In situ green synthesis of copper(II) oxide (CuO) and maleic anhydride grafted polypropylene (PP-MAH) for highly efficient nanocatalysis in tannery wastewater treatment†
Received
29th October 2023
, Accepted 14th November 2023
First published on 14th November 2023
Abstract
The discharge of substantial volumes of wastewater laden with toxic contaminants from tannery factories poses severe environmental challenges. This study delves into the synthesis of a CuO–PP-MAH nanocomposite and explores its efficacy in reducing the BOD/COD levels in tannery wastewater. Addressing this issue necessitates the development of nanoparticles incorporated within polymeric nanocomposites, utilizing eco-friendly resources and minimizing the use of hazardous precursors. In this context, a novel in situ melt mixing and extrusion technique has been introduced for the synthesis of CuO–PP-MAH, wherein copper oxide (CuO) nanoparticles are immobilized onto maleic anhydride grafted polypropylene (PP-MAH). Scanning and transmission electron microscopy revealed well-dispersed copper oxide nanoparticles on the polymeric support, exhibiting diameters ranging from 20 to 60 nm due to maleic anhydride functionalization. Fourier transform infrared spectroscopy confirmed the complexation of copper moieties with maleic anhydride grafted onto the polymeric chains. This method yielded a stable, high surface area, highly efficient, and regenerative catalytic nanocomposite. The potential of this nanocomposite as a green catalyst was assessed for COD/BOD reduction in industrial tannery wastewater, demonstrating remarkable catalytic activity in diminishing COD/BOD. Notably, the process did not involve any toxic solvents and adhered to the principles of green chemistry. Furthermore, this approach is scalable for industrial applications, indicating its practical viability.
Water impact
One of the main problems in reaching a circular economy is reduction of CO2 generation while also preventing migration of different materials toward bodies of water. The aim of the present work is creation of a catalyst which is stable and couldn't migrate because of the grafting and thermoplastic behavior of the base material (PP), while the catalyst can easily be shaped via normal molding procedures. Also this catalyst is active under normal sun radiation and the required energy for action is zero.
|
1 Introduction
The leather industry constitutes a vital economic sector in many countries, contributing significantly to the economy through a diverse range of value-added products. However, a pressing concern arises from the substantial volumes of wastewater these factories discharge, containing many toxic contaminants. This issue has raised significant environmental alarms.1 Tannery units discharge effluents with elevated salinity, increased chemical and biochemical oxygen demand (COD and BOD), and various toxic heavy metals.2 In response to these challenges, environmental agencies have established stringent emission standards. These regulations aim to draw attention to the pollutants and strive to maintain the integrity of global water supplies, ensuring their healthiness.3 Although industries employ wastewater treatment processes to comply with these standards, challenges persist due to the persistence of high COD, BOD, and suspended solids, which continue to pose ecological threats.4 To address these challenges, researchers have explored a variety of physicochemical methods to decontaminate wastewater emanating from leather industries.5 For instance, Liu et al. conducted a study focusing on chromium removal from leather industry wastewater, achieving some success.6 However, these effluents' high toxicity and intricate composition complicate the efficacy of traditional treatment methods. Issues such as secondary pollution arising from solid waste, the financial implications of the procedures involved, and low BOD/COD reduction dampen their practical applicability in real-world scenarios.7 In response to the challenges above, scientists have actively pursued innovative and economically viable technologies. This study delves into the pivotal role played by metal/metal oxide nanoparticle-based nanocomposites in mitigating the BOD and COD of tannery wastewater. The utilization of nanocomposites featuring metal/metal oxide nanoparticles has garnered significant interest in the field of catalysis, particularly concerning environmental remediation.8 Notably, copper/copper oxide (CuO) polymer composites have emerged as promising candidates, showcasing remarkable photocatalytic and antimicrobial properties.9 Beyond their catalytic properties,10 CuO nanoparticles have found extensive application as antimicrobial agents, effectively combatting various pathogens.11 Their inherent low toxicity and cost-effectiveness render them particularly appealing for these applications when compared to other metal counterparts possessing antibacterial properties, such as silver. Consequently, substantial research efforts have been dedicated to the development of catalyst–polymer composites and their employment in purifying contaminated water sources.12 For instance, Atta et al. conducted a noteworthy study focusing on the elimination of methylene blue dye from wastewater by synthesizing magnetite/cuprous oxide/poly (AMPS/NIPAm) composites.13
In the realm of catalyst–polymer composite preparation, ex situ and in situ methods emerge as pivotal techniques. The former approach involves the discrete synthesis of nanoparticles and the polymerization of monomers. Subsequently, these components are melded together through extrusion, solution phase blending, spraying, or dip coating, depositing nanoparticles onto the polymer surface. Conversely, the latter approach entails the simultaneous polymerization of monomers alongside nanoparticle synthesis.
Polypropylene (PP) stands out as a widely employed thermoplastic polymer, finding diverse applications in textiles, automotive engineering, and packaging owing to its favorable processability and robust physical and thermal properties. Palza et al. applied the melt mixing technique to synthesize copper–polypropylene composites, leveraging copper ion release for antibacterial activity against E. coli.14,15 Another study adopted the phase inversion method, incorporating CuO nanoparticles into mixed cellulose acetate and polyether sulfone matrices, demonstrating efficacy as a dye adsorbent.16 Furthermore, innovative approaches led to the development of composite materials like urchin-like CuO microparticles and polyvinylidene fluoride, serving as efficient photocatalysts for dye degradation under visible light irradiation.17 Recent advancements featured the utilization of chitosan-supported Cu2O/CuO nanocomposites, showcasing remarkable catalytic activity in the reduction of cationic and anionic dyes and 4-nitrophenol.18
In the realm of developing efficient copper composites, a key challenge lies in preventing the agglomeration of nanoparticles within the polymeric matrix. Agglomeration significantly diminishes the effectiveness of the resulting nanocomposite. A promising strategy to avoid this issue involves immobilizing nanoparticles on diverse polymeric supports.19 These supports encompass a range of materials, including (i) biopolymers such as agar,20 carboxymethylcellulose (CMC),21 and chitosan;22 (ii) synthetic polymers like epoxy resin,23 nylon,24 and polyaniline (PANI);25 (iii) hydrogels derived from acrylamide acrylic acids,26 polyvinyl alcohol (PVA),27 and polyvinyl alcohol–acrylic acid;28 and (iv) inorganic polymers, notably KIT-5 mesoporous silica.29
Furthermore, our prior studies have illuminated a practical approach to mitigate this challenge through the maleic acid functionalization of the polymeric matrix.30,31 In nanocomposite synthesis, the challenge of developing a facile and cost-effective method for large-scale production remains a prominent concern.31 This study delves into the synthesis of CuO–PP-MAH via the innovative melt mixing and extrusion technique. In this process, CuO nanoparticles were strategically immobilized on maleic anhydride-grafted polypropylene (PP) to curb their aggregation and prevent their leaching from the polymeric matrix. Remarkably, this method was executed without employing any toxic solvents, adhering to the principles of green chemistry, thereby yielding a high-surface-area catalytic nanocomposite tailored for wastewater remediation.
Furthermore, the potential of this nanocomposite as a stable, highly efficient, and regenerative catalyst for COD and BOD removal from industrial tannery wastewater was explored. Characterization of the CuO nanoparticles, PP functionalized with maleic anhydride, and the resultant CuO–PP nanocomposite was meticulously performed utilizing advanced techniques such as field emission scanning electron microscopy (FESEM), transmission electron microscopy (TEM), and Fourier-transform infrared spectroscopy (FTIR). This study explored and analyzed the impact of crucial adsorption parameters, specifically contact time and the mass ratio of the CuO–PP adsorbent content, on the reduction of COD and BOD in wastewater. The FTIR spectrum indicated the presence of copper within the polypropylene matrix. Moreover, the SEM images illustrated the presence of copper nanoparticles ranging in size from 20 to 60 nanometers. Rigorous experimentation aimed at reducing BOD and COD exhibited a substantial reduction exceeding 70%. Notably, the results underscored the potential of CuO–MAH-PP as a stable and reusable catalytic support for BOD/COD reduction in tannery wastewater.
2 Experimental section
In this section, our primary objective is to synthesize a copper metal nanopolymer utilizing the in situ melt mixing and extrusion technique. The resulting nanopolymer will subsequently be employed to reduce BOD and COD levels in tannery wastewater.
2.1 Materials
All chemicals were procured commercially and employed without additional purification. The reagents and solvents utilized were of high purity and sourced from reputable suppliers such as Merck and Sigma-Aldrich.
2.2 Instrumental analysis
The FT-IR spectra of polypropylene (PP) and the nanocomposite were acquired in a film format without KBr pelleting, utilizing an FT-IR spectrophotometer (Bruker, Germany). Morphological studies were carried out using a scanning electron microscopy (SEM) apparatus (VEGA Tescan, Czech Republic) coupled with energy-dispersive X-ray spectroscopy (EDX) tests conducted on an INCA model apparatus (Oxford Instruments, UK). The SEM apparatus operated under the conditions of a 3 A electric current, a voltage of 15 kV, and a working pressure of 5 Pa. Before imaging, the samples underwent etching with dimethyl sulfoxide for 4 hours at 50 °C to remove ethanol (EtOH), followed by a 24 hour drying period at 50 °C. Their cross-sections were used for analysis after freeze-fracturing in liquid nitrogen and subsequent gold-sputtering. The copper content in the samples was determined through inductively coupled plasma atomic emission spectroscopy (ICP-AES) in conjunction with EDX analysis.
2.3 Functionalization of the polymeric support: synthesis of PP-MAH
PP-MAH was synthesized via in situ bulk polymerization, following our previous work.30 Initially, polypropylene granules were reacted with maleic anhydride monomer in the presence of dicumyl peroxide as an initiator and acetone as a solvent under a nitrogen atmosphere at 70 °C for 1.5 hours. Upon completion of the reaction, the reaction vessel was gradually cooled to room temperature. The resulting precipitate was carefully filtered and subsequently washed with hot acetone. The solid precipitate obtained was then dried overnight in a vacuum oven at 60 °C.
2.4 Preparation of the CuO–PP-MAH nanocomposite
The grafting of CuO onto PP-MAH was accomplished using a co-rotating twin screw extruder with potassium hydroxide as the catalyst and deionized water as the solvent for CuO. To create the grafting solution, 5% wt of CuO was dispersed into a mixture of KOH and water (KOH/water ratio of 1/10 by weight). This solution was evenly sprayed onto the blend granules during turbo mixing. Subsequently, the mixture was fed into the extruder at a constant rate of 5 kg h−1, with the feeding and screw speeds set to 350 rpm. The extruder operated at a series of temperatures: 120–150–190–190–210–210–205–200 °C. After the grafting process, the extruded strings were granulated following cooling to ambient temperature.
2.5 Tannery wastewater treatment experiments in batch mode
The experiments were conducted in sealed conical flasks acting as batch reactors, maintained at room temperature. Various quantities of the CuO–PP-MAH nanocomposite (0, 5, 10, 15, 20, 25 g) were introduced into 60 mL samples of tannery wastewater with known initial COD and BOD levels. After 80 minutes of agitation, samples were withdrawn at specific intervals, filtered, and subsequently analyzed for residual BOD and COD concentrations. The study investigated the impact of the weight percentage of CuO within the CuO–PP-MAH nanocomposite, treatment duration, and nanocomposite dosage. All other conditions were held constant, with only the specified factor being altered.
Following the batch adsorption treatment, the reduction percentages of COD and BOD were calculated using eqn (1) and (2):32
| 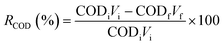 | (1) |
| 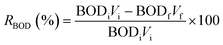 | (2) |
The variables COD
i, BOD
i, COD
f, and BOD
f represent the initial and final concentrations at a specific time, measured in milligrams per liter (mg L
−1).
Vi and
Vf denote the volumes of the initial and treated wastewater solutions expressed in liters (L), respectively.
2.6 Desorption and regeneration studies
Desorption experiments were conducted in batch mode. Initially, the adsorbent was saturated with tannery wastewater of predetermined COD and BOD concentrations. Subsequently, the exhausted material was regenerated through sequential washing with 1 M HCl and 1 M NaOH. Post-elution, the adsorbent was rewashed with distilled water until the effluent pH reached a neutral level and then dried at 100 °C for 24 hours. Six cycles of “sorption–desorption–regeneration” were performed to assess the adsorbent capacity. COD and BOD reduction percentages were determined for each cycle, providing valuable insights into the efficacy of the process.
3 Results and discussion
3.1 Preparation and characterization of the CuO–PP-MAH nanocomposite
The polypropylene substrate, its functionalization with MAH, and the attachment of the CuO nanomaterial onto the polymeric surfaces were thoroughly examined utilizing FTIR. Fig. 1 illustrates the spectrum obtained for pure polypropylene. Additionally, the distinct spectrum corresponding to copper oxide nanoparticles is presented separately.
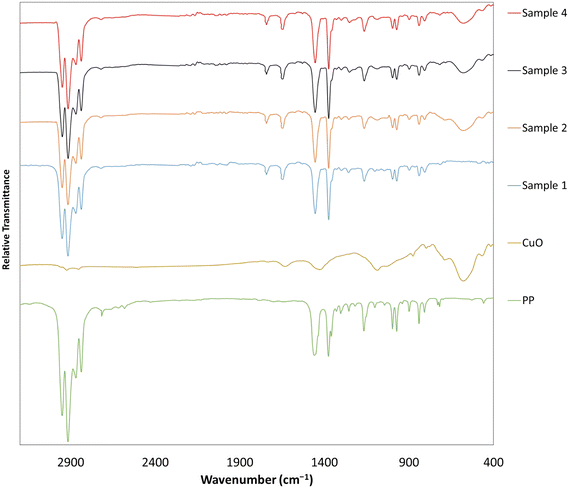 |
| Fig. 1 FTIR spectra for PP, CuO, PP-MAH, and CuO–PP-MAH. | |
Fig. 1 illustrates four distinct copper samples. Sample 1 consists of polypropylene on which maleic anhydride groups were placed. For samples 2, 3, and 4, the presence of copper on the polymer substrate was confirmed by placing copper oxide nanoparticles onto the prepared samples. The presence of specific peaks at certain wavelengths supports this assertion. In samples 2 to 4, the peaks observed at 809 and 841 cm−1 correspond to the stretching vibrations of –CH2 and –CH3, while the bending vibrations of –CH3 manifest at 973 and 997 cm−1. The distinct sharp bands at 1376 and 1460 cm−1 are also attributed to the bending vibrations of –CH, –CH2, and –CH3 functional groups. The appearance of a peak within the 2780–3000 cm−1 range is assigned to the –CH stretching vibration of the polypropylene chain.33
The successful functionalization of polypropylene with MAH in CuO–PP-MAH was confirmed through the presence of the absorption peak corresponding to the symmetric stretching C
O of the anhydride function grafted onto PP, observed at 1600–1700 cm−1. Furthermore, the FTIR results revealed a peak at 879 cm−1, attributed to vinylidene in enriched unsaturated PP due to benzoic acid.
In the FTIR spectrum of copper oxide nanoparticle incorporated polypropylene, a distinct sharp band emerged at 1378 cm−1, which was assigned to the Cu–O vibrations in the infrared region.
The morphological characteristics of the CuO–PP-MAH nanocomposites, synthesized through the melt mixing and extrusion technique, were examined using scanning electron microscopy (SEM). The experiments were conducted utilizing a field-emission scanning electron microscope (FESEM) apparatus (ZEISS, Germany, model: SIGMA VP). The SEM micrographs of the washed CuO–PP-MAH surfaces are shown in Fig. 2 and 3, providing a detailed visualization of the nanocomposite structure.
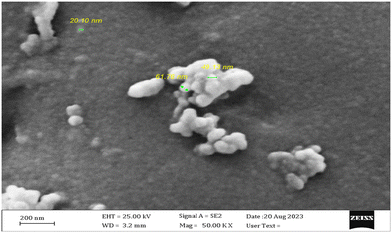 |
| Fig. 2 SEM micrograph with particle size. | |
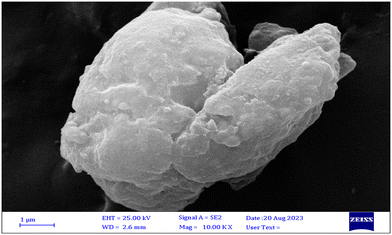 |
| Fig. 3 SEM micrograph. | |
In Fig. 2, distinct bright particles ranging from 20 nm to 60 nm in size are discernible. In regions where enhanced copper stabilization has taken place, a noticeable increase in size at the nanometer scale is observed, accompanied by a significant enhancement in transparency. The presence of smaller CuO particles, potentially around the resolution limit of SEM, might go undetected. It is assumed that two distinct CuO structures exist within the polymeric matrix. Initially, CuO nanoparticles of approximately 20 nm in diameter are formed, followed by a minor degree of agglomeration, resulting in particles approximately 60 nm in size. Consequently, the uniform dispersion of primary CuO nanoparticles on polymer substrates is evident, confirming the successful conjugation of CuO nanoparticles with the polymeric substrate. This observation attests to the homogeneous immobilization of CuO nanoparticles on the PP–MAH surface, particularly at lower concentrations.
The EDX analysis result, depicted in Fig. 4, illustrates the weight percentages of elements present on the polymer surface. These findings align notably well with the expected nominal weight percentages of CuO. Furthermore, the detection of carbon and nitrogen atoms signifies the presence of a general PP–MAH structure, complemented by the presence of oxygen. This oxygen presence could stem from the polymer matrix and the metal oxide component.
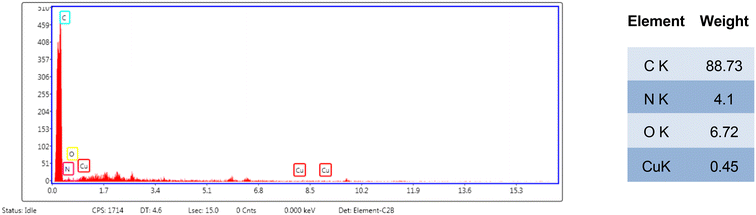 |
| Fig. 4 EDX analysis of CuO–PP-MAH. | |
Fig. 5 presents bright-field TEM images, confirming the presence of CuO within the matrix at nanoscale dimensions. Notably, it indicates a proportional increase in the average size of CuO species with the CuO percentage, as evidenced by SEM. Notably, unlike the results from energy-dispersive X-ray (EDX) analysis, the CuO nanoparticles measuring approximately 10 nm remained indistinct in TEM imaging.
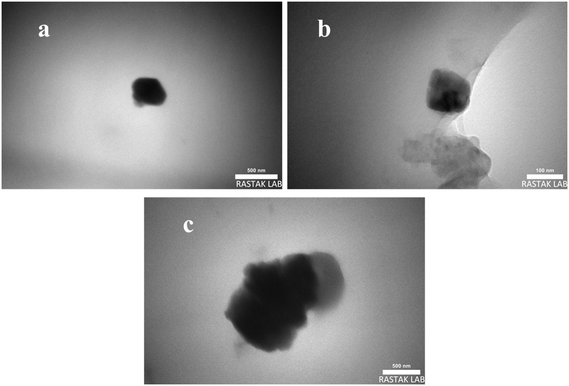 |
| Fig. 5 TEM micrographs of CuO–PP-MAH, (a)–(c). | |
In the subsequent analysis, ICP-AES was employed to accurately determine the copper content in CuO–PP-MAH following the digestion of samples in a concentrated solution of HNO3 and HCl in a 1
:
1 ratio. The CuO contents were measured to be 0.30%, 0.43%, and 1.11% (w/w) for the three samples. Compared to nominal weight loadings and EDX analysis, ICP-AES provided precise and consistent determination of the CuO content within the samples. These findings align with the results obtained from the EDX analysis.
3.2 Tannery wastewater treatment by the CuO–PP-MAH nanocomposite
3.2.1 Impact of CuO weight percentage in the CuO–PP-MAH nanocomposite.
The influence of the CuO nanoparticle content on the efficiency of the nanocomposite in COD/BOD reduction was examined. Fig. 6a illustrates that with the increase in CuO content, the R% values exhibited a corresponding enhancement. Notably, the nanocomposite containing 1 wt% of CuO demonstrated superior activity compared to other compositions. Consequently, the 1% wt CuO–PP-MAH nanocomposite was chosen for further investigations. These results showcased enhanced performance despite the observation of CuO nanoparticle clustering at the 1 wt% level in the SEM images. This phenomenon could potentially be attributed to the presence of additional catalytic sites, thereby contributing to the improved activity of the nanocomposite.
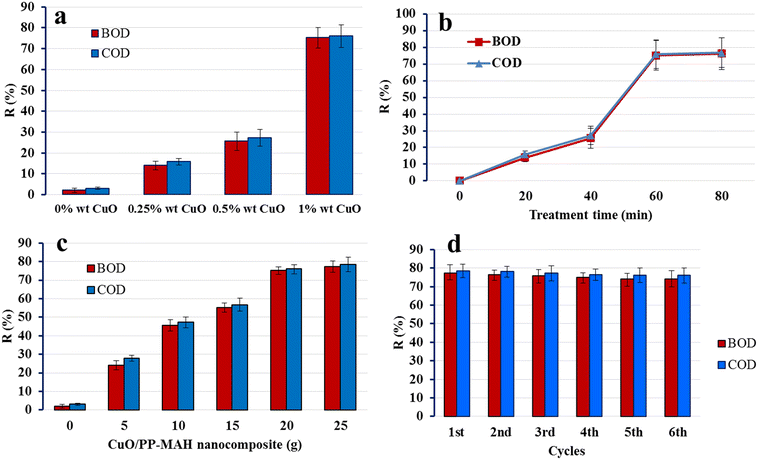 |
| Fig. 6 Effect of (a) CuO content in CuO–PP-MAH, (b) treatment time, and (c) CuO–PP-MAH dosage on COD and BOD reduction in raw tannery wastewater, and (d) regeneration–reuse of CuO–PP-MAH. | |
3.2.2 Effect of treatment time.
In evaluating the nanocomposite's performance, it was utilized to treat raw tannery effluent with known initial BOD and COD levels. The correlation between the percentage reduction in BOD and COD concerning treatment duration using CuO–PP-MAH is depicted in Fig. 6b. Notably, over 75% of the reduction in BOD/COD was rapidly achieved within the initial 60 minutes. Subsequently, a state of equilibrium was achieved. After 80 minutes of treatment, the maximum reductions observed were 77.2% for BOD and 78.47% for COD.
The outcomes indicate that during the initial phase of the process, impurities linked to COD and BOD were adsorbed on the external surface of the nanocomposite, leading to a relatively fast adsorption rate. With the progress of treatment time, saturation occurred on the nanocomposite's exterior surface. Subsequently, more molecules diffused into the pores and underwent adsorption within the material's interior. Consequently, relatively slower sorption rates were observed,34 leading to a less significant reduction in COD and BOD.
3.2.3 Influence of nanocomposite quantity.
The impact of CuO–PP-MAH dosage on the reduction of BOD and COD in raw effluents was investigated while maintaining the treatment time constant at 80 minutes. The results, illustrated in Fig. 6c, demonstrate a significant enhancement in both BOD and COD reduction when the dosage of the nanocomposite increased from 5 to 20 g, after which the reduction rates stabilized. This observed increase can be attributed to several factors inherent to CuO–PP-MAH, notably its larger surface area, abundant adsorption sites, and a more potent driving force. The subsequent gradual plateau reduction can be attributed to the intra-particle diffusion of organic species, occurring concurrently with the dominance of the adsorption process.35 Notably, a dosage of 20 g of CuO–PP-MAH proved crucial in achieving a remarkable over 75% reduction in COD/BOD.32,36 Visual evidence of this reduction process is presented in Fig. S1,† depicting the color changes in tannery wastewater samples with varying CuO–PP-MAH dosages from 0 to 20 g, highlighting the observable transition from the initial blue color of the wastewater.
3.2.4 Regeneration studies.
The adsorbent's reusability is a pivotal criterion in evaluating its practical applicability. In order to assess the reusability of the developed nanocomposite, the spent material underwent desorption using 1 M NaOH, subsequent washing with 1 M HCl and drying at 100 °C. The regenerated material was subjected to six sorption–desorption cycles and employed in COD and BOD reduction processes. Remarkably, after six cycles, the material exhibited a reduction of over 70% in both BOD and COD (as illustrated in Fig. 6d), underscoring its exceptional regenerative capacity.
4 Conclusion
A sustainable and environmentally friendly methodology has been devised to fabricate CuO–PP-MAH nanocomposites. This innovative process eliminates toxic solvents and employs an in situ melt mixing technique to deposit copper nanoparticles onto a polymer substrate. This approach sets our research apart from previous studies in this field. The resulting material was comprehensively characterized using techniques including FTIR, SEM, EDX, and TEM, confirming the nanocomposite's superior attributes, notably the well-dispersed and firmly attached CuO nanoparticles on the MAH-grafted PP matrix. Following the optimization of critical experimental parameters, the nanocomposite was employed to treat tannery wastewater in an industrial context. Remarkable outcomes were achieved, with a maximum reduction of 77.2% for BOD and 78.47% for COD after an 80 minute treatment period. Even more noteworthy is the nanocomposite's sustained performance, maintaining over 70% reductions in BOD and COD through six regeneration cycles. These results underscore the potential of CuO–PP-MAH as a stable, high-surface-area, highly efficient, and regenerative catalytic nanocomposite for significantly mitigating BOD and COD in tannery wastewater treatment.
Conflicts of interest
There are no conflicts to declare.
References
-
N. Sivaram and D. Barik, in Energy from toxic organic waste for heat and power generation, Elsevier, 2019, pp. 55–67 Search PubMed.
-
H. Sawalha, M. Al-Jabari, A. Elhamouz, A. Abusafa and E. R. Rene, in Waste biorefinery, Elsevier, 2020, pp. 679–705 Search PubMed.
- S. Dixit, A. Yadav, P. D. Dwivedi and M. Das, J. Cleaner Prod., 2015, 87, 39–49 CrossRef CAS.
-
M. Hutton and M. Shafahi, Energy Sustainability, 59094, V001T10A002, 2019 Search PubMed.
-
U. Mahapatra, A. K. Manna and A. Chatterjee, Removal of Refractory Pollutants from Wastewater Treatment Plants, 2021, pp. 249–266 Search PubMed.
- X. Liu, Y. Wang, X. Wang, T. Han, W. Wang and H. Jiang, Green Chem., 2022, 24, 2179–2192 RSC.
- N. A. Urbina-Suarez, F. Machuca-Martínez and A. F. Barajas-Solano, Molecules, 2021, 26, 3222 CrossRef CAS PubMed.
-
P. P. Singh, in New polymer nanocomposites for environmental remediation, Elsevier, 2018, pp. 223–241 Search PubMed.
- L. Tamayo, M. Azócar, M. Kogan, A. Riveros and M. Páez, Mater. Sci. Eng., C, 2016, 69, 1391–1409 CrossRef CAS PubMed.
- R. Mirsafaei, M. M. Heravi, T. Hosseinnejad and S. Ahmadi, Appl. Organomet. Chem., 2016, 30, 823–830 CrossRef CAS.
- S. E.-D. Hassan, A. Fouda, A. A. Radwan, S. S. Salem, M. G. Barghoth, M. A. Awad, A. M. Abdo and M. S. El-Gamal, JBIC, J. Biol. Inorg. Chem., 2019, 24, 377–393 CrossRef CAS PubMed.
- M. Du, Y. Du, Y. Feng, K. Yang, X. Lv, N. Jiang and Y. Liu, Carbohydr. Polym., 2018, 195, 393–400 CrossRef CAS PubMed.
- A. M. Atta, S. A. Al-Hussain, H. A. Al-Lohedan, A. O. Ezzat, A. M. Tawfeek and T. Al-Otabi, Polym. Int., 2018, 67, 471–480 CrossRef CAS.
- H. Palza, S. Gutiérrez, K. Delgado, O. Salazar, V. Fuenzalida, J. I. Avila, G. Figueroa and R. Quijada, Macromol. Rapid Commun., 2010, 31, 563–567 CrossRef CAS PubMed.
- K. Delgado, R. Quijada, R. Palma and H. Palza, Lett. Appl. Microbiol., 2011, 53, 50–54 CrossRef CAS PubMed.
- N. Gowriboy, R. Kalaivizhi and S. Sivasankari, Polym. Sci., Ser. B, 2021, 63, 322–331 CrossRef CAS.
- X. Liu, Y. Cheng, X. Li and J. Dong, Appl. Surf. Sci., 2018, 439, 784–791 CrossRef CAS.
- M. F. Zayed, W. H. Eisa, M. H. Abd ElHameed and A. M. Abou Zeid, J. Alloys Compd., 2020, 835, 155306 CrossRef CAS.
- M. S. A. Darwish, M. H. Mostafa and L. M. Al-Harbi, Int. J. Mol. Sci., 2022, 23, 1023 CrossRef CAS PubMed.
- S. Shankar, X. Teng and J.-W. Rhim, Carbohydr. Polym., 2014, 114, 484–492 CrossRef CAS PubMed.
- M. Yadollahi, I. Gholamali, H. Namazi and M. Aghazadeh, Int. J. Biol. Macromol., 2015, 73, 109–114 CrossRef CAS PubMed.
- A. Manikandan and M. Sathiyabama, J. Nanomed. Nanotechnol., 2015, 6, 1 Search PubMed.
- G. Das, R. D. Kalita, P. Gogoi, A. K. Buragohain and N. Karak, Appl. Clay Sci., 2014, 90, 18–26 CrossRef CAS.
- Z. Komeily-Nia, M. Montazer and M. Latifi, Colloids Surf., A, 2013, 439, 167–175 CrossRef CAS.
- U. Bogdanovic, V. Vodnik, M. Mitric, S. Dimitrijevic, S. D. Skapin, V. Zunic, M. Budimir and M. Stoiljkovic, ACS Appl. Mater. Interfaces, 2015, 7, 1955–1966 CrossRef CAS PubMed.
- S. Pourbeyram and S. Mohammadi, J. Non-Cryst. Solids, 2014, 402, 58–63 CrossRef CAS.
- T. Zhong, G. S. Oporto, J. Jaczynski and C. Jiang, BioMed Res. Int., 2015, 2015, 456834 Search PubMed.
- A. Taheri Kal-Kashvandi, M. M. Heravi, S. Ahmadi and T. Hosseinnejad, J. Inorg. Organomet. Polym. Mater., 2018, 28, 1457–1467 CrossRef CAS.
- R. Mirsafaei, M. M. Heravi, S. Ahmadi, M. H. Moslemin and T. Hosseinnejad, J. Mol. Catal. A: Chem., 2015, 402, 100–108 CrossRef CAS.
- N. Pourmohammad, M. M. Heravi, S. Ahmadi and T. Hosseinnejad, Appl. Organomet. Chem., 2019, 33, e4967 CrossRef.
- E. Hashemi, Y. S. Beheshtiha, S. Ahmadi and M. M. Heravi, Transition Met. Chem., 2014, 39, 593–601 CrossRef CAS.
- R. Devi, V. Singh and A. Kumar, Bioresour. Technol., 2008, 99, 1853–1860 CrossRef CAS PubMed.
- N. Baig and T. A. Saleh, Glob. Chall., 2019, 3, 1800115 CrossRef PubMed.
- X. Gao, Y. Zhang, Y. Dai and F. Fu, J. Solid State Chem., 2016, 239, 265–273 CrossRef CAS.
- A. A. Oladipo and M. Gazi, Toxicol. Environ. Chem., 2016, 98, 189–203 CrossRef CAS.
- A. A. Oladipo, M. Gazi and E. Yilmaz, Chem. Eng. Res. Des., 2015, 104, 264–279 CrossRef CAS.
|
This journal is © The Royal Society of Chemistry 2024 |
Click here to see how this site uses Cookies. View our privacy policy here.