Soluble and reusable polymer-based catalysts with Brønsted and Lewis acidity for the one-pot synthesis of hydroxymethylfurfural from glucose†
Received
16th September 2022
, Accepted 18th November 2022
First published on 25th November 2022
Abstract
Hydroxymethylfurfural (HMF) is an interesting renewable platform molecule due to the number of products that can be obtained from it. Various catalytic systems have been used to produce HMF from glucose; however, challenges, such as the lack of recovery and reutilization and/or low catalytic activity, have been encountered. This article reports a series of novel polystyrene sulfonic acid (PSSA)-based catalysts with both Brønsted and Lewis acid sites for the one-pot synthesis of HMF from glucose. These catalysts combine the advantages of both homogeneous and heterogeneous catalysts, as they are soluble in water (highly active) and recoverable by ultrafiltration for further use. Due to the presence of Brønsted and Lewis acid sites, these catalysts have the ability to perform both the isomerization of glucose to fructose and the dehydration of fructose to HMF. The interplay between Brønsted and Lewis acid sites was investigated by synthesizing a series of PSSA–AlCl3 catalysts with different Brønsted
:
Lewis acid ratios. A maximum HMF yield of ∼55 mol% was obtained with the PSSA–AlCl3 catalyst with H+/Al mole ratio = 4 after 4 h of reaction, and this was recycled and reused up to five times without significant loss of activity. Remarkably, this catalyst was effective in the valorization of highly concentrated solutions of glucose in water (up to 16.7 wt%). A techno-economic analysis estimated that the minimum fuel selling price (MFSP) of this HMF would be $1.94 per kg at a feed price of $0.30 per kg glucose. This MFSP could be further reduced by improving the HMF yield, minimizing the volume of solvent used, or using a lower-cost feedstock.
Introduction
Due to the uncertainty in the continuous availability of petroleum and the environmental challenges associated with its use, recent research efforts have been geared towards the search for other alternative energy sources.1–3 Lignocellulosic biomass is a sustainable substitute because it is renewable and widely available. Among the different biomass valorization routes, the conversion of the sugar fraction into valuable products like hydroxymethylfurfural (HMF) has recently gained a lot of attention.4 In fact, the United States Department of Energy (DOE) listed HMF as one of the top 10 platform chemicals due to the myriad of products obtained from it.5–11 For instance, the complete oxidation of HMF produces 2,5-furandicarboxylic acid (FDCA) that can be converted to polyethylene furanoate (PEF), which is similar to polyethylene terephthalate (PET) but with improved barrier properties.12 Another example of an HMF-derived chemical is adipic acid, which is used to produce nylon.
HMF can be produced by the acid-catalyzed dehydration of simple sugars like glucose and fructose. The production from fructose is easier because, in solution, about 21.5% of fructose exists as a furanose tautomer with a structure similar to HMF, which results in high HMF selectivity.13–15 Nevertheless, the production from glucose is preferable because it is the most abundant monosaccharide and has a lower cost.16–20 To do so, it is necessary to isomerize glucose to fructose using a Lewis acid catalyst, followed by the dehydration of fructose to HMF with a Brønsted acid catalyst (Fig. 1).
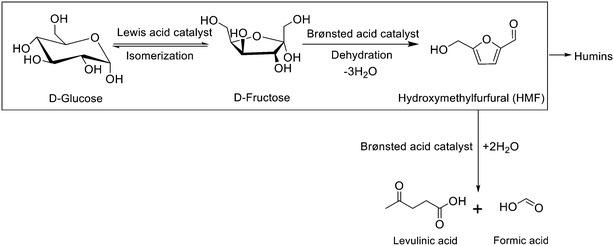 |
| Fig. 1 One-pot synthesis of HMF from glucose. | |
Different combinations of homogeneous Brønsted and Lewis acid catalysts have been used to produce HMF from glucose. For instance, mineral acids (e.g., H2SO4, HCl), mineral salts (e.g., AlCl3, CrCl2), and ionic liquids ([EMIM] Cl) are some of the homogeneous catalysts reported in the literature.21–30 However, their difficult separation and reutilization, as well as the high cost of ionic liquids, are some of the challenges associated with their use. On the other hand, heterogeneous catalysts, such as mesoporous tantalum oxide, mesoporous tantalum phosphate, chromium-exchanged zirconium phosphate, chromium-exchanged montmorillonite, Hβ-zeolite (Si/Al = 25), SO42−/ZrO2, SO42−/ZrO2–Al2O3, MCM-41 mesoporous silica containing ZrO2, Sn-ceramic powder, Al2O3–B2O3, Sn-beta zeolite, Sn-montmorillonite, TiO2–ZrO2, and Amberlyst-15 sulfonic resin have also been explored for the conversion of glucose into HMF.31–48 Nevertheless, challenges such as slower reaction kinetics and deactivation due to the formation of humins are some of the difficulties encountered by their use. Humins are formed when glucose, fructose, and HMF undergo aldol addition/condensation (in the presence of Brønsted acid sites) to form an active intermediate named 2,5-dioxo-6-hydroxyhexanal (DHH) that reacts with another HMF molecule.49 Humins get irreversibly chemisorbed on the active sites of the catalyst, thus reducing the number of active centers available for reaction.50
In order to overcome the challenges of the use of homogeneous and heterogeneous catalysts, in this work, we synthesized a series of soluble and reusable polymer-based catalysts containing both Brønsted and Lewis acid sites for the one-pot production of HMF from glucose. Polystyrene sulfonic acid (PSSA) has been reported as an active catalyst for reactions that require Brønsted acidity (e.g., production of biodiesel from vegetable oil, xylose dehydration to furfural, and oxidation of furfural into succinic and maleic acids).51–54 Interestingly, PSSA is soluble in polar solvents, which makes it highly active due to easy accessibility to the Brønsted acid sites, and it can also be recovered by ultrafiltration due to its high molecular weight. Now, in order to make that polymer catalyst suitable for the production of HMF from glucose, we added another functionality (Lewis acidity) by crosslinking PSSA chains with AlCl3. Previous studies in the literature described the addition of AlCl3 to sulfonic resins to generate solid catalysts with both functionalities. For example, Magnotta et al. reported the synthesis of heterogeneous PSSA–AlCl3 catalysts by spraying AlCl3 gas onto PSSA beads under an inert atmosphere at 105 °C.55 On the other hand, Wang et al. synthesized a ZnCl2-modified resin by mixing PSSA and ZnCl2 in ethanol for 6 h.56 In this report, however, we aimed to synthesize soluble and recoverable PSSA–AlCl3 catalysts to benefit from the advantages of both homogeneous and heterogeneous catalysis: high activity and reusability. To do so, we developed a facile method to carry out the crosslinking of PSSA with AlCl3 in an alcoholic medium at room temperature while maintaining the polymer catalyst in solution.30,48,57 A series of PSSA–AlCl3 catalysts with different Brønsted
:
Lewis acid ratios was synthesized, characterized, and studied in the one-pot production of HMF from glucose. Additionally, reutilization studies were carried out to demonstrate the recoverability and reusability of the catalysts. Lastly, a techno-economic analysis helped determine the minimum furan selling price (MFSP) of HMF produced. Remarkably, a low MFSP was obtained amid the high costs in 2022, mostly due to the reutilization of the catalysts.
Experimental
Materials
Poly(sodium 4-styrenesulfonate) solutions (Mw ∼200 kDa and 1000 kDa), 99.8% anhydrous methanol, anhydrous ethanol with ≤0.003% water, ≥99% methyl isobutyl ketone (MIBK), 99% HMF, 98% levulinic acid, 99% formic acid, ≥99.9% acetonitrile, 99.5% D-(+)-glucose, 98% sulfuric acid, 99.95% potassium hydrogen phthalate, phenolphthalein, and 99.5% sodium hydroxide were all purchased from MilliporeSigma, USA. Amberlyst® 15(H) dry was purchased from Alfa Aesar, USA, 99.99% aluminum chloride was obtained from Strem Chemicals, USA, and 99% 2-butanol and 99% D-(−)-fructose from Acros Organics, USA. 5 kDa nominal molecular weight limit (NMWL) Biomax polyethersulfone ultrafiltration discs were obtained from MilliporeSigma, USA, and used in 75 and 500 mL Amicon stirred ultrafiltration cells. Milli-Q water (∼18 MΩ cm−1) was used for all the experiments.
Catalyst synthesis
Synthesis of polystyrene sulfonic acid (PSSA) catalysts.
Commercial poly (sodium 4-styrenesulfonate) (NaPSS) with a weight average molecular weight (Mw) of 1000 kDa was used as a precursor for the synthesis of polystyrene sulfonic acid (PSSA). This polymer salt was converted into its acidic form by ion exchange with Amberlyst® 15(H) sulfonic resin. In a typical synthesis, 100 mL of a 30 wt% NaPSS solution was added to 500 mL of Milli-Q water, followed by the addition of 60 g of crushed Amberlyst® 15(H) resin (H+ capacity = 4.7 meq g−1). The mixture was then stirred at 400 rpm overnight. After that, the sulfonic resin was removed by conventional filtration. The filtered solution containing PSSA was then heated in an oven at 60 °C to evaporate the water. The dried solid was then dissolved in methanol under vigorous stirring, followed by ultrafiltration of the PSSA–methanol solution using a 5 kDa Biomax polyethersulfone membrane to get rid of shorter PSSA chains. The ultrafiltration membrane was previously conditioned by passing 600 mL of Milli-Q water in a cell pressurized to 20 psi with N2. The retentate was then dried in an oven at 60 °C and stored in a vial. A similar protocol was used to synthesize PSSA with a Mw of 200 kDa (Fig. 2(a)) with slight modification. To ensure that the ion exchange was complete, the mass of crushed Amberlyst® 15(H) was doubled to 120 g, and the solution was stirred for 24 h.
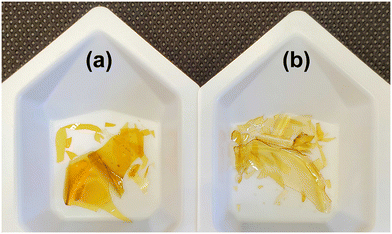 |
| Fig. 2 Pictures of (a) 200-PSSA and (b) 200-PSSA-AlCl3 4.0 catalysts. | |
Synthesis of PSSA–AlCl3 catalysts with Mw of 1000 kDa (1000-PSSA-AlCl3).
The Lewis acid functionality was incorporated by crosslinking PSSA chains with AlCl3 in a liquid medium at room temperature. As AlCl3 is highly sensitive to air and moisture, this was carried out using anhydrous solvents inside a glove box filled with ultra-high purity (UHP) argon. Since PSSA is soluble in methanol but slightly in ethanol, and AlCl3 is soluble in ethanol but not in methanol, we first performed a series of solubility tests to maximize the incorporation of AlCl3. To do so, the volume of ethanol was kept constant while varying the volume of methanol and the mass of PSSA and AlCl3. This study generated a solubility diagram, and the methanol (MeOH)–ethanol (EtOH) ratio used for the synthesis was selected from the region in which both PSSA and AlCl3 were soluble.
In a typical synthesis, 1 g of PSSA (Mw = 1000 kDa) was dissolved in 30 mL of anhydrous methanol, and an appropriate mass of AlCl3 was dissolved in 20 mL of anhydrous ethanol in separate flasks. To ensure uniform dissolution, the methanolic solution of PSSA and ethanolic solution of AlCl3 were stirred independently for 1 h, after which the AlCl3–ethanol mixture was transferred to the PSSA–methanol mixture with the aid of a peristaltic pump at a flow rate of about 0.6 mL min−1. Then, the PSSA–AlCl3 alcoholic solution was stirred at 1000 rpm for 3 h at room temperature. The solution was then ultrafiltered using a 5 kDa Biomax polyethersulfone membrane. The retentate was casted and dried overnight at 60 °C. A series of PSSA–AlCl3 catalysts with different Brønsted
:
Lewis acid ratios was synthesized, and these catalysts were labeled as 1000-PSSA-AlCl3X, where 1000 indicates Mw in kDa and X indicates the actual H+/Al mole ratio obtained from characterization (e.g., 1000-PSSA-AlCl3 4.0 is the 1000 kDa catalyst with an actual H+/Al mole ratio of 4). As previously stated, our goal was to synthesize soluble and reusable polymer-based catalysts with both Brønsted and Lewis acid sites; however, by following the protocol described above, the 1000-PSSA-AlCl3 4.0 preparation resulted in the precipitation of the polymer. We believe this could be due to increased crosslinking and reduced hydrophilicity by consumption of sulfonic groups, although it could also be that the volume of alcohols used was insufficient to maintain the polymer in solution during the synthesis. For this reason, we decided to modify the synthesis by using PSSA with a lower Mw of 200 kDa and larger volumes of alcohols.
Synthesis of PSSA–AlCl3 catalysts with Mw of 200 kDa (200-PSSA-AlCl3).
To synthesize soluble PSSA–AlCl3 catalysts with a higher content of Lewis acid sites, the synthesis protocol was further optimized to ensure that PSSA remained in solution during the incorporation of AlCl3. To do so, we used 200 kDa PSSA and maintained a constant methanol volume fraction of 0.6 (MeOH/(MeOH + EtOH)). For example, to synthesize the 200-PSSA-AlCl3 catalyst with an actual H+/Al mole ratio of 4, we dissolved 1 g of 200 kDa PSSA in 240 mL of anhydrous methanol, and 180 mg of AlCl3 in 160 mL of anhydrous ethanol in separate flasks (Table S1†). To ensure uniform dissolution, the methanolic solution of PSSA and ethanolic solution of AlCl3 were stirred independently for 1 h. Then, the AlCl3–ethanol mixture was transferred to the PSSA–methanol mixture with the aid of a peristaltic pump at a flow rate of about 0.6 mL min−1. The PSSA–AlCl3 alcoholic solution was then stirred at 1000 rpm overnight to ensure maximum incorporation of AlCl3 into the PSSA structure. The solution was then ultrafiltered using a 5 kDa Biomax polyethersulfone membrane, and the retentate was dried overnight at 60 °C (Fig. 2(b)). A series of PSSA–AlCl3 catalysts with different Brønsted
:
Lewis acid ratios was synthesized, and these catalysts were labeled as 200-PSSA-AlCl3X, where 200 indicates Mw in kDa and X indicates the actual H+/Al mole ratio (e.g., 200-PSSA-AlCl3 4.0 is the 200 kDa catalyst with an actual H+/Al mole ratio of 4).
Characterization of the fresh and used 200-PSSA and 200-PSSA-AlCl3 catalysts
Acid–base titration.
To investigate the reduction in the number of Brønsted acid sites upon AlCl3 incorporation, as well as the stability of the materials and potential leaching of the sulfonic groups, we conducted acid–base titration of the catalysts. In a typical experiment, 30 mg of 200-PSSA (or 200-PSSA-AlCl3) catalyst was dissolved in 10 mL of Milli-Q water and titrated against 0.01 N NaOH using phenolphthalein as an indicator. The NaOH solution was first standardized by titration with potassium hydrogen phthalate. Since these catalysts are highly hygroscopic, the mass of water (obtained by thermogravimetric analysis) was subtracted from the catalyst weight to determine the effective mass of the catalyst used for acid–base titration.
Inductively Coupled Plasma – Mass Spectrometry (ICP-MS) analysis.
ICP-MS analyses were performed to quantify the amount of Al incorporated into the polymer structure. In a typical analysis, 100 mg of sample was digested in pure HNO3 using a CEM Mars microwave. After digestion, the sample was filtered to remove particulate and undissolved material. The filtrate was then diluted with 3.5% HNO3 to ensure it was within the calibration range of 20–1000 ppb for ICP-MS analysis (Thermo Scientific XSeries 2, USA). For quantitative analysis, standard solutions were prepared using certified ICP-MS standards from Inorganic Ventures with correlation coefficients above 0.999.
Thermogravimetric Analysis (TGA).
Thermogravimetric analyses of 200-PSSA and 200-PSSA-AlCl3 catalysts were conducted using a TA Instruments Q50 TGA. In a typical analysis, about 5 mg of the sample was heated from room temperature to 800 °C using a ramp of 10 °C min−1 under a flow of N2.
Micro-Attenuated Total Reflection Fourier Transform Infrared Spectroscopy (Micro-ATR FTIR) analysis.
To examine the consumption of Brønsted acid sites and the incorporation of AlCl3 into the polymer structure, 200-PSSA and 200-PSSA-AlCl3 catalysts were characterized by Fourier transform infrared spectroscopy (FTIR) in a micro-ATR mode. Briefly, about 7 mg of the polymer film was placed on the equipment and analyzed using a germanium crystal and 256 scans. The polymer film was obtained by dissolving ∼0.4 g of the polymer catalyst in 13.8 mL of Milli-Q water. The polymer solution was then casted in a weighing boat, dried in an oven at 60 °C, and further dried using a vacuum oven at 60 °C before analysis.
Inductively Coupled Plasma – Optical Emission Spectrometry (ICP-OES) analysis.
ICP-OES analyses were performed by Galbraith Laboratories, Inc. to assess the stability of the catalysts and potential leaching of the sulfonic or Al-containing groups. In a typical analysis, about 20 mg of the sample was charred using H2SO4. After that, HNO3 was added, and the sample was refluxed to solubilize the metal present. The clear digestate was quantitatively transferred to a volumetric flask for analysis using an ICP-OES 3300DV equipment.
Determination of total halogens by potentiometric titration.
The Cl content in the filtrates, fresh, and used 200-PSSA-AlCl3 4.0 catalysts was determined using potentiometric titration using AgNO3. In a typical analysis, chlorine in the sample is converted to halide by oxygen flask combustion. Then, halide is directly measured using a Metrohm 716 DMS Titrino with 730 Sample Changer.
Elemental analysis.
The percentages of carbon (C), hydrogen (H), and sulfur (S) on the fresh and used 200-PSSA-AlCl3 4.0 catalysts were determined by combusting the samples under static conditions using a PerkinElmer 2400 series II elemental analyzer and a LECO SC-632 carbon/sulfur determinator. To do so, about 1.4 mg of sample was subjected to combustion in pure oxygen at 920–980 °C under static conditions to produce CO2, H2O, and N2. The equipment automatically separates and analyzes those products in a self-integrating, steady-state thermal conductivity analyzer. On the other hand, the S content was obtained by subjecting about 9 mg of sample to combustion at 135 °C in an atmosphere of oxygen and analyzing released SO2 by infrared absorption.
Measurements of catalytic activity
One-pot synthesis of HMF from glucose using 200-PSSA and 200-PSSA-AlCl3 catalysts.
In a typical reaction, 150 mg of glucose was added to a ∼15 mL Ace pressure tube (heavy wall borosilicate glass tube, 10.2 cm L × 25.4 mm O.D.) containing 1.5 mL of Milli-Q water (9.1 wt% glucose solution). Next, 32 mg of 200-PSSA catalyst was added, and the mixture vortexed until dissolution. It is worth mentioning that PSSA–AlCl3 catalysts with lower contents of Lewis acid sites (up to 200-PSSA-AlCl3 4.0) were soluble in the aqueous solution of glucose at room temperature. However, those catalysts with higher Lewis acid contents were not fully soluble, resulting in cloudy solutions. The amount of Brønsted acid sites used was kept constant to effectively compare all the catalysts, leading to different masses of catalysts used. In order to minimize the occurrence of side reactions (Fig. 1), a biphasic medium was used, so that HMF could be extracted by the organic phase as soon as it was formed. Therefore, 9 mL of a mixture of MIBK and 2-butanol (7
:
3 v/v) was added to the pressure tube, closed with a front-seal cap with CAPFE O-ring, and the reactions were carried out at 150 °C using a stirred silicon oil bath (1000 rpm). Notably, water/MIBK–2-butanol biphasic media have been previously reported in the literature for the one-pot synthesis of HMF from glucose.58 However, all of them used salts (e.g., NaCl) in the aqueous phase to improve the partitioning of HMF in the organic solvent, known as the “salting-out effect”. In our case, since the addition of NaCl is incompatible with the use of PSSA because this would revert it back to NaPSS with the release of H+, we compensated for this by the addition of a larger volume of organic phase for efficient HMF extraction. Upon completion, the reactor was immersed in an ice bath to stop the reaction, and aqueous and organic phases were separated. Details about the analysis of aqueous and organic phases can be found in the ESI.†
One-pot synthesis of HMF from glucose using homogeneous catalysts.
Pure homogeneous catalysts (H2SO4 and AlCl3) with equivalent H+ and Al contents as the 200-PSSA-AlCl3 4.0 catalyst were used to produce HMF from glucose. In a typical reaction, the feed solution was prepared by dissolving 3 g of glucose and 0.16 g of AlCl3 in a beaker containing 30 mL of an 81.3 mM H2SO4 solution. Since AlCl3 was stored inside the glove box, this was weighed inside, transferred to a beaker, and taken out to prepare the stock feed solution. Next, 1.5 mL of the feed solution was transferred to a ∼15 mL Ace pressure tube (heavy wall borosilicate glass tube, 10.2 cm L × 25.4 mm O.D.), followed by the addition of 9 mL of a mixture of MIBK and 2-butanol (7
:
3 v/v) to continuously extract HMF as soon as it was formed. The reactor was then closed with a front-seal cap with CAPFE O-ring, and reactions were carried out at 150 °C between 1 and 4 h using a stirred silicon oil bath (1000 rpm). Upon completion, the reactor was immersed in an ice bath to stop the reaction, and aqueous and organic phases were separated. Details about the analysis of aqueous and organic phases can be found in the ESI.†
Reutilization experiments.
The most promising catalyst in the one-pot synthesis of HMF from glucose was reutilized several times to assess its stability in reaction. In order to minimize the fraction of catalyst lost due to handling after every cycle, the process was scaled up. In a typical reutilization experiment, 330 mg of 200-PSSA-AlCl3 4.0 catalyst was transferred to a ∼60 mL Ace pressure tube (heavy wall borosilicate glass tube, 10.2 cm L × 38.1 mm O.D.), followed by the addition of 4.5 mL of a 16.7 wt% aqueous solution of glucose. The mixture was then vortexed until dissolution. Next, 27 mL of a mixture of MIBK and 2-butanol (7
:
3 v/v) was added for continuous extraction of HMF. The reactions were performed at 150 °C for 1 h to obtain low glucose conversions that would allow us to monitor the potential deactivation of the catalyst. Upon completion, the reactor was immersed in an ice bath to stop the reaction, and the aqueous and organic phases were separated. The aqueous phase was then centrifuged at 1400 rpm to remove insoluble humins, and ultrafiltered using an Amicon stirred cell with a 5 kDa NMWL Biomax polyethersulfone membrane. Then, both the retentate and water used to rinse the cell several times were added to the glass tube. The reactor was then dried to evaporate the water, and the contained catalyst was used for a subsequent run. Acid–base titrations of the filtrate solutions were performed to assess the potential leaching of sulfonic groups.
Techno-economic analysis
Based on the experimental results, we performed a techno-economic assessment for the production of HMF from glucose with the 200-PSSA-AlCl3 4.0 catalyst. A process flow model (Fig. 3) was developed for an aqueous feed of 9.1 wt% glucose at a flow rate of 10 MT h−1 (dry-sugar basis). In the process design, the dehydration of glucose occurs in a packed bed reactor-extractor (R101) where an aqueous stream containing glucose and 200-PSSA-AlCl3 4.0 and an organic solvent stream are fed counter-currently. After reaction, the aqueous stream is sent to an ultrafiltration unit (F101) to recover the polymer catalyst for re-use, and the organic stream is sent to a distillation unit (D101) for product and solvent recovery. Mass and energy balance calculations across the reactor were performed based on experimental results and enthalpy differences between feed and product streams in MS Excel. The equipment size was estimated based on liquid hold-up volume and experimentally determined residence time.59 Next, data of the organic phase on the reactor outlet stream was fed as input to a distillation unit in Aspen Plus to determine the number of stages, reboiler, and condenser duty. To recover the polymer catalyst, the membrane area required was estimated based on the typical flux of 50 L m−2 h−1 in commercial ultrafiltration modules.60 Intermediate heat exchangers were designed based on heat duty obtained from the enthalpy difference of process streams.
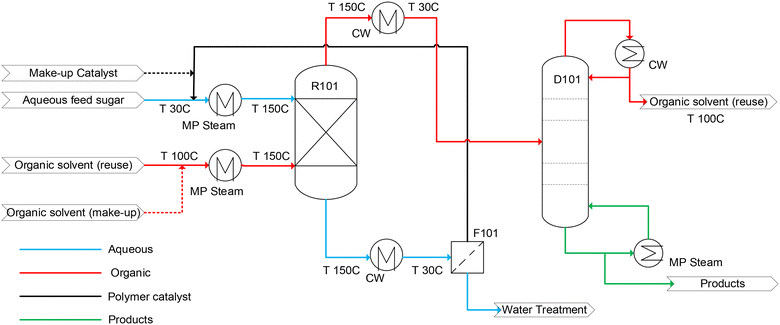 |
| Fig. 3 Process flow diagram for techno-economic analysis. | |
Capital costs of all equipment were determined using CAPCOST® – an MS Excel-based program that uses a module-costing approach.61 A Chemical Engineering Plant Cost Index (CEPCI) value of 805 was used to estimate installed capital cost based on 2022$.62 The cost of land was assessed to be $0.5M and is consistent with previous techno-economic models for the conversion of lignocellulosic biomass to hydrocarbons.63 A 2-year construction period was assumed, and the capital investment was uniformly distributed over this period. Total fixed capital investment excluding land (FCIL) was estimated from the sum of the total module cost of all equipment and capital and operating costs of the ultrafiltration unit were determined using correlations provided by Guo et al.64 The cost of manufacturing (COM) was determined based on the cost of raw material (CRM), cost of utility (CUT), cost of wastewater treatment (CWT), and cost of operating labor (COL). CRM was determined based on estimates of material consumed in the process, where an additional 10% was added to make up for annual process losses of all recycled chemicals and catalyst. Replacement of all recycled chemicals and catalyst was accounted for every 3 years and was distributed to the annual cost of raw material. A feedstock price of $0.30 per kg of glucose was used19 and the price of the catalyst ($15 per kg) was assumed to be 5 times the cost of its raw materials – PSSA and AlCl3. Prices of other chemicals are listed in Table 1. To estimate the CUT, medium-pressure steam was assumed as a heating utility at the price of $4.77 per GJ,65 electricity at a price of $0.07 per kWh to pump process fluids,66 and cooling water at a price of $0.378 per GJ. A wastewater treatment cost of $0.5M per year was added to the cost of manufacturing, and operating labor was estimated based on the number and type of equipment. Working capital estimates were factored from CRM, cost of land, and COL. Parameters used for the techno-economic analysis are listed in Table 2.
Table 1 Total operating cost
Material/utility |
Price |
Total operating cost |
Comment/references |
$ |
M$ |
% |
Glucose, kg |
0.30 |
25.95 |
66.8 |
63
|
MIBK, kg |
1.00 |
0.61 |
1.6 |
Market price |
2-Butanol, kg |
1.00 |
0.30 |
0.8 |
Market price |
200-PSSA-AlCl3 4.0, kg |
15.0 |
0.72 |
1.9 |
5 × [market price of PSSA ($4 per kg) + AlCl3 ($1 per kg)] |
Steam, GJ |
4.77 |
8.53 |
22.0 |
61, 65 |
Cooling water, GJ |
0.38 |
0.63 |
1.6 |
61, 65 |
Electricity, kWh |
0.07 |
0.24 |
0.6 |
66
|
Wastewater treatment |
Lumpsum |
0.5 |
1.3 |
63
|
Operating labor |
Lumpsum |
0.87 |
2.2 |
63
|
Ultrafiltration |
Flow rate correlation |
0.49 |
1.3 |
64
|
Total (M$)
|
|
38.84
|
|
|
Table 2 Parameters used for techno-economic analysis
Parameter |
Value |
Units |
Capacity (9.1 wt% glucose) |
10 000 |
kg h−1 (dry basis) |
Operating hours |
8650 |
h per year |
Project life |
20 |
Years |
Construction period |
2 |
Years |
Taxation rate |
21% |
— |
Annual interest rate |
10% |
— |
Total module factor |
1.18 |
— |
CEPCI |
805 |
— |
Cost of land |
0.5 |
$M |
Depreciation |
7-year MACRS |
— |
Catalyst : sugar |
0.33 |
kg/kg |
Solvent ratio |
6 |
v/v |
Revenue was generated by the sale of HMF. Net present value (NPV) was determined using discounted cash flow analysis with a discount rate of 10% and a taxation rate of 21%, which includes federal and state taxes.61 Capital equipment was depreciated in accordance with the 7-year modified accelerated cost recovery system (MACRS), and salvage value was assessed as 10% of FCIL after the project-life of 20 years. To determine the minimum furan selling price (MFSP), the selling price of furans was iterated to obtain a NPV approximately equal to zero. Although the process also generates levulinic acid, formic acid, and humins as by-products, these are too low to be recovered economically; thereby, minor streams are processed in the wastewater treatment plant.
Results and discussion
Phase diagram to identify the solvent ratio for solubility of AlCl3 and PSSA
Solubility studies were performed to ensure the crosslinking between PSSA and AlCl3 without precipitation of its components. To do so, the volume of ethanol was kept constant while changing the volume of methanol and the masses of 1000 kDa PSSA (1000-PSSA) catalyst and AlCl3. Fig. S1† shows the phase diagram obtained, where the green and purple areas indicate the solubility (1 phase) or macroscopic precipitation (2 phases) of 1000-PSSA and AlCl3, respectively, in different alcoholic mixtures. As the MeOH/(MeOH + EtOH) ratio of 0.6 resulted in the maximum solubility of both 1000-PSSA and AlCl3, that ratio was chosen to carry out all PSSA–AlCl3 syntheses. As previously stated, when 1000-PSSA was used to synthesize 1000-PSSA-AlCl3 catalysts, H+/Al mole ratios ≤4 resulted in the precipitation of the polymer catalysts. As a result, we decided to modify the synthesis by using a shorter-chain PSSA (200 kDa) and a larger volume of alcohol (Table S1†) while maintaining a MeOH/(MeOH + EtOH) volume ratio of 0.6. When 200 kDa PSSA (200-PSSA) was used, we were able to synthesize a series of catalysts with different H+/Al mole ratios ranging from 17.2 to 1.2, which reflects different degrees of AlCl3 incorporation to PSSA.
Acid–base titration of 200-PSSA and 200-PSSA-AlCl3 catalysts
The amount of Brønsted acid sites on 200-PSSA and 200-PSSA-AlCl3 was determined by acid–base titration using a standardized 0.01 N NaOH solution. Table 3 shows the average values from three titrations. Table 3 and Fig. 4 also show the actual Al loading obtained by ICP-MS. As expected, there is a decrease in the content of Brønsted acid sites (H+) due to the incorporation of AlCl3 into the polymer structure.
Table 3 Brønsted acid sites (acid–base titration) and Al loading (ICP-MS) on 200-PSSA and 200-PSSA-AlCl3 catalysts
Catalyst |
Brønsted acid sites (mmol H+ gcat−1) |
Al loading (mmol Al gcat−1) |
H+/Al mole ratio |
200-PSSA |
5.40 |
N/A |
N/A |
200-PSSA-AlCl3 17.2 |
5.00 |
0.29 |
17.2 |
200-PSSA-AlCl3 7.4 |
4.63 |
0.63 |
7.4 |
200-PSSA-AlCl3 5.0 |
4.60 |
0.93 |
5.0 |
200-PSSA-AlCl3 4.0 |
4.44 |
1.10 |
4.0 |
200-PSSA-AlCl3 3.6 |
4.38 |
1.22 |
3.6 |
200-PSSA-AlCl3 3.0 |
4.11 |
1.35 |
3.0 |
200-PSSA-AlCl3 2.7 |
3.94 |
1.48 |
2.7 |
200-PSSA-AlCl3 1.7 |
2.71 |
1.56 |
1.7 |
200-PSSA-AlCl3 1.2 |
2.27 |
1.89 |
1.2 |
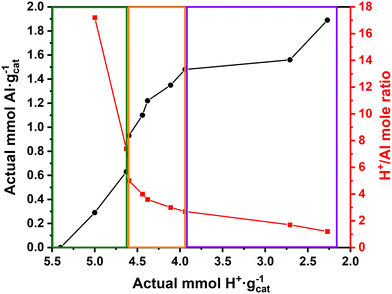 |
| Fig. 4 Actual H+vs. Al content and H+/Al mole ratio on 200-PSSA-AlCl3 catalysts upon addition of AlCl3. | |
Inductively Coupled Plasma – Mass Spectrometry (ICP-MS) analysis of 200-PSSA-AlCl3 catalysts
ICP-MS analyses were conducted to determine the amount of aluminum successfully incorporated into the polymer structure. Table 3 and Fig. 4 show that the Al content increases upon addition of AlCl3 while the concentration of Brønsted acid sites (H+) decreases. Fig. 4 also shows how the H+/Al mole ratio varied as AlCl3 was incorporated into PSSA. Remarkably, three different regions can be clearly observed in Fig. 4: one at low AlCl3 loadings with slow incorporation of Al (left), another in which there is a fast increase in the Al content while the H+ concentration is only slightly reduced (middle), and a final one in which the incorporation of Al plateaus at higher AlCl3 loadings (right). As suggested by Magnotta et al. and Wang et al.,55,56,67 we also expect AlCl3 to be incorporated between two sulfonic groups to form structure (I) with the release of HCl (Fig. 5). Then, unstable structure (I) can reversibly form structures (II) and (III) in the presence of another sulfonic group (Fig. 5). As a result, Fig. 4 would be consistent with that mechanism, as the equilibrium between structures (I) and (II) & (III) would be affected by the number of Brønsted acid sites available during the synthesis.
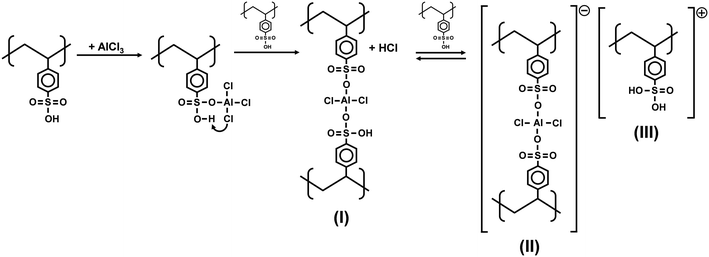 |
| Fig. 5 Structures formed by coordination between sulfonic groups of PSSA and AlCl3. | |
Thermogravimetric Analysis (TGA) of 200-PSSA and 200-PSSA-AlCl3 catalysts
Fig. 6 compares the weight loss and derivative weight loss curves obtained from 200-PSSA and 200-PSSA-AlCl3 catalysts. The weight loss before 200 °C was attributed to the loss of water, which is due to the hygroscopic nature of the polymer.51,52 The loss of weight between 225–375 °C corresponds to the decomposition of the sulfonic groups, as reported elsewhere.51,52 As shown in the derivative weight plot (Fig. 6(b)), there is a gradual decrease in the intensity of this evolution upon the addition of AlCl3, which is due to the consumption of sulfonic groups by crosslinking with AlCl3. Interestingly, the decomposition of sulfonic groups on PSSA-AlCl3 4.0 and PSSA-AlCl3 3.6 catalysts occurred at higher temperatures (shoulder centered at around 350 °C), which might be attributed to the increased stability of the remaining sulfonic groups. Finally, the evolution beyond 400 °C corresponds to the decomposition of the polystyrene backbone.51,52 As AlCl3 is added to the PSSA structure to form PSSA–AlCl3 catalysts, the decomposition of the as-synthesized materials occurs at higher temperatures, which is attributed to the increased rigidity due to crosslinking.
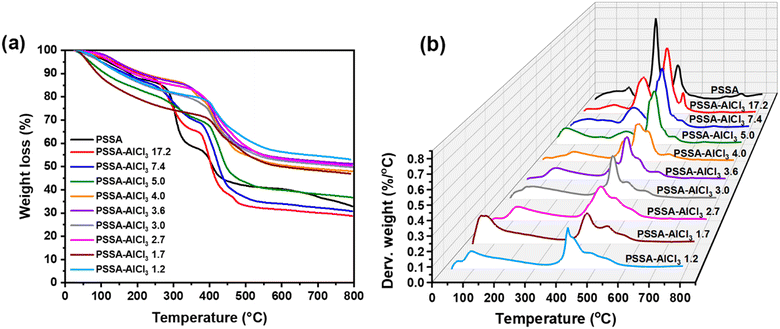 |
| Fig. 6 (a) Weight loss and (b) derivative weight loss of 200-PSSA and 200-PSSA-AlCl3 catalysts. | |
Micro-Attenuated Total Reflection Fourier Transform Infrared Spectroscopy (Micro-ATR FTIR) analysis of 200-PSSA and 200-PSSA-AlCl3 catalysts
To better understand the nature of 200-PSSA and 200-PSSA-AlCl3 catalysts, materials were also characterized by FTIR in micro-ATR mode. Assuming that the structure of the aromatic rings remained intact upon the addition of AlCl3, all spectra were normalized using the intensity of the band at 1600 cm−1, which is attributed to the C
C vibrations in the aromatic ring.68 As shown in Fig. 7, all spectra look similar except for the bands at 1080, 1125, and 1155 cm−1. The band at 1080 cm−1 is assigned to the symmetric stretching vibration of –SO3−,68 and this decreases as the number of sulfonic groups is reduced by the incorporation of AlCl3. On the other hand, the bands at 1125 and 1155 cm−1 increase their intensity upon addition of AlCl3, which clearly indicates that AlCl3 is modifying the sulfonic groups, although these bands are more difficult to interpret due to the coexistence of structures (I), (II), and (III) (Fig. 5).
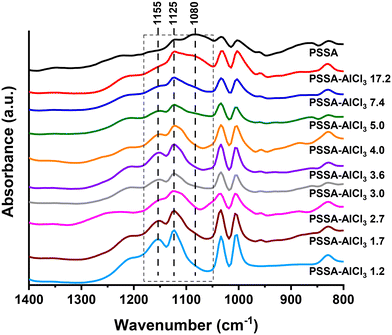 |
| Fig. 7 Micro-ATR FTIR spectra of 200-PSSA and 200-PSSA-AlCl3 catalysts. | |
Catalytic studies
HMF production from glucose using 200-PSSA and 200-PSSA-AlCl3 catalysts.
HMF production from glucose can proceed through two reaction pathways.69 The first one is the direct dehydration of glucose to HMF in the presence of Brønsted acid sites. The other route involves the isomerization of glucose to fructose in the presence of a Lewis acid catalyst, followed by the subsequent dehydration of fructose to HMF with Brønsted acid catalysts. In this work, 200-PSSA (only containing Brønsted acidity) and 200-PSSA-AlCl3 catalysts (with both Brønsted and Lewis acidities) were used to catalyze the production of HMF from glucose. In order to effectively compare the series of 200-PSSA-AlCl3 catalysts with different Brønsted
:
Lewis acid ratios, the amount of Brønsted acid sites (H+) was kept constant in all experiments. Fig. 8 shows the glucose conversion, HMF yield, and levulinic acid (= formic acid) yield obtained with 200-PSSA and 200-PSSA-AlCl3 catalysts in the production of HMF from glucose (9.1 wt% solution in water). Low glucose conversion (60 mol%) and HMF yield (25 mol%) were recorded when using the 200-PSSA catalyst, which was expected as the acid-catalyzed dehydration of glucose in water is not selective toward HMF. This is because glucose in solution only contains 1% of furanose isomer with a structure similar to HMF, thus complicating the direct conversion of glucose into HMF.69–71 In order to improve the glucose conversion and subsequent production of HMF, we explored the use of 200-PSSA-AlCl3 catalysts with different Brønsted
:
Lewis acid ratios. As shown in Fig. 8, both the glucose conversion and HMF yield increased when increasing the Al content (concentration of Lewis acid sites) until reaching a maximum HMF yield of ∼55 mol% with the 200-PSSA-AlCl3 4.0 catalyst. This is attributed to an enhanced isomerization of glucose to fructose by intramolecular hydride shift,33,69,70 which results in a higher concentration of furanose isomers in solution that can be readily converted into HMF.71 The long induction period observed in the conversion of glucose with 200-PSSA and 200-PSSA-AlCl3 7.4 catalysts is due to the absence or low content of Lewis acid sites, which results in the slow direct dehydration of glucose to HMF without the intermediate isomerization step. In addition, it can be observed that the carbon balance does not close in any case, which is attributed to the formation of humins.
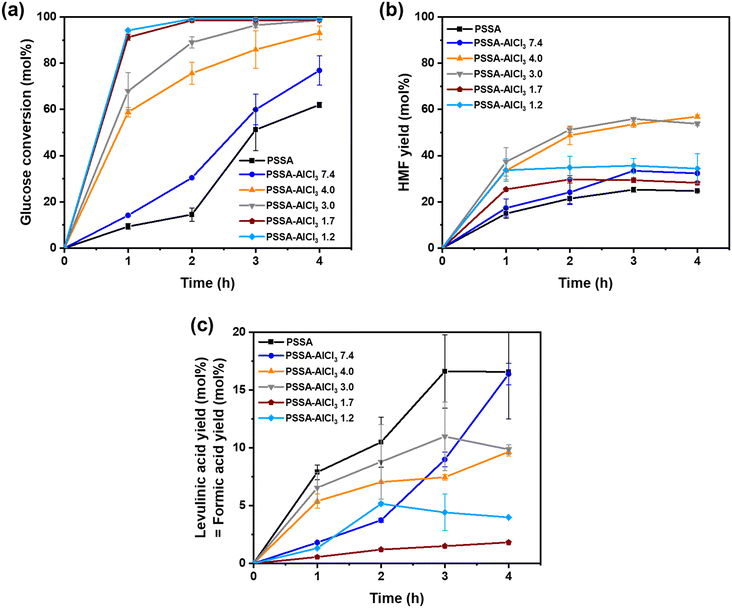 |
| Fig. 8 Glucose conversion to HMF in a biphasic water/MIBK–2-butanol system using 1.5 mL of a 9.1 wt% glucose solution in water, 9 mL MIBK–2-butanol 7 : 3 (v/v), and 0.244 mmol H+ at 150 °C and 1000 rpm: (a) glucose conversion (mol%), (b) HMF yield (mol%), and (c) levulinic acid (= formic acid) yield (mol%). Experiments were repeated at least twice and the error bars represent the standard deviation from the mean. | |
However, Fig. 8(b) shows that the HMF yield decreased when using catalysts with a high concentration of Lewis acid sites (200-PSSA-AlCl3 1.7 and 1.2). Although high glucose conversions were obtained with those two catalysts, the HMF yield was low due to the imbalance between Brønsted and Lewis acid sites. Additionally, part of the reduced activity of 200-PSSA-AlCl3 1.7 and 1.2 catalysts could be attributed to their reduced solubility in water due to their lower content of sulfonic groups and/or higher molecular weight due to crosslinking. As expected, the levulinic acid (and formic acid) yields were smaller when using the catalysts with lower Brønsted acidity (Fig. 8(c)). Since the mass balance ranged between 75–90 wt% in all cases, being higher at lower reaction times, it can be concluded that the production of humins was significant at longer reaction times.
Catalytic activity of 200-PSSA-AlCl3 4.0 vs. combination of homogeneous Brønsted and Lewis acid catalysts (H2SO4 + AlCl3).
Since 200-PSSA-AlCl3 4.0 showed the highest glucose conversion and HMF yield (Fig. 8), its activity was compared to that of a combination of pure homogeneous catalysts (H2SO4 + AlCl3) with the same H+ and Al content (Fig. 9). Interestingly, the glucose conversion and HMF yield obtained with the homogeneous catalysts were not higher than those with the polymer catalyst, with the advantage that 200-PSSA-AlCl3 4.0 can be recovered by ultrafiltration to be reused. Additionally, 200-PSSA-AlCl3 4.0 contributed to the lower production of side products (levulinic and formic acids). This could be due to the close vicinity of Brønsted and Lewis acid sites in 200-PSSA-AlCl3 4.0, which contributes to the rapid dehydration of fructose formed in a near Lewis site to HMF, as compared to the combination of homogenous catalysts (H2SO4 + AlCl3).
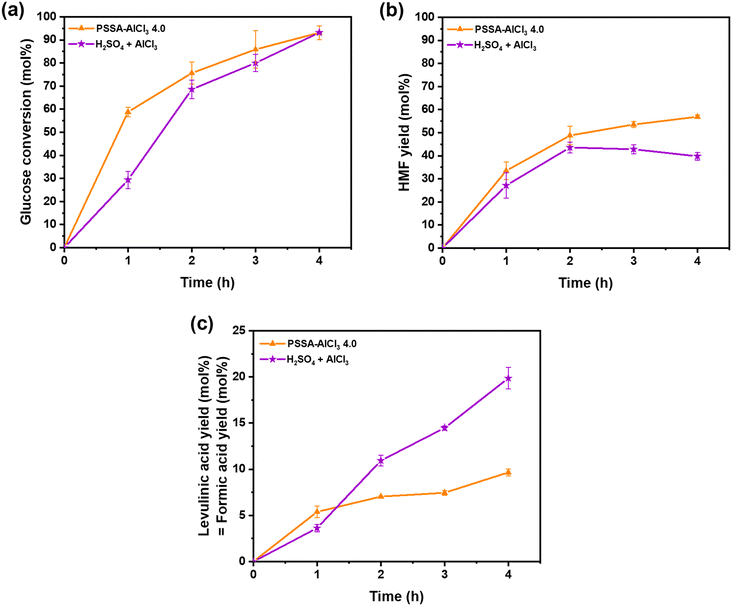 |
| Fig. 9 Glucose conversion to HMF in a biphasic water/MIBK–2-butanol system using 1.5 mL of a 9.1 wt% glucose solution in water, 9 mL MIBK–2-butanol 7 : 3 (v/v), 0.244 mmol H+, and 6 μmol Al at 150 °C and 1000 rpm: (a) glucose conversion (mol%), (b) HMF yield (mol%), and (c) levulinic acid (= formic acid) yield (mol%). Experiments were repeated at least twice, and the error bars represent the standard deviation from the mean. | |
Reutilization of the most promising 200-PSSA-AlCl3 catalyst.
As 200-PSSA-AlCl3 4.0 showed the highest glucose conversion and HMF yield (Fig. 8), this was selected to demonstrate its recovery and reusability. It is worth noting that a new batch of catalyst was prepared for the reutilization experiments, which showed a slightly different H+/Al ratio of 4.8. For that reason, that catalyst was labelled as 200-PSSA-AlCl3 4.8. To obtain low glucose conversions (∼50 mol%) to properly assess the potential deactivation of the catalyst, the reutilization experiments were conducted with a 16.7 wt% glucose solution in water for 1 h. Fig. 10(a) shows the turnover frequency (TOF) obtained when 330 mg of 200-PSSA-AlCl3 4.8 was reused up to five times in the one-pot synthesis of HMF from glucose. Although there is some loss of activity in the first two cycles, there is no significant deactivation after that. Upon completion of every catalytic cycle, the aqueous phase was centrifuged to remove insoluble humins, added to 10 mL of Milli-Q water, and ultrafiltered. Further, in order to properly account for any potential loss of –SO3H groups during the reutilization experiment, 2 mL of the filtrate was titrated every time. Fig. 10(a) shows the TOF obtained in every cycle, assuming that there is no catalyst loss due to handling or leaching (1.551 mmol H+ in all cases). That plot was also normalized considering mmol H+ (assumed in the form of –SO3H groups) leached in every cycle (Table 4 and Fig. 10(b)).
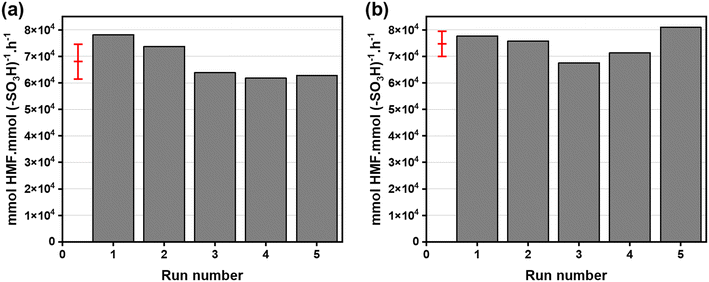 |
| Fig. 10 Turnover frequency (mmol HMF mmol (–SO3H)−1 h−1) obtained with 330 mg of 200-PSSA-AlCl3 4.8 (1.551 mmol H+) in the one-pot synthesis of HMF from glucose. Reaction conditions: 4.5 mL of a 16.7 wt% glucose solution in water and 27 mL of MIBK–2-butanol (7 : 3 v/v), 1 h, 150 °C, 1000 rpm: (a) assuming constant mmol –SO3H (1.551 mmol –SO3H) in all cycles and (b) normalized considering mmol H+ in the filtrate after every cycle. Bars represent the mean and standard deviation of the five reaction cycles. | |
Table 4 Proton content (assuming in the form of –SO3H groups) in the filtrate after every catalytic cycle and mmol H+ used in every cycle after subtracting the leached amount in the previous one
Cycle # |
mmol H+ in the filtrate (% mmol H+ leacheda) |
mmol H+ used to normalize the TOF plot (Fig. 10(b)) |
Initial: 1.551 mmol H+;0.479 mmol H+ total leached; (0.479/1.551)·100 = 30.8% mmol H+ lost (after 5 cycles). |
1 |
0.051 (3.3%) |
0.33 g × 4.7 mmol H+ gcat−1 = 1.551 (1st cycle) |
2 |
0.044 (2.8%) |
1.551–0.051 = 1.500 (2nd cycle) |
3 |
0.123 (7.9%) |
1.500–0.044 = 1.456 (3rd cycle) |
4 |
0.138 (8.9%) |
1.456–0.123 = 1.333 (4th cycle) |
5 |
0.123 (7.9%) |
1.333–0.138 = 1.195 (5th cycle) |
Thermogravimetric analysis of fresh and used 200-PSSA-AlCl3 4.8 catalyst.
To assess the stability of the 200-PSSA-AlCl3 4.8 catalyst, fresh and used (after 5 cycles) samples were characterized by thermogravimetric analysis. Fig. S2† compares the weight loss and derivative weight loss curves for both fresh and used 200-PSSA-AlCl3 4.8 catalysts. Unfortunately, a direct comparison is not possible even when using the same sample mass for TGA. This is because the used sample also contain humins that contribute to the mass of the catalyst. However, it can be clearly seen that the used sample has a higher water content (evolution between 75–225 °C) as a result of the reaction in the aqueous phase. As shown in Fig. S2(b),† there are two other evolutions beyond 225 °C, the first one corresponding to the sulfonic groups and the second to the decomposition of the polystyrene backbone and crosslinked AlCl3. It is observed that the evolution corresponding to the loss of sulfonic groups is negligible with the used catalyst, which is consistent with the occurrence of leaching, as shown in Table 4. Additionally, the weight loss is more gradual, which can be attributed to the continuous pyrolysis of humins.
Acid–base titration, ICP-OES, and elemental analysis of the fresh and used 200-PSSA-AlCl3 4.8 catalysts.
200-PSSA-AlCl3 4.8 fresh and used (after 5 cycles) samples were also characterized by acid–base titration, ICP-OES, and elemental analysis to determine the stability of the catalyst (Table 5). As previously stated, a new batch of catalyst was synthesized for the reutilization experiments, which explains the slightly different H+ content (4.7 mmol H+ gcat−1) when compared to that of 200-PSSA-AlCl3 4.0 (4.44 mmol H+ gcat−1) in Table 3. The acid–base titration of the used catalyst showed a decrease in the amount of Brønsted acid sites, which at first might indicate that there is some leaching of the sulfonic groups. However, the increase in the carbon content (elemental analysis) suggests that there are some carbonaceous species (humins) on the used catalyst, which also contributes to the overall mass. Therefore, it would be necessary to consider the real mass (without humins) of the used catalyst to properly assess the potential contribution of leaching. The same consideration applies to the Al content determined by ICP-OES. Some calculations aiming to quantify that are shown in the ESI† and the results are summarized in the last row of Table 5.
Table 5 Acid–base titration, ICP-OES, and elemental analysis results obtained with 200-PSSA-AlCl3 4.8 fresh and used. Values were corrected considering the mass of water in each sample (by TGA), which is roughly 15 and 25 wt% for fresh and used samples, respectively
Catalyst |
Titration |
ICP-OES (wt%) |
Elemental analysis (wt%) |
mmol H+ gcat−1 |
Al |
Cl |
C |
H |
S |
200-PSSA-AlCl3 4.8 fresh |
4.7 |
2.63 |
<1.07 |
42.42 |
6.04 |
14.95 |
200-PSSA-AlCl3 4.8 used (after 5 cycles) |
3.2 |
0.57 |
<1.22 |
53.23 |
5.96 |
9.53 |
200-PSSA-AlCl3 4.8 used (after 5 cycles), considering mass change |
3.7 |
0.66 |
<1.41 |
61.68 |
6.91 |
11.02 |
To further study the potential deactivation of the catalyst, the filtrates after the first and fifth cycles were also analyzed by ICP-OES. While the Al and Cl contents were <0.00078 ppm and <8500 ppm after the first cycle, these were of 9 ppm and 10
900 ppm after the fifth one. Table 6 shows those values translated into mmol Al and mmol Cl in the filtrates. Those are negligible compared with the 0.322 mmol Al on the loaded catalyst (330 mg of 200-PSSA-AlCl3 4.8 with 2.63 wt% Al); therefore, that would not explain the loss of Al observed in Table 5. An explanation could be that an insoluble aluminum species (e.g., boehmite, AlO(OH)) was formed, and this was separated from the aqueous medium during the centrifugation step prior to ultrafiltration.72
Table 6 Al and Cl contents in filtrate after 1st and 5th cycles by ICP-OES
Cycle # |
mmol Al in filtrate |
mmol Cl in filtrate |
1 |
<4.20 × 10−7 |
<3.48 × 10−4 |
5 |
4.84 × 10−7 |
4.46 × 10−4 |
It is known that, in an aqueous medium, AlCl3 dissociates to form metal cations. Then, those metal ions are solvated by water forming complexes, such as [Al(H2O6)]3+], that can be hydrolyzed according to eqn (1) with the release of a proton.72
| [Al(H2O)6]3+ + xH2O ⇌ [Al(H2O)6−x(OH)x](3−x)+ + xH3O+ | (1) |
Among the different species that can be obtained, Tang
et al. proposed that [Al(H
2O)
4(OH)
2]
1+ was the active species when using AlCl
3 for the isomerization of glucose to fructose.
73 Although it is unclear what complexes are being formed by solvation of coordinated aluminum chloride in PSSA, it cannot be discarded that some H
+ and Al lost can be derived from those.
Techno-economic analysis.
The process was modeled for 10 MT h−1 of dry-glucose feed and 4 MT h−1 of HMF generated, which corresponds to 57 mol% of the theoretical yield from glucose (Fig. 8). The total FCIL was of $50.82M, with a major contribution of the dehydration reactors (77%) due to residence time of 4 h and organic
:
aqueous solvent ratio of 6. The operating cost was of $38.84M, where the feedstock cost was the dominating factor (67%). Detailed break-up of operating and capital costs is listed in Tables 1 and 7. The MFSP was estimated to be $1.94 per kg-HMF from an aqueous glucose feed at a price of $0.30 per kg-glucose. Earlier, Torres et al.74 conducted a techno-economic analysis of an HCl-based process and estimated an MFSP of $1.78 per kg-HMF from corn-based fructose as starting material ($0.55 per kg-fructose). The estimates of MFSP from the process here reported are similar to the selling price estimates of the process modeled by Torres et al.,74 especially when previously reported MFSP values are corrected to 2022$.75 The advantage of our process, however, is potentially lower environmental impact due to catalyst reuse. More recently, Motagamwala et al.19 estimated an MFSP of $1.71 per kg-HMF in a process where the dehydration of 25% fructose ($0.816 per kg) was performed in a water–acetone solvent system and $1.46 per kg-HMF when using 25% glucose ($0.236 per kg). Although those MFSP values seem more promising than the value here presented, it must be taken into account that our process is much simpler since pre-isomerization of glucose to fructose is not included. It is likely that including (at least a partial) feed isomerization will lower the MFSP of the PSSA-based dehydration process, similar to improvements reported by Motagamwala et al. when upstream feed isomerization was included in their HMF process.19
Table 7 Total equipment cost
Equipment |
Equipment cost ($M) |
Bare module cost |
Total module cost |
Total module cost (%) |
Dehydration reactor |
33.19 |
39.16 |
77.1 |
Distillation |
0.67 |
0.80 |
1.6 |
Heat exchangers |
4.44 |
5.24 |
10.3 |
Pumps |
1.26 |
1.49 |
2.9 |
Ultrafiltration |
— |
4.13 |
8.1 |
Total
|
|
50.82
|
|
Fig. 11 shows the results from a sensitivity analysis of the process by accounting for 10% favorable and unfavorable variations in the process due to uncertainty and market forces. Selectivity towards HMF was found to be the most sensitive parameter. The MFSP can be reduced to $1.76 per kg-HMF if the HMF yield can be improved by 10% to 62.7 mol%. This improvement can potentially be achieved by staged operation of isomerization and dehydration reactions at different temperatures, fine tuning of the catalyst, and efficient concurrent removal of products from the reaction mixture. If the feedstock price is reduced by 10%, MFSP decreases to $1.84 per kg. The price of sugar from a bio-refinery can be reduced if high-value products can be made from lignin. With solvent minimization by 10%, MFSP decreases to $1.91 per kg due to energy-savings and equipment volume reduction. Additionally, a drop in CEPCI by 10% would decrease the MFSP to $1.89 per kg.
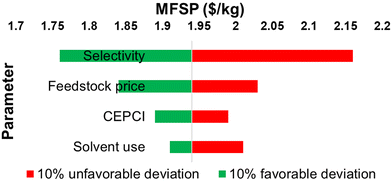 |
| Fig. 11 Sensitivity analysis of TEA for the HMF production process (base MFSP = $1.94 per kg-HMF). | |
Conclusions
We developed a series of soluble and reusable polystyrene-based catalysts containing both Brønsted and Lewis acid sites for the valorization of highly concentrated solutions of glucose to HMF. These were synthesized by successful incorporation of AlCl3 (Lewis acidity) into polystyrene sulfonic acid (Brønsted acidity) in an alcoholic medium. Among them, the 200-PSSA-AlCl3 4.0 catalyst (H+/Al mole ratio of 4) outperformed all others, likely due to an optimum combination of Lewis and Brønsted acid sites for glucose isomerization, fructose dehydration to HMF, and solubility in the reaction medium. This polymer-based catalyst presented similar catalytic activity as a combination of pure homogeneous catalysts (H2SO4 + AlCl3), although it showed two important advantages: (i) can be recovered by ultrafiltration for further use and (ii) lower generation of side products, which is beneficial from a separation point of view. 200-PSSA-AlCl3 4.8 (H+/Al mole ratio of 4.8) was effectively reused up to five times without significant loss of activity, and the techno-economic analysis of the process reported a minimum selling price of $1.94 per kg-HMF, a value similar to furan selling process reported in the literature for direct glucose conversion. Finally, this work presents an interesting proof of concept for the development of soluble and reusable multifunctional polymer catalysts, which could be expanded upon in a wide variety of new applications.
Conflicts of interest
There are no conflicts to declare.
Acknowledgements
This work was supported by the University of Toledo start-up funds and the Rocket Fuel Fund. The authors would like to thank the staff at the Center for Materials and Sensor Characterization (CMSC) at the University of Toledo for providing training on ATR and TGA. The authors are also grateful to S. J. Saluga and V. Bamunuarachchi for their invaluable contribution to this project, as well as G. Alba for the design of the graphical abstract. We would also like to acknowledge Z. Pittman, C. Kitchens, S. T. Nekkanti, F. Hauck, and F. C. F. Marcos for helping complete some experiments during the review process.
References
- J. J. Bozell, Science, 2010, 329, 522–523 CrossRef PubMed.
- F. Cherubini, Energy Convers. Manage., 2010, 51, 1412–1421 CrossRef.
- S. Lim and L. K. Teong, Renewable Sustainable Energy Rev., 2010, 14, 938–954 CrossRef.
- S. Albonetti, C. Hu and S. Saravanamurugan, ChemSusChem, 2022, 15, e202201057 CrossRef PubMed.
- M. M. Seitkalieva, A. V. Vavina, A. V. Posvyatenko, K. S. Egorova, A. S. Kashin, E. G. Gordeev, E. N. Strukova, L. V. Romashov and V. P. Ananikov, ACS Sustainable Chem. Eng., 2021, 9, 3552–3570 CrossRef.
- D. Steinbach, A. Kruse, J. Sauer and P. Vetter, Energies, 2018, 11, 645 CrossRef.
- Y. Su, H. M. Brown, X. Huang, X.-d. Zhou, J. E. Amonette and Z. C. Zhang, Appl. Catal., A, 2009, 361, 117–122 CrossRef.
- R.-J. van Putten, J. C. van der Waal, E. de Jong, C. B. Rasrendra, H. J. Heeres and J. G. de Vries, Chem. Rev., 2013, 113, 1499–1597 CrossRef.
- T. Wang, M. W. Nolte and B. H. Shanks, Green Chem., 2014, 16, 548–572 RSC.
- Y. Wang, C. A. Brown and R. Chen, AIMS Microbiol., 2018, 4, 261–273 Search PubMed.
-
T. Werpy and G. Petersen, Top Value Added Chemicals from Biomass: Volume I -- Results of Screening for Potential Candidates from Sugars and Synthesis Gas, National Renewable Energy Lab., Golden, CO (US), United States, 2004 Search PubMed.
- S. K. Burgess, J. E. Leisen, B. E. Kraftschik, C. R. Mubarak, R. M. Kriegel and W. J. Koros, Macromolecules, 2014, 47, 1383–1391 CrossRef.
- J. M. R. Gallo, D. M. Alonso, M. A. Mellmer and J. A. Dumesic, Green Chem., 2013, 15, 85–90 RSC.
- J. He, H. Li, S. Saravanamurugan and S. Yang, ChemSusChem, 2019, 12, 347–378 CrossRef.
- C. Wang, L. Zhang, T. Zhou, J. Chen and F. Xu, Sci. Rep., 2017, 7, 40908 CrossRef PubMed.
- A. Al Ghatta, J. D. E. T. Wilton-Ely and J. P. Hallett, Green Chem., 2021, 23, 1716–1733 RSC.
- R. Huang, W. Qi, R. Su and Z. He, Chem. Commun., 2010, 46, 1115–1117 RSC.
- I. Jiménez-Morales, A. Teckchandani-Ortiz, J. Santamaría-González, P. Maireles-Torres and A. Jiménez-López, Appl. Catal., B, 2014, 144, 22–28 CrossRef.
- A. H. Motagamwala, K. Huang, C. T. Maravelias and J. A. Dumesic, Energy Environ. Sci., 2019, 12, 2212–2222 RSC.
- L. Zhang, G. Xi, Z. Chen, Z. Qi and X. Wang, Chem. Eng. J., 2017, 307, 877–883 CrossRef CAS.
- T. Dallas Swift, H. Nguyen, A. Anderko, V. Nikolakis and D. G. Vlachos, Green Chem., 2015, 17, 4725–4735 RSC.
- S. Jia, Z. Xu and Z. C. Zhang, Chem. Eng. J., 2014, 254, 333–339 CrossRef CAS.
- M. Li, W. Li, Y. Lu, H. Jameel, H.-m. Chang and L. Ma, RSC Adv., 2017, 7, 14330–14336 RSC.
- F. Menegazzo, E. Ghedini and M. Signoretto, Molecules, 2018, 23, 2201 CrossRef PubMed.
- G. Portillo Perez, A. Mukherjee and M.-J. Dumont, J. Ind. Eng. Chem., 2019, 70, 1–34 CrossRef CAS.
- J. Tang, L. Zhu, X. Fu, J. Dai, X. Guo and C. Hu, ACS Catal., 2017, 7, 256–266 CrossRef CAS.
- Z.-L. Xu, X.-Y. Wang, M.-Y. Shen and C.-H. Du, Chem. Pap., 2016, 70, 1649–1657 CAS.
- Y. Yang, C. Hu and M. M. Abu-Omar, J. Mol. Catal. A: Chem., 2013, 376, 98–102 CrossRef CAS.
- X. Zhang, P. Murria, Y. Jiang, W. Xiao, H. I. Kenttämaa, M. M. Abu-Omar and N. S. Mosier, Green Chem., 2016, 18, 5219–5229 RSC.
-
S. Kalidindi, MS thesis, The University of Toledo, 2017 Search PubMed.
- T. C. Acharjee and Y. Y. Lee, Environ. Prog. Sustainable Energy, 2018, 37, 471–480 CrossRef CAS.
- B. Agarwal, K. Kailasam, R. S. Sangwan and S. Elumalai, Renewable Sustainable Energy Rev., 2018, 82, 2408–2425 CrossRef CAS.
- I. Agirrezabal-Telleria, I. Gandarias and P. L. Arias, Catal. Today, 2014, 234, 42–58 CrossRef CAS.
- S. M. Al-Amsyar, F. Adam and E.-P. Ng, Surf. Interfaces, 2017, 9, 1–8 CrossRef CAS.
- V. Choudhary, A. B. Pinar, R. F. Lobo, D. G. Vlachos and S. I. Sandler, ChemSusChem, 2013, 6, 2369–2376 CrossRef CAS.
- V. Degirmenci, E. A. Pidko, P. C. M. M. Magusin and E. J. M. Hensen, ChemCatChem, 2011, 3, 969–972 CrossRef CAS.
- S. Despax, B. Estrine, N. Hoffmann, J. Le Bras, S. Marinkovic and J. Muzart, Catal. Commun., 2013, 39, 35–38 CrossRef CAS.
- Q. Guo, L. Ren, S. M. Alhassan and M. Tsapatsis, Chem. Commun., 2019, 55, 14942–14945 RSC.
- Q. Hou, M. Zhen, L. Liu, Y. Chen, F. Huang, S. Zhang, W. Li and M. Ju, Appl. Catal., B, 2018, 224, 183–193 CrossRef CAS.
- F. Huang, Y. Su, Y. Tao, W. Sun and W. Wang, Fuel, 2018, 226, 417–422 CrossRef CAS.
- C. M. Lew, N. Rajabbeigi and M. Tsapatsis, Ind. Eng. Chem. Res., 2012, 51, 5364–5366 CrossRef CAS.
- M. Ohara, A. Takagaki, S. Nishimura and K. Ebitani, Appl. Catal., A, 2010, 383, 149–155 CrossRef CAS.
- J. E. Romo, N. V. Bollar, C. J. Zimmermann and S. G. Wettstein, ChemCatChem, 2018, 10, 4805–4816 CrossRef.
- J. Siqueira Mancilha Nogueira, J. P. Alves Silva, S. I. Mussatto and L. Melo Carneiro, Energies, 2020, 13, 655 CrossRef.
- Q. Xu, Z. Zhu, Y. Tian, J. Deng, J. Shi and Y. Fu, BioResources, 2014, 9, 303–315 CAS.
- Z. Xue, M.-G. Ma, Z. Li and T. Mu, RSC Adv., 2016, 6, 98874–98892 RSC.
- Y. Zhao, K. Lu, H. Xu, L. Zhu and S. Wang, Renewable Sustainable Energy Rev., 2021, 139, 110706 CrossRef CAS.
-
I. Omodolor, PhD dissertation, The University of Toledo, 2022 Search PubMed.
- G. Tsilomelekis, M. J. Orella, Z. Lin, Z. Cheng, W. Zheng, V. Nikolakis and D. G. Vlachos, Green Chem., 2016, 18, 1983–1993 RSC.
-
M. Marafi, A. Stanislaus and E. Furimsky, in Handbook of Spent Hydroprocessing Catalysts, ed. M. Marafi, A. Stanislaus and E. Furimsky, Elsevier, 2nd edn, 2017, pp. 67–140, DOI:10.1016/B978-0-444-63881-6.00004-4.
- N. Alonso-Fagúndez, V. Laserna, A. C. Alba-Rubio, M. Mengibar, A. Heras, R. Mariscal and M. L. Granados, Catal. Today, 2014, 234, 285–294 CrossRef.
- M. L. Granados, A. C. Alba-Rubio, I. Sádaba, R. Mariscal, I. Mateos-Aparicio and Á. Heras, Green Chem., 2011, 13, 3203–3212 RSC.
- X. Qian, J. Lei and S. R. Wickramasinghe, RSC Adv., 2013, 3, 24280–24287 RSC.
- A. Vu, S. R. Wickramasinghe and X. Qian, Ind. Eng. Chem. Res., 2018, 57, 4514–4525 CrossRef CAS.
- V. L. Magnotta and B. C. Gates, J. Polym. Sci., Polym. Chem. Ed., 1977, 15, 1341–1347 CrossRef CAS.
- B.-H. Wang, J.-S. Dong, S. Chen, L.-L. Wang and J. Zhu, Chin. Chem. Lett., 2014, 25, 1423–1427 CrossRef CAS.
-
A. C. Alba-Rubio, M. R. Coleman, S. Kalidindi, A. S. Joshi and I. S. Omodolor, Homogeneous and Reusable Superacid Polymer Catalyst for the Synthesis of 5-Hydroxymethylfurfural, From Glucose, US2020/0360910A1, 2020.
- J. N. Chheda, Y. Román-Leshkov and J. A. Dumesic, Green Chem., 2007, 9, 342–350 RSC.
- R. Gogar, S. Viamajala, P. A. Relue and S. Varanasi, ACS Sustainable Chem. Eng., 2021, 9, 3428–3438 CrossRef CAS.
-
L. U. Guangzhou Vocee Membrane Technology Co., https://www.alibaba.com/product-detail/78m2-PVDF-ultrafiltration-Hollow-fiber-UF_62100789938.html?spm=a2700.galleryofferlist.0.0.78244589YrbC8s, (accessed February 20, 2020).
-
R. Turton, J. A. Shaeiwitz, D. Bhattacharyya and W. B. Whiting, Analysis, Synthesis, and Design of Chemical Processes, Pearson, 2018 Search PubMed.
-
Chemical Engineering Essentials for the CPI Professional, ed. D. Lozowski, G. Ondrey, S. Jenkins and M. P. Bailey, June 2022 Search PubMed.
-
R. Davis, L. Tao, E. C. D. Tan, M. Biddy, G. T. Beckham, C. J. Scarlata, J. J. Jacobson, K. G. Cafferty, J. A. Ross, J. C. Lukas, D. Knorr and P. Schoen, Process Design and Economics for the Conversion of Lignocellulosic Biomass to Hydrocarbons: Dilute-Acid and Enzymatic Deconstruction of Biomass to Sugars and Biological Conversion of Sugars to Hydrocarbons, 2015 Search PubMed.
- T. Guo, J. Englehardt and T. Wu, Water Sci. Technol., 2014, 69, 223–234 CrossRef.
-
Office of Energy Efficiency & Renewable Energy, U.S. Department of Energy
.
-
U.S. Energy Information Administration, Annual Energy Outlook, 2022 Search PubMed.
- V. L. Magnotta and B. C. Gates, J. Catal., 1977, 46, 266–274 CrossRef CAS.
- D. Merche, J. Hubert, C. Poleunis, S. Yunus, P. Bertrand, P. De Keyzer and F. Reniers, Plasma Processes Polym., 2010, 7, 836–845 CrossRef CAS.
- Y. J. Pagán-Torres, T. Wang, J. M. R. Gallo, B. H. Shanks and J. A. Dumesic, ACS Catal., 2012, 2, 930–934 CrossRef.
- X. Qian, Top. Catal., 2012, 55, 218–226 CrossRef CAS.
- R.-J. van Putten, J. N. M. Soetedjo, E. A. Pidko, J. C. van der Waal, E. J. M. Hensen, E. de Jong and H. J. Heeres, ChemSusChem, 2013, 6, 1681–1687 CrossRef CAS.
- A. M. Norton, H. Nguyen, N. L. Xiao and D. G. Vlachos, RSC Adv., 2018, 8, 17101–17109 RSC.
- J. Tang, X. Guo, L. Zhu and C. Hu, ACS Catal., 2015, 5, 5097–5103 CrossRef CAS.
- A. I. Torres, M. Tsapatsis and P. Daoutidis, Comput. Chem. Eng., 2012, 42, 130–137 CrossRef CAS.
-
https://tradingeconomics.com/united-states/inflation-cpi)
.
Footnotes |
† Electronic supplementary information (ESI) available. See DOI: https://doi.org/10.1039/d2cy01619b |
‡ Equal contribution. |
§ Current affiliation: Department of Chemical and Biological Engineering, Tufts University, Medford, MA 02155, USA. |
¶ Current affiliation: Department of Chemical and Biomolecular Engineering, Clemson University, Clemson, SC 29634, USA. |
|
This journal is © The Royal Society of Chemistry 2023 |
Click here to see how this site uses Cookies. View our privacy policy here.