DOI:
10.1039/D3RA00349C
(Paper)
RSC Adv., 2023,
13, 8299-8306
Free-standing TiO2 nanograssy tubular hybrid membrane for polysulfide trapping in Li–S battery†
Received
17th January 2023
, Accepted 23rd February 2023
First published on 13th March 2023
Abstract
During the growth of anodic TiO2 nanotubes with a high layer thickness of greater than 20 μm, “nanograss” structures are typically formed on the outermost surface. This happens due to the fact that the engraving of the oxide tubes arises during prolonged exposure to an F- ion containing electrolyte. These TiO2 nanotubular layers have a high aspect ratio with astonishing bundles of nanograss structures on the tube top and especially a high surface area with anatase crystallites in the tubes. By two-step anodization in synergy with the hybridization of a rubber polymer binder, freestanding nanotubular layers consisting of nanograssy surfaces with nano-crystalline particles in the tubes were successfully obtained. Under the highly efficient polysulfide trapping and electrolyte perturbation, this nanotubular hybrid membrane could deliver an enriched performance with a capacity of 618 mA h g−1 after 100 cycles at 0.1C in Li–S batteries.
Introduction
Urging for enormous power sources is ascribed to meeting the incessant flow demand in electric mobility and energy storage systems.1–5 Present Li-ion battery-based intercalation compounds (e.g., LiCoO2 and LiFePO4) have a limited specific energy.6–8 Li–S batteries with a striking high energy density of 2567 W h kg−1 and a high specific capacity of 1672 mA h g−1 have generated a potential interest for such applications.1,9–11 From the aspects of low cost, eco-friendly, and abundance, Li–S batteries depict a prominent interest in large-scale applications in the field of renewable energy.2,12 However, two main challenges impede the commercialization of sulfur as the cathode in Li–S cells. Firstly, the specific discharge capacity of Li–S cells is limited by poor active material utilization caused by the insulating nature of dissolving polysulfides in the electrolyte. Next, the cycle life and low coulombic efficiency are affected by the combination of polysulfide diffusion and its “shuttle effect” during the redox process. The highly soluble long-chain polysulfides (Li2Sx, 4 < x ≤ 8) are easily permeable through the separator and induces the loss of active material and severe fading of capacity. The diffused polysulfides further react with the Li anode and corrode it, which results in cell failure.6,9,13,14
To resolve these problems, contemporary efforts are focused on the development of new constraints for polysulfide dissolution.12,14–18 Thus far, many approaches have been developed in physically confined polysulfides trapping in mesocarbon materials,19–21 graphene,22–24 and hollow carbon spheres.20,26 However, the polysulfides diffuse out of the hydrophobic pores of carbon materials due to the fact that it does not bind to the polar and ionic sulfides because carbon is non-polar in nature.8 Recently, Cui Yi group has shown that sulfur TiO2 composite achieves a high specific capacity27 and in a further study they demonstrated that the strong chemical bonds between Ti(n)O2(n−1) and S-species contribute importantly to the improvement of the electrochemical properties.28 Therefore, it is a remarkable approach to absorb the polysulfides into hydrophilic metal oxides such as carbon-modified TiO2 as a separator host material. Moreover, there are also reports addressing the use of anodic TiO2 nanotube layers in conventional Li-ion batteries.25,29–35,40,41 These applications are commonly based on the use of TiO2 nanotubular structures along with a titanium metal substrate as an electrode. Until now, there is ambiguity on the direct application of such free-standing membrane38 in Li-ion batteries.
Herein, we report a novel TiO2 nanotubular hybrid membrane preparation and application as a polysulfide scavenger in Li–S battery. Recently, Schmuki et al. successfully showed the preparation of pure anatase membranes for a flow-through photocatalytic application by multi-step anodization.39 We introduced a synthetic strategy of two-step anodization combined with polymer hybridization to prepare the free-standing TiO2 nanoporous structure. These TiO2 membranes have a spectacular morphology of extremely high aspect ratio nanotube layer with coalescing fiber-like porous “nanograss” on the tube top.36 The individual tubes also have a nanoporous morphology of a highly ordered 1D structure with a TiO2 nanoparticulated inner shell and pure TiO2 outer wall of the nanotube.38 Such highly ordered TiO2 nanostructures with high aspect ratios have a fast electron/ion transport property in electrochemical applications.44,45 In the present work, for the first time we report a novel TiO2 nanotubular hybrid membrane preparation and its application as a polysulfide scavenger in Li–S battery. With the superior physical properties of a highly porous membrane, large amounts of polysulfides are trapped in the TiO2 nanostructured membrane enhancing the Li-ion transport.
Results and discussion
Preparation of free-standing nanograssy tubular hybrid membrane
TiO2 nanotube membranes were prepared by a novel approach of two-step anodization combined with polymer hybridization as shown in the schematic illustration of Fig. 1a. In the first step, nanotubular layers are formed on the Ti substrate by electrochemical anodization in fluoride ions containing the electrolyte. These anodic TiO2 nanotube arrays are grown perpendicular to the titanium substrate with highly complied adherence. The highly porous TiO2 nanograssy structures are typically formed on the tube tops due to the deformation of the tube walls by chemical engravings.36 To detach the anodized TiO2 nanograssy layers from the substrate, the layers have to be durable in the chemical etchant. In fact, even if the layer thickness is higher in order of 25 μm, the amorphous oxides are considerably dissolved out in the etchant. For withstanding the chemical etching, the entire amorphous layers (as prepared) were annealed up to 450 °C to convert them into crystalline layers. Subsequently, on the surface of the crystalline structure, a thin polymer layer of the elastic rubber binder (styrene butadiene rubber, SBR) was spin-coated for electrical insulation and especially for membrane protection without any cracking and crumbling. In the later stage of the second anodization, the tube stack was formed with other amorphous nanotubes underneath the crystalline layers, as shown in Fig. 1b.
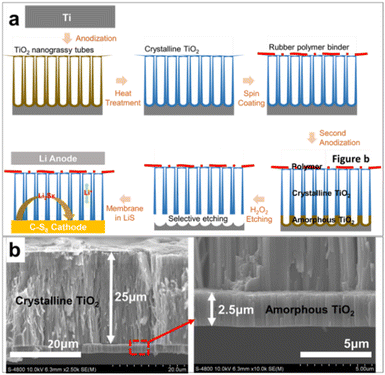 |
| Fig. 1 (a) Schematic illustration of the fabrication of the free-standing TiO2 nanograssy membrane and its application in Li–S battery (b) FE-SEM cross-sectional image of multi-layered TiO2 nanotube (TNT) prepared by 2-step anodization. The magnified image of (b) showing that amorphous TNTs grown underneath the crystallized TNTs. | |
It is noteworthy that the continued tube growth indicated that the electrolyte was able to flow locationally through the membrane without any blocking of the ion diffusion for the anodization. In the tube stack, the second layer was the amorphous sacrificial layer for the next etching step. After soaking in the H2O2 etchant, the amorphous layer was selectively dissolved between the substrate and the crystalline nanotube layers. The crystalline layer was detached from the substrate and floated on the H2O2 solution instantly after the chemical etching. Through this process, the free-standing TiO2 nanograssy tubular hybrid membrane was obtained and directly applicated to the Li–S battery as a membrane.
The morphology of the free-standing nanotubular hybrid membrane is shown in Fig. 2a. The digital image shows amorphous (as prepared), annealed, and detached layers, respectively. The obtained free-standing membrane has a uniform thickness of approximately 25 μm. The cross-sectional FE-SEM images in Fig. 2b–d show the top, low, and middle parts of the TiO2 nanotube membrane, respectively. The tube walls are well separated into individual entities with a diameter of approximately 140–180 nm. It is apparent from the top of the tube shown in Fig. 2b that the membrane surface has a very irregular morphology and the tube top walls also have disintegrated morphology that is partially etched with the initial tube layer after anodization in the NH4F + ethylene glycol-based electrolyte.36 The chemical etching of the TiO2 tube wall gives rise to the falling down of tube walls with the formation of the TiO2 nanoporous grassy structure (TNT) (see Fig. S1 in the ESI†). On the tube top, an approximately 1 μm thick polymer binder covers the entire surface regularly. As shown in the image from the top to bottom part, the TiO2 nanotubular membrane has an extremely high aspect ratio with both sides open, i.e., flow-through membrane.37 This highly ordered TiO2 structure covering the porous tube top has a spectacular characteristic for absorbing the chemical products in the framework as a membrane. Moreover, individual tubes also consist of a highly porous structure as shown in the TEM image of Fig. 2e. TiO2 nanocrystallites in the range of several nanometers are present in the outer tube wall and the carbon species are mainly incorporated in the inner shell during the heat treatment process with the remaining ethylene glycol-based electrolyte,38 which is favorable in a view of chemical absorption and ionic pathways in the nanostructure. The XRD pattern of this sample shown in Fig. 2f confirmed the conversion to a crystalline anatase structure due to the annealing temperature of 450 °C.
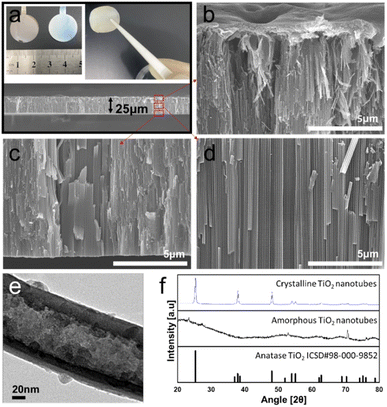 |
| Fig. 2 FE-SEM cross-section images of (a) full view, (b) top, (c) bottom, and (d) middle view of nanograssy hybrid membrane. (e) HR-TEM image of the inner shell (IST) and outer shell (OST) of the TiO2 nanotube membrane. (f) XRD patterns of crystalline and amorphous nanotube layers. The sharp peaks in the amorphous phase were detected from the edge part of the Ti metal substrate. Digital image of (a) represents after anodization of Ti foil (left: “as prepared”, amorphous TNT) and after annealing of the anodized sample (right: crystalline TNT) with tweezer handling of the free-standing TiO2 hybrid membrane that was prepared as described in Fig. 1. | |
Nano grass formation and polymer hybridization
We investigated the anodization time dependence for the nanograss formation (see Fig. S1 in the ESI†). In the anodization of the Ti substrate in the NH4F + ethylene glycol-based electrolyte, the chemical etching occurred on the earliest formed tubes. This process accelerated substantial thinning and finally disintegrated parts of the tube walls, which led to nanograssy appearance on the tube tops.36 Anodic TiO2 nanotubes are vertically split off by electric-field-directed chemical etching and fall down as a bundled TiO2 nanoporous structure typically known as the “nanograss” structure is formed on the top layer. As shown in Fig. 3a and b, it is apparent that on the top surface, TiO2 nanograssy bundles are formed with an extremely high aspect ratio. Coalescing TiO2 fibers have highly nanoporous networks, which also have similar morphology to that of the commercial organic separator but they are nanoscaled. Therefore, such nanoporous reservoirs can be available for use as polysulfides inhibitor with 3-dimensional accessible pathways for Li-ion diffusion. Even after polymer coating on the nanograssy structures, the membrane was not blocked, as shown in Fig. 3c and d. The polymer styrene butadiene rubber (SBR) binder is uniformly coated on the nanograss but the macropores are still present on the surface that shows the membrane structure (see Fig. S2 in the ESI†). Meanwhile, from scanning electron microscopy of the bottom surface view in Fig. 2e and f, it is evident that the TiO2 nanotube wall consists of two different regions: an outer shell of the tube (OST) and the inner shell of the tube (IST) that are typically formed during the heat treatment at 450 °C. The total thickness of these two parts changes along the tube wall (see Fig. S1 in the ESI†). The thickness of OST and IST increase along the tube wall a few nm from the tube top to bottom of approximately 25 nm and 35 nm, respectively.38 However, the nanoscopic sizes of the TiO2 nanotubes strongly depend on the anodizing parameters such as the electrolyte species and applied voltage.42 After anodization, the electrolyte species that are present in the IST, especially carbon-based compounds from the inner shell evaporate after the annealing procedure resulting in the inner shell becoming porous in nature that can be revealed from the TEM image shown in Fig. 2e and the FE-SEM image in Fig. 3e. The distribution of carbon in the tubes is well co-ordinated in IST and the further annealing process results in the porous structure of double-walled open tubes (DWOT), i.e., the OST becoming compact and the IST becoming porous with a carbon-rich layer.38 TiO2 nanocrystallites in the OST are formed along the carbonized inner wall of DWOT. The nanoporous architecture of double-walled open tubes with the nano grassy structures has a unique morphology to be used in the highly-efficient polysulfide absorbing membrane.
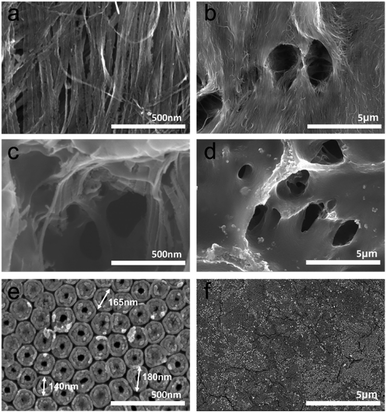 |
| Fig. 3 FE-SEM image of nanograss surface view in high and low magnification before (a and b), after (c and d) polymer coating, and (e and f) double-walled nanotubes at the bottom surface. | |
Electrochemical analysis
In Li–S battery, a series of electrochemical reaction converted the long-range polysulfides of S8 into lower-order polysulfides of Li2S that is almost insoluble and precipitate from the organic electrolyte at the transition point between the upper and lower plateau profiles (see Fig. S3 in the ESI†). Thus, the shuttle effect induces the formation of Li2S insulating layers on the surface of the Li-metal anode and deteriorates its electrochemical performance owing to the degradation of the active material, capacity fading, cycling stability deterioration, and a decrease in ionic conductivity. The passivated layer formed on the anode side is a critical factor in increasing the resistance and accelerating Li metal anode oxidation, thus reducing the cycle stability of Li–S batteries.27 Fig. 4a shows the cyclic voltammetry plots (CV) of the nanotubular membrane for the initial five cycles with a scan rate of 0.1 mV s−1 in the voltage range of 1.5–3.0 V. The cell was initially swept from the open-circuit voltage to 3.0 V, ensuring a complete conversion of Li2S6 to S8/Li2S8 transformation. After the active material encapsulation via the in situ conversion of dissolved polysulfides, the CV curves show the typical two-step sulfur reduction process. The cathodic peaks at 2.29 V and 1.98 V represent the transition from elemental sulfur to long-chain polysulfides (Li2Sn, 4 < n < 8). The two peaks are related to the transition from long-chain to short-chain polysulfides (Li2S2 to Li2S), respectively.6,9 The subsequent anodic cycle (3–5th cycles) of the oxidation peaks shifting to the position at 2.5 V is related to the complete conversion of Li2S into elemental S during the formation of Li2Sn (n > 2).11 The two Peaks located at 1.72 V(III) and 2.03 V(IV) clearly reveal the lithiation and delithiation of the TiO2 nanotubular membrane.29
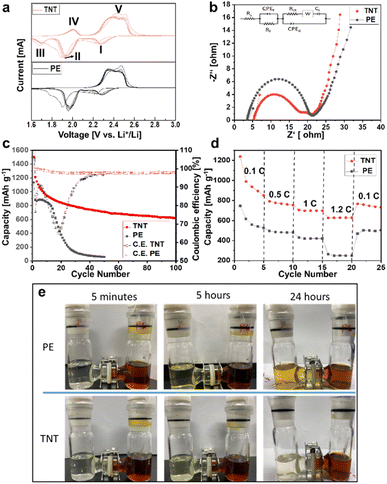 |
| Fig. 4 Electrochemical performance of commercial polyethylene (PE) separator and TiO2 nanograssy tube (TNT) hybrid membrane in Li–S cells: (a) cyclic voltammetry (CV) versus Li/Li + profiles at a scan rate of 0.1 mV s−1 over the potential window of 1.6 to 2.8 V for the first 5 cycles, (b) electrochemical impedance spectroscopy (EIS), inset shows the equivalent circuit, (c) cycling performance profiles at 0.1 C-rate, (d) cycling performance profiles at 0.1C to 1.2C of different C-rates, and (e) photographs for the diffusion properties of the Li2Sx solution through (upper row) polyethylene (PE) separators and (lower row) TiO2 nanograssy tube (TNT) membrane at different time intervals. | |
Meanwhile, the overlapped anodic profile in the first 5 cycles of charging at 2.2 and 2.5 V (see the ESI of Fig. S3b†) is related to the oxidation reactions from Li2S to Li2S8. The absence of overpotential in the cathodic profile indicates decreased polarization because the active material migrates to electrochemically stable sites of the TiO2 nanotubular membrane during the first cycle. The complete upper discharge plateaus suggest that the migrating polysulfides are localized in the cathode region and that severe active material loss has not occurred. The appearance of the vertical voltage rise at 2.8 V typically indicates a complete charge process. The initial discharge capacity of the cell with TiO2 nanograssy membrane is 1499 mA h g−1, which approaches 90% of the theoretical capacity of sulfur (1675 mA h g−1). In subsequent cycles, the overlapping cathodic and anodic peaks maintained their peak shape and displayed no obvious peak intensity changes and potential shifts, which suggested superior cycling stability and highly reversible redox reactions. This superior cyclability from the charging/discharging profiles is in line with the results of the cyclic voltammetry performance of the TiO2 nanotubular membrane, as shown in Fig. 4a. The high active material utilization results from enriched polysulfide trapping in the TiO2 nanotubular membrane towards the cathode side. The cycling performance in Fig. 4c reveals that the cells with TiO2 nanograssy (TNT) membrane have stable cyclability, a high discharge capacity of 618 mA h g−1, and high coulombic efficiency of > 97% for over 100 cycles compared to the conventional PE separator. In the case of the PE separator, it shows an abrupt performance for up to 40 cycles after that the cell performance sets to zero due to the non-polar nature of MWCNT, which affects the trapping of polysulfides.8 In the case of TNT membrane, it absorbs polysulfides enormously due to the chemical absorption property of highly porous TNT membrane.27
The stable cyclability and the high-capacity retention resulted from the synergistic effects of highly nanoporous double-walled open tubes (DWOT) at the bottom part and the extremely high aspect ratio of TiO2 nanograssy networks at the top part (a stable cycling performance for a comparison with other TiO2 membranes, as shown in the ESI of Table S1†). Firstly, the natural nanopore networks are critical for allowing the Li-ion to diffuse into the cathode and absorbing the polysulfides during the charge–discharge process, which reduces the degradation of the active material and shows better performance. Secondly, the nanoporous membrane provides the essential pathways for the electrolyte diffusion to localize the catholyte within the cathode region and allows the polysulfides to be captured into the surrounding nano-framework, forming a favorite contact among the electrolyte, active material, and carbon matrix. Thirdly, the interfacial resistance was greatly suppressed by the double-walled open tubes (DWOT) that resulted in high chemisorption of polysulfide also providing continuous electron pathways to enhance sulfur utilization. The impedance analysis shown in Fig. 4b confirmed that the TiO2 nanograssy membrane has higher ionic conductive kinetics towards the cathode side (smaller the semi-circle) than the commercial polyethylene (PE) separator. Although the TiO2 nanograssy membrane has a high polysulfides inhibition, it still has the overall semiconducting behavior between the two electrodes with the corresponding value of the charge transfer resistance (Rct) compared to commercial PE separator of approximately 20 Ohm and 21.1 Ohm, respectively. The impedance indicates that the long-range continuity of the TiO2 nanograssy fiber network facilitates electron transfer and enhances electrochemical kinetics without any carbon-modified membrane in the TiO2 membrane (see ESI of Table S1†). It is remarkable that the TiO2 nanograssy (TNT) membrane shows excellent cycling stability under continuously varying C-rates of 0.1C (0.39 mA cm−2), 0.5C (0.69 mA cm−2), 1C (1.7 mA cm−2), 1.2C (4.1 mA cm−2) with loading value of 1.34 mg cm−2. A reversible high and stable capacity of 852.4 mA h g−1 was maintained after 5 cycles at a C-rate of 0.1C. At a high C-rate of 0.5C and 1.2C TiO2 membrane still exhibited the capacity retention of 698 mA h g−1 and 624 mA h g−1. It revealed that the fast reaction kinetics notably at the high C-rates are abruptly switched back from 1.2C to 0.1C, and again the capacity recovered to 760.27 mA h g−1. The PE separator showed relatively lower capacity value when switched back into different C-rate values of 0.1C (0.3 mA cm−2),0.5C (0.6 mA cm−2), 1C (1.5 mA cm−2), 1.2C (3.7 mA cm−2) with the loading value of 1.32 mg cm−2 due to non-polar nature of the carbon matrix.8
Polysulfide dissolution
We investigate the effectiveness of polysulfide absorption with an H-cell configuration. The polysulfides solution of 0.01 M Li2S8 in 1,3-dioxalane (DOL) and 1,2-dimethyoxyethane (DME) = 1
:
1 (v: v) was used on the right side of the cell and pure solvent mixture was equilibrated at various time interval as shown in Fig. 4e. The TiO2 membrane was sandwiched with the same PE separator between the two cells. Double-walled open tubes (bottom part of the membrane) were placed towards the right side of polysulfides solution. After 24 hours of dwell time, the pristine PE separator permeably changed its color to reddish-brown owing to the diffusion of polysulfides. During that time, the contrast of TiO2 nanograssy (TNT) membrane showed no appreciable color change due to the successive suppression of polysulfides. This can be attributed to the synergistic contribution of the primary physical capture via the nanoporous nature in the nanograssy membrane and, moreover, the TiO2 crystallites on the outer shell of DWOT also contributed to the physical absorption of the Li2Sx. Based on the chemical interaction between the discharged polysulfides of Li2Sx and the TiO2 nanotubular membrane (TNT), it showed enhanced performance in absorbing the large amount of Li2Sx from the sulfur cathode.
Experimental
Materials
Ti foils (Nilaco, 99.6%, 0.125 mm thickness) were pre-cleaned using ethanol in a sonication bath and dried at room temperature. Anodization was carried out in a two-electrode cell: a degreased Ti foil with a diameter of Ø 19 mm was cut into pieces and welded with the Ti metal current connector for electrical connection as a working electrode and platinum mesh is used as a counter electrode in a high-voltage potentiostat (ODA, OPS-22101, Incheon, Korea) by applying a ramped voltage of 60 V at 1 V s−1 for 4 hours in an organic electrolyte of ethylene glycol + 0.5 wt% NH4F + 1 vol% H2O.25,31 After anodization, the sample was rinsed and soaked in ethanol for 10 minutes then finally dried at room temperature. To convert the ‘as-prepared’ layer into anatase TiO2; the sample was annealed at 450 °C in the air for 1 hour at a heating rate of 15 °C min−1 using a rapid thermal annealer.
Membrane preparation
For the hybridization of the TiO2 layer, styrene-butadiene rubber (JSR Corporation, SBR 48%) binder was spin-coated at (2000 rpm, 300 seconds) and dried in an oven at 50 °C. In order to form a sacrificial layer, the polymer-coated sample was secondly anodized at 60 V for 20 minutes in the same electrolyte. To obtain the free-standing hybrid membrane, the sample was etched in H2O2 (Duksan chemicals, 30 wt%) for 10 minutes at room temperature. After the etching step, the free-standing membrane was rinsed in ethanol and dried at 50 °C for 1 hour.
Morphological characterization
Morphological characterization of the samples was performed using a field-emission scanning electron microscopy Hitachi S4800. The cross-sectional images were taken from the scissors-cut of membrane. X-ray diffraction analysis (XRD) was performed on an X-ray diffractometer (Philips X'pert-MPD) with a Panalytical X'celerator detector with graphite monochromized Cu Kα radiation (λ = 1.54056 Å).
Electrochemical analysis
Coin cell assembly was performed in a dry room to evaluate the performance of the samples. Sulfur powder (Sigma-Aldrich, < 99%, USA) was mixed along with multi-walled carbon nanotubes (MWCNTs, diameter = 9.5 nm, Nanocyl, Belgium) (S
:
MWCNT = 7
:
3 wt%) in ethanol by a ball-milling process (450 rpm, 30 minutes, 5 cycles). Ethanol was eliminated by the vacuum filtration technique. The obtained MWCNT@S composite cathode material was treated at 70 °C for 24 hours in a vacuum oven to remove any traces of the solvents and then heat treated at 155 °C for 2 hours to diffuse elemental S into the MWCNT network.43 The MWCNT-based S cathode was obtained with a controlled film thickness of 200 μm on an Al current collector with a mass loading of 1.23 mg cm−2 containing the active material: conducting agent: a binder of 70
:
20
:
10 with S/MWCNT
:
Super-P
:
Poly (ethylene oxide), which served as a cathode. TiO2 nanograssy hybrid membrane (25 μm) as a supporting film was attached to the separator facing the nanograssy surface to the cathode part. A 500 μm thick Li-metal foil was used as an anode. The electrolyte was 1 M lithium bis (trifluoromethylsulfonyl) imide (LiTFSI) (Sigma-Aldrich, 99.0%) dissolved in DOL and DME = 1
:
1 (v: v) with a 1 wt% LiNO3(Sigma-Aldrich, 99.99%) additive as an electrolyte. The coin cell was galvanostatically charged/discharged at a C-rate of 0.1C. Rate performances with a multichannel battery tester (MACCORE) were evaluated for different C-rates from 0.1C to 1.2C, at a potential range of 1.8–2.8 V. Cyclic voltammetry (CV) and electrochemical impedance spectroscopy (EIS) were conducted on an electrochemical setup (Bio Logic model, VMP3, France). CV was performed at a scan rate of 1 mV s−1 in a voltage range of 1.6–3.0 V while EIS was performed after 100 cycles at different bias potentials in a frequency range of 10 kHz to 100 MHz with an AC signal amplitude of 10 mV.43 The dissolution of Li2S8 of (0.01 M) in 1,3-dioxalane (DOL) and 1,2-dimethoxyethane (DME) was studied by comparing the PE separator (W-Scope, pore volume: 43%, pore size: 60 nm, thickness: 16 μm, Tokyo, Japan) and the TiO2 nanotubular grassy (TNT) membrane as a polysulfides inhibitor in H-cell configuration.
Conclusions
In summary, we have shown the preparation of a free-standing TiO2 nanotubular hybrid membrane by two-step electrochemical anodization incorporated with polymer hybridization. The TiO2 nanotubular membrane has bundles of nanograss on the tube top and double-walled nanostructures in the tube. The double-walled nanotubes consist of a porous TiO2 nanoparticulate inner shell and pure TiO2 in the outer shell. The nanopores and macroscopic networks of nanograssy tubular layer, which could absorb the soluble polysulfides and channel the electrolyte have the potential to substitute the conventional TiO2 nanoparticle membrane. Even though a feasibility study on the anodically obtained membrane for Li–S battery was addressed here, there is still room for reinforcing the performance of this novel free-standing TiO2 nanograssy tubular hybrid membrane in energy storage by further modification with some metal nanoparticles or some conductive materials.
Author contributions
Conceptualization: S. Dasarathan, J. Sung, D. Kim, J.-W. Park. Data curation: Y.-S. Jo, J.-W. Hong. Formal analysis: B.-G. Kim. Funding acquisition: Y.-J. Lee, H.-Y. Choi. Investigation: H.-Y. Choi. Methodology: S. Dasarathan, J. Sung, D. Kim. Project administration: Y.-J. Lee. Resources: J.-W. Park, D. Kim. Software: J. Sung, J.W. Hong. Supervision: B.-G. Kim, D. Kim. Validation: B.-G. Kim, J.-W. Park. Visualization: H.-Y. Choi, Y.-J. Lee. Writing – original draft: S. Dasarathan, D. Kim. Writing – review and editing: D. Kim, J.-W. Park.
Conflicts of interest
“There are no conflicts to declare”.
Acknowledgements
This work was supported by the Primary Research Program (23A01030) of the Korea Electro-Technology Research Institute and by the Technology Innovation Program (20014581) of the Ministry of Trade, Industry, and Energy (MOTIE, Korea).
Notes and references
- C. Xu, B. Xu, Y. Gu, Z. Xiong, J. Sun and X. S. Zhao, Graphene-based electrodes for electrochemical energy storage, Energy Environ. Sci., 2013, 6, 1388 RSC.
- Y. X. Yin, S. Xin, Y. G. Guo and L. J. Wan, Lithium–Sulfur Batteries: Electrochemistry, Materials, and Prospects, Angew. Chem., Int. Ed., 2013, 52, 13186 CrossRef CAS PubMed.
- X. W. Zhang, A. Wang, Y. Wang, K. Huang, Z. Yuan, J. Yu, Y. Qiu and J. Yang, Improved cycle stability and high security of Li-B alloy anode for lithium–sulfur battery, J. Mater. Chem. A, 2014, 2, 11660 RSC.
- W. Si, I. Mönch, C. Yan, J. Deng, S. Li, G. Lin, L. Han, Y. Mei and O. G. Schmidt, A Single Rolled-Up Si Tube Battery for the Study of Electrochemical Kinetics, Electrical Conductivity, and Structural Integrity, Adv. Mater., 2014, 26, 7973 CrossRef CAS PubMed.
- Y. Zhou, C. D. Gu, J. P. Zhou, L. J. Cheng, W. L. Liu, Y. Q. Qiao, X. L. Wang and J. P. Tu, Effect of carbon coating on low temperature electrochemical performance of LiFePO4/C by using polystyrene sphere as carbon source, Electrochim. Acta, 2011, 56, 5054 CrossRef CAS.
- Z. Lin and C. Liang, Lithium–sulfur batteries: from liquid to solid cells, J. Mater. Chem. A, 2015, 3, 936 RSC.
- A. Manthiram, Y. Fu and Y. Su, Challenges and Prospects of Lithium–Sulfur Batteries, Acc. Chem. Res., 2013, 46, 1125–1134 CrossRef CAS PubMed.
- Q. Pang, D. Kundu, M. Cuisinier and L. F. Nazar, Surface-enhanced redox chemistry of polysulphides on a metallic and polar host for lithium-sulphur batteries, Nat. Commun., 2014, 5, 3 CrossRef PubMed.
- Z. Liang, G. Zheng, W. Li, Z. W. Seh, H. Yao, K. Yan, D. Kong and Y. Cui, Sulfur Cathodes with Hydrogen Reduced Titanium Dioxide Inverse Opal Structure, ACS Nano, 2014, 8, 5249 CrossRef CAS PubMed.
- X. Cui, Z. Shan, L. Cui and J. Tian, Enhanced electrochemical performance of sulfur/carbon nanocomposite material prepared via chemical deposition with a vacuum soaking step, Electrochim. Acta, 2013, 105, 23 CrossRef CAS.
- Z. Zhang, Z. Li, F. Hao, X. Wang, Q. Li, Y. Qi, R. Fan and L. Yin, 3D Interconnected Porous Carbon Aerogels as Sulfur Immobilizers for Sulfur Impregnation for Lithium-Sulfur Batteries with High Rate Capability and Cycling Stability, Adv. Funct. Mater., 2014, 24, 2500 CrossRef CAS.
- Z. Wang, Y. Dong, H. Li, Z. Zhao, H. Bin Wu, C. Hao, S. Liu, J. Qiu and X. W. D. Lou, Enhancing lithium–sulphur battery performance by strongly binding the discharge products on amino-functionalized reduced graphene oxide, Nat. Commun., 2014, 5, 5002 CrossRef CAS PubMed.
- Y. Cui, A. Abouimrane, C. J. Sun, Y. Ren and K. Amine, Li–Se battery: absence of lithium polyselenides in carbonate-based electrolyte, Chem. Commun., 2014, 50, 5576 RSC.
- J. H. Kim, K. Fu, J. Choi, S. Sun, J. Kim, L. Hu and U. Paik, Hydroxylated carbon nanotube enhanced sulfur cathodes for improved electrochemical performance of lithium–sulfur batteriesChem, Commun, 2015, 51, 13682 RSC.
- C. Zhang, H. Bin Wu, C. Yuan, Z. Guo and X. W. Lou, Confining Sulfur in Double-Shelled Hollow Carbon Spheres for Lithium–Sulfur Batteries, Angew. Chem., Int. Ed., 2012, 51, 9592 CrossRef CAS PubMed.
- W. Zhou, Y. Yu, H. Chen, F. J. Disalvo and H. D., Abruna, Amylopectin Wrapped Graphene Oxide/Sulfur for Improved Cyclability of Lithium–Sulfur Battery, ACS Nano, 2013, 7(10), 8801–8808 CrossRef CAS PubMed.
- H. Wang, Y. Yang, Y. Liang, J. T. Robinson, Y. Li and A. Jackson, Graphene-Wrapped Sulfur Particles as a Rechargeable Lithium–Sulfur Battery Cathode Material with High Capacity and Cycling Stability, Nano Lett., 2011, 11, 2644 CrossRef CAS PubMed.
- Y. Yang, G. Zheng and Y. Cui, Nanostructured sulfur cathodes, Chem. Soc. Rev., 2013, 42, 3018 RSC.
- X. Zhou, J. Xie, J. Yang, Y. Zou, J. Tang, S. Wang, L. Ma and Q. Liao, Improving the performance of lithium–sulfur batteries by graphene coating, J. Power Sources, 2013, 243, 993 CrossRef CAS.
- F. Sun, J. Wang, H. Chen, W. Li, W. Qiao, D. Long and L. Ling, High Efficiency Immobilization of Sulfur on Nitrogen-Enriched Mesoporous Carbons for Li–S Batteries, ACS Appl. Mater. Interfaces, 2013, 5, 5630 CrossRef CAS PubMed.
- Y. Yao, H. Liu, G. Li, H. Peng and K. Chen, Synthesis and electrochemical performance of phosphate-coated porous LiNi1/3Co1/3Mn1/3O2 cathode material for lithium-ion batteries, Electrochim. Acta, 2013, 113, 340 CrossRef CAS.
- J. Rong, M. Ge, X. Fang and C. Zhou, Solution Ionic Strength Engineering As a Generic Strategy to Coat Graphene Oxide (GO) on Various Functional Particles and Its Application in High-Performance Lithium–Sulfur (Li–S) Batteries, Nano Lett., 2014, 14, 473 CrossRef CAS PubMed.
- S. Lu, Y. Chen, X. Wu, Z. Wang and Y. Li, Experimental visualization of the diffusion pathway of sodium ions in the Na3[Ti2P2O1F] anode for sodium-ion battery, Sci. Rep., 2014, 4, 4 Search PubMed.
- X. Ji, S. Evers, R. Black and L. F. Nazar, Stabilizing lithium–sulphur cathodes using polysulphide reservoirs, Nat. Commun., 2011, 2, 325 CrossRef PubMed.
- S. Pervez, D. Kim, C. H. Doh, U. Farooq, A. Yaqub, J. H. Choi, Y. J. Lee and M. Saleem, High areal capacity for battery anode using rapidly growing self-ordered TiO2 nanotubes with a high aspect ratio, Mater. Lett., 2014, 137, 347 CrossRef CAS.
- W. Zhou, X. Xiao, M. Cai and L. Yang, Polydopamine-Coated, Nitrogen-Doped, Hollow Carbon–Sulfur Double-Layered Core–Shell Structure for Improving Lithium–Sulfur Batteries, Nano Lett., 2014, 14, 5250 CrossRef CAS PubMed.
- Z. W. Seh, W. Li, J. J. Cha, G. Zheng, Y. Yang, M. T. McDowell, P. C. Hsu and Y. Cui, Sulphur–TiO2 yolk–shell nanoarchitecture with internal void space for long-cycle lithium–sulphur batteries, Nat. Commun., 2013, 4, 1331 CrossRef PubMed.
- X. Tao, J. Wang, Z. Ying, Q. Cai, G. Zheng, Y. Gan, H. Huang, Y. Xia, C. Liang, W. Zhang and Y. Cui, Strong Sulfur Binding with Conducting Magnéli-Phase TinO2n–1 Nanomaterials for Improving Lithium–Sulfur Batteries, Nano Lett., 2014, 14, 5288 CrossRef CAS PubMed.
- A. Sabbaghi, C. H. Wong, X. Hu and F. L. Y. Lam, Titanium dioxide nanotube arrays (TNTAs) as an effective electrocatalyst interlayer for sustainable high-energy density lithium-sulfur batteries, J. Alloys Compd., 2022, 899, 163268 CrossRef CAS.
- Y. Chen, W. Tang, J. Ma, B. Ge, X. Wang, Y. Wang, P. Ren and R. Liu, Nickel-decorated TiO2 nanotube arrays as a self-supporting cathode for lithium-sulfur batteries, Front. Mater. Sci., 2020, 14, 266–274 CrossRef.
- S. Dasarathan, M. Ali, T. J. Jung, J. Sung, Y. C. Ha, J. W. Park and D. Kim, Vertically Aligned Binder-Free TiO2 Nanotube Arrays Doped with Fe, S and Fe-S for Li-ion Batteries, Nanomaterials, 2021, 11, 1 CrossRef PubMed.
- J. K. Ha, Y. G. Gwag, J. S. Song, G. B. Cho, H. J. Ahn, J. H. Ahn and K. K. Cho, Effect of surface coating on the electrochemical performance of cathode made of sulfur–loaded TiO2 nanotube arrays, J. Alloys Compd., 2018, 737, 248 CrossRef CAS.
- Z. J. Zhang, J. Zhao, Z. J. Qiao, J. M. Wang, S. H. Sun, W. X. Fu, X. Y. Zhang, Z. Y. Yu, Y. H. Dou, J. L. Kang, D. Yuan, Y. Z. Feng and J. M. Ma, Nonsolvent-induced phase separation-derived TiO2 nanotube arrays/porous Ti electrode as high-energy-density anode for lithium-ion batteries, Rare Met., 2021, 40, 393 CrossRef CAS.
- Y. Zhao, W. Zhu, G. Z. Chen and E. J. Cairns, Polypyrrole/TiO2 nanotube arrays with coaxial heterogeneous structure as sulfur hosts for lithium sulfur batteries, J. Power Sources, 2016, 327, 447 CrossRef CAS.
- M. Zhang, C. Wang, H. Li, J. Wang, M. Li and X. Chen, Enhanced performance of lithium ion batteries from self-doped TiO2 nanotube anodes via an adjustable electrochemical process, Electrochim. Acta, 2019, 326, 134972 CrossRef CAS.
- D. Kim, A. Ghicov and P. Schmuki, TiO2 Nanotube arrays: Elimination of disordered top layers (“nanograss”) for improved photoconversion efficiency in dye-sensitized solar cells, Electrochem. Commun., 2008, 10, 1835 CrossRef CAS.
- S. P. Albu, A. Ghicov, J. M. Macak, R. Hahn and P. Schmuki, Self-Organized, Free-Standing TiO2 Nanotube Membrane for Flow-through Photocatalytic Applications, Nano Lett., 2007, 7, 1286 CrossRef CAS PubMed.
- S. P. Albu, A. Ghicov, S. Aldabergenova, P. Drechsel, D. LeClere, G. E. Thompson, J. M. Macak and P. Schmuki, Formation of Double-Walled TiO2 Nanotubes and Robust Anatase Membranes, Adv. Mater., 2008, 20, 4135 CAS.
- S. So, I. Hwang, F. Riboni, J. Yoo and P. Schmuki, Robust free-standing flow-through TiO2 nanotube membranes of pure anatase, Electrochem. Commun., 2016, 73–78 CrossRef CAS.
- G. F. Ortiz, l. Hanzu, T. Djenizian, P. Lavelo, J. L. Tirado and P. Knauth, Alternative Li-Ion Battery Electrode Based on Self-Organized Titania Nanotubes, Chem. Mater., 2009, 21(1), 63–67 CrossRef CAS.
- G. D. Salian, M. Krbal, H. Sopha, C. Lebouin, M.-V. Coulet, J. Michalicka, L. Hromadko, A. T. Tesfayer, J. M. Macak and T. Djenizian, Self-supported sulphurized TiO2 nanotube layers as positive electrodes for lithium microbatteries, Appl. Mater. Today, 2019, 257–264 CrossRef.
- P. Roy, S. Berger and P. Schmuki, TiO2 Nanotubes: Synthesis and Applications, Angew. Chem., Int. Ed., 2011, 50, 2904–2939 CrossRef CAS PubMed.
- S.-C. Jo, J.-W. Hong, I.-K. Choi, M.-J. Kim, B.-G. Kim, Y.-J. Lee, H.-Y. Choi, D. Kim, T.-Y. Kim, K.-J. Baeg and J.-W. Park, Multimodal Capturing of Polysulfides by Phosphorus-Doped Carbon Composites for Flexible High-Energy-Density Lithium–Sulfur Batteries, Small, 2022, 18(21), 2200326 CrossRef CAS PubMed.
- B. Chen, J. Sha, W. Li, F. He, E. Liu, C. Shi, C. He, J. Li and N. Zhao, Graphene Oxide-Assisted Synthesis of Micro sized Ultrathin Single-Crystalline Anatase TiO2 Nanosheets and Their Application in Dye-Sensitized Solar Cells, ACS Appl. Mater. Interfaces, 2016, 8(4), 2495–2504 CrossRef CAS PubMed.
- B. Chen, Y. Meng, F. Xie, F. He, C. He, K. Davey and N. Zhao, 1D Sub-Nanotubes with Anatase/Bronze TiO2 Nanocrystal Wall for High-Rate and Long-Life Sodium-Ion Batteries, Adv.Mater., 2018, 30, 1804116 CrossRef PubMed.
Footnotes |
† Electronic supplementary information (ESI) available. See DOI: https://doi.org/10.1039/d3ra00349c |
‡ S. Dasarathan, J. Sung, J.-W. Park and D. Kim contributed equally to this work. |
|
This journal is © The Royal Society of Chemistry 2023 |
Click here to see how this site uses Cookies. View our privacy policy here.