced from plant biomass and bacteria using mechanical, chemical, or enzymatic treatments. The properties of nanocellulose depend on the biomass source, isolation technique, and surface modifications. Nanocellulose surface can be modified by charged or hydrophobic moieties (e.g., esterification, sulfonation). Nanocellulose is known for its excellent mechanical strength, biocompatibility, tuneable self-assembly, thixotropic, and photonic properties, making it an attractive candidate in nanomaterials and nanocomposites.40 The applications of nanocellulose include packaging, reinforced polymer composites, biosensors, catalysis, and optoelectronics. A limited study has been done on the hydrolysis of nanocellulose into glucose using enzymatic hydrolysis.41 In this work, cellulase from Trichoderma sp. afforded a 47% glucose yield starting from cellulose nanoplatelets (37 °C, 60 h), whereas microcrystalline cellulose provided only a 22% glucose yield. The TiO2-coupled nanocellulose catalyzed the hydrolysis of sugarcane bagasse into glucose.42
Glucose is commercially used as a sweetener, thickener, and moisture-retainer in various canned and baked food products.43 The glucose to fructose isomerization can be catalyzed by a Lewis acid or a Brønsted base.44,45 Fructose syrup is used in several foods and beverages because of its relatively low cost and high sweetness (more than twice that of glucose).46
In this section, the compounds directly obtained by the catalytic conversion of glucose are elaborated. For example, the selective hydrogenation of the aldehyde group in glucose forms D-sorbitol (Scheme 1). D-Sorbitol has major applications as a low-calorie sweetener, humectant in cosmetics, additive in various pharmaceutical formulations, and chemical feedstock for value-added chemicals by synthetic upgrading.47 The aldehyde group in glucose can be selectively oxidized to carboxylic acid by a chemical-catalytic process forming gluconic acid (GCA), which has applications in cleaning products, paints, dyes, metal finishing, textile, and water purification.48,49 The dicarboxylic acid formed by oxidizing the terminal carbon atoms of glucose molecule is called glucaric acid (GRA). GRA has applications as a corrosion inhibitor, a component in cleaning products, and an important chemical intermediate for synthesizing adipic acid (AA).50,51 The hydrogenation of glucose to sorbitol followed by the acid-catalyzed double dehydration of the latter forms 1,4:3,6-dianhydro-D-sorbitol or isosorbide (IS).52 The derivatives of IS have found applications as green solvents, plasticizers, surfactants, and a monomer for several classes of biorenewable polymers (discussed in detail in the next section).53,54 The sequential elimination of three water molecules from a glucose molecule under acid catalysis forms 5-(hydroxymethyl)furfural (HMF).55 2-Hydroxyacetyl furan, another C6 furanic compound, is often coproduced in smaller quantities under acid catalysis.56 HMF is one of the most recognized biomass-derived chemical intermediates with huge commercial potential for synthesizing fuels, chemicals, and materials.57 More extensive reduction of glucose forms 1,2,6-hexanetriol (HTO), a potential alternative for glycerol in making polymers.58 Extensive hydrodeoxygenation (HDO) of glucose-derived sorbitol leads to n-hexane.59 Partial HDO of sorbitol to 1,6-hexanediol (HD) followed by oxidation of the latter forms AA.60,61 Many of the products in Scheme 1 are potential monomers for polymeric applications. Other important derivatives of glucose include alkyl glucosides and alkyl glucosamides, formed by condensing glucose or GCA with fatty alcohols and amines, with applications as nonionic surfactants in detergents and personal care products.62,63
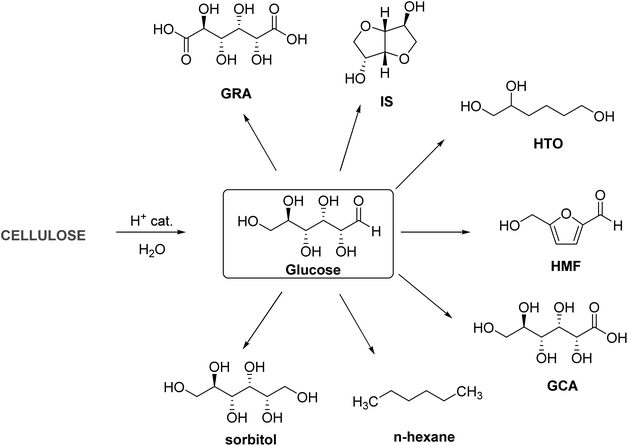 |
| Scheme 1 Direct transformation of glucose into various high-value chemicals and materials. | |
In this regard, two types of polymers are targeted from biomass resources like glucose or cellulose. In the first kind, the existing commercial polymers are prepared using biomass as the renewable resources for the monomer components, making the process greener and more sustainable.64 In the second kind, novel polymers are produced with a higher degree of control on their properties and biodegradability.65 In this review, only those polymers are highlighted that comprise C6 monomers originating from glucose. Selective HDO of the secondary –OH groups in glucose under catalytic hydrogenation conditions forms HD. Alternatively, the ring-opening hydrogenation of 2,5-bis(hydroxymethyl)tetrahydrofuran (BHMTHF) (discussed in Section 4) can lead to HD.66,67 HD is a potential diol-based renewable monomer for various polymers like polycarbonate and polyester.68,69 HD can be diaminated to form hexamethylenediamine (HMDA), a key monomer for polyamides, polyurethanes, and epoxy resins, reacting with ammonia in the presence of a suitable heterogeneous catalyst.70 Glucose can be oxidized to GRA, which on selective HDO forms AA.50 Alternative routes for synthesizing AA from glucose include the oxidation of HD and reductive conversion of FDCA.71–73 Therefore, both AA and HMDA, the monomers of the high-volume commercial polymer nylon-66 can be renewably sourced from glucose.
Several high-performance polymers have been synthesized from glucose using C6 monomers. For example, a novel polymer was prepared using IS as a diol and FDCA as a diacid monomer (Scheme 2). The resulting rigid polyester showed excellent mechanical strength, high glass transition temperature, and superior gas barrier properties.74
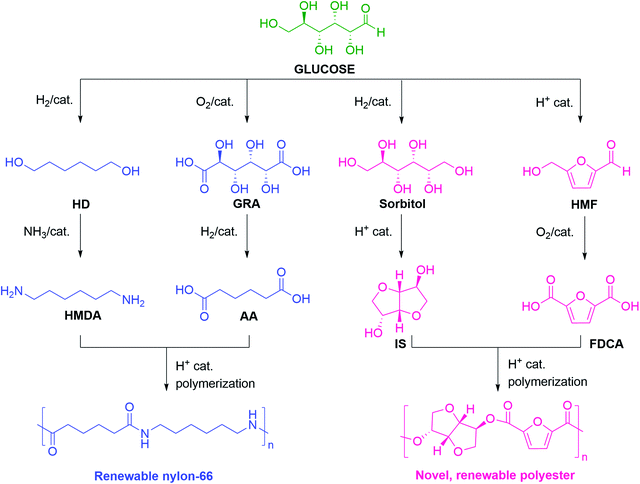 |
| Scheme 2 Renewable syntheses of commercial and novel polymers from glucose-derived C6 monomers. | |
Several metal-based heterogeneous catalysts have been developed for the selective hydrogenation of glucose into sorbitol in an aqueous medium under operationally simple and environmentally acceptable conditions. Both noble metal-based and earth-abundant transition metal-based catalysts have been explored for the above transformation (Table 1). Both commercial catalysts and lab-made catalysts have been studied and shown promising results. The challenge in this area is to produce sorbitol in good scalability and isolated yield starting from untreated or minimally-treated cellulosic biomass.
Table 1 Literature on producing sorbitol from glucose/cellulose by catalytic hydrogenation (published during 2016–2021)a
S/N |
Feedstock |
Catalyst |
Reaction conditions |
Yield (%) |
Ref. |
Abbreviations: BM, Ball-milled; 5RuNb2O5_C, 5 wt% Ru/Nb2O5 in crystalline phase; L2, bis(diphenylphosphinomethyl)aminoalkyl ligand; LHT-OX, oxidized carbon nanofiber; HT, hydrotalcite; PBC, phosphoric acid-containing porous biochar (from bamboo power); ZP-A, phosphated zirconia-alumina; MC, mesoporous carbon; CB, carbon black; SP, sodium propionate; NDC, nitrogen-doped carbon; HPS-N: hypercrosslinked polystyrene modified with ammonia; Ni–P-m, Ni–P/mSiO2–NH2&CH3 in a NaOH solution; SA, pristine commercial mesoporous activated carbon; AMSA, amino poly(styrene-co-maleic)polymer; CCD, carbonized cassava dreg; AG-CNT, activated carbon nanotube; Ru-TSu, Ru supported on carbon T treated with H2SO4; AC-B, activated carbon reduced by NaBH4; C-HT, calcined hydrotalcite; PW, phosphotungstic acid; Cs3HSiW12O40, Cs exchanged silicotungstic acid; AFPS, amino functionalized nanoporous polymer; *selectivity; #conversion. |
1 |
Glucose |
5RuNb2O5_C (10 wt%) |
100 °C, 4 h, 6 MPa H2, water |
83.30 |
75 |
2 |
Glucose |
Fe3O4@SiO2@L2-Ru(II) (55.5 wt%) |
150 °C, 1 h, 2-propanol, water, K2CO3 (0.1 mmol), MW |
96.31 |
76 |
3 |
Glucose |
FeNi/CB (12 wt%) |
140 °C, 2 h, 3 MPa H2, water |
25.46 |
77 |
4 |
Glucose |
Nano-Ni2P-HT (3 mol%) |
80 °C, 24 h, 4 MPa H2, water |
>99 |
78 |
5 |
Glucose |
Pt(2)Sn(0.25)/γ-Al2O3 (50 wt%) |
80 °C, 6 h, 1.6 MPa H2, C-HT (0.75 g), water |
76 |
79 |
6 |
Cellulose |
3%Ru-PW/ZrO2-550 (100 wt%) |
180 °C, 7 h, 7 MPa H2, water |
66 |
80 |
7 |
Glucose |
Ru/LHT-OX |
120 °C, 2 h, 3 MPa H2, water |
62 |
81 |
8 |
Microcrystalline cellulose |
Ni/ZrP2 (100 wt%) |
200 °C, 5 h, 5 MPa H2, water |
60.8 |
82 |
9 |
H3PO4 pretreated cellulose |
Ru/PBC (33.33 wt%) |
150 °C, 8 h, 5 MPa H2, water |
87.1 |
83 |
10 |
Glucose |
Ru/ZP-A (27.7 wt%) |
90 °C, 7 h, 1.25 MPa H2, water |
85.36 |
84 |
11 |
Cellulose |
Ru/Cs3HSiW12O40 (100 wt%) |
180 °C, 3 h, 5 MPa H2, water |
58 |
85 |
12 |
Mixed milled cellulose |
ZrP (180 wt%) and Ru/MC (12 wt%) |
190 °C, 1.5 h, 5 MPa H2, water |
66.4 |
86 |
13 |
Glucose |
Ru–ZrO2-SBA-15 (0.5 mol%) |
150 °C, 6 h, 4 MPa H2, water |
85 |
87 |
14 |
Glucose |
Pt/CB_SP0.5 (40 wt%) |
140 °C, 5 h, 4.5 MPa H2, water |
89 |
88 |
15 |
Glucose |
HPS-N-Ni-25% |
160 °C, 4 MPa H2, water |
98* |
89 |
16 |
Glucose |
35Ni/NDC |
125 °C, 2.5 MPa H2, water, continuous stream (40 h) |
84 |
90 |
17 |
Glucose |
Ni–P-m (10 wt%) |
100 °C, 4 h, 4 MPa H2, water |
97 |
91 |
18 |
BM cellulose |
Ru/SA (25 wt%) |
190 °C, 3 h, 5 MPa H2, water |
48 |
92 |
19 |
Cellulose |
ZrP (180 wt%) and Ru@MC (12 wt%) |
170 °C, 1.5 h, 5 MPa H2, water |
72.4 |
93 |
20 |
Glucose |
5%Ru/γ-Al2O3@ASMA (20 wt%) |
120 °C, 2 h, 5 MPa H2, water |
90 |
94 |
21 |
BM cellulose |
Ru/CCD-SO3H (80 wt%) |
180 °C, 10 h, 4 MPa H2, water |
63.8 |
95 |
Glucose |
180 °C, 1 h, 4 MPa H2, water |
85.5 |
22 |
Glucose |
(RuO2)0.038(SiO2)0.962 (250 wt%) |
120 °C, 6 h, 2 MPa H2, water |
35# |
96 |
23 |
BM cellulose |
Ru/AG-CNT1200 (40 wt%) |
205 °C, 5 h, 5 MPa H2, water |
64 |
97 |
24 |
Glucose |
5% Ni/Al2O3-70 °C-0.17 (33.3 wt%) |
130 °C, 4 h, 3 MPa H2, hydrazine/water |
52# |
98 |
25 |
Glucose |
RANEY® Ni (100 wt%) |
150 °C, 6 h, ethanol, water |
57 |
99 |
26 |
Cellobitol |
Ni–Pt/CNT |
200 °C, 3 h, 4 MPa H2, water |
65.4 |
100 |
27 |
Glucose |
Ni/NiO (4.1 wt%) |
130 °C, 5 MPa H2, water |
84 |
101 |
28 |
Glucose |
NiCo/HZSM-5 (55.5 wt%) |
120 °C, 5 h, 5 MPa H2, water |
98 |
102 |
Cellobiose |
NiCo/HZSM-5 (58 wt%) |
180 °C, 5 h, 5 MPa H2, water |
86 |
29 |
BM cellulose |
(RuAC)mix (40 wt%) |
205 °C, 6 h, 5 MPa H2, water |
46 |
103 |
30 |
BM cellulose |
Nafion NR50 (40 wt%) and Ru/AC (100 wt%) |
150 °C, 1 h, 5 MPa H2, water, [Amim]Cl (1 g) |
34.3 |
104 |
31 |
Glucose |
Ru/CCD (1 wt%) |
120 °C, 1.5 h, 3 MPa H2, water |
98.6 |
105 |
32 |
Glucose |
Ni powder (4 wt%) and TiO2 pillared bentonite (40 wt%) |
Irradiation with UV sunlight, 30 days |
66.8 |
106 |
33 |
Glucose |
Ru-TSu (25 wt%) |
190 °C, 3 h, 5 MPa H2, water |
32.7 |
107 |
34 |
Glucose |
5%Pt/AC-B (42 wt%) |
180 °C, 3 h, 2 MPa H2, water |
92 |
108 |
35 |
Glucose |
HPS-Ni-25% |
140 °C, 85 min, 4 MPa H2, water |
∼98 |
109 |
36 |
Mixed milled cellulose |
Ru/AC (40 wt%) |
205 °C, 5 h, 5 MPa H2, water |
60 |
110 |
37 |
Cellulose |
Ru/CNT (40 wt%) |
205 °C, 5 h, 5 MPa H2, water |
50.8 |
111 |
38 |
BM cellulose |
Ru–Ni/AC (40 wt%) |
205 °C, 4 h, 5 MPa H2, water |
74.3 |
112 |
39 |
Cellulose |
1.0% Ru/MN-270 (0.422 mol%) |
245 °C, 5 min, 6 MPa H2, water |
25 |
113 |
40 |
Glucose |
Ni–Co-1-1 (40 wt%) |
90 °C, 4 h, 3 MPa H2, water |
96 |
114 |
41 |
Glucose |
Ru:Ni/MCM-48 |
140 °C, 1.5 h, 2.5 MPa H2, water |
60 |
115 |
42 |
Glucose |
Pt/SBA-15 (20 wt%) |
140 °C, 4 h, 4 MPa H2, water |
65# |
116 |
43 |
Glucose |
5Ru/AFPS (5 wt%) |
100 °C, 1.5 h, 6 MPa H2, water |
73 |
117 |
44 |
Glucose |
Ru/MCM-48 |
120 °C, 45 min, 2.5 MPa H2, water |
89.5 |
118 |
Numerous research works have been performed on preparing sorbitol from glucose/cellulose, emphasizing on design, selectivity, efficiency, and recyclability of the catalyst. The Ru, Ni, Pt, and Pd metal-based catalysts impregnated on appropriate heterogeneous supporting materials were successfully used for the hydrogenation step. Among the non-noble transition metal catalysts, Ni-catalysts have shown remarkable activity (e.g., high conversion, good selectivity) but low recyclability. The hydrogenation of glucose requires relatively milder reaction conditions (<150 °C, 1–5 MPa H2) than that of cellulose (>160 °C, 6–8 MPa H2). The pretreated, ball-milled, and mixed ball-milled cellulose showed better conversion and selectivity toward sorbitol than untreated cellulose. The pretreatment processes lower cellulose's recalcitrant nature and make it more amenable to the catalyst and chemical reagent, thereby assisting in the subsequent saccharification step. The reaction was attempted under batch as well as continuous process conditions. A base additive is frequently introduced in the reaction medium to maintain an alkaline pH favoring the equilibrium toward the acyclic form of glucose. Like all other biorefinery processes, the development of robust, inexpensive, efficient, and eco-friendly catalysts is indispensable for the commercial production of sorbitol. The supporting material for the metal catalyst has multifaceted roles that encompass introducing additional characteristics (e.g., acid sites) to the catalyst, dispersing the metal sites, modifying the selectivity of the metal sites, providing mechanical stability to the catalyst, and assisting in the catalytic recovery. The most commonly used supports are carbon-based materials, but other supporting materials like zeolites, inorganic oxides, silica, heteropoly acids (HPAs), polymeric resins, and hydrotalcite (HT) are also not uncommon. The use of a homogeneous acid catalyst alongside a metal catalyst has been reported in the literature for producing sorbitol directly from cellulose. Developing bifunctional heterogeneous catalysts with acidic and metal sites is crucial for directly converting polysaccharides into sorbitol.
Sorbitan, a mixture of isomeric five- and six-membered cyclic ethers containing primary and secondary hydroxyl groups (total four), is formed by removing a molecule of water from sorbitol under acid catalysis. The sugar-derived polyols are well documented in the literature with potential application as the starting material for food additives, nonionic surfactants, and emulsifiers.119,120 1,4-Sorbitan is formed as the single major product from sorbitol when dehydrated by sulfuric acid catalyst under conventional heating.120 The synthesis of 1,4-sorbitan under microwave irradiation has also been reported.121 However, the mineral acid catalysts suffer from serious issues like poor recyclability and corrosiveness. In addition, the homogeneous acids promote double-dehydration of sorbitol to IS, thereby reducing the selectivity toward sorbitan. Therefore, the design of robust heterogeneous catalysts with precise control over their acid sites is of immense significance in this chemistry.122–125 The synthesis of sorbitan directly from glucose/cellulose is also reported in the literature by employing a mixture of acid and metal catalysts or a single bifunctional catalyst containing both metal and acid sites. For example, cellulose was selectively converted into sorbitan using a combination of Ru/C and mineral acids under an overpressure of hydrogen gas.54,126 A series of phosphate-supported nickel catalysts having both metal and acid sites were prepared and used as bifunctional catalysts for the value addition of cellulose. The use of Ni/TiP2 gave a 34.7% yield of 1,4-sorbitan starting from microcrystalline cellulose, whereas other catalysts like Ni/ZrP1, Ni/ZrP0.5, and Ni/ZrP2 gave sorbitol as a major product.82 The combination of HCl and Ru/C was employed to deconstruct microcrystalline cellulose (99.4% conversion) into 1,4-sorbitan and 3,6-sorbitan (a combined yield of 46.2%) under optimized conditions (215 °C, 30 min, 6 MPa H2).127 Sorbitan is often formed as the side product during the conversion of cellulose/glucose into sorbitol under catalytic hydrogenation conditions.126,128
1,4-Sorbitan is used as an environmentally benign surfactant, an emulsifier, and a plasticizer in various industries.124,129 Sorbitan fatty acid esters [Fig. 1(a–d), SFAEs] were prepared by reacting sorbitan with fatty acids or their esters under Fischer esterification or transesterification reaction conditions. They are commercially named Span® and used in applications like paints, emulsifiers, cosmetics, and pharmaceutical industries.130–132 SFAEs can be synthesized from sorbitol by combining dehydration and esterification reactions. The esterification of four hydroxyl groups in sorbitan leads to mono- to tetra-esters or a mixture thereof (Fig. 1). The direct synthesis of SFAEs from sorbitol involves dehydration and subsequent esterification.133,134 For the one-pot protocol, simultaneous dehydration and esterification were carried out in the presence of suitable acid and base catalysts.135 The direct synthesis of SFAEs from sorbitol was patented using a combination of acid and base catalysts in varying molar ratios.134,136 SFAEs can also be prepared by acylating 1,4-sorbitan with activated carbonyl compounds, such as acyl chloride, even at room temperature.137 The SFAEs are extensively used as food additives and have promising applications as nonionic surfactants.138 The mono- and dilinseed sorbitan esters were prepared directly from sorbitol and used as linseed oil-based emulsifiers in paints.139 Sorbitan monooleate was used to prepare electrospun poly(L-lactide-co-ε-caprolactone) core–shell type nanofibers via electrospinning techniques.140 The sorbitan esters have also found applications in drug delivery systems.141,142 For example, vesicles (niosomes) made of sorbitan monoesters were used as nonionic surfactants in oral drug delivery systems and demonstrated their inulin-protection ability in the presence of proteolytic enzymes.143 Monopalmitate-based proniosomal gel was developed and successfully used for the transdermal drug delivery of chlorpheniramine maleate, an antihistamine drug.144 The reaction between sorbitan esters and ethylene oxide results in the presence of a suitable base catalyst that forms polysorbates, marketed under brand names like Scattics® and Tween®, which have properties similar to SFAEs.130,145
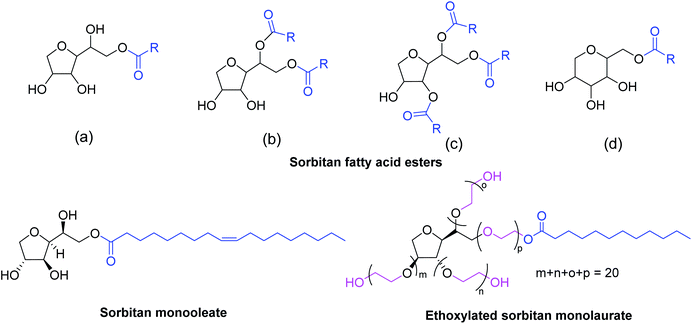 |
| Fig. 1 Molecular structure of some sorbitan fatty acid esters (SFAEs, general formula), polysorbate (Tween®20), and sorbitan monooleate (E494, a food additive). | |
Glucose can also be transformed into AA, a crucial chemical for several commodity products, such as polyurethane, cosmetics, fertilizers, insecticides, adhesives, and nylon-66.146 Around 75% of 6.9 billion pounds of AA projected to be produced worldwide in 2021 will be directed to form nylon-66.147 Bio-based AA is a greener and sustainable alternative to fossil-derived AA. AA can be synthesized from glucose via both chemocatalytic and enzymatic routes. Though the enzymatic pathway affords good selectivity toward AA, they are relatively slow, require a unique reactor design, and conform to strict regulatory guidelines.148 On the other hand, the chemocatalytic route enjoys technological support from the prevalent petrorefinery infrastructure and, therefore, is commercially more attractive. Glucose can be oxidized into AA following two mechanistic pathways via GRA or FDCA intermediate.147 The process passes through a series of selective oxidation and reduction steps. Glucose is first oxidized to GRA in the first pathway, then subjected to hydrogenolysis to remove the four secondary alcohols using metal catalysts under an overpressure of hydrogen gas forming AA.149 The main challenge in this synthetic pathway is the formation of side products by retro-Diels–Alder reaction of the GCA and glucuronic acid intermediates into molecules of smaller carbon chain lengths (e.g., lactic acid, glyceric acid).
In the second synthetic pathway, glucose-derived HMF is oxidized to FDCA, then selectively hydrogenated to AA using metal catalysts and acid promoters using molecular hydrogen as the reducing agent.71 Another potential synthetic route for AA involves the hydrogenation of HMF into HD followed by oxidation of the latter.60 FDCA can be obtained in excellent isolated yields under base-free conditions by using inexpensive, innocuous oxidants.150 Though noble metal catalysts (e.g., Pt, Au) have shown satisfactory activity, recent research in this area focuses on developing earth-abundant, transition metal-based catalysts.151 The ring-opening of FDCA requires relatively harsh reagents, such as HI, and the current focus is on improving the selectivity of the process under mild reaction conditions.152 The selective oxidation of the aldehyde group in glucose to a carboxylic acid forms GCA and is naturally present in many food products, such as honey, fruits, and wine. Sodium gluconate is a food additive (E574) and an acidity regulator, whereas calcium gluconate is a calcium supplement. The gluconate anion acts as a chelating agent for several metal ions and could be used as a cleaning agent.153 Although nitric acid as an oxidant has been used extensively for this process, the current focus is on using greener oxidants (e.g., aq. H2O2) that do not form toxic wastes and environmental pollutants.154 Table 2 lists recent literature references on oxidizing glucose to various C6 oxidation products.
Table 2 Direct oxidation of glucose to various sugar carboxylic acids without C–C bond cleavage reactiona
S/N |
Feedstock |
Product |
Catalyst |
Reaction conditions |
Yield (%) |
Ref. |
Abbreviations: GCA, gluconic acid; GRA, glucaric acid; CoPz, cobalt tetra(2,3-bis(butylthio)maleonitrile)porphyrazine; NR, Nanorod; MW, microwave; RT, room temperature. *Selectivity. |
1 |
Glucose |
GCA |
Au/SBA-15 |
110 °C, 2 h, glucose (0.2 M, 10 mL), catalyst (0.01 g), water, 0.5 MPa O2 |
95.2 |
155 |
2 |
Glucose |
GCA |
Co/Al2O3 |
60 °C, 3 h, glucose (20 wt%, 7.5 g), catalyst (0.016 g), pH 9 (controlled), water, D-glucose/30 wt% H2O2 (1/1 molar ratio) |
82 |
156 |
3 |
Glucose |
GCA |
Au-HBeta (AP) |
110 °C, 2 h, glucose (0.2 M, 20 mL), glucose/Au (1970/1 molar ratio), water, 0.5 MPa O2 |
90 |
157 |
4 |
Glucose |
GCA |
Au/MCM-41 |
37 °C, 45 min, glucose (0.15 M), glucose/Au (118 200/1 molar ratio), pH 7.4 (controlled), water, dissolved O2 (6–8 mg L−1) |
85* |
158 |
5 |
Glucose |
GCA |
PdBi/Al2O3 |
60 °C, 110 min, glucose (0.6 moL l−1, 25 mL), glucose/Pd (1900/1 molar ratio), pH 8.8–9.2, 10 mL min−1 O2 |
95.5 |
159 |
6 |
Glucose |
GCA |
g-C3N4/CoPz |
300 W xenon lamp (2 W cm−2), 20 min, glucose (1 mmol L−1, 30 mL), catalyst (0.02 g), water, H2O2 (30 μL) |
31 |
160 |
7 |
Glucose |
GCA |
Au61Pd39/Ce-NR |
80 °C, 6 h, catalyst (100 mol% of metal), pH 9.5 (initial), water, 0.6 MPa O2 |
97.7 |
161 |
8 |
Glucose |
GCA |
Gold electrode |
5 °C, 65 h, 0.55 VRHE for 30 s, 2.40 VRHE for 1 s, 0 VRHE for 1 s, 0.04 M glucose in 0.1 M NaOH |
86.6* |
162 |
9 |
Glucose |
GCA |
SnO2/FePz(SBu)8 |
Light intensity (2 W cm−2), 1 h, glucose (1 mmol L−1, 50 mL), catalyst (0.02 g), airflow (0.4 L min−1) |
18 |
163 |
10 |
Glucose |
GCA |
Au/HAP-LDH |
110 °C, 2 h, glucose (2 mmol), glucose/Au (1000/1 molar ratio), water (12 mL), 0.5 MPa O2 |
98 |
164 |
11 |
Glucose |
GCA |
Pd/Cellulose |
RT, 3 h, glucose (0.5 mmol, 0.053 g), catalyst (0.04 g), Na2CO3 (0.053 g), water (10 mL), 30 mL min−1 O2 |
91.2 |
165 |
12 |
Cellulose |
GCA |
FeCl3 |
110 °C, 2 h (hydrolysis in 60% FeCl3 and oxidation in 40% FeCl3), glucose (0.25 g), air |
50 |
166 |
13 |
Cellulose |
GCA |
FeCl3·6H2O/ethylene glycol (2 : 1) |
120 °C, 1 h, FeCl3 (oxidant) |
52.7 |
167 |
14 |
Cellobiose |
GCA |
CuO–CeO2 |
160 °C, 3 h, cellobiose (0.205 g), catalyst (0.050 g), water (15 mL), CuO as oxidant |
51 |
168 |
15 |
Glucose |
GRA |
AuBi/AC |
80 °C, 3 h, glucose/metal/NaOH (4.4/0.0088/13.2), water (15 mL), 1.3 MPa O2 |
>35 |
169 |
16 |
Glucose |
GRA |
Au–Pt/ZrO2 |
100 °C, 4 h, glucose/metal (80/1), 4 MPa O2 |
50 |
170 |
17 |
Glucose |
GRA |
NiFeOx-NF |
2 h, 10 mM glucose in 1 M KOH, E = 1.30 V, J = 17.7 mA cm−2, potential applied = 1.30 V |
83.3 |
171 |
18 |
Glucose |
Glucuronic acid |
Au/CeO2 |
130 °C, 4 h, glucose (0.55 mol L−1, 10 mL), catalyst (0.02 g), water (10 mL), 1.5 MPa O2 |
48 |
49 |
19 |
Glucose |
Glucuronic acid |
— |
25 °C, 4 h, water (100 mL), 10 mL min−1 O2 bubbling, ultrasonic irradiation (550 kHz, Pacouc = 0.36 W mL−1) |
94 |
172 |
20 |
Glucose |
Galacturonic acid |
Zinc–vanadium mixed oxide |
100 °C, 30 min, catalyst (0.01 g), water and H2O2 (10 mL), MW irradiation |
59.6 |
173 |
Several journal publications unveiled novel catalysts and process optimizations for selectively oxidizing glucose into targeted sugar acids (e.g., GCA, GRA).174,175 The heterogeneous catalysts bearing gold nanoparticles showed maximum catalytic efficiency toward glucose oxidation without C–C bond cleavage reactions. The monometallic or bimetallic catalysts using earth-abundant transition metals have also gained significant attention due to their better availability, lower cost, and lesser environmental footprint compared to noble metals. Many reports demonstrated that maintaining an alkaline pH during the reaction is beneficial for faster kinetics and better catalyst recyclability. However, the use of alkali additives during the reaction results in forming the salts of sugar acids. The isolation of sugar acids requires a protonation step, which produces inorganic salts as waste, and requires an additional purification step. Besides, an aqueous base facilitates the isomerization of glucose to fructose. Therefore, the base-free synthesis of sugar acids by the catalytic oxidation of glucose is paramount.
The preparation of sugar acids using eco-friendly materials (e.g., ion-exchange resins, deep eutectic solvent), and efficient processes (e.g., electrocatalysis, photocatalysis) are the recent trends. Molecular oxygen is one of the most sought-after terminal oxidants for the above transformation under batch and continuous flow conditions.172 The applications of peroxides (e.g., aq. H2O2) as oxidants are also well-documented in the literature.156,160 The catalytic deactivation was mainly due to sintering, leaching, and poisoning of active sites. Washing the recovered catalysts with polar solvents after each cycle and calcining helped remove organic depositions from the catalyst surface and regain their activity. The high-yielding productions of GRA, glucuronic acid, galacturonic acid, and AA from glucose have been reported. The direct use of polymeric carbohydrates (ca. cellulose) for oxidation products would be preferred for feedstock flexibility and better process economics. However, the process is substantially more challenging since it requires a cascade of transformations like hydrolysis and oxidation reactions in the appropriate sequence, requiring a more intricate catalyst design and other process parameters.
3. Value addition of glucose/cellulose via the isosorbide intermediate
The removal of a single molecule of water from sorbitol forms sorbitans. The removal of the second molecule of water from 3,6-sorbitan and 1,4-sorbitan under acid catalysis leads to IS (Fig. 2).176,177 However, other sorbitans like 2,5-sorbitan and 1,5-sorbitan lead to side products (i.e., humin) formation. The polyols often undergo not-so-well-understood decomposition reactions forming humin.
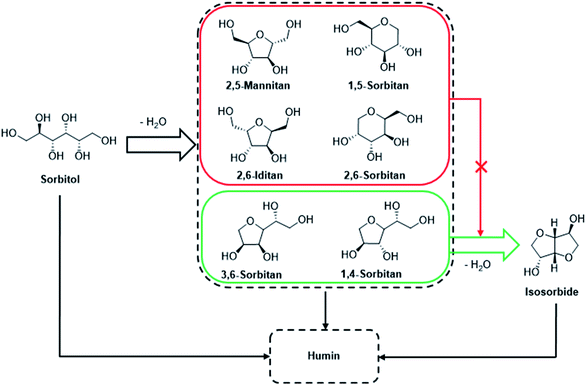 |
| Fig. 2 Schematic of the formation of IS starting from glucose-derived sorbitol. | |
The major challenge in forming IS is to develop a robust, inexpensive, selective, and recyclable catalyst that affords IS in high isolated yield in a readily scalable process. Various classes of homogeneous and heterogeneous acid catalysts have been examined for the dehydration reaction of sorbitol to IS. IS has been identified as a diol-based renewable monomer for various high-volume polymers with high thermal and chemical stability like polyesters, polycarbonates, polyethers, and polyurethanes.178–180 Many researchers have attempted to prepare IS from sorbitol or directly from glucose/cellulose, and the works have also been reviewed.52,177,181 The following table (Table 3) lists recent journal publications on the catalytic preparation of IS directly from glucose, cellulose, and cellulosic biomass.
Table 3 A table for the high-yielding preparation of IS from glucose and cellulose using different classes of acid catalystsa
S/N |
Feedstock |
Catalyst |
Acid |
Reaction conditions |
Yield (%) |
Ref. |
Abbreviations: MC, microcrystalline; NDC, nitrogen-doped carbon; SiW, silicotungstic acid; A70, Amberlyst 70. |
1 |
Cellulose |
Ru/C (10 wt%) |
HCl (0.10 M) |
215 °C, 6 h, 6 MPa H2, water |
49.5 |
127 |
2 |
MC-cellulose |
Ru/C (1.7 wt%) |
H2SO4 (0.5 M) |
220 °C, 2 h, 4 MPa H2, water |
50 |
182 |
Glucose |
60 |
3 |
MC-cellulose |
Ru/C (25 wt%) |
SiW (0.547 M) |
210 °C, 1 h, 5 MPa H2, water |
52 |
183 |
4 |
MC-cellulose |
Ru5.5@mNbPO (10 wt%) |
— |
220 °C, 1 h, 6 MPa H2, water |
53 |
184 |
5 |
Cellulose |
Ru/NbOPO4-pH2 (83 wt%) |
— |
230 °C, 24 h, 4 MPa H2, water |
13.2 |
185 |
6 |
Milled cellulose |
Ru/C (62 wt%) |
A70 (3.0 g) |
190 °C, 16 h, 5 MPa H2, water |
55.8 |
186 |
7 |
Japanese Cedar |
Ru/C (62 wt%) |
A70 (3.0 g) |
190 °C, 16 h, 5 MPa H2, water |
25.4 |
187 |
8 |
Glucose (0.1 M) |
Ru@Dowex-H (0.104 g) |
— |
190 °C, 48 h, 3 MPa H2, water |
84.9 |
188 |
9 |
Cellulose |
Ru2·2/Fe3O4@void@PMOSO3H0.14 (10 wt%) |
— |
220 °C, 2 h, 6 MPa H2, water |
58.1 |
189 |
10 |
Cellulose |
Ni/NbOPO4 |
— |
200 °C, 24 h, 3 MPa H2, water |
47 |
190 |
11 |
Glucose (0.05 M) |
35Ni/NDC (10 g) |
β-zeolite (30 g) |
Reactor 1: 150 °C, water |
54 |
191 |
Reactor 2: 230 °C, 50 h, 4.0 MPa |
The one-pot conversion of glucose or cellulose into IS reduces the number of synthetic steps and offers operational simplicity; however, catalyst deactivation remains an issue.181 Although the direct synthesis of IS from carbohydrates could improve the process economy by avoiding isolation and purification of sorbitol, there are daunting challenges to overcome.52 The conversion of glucose to IS requires a hydrogenation step followed by double-dehydration of the sorbitol intermediate. The use of cellulose as the feedstock requires an additional hydrolytic depolymerization step in the beginning.192 An assortment of chemical transformations working in perfect sequence requires a multifunctional catalyst or the right combination of catalytic candidates.183,186,190 The reaction parameters have to be optimized explicitly to minimize side products formation. The catalyst recovery is more challenging due to the accumulation of various chemical species from alternative reaction pathways. The combination of HCl and Ru/C catalyst was successfully used to convert cellulose directly to IS. IS was isolated in 49.5% yield at the quantitative conversion of cellulose under optimized parameters (215 °C, 6 h, 6 MPa H2).127 The use of cellulose and glucose as the substrate resulted in 51% and 60% yield of IS, respectively, when the reaction was performed at 220 °C for 2 h using 0.4 M H2SO4 and 4 MPa H2 pressure.182
In 2011, Op de Beeck et al. reported synthesizing IS from microcrystalline cellulose and lignocellulosic biomass (ca. hardwood, softwood, and wheat straw) using a combination of silicotungstic acid (H4SiW12O40) and Ru/C as an acid catalyst and metal catalyst, respectively.183 A maximum of 52% and 63% yields of IS were obtained from cellulose and delignified wheat straw pulp, respectively, under optimized reaction conditions. After first use, the loss of catalytic activity was due to the formation of polymeric byproducts and fouling caused by the deposition of polymeric byproducts on the catalyst surface.
The bifunctional Ru nanoparticles supported on mesoporous niobium phosphate without adding any soluble acids were used to synthesize IS. Quantitative conversion of cellulose was achieved with a 53% yield of IS by using 3 wt% Ru@mNbPO catalyst. The Ru NPs had a mean particle size of 5.5 nm and were recycled up to six catalytic cycles without losing activity significantly.184 The use of robust and mesoporous solid acid catalysts like niobium phosphate (NbOPO4)-based Ru/NbOPO4-pH2 resulted in only 13.2% IS via a one-step synthesis.185 However, using a combination of Ru/NbOPO4-pH2 and NbOPO4-pH2 in a two-step process gave a 56.7% yield of IS.
A combination of Pt/C (or Ru/C) and Amberlyst 70 (A70) catalysts were used for the one-pot conversion of milled cellulose to IS. The use of 4% Pt/C and A70 catalyst gave 29.9% yield of IS under optimized conditions (180 °C, 16 h, 5 MPa H2).186 Using a combination of 4% Ru/C and A70 improved the yield of IS to 55.8%. The size of Ru NPs influenced the yield of IS, where an average particle size of 5.3 nm showed superior catalytic activity than 2.3 nm. Unfortunately, the catalyst activity dropped catastrophically to 10.6% from 55.8% due to coke deposition of the catalyst surface. In a later report, the authors extended the synthetic strategy to real lignocellulosic biomasses like Japanese Cedar, Eucalyptus, and Bagasse and obtained 25.4%, 8.3%, and 12.8% yield of IS, respectively.187
A high-yielding synthesis of IS from glucose was obtained using a single heterogeneous catalyst containing immobilized metal and acid sites for hydrogenation and dehydration reactions. The high selectivity of metal catalyst was attributed to the narrow size distribution of immobilized metal and the high density of strong Brønsted acid sites on the microporous catalyst surface. An 84.9% yield of IS was obtained using Ru@Dowex-H as an efficient and recyclable catalyst.188 The magnetic Ru–SO3H reaction site was designed by dispersing Ru NPs on yolk–shell nanoarchitecture with Fe3O4 core and a sulfoacid-containing periodic mesoporous organosilica (PMO) shell.189 The PMO shell was hydrophobic and provided a suitable surface for dispersing the Ru NPs. The Fe3O4 core allowed an easy recovery of the catalyst by using an external magnet. The loading of Ru NPs and sulfonic acid were varied to study their effects on the catalyst activity. Up to a 58.1% yield of IS was obtained using the Ru2.2/Fe3O4@void@PMO-SO3H0.14 (2.2 nm Ru NPs) catalyst. The catalyst was recycled up to four cycles without a significant decline in IS yield.
A Ni-catalyst supported on niobium phosphate (Ni/NbOPO4) was prepared that contained both metal and acid sites to convert cellulose into IS.190 A series of catalysts with different Ni loading and different Brønsted to Lewis (B/L) acid ratios were prepared. IS was isolated in a 47% yield with 70 wt% loading Ni on support and the highest B/L ratio. Mechanistic studies of the reaction revealed that metallic Ni sites were responsible for the hydrogenation reaction. The Brønsted acidity originated from the P–OH, N–OH, and partially-hydrolyzed framework of Nb species, whereas the Lewis acidity came from coordinatively unsaturated Nb(V) sites. The 70%Ni/NbOPO4 catalyst was recycled and reused for up to five consecutive cycles with only a slight decrease in the catalytic activity.
Two fixed bed reactors were integrated for the direct conversion of an aqueous solution of glucose to IS in 54% yield by using a combination of Ni metal supported on nitrogen-doped carbon (Ni/NDC) and β-zeolite as the catalyst system.191 Initially, an aqueous solution of glucose (0.7 cm3 min−1) was hydrogenated to sorbitol in the first reactor at 150 °C using 35Ni/NDC as the catalyst. Sorbitol was then dehydrated to IS in the second reactor by treating it with β-zeolite as the acid catalyst at 230 °C.
The use of homogeneous mineral acid mandates an additional neutralization step or separation of acid from the product. The cyclodehydration of sorbitan to IS requires a higher temperature (>200 °C), whereas sorbitol synthesis from cellulose/glucose generally works at a lower temperature (<190 °C). Typically, the one-pot synthesis of IS from glucose or cellulose requires a reaction temperature of 180–220 °C. However, the reaction condition also triggered glucose dehydration to furanic products like HMF and the formation of some polymeric products like humin. The deposition of humin on the catalyst surface often led to catalyst deactivation. Therefore, the design of efficient bifunctional catalysts and the reaction conditions are necessary prerequisites for the satisfactory yield of IS and convenient catalyst recovery. Various supporting materials like HPAs, metal oxides, and metal salts with appropriate acidity, have been used to dehydrate cellulose to glucose and the cyclodehydration of sorbitol to IS. The choice of catalyst is important not to facilitate the isomerization of glucose to fructose since the hydrogenation–dehydration of the latter forms a mixture of IS and isomannide (IM). The HPAs are of great interest owing to their tunable acidity and easy recoverability. The use of acidic resins worked as the most efficient acid catalyst for the dehydration of sorbitol to IS.
IS has been recognized as a glucose/cellulose-derived renewable diol-based chemical building block for synthesizing various classes of products of commercial significance (Scheme 3). It is a chiral heterocyclic molecule containing only carbon, hydrogen, and oxygen atoms containing two secondary alcohol groups. The endo and exo-OH groups have different reactivities. The endo-OH has more nucleophilic character than the exo-OH group since the former makes a strong intramolecular hydrogen bond. On the other hand, the exo-OH group is less sterically hindered and more accessible to the reagents. High stability (e.g., chemical, thermal), renewability, inexpensiveness, and biodegradability of IS make it a lucrative monomer for several high-volume and engineering polymers, including polyesters, polycarbonates, polyurethanes, and polyamides.193–195 IS has also been used to synthesize small molecules, such as fuel oxygenates, solvents, plasticizers, surfactants, flame retardants, and pharmaceuticals.
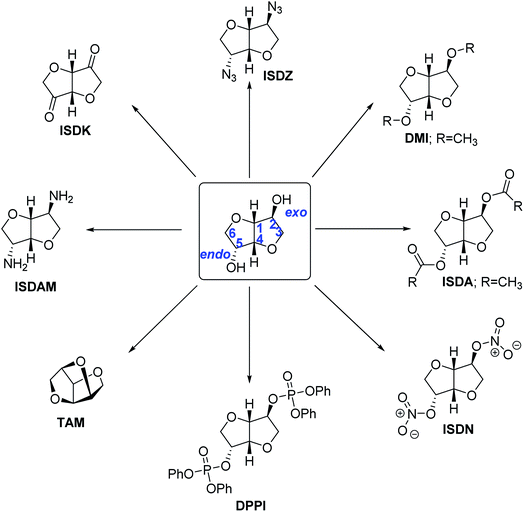 |
| Scheme 3 Some important derivatives of glucose/cellulose-derived IS. | |
3.1 Ethers of IS
IS shows the typical reactivity patterns of secondary alcohols. The ethers of IS, such as dimethyl isosorbide (DMI), can be synthesized by reacting IS or even sorbitol with dimethyl carbonate at elevated temperatures in the presence of a suitable organic or inorganic base to form DMI.196,197 The reaction passes through an ester intermediate, and CO2 is formed as the byproduct. DMI has potential uses as a green solvent, an active ingredient in various home care products, and pharmaceutical formulations.198–200 A dehydrative ether 1,4:2,5:3,6-trianhydro-D-mannitol (TAM) can be produced from IS in multi-step synthesis and used as a monomer for novel polyethers by ring-opening polymerization (ROP) of the bridgehead ether group in TAM.201
3.2 Esters of IS
The di- and mono-esters of IS have potential applications as renewable surfactants and plasticizers. Isosorbide-2,5-diacetate (ISDA) can be synthesized by reacting with powerful electrophiles like acetic anhydride or acetyl chloride.202 A greener process uses glacial acetic acid as the reagent, p-toluenesulfonic acid as a strong Brønsted acid catalyst, and toluene as the heteroazeotropic solvent for water removal by a Dean–Stark apparatus has afforded good results.203 Recently, Amberlyst-15 (A-15), a heterogeneous ion-exchange resin, has been used as an efficient and recyclable catalyst for the salable and high-yielding synthesis of ISDA by reacting IS with glacial acetic acid using n-propyl acetate as a green solvent.204 Various sulfonic acids have been examined as acid catalysts for the esterification of IS with acetic acid and octanoic acid.205 The process was successfully extended to one-pot, two-step production of diesters of IS directly from sorbitol.
The differential reactivity of exo- and endo-OH groups in IS can be exploited for preparing isosorbide-2-acetate (IS2Ac), a pharmaceutical intermediate. Using acetic anhydride as the reagent and lead(II) acetate catalyst gave excellent yield (ca. 85%) of IS2Ac even at RT.206 Using acetic acid instead of acetic anhydride required a strong Brønsted acid catalyst and elevated reaction temperature. The diesters of IS with carboxylic acids containing long alkyl chains (e.g., fatty acid) have been prepared using fatty acid chlorides as the reagent and pyridine as a base.207 The bio-derived diesters have potential applications as phytosanitary adjuvants.
3.3 Amination of IS
The –OH groups in IS can be transformed into isosorbide diamine (ISDAM) to be used as an intermediate for further value addition and novel monomer for polymeric applications.194 Direct amination of IS using ammonia in the presence of a homogeneous Ru3(CO)12 catalyst and a PNP pincer ligand has been reported.208 However, a mixture of isomers of diaminated IS, IM, and isoidide (II) was obtained. Heterogeneous Ru/C catalyst has also shown promising activity in the amination of IS using aqueous ammonia.209 Alternative processes include a multi-step synthesis where the –OH groups are initially converted into tosylate using tosyl chloride and pyridine as a base additive. In the second step, the tosylates are nucleophilically substituted with benzylamine. The Pd-catalyzed hydrogenolysis of the benzyl amines forms diamino IS with toluene as the byproduct in the final step.210 In 2019, a novel two-step synthesis of isomannide diamine (IMDAM) was reported.211 In the first step, the –OH groups in IS were replaced with benzylamine using cooperative catalysis between an iridium complex and a Brønsted acid. The benzyl group was deprotected in the second step by catalytic hydrogenation, forming IMDAM in 59% overall yield. The same strategy provided various mono-aminated products of IS in good yields. Isosorbide-2,5-diazide (ISDZ), produced by reacting sodium azide with IS containing good leaving groups (e.g., tosylate), can be catalytically reduced to form ISDAM.212
3.4 Isosorbide nitrates
The nitrates of IS are well-known medications for treating coronary diseases by relaxing the heart muscles and dilating the blood vessels.213 Isosorbide-2,5-dinitrate (ISDN) (Scheme 4) is rapidly metabolized in the body and produces isosorbide-2-nitrate (IS2MN) and isosorbide-5-nitrate (IS5MN) as metabolites. Among the three compounds, IS5MN has received maximum importance because of its superior bioavailability, half-life, toxicity, and oral applicability.214 IS5MN is the active pharmaceutical ingredient (API) in several pharmaceutical preparations and is sold under branded names like Somonit, Imdur, Monoket, and Chemydurin. An earlier method proposed a three-step synthesis that involved selective protection and deprotection of the –OH groups.215 In the first step, IS was selectively acetylated to IS2Ac. Any ISDA formed was deacylated to IS2Ac by reacting with fresh IS. In the second step, the endo-OH group at 5-position was nitrated by using the nitrating mixture. In the final step, the acetyl group was hydrolyzed in the presence of a suitable base such as KOH. The process afforded IS5MN in >60% overall yield. Over the past decades, several attempts have been made in greening the process with fewer synthetic steps, better selectivity, and improved atom economy.216 An alternative route produces ISDN by reacting IS with the nitrating mixture, which is then selectively reduced to IS5MN. Various reducing agents have been explored over the years, including hydrazine hydrate,217,218 borohydride reagents,219 and metal catalysts in the presence of molecular hydrogen.220 Selective nitration of IS to IS5MN has also been attempted, albeit with low selectivity.221
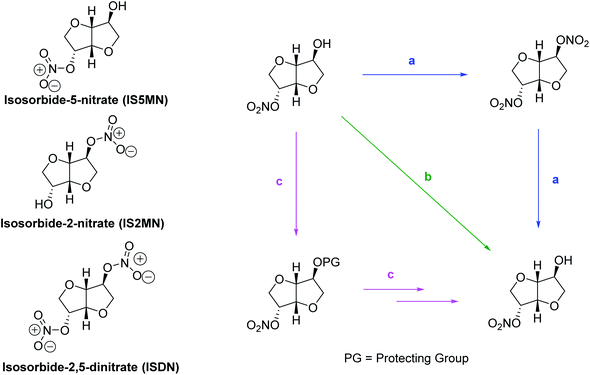 |
| Scheme 4 Various nitrated derivatives of IS (left) and the various preparative routes for IS5MN (right): (a) synthesis of IS5MN by selective reduction of ISDN, (b) direct mononitration of IS to IS5MN, and (c) multi-step synthesis of IS5MN by temporarily masking the exo-OH with a protecting group (PG). | |
3.5 Isosorbide diphosphates
The derivatives of IS decorated with sulfur, silicon, or phosphorus-containing substituents, have been used as fire retardants (FRs) for polymers like polybutylene succinate.222 Thermal characteristics of the bis-phosphorus isosorbide ester-based FRs depended on the oxidation state of phosphorus. The novel FRs could be greener (e.g., non-toxic, biodegradable, renewable) replacements for organohalogen FRs (Fig. 3).223 Diphenylphosphinate isosorbide (DPPII) was found to be a promising phosphinate FR, whereas phosphonate and phosphate-based FRs include diphenylphosphate isosorbide (DPPI) and di-DOPO-isosorbide (DDI).222 Polymeric FRs such as polyphenylphosphate isosorbide (PPPAI) have also been synthesized and studied. Castor oil-derived 10-undecenoic acid and IS have been used as biorenewable feedstock for the multi-step synthesis of di[14-(diethylphosphato)-12-thiatetradecanoate] isosorbide (DPPEI), a novel phosphate-based FR.224
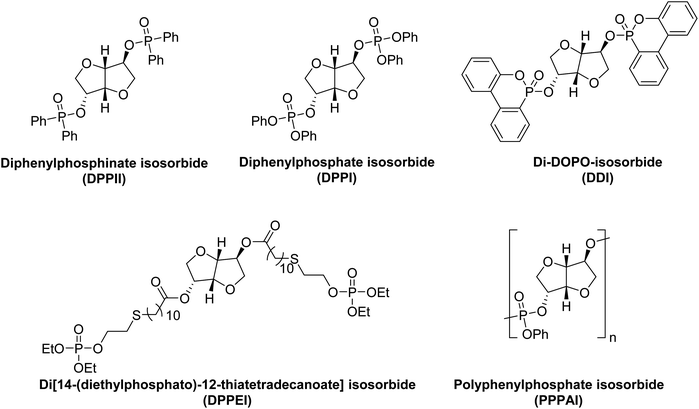 |
| Fig. 3 Phosphinate, phosphonate, and phosphate-based small molecules and polymers as flame retardants. | |
3.6 Isomerization of IS
The two secondary hydroxyl groups in IS are in the exo and endo geometry. The spatial geometry of the hydroxyl groups modulates their reactivity, which is often exploited in preparing specialty chemicals. IS, IM, and II, collectively known as isohexides, are sourced from glucose, mannose, and idose, respectively.225 The exo, exo geometry of the two –OH groups in II makes it a better monomer than IS for synthesizing high molecular weight polymers with superior physicochemical properties.226 However, idose is a rare sugar and orders of magnitude more expensive than glucose. Therefore, the commercial venture of sourcing II from idose is untenable. Interestingly, the isomerization of IS into II under catalytic hydrogenation conditions opens up an economically viable pathway for synthesizing the latter. In a typical process, an aqueous solution of IS is heated in the presence of a metal-based hydrogenation catalyst under an overpressure of hydrogen gas. IS is isomerized into an equilibrium mixture of IS, IM, and II with an approximate ratio of 36
:
7
:
57. After evaporating the solvent, II is isolated from the equilibrium mixture by fractional distillation under vacuum. Even though alternative mechanisms have also been suggested, the isomerization reaction is believed to pass through a transient ketone intermediate. There have been recent attempts in moderating the reaction parameters for better energy efficiency and higher mass balance. In recent work, IS has been isomerized into II under relatively mild conditions by catalytic transfer hydrogenation (CTH) using 2-propanol as the hydrogen donor and 5% Ru/C as the catalyst.227 A novel and efficient purification process of II by aqueous-organic extraction by selectively acetylating the endo-OH group(s) of IM and IS in the product mixture was also demonstrated. The process opens up a straightforward, inexpensive, and scalable preparation of II, which will help in exploring its derivative chemistry.
3.7 Oxidation of IS
IS has been oxidized to mono- and di-ketones, which can act as chemical intermediates for various known as well as novel derivatives. For example, the di-ketone of IS has been proposed as a reactive intermediate for synthesizing ISDAM by reductive amination. Both chemical and enzymatic oxidation protocols have been employed for the oxidation and have provided satisfactory results. The aerobic oxidation of IS (also IM) using a combination of TEMPO and laccase provided a nearly quantitative (ca. 99%) yield of isosorbide-2,5-diketone (ISDK) under ambient temperature.228 Chromic acid and PtO2 catalyst (in an O2 atmosphere) led to selective oxidation of the endo-OH group in IS, forming a mono-ketone.229
4. Value addition of glucose/cellulose via the HMF intermediate
5-(Hydroxymethyl)furfural (HMF) is formed by sequentially removing three water molecules from a glucose molecule, which is promoted by acid and heat.230 HMF can be formed directly from complex carbohydrates like starch and cellulose by combining hydrolysis and dehydration reactions. The mechanistic pathways proposed for HMF formation from glucose goes through both cyclic and acyclic intermediates.231 In one mechanistic pathway, glucose is isomerized into fructose, and water molecules are selectively eliminated from the fructofuranose form of the latter. Reaction conditions that promote the isomerization of glucose to fructose give better yields of HMF and fewer decomposition products (i.e., humin).232 There are hundreds of literature reporting the preparation and derivative chemistry of HMF starting from glucose or cellulose, and these works have been reviewed periodically.232–235 Therefore, only a brief overview of the HMF chemistry is discussed in this section. The readers are directed to dedicated reviews on the production and derivative chemistry of HMF for comprehensive information. HMF has been established as one of the most promising renewable chemical building blocks in the biorefinery concept. HMF retains some of the key functionalities of glucose (e.g., aldehyde, hydroxyl), which are used for downstream synthetic value addition pathways into compounds of varying structural and functional complexities.233 Two mechanistic pathways are proposed for the dehydration of glucose into HMF. In the first pathway, glucose is first isomerized into fructose in the reaction medium. The sequential elimination of three molecules of water from the fructofuranose form of fructose forms HMF (Scheme 5). In the second pathway, the dehydration starts in the open form of glucose itself, with enol and enone forming as reactive intermediates. As evident from the pathways, the elimination of water molecules from fructofuranose is relatively straightforward to form HMF. Therefore, reaction conditions that promote the isomerization of glucose into fructose improve HMF yield. The formation of side products and humin can begin with any of the reactive intermediates or even HMF.
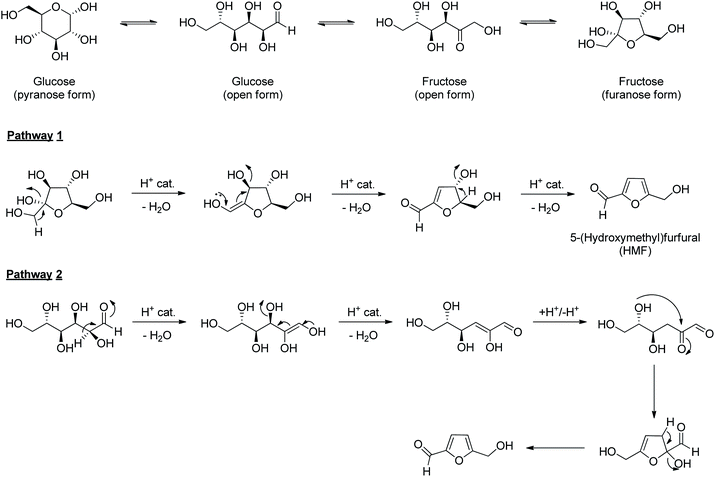 |
| Scheme 5 Mechanistic pathways of HMF formation from glucose. | |
The transformation of HMF into fuels and chemicals often involves C–C bond cleavage and formation reactions.234,235 In this review, some of the crucial derivatives of HMF are highlighted that retain all the six carbon atoms of the parent sugar molecule. Many of the critical derivatives of HMF involve redox chemistry, where the existing functional groups in HMF (i.e., hydroxymethyl, aldehyde, furan ring) are selectively oxidized/reduced to other functional groups.236,237 The sequential reduction of HMF under catalytic hydrogenation conditions leads to a series of furanic and non-furanic derivatives (Scheme 6). For example, selective hydrogenolysis of the C–OH bond in HMF forms 5-methylfurfural (MF).238 MF has potential applications as a fuel oxygenate and a chemical intermediate in other value addition pathways. Catalytic hydrogenation of aldehyde and the hydroxymethyl group in HMF to methyl groups forms 2,5-dimethylfuran (DMF).239 The transformation passes through various furanic intermediates such as MF, 2,5-bis(hydroxymethyl)furan (BHMF), and 5-(hydroxymethyl)-5-methylfuran (HMMF). DMF is a promising biofuel with a high research octane number (RON = 119) and similar properties (e.g., physicochemical, thermal) to those of petro-gasoline.240 Besides, DMF has been recognized as a key starting material in synthesizing p-xylene for renewable polyethylene terephthalate and related polymers.241 Hydrogenation of the furan ring in DMF forms 2,5-dimethyltetrahydrofuran (DMTHF), a potential fuel oxygenate and an attractive green solvent.242,243 Hydrogenolysis of DMTHF produces 2-hexanol, which on further hydrogenolysis leads to n-hexane.66 Other furanic intermediates can also be produced selectively by employing appropriate catalysts and reaction conditions. Hydrogenation of the aldehyde group in HMF leads to BHMF, which on ring-hydrogenation forms BHMTHF.244 Both BHMF and BHMTHF are potential renewable monomers to prepare new generation biopolymers.245 The glucose to n-hexane transformation through HMF intermediate allows step-wise removal of oxygen atoms from glucose in the form of water without involving the C–C bond scission reactions. Seven moles of hydrogen are required for the transformation of a mole of glucose to n-hexane. A one-pot transformation of cellulose to n-hexane used Ir-ReOx/SiO2 as the catalyst and HZSM-5 as the cocatalyst in a dodecane/water biphasic reaction mixture.246 The oxophilic metals assisted in the HDO chemistry of the sorbitol intermediate, and a 78% yield of n-hexane was ensured from microcrystalline cellulose under optimized conditions (190 °C, 12 h, 6 MPa H2). Many of the partially-reduced furanic derivatives discussed above have been targeted starting from glucose or directly from cellulose. For example, several papers reported satisfactory yields of DMF starting from glucose or cellulose. Although a one-pot synthesis is preferable since the isolation and purification of intermediates like HMF can be avoided, the catalyst recyclability is often challenged by many side products deactivating the active sites.
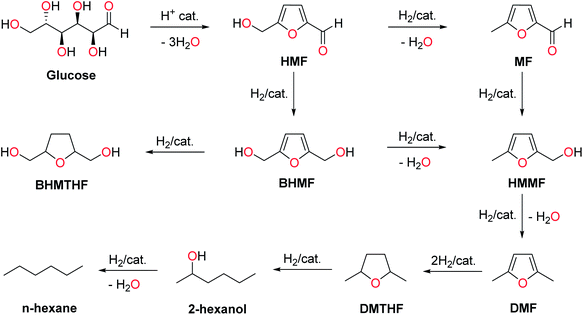 |
| Scheme 6 Selective deoxygenation of glucose to n-hexane under catalytic hydrogenation conditions through the HMF intermediate. | |
The selective oxidation of HMF also produces several crucial furanic chemical building blocks. Oxidation of the hydroxymethyl arm in HMF to an aldehyde group leads to 2,5-diformylfuran (DFF), which is a potential monomer for polymeric application and a chemical intermediate.247 Oxidation of both the hydroxymethyl and aldehyde groups of HMF into carboxylic acid produces 2,5-furandicarboxylic acid (FDCA), which passes through partially-oxidized intermediates like DFF, 5-(hydroxymetyl)-2-furoic acid (HMFCA), and 5-formyl-2-furancarboxylic acid (FFCA) (Scheme 7). FDCA has been proposed as a renewable replacement of terephthalic acid for the synthesis of polyesters.248 The synthesis of DFF and FDCA from HMF using innocuous oxidants (e.g., O2) and eco-friendly catalysts is preferred over stoichiometric oxidants to avoid forming wastes.249 Recent studies have focused on developing efficient heterogeneous catalysts for the scalable, high-yielding synthesis of furanic compounds starting from HMF. The hydrophobic analogs of HMF, which have superior hydrolytic and thermal stability, have also been used to substitute HMF in synthesizing various furanic derivatives.250
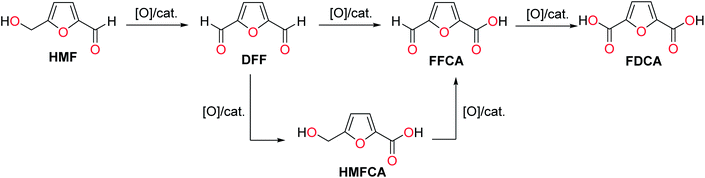 |
| Scheme 7 Value-addition of glucose-derived HMF into C6 chemicals by oxidation reactions. | |
Several C6 chemical intermediates with potential applications as biofuels, chemicals, and monomers for renewable polymers have been prepared selectively from HMF.
HMF can be transformed into several other straight-chain and cyclic compounds with differing carbon skeletal systems without C–C bond cleavage or C–C bond forming reactions. For example, catalytic hydrogenation of HMF to DMF followed by hydrolysis of the latter in aqueous acid forms hexane-1,6-dione (HDN) (Scheme 8).251 HDN has been used as the starting material for the synthesis of cyclic hydrocarbon-based aviation fuels.252 HMF can be reacted with alkyl alcohols under acid catalysis to form ethers, such as 5-(ethoxymethyl)furfural (EMF), a promising fuel oxygenate.253 HMF can be esterified with carboxylic acids (e.g., acetic acid) to form furanic esters with potential applications as renewable surfactants and chemical intermediates.254 In these derivatives of HMF, the furan ring remains intact while the functionalities attached to the ring are subjected to synthetic modifications.
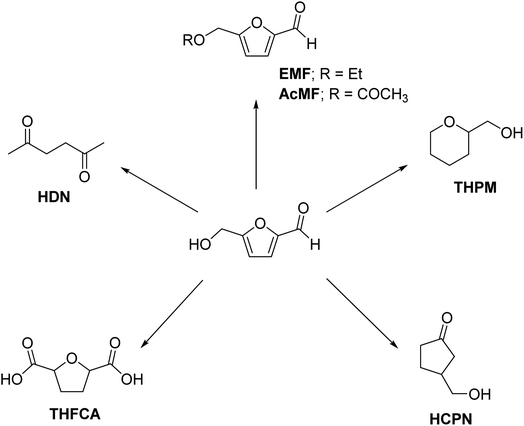 |
| Scheme 8 Value-addition of glucose-derived HMF into C6 chemicals having different carbon skeletons in the molecular structure. | |
The molecular rearrangement of HMF in water under catalytic hydrogenation conditions forms 3-(hydroxymethyl)cyclopentanone (HCPN).255 Over the past few years, significant research has been conducted on designing robust, efficient, inexpensive, and eco-friendly catalysts and understanding the roles of various reaction parameters for the scalable and high-yielding synthesis of HCPN from HMF.256 The synthetic derivatives of HCPN have potential applications as biofuels, renewable solvents, and fragrances. Partial reduction of HMF followed by dehydrative cyclization forms tetrahydropyran-2-methanol (THPM). The oxidation of HMF to FDCA followed by hydrogenating the furan ring in the latter compound forms tetrahydrofuran-2,5-dicarboxylic acid (THFCA), a promising monomer for sustainable polyesters.
During the hydration of glucose into HMF, 2-(hydroxyacetyl)furan (HAF), a C6 furanic compound, is typically formed as a minor product.257 HAF has the potential to be used as a renewable chemical platform owing to the presence of reactive functionalities in its moiety. However, there is no report to date on the targeted, high-yielding production of HAF from glucose.
5. Conclusion and future prospects
This review has described the chemocatalytic transformation of glucose and cellulose into fuels and chemicals without the carbon–carbon bond cleavage and formation reactions. As apparent from the previous sections, the derivatives of glucose bearing six carbons branch out from a handful of chemical intermediates such as sorbitol, sorbitan, HMF, IS, and GCA. Therefore, the commercial feasibility of synthesizing the high-value compounds relies on the scalability and process economics of producing the chemical intermediates. Catalysis plays a crucial role in the synthetic upgrading of glucose (or cellulose) to fuels and chemicals. A new generation of robust, selective, inexpensive, and eco-friendly catalysts is being developed for that purpose. Many of the chemical transformations involved one or more oxidation and reduction steps. Inexpensive and innocuous reagents such as molecular oxygen as the oxidant and molecular hydrogen as the reducing agent are employed for the processes. Noble metal-based catalysts generally show superior activity, recyclability, and function under relatively mild conditions. In recent years, earth-abundant transition-metal-based catalysts are increasingly popular for their low cost, better availability, and less environmental impact (e.g., mining of noble metals). However, the transition metal catalysts generally require special preparation techniques and often require more demanding reaction conditions than their noble metal counterpart. Therefore, serious consideration must be attributed to determining the overall impact of replacing a noble metal catalyst with a transition metal catalyst in energy requirement, recyclability, and waste management. Selectivity remains a crucial aspect in virtually all of the chemical transformations involving glucose or glucose-derived C6 intermediates. A high selectivity (and yield) of the targeted product(s) improve environmental benefits such as waste minimization and simplified product purification and ensure superior process economics. The selectivity of a catalytic transformation depends on the type of catalyst and the reaction parameters involved in the process. A new library of highly efficient catalysts has been built, which is getting expanded rapidly. Heterogeneous catalysts are largely favored over their homogeneous counterparts for obvious reasons like ease of separation of catalyst, product purification, and catalyst recyclability. In recent years, nanocatalysts and single-atom catalysts (SACs) have been increasingly used for significantly higher reactivity and selectivity than traditional heterogeneous catalysts. Significant research has been performed to understand their involvement in the reaction mechanism and catalytic action. Detailed studies are being undertaken to comprehend the role of particle size, morphology, and electronic interaction between the active catalytic species with the supporting material on the catalytic activity. In addition to the traditional supporting materials, various new supporting materials such as metal–organic framework (MOF), carbon nanotube (CNT), and graphene oxide (GO) have shown promise. Future research in this area will likely concentrate on designing highly efficient, multitasking, stable, and recyclable catalysts. A multifunctional integrated catalyst having intimate and synergistic active sites is crucial for catalyzing a cascade of reactions in a one-pot synthesis of products from the inexpensive feedstock. For example, a catalyst containing both metal sites (for hydrogenation) and acid sites (for hydrolysis and dehydration) can produce IS directly cellulose. The process would avoid producing and purifying glucose from cellulose in the initial step, thereby improving the scalability and process economics. A detailed theoretical understanding (e.g., electronic interactions between various components of the catalyst candidate and with intermediates of the chemical transformation) backed with experimental data will expedite the research.
Attempts must be taken to directly convert lignocellulosic biomass and cellulosic wastes instead of pure cellulose or glucose, which would lower the production cost and enhance the environmental incentives of the processes. In this regard, the catalytic production of sorbitol and isosorbide from glucose has reached maturity. However, more research is required in making these compounds directly from cellulose or cellulosic biomasses using eco-friendly catalysts under energy-efficient reaction conditions. In recent years, the focus has been shifted on the production of renewable polymers from isohexides with designed properties and targeted applications. Novel fuel oxygenates, renewable solvents, and biosurfactants are also being produced using isohexides as the molecular scaffold. It can be safely predicted that sorbitol and isohexides will be integral parts of biorefineries that employ glucose/cellulose as feedstock. However, some other derivatives such as HMF and GCA need more research to reach commercialization. Though good yields of HMF were obtained in isolated cases, the inherent hydrophilicity and instability in aqueous acid continue to plague its scalability and commercial production. The derivative chemistry of HMF is actively being explored to encompass all major classes of chemicals and materials originating from petroleum. For example, the redox reaction of HMF is well-studied, and a wealth of data is already available in the literature. Attempts have been made in commercializing the HMF derivatives, such as DMF and FDCA, into high-volume polymers. The sugars-derived acids (e.g., GCA, GRA) and polyols (e.g., sorbitans) are being used for materials applications, including surfactants and polymers. The selective synthesis of n-hexane from glucose/cellulose has received serious attention as a direct entry to naphtha-range hydrocarbons from carbohydrates. In a biorefinery employing glucose as the feedstock, access to all the intermediates discussed in this review will ensure a broader product portfolio and provide economic advantages.
Author contributions
Dr Saikat Dutta is responsible for the conceptualization, data analysis, and manuscript writing. Miss Navya Subray Bhat is responsible for collecting resources and editing the manuscript.
Conflicts of interest
There are no conflicts to declare.
Acknowledgements
SD thanks the Council of Scientific and Industrial Research (CSIR), India, for financial assistance under project number 02(0301)/17/EMR-II. NSB thanks NITK, Surathkal, for the scholarship support.
References
- R. Ahorsu, F. Medina and M. Constantí, Energies, 2018, 11, 3366 CrossRef CAS.
- K. Kohli, R. Prajapati and B. K. Sharma, Energies, 2019, 12, 233 CrossRef CAS.
- E. Cséfalvay and I. T. Horváth, Chemicals from renewable feedstocks, McGraw-Hill Yearbook of Science & Technology 2013, New York, USA, 2013 Search PubMed.
- A. Demirbaş, Energy Convers. Manage., 2001, 42, 1357–1378 CrossRef.
- E. S. Abdel-Halim, Arabian J. Chem., 2014, 7, 362–371 CrossRef CAS.
- F. H. Isikgor and C. R. Becer, Polym. Chem., 2015, 6, 4497–4559 RSC.
- H. Yang, X. Zhang, H. Luo, B. Liu, T. M. Shiga, X. Li, J. I. Kim, P. Rubinelli, J. C. Overton, V. Subramanyam, B. R. Cooper, H. Mo, M. M. Abu-Omar, C. Chapple, B. S. Donohoe, L. Makowski, N. S. Mosier, M. C. McCann, N. C. Carpita and R. Meilan, Biotechnol. Biofuels, 2019, 12, 171 CrossRef PubMed.
- Y.-B. Huang and Y. Fu, Green Chem., 2013, 15, 1095–1111 RSC.
- S. Hari Krishna and G. V. Chowdary, J. Agric. Food Chem., 2000, 48, 1971–1976 CrossRef CAS PubMed.
- D. J. Tenenbaum, Environ. Health Perspect., 2008, 116, A254–A257 Search PubMed.
- J. Song, H. Fan, J. Ma and B. Han, Green Chem., 2013, 15, 2619–2635 RSC.
- The role of green chemistry in biomass processing and conversion, ed. H. Xie and N. Gathergood, John Wiley & Sons, Inc., 2012 Search PubMed.
- D. Mohan, C. U. Pittman and P. H. Steele, Energy Fuels, 2006, 20, 848–889 CrossRef CAS.
- R. H. Crabtree, J. Chem. Soc., Dalton Trans., 2001, 17, 2437–2450 RSC.
- R. A. Lee and J.-M. Lavoie, Anim. Front., 2013, 3, 6–11 CrossRef.
- E. M. M. Abdelraheem, H. Busch, U. Hanefeld and F. Tonin, React. Chem. Eng., 2019, 4, 1878–1894 RSC.
- K. Rosenthal and S. Lütz, Curr. Opin. Green Sustain., 2018, 11, 58–64 CrossRef.
- C.-H. Zhou, X. Xia, C.-X. Lin, D.-S. Tong and J. Beltramini, Chem. Soc. Rev., 2011, 40, 5588–5617 RSC.
- X. Huang, M. Cao and H. Zhao, Curr. Opin. Chem. Biol., 2020, 55, 161–170 CrossRef CAS PubMed.
- P. A. Jacobs, M. Dusselier and B. F. Sels, Angew. Chem., Int. Ed., 2014, 53, 8621–8626 CrossRef CAS PubMed.
- S. Zhang, Y. Yu, K. Sheng, J. Liu, E. Shuang, C. Jin, Z. Xu and X. Zhang, Biofuels, Bioprod. Biorefin., 2021, 15, 592–608 CrossRef CAS.
- L. Liu and A. Corma, Chem. Rev., 2018, 118, 4981–5079 CrossRef CAS PubMed.
- M. S. Hamdy, M. A. Eissa and S. M. A. S. Keshk, Green Chem., 2017, 19, 5144–5151 RSC.
- S. Dutta and N. S. Bhat, ChemCatChem, 2021, 13, 3202–3222 CrossRef CAS.
- Y. Hirano, Y. Kasai, K. Sagata and Y. Kita, Bull. Chem. Soc. Jpn., 2016, 89, 1026–1033 CrossRef CAS.
- C. Wang, X. Chen, M. Qi, J. Wu, G. Gözaydın, N. Yan, H. Zhong and F. Jin, Green Chem., 2019, 21, 6089–6096 RSC.
- Y.-Y. Li, B. Wang, M.-G. Ma and B. Wang, Int. J. Polym. Sci., 2018, 2018, e8973643 Search PubMed.
- M. Tobiszewski, M. Marć, A. Gałuszka and J. Namieśnik, Molecules, 2015, 20, 10928–10946 CrossRef CAS PubMed.
- Y. Liu, S. Ahmed, D. E. Sameen, Y. Wang, R. Lu, J. Dai, S. Li and W. Qin, Trends Food Sci. Technol., 2021, 112, 532–546 CrossRef CAS.
- E. B. Jackson, in Handbook of Starch Hydrolysis Products and their Derivatives, ed. M. W. Kearsley and S. Z. Dziedzic, Springer US, Boston, MA, 1995, pp. 245–268 Search PubMed.
- P. K. Gupta, S. S. Raghunath, D. V. Prasanna, P. Venkat, V. Shree, C. Chithananthan, S. Choudhary, K. Surender and K. Geetha, An update on overview of cellulose, its structure and applications, IntechOpen, 2019 Search PubMed.
- K. Wasilewska and K. Winnicka, Materials, 2019, 12, 3386 CrossRef CAS PubMed.
- J. Wolfs and M. A. R. Meier, Green Chem., 2021, 23, 4410–4420 RSC.
- G. Joshi, V. Rana, S. Naithani, V. K. Varshney, A. Sharma and J. S. Rawat, Carbohydr. Polym., 2019, 223, 115082 CrossRef CAS PubMed.
- C. W. Saunders and L. T. Taylor, J. Energ. Mater., 1990, 8, 149–203 CrossRef CAS.
- G. Chen, B. Zhang, J. Zhao and H. Chen, Carbohydr. Polym., 2013, 95, 332–337 CrossRef CAS PubMed.
- D. R. Mulinari, H. J. Voorwald, M. O. Cioffi and M. L. da Silva, J. Compos. Mater., 2017, 51, 1807–1815 CrossRef CAS.
- Z. N. Terzopoulou, G. Z. Papageorgiou, E. Papadopoulou, E. Athanassiadou, E. Alexopoulou and D. N. Bikiaris, Ind. Crops Prod., 2015, 68, 60–79 CrossRef CAS.
- K.-Y. Lee, Y. Aitomäki, L. A. Berglund, K. Oksman and A. Bismarck, Compos. Sci. Technol., 2014, 105, 15–27 CrossRef CAS.
- B. Thomas, M. C. Raj, K. B. Ahthira, M. H. Rubiyah, J. Joy, A. Moores, G. L. Drisko and C. Sanchez, Chem. Rev., 2018, 118, 11575–11625 CrossRef CAS PubMed.
- L. Chávez-Guerrero, J. Silva-Mendoza, S. Sepúlveda-Guzmán, N. A. Medina-Aguirre, S. Vazquez-Rodriguez, M. E. Cantú-Cárdenas and N. A. García-Gómez, Carbohydr. Polym., 2019, 210, 85–91 CrossRef PubMed.
- S. A. Jabasingh, D. Lalith, M. A. Prabhu, A. Yimam and T. Zewdu, Carbohydr. Polym., 2016, 136, 700–709 CrossRef CAS PubMed.
- N. N. Potter and J. H. Hotchkiss, Food Science, 5th edn, Springer US, 1995 Search PubMed.
- A. A. Marianou, C. M. Michailof, A. Pineda, E. F. Iliopoulou, K. S. Triantafyllidis and A. A. Lappas, ChemCatChem, 2016, 8, 1100–1110 CrossRef CAS.
- A. A. Marianou, C. M. Michailof, D. K. Ipsakis, S. A. Karakoulia, K. G. Kalogiannis, H. Yiannoulakis, K. S. Triantafyllidis and A. A. Lappas, ACS Sustainable Chem. Eng., 2018, 6, 16459–16470 CrossRef CAS.
- F. Bruni, C. Di Mino, S. Imberti, S. E. McLain, N. H. Rhys and M. A. Ricci, J. Phys. Chem. Lett., 2018, 9, 3667–3672 CrossRef CAS PubMed.
- R. C. Deis and M. W. Kearsley, in Sweeteners and Sugar Alternatives in Food Technology, John Wiley & Sons, Ltd, 2006, pp. 249–261 Search PubMed.
- M. Abert, N. Mora and J.-M. Lacombe, Carbohydr. Res., 2002, 337, 997–1006 CrossRef CAS PubMed.
- R. Wojcieszak, I. M. Cuccovia, M. A. Silva and L. M. Rossi, J. Mol. Catal. A: Chem., 2016, 422, 35–42 CrossRef CAS.
- W. Deng, L. Yan, B. Wang, Q. Zhang, H. Song, S. Wang, Q. Zhang and Y. Wang, Angew. Chem., Int. Ed., 2021, 60, 4712–4719 CrossRef CAS PubMed.
- V. B. Thaore, R. D. Armstrong, G. J. Hutchings, D. W. Knight, D. Chadwick and N. Shah, Chem. Eng. Res. Des., 2020, 153, 337–349 CrossRef CAS.
- C. Dussenne, T. Delaunay, V. Wiatz, H. Wyart, I. Suisse and M. Sauthier, Green Chem., 2017, 19, 5332–5344 RSC.
- D. J. Saxon, A. M. Luke, H. Sajjad, W. B. Tolman and T. M. Reineke, Prog. Polym. Sci., 2020, 101, 101196 CrossRef CAS.
- R. Palkovits, K. Tajvidi, J. Procelewska, R. Rinaldi and A. Ruppert, Green Chem., 2010, 12, 972–978 RSC.
- S. Meier, Catal. Sci. Technol., 2020, 10, 1724–1730 RSC.
- K. Yoshioka, T. Yamada, H. Ohno and H. Miyafuji, RSC Adv., 2015, 5, 72405–72409 RSC.
- X. Kong, Y. Zhu, Z. Fang, J. A. Kozinski, I. S. Butler, L. Xu, H. Song and X. Wei, Green Chem., 2018, 20, 3657–3682 RSC.
- T. Buntara, S. Noel, P. H. Phua, I. Melián-Cabrera, J. G. de Vries and H. J. Heeres, Top. Catal., 2012, 55, 612–619 CrossRef CAS.
- J. Xi, Q. Xia, Y. Shao, D. Ding, P. Yang, X. Liu, G. Lu and Y. Wang, Appl. Catal., B, 2016, 181, 699–706 CrossRef CAS.
- N. Capece, A. Sadier, C. P. Ferraz, J. Thuriot-Roukos, M. Pietrowski, M. Zieliński, S. Paul, F. Cavani and R. Wojcieszak, Catal. Sci. Technol., 2020, 10, 2644–2651 RSC.
- M. Mounguengui-Diallo, F. Vermersch, N. Perret, C. Pinel and M. Besson, Appl. Catal., A, 2018, 551, 88–97 CrossRef CAS.
- R. Lebeuf, C.-Y. Liu, C. Pierlot and V. Nardello-Rataj, ACS Sustainable Chem. Eng., 2018, 6, 2758–2766 CrossRef CAS.
- W. von Rybinski and K. Hill, Angew. Chem., Int. Ed., 1998, 37, 1328–1345 CrossRef CAS PubMed.
- J. Pang, M. Zheng, R. Sun, A. Wang, X. Wang and T. Zhang, Green Chem., 2016, 18, 342–359 RSC.
- J.-G. Rosenboom, D. K. Hohl, P. Fleckenstein, G. Storti and M. Morbidelli, Nat. Commun., 2018, 9, 2701 CrossRef PubMed.
- B. Xiao, M. Zheng, X. Li, J. Pang, R. Sun, H. Wang, X. Pang, A. Wang, X. Wang and T. Zhang, Green Chem., 2016, 18, 2175–2184 RSC.
- J. Tuteja, H. Choudhary, S. Nishimura and K. Ebitani, ChemSusChem, 2014, 7, 96–100 CrossRef CAS PubMed.
- Y. Gu, M. Tamura, Y. Nakagawa, K. Nakao, K. Suzuki and K. Tomishige, Green Chem., 2021, 23, 5786–5796 RSC.
- M. Lomelí-Rodríguez, J. R. Corpas-Martínez, S. Willis, R. Mulholland and J. A. Lopez-Sanchez, Polymers, 2018, 10, 600 CrossRef PubMed.
- Y. Li, H. Cheng, C. Zhang, B. Zhang, T. Liu, Q. Wu, X. Su, W. Lin and F. Zhao, Sci. China: Chem., 2017, 60, 920–926 CrossRef CAS.
- L. Wei, J. Zhang, W. Deng, S. Xie, Q. Zhang and Y. Wang, Chem. Commun., 2019, 55, 8013–8016 RSC.
- H. Shi, L. Zhang, Y. Wu, R. Yu, Y. Peng, Y. Wang, T. Li and W. Yang, Catal. Lett., 2021, 151, 338–343 CrossRef CAS.
- T. R. Boussie, G. M. Diamond, E. Dias and V. Murphy, in Chemicals and Fuels from Bio-Based Building Blocks, John Wiley & Sons, Ltd, 2016, pp. 151–172 Search PubMed.
- Z. Terzopoulou, N. Kasmi, V. Tsanaktsis, N. Doulakas, D. N. Bikiaris, D. S. Achilias and G. Z. Papageorgiou, Materials, 2017, 10, 801 CrossRef PubMed.
- J. G. A. B. Silva, R. C. Santos, E. Rodríguez-Castellón, L. S. G. Teixeira and L. A. M. Pontes, Mol. Catal., 2021, 507, 111567 CrossRef CAS.
- S. Uruş, H. Eskalen, M. Çaylar and M. Akbulut, J. Mol. Struct., 2021, 1237, 130313 CrossRef.
- Y. Fu, L. Ding, M. L. Singleton, H. Idrissi and S. Hermans, Appl. Catal., B, 2021, 288, 119997 CrossRef CAS.
- S. Yamaguchi, S. Fujita, K. Nakajima, S. Yamazoe, J. Yamasaki, T. Mizugaki and T. Mitsudome, Green Chem., 2021, 23, 2010–2016 RSC.
- A. P. Tathod and P. L. Dhepe, Carbohydr. Res., 2021, 505, 108341 CrossRef CAS PubMed.
- N. V. Gromov, T. B. Medvedeva, Y. A. Rodikova, M. N. Timofeeva, V. N. Panchenko, O. P. Taran, I. V. Kozhevnikov and V. N. Parmon, Bioresour. Technol., 2021, 319, 124122 CrossRef CAS PubMed.
- S. Carlier, J. Gripekoven, M. Philippo and S. Hermans, Appl. Catal., B, 2021, 282, 119515 CrossRef CAS.
- X. Liu, X. Liu, N. Li, P. Ma and Y. Zhang, Green Chem., 2021, 23, 1353–1360 RSC.
- F. Mao, S. Chen, Q. Zhang, L. Yang, F. Wan, D. Jiang, M. Xiong, C. Zhang, Y. Liu and Z. Fu, Bull. Chem. Soc. Jpn., 2020, 93, 1026–1035 CrossRef CAS.
- J. J. Musci, M. Montaña, E. Rodríguez-Castellón, I. D. Lick and M. L. Casella, Mol. Catal., 2020, 495, 111150 CrossRef CAS.
- N. V. Gromov, T. B. Medvedeva, O. P. Taran, M. N. Timofeeva, O. Said-Aizpuru, V. N. Panchenko, E. Y. Gerasimov, I. V. Kozhevnikov and V. N. Parmon, Appl. Catal., A, 2020, 595, 117489 CrossRef CAS.
- G. Zhang, T. Chen, Y. Zhang, T. Liu and G. Wang, Catal. Lett., 2020, 150, 2294–2303 CrossRef CAS.
- J. A. Melero, J. Moreno, J. Iglesias, G. Morales, J. L. G. Fierro, R. Sánchez-Vázquez, A. Cubo and B. García, Mol. Catal., 2020, 484, 110802 CrossRef CAS.
- M. Y. Byun, D.-W. Park and M. S. Lee, Catal. Today, 2020, 352, 88–94 CrossRef.
- R. V. Brovko, V. Y. Doluda, O. V. Lefedova, I. A. Tarasyuk, D. V. Filippov and A. R. Latypova, Chem. Chem. Technol., 2020, 63, 51–58 CAS.
- F. Brandi, M. Bäumel, V. Molinari, I. Shekova, I. Lauermann, T. Heil, M. Antonietti and M. Al-Naji, Green Chem., 2020, 22, 2755–2766 RSC.
- Y. Yang, H. Gu, Q. Zhang, H. Li and H. Li, ACS Appl. Mater. Interfaces, 2020, 12, 26101–26112 CrossRef PubMed.
- F.-Z. Azar, M. Á. Lillo-Ródenas and M. C. Román-Martínez, Energies, 2020, 13, 4394 CrossRef CAS.
- G. Zhang, T. Chen, Y. Zhang, T. Liu and G. Wang, New J. Chem., 2020, 44, 15169–15176 RSC.
- J. Zhao, X. Yang, W. Wang, J. Liang, Y. Orooji, C. Dai, X. Fu, Y. Yang, W. Xu and J. Zhu, Catalysts, 2020, 10, 1068 CrossRef CAS.
- Z. Li, Y. Liu, C. Liu, S. Wu and W. Wei, Bioresour. Technol., 2019, 274, 190–197 CrossRef CAS PubMed.
- S. Esposito, B. Silvestri, V. Russo, B. Bonelli, M. Manzoli, F. A. Deorsola, A. Vergara, A. Aronne and M. Di Serio, ACS Catal., 2019, 9, 3426–3436 CrossRef CAS.
- N. Rey-Raap, L. S. Ribeiro, J. J. de Melo Órfão, J. L. Figueiredo and M. F. R. Pereira, Appl. Catal., B, 2019, 256, 117826 CrossRef CAS.
- L. Silvester, F. Ramos, J. Thuriot-Roukos, S. Heyte, M. Araque, S. Paul and R. Wojcieszak, Catal. Today, 2019, 338, 72–80 CrossRef CAS.
- B. García, J. Moreno, J. Iglesias, J. A. Melero and G. Morales, Top. Catal., 2019, 62, 570–578 CrossRef.
- E. Frecha, D. Torres, A. Pueyo, I. Suelves and J. L. Pinilla, Appl. Catal., A, 2019, 585, 117182 CrossRef.
- H. Singh, A. Rai, R. Yadav and A. K. Sinha, Mol. Catal., 2018, 451, 186–191 CrossRef CAS.
- B. Zada, L. Yan and Y. Fu, Sci. China: Chem., 2018, 61, 1167–1174 CrossRef CAS.
- M. Almohalla, I. Rodríguez-Ramos, L. S. Ribeiro, J. J. M. Órfão, M. F. R. Pereira and A. Guerrero-Ruiz, Catal. Today, 2018, 301, 65–71 CrossRef CAS.
- K. Gao, J. Xin, D. Yan, H. Dong, Q. Zhou, X. Lu and S. Zhang, J. Chem. Technol. Biotechnol., 2018, 93, 2617–2624 CrossRef CAS.
- Z. Li, Y. Liu and S. Wu, BioResources, 2018, 13, 1278–1288 CAS.
- M. Supeno, N. Pasaribu and R. Siburian, Orient. J. Chem., 2018, 34, 2819–2825 Search PubMed.
- M. D. Adsuar-García, J. X. Flores-Lasluisa, F. Z. Azar and M. C. Román-Martínez, Catalysts, 2018, 8, 572 CrossRef.
- P. A. Lazaridis, S. A. Karakoulia, C. Teodorescu, N. Apostol, D. Macovei, A. Panteli, A. Delimitis, S. M. Coman, V. I. Parvulescu and K. S. Triantafyllidis, Appl. Catal., B, 2017, 214, 1–14 CrossRef CAS.
- A. Malinovsky, V. Matveeva, E. Sulman, V. Doluda, A. Stepacheva and E. Rebrov, Chem. Eng. Trans., 2017, 61, 613–618 Search PubMed.
- L. S. Ribeiro, J. J. Delgado, J. J. de Melo Órfão and M. F. R. Pereira, Catal. Today, 2017, 279, 244–251 CrossRef CAS.
- L. S. Ribeiro, J. J. de Melo Órfão and M. F. R. Pereira, Bioresour. Technol., 2017, 232, 152–158 CrossRef CAS PubMed.
- L. S. Ribeiro, J. J. Delgado, J. J. Órfão and M. F. R. Pereira, Appl. Catal., B, 2017, 217, 265–274 CrossRef CAS.
- V. G. Matveeva, E. M. Sulman, O. V. Manaenkov, A. E. Filatova, O. V. Kislitza, A. I. Sidorov, V. Y. Doluda, M. G. Sulman and E. V. Rebrov, Catal. Today, 2017, 280, 45–50 CrossRef CAS.
- Q. Dong, Y. Huang, H. Yang, J. Pei, K. Li, M. Yuan, W. Xiao, W. Ni and Z. Hou, Top. Catal., 2017, 60, 666–676 CrossRef CAS.
- A. Romero, A. Nieto-Márquez and E. Alonso, Appl. Catal., A, 2017, 529, 49–59 CrossRef CAS.
- X. Zhang, L. J. Durndell, M. A. Isaacs, C. M. A. Parlett, A. F. Lee and K. Wilson, ACS Catal., 2016, 6, 7409–7417 CrossRef CAS.
- A. A. Dabbawala, D. K. Mishra and J. S. Hwang, Catal. Today, 2016, 265, 163–173 CrossRef CAS.
- A. Romero, E. Alonso, Á. Sastre and A. Nieto-Márquez, Microporous Mesoporous Mater., 2016, 224, 1–8 CrossRef CAS.
- H. Sun, R. Yang, J. Wang, X. Yang, J. Tu, L. Xie, C. Li, Q. Lao and C. Sun, RSC Adv., 2017, 7, 15127–15138 RSC.
- S. Soltzberg, R. M. Goepp Jr and W. Freudenberg, J. Am. Chem. Soc., 1946, 68, 919–921 CrossRef CAS PubMed.
- S. J. Howard and A. J. Alexandra, US Pat., US9090550B2, 2015 Search PubMed.
- M. Yabushita, in A Study on Catalytic Conversion of Non-Food Biomass into Chemicals: Fusion of Chemical Sciences and Engineering, ed. M. Yabushita, Springer, Singapore, 2016, pp. 127–140 Search PubMed.
- J. Yang, X. Li, Y. Cheng, C. Fan, C. Pan, B. Huang, X. Meng, J. Zhang, A. Zheng, X. Ma, L. Guo, R. Luque, W. Zhang and Y. Sun, Green Chem., 2020, 22, 5333–5344 RSC.
- Y. Morita, S. Furusato, A. Takagaki, S. Hayashi, R. Kikuchi and S. T. Oyama, ChemSusChem, 2014, 7, 748–752 CrossRef CAS PubMed.
- Y. Xiu, A. Chen, X. Liu, C. Chen, J. Chen, L. Guo, R. Zhang and Z. Hou, RSC Adv., 2015, 5, 28233–28241 RSC.
- J. Geboers, S. Van de Vyver, K. Carpentier, K. de Blochouse, P. Jacobs and B. Sels, Chem. Commun., 2010, 46, 3577–3579 RSC.
- G. Liang, C. Wu, L. He, J. Ming, H. Cheng, L. Zhuo and F. Zhao, Green Chem., 2011, 13, 839–842 RSC.
- H. Kobayashi, Y. Ito, T. Komanoya, Y. Hosaka, P. L. Dhepe, K. Kasai, K. Hara and A. Fukuoka, Green Chem., 2011, 13, 326–333 RSC.
- R. S. Lanigan and T. A. Yamarik, Int. J. Toxicol., 2002, 21, 93–112 CAS.
- T. Cottrell and J. van Peij, in Emulsifiers in Food Technology, John Wiley & Sons, Ltd, 2014, pp. 271–296 Search PubMed.
- P. Foley, A. K. Pour, E. S. Beach and J. B. Zimmerman, Chem. Soc. Rev., 2012, 41, 1499–1518 RSC.
- C. Márquez-Alvarez, E. Sastre and J. Pérez-Pariente, Top. Catal., 2004, 27, 105–117 CrossRef.
- J. Smidrkal, R. Cervenkova and V. Filip, Eur. J. Lipid Sci. Technol., 2004, 106, 851–855 CrossRef CAS.
- G. J. Stockburger, US Pat.US4297290A, 1981 Search PubMed.
- S. L. Guenic, L. Chaveriat, V. Lequart, N. Joly and P. Martin, J. Surfactants Deterg., 2019, 22, 5–21 CrossRef.
- J. M. H. Ellis, J. J. Lewis, and R. J. Beattie, WO1998004540A1, 1998.
- L. Zarif, J. Greiner and J. G. Riess, J. Fluorine Chem., 1989, 44, 73–85 CrossRef CAS.
- A. Mortensen, F. Aguilar, R. Crebelli, A. D. Domenico, B. Dusemund, M. J. Frutos, P. Galtier, D. Gott, U. Gundert-Remy, J.-C. Leblanc, O. Lindtner, P. Moldeus, P. Mosesso, D. Parent-Massin, A. Oskarsson, I. Stankovic, I. Waalkens-Berendsen, R. A. Woutersen, M. Wright, M. Younes, P. Boon, D. Chrysafidis, R. Gürtler, P. Tobback, A. Altieri, A. M. Rincon and C. Lambré, EFSA J., 2017, 15, e04788 Search PubMed.
- W. L. Kubie, J. L. O'Donnell, H. M. Teeter and J. C. Cowan, J. Am. Oil Chem. Soc., 1963, 40, 105–107 CrossRef CAS.
- X. Li, Y. Su, X. Zhou and X. Mo, Colloids Surf., B, 2009, 69, 221–224 CrossRef CAS PubMed.
- R. Kamel, M. Basha and S. H. Abd El-Alim, J. Liposome Res., 2013, 23, 28–36 CrossRef CAS PubMed.
- E. Gianasi, F. Cociancich, I. F. Uchegbu, A. T. Florence and R. Duncan, Int. J. Pharm., 1997, 148, 139–148 CrossRef CAS.
- J. Varshosaz, A. Pardakhty, V. Hajhashemi and A. R. Najafabadi, Drug Delivery, 2003, 10, 251–262 CrossRef CAS PubMed.
- J. Varshosaz, A. Pardakhty, S. Mohsen and H. Baharanchi, Drug Delivery, 2005, 12, 75–82 CrossRef CAS PubMed.
- E. J. Nilsson, T. K. Lind, D. Scherer, T. Skansberger, K. Mortensen, J. Engblom and V. Kocherbitov, CrystEngComm, 2020, 22, 3840–3853 RSC.
- D. R. Vardon, N. A. Rorrer, D. Salvachúa, A. E. Settle, C. W. Johnson, M. J. Menart, N. S. Cleveland, P. N. Ciesielski, K. X. Steirer, J. R. Dorgan and G. T. Beckham, Green Chem., 2016, 18, 3397–3413 RSC.
- X. Jin, M. Liu, G. Zhang, J. Wang, Q. Xia, Y. Sun, Z. Zhou, W. Zhang, S. Wang, C. H. Lam, J. Shen, C. Yang and R. V. Chaudhari, ACS Sustainable Chem. Eng., 2020, 8, 18732–18754 CrossRef CAS.
- W. Niu, K. M. Draths and J. W. Frost, Biotechnol. Prog., 2002, 18, 201–211 CrossRef CAS PubMed.
- J. Lin, H. Song, X. Shen, B. Wang, S. Xie, W. Deng, D. Wu, Q. Zhang and Y. Wang, Chem. Commun., 2019, 55, 11017–11020 RSC.
- X. Han, L. Geng, Y. Guo, R. Jia, X. Liu, Y. Zhang and Y. Wang, Green Chem., 2016, 18, 1597–1604 RSC.
- S. Hameed, L. Lin, A. Wang and W. Luo, Catalysts, 2020, 10, 120 CrossRef CAS.
- M. J. Gilkey, A. V. Mironenko, D. G. Vlachos and B. Xu, ACS Catal., 2017, 7, 6619–6634 CrossRef CAS.
- S. Ramachandran, P. Fontanille, A. Pandey and C. Larroche, Food Technol. Biotechnol., 2006, 44, 185–195 CAS.
- Y.-M. Mao, J. Food Process. Preserv., 2017, 41, e12742 CrossRef.
- J. Wisniewska, I. Sobczak and M. Ziolek, Chem. Eng. J., 2021, 413, 127548 CrossRef CAS.
- M. H. Ab. Rahim, P. X. Ng, A. S. Haji Saud, M. A. Deraman and G. P. Maniam, Iran. J. Catal., 2021, 11, 23–35 CAS.
- J. Wolska, A. Walkowiak, I. Sobczak, L. Wolski and M. Ziolek, Catal. Today, 2021, 382, 48–60 CrossRef CAS.
- M. C. Ortega-Liebana, J. Bonet-Aleta, J. L. Hueso and J. Santamaria, Catalysts, 2020, 10, 333 CrossRef CAS.
- M. P. Sandu, V. S. Sidelnikov, A. A. Geraskin, A. V. Chernyavskii and I. A. Kurzina, Catalysts, 2020, 10, 271 CrossRef CAS.
- Q. Zhang, X. Xiang, Y. Ge, C. Yang, B. Zhang and K. Deng, J. Catal., 2020, 388, 11–19 CrossRef CAS.
- M. Khawaji, I. Graça, E. Ware and D. Chadwick, Catal. Today, 2021, 365, 257–264 CrossRef CAS.
- G. Moggia, T. Kenis, N. Daems and T. Breugelmans, ChemElectroChem, 2020, 7, 86–95 CrossRef CAS.
- Q. Zhang, Y. Ge, C. Yang, B. Zhang and K. Deng, Green Chem., 2019, 21, 5019–5029 RSC.
- Y. Zhuge, G. Fan, Y. Lin, L. Yang and F. Li, Dalton Trans., 2019, 48, 9161–9172 RSC.
- X. Zhang, H. Shi, Q. Chi, X. Liu and L. Chen, Polym. Bull., 2020, 77, 1003–1014 CrossRef CAS.
- H. Zhang, N. Li, X. Pan, S. Wu and J. Xie, ACS Sustainable Chem. Eng., 2017, 5, 4066–4072 CrossRef CAS.
- F. Liu, Z. Xue, X. Zhao, H. Mou, J. He and T. Mu, Chem. Commun., 2018, 54, 6140–6143 RSC.
- P. N. Amaniampong, Q. T. Trinh, K. Li, S. H. Mushrif, Y. Hao and Y. Yang, Catal. Today, 2018, 306, 172–182 CrossRef CAS.
- S. Solmi, C. Morreale, F. Ospitali, S. Agnoli and F. Cavani, ChemCatChem, 2017, 9, 2797–2806 CrossRef CAS.
- E. Derrien, M. Mounguengui-Diallo, N. Perret, P. Marion, C. Pinel and M. Besson, Ind. Eng. Chem. Res., 2017, 56, 13175–13189 CrossRef CAS.
- W.-J. Liu, Z. Xu, D. Zhao, X.-Q. Pan, H.-C. Li, X. Hu, Z.-Y. Fan, W.-K. Wang, G.-H. Zhao, S. Jin, G. W. Huber and H.-Q. Yu, Nat. Commun., 2020, 11, 265 CrossRef CAS PubMed.
- P. N. Amaniampong, A. Karam, Q. T. Trinh, K. Xu, H. Hirao, F. Jérôme and G. Chatel, Sci. Rep., 2017, 7, 40650 CrossRef PubMed.
- K. Khallouk, A. Solhy, N. Idrissi, V. Flaud, A. Kherbeche and A. Barakat, Chem. Eng. J., 2020, 385, 123914 CrossRef CAS.
- J. Iglesias, I. Martínez-Salazar, P. Maireles-Torres, D. M. Alonso, R. Mariscal and M. L. Granados, Chem. Soc. Rev., 2020, 49, 5704–5771 RSC.
- Q. Zhang, Z. Wan, I. K. M. Yu and D. C. W. Tsang, J. Clean. Prod., 2021, 312, 127745 CrossRef CAS.
- P. Sun, D. H. Yu, Y. Hu, Z. C. Tang, J. J. Xia, H. Li and H. Huang, Korean J. Chem. Eng., 2011, 28, 99–105 CrossRef CAS.
- F. Delbecq, M. R. Khodadadi, D. Rodriguez Padron, R. Varma and C. Len, Mol. Catal., 2020, 482, 110648 CrossRef CAS.
- V. Besse, R. Auvergne, S. Carlotti, G. Boutevin, B. Otazaghine, S. Caillol, J.-P. Pascault and B. Boutevin, React. Funct. Polym., 2013, 73, 588–594 CrossRef CAS.
- S. Chatti, M. Bortolussi, A. Loupy, J. C. Blais, D. Bogdal and M. Majdoub, Eur. Polym. J., 2002, 38, 1851–1861 CrossRef CAS.
- S. Yum, H. Kim and Y. Seo, Polymer, 2019, 179, 121685 CrossRef CAS.
- I. Bonnin, R. Mereau, T. Tassaing and K. D. O. Vigier, Beilstein J. Org. Chem., 2020, 16, 1713–1721 CrossRef CAS PubMed.
- J. Keskiväli, S. Rautiainen, M. Heikkilä, T. T. Myllymäki, J.-P. Karjalainen, K. Lagerblom, M. Kemell, M. Vehkamäki, K. Meinander and T. Repo, Green Chem., 2017, 19, 4563–4570 RSC.
- B. Op de Beeck, J. Geboers, S. Van de Vyver, J. Van Lishout, J. Snelders, W. J. J. Huijgen, C. M. Courtin, P. A. Jacobs and B. F. Sels, ChemSusChem, 2013, 6, 199–208 CrossRef CAS PubMed.
- P. Sun, X. Long, H. He, C. Xia and F. Li, ChemSusChem, 2013, 6, 2190–2197 CrossRef CAS PubMed.
- J. Xi, Y. Zhang, D. Ding, Q. Xia, J. Wang, X. Liu, G. Lu and Y. Wang, Appl. Catal., A, 2014, 469, 108–115 CrossRef CAS.
- A. Yamaguchi, O. Sato, N. Mimura and M. Shirai, Catal. Commun., 2015, 67, 59–63 CrossRef CAS.
- A. Yamaguchi, N. Mimura, M. Shirai and O. Sato, J. Jpn. Pet. Inst., 2016, 59, 155–159 CrossRef CAS.
- P. Barbaro, F. Liguori and C. Moreno-Marrodan, Green Chem., 2016, 18, 2935–2940 RSC.
- Y. Yang, W. Zhang, F. Yang, B. Zhou, D. Zeng, N. Zhang, G. Zhao, S. Hao and X. Zhang, Nanoscale, 2018, 10, 2199–2206 RSC.
- M. He, J. Guo, X. Wang, Y. Song, S. Liu, H. Wang and C. Li, New J. Chem., 2020, 44, 10292–10299 RSC.
- F. Brandi, I. Khalil, M. Antonietti and M. Al-Naji, ACS Sustainable Chem. Eng., 2021, 9, 927–935 CrossRef CAS.
- R. M. de Almeida, J. Li, C. Nederlof, P. O’Connor, M. Makkee and J. A. Moulijn, ChemSusChem, 2010, 3, 325–328 CrossRef PubMed.
- O. Gómez-de-Miranda-Jiménez-de-Aberasturi, A. Centeno-Pedrazo, S. Prieto Fernández, R. Rodriguez Alonso, S. Medel, J. María Cuevas, L. G. Monsegue, S. De Wildeman, E. Benedetti, D. Klein, H. Henneken and J. R. Ochoa-Gómez, Green Chem. Lett. Rev., 2021, 14, 534–544 CrossRef.
- J. Hong, D. Radojčić, M. Ionescu, Z. S. Petrović and E. Eastwood, Polym. Chem., 2014, 5, 5360–5368 RSC.
- A. Caretto, V. Passoni, N. Brenna, M. Sitta, L. Ogliosi, G. Catel, S. Turri and G. Griffini, ACS Sustainable Chem. Eng., 2018, 6, 14125–14134 CrossRef CAS.
- P. Tundo, F. Aricò, G. Gauthier, L. Rossi, A. E. Rosamilia, H. S. Bevinakatti, R. L. Sievert and C. P. Newman, ChemSusChem, 2010, 3, 566–570 CrossRef CAS PubMed.
- M. Annatelli, D. D. Torre, M. Musolino and F. Aricò, Catal. Sci. Technol., 2021, 11, 3411–3421 RSC.
- F. Russo, F. Galiano, F. Pedace, F. Aricò and A. Figoli, ACS Sustainable Chem. Eng., 2020, 8, 659–668 CrossRef CAS.
- K. L. Wilson, J. Murray, H. F. Sneddon, C. Jamieson and A. J. B. Watson, Synlett, 2018, 29, 2293–2297 CrossRef CAS.
- M. Durand, Y. Zhu, V. Molinier, T. Féron and J.-M. Aubry, J. Surfactants Deterg., 2009, 12, 371–378 CrossRef CAS.
- D. J. Saxon, M. Nasiri, M. Mandal, S. Maduskar, P. J. Dauenhauer, C. J. Cramer, A. M. LaPointe and T. M. Reineke, J. Am. Chem. Soc., 2019, 141, 5107–5111 CrossRef CAS PubMed.
- A. Roy and H. P. S. Chawla, Enzyme Microb. Technol., 2001, 29, 490–493 CrossRef CAS.
- K. Schönafinger, European Pat. EP0070401A2, 1983.
- A. Inayat, A. van Assche, J. H. Clark and T. J. Farmer, Sustainable Chem. Pharm., 2018, 7, 41–49 CrossRef.
- J. M. Fraile and C. J. Saavedra, ChemistrySelect, 2017, 2, 1013–1018 CrossRef CAS.
- Z. Li, Q. Hu, S. Kang, J. Li, H. Li and X. Xiong, J. Chem. Res., 2018, 42, 215–218 CrossRef CAS.
- C. Cecutti, Z. Mouloungui and A. Gaset, Bioresour. Technol., 1998, 66, 63–67 CrossRef CAS.
- M. Pera-Titus and F. Shi, ChemSusChem, 2014, 7, 720–722 CrossRef CAS.
- R. Pfützenreuter and M. Rose, ChemCatChem, 2016, 8, 251–255 CrossRef.
- S. Thiyagarajan, L. Gootjes, W. Vogelzang, J. van Haveren, M. Lutz and D. S. van Es, ChemSusChem, 2011, 4, 1823–1829 CrossRef CAS PubMed.
- F. Bahé, L. Grand, E. Cartier, M. Jacolot, S. Moebs-Sanchez, D. Portinha, E. Fleury and F. Popowycz, Eur. J. Org. Chem., 2020, 2020, 599–608 CrossRef.
- F. Fenouillot, A. Rousseau, G. Colomines, R. Saint-Loup and J.-P. Pascault, Prog. Polym. Sci., 2010, 35, 578–622 CrossRef CAS.
- M. van Hasselt, M. Weiss and W. Haase, Curr. Med. Res. Opin., 1984, 9, 107–112 CrossRef CAS PubMed.
- Z. Tan, X. Shang, L. Li, L. Tian, Y. Ma, Y. Peng and L. Gao, Exp. Ther. Med., 2013, 5, 1133–1136 CrossRef CAS.
- R. Seemayer, N. Bar and M. P. Schneider, Tetrahedron: Asymmetry, 1992, 3, 1123–1126 CrossRef CAS.
- S.-G. Zhu, J.-T. Yang, G.-M. Zhang, C.-F. Chen and F.-L. Zhang, Org. Process Res. Dev., 2018, 22, 991–995 CrossRef CAS.
- A. Furst, R. C. Berlo and S. Hooton, Chem. Rev., 1965, 65, 51–68 CrossRef CAS.
- T. Toyokuni, S. Cai and B. Dean, Synthesis, 1992, 1992, 1236–1238 CrossRef.
- K. S. Ravikumar and S. Chandrasekaran, Synthesis, 1994, 1994, 1032–1034 CrossRef.
- C. Brown, R. W. Marston, P. F. Quigley and S. M. Roberts, J. Chem. Soc., Perkin Trans. 1, 2000, 1809–1810 RSC.
- T. Itoch, S. Ishiguro, F. Shimada and K. Ishibashi, US Pat.US4584391A, 1986 Search PubMed.
- C. Hu, S. Bourbigot, T. Delaunay, M. Collinet, S. Marcille and G. Fontaine, Polym. Degrad. Stab., 2019, 164, 9–17 CrossRef CAS.
- Y. G. Daniel and B. A. Howell, Polym. Degrad. Stab., 2017, 140, 25–31 CrossRef CAS.
- B. A. Howell and Y. G. Daniel, in Green Polymer Chemistry: Biobased Materials and Biocatalysis, American Chemical Society, 2015, vol. 1192, pp. 339–367 Search PubMed.
- J. Wu, P. Eduard, L. Jasinska-Walc, A. Rozanski, B. A. J. Noordover, D. S. van Es and C. E. Koning, Macromolecules, 2013, 46, 384–394 CrossRef CAS.
- D. S. van Es, J. Renewable Mater., 2013, 1, 61–72 CrossRef CAS.
- J. Saska, S. Dutta, A. Kindler, S. J. Zuend and M. Mascal, ACS Sustainable Chem. Eng., 2021, 9, 11565–11570 CrossRef CAS.
- J. Gross, K. Tauber, M. Fuchs, N. G. Schmidt, A. Rajagopalan, K. Faber, W. M. F. Fabian, J. Pfeffer, T. Haas and W. Kroutil, Green Chem., 2014, 16, 2117–2121 RSC.
- A. Fawzy, N. E. Guesmi, I. I. Althagafi and B. H. Asghar, Transition Met. Chem., 2017, 3, 229–236 CrossRef.
- U. M. Shapla, M. Solayman, N. Alam, M. I. Khalil and S. H. Gan, Chem. Cent. J., 2018, 12, 35 CrossRef CAS PubMed.
- C. Perez Locas and V. A. Yaylayan, J. Agric. Food Chem., 2008, 56, 6717–6723 CrossRef PubMed.
- B. F. M. Kuster, Starch/Staerke, 1990, 42, 314–321 CrossRef CAS.
- S. Dutta, Biomass Convers. Biorefin., 2021 DOI:10.1007/s13399-021-01924-w.
- P. A. Chithra and S. Darbha, Catal. Commun., 2020, 140, 105998 CrossRef CAS.
- A. Bohre, B. Saha and M. M. Abu-Omar, ChemSusChem, 2015, 8, 4022–4029 CrossRef CAS PubMed.
- S. Chen, C. Ciotonea, K. de O. Vigier, F. Jérôme, R. Wojcieszak, F. Dumeignil, E. Marceau and S. Royer, ChemCatChem, 2020, 12, 2050 CrossRef CAS.
- Q. Li, H. Wang, Z. Tian, Y. Weng, C. Wang, J. Ma, C. Zhu, W. Li, Q. Liu and L. Ma, Catal. Sci. Technol., 2019, 9, 1570–1580 RSC.
- Y. Peng, X. Li, T. Gao, T. Li and W. Yang, Green Chem., 2019, 21, 4169–4177 RSC.
- B. S. Solanki and C. V. Rode, J. Saudi Chem. Soc., 2019, 23, 439–451 CrossRef CAS.
- X. P. Nguyen, A. T. Hoang, A. I. Ölçer, D. Engel, V. V. Pham and S. K. Nayak, Fuel Process. Technol., 2021, 214, 106687 CrossRef CAS.
- L. T. Mika, E. Cséfalvay and Á. Németh, Chem. Rev., 2018, 118, 505–613 CrossRef CAS PubMed.
- A. Pellis, F. P. Byrne, J. Sherwood, M. Vastano, J. W. Comerford and T. J. Farmer, Green Chem., 2019, 21, 1686–1694 RSC.
- W. Guo, H. Liu, S. Zhang, H. Han, H. Liu, T. Jiang, B. Han and T. Wu, Green Chem., 2016, 18, 6222–6228 RSC.
- D. K. Mishra, H. J. Lee, C. C. Truong, J. Kim, Y.-W. Suh, J. Baek and Y. J. Kim, Mol. Catal., 2020, 484, 110722 CrossRef CAS.
- K. Vikanova, E. Redina, G. Kapustin, M. Chernova, O. Tkachenko, V. Nissenbaum and L. Kustov, ACS Sustainable Chem. Eng., 2021, 9, 1161–1171 CrossRef CAS.
- S. Liu, M. Tamura, Y. Nakagawa and K. Tomishige, ACS Sustainable Chem. Eng., 2014, 2, 1819–1827 CrossRef CAS.
- J. Dai, Green Energy Environ., 2021, 6, 22–32 CrossRef.
- A. F. Sousa, C. Vilela, A. C. Fonseca, M. Matos, C. S. R. Freire, G.-J. M. Gruter, J. F. J. Coelho and A. J. D. Silvestre, Polym. Chem., 2015, 6, 5961–5983 RSC.
- M. Sajid, X. Zhao and D. Liu, Green Chem., 2018, 20, 5427–5453 RSC.
- H. N. Anchan and S. Dutta, Biomass Convers. Biorefin., 2021 DOI:10.1007/s13399-021-01315-1.
- Y. Li, G. Lv, Y. Wang, T. Deng, Y. Wang, X. Hou and Y. Yang, ChemistrySelect, 2016, 1, 1252–1255 CrossRef CAS.
- Y. Liu, G. Li, Y. Hu, A. Wang, F. Lu, J.-J. Zou, Y. Cong, N. Li and T. Zhang, Joule, 2019, 3, 1028–1036 CrossRef CAS.
- S. Alipour, H. Omidvarborna and D.-S. Kim, Renewable Sustainable Energy Rev., 2017, 71, 908–926 CrossRef CAS.
- S. Shinde, K. Deval, R. Chikate and C. Rode, ChemistrySelect, 2018, 3, 8770–8778 CrossRef CAS.
- J. Ohyama, R. Kanao, A. Esaki and A. Satsuma, Chem. Commun., 2014, 50, 5633–5636 RSC.
- S. Chen, R. Wojcieszak, F. Dumeignil, E. Marceau and S. Royer, Chem. Rev., 2018, 118, 11023–11117 CrossRef CAS PubMed.
- J. N. M. Soetedjo, H. H. van de Bovenkamp, P. J. Deuss and H. J. Heeres, ACS Sustainable Chem. Eng., 2017, 5, 3993–4001 CrossRef CAS PubMed.
|
This journal is © The Royal Society of Chemistry 2022 |
Click here to see how this site uses Cookies. View our privacy policy here.