DOI:
10.1039/D3RA01720F
(Paper)
RSC Adv., 2023,
13, 11393-11405
Immobilized Ni on TMEDA@βSiO2@αSiO2@Fe3O4: as a novel magnetic nanocatalyst for preparation of pyrido[2,3-d:6,5-d′]dipyrimidines†
Received
15th March 2023
, Accepted 26th March 2023
First published on 14th April 2023
Abstract
In the current body of research, a very quick and effectual procedure for the synthesis of pyrido[2,3-d:6,5-d′]dipyrimidines has been developed. This method is accomplished through the one-pot multi-component reaction of 2-thiobarbituric acid, NH4OAc and aldehydes utilizing Ni-TMEDA@βSiO2@αSiO2@Fe3O4 as a novel mesoporous nanomagnetic catalyst at room temperature. This protocol is one of the few reports of the preparation of these derivatives without the use of conventional heating as well as energies such as microwave and ultrasound radiation. The characterization of the prepared catalyst was well accomplished by different techniques such as FT-IR, ICP-OES, SEM, TEM, BET, XRD, VSM, TGA, EDX and Elemental mapping. This organometallic catalyst was reusable for seven times with negligible decrement in its catalytic performance. In addition, all of the products were produced with high TON and TOF values, which demonstrates that our catalyst has a very high level of activity in the preparation of pyrido[2,3-d:6,5-d′]dipyrimidines.
1. Introduction
During recent decades, the design of recyclable catalysts has been greatly developed in the chemical and pharmaceutical industries.1 Hence, anchoring catalysts to suitable solid substrates has become very important in various fields of chemical reactions.2,3 These materials act as an interface between homogeneous and heterogeneous catalysis for reasons such as significant efficiency, physical and chemical stability, recyclability, large surface/volume ratio, and good biocompatibility.1–5 In particular, Fe3O4 nanoparticles have garnered a lot of interest in organic synthesis and other fields of science due to their unique properties.6–8 Perhaps the best feature of magnetic nanoparticles, which increases the versatility of work up steps, is their simple segregation from reaction mixtures via an external magnet.6–8 In this same regard, different forms of mesoporous silica have attracted attention by reason of their unique properties in the fields of catalysis.2,3 Among these properties, we can mention their uniform and large pore size for stabilizing metals and organic ligands, their ability to be used in harsh reaction conditions due to thermal stability above 900 °C, as well as high loading capacity to immobilize catalysts due to their high surface area (>1200 m2 g−1).9,10 These characteristics encourage chemists to place Fe3O4 particles in the mesoporous silica channels for the synthesis of magnetic silica nanoparticles and in this way benefit these materials as substrates for various kinds of catalysts.9,10
In organic and medicinal chemistry, there has been a lot of interest in multi-component reactions, sometimes known as MCRs.11 This reactions are well-known, practical and useful protocols which have been used for production of a wide range of organic compounds.11 MCRs that result in the production of a heterocycle core are of significant interest due to the fact that a heterocyclic scaffold is a necessary component of a great deal of pharmaceuticals and biologically active compounds.12 They are reactions that combine three or more small-molecular-weight building components into a single product with good selectivity and combinatorial effectivity. In addition, MCRs save time, reduce the amount of energy that is used, increase the amount of raw materials that are consumed, limit or eliminate the synthesis of waste and byproducts, and lower the amount of volatile organic solvents that are used.12–14 In light of this, the application of this approach complies well with the protocols of green chemistry; in addition, the application of this technique is simpler and more cost-effective in comparison to traditional multi-step reactions.12–15
Transition metals on solid supports, and also oxides of these metals have been used as effective catalysts in various chemical reactions, including oxidation and reduction,16–19 C–S, C–O and C–C coupling,3,20–22 and multicomponent reactions.3,23–25 Rapid development in this field is taking place due to its importance in biological, pharmaceutical, industrial and chemical fields.25 Among transition metals, nickel is a versatile catalyst that able to use in a different of synthetic transformations.25 In the literature, the advances in the field of nickel-catalyzed multicomponent reactions are mentioned.25
Heterocyclic compounds containing pyrido-pyrimidine framework are of importance because they are an vital moiety of many drugs and biological active substances, such as anti-inflammatory,26 antimicrobial,27 antihypertensive,28 antiallergic,29 anticonvulsants,30 calcium channel antagonists, antibacterial,31 fibroblast growth factors (FGFs),32 anti-HIV,33 antifolate,34 and potassium sparing agents.35 They have been also utilized as anticancer agents in the control of tyrosine kinases.36,37 The one-pot MCR of arylaldehydes with 2-thiobarbituric acid and NH4OAc has been applied as a useful synthetic route toward pyrido[2,3-d:6,5-d′]dipyrimidines; few catalysts have been reported for this synthesis.2,38–45 Among these catalysts, we rarely come across cases where the synthesis of these compounds occurs at room temperature without the need for high temperatures or energies such as ultrasound and microwaves.42,43 This is something that should be taken into consideration.
According to the above points, we report here Ni-TMEDA@βSiO2@αSiO2@Fe3O4 as a highly effective and magnetic nanocatalyst for the preparation of pyrido[2,3-d:6,5-d′]dipyrimidine derivatives through the Hantzsch reaction in water solvent at 25 °C under mild conditions.
2. Experimental
2.1. Preparation of Fe3O4
In order to prepare magnetic nanoparticles made of iron oxide (Fe3O4) using the chemical co-precipitation process, at first, 1.165 gr of FeCl3·6H2O was added to a solution that included 100 mL of H2O and 0.429 g of FeCl2·4H2O. The mixture was stirred for two hours at 70 °C under N2 atmosphere. After that, 20 mL of ammonia was added to the combination of reactants in a drop-by-drop fashion. After a total of three hours of stirring, the finished mixture was cooled to room temperature. By means of an outside magnet, the black precipitate was separated and rinsed in hot, deionized water six times. The resulting nano-Fe3O4 was then dried for 8 hours at 80 °C (Scheme 1).46
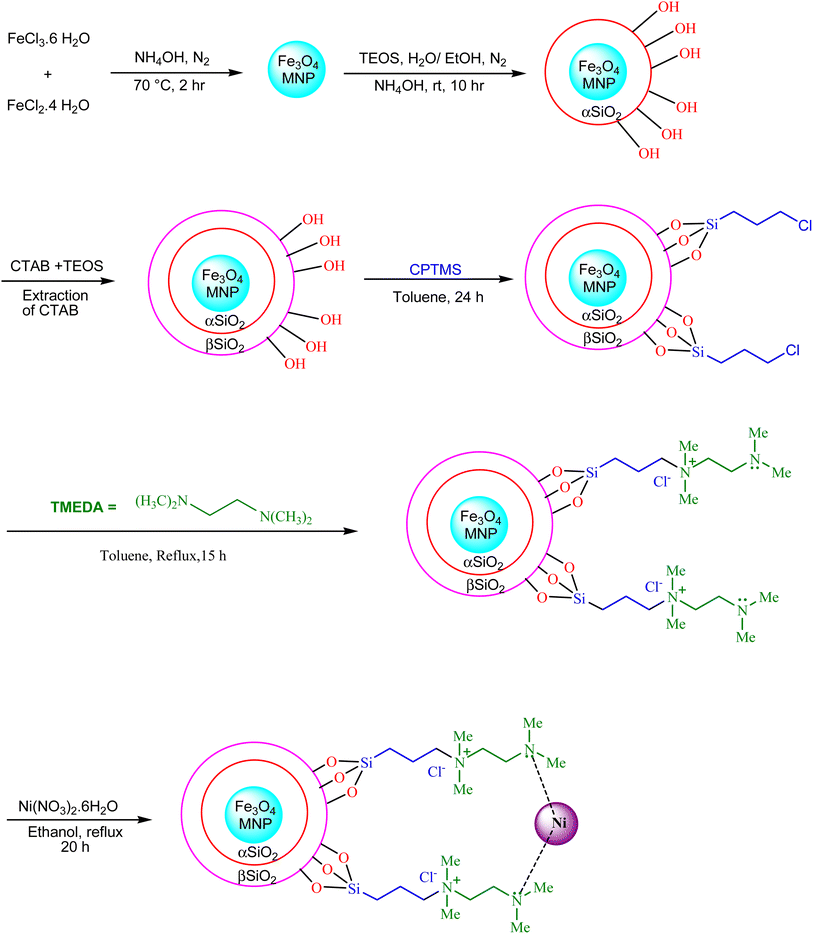 |
| Scheme 1 Synthesis of Ni-TMEDA@βSiO2@αSiO2@Fe3O4. | |
2.2. Preparation of βSiO2@αSiO2@Fe3O4
In order to create silica-coated magnetite, 2.5 g of Fe3O4 nanoparticles were diluted with 160 mL of deionized H2O and 300 mL of ethanol, and then this solution was dispersed in an ultrasonic bath for a period of forty minutes. The combination was then given an addition of 5 mL of a concentrated ammonia aqueous solution. This step took place in the presence of N2. After that, 2 mL of tetraethyl orthosilicate were gradually added to this dispersion while stirring it at a temperature of 25 °C for ten hours. Finally, the αSiO2@Fe3O4 nanoparticles were separated employing a magnet, washed many times in EtOH and distilled H2O, and dried at 60 °C. Nanoporous SiO2 shells were covered on the particles via dispersing the produced αSiO2@Fe3O4 (0.1 g) in a solution including cetyltrimethyl ammonium bromide (CTAB, 0.3 g), EtOH (40 mL), NH4OH (25 wt%, 1 mL) and distilled H2O (60 mL). In continue 0.5 mL TEOS were added (drop by drop) into the suspension, then the solution produced was stirred for 20 h (at 25 °C). In the next step, the βSiO2@αSiO2@Fe3O4 was isolated by external magnet and washed and dried using the procedure expressed in the previous section (Scheme 1).
2.3. Preparation of Ni-TMEDA@βSiO2@αSiO2@Fe3O4
At this stage, to prepare nPr-Cl@βSiO2@αSiO2@Fe3O4, first 2 g of βSiO2@αSiO2@Fe3O4 were sonicated in 60 mL of n-hexane for 35 min, after that, 3.5 milliliters 3-chloropropyltrimethoxysilane (CPTMS) was added to the solution that had been prepared and stirred for 24 hours in toluene reflux. Then, magnetic nanoparticles (nPr-Cl @βSiO2@αSiO2@Fe3O4) were washed with ethanol, separated with an external magnet, and dried at 50 °C. Next, the nPr-Cl @βSiO2@αSiO2@Fe3O4 MNPs solid (1 g) is mixed with (1 mmol) N,N,N′,N′-tetramethylethane-1,2-diamine in toluene (15 mL) and let to stand at 115 °C for 15 hours to immobilize the TMEDA on the surface of the MNPs. In the last step of the method, nickel was immobilized onto TMEDA@βSiO2@αSiO2@Fe3O4. This was accomplished by first dissolving 1 gr of TMEDA@βSiO2@αSiO2@Fe3O4 NPs in ethanol, and then adding Ni(NO3)2·6H2O (4 mmol, 1.163 g) to the resulting mixture. The resultant mixture was subjected to a total of twenty hours of agitation while in a condition of reflux. The Ni-TMEDA@βSiO2@αSiO2@Fe3O4 NPs that had been generated were eventually dried in an air environment after being filtered and washed with ethanol many times (Scheme 1).
2.4. General method for the preparation of pyrido[2,3-d:6,5-d′]dipyrimidines using a by catalyst Ni-TMEDA@βSiO2@αSiO2@Fe3O4
A mixture that included 2-thiobarbituric acid (2 mmol, 0.288 g), NH4OAc (1.3 mmol 0.100 g), aldehyde (1 mmol), Ni-TMEDA@βSiO2@αSiO2@Fe3O4 (2.6 mol%, 0.01 g), and H2O (2 mL) as a solvent was agitated at a temperature of 25 °C. After completion of the reaction (as observed by TLC), 20 mL of H2O was added to the reaction mixture, stirred for 1 min (at 50 °C), and filtered to separate the catalyst (in the presence of a magnet). The isolated catalyst was washed by EtOH (2 × 3 mL), dried and used for next run. Finally, the water was evaporated, and the remainder precipitate was recrystallized from EtOH (96%) to afford the pure product (Scheme 2).
 |
| Scheme 2 Ni-TMEDA@βSiO2@αSiO2@Fe3O4 catalyzed the synthesis pyrido[2,3-d:6,5-d′]dipyrimidines. | |
3. Results and discussion
3.1. Catalyst characterization
FT-IR data of Fe3O4, βSiO2@αSiO2@Fe3O4, TMEDA@βSiO2@αSiO2@Fe3O4 and Ni-TMEDA@βSiO2@αSiO2@Fe3O4 are summarized in Table 1 (Fig. 1). These data confirm the presence of the expected bonds, the immobilization of SiO2 on Fe3O4 and the subsequent formation of TMEDA@βSiO2@αSiO2@Fe3O4. Also, the functionalization of βSiO2@αSiO2@Fe3O4 with TMEDA was exhibits by stretching vibration of C–N at 1386 cm−1, which this band was shifted to lower frequency in the Ni-TMEDA@βSiO2@αSiO2@Fe3O4 (1382 cm−1), which is due to the coordination of Ni to supported TMEDA onto functionalized βSiO2@αSiO2@Fe3O4.47 Based on these observations, the well anchoring of nickel onto TMEDA@βSiO2@αSiO2@Fe3O4 is verified.
Table 1 The FT-IR data of Fe3O4 (A), βSiO2@αSiO2@Fe3O4 (B), TMEDA@βSiO2@αSiO2@Fe3O4 (C) and Ni-TMEDA@βSiO2@αSiO2@Fe3O4 (D)
Peak (spectrum name) (cm−1) |
Assignments |
579 (A), 578 (B), 579 (C), 588 (D) |
Fe–O stretching47 |
805 (B), 800 (C), 798 (D) |
Si–O–Si symmetric stretching2 |
950 (B), 952 (C), ∼950 (D) |
Si–O–Fe stretching2 |
1076 (B), 1098 (C), 1091 (D) |
Si–O–Si asymmetric stretching47 |
1386 (C), 1382 (D) |
C–N stretching2 |
∼1482 (C), 1482 (D) |
CH2 bending2 |
1630 (A), 1630 (B), 1634 (C), 1653 (D) |
OH bending on the surface of the Fe3O4 and SiO2 (ref. 2 and 47) |
2939 (C), 2938 (D) |
C–H symmetric stretching2 |
3429 (A), 3433 (B), 3435 (C), 3428 (D) |
OH stretching on the surface of the Fe3O4 and SiO2 (ref. 2 and 47) |
 |
| Fig. 1 The FT-IR spectrums of Fe3O4 (A), βSiO2@αSiO2@Fe3O4 (B), TMEDA@βSiO2@αSiO2@Fe3O4 (C) and Ni-TMEDA@βSiO2@αSiO2@Fe3O4 (D). | |
The scanning electron microscope (SEM) method was used in order to produce high-resolution pictures of Ni-TMEDA@βSiO2@αSiO2@Fe3O4. The images obtained from this technique were employed to specify the morphology of the catalyst; these images show that most of the particles are quasi-spherical (Fig. 2(a)). Also, the particle size distribution of the Ni-TMEDA@βSiO2@αSiO2@Fe3O4 demonstrated that these nanoparticles have a size in the range of 10–100 nm and an average diameter of 47.72 nm (Fig. 2(b)).
 |
| Fig. 2 The FE-SEM images (a) and particle size distribution (b) of Ni-TMEDA@βSiO2@αSiO2@Fe3O4. | |
The TEM micrograph of Ni-TMEDA@βSiO2@αSiO2@Fe3O4 is shown in Fig. 3; we observe quasi-spherical cases from the micrograph. The calculated amount of Ni in nanocatalyst which was achieved via inductively coupled plasma (ICP) analysis was found to be 2.6 × 10−3 mol g−1.
 |
| Fig. 3 The TEM Ni-TMEDA@βSiO2@αSiO2@Fe3O4. | |
EDX analysis of the Ni-TMEDA@βSiO2@αSiO2@Fe3O4 was carried out so that the elements that were present in the catalyst structure could be identified (Fig. 4). This study reveals the presence of carbon, oxygen, silicon, nitrogen, iron, and nickel. In addition to this, the outcomes of the EDS were validated by the elemental mapping analysis, as demonstrated in (Fig. 5). Homogeneous distribution of all elements and dispersion of nickel throughout the support was clearly observed in this analysis.
 |
| Fig. 4 The EDX Ni-TMEDA@βSiO2@αSiO2@Fe3O4. | |
 |
| Fig. 5 The mapping of Ni-TMEDA@βSiO2@αSiO2@Fe3O4. | |
The VSM technique was used to evaluate the magnetic properties of Fe3O4 and Ni-TMEDA@βSiO2@αSiO2@Fe3O4. As can be seen in Fig. 6, Ni-TMEDA@βSiO2@αSiO2@Fe3O4 has a lower magnetic value than Fe3O4. This is because organic groups act as a shield for the surface of Fe3O4, reducing its magnetic strength.
 |
| Fig. 6 Magnetization curves for Fe3O4 (a) and Ni-TMEDA@βSiO2@αSiO2@Fe3O4 (b). | |
The XRD spectrum of Ni-TMEDA@βSiO2@αSiO2@Fe3O4 was studied at 2θ = 10° to 80° (Fig. 7); in this spectrum, the diffraction lines observed at 2θ = 33.4°, 38.3°, 42.7°, 54.4°, 58.4° and 61.7° are related to the crystalline nature of Fe3O4 particles.47 These findings affirmed that the modification of SiO2 nanoparticles on Fe3O4 did not lead to a changes in the crystalline nature of magnetite nanoparticles; this is in accordance with the previous literature.48 The Bragg angles (2θ) at 44.5 (111), 50.6 (200) and 73.4 (220) confirmed the presence of nickel in the catalyst and its immobilization on βSiO2@αSiO2@Fe3O4.49 Also, the broad peak observed at 2θ = 20°-30° is associated to the silica skeleton (especially amorphous silica) in the catalyst body;2 the amorphous and crystalline percentages of Ni-TMEDA@βSiO2@αSiO2@Fe3O4 were 21.56 and 78.44%, respectively.
 |
| Fig. 7 The XRD pattern of Ni-TMEDA@βSiO2@αSiO2@Fe3O4. | |
The thermal stability diagram of Ni-TMEDA@βSiO2@αSiO2@Fe3O4 is displayed in Fig. 8. In the first stage, the TGA diagram demonstrates a weight loss of 6% at temperatures below 200 °C, which is possibly associated with the elimination of adsorbed organic solvents.3,48 The weight loss of the second stage (∼7%) in this graph, which occurs in the temperature range of 250–700 °C, can be related to the decomposition of immobilized organic groups on the surface of Fe3O4. These data provide compelling evidence that the material has a high thermal stability.3,48
 |
| Fig. 8 TGA analysis of Ni-TMEDA@βSiO2@αSiO2@Fe3O4. | |
Nitrogen adsorption desorption method was used to investigate the porosity of Ni-TMEDA@βSiO2@αSiO2@Fe3O4 nanocatalyst and its producing components (Fig. 9–11). The results of this study are summarized in Table 2. Based on the data in this table, the specific surface area of Ni-TMEDA@βSiO2@αSiO2@Fe3O4 has decreased compared to TMEDA@βSiO2@αSiO2@Fe3O4, αSiO2@Fe3O4 and Fe3O4; this is due to the stabilization of organic groups and nickel complexes on the mesoporous channels of magnetic silica nanoparticles.50,51 The specific surface (SBET) of each material can be calculated through eqn (1), where, AN2 is atomic surface area of N2 at 77 K (0.162 nm2), N and Vm are the Avogadro's number and monolayer volume, respectively (eqn (2)).52
|
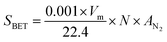 | (1) |
|
 | (2) |
 |
| Fig. 9 Nitrogen adsorption–desorption isotherms of (a) αSiO2@Fe3O4 (b) TMEDA@βSiO2@αSiO2@Fe3O4 (c) Ni-TMEDA@βSiO2@αSiO2@Fe3O4. | |
 |
| Fig. 10 The pore size distribution (BJH model) of Ni-TMEDA@βSiO2@αSiO2@Fe3O4. | |
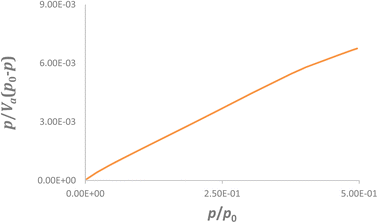 |
| Fig. 11 The BET curve of Ni-TMEDA@βSiO2@αSiO2@Fe3O4. | |
Table 2 Texture properties of Ni-TMEDA@αSiO2@βSiO2@Fe3O4
Sample |
SBET (m2 g−1) |
Pore diam by BJH method (nm) |
Pore vol (cm3 g−1) |
Ref. |
Fe3O4 |
480.0 |
1.254 |
0.803 |
50 |
αSiO2@Fe3O4 |
455.2 |
1.564 |
0.789 |
— |
TMEDA@βSiO2@αSiO2@Fe3O4 |
404.6 |
1.798 |
0.716 |
— |
Ni-TMEDA@βSiO2@αSiO2@Fe3O4 |
330.1 |
2.012 |
0.621 |
— |
3.2. Study of catalytic property
After successful synthesis and characterization of Ni-TMEDA@βSiO2@αSiO2@Fe3O4 catalyst, its catalytic performance was carefully investigated in the preparation of pyrido[2,3-d:6,5-d′]dipyrimidines at room temperature. In this regard, for selection of the best catalyst amount, type and amount of solvent, the condensation of 2-nitrobenzaldehyde (1 mmol) with 2-thiobarbituric acid (2 mmol) and NH4OAc (1.3 mmol) was chosen as a model reaction (Scheme 1), and examined in the presence of different amounts of Ni-TMEDA@βSiO2@αSiO2@Fe3O4 using various solvents. The results are briefed in Table 3. As it is indicated in this Table, higher yield of the product was acquired in shorter time by utilization of 0.01 g of nanomagnetic catalyst in water solvent (2 mL) (Table 3, entry 2). The reason for this is that non-polar solvents are unsuitable for dissolving ammonium acetate salt (Table 3, entries 6–8); also, the results showed that the mixture of water and ethanol (3
:
1) was equally effective but in a longer time (Table 3, entry 9). In another research, the reaction was examined under optimal conditions in the presence of the reactants for the synthesis of Ni-TMEDA@βSiO2@αSiO2@Fe3O4, i.e. TMEDA (Table 3, entry 10), Fe3O4 (Table 3, entry 11), βSiO2@αSiO2@Fe3O4 (Table 3, entry 12), TMEDA@βSiO2@αSiO2@Fe3O4 (Table 3, entry 13), and also Ni(NO3)2·6H2O (Table 3, entry 14), and Ni-TMEDA@αSiO2@Fe3O4 (which prepared using monolayer of silica) (Table 3, entry 15). Then, the amount of nickel in the Ni-TMEDA@βSiO2@αSiO2@Fe3O4 and Ni-TMEDA@αSiO2@ Fe3O4 was calculated through Inductively Coupled Plasma (ICP) analysis, which was equal to 2.6 × 10−3 and 1.4 × 10−3 mol g−1, respectively. The results from Table 3 and ICP analysis showed that our strategy of using two layers of silica (αSiO2 and βSiO2) on Fe3O4 and also immobilizing nickel on the TMEDA@βSiO2@αSiO2@Fe3O4 was useful to promote the reaction efficiently, because none of the components of the catalyst alone have a significant role in the progress of the reaction, but when they are connected to each other and form the catalyst, they show a strong synergistic effect. Using two layers of silica on Fe3O4 causes more organic groups and thus more nickel metal to enter the mesoporous channels. In addition, the immobilization of SiO2 on Fe3O4 prevents the aggregation of Fe3O4 particles (Scheme 3).
Table 3 Investigating influence of catalyst, catalyst amount, type and amount of solvent on the model reaction
Entry |
Catalyst |
Catalyst amount (g) |
Solvents |
Solvent amount (mL) |
Time (min) |
Yielda (%) |
Yield of isolated product. |
1 |
Ni-TMEDA@βSiO2@αSiO2@Fe3O4 |
0.01 |
H2O |
2 |
25 |
80 |
2 |
Ni-TMEDA@βSiO2@αSiO2@Fe3O4 |
0.02 |
H2O |
2 |
15 |
99 |
3 |
Ni-TMEDA@βSiO2@αSiO2@Fe3O4 |
0.03 |
H2O |
2 |
15 |
99 |
4 |
Ni-TMEDA@βSiO2@αSiO2@Fe3O4 |
0.02 |
H2O |
1 |
15 |
90 |
5 |
Ni-TMEDA@βSiO2@αSiO2@Fe3O4 |
0.02 |
H2O |
3 |
20 |
99 |
6 |
Ni-TMEDA@βSiO2@αSiO2@Fe3O4 |
0.02 |
EtOH |
2 |
15 |
76 |
7 |
Ni-TMEDA@βSiO2@αSiO2@Fe3O4 |
0.02 |
Acetone |
2 |
30 |
39 |
8 |
Ni-TMEDA@βSiO2@αSiO2@Fe3O4 |
0.02 |
CH3CN |
2 |
30 |
42 |
9 |
Ni-TMEDA@βSiO2@αSiO2@Fe3O4 |
0.02 |
H2O/EtOH (3 : 1) |
2 |
20 |
99 |
10 |
TMEDA |
0.02 |
H2O |
2 |
15 |
Trace |
11 |
Fe3O4 |
0.02 |
H2O |
2 |
15 |
32 |
12 |
βSiO2@αSiO2@Fe3O4 |
0.02 |
H2O |
2 |
15 |
35 |
13 |
TMEDA@βSiO2@αSiO2@Fe3O4 |
0.02 |
H2O |
2 |
15 |
40 |
14 |
Ni(NO3)2·6H2O |
0.02 |
H2O |
2 |
15 |
Trace |
15 |
Ni-TMEDA@αSiO2@Fe3O4 |
0.02 |
H2O |
2 |
15 |
70 |
 |
| Scheme 3 The model reaction. | |
To confirm that Ni-TMEDA@βSiO2@αSiO2@Fe3O4 is general and effectual catalyst for the synthesis of pyrido-dipyrimidines, various aromatic aldehydes were reacted with 2-thiobarbituric acid and NH4OAc under the optimal conditions. In this investigation, arylaldehydes bearing electron-attracting, halogens and electron-donating substituents on ortho, meta and para positions were exerted. The results are displayed in Table 4. As the data in this table illustrate, arylaldehydes bearing halogen, electron-releasing and electron-withdrawing substituents on ortho, meta and para positions afforded the relevant products in high yields and short times as well as high TON and TOF values. Accordingly, Ni-TMEDA@βSiO2@αSiO2@Fe3O4 was general and highly effectual catalyst for the reaction at room temperature.
Table 4 The synthesis of pyrido[2,3-d:6,5-d′]dipyrimidines by Ni-TMEDA@βSiO2@αSiO2@Fe3O4a,b
Reaction conditions 1a–14a: aromatic aldehyde (1 mmol), 2-thiobarbituric acid (2 mmol), NH4OAc (1.3 mmol), and catalyst (0.01 g). Also reaction conditions 15a and 16a: terephthalaldehyde or isophthalaldehyde (1 mmol), 2-thiobarbituric acid (4 mmol), NH4OAc (2.6 mmol), and catalyst (0.01 g). Isolated yield. |
|
A performance of Ni-TMEDA@βSiO2@αSiO2@Fe3O4 for the production of pyrido-dipyrimidines in comparison with previous literature in this field by comparing factors such as TOF, TON, yield, time and the reaction temperature in the preparation of pyrido[2,3-d:6,5d′]dipyrimidine derivatives in the Table 5 have been reported. According to the data in the table, our c catalyst had a significant advantage over other catalysts in at least three or four comparative factors.
Table 5 Comparison of the reaction results of Ni-TMEDA@βSiO2@αSiO2@Fe3O4 with previously published catalysts in the preparation of pyrido[2,3-d:6,5-d′]dipyrimidine derivatives
Catalyst |
Conditions |
Time (min) |
Yield (%)a |
TON |
TOF (min−1) |
Ref. |
In this manuscript, we were unable to measure TON and TOF because the molar percentage of catalyst was not reported. |
Our catalyst |
H2O, r.t. |
15–30 |
89–99 |
34.2–38.0 |
1.14–2.53 |
— |
Nano-[DMSPDE][Cl]a |
Solvent-free, 110 °C |
5–20 |
84–91 |
— |
— |
2 |
Nano-[SiO2-R-NMe2SO3H][Cl] |
Solvent-free, 90 °C |
5–15 |
88–95 |
33.3–35.9 |
2.22–7.18 |
38 |
Nano CuFe2O4 |
H2O, ultrasonic (40 W) |
4–30 |
0–99 |
0.0–9.9 |
0.00–2.45 |
39 |
Nano CuFe2O4 |
H2O, microwave (100 W) |
1–2 |
90–98 |
9.0–9.8 |
4.50–9.80 |
40 |
γ-Fe2O3@HAp-SO3H |
DMF, 110 °C |
20–75 |
70–95 |
7.7–10.5 |
0.10–0.47 |
41 |
Fe-MCM-41-IL |
H2O, r.t. |
57–25 |
95–80 |
18.2–21.6 |
0.33–0.86 |
42 |
Nano CuFe2O4 |
H2O, r.t. |
120–20 |
99–0 |
0.0–9.9 |
0.00–0.49 |
43 |
[HNMP]+[HSO4]− |
H2O, ultrasonic (26.5 W) |
5–30 |
<98–5 |
<0.3–6.5 |
<0.01–1.30 |
44 |
[Et3N–SO3H][MeSO3] |
EtOH, reflux |
2–5 |
99–93 |
9.3–9.9 |
1.86–4.95 |
45 |
Based on the previous literature, which used supported nickel as an electrophilic activator,3,23 a logical mechanism for the synthesis of pyrido-dipyrimidine derivatives using our catalyst is presented in Scheme 4.38–40 Initially, the activated aldehyde by nickel as the active center of nanocatalyst reacts with intermediate II (which is produced as a result of the activation of tautomer I of 2-thiobarbituric acid in the presence of a catalyst) to provide intermediate III after removal of a water molecule. In the other hand, the activated another molecule of tautomer I by catalyst reacts with ammonia to form intermediate IV after removal of a H2O molecule. The next step is a michael addition of intermediate IV to intermediate III (which activated with catalyst), and tautomerization to form intermediate V. Finally, pyrido-dipyrimidine is produced by the intermolecular nucleophilic attack of the amine nitrogen to its activated carbonyl group in intermediate V, and elimination of a H2O molecule.
 |
| Scheme 4 The suggested mechanism for the production of pyrido-dipyrimidines. | |
3.3. Reusability of the nanocatalyst
In both the laboratory and the industrial settings, the fact that the catalysts may be recycled several times is an essential consideration. Therefore, the reusability of Ni-TMEDA@βSiO2@αSiO2@Fe3O4 was investigated during the synthesis of compound 2a; the findings obtained are summarized in Fig. 12. Recycling the catalyst was obtained by the stated method in the experimental section. The recycled catalyst was reused up to seven times without a noticeable decrease in catalytic activity. The average yields is 96.42% for 7 consecutive runs, which shows the excellent recyclability of our catalyst.
 |
| Fig. 12 The recycling experiment of Ni-TMEDA@βSiO2@αSiO2@Fe3O4 in the production of compound 2a. | |
3.4. Leaching study of catalyst
For the leaching of nickel from Ni-TMEDA@βSiO2@αSiO2@Fe3O4, ICP analysis and hot filtration test was used. According to ICP analysis, the amount of Ni in the fresh and reused catalyst was 2.60 × 10−3 mol g−1 and 2.575 × 10−3 mol g−1, respectively, which showed that Ni leaching of this catalyst is insignificant. Also, to confirm that the catalyst used is heterogeneous nature in the reaction conditions, a hot filtration test was studied for the preparation of compound 2a. In this experiment, 53% of the product was formed in half the reaction time (reaction time 15 min). Next, this reaction was reiterated and after 7.5 min from the start of the reaction, the catalyst was detached and the filtrated solution was allowed to progress for another 7.5 min without the catalyst. After this time, only 56% of product 2a was formed. This observation confirms that the leaching of Ni did not happen.
4. Conclusions
Concisely, an effectual and reusable heterogeneous catalyst known as Ni-TMEDA@βSiO2@αSiO2@Fe3O4 was produced and successfully used in the production of pyrido[2,3-d:6,5-d′]dipyrimidines. The current protocol provides very suitable turnover frequency (TOF) and turnover number (TON) values in the synthesis of all derivatives. This nanocatalyst has the advantages of both Fe3O4 (e.g. simple separation through an external magnet) and mesoporous silica (e.g. large surface area and suitable pore size for stabilizing organic ligands) systems. In addition, Ni-TMEDA@βSiO2@αSiO2@Fe3O4 was reused up to 7 times without significant loss of its activity and produced all products with high efficiency without producing any unwanted side products at room temperature.
Conflicts of interest
There are no conflicts to declare.
Acknowledgements
The authors are grateful to acknowledge the Research Council of King Saud University, Riyadh, Saudi Arabia.
References
- R. Mozafari, F. Heidarizadeh and M. Azaroon, RSC Adv., 2018, 8, 40261–40266 RSC.
- A. Zare, A. Kohzadian, Z. Abshirini, S. S. Sajadikhah, J. Phipps, M. Benamara and M. H. Beyzavi, New J. Chem., 2019, 43, 2247–2257 RSC.
- H. Filian, A. Ghorbani-Choghamarani and E. Tahanpesar, J. Iran. Chem. Soc., 2019, 16, 2673–2681 CrossRef CAS.
- P. Kumar, V. Tomar, D. Kumar, R. K. Joshi and M. Nemiwal, Tetrahedron, 2022, 106, 132641 CrossRef.
- M. N. Chen, L. P. Mo, Z. S. Cui and Z. H. Zhang, Curr. Opin. Green Sustain. Chem., 2019, 15, 27–37 CrossRef.
- M. B. Gawande, P. S. Branco and R. S. Varma, Chem. Soc. Rev., 2013, 42, 3371–3393 RSC.
- P. Rana, R. Dixit, S. Sharma, S. Dutta, S. Yadav, B. Arora, B. Kaushik, M. B. Gawande and R. K. Sharma, Nanoscale, 2023, 15, 3482–3495 RSC.
- I. Dindarloo Inaloo, S. Majnooni, H. Eslahi and M. Esmaeilpour, ACS Omega, 2020, 5, 7406–7417 CrossRef CAS PubMed.
- S. You, R. Xiao, H. Liu and M. Cai, New J. Chem., 2017, 41, 13862–13870 RSC.
- M. Nikoorazm, A. Ghorbani-Choghamaranai, M. Khanmoradi and P. Moradi, J. Porous Mater., 2018, 25, 1831–1842 CrossRef CAS.
- P. Singh, P. Yadav, A. Mishra and S. K. Awasthi, ACS Omega, 2020, 5, 4223–4232 CrossRef CAS PubMed.
- P. G. Kargar, G. Bagherzade and H. Eshghi, RSC Adv., 2020, 10, 37086–37097 RSC.
- A. Kohzadian and A. Zare, Res. Chem. Intermed., 2019, 45, 5473–5485 CrossRef CAS.
- R. C. Cioc, E. Ruijter and R. V. A. Orru, Green Chem., 2014, 16, 2958–2975 RSC.
- L. A. Taib and M. Keshavarz, Polyhedron, 2022, 213, 115630 CrossRef CAS.
- C. Parmeggiani, C. Matassini and F. Cardona, Green Chem., 2017, 19, 2030–2050 RSC.
- A. Yusuf, C. Snape, J. He, H. Xu, C. Liu, M. Zhao, G. Z. Chen, B. Tang, C. Wang, J. Wang and S. N. Behera, Catal. Rev., 2017, 59, 189–233 CrossRef CAS.
- Y. Wang, J. Li and Z. Wei, J. Mater. Chem. A, 2018, 6, 8194–8209 RSC.
- M. A. Abdelkareem, T. Wilberforce, K. Elsaid, E. T. Sayed, E. A. Abdelghani and A. G. Olabi, Int. J. Hydrogen Energy, 2021, 46, 23529–23547 CrossRef CAS.
- B. Tahmasbi and A. Ghorbani-Choghamarani, New J. Chem., 2019, 43, 14485–14501 RSC.
- A. Ghorbani-Choghamarani, Z. Taherinia and M. Mohammadi, Environ. Technol. Innovat., 2021, 24, 102050 CrossRef CAS.
- S. Pal, V. Chatare and M. Pal, Curr. Org. Chem., 2011, 15, 782–800 CrossRef CAS.
- A. Kohzadian, H. Filian, Z. Kordrostami, A. Zare and A. Ghorbani-Choghamarani, Res. Chem. Intermed., 2020, 46, 1941–1953 CrossRef CAS.
- H. Filian, A. Kohzadian, M. Mohammadi, A. Ghorbani-Choghamarani and A. Karami, Appl. Organomet. Chem., 2020, 34, e5579 CrossRef CAS.
- C. R. Nathaniel, R. Dhanya, P. V. Saranya and G. Anilkumar, ChemistrySelect, 2022, 7, e202202763 CrossRef CAS.
- V. Kolla, A. Deyanov, F. Y. Nazmetdinov, Z. Kashina and L. Drovosekova, Pharm. Chem. J., 1993, 27, 635–636 CrossRef.
- I. O. Donkor, C. L. Klein, L. Liang, N. Zhu, E. Bradley and A. M. Clark, J. Pharm. Sci., 1995, 84, 661–664 CrossRef CAS PubMed.
- J. W. Ellingboe and N. J. Princeton, Chem. Abstr., 1996, 124, 176134q Search PubMed.
- K. Furukawa and T. Hasegawa, Can. Pat. Appl.CA 2151871, 1995 Search PubMed; K. Furukawa and T. Hasegawa, Chem. Abstr., 1996, 124, 289568c Search PubMed.
- A. Deyanov, R. K. Niyazov, F. Y. Nazmetdinov, B. Y. Syropyatov, V. Kolla and M. Konshin, Pharm. Chem. J., 1991, 25, 248–250 CrossRef.
- A. Pastor, R. Alajarin, J. J. Vaquero, J. Alvarez-Builla, M. F. de Casa-Juana, C. Sunkel, J. G. Priego, I. Fonseca and J. Sanz-Aparicio, Tetrahedron, 1994, 50, 8085–8098 CrossRef CAS.
- L. L. Corre, A.-L. Girard, J. Aubertin, F. Radvanyi, C. Benoist-Lasselin, A. Jonquoy, E. Mugniery, L. Legeai-Mallet, P. Busca and Y. L. Merrer, Org. Biomol. Chem., 2010, 8, 2164–2173 RSC.
- R. K. Rawal, R. Tripathi, S. Katti, C. Pannecouque and E. De Clercq, Bioorg. Med. Chem., 2007, 15, 3134–3142 CrossRef CAS PubMed.
- A. Rosowsky, C. E. Mota and S. F. Queener, J. Heterocycl. Chem., 1995, 32, 335–340 CrossRef CAS.
- A. Monge, V. Martinez-Merino, C. Sanmartin, F. J. Fernandez, M. C. Ochoa, C. Bellver, P. Artigas and E. Fernandez-Alvarez, Eur. J. Med. Chem., 1989, 24, 209–216 CrossRef CAS.
- J. A. Kovacs, C. J. Allegra, J. C. Swan, J. C. Drake, J. E. Parrillo, B. A. Chabner and H. Masur, Antimicrob. Agents Chemother., 1988, 32, 430–433 CrossRef CAS PubMed.
- S. Trumpp-Kallmeyer, J. R. Rubin, C. Humblet, J. M. Hamby and H. D. H. Showalter, J. Med. Chem., 1998, 41, 1752–1763 CrossRef CAS PubMed.
- A. Kohzadian and A. Zare, Silicon, 2020, 12, 1407–1415 CrossRef CAS.
- H. Naeimi and A. Didar, Ultrason. Sonochem., 2017, 34, 889–895 CrossRef CAS PubMed.
- H. Naeimi, A. Didar and Z. Rashid, J. Iran. Chem. Soc., 2017, 14, 377–385 CrossRef CAS.
- M. Mamaghani, L. Moslemi and A. Badrian, Org. Chem. Res., 2018, 3, 1–10 CrossRef.
- H. Naeimi, V. Nejadshafiee and M. R. Islami, Micropor. Mesopor. Mater., 2016, 227, 23–30 CrossRef CAS.
- H. Naeimi and A. Didar, J. Mol. Struct., 2017, 1137, 626–633 CrossRef CAS.
- H. Naeimi, A. Didar, Z. Rashid and Z. Zahraie, J. Antibiot., 2017, 70, 845–852 CrossRef CAS PubMed.
- A. Zare, A. Kohzadian, H. Filian, M. S. Ghoreishi Nezhad and A. Karami, Res. Chem. Intermed., 2022, 48, 1631–1644 CrossRef CAS.
- M. Anbarasu, M. Anandan, E. Chinnasamy, V. Gopinath and K. Balamurugan, Spectrochim. Acta, Part A, 2021, 135, 536–539 CrossRef PubMed.
- A. Ghorbani-Choghamarani, B. Tahmasbi, N. Noori and S. Faryadi, C. R. Chim., 2017, 20, 132–139 CrossRef CAS.
- M. Nikoorazm, F. Ghorbani, A. Ghorbani-Choghamarani and Z. Erfani, Appl. Organomet. Chem., 2018, 32, e4282 CrossRef.
- N. A. M. Barakat, B. Kim and H. Y. Kim, J. Phys. Chem. C, 2009, 113, 531–536 CrossRef CAS.
- M. Esmaeilpour, A. R. Sardarian and J. Javidi, J. Organomet. Chem., 2014, 749, 233–240 CrossRef CAS.
- M. Nikoorazm, N. Noori, B. Tahmasbi and S. Faryadi, Transit. Met. Chem., 2017, 42, 469–481 CrossRef CAS.
- H. Tian, L. Pan, X. Xiao, R. W. T. Wilkins, Z. Meng and B. Huang, Mar. Pet. Geol., 2013, 48, 8–19 CrossRef CAS.
|
This journal is © The Royal Society of Chemistry 2023 |
Click here to see how this site uses Cookies. View our privacy policy here.