DOI:
10.1039/D3RA03509C
(Paper)
RSC Adv., 2023,
13, 22538-22548
Fe3O4 supported [Cu(II)(met)(pro-H)2] complex as a novel nanomagnetic catalytic system for room temperature C–O coupling reactions†
Received
25th May 2023
, Accepted 20th July 2023
First published on 25th July 2023
Abstract
In this study, a newly-designed copper(II) complex of metformin and L-proline which was immobilized on Fe3O4 MNPs was developed. The structure of the catalyst platform was fully characterized using spectroscopic analyses. Moreover, the catalytic activity of [Fe3O4@Cu(II)(Met)(Pro-H)2] was investigated in a one-pot synthesis of a variety of functionalized ethers in reasonable to excellent yields through Ullman reaction in an aqueous environment using various aryl halides, phenol, and Cs2CO3 and without using any external Cu-reducing agents. Notably, gentle catalytic conditions, quick reaction times, applicability, low cost, and preventing dangerous chemicals and solvents during synthesis and catalytic application are some of the superior properties of the [Fe3O4@Cu(II)(Met)(Pro-H)2] complex. Furthermore, the catalyst can be reused for several runs (at least eight times) without remarkable loss in efficiency.
1. Introduction
Nowadays, supported heterogeneous catalysts have attracted a lot of interest due to their simplicity in product separation, which enables recycling, the versatility of the supports, which facilitates adaptability, and variable surface area due to changes in shape and composition, which boosts overall efficiency to achieve maximum yield.1–5 A further benefit of the magnetic supports is their ease of mechanical separation.2,6 As a result, the current research has focused on the use of magnetic nanocomposites for their better physical and mechanical qualities, as well as their economic and environmental benefits.7,8 Due to their outstanding magnetic characteristics, high surface area and high catalytic activity, mixed metal oxide nanocomposites—especially metal-ferrites—are widely used in synthetic organic chemistry.9–12
Copper is often used in homo- and cross-coupling reactions that result in the creation of C–C, C–N, and C–O bonds.13–16 In order to successfully produce diaryl ethers, it is the common procedure to make use of supported palladium and copper catalysts.17 This cross-coupling reaction involves the use of aryl halides and phenols. Regarding the use of aryl halide-phenol cross-coupling technique, highly functionalized diaryl ethers may be produced in a more straightforward and time-efficient manner.17–19 Diaryl ethers have a variety of applications, i.e. in producing novel materials with improved functionalities, synthesis, and creating new medications.20–22 The Ullmann reaction has been put to use over the course of many years in the process of direct synthesis of aryl–heteroatom bonds originating from aryl halides.17,23,24 This is because the Ullmann reaction is very effective and produces just a limited amount of unwanted byproducts. The Ullmann reaction, which is used in the synthesis of the functionalized diaryl ethers, necessitates the presence of severe reaction conditions, an extended reaction duration, and an inert environment.
Numerous procedures using various reagents have been described so far for the Ullmann synthesis of diaryl ethers.25–27 In this sense, homogeneous copper-mediated methods have attracted interesting attention.28–30 Heretofore, various reducing agents have been utilized as an electron source to activate the Cu species.31–33 The major downsides of utilizing these chemicals are their low selectivity for desired products, production of unwanted and ecologically harmful by-products, need for stoichiometric concentration of reagents, the length of reaction durations, catalyst disposable and their reactivity with other functional groups.
Metformin consists of a 1,1-dimethyl-biguanide structure, in which two guanide molecules are bonded together, with a mode of action and application comparable to other biguanides.34 The intermolecular hydrogen bonding, conjugation system and arrangement of C
NH groups and their N–C
NH ↔ R–N
C–NH resonance forms – consisting of anomeric effects – increase the electron-donating ability of NH groups and turn it into an attractive ligand. On the other hand, the presence of an NH2 group at the end of the molecule chain gives it a special ability for further functionalization.35–37 Metformin was previously used as a biguanide ligand in copper-catalyzed Ullmann-type C–N and C–O cross-couplings that show its ability in these types of reactions.38 To address the above-mentioned deficiencies, we focus on the immobilization of metformin on the nanomagnetic Fe3O4 MNPs and its complexation with copper nitrate trihydrate and L-proline to generate the desired biguanide–copper catalyst for Ullmann-type cross-coupling of aryl halides with phenol – which results in generating the diaryl ethers under green conditions.
2. Experimental
2.1. Typical procedure for the synthesis of [Fe3O4@Cu(II)(Met)(Pro-H)2] MNPs
The initial step was to synthesize Fe3O4 MNPs using the chemical co-precipitation technique39 and, then, a layer of alkyl chloride functionalities was placed around their surface using the CPTMS linker as mentioned in scientific literature.40 In the next step, 1 g of Fe3O4@CPTMS was dispersed in DMSO containing 5 mmol of NaI (0.745 g) for 30 min and, then, 5 mmol of metformin (0.646 g) was added to the reaction mixture and stirred under reflux conditions for 48 hours. After the mixture was cooled, the synthesized Fe3O4@metformin MNPs were accumulated using an external magnet, washed with water and ethanol and, finally, dried at 80 °C. Eventually, 1 g of Fe3O4@metformin MNPs was dispersed in 100 mL of ethanol and, then, it was treated with Cu(NO3)2·3H2O (0.241 g, 1 mmol) and proline (0.230 g, 2 mmol) and stirred under reflux conditions for 24 h. The obtained [Fe3O4@Cu(II)(Met)(Pro-H)2] complex was accumulated applying an external magnet, washed using water and, finally, dried at 80 °C.
2.2. General procedure for the preparation of 2,4-diarylquinoline derivatives in the presence of [Fe3O4@Cu(II)(Met)(Pro-H)2]
A mixture of phenol (1 mmol), aryl halide (1 mmol), Cs2CO3 (1.5 mmol) and [Fe3O4@Cu(II)(Met)(Pro-H)2] (8 mg) was stirred in water (2 mL) for the appropriate time at reflux conditions. After reaction completion, it was monitored using TLC. Furthermore, the catalyst was collected via magnetic decantation and, then, the produced organic product was extracted using ethyl acetate. Subsequently, it was dried using anhydrous sodium sulfate and, then, purified applying column chromatography.
3. Results and discussion
3.1. Characterization of the catalyst
It is in Scheme 1 that preparation of the catalyst is depicted. The following approaches were used to extensively characterize the as-prepared catalyst.
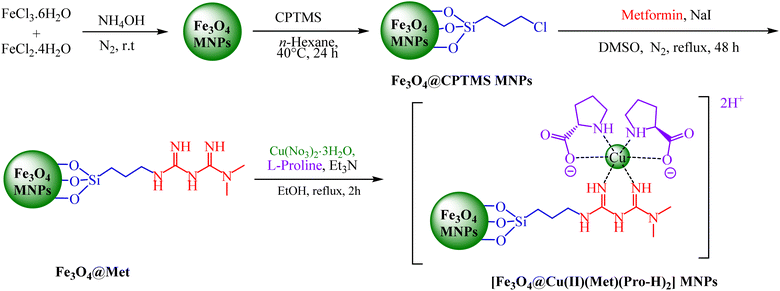 |
| Scheme 1 Synthesis of [Fe3O4@Cu(II)(Met)(Pro-H)2] MNPs. | |
3.1.1. FT-IR spectroscopy. In order to explore the synthesis of catalytic support and stabilization of diverse functional groups; including, linker, ligand and formation of catalytic complex on its surface, FTIR analysis was performed on different synthesis stages. As depicted in Fig. 1, the Fe3O4, Fe3O4@CPTMS and Fe3O4@Met FT-IR spectra perfectly match with the earlier reports on the fingerprint of these samples.41,42 The peaks appearing at 580 cm−1 and 630 cm−1 are attributed to characteristic stretching vibration mode of metal–oxygen (Fe–O) bonds.43 Moreover, the faint peak at 810 cm−1 and the sharp and broad absorption peaks at around 960 cm−1 to −1200 cm−1 are attributed to symmetric and asymmetric Si–O–Si bond stretches, respectively.44 The bands from 1954 cm−1 to 1988 cm−1 are due to the C–H stretching vibrations of the CH2 groups of the CPTMS linker.40 Regarding Fe3O4@Met MNPs, C–Cl peak was not observed in the spectra because of its removal during SN2 nucleophilic substitution reaction. Furthermore, the stretching vibrations of C
N and C–N bands can be identified due to the presence of strong peaks in the band at around 1702 and 1636 cm−1, that confirms the hybridization of metformin groups with the surface of modified nanoparticles.45 Considering the FT-IR spectrum of [Fe3O4@Cu(II)(Met)(Pro-H)2], the aberrance of C
O bands in addition to the shift on C
N band can clearly confirm the complexation of Cu with L-proline and the heterogenized metformin moieties and also the generation of [Cu(II)(Met)(Pro-H)2] complex on the surface of Fe3O4 MNPs.46
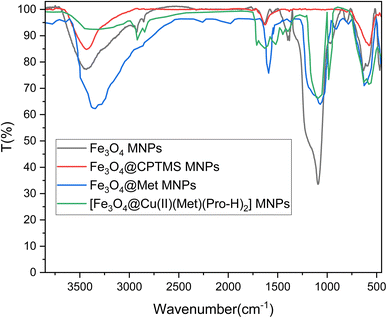 |
| Fig. 1 FTIR of (black curve) Fe3O4, (red curve)) Fe3O4@CPTMS, (blue curve) Fe3O4@Met and (green curve) [Fe3O4@Cu(II)(Met)(Pro-H)2] MNPs. | |
3.1.2. P-XRD characterization. The crystalline structure of [Fe3O4@Cu(II)(Met)(Pro-H)2] complex was assessed using XRD measurements (Fig. 2). The XRD pattern shows a high degree of crystallization and characteristic peaks of Fe3O4 at 2θ = 30.23°, 35.60°, 43.50°, 54.01°, 57.49°, 62.86°, 71.48°, and 74.27°. Furthermore, due to the addition of CPTMS linker and its polymerization around the surface, SiO2 amorphous phase peaks can be observed at around 2θ = 17–29°, demonstrating successful hybridization of inorganic support and organic phases in nanocomposites. Furthermore, the average particle size of the [Fe3O4@Cu(II)(Met)(Pro-H)2] MNPs turned out to be 23.57 nm using the Scherer equation.
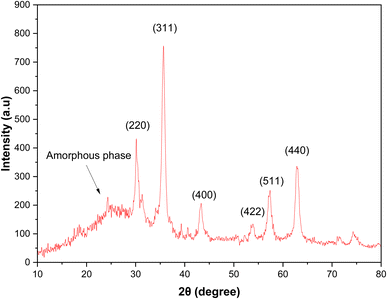 |
| Fig. 2 XRD pattern of [Fe3O4@Cu(II)(Met)(Pro-H)2] MNPs. | |
3.1.3. Thermogravimetric analysis. To examine the stability of the produced catalyst, thermogravimetric analysis (TGA) was performed (Fig. 3). Moreover, it is worth mentioning that the TGA curves reveal three phases of deterioration. At the first step, a typical weight loss of 6% is observed in the composites (happened before 200 °C) which is due to the removal of the moisture. Furthermore, the second step starts at above 230 °C. Regarding Fe3O4@CPTMS (about 5%), this step is attributed to CPTMS linker removal through the thermal decomposition to produce CO2 and water gases. Considering Fe3O4@Cu(II)(Met)(Pro-H)2, the observed increment (about 20%) at the weight loss is attributed to the decomposition of the immobilized metformin and L-proline organic moieties in [Cu(II)(Met)(Pro-H)2] complex (Fig. 3). Notably, these findings attest to the effective synthesis of the intended catalyst. Consistent with these results, the [Fe3O4@Cu(II)(Met)(Pro-H)2] is stable before 200 °C and can be used in various organic transformations.
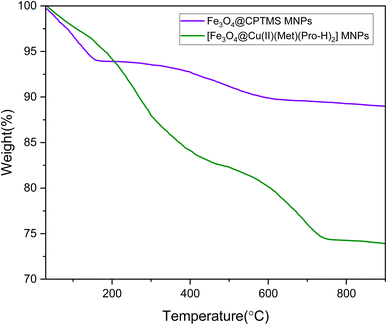 |
| Fig. 3 TGA analysis of Fe3O4@CPTMS and [Fe3O4@Cu(II)(Met)(Pro-H)2] MNPs. | |
3.1.4. Elemental analysis. Regarding EDX analysis, the elemental composition of [Fe3O4@Cu(II)(Met)(Pro-H)2] MNPs was assessed, verifying the presence of the Fe, O, Si, C, N, and Cu components. Significantly, the findings are in good agreement with the expected composition of the desired catalytic support and its surface functionalities (Fig. 4). As shown in Fig. 4, the absence of Cl and presence of copper affirm the successful immobilization of metformin and also the construction of the final complex, respectively.
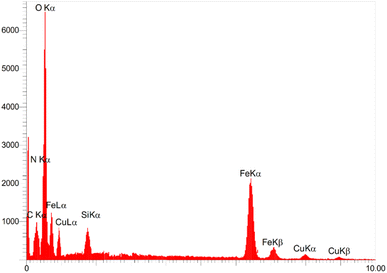 |
| Fig. 4 EDX analysis of [Fe3O4@Cu(II)(Met)(Pro-H)2] complex. | |
3.1.5. Elemental mapping analysis. Elemental mapping studies were used to analyze how the above-mentioned elements were distributed, the results of which demonstrate that the components of the produced structure – including iron, oxygen, silica, carbon, nitrogen, and copper – were uniformly distributed on the catalyst surface (Fig. 5). Additionally, [Fe3O4@Cu(II)(Met)(Pro-H)2] MNPs examination, applying inductively coupled plasma atomic emission spectroscopy (ICP-AES), revealed the presence of 1.27 mmol of Cu per 1 gram of the sample.
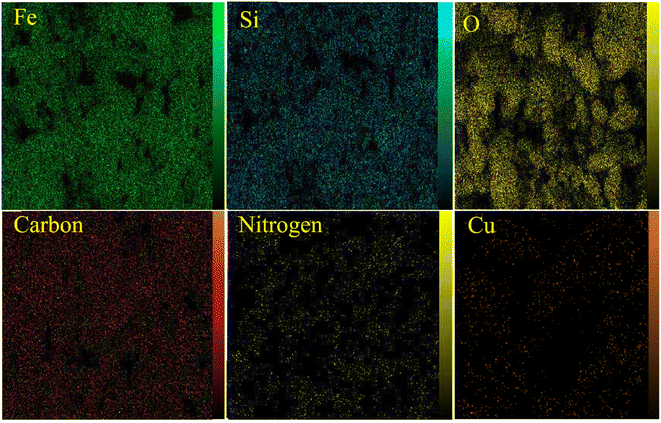 |
| Fig. 5 EDX-mapping images of [Fe3O4@Cu(II)(Met)(Pro-H)2] complex. | |
3.1.6. SEM analysis. Fig. 6 illustrates SEM image of [Fe3O4@Cu(II)(Met)(Pro-H)2] MNPs, in which it can be seen that the surface of the bar Fe3O4 MNPs is potentially covered via a mixture of the linker and catalytic complex composites, confirming an even functionalization of the catalyst nano-surface. Regarding the higher-magnification photographs at nanoscale, it can be seen that the surface of the coated particles seemed comparatively smooth and the approximately spherical particles are formed in average size of 18–28 nm. Despite this finding, the characteristics of spinel ferrite support persisted inside the structure, preserving a large specific surface area for high efficiency in catalysis applications.
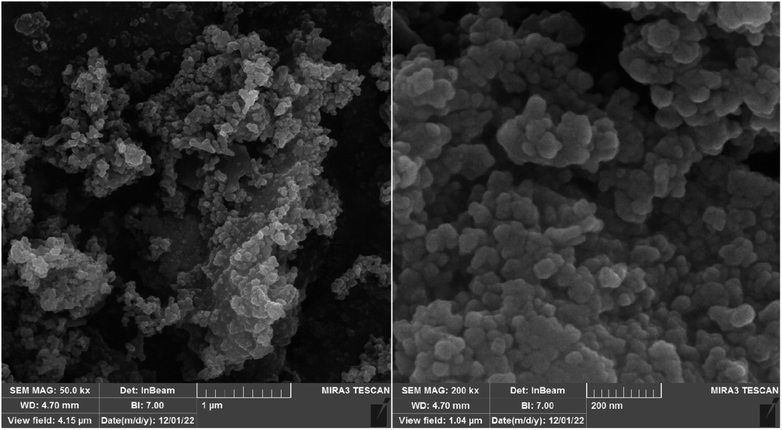 |
| Fig. 6 SEM images of [Fe3O4@Cu(II)(Met)(Pro-H)2] complex. | |
3.1.7. TEM analysis. TEM analysis was carried out to get additional information and in-depth morphological and structural information of [Fe3O4@Cu(II)(Met)(Pro-H)2] MNPs sample (Fig. 7). TEM image describes that the particles were formed in average size of 18–27 nm with a spherical structure, in which the catalytic complex together with catalyst support and [Cu(II)(Met)(Pro-H)2] shell – that covers spinel iron particles – have a thickness of around 5–8 nm. The HR-TEM results also show that the as-prepared [Fe3O4@Cu(II)(Met)(Pro-H)2] MNPs have an excellent single-crystal structure. Herein, it is worth noting that the particle dispersion is dense and the crystal superposition is shown by the dark color patches. This effect predicts that there will be a significant particle interaction and that excellent stability during the catalysis process will result from that contact.
3.1.8. Magnetic properties. The magnetic power of [Fe3O4@Cu(II)(Met)(Pro-H)2] nanoparticles was determined using VSM analysis. The saturation magnetization of the catalyst (57.03 emu g−1) is, as predicted, much lower than that of Fe3O4 nanoparticles (98 emu g−1).47,48 The addition of CPTMS linker, metformin ligand and the final [Cu(II)(Met)(Pro-H)2] complex to the surface of iron nanoparticles causes this decrease. However, the prepared nano-catalyst retains significant magnetic characteristics and can be readily isolated from the reaction mixture using an external magnet (Fig. 8).
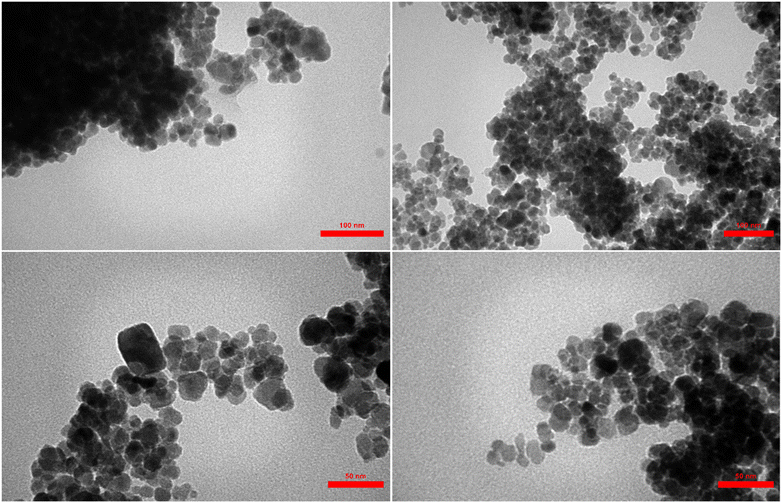 |
| Fig. 7 TEM images of [Fe3O4@Cu(II)(Met)(Pro-H)2] complex. | |
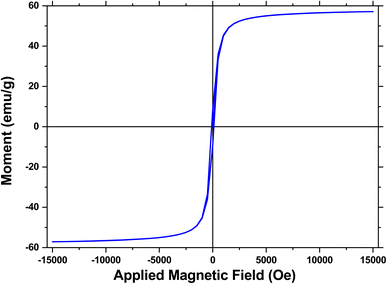 |
| Fig. 8 VSM analysis of [Fe3O4@Cu(II)(Met)(Pro-H)2] complex. | |
3.2. Catalytic properties of [Fe3O4@Cu(II)(Met)(Pro-H)2] complex
3.2.1. Optimization of reaction parameters. The [Fe3O4@Cu(II)(Met)(Pro-H)2] complex was successfully made and characterized. Afterwards, its catalytic effectiveness in the Ullmann synthesis of diaryl ethers was evaluated. This choice was made with the presumption that, under basic conditions, Cu(II) complex seems to provide a formidable weapon for the C–X bond insertion reaction to the substituted aryl halides and its cross-coupling reaction with nucleophiles – i.e. deprotonated phenol. In order to achieve the Ullmann synthesis of diaryl ethers, the reaction of iodobenzene (1 mmol), phenol (1 mmol), and K2CO3 (1.5 mmol) – in presence of [Fe3O4@Cu(II)(Met)(Pro-H)2] in 2 mL of water – was taken into consideration as the model reaction. In addition, various tests were designed to determine the optimal conditions for this organic transformation. In the first step, the amount of the catalyst was varied from 0 to 10 mg, and the results of the study showed that the yield increased in direct proportion to the amount of catalyst used (entries 1–6, Table 1). Although the highest yield was obtained when 8 mg of [Fe3O4@Cu(II)(Met)(Pro-H)2] was employed, no significant increment was occurred as compared to the run using 10 mg of the catalytic complex under the same conditions (entry 5 vs. entry 6, Table 1). As a result, 80 mg of the [Fe3O4@Cu(II)(Met)(Pro-H)2] was chosen as the optimal catalyst amount for future optimization.
Table 1 Optimization of the Ullmann synthesis of diphenyl ethers over the catalysis of [Fe3O4@Cu(II)(Met)(Pro-H)2] complex under different conditions

|
Entry |
Amount of catalyst (mg) |
Base type |
Solvent |
Temperature (°C) |
Time (h) |
Yielda,b (%) |
Reaction conditions: iodobenzene (1 mmol), phenol (1 mmol) and base (1.5 mmol) catalyst (mg) and solvent (2 mL). Isolated yields. |
1 |
— |
K2CO3 |
Water |
Reflux |
5 |
NR |
2 |
2 |
K2CO3 |
Water |
Reflux |
1 |
49 |
3 |
4 |
K2CO3 |
Water |
Reflux |
1 |
78 |
4 |
6 |
K2CO3 |
Water |
Reflux |
1 |
90 |
5 |
8 |
K2CO3 |
Water |
Reflux |
1 |
93 |
6 |
10 |
K2CO3 |
Water |
Reflux |
1 |
93 |
7 |
8 |
K2CO3 |
n-Hexane |
Reflux |
1 |
NR |
8 |
8 |
K2CO3 |
Cyclohexane |
Reflux |
1 |
NR |
9 |
8 |
K2CO3 |
Toluene |
100 |
1 |
Trace |
10 |
8 |
K2CO3 |
PEG-400 |
100 |
1 |
88 |
11 |
8 |
K2CO3 |
EtOH |
Reflux |
1 |
84 |
12 |
8 |
K2CO3 |
MeOH |
Reflux |
1 |
87 |
13 |
8 |
— |
Water |
Reflux |
1 |
Trace |
14 |
8 |
KOH |
Water |
Reflux |
1 |
23 |
15 |
8 |
NaOH |
Water |
Reflux |
1 |
27 |
16 |
8 |
Na2CO3 |
Water |
Reflux |
1 |
96 |
17 |
8 |
Cs2CO3 |
Water |
Reflux |
1 |
98 |
18 |
8 |
Et3N |
Water |
Reflux |
1 |
47 |
19 |
8 |
Pyridine |
Water |
Reflux |
1 |
35 |
20 |
8 |
Cs2CO3 |
Water |
80 |
1 |
84 |
21 |
8 |
Cs2CO3 |
Water |
60 |
1 |
42 |
22 |
8 |
Cs2CO3 |
Water |
40 |
1 |
31 |
23 |
8 |
Cs2CO3 |
Water |
r.t. |
3 |
Trace |
The influence of the solvent on the model reaction was then examined (entries 7–12, Table 1). Accordingly, the good yield in water prompted the use of green solvents. Thus, a variety of sustainable mediums was investigated to provide a high yield of the required product. Initially, we performed the reaction in nonpolar solvents; but no substantial yield was detected (entries 7–9, Table 1). Furthermore, polar solvents such as PEG-400, EtOH and MeOH failed to produce a higher yield of C–O cross-coupling product in comparison to water (entries 8–12 vs. 6, Table 1). Significantly, considering reactions that occur on water, the hydrophobic nature of the reactants causes them to come closer together, leading to an increase in reaction rates. Additionally, the hydrogen bonding between organic compounds and water at the interface can activate the reactants and sometimes stabilize the transition states. Therefore, water can serve as both a solvent and a catalyst in these reactions.49–52 Fortunately, water was identified to be the suitable solvent, due to the act that it produced a high yield of the target product in a low reaction temperature and minimized the release of dangerous chemicals into the environment (entry 6, Table 1).
Afterwards, numerous inorganic and organic bases were screened as part of the optimization research (entries 14–19, Table 1). In the absence of a base, a really low yield of the diaryl ether product was achieved (entry 13, Table 1). Strong bases, including KOH and NaOH produced modest yields (entries 14–15, Table 1). Considering a variety of bases, Cs2CO3 was identified to be an appropriate base for the high yield synthesis of the target product (entry 18, Table 1).
Further efforts (entries 20–23, Table 1) revealed that the temperature was more effective on the reaction efficiency than any other parameter. At room temperature, the Ullmann synthesis of diaryl ethers required a longer reaction time, resulting in a considerably decreased product. Considering the product yield, the optimal parameters of the present protocol are 8 mg of catalyst and 1.5 equivalents of Cs2CO3 in an aqueous medium at reflux conditions (entry 17, Table 1).
3.2.2. Reaction scope. Therefore, the generality and practical versatility of [Fe3O4@Cu(II)(Met)(Pro-H)2] complex-catalyzed Ullmann synthesis of diaryl ethers under the optimized conditions were explored using various combinations of the substituted aryl halide and phenol substrates under standard conditions (Table 2). In most cases, highly functionalized diaryl ether adducts were synthesized from the reaction of different substituted aryl halides (I, Br and Cl) and phenol in good to outstanding yields with no by-products. The catalyst indicated unique performance for aromatic halides including electron-donating and electron-withdrawing groups. The reaction proceeded easily for highly functional aryl halides and led the synthesis of highly substituted diaryl ethers in good yields. According to the results, aryl iodides are much more reactive than aryl bromides and chlorides, respectively. Additionally, it is worth mentioning that phenols bearing different functional groups splendidly reacted under the optimal conditions. Moreover, we believe that the absence of homo-coupling products further supports the selectivity and efficiency of our developed method. Finally, a gram-scale experiment was performed on the model reaction and, accordingly, the corresponding diphenyl ether was successfully isolated with 96% of yield, confirming the scalability of this procedure.
Table 2 The Ullmann synthesis of diaryl ethers over the catalysis of [Fe3O4@Cu(II)(Met)(Pro-H)2] complex in water
3.2.3. Reaction mechanism. Based on earlier studies,54 Fig. 3 shows a probable mechanism for the reductive Ullmann C–O cross-coupling reaction. Initially, Ar–O–Cu species are formed through the base-assisted deporotonation of phenol and its nucleophilic substitution to the Cu complex. In the next step, the copper complex undergoes oxidative addition into the aryl bond, resulting in the formation of intermediate (b). In the next step, the base-assisted displacement of the halogen atom leads to the formation of intermediate (c). Finally, the reductive elimination produces the required diaryl ether product and regenerates catalytic Cu species (Scheme 2).
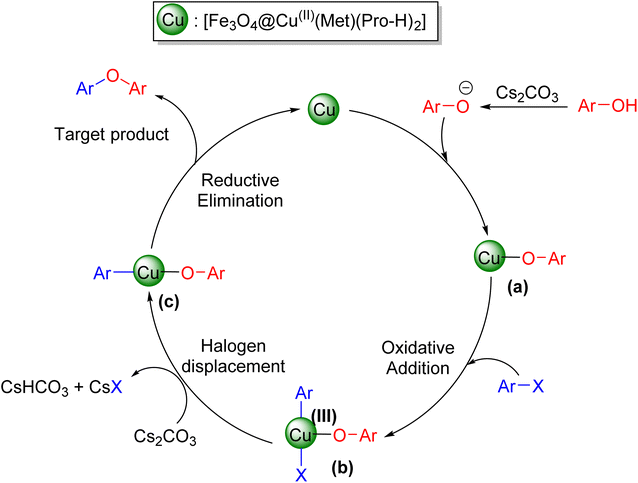 |
| Scheme 2 The proposed mechanism for the Ullmann synthesis of diaryl ethers over [Fe3O4@Cu(II)(Met)(Pro-H)2] catalyst. | |
3.3. Cycling stability
One of the most notable characteristics of environmentally friendly catalysts is their capacity to be recycled. In fact, the reusability of a new catalyst should be checked in order to understand its cycling stability and operational applicability. In this regard, a research on the reusability of the synthesized [Fe3O4@Cu(II)(Met)(Pro-H)2] complex was carried out. After the reaction was finished, an external magnet was used to separate the [Fe3O4@Cu(II)(Met)(Pro-H)2] catalytic complex from the reaction medium. Afterwards, the nanocomposite was washed using water, acetone, and ethanol. Eventually, the newly acquired catalyst was used in the subsequent reaction cycles. It is intriguing to note that the recovered [Fe3O4@Cu(II)(Met)(Pro-H)2] complex could maintain its catalytic activity with very little loss throughout the course of eight consecutive reaction cycles, as shown in Fig. 9.
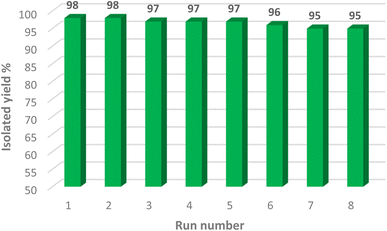 |
| Fig. 9 Reusability of [Fe3O4@Cu(II)(Met)(Pro-H)2] MNPs. | |
3.3.1. Hot-filtration and leaching test. In order to evaluate the [Fe3O4@Cu(II)(Met)(Pro-H)2] MNPs heterogeneity, hot filtration test was carried out. After 10–20% of conversion, [Fe3O4@Cu(II)(Met)(Pro-H)2] MNPs were completely withdrawn from the reaction mixture so as to reduce the amount of leached copper that would be reabsorbed onto the surface of the catalyst. Moreover, the filtrate was reintroduced into the oil bath and was allowed to proceed for the remaining time of its progress. Following the completion of the reaction, the filtrate was collected in order to conduct an analysis using ICP-AES to quantify the content of leached copper. Significantly, copper was not detected in the filtrate in any appreciable concentrations at all. Furthermore, the rate of conversion in the collected filtrates did not rise any further after the separation of the catalyst. The results of the hot filtration and leaching tests demonstrate that [Fe3O4@Cu(II)(Met)(Pro-H)2] complex performs an effective catalytic function in the successful synthesis of the respective target molecules without causing any leaching to occur in the reaction media. Based on these findings, it seems that the nanocatalyst had a heterogeneous composition.
3.3.2. Comparison. Table 3 presents the results of a comparison between the effectiveness of our method and that of other methods proposed for the preparation of diaryl ethers. Regarding the current method, [Fe3O4@Cu(II)(Met)(Pro-H)2] complex produced higher yields while maintaining the same level of efficiency. On the contrary, the previously reported methodologies were mediated by costly catalysts. Notably, the use of this strategy as an alternative to the Ullmann C–O cross-coupling reactions is made possible by the combination of a low-cost complex and utilizing an environmentally friendly and recyclable solvent, which is water. Additionally, the suitability of this strategy is partly due to the fact that toxic materials are not applied and used.
Table 3 Comparison the efficiency of [Fe3O4@Cu(II)(Met)(Pro-H)2] with existing catalysts
Entry |
Catalyst |
Time (min) |
Yielda (%) |
Ref. |
Isolated yields. |
1 |
Cu-IS-AMBA |
180 |
97 |
55 |
2 |
Fe3O4@AMCA-MIL53(Al)-NH2-CoII |
360 |
95 |
56 |
3 |
(1,4-C6H4)(GO-CPTMS@HPTPy-Pd-TPy)2 |
24 h |
96 |
57 |
4 |
Cu-IS-AMBA-MNPs |
180 |
97 |
55 |
5 |
MWCNTs-Met/CuCl |
8 |
96 |
35 |
6 |
CuI |
22 h |
95 |
19 |
7 |
[Fe3O4@Cu(II)(Met)(Pro-H)2] |
60 |
98 |
This work |
4. Conclusion
Considering the L-proline–Cu-complex support, we were able to successfully show the use of a commonly accessible and environmentally friendly metformin-modified Fe3O4 MNPs platform in the course of this research. The [Fe3O4@Cu(II)(Met)(Pro-H)2] complex was generated and evaluated – regarding its effectiveness in the Ullman reaction as a magnetic heterogeneous nanocatalyst that is environmentally friendly, efficient, stable, and reusable. The synthesis of diaryl ethers was successfully accomplished in reflux conditions of water as an environmentally friendly solvent. This approach resulted in high to exceptional yields of the respective ethers in a relatively short amount of time. The reported protocol offered notable features, i.e. using readily available commercial materials, applying relatively inexpensive raw materials, recyclability of the catalyst for at least four times, ease of catalyst separation from the reaction medium with the assistance of external magnets, short reaction times, good to decent yields with excellent selectivity, and gentle reaction conditions.
Conflicts of interest
There are no conflicts to declare.
References
- M. Atarod, J. Safari and H. Tebyanian, Synth. Commun., 2020, 50, 1993–2006 CrossRef CAS
. - W. Sun, J. Zhu, M. Zhang, X. Meng, M. Chen, Y. Feng, X. Chen and Y. Ding, Chin. J. Catal., 2022, 43, 2273–2300 CrossRef CAS
. - F. Ghobakhloo, D. Azarifar, M. Mohammadi, H. Keypour and H. Zeynali, Inorg. Chem., 2022, 61, 4825–4841 CrossRef CAS PubMed
. - A. Nikseresht, R. Bagherinia, M. Mohammadi and R. Mehravar, RSC Adv., 2023, 13, 674–687 RSC
. - H. Keypour, J. Kouhdareh, S. Alavinia, K. Rabiei, M. Mohammadi, A. Maryamabadi and S. Babaei, J. Organomet. Chem., 2023, 989, 122646 CrossRef CAS
. - V. B. Khajone, K. R. Balinge and P. R. Bhagat, Catal. Lett., 2021, 151, 1948–1960 CrossRef CAS
. - P. Salehpour and A. Abri, Colloids Surf., B, 2022, 220, 112903 CrossRef CAS PubMed
. - F. Ghobakhloo, D. Azarifar and M. Mohammadi, J. Phys. Chem. Solids, 2023, 175, 111222 CrossRef CAS
. - M. K. Bharti, S. Chalia, P. Thakur, S. N. Sridhara, A. Thakur and P. B. Sharma, Environ. Chem. Lett., 2021, 19, 3727–3746 CrossRef CAS
. - N. Thomas, D. D. Dionysiou and S. C. Pillai, J. Hazard. Mater., 2021, 404, 124082 CrossRef CAS PubMed
. - L. E. Caldeira, Eng. Mater., 2022, 1–16 Search PubMed
. - M. A. C. Florez, G. F. Ribas, J. J. R. Rovira, A. M. M. García, S. A. S. da Mata, E. Rodríguez-Castellón and M. J. G. da Silva, Metall. Mater. Trans. A, 2022, 53, 1276–1293 CrossRef CAS
. - K. Kunz, U. Scholz and D. Ganzer, Synlett, 2003, 2003, 2428–2439 CrossRef
. - F. Zhou and Q. Cai, Beilstein J. Org. Chem., 2015, 11, 2600–2615 CrossRef CAS PubMed
. - F. Cheng, T. Chen, Y.-Q. Huang, J.-W. Li, C. Zhou, X. Xiao and F.-E. Chen, Org. Lett., 2022, 24, 115–120 CrossRef CAS PubMed
. - Y. Liu and J. Wan, Chem.–Asian J., 2012, 7, 1488–1501 CrossRef CAS PubMed
. - H.-J. Cristau, P. P. Cellier, S. Hamada, J.-F. Spindler and M. Taillefer, Org. Lett., 2004, 6, 913–916 CrossRef CAS PubMed
. - S. Akkarasamiyo, S. Ruchirawat, P. Ploypradith and J. S. M. Samec, Synthesis, 2020, 52, 645–659 CrossRef CAS
. - J. W. W. Chang, S. Chee, S. Mak, P. Buranaprasertsuk, W. Chavasiri and P. W. H. Chan, Tetrahedron Lett., 2008, 49, 2018–2022 CrossRef CAS
. - T. Chen, H. Xiong, J.-F. J.-F. Yang, X.-L. X.-L. Zhu, R.-Y. R.-Y. Qu and G.-F. G.-F. Yang, J. Agric. Food Chem., 2020, 68, 9839–9877 CrossRef CAS PubMed
. - K. Smith and D. Jones, J. Chem. Soc., Perkin Trans. 1, 1992, 407 RSC
. - N. Jalalian, E. E. Ishikawa, L. F. Silva and B. Olofsson, Org. Lett., 2011, 13, 1552–1555 CrossRef CAS PubMed
. - Anuradha, S. Layek, B. Agrahari and D. D. Pathak, ChemistrySelect, 2017, 2, 6865–6876 CrossRef CAS
. - M. L. Rahman, M. S. Sarjadi, C. J. Fui, S. Guerin, S. C. Pillai and S. M. Sarkar, J. Cleaner Prod., 2023, 390, 136015 CrossRef CAS
. - Z. Noorpoor and S. Tavangar, J. Coord. Chem., 2021, 74, 1651–1662 CrossRef CAS
. - R. M. Al-Zoubi, R. M. Altamimi, W. K. Al-Jammal, K. Q. Shawakfeh, M. S. Al-Zoubi, M. J. Ferguson, A. Zarour, A. Yassin and A. Al-Ansari, Synth, 2021, 53, 2665–2675 CrossRef CAS
. - S. Tanaka and K. Maeyama, Chem. Lett., 2023, 52, 296–298 CrossRef CAS
. - C. J. Fui, M. S. Sarjadi, S. M. Sarkar and M. L. Rahman, Catalysts, 2020, 10, 1103 CrossRef CAS
. - N. Kaur, Synth. Commun., 2019, 49, 879–916 CrossRef CAS
. - R. Akhtar, A. F. Zahoor, M. Irfan, T. H. Bokhari and A. ul Haq, Chem. Pap., 2022, 76, 7275–7293 CrossRef CAS
. - M. B. Gawande, A. Goswami, F.-X. Felpin, T. Asefa, X. Huang, R. Silva, X. Zou, R. Zboril and R. S. Varma, Chem. Rev., 2016, 116, 3722–3811 CrossRef CAS PubMed
. - A. Khan, A. Rashid, R. Younas and R. Chong, Int. Nano Lett., 2016, 6, 21–26 CrossRef CAS
. - M. Bollenbach, P. Wagner, P. G. V. Aquino, J. J. Bourguignon, F. Bihel, C. Salomé and M. Schmitt, ChemSusChem, 2016, 9, 3244–3249 CrossRef CAS
. - M. T. da Trindade, A. C. Kogawa and H. R. N. Salgado, Crit. Rev. Anal. Chem., 2018, 48, 66–72 CrossRef PubMed
. - E. Akhavan, S. Hemmati, M. Hekmati and H. Veisi, New J. Chem., 2018, 42, 2782–2789 RSC
. - M. Nasrollahzadeh, Z. Nezafat, K. Pakzad and F. Ahmadpoor, J. Organomet. Chem., 2021, 948, 121915 CrossRef CAS
. - Z. S. Robatjazi, M. R. Naimi-Jamal and M. Tajbakhsh, Sci. Rep., 2022, 12, 4949 CrossRef CAS PubMed
. - R. Ghorbani-Vaghei, S. Hemmati and H. Veisi, Tetrahedron Lett., 2013, 54, 7095–7099 CrossRef CAS
. - B. Nammalwar, N. P. Muddala, R. Pitchimani and R. A. Bunce, Molecules, 2015, 20, 22757–22766 CrossRef CAS PubMed
. - A. Jafari, S. Heydari, M. Ariannezhad, S. Ahmadi and D. Habibi, Chem. Phys. Lett., 2022, 786, 139195 CrossRef CAS
. - H. Yao, Y. Wang and M. K. Razi, RSC Adv., 2021, 11, 12614–12625 RSC
. - A. Mazaheri and M. Bostanian, Res. Chem. Intermed., 2020, 46, 2327–2350 CrossRef CAS
. - N. Taheri, F. Heidarizadeh and A. Kiasat, J. Magn. Magn. Mater., 2017, 428, 481–487 CrossRef CAS
. - I. Dindarloo Inaloo, S. Majnooni, H. Eslahi and M. Esmaeilpour, Appl. Organomet. Chem., 2020, 34, e5662 CrossRef CAS
. - F. Hajizadeh, A. Amiri, B. Maleki and F. Mohammadi Zonoz, Microchem. J., 2022, 175, 107176 CrossRef CAS
. - G. K. Kharmawlong, R. Nongrum, B. Chhetri, J. W. S. Rani, N. Rahman, A. K. Yadav and R. Nongkhlaw, Synth. Commun., 2019, 49, 2683–2695 CrossRef CAS
. - M. Colombo, S. Carregal-Romero, M. F. Casula, L. Gutiérrez, M. P. Morales, I. B. Böhm, J. T. Heverhagen, D. Prosperi and W. J. Parak, Chem. Soc. Rev., 2012, 41, 4306 RSC
. - M. D. Nguyen, H.-V. Tran, S. Xu and T. R. Lee, Appl. Sci., 2021, 11, 11301 CrossRef CAS PubMed
. - N. A. Harry, S. Radhika, M. Neetha and G. Anilkumar, ChemistrySelect, 2019, 4, 12337–12355 CrossRef CAS
. - T. Kitanosono, K. Masuda, P. Xu and S. Kobayashi, Chem. Rev., 2018, 118, 679–746 CrossRef CAS PubMed
. - T. Kitanosono and S. Kobayashi, Chem.–Eur. J., 2020, 26, 9408–9429 CrossRef CAS PubMed
. - M. Cortes-Clerget, J. Yu, J. R. A. Kincaid, P. Walde, F. Gallou and B. H. Lipshutz, Chem. Sci., 2021, 12, 4237–4266 RSC
. - A. Ghorbani-Choghamarani, Z. Seydyosefi and B. Tahmasbi, Appl. Organomet. Chem., 2018, 32, e4396 CrossRef
. - R. Giri, A. Brusoe, K. Troshin, J. Y. Wang, M. Font and J. F. Hartwig, J. Am. Chem. Soc., 2018, 140, 793–806 CrossRef CAS PubMed
. - M. M. Khodaei, A. Alizadeh and M. Haghipour, Res. Chem. Intermed., 2019, 45, 2727–2747 CrossRef CAS
. - A. Mohammadinezhad and B. Akhlaghinia, Catal. Lett., 2020, 150, 332–352 CrossRef CAS
. - K. Bahrami and H. Targhan, Appl. Organomet. Chem., 2019, 33, e4842 CrossRef
.
|
This journal is © The Royal Society of Chemistry 2023 |
Click here to see how this site uses Cookies. View our privacy policy here.