Preparation of a high-performance chitosan-based triboelectric nanogenerator by regulating the surface microstructure and dielectric constant†
Received
7th October 2022
, Accepted 29th November 2022
First published on 1st December 2022
Abstract
The rapid development of electronic technology has put forward increased requirements to find more suitable energy sources. Triboelectric nanogenerators (TENGs) have achieved widespread success in converting ambient mechanical energy into electric power. However, it remains challenging to improve the output performance of sustainable material-based TENGs for extensive applications. Herein, a method of combining micro surface construction and dielectric constant control was developed to enhance the output performance of chitosan (CS)-based TENGs. The introduction of conductive filler Ag nanowires (AgNWs) significantly enhanced the dielectric constant of the CS composite film. Duplication of the microstructure using sandpaper increased the effective contact surface. With optimized AgNW content and surface roughness, an open-circuit voltage of 47.9 V, short-circuit current of 4.1 μA, and transfer charge of 17.5 nC were obtained, corresponding to a peak power density of 137.6 mW m−2. The generated output power was capable of remaining stable over 10
000 cycles and charging capacitors to drive light-emitting diodes (LEDs). The composite films had good flexibility and could be easily twisted, bent and folded, enabling the device to attach to multiple parts of the human body (elbows, palms, feet) and harvest the mechanical energy of human motion. This work indicates the potential scope of CS in the practical application of TENGs and demonstrates a promising method for exploring environmentally friendly energy harvesters with high performance.
1. Introduction
Intelligent electronic devices such as smartphones and sports bracelets are rapidly evolving as powerful components of modern life. They entail low power consumption, mobility and sustainability, which imposes new requirements for more suitable energy sources.1 Considering the problem of environmental pollution and the fossil energy crisis, alternative renewable energy sources must be urgently developed. Mechanisms for producing renewable energy include solar cells,2 thermoelectricity,3,4 photovoltaics,5 piezoelectricity,5–9 and triboelectricity.10,11 Among them, triboelectric nanogenerators (TENGs)12 propose a good solution for low-power-consumption devices owing to their high power density, low cost and simple manufacturing process.13–18 Based on the coupling of triboelectrification and electrostatic induction, TENGs have been proven to derive energy from the surrounding environment and biological systems, such as from water flow,19–21 wind22–24 and human activities.25–27 Most reported TENGs are built using nondegradable and nonrenewable polymers, which significantly compromises the overall sustainability of TENGs and limits their application. More sustainable materials need to be designed to fully realize the potential of TENGs as sustainable energy harvesters.
Chitosan (CS) is made from the deacetylation of chitin, which is widely found in nature.28 Owing to its excellent properties, CS has been widely used in water treatment,29,30 drug delivery,31,32 cosmetics33 and tissue engineering.34 More recently, CS has also been selected by some researchers to manufacture TENGs. Wang et al.35 mixed CS with lignin, starch, and glycerol to engineer the properties of CS nanocomposites for optimized triboelectric power generation. Liu et al.36 developed a chitosan/zinc oxide–based TENG to detect acetone concentration and resist humidity changes in the environment. Besides, Kim et al.37 developed chitosan-diatom TENG for biofriendly and wearable devices. Meanwhile, chitosan-based functional textile for humidity, sweat, and gait phase detection has also been developed.38 Chitosan-based TENGs also presented good performance in monitoring the health status of patients with diabetes and Parkinson's disease.39,40 However, these CS-based TENGs showed low output performance compared with other TENGs made from synthetic materials, which could hinder their application in some specific fields. Therefore, how to prepare CS-based triboelectric nanogenerators with high performance in a simple and effective method is still an urgent problem to be solved.
So far, some strategies, including improving the surface charge density, increasing contact area and dielectric constant of materials, have been proven to be effective for enhancing the output performance.41 In order to obtain higher surface charge density, researchers usually chose two kinds of materials with relatively different electronegative properties.42,43 In addition, the output performance of TENGs could be improved by constructing microstructures44 or growing nanowires on the triboelectric materials45 to increase the contact surface area. It is also an effective method to increase the power density through chemical modification or the introduction of functional particles to obtain more effective electrostatic induction.46–48 However, in these reported works, special equipment or complex processes are often required. Therefore, it is necessary to find a simple and effective method to produce TENGs with excellent performance.
In this work, we proposed a simple and effective template casting strategy to adjust the surface microstructure and dielectric constant of CS films to prepare environmentally friendly TENG with high performance. CS/Ag nanowires (AgNWs) composite films with surface microstructure were prepared by a simple casting process, in which nanocapacitors were formed between adjacent AgNWs to improve the dielectric constant of CS matrix. In addition, a microstructure was built by casting solution on sandpaper. As a result, the output performance of CS based TENG can be enhanced by the synergistic effect. Furthermore, the effects of AgNWs contents and sandpaper mesh number on the output performance of CS/AgNWs composite films were studied systematically. The results showed that the CS/AgNWs composite films obtained the highest output performance when the weight ratio of AgNWs was 0.20% and the mesh number of sandpaper was 5000. The maximum short-circuit current, open-circuit voltage, and transfer charge quantity were 4.1 μA, 47.9 V, and 17.5 nC, respectively. Meanwhile, a maximum power density of 137.6 mW m−2 was obtained in series with an external resistor of 10 MΩ. In addition, the CS/AgNWs based TENGs showed good flexibility and stability in 10
000 cycles, so it could be integrated with human skin or clothing easily. When attaching to the elbow, hands, and feet, respectively, the device can realize the collection and transport of human transport function of power of the state of the sensor. This study provides a simple, low-cost strategy to control the surface microstructure of composite films and improve the dielectric constant, showing great potential in wearable electronic device applications.
2. Experimental section
2.1 Preparation of CS/AgNWs composite film
The CS/AgNWs composite films were prepared by a simple film casting process. 0.5 g CS powder (deacetylation ≥95%, viscosity 100–200 mPa s, Macklin) was added to 40 mL acetic acid solution (concentration ≥99.5%, Bodi Chemical Co., LTD) with 2% volume fraction, stirred for 3 h until CS was completely dissolved. Different amounts of AgNWs (diameter: 100 nm, concentration: 20 mg mL−1, XFNANO) aqueous dispersion were added to the CS solution (the weight ratio was 0.06%, 0.10%, 0.20%, 0.30%, 0.40%). The solution was ultrasonically treated for 30 min and then stirred for 1 h to improve the dispersion of AgNWs. The mixed solution was poured into a Petri dish, and CS/AgNWs composite films were achieved after the solvent was completely evaporated. The samples with different contents of AgNWs were named CS, CS/AgNWs-0.06, CS/AgNWs-0.10, CS/AgNWs-0.20, CS/AgNWs-0.30, and CS/AgNWs-0.40, respectively.
2.2 Preparation of CS/AgNWs composite film with surface microstructure
As shown in Fig. 1a, the mixed solution of AgNWs with a weight ratio of 0.20% was obtained according to the same procedure as that for the above smooth CS/AgNWs composite film, and then the mixed solution was poured into a Petri dish with sandpaper as the substrate with different mesh numbers (220, 800, 2000, 5000) and placed in an oven at 40 °C for 12 h. Finally, the CS/AgNWs composite films were carefully removed from the sandpaper. The samples obtained by casting on different mesh sandpapers were named CS/AgNWs-0.20-220#, CS/AgNWs-0.20-800#, CS/AgNWs-0.20-2000#, and CS/AgNWs-0.20-5000#, respectively.
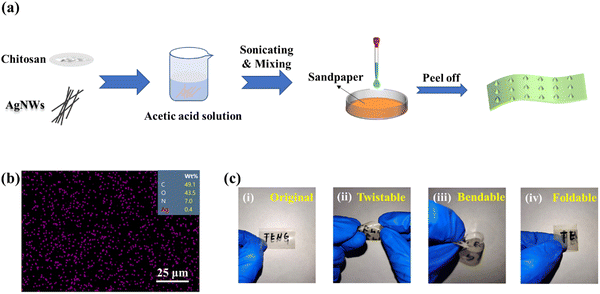 |
| Fig. 1 (a) CS/AgNWs composite film preparation process. (b) EDS image of the CS/AgNWs-0.20 film. (c) Digital photos of different deformations to show the flexibility of CS/AgNWs composite film. | |
2.3 Preparation of CS-based TENG
CS-based TENG was composed of CS/AgNWs composite film and polyvinylidene fluoride (PVDF) film to design the vertical contact-separation TENG. The PVDF film was obtained by hot pressing PVDF powder (FR903). The CS/AgNWs composite film and PVDF film were cut into 2 cm × 2 cm, and a layer of copper tape was pasted underneath as an electrode.
2.4 Characterization and measurements
The crystalline structures of CS and CS/AgNWs composite films were characterized by X-ray diffractometry (XRD) (DX-1000X) using a Cu Kα radiation source (λ = 0.154056 nm, 40 kV, 40 mA) in the reflection mode. The scanning range was from 2° to 80° at a scanning speed of 10 °C min−1. The surface morphology and composition of the films were characterized by field emission scanning electron microscopy (SEM) and energy dispersive spectroscopy (EDS) (FEI, Inspec F) operating at 20.0 kV. The surface images and the roughness of surface average (RSa) of the CS composite films were measured by using a confocal laser scanning microscope (CLSM) (LSM700). The dielectric constant was measured using a broadband impedance spectrometer at a temperature of 25 °C and a frequency of 1 Hz to 103 Hz. The tensile properties of 25 mm × 4 mm splines were measured by a universal tensile testing machine at the rate of 5 mm min−1 below room temperature. Keithley 6514 was used to measure the output performance of CS-based TENG, including open-circuit voltage, short-circuit current, and transfer charge.
3. Results and discussions
Fig. 1a shows the preparation process of CS/AgNWs composite films with surface microstructure by simple template casting method. The film thickness and size can be controlled by applying more solution in the container, while there was no limitation on the size of films, demonstrating the excellent scalability of this preparation technique. As shown in Fig. 1b, EDS was used for observing the distribution of AgNWs in CS matrix, indicating AgNWs has good dispersion in CS matrix. Besides, the CS/AgNWs composite films owned good flexibility, and they can undergo deformation, twisting, bending, and folding (Fig. 1c). The stress–strain curve of the CS/AgNWs composite films in Fig. S1 (ESI†) proved that the introduction of AgNWs had little effect on the tensile properties of chitosan itself. For the composite film with 0.20% AgNWs content, its tensile strength was 38.1 MPa, and elongation at break was 47.9%.
The working mechanism of TENG is shown in Fig. 2 and the system is the vertical contact separation mode of dielectric–dielectric materials. PVDF was used as a negative layer during all the tests to evaluate the output performance of CS/AgNWs based TENG. In the initial state, there was no potential difference between the negative film and the positive film. When they are in contact with each other, the charges on the surface of the CS/AgNWs films would be transferred to the surface of PVDF films because of the different electronegativity between the two materials, which resulted in equal and opposite charges for CS/AgNWs composite film and PVDF film, respectively (Fig. 2a). As shown in Fig. 2b, the electrostatic induction would happen once the two triboelectric materials were separated, and the charges were induced on the two electrodes. As a result, a potential difference was formed, resulting in a flow of electrons in the external circuit until an equilibrium state was reached (Fig. 2c). Then, the induced potential difference generated by triboelectric charges would disappear when the two triboelectric materials contacted again, and the electrons moved in an inverse way for a new electrical equilibrium (Fig. 2d). The periodic contact and separation between the two triboelectric materials drove the induced electrons to flow back and forth between the two electrodes, resulting in an alternating current output in the external circuit.
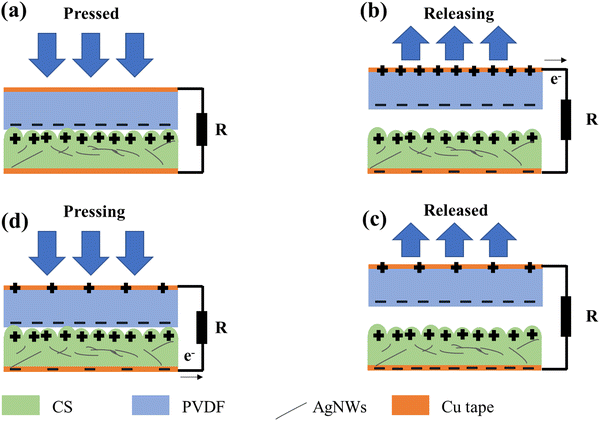 |
| Fig. 2 Schematic of the CS/PVDF triboelectric energy generation process. | |
In order to study the effect of AgNWs content on improving the output performance of TENG, CS/AgNWs composite films with different AgNWs contents were prepared. The SEM in Fig. 3a showed the surface morphology of CS/AgNWs-0.20 composite film, and it could be seen that the surface of the composite films was relatively smooth. Moreover, single AgNWs were obviously distributed on the surface of the composite film. XRD was used to further analyze the crystal structure of the composite films (Fig. S2, ESI†); the peaks of pure chitosan appeared at 11.3°, 18.1°, and 22.9°, respectively. This was mainly due to the crystallization of chitosan, hydration crystallization, and anhydrous crystallization. Compared with the pure CS film, the new peaks of 38.1°, 44.2°, 64.2°, and 77.2° appeared in the composite film, which corresponded to the (1 1 1), (2 0 0), (2 2 0), and (3 1 1) crystal planes of silver, respectively. When the CS membrane was bound to AgNWs, the peaks of both CS and AgNWs were retained, indicating that the structures of CS and silver were not altered during the preparation.49Fig. 3b shows the dielectric enhancement mechanism of the composite film. According to the percolation theory, AgNWs are conductive phases, while CS is the low-loss electrical potential barrier. The AgNWs were separated by thin potential barriers in the CS region, forming nano capacitors between adjacent AgNWs wrapped by the CS matrix.50,51 Consequently, the dielectric constant would be improved by introducing AgNWs filler. Furthermore, the dielectric constant of composite films with different AgNWs contents was characterized (Fig. 3c). The dielectric constant of composite films showed an increasing trend with the increase of AgNWs content, and this phenomenon was attributed to the formation of nanocapacitors between conductive AgNWs.
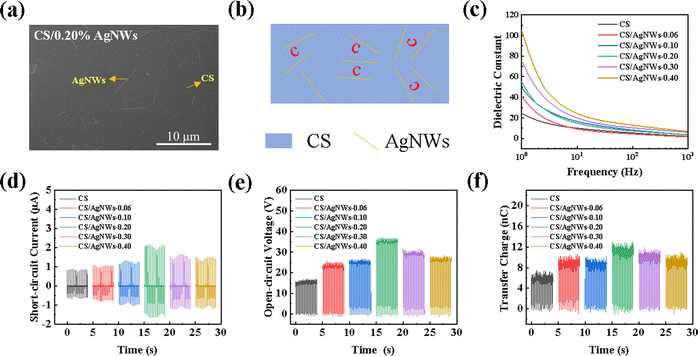 |
| Fig. 3 (a) SEM image of the CS/AgNWs-0.20 film. (b) Schematic diagram of the dielectric constant enhancement mechanism of the CS/AgNWs composite films. (c) Dielectric constant values and resistance of CS composite films with different contents of AgNWs. (d) Short-circuit current, (e) open-circuit voltage and (f) transfer charge quantity of CS composite films with different contents of AgNWs. | |
Fig. 3(d)–(f) display the electrical output generated by CS composite film based TENG with different contents of AgNWs at an applied frequency of 3 Hz. For pure CS based TENG, the short-circuit current, open-circuit voltage, and transfer charge quantity were 0.9 μA, 17.1 V, 7.2 nC, respectively. Obviously, the output performance was enhanced when introducing AgNWs, and optimal performance can be achieved when the content of AgNWs is 0.20%. The short-circuit current, open-circuit voltage, and transfer charge quantity were 2.3 μA, 36.4 V, and 12.3 nC, respectively.
The improvement of the electrical output performance of the CS/AgNWs-0.20 sample compared to the pure CS sample was mainly attributed to the improvement of its dielectric constant. Numerous studies have shown that the dielectric constant of triboelectric materials has a crucial influence on the output performance of TENG, and the short-circuit current, open-circuit voltage, and transfer charge quantity were proportional to the surface charge density.52,53 Additionally, the maximum transferred charge density is related to the dielectric constant of fraction material, and the relationship between the maximum charge density and the dielectric constant of the triboelectric materials could be expressed as:
| 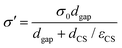 | (1) |
where
εcs,
dcs,
dgap, and
σ0 corresponded to the dielectric constant of CS composite films, the thickness of composite films, the distance between two layers of friction, and the surface charge density of triboelectric material at equilibrium, respectively. Therefore, the increase in dielectric constant was beneficial to the saturated surface charge density.
The output performance of CS/AgNWs composite film slightly decreased when further increasing the AgNWs content. It could be attributed to more AgNWs exposed on the surface, hindering the effective contact between CS and PVDF53 (Fig. S3, ESI†). In addition, the increase in AgNWs content led to the improvement of the conductive property of the composite film, which would make the charge generated in the process of friction contact more easily dissipated (Fig. S4, ESI†). These two factors restricted the output current from rising further with the increase in AgNWs content.
The surface morphology of the contact surface is an important parameter to determine the output performance.54 Effective contact surface is beneficial to enhancing the charge density. In order to further improve the output performance of CS-based TENG, the surface structure of CS/AgNWs-0.20 film was further regulated. The composite films with microstructure were prepared by casting CS/AgNWs-0.20 solution on sandpaper with different mesh numbers (220#, 800#, 2000#, 5000#). As mentioned above, the CS/AgNWs-0.20 film formed a relatively flat structure. While the surface of films possessed by sandpaper became rough, an embossed structure was formed, and hierarchical surface morphology was achieved, as shown in Fig. 4. The CS/AgNWs-0.20 film could re-engrave the morphology of sandpaper successfully and the microstructures could be controlled by mesh numbers of sandpaper. While the mesh number of sandpaper increased from 220 to 5000, the microstructures seemed much denser (Fig. S5, ESI†). CLSM images were also used to show that layered embossed structures can be formed using sandpaper as a template casting process. The surface of the sample without sandpaper treatment was smooth and flat. Since the protrusions were molded from the holes of the sandpaper, and the grooves and undercuts were molded from the bulging grains, microstructures were formed on the surface of the samples. With the increase in the number of sandpaper mesh, the degree of protrusion gradually decreased in the direction of the vertical film surface, and the microstructures gradually became dense (Fig. 4c and Fig. S6, ESI†), which is also consistent with SEM images.
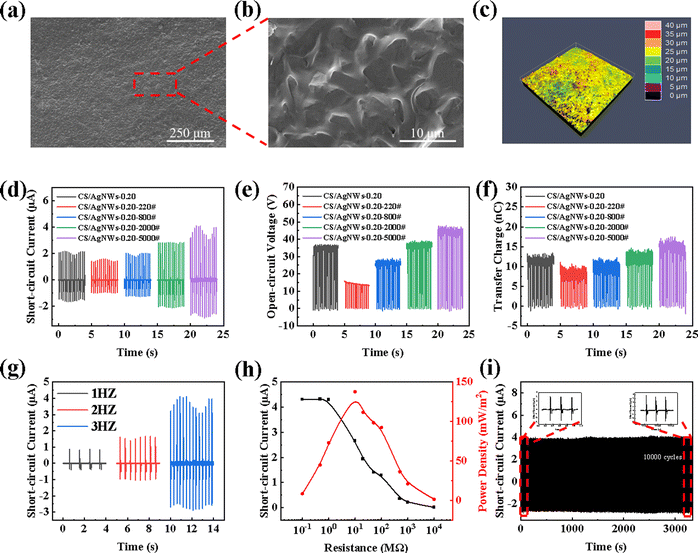 |
| Fig. 4 SEM images of the CS/AgNWs-0.20-5000# film at different scales. (c) CLSM image of the CS/AgNWs-0.20-5000# film. (d) Short-circuit current, (e) open-circuit voltage and (f) transfer charge quantity of CS/AgNWs-0.20 films processed by sandpaper with different mesh numbers. (g) Short-circuit current of a TENG with the CS/AgNWs-0.20-5000# film driven by a mechanical motor at different frequencies. (h) Dependence of current and instantaneous power density of the TENG on different load resistances of the CS composite–based TENG with the CS/AgNWs-0.20-5000# film. (i) Durability of the CS composite-based TENG with the CS/AgNWs-0.20-5000# film. | |
Fig. 4(d)–(f) present the short-circuit current, open-circuit voltage, and transfer charge quantity of CS/AgNWs-0.20 films based TENG with different microstructures. The output performance of CS/AgNWs-0.20-220# and CS/AgNWs-0.20-800# films processed with small mesh sandpaper was lower than that of unprocessed films. This was mainly due to the larger grain size of 220# and 800# of sandpaper, resulting in a higher degree of protrusion in the vertical direction and lesser number of microstructures. Thus, the friction contact of the deep friction material in the vertical direction was hindered in the actual friction process. However, the output performance of TENG increased gradually with the further increase of the mesh number of sandpaper, which was mainly attributed to the increase of the number of microstructures per unit area and the decrease of the vertical height. Consequently, the effective contact area was improved in the contact process. When the mesh number of sandpaper was 5000, the output performance of TENG increased to the maximum, and the short-circuit current, open-circuit voltage, and transfer charge quantity were 4.1 μA, 47.9 V, and 17.5 nC, respectively.
In addition, the CS/AgNWs-0.20-5000# film at different frequencies is shown in Fig. 4g. As the frequency increased from 1 Hz to 3 Hz, the short-circuit current increased from 0.9 μA to 4.1 μA. The improved current could be attributed to the increase in the contact speed of the two triboelectric materials, affording acceleration of charge transfer between them due to the increase in test frequency.41,55 In order to ensure that TENG can power some small electronics in daily life, the electrical output performance was further investigated. The effective power of the sample of CS/AgNWs-0.20-5000# film was measured by connecting the TENG to a resistor acting as an external load of 0.1 Ω to 10 GΩ. As shown in Fig. 4h, the output current decreased gradually as the resistance increased. Based on the load resistance and output current, the power density was calculated, and the maximum instantaneous power density was 137.6 mW m−2 when the external load was about 10 MΩ. Furthermore, durability and stability were two important characteristics that affected practical TENG applications. The output current remained stable during 10
000 cycles (Fig. 4i), showing good stability.
Due to the flexibility of CS composite films and PVDF, CS based TENG could be easily integrated with mobile electronic devices to collect energy from human motion and detect human motion state. CS-based TENG was pasted on the elbow, palm, and sole of the foot, respectively, and the output voltage generated during these motions was measured. Fig. 5(a)–(c) gave the different output electrical signals obtained in different parts of the body and under different motion states. The output voltages were 19.5 V and 37.5 V for slow elbow bending and fast elbow bending (Fig. 5a), 14.3 V and 16.9 V for slow clapping and fast clapping (Fig. 5b), and 19.6 V and 36.2 V for slow walking and fast walking (Fig. 5c). In addition, compared with slow motion, the output voltage signal generated by fast motion was also of high-frequency, which could be used to identify the state of individuals in motion through different electrical signals. Therefore, CS-based TENG had good performance in collecting the energy of human motion and detecting the motion state of human body.
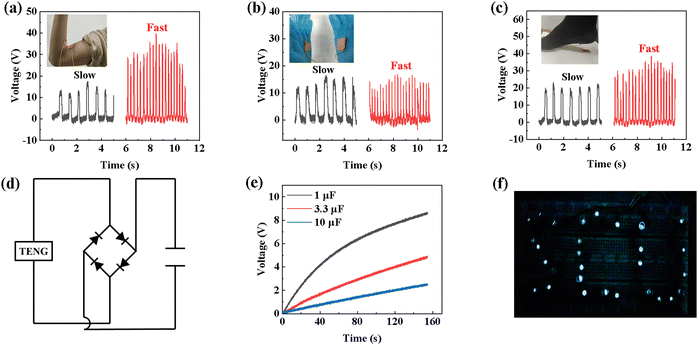 |
| Fig. 5 Applications of harvesting mechanical energy, powering portable electronics, and self-powered motion monitoring using the CS/AgNWs-0.20-5000#-based TENG. Voltage signals during (a) bending elbows, (b) clapping hands and (c) walking for real-time human motion monitoring; insets: photographs of the experimental set-up. (d) Schematic diagram of the TENG charging circuit. (e) Charge curves for different capacitors using the CS/AgNWs-0.20-5000#-based TENG. (f) Letter pattern comprising LEDs (working voltage: 3.0–3.4 V) directly powered by the CS/AgNWs-0.20-5000#-based TENG via a standard circuit. | |
Further, in order to verify the storage capacity of the charge collected by TENG. CS/AgNWs-0.20-5000# based TENG was connected with capacitors through a full-wave rectifier bridge (Fig. 5d). The results demonstrated that the TENG had the characteristic of fast-charging speed by the standard circuit, especially connected to the electrolytic capacitors with low capacitance. For example, the voltage on the 1 μF capacitor up to about 8.5 V was achieved in 150 s using the standard charging circuit. In addition, the TENG pass-through full-wave rectifier bridge based on CS/AgNWs-0.20-5000# can be used to drive light emitting diodes (LEDs), as shown in Fig. 5f, which could light up 28 LEDs with “SCU” pattern in series. This showed that TENG based on CS/AgNWs-0.20-5000# film can not only be used as a device to collect human motion energy, but also can detect the individual motion state in real time. It is expected to be used for health reminders, behavior detection, and other applications. Therefore, TENG based on CS/AgNWs-0.20-5000# film showed a broad application prospect in the fields of self-powered sensors (motion sensors,56 heart sensors, etc.57), human–computer interactions, and artificial intelligence.
4. Conclusion
In summary, a bio-triboelectric nanogenerator based on an environmentally friendly CS composite was developed. By enhancing the dielectric constant and adjusting its surface microstructure, the output performance of TENG was improved. The dielectric constant of the CS film was dramatically increased with AgNWs. It was found that when the content of AgNWs was 0.20%, the maximum output was achieved. The output performance was further enhanced with a combination of surface modification and dielectric constant control. When microstructure was constructed by the re-engraved structure of sandpaper, the optimal short-circuit current, open-circuit voltage, and transfer charge quantity were obtained, 4.1 μA, 47.9 V, and 17.5 nC, respectively, which are 310%, 185%, and 140% higher than pure CS based TENG. The output power density showed a value of 137.6 mW m−2 at an external load of 10 MΩ. Meanwhile, the output performance remained stable during 10
000 cycles, presenting good durability. The demonstrated output power could drive tiny electronic devices, and the output electrical signal could be adopted as a self-powered sensor to detect human motion, such as bending elbows, clapping hands, and walking. This study provided a simple, low-cost strategy to improve permittivity and further regulate microstructures, showing the promise of biocompatibility applications in wearable electronic devices.
Author contributions
Yu-Hao Zhang: conceptualization, investigation, writing – original draft. Yan Shao: writing – reviewing and editing. Chen Luo: investigation, validation. Hong-Zhi Ma: visualization. Hua Yu: resources. Xu Liu: resources. Bo Yin: conceptualization, writing – reviewing and editing, funding acquisition, supervision, project administration. Jun-Liang Wu: supervision, conceptualization, funding acquisition, methodology. Ming-Bo Yang: supervision, project administration.
Conflicts of interest
There are no conflicts to declare.
References
- Z. L. Wang and J. H. Song, Piezoelectric Nanogenerators Based on Zinc Oxide Nanowire Arrays, Science, 2006, 312, 242–246 CrossRef CAS PubMed.
- M. Danesh and J. R. Long, An Autonomous Wireless Sensor Node Incorporating a Solar Cell Antenna for Energy Harvesting, IEEE Trans. Microwave Theory, 2011, 59, 3546–3555 CAS.
- Y. K. Ramadass and A. P. Chandrakasan, A Battery-Less Thermoelectric Energy Harvesting Interface Circuit With 35 mV Startup Voltage, IEEE J. Solid-State Circuits, 2011, 46, 333–341 Search PubMed.
- Y. Sun, H. Cheng, S. Gao, Q. Liu, Z. Sun, C. Xiao, C. Wu, S. Wei and Y. Xie, Atomically Thick Bismuth Selenide Freestanding Single Layers Achieving Enhanced Thermoelectric Energy Harvesting, J. Am. Chem. Soc., 2012, 134, 20294–20297 CrossRef CAS.
- P.-T. Hsiao, W.-T. Hung, Y.-C. Chen, L.-K. Huang, C.-C. Chang, C.-F. Chen, H.-W. Chen, M.-D. Lu, Y.-P. Lin and Y.-L. Tung, Pilot Operation and Lifetime Assessment for Indoor Light Energy Harvesting Photovoltaics, Renewable Energy, 2020, 152, 67–74 CrossRef.
- H. A. Sodano, D. J. Inman and G. Park, Comparison of Piezoelectric Energy Harvesting Devices for Recharging Batteries, J. Intell. Mater. Syst. Struct., 2005, 16, 799–807 CrossRef.
- Y. C. Shu and I. C. Lien, Analysis of Power Output for Piezoelectric Energy Harvesting Systems, Smart Mater. Struct., 2006, 15, 1499–1512 CrossRef CAS.
- R. Caliò, U. B. Rongala, D. Camboni, M. Milazzo, C. Stefanini, G. De Petris and C. M. Oddo, Piezoelectric Energy Harvesting Solutions, Sensors, 2014, 14, 4755–4790 CrossRef.
- M. İ. Beyaz, F. Tat, K. Y. Özkaya and R. Özbek, Hybrid Magnetic-Piezoelectric Energy Harvester for Power Generation around Waistline During Gait, J. Electr. Eng. Technol., 2020, 15, 227–233 CrossRef.
- X.-S. Zhang, M.-D. Han, B. Meng and H.-X. Zhang, High Performance Triboelectric Nanogenerators Based on Large-Scale Mass-Fabrication Technologies, Nano Energy, 2015, 11, 304–322 CrossRef CAS.
- Z. Zhao, C. Yan, Z. Liu, X. Fu, L. M. Peng, Y. Hu and Z. Zheng, Machine-Washable Textile Triboelectric Nanogenerators for Effective Human Respiratory Monitoring through Loom Weaving of Metallic Yarns, Adv. Mater., 2016, 28, 10267–10274 CrossRef CAS.
- F.-R. Fan, Z.-Q. Tian and Z. Lin Wang, Flexible Triboelectric Generator, Nano Energy, 2012, 1, 328–334 CrossRef CAS.
- L. Long, W. Liu, Z. Wang, W. He, G. Li, Q. Tang, H. Guo, X. Pu, Y. Liu and C. Hu, High Performance Floating Self-Excited Sliding Triboelectric Nanogenerator for Micro Mechanical Energy Harvesting, Nat. Commun., 2021, 12, 4689 CrossRef CAS.
- Y. Yun, M. La, S. Cho, S. Jang, J. H. Choi, Y. Ra, D. Kam, S. J. Park and D. Choi, High Quality Electret Based Triboelectric Nanogenerator for Boosted and Reliable Electrical Output Performance, Int. J. Precis. Eng. Manuf., 2021, 8, 125–137 Search PubMed.
- L. Zhao, Q. Zheng, H. Ouyang, H. Li, L. Yan, B. Shi and Z. Li, A Size-Unlimited Surface Microstructure Modification Method for Achieving High Performance Triboelectric Nanogenerator, Nano Energy, 2016, 28, 172–178 CrossRef CAS.
- Y. Ra, J. H. Choi, S.-J. Choi, M. La, S. J. Park, M.-J. Kim and D. Choi, Cold Rolled Robust Metal Assisted Triboelectric Nanogenerator for Extremely Durable Operation, Extreme. Mech. Lett., 2020, 40, 100910 CrossRef.
- J. Peng, D. Kang Stephen and G. J. Snyder, Optimization Principles and The Figure of Merit for Triboelectric Generators, Sci. Adv., 2017, 3, 2375–2548 Search PubMed.
- J. Zhao, G. Zhen, G. Liu, T. Bu, W. Liu, X. Fu, P. Zhang, C. Zhang and Z. L. Wang, Remarkable Merits of Triboelectric Nanogenerator than Electromagnetic Generator for Harvesting Small-Amplitude Mechanical Energy, Nano Energy, 2019, 61, 111–118 CrossRef CAS.
- X. Wang, Z. Wen, H. Guo, C. Wu, X. He, L. Lin, X. Cao and Z. L. Wang, Fully Packaged Blue Energy Harvester by Hybridizing a Rolling Triboelectric Nanogenerator and an Electromagnetic Generator, ACS Nano, 2016, 10, 11369–11376 CrossRef CAS.
- B. D. Chen, W. Tang, C. He, C. R. Deng, L. J. Yang, L. P. Zhu, J. Chen, J. J. Shao, L. Liu and Z. L. Wang, Water Wave Energy Harvesting and Self-Powered Liquid-Surface Fluctuation Sensing Based on Bionic-Jellyfish Triboelectric Nanogenerator, Mater. Today, 2018, 21, 88–97 CrossRef CAS.
- G. Zhu, Y. Su, P. Bai, J. Chen, Q. Jing, W. Yang and Z. L. Wang, Harvesting Water Wave Energy by Asymmetric Screening of Electrostatic Charges on a Nanostructured Hydrophobic Thin-Film Surface, ACS Nano, 2014, 8, 6031–6037 CrossRef CAS.
- H. Yong, J. Chung, D. Choi, D. Jung, M. Cho and S. Lee, Highly Reliable Wind-Rolling Triboelectric Nanogenerator Operating in A Wide Wind Speed Range, Sci. Rep., 2016, 6, 33977 CrossRef CAS.
- L.-b Huang, W. Xu, G. Bai, M.-C. Wong, Z. Yang and J. Hao, Wind Energy and Blue Energy Harvesting Based on Magnetic-Assisted Noncontact Triboelectric Nanogenerator, Nano Energy, 2016, 30, 36–42 CrossRef CAS.
- H. Lin, M. He, Q. Jing, W. Yang, S. Wang, Y. Liu, Y. Zhang, J. Li, N. Li, Y. Ma, L. Wang and Y. Xie, Angle-Shaped Triboelectric Nanogenerator for Harvesting Environmental Wind Energy, Nano Energy, 2019, 56, 269–276 CrossRef CAS.
- J. Wang, H. Zhang, Y. Xie, Z. Yan, Y. Yuan, L. Huang, X. Cui, M. Gao, Y. Su, W. Yang and Y. Lin, Smart Network Node Based on Hybrid Nanogenerator for Self-Powered Multifunctional Sensing, Nano Energy, 2017, 33, 418–426 CrossRef CAS.
- A. Pratap, N. Gogurla and S. Kim, Elastic and Skin-Contact Triboelectric Nanogenerators and Their Applicability in Energy Harvesting and Tactile Sensing, ACS Appl. Electron. Mater., 2022, 4, 1124–1131 CrossRef CAS.
- S. Hu, J. Weber, S. Chang, G. Xiao, J. Lu, J. Gao, W. Jiang, Y. Zhang and Y. Tao, A Low-Cost Simple Sliding Triboelectric Nanogenerator for Harvesting Energy from Human Activities, Adv. Mater. Technol., 2022, 7, 2200186 CrossRef CAS.
- M. N. V. Ravi Kumar, A Review of Chitin and Chitosan Applications, React. Funct. Polym., 2000, 46, 1–27 CrossRef.
- P. Sirajudheen, N. C. Poovathumkuzhi, S. Vigneshwaran, B. M. Chelaveettil and S. Meenakshi, Applications of Chitin and Chitosan Based Ciomaterials for The Adsorptive Removal of Textile Dyes from Water—A Comprehensive Review, Carbohydr. Polym., 2021, 273, 118604 CrossRef CAS PubMed.
- A. Bhatnagar and M. Sillanpää, Applications of Chitin- and Chitosan-Derivatives for The Detoxification of Water and Wastewater—A Short Review, Adv. Colloid Interface Sci., 2009, 152, 26–38 CrossRef CAS PubMed.
- R. Parhi, Drug Delivery Applications of Chitin and Chitosan: A Review, Environ. Chem. Lett., 2020, 18, 577–594 CrossRef CAS.
- S. A. Agnihotri, N. N. Mallikarjuna and T. M. Aminabhavi, Recent Advances on Chitosan-Based Micro-and Nanoparticles in Drug Delivery, J. Controlled Release, 2004, 100, 5–28 CrossRef CAS PubMed.
- I. Hamed, F. Özogul and J. M. Regenstein, Industrial Applications of Crustacean by-Products (chitin, chitosan, and chitooligosaccharides): A Review, Trends Food Sci. Technol., 2016, 48, 40–50 CrossRef CAS.
- X. Li, Q. Feng, Y. Jiao and F. Cui, Collagen-Based Scaffolds Reinforced by Chitosan Fibres for Bone Tissue Engineering, Polym. Int., 2005, 54, 1034–1040 CrossRef CAS.
- R. Wang, S. Gao, Z. Yang, Y. Li, W. Chen, B. Wu and W. Wu, Engineered and Laser-Processed Chitosan Biopolymers for Sustainable and Biodegradable Triboelectric Power Generation, Adv. Mater., 2018, 30, 1706267 CrossRef PubMed.
- B. Liu, S. Wang, Z. Yuan, Z. Duan, Q. Zhao, Y. Zhang, Y. Su, Y. Jiang, G. Xie and H. Tai, Novel hitosan/ZnO Bilayer Film With Enhanced Humidity-Tolerant Property: Endowing Triboelectric Nanogenerator with Acetone Analysis Capability, Nano Energy, 2020, 78, 105256 CrossRef CAS.
- J.-N. Kim, J. Lee, T. W. Go, A. Rajabi-Abhari, M. Mahato, J. Y. Park, H. Lee and I.-K. Oh, Skin-Attachable and Biofriendly Chitosan-Diatom Triboelectric Nanogenerator, Nano Energy, 2020, 75, 104904 CrossRef CAS.
- Y.-T. Jao, P.-K. Yang, C.-M. Chiu, Y.-J. Lin, S.-W. Chen, D. Choi and Z.-H. Lin, A Textile-Based Triboelectric Nanogenerator with Humidity-Resistant Output Characteristic and Its Applications in Self-Powered Healthcare Sensors, Nano Energy, 2018, 50, 513–520 CrossRef CAS.
- Y. Su, T. Yang, X. Zhao, Z. Cai, G. Chen, M. Yao, K. Chen, M. Bick, J. Wang, S. Li, G. Xie, H. Tai, X. Du, Y. Jiang and J. Chen, A Wireless Energy Transmission Enabled Wearable Active Acetone Biosensor for Non-Invasive Prediabetes Diagnosis, Nano Energy, 2020, 74, 104941 CrossRef CAS.
- J.-N. Kim, J. Lee, H. Lee and I.-K. Oh, Stretchable and Self-Healable Catechol-Chitosan-Diatom Hydrogel for Triboelectric Generator and Self-Powered Tremor Sensor Targeting at Parkinson Disease, Nano Energy, 2021, 82, 105705 CrossRef CAS.
- S. Niu, S. Wang, L. Lin, Y. Liu, Y. S. Zhou, Y. Hu and Z. L. Wang, Theoretical Study of Contact-Mode Triboelectric Nanogenerators as An Effective Power Source, Energy Environ. Sci., 2013, 6, 3576–3583 RSC.
- H.-W. Park, N. D. Huynh, W. Kim, C. Lee, Y. Nam, S. Lee, K.-B. Chung and D. Choi, Electron Blocking Layer-Based Interfacial Design for Highly-Enhanced Triboelectric Nanogenerators, Nano Energy, 2018, 50, 9–15 CrossRef CAS.
- C. Yao, X. Yin, Y. Yu, Z. Cai and X. Wang, Chemically Functionalized Natural Cellulose Materials for Effective Triboelectric Nanogenerator Development, Adv. Funct. Mater., 2017, 27, 1700794 CrossRef.
- V. T. Bui, Q. Zhou, J. N. Kim, J. H. Oh, K. W. Han, H. S. Choi, S. W. Kim and I. K. Oh, Treefrog Toe Pad-Inspired Micropatterning for High-Power Triboelectric Nanogenerator, Adv. Funct. Mater., 2019, 29, 1901638 CrossRef.
- H. Kang, H. T. Kim, H. J. Woo, H. Kim, D. H. Kim, S. Lee, S. Kim, Y. J. Song, S.-W. Kim and J. H. Cho, Metal Nanowire–Polymer Matrix Hybrid Layer for Triboelectric Nanogenerator, Nano Energy, 2019, 58, 227–233 CrossRef CAS.
- H. Wang, M. Shi, K. Zhu, Z. Su, X. Cheng, Y. Song, X. Chen, Z. Liao, M. Zhang and H. Zhang, High Performance Triboelectric Nanogenerators with Aligned Carbon Nanotubes, Nanoscale, 2016, 8, 18489–18494 RSC.
- J. Chun, J. W. Kim, W.-S. Jung, C.-Y. Kang, S.-W. Kim, Z. L. Wang and J. M. Baik, Mesoporous Pores Impregnated with Au Nanoparticles as Effective Dielectrics for Enhancing Triboelectric Nanogenerator Performance in Harsh Environments, Energy Environ. Sci., 2015, 8, 3006–3012 RSC.
- J. Chen, H. Guo, X. He, G. Liu, Y. Xi, H. Shi and C. Hu, Enhancing Performance of Triboelectric Nanogenerator by Filling High Dielectric Nanoparticles into Sponge PDMS Film, ACS Appl. Mater. Interfaces, 2016, 8, 736–744 CrossRef CAS PubMed.
- K. Shahzadi, L. Wu, X. Ge, F. Zhao, H. Li, S. Pang, Y. Jiang, J. Guan and X. Mu, Preparation and Characterization of Bio-based Hybrid Film Containing Chitosan and Silver Nanowires, Carbohydr. Polym., 2016, 137, 732–738 CrossRef CAS PubMed.
- M. Tian, Q. Ma, X. Li, L. Zhang, T. Nishi and N. Ning, High Performance Dielectric Composites by Latex Compounding of Graphene Oxide-Encapsulated Carbon Nanosphere Hybrids with XNBR, J. Mater. Chem. A, 2014, 2, 11144–11154 RSC.
- Z. M. Dang, Y. H. Lin and C. W. Nan, Novel Ferroelectric Polymer Composites with High Dielectric Constants, Adv. Mater., 2003, 15, 1625–1629 CrossRef CAS.
- Y. Shao, C.-p Feng, B.-w Deng, B. Yin and M.-b Yang, Facile Method to Enhance Output Performance of Bacterial Cellulose Nanofiber Based Triboelectric Nanogenerator By Controlling Micro-Nano Structure and Dielectric Constant, Nano Energy, 2019, 62, 620–627 CrossRef CAS.
- H. Yu, Y. Shao, C. Luo, Y. Li, H.-Z. Ma, Y.-H. Zhang, B. Yin, J.-B. Shen and M.-B. Yang, Bacterial Cellulose Nanofiber Triboelectric Nanogenerator Based on Dielectric Particles Hybridized System, Composites, Part A, 2021, 151, 106646 CrossRef CAS.
- J. Wang, Z. Wen, Y. Zi, P. Zhou, J. Lin, H. Guo, Y. Xu and Z. L. Wang, All-Plastic-Materials Based Self-Charging Power System Composed of Triboelectric Nanogenerators and Supercapacitors, Adv. Funct. Mater., 2016, 26, 1070–1076 CrossRef CAS.
- X.-S. Zhang, M.-D. Han, R.-X. Wang, F.-Y. Zhu, Z.-H. Li, W. Wang and H.-X. Zhang, Frequency-Multiplication High-Output Triboelectric Nanogenerator for Sustainably Powering Biomedical Microsystems, Nano Lett., 2013, 13, 1168–1172 CrossRef CAS PubMed.
- J. Wang, S. Li, F. Yi, Y. Zi, J. Lin, X. Wang, Y. Xu and Z. L. Wang, Sustainably Powering Wearable Electronics Solely by Biomechanical Energy, Nat. Commun., 2016, 7, 12744 CrossRef CAS PubMed.
- H. Ouyang, Z. Liu, N. Li, B. Shi, Y. Zou, F. Xie, Y. Ma, Z. Li, H. Li, Q. Zheng, X. Qu, Y. Fan, Z. L. Wang, H. Zhang and Z. Li, Symbiotic Cardiac Pacemaker, Nat. Commun., 2019, 10, 1821 CrossRef PubMed.
|
This journal is © The Royal Society of Chemistry 2023 |
Click here to see how this site uses Cookies. View our privacy policy here.