DOI:
10.1039/D3RA03835A
(Paper)
RSC Adv., 2023,
13, 24944-24954
Performance investigation of LiCl·H2O-γ-Al2O3 composite materials for low-grade heat storage
Received
8th June 2023
, Accepted 14th August 2023
First published on 22nd August 2023
Abstract
In this study, the influences of nano γ-Al2O3 on the thermal storage performance of LiCl were experimentally investigated. The XRD results show that a complex of lithium aluminium oxychloride (LiAlOCl2) was formed through the LiCl·H2O and γ-Al2O3 composites preparation process. The in situ diffuse reflectance infrared Fourier transform spectroscopy measurement reveals that the addition of γ-Al2O3 accelerated the hydration rate of LiCl composites, concentrated the spectrum utilization range, and promoted the desorption rate of physical adsorbed H2O and low-frequency structural –OH in the materials. The highest specific surface area of the composite is 34.5 times higher than that of pure LiCl. The addition of γ-Al2O3 can increase the conversion rate of LiCl·H2O to approximately 100% at the hydration time of 1 h and the addition content of γ-Al2O3 at 15 wt%. A maximum heat storage density (HSD) for the LiCl·H2O-γ-Al2O3 composite can reach 714.7 kJ kgLiCl·H2O−1 in 1 h when the addition content of γ-Al2O3 was 15%wt and its water uptake can reach 0.26 g g−1 in 1 h. It also can be found that the addition of Al2O3 in LiCl resulted in a decrease of the activation energy from 90.89 kJ mol−1 to 79.76 kJ mol−1. However, the thermal conductivity of the LiCl·H2O-γ-Al2O3 composite slightly decreased with the increase of nano γ-Al2O3 content.
1 Introduction
Plenty of waste heat, about 66% being low-grade heat (below 200 °C), is discharged into the environment directly during industrial processes.1,2 Therefore, the efficient use of low-grade waste heat can reduce energy consumption, which has been attracting much attention during recent decades.3–5 Unfortunately, low-grade waste heat is difficult to recover and utilize due to its low exergy.6 Thermal energy storage (TES) technologies are some of the most hopeful methods for realizing continuous and stable utilization of waste heat,7 which is classified into three types: sensible,8,9 latent10,11 and thermochemical heat storage (TCS).12–14 TCS utilizing reversible chemical reactions to store and release energy with high HSD15–17 and lossless heat storage18 makes a promising and useful contribution to the storage of low-grade thermal energy. Various TCS materials have been studied, such as metal salts with water,19,20 ammonia,21–23 methanol,24,25 or metal alloys with hydrogen.26,27 In a relevant research article, Cot-Gores et al. reported that water as an environmentally friendly adsorbate could meet the requirements of safety system, and crystalline hydrate as a heat storage material had a good development prospect.28 Hygroscopic salts like LiCl, LiBr, KBr, and CaCl2 can be used as suitable heat storage materials.29
Lithium chloride hydrate (LiCl·nH2O) was selected as a promising candidate for low-grade heat storage.30 The reversible chemical reaction31 for LiCl at normal temperatures and pressures is as follows:
|
LiCl·H2O(s) ↔ LiCl(s) + H2O(g)
| (1) |
The deliquescence relative humidity (DRH) value for LiCl at 30 °C is 11%. The complete water absorption process of inorganic salts can be considered as a three-phase process involving chemisorption (mainly energy storage part), gas/liquid/solid three-phase liquid hydrolysis/crystallization, liquid/gas absorption and other processes. Most scholars mainly pay attention to the total amount of water vapor adsorption of hygroscopic salt materials to increase the HSD,32–34 but rarely pay attention to the adsorption amount per unit time (sorption kinetics) on materials' use. In some industrial waste heat recycle, a large amount of waste heat needs to be treated or recovered promptly. For the short-term TCS, the proportion of chemical heat storage should be enhanced to increase the HSD per unit time.35 To improve the sorption kinetics and solve limitations (deliquescence and agglomeration) of LiCl, composites are usually advanced by adding porous media with high specific surface area to increase the contact abilities with water.30,36–39 Zhao et al. modified LiCl with zeolite, and the water uptake capacity within 1 h was less than 0.15 g g−1 at 25 °C and 80% RH.40 Zhang et al. chose activated alumina spherical grain (3.29–5.30 mm) as the matrix and LiCl as the inserted salt and the maximum water uptake capacity within 1 h was about 0.2 g g−1 at 20 °C and 80% RH and its adsorption capacity per unit time has been greatly improved compared with other materials.41 Existing studies mainly focus on the thermochemical characterizations of the prepared composite materials, there is a lack of further theoretical analyses and in-depth study on the reaction kinetics of hydration and dehydration process, which is of exceptional importance for deeper understanding of the heat storage mechanism. Moreover, to motivate advancement of TCE in the field short-term energy storage, the sorption performances of composite materials must be further improved. Powdered nano aluminum oxide (Al2O3) attracts the attention of many scholars to choose it to selective adsorption for gases, water vapor and water in some liquids as the additive due to its high porosity, high activity, and low cost.42–46 And it was also proven that a small amount of transition metals and their oxides have a large effect on the thermodynamic properties of MgH2 (ref. 47) and the cations had a strong influence on the hydration energy.48–50
To further improve the water sorption kinetics of materials for short-term TCS, this paper selected powdered nano γ-Al2O3 as the additive which can increase the contact opportunities and binding capacity with water, and the proportion of LiCl is greatly increased to strengthen the hydration reactants. The structure and properties of LiCl-γ-Al2O3 TCS composites were analyzed by in situ diffuse reflectance infrared Fourier transform (DRIFT) spectroscopy, X-ray diffraction (XRD), and other micro characterization methods. Then, a further study on how γ-Al2O3 affected the sorption kinetics and thermal storage performance of LiCl from the aspect of reaction mechanism was investigated.
2 Experimental methods
2.1 Materials and preparation procedure
All the raw materials are purchased from Aladdin Reagent Co., Ltd. The LiCl (purity, >99.99%) was used as hydrated salt. Nano γ-Al2O3 (purity, >99.9%) was selected as the porous matrix. Fig. 1 schematically illustrates the preparation process of LiCl-γ-Al2O3 composites. Firstly, pretreat LiCl and γ-Al2O3 with an oven at 100 °C for 2 h and prepare four LiCl solutions which concentration are 10% and volume is 90 ml respectively. Then different mass (526.3 mg, 1111.1 mg, 1764.7 mg, 2500 mg) of γ-Al2O3 was impregnated with the LiCl solution at a stirring rate of 600 rpm for 12 h to form the composite solution. Finally, the composite solutions were dried at 100 °C for 12 h, and then at 200 °C for 6 h in the oven, to obtain the anhydrous composites (LiCl-Al2O3). The hydrous composites (LiCl·H2O-Al2O3) were acquired by the hydration of the anhydrous composites in a constant temperature and humidity chamber (Labonce-60CH, ±0.5 °C, ±3% RH) at 30 °C and 60% RH. The masses were measured by an analytical balance (MS105DU, Mettler-Toledo, ±0.01 mg). The resulting materials were sequentially named LiCl·H2O-Al2O3-5%, LiCl·H2O-Al2O3-10%, LiCl·H2O-Al2O3-15% and LiCl·H2O-Al2O3-20%.
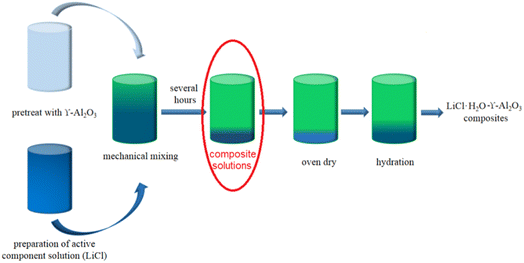 |
| Fig. 1 Preparation flow chart of LiCl-γ-Al2O3 composites. | |
2.2 Characterization and thermal storage performance evaluation of composites
The transmission electron micrographs (TEM) equipped with a FEI Tecnai G212 and a JEOL JEM-2100F was used to record microstructure pictures. The crystal structures of the samples were analyzed and obtained on a D8-advance X-ray diffractometer with a scanning step of 0.0167° and counting time of 10.160 s per step. The thermal conductivity was measured by a hot disk thermal constant analyzer (TPS 500 (S), Hot Disk AB Company, Sweden, ±5%). The Brunauer–Emmett–Teller (BET) specific surface area and pore volume were evaluated by the nitrogen physical adsorption method with the Quantachrome QDS-30 analyzer (±1%). After obtaining hydrates, the thermogravimetric and differential thermal analyzer (TG-DSC, STA-200, Nanjingdazhan, ±0.1 °C) was used to measure the endothermic heat and weight change during the dehydration step. The TG-DSC curves were described by heating the samples from 30 °C to 200 °C at the heating rate of 10 °C min−1 under the nitrogen atmosphere.
The uncertainty of the composite content was mainly caused by the mass measurements of the LiCl and Al2O3. Therefore, the content of LiCl in composite (z) is calculated from:
|
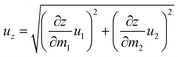 | (2) |
where, the masses of LiCl and Al
2O
3 are respectively denoted as
m1 and
m2;
u1 and
u2 are the uncertainties associated with
m1 and
m2, respectively. The accuracy of the electronic balance is ±0.01 mg. Therefore, the uncertainties of the composite content of 95%, 90%, 85%, 80% are ±0.00045%, ±0.00041%, ±0.00037%, and ±0.00033%, respectively.
The uncertainty analysis of the hydration conversion of LiCl (αLiCl) can be evaluated by the following equation.
|
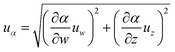 | (3) |
where
uw is the uncertainty of the relative mass change (
w) measurement. The accuracies of the electronic balance in TG-DSC, is ±0.01 mg. Finally, the uncertainty of
αLiCl is about 1.11–1.61%.
2.3 Presentation of in situ DRIFT spectroscopy
KBr (99.99% spectroscopy grade), obtained from Aladdin Reagent Co., Ltd, was used as the background material and was dried at 200 °C for 6 h before testing. The effect of nano γ-Al2O3 on the hydration/dehydration reaction of LiCl·H2O in a quasi environmental state was studied by in situ DRIFT spectroscopy Nicolet 6700 and thermogravimetric analysis of TA tgaq50, USA. Prior to the acquisition of in situ DRIFT spectra, pure LiCl and the LiCl-γ-Al2O3 composites were dried at 200 °C for 8 h in the oven, and the reactor was purged with N2 for 20 min. Then, the samples were placed in the in situ reactor immediately. The reactor was purged using an N2 flow with water vapor (100 ml min−1). The condition for hydration was at 26 °C and around 60% RH. After the hydration reaction, the LiCl·H2O was heated at a rate of 10 °C min−1 under the control of temperature-programmed technology with a dry N2 flow.
3 Results and discussion
XRD patterns of pure LiCl and LiCl·H2O-Al2O3 composites were recorded at room temperature as shown in Fig. 2. Diffraction peaks at around 23.08°, 32.97°, 34.97°, 40.71°, 47.46° and 58.67° are attributed to LiCl·H2O, while peaks at 30.18°, 34.97°, 50.24°, 54.51° and 59.12° belong to LiAlOCl2, a complex formed by LiCl·H2O and γ-Al2O3.51 In the XRD pattern of the composites, even if the mass fraction of γ-Al2O3 is as high as 20%, there is no corresponding peak of γ-Al2O3. This indicates that Li+ with small radius is likely to enter into the lattice of γ-Al2O3 and react in bulk.50 Both LiCl and Al2O3 are Lewis acids. In the process of obtaining dehydrated composite materials by impregnation, the following equation mainly occurs: |
LiCl·H2O(s) → LiCl(s) + H2O(g)
| (4) |
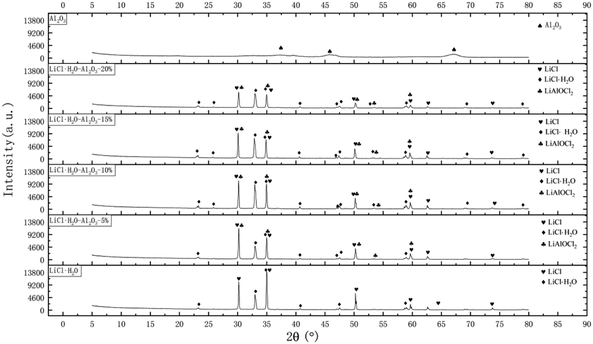 |
| Fig. 2 XRD patterns of pure LiCl·H2O, γ-Al2O3, LiCl·H2O-Al2O3-5%, LiCl·H2O-Al2O3-10%, LiCl·H2O-Al2O3-15%, LiCl·H2O-Al2O3-20% samples with different nano γ-Al2O3 contents. | |
However, in the process of heating, hydrolysis will also occur,52 as follows:
|
LiCl·H2O(s) → LiOH(s) + HCl(g)
| (5) |
Al2O3 is an amphoteric substance which can react both with base (LiOH) or acid (HCl).
|
6LiOH + Al2O3 → 2Al(OH)3 + 3Li2O
| (6) |
|
6HCl + Al2O3 → 2AlCl3 + 3H2O
| (7) |
Meanwhile, HCl can react with Al(OH)3 as follows.
|
6HCl + 2Al(OH)3 → 2AlCl3 + 3H2O
| (8) |
At this time, LiCl and AlCl3 may form composite salt LiAlCl4.53
|
AlCl3 + LiCl → LiAlCl4
| (9) |
Then, LiAlOCl2 may be generated by the following equation:51
|
Li2O + LiAlCl4 → LiAlOCl2 + 2LiCl
| (10) |
Compared to the XRD patterns of pure LiCl, there was a clear reduction of the relative intensity of the Bragg diffraction peaks at ambient temperature with the increase of γ-Al2O3 content. In addition, there are many diffraction peaks of LiCl·H2O in the composites, which are 25.87°, 47.02°, 68.99°, and 78.94° respectively. It is speculated that –AlCl bond is formed after the reaction of LiCl with γ-Al2O3, which reduces the activation energy of hydration reaction.54 It can be seen from XRD patterns that the diffraction intensity become lower and the diffraction peak range become wider. According to Scherrer formula, the reason for the above phenomenon may be that the addition of γ-Al2O3 provides more loading area for LiCl, so that LiCl can absorb more water vapor in the same test environment and time, resulting in the decrease of diffraction intensity; and the other reason is that the particles size of the composites become smaller and more dispersed than that of pure LiCl which can be seen in the TEM images.
The TEM images of pure LiCl, LiCl·H2O-Al2O3-5%, LiCl·H2O-Al2O3-10%, LiCl·H2O-Al2O3-15%, and LiCl·H2O-Al2O3-20% are shown in Fig. 3a–j. It can be seen that after contacting with water vapor during the TEM experiment, the pure LiCl generates agglomeration as a whole shown in Fig. 3a with strip crystal structure (about 7.3 nm, the blue part in Fig. 3b). This is due to the rapid reaction of LiCl with water vapor in the air during the preparation process before the test. When TEM shooting, there will be small moving layers (about 30 nm, the red part in Fig. 3b) on the edge and surface of the sheet structure, and the small moving layers and strip crystal structure will be significantly reduced after adding γ-Al2O3 (Fig. 3c–j). In addition, it can be found that with the increase of γ-Al2O3 content, the transparency of TEM images increases gradually which is mainly because the distribution of Al2O3 becomes uniform. When the content of γ-Al2O3 reaches 20% (Fig. 3i and j), the average particle size of γ-Al2O3 nanoparticles can be reduced to around 11.07 nm, and the distribution of Al2O3 is more consistent than that observed in Fig. 3c–h (with lower γ-Al2O3 content).
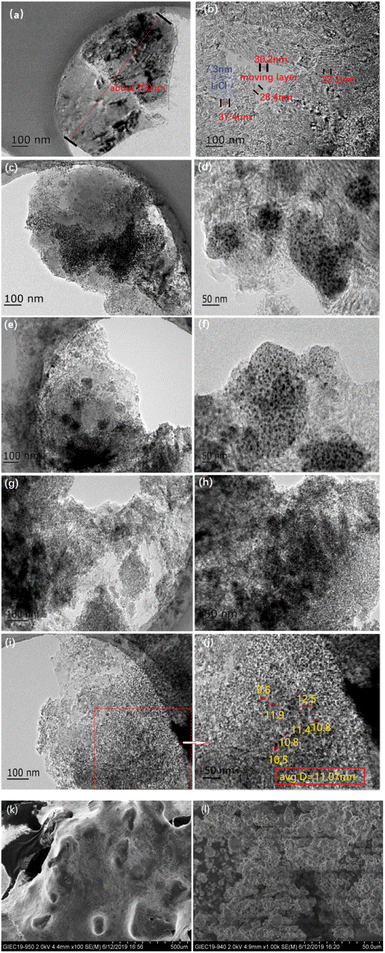 |
| Fig. 3 TEM images of samples: (a and b) pure LiCl; (c and d) LiCl·H2O-Al2O3-5%, (e and f) LiCl·H2O-Al2O3-10%; (g and h) LiCl·H2O-Al2O3-15%; (i and j) LiCl·H2O-Al2O3-20% with different nano γ-Al2O3 contents; SEM images of samples; (k) pure LiCl·H2O; (l) LiCl·H2O-Al2O3-20%. | |
The SEM images of pure LiCl and LiCl·H2O-Al2O3-20% are shown in Fig. 3k and l. The pure LiCl generates agglomeration as a whole (≫500 μm) shown in Fig. 3k. While the particles size range of LiCl·H2O-Al2O3-20% is 2.5–10 μm which is much smaller than that of pure LiCl. In summary, the results show that the increase of γ-Al2O3 content is beneficial to the dispersion of LiCl, effectively inhibit the agglomeration of LiCl and LiCl·H2O, and facilitate the hydration process.
Fig. 4 can be used to observe the whole process of hydration and dehydration of pure LiCl·H2O and composites. The in situ DRIFT spectroscopy of the hydration reaction of LiCl and H2O are showed in Fig. 4a. The materials were dried at 200 °C for 8 h in the oven before hydration, while the weak peaks standing for structural –OH and physical adsorbed H2O can be observed in Fig. 4a, demonstrating that the materials partially hydrated during the sample placement due to the hygroscopic property of LiCl. The stretching vibrations of structural –OH and physical adsorbed H2O always assign to the bands in the range of 3800–2200 cm−1.50 The bands at 3630–2950 cm−1 and at 1700–1580 cm−1 which the peak was centered at around 1673 cm−1 in the spectra can be respectively attributed to the stretching vibrations (νOH-s) and bending vibrations (βOH-s) of the structural –OH in LiCl·H2O.54,55 Moreover, the broad peak in the 3423–2842 cm−1 range centered around 3400 cm−1 and the peak at 1640 cm−1, respectively, belonged to the stretching vibrations (νOH-p) and bending vibrations (βOH-p) of the physical adsorbed H2O. The band between νOH-p and βOH-p (2500–1900 cm−1 centered at 2125 cm−1) was called the sum frequency absorption H2O band.50,54 As the hydration reaction proceeds, the bandwidth of νOH-s markedly increased from 10 min to 70 min, indicating the continuous reaction of LiCl and H2O after 70 min, the hydration reaction rate gradually decreased. In addition, it can be observed that the peak intensities of βOH-s gradually decreased while the βOH-p gradually appeared due to the deliquescence of LiCl. At the same time, the sum frequency absorption H2O band gradually became wider.
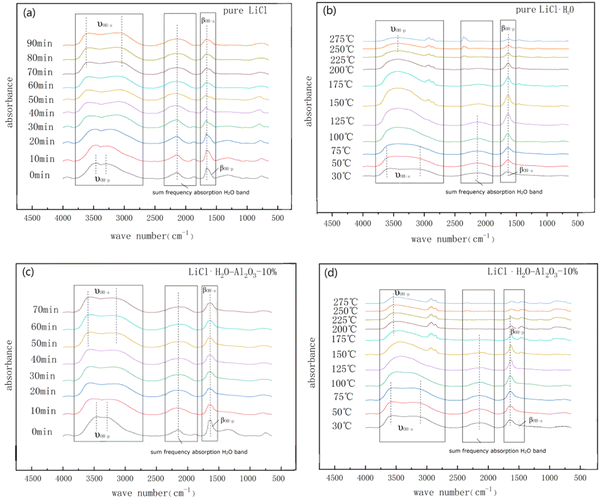 |
| Fig. 4 The in situ DRIFT spectroscopy of (a) the hydration reaction of LiCl; (b) dehydration reaction of LiCl·H2O; (c) hydration reaction of LiCl·H2O-Al2O3-10%; (d) dehydration reaction of LiCl·H2O-Al2O3-10%. | |
Fig. 4b shows the dehydration reaction process of LiCl·H2O obtained from 1.5 h hydration of LiCl in situ DRIFT spectroscopy reactor. Because the reactor required a certain time to reach the set temperature, the ending and initial curves in Fig. 4a and b are slightly different. When heated above 75 °C, the νOH-s was getting narrower and the peak intensities of βOH-s started to rise and the trend became more evident over 100 °C. With the increase of temperature, structural –OH and physical adsorbed H2O gradually disappeared.
Fig. 4c shows the hydration reaction process of LiCl-Al2O3-10% and H2O in situ DRIFT spectroscopy reactor. The νOH-s bands showed an obvious broadening to 3630–2950 cm−1 within 10 min hydration because of the existing metal coordination bond (Al3+), which formed the complex compound LiAlOCl2. It took 40 min that the νOH-s bands were virtually no longer wider, shorter than that of pure LiCl (70 min), indicating that the nano γ-Al2O3 addition enhanced the hydration reaction rate of LiCl.
Fig. 4d presents the in situ DRIFT spectroscopy of dehydration reaction of LiCl·H2O-Al2O3-10%. When LiCl·H2O-Al2O3-10% was heated over 75 °C, the peak intensities of νOH-s and βOH-s became sharper and narrower; beyond 125 °C, the dehydration of the composite gradually slowed down. The hydrogen bonding with Al3+ on the surface of γ-Al2O3 started to decompose. The peak intensities of –OH in structural H2O did not change until 175 °C, which was lower than that of pure LiCl·H2O (225 °C). It can be found that the addition of γ-Al2O3 accelerated the hydration rate of LiCl, concentrated the utilization range of the spectrum, and promoted the desorption rate of physical adsorbed H2O and low-frequency structural –OH in the materials that are consistent with our XRD data. The main reason is that the addition of Al3+ can enhance the stretching vibration of structural –OH (3630–2950 cm−1), lead to the formation of coordination bonds between structural –OH and metal ions and promote the formation of intermolecular hydrogen bonds that further strengthens the binding of water molecules.50,51
The nitrogen adsorption isotherms and pore size distributions of LiCl·H2O-Al2O3-5%, LiCl·H2O-Al2O3-10%, LiCl·H2O-Al2O3-15% and LiCl·H2O-Al2O3-20% were carried out by the nitrogen adsorption method and shown in Fig. 5. It can be seen from Fig. 5a that in the low pressure region (p/p0 < 0.2), there is a weak interaction between the adsorbate and the pore wall, and the adsorption curve rises slowly. With the increase of relative pressure, that is, when 0.2 < p/p0 < 1, the adsorption curve rises gradually. This is a typical type III adsorption isotherm, indicating that the pores are mainly mesoporous. With the increase of Al2O3 concentration, the increasing range of adsorption curve will be higher, and the hysteresis loop appears, which is due to the occurrence of mesoporous capillary condensation in the adsorption process, resulting in irreversible desorption process. This is a typical isotherm of type III combined with type V. In addition, a small amount of micropores gradually appear with the increase of the proportion of Al2O3. According to Fig. 5b, avery small amount of 5–10 nm pores were present in the pure LiCl which may result from the stacking or the voids between of LiCl particles. However, the cumulative pore volume of pure LiCl can be ignored as compared to the γ-Al2O3, as indicated in Table 1. In contrast, the pore size distribution of LiCl-Al2O3 changed significantly (Fig. 5c) and mainly concentrated within 8–15 nm, which indicated that the addition of nano γ-Al2O3 formed a large number of nano-scale pores. As shown in Table 1, the specific surface area of pure LiCl is low (0.4 m2 g−1), and the biggest specific surface area (15.18 m2 g−1) of the composite (LiCl·H2O-Al2O3-20%) is 34.5 times higher than that of pure LiCl and the specific surface area (calculated by BET method), the pore volume and their proportion (microporous and mesoporous ratio) of the composites increase with the increase of the ratio of Al2O3. However, it has been pointed out that the mechanical mixing of additive (nano γ-Al2O3) and reactive salt (LiCl) could also lead to a increase of BET surface area compared to the reactive salt, due to the relatively high specific surface area of the additive.56 For the purpose of assess the real change of surface area caused by the addition of nano γ-Al2O3, it is proposed that the surface area should be normalized relative to the additive weight in the composite rather than the composite weight. The normalized surface (NSA) was defined as:
|
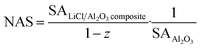 | (11) |
where SA is the specific surface area of the parent Al
2O
3 or LiCl-Al
2O
3 composite,
z is the percentage of LiCl content in composites, which is 95%, 90%, 85%, 80% for LiCl·H
2O-Al
2O
3-5%, LiCl·H
2O-Al
2O
3-10%, LiCl·H
2O-Al
2O
3-15%, LiCl·H
2O-Al
2O
3-20%, respectively. Thus the NAS for LiCl·H
2O-Al
2O
3-5%, LiCl·H
2O-Al
2O
3-10%, LiCl·H
2O-Al
2O
3-15%, LiCl·H
2O-Al
2O
3-20% is 0.25, 0.38, 0.40, 0.43. It can be found that the NSA of composites increases with the increase of Al
2O
3 content, which is consistent with the changes of BET surface area and pore volume as shown in
Table 1. However, all of these values are much less than 1, indicating that LiCl particles with the size less than the pore diameter are at least partially located inside the pore while substantial pore blocking by large LiCl particles (whose sizes are comparable or higher than Al
2O
3 pore diameter) exist.
56,57
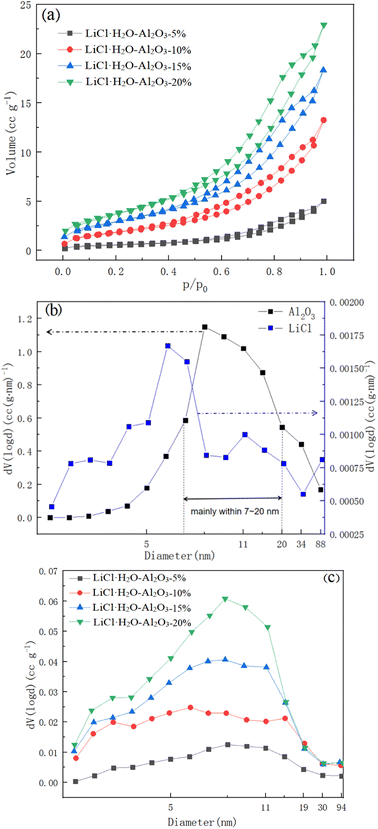 |
| Fig. 5 (a) Nitrogen adsorption isotherms of LiCl·H2O-Al2O3-5%, LiCl·H2O-Al2O3-10%, LiCl·H2O-Al2O3-15%, LiCl·H2O-Al2O3-20%; pore size distributions of; (b) LiCl and Al2O3; (c) LiCl·H2O-Al2O3-5%, LiCl·H2O-Al2O3-10%, LiCl·H2O-Al2O3-15%, LiCl·H2O-Al2O3-20%. | |
Table 1 Texture parameters of pure LiCl and composites with different nano γ-Al2O3 contents
Samples |
BET Surface area (m2 g−1) |
Pore volume (cc g−1) |
Average pore size (nm) |
γ-Al2O3 |
176.3 |
0.7 |
15.8 |
LiCl·H2O-Al2O3-20% |
15.2 |
0.04 |
10.1 |
LiCl·H2O-Al2O3-15% |
10.7 |
0.03 |
10.6 |
LiCl·H2O-Al2O3-10% |
6.8 |
0.02 |
12.1 |
LiCl·H2O-Al2O3-5% |
2.2 |
0.009 |
14.2 |
Pure LiCl |
0.4 |
0.001 |
12.6 |
The thermal storage performance and reaction mechanism of LiCl chemical thermal storage materials were studied by TG-DSC curve. The calculation quality of material HSD is based on the quality after material hydration. Fig. 6 is the TG-DSC curve of LiCl·H2O-Al2O3 composites, which have been hydrated for 1 h at 30 °C and 60% RH. The hydration conversion of LiCl (αLiCl) was calculated according to the relative mass change (w) and the percentage of LiCl content in composites (z). The calculation formula is as followed:
|
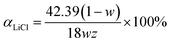 | (12) |
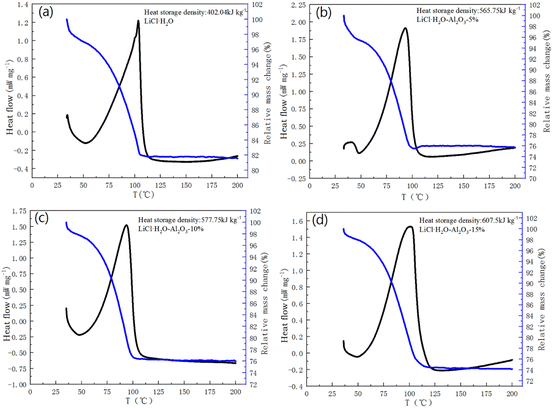 |
| Fig. 6 TG-DSC curves of: (a) LiCl·H2O; (b) LiCl·H2O-Al2O3-5%; (c) LiCl·H2O-Al2O3-10%; (d) LiCl·H2O-Al2O3-15%. | |
Due to the slow hydration rate of pure LiCl, only 51.70% of LiCl is hydrated after 1 h and its HSD is only about 402.04 kJ kg−1 (Fig. 6a). Compared with the pure LiCl, the LiCl conversion in composites can achieve 78.28%, 82.63% and 97.34% after 1 h hydration corresponding to LiCl·H2O-Al2O3-5%, LiCl·H2O-Al2O3-10% and LiCl·H2O-Al2O3-15% respectively, demonstrating that nano γ-Al2O3 is beneficial to enhance the LiCl hydration reaction rate. By changing the content of nano γ-Al2O3, the overall HSD of composites can reach 565.75 kJ kg−1 (5%), 577.75 kJ kg−1 (10%), and 607.5 kJ kg−1 (15%) respectively, and the highest HSD of LiCl·H2O monomer can be increased to 714.7 kJ kg−1 (LiCl·H2O-Al2O3-15%). Table 2 shows the comparison of water uptake amount for 1 h of the prepared composite with other reported composites for TCS. It can be found that the water uptake amount of composite prepared in this work can reach 0.26 g g−1 after 1 h hydration, exhibiting superior performance compared to other composites. Therefore, although some pores of Al2O3 are blocked by LiCl particles as discussed above, the hydration performance of reactive salt is improved by the addition of Al2O3.
Table 2 Comparison of water uptake capacity at 1 h hydration between the prepared composite and composites from literature
Composite |
LiCl (or LiOH) content [%] |
Temperature (°C) |
Relative humidity (%) |
Water uptake value (g g−1) |
LiCl/ENG-TSA/silica32 |
33.3%LiCl |
30 |
60 |
0.14 |
LiCl/zeolite40 |
47.1%LiCl |
25 |
80 |
0.15 |
LiCl/alumina spherical grain46 |
14.7%LiCl |
20 |
80 |
0.20 |
LiCl/HKUST-1 (ref. 58) |
52.4%LiCl |
35 |
50 |
0.21 |
This study |
85.0%LiCl |
30 |
60 |
0.26 |
Meanwhile, the decomposition temperature of composites were reduced compared with that of the pure material. There are two possible reasons why the hydration rate and HSD of LiCl·H2O-Al2O3 composites have been greatly increased. First, the addition of Al3+ forms coordination bonds between structural –OH and metal ions and forms more intermolecular hydrogen bonds, further strengthening the binding of water molecules and enhancing the adsorption capacity of materials on water molecules to improve the hydration reaction rate. Second, when nano γ-Al2O3 compounded with LiCl·H2O, the size of LiCl·H2O particles reaches nano-scale and the surface atomic quantity increases significantly.59
Fig. 7 illustrates the thermal conductivity (on left-hand side) and HSD (for 1 h hydration on right-hand side) of pure LiCl and LiCl-γ-Al2O3 composites after a drying period of 8 h at 200 °C. It can be seen from Fig. 7 that the thermal conductivity decreases with the increase of nano γ-Al2O3 content due to the low thermal conductivity of nano γ-Al2O3, which is about 0.3 W (m K)−1. The porosity of the initial material is the largest under the same reaction environment and the thermal conductivity is the lowest. Due to the thermal conductivity measurement was conducted immediately after the drying treatment, it can be considered that there was no water present in the composites. Therefore, the data obtained can reflect the thermal conductivity of composite materials during the initial hydration reaction. On the other hand, the HSD of composites (30 °C and 80% RH for 1 h hydration) increases along with the γ-Al2O3 ratio, demonstrating that the addition of nano γ-Al2O3 promotes the HSD of composites. The heat and mass transfer are two factors that need to be considered comprehensively for chemical heat storage. From the perspective of heat transfer, it can be seen from Fig. 7 that the optimal γ-Al2O3 addition ratio should be less than 5%. However, it also can be found that the rising ratio of HSD and the falling ratio of thermal conductivity become slow with the γ-Al2O3 addition ratio of more than 5%. For this study, the optimum addition ratio of γ-Al2O3 would be 5–10%. Consequently, there is a trade-off between thermal conductivity and HSD for practical applications.
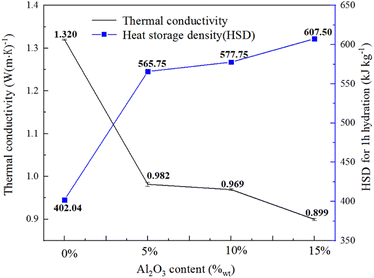 |
| Fig. 7 Variations of thermal conductivity and HSD of the composites with the Al2O3 mass content. | |
Activation energy refers to the energy required for a molecule to change from normal to an active state which is prone to chemical reactions. The chemical reaction rate is closely related to the size of the activation energy. The lower the activation energy, the faster the reaction rate. Therefore, studying the value of the activation energy can also effectively reflect the speed of the reaction.60 The activation energy of dehydration performance of LiCl and LiCl·H2O-Al2O3-15% were calculated by Ozawa method61 for computing the activation energy of thermal decomposition and dehydration reaction.62 According to Ozawa method, the following equation can be obtained:
|
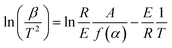 | (13) |
E is activation energy [kJ mol
−1], the value of heating rate (
β) is 3, 5, 7 and 10 [K (min)
−1],
T is temperature [K], the value of
R is 8.314 [J (mol K)
−1],
A is the pre-exponential factor,
α is the dehydration conversion and
f(
α) is the function of dehydration conversion. During the calculation of activation energy, the dehydration conversion kept constant at 70%.
61,62 As shown in
Fig. 8, the activation energy of dehydration reaction for LiCl and LiCl·H
2O-Al
2O
3-15% is 90.89 kJ mol
−1 and 79.76 kJ mol
−1, respectively. It can be found that the addition of Al
2O
3 is useful for decreasing the activation energy of composites. It is speculated that the addition of γ-Al
2O
3 provides more loading area for LiCl, so that LiCl can absorb more water vapor in the same test environment and time to promote hydration reaction. And –AlCl bond is formed after the reaction of LiCl with γ-Al
2O
3, which reduces the activation energy of dehydration reaction.
54
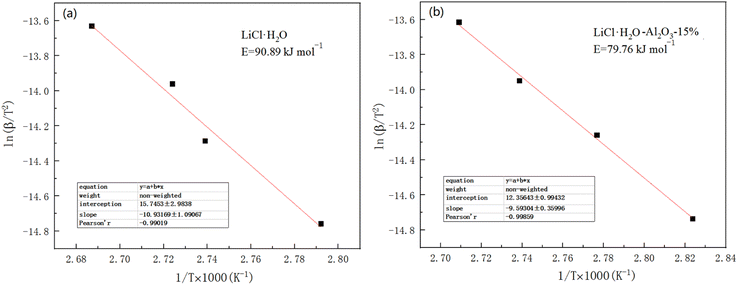 |
| Fig. 8 The activation energy of dehydration reaction of (a) LiCl·H2O, (b) LiCl·H2O-Al2O3-15%. | |
4 Conclusions
In this study, the LiCl·H2O-Al2O3 composites were successfully constructed and characterized. The structural properties of these composites was experimentally investigated by XRD, SEM, BET, in situ DRIFT spectroscopy and the thermal performance were obtained by TG-DSC and a hot disk thermal constant analyzer. The following findings can be addressed:
(1) Results of XRD show that a complex of LiAlOCl2 was formed by LiCl·H2O and Al2O3. Moreover, with the increase of γ-Al2O3 content, the particle size of LiCl·H2O-Al2O3 composites gradually decreased and became uniform through TEM graphs.
(2) According to the in situ DRIFT spectroscopy results, the addition of Al2O3 accelerated the hydration rate of the material, concentrated the utilization range of spectrum, and promoted the desorption of physical adsorbed H2O and low-frequency structural –OH in the materials. Furthermore, LiCl-Al2O3-20% exhibited the highest specific surface area (15.18 m2 g−1), which is 34.5 times higher than that of pure LiCl.
(3) Compared with pure LiCl·H2O, LiCl·H2O-Al2O3 composites exhibited better thermal storage performance, higher HSD of LiCl·H2O monomer (714.7 kJ kg−1) and water uptake (0.26 g g−1). Meanwhile, the desorption temperature of composites decreased compared with that of the pure LiCl and the addition of Al2O3 is useful for decreasing the activation energy of composites (90.89 kJ mol−1 to 79.76 kJ mol−1). However, the thermal conductivity of composite decreased with the increase of nano γ-Al2O3 content. Further research should be undertaken to improve this aspect.
Conflicts of interest
There are no conflicts to declare.
Acknowledgements
The authors gratefully acknowledge financial support from the National Natural Science Foundation of China (no. 52176091 and no. 52006158), and the Open Fund of Science and Technology on Thermal Energy and Power Laboratory (no. TPL2020A02). We would also like to acknowledge Juan Fu from GuangZhou Institute of Energy Conversion for the experimental guidance.
References
- Global Temperature--Latest Annual Average Anomaly (2020) Global Climate Change, https://climate.nasa.gov/vital-signs/global-temperature/.
- C. Haddad, C. Périlhon, A. Danlos, M.-X. François and G. Descombes, Some efficient solutions to recover low and medium waste heat: competitiveness of the thermoacoustic technology, Energy Procedia, 2014, 50, 1056–1069, DOI:10.1016/j.egypro.2014.06.125.
- M. R. Biradar, S. V. Bhosale, P. P. Morajakar and S. V. Bhosale, A review on energy storage devices based on rylene imide dyes: Synthesis, applications and challenges, Fuel, 2022, 310, 122487, DOI:10.1016/j.fuel.2021.122487.
- C. Che and Y. Yin, Improvement of low-grade heat utilization: Sensitivity mechanism of saturated vapor pressure–temperature in dehumidified materials, Appl. Therm. Eng., 2023, 230, 120788, DOI:10.1016/j.applthermaleng.2023.120788.
- M. Papapetrou, G. Kosmadakis, A. Cipollina, U. L. Commare and G. Micale, Industrial waste heat: estimation of the technically available resource in the EU per industrial sector, temperature level and country, Appl. Therm. Eng., 2018, 138, 207–216, DOI:10.1016/j.applthermaleng.2018.04.043.
- M. Yu, X. Liu, Z. Liu and S. Yang, Energy, exergy, economic and environmental (4E) analysis of a novel power/refrigeration cascade system to recover low-grade waste heat at 90–150 °C, J. Cleaner Prod., 2022, 363, 132353, DOI:10.1016/j.jclepro.2022.132353.
- S. Daniarta, M. Nems and P. Kolasinski, A review on thermal energy storage applicable for low- and medium- temperature organic Rankine cycle, Energy, 2023, 27, 127931, DOI:10.1016/j.energy.2023.127931.
- R. K. Sambare, S. Joshi and N. C. Kanojiya, Improving the freshwater production from tubular solar still using sensible heat storage materials, Therm. Sci. Eng. Prog., 2023, 38, 101676, DOI:10.1016/j.tsep.2023.101676.
- S. Yu, D. Han, W. He, M. Zhou, L. Zhu, Y. Gao, G. Cui and T. Peng, Analysis and optimization of transient heat dissipation characteristics of high power resistors with a sensible heat storage method, Appl. Therm. Eng., 2023, 226, 120246, DOI:10.1016/j.applthermaleng.2023.120246.
- Y. B. Tao and Y. L. He, A review of phase change material and performance enhancement method for latent heat storage system, Renewable Sustainable Energy Rev., 2018, 93, 245–259, DOI:10.1016/j.rser.2018.05.028.
- V. V. Upadhyay and S. Singhal, A review of current developments in the use of materials with latent heat phase changes for the storage of thermal energy, Mater. Today, 2023, 4, DOI:10.1016/j.matpr.2023.02.187.
- J. Lin, Q. Zhao, H. Huang, H. Mao, Y. Liu and Y. Xiao, Applications of low-temperature thermochemical energy storage systems for salt hydrates based on material classification: A review, Sol. Energy, 2021, 214, 149–178, DOI:10.1016/j.solener.2020.11.055.
- K. E. N'Tsoukpoe, G. Restuccia, T. Schmidt and X. Py, The size of sorbents in low pressure sorption or thermochemical energy storage processes, Energy, 2014, 77, 983–998, DOI:10.1016/j.energy.2014.10.013.
- W. Hua, H. Yan, X. Zhang, X. Xu, L. Zhang and Y. Shi, Review of salt hydrates-based thermochemical adsorption thermal storage technologies, J. Energy Storage, 2022, 56, 106158, DOI:10.1016/j.est.2022.106158.
- Z. Chen, Y. Zhang, Y. Zhang, Y. Su and S. Riffat, A study on vermiculite-based salt mixture composite materials for low-grade thermochemical adsorption heat storage, Energy, 2023, 30, 127986, DOI:10.1016/j.energy.2023.127986.
- J. T. Chen, B. Q. Xia and C. Y. Zhao, Topology optimization for heat transfer enhancement in thermochemical heat storage, Int. J. Heat Mass Transfer, 2020, 154, 119785, DOI:10.1016/j.ijheatmasstransfer.2020.119785.
- S. Wu, T. X. Li, T. Yan and R. Z. Wang, Advanced thermochemical resorption heat transformer for high-efficiency energy storage and heat transformation, Energy, 2019, 175, 1222–1233, DOI:10.1016/j.energy.2019.03.159.
- H. Böhm and J. Lindorfer, Techno-economic assessment of seasonal heat storage in district heating with thermochemical materials, Energy, 2019, 179, 1246–1264, DOI:10.1016/j.energy.2019.04.177.
- A. U. Rehman, T. Zhao, I. Muhammad, S. Rasheed, R. Shah, A. R. Altaf, F. Zhang and S. Yun, MgCl2-MXene based nanohybrid composite for efficient thermochemical heat storage application, J. Energy Storage, 2023, 59, 106509, DOI:10.1016/j.est.2022.106509.
- T. Yan and H. Zhangr, A critical review of salt hydrates as thermochemical sorption heat storage materials: Thermophysical properties and reaction kinetics, Sol. Energy, 2022, 242, 157–183, DOI:10.1016/j.solener.2022.07.002.
- T. Yan, Z. H. Kuai and S. F. Wu, Multi-mode solid-gas thermochemical resorption heat transformer using NiCl2-SrCl2/NH3, Appl. Therm. Eng., 2020, 167, 114800, DOI:10.1016/j.applthermaleng.2019.114800.
- T. Yan, R. Z. Wang and T. X. Li, Experimental investigation on thermochemical heat storage using manganese chloride/ammonia, Energy, 2018, 143, 562–574, DOI:10.1016/j.energy.2019.07.105.
- J. Fitó, A. Coronas, S. Mauran, N. Mazet, M. Perier-Muzet and D. Stitou, Hybrid system combining mechanical compression and thermochemical storage of ammonia vapor for cold production, Energy Convers. Manage., 2019, 180, 709–723, DOI:10.1016/j.enconman.2018.11.019.
- A. Gordeeva, S. Strelova, L. Gordeeva and Y. Aristov, “LiCl/vermiculite – Methanol” as working pair for adsorption heat storage: Adsorption equilibrium and dynamics, Energy, 2019, 186, 0360–5442, DOI:10.1016/j.energy.2019.07.105.
- R. Xie, J. Sun, Y. Shi and J. Wei, Baffled-type thermochemical reactor for high-efficient hydrogen production by methanol steam reforming, Int. J. Hydrogen Energy, 2023, 48(61), 23425–23439, DOI:10.1016/j.ijhydene.2023.03.166.
- K. S. Babu, E. A. Kumar and S. S. Murthy, Thermochemical energy storage using coupled metal hydride beds of Mg-LaNi5 composites and LaNi5 based hydrides for concentrated solar power plants, Appl. Therm. Eng., 2023, 219, 119521, DOI:10.1016/j.applthermaleng.2022.119521.
- Y. Zhao, C. Y. Zhao, C. N. Markides, H. Wang and W. Li, Medium- and high-temperature latent and thermochemical heat storage using metals and metallic compounds as heat storage media: A technical review, Appl. Energy, 2020, 280, 115950, DOI:10.1016/j.apenergy.2020.115950.
- J. Cot-Gores, A. Castell and L. F. Cabeza, Thermochemical energy storage and conversion: a state of the art review of the experimental research under practical conditions, Renewable Sustainable Energy Rev., 2012, 16, 5207–5224, DOI:10.1016/j.rser.2012.04.007.
- H. A. Ousaleh, S. Sair, S. Mansouri, Y. Abboud, M. Zahouily, A. Faik and A. E. I. Bouari, Enhanced inorganic salts stability using bentonite clay for high-performance and low-cost thermochemical energy storage, J. Energy Storage, 2022, 49, 104140, DOI:10.1016/j.est.2022.104140.
- L. Calabrese, D. Palamara, E. Piperopoulos, E. Mastronardo, C. Milone and E. Proverbio, Deviceful LiCl salt hydrate confinement into a macroporous silicone foam for low-temperature heat storage application, J. Sci.: Adv. Mater. Devices, 2022, 7, 100463, DOI:10.1016/j.jsamd.2022.100463.
- V. Brancato, L. G. Gordeeva, A. L. Sapienza, V. Palomba, S. Vasta, A. D. Grekova, A. Frazzica and Y. I. Aristov, Experimental characterization of the LiCl/vermiculite composite for sorption heat storage applications, Int. J. Refrig., 2019, 105, 92–100, DOI:10.1016/j.ijrefrig.2018.08.006.
- G. Whiting, D. Grondin, S. Bennici and A. Auroux, Heats of water sorption studies on zeolite-MgSO4 composites as potential thermochemical heat storage materials, Sol. Energy Mater. Sol. Cells, 2013, 112, 112–119, DOI:10.1016/j.solmat.2013.01.020.
- A. D. Grekova, L. G. Gordeeva, Z. Lu, R. Wang and Y. I. Aristov, Composite “LiCl/MWCNT” as advanced water sorbent for thermal energy storage: Sorption dynamics, Sol. Energy Mater. Sol. Cells, 2018, 176, 273–279, DOI:10.1016/j.solmat.2017.12.011.
- X. Ke and V. A. Baki, Assessing the suitability of alkali-activated metakaolin geopolymer for thermochemical heat storage, Sol. Energy Mater. Sol. Cells, 2021, 325, 111329, DOI:10.1016/j.micromeso.2021.111329.
- N. Yu, R. Z. Wang, Z. S. Lu and L. W. Wang, Study on consolidated composite sorbents impregnated with LiCl for thermal energy storage, Int. J. Heat Mass Transfer, 2015, 84, 660–670, DOI:10.1016/j.ijheatmasstransfer.2015.01.065.
- X. Zheng and R. Z. Wang, Microstructure and sorption performance of consolidated composites impregnated with LiCl, Int. J. Refrig., 2019, 98, 452–458, DOI:10.1016/j.ijrefrig.2018.11.031.
- J. Aarts, B. V. Ravensteijn, H. Fischer, O. Adan and H. Huinink, Polymeric stabilization of salt hydrates for thermochemical energy storage, Appl. Energy, 2023, 341, 121068, DOI:10.1016/j.apenergy.2023.121068.
- X. Zheng, T. S. Ge, Y. Jiang and R. Z. Wang, Experimental study on silica gel-LiCl composite desiccants for desiccant coated heat exchanger, Int. J. Refrig., 2015, 51, 24–32, DOI:10.1016/j.ijrefrig.2014.11.015.
- L. Z. Zhang, Y. Y. Wang, C. L. Wang and H. Xiang, Synthesis and characterization of a PVA/LiCl blend membrane for air dehumidification, J. Membr. Sci., 2008, 308, 198–206, DOI:10.1016/j.memsci.2007.09.056.
- H. Zhao, Z. Wang, Q. Li, T. Wu, M. Zhang and Q. Shi, Water sorption on composite material “zeolite 13X modified by LiCl and CaCl2”, Microporous Mesoporous Mater., 2020, 299, 110109, DOI:10.1016/j.micromeso.2020.110109.
- Y. N. Zhang, R. Z. Wang and T. X. Li, Thermochemical characterizations of high-stable activated alumina/LiCl composites with multistage sorption process for thermal storage, Energy, 2018, 156, 240–249, DOI:10.1016/j.energy.2018.05.047.
- D. G. Gunjo, S. R. Jena, P. Mahanta and P. S. Robi, Melting enhancement of a latent heat storage with dispersed Cu, CuO and Al2O3 nanoparticles for solar thermal application, Renewable Energy, 2018, 121, 652–665, DOI:10.1016/j.renene.2018.01.013.
- H. Sun, Y. Li, X. Yan, J. Zhao and Z. Wang, Thermochemical energy storage performance of Al2O3/CeO2 co-doped CaO-based material under high carbonation pressure, Appl. Energy, 2020, 263, 114650, DOI:10.1016/j.apenergy.2020.114650.
- M. Bahari, B. Najafi and A. Babapoor, Evaluation of α-AL2O3-PW nanocomposites for thermal energy storage in the agro-products solar dryer, J. Energy Storage, 2020, 28, 101181, DOI:10.1016/j.est.2019.101181.
- X. Lao, X. Xu, H. Cheng, H. Liu and L. Liang, Effect of rare-earth oxides on microstructure and thermal shock resistance of Al2O3-SiCw composite ceramics for solar thermal storage, Ceram. Int., 2019, 45, 2003–2011, DOI:10.1016/j.ceramint.2018.10.098.
- W. Miao, Y. Wang, X. Li, S. Gan, Y. Lv and Z. Liu, Development of spherical α-Al2O3-based composite phase change materials (PCMs) and its utilization in thermal storage building materials, Thermochim. Acta, 2019, 676, 177–185, DOI:10.1016/j.tca.2019.04.010.
- S. Bahou, H. Labrim, M. Lakhal, M. Bhihi, B. Hartiti and H. Ez-Zahraouy, Improving desorption temperature and kinetic properties in MgH2 by vacancy defects: DFT study, Int. J. Hydrogen Energy, 2020, 45(18), 10806–10813, DOI:10.1016/j.ijhydene.2020.02.024.
- H. Wu, P. Trens, B. Fraisse, F. Salles and J. Zajac, Hydration mechanism in Ce-exchanged zeolites and heat release performances upon adsorption of water vapour in support of their potential use in thermochemical storage of energy under mild conditions of adsorbent regeneration and saturation, Microporous Mesoporous Mater., 2020, 296, 109999, DOI:10.1016/j.micromeso.2020.109999.
- K. M. Kim, H. T. Oh, S. J. Lim, K. Ho, Y. Park and C. H. Lee, Adsorption equilibria of water vapor on zeolite 3A, zeolite 13X, and dealuminated Y zeolite, J. Chem. Eng., 2016, 61, 1547–1554, DOI:10.1021/acs.jced.5b00927.
- S. P. Weng, Fourier transform infrared spectrometer, Chemical Industry Press, 2005, https://max.book118.com/html/2019/0724/8043041133002036.shtm Search PubMed.
- G. Hambitzer, J. Heitbaum, C. Dambach, M. Kampa, C. Pszolla and C. Ripp, Rechargeable electrochemical cell, US pat. 20140113182, 2014-04-24, http://www.patentsencyclopedia.com/app/20140113182 Search PubMed.
- D. H. Zhou, Lithium industry, Chemical Industry Press, 1996 Search PubMed.
- W. Y. Xu, C. J. Yao, Y. C. Xu and S. G. Hong, Preparation of dimethyldichlorosilane by catalytic disproportionation of LiAlCl4/γ-Al2O3, J. Zhengzhou Univ., 2017, 38, 92–96, DOI:10.13705/j.issn.1671-6833.2017.06.014.
- L. Zhao, X. Y. Li, C. Hao and C. L. Raston, SO2 adsorption and transformation on calcined NiAl hydrotalcite-like compounds surfaces: An in situ FTIR and DFT study, Appl. Catal., B, 2012, 117–118, 339–345, DOI:10.1016/j.apcatb.2012.01.034.
- T. Szabo, O. Berkesi, P. Forgo, K. Josepovits, Y. Sanakis, D. Petridis and I. Dekany, Evolution of surface functional groups in a series of progressively oxidized graphite oxides, Chem. Mater., 2006, 18, 2740–2749, DOI:10.1021/cm060258+.
- L. Vradmana, M. V. Landaub, D. Kantorovich, Y. Koltypin and A. Gedanken, Evaluation of metal oxide phase assembling mode inside the nanotubular pores of mesostructured silica, Microporous Mesoporous Mater., 2005, 79(1–3), 307–318, DOI:10.1016/j.micromeso.2004.11.023.
- L. G. Gordeeva, A. Freni, T. A. Krieger, G. Restuccia and Y. I. Aristov, Composites “lithium halides in silica gel pores”: Methanol sorption equilibrium, Microporous Mesoporous Mater., 2008, 112(1–3), 254–261, DOI:10.1016/j.micromeso.2007.09.040.
- H. Zhao, M. Lei, T. Liu, T. Huang and M. Zhang, Synthesis of composite material HKUST-1/LiCl with high water uptake for water extraction from atmospheric air, Inorg. Chim. Acta, 2020, 511, 119842, DOI:10.1016/j.ica.2020.119842.
- B. X. Wang, L. P. Zhou and X. F. Peng, Surface and size effects on the specific heat capacity of nanoparticles, Int. J. Thermophys., 2006, 27, 139–151, DOI:10.1007/s10765-006-0022-9.
- H. Zou, F. Evrendilek, J. Liu and M. Buyukada, Combustion behaviors of pileus and stipe parts of Lentinus edodes using thermogravimetric-mass spectrometry and Fourier transform infrared spectroscopy analyses: thermal conversion, kinetic, thermodynamic, gas emission and optimization analyses, Bioresour. Technol., 2019, 288, 121481, DOI:10.1016/j.biortech.2019.121481.
- M. Kubota, S. Matsumoto, H. Matsuda, H. Y. Huang, Z. H. He and X. X. Yang, Chemical heat storage with LiOH/LiOH·H2O reaction for low-temperature heat below 373 K, Adv. Mater. Res., 2014, 953–954, 757–760, DOI:10.4028/www.scientific.net/AMR.953-954.757.
- S. Li, H. Huang, X. Yang, Y. Bai, J. Li, N. Kobayashi and M. Kubota, Hydrophilic substance assisted low temperature LiOH·H2O based composite thermochemical materials for thermal energy storage, Appl. Therm. Eng., 2018, 128, 706–711, DOI:10.1016/j.applthermaleng.2017.09.050.
|
This journal is © The Royal Society of Chemistry 2023 |
Click here to see how this site uses Cookies. View our privacy policy here.