DOI:
10.1039/D3GC03479H
(Critical Review)
Green Chem., 2023,
25, 9644-9658
Recycling and recovery of fiber-reinforced polymer composites for end-of-life wind turbine blade management
Received
14th September 2023
, Accepted 2nd November 2023
First published on 7th November 2023
Abstract
The 3R (reuse, recycling, and recovery) waste management of wind turbine blades (WTBs) is becoming a popular subject, since it has a great practical significance in the disposal of the large numbers of upcoming end-of-life WTBs. Repurposing or reuse is a priority option, but the disposal of end-of-life WTBs on a large scale is a great challenge. Recycling or recovery is considered a priority for effectively dealing with end-of-life WTBs. This review focuses on the progress and challenges in the recycling and recovery of end-of-life WTBs, which are mainly composed of fiber-reinforced polymer composites. Among the commonly-used recycling methods, one advantage of thermal recycling processes is their tolerance of contaminated material. Thermal recycling processes can also effectively treat various polymer composites on a large scale. In particular, pyrolysis and cement kiln co-processing currently show the highest potential in treating end-of-life WTBs in commercial applications. In addition, chemical recycling processes such as solvolysis are promising methods that can achieve the closed-loop recovery of monomers and high-quality fibers, if green and recyclable solvents as well as mild reaction processes can be developed. Importantly, the life cycle management (LCM) of WTBs ending with solvolysis recycling is identified as the most circular and low-carbon solution. The recycling and recovery of end-of-life WTBs have been developed at an initial stage. Although a number of commercial applications have been achieved, most of these projects are built on extensive methods, focusing on mechanical recycling and cement kiln co-processing. This review will guide researchers to make more effort in the recycling of end-of-life WTBs, covering the reuse of gas and oil products as fuels for sustaining thermal processes and the development of green closed-loop recycling processes.
1. Introduction
1.1. End-of-life WTB production
Wind energy is an important renewable and clean energy for reducing greenhouse gas emissions, which are mostly caused by the consumption of fossil fuels.1 However, large amounts of waste will be produced during the manufacture and utilization of wind power equipment.2 China has become the world's largest wind power market. In 2021, China installed 30.7 GW of new onshore wind capacity and 16.8 GW of offshore wind capacity, accounting for around 67% and 80% of global new installations, respectively.3 Since they are limited by the 20-year design life of wind turbines,4,5 the earliest batch of wind turbines installed in China will soon be retired. It is estimated that around 85
000 tons of end-of-life wind turbine blades (WTBs) will be produced in China by 2050.6 How to dispose of discarded blades on a large scale has become a significant problem restricting the sustainable development of the wind power industry in China and all over the world.7
1.2. WTB components
The structure and main components of commonly-used WTBs are displayed in Fig. 1. The WTBs are composed of three parts from the root to the tip, which are the inner, middle and outer.3 The root of the fan blade is a cylinder structure, which is pressed by glass-fiber-reinforced resin, and the midspan and tip of the blade are stacked in a “sandwich” structure. The main beam of the fan blade is made of a composite material with high strength, and the front and back edges and web plates are made of a sandwich material with a “sandwich” structure. The sandwich structure usually consists of two thin plates holding a lightweight core material, which is bonded together by an adhesive (Fig. 1a). The panels are usually made of composite materials, and the core is usually made of lightweight materials, such as balsa wood and polyvinyl chloride.8 WTBs are mainly composed of a polymer (e.g., epoxy or polyester resin) composite reinforced with glass fiber (GF), carbon fiber (CF), and their combinations, which are lightweight with a cross-linked matrix material structure resulting in high fatigue resistance and mechanical strength (Fig. 1b).8 Usually, WTBs made of composite materials include 60–70 wt% reinforcing fibers and 30–40 wt% polymer matrix. Additionally, there is approximately 9 wt% foam core and adhesive, and 5 wt% metals.9 In addition to the composites being virtually impossible to separate for recycling due to the cross-linking that occurs between the resin and fiber during curing, the GF is considered a low value material, thus making the incentives for recycling even less attractive.10
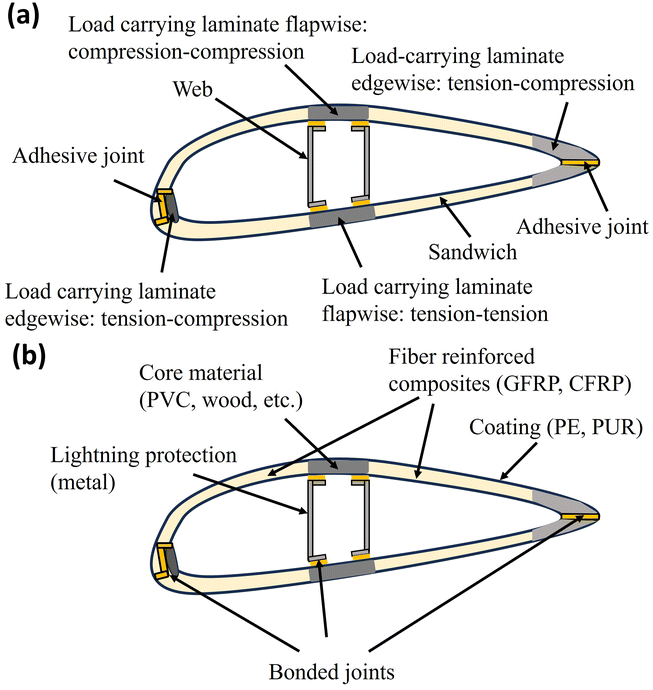 |
| Fig. 1 Schematic diagrams of (a) the structure and (b) the main components of commonly-used WTBs. | |
1.3. End-of-life WTB management
The flow of end-of-life WTBs tracks the initial sequence of installation, with early growth in the EU followed by the United States, China, and other regions.11 So far, end-of-life WTBs have been disposed of mainly in landfill sites or incinerators,9 involving a significant loss of resources and causing environmental impacts. Alternative end-of-life management solutions for WTBs have been widely explored,12 from repurposing solutions (reusing a product or its parts for applications other than the original13) to recycling (by mechanical, thermal, and chemical methods)14 or recovery (by cement kiln), by incorporating circular economy criteria15,16 of narrowing (using fewer resources), slowing (using resources for a longer time) and closing (recovering resources) resource loops.17 End-of-life WTB management was first proposed in the EU.18,19 The EU has strictly prohibited the disposal of end-of-life WTBs by land-filling. A hierarchical order of waste management (i.e., prevention, reduction, refurbishment, repurposing, recycling, recovery, and disposal) is suitable for the end-of-life management of WTBs (as illustrated in Fig. 2).20 A variety of potential technological solutions have been identified to drive the wind energy industry towards more sustainable practices, which could come from aspects of engineering, the development of emerging materials, and the implementation of recycling technologies. The waste management hierarchy shows high potential for sustainable development and resource efficiency using a top-down strategy. The main goal of the waste hierarchy is to facilitate the selection of options to deliver the optimal overall environmental benefits.16 Therefore, the 5R waste hierarchy can serve as a template to provide different potential opportunities to overcome the potential environmental crisis that results from the disposal of end-of-life WTBs.21
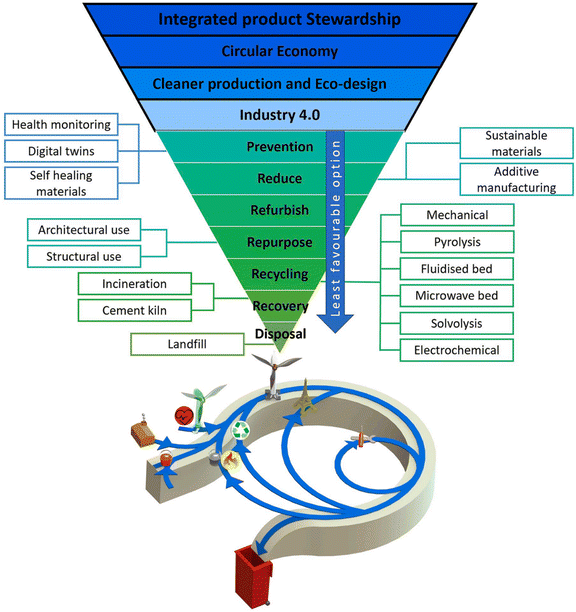 |
| Fig. 2 Integrated multilevel product stewardship framework for WTBs including circular economy, cleaner production/eco-design, industry 4.0, and the 5R waste management hierarchy. Reproduced from ref. 20 with permission from Elsevier, copyright [2022]. | |
Designing out waste and keeping products and materials in use at the highest possible value are the core principles of a circular economy, which aims to preserve resource functionality and value by recovering products and materials.22 In the waste management hierarchy, the 3R (reuse, recycling, and recovery) management of end-of-life WTBs is becoming a popular subject, since the disposal of the large amounts of upcoming end-of-life WTBs has great practical significance. Most value is preserved when the product or material remains close to its original state.23 Owing to good techno-economic feasibility, repurposing solutions through reusing the waste composite material to make a new product are a promising way to achieve the cascade utilization of end-of-life WTBs.24–27 However, the solid structural characteristics limit their repurpose or reuse. For example, taking advantage of the long length, WTBs can be lined up with overlapping tips and used as property walls, parts of a wall or cattle fence, land bridges over highways for wildlife, sound walls, pedestrian and bike ways, urban furniture, or parking lot shade shelters.28 Therefore, repurposing is a priority for consideration, but there are big challenges in the disposal of end-of-life WTBs on a large scale. Recycling or recovery is considered an important way in which end-of-life WTBs can be effectively dealt with. The following sections summarize the current progress and future challenges in the recycling and recovery of end-of-life WTBs composed of fiber-reinforced polymer composites.
2. Recycling
The commonly-used methods for recycling fiber-reinforced polymer composites mainly include mechanical recycling, thermal recycling and chemical recycling as illustrated in Fig. 3. Mechanical recycling is a mature technology that has been widely used for the recovery of raw materials from polymer composites. Mechanical processes such as shredding, crushing, and milling are used to reduce the size of large components and parts to produce a fibrous or powder product for reuse.29 Thermal recycling processes (e.g., pyrolysis) are used for treating fiber-reinforced polymer composites to produce fuels and fibers.30 Compared with mechanical and chemical recycling processes, one advantage of thermal recycling processes is their tolerance of contaminated material.30 Moreover, thermal recycling processes can effectively deal with various polymer composites on a large scale. Chemical recycling involves the depolymerization of polymers using chemical dissolution reagents. The outputs of chemical recycling processes of polymer composites are fibers (CF or GF) and the depolymerized matrix in the form of monomers or petrochemical feedstock.20 Recent developments in the recycling of polymer composites of end-of-life WTBs are summarized below.
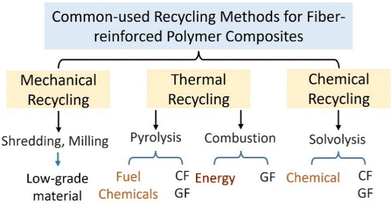 |
| Fig. 3 Commonly-used recycling methods for fiber-reinforced polymer composites. | |
2.1. Mechanical recycling
End-of-life WTBs often need to be pretreated by mechanical processes such as shredding, crushing, and milling before recycling and recovery because of their heavy weight, large volume, and high strength. They can be mechanically treated to produce small pieces, particles or powders with different sizes, which are determined by the further applications. Mechanical recycling processes are simple and mature technologies that will not change the chemical properties of end-of-life WTBs for direct reuse (as illustrated in Fig. 4). In general, WTBs are made of fiber-reinforced polymer composites, which have high strength and good mechanical performances, even at end-of-life. Therefore, decommissioned WTBs can be cut directly by the method of line sawing or circular sawing. Line sawing cuts the WTBs by enwinding a diamond-coated steel wire onto the blade, which can be used for cutting WTBs of all sizes. This process generates less dust, the incision is smooth, and the outline is clear. Diamond circular saws have a wide range of sizes, from hand-held to hydraulic drive controlled to 2 m in diameter. Suitable circular saws can be selected according to the blade sizes. Circular saws can independently cut in various parts of the WTBs, but the blades need to be cut multiple times to get the ideal shape, thus generating a lot of dust in different sections.31
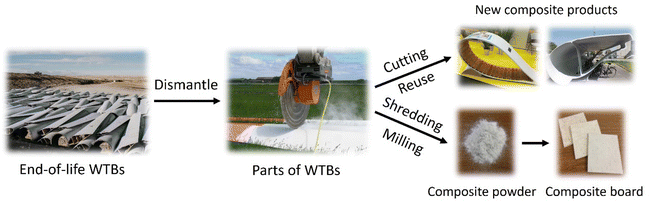 |
| Fig. 4 Mechanical recycling processes of end-of-life WTBs. | |
WTBs can be cut into smaller composite materials with different shapes for various applications depending on the different parts. Superuse Studios has spearheaded several projects to repurpose WTBs into urban furniture, using them to design playgrounds, bus shelters, public seating and signposts for recycling centers.32 The widespread application of the structural properties of the blades shows that they can be reused while also replacing the materials originally used to build these structures. The City Furniture in Aalborg, Denmark, also uses a similar blade component as a bicycle-shed material.33 These projects have specific use requirements, and the consumption of blades is small, so it is still difficult to recycle end-of-life WTBs on a large scale. When the blades are cut, the generated scraps and particles can be further crushed and recycled for building materials according to their sizes.34,35Table 1 shows the mechanical recycling processes of end-of-life WTBs for various applications according to different parts and different sizes. When the composite material is crushed to 10 mm-50 μm using a high-speed mill, air, gravity or vibration can be used for the separation of the resin and fiber.36,37 The fiber can be reused, but the surface of the crushed fiber is attached to the unseparated resin, leading to a significant degradation of the mechanical properties.38 Therefore, much effort has been made to reuse the polymer composites (e.g., glass fiber-reinforced polymer composite) in concrete,39–41 since this is a way to recycle WTBs on a large scale.
Table 1 Mechanical recycling processes of end-of-life WTBs for various applications according to different parts and different sizes
Blade part |
Cutting method |
Product shape |
Component applications |
Root |
Circular saw |
Column |
Sewer pipe embedded fittings, mechanized shaftmouth platform, etc. |
Central |
Line saw |
Plane |
Skateboarding, park bench, landscape railing, etc. |
Front |
Circular saw |
Entire |
Landscape-sculpture design, sign plates, etc. |
Scraps |
Crushing |
Particles |
Filler, building material, light cement floor, etc. |
Particle size |
Potential applications |
>25 mm |
Filler for agricultural floor, light cement board, etc. |
3–9 mm |
Cover material and acoustic insulating material, e.g., roofing asphalt and reinforcing agent for paving material |
10 mm–50 μm |
Separation of resin and fiber (fiber reuse) |
In general, mechanical processing is appropriate for the recycling of composite materials in end-of-life WTBs. However, other components, such as PVC, balsa wood, and polyurethane, cannot be treated effectively. Additionally, the structural characteristics of glass fiber-reinforced composites result in a poor cutting process, high energy consumption, and the production of a lot of dust and noise in the cutting process, which has a significant impact on the environment and the health of the workers. Additionally, WTBs have a concave structure and different thicknesses, so it is hard to cut them into more uniform parts. In mechanical processing, there are also widespread problems such as dust and noise emissions being not up to standard, illegal emissions by enterprises, and low economic benefits, which result in low recognition of the mechanical recycling of end-of-life WTBs by the public. Therefore, it is necessary to develop intelligent cutting and crushing equipment and scraps to building materials technology with the aim of maximizing the daily processing capacity and reducing the dust emissions.
2.2. Thermal recycling
Thermal processes such as pyrolysis and combustion are mature technologies for the large-scale recycling of end-of-life WTBs. Through the pyrolysis process, polymer composites and other organic components can be efficiently converted into valuable fuels, chemicals and fibers (e.g., GF, CF).42 Through the combustion process, polymer composites can be converted into a large amount of heat (released from the combustion of the polymer) and fiber (e.g., GF).
Pyrolysis has attracted much attention as a sustainable waste upcycling process.43 In our previous work, we found that pyrolysis has a high potential for the recycling of various types of waste, even including polymer composites for recovering fuels and materials.44–47 Pyrolysis has recently been considered as a promising option for recycling end-of-life WTBs.5 Pyrolysis has been proven to be more successful at recovering WTBs with a high yield of GF48 while requiring less energy to degrade the polymer matrix in composites than other techniques.35 Additionally, pyrolysis does not need complex pretreatments, such as shredding and disassembly operations.49 In general, end-of-life WTBs are first dismantled and cut into composite scraps according to the requirements of thermal recycling. The pyrolysis process in an oxygen-free or anoxic environment can decompose the polymer matrix into pyrolysis gas composed of alkanes, olefins and syngas, and residual fibers, metals, coke and other solid products, each of which can be further reused after separation.50 The pyrolysis process is normally performed in different types of reactors such as fixed-bed reactors, screw reactors, rotary kilns, and fluidized-bed reactors.42 As illustrated in Fig. 5, fixed- and fluidized-bed reactors have been widely developed for the pyrolysis recycling of WTBs. Compared with fixed-bed pyrolysis, fluidized-bed pyrolysis shows a lower technological readiness level (TRL) and a higher operation cost. Furthermore, fluidized-bed pyrolysis has a higher requirement of the composite (e.g., small particle size).16
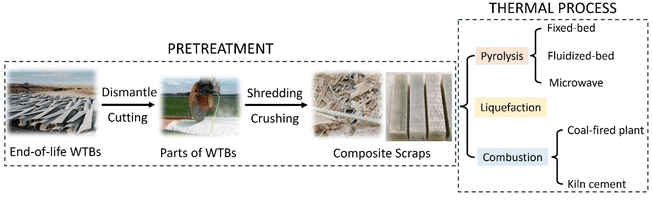 |
| Fig. 5 Thermal recycling processes of end-of-life WTBs. | |
In addition to the reactor type, the characteristics, kinetics and product distributions of end-of-life WTB pyrolysis have been investigated mostly on the lab scale.51–55
The pyrolysis temperature, as the most important parameter, is 450–700 °C for end-of-life WTBs, depending on the resin type. In particular, polyester resins decompose at 400–450 °C, while epoxy resins decompose at 500–550 °C.56
A higher pyrolysis temperature can destroy the fiber, making it difficult to replace the original fiber material. Generally, the pyrolysis temperature of WTBs is controlled at 500–550 °C. Although the properties of the residual GF are reduced by more than 50% compared with the original fiber, the pyrolysis process is still the best method to completely retain the tensile strength of the GF. Since the matrix material is pyrolyzed into a variety of simple chemical compounds, the composites can be treated with different matrix materials, containing paint, adhesives or hybrid fibers. Torres et al.57 studied the effect of temperature on the composite pyrolysis. When the pyrolysis temperature was above 400 °C, the products were not obviously affected, and the liquid products were mainly C5–C20 aromatic compounds. Yun58 and Giorgini59et al. studied the pyrolysis characteristics of fiber-reinforced resins at 600–1000 °C. It was found that the main components of the gas products included H2, CH4, CO and CO2, while the main components of the liquid products included benzene, toluene and ethylbenzene. Chen et al.51 recently investigated the characteristics, kinetics and product distribution of the pyrolysis of end-of-life WTBs. It was also found that the pyrolysis process of WTBs can occur with less energy consumption. The carbon chain distribution of the pyrolysis products was mostly C9–C16 compounds (48.97–72.73%), including phenolic compounds, alcohols, ketones and carboxylic acids. As illustrated in Fig. 6, high-temperature pyrolysis can promote the reactions of decarboxylation and cyclization. Furthermore, a high temperature and long residence time can enhance the production of aromatics and furans. Low-temperature pyrolysis can contribute to the selective recovery of phenols (e.g., bisphenol A). To date, the pyrolysis mechanisms of the composites in end-of-life WTBs have been widely studied on a small scale or using pure composite materials. Owing to the complex components of end-of-life WTBs, more research should be carried out on a large scale.
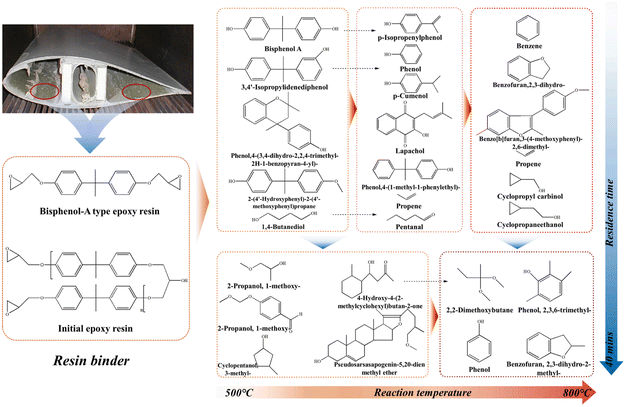 |
| Fig. 6 Pyrolysis conversion pathway of resin binder and its change with temperature and residence time. Reproduced from ref. 51 with permission from Elsevier, copyright [2023]. | |
The mechanical properties of GF can be significantly reduced after pyrolysis, but its thermal conductivity is comparable to commercial thermal insulation materials.42 Moreover, the GF recovered from the pyrolysis of end-of-life WTBs is suitable for heat insulation and sound insulation materials. Therefore, the pyrolysis process can completely dispose of end-of-life WTBs, and has the advantages of capacity reduction and resource recovery. However, the economic benefit of the pyrolysis process of WTBs is low due to the high treatment cost (e.g., high energy consumption) and the complex pyrolysis products, which make the development of pyrolysis recycling of WTBs a big challenge. To reduce the energy consumption of the pyrolysis process, some emerging heating methods such as microwave-assisted pyrolysis,60 photothermal pyrolysis,61 and liquefaction62,63 have been developed for recycling end-of-life WTBs. In particular, microwave-assisted pyrolysis reactors use high-frequency microwaves for heating owing to the advantages of rapid and uniform heating of the feedstock and facile control of the pyrolysis temperature.64,65 For example, the energy demands of the conventional and microwave-assisted pyrolysis of fiber-reinforced polymer composites have been reported to be approximately 21.2 MJ kg−1 (ref. 9) and 10 MJ kg−1,66 respectively. However, microwave heating requires external resources for electricity and mass flow control due to the rapid reaction rate.67 These emerging pyrolysis processes show good performances in the recycling of end-of-life WBs, but they have lower TRL and higher apparatus cost, limiting their large-scale applications.
Pollutant emission is another problem for the thermal processing of end-of-life WTBs. Additionally, other fuels (e.g., coal) can be used directly or indirectly to improve the thermal recycling efficiency of WTBs.68,69 Cheng et al.68 proved that the resin matrix of WTBs could be carbonized and then oxidized by heating with flue gas. The GF was finally recycled. When WTBs were pyrolyzed at 420–450 °C for 5–6 h, the purity of the GF was >99% and its tensile strength decreased <10% compared with the original fiber. With the increase of the pyrolysis temperature, the purity of the GF increased while its tensile strength decreased. In coal-fired power plants, the flue gas after dust removal was sent to a furnace for the pyrolysis of WTBs. The tail gas could be transported to the boiler furnace for complete combustion and then purified by the existing pollutant purification system. The proposed thermal co-processing of WTBs and coal is a current alternative method for recovering the energy and fiber material (e.g., GF), because existing coal-fired plants equipped with a pollutant purification system can be adopted. In addition, organic components (e.g., resin) in WTBs can be converted into gas, oil and fiber (e.g., GF) products via pyrolysis. Moreover, the gas and oil products can be recycled and upgraded into fuels to self-sustain the pyrolysis process (as illustrated in Fig. 7), thus greatly reducing the cost of the pyrolysis recycling process.
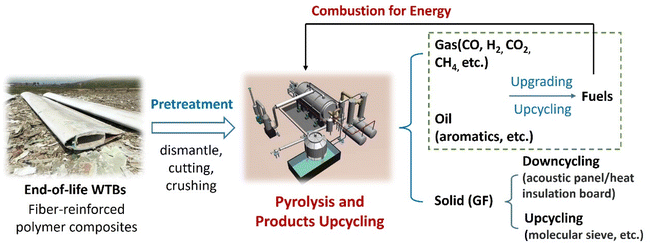 |
| Fig. 7 Integrated pyrolysis and combustion process for the energy self-sustaining recycling of end-of-life WTBs. | |
2.3. Chemical recycling
Chemical recycling, also known as solvolysis, is considered a promising WTB-recycling method, which can degrade and dissolve the resin in composites into monomers, oligomers, or other substances by using solvents with or without catalyst, finally producing useful chemicals and recovering clean fibers. Chemical recycling is normally carried out in super- and subcritical fluids under mild conditions. Under super- and subcritical conditions, the recycling process has a high energy consumption, only carbon fibers are recovered, and the degradation products of the resin are complex.70–72 Recently, Tian et al.73 summarized the chemical recycling methods (e.g., oxidation, solvolysis, and alcoholysis) for carbon fiber reinforced composites (CFRCs). Chemical recycling can selectively depolymerize specific resin bonds to achieve controllable degradation. Epoxy resin matrix is degraded into monomers or oligomers, and the carbon fibers can be recycled. Zhao et al.74 summarized the recovery of epoxy thermosets and their composites. It was highlighted that application-oriented chemical recycling should be developed based on selective degradation and effective reconstruction.
In general, the solvolysis recycling process involves the depolymerization of the thermosets in the composites of end-of-life WTBs.75 Then, each component in the composites can be easily separated, recycled and reused. The solvent is normally water, glycol, or ketone.35 After mechanical processing, the pretreated blade is dissolved by adding chemical reagents, and the GF can be recovered after the depolymerization of the resin. Under the effects of temperature and pressure, the solvent diffuses into the composites, breaking specific bonds in the resin, thus eliminating the cross-binding between the resin and the fiber. The chemical dissolution process can recover the fiber and the monomer from the resin.11,75 Piñero-Hernanz et al.76,77 pointed out that the dissolution reaction of the resin is an unstable process. The chemical reagent first diffuses and then reacts on the fiber surface. The small molecule products after bond breaking are dissolved in the solvent. During the depolymerization process, the thickness of the resin layer decreases continuously until it is completely separated from the fiber, so that the fiber that is insoluble in the solvent can be recovered. The recovered fibers retain 85–99% of the strength of the original fibers. The solvolysis process can avoid the complete destruction of the fibers in the composites, and the strength retention rate of the recovered fibers is related to the mild conditions. The recovery rate of GF can reach 90%. Because the chemicals used in the solvolysis processes may pollute the environment, there are greater environmental risks than for mechanical and thermal recycling processes. The solvolysis process is usually carried out under high temperature and pressure conditions, resulting in the construction of industrial chemical waste recycling sites and demonstration projects are very difficult. In addition, the solvolysis recycling process is relatively complex and expensive, limiting its application on a large-scale. Therefore, much attention has been paid to the development of efficient, green and closed-loop solvolysis processes for the recycling of the composites in end-of-life WTBs,78–82 mostly focusing on the use of green or recyclable solvents, efficient and low-cost catalysts, and mild reaction conditions. Recently, the journal Nature reported a metal-catalyzed protocol for recovering the polymer building block bisphenol A and intact fibers from epoxy resin composites.83 A ruthenium (Ru)-catalyzed, dehydrogenation/bond cleavage/reduction cascade disconnects the C(alkyl)–O bonds of the most common linkages of the polymer. It was found that this methodology could be applied to relevant unmodified amine-cured epoxy resins as well as commercial composites such as end-of-life WTBs (Fig. 8). The results demonstrated that chemical recycling processes for thermoset epoxy resins and composites are achievable in a short time under mild conditions (e.g., relatively low reaction temperature and pressure). However, this innovative technology cannot be immediately extended because the catalytic system is not efficient enough for industrial implementation, and Ru is a rare and expensive metal, leading to high-cost recycling. Therefore, improving the efficiency of the catalytic system and developing efficient and economical catalysts are future directions to realize the industrialization of this technology.
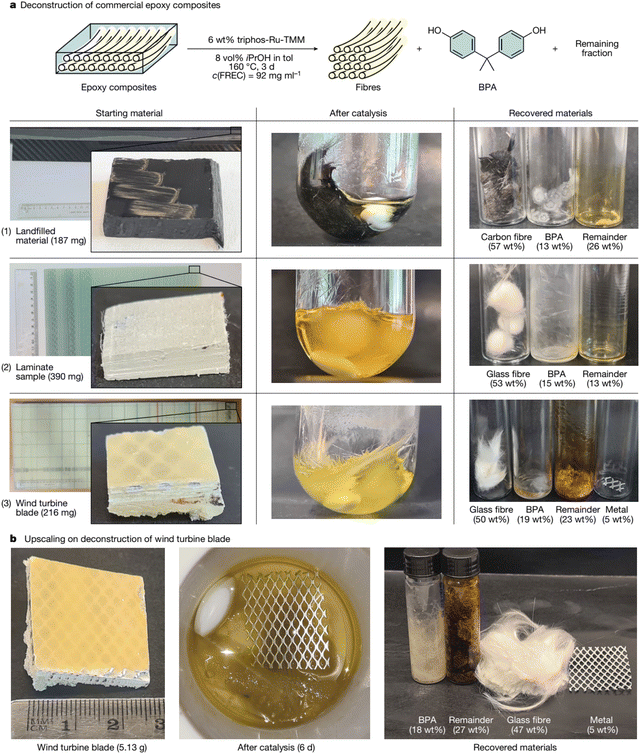 |
| Fig. 8 Recovery of BPA and fibers from commercial epoxy composites using Ru catalysis. (a) Scope of the composite samples subjected to catalysis (both length and width of composite pieces 1, 2 and 3: 1.0–1.5 cm) and (b) upscaling of deconstruction conditions for end-of-life WTBs. Reproduced from ref. 83 with permission from Springer Nature, copyright [2023]. | |
The implementation of chemical recycling with conventional heating approaches is not feasible for the recycling of GFRP composites as the cost of GF is less than that of CF. Usually, the overall cost of the recycling process should be less than the original product value. To recycle GFRP composites, an energy-efficient and low-cost recycling method is required. Compared with conventional heating, microwave heating can avoid the non-uniform degradation reaction from the outside to the inside along with heat conduction.84–87 The principle of microwave heating is that under the action of an external electromagnetic field, the polar molecules in the substance move violently to generate heat. Microwave heating enables heating of both the inside and outside of the thermosets in the degradation process and improves the reaction efficiency. Zabihi et al.85,86 used microwave heating to degrade CF and GF reinforced polymers in tartaric acid and H2O2 solvents. Due to the introduction of microwaves, the epoxy resin composite was degraded completely within 1–3 min to obtain fibers. Rani et al.87 later developed a sustainable microwave-assisted chemical recycling process to recycle GFRP composites, which was applied to end-of-life WTBs, which could be depolymerized using hydrogen peroxide and acetic acid with microwave irradiation (Fig. 9). Under the optimal conditions, the chemical solvent ratio (hydrogen peroxide/acid: 30/70, 50/50) with microwave heating (700 W, 180 s) could achieve complete degradation of the epoxy resin. In addition, the recovered GF showed 99.8% ultimate tensile strength, 93.3% Young's modulus, and 95.7% strain-to-failure compared to the virgin GF.
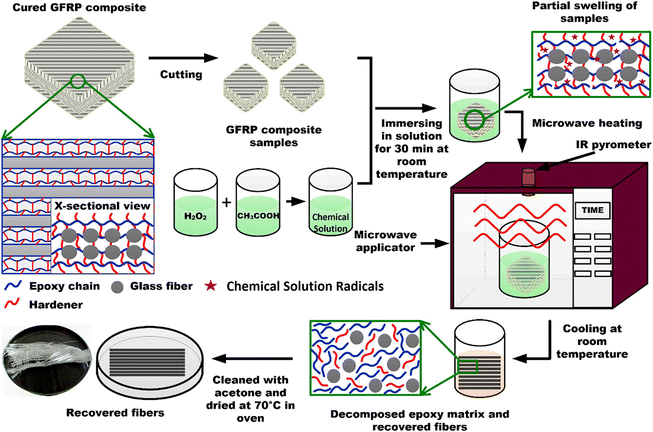 |
| Fig. 9 Schematic diagram of the microwave-assisted chemical recycling process of GFRP composites to recover GF. Reproduced from ref. 87 with permission from Elsevier, copyright [2022]. | |
3. Recovery
In general, the recovery processes of end-of-life WTBs include two pathways. First, thermal energy is recovered through incineration to supply heat or heat water to produce steam for power generation; second, WTBs are co-fired in a cement kiln, where the combustible component in the WTBs is burnt to provide heat, and GF is recovered as a raw material for producing cement clinker.20 It has also been reported that two recovery processes with a high TRL have been commercialized in the disposal of end-of-life WTBs.88
3.1. Incineration and co-incineration
Incineration involves burning the composite with air to recover energy.89 For the incineration of WTBs, they must first be dismantled, crushed, and transported; then the composites are burnt to produce ash (about 50% of the composite).90 In the case of CF composites, incineration needs proper measures to avoid the release of residual fibers into the environment.91 Despite the wide use of incineration to dispose of the composite, it is not a completely environmentally friendly process. The incineration of waste produces CO2.92 The incineration of composite materials is not always possible due to it being cost prohibitive and the GF residue causing process stoppages.93 Co-incineration is a better alternative than incineration. This process counteracts some of the disadvantages of the incineration allowing the recovery of energy and material.94 Co-incineration recovers the ash (accounting for 30–35 wt% (ref. 95)) to be used as a filler for the preparation of cement composites.96,97 In co-incineration, the energy recovered by the combustion of waste composites can also reduce the amount of coal used in the combustion furnace. This approach can aid the reduction of CO2 emissions and the minimization of the consumption of natural materials.96,98 In addition, the recovered ash rich in GF and alkaline oxides can be used in flue gas desulfurization (FGD).99
3.2. Cement kiln co-processing
Cement kiln co-processing is a promising method for treating crushed WTBs. The end-of-life WTBs are cut into smaller pieces (1.5 cm3) on site, and transported to the receiving cement plant. Then, the small pieces are crushed into particles of less than 40 mm3. After the metal components are removed, the particles are mixed with cement raw materials in a certain proportion, and fed into the kiln for burning. The combustion of the combustible component in WTBs releases heat which can be used for sintered cement, and the solid residues (e.g., GF) can be used as cement clinker raw materials.42 It has been reported that each ton of blade waste can replace 600 kg of coal fuel, equivalent to 4.16 GJ of energy.25 Moreover, inorganic materials such as GF can be reused as cement raw materials, which removes 127 kg of CO2 emissions.43 However, due to the presence of boron in some composite materials, the cement curing time may be increased if the mixing ratio is greater than 10%, so the mixing ratio of waste blades should be strictly controlled.30,39 If the waste blades stay in the high temperature area (normally 800–1500 °C) of the kiln for a long time, the combustible components can be completely burned and utilized, basically without the release of dioxins in the flue gas. Cement kiln co-processing shows high potential to be used for the disposal of end-of-life WTBs on a large scale, if the energy consumption and pollutant gas emission can be reduced. At present, some cement-related enterprises have begun to invest in the cement kiln co-processing of end-of-life WTBs. For example, Holcim has invested in a cement plant in Germany for the recycling of WTBs. The cement plant of a waste recycling management company (Geocycle) uses collaborative disposal technology to recycle WTBs and partially replace fossil fuels and other raw materials in cement production.26
4. Comparison of recycling and recovery methods
4.1. Advantages and disadvantages
The recycling and recovery methods for end-of-life WTBs are compared in Table 2. At present, mechanical processes and thermal processes (e.g., pyrolysis, kiln cement co-processing) have the advantages of high TRL and easy control, thus contributing to their commercial applications. In particular, the mechanical recycling process is a simple and mature technology that will not change the chemical properties of end-of-life WTBs for direct reuse, since WTBs made of fiber-reinforced polymer composites have high strength and good mechanical performances even at end-of-life. Due to high TRL and high efficiency, thermal recycling processes are promising alternatives for the management of end-of-life WTBs on a large scale if the energy consumption and pollutant emission can be reduced. Cement kiln co-processing can recover heat energy and GF for cement composite production, thus achieving the full utilization of the composite materials. For the future, the pyrolysis and solvolysis recycling processes are the most promising methods, since they can retain fibers (especially CF) with properties close to those of the virgin fibers. Meanwhile, the resins can be converted into high-value fuels and monomers through upcycling. In particular, the pyrolysis recycling process needs to be widely developed since it has a high TRL for the large-scale upcycling of end-of-life WTBs.
Table 2 Comparison of recycling and recovery methods for end-of-life WTBs
Method |
Advantages |
Disadvantages |
Products |
Project case |
Ref. |
Mechanical process |
High TRL (9), lower cost |
Small scale treatment, dust pollution |
Low-quality composite materials |
(1) ERCOM (Germany) and Phoenix (Canada) companies project (year 1990); (2) GENVIND (Denmark) project (year 2012–2016) |
31 and 100 |
Solvolysis |
Efficient recovery of GF and CF, less damage of GF |
Low TRL (4–5), difficult to control the reaction conditions, secondary pollution of chemical solvents, relatively high cost, small scale treatment |
GF, CF, chemicals (monomer) |
Research stage |
73
|
Pyrolysis |
Less damage of GF, high TRL (9), large-scale treatment |
Relatively high energy consumption, complex oil and gas products |
GF, CF, fuel oil and gas products |
Milled Carbon Company (England) project (year 2003) |
42 and 101 |
Incineration |
High TRL (9), facile operation |
Low combustion efficiency due to high content of GF, large amounts of ash production, toxic gas emission |
Heat energy |
Research stage |
8 and 102 |
Cement kiln co-processing |
Full utilization of end-of-life WTBs, high TRL (9), lower operation cost |
High requirement of the blade size, hard to control the ratio of the blade and cement |
Heat energy, concrete |
Holcim (Germany) and Geocycle (Canada) company projects (year 2010 and 2021) |
10 and 26 |
4.2. Techno-economic and environmental-impact assessment
Techno-economic and environmental-impact assessment is very important to select suitable technology for end-of-life WTBs management. So far, there has been a lack of a reasonable evaluation due to limited research data and industrial cases. The EU's recycling of WTBs is at an early stage. The above technologies to recycle GF and CF from end-of-life WTBs are yet to be widely available at the industrial scale and to be cost-competitive. In many cases, the recycled material cannot compete with the price of virgin materials. The price of virgin GF does not make the recovery of fibers as a standalone product economically competitive. The relative costs and values of resin composite recycling technologies have been evaluated.14 As shown in Fig. 10, mechanical grinding and cement kiln co-processing have relatively low process costs along with high TRL, which contribute to their existing applications on industrial scales. Solvolysis and pyrolysis show a high potential in the recovery of GF and CF, which are also the main products, especially CF, with relatively high values.103 Furthermore, it is envisaged that this will be an important route for the directional recovery of chemical building blocks from the entirety of composite materials through cost-effective, efficient and sustainable solvolysis. An economic analysis indicated that the recovery of constituent materials from the resin composite can be economically feasible when they can displace virgin materials in the supply chain. This feasibility is contingent on reducing labor costs, obtaining a minimal knockdown on the polymer, and maximizing the GF resale. The economic feasibility of this process will increase by 3–6 times for CF composites.35
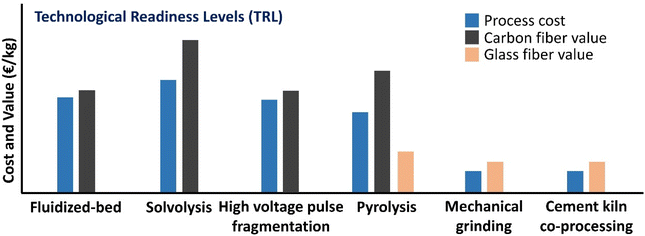 |
| Fig. 10 Relative costs and values of resin composite recycling technologies (the sizes of the bars are indicative and vary among EU recyclers using the same process due to varying process parameters such as throughput rates/capacity, temperature/pressure and retention time in the reactor).14 | |
As for the environmental impact, mechanical treatment such as cutting and grinding can produce a large amount of dust and noise, which has a great impact on the environment and the health of workers. Also, there are widespread problems such as substandard dust and noise emissions and illegal emissions by enterprises. Thermal treatment can produce large amounts of toxic gases and CO2 (greenhouse gas), so downstream gas purification systems are normally required. In particular, the recovery of energy widely through incineration processes can be efficient treatment of end-of-life WTBs, but it is not a completely environmentally friendly process. The incineration of waste releases CO2, which contributes to climate change, including toxic emissions that represent hazards to human health and the environment.20 Among these technologies, chemical treatment, especially for solvolysis, would have a high benefit for environmental impact if green solvents were developed. In the future, much effort should be given to techno-economic combined with environmental-impact assessment of WTB recycling technologies based on the entire pre- and post-treatment systems and the industrial application cases.
5. Life cycle management (LCM) of WTBs
Various methods with different advantages and disadvantages have been developed for the recycling and recovery of end-of-life WTBs. The selection of an appropriate recycling process should be carried out based on the principle of a circular economy. Furthermore, integrated processes will be considered to achieve a closed-loop, efficient and cost-effective recycling process. Therefore, an integrated analysis of the correlation between circularity performance and potential carbon footprint of the life cycle of WTBs is necessary, mainly considering different waste management alternatives to propose research innovations and recommendations for the design and sustainable management of these products.104 Recently, Diez-Cañamero et al.105 evaluated the correlation between the circular economy performance and the carbon footprint of end-of-life WTB management solutions including repurposing, grinding, solvolysis, pyrolysis, cement kiln co-processing, incineration and landfilling. The circular economy performance was analyzed by the calculation of the product circularity indicator, while the carbon footprint was determined by the life cycle assessment (LCA) using the global warming indicator and considering the management of three WTBs from cradle-to-gate as a functional unit (Fig. 11). The LCM of WTBs ending with solvolysis recycling was identified as the most circular and low-carbon solution. Though increasing material quality is key to achieving carbon savings, it should be increased by 50% in the cases of solvolysis and pyrolysis recycling to generate significant savings. To improve the circularity performance, innovations must be made in terms of reducing waste generation, prolonging the service life of WTBs and using the recovered materials through closed-loop systems to avoid downcycling processes, which lead to the reduction of environmental credits.106
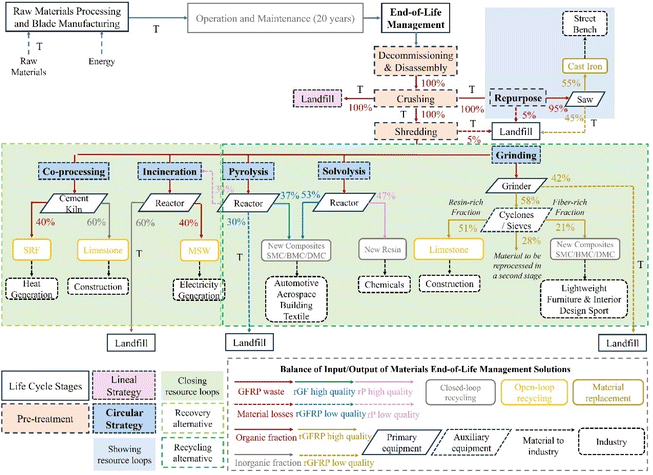 |
| Fig. 11 Main stages of the life cycle of WTBs including end-of-life management alternatives. Reproduced from ref. 105 with permission from Elsevier, copyright [2023]. | |
6. Conclusions and perspectives
Alternative management solutions for end-of-life WTBs have been widely explored, from repurposing to recycling (by mechanical, thermal, and chemical methods) or recovery (by co-incineration or cement kiln co-processing), by incorporating circular economy criteria for narrowing, slowing and closing resource loops. The 3R (reuse, recycling, and recovery) management of end-of-life WTBs has become a popular subject, since it has great practical significance in the disposal of the large amounts of upcoming end-of-life WTBs. Repurposing (reuse) is a priority option, but it is a big challenge to dispose of end-of-life WTBs on a large scale. Recycling or recovery is considered an important way in which end-of-life WTBs can be effectively dealt with. This review summarized the current progress in the recycling and recovery of end-of-life WTBs composed of fiber-reinforced polymer composites. Among the recycling methods, one advantage of thermal recycling processes is tolerance to contaminated material. Thermal recycling processes can also be used to effectively treat various polymer composites on a large scale. In particular, currently, the pyrolysis and cement kiln co-processing methods show the highest potential in efficiently dealing with end-of-life WTBs towards large-scale commercial applications. In addition, chemical recycling processes such as solvolysis are considered promising methods that can achieve the closed-loop recovery of chemical monomers and high-quality fibers, if green and recyclable solvents as well as mild reaction processes can be developed. Importantly, the LCM of WTBs ending with solvolysis recycling is identified as the most circular and low-carbon solution.
The recycling and recovery of fiber reinforced polymer composites in end-of-life WTBs have been researched and developed at an initial stage. Although a number of commercial applications have been achieved, most of these projects are built on extensive methods, focusing on mechanical recycling and cement kiln co-processing. In the future, much effort should be directed based on research recommendations. (i) Mechanical processing is an initial step prior to recycling and recovery processes due to the huge volume, specific structure, and high strength of end-of-life WTBs. Therefore, it is necessary to develop intelligent cutting and crushing equipment and scraps to building materials technology with the aim of maximizing the daily processing capacity and reducing the dust emissions.
(ii) The solvolysis process can achieve the closed-loop recovery of monomers and high-quality fibers from the polymer composites in end-of-life WTBs. It is necessary to develop green and recyclable solvents as well as mild reaction processes with the aim of reducing the secondary pollution and the operation cost.
(iii) Thermal recycling processes such as pyrolysis and co-incineration show a high potential for the recovery of energy and materials from end-of-life WTBs on a large scale. More research work should be carried out on the use of gas and oil products as fuels for self-sustaining the thermal processes with the aim of reducing the cost of the whole recycling process and further achieving on-site recycling.
(iv) The selection of an appropriate recycling process should be carried out based on the circular economy. A closed-loop, efficient and cost-effective recycling process can be achieved by rationally designing processes such as mechanical recycling integrated with thermal or chemical recycling. Therefore, an integrated analysis of the correlation between the circularity performance and carbon footprint of the life cycle of WTBs is necessary. Furthermore, on-site wind energy can be integrated to reduce the energy consumption of the recycling process.
(v) The recovered fibers (e.g., GF, CF) are normally of lower quality than the original fibers. It is necessary to urgently develop more utilization scenarios for the recovered degraded fibers. For example, recovered GF shows a decrease in mechanical performance, but has good heat conductivity and sound absorption capacity compared with commercial materials, and is suitable to be used as a heat and sound insulation material.
Conflicts of interest
There are no conflicts to declare.
References
- P. Liu, F. Meng and C. Y. Barlow, Resour., Conserv. Recycl., 2022, 180, 106202 CrossRef.
- J. Beauson, A. Laurent, D. P. Rudolph and J. P. Jensen, Renewable Sustainable Energy Rev., 2022, 155, 111847 CrossRef CAS.
-
Globle Wind Energy Council
, Global Wind Report, 2022, p. 2022.
-
J. Beauson and P. Brøndsted, Wind turbine blades: An end of life perspective. in MAREWINT: New Materials and Reliability in Offshore Wind Turbine Technology, ed. W. Ostachowicz, M. McGugan, J.-U. Schroder-Hinrichs and M. Luczak, Springer International Publishing,Cham, 2016, pp. 421–432 Search PubMed.
- M. Rani, P. Choudhary, V. Krishnan and S. Zafar, Composites, Part B, 2021, 215, 108768 CrossRef CAS.
- Y. Chen, G. Cai, L. Zheng, Y. Zhang, X. Qi, S. Ke, L. Gao, R. Bai and G. Liu, Resour., Conserv. Recycl., 2021, 169, 105533 CrossRef.
- N. Cong, Y. Song, M. Zhang and W. Wu, Environ. Impact Assess. Rev., 2023, 100, 107072 CrossRef.
- P. Liu, F. Meng and C. Y. Barlow, J. Cleaner Prod., 2019, 212, 1268–1281 CrossRef.
- A. J. Nagle, E. L. Delaney, L. C. Bank and P. G. Leahy, J. Cleaner Prod., 2020, 277, 123321 CrossRef.
- E. B. Paulsen and P. Enevoldsen, Energies, 2021, 14, 4247 CrossRef.
- A. Cooperman, A. Eberle and E. Lantz, Resour., Conserv. Recycl., 2021, 168, 105439 CrossRef.
- J. M. F. Mendoza, A. Gallego-Schmid, A. P. M. Velenturf, P. D. Jensen and D. Ibarra, Renewable Sustainable Energy Rev., 2022, 163, 112523 CrossRef.
-
L. Bank, J. F. Chen, R. Gentry, P. Leahy, A. Nagle, B. Tasistro-Hart, C. Graham, E. Delaney, F. Gough, F. Arias, G. Mullally, H. Lemmertz, J. McKinley, M. Nicholl, N. Dunphy, R. Suhail, R. Morrow and T. Al-Hadda, Re-Wind Design Atlas. 2018. https://www.re-wind.info/product/2020/8/5/re-wind-releases-its-design-atlascreative-commons-license-cc-by-nc-sa-40.
-
OGTC, 2021. Sustainable decommissioning: wind turbine blade recycling. OGCT, Aberdeen (Scotland) https://ore.catapult.org.uk/wp-content/uploads/2021/03/CORE_Full_Blade_Report_web.pdf.
- F. Blomsma, M. Pieroni, M. Kravchenko, D. C. A. Pigosso, J. Hildenbrand, A. R. Kristinsdottir, E. Kristoffersen, S. Shahbazi, K. D. Nielsen, A. K. Jonbrink, J. Li, C. Wiik and T. C. McAloone, J. Cleaner Prod., 2019, 241, 118271 CrossRef.
-
WindEurope, 2020. Accelerating Wind Turbine Blade Circularity. WindEurope, Brussels (Belgium). https://windeurope.org/wp-content/uploads/files/about-wind/reports/WindEurope-Accelerating-wind-turbine-blade-circularity.pdf.
- N. M. P. Bocken, I. de Pauw, C. Bakker and B. van der Grinten, J. Ind. Prod. Eng., 2016, 33(5), 308–320 Search PubMed.
- J. Beauson, A. Laurent, D. P. Rudolph and J. P. Jensen, Renewable Sustainable Energy Rev., 2022, 155, 111847 CrossRef CAS.
- V. Sommer and G. Walther, Waste Manage., 2021, 121, 265–275 CrossRef CAS PubMed.
- D. Martinez-Marquez, N. Florin, W. Hall, P. Majewski, H. Wang and R. A. Stewart, Resour. Conserv. Recycl. Adv., 2022, 15, 200109 Search PubMed.
- L. Mishnaevsky, Materials, 2021, 14, 1124 CrossRef CAS PubMed.
-
Ellen MacArthur Foundation, Towards the Circular Economy 1, Ellen MacArthur Foundation, 2013 Search PubMed.
-
C. A. Bakker, M. den Hollander, D. Peck and A. R. Balkenende, Circular product design; addressing critical materials through design, in Critical Materials: Underlying Causes and Sustainable Mitigation Strategies, ed. S. E. Offerman, World Scientific Publishing Co. Pts. Ltd., Singapore, 2019, pp. 179–192 Search PubMed.
- J. Joustra, Cascading composites, Jelle Joustra Res. Des., 2019 Search PubMed , https://jellejoustra.nl/?p=347. (Accessed 23 June 2021).
- J. Joustra, B. Flipsen and R. Balkenende, Resour., Conserv. Recycl., 2021, 167, 105393 CrossRef.
- K. Ruane, M. Soutsos, A. Huynh, Z. Zhang, A. Nagle, K. McDonald, T. R. Gentry, P. Leahy and L. C. Bank, Sustainability, 2023, 15, 3366 CrossRef.
- A. J. Nagle, G. Mullally, P. G. Leahy and N. P. Dunphy, J. Environ. Manage., 2022, 302, 113994 CrossRef CAS PubMed.
- R. Martini and G. Xydis, Environ. Prog. Sustainable Energy, 2023, 42, e13932 CrossRef CAS.
- D. Ayre, Curr. Opin. Green Sustainable Chem., 2018, 13, 108–112 CrossRef.
-
J. Bhadra, N. Al-Thani and A. Abdulkareem, 11 - Recycling of polymer-polymer composites, in Micro and Nano Fibrillar Composites (MFCs and NFCs) from Polymer Blends, ed. R. K. Mishra, S. Thomas and N. Kalarikkal, Woodhead Publishing, UK, 2017, pp. 263–277 Search PubMed.
- J. P. Jensen and K. Skelton, Renewable Sustainable Energy Rev., 2018, 97, 165–176 CrossRef.
- S. Job, Reinf. Plast., 2014, 58(5), 32–38 CrossRef.
- A. D. La Rosa, D. R. Banatao and S. J. Pastine,
et al.
, Composites, Part B, 2016, 104, 17–25 CrossRef CAS.
- S. H. Mamanpush, H. Li, K. Englund and A. T. Tabatabaei, Waste Manage., 2018, 76, 708–714 CrossRef CAS PubMed.
- S. Cousins Dylan, Y. Suzuki and E. Murray Robynne,
et al.
, J. Cleaner Prod., 2019, 209, 1252–1263 CrossRef.
- J. Beauson, B. Madsen, C. Toncelli, P. Brondsted and J. I. Bech, Composites, Part A, 2016, 90, 390–399 CrossRef CAS.
- R. Correia João, M. Almeida Nuno and R. Figueira João, J. Cleaner Prod., 2011, 19(15), 1745–1753 CrossRef.
- S. K. Gopalraj and T. Karki, Processes, 2020, 8(8), 954 CrossRef CAS.
- V. Revilla-Cuesta, M. Skaf, V. Ortega-Lopez and J. M. Manso, Resour., Conserv. Recycl., 2023, 198, 107160 CrossRef CAS.
- D. Baturkin, O. A. Hisseine, R. Masmoudi, A. Tagnit-Hamou and L. Massicotte, Resour., Conserv. Recycl., 2021, 174, 105807 CrossRef CAS.
- Y. Tao, S. A. Hadigheh and Y. Wei, Structures, 2023, 53, 1540–1556 CrossRef.
- W. Yang, K.-H. Kim and J. Lee, J. Cleaner Prod., 2022, 376, 134292 CrossRef.
- W. A. Wan Mahari, E. Azwar, S. Y. Foong, A. Ahmed, W. Peng, M. Tabatabaei, M. Aghbashlo, Y.-K. Park, C. Sonne and S. S. Lam, Chem. Eng. J., 2021, 421, 129749 CrossRef CAS.
- Y. Shen, R. Yuan, X. Chen, X. Ge and M. Chen, ACS Sustainable Chem. Eng., 2018, 6(7), 9086–9093 CrossRef CAS.
- Y. Shen, Waste Manage., 2018, 76, 537–543 CrossRef CAS PubMed.
- Y. Shen, X. Chen, X. Ge and M. Chen, J. Cleaner Prod., 2018, 176, 1045–1053 CrossRef CAS.
- Y. Shen, X. Chen, X. Ge and M. Chen, J. Environ. Manage., 2018, 214, 94–103 CrossRef CAS PubMed.
- R. S. Ginder and S. Ozcan, Recycling, 2019, 4, 24 CrossRef.
-
J. Koelega, Recycling Wind Turbine Blades: a Study into the Possibilities of Implementing Pyrolysis as End of Life Solution for Glass Fibre Reinforced Composties from Wind Turbine Blades in the Port of Rotterdam, MS Thesis, Industrial Ecology. Delft University of Technology and Leiden University, 2019 Search PubMed.
- S. R. Naqvi, H. M. Prabhakara and E. A. Bramer,
et al.
, Resour., Conserv. Recycl., 2018, 136, 118–129 CrossRef CAS.
- W. Chen, M. Ye, M. Li, B. Xi, J. Hou, X. Qi, J. Zhang, Y. Wei and F. Meng, J. Anal. Appl. Pyrolysis, 2023, 169, 105859 CrossRef CAS.
- Y. Wu, Z. Ge, C. Huang, Z. Zha, M. Zeng, Y. Ma, L. Sun, Z. Hou, S. Chu and H. Zhang, Waste Manage., 2023, 168, 54–62 CrossRef CAS PubMed.
- S. Yousef, J. Eimontas, K. Zakarauskas and N. Striugas, J. Anal. Appl. Pyrolysis, 2023, 173, 106100 CrossRef CAS.
- M. Xu, H. Ji, Y. Wu, J. Di, X. Meng, H. Jiang and Q. Lu, Composites, Part B, 2023, 251, 110493 CrossRef CAS.
- M. Xu, J. Di, Y. Wu, X. Meng, H. Ji, H. Jiang, J. Li and Q. Lu, Chem. Eng. J., 2023, 473, 145404 CrossRef CAS.
- G. Oliveux, L. O. Dandy and G. A. Leeke, Prog. Mater. Sci., 2015, 72, 61–99 CrossRef CAS.
- A. Torres, I. D. Marco and B. M. Caballero,
et al.
, Fuel, 2000, 79, 897–902 CrossRef CAS.
- Y. M. Yun, M. W. Seo and G. H. Koo,
et al.
, Fuel, 2014, 137, 321–327 CrossRef CAS.
- L. Giorgini, T. Benelli and L. Mazzocchetti,
et al.
, Polym. Compos., 2015, 36(6), 1084–1095 CrossRef CAS.
- L. Zhang, W. Liu, H. Jiang, X. Zhang, Y. Shang, C. Jiang, X. Wang, G. Qi, B. Li, P. Xu and J. Qiao, Compos. Sci. Technol., 2023, 231, 109824 CrossRef CAS.
- Q. Ren, Z. Lei, S. Hu, Y. Ding, L. He, S. Su, Y. Wang, L. Jiang, J. Xu and J. Xiang, J. Anal. Appl. Pyrolysis, 2023, 169, 105828 CrossRef CAS.
- S. Ge, S. Y. Foong, N. L. Ma, R. K. Liew, W. A. Wan Mahari, C. Xia, P. N. Y. Yek, W. Peng, W. L. Nam, X. Y. Lim, C. M. Liew, C. C. Chong, C. Sonne and S. S. Lam, Renewable Sustainable Energy Rev., 2020, 127, 109871 CrossRef CAS.
- H. Mumtaz, S. Sobek, M. Sajdak, R. Muzyka and S. Werle, Renewable Energy, 2023, 211, 269–278 CrossRef CAS.
- H. Mumtaz, S. Sobek, M. Sajdak, R. Muzyka, S. Drewniak and S. Werle, Energy, 2023, 278, 127950 CrossRef CAS.
- S. S. Lam, W. A. Wan Mahari, N. L. Ma, E. Azwar, E. E. Kwon, W. Peng, C. T. Chong, Z. Liu and Y.-K. Park, Chemosphere, 2019, 230, 294–302 CrossRef CAS PubMed.
-
T. Suzuki and J. Takahashi, Prediction of energy intensity of carbon fiber reinforced plastics for mass-produced passenger cars. In: Proceedings of 9th Japan International SAMPE Symposium, 2005, pp. 14–19.
- Y.-F. Huang, P.-T. Chiueh, W.-H. Kuan and S.-L. Lo, Energy, 2016, 100, 137–144 CrossRef CAS.
- G. Cheng, S. Yang, X. Wang, Z. Guo and M. Cai, Study on the recycling of waste wind turbine blades, J. Eng. Res., 2023 DOI:10.1016/j.jer.2023.100070.
- X. Xiong, L. Li, F. Chen, J. Zhang and H. Tan, J. Anal. Appl. Pyrolysis, 2022, 168, 105771 CrossRef CAS.
- Y. N. Kim, Y.-O. Kim and S. Y. Kim,
et al.
, Compos. Sci. Technol., 2019, 173, 66–72 CrossRef CAS.
- M. J. Keith, L. A. Román-Ramírez and G. Leeke,
et al.
, Polym. Degrad. Stab., 2019, 161, 225–234 CrossRef CAS.
- I. Okajima and T. Sako, Polym. Degrad. Stab., 2019, 163, 1–6 CrossRef CAS.
- Z. Tian, Y. Wang and X. Hou, New Carbon Mater., 2022, 37, 1021–1045 CrossRef CAS.
- X. Zhao, Y. Long, S. Xu, X. Liu, L. Chen and Y. Wang, Mater. Today, 2023, 64, 72–97 CrossRef CAS.
- R. Muzyka, S. Sobek, A. Korytkowska-Walach, L. Drewniak and M. Sajdak, Sci. Rep., 2023, 13, 9270 CrossRef CAS PubMed.
- R. Piñero-Hernanz, C. Dodds and J. Hyde,
et al.
, Composites, Part A, 2008, 39, 454–461 CrossRef.
- R. Piñero-Hernanz, J. García-Serna and C. Dodds,
et al.
, J. Supercrit. Fluids, 2008, 46, 83–92 CrossRef.
- H. Feng, X. Xu, B. Wang, Y. Su, Y. Liu, C. Zhang, J. Zhu and S. Ma, Composites, Part B, 2023, 257, 110677 CrossRef CAS.
- Z. Huang, Z. Deng, C. Dong, J. Fan and Y. Ren, Chem. Eng. J., 2022, 446, 137254 CrossRef CAS.
- J. Zhao, P. Liu, J. Yue, H. Huan, G. Bi and L. Zhang, Composites, Part B, 2023, 254, 110435 CrossRef CAS.
- C. Liu, W. Hong, B. Yang, C. Lin, L. Wang and C. Chen, J. Cleaner Prod., 2022, 378, 134334 CrossRef CAS.
- X. Ma, H. Xu and Z. Xu, ACS Macro Lett., 2021, 10, 1113–1118 CrossRef CAS PubMed.
- A. Ahrens, A. Bonde, H. Sun, N. K. Wittig, H. C. D. Hammershøj, G. M. F. Batista, A. Sommerfeldt, S. Frølich, H. Birkedal and T. Skrydstrup, Nature, 2023, 617, 730–737 CrossRef CAS PubMed.
- X. Zhao, W. Wang, F. Tian, W. An, S. Xu and Y. Wang, Green Chem., 2019, 21, 2487–2493 RSC.
- O. Zabihi, M. Ahmadi, C. Liu, R. Mahmoodi, Q. Li, M. R. G. Ferdowsi and M. Naebe, Sustainability, 2020, 12, 641 CrossRef CAS.
- O. Zabihi, M. Ahmadi, C. Liu, R. Mahmoodi, Q. Li and M. Naebe, Composites, Part B, 2020, 184, 107750 CrossRef CAS.
- M. Rani, P. Choudhary, V. Krishnan and S. Zafar, Resour., Conserv. Recycl., 2022, 179, 106107 CrossRef CAS.
- X. Tong, Electric Power Technol. Environ. Prot., 2023, 39, 292–298 Search PubMed.
-
B. o. E. S. a. Toxicology, et al., Waste Incineration & Public Health, National Academy Press, Washington, D.C, 2000 Search PubMed.
- R. E. Murray,
et al.
, Renewable Energy, 2019, 131, 111–119 CrossRef.
- N. Vijay, V. Rajkumara and P. Bhattacharjee, Procedia Environ. Sci., 2016, 35, 563–570 CrossRef.
- S. A. Cormier,
et al.
, Environ. Health Perspect., 2006, 114(6), 810–817 CrossRef CAS PubMed.
- A. Jacob, Reinf. Plast., 2011, 55(3), 45–46 CrossRef.
- P. A. Vo Dong, C. Azzaro-Pantel and A. L. Cadene, Resour., Conserv. Recycl., 2018, 133, 63–75 CrossRef.
- A. Polettini,
et al.
, J. Hazard. Mater., 2001, 88, 123–138 CrossRef CAS PubMed.
- X. G. Li,
et al.
, J. Cleaner Prod., 2012, 32, 96–100 CrossRef CAS.
- J. E. Aubert, B. Husson and N. Sarramone, J. Hazard. Mater., 2006, 136, 624–631 CrossRef CAS PubMed.
- Z. Yang,
et al.
, Constr. Build. Mater., 2018, 162, 794–801 CrossRef CAS.
- G. Qiao, Electric Power Technol. Environ. Prot., 2004, 03, 19–21 Search PubMed.
- N. Sakellariou, Energy Syst., 2017, 9(4), 981–1023 CrossRef.
- K. Korniejenko, B. Kozub and A. Bak,
et al.
, J. Compos. Sci., 2021, 5(9), 243–261 CrossRef CAS.
- Y. Yang, R. Boom and B. Irion,
et al.
, Chem. Eng. Process., 2012, 51, 53–68 CrossRef CAS.
- R. Fonte and G. Xydis, J. Environ. Manage., 2021, 287, 112269 CrossRef PubMed.
- A. J. Nagle, G. Mullally, P. G. Leahy and N. P. Dunphy, J. Environ. Manage., 2022, 302, 113994 CrossRef CAS PubMed.
- B. Diez-Cañamero and J. M. F. Mendoza, Waste Manage., 2023, 164, 94–105 CrossRef PubMed.
- M. Y. Khalid, Z. U. Arif, M. Hossain and R. Umer, Renewable Energy Focus, 2023, 44, 373–389 CrossRef.
|
This journal is © The Royal Society of Chemistry 2023 |
Click here to see how this site uses Cookies. View our privacy policy here.