DOI:
10.1039/D3SC00257H
(Edge Article)
Chem. Sci., 2023,
14, 4346-4350
Catalytic utilization of converter gas – an industrial waste for the synthesis of pharmaceuticals†
Received
13th January 2023
, Accepted 12th March 2023
First published on 31st March 2023
Abstract
Converter gas is a large scale waste product that is usually burned to carbon dioxide and contributes to the world emission of greenhouse gases. Herein we demonstrate that instead of burning the converter gas can be used as a reducing agent in organic reactions to produce valuable pharmaceuticals and agrochemicals. In particular, amide-based selected drug molecules have been synthesized by a reaction of aromatic nitro compounds and carboxylic acids in the presence of converter gas. In addition, we showed that this gas can also be conveniently utilized to carryout classical reductive amination reaction.
Introduction
Converter gas is one of the largest waste products of the steel industry.1 Each year millions of tons of converter gas is formed.2 Typically this gas is burned to carbon dioxide which is then released to the atmosphere and makes a significant contribution to the world emission of greenhouse gases (Fig. 1).3,4 While the emission of greenhouse gases from burning fossil fuels can be reduced by using other energy sources (such as electricity from solar, hydro, or nuclear plants), emissions from steel production are currently unavoidable. Therefore, it is highly desirable not to burn converter gas but rather to apply it in the chemical industry for the synthesis of valuable products. Herein, we address this challenge and demonstrate that converter gas can be used as a reducing agent for the production of a variety of organic chemicals including pharmaceuticals.
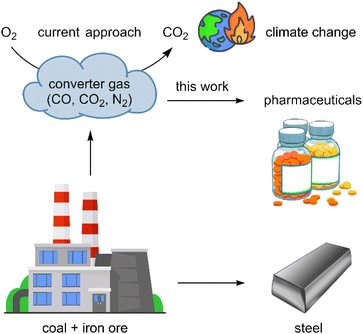 |
| Fig. 1 The formation and possible applications of converter gas for production of pharmaceuticals, polymers, and other chemicals. | |
The composition of converter gas depends on the temperature of the steel-making process, but typically it contains 60–95% of CO, as well as N2 and CO2 as the main components.5 During the traditional burning process, the converter gas acts essentially as a reducing agent for atmospheric oxygen. Therefore, it may be also possible to use it in a similar manner for reduction of organic compounds. Recently we and others have used CO as a reducing agent in various transformations.6–9 In the course of these studies, we found that converter gas can be used for the direct amidation of nitroarenes and carboxylic acids without any additives or coupling agents (Scheme 1). This atom- and step-economic process converts the industrial starting materials into valuable amide derivatives. The amide bond is one of the most important bonding motifs in organic chemistry and provides the basis for the unique physical and biological properties of many high-performance materials, natural products and biology related molecules.10–12 Consequently, amides are found in numerous pharmaceutical drugs13–15 and agrochemicals. To show the practical potential of the amidation reaction using converter gas, we applied it for the synthesis of various pharmaceuticals.
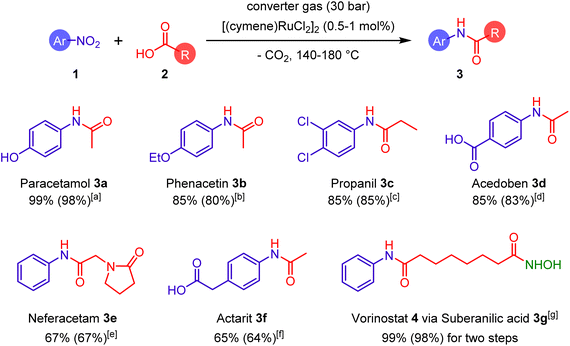 |
| Scheme 1 Synthesis of selected pharmaceuticals by catalytic amidation of nitroarenes and carboxylic acids with the aid of converter gas. Reaction conditions (detailed reaction conditions are provided in the ESI†): a 1 mol% of [(cymene)RuCl2]2, 1 equiv. of 2, 10 equiv. of 1, 30 bar of converter gas, 140 °C, 20 h; b 0.5 mol% of [(cymene)RuCl2]2, 1 equiv. of 2, 10 equiv. of 1, 50 bar of converter gas, 180 °C, 20 h; c 0.5 mol% of [(cymene)RuCl2]2, 1 equiv. of 2, 10 equiv. of 1, 30 bar of converter gas, 160 °C, 20 h; ] 0.5 mol% of [(cymene)RuCl2]2, 1 equiv. of 2, 10 equiv. of 1, 30 bar of converter gas, 170 °C, 20 h; e 0.5 mol% of [(cymene)RuCl2]2, 1 equiv. of 2, 5 equiv. of 1, 30 bar of converter gas, 170 °C, 20 h; f 0.75 mol% of [(cymene)RuCl2]2, 1 equiv. of 2, 10 equiv. of 1, 30 bar of converter gas, 140 °C, 20 h; g for preparation of 3g: 0.75 mol% of [(cymene)RuCl2]2, 1 equiv. of 2, 5 equiv. of 1, 30 bar of converter gas, 170 °C, 20 h. NHOH group highlighted by green color was introduced in a second step. | |
Results and discussion
First, we studied the reaction of 4-nitrophenol with acetic acid in the presence of converter gas to produce paracetamol (3a). In accordance with previous reports on related processes,7,16–19 we found that ruthenium complexes are efficient catalysts for this transformation. Under optimal conditions, the commercially available ruthenium catalyst [(cymene)RuCl2]2 (at 1 mol% loading) allowed us to obtain paracetamol (3a) in 99% yield (Table 1, entry 1). Noteworthy, other ruthenium complexes can be used as catalysts but reaction did not proceed at all in the absence of the ruthenium source or in the absence of the converter gas (Table 1, entry 7; full details of conditions optimization are provided in the ESI†). Both Ru(acac)3 and RuCl3 can be used as catalysts indicating that the nature of ligands is not crucial for the process (Table 1, entries 2 and 3). Water can be used as a solvent for the reaction, which makes the reaction attractable for the industrial chemistry (Table 1, entry 4). The optimal conditions are 140 °C and 30 bar; reactions at lower temperature or pressure gave lower yields (Table 1, entries 5 and 6).
Table 1 Selected optimization results
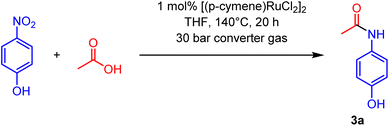
|
Entry |
Deviation from the optimal conditions |
Yield of 3a |
1 |
None |
99% |
2 |
Ru(acac)3 instead of [(cymene)RuCl2]2 |
84% |
3 |
RuCl3 instead of [(cymene)RuCl2]2 |
31% |
4 |
Water instead of THF |
85% |
5 |
20 bar of converter gas |
47% |
6 |
130 °C instead of 140 °C |
56% |
7 |
No catalyst or CO2 instead of converter gas |
0% |
8 |
CO instead of converter gas |
86% |
In a similar manner, other important pharmaceuticals such as phenacetin (3b), propanil (3c), acedoben (3d), nefiracetam (3e), and actarit (3f) were produced in 65–85% yields (Scheme 1). It is important to note that this amidation reaction is compatible with various functional groups including hydroxyl (in paracetamol), chloride (in propanil), amide (in nefiracetam), and carboxylic acid (in actarit and acedoben). In addition, vorinostat (4), one of the main drugs against T cell lymphoma,20 was synthesized in two steps from suberic acid, nitrobenzene, and hydroxylamine in almost quantitative yield. The function of converter gas in these syntheses is essential to capture and remove the excessive oxygen atoms from the nitro- and carboxylic groups of the reagents. Since the industrial converter gas may contain sulfur-based impurities,21 we tested the catalytic amidation in the presence of thiophene. Fortunately, this did not lead to poisoning of the catalyst (see ESI, Table S7†).
The exact mechanism of the catalytic amidation is not clear, but we can propose a possible sequence based on experimental observations and previous literature reports7,22–24 (Scheme 2). First the nitro compounds are reduced by CO in the presence of ruthenium carbonyl species25 Rux(CO)y to give isocyanates or amines.26 Then isocyanates or amines can react with carboxylic acid to give the desired amide similar to the known organic transformation. The detailed discussion of the possible mechanism is provided in the ESI.†
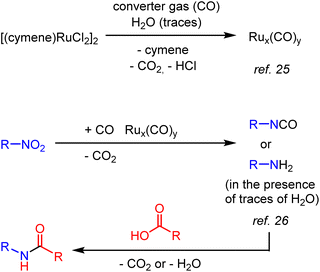 |
| Scheme 2 Possible mechanism of the catalytic amidation reaction. | |
In order to prove that converter gas can be used in a general manner for other reductive transformations, we explored another important reaction involving the formation of C–N bonds, namely, the reductive amination (Scheme 3).27–32
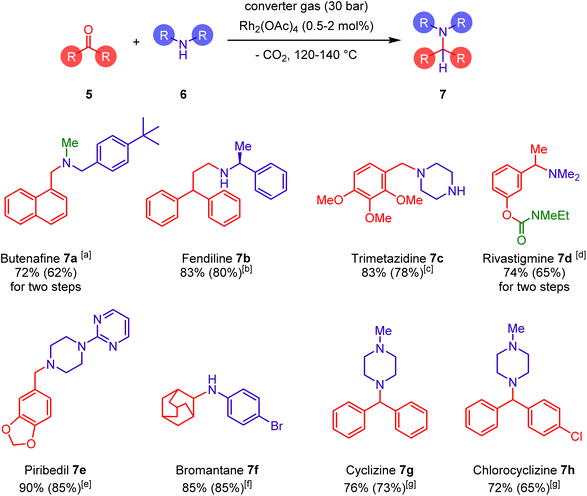 |
| Scheme 3 Catalytic reductive aminations using converter gas: synthesis of selected pharmaceuticals. Reaction conditions (detailed reaction conditions are provided in the ESI†): a 0.5 mol% of Rh2(OAc)4, 1.5 equiv. 6, 1 equiv. of 5, 30 bar of converter gas, 120 °C, 22 h. After 22 h 2.20 equiv. of formaline were added for an additional 22 h to achieve methylation (highlighted by green color); b 0.5 mol% of Rh2(OAc)4, 1.1 equiv. of % 6, 1 equiv. of 5, 30 bar of converter gas, 140 °C, 22 h; c 1 mol% of [(η4-cyclooctadiene)Rh(η6-2,3,6,7-tetramethoxy-9,10-dimethylanthracene)]BF4, 10 equiv. of 6, 1 equiv. of 5, 30 bar of converter gas, 120 °C, 22 h; d reductive amination step: 0.5 mol% of Rh2(OAc)4, 5 equiv. of 6, 1 equiv. of 5, 30 bar of converter gas, 120 °C, 48 h. C(O)NMeEt group highlighted by green color was introduced in the next step; e 0.5 mol% of Rh2(OAc)4, 1 equiv. of 6, 1 equiv. of 5, 30 bar of converter gas, 120 °C, 22 h; f 0.5 mol% of Rh2(OAc)4, 1 equiv. of 6, 2 equiv. of 5, 42 bar of converter gas, 120 °C, 22 h; g 2 mol% of Rh2(OAc)4, 5 equiv. of 6, 1 equiv. of 5, 45 bar of converter gas, 130 °C, 48 h. | |
Indeed, it was found that this reaction between readily available carbonyl compounds and amines proceeded in the presence of converter gas and was catalysed by a simple rhodium acetate without any additional expensive ligands. This way we synthesized antifungal agent butenafine (7a) directly from formaline, naphthaldehyde, and 4-tert-butylbenzylamine. Further expansion of this method provided other drugs such as fendiline (7b), trimetazidine (7c), rivastigmine (7d), piribedil (7e), bromantane (7f), cyclizine (7g), and chlorocyclizine (7h) (detailed reaction conditions are provided in the ESI†). Once again, the reaction displayed excellent selectivity and was not inhibited by various functional groups.
As in the previous case, the main role of converter gas is to remove the oxygen atoms from the carbonyl molecules. We assume that rhodium species first coordinate with CO, which is then attacked by the OH group of the hemiaminal intermediate to give the Rh–COOH group. Its further decarboxylation gives rhodium hydride species, which immediately reduce the iminium cation similar to previous reports33,34 (Scheme 4).
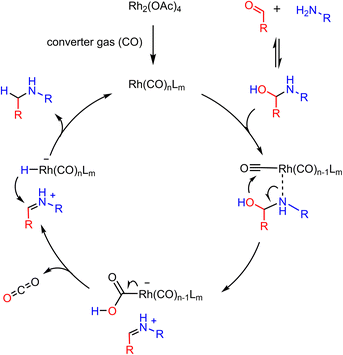 |
| Scheme 4 Possible mechanism for reductive amination by CO in the presence of a rhodium catalyst. | |
Experimental
Preparation of converter gas
The model converter gas was prepared in a 40 liter gas cylinder at room temperature. The gas cylinder was filled with 29 bar of carbon monoxide, followed by 10 bar of carbon dioxide and 11 bar of nitrogen.35
General procedure for the reductive amidation
The ruthenium catalyst [(p-cymene)RuCl2]2 (0.5–1 mol%), nitroarene, acetic acid, THF, and a magnetic stirring bar were placed into an autoclave. The autoclave was sealed, flushed three times with 10 bar of converter gas, and then charged with 30 bar of converter gas. The autoclave was placed into an oil bath preheated to the required temperature (140–180 °C). After the indicated time (typically 20 h), the autoclave was cooled to room temperature and depressurized. The reaction mixture was transferred into a flask and the autoclave was additionally washed with dichloromethane (2 × 1 mL). The solvents were removed using a rotary evaporator, and the residue was analyzed by NMR.
General procedure for the reductive amination
Rhodium(II) acetate (0.5–2 mol%), amine, and the carbonyl compound were placed into an autoclave. The autoclave was sealed, flushed three times with 10 bar of converter gas, and then charged with 45 bar of converter gas. The reactor was placed into an oil bath preheated to the required temperature (120–140 °C). After the indicated time (20–48 h), the autoclave was cooled to room temperature and depressurized. The reaction mixture was transferred into a flask and the autoclave was additionally washed with dichloromethane (2 × 1 mL). The solvents were removed using a rotary evaporator, and the residue was analyzed by NMR.
Conclusions
To conclude, we have demonstrated that, instead of burning converter gas, it can be conveniently used to synthesize valuable organic life science products. The generality of this approach is showcased in the preparation of several current pharmaceuticals via the reductive amidation protocol as well as via more classical reductive amination. We believe that converter gas can be used for many other atom- and step-economical reduction transformations in the near future. In particular, converter gas from steel plants might replace natural gas sources in well-known large-scale industrial processes involving CO such as synthesis of acetic acid,36–38 hydroformylation,39–41 urea synthesis,8,42–44etc. Hopefully, this discovery will attract other researchers to develop chemical processes involving converter gas.
Data availability
All data associated with this report may be found in the ESI.†
Author contributions
S. A. R., O. I. A., E. A. K. carried out all experiments, D. S. P. carried out quantum chemical modelling. D. C. generated an idea of the paper and coordinated all project. R. V. J. and M. B. involved in the development of this project. O. I. A., D. S. P., R. V. J., M. B., D. C. wrote the manuscript.
Conflicts of interest
There are no conflicts to declare.
Acknowledgements
This work was supported by the Russian Science Foundation (Grant No. 22-73-10020). The NMR data were collected using the equipment of the Center for molecular composition studies of INEOS RAS with financial support from the Ministry of Science and Higher Education of the Russian Federation (Contract No. 075-03-2023-642).
Notes and references
- K. He and L. Wang, Renewable Sustainable Energy Rev., 2017, 70, 1022–1039 CrossRef.
- T. A. Napp, A. Gambhir, T. P. Hills, N. Florin and P. S. Fennell, Renewable Sustainable Energy Rev., 2014, 30, 616–640 CrossRef CAS.
- A. Hasanbeigi, M. Arens and L. Price, Renewable Sustainable Energy Rev., 2014, 33, 645–658 CrossRef CAS.
-
J. R. Vehec, AISI/DOE Technology Roadmap Research Program for the Steel Industry, Washington, DC, 2010 Search PubMed.
- S. K. Ray, G. Chattopadhyay and A. K. Ray, J. Air Waste Manag. Assoc., 1997, 47, 716–721 CrossRef CAS.
- A. Ambrosi and S. E. Denmark, Angew. Chem., Int. Ed., 2016, 55, 12164–12189 CrossRef CAS PubMed.
- F. Ferretti, D. R. Ramadan and F. Ragaini, ChemCatChem, 2019, 11, 4450–4488 CrossRef CAS.
- A. A. Tsygankov, M. Makarova and D. Chusov, Mendeleev Commun., 2018, 28, 113–122 CrossRef CAS.
- E. Podyacheva, O. I. Afanasyev, A. A. Tsygankov, M. Makarova and D. Chusov, Synthesis, 2019, 51, 2667–2677 CrossRef CAS.
- A. Harrington and Y. Tal-Gan, Future Med. Chem., 2019, 11, 2759–2763 CrossRef CAS PubMed.
-
The Amide Linkage: Structural Significance in Chemistry, Biochemistry, and Materials Science, A. Greenberg, C. M. Breneman and J. F. Liebman, ed. Wiley-Interscience, 2000 Search PubMed.
- S. H. Yun, P. G. Ingole, W. K. Choi, J. H. Kim and H. K. Lee, J. Mater. Chem. A, 2015, 3, 7888–7899 RSC.
- V. R. Pattabiraman and J. W. Bode, Nature, 2011, 480, 471–479 CrossRef CAS PubMed.
- R. M. de Figueiredo, J.-S. Suppo and J.-M. Campagne, Chem. Rev., 2016, 116, 12029–12122 CrossRef CAS PubMed.
- S. Kumari, A. V Carmona, A. K. Tiwari and P. C. Trippier, J. Med. Chem., 2020, 63, 12290–12358 CrossRef CAS PubMed.
- S. E. Denmark, M. Y. S. Ibrahim and A. Ambrosi, ACS Catal., 2017, 7, 613–630 CrossRef CAS.
- I. Choi, S. Chun and Y. K. Chung, J. Org. Chem., 2017, 82, 12771–12777 CrossRef CAS PubMed.
- A. A. Tsygankov, M. Makarova, O. I. Afanasyev, A. S. Kashin, A. V. Naumkin, D. A. Loginov and D. Chusov, ChemCatChem, 2020, 12, 112–117 CrossRef CAS.
- J. W. Park and Y. K. Chung, ACS Catal., 2015, 5, 4846–4850 CrossRef CAS.
- P. A. Marks and R. Breslow, Nat. Biotechnol., 2007, 25, 84–90 CrossRef CAS PubMed.
- O. Hegen, J. I. Salazar Gómez, C. Grünwald, A. Rettke, M. Sojka, C. Klucken, J. Pickenbrock, J. Filipp, R. Schlögl and H. Ruland, Chem. Ing. Tech., 2022, 94, 1405–1412 CrossRef CAS.
- S. J. Skoog, J. P. Campbell and W. L. Gladfelter, Organometallics, 1994, 13, 4137–4139 CrossRef CAS.
- J. D. Gargulak, A. J. Berry, M. D. Noirot and W. L. Gladfelter, J. Am. Chem. Soc., 1992, 114, 8933–8945 CrossRef CAS.
- J. D. Gargulak and W. L. Gladfelter, J. Am. Chem. Soc., 1994, 116, 3792–3800 CrossRef CAS.
- A. F. Hill, Angew. Chem., Int. Ed., 2000, 39, 130–133 CrossRef CAS PubMed.
- A. M. Tafesh and J. Weiguny, Chem. Rev., 1996, 96, 2035–2052 CrossRef CAS PubMed.
- T. Irrgang and R. Kempe, Chem. Rev., 2020, 120, 9583–9674 CrossRef CAS PubMed.
- K. Murugesan, T. Senthamarai, V. G. Chandrashekhar, K. Natte, P. C. J. Kamer, M. Beller and R. V Jagadeesh, Chem. Soc. Rev., 2020, 49, 6273–6328 RSC.
- O. I. Afanasyev, E. A. Kuchuk, K. M. Muratov, G. L. Denisov and D. Chusov, Eur. J. Org. Chem., 2021, 2021, 543–586 CrossRef CAS.
- N. U. D. Reshi, V. B. Saptal, M. Beller and J. K. Bera, ACS Catal., 2021, 11, 13809–13837 CrossRef CAS.
- J. Gallardo-Donaire, M. Hermsen, J. Wysocki, M. Ernst, F. Rominger, O. Trapp, A. S. K. Hashmi, A. Schäfer, P. Comba and T. Schaub, J. Am. Chem. Soc., 2018, 140, 355–361 CrossRef CAS PubMed.
- A. C. Brewer, J. C. Ruble, H. G. Vandeveer, S. A. Frank and C. R. Nevill, Org. Process Res. Dev., 2021, 25, 576–582 CrossRef CAS.
- D. Chusov and B. List, Angew. Chem., Int. Ed., 2014, 53, 5199–5201 CrossRef CAS PubMed.
- E. Podyacheva, O. I. Afanasyev, V. S. Ostrovskii and D. Chusov, ACS Catal., 2022, 12, 5145–5154 CrossRef CAS.
-
P. Grammelis, N. Margaritis and E. Karampinis, Solid fuel types for energy generation: coal and fossil carbon-derivative solid fuels, ed. J. Oakey, Woodhead Publishing, Boston, 2016, pp. 29–58 Search PubMed.
- P. M. Maitlis, A. Haynes, G. J. Sunley and M. J. Howard, J. Chem. Soc., Dalton Trans., 1996, 2187–2196 RSC.
- J. Qi, J. Finzel, H. Robatjazi, M. Xu, A. S. Hoffman, S. R. Bare, X. Pan and P. Christopher, J. Am. Chem. Soc., 2020, 142, 14178–14189 CrossRef CAS PubMed.
- P. Kalck, C. Le Berre and P. Serp, Coord. Chem. Rev., 2020, 402, 213078 CrossRef CAS.
- R. Franke, D. Selent and A. Börner, Chem. Rev., 2012, 112, 5675–5732 CrossRef CAS PubMed.
-
M. Wang and A. Lu, Hydroformylation: Alternatives to Rh and Syn-gas, Elsevier, 2021 Search PubMed.
- M. Sigrist, Y. Zhang, C. Antheaume and P. Dydio, Angew. Chem., Int. Ed., 2022, e202116406 CAS.
- B. Gabriele, G. Salerno, R. Mancuso and M. Costa, J. Org. Chem., 2004, 69, 4741–4750 CrossRef CAS PubMed.
- Q. Wu, J. Chen, Z. Liu and Y. Xu, ACS Appl. Mater. Interfaces, 2020, 12, 48700–48711 CrossRef CAS PubMed.
- D. Madej, A. Konopko, P. Piotrowski and A. Krogul-Sobczak, Catalysts, 2020, 10, 877 CrossRef CAS.
|
This journal is © The Royal Society of Chemistry 2023 |
Click here to see how this site uses Cookies. View our privacy policy here.