DOI:
10.1039/D2RA03406A
(Paper)
RSC Adv., 2022,
12, 21223-21234
Non-edible plant seeds of Acacia farnesiana as a new and effective source for biofuel production†
Received
1st June 2022
, Accepted 5th July 2022
First published on 2nd August 2022
Abstract
Currently, the energy crisis is a hot topic for researchers because we are facing serious problems due to overpopulation and natural energy sources are vanishing day-by-day. To overcome the energy crisis, biofuel production from non-edible plant seeds is the best solution for the present era. In the present study, we select the non-edible seeds of Acacia farnesiana for biofuel production from different areas of Pakistan with better oil production results. Different kinds of analytical method, like the American Standard for Testing and Materials and techniques like Fourier transform infra-red spectroscopy, nuclear magnetic resonance spectroscopy, gas chromatography, and inductively coupled plasma optical emission spectrometry, were used to evaluate the chemical compositions. The maximum oil extraction rate (23%) was produced by petroleum ether. Potassium hydroxide exhibited the best conversion result of 96% fatty acid methyl ester. The transesterification method was used for the preparation of fatty acid methyl ester (96%) using potassium hydroxide and methanol. The viscosity and density of Acacia farnesiana seed oil biodiesel was comparable to American Standard for Testing Material biodiesel standards. By using gas chromatography-mass spectrometry, five fatty acids were detected comprising palmitic acid (6.85%), stearic acid (2.36%), oleic acid (12.13%), linoleic acid (46.85%), and α-linolenic acid (1.23%). This study concludes that Acacia farnesiana seed oil biodiesel could be an intriguing raw material for yielding Acacia farnesiana seed oil methyl ester as an alternative fuel source.
1. Introduction
As a result of the fast decay of fossil fuels due to the rapid growth in population, the clean energy demand is increasing day-by-day.1 For such type of energy, it is essential to develop alternate clean and renewable energy sources.2 Energy plays a crucial role in all features of our community and economic life due to being a vibrant part in the existence and safety of the entire world. Other sources of energy are vanishing so fast that we need alternate sources of energy.2,3 Among all of the energy sources, biodiesel (BD) is the most economic and clean source of energy.1,4 The feedstock has the most vital and fundamental importance for biodiesel enhancement. Biomass is resultant from the reaction of carbon dioxide (CO2) and water (H2O) using sunlight. This reaction is responsible for carbohydrate production through photosynthesis and converts solar energy into useful chemical energy.5,6 A biomass of about 170 billion tons is produced on the earth every year. Biomass is appraised as a key source of useful energy for human beings. It is currently estimated to account for about 10 to 14% of the energy supply of the entire world. Less developed areas account for more than 60%, and more than 2.5 billion people are using 90% energy coming from biomass energy.5 Being easily combustible, less pollution causing, and low in the content of ash are the key advantages of bio-energy.7 The disadvantages are low calorific rate and less thermal efficiency, and being large in volume and difficult to transport. The thermal efficacy for combustion reactions of biomass is only 10 to 15%. Biomass energy can be effectively used through energy conversion technology;5 for example, through chemical means which convert biomass into liquid and gaseous fuels as biodiesel.6–8 Recently, the survey and growth of valued energy-based plant seeds as a source of biodiesel has become a hot topic for researchers. Amongst these substitute foundations, vegetable oils have gained substantial consideration because they can be obtained from renewable sources and produced internally, and are not as detrimental to the environment as petrol.9 There is a severe shortage of fuel in several emerging countries, so the energy disaster has become the day-to-day reality of most households.10 Raw materials from commercial sources come from palm, sunflower, coconut, rapeseed, soybean, flaxseed, etc.11
BD contains alkyl esters of long-chain fatty acids12 and the oxygen content of BD is more than that of petroleum diesel, which make BD more prominent over petroleum diesel.13 BD is a recyclable, non-poisonous, decomposable, and environmentally friendly fuel.14,15 The high amount of Erucic acid makes the oil unsuitable for human consumption16,17 but it leads to high stability and low melting point.18 Recently, the production of biofuel from plant oils has been a hot topic.19 Biodiesel is mainly synthesized via transesterification reaction, which is a modest and operative production method for biofuel.20,21
Edible oil is the main source of biodiesel, and there is less research on the yield of BD from inedible and low-cost oil.22 The high cost of biodiesel is the main obstacle to its commercialization. In order to regulate this condition, it is vital to discover resources of non-edible oil, which can prove to be economical and can solve food complications.22,23 It makes sense to develop substitute bases of renewable oil, which not only advance the commercial feasibility of biodiesel but also upsurge the probable amount of such fuels. The main obstacle to commercializing biodiesel is its high cost.24,25 According to researchers, 85–95% is the cost of the raw material, which plays an essential role in the cost of the biodiesel.26 Consequently, there is a need to obtain biodiesel from lower charge fossil resources, such as inedible oils. Using non-edible raw materials can easily produce biodiesel27,28 while gaining multiple benefits, such as higher energy security, diversification of energy and agriculture, and accelerated development of rural areas, thereby increasing employment opportunities. Therefore, the growth of mainly inedible oil-bearing plants and the production of biofuels can promote the use of cultivated land by increasing the value of marginal land and limiting competition with food crops.29,30 Beside, most non-edible oil seeds can be cultivated under dry conditions and can withstand resource-scarce circumstances without concentrated care.31 As a result, inedible oil crops can be created, such as Jatropha curcas, Pongamia pinnata, Madhuca indica, soapnut seeds (Sapindus mukorossi), cotton seeds (Gossypium), terebinth (Pistacia terebinthus), rubber seeds oil, honne oil, rice bran oil, palm oil, etc., that can be planted on a large area in non-planted wasteland. In general, the effects of numerous manipulated variables on transesterification reactions have been studied, and the fuel characteristics of biodiesel formed from inedible oils have been resolute.32 They are suitable sources for the production of biodiesel. However, there are additional inedible oils that have not been considered as raw resources for biodiesel manufacturing. So far, Acacia farnesiana oil (AFO) is one of them.
In this study, Acacia farnesiana (AF) is chosen as the non-edible raw material for the production of biodiesel. To study the optimal reaction parameters for the manufacture of FAMEs from raw AF seed oil, the best optimization conditions were obtained, including an oil to methanol molar ratio of 6
:
1, KOH (catalyst) amount of 3.0 wt%, temperature of 65 °C, stirring speed of around 700 rpm, and reaction duration of 60 minutes. The different kinds of physico-chemical properties and configurations of FAMEs were studied. The biodiesel quality was associated with the BD100 standard and acceptable. The different parameters, like kinematic viscosity, density, pour point, cloud point, flashpoint, ignition point, refractive index, cetane number, oxidation stability, saponification value, iodine value, acid value, specific gravity, ash content, and cold filter point of biodiesel products, have reached the quality of biodiesel. It was found that the value of the fuel characteristics was comparable to that of mineral diesel.
2. Materials and methods
2.1. Materials
AF seeds were gathered from three different places in Pakistan, F.R Lakki Marwat (20%), Dera Ismail Khan (18.2%), and Karak (23.1%). To remove the dust and dirt, the seeds were washed with pure water. In the next step, the seeds were dried in an oven for 24 hours at 60 °C, ground and packed in a plastic tube, and then frozen at −20 °C in a common lab fridge and stored until further analysis. The oil was extracted by using a Soxhlet extractor (FANGTAI SHIBAYOUFANG FL-S2017, China) employing solvent and an electric oil presser (FANGTAI SHIBAYOUFANG J508, China). Methanol (purity 99.9%), KOH, and Na2SO4 were purchased from Merck (Germany) and used without further purification throughout the experiments.
2.2. Preparation of feedstock
The dried AF seeds were ground in a heavy mill (XIANTAOPAI XTP-10000A, China) to pass through a 40 mesh screen. The seed oil extraction process was in a Soxhlet extractor using five different solvents (n-hexane, petroleum ether, dichloromethane, acetone, and ethyl acetate at 60–110 °C) for 8 h. After removing impurities and solid particles by filtration, the oil and solvent were separated by a rotary evaporator.
2.3. Reagents and chemicals
Methanol of analytical grade, phosphoric acid (H3PO4), sulphuric acid (H2SO4), potassium hydroxide (KOH), sodium hydroxide (NaOH), potassium methoxide (CH3OK), sodium methoxide (CH3OK), sodium sulphate (Na2SO4), calcium oxide (CaO), calcium chloride (CaCl2), and zirconium dioxide (ZrO2) were obtained from Aladdin, Sigma and Sinopharm Ltd China. The chemicals are analytically pure (99.98%) and can be used without additional purification.
2.4. Oil extraction
A sample of 20 g of seed powder was extracted using a Soxhlet extractor, and a large amount of seed oil was extracted by implementation of a mechanical extractor (Table S1, ESI†). The dried AF seed powder was placed in a Soxhlet extractor, and for the extraction of oil, various solvents were used. For the removal of the solvent, refluxing conditions were used for 8 hours at 70 °C temperature via a rotary evaporator (TOKYO RIKAKIKAI Co. Ltd N-1210B). After the removal of the solvent, the sample was placed in a desiccator and dried thoroughly to a constant weight. Based on the ratio of the mass of oil obtained to the crushed seeds mass, the oil content in A. farnesiana seeds can be calculated by a previously reported method.33 A huge quantity of oil was extracted from the AF seeds by implementation of mechanical pressing. This process is given in S2 (ESI†).
2.5. Transesterification of oil
The transesterification reaction was performed in a 250 mL flask with constant stirring connected with a reflux condenser and thermometer. For the production of biodiesel, 15–17 g of oil was heated up to 50 °C in an oil and methanol mixture (6
:
1 ratio) using KOH (3.0 wt%) as a catalyst. The mixture was allowed to react for one hour, which is the basic transesterification reaction condition. Scheme 1 shows the basic transesterification reaction of the present work. After standing for 24 hours, separation occurred in the funnel, and the upper layer (biodiesel) was used for analysis, while the second lower layer (glycerine) was discarded. The residual catalyst containing methanol and soap is removed by continuous rinsing with distilled water until the mixture becomes pure. Anhydrous sodium sulphate was used to dry the washed over biodiesel, and then it was filtered under concentrated compression. The transesterification reaction was performed as already reported with slight modification.34
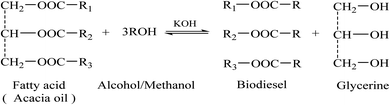 |
| Scheme 1 The transesterification reaction of AF biodiesel. | |
2.6. Biodiesel production
Biodiesel production catalyzed by KOH is also carried out in microwave reactors. After optimization, the reaction conditions of biodiesel were as follows: the reaction temperature was 65 °C for 60 minutes, the oil/methanol molar ratio was 6
:
1, and the KOH (catalyst) amount was 3.0 wt% by weight.34 Also, through GC-MS, the biodiesel chemical composition was analyzed.
2.7. FAMEs cleansing
After separating the two layers, the upper part of the biodiesel was cleaned by fractionation at 60 °C of the remaining methanol. By addition of 1–2 drops of pure acetic acid, the respective catalyst was neutralized, and by continuous washing, using purified water, the remaining catalyst was detached. Furthermore, by handling with anhydrous sodium sulfate (Na2SO4), the remaining water was removed and then filtered.
2.8. Property evaluation of the biodiesel product
The key physiochemical features of AF FAMEs were evaluated by using the Standard technique under ASTM D-6751 (American Standard for Testing and Materials) and EN (European Norm).
2.9. Analytical methods
Through the ASTM method, the synthesized AF FAME properties were determined. Various analytical techniques have been applied to the process of identifying and monitoring FAMEs. An FTIR Bruker Vertex 70 FT-IR spectrometer (Germany) was used to characterize the A. farnesiana oil biodiesel in the range of 4000–400 cm−1. The perseverance was 1 cm−1 and 15 scans were performed.
NMR analysis was executed using a Bruker Avance III 400 NMR spectrometer (Germany) equipped with a 5 mm BBO probe of 7.05T, deuterated chloroform (CDCl3) as a solvent, and tetramethylsilane (TMS) as an internal standard.35 The recorded 13C (75 MHz) spectrum has a pulse interval of 30°, a cyclic delay of 1.89 s, and a scan count of 160 times. The 1H NMR (300 MHz) spectra were recorded with 1.0 s of cyclic delay, 8 times of multiple scans, and 30° of pulse duration.
The FAME composition of the A. farnesiana oil biodiesel was evaluated by gas chromatography (QP2010SE, SHIMADZU, Japan). The detailed procedure is given in Tables 1 and S3 (ESI†).
Table 1 Conditions for gas chromatography34
Parameter |
Descriptions |
Column |
QP2010SE, Shimadzu |
PEG-20M |
Length: 30 m |
Internal diameter: 0.32 mm |
Film thickness: 1 μm |
Injector temperature |
220 °C |
Detector temperature (EI 250) |
210 °C |
Carrier gas |
Helium, flow rate = 1.2 mL min−1 |
Injection |
V = 1 μL |
Split ratio |
Flow rate = 40 : 1 |
Temperature program |
Initial temperature = 100 °C |
Rate of progression = 10 °C min−1 |
Final temperature = 210 °C, 20 min |
2.10. Elemental analysis
The element concentrations (Na, K, Ca, Mg) in the biodiesel were determined by inductively coupled plasma optical emission spectrometry (Spectro-blue, Germany). The detailed process is given in S4 (ESI†).
The CHN and oxygen content of the biodiesel was determined by a Vario EL CUBE (Germany) Elemental Analyzer (EA). This procedure is given in S5 (ESI†).
3. Results and discussion
Fig. 1 displays a complete description of the respective plant flowers, seeds, and seed pods. To extract oil from AF seed powder, different types of solvent were used (Table 2).
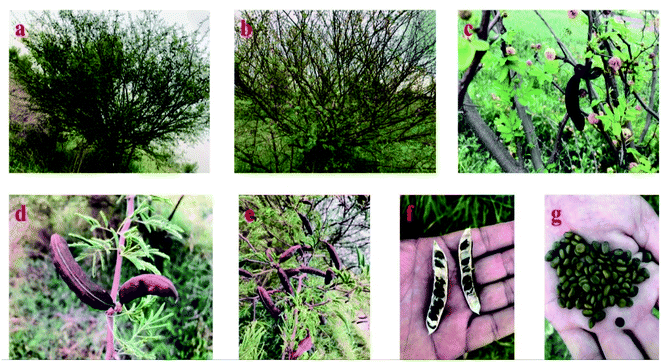 |
| Fig. 1 (a–g) Optical plant photographs (flowers, seedpods, and seeds). | |
Table 2 Solvent effect on FFA and oil content
Solvent |
Oil content in wt% |
FFA content in wt% |
Petroleum ether |
23 |
0.4 |
Hexane |
19.7 |
1 |
Acetone |
17.4 |
1.3 |
Dichloromethane |
15.2 |
1.7 |
Ethyl acetate |
18.8 |
1.5 |
The oil and FFA content obtained vary and appear to be associated with the polarization of the extracted solvent, in the order of petroleum naphtha, acetone, n-hexane, ethyl acetate, and dichloromethane. Large quantities of non-polar oils like triglycerides can be extracted through solvents of less polar nature and small amounts of highly polar FFA, and vice versa. The oil content of the solvent n-hexane is 19.7% by weight (FFA = 1%). The oil content of ethyl acetate is as low as 18.8% by weight (FFA = 1.5%), while the oil contents of more polar solvents (such as acetone and dichloromethane) are slightly lower (17.4–15.2%) (FFA = 1.3–1.7%). According to the extraction results, the use of petroleum ether and its capability to yield AF seed oil make AF a useful alternative energy source for the manufacture of biodiesel.34
In this work on AF crude oil, different catalysts were used to check which catalyst was more productive with the highest conversion rates obtained for FAMEs; see Fig. 2 and Table S2 (ESI†). The optimized KOH conversion rate can reach 96%, the NaOH conversion rate was 93.5%, the CaO conversion rate was 92%, the CH3ONa conversion rate was 91.5%, the CH3OK conversion rate was 91%, and the ZrO2 conversion rate was 90%. KOH provided the best FAME transformation results, so KOH was used throughout the experiment.
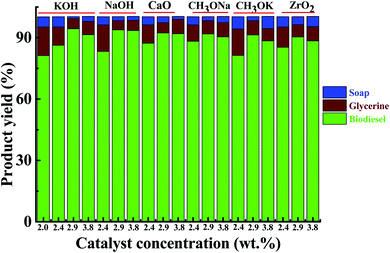 |
| Fig. 2 Catalysts impact on conversion yield. | |
The catalyst effect was determined on the manufacture of Acacia farnesiana Oil Methyl Esters (AFOMEs). Six experiments were performed using different catalysts, namely KOH, NaOH, CH3ONa, CH3OK, CaO, and ZrO2, at a concentration of 2.0–4.0% (w/w). In the above mentioned experiments, the other variables, such as molar ratio of oil to methanol (6
:
1), rate of stirring (700 rpm), and reaction temperature (65 °C), were kept constant. The best product yield of AFOMEs was achieved with the catalyst of KOH, as shown in Fig. 2. From the results, it was confirmed that the hydroxide-based catalysts, like NaOH and KOH, produced higher ester yields than the analogous methoxide catalysts (CH3Ona and CH3OK), indicating that they have a better catalytic effect on transesterification. The present catalytic developments are consistent with some earlier research work on methanolysis of Pongamia pinnata,36 Brassica carinata,37 and rapeseed oil,38 indicating that a KOH catalyst is a much better catalyst as compared to others. In addition, analogous findings to this study were observed for okra oil methyl ester.39 A few researchers, like Martinez, Vicente, and Aracil,40 have published articles reporting that the usage of a sodium methoxide catalyst is highly suitable for oil transesterification. This change in catalyst activity may be attributed to the different nature of the raw vegetable oil and the different concentration of the catalyst, because different investigators used different oil and catalyst concentrations in the experiment.
The experimental results obtained in this work include the oil obtained from the extracted AF seed oil and the methyl ester yield of AF produced by the transesterification reaction with a KOH catalyst; under similar reaction circumstances, using KOH as the catalyst, the production of methyl ester attained by the transesterification reaction of AF oil and the fuel properties of AF oil were compared.
3.1. Properties of AF oil biodiesel
The ASTM technique was used to characterize the AF oil biodiesel, including its cloud point, pour point, flashpoint, acid value, density, kinematic viscosity, and content of sulfur. Table 3 lists several important properties (physical/chemical) as well as fuel characteristics of the optimized AFOMEs/biodiesel manufactured in comparison to renowned biofuel standards ASTM D-6751 and EN 14214. The density of AF oil biodiesel measured at 15 °C was 0.83134 g cm−3, which follows well the required parameters for biodiesel.
Table 3 Physio-chemical characterizations of AFOMEs and their comparison with standards and petrodiesela
Parameters studied |
EN 14214 |
ASTM D-6751 |
Petro-diesel |
Experimental result |
RSOB41 |
AAOB42 |
HMOB43 |
References for comparative analysis: RSOB:41 rubber seed oil biodiesel, AAOB:42 Ailanthus altissima oil biodiesel, and HMOB:43 Hodgsonia macrocarpa oil biodiesel. |
Density @ 15 °C (g cm−3) |
0.86–0.90 |
0.86–0.90 |
0.809 |
0.831 |
— |
0.91 |
0.88 |
Kinematic viscosity@ 40 °C (cps) |
3.5–5.0 |
1.9–6.0 |
1.3–4.1 |
5.32 |
4.5 |
36 |
4.1 |
Flashpoint, (°C) |
Min. 120.0 |
Min. 130 |
60–80 |
158 |
120 |
— |
153 |
Acid value, (mg KOH g−1) |
Max. 0.50 |
Max. 0.5 |
— |
0.40 |
0.12 |
0.64 |
0.35 |
Saponification value (mg KOH g−1) |
— |
— |
— |
174.8 |
— |
— |
— |
Iodine value, (g I2 per 100 mg) |
Max. 120 |
Max. 120 |
— |
142.5 |
— |
132.11 |
— |
Cloud point (°C) |
— |
— |
−15 to 5 |
7 |
3 |
— |
— |
Pour point (°C) |
— |
— |
−2.0 |
−28 |
−5 |
— |
−9 |
Cetane number |
Min. 51 |
Min. 47 |
49.7 |
52 |
— |
— |
51.2 |
Fire point (°C) |
— |
— |
— |
189 |
— |
— |
— |
Oxidation stability (110 °C, h) |
Min. 6 |
Min. 3 |
25.8 |
2.75 |
— |
— |
— |
Ash content |
— |
— |
— |
0.002 |
— |
— |
0.01 |
Specific gravity |
— |
— |
— |
0.83134 |
0.85 |
— |
— |
Free fatty acid (%) |
— |
— |
— |
0.4 |
Cold filter plug point (°C) |
Max. 19 |
Max. 19 |
−16 |
−25 |
— |
— |
— |
The most critical characteristic of biodiesel is the viscosity, because this influences the process of fuel immunization devices, especially at low heats, which distresses the flow of fuel. The poor atomization of the fuel spray occurs due to high viscosity. The kinematic viscosity of A. farnesiana oil biodiesel measured at 40 °C was 5.32 cps, which is in the range of ASTM D6751 for biodiesel and ASTM D975 for petroleum diesel as displayed in Table 3.
Pour point (pp) is the heat rate at which the quantity of wax extracted from the solution is appropriate to achieve fuel. Therefore, at such low limits of temperature, the fuel will flow and the cloud point (cp) is the heat rate; when the fuel is cold, the wax becomes visible on it. AF oil biodiesel has a pp and cp of −28 and 7 °C, respectively, which follows the diesel restrictions quantified in ASTM (Table 3). The handling, storage, and safety of fuels and flammable materials are considered based on the flashpoint parameters. The measured flashpoint (158 °C) of AF oil biodiesel is much higher than that of petroleum diesel ASTM D975, and is equal to the value of ASTM D6751 of biodiesel (Table 3).
The acid value can be measured by the presence of free fatty acids in petroleum and biodiesel. The acid value of oil and biodiesel is determined by the titration of an acid-based solution. In the respective experiment, phenolphthalein indicator was used and the oil of AF was titrated alongside a customary KOH solution. A blank titration was also performed with isopropanol. 1 mL of the sample was titrated. The following formula was used to calculate the acid value.
|
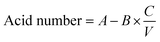 | (1) |
In the above equation, A stands for the used KOH volume in mL for the sample, B is the KOH volume used for the blank, C stands for KOH concentration, and V stands for the sample volume in mL.
The measured value of the acid number of AF oil biodiesel was found to be 0.32 mg KOH g−1 of sample, as shown in Table 3.
3.2. Optimization of the reaction conditions for the transesterification of AF oil
The transesterification method was examined under various parameters to acquire higher yields of biodiesel, like ratio of oil/methanol, amount of catalyst, intensity of agitation, time of reaction, and temperature. The comprehensive optimization procedure is displayed in Fig. 3, and Table S3 (ESI†). The initial yield of FAMEs was only 91.5%, but after optimization, it increased to 96%. We studied five different constraints, applied different conditions to them, and tested each parameter under three different states to confirm that this is the most appropriate condition to obtain the best results. The five configurations are as follows and discussed one by one in Fig. 3.
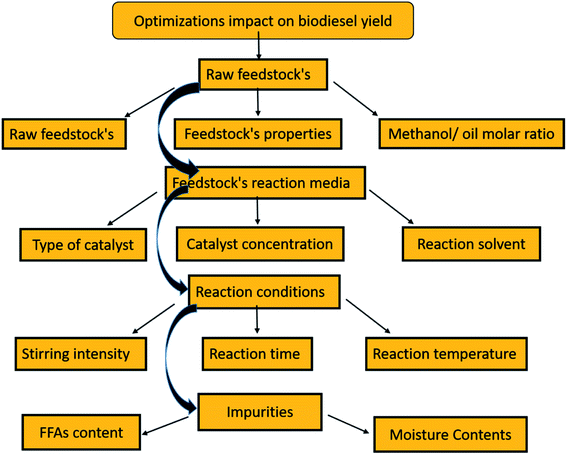 |
| Fig. 3 Transesterification reaction of AF biodiesel. | |
3.3. The effect of oil to methanol ratio on FAME yield
The oil to methanol ratio is the most acute variable that highly affects the FAME performance. The main goal is to adjust different variables for the respective process to maximize the product output and to minimize the formation of soap. The oil to methanol ratio effect (4
:
1, 5
:
1, 6
:
1, and 7
:
1) on the yield of biodiesel is displayed in Fig. 4. It was observed that with the enhancement of the oil to methanol molar ratio from 4
:
1 to 6
:
1, the biodiesel production increased significantly (96%), and additional increases in the molar ratio (7
:
1) resulted in a slight reduction in the production of biodiesel (90%). Besides, separating glycerin from biodiesel is very difficult. Because of high solubility, the higher alcohol molar ratio interferes with the glycerol separation. Therefore, excessive glycerol in the biodiesel phase permits the reaction to proceed backwards and recombination with methyl ester occurs to form monoglycerides.44 The present results illustrate that unnecessary methanol usage has no considerable positive impact on the FAME production. The separation of esters and glycerin is complicated. Generally, acid-catalyzed methods require higher molar ratios than base-catalyzed methods. It can be seen that the primary variables affecting the production of esters are the types of alcohol and triglycerides. Generally, alcohols of short-chain, such as methanol, ethanol, propanol, and butanol, can be used in the transesterification reaction to acquire high ester yield.
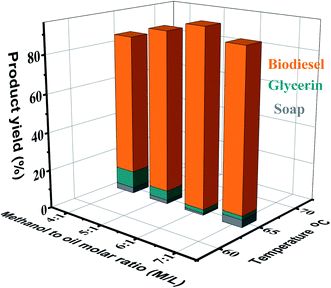 |
| Fig. 4 Effect of molar ratio on the biodiesel yield. | |
A possible explanation of the obtained results is that when the molar ratio of oil to methanol becomes greater than the optimal level (6
:
1), the separation of the ester layer from glycerol becomes difficult. Excessive methanol hampers gravity decantation, resulting in a decrease in the visible AFOME yield, since the glycerol part and other contaminants persist in the phase of biodiesel.45,46 Goff et al.47 have previously reported that a molar ratio greater than 6
:
1 has no significant influence on the production of esters, but an additional amount of methanol will cause problems in ester recovery and increase process costs. A molar ratio of oil to methanol greater than 6
:
1 may indicate a dilution influence, while a molar ratio of less than 6
:
1 will result in inadequate reactant mixing in the two-phase system of the transesterification reaction, which may lead to a decrease in ester yield. Our current research outcomes are consistent with the results of already reported literature.47 It was reported that the best ester yields were obtained by using a molar ratio of about 6
:
1 in tobacco, Pongamia pinnata, and rapeseed oil methanolysis.
3.4. Influence of catalyst concentration on biodiesel yield
Various catalysts have been used for triglyceride transesterification, including alkali-based, acid-based, enzyme-based, and heterogeneous-based catalysts. Basic catalysts like sodium methoxide (NaOMe) and potassium methoxide (KOMe) are highly effective.48 The effectiveness of these catalysts for the transesterification of AF oil was evaluated, and the best catalyst concentration and activity were determined. We applied and used six different catalysts (KOH, NaOH, CaO, OCH3Na, CH3OK, and ZrO2) to check which catalyst is more effective. Based on the maximum/optimal conversion rate (96%), KOH was selected to conduct further research and optimization. In the present study, KOH is the most commonly used catalyst and optimized based on the maximum conversion yield. The screening data of the tested catalysts are shown in Fig. 5. The reaction product is expressed as a percentage of FAME in the reaction. The concentration of the substance is an important parameter in this study. The catalyst (KOH) concentration selected in this study was 2.0, 2.5, 3.0, 3.5, and 4.0 wt% (on the bases of crude oil mass). Throughout the transesterification reaction, the operating conditions for producing biodiesel from AF oil were: reaction temperature (65 °C), reaction time (60 minutes), molar ratio of oil to methanol (6
:
1), and stirring rate (700 rpm). The results show that the best KOH concentration needed for transesterification of AF oil was 3.0 wt% (94%). It was perceived that if the concentration of KOH is reduced under or increased beyond the optimal value, the production of biodiesel will not increase significantly; on the contrary, glycerol and emulsion formation will increase. This formation might be due to the presence of free acid in the respective oil. With the enhancement of the concentration of the catalyst to 4.0 wt%, the methyl ester yield reduced to 91%. The present results are comparable with the literature,49,50 which reports that soap formation in the presence of a huge quantity of used catalyst increases the reactant viscosity, which results in a decrease in the FAME yield. This deterioration is logical since the addition of an extra quantity of alkali-based catalyst leads to emulsion formation through enhancing the viscosity and confuses methyl ester retrieval.51,52 In fact, this confines the glycerine partitioning and, as a result, saponification consumes the base catalyst and decreases the product yield.
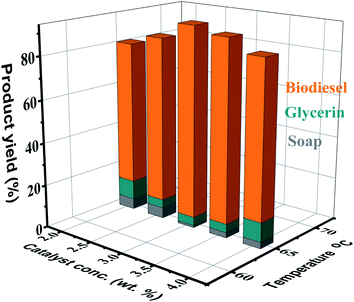 |
| Fig. 5 Effect of catalyst concentration on biodiesel yield. | |
3.5. Effect of reaction temperature on biodiesel production
The reaction rate is highly temperature-dependent. At ambient temperature, the reaction almost completed, but took a long time.48 Generally, the response plateaus at around the methanol boiling point (60–70 °C) and atmospheric pressure.53 Depending on the oil used, the transesterification reaction takes place at different temperatures. In the base-catalyzed transesterification reaction, the researchers maintained a series of steps in the temperature range of 65–75 °C. The methanol boiling point is 64.9 °C. Temperatures above this range will cause alcohol burning, resulting in a decrease in yield. To optimize the transesterification with the refined AF oil to methanol ratio (6
:
1) and 3.0 wt% KOH, the present reaction was monitored at four different temperatures (60, 65, 70, and 75 °C). As displayed in Fig. 6, it was observed that with enhancement of the temperature from 60 °C to 65 °C, the biodiesel production was enhanced. The best product yield (96%) was acquired at 65 °C. According to reports, a further increase in temperature (70 °C and 75 °C) will impair the conversion rate (90% and 85%).54 Temperature affects the reaction rate and ester yield.55
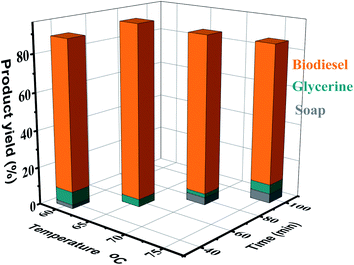 |
| Fig. 6 Effect of temperature on biodiesel yield. | |
3.6. Influence of reaction time on FAME production
The conversion rate of methyl ester is enhanced with increase in the reaction time. The transesterification reaction was studied under the optimal conditions of temperature (65 °C) keeping the timing in the range of 40–100 minutes. Fig. 7 displays the influence of the time factor on the FAME performance, indicating that the fatty acid methyl ester yield is lower (87%) within 40 minutes after the start of the reaction, and the maximum result (95%) is reached within 60 minutes. When the reaction time further increased, the yield decreased slightly to 93% and 90% within 80 minutes and 100 minutes, respectively. This is consistent with the literature data, indicating that due to the transesterification (hydrolysis) reverse reaction, a lengthier reaction time will result in a lower production yield, which usually results in extra fatty acid soap formation.56,57
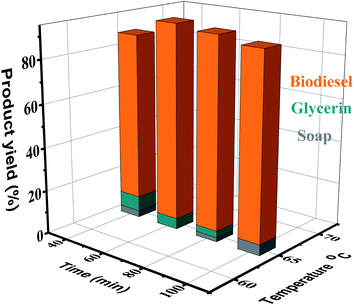 |
| Fig. 7 Effect of time on biodiesel yield. | |
3.7. Influence of agitation rate on FAME yield
For transesterification reactions, the agitation rate is vital because the grease is not very miscible with the KOH in methanol. The reaction can be controlled by dissemination because the weak diffusion between the phases will cause the speed to decrease. Once the two parts are mixed and the response begins, no stirring is required. In four conditions/experiments, the effects of stirring on AFOMEs were studied at different stirring speeds (500 rpm, 600 rpm, 700 rpm, and 800 rpm). In all operations, the molar ratio of oil to methanol was 6
:
1, the reaction temperature was 65 °C, and the (KOH) catalyst concentration was 3.0 wt%. As shown in Fig. 8, the direct relationship between the stirring rate and AFOME production was clarified. That is, as the stirring speed increases, an increase in productivity is observed. Therefore, a 700 rpm mixing speed provides AFOMEs with the best AF oil conversion rate (96%). This is consistent with previous studies,58–60 which indicated that enhancing the stirring speed will highly stimulate the reactant homogenization, resulting in improved yields of methyl esters. A further increase in stirring rate (800 rpm) will negatively affect the conversion yield (88%).
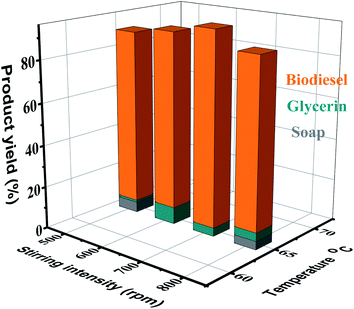 |
| Fig. 8 Stirring intensity effect on biodiesel yield. | |
3.8. FTIR analysis
FT-IR spectroscopy was used to characterize and confirm the biodiesel produced by AFO (Acacia farnesiana oil). Esters have two characteristic absorption bands, which are generated by the stretching of methoxycarbonyl groups and the stretching of CO.61 The methoxycarbonyl group in A. farnesiana oil biodiesel can be observed at 1743 cm−1. The FT-IR spectrum of A. farnesiana oil biodiesel is shown in Fig. 9A and Table S4 (ESI†). The small change in carbonyl frequency is due to the electron-donating effect of the methyl and C
O groups present in biodiesel. FT-IR spectroscopy shows that the characteristic band of fatty acid methyl esters corresponds to asymmetric and symmetric CH3 stretching vibration (–CO–O–CH3) in the range of 3000–2854 cm−1, and the stretching band of the methyl group appears in the region of 2926 cm−1. However, the stretching band of methylene and the asymmetric CH3 deformation vibration appear at 2854 cm−1 and 1434 cm−1, respectively, the bending wave of the methyl group appears at 1434 and 1360 cm−1, and the rocking (bending) of the methylene group appears at 723 cm−1. Due to the presence of the stretching vibration of CO, the biodiesel shows two asymmetric coupling vibrations around 1170 cm−1, ν C–C(
O)–O, and 1016 cm−1, while the peak at 1170 cm−1 corresponds to the CH3 rocking vibration. The peaks around 1244–1015 cm−1 correspond to the C–O ester group stretching vibration. These results reveal the successful transformation of triglycerides to methyl esters.34,62
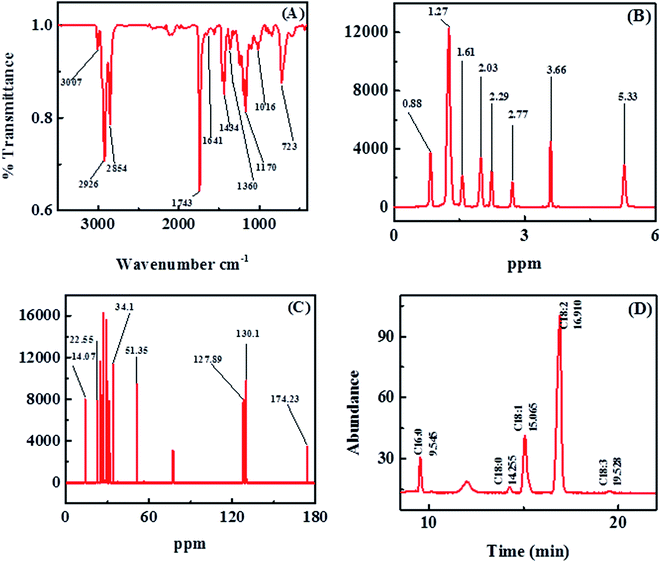 |
| Fig. 9 AFOME FTIR analysis (A), 1H NMR analysis of AFOMEs (B), 13C NMR analysis of AFOMEs (C), and GCMS study of AFOMEs (D). | |
3.9. Analysis of NMR
The 1H and 13C NMR spectra of the AFMEs were also recorded and are shown in Fig. 9B and C, and Tables S5 and S6 (ESI†).
The 1H NMR spectrum (Fig. 9B) was consistent with the range of vegetable oil methyl esters with similar composition, which can be further confirmed by calculating the fatty acid spectrum using the peak integral value.34,62 Therefore, signals were observed at 5.33 (CH CH), 3.66 (COOCH3), 2.77 (CH CH CH2 CH CH), 2.29 (CH3OOC CH2), 2.03 (CH2 CH CH), 1.61 (CH3OOC CH2 CH2), 1.27 (CH2), and 0.88 (CH2 CH3) ppm.
The signals in the 13C NMR spectra (Fig. 9C) were observed at 174.23 (COOCH3), 130.1 and 127.89 (CH CH), 51.35 (COOCH3), 34.1 (various CH2), 22.55 (CH2 CH3), and 14.07 (CH2 CH3) ppm.
3.10. Analysis of gas chromatography and mass spectrometry
The chemical configuration of the prepared AF-based biodiesel was accomplished by GC-MS chromatography. Five main peaks were detected in the GC spectrum of AF oil biodiesel (Fig. 9D). Each peak is identified from library matching software (NIST. 14) and corresponds to a fatty acid methyl ester. The identified FAMEs and their retention times are shown in Table 4. First, the FAMEs were identified by retention time data and then verified by mass spectrometry investigation. The chain length, number, and position of double bonds are also determined by mass spectrometry. Mass spectrometry was performed using an electron collision (EI) ion source.34,63
Table 4 Fatty acid composition (GCMS analysis) of AFOMEs
Fatty acids |
Retention time |
Number of carbons and double bonds |
Fatty acid (weight %) |
Chemical name |
Chemical structure |
Molecular weight |
Palmitic acid |
9.545 |
C16:0 |
6.85 |
Hexadecanoic acid, methyl ester |
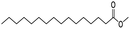 |
270 |
Stearic acid |
14.248 |
C18:0 |
2.36 |
Octadecanoic acid |
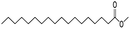 |
298 |
Oleic acid |
15.042 |
C18:1 |
12.13 |
9-Octadecenoic acid (Z)–, methyl ester |
 |
296 |
Linoleic acid |
16.797 |
C18:2 |
46.85 |
9,12-Octadecadienoic acid (Z, Z)–, methyl ester |
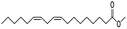 |
294 |
α-Linolenic acid |
19.565 |
C18:3 |
1.23 |
9,12,15-Octadecatrienoic acid |
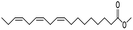 |
278 |
3.11. Elemental analysis
Several elements in biodiesel can cause problems, such as stimulating biodiesel quality, engine performance degradation, operability problems, common complications (such as ecological pollution), and subsequent physical hazards, and thats why they are objectionable.64 The main elements in the product from the biodiesel production mechanism are sodium (Na) and potassium (K), and their presence and concentration need to be controlled so that their content is below the limit of biodiesel. The Na and K maximum reasonable concentration in produced biodiesel is 5 mg kg−1, while that of phosphorus (P) and sulfur (S) is 10 mg kg−1.65 Excessive concentrations of Na and K cause soap formation. Further washing is essential to decrease the sodium and potassium content below the amount specified in the standard. Additional fundamental elements such as calcium (Ca), magnesium (Mg), and phosphorus (P) are present in raw materials used for biodiesel production. Phosphorus (P) comes from the used raw materials in the product, and controlling its quantity in biodiesel is also essential. The element concentration of AF oil biodiesel (AFOBD) was also compared with petroleum diesel, and the results confirmed that the element concentration of AFOBD was relatively lower than that of petroleum diesel. Elements in biodiesel, such as K, Na, Mg, and Ca, are directed to the fuel injection nozzles to promote drainage, wear of pistons and piston rings, and locomotive passing filter plug precipitation.66 Table S7 (ESI†) shows the detailed AFOB element concentration results, and the AFOBD K, Na, Mg, and Ca concentrations are 4.9, 25.2, 1.26, and 10.3 μg g−1, which are lower than the levels of petroleum diesel (213.3, 868.3, 35.6, and 21.4 μg g−1). However, the optimum concentration of S and P in biodiesel is 10 mg kg−1, though for Na and K the maximum amount is 5 mg kg−1 (Fig. 10A). The presence of other kinds of elements like Ca, Mg, and P comes from the raw resources used in biodiesel manufacture. If the Na concentration is high enough, it will help to form soap while reducing the yield of FAMEs. In this case, if the content of the above elements is too high, further cleaning is required to reduce the content below the prescribed standard.
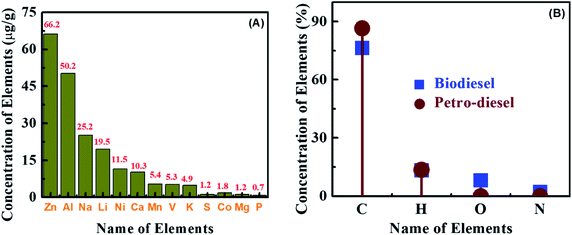 |
| Fig. 10 AFOB FAME ICP-OES study (A) and AFO FAME EA analysis (B). | |
The carbon (C), hydrogen (H), nitrogen (N), and oxygen (O) documented concentrations are declared in Fig. 10B and Table S8 (ESI†). A significant difference between biodiesel and petroleum diesel is the presence of oxygen. Biodiesel mainly contains oxygen, while oxygen is absent in diesel. The presence of oxygen can increase the combustion atmosphere, reduce the ignition delay time, and make the fuel burn more fully, thereby reducing the emissions of carbon monoxide (CO), PM, and other kinds of exhaust gases. Numerous researchers67–69 have established that if the content of oxygen in biodiesel is high, it can efficiently decrease emissions of PM in diesel engines. Fig. 10B shows that the content of oxygen in AF BD100 is 8.11%, but the oxygen content in biodiesel is usually about 10%.70,71 The higher hydrogen content in biodiesel is attractive for its use as a fuel (13.34%).72,73 A high ratio of H/C means that the H2 molecules in the fuel are more advanced because hydrogen has the maximum combustion rate of all fuels (gases or liquids). Enhancing the hydrogen portion of the fuel mixture means that the produced fuel will burn faster and cleaner. Since the hydrogen heating value is higher than that of carbon, the H to C ratio increases, so the heating value usually increases.
4. Conclusions
The present energy crisis all over the world and rapid decay of natural resources have driven research attention towards non-edible seeds to explore new energy resources. Among all the resources, biofuel is the most economic and friendly resource for energy production. The aim of the present work was to produce biofuel from non-edible seeds of Acacia farnesiana with oil content up to 23% and 0.4% lower content of free fatty acids was estimated by Soxhlet extraction. A comprehensive study of AFO was conducted to yield biodiesel. The maximum biodiesel yield transformation of 96% was acquired through the optimized protocol during the alkaline-catalyzed transesterification, keeping the reaction temperature at 65 °C with a molar ratio (methanol to oil) of 6
:
1 and KOH concentration of 2.9 wt% at a mixing rate of 700 rpm and time of 60 minutes. Most features of AFSOME fit well to ASTM D-6751, EN 14214, and high speed diesel; in particular, the viscosity (5.32 mm2 s−1 at 40 °C), flashpoint (158 °C), and Cetane number (52) are excellent. In general, AFSOMEs can be used as a potential substitute for non-edible oil sources for biodiesel production. The fuel properties of AF oil methyl ester are comparable to the recognized biodiesel standard, indicating that the transesterification of the oil improves its performance and makes it similar to petroleum diesel. Since the Pakistan environment and soil are suitable for AF planting, with all of these characteristics in mind, it can be concluded that this method can be used to overcome future energy crises and achieve production on a larger scale. Overall, AF is a potential low-cost and high-quality raw material for biodiesel production in Pakistan and other subtropical regions and will be very helpful for the implementation of such type of non-edible seeds for biofuel production. However, researchers are still facing the problem of implementation.
Conflicts of interest
We wish to confirm that both the authors declare that there are no known conflicts of interest associated with this publication.
References
- M. Munir, M. Ahmad, M. Mubashir, S. Asif, A. Waseem, A. Mukhtar, S. Saqib, H. S. H. Munawaroh, M. K. Lam, K. S. Khoo, A. Bokhari and P. L. Show, Bioresour. Technol., 2021, 328, 1–10 CrossRef PubMed.
- S. Dawood, A. K. Koyande, M. Ahmad, M. Mubashir, S. Asif, J. J. Klemes, A. Bokhari, S. Saqib, M. Lee, M. A. Qyyum and P. L. Show, Chemosphere, 2021, 278, 1–12 CrossRef PubMed.
- S. Bhattacharyya, Heliyon, 2022, 8, 1–7 CrossRef.
- S. Dawood, M. Ahmad, M. Zafar, S. Asif, J. J. Klemes, A. Bokhari d, M. Mubashir, N. Han, M. M. Ibrahim, Z. M. El-Bahy and K. S. Khoo, Chemosphere, 2022, 291, 1–9 CrossRef PubMed.
- A. Srivastava and R. Prasad, Renew. Sustain. Energy Rev., 2000, 4, 111–133 CrossRef CAS.
- Y. C. Sharma, B. Singh and S. N. Upadhyay, Fuel, 2008, 87, 2355–2377 CrossRef CAS.
- Rozina, S. R. Chia, M. Ahmad, S. Sultana, M. Zafar, S. Asif, A. Bokhari, S. Nomanbhay, M. Mubashir, K. S. Khoo and P. L. Show, Fuel, 2022, 323, 1–14 CrossRef.
- P. Vasudevan, S. Sharma and A. Kumar, J. Sci. Ind. Res., 2005, 64, 822–831 CAS.
- M. A. Hazrat, M. G. Rasul, M. M. K. Khan, M. Mofijur, S. F. Ahmed, H. C. Ong, D.-V. N. Vo and P. L. Show, Environ. Chem. Lett., 2021, 19, 2209–2236 CrossRef CAS.
- A. Demirbas, Energy Convers. Manage., 2009, 50, 14–34 CrossRef CAS.
- C. L. Preston and D. L. Reece, Biomass Bioenergy, 2000, 10, 331–336 Search PubMed.
- W. Korbitz, Renewable Energy, 1999, 16, 1078–1083 CrossRef CAS.
- M. Barrios, M. A. Martin, A. F. Chica and A. Martin, Appl. Energy, 2011, 88, 3625–3631 CrossRef.
- T. Murayama, Inform, 1994, 5, 1138–1145 Search PubMed.
- A. Karmakar, S. Karmakar and S. Mukherjee, Bioresour. Technol., 2010, 101, 7201–7210 CrossRef CAS PubMed.
- M. Balat and H. Balat, Appl. Energy, 2010, 87, 1815–1835 CrossRef CAS.
- W. T. Wazilewski, R. A. Bariccatti, G. I. Martins, D. Secco, S. M. N. Souza, H. A. Rosa and L. I. Chaves, Ind. Crop. Prod., 2013, 43, 207–212 CrossRef CAS.
- A. M. Maciel, C. C. Ming, A. P. B. Ribeiro, R. C. Silva, L. A. Gioielli and L. A. G. Gonçalves, J. Am. Oil Chem. Soc., 2014, 91, 111–123 CrossRef.
- J. M. Vargas-Lopez, D. Wiesenborna, K. Tostensona and L. Cihacekc, J. Am. Oil Chem. Soc., 1999, 76, 801–809 CrossRef CAS.
- M. Balat, Energy Convers. Manage., 2011, 52, 1479–1492 CrossRef CAS.
- C. Angelo, L. N. Lilian, J. C. Michelle, M. Núbia, A. Ednildo, A. Wilson, A. Pedro and B. Jailson, J. Braz. Chem. Soc., 2005, 16, 1313–1330 CrossRef.
- G. Vicente, M. Martínez and J. Aracil, Bioresour. Technol., 2007, 98, 1724–1733 CrossRef CAS PubMed.
- A. S. Ramadhas, S. Jayaraj and C. Muraleedharan, Fuel, 2005, 84, 335–340 CrossRef CAS.
- M. J. Haas, K. M. Scott, W. N. Marmer and T. A. Foglia, J. Am. Oil Chem. Soc., 2004, 81, 83–89 CrossRef CAS.
- G. Antolin, F. V. Tinaut, Y. Briceno, V. Castano, C. Perez and A. I. Ramirez, Bioresour. Technol., 2002, 83, 111–114 CrossRef CAS.
- A. Demirbas, Appl. Energy, 2009, 86, S108–S117 CrossRef CAS.
- L. Lin, D. Ying, S. Chaitep and S. Vittayapadung, Appl. Energy, 2009, 86, 681–688 CrossRef CAS.
- J. Connemann and J. Fischer, in Biodiesel in Europe 1998: biodiesel processing technologies, International liquid biofuels congress, Curitiba, Parana, Brazil, 1998 Search PubMed.
- A. Demirbas, Energy Convers. Manage., 2003, 44, 2093–2109 CrossRef CAS.
- A. Demirbas, Energy Convers. Manage., 2007, 49, 125–130 CrossRef.
- J. C. Escobar, E. S. Lora, O. J. Venturini, E. E. Yanez, E. F. Castillo and O. Almazan, Renew. Sustain. Energy Rev., 2009, 13, 1275–1287 CrossRef CAS.
- R. Zah, H. Boni, M. Gauch, R. Hischier, M. Lehmann and P. Wager, Environmentle assessment of biofuel, EMPA, Technology, and Society Lab, 2007 Search PubMed.
- D. Y. C. Leung, X. Wu and M. K. H. Leung, Appl. Energy, 2010, 87, 1083–1095 CrossRef CAS.
- I. U. Khan and A. Haleem, Biomass Bioenergy, 2022, 158, 1–9 CrossRef.
- I. Y. Chindo, W. Danbature and M. Emmanuel, J. Korean Chem. Soc., 2013, 57, 377–381 CrossRef.
- M. Ahmad, S. Ahmad, H. Fayyaz, M. Arshad, M. A. Khan, M. Zafar and S. Sultana, Afr. J. Biotechnol., 2010, 9, 8630–8635 CAS.
- L. C. Meher, S. S. Vidya and S. N. N. Dharmagadda, Bioresour. Technol., 2006, 97(12), 1392–1397 CrossRef CAS PubMed.
- M. P. Dorado, E. Ballesteros, F. J. Lopez and M. Mittelbach, Energy Fuel., 2004, 18(1), 77–83 CrossRef CAS.
- U. Rashid and F. Anwar, Fuel, 2008, 87(3), 265–273 CrossRef CAS.
- F. Anwar, U. Rashid, M. Ashraf and M. Nadeem, Appl. Energy, 2010, 87(3), 779–785 CrossRef CAS.
- G. Vicente, M. Martinez and J. Aracil, Bioresour. Technol., 2004, 92, 297–305 CrossRef CAS PubMed.
- M. Morshed, K. Ferdous, M. K. Khan, M. S. I. Mazumder, M. A. Islam and Md. T. Uddin, Fuel, 2011, 90, 2981–2986 CrossRef CAS.
- S. S. Hoseini, G. Najafi, B. Ghobadian, R. Mamat, M. T. Ebadi and T. Yusaf, Fuel, 2018, 220, 621–630 CrossRef CAS.
- L. Cao and S. Zhang, Appl. Energy, 2015, 146, 135–140 CrossRef CAS.
- J. M. Encinar, J. F. Gonzalez and A. Rodriguez-Reinares, Ind. Eng. Chem. Res., 2005, 44, 5491–5499 CrossRef CAS.
- D. Y. C. Leung and Y. Guo, Fuel Process. Technol., 2006, 87(10), 883–890 CrossRef CAS.
- M. J. Goff, N. S. Bauer, S. Lopes, W. R. Sutterlin and G. J. Suppes, J. Am. Oil Chem. Soc., 2004, 81, 15–420 CrossRef.
- N. Usta, Biomass Bioenergy, 2005, 28, 77–86 CrossRef CAS.
- K. Pramanik, Renewable Energy, 2003, 28, 239–248 CrossRef CAS.
- M. P. Dorado, E. Ballesteros, F. J. Lopez and M. Mittelbach, Energy Fuel., 2004, 18, 77–83 CrossRef CAS.
- J. M. Encinar, J. F. González, E. Sabio and M. J. Ramiro, Ind. Eng. Chem. Res., 1999, 38, 2927–2931 CrossRef CAS.
- F. Ma, L. D. Clements and M. A. Hanna, Trans. Am. Soc. Agric. Eng., 1998, 41(5), 1261–1264 CAS.
- Y. Zhang, M. A. Dube, D. D. Mclean and M. Kates, Bioresour. Technol., 2003, 90(3), 229–240 CrossRef CAS PubMed.
- B. Freedman, E. H. Pryde and T. L. Mounts, J. Am. Oil Chem. Soc., 1984, 61, 1638–1643 CrossRef CAS.
- I. Lee, L. A. Johnson and E. G. Hammond, J. Am. Oil Chem. Soc., 1995, 72, 1155–1160 CrossRef CAS.
- A. S. Ramadhas, S. Jayaraj and C. Muraleedharan, Renewable Energy, 2004, 29, 727–742 CrossRef CAS.
- A. V. Tomasevic and S. S. Siler-Marinkovic, Fuel Process. Technol., 2003, 82, 1–6 CrossRef.
- T. Eevera, K. Rajendran and S. Saradha, Renewable Energy, 2009, 34, 762–765 CrossRef CAS.
- U. Rashid and F. Anwar, Fuel, 2008, 87, 265–273 CrossRef CAS.
- F. Ma, L. D. Clements and M. A. Hanna, Bioresour. Technol., 1999, 69, 289–293 CrossRef CAS.
- C. L. Peterson, D. L. Reece, R. Cruz and J. Thompson, Processing Alternative Energy Conference, ASAE, 1992, pp. 99–110 Search PubMed.
- V. Gupta and A. K. Gupta, J. Sci. Ind. Res., 2004, 63, 39–47 Search PubMed.
- N. P. G. Roeges, A guide to complete interpretation of infrared spectra of organic structures, John Wiley and Sons, Chicester, 1994 Search PubMed.
- G. Knothe and J. A. Kenar, Eur. J. Lipid Sci. Technol., 2004, 106, 88–96 CrossRef CAS.
- A. Bano, A. Mushtaq, T. B. Hadda, A. Saboor, S. Sultana, M. Zafar, M. P. Khan, M. Arshad and M. A. Ashraf, J. Ethnobiol. Ethnomed., 2014, 10, 1–18 CrossRef PubMed.
- S. Schober and M. Mittelbach, Eur. J. Lipid Sci. Technol., 2005, 107, 268–271 CrossRef CAS.
- M. d. G. A. Korn, D. S. S. dos Santos, B. Welz, M. G. R. Vale, A. P. Teixeira, D. d. C. Lima and S. L. C. Ferreira, Talanta, 2007, 73, 1–11 CrossRef CAS PubMed.
- R. L. McCormick, T. L. Alleman, M. Ratcliff, L. Moens and R. Lawrence, Technical report of National Renewable Energy Laboratory, USA, 2005 Search PubMed.
- H. Song, K. S. Quinton, Z. Peng, H. Zhao and N. Ladommatos, Energies, 2016, 9, 28 CrossRef.
- J. K. Mwang, W. J. Lee, Y. C. Chang, C. Y. Chen and L. C. Wang, Appl. Energy, 2015, 159, 214–236 CrossRef.
- D. Singh, K. A. Subramanian, M. Juneja, K. Singh and S. Singh, Environ. Prog. Sustain. Energy, 2017, 36, 214–221 CrossRef CAS.
- A. Demirbas, Energy Sources, Part A, 2009, 31, 602–609 CrossRef CAS.
- G. W. Huber, S. Iborra and A. Corma, Synthesis of transportation fuels from biomass: chemistry, catalysts, and engineering, Chem. Rev., 2006, 106, 4044–4098 CrossRef CAS PubMed.
|
This journal is © The Royal Society of Chemistry 2022 |
Click here to see how this site uses Cookies. View our privacy policy here.