DOI:
10.1039/D4GC04768K
(Tutorial Review)
Green Chem., 2024,
26, 11832-11859
Advances in catalytic chemical recycling of synthetic textiles
Received
23rd September 2024
, Accepted 23rd October 2024
First published on 1st November 2024
Abstract
Synthetic fibres cover most of the textile market, but their value chain is almost entirely linear. Common raw materials are non-renewable and oil-derived while requiring large amounts of (toxic) chemicals and energy for their processing into final products. In addition, synthetic textiles are usually non-biodegradable polymers; therefore, sustainable approaches for their depolymerisation into reusable monomers have not been implemented yet. As a result, most post-consumer synthetic textile waste ends up being landfilled, dispersed in the environment or incinerated, thus contributing significantly to global pollution. A possible solution to this issue is the design and use of advanced catalysts for their chemical recycling. This manuscript reviews the most significant approaches that appeared in the literature in the time span of 2015–2024, covering the selective depolymerisation process of synthetic waste textile to added-value reusable monomers using chemical catalysts. Unselective processes, for example, to produce fuel mixtures, biocatalytic methods and depolymerisation of polyolefins are not covered. The general aspects of the catalytic depolymerisation of synthetic polymers are briefly discussed, and the catalytic chemical recycling of synthetic textiles is detailed by the polymer type. While contributing to the overall achievement of the sustainable development goals, chemical recycling of synthetic textile waste may represent a useful strategy toward the circularity of the textile sector, which is almost unexplored.
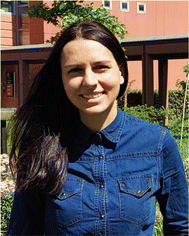 Carmen Moreno-Marrodán | Carmen Moreno-Marrodán studied Chemistry at the University of La Rioja, Spain. In 2008, she won a Leonardo da Vinci European Programme Fellowship in the chemical industry in Cork, Ireland. In 2009, she won a Marie Sklodowska Curie Fellowship and joined the ITN NanoHOST at ICCOM-CNR in Florence, Italy. In 2013, she received her PhD in Chemistry from the University of Florence and is currently a permanent researcher at the Italian National Research Council (ICCOM) in Florence. Her research interests focus on the chemical recycling of plastic waste and biomass valorisation through the development of heterogeneous catalysis and flow technologies. |
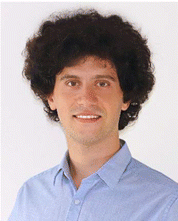 Francesco Brandi | Francesco Brandi studied Chemistry at the University of Florence. He obtained his PhD in 2022 from the Max Planck Institute of Colloids and Interfaces under the supervision of Prof. M. Antonietti and Dr M. Al-Naji. His PhD focused on continuous flow valorisation of lignocellulosic biomass over heterogeneous catalysts. Then, he joined Prof. B.F. Sels’ group in KU Leuven as a postdoctoral fellow working on the catalytic downstream of lignin-derived molecules. Currently, he is a fixed-term researcher at CNR-ICCOM, where his research focuses on the catalytic depolymerization of waste streams of plastic. |
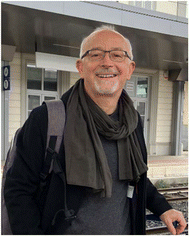 Pierluigi Barbaro | Pierluigi Barbaro is Research Director at the Istituto di Chimica dei Composti Organo Metallici, CNR, Firenze. He obtained his PhD in chemistry from the University of Firenze. He was a one-year post-doctorate researcher at ETH Zurich and two-year post-doctorate researcher at the University of Firenze. He is a member of the Network of Excellence IDECAT and coordinator of the Initial Training Network NANO-HOST (EC VII° FP) and a member of the Board of Directors of the European Research Institute of Catalysis. He is the coordinator of two European Projects, two National Projects and eleven research contracts. Being the author of >100 ISI research papers, his research activities are in the field of sustainable chemistry, catalysis, biomass valorisation and chemical recycling. |
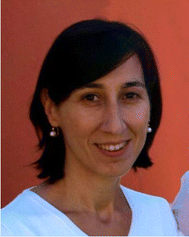 Francesca Liguori | Francesca Liguori got her degree in Chemistry in 1999 and PhD in Chemistry in 2005 from the University of Florence. After a post-doctoral fellowship at ISMAC-CNR, she was a Grant-holder at ICCOM-CNR. Since November 2011, she has been a permanent researcher at ICCOM-CNR. She obtained the National Scientific qualification as Associate Professor in “Industrial Chemistry”, “Fundaments of Chemical Science and Inorganic Systems” and in “Organic Chemistry” (2018). She is an investigator in several Industrial and European Projects and Research Contracts, co-editor of 1 Book with ISBN, and co-author of 38 articles in ISI journals, and she has 4 patents. Research interests: heterogeneous catalysis, green chemistry and sustainable processes. |
1. Introduction
Synthetic textiles are widespread in our everyday life. They are present in clothes, shoes, home furnishings (carpets, curtains, couches), accessories (towels, cushions), safetywear, workwear and sportswear. They are also present in technical equipment and in the seats of cars, trains and aircraft. As opposed to textiles from natural fibres, which are derived from living organisms (animals, plants), synthetic textiles are made of artificial organic polymers manufactured by chemical (co)polymerisation processes, mostly using non-renewable, fossil-sourced monomers. Common raw materials are crude oil, natural gas, and aromatic hydrocarbons, which are processed into olefins, glycols, acids and nitrile intermediates.1 Other man-made fibres exist, for instance, those obtained by the chemical treatment of naturally occurring polymers (e.g. cellulose) and inorganic materials, however, with more limited use. The classification and nomenclature of man-made fibres are available from The International Bureau for Standardisation of Man-made Fibres2 and schematically reported in Fig. 1. The use of (generic) textile fibre names and related labelling is defined by the EU Regulation 1007/201.3,4 Classification of synthetic polymers is usually based on the chain linkage, either polyesters, polyamides, polyurethanes, acrylics or polyolefins, which are the most popular ones (Table 1).
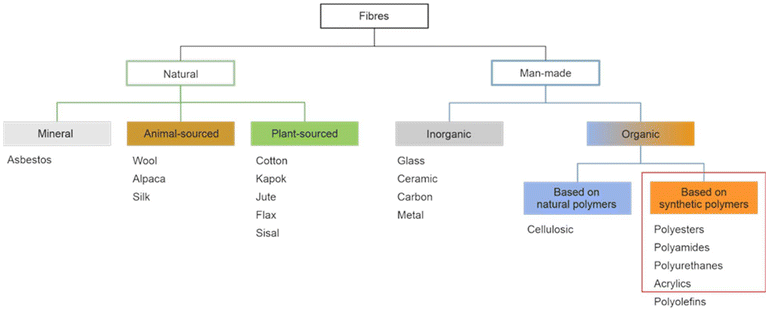 |
| Fig. 1 Possible classification of main fibre types with representative examples. Adapted from ref. 4. Fibres covered by the present review are circled in red. | |
Table 1 Classification of synthetic fibres based on the polymer chain linkage, with sketches and representative examples
Polymer |
Polyesters |
Polyamides |
Polyurethanes |
Acrylics |
Polyolefin |
Abbreviations: PET, poly(ethylene terephthalate); PBT, poly(butylene terephthalate); PTT, poly(trimethylene terephthalate); nylon 6, polycaprolactam; nylon 6.6, poly(hexamethylene adipamide); EL, elastane; PAN, polyacrylonitrile; MAC, modacrylic; PE, polyethylene; PP, polypropylene.
|
Linkage |
|
|
|
|
|
Examplesa |
PET |
Nylon 6 |
EL |
PAN |
PE |
PBT |
Nylon 6,6 |
MAC |
PP |
PTT |
Synthetic fibres are relatively inexpensive and versatile. Compared to natural fibres, they have significantly lower prices (Fig. 2)5 and environmental costs due to their manufacturing process (Fig. 3), whereby cotton poses severe concerns in terms of land and water consumption. Synthetic fibres are provided with specific properties, including strength, resistance to shrinking, elasticity and quick drying, which allow the production of a variety of durable fabrics. The large market potential associated with it has resulted in the so-called “fast-fashion” business model, i.e. the “cheap and mass manufacturing, frequent consumption and use of short-lived garments of clothes replicating high-fashion design”.6 Thus, clothes made of synthetic textiles have become quick consumer goods, which are rapidly produced as the demand is growing.
 |
| Fig. 2 Price trends of representative natural and synthetic fibres: cotton, polyester, nylon (polyamide) and wool. Data from ref. 5. | |
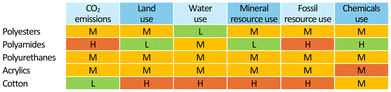 |
| Fig. 3 Schematic comparison of the environmental impacts of the manufacturing of identical amounts of selected fabrics: H, high; M, moderate; L, low. Based on estimates from ref. 4. | |
All of the above justifies the current fibre market as being dominated by synthetic materials. It is estimated that the global fibre production was around 109 million tonnes in 2020, with a 62% share of synthetic ones well above that of plant-sourced (polyesters 57 Mton, polyamides 5 Mton, cotton 26 Mton), as represented in Fig. 4.7,8 The manufacturing of synthetic fibres steadily increased over the last forty years. It surpassed that of cotton in late 1990s, with an average annual growth rate of around 7% during the period 2009–2019 (cotton 1.5%), which is expected to increase further to ca. 81 million tonnes in 2025, as shown in Fig. 5.
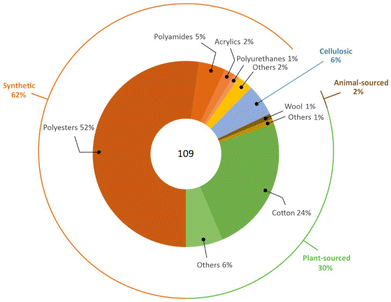 |
| Fig. 4 Global production of textile fibres in 2020 (million tonnes). Data from ref. 7 and 8. | |
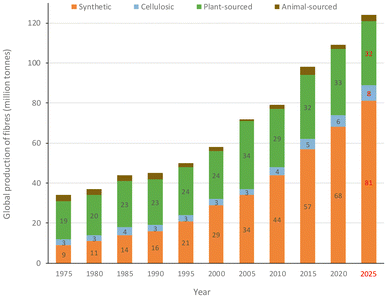 |
| Fig. 5 Global fibres production in the period 1975–2020. Data from ref. 7 and 8. | |
Unfortunately, besides their unquestionable benefits, synthetic fibres also have drawbacks. Unlike natural fibres and analogously to other artificial polymers (i.e. plastics), most synthetic fibres are not biodegradable,9 meant as “susceptible to lower their molar masses by an enzymatic process resulting from the action of cells”.10 Hence, they considerably contribute to the amount of domestic and industrial waste that may accumulate in the environment if not processed. With around 300 million tonnes per year, plastics are a major portion of the non-biodegradable waste globally generated,11 where synthetic textiles provide one of the highest shares per industrial sector (ca. 14%, Fig. 6).12,13 Most synthetic textiles produced (ca. 60 Mton) ends up being trashed (ca. 40 Mton), which represents an unexploited resource potentially reusable in production streams. The amount and composition of textile waste may significantly vary with source and location. For instance, around 13% (w/w) of the total municipal solid waste in the USA in 2017 were plastic materials,14 while plastics represented ca. 10% (w/w) of the separate collection of municipal solid waste in Italy in 2021.15 Batch-automated sorting tests of post-consumer textile waste collected from the Greater Copenhagen area in 2021 revealed the amount of synthetic fibres to be at least 35% (w/w) in both wearable and non-wearable materials,16 as shown in Fig. 7.
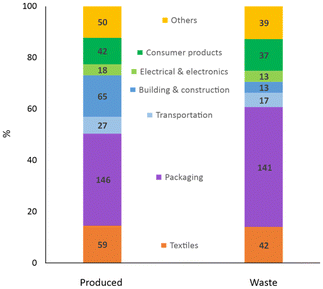 |
| Fig. 6 Global primary plastics production (left) and waste generation (right) in million tonnes per industrial use sector. Data of 2015 from ref. 13. | |
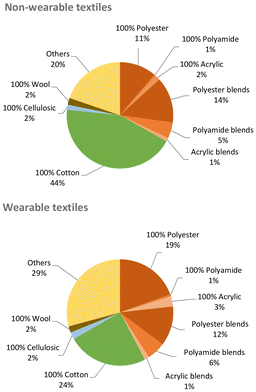 |
| Fig. 7 Material composition of non-wearable (top) and wearable (bottom) textile waste collected from the Greater Copenhagen area in 2021. Data from ref. 16. | |
Despite the remarkable CO2 emissions, use of energy, resources and chemicals associated with textile production (see Fig. 3),4,6 only a minor portion of the textile waste is recovered for reuse or recycling.17,18 It has been estimated that most post-consumer clothing fibres end up being dispersed in the habitat, landfilled or incinerated (overall ca. 88% w/w), whereas a modest 12% is reused in similar and lower-value goods or recycled into substantially different applications after mechanical or chemical treatment,19 as summarised in Fig. 8.20 Downcycling of waste clothes to insulation materials, mattress stuffing or cleaning cloths is around 11%, whilst ca. 1% are reused alike. Only a smaller portion of the recovered wearable textiles currently undergoes selective depolymerisation,21 which is usually referred as chemical recycling (vide infra). Whereas (mechanical) recycling of synthetic polymer waste in general (non-fibre plastic, e.g. packaging, bottles) has achieved technological maturity and significant volumes, to date, recycling of synthetic textiles shows comparably lower share and size. According to a study by Plastics Europe, recycling of the EU post-consumer houseware, leisure and sports plastic goods is around 7% of the amount produced (36% landfilled, 57% incinerated), whereas plastic packaging materials are recycled by 46%.22 The reason for this shortfall is attributable to a combination of factors, which include23,24
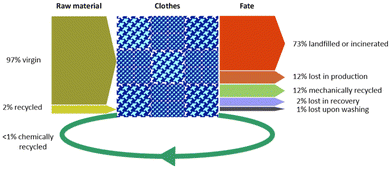 |
| Fig. 8 Global raw materials source and fate for clothes in 2015. Data from ref. 20. | |
• Waste textiles often consist of composite or mixed, hardly separable materials made up of several additives and dyes,
• Waste clothes may contain trims, hard parts and fasteners (e.g. buttons, zippers),
• Sorting technologies are inadequately developed,
• Chemical recycling methods for synthetic polymers are still in their infancy and mostly operating at the lab or pilot scale,
• Focused policies and regulations on textile recycling are lacking,
• Public awareness and motivation are insufficient,
• Collection options for textile waste are unsatisfactory.
The above considerations partly explain why a circular economy for synthetic textiles has not yet been developed, whereby textile recycling facilities are basically limited to cotton. Particularly, separate collection and sorting, which is usually performed through a sequence of automated infrared spectroscopy and X-ray fluorescence steps,25,26 is deemed crucial, as it is estimated they may provide up to a 13-fold increase in waste plastic recycling rates.22 As a consequence, the synthetic textile industry ranks second in the contribution to global pollution.27 Synthetic fibres in apparel have been identified as the major factor responsible for microplastic contamination of oceans28,29 simply as a result of cloth washings.30
To address these challenges, focused strategies and policies for textile recycling have been released both at the European and National levels.31,32 The Circular Economy Action Plan, as a part of the European Green Deal, identifies plastics and textiles as priority fields of intervention.33 The EU Strategy for Sustainable and Circular Textiles,34 and other specific measures for plastic recycling,35 have been launched in response to the EC Waste Framework Directive, which declares that the Member States shall set up separate collections for textiles by 1 January 2025.36,37 The European Environmental Agency in 2019
38 and the Organisation for Economic Co-operation and Development (OECD) in 2020
39 have indicated that recycling synthetic fibres is key to achieving a viable circular system for textiles. Textile Recycling Hubs have been proposed both in Europe40 and Italy,41 the latter as a part of the National Recovery and Resilience Plan funded by the Next Generation EU programme,42 aimed at strengthening the recovery, mechanical and chemical recycling of textiles. Both the German Federal Ministry for Economic Cooperation and Development43 and the Nordic Region Cooperation44 have proposed their own agendas for textile fibre recycling. The European Clothing Action Plan project,45 funded under the EU LIFE scheme, aims to drive fashion and textile sectors toward circularity, focusing, inter alia, on diverting clothing waste from landfills and incineration through resource-efficient design and recycling. It was highlighted that, besides targeting the minimisation of environmental impact and depletion of natural resources, the transition toward a circular economy model for synthetic textiles represents a significant opportunity in terms of new jobs and manufacturing.46,47
The next section summarises the main strategies in use for recycling synthetic textiles with a focus on selective depolymerisations using chemo-catalytic methods. A number of reviews have been previously published on textile recycling, dealing with natural fibres,48,49 general aspects of recycling techniques,50,51 biocatalytic methods52 engineering,53,54 or economic issues.55,56
2. General concepts of catalytic chemical recycling of synthetic textiles
Various strategies are in place for the recycling of synthetic polymers, including textiles. A generally accepted classification includes zero-order recycling (i.e. reuse), mechanical recycling, chemical recycling, and energy recovery (i.e. combustion).57,58 Mechanical recycling refers to those methods in which the polymeric structure of the material is not modified, while changing the appearance and the use, which is usually achieved by grinding, melting and assembling of new parts and products, possibly using additives or blending with fresh polymers.59,60 Chemical recycling is less unambiguously defined, whereby the lack of a clear nomenclature and the use of very broad terms may lead to occasional inconsistencies,61,62 and to a misunderstanding of the role of chemical recycling in a circular economy perspective.63,64 Among the various definitions proposed, the one we believe is the most accurate and representative of the circularity concept is that provided by Plastics Europe: “Chemical recycling converts, e.g. polymeric waste by changing its chemical structure to produce substances that are used as products or as raw materials for the manufacturing of products. Products exclude those used as fuels or means to generate energy”.22 From this definition, it is clear that all those unselective, thermal conversion processes (300–1000 °C), leading to small molecules or energy vectors (CO, CO2, CH4, H2), light hydrocarbons, diesel oil or fuel mixtures, are not strictly considered as “chemical recycling”.65,66 These processes include pyrolysis,67,68 catalytic (hydro)cracking69,70 and gasification.71 By contrast, chemolysis techniques, which use chemical reagents to achieve selective depolymerisation, allow obtaining reprocessable monomers, building blocks or finished chemicals, thus providing valuable products for the process industry and ultimately converting plastic waste into useful materials.72,73 These processes are usually performed using a solvent (i.e. hydrolysis, alcoholysis, glycolysis, aminolysis),74,75 or dihydrogen (i.e. hydrogenolysis),76 as chain linkage cleaving agents. A variety of products, including alcohols, acids, amines and esters can be obtained, depending on the starting polymer and the cleaving agent used. Chemolytic processes may benefit from the use of a catalyst, as it will be illustrated in the following paragraphs. Other techniques are sometimes referred as “chemical” recycling, though they are not. These include dissolution/precipitation, where a solvent is used to extract and purify a synthetic organic polymer from contaminants or other materials.77,78
Chemical recycling is to be considered complementary to mechanical recycling: not all synthetic polymer waste can be mechanically recycled and mechanical recycling cannot be reiterated indefinitely because of the gradual quality loss of the recycled material due to oxidation, hydrolysis or mechanical degradation.79,80 Chemical recycling via chemolysis allows the treatment of difficult-to-recycle plastic waste and those synthetic polymers that are not recyclable otherwise.81 By converting a synthetic polymer into chemicals, chemical recycling may enable a true circular economy for plastics, where plastic wastes represent secondary raw materials, from which myriads of products can be re-manufactured, including solvents, (pharma)building blocks, dyes, additives and monomers, thus to replace the virgin fossil-based ones, as sketched in Fig. 9.82 For this reason, the term “plastic refinery” has been proposed to identify an alternative facility to conventional petrol-based plants.83 Noteworthy, “closed-loop” catalytic systems have also been developed, whereby easily depolymerisable polymers can be efficiently re-polymerised under mild conditions.84,85 Thus, chemical recycling of synthetic polymers is likely one of the clearest application examples of the circular chemistry concept.86 Besides the significant benefits in terms of the reduction of landfills, incineration and consumption of non-renewable sources, chemical recycling of synthetic textiles may significantly contribute to the reduction of CO2 emissions with respect to the production of virgin materials.87,88 In the case of polyesters, it has been estimated that alcoholysis provides a 60–70% greenhouse gas (GHG) emissions saving, compared to the conventional manufacturing sequence.89 Consequently, chemical recycling technologies are considered indispensable in view of a transition to a climate-neutral economy. European plastics manufacturers plan to invest 7.2 billion euros in chemical recycling by 2030, whilst the production of recycled plastics via chemical recycling is estimated to increase from 0.1 million tonnes in 2020 to 3.4 million tonnes in 2030.22
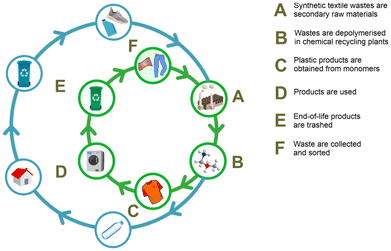 |
| Fig. 9 Circular economy model based on molecular recycling of synthetic textile waste. A variety of products can be manufactured, including virgin textiles (green loop) or packaging materials (blue loop). | |
However, current chemical recycling via chemolysis suffers from several limitations, particularly concerning synthetic textiles. One reason for this is that the related technologies are poorly developed, and the research in the field is relatively young.90 To date, most chemolytic depolymerisation processes rely on organic (noxious) solvents, harsh reaction conditions, high pressures of gas, need for soluble promoters, corrosion issues, limited selectivity, and generation of a considerable amount of (salt) waste, which ultimately result in costly downstream purifications and high energy inputs.91,92 Applicability to specific waste streams may also be an issue.93 Overall, chemolytic methods have to face economic and environmental sustainability indicators, whereby technological and financial viability, integration with the local market, and impact on human health and habitat are key parameters to be taken into account.94 So far, chemical recycling is rarely competitive with mechanical recycling, which is more developed and hence favoured.95,96 Advancements in chemolysis processes are mostly expected in relation to improved selectivity and more friendly reaction conditions.
Understandably, depolymerisation of plastics is hampered by the recalcitrance to chain scission due to thermodynamic and kinetic barriers, which depend on the polymer composition and structure.97 To achieve efficient and selective depolymerisation at reasonable reaction temperatures (e.g. ≤ceiling temperature98), the polymer substrate should originate from low exergonic polymerisation reactions (ΔGpolymerisation ≈ 0).99,100 For instance, this is not the case for polyolefins because of the inherent strength of the C–C bonds. Therefore, polyolefins usually depolymerise with poor selectivity under harsh conditions.101,102 Moreover, even if thermodynamic requirements are favourable, high activation energies may slow down the depolymerisation kinetics, thus resulting in long reaction times for complete depolymerisation to occur at low temperatures. To circumvent this limitation, a possible solution is using a catalyst.103,104 The clear advantage of catalysis is decreasing the activation barrier, thereby minimizing energy inputs, while maximising reaction rates, monomer yields and selectivity.105,106 Representative examples may illustrate the macroscopic benefits. Compared to the catalyst-free process, the hydrolysis reaction of polylactic acid (PLA) has been reported to occur in 100% yield at a 30 °C lower temperature in the same reaction time using ZnO catalyst. In the case of PET, analogous results were obtained at a reaction temperature that is 60 °C lower.107 In other words, under the same reaction temperature (i.e. 130 and 180 °C for PLA and PET, respectively), the monomer yield was around eight times higher over the ZnO catalyst compared to the uncatalysed reactions. In another example, the monomer yield was around four times higher for the glycolysis reaction of PET at 190 °C after 1 hour using titanium(IV) n-butoxide as the catalyst, with respect to the uncatalysed reaction at 220 °C.108 In terms of the activation energy, the hydrolytic depolymerisation of nylon 6 to ε-caprolactam, in the temperature range 553–603 K, was ca. 9.26 kJ mol−1 lower using 3% phosphotungstic heteropoly acid catalyst, compared to the catalyst-free process.109
Still, problems with chemo-catalytic recycling arise from the use of homogeneous catalysts,110 strong acid–base soluble activators,111 poor efficiency of biological catalysts,112,113 and the need for toxic promoters or solvents.114,115 Heterogeneous catalysts are preferred at the industrial level due to the ease of separation, recovery, reuse and integration into existing reactor equipment, including semi-batch and continuous flow set-ups, which may result in improved process intensification, long-term productivity, product purity and reduction of downstream processing.116,117 Limitations may arise in terms of catalyst activity and durability, the need for catalyst regeneration and leaching of metal species.118 Particularly for polymeric substrates, further drawbacks originate from their insolubility in common solvents, which results in restricted accessibility of the bulk polymer to a solid catalyst interface, where reactive interactions occur.119 Hence, high reaction temperatures and stirring rates may be needed using heterogeneous catalysts in order to enhance the diffusion rate of reactants within the polymer and the catalyst.120,121 Therefore, chemolytic depolymerisations via heterogeneous catalysis usually necessitate the design of more sophisticated systems, for instance, involving materials having large surface areas, porosities and stability.122,123 On the other hand, for the above-mentioned reasons, homogeneous catalysts for depolymerisation are usually significantly more active compared to heterogeneous, although high catalyst loadings (e.g. alkali hydroxides, ZnCl2), sophisticated metal ligands (e.g. for pincer molecular complexes), toxic or corrosive species (e.g. Zn salts, H2SO4) may be required.124,125 In addition, issues related to catalyst/product separation, metal contamination, generation of considerable amounts of salt waste streams and non-reusability of the catalyst may contribute to increasing the process costs, thus making the system economically unattractive. Irrespective of the catalyst, whether homogeneous or heterogeneous, the mechanism of solvolytic depolymerisations usually involves the acidic/basic activation of the functional group chain linkages (e.g. ester) by the appropriate catalytically active species. This is, for instance, the case of the hydrolysis or glycolysis reaction of polyesters mediated by conventional, soluble Zn2+ salts, where the Zn ions act as Lewis acid centres toward the carbonyl ester bonds, which then undergo a nucleophilic attack by the solvent molecules, leading to chain scission.126,127 The mechanism of catalytic hydrogenative depolymerisation is less investigated, though it usually involves ruthenium centers due to the high affinity for C
O bonds and is achieved using soluble molecular complexes, where the cleavage of the chain linkage occurs in a concerted manner by a heterolytic route.128,129
In the case of synthetic textiles, the reported strategies for chemical recycling are analogous to those used for other plastic materials. However, additional hurdles come from the complexity of textile goods, particularly in relation to macroscopic aspects (e.g. size, mechanical resistance, blending with different fibre types, presence of additives, contaminants and hard parts),31 as outlined in section 1. Therefore, besides disassembling, sorting and selection, pre-treatments may be required to achieve effective depolymerisation. Typical is the case of dissolution in organic solvents or contact with acids. Pre-treatment methods are polymer-dependent; hence, they will be described case-by-case in the next section, e.g. polyurethanes in section 3.3.
The next sections review the most significant advancements recently achieved in the catalytic chemical recycling of synthetic textiles, broken down by polymer type. No polyolefins are considered due to the fuel product mixtures usually obtained.
3. Applications of catalytic chemical recycling of synthetic textiles
3.1. Polyesters
Polyesters, particularly polyethylene terephthalate (PET), are the most common synthetic yarns. PET is also widely used in the food and beverage packaging industry. The global production of PET is around 72 Mt per year (2019), and 65% is used in fabrics for clothes, sportswear and home furnishings.130,131 In addition to its ubiquity, PET is hardly biodegradable,132,133 which justifies PET being among the polymers most investigated for chemical recycling. Several reviews are available in the literature describing the strategies for PET depolymerisation in general.134,135 Most methods rely on the use of soluble catalysts (e.g. NaOH, ZnCl2 or ionic liquids), either for hydrolysis, alcoholysis and glycolysis reactions under harsh conditions, or for hydrogenolysis (e.g. pincer Ru complexes), the former with drawbacks in terms of energy inputs, corrosion, downstream purification, and management of salt waste.136 In a few instances, the use of insoluble catalysts has been described (e.g. ZnO, hydrotalcite).137,138 Solvolysis of polyesters may take advantage of strong Brønsted base or Lewis acid catalysts acting as activators of the carbonyl ester bond.139 Two-step catalytic solvolysis-hydrogenation reactions in cascade have also been reported.140,141
PET fibres are made of ethylene glycol and valued petroleum-derived terephthalic acid (TPA),142,143 but they are often blended with other natural materials, e.g. cotton, to obtain textiles for use in shirts and blouses. Common trade names include Trevira, Diolen, Dacron, and Coolmax. An overview has been published on the recycling (mechanical, thermomechanical, thermochemical, chemical, and biochemical) of PET from cellulose blended fabrics.144 Several synthetic additives are used in the manufacturing of PET textiles, mostly as finishing to provide fire retardants, antistatic, antimicrobial, water or stain-repelling properties, or as colorants. Coatings may contribute up to 5–20% of the weight of the final textile product. Additives may not degrade or be removed easily,145 while having toxic potential, as warned by the European Chemicals Agency (ECHA).146 Recent studies on the recycling of PET-based textiles mainly concern sorting,147 dissolution-separation techniques,148,149 removal of dyes,150,151 and the effect of additives on recycling.152,153 A few reports exist on the catalytic depolymerisation of PET-based textiles, which include glycolysis, hydrolysis and methanolysis reactions (Fig. 10). A summary of recent findings is reported in Table 2.
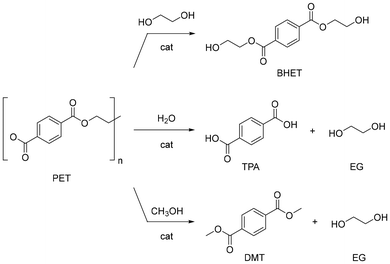 |
| Fig. 10 General scheme of homo- and heterogeneously-catalysed glycolysis (top), hydrolysis (middle) and methanolysis (bottom) reactions of PET. | |
Table 2 Representative literature results for the lab-scale catalytic chemical recycling of PET textilesa
Method |
Catalyst |
Catalyst type |
Reaction conditions |
Pre-treatment |
Product (yield) |
Ref. |
Abbreviations: NP, nanoparticles; C3N4, carbon nitride; MeOH, methanol.
Viscose/PET blend.
|
Glycolysis |
Zn acetate |
Homogeneous |
180 °C, PET : EG = 1 : 5 |
40% NaOH, 100 °C |
BHET (85%) |
155
|
Glycolysis |
Zn acetate |
Homogeneous |
198 °C, PET : EG = 1 : 2 |
Water/acetone |
BHET (80%) |
156
|
Glycolysis |
Mg–Al double oxides |
Heterogeneous |
240 °C, PET : EG = 1 : 5 |
n.a. |
BHET (80%) |
157
|
Glycolysis |
Ag-doped ZnO NP |
Heterogeneous |
200 °C, PET : EG = 1 : 44 |
Water |
BHET (90%) |
158
|
Glycolysis |
In-doped ZnO/C3N4 |
Heterogeneous |
200 °C, PET : EG = 1 : 22 |
200 °C |
BHET (90%) |
159
|
Hydrolysis |
None |
|
250 °C, 40 bar, PET : H2O = 1 : 10 |
n.a. |
TPA (92%) |
160
|
Hydrolysisb |
NaOH |
Homogeneous |
90 °C, PET : H2O = 1 : 100 |
Water 60 °C |
TPA (99%) |
161
|
Methanolysis |
Triethylamine |
Homogeneous |
200 °C, PET : MeOH = 1 : 12 |
n.a. |
DMT (82%) |
164
|
Glycolysis is usually performed using an excess of ethylene glycol (EG) to yield bis(2-hydroxyethyl)terephthalate (BHET), formally through a (reversible) transesterification reaction (Fig. 10, top). Drawbacks of the method may be the high reaction temperatures (≥190 °C) and the difficulty of purification of BHET. In an earlier paper, the glycolytic depolymerisation of PET fibre waste of 1.44 denier was achieved using 0.3–1% (w/w) sodium sulphate catalyst and 1
:
6 = PET
:
EG ratio at 197 °C. BHET was obtained in 60% yield after 8 h and crystallization from water.154 In a further study, a two-step treatment of post-consumer polyester clothes, based on the addition of 40 wt% alkali solution (1 h, 100 °C), followed by glycolysis with 1% zinc acetate catalyst (PET
:
EG = 1
:
5 (w/w), 180 °C, 8 h), gave BHET in ca. 85% yield, after washing with water to remove cellulose, titania contaminants, EG, sodium and zinc salts.155 Similarly, 80% BHET yield was obtained by the treatment of PET fabric waste with water and acetone, followed by glycolysis using 0.2 wt% zinc acetate catalyst, PET
:
EG = 1
:
2 (w/w), 198 °C, 4 h, and crystallisation.156 More recently, the glycolysis of white and uncoloured post-industrial PET fibre wastes was reported over insoluble Mg–Al double oxide pellet catalyst (diameter 6 mm, height 8 mm, 1.5 wt%) to give BHET in ca. 80% yield after 2 h at 240 °C (PET
:
EG = 1
:
5). The catalyst could be reused three times with no significant decrease in catalytic activity, after which regeneration at 1000 °C was required.157 Other solid catalysts used include 2 mol% Ag-doped ZnO nanoparticles for the depolymerisation of red, blue, and green PET textile waste threads under microwave irradiation. Around 90% BHET yield was obtained at full PET conversion after recrystallization (5 wt% catalyst to PET ratio, 300 W, 30 min, 200 °C, PET
:
EG = 1
:
44 w/w).158 Under similar conditions, 10 wt% In-doped ZnO-carbon nitride nanocomposite catalyst gave BHET in 90% yield after extraction with chloroform from the water solution washings.159 The heterogeneous catalyst could be reused with ca. 5% BHET yield loss upon each recycling.
The hydrolytic depolymerisation of PET produces EG and water-insoluble TPA (Fig. 10, middle). Hydrolysis reactions clearly benefit the use of water as a friendly and economic reagent; however, harsh conditions are needed to achieve complete depolymerisation without catalysts. For instance, in the case of textiles, PET fibres with different viscosities and containing titanium dioxide to reduce luster were depolymerised to TPA in 92 wt% yield under 250 °C, 40 bar pressure, PET
:
H2O ratio 1
:
10, and hydrolysis time of 30 min after reaching the steady-state conditions.160 By contrast, alkali-catalysed hydrolysis of viscose/PET fabrics (70/30) (5 wt% NaOH, 24 h) allowed producing pure TPA in ca. 99% yield under 90 °C reaction temperature, with concurrent cellulose recovery.161,162 TPA was isolated after filtration of the aqueous reaction mixture and neutralization with H2SO4. After the fabric treatment, the intrinsic viscosity of the recovered cellulose was decreased by up to 35%. An in-depth techno-economic and process upscaling analysis was included, indicating the need to reduce the consumption of (costly) NaOH, increase the hydrolysis rate by adopting appropriate catalysts, and improve the downstream separation and purification technologies from the resulting EG/Na2SO4 stream. Taking advantage of the fact that TPA acts as a linker in metal–organic frameworks (MOF), in a recent work, TPA was extracted by reactive crystallization from mixed-TPA fibres (cotton, dyes) in the form of Ga-TPA MOF (10% NaOH, 200 °C, 200 min, Ga(NO3)3, 210 °C, 5 h).163 Pure TPA was then obtained by decomposition of the MOF by nitric acid treatment.
In a recent paper, the methanolysis reaction of PET fibres to give dimethyl terephthalate (DMT) and EG was described using triethylamine as an organocatalyst (Fig. 10, bottom).164 Running the reaction with an excess of methanol, 7% (v/v) NEt3 and 200 °C resulted in an 82% DMT yield, which was brought to 88% using a 1
:
1 (v
:
v) methanol
:
toluene mixture. No solvolysis took place without a catalyst under the same condition. More than 91% of the initial solvent/catalyst volume was recovered after five depolymerization cycles. Importantly, a life cycle assessment (LCA) analysis showed the process of avoiding the emission of 1.88 kg of CO2 equivalent compared to the conventional DMT manufacturing route. DMT could be crystallized in 56% yield from the methanolysis reaction of dye-free polycotton (50% polyester/cotton).
Generally, the choice of the solvolytic method may be driven by the comparison of environmental, technical and cost factors.165,166 For instance, EG is not warned by the REACH regulation and may be produced from renewable sources; however, its high boiling point may result in difficulties in product separation and in the management of the excesses. By contrast, methanol, although toxic, is a better nucleophile than other alcohols; hence, using methanol often results in faster reaction kinetics and higher depolymerisation yields. Of course, water is the cheapest and safer option; still, shortcomings may arise from the poor solubility of reaction products (e.g. TPA), need for strongly basic conditions (e.g. NaOH) to achieve full depolymerisation, and instability of catalysts in the presence of nascent carboxylic acid generated upon hydrolysis.107 In addition, it must be considered that all products obtained from the glycolysis, hydrolysis and methanolysis reaction of waste PET fabrics (i.e. TPA, BHET, DMT) are usable intermediates for manufacturing the virgin polymer or other plastic materials for diverse applications (polyesters, polyurethanes, epoxy resins),167,168 as well as acrylics, dyes or antibacterial drugs.169,170
Finally, it is worth mentioning that the conversion of unspecified PET-based clothes to a mixture of benzene, toluene and xylene was reported over Ru@Nb2O5 catalyst, with a 46%, 46% and 8% selectivity, respectively, at an overall 81.6% hydrocarbon yield.171 The process conducted using water, a PET
:
catalyst ratio = 1
:
1 (w/w), 280 °C and 16 h, consists of a sequence of tandem hydrolysis, reforming, hydrogenolysis and decarboxylation steps, where the reforming of EG obtained by hydrolysis provides in situ generated H2.
Industrial-scale technologies for the chemical recycling of synthetic textiles are still at an early market stage, whereby a few operate and others are under development.172 Because of their commercial nature, most of the related processes lack significant information concerning the reagents and catalysts (if any) used, energy inputs, nature of manageable streams, including contaminants, and the environmental performance. In the case of PET, the vast majority of recycled material comes from post-consumer bottles (ca. 99%), whereas only a minor amount is due to recycled textile waste or fabric processing residues.173Table 3 summarises the industrial processes claimed for the catalytic chemical recycling of synthetic textiles, broken down by polymer type, wherein at least basic details are available. Additional information on complementary technologies for synthetic textile recycling can be retrieved from the literature.7,92 Ioniqa, a spinoff from the Eindhoven University of Technology, has developed an efficient depolymerisation strategy based on glycolysis at 197 °C accelerated by an ionic liquid metal catalyst, namely bmimFeCl4 (bmim = butylmethylimidazolium).174,175 Notably, linking the catalyst to magnetic particles enables catalyst recovery and reuse. Although the method uses PET bottles as feedstock, it is planned to be performed on PET fibres.176 Jeplan has developed a “clothing-to-clothing” BRING Technology™ in which discarded PET clothing and fibres are converted to BHET by glycolysis, then re-polymerised to PET yarns.177 The depolymerisation step is brought about by heating the input stream with an equivalent weight amount of BHET, followed by glycolysis at 200 °C using EG and sodium methylate as a catalyst.178 The final BHET monomer is isolated after treating the product with activated carbon and ion-exchange resins. Japan-based Teijin Company announced to have developed a depolymerisation method for coloured polyester fibres to give BHET, arguably by glycolysis, using a new, undisclosed catalyst.179 Italian Garbo is implementing a medium-scale production facility of BHET (55–65 ton per day) from PET waste, including fabrics, likely taking advantage of the Zn acetate catalyst.180,181 Similarly, Poseidon Plastics is producing BHET by glycolysis from several forms of waste PET plastic, including textiles and carpets, at the Teesside facility (UK).182 Typical conditions involve the use of a zinc acetate–urea catalyst system (NH2CONH2)nZn(CH3CO2)2, around 190 °C reaction temperature, EG to PET ratio 4. BHET purification follows, which includes recrystallisation from alcohols and decolouration over cation exchange resins.183,184 Axens runs a demonstration plant based on the Rewind® PET glycolysis process for PET fibres.185 No information on catalyst usage is available. As a part of the EU Horizon DEMETO project,186 NextChem completed a demonstration plant in Italy for the depolymerisation of PET from textiles, co-licensed with the Swiss start-up Gr3n, using a microwave-assisted alkaline hydrolysis technology (NaOH, KOH or LiOH catalyst).187,188 US Tyton BioSciences has developed a hydrolysis method to recover TPA from PET waste textiles or PET/cotton blends, using 0.5% (w/v) NaOH at 180 °C to increase the reaction rate.189 TPA is isolated by adjusting the pH to 2–4. EG can be recovered by conventional distillation. Swiss start-up DePoly company operates a low-temperature chemical recycling process for polyester textiles into TPA and EG, hence inferred via hydrolysis.190 No information on catalyst use is provided. Mistra Future Fashion claims the Blend Re:Wind hydrolysis process for polycotton fibres, based on treatment with 10% NaOH, benzyltributylammonium chloride (BTBAC) and H2SO4, in collaboration with the Chalmers University of Technology in Göteborg.191,192 The RevolTex® hydrolysis process has been developed by Rittec, in cooperation with the Braunschweig Technical University, for the depolymerisation of waste polyester textiles into TPA using concentrated NaOH solutions.193 Eastman reported the chemical recycling of polyester plastic waste, including carpets and clothing, via glycolysis or methanolysis using an undisclosed catalyst.194 The latter process was estimated to result in 29% lower greenhouse gas emissions compared to conventional DMT production from fossil sources.195 Loop Industries’ depolymerisation technology converts PET fibre waste into DMT, EG and TPA by treatment with 30–40% (w/w) KOH, methanol and dichloromethane at room temperature, followed by acidification with H2SO4.196,197
Table 3 Industrial processes for the catalytic chemical recycling of synthetic textile streams to reprocessable productsa
Company |
Input material |
Method |
Product |
Catalyst |
Catalyst type |
Ref. |
Selective depolymerisation methods, see definition in section 2. Enzymatic methods and methods leading to fuel products are not covered.
|
Ioniqa |
PET |
Glycolysis |
BHET |
[bmim][FeCl4] |
Heterogeneous |
174
|
Jeplan |
PET |
Glycolysis |
BHET |
Sodium methoxide |
Homogeneous |
177
|
Teijin |
PET |
Glycolysis |
BHET |
n.a. |
|
179
|
Garbo |
PET |
Glycolysis |
BHET |
n.a. |
|
181
|
Poseidon Plastics |
PET |
Glycolysis |
BHET |
Zn acetate–urea |
Homogeneous |
182
|
Axens |
PET |
Glycolysis |
BHET |
n.a. |
|
185
|
NextChem |
PET |
Hydrolysis |
TPA, EG |
Alkali hydroxides |
Homogeneous |
187
|
Tyton BioSciences |
PET and blends |
Hydrolysis |
TPA, EG |
NaOH |
Homogeneous |
189
|
DePoly |
PET |
Hydrolysis |
TPA, EG |
n.a. |
|
190
|
Mistra Future Fashion |
Polycotton |
Hydrolysis |
TPA |
NaOH, BTBAC |
Homogeneous |
191
|
Rittec |
PET |
Hydrolysis |
TPA, EG |
NaOH |
Homogeneous |
193
|
Eastman |
PET |
Methanolysis |
DMT |
n.a. |
|
194
|
Loop Industries |
PET |
Methanolysis |
DMT, TPA, EG |
KOH, NaOH |
Homogeneous |
196
|
Aquafil |
PA and composites |
Hydrolysis |
CPL |
Acid |
Homogeneous |
230
|
Other industrial processes are in place for PET textile waste recycling based on the dissolution/precipitation strategy, thereby not involving depolymerization. For example, Worn Again Technologies has patented a process to convert PET textiles, including cotton blends, into pellets.198,199 Another start-up company, Ambercycle, has developed a technology to purify and separate polyesters from different garments and is planning a demonstration plant to produce a metric ton of recycled material per day.200,201 Recycling polycotton fibres has been described as a treatment with sulfuric acid and water to yield cellulose powder and unreacted PET.202
3.2. Polyamides
Polyamides (PA), also known under the trade name nylons, are the second most common synthetic fibres. PA are largely used for sport- and underwear, hosiery, umbrellas, technical fabrics, ropes and carpets due to their suitable thermal and mechanical properties, including high strength, flexibility, elasticity, toughness and low moisture absorption. It is estimated that textiles account for around 70% of global PA production (2018),203 whereas carpets contribute around 17%.204 Nylons are aliphatic condensation polymers formally derived from organic acids and amines, whereby homo-polymers resulting from amino-acids or lactams (PA n) or from dicarboxylic acids and diamines dyads (PA n,n) exist (n indicates the number of carbon atoms). The PA textiles market is dominated by PA 6 (ca. 55%) and PA 6,6 (ca. 35%) (Fig. 11).205
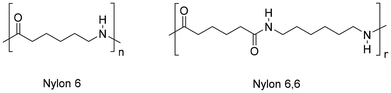 |
| Fig. 11 Structures of nylon 6 and nylon 6,6. | |
Similar to polyesters, depolymerisation of PA via chemical recycling is possible via hydrolysis, alcoholysis, glycolysis, aminolysis and hydrogenolysis reactions.206,207 By contrast, the superior resistance of PA results in more drastic reaction conditions. At the molecular level, this is attributable to the resonance stabilisation of the amide bond, which hampers the nucleophilic attack by lytic agents.208 In the case of PA 6,6, chemical recycling is further complicated by the strong intermolecular hydrogen bonds, resulting in a semi-crystalline polymer structure with higher tensile strength, melting point and lower solubility in common solvents.209 Most works addressing the depolymerisation of PA6 to monomers relate to the water-assisted conversion to ε-caprolactam (CPL) which, irrespective of the mechanism, is formally achieved through hydrolysis-cyclocondensation steps, usually at high reaction temperatures (240–600 °C), or aided by strong acidic or basic catalysts (H3PO4, H2SO4, HCl, NaOH, H3PW12O40) (Fig. 12, top).210,211 In the case of PA 6,6, the process is limited by repolymerisation of the resulting acid and amine reaction mixture to provide polyamide resins.212 Despite the significant amount of literature related to these systems, few works describe the depolymerisation of actual PA-based textiles, most likely due to the usual blending with other polymers (PET, polyolefins).213 As a consequence, the recycling of nylon textiles is currently confined to dissolution–precipitation214,215 or energy recovery processes via incineration; however, it has serious drawbacks in terms of the emission of greenhouse gases (N2O).216 With the exception of unselective deconstruction processes (e.g. pyrolysis),217 the catalytic depolymerisation studies of nylon-based textiles are briefly reviewed in the following paragraphs.
 |
| Fig. 12 Sketch of cyclodepolymerisation processes of nylon 6 to CPL. Top: conventional water-assisted or solvent-free reaction. Bottom: acetic anhydride fragmentation, followed by trans-acetylation. | |
In an earlier study, the catalyst-free cyclodepolymerisation of nylon 6 carpets was reported in the presence of steam to give CPL in 90% yield, under 1.5 MPa and 340 °C (Fig. 12, top).218,219 More recently, the use of water under sub-critical conditions (i.e. below 374 °C and 22.1 MPa), with no external catalyst added, 300 °C reaction temperature, 60 min and 11
:
1 H2O/nylon 6 mass ratio, resulted in ca. 91% CPL yield and 10 wt% solid residue.220 Nylon 6 waste was pulverised prior to use. A careful analysis of reaction by-products revealed the n-value of oligomers in the liquid phase to range from 0 to 5. Protons generated by water dissociation under the reaction conditions were ascribed to be the catalytically active species in that case. Friendlier reaction conditions were possible by the addition of catalysts. Shukla et al. reported the treatment of nylon 6 fibre waste using a concentrated aqueous solution of HCl (30%) or H2SO4 (15%) as an acid catalyst under reflux temperature, which resulted in low-molecular-weight compounds of various chain lengths and in 93% and 79% aminocaproic acid yield, respectively.221 Nylon 6 processing wastes were also hydrolysed over a series of γ-Al2O3 supported solid acid catalysts and commercial zeolites.222 Depolymerisations were performed under sub-critical conditions at a mass ratio of water/nylon 30
:
1, 345 °C, 30 min and 30 wt% catalyst loading. Zeolite Hβ-25 exhibited higher activity and better recyclability than Al2O3 catalysts. Up to 90% conversion to soluble oligomers and 63% CPL yield was observed over Zeolite Hβ-25. Kinetic studies indicated consecutive oligomerisation and cyclisation steps, showing the catalyst to be effective in accelerating the hydrolysis step, compared to the un-catalysed process. The preferential formation of linear oligomers was attributed to the microporous structure of the zeolite.
Solvent-free processes were also reported for the conversion of nylons to CPL. Around 80% yield, with 99% pure CPL was obtained by contacting coloured waste and scrap PA6 textiles over 4 wt% solid NaOH at a high temperature of 320 °C required to melt NaOH and PA6.223 A number of by-products obtained by decolourization were identified in the vapour phase. An intricate depolymerisation mechanism was postulated involving hydrolysis with adventitious water, decarboxylation and hydrogen transfer steps. Differently, solid catalysts with lower basic strength, and based on γ-Al2O3 supported metal catalysts (Ni, Cu, Fe, Co), required much higher temperatures to achieve cyclodepolymerization.224 Thus, using stockings with diverse compositions (nylons, cotton and elastane) as a feedstock, a modest increase in CPL yield from 54% to 69%, without and with Cu@Al2O3 catalyst, respectively, was obtained at 500 °C reaction temperature. Based on nylon content, the effective CPL yield was 95.3 wt%. Recently, solvent-free processes promoted by homogeneous lanthanide-based catalysts were reported. In the first example, commercially available tris-amido complexes of the general formula Ln(N(TMS)2)3 (Ln = lanthanide) afforded CPL in 90% yield and 95% purity at 240 °C reaction temperature, showing the catalytic activity to be higher for lanthanides with larger ionic radius.225 The process was adaptable to post-consumer nylon 6 and blends (1
:
1 wt) of nylon 6 with PE, PP and PET where the CPL yields were 93%, 91% and 77%, respectively, and the unreacted PE and PP were recovered at the end of the reaction. Kinetic and theoretical investigations suggested a mechanism involving a first deprotonation step of the nylon NH bond, followed by a chain-end backbiting step in which CPL units are sequentially removed from the chain ends. In a second example from the same group, the use of metallocene-lanthanide complex catalysts resulted in the formation of CPL in 81% yield, with a high TOF of 810 h−1, under 240 °C and 0.2% catalyst loading.226 The catalysts can be reused without significant deactivation. The process required fine grinding and washing of polymers with 1 M KOH solution, careful drying, and the use of an oxygen-free environment under a 10−3 Torr vacuum. Under these conditions, actual feedstock (fishing nets, carpets, yarns, t-shirts, medical gloves) was converted in 65%–99% CPL yield.
Depolymerisation of nylon 6 commodities was also reported using acetic anhydride as a lytic agent and 4-dimethylaminopyridine (DMAP) as an organocatalyst (5% mol) (Fig. 12).227 In a typical reaction, a mixture of N-acetylcaprolactam (ACPL) and acyclic acetylimides by-products were obtained in around 60
:
40 ratio under microwave irradiation at 260 °C. Under these conditions, ACPL was obtained in 20%–78% yield by treatment of nylon 6-based stripes, threads, hammocks, and patches. Free CPL could be obtained by trans-acetylation of ACPL with an equimolar amount of ethanolamine at 80 °C.
In a different approach, nylon 6,6, and the PP mixture thereof, was effectively depolymerised through a transamidation reaction to give a mixture of amide dimers and monomers (Fig. 13).228 A 20% and 69% yield was obtained, respectively (together with a stoichiometric amount of adipamide), by contacting with a ca. 18-fold excess acetamide, under 200 °C, 3 bar NH3 and Nb2O5 catalyst. Nb2O5 is a well-established and water-tolerant solid acid catalyst, which has been used in a variety of applications, including dehydration, esterification, and hydrolysis.229 Herein, a mechanism was proposed where the Lewis acid Nb2O5 activates the amide bond of Nylon, which then undergoes the nucleophilic attack of ammonia.
 |
| Fig. 13 Sketch of transamidation reaction of nylon 6,6 over heterogeneous Nb2O5 catalyst. | |
On the industrial scale, chemical recycling of nylon 6, or composites with glass, PE or polyurethanes from waste carpets and clothing textiles, is operated by Aquafil,230,231via hydrolytic depolymerisation to caprolactam at 200–400 °C, 0.2–20 bar, using a soluble acid catalyst (Econyl process)232,233 (Table 3). Asahi Kasei claimed a chemical recycling process using microwaves to depolymerize polyamide 6,6 from waste airbags and automobile parts into hexamethylenediamine and adipic acid monomers.234
3.3. Polyurethanes
Polyurethanes (PU) are an important class of specialty polymers with a vast array of applications and a global market volume expected to reach 28 Mton in 2025.235 PU refers to all those polymers that contain urethane linkages (–HN–COO–) in their backbone, regardless of the rest of the molecule. Typically, PU is synthesized by condensation of a di-isocyanate with a polyol, either a monomer or a polymer. Consequently, by varying the type of PU precursors, it is possible to tailor the properties of the final material to result in superior performances in terms of elasticity, durability, and insulation.236 PU is classified into two major categories: foams (soft and rigid) and CASE (coatings, adhesives, sealants, elastomers).237 PU elastomers are used in textiles because of their elasticity. The most common PU elastomers are commercialized with the trade name elastane (EL), Spandex or Lycra®, whose global production was 1.24 Mton in 2022.238 EL is composed of at least 85 wt% of segmented polyurethane elastomers and possesses high elasticity, showing elongations up to 100–600% of its original length.239 From a molecular viewpoint, EL is a polyurethane–polyurea block copolymer, resulting from the condensation of 4,4-methylenediisocyanate (MDI) and poly-tetrahydrofuran (polyTHF) as polymeric diol. In addition, EL often contains short diamines, mostly ethylenediamine, used as chain extenders. The latter is commonly obtained from oil, whereas polyols may be bio-sourced. For example, the Lycra company markets a 70 wt% bio-elastane based on corn starch.240 PU is increasingly used in the textile industry because of additional properties. It is worth mentioning that waterborne polyurethane is used as coatings to provide textiles with resistance to abrasion and waterproofing. PU coatings are also used on PET to produce synthetic leather and on PA to reinforce light-weight work wear.241 EL may be used as an additive to enhance the stretchability and shaping behaviour of other textiles, such as cotton. Additionally, the current landscape is progressively enriched with complex yarns containing EL blended fibres. Therefore, garments rarely contain 100% EL yarn; instead, EL ranges between 1 and 10%, but it can reach up to 49%.242 For instance, Alcantara® is an aesthetic and sensor-like leather material for interiors made of PET and PU fibres (ca. 70
:
30).243 Despite the current relatively low market (Fig. 4), EL is quickly diffusing in the textile sector, wherein it is expected to contribute with around 30% of all recovered materials by 2030.244 Unfortunately, when it comes to recycling, the elastic properties provided by EL represent a major hurdle.245 Indeed, even small amounts of EL may hamper textile recycling. It has been estimated that almost 20% of the non-recyclable textiles in EU contain elastane.246 Therefore, the valorisation of EL plays a major role in facilitating garment recycling and, more generally, enhancing the circularity of the textile industry.
The valorisation of EL-containing blends is achieved by two distinct strategies, namely the separation of components by dissolution, possibly followed by depolymerisation (Fig. 14, path A) or the selective deconstruction of one fibre, while keeping the other component intact (Fig. 14, path B). Although not categorised as a chemical recycling method (see section 2), the dissolution-based methodology may remove EL, which is usually selectively solubilized. Typical solvents used for this aim are the REACH-restricted dimethyl formamide (DMF), dimethyl sulfoxide (DMSO), tetrahydrofuran (THF), or potentially green solvent as cyrene, tetrahydrofurfuryl alcohol, and γ-valerolactone.247,248 Moreover, the reusability of the recovered EL is not always effective due to fibre degradation upon extraction. Innovative solutions have been investigated for this approach, including the usage of deep eutectic solvents or ionic liquids.249
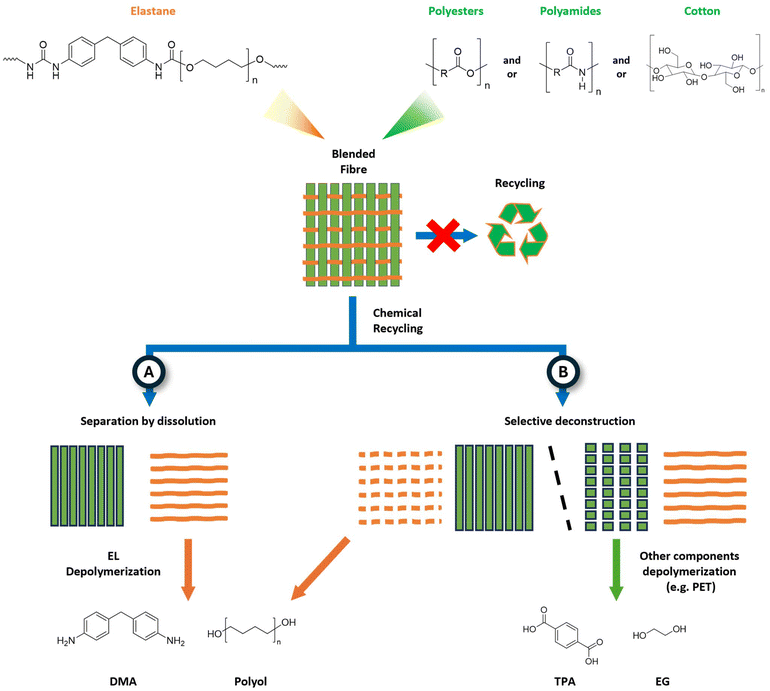 |
| Fig. 14 Schematic of elastane blended fibres and chemical recycling pathways: (A) separation by dissolution and (B) separation by selective deconstruction. | |
The second strategy exploits the suitability of a given depolymerisation process for a single (or multiple) component of the blended yarn, which then may undergo upcycling to reusable materials (Fig. 14, path B). For example, Zhang et al. claimed the extraction and depolymerisation of PET into terephthalic acid from a 95
:
5% PET
:
Spandex blend using a dichloromethane/ethanol solvent mixture and an excess of KOH at 30 °C for 30 min.250 Hummel and Sanchez et al. described an aminolysis-based technique to selectively degrade EL from cotton (vide infra). Although conceptually feasible, it must be noted that the deconstruction of yarns is particularly challenging due to the variety of blended textiles that would require specific processing. To date, catalytic systems enabling the selective cleavage of mixed EL fibres have not been adequately developed, as described in the following section.
PU comprises complex polymers that may contain different bonds in their backbone (e.g. urethane, esters, ethers, urea). Depolymerisation reactions of PU may affect any of these bonds. Herein, we will focus only on those processes resulting in the cleavage of the urethane chain linkage (Fig. 15). Indeed, most works performed with commercial and model polyurethanes that target urethane linkages could ideally be extended to EL chemistry. In this section, the generic chemistry of PU depolymerization will be considered. The most common depolymerisation strategy is based on a transcarbamoylation reaction, consisting of the transfer of a carbamoyl moiety (R-NH-CO) from a “donor”, usually PU, to an acceptor group. Based on the type of acceptor, the process can be referred to as alcoholysis (glycolysis), aminolysis or acidolysis (Fig. 15a–c).251 In addition, hydrolysis and hydrogenolysis processes can be used to cleave the urethane bonds. Notably, these latter reactions are useful in “closing the loop” for PU production by providing reprocessable diamines and polyols.
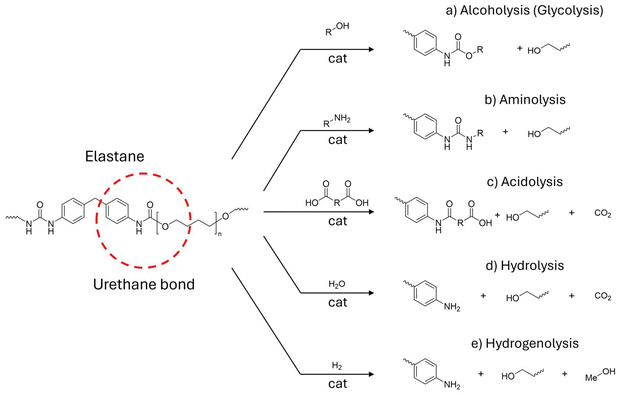 |
| Fig. 15 Scheme of the major possible EL chemical depolymerization reactions involving the urethane bond using homogeneous-phase catalysts: (a) glycolysis, (b) aminolysis, (c) alcoholysis, (d) hydrolysis, and (e) hydrogenolysis. | |
Among these methods, glycolysis is the most used chemical recycling method for PU and the only one used in the industry, though applied to flexible foams (e.g. by EniChem,252 Troy polymers,253 Rampf254), slabs, shoe soles waste, and not specifically designed for textiles, and often without catalysts.255 An exhaustive review of industrial glycolysis of polyurethanes can be found in the literature.256 In a typical PU glycolysis reaction, an excess of ethylene glycol is used in the temperature range of 150–300 °C to provide low-molecular weight functionalised carbamates and a polyol.257 Recently, Xu and co-workers reported a two-step process for the glycolysis of a polyester–spandex blended fabric (94
:
6 ratio), where spandex is first dissolved in DMF at 75 °C, whereas insoluble PET is recovered to undergo conventional methanolysis depolymerisation (Fig. 10).258 Spandex is then depolymerised using an excess of EG and K2CO3 as a catalyst and 200 °C reaction temperature to give 4,4-diaminodiphenylmethane (DMA) (10 wt% yield), 2-imidazolidinone and sticky polyTHF as main products. The drawbacks of the method are the use of DMF and the cost of product mixture separation, as usual for glycolysis processes.
Alcoholysis, e.g. using super-critical methanol,259 may be a friendlier option for PU depolymerisation. Skrydstrup's group reported a solvolysis process whereby elastane was simultaneously extracted and depolymerized from blended textiles using tert-amyl alcohol and KOH catalyst (0.19 wt%) at 225 °C for 4.5 h.260,261 The approach was highly versatile and adaptable to a wide variety of textiles, including pure elastane, 8–27 wt% elastane blends, and PU-coated textiles (PET/PU and PA/PU, gloves, jackets) (Table 4). Noteworthy, up to 98% overall mass recovery was possible with the tested fibres.
Table 4 Solvolysis of elastane from mixed fabrics and PU coated fabricsa
Garment type |
Blends type |
DMA yield (wt%) |
Polyol yield (wt%) |
Leftover solid (wt%) |
Isolated yield. Data from ref. 260.
|
Elastane fibres |
EL 100% |
13 |
74 |
n.a. |
Blended tissue |
Cotton-EL 14% |
3.9 |
77 |
75 |
Synthetic leather |
PET/EL coated |
8.2 |
21 |
0.65 |
Post dissolution extract |
EL 100% |
12 |
72 |
n.a. |
Workwear: glove |
PA-EL coated |
6.5 |
24 |
61 |
Synthetic leather jacket |
PA-EL coated |
9.0 |
30 |
61 |
Nylon tights |
PA-EL 73%–27% |
9.8 |
77 |
75 |
In another approach, primary and secondary amines or ammonia were used to perform the transcarbamoylation of PU-based materials via aminolysis using a series of aminic organocatalysts at 160 °C (Fig. 15b).262 Compared to alcohols, amines are stronger nucleophiles, hence more effective in transcarbamoylation reactions, for instance at lower reaction temperatures. Sanchez and Hummel's group reported the aminolysis of EL from cotton-EL blended yarns using diethylammine and 1,4 diazobicylo-non-5-ene catalyst in DMF or DMSO at 80 °C.263 Yet, aminolysis has been scarcely investigated in PU depolymerisation so far, likely due to hazards related to the use of amines.
In the acidolysis process, a dicarboxylic acid, such as maleic or fumaric acids, is used to cleave PU into an amide, a polyol and CO2 (Fig. 15c).264 To date, acidolysis is claimed at a pilot scale by RAMPFT and Anace; however, process details are not available.265,266 Acidolysis is mostly used for the recovery of polyols, whereas amide moieties cannot be reprocessed easily. To the best of our knowledge, acidolysis has not yet been applied to EL or textiles but to PU foams.
PU hydrolysis was first developed by Ford Motor in the 70s.267 It consists of the cleavage of the urethane bond using hot water or steam to give diamines, polyols, and carbon dioxide (Fig. 15d).268 To be efficient, hydrolysis requires high temperatures (150–350 °C), high pressure (up to 50 atm), and the presence of an acid or base.269 Despite being the first PU depolymerization technique developed, hydrolysis has not yet been industrialized due to the costs associated with energy inputs and the biphasic separation of water and polyols.
All the above depolymerisation methods involve the management of considerable amounts of solvents or the usage of strong acids or bases, which results in poor control over product selectivity. Recently, the reductive catalytic cleavage of the urethane linkage, i.e. hydrogenolysis (Fig. 15d), has emerged as a promising strategy for the chemical upcycling of PU.76 The process affords diamines and polyols alongside methanol. The approach has the double benefit of: (i) producing reprocessable chemicals, (ii) avoiding excesses of reactants and using H2 as a clean reducing agent. PU hydrogenolysis typically involves homogeneous organo-metallic hydrogenation catalysts and a base co-catalyst. Kumar and co-workers reported the depolymerization of polyurethane resins using a Ru pincer complex at 135 °C, in the presence of 60 bar of H2 and KOtBu as a base.270 Similarly, Skrydstrup's group described the reductive deconstruction of commercial end-of-life polyurethanes using the manganese complex Mn-PhMACHO, isopropyl alcohol, KOH as a base, at 180 °C and 50 bar of H2.271 DMA-based PU foams were depolymerised with a diamine yield of up to 90 mol%. Schaub et al. reported the hydrogenation of MDI-based polyurethane using a Ru complex and KOtBu (4 mmol%) as catalysts in THF at 120 °C, under 50 bar of H2, to yield 76% MDI and 85% 1,6-hexane diol.272 In these studies, the solubility of the polymer is indicated as a key to enabling the optimal conversion, whilst a synergistic effect of solvolysis–hydrogenolysis has been highlighted for efficient depolymerisation.
3.4. Polyacrylics
Unlike polyesters and polyamides, polyacrylates are thermosetting materials that cannot reshaped by melting. Acrylics find applications in various fields, including textiles. acrylic fibres, particularly polyacrylonitrile (PAN) and modacrylic (MAC), are mostly used in home furnishings, e.g. blankets, and in wool-like clothing, e.g. sweaters and socks, due to their favourable strength, density, softness, heat retention and flexibility properties.273 PAN is a homopolymer of acrylonitrile, whereas MAC is a more complex co-polymer of PAN with vinyl chloride or vinylidene chloride monomers (Fig. 16).274 Due to the strong C–C bonds, these polymers are particularly resistant to depolymerisation and biological degradation.275 Polyacrylics are produced in around 2 Mton per year, and less than 10% is recycled.276 In most cases, polyacrylate fabrics are not composed of pure acrylic fibres, but rather mixtures with other materials, such as polyesters, polyamides, cotton and wool, and are usually pigmented.
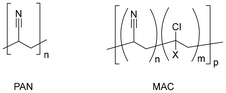 |
| Fig. 16 Structures of PAN and MAC. X = H or Cl, m 15–65%. | |
For the above-mentioned reasons, the mechanical recycling of acrylic-based textiles is unfavourable and expensive.277 In addition, acrylates are quite insoluble polymers (e.g. in DMF, dimethylacetamide, nitric acid, ethylene carbonate), which makes their recycling by dissolution/precipitation (with water) industrially unattractive. Depolymerisation is also troublesome. Thermal processes may lead to the formation of carbonaceous solid waste, as well as toxic gases (e.g. HCN, NH3), whilst controlled depolymerisation processes are still at the very early development stage. Since PAN is the main precursor of carbon fibres, some studies have focused on the thermal upcycling of waste acrylic textiles for this aim.278 Dissolution in organic solvents still remains the most pursued recycling route to date.279
No studies have been reported on the catalytic depolymerisation of PAN and MAC waste. Recent findings are limited to the treatment of the parent poly(methyl methacrylate) (PMMA), commonly used as a glass substitute (Plexiglas). Thus, depolymerization of PMMA was achieved at 290 °C, with >90% yield of methyl methacrylate (MMA), via reversible-deactivation radical polymerization by the incorporation of thermolytically labile end-groups (N-hydroxyphthalimide esters and trithiocarbonates), under solvent-free conditions.280 Depolymerization of PMMA and poly(n-butyl methacrylate) (PBMA), with terminal chlorine chain-end functionality, was reported over iron chloride at 170 °C, using tetra(ethylene glycol) dimethyl ether as solvent.281 A conversion of >70% was achieved, where the monomer could be recovered by distillation.
Alternative to depolymerisation, upcycling of waste acrylics has been possible by chemical functionalisation. For instance, recycled PAN fibres from textiles were amino-functionalized by means of ethylenediamine and used for the adsorption of Hg(II) ions from contaminated water media, with 99% removal efficiency and an adsorption capacity of 1116 mg g−1.282
4. Conclusions and prospects
Economic indicators suggest the synthetic textile market will considerably grow in the coming years, mostly as a consequence of the fast-fashion phenomenon and the ease of synthetic fibre manufacturing. In addition to the high turnover rate of clothes in stores, unsold and used disposable garments are also rapidly destroyed, mainly in pulping mills or incinerators. Fundamentally hydrocarbon-based and non-biodegradable synthetic yarns may also be low-quality, often containing significant amounts of toxic substances (DMF, heavy metals, phthalates, aromatic polycyclics), even exceeding the REACH limits.283,284 Therefore, fashion is considered the most polluting industry in the world after oil. This mainly affects developing countries (e.g. Ghana, Nigeria, Kenya, Tanzania, Chile), where about 70 tonnes of waste garments are estimated to be daily transferred in illegal dumps or ditches from the second-hand cloth markets of Accra.285,286 Strong commitments have been undertaken by policymakers, both at the European and global level, to increase sustainability and circularity of the textile sector by adopting strategies to improve recycling while minimising disposable fashion and making textile products more repairable, reusable, recyclable and free of hazardous substances.287,288 Current limitations are due to the lack of circular textile supply chains, which are mostly structured around recovery, selection and mechanical recycling.
Complementary to mechanical recycling, depolymerisation via chemical recycling is considered an industrially attractive option. Treatment of plastic waste to recover monomers, which are reprocessable into virgin yarns, other plastic goods or valuable chemicals, may help diminish the depletion of non-renewable oil feedstock, the economic and environmental impact of synthetic polymer production, and the accumulation of non-biodegradable materials in landfills. The strategy may ensure the supply of future raw materials for bottle-to-textile and textile-to-textile circular chains or the development of innovative value chains, which may expand the concept of plastic refinery. Drawbacks of depolymerisation include the massive use of solvents or chemicals, soluble promoters, corrosive conditions and the need for high reaction temperatures. Using a catalyst may significantly improve the processes by decreasing the energy inputs and reaction times while enabling selective depolymerisation to be driven into a variety of useful monomers under mild conditions. However, unlike other plastic materials, the complexity of synthetic textile waste poses further problems. These waste streams are intricate mixtures of additives, dyes, hard parts and different fibre-type blends. In addition to precise upstream sorting and separation, this would require demanding pre-treatments, such as grinding, dissolution or selective disintegration. Specialised catalysts with enhanced resistance and versatility may also be needed.104
Depolymerisation of polyester, polyamide, polyurethane and polyacrylic textiles illustrated in the previous sections show that despite the growing interest in the catalytic chemical recycling of these polymer types, few studies directly focus on textiles, whereas the majority relate to pure polymers or model compounds. Depolymerization of PET fibres (section 3.1) is surely the most advanced, with catalytic depolymerization processes usually involving solvolysis. However, catalyst selectivity and durability are still obstacles to the handling of post-consumer products. Similarly, catalytic depolymerisation of PA has been mostly proven at the laboratory scale using homogeneous and heterogeneous catalysts (section 3.2). By contrast, PU catalytic depolymerization is still in its infancy, especially targeting elastane. Model polyurethanes are usually employed, and very few works focus on elastane (section 3.3). In addition, EL research suffers from a lack of standards and the high complexity and diversity of commercial EL on the market. Therefore, joint efforts between researchers and EL manufacturers are needed to standardize R&D benchmarks. Finally, depolymerisation of polyacrylics such as PAN and MAC has seldom been investigated (section 3.4).
All the above considerations explain why the few existing chemical recycling processes for synthetic textiles are currently demonstrated mostly on a small scale, whereas their implementation on a large scale has not yet been developed. To this aim, these technologies should be radically improved. Some challenges and priorities in this direction may be highlighted.
Innovative, preferably heterogeneous, catalysts must be designed, whose structure, morphology and composition may dramatically affect the fate of depolymerisation.83 Particularly, granulometry and porosity of solid catalysts may control the surface interaction with (insoluble) synthetic polymers and diffusion within the catalyst body. Catalysts with nanometric size and macroporosity may be the preferred choice. Heterogeneous catalysts may show improved thermal and chemical resistance under the usual reaction conditions of solvolytic depolymerisation, and they are preferred by the industry due to the easier recovery and implementation into the existing reactor equipment. Further, bifunctional catalysts may enable complex reaction sequences to efficiently occur in cascade and in one-pot, thus allowing otherwise inaccessible reaction pathways and products.99 This is, for instance, the case of solvolysis-hydrogenation paths.289,290 Coupling heterogeneous catalysis with continuous flow reactor engineering can add substantial process intensification, which, to date, in the field of plastic material waste is limited to unselective cracking.291 The use of earth-abundant or low-cost catalytic precursors should also be considered for the establishment of depolymerisation processes at large.
Given the complexity of (depolymerisation) treatments and downstream purifications inherent to the chemical recycling of synthetic textiles, careful technical, economic and environmental analyses shall be performed to assess the sustainability, feasibility and competitiveness of the overall processes.292,293 This may include, for example, either (Environmental) Life Cycle Assessment, Life Cycle Sustainability Assessment (ELCA, LCA and LCSA),294,295 or Life Cycle Cost (LCC) analyses.296,297
Particularly for research in Chemical Sciences, together with an accurate catalyst and process design, upstream material design is desirable. This may include recyclable-by-design, for instance, in terms of separability, biodegradability or ease of chemical depolymerisation,72,298 and safe-by-design, for instance, fibres devoid of noxious monomeric components, additives or contaminants.299,300
Traceability technologies and labelling and information declaration for textiles shall be improved and implemented. These may include textile fibre name, origin, composition, use of recycled materials, sorting and recycling options.301
Finally, consumer awareness regarding textile usage, disposal, reuse and recycling should be increased. Consumers may not be aware of the synthetic content of their clothes, nor their fate or negative impact on the environment when discarded. Separation, collection and recycling options for textiles, particularly synthetic ones, should be made known to the public at large. Recycled garments, second-hand clothes or textiles made of recycled or secondary raw materials often suffer from negative perceptions, which may include safety and low-quality prejudices. Market acceptance of recycled materials may be improved by education and the commitment of brands to sustainability.
In conclusion, advancements in textile chemical recycling require a collective effort from all stakeholders across the value chain, including researchers, policymakers, consumers, textile producers, and recycling companies. To this respect, innovation in catalytic chemical recycling has the clear potential to provide new pathways toward a closed-loop circular economy for textiles, hence reinforcing the overall objectives of the European Green Deal302 and supporting the achievement of the Ecological Transition and Sustainable Development Goals.303,304
Data availability
No primary research results, software or code have been included and no new data were generated or analysed as part of this review.
Conflicts of interest
There are no conflicts to declare.
Acknowledgements
Thanks are due to the Circular and Sustainable Made in Italy Extended Partnership (MICS) funded by the European Union Next-Generation EU. (Piano Nazionale di Ripresa e Resilienza (PNRR) – Missione 4, Componente 2, Investimento 1.3 – D.D. 1551.11-10-2022, PE00000004, CUP B53C22004100001) for financial support. Thanks are also due to the LABSolve “Lactic acid based new green solvents: design, synthesis and use in catalysis” project (20229P7PPM, CUP B53D23015230006) funded by the European Union Next-Generation EU, PNRR, Missione 4 “Istruzione e Ricerca” – Componente C2 Investimento 1.1, “Fondo per il Programma Nazionale di Ricerca e Progetti di Rilevante Interesse Nazionale (PRIN)”.
References
-
https://www.igtpan.com/Ingles/mercado.asp
(accessed August 2024).
-
BISFA, Terminology of man-made fibres, Brussels, 2017. https://bisfa.org/generic-fibre-names/ (accessed September 2024) Search PubMed.
- Regulation (EU) No 1007/2011 of the European Parliament and of the Council of 27 September 2011 on textile fibre names and related labelling and marking of the fibre composition of textile products and repealing Council Directive 73/44/EEC and Directives 96/73/EC and 2008/121/EC of the European Parliament and of the Council. https://eur-lex.europa.eu/legal-content/EN/TXT/?uri=celex%3A32011R1007.
- European Environment Agency - European Topic Centre on Waste and Materials in a Green Economy, Plastic in textiles: potentials for circularity and reduced environmental and climate impacts, Eionet Report – ETC/WMGE 2021/1, Mol, 2021. https://www.eionet.europa.eu/etcs/etc-wmge/products/etc-wmge-reports/plastic-in-textiles-potentials-for-circularity-and-reduced-environmental-and-climate-impacts.
- Data from TexPro, https://texpro.fibre2fashion.com (accessed 15 March 2022). Benchmark materials are as follows. Cotton: cotton fibre, Cotlook A index. Polyester: polyester Filament Yarn (FDY 50D/24F), Asia - Domestic China index. Nylon: nylon Filament Yarn (FDY 20D SD), Asia - FOB India index. Wool: wool (19 micron), Australia - Sydney index.
- K. Niinimäki, G. Peters, H. Dahlbo, P. Perry, T. Rissanen and A. Gwilt, The environmental price of fast fashion, Nat. Rev. Earth Environ., 2020, 1, 189–200, DOI:10.1038/s43017-020-0039-9.
- Textile Exchange, Preferred Fiber & Materials Market Report, October 2022. https://textileexchange.org/knowledge-center/reports/preferred-fiber-and-materials.
- CIRFS - European Man-Made Fibres Association. https://www.cirfs.org/man-made-fibers/Fibre-range (accessed September 2023).
- R. Wei and W. Zimmermann, Microbial enzymes for the recycling of recalcitrant petroleum-based plastics: how far are we?, Microb. Biotechnol., 2017, 10, 1308–1322, DOI:10.1111/1751-7915.12710.
- M. Vert, Y. Doi, K. H. Hellwich, M. Hess, P. Hodge, P. Kubisa, M. Rinaudo and F. Schué, Terminology for biorelated polymers and applications (IUPAC Recommendations 2012), Pure Appl. Chem., 2012, 84, 377–410, DOI:10.1351/PAC-REC-10-12-04.
-
M. W. Ryberg, A. Laurent and M. Hauschild, Mapping of global plastics value chain and plastics losses to the environment, 2018, United Nations Environment Programme. https://www.unep.org/resources/report/mapping-global-plastics-value-chain-and-plastics-losses-environment-particular Search PubMed.
-
Plastics Europe, Association of Plastics Manufacturers, Plastics - The Facts 2022, Brussels, 2022. https://plasticseurope.org/knowledge-hub/plastics-the-facts-2022 Search PubMed.
- R. Geyer, J. R. Jambeck and K. Lavender Law, Production, use, and fate of all plastics ever made, Sci. Adv., 2017, 3, e1700782, DOI:10.1126/sciadv.1700782.
-
United States Environmental Protection Agency, Advancing Sustainable Materials Management: 2016 and 2017 Tables and Figures, 2019. https://www.epa.gov/facts-and-figures-about-materials-waste-and-recycling/advancing-sustainable-materials-management Search PubMed.
-
Istituto Superiore per la Protezione e la Ricerca Ambientale (ISPRA), Rapporto Rifiuti Urbani Edizione 2022, Roma, 2022. https://www.isprambiente.gov.it/it/pubblicazioni/rapporti/rapporto-rifiuti-urbani-edizione-2022 Search PubMed.
- Circular Copenhagen, Results from automatic sorting of recyclable textiles, June 2022, https://circular.kk.dk/nyheder/results-from-automatic-sorting-of-recyclable-textiles (accessed September 2024).
-
D. Watson, S. Trzepacz, N. Lander Svendsen, S. Wittus Skottfelt, N. Kiørboe, M. Elander and H. Ljungkvist Nordin, Towards 2025: Separate collection and treatment of textiles in six EU countries, Danish Environmental Protection Agency, 2020. https://www.mst.dk (accessed September 2024) Search PubMed.
- G. Sandin and G. M. Peters, Environmental impact of textile reuse and recycling e A review, J. Cleaner Prod., 2018, 184, 353–365, DOI:10.1016/j.jclepro.2018.02.266.
-
European Environment Agency, Textiles and the environment: the role of design in Europe's circular economy, 2022. https://www.eea.europa.eu/publications/textiles-and-the-environment-the Search PubMed.
- Ellen MacArthur Foundation, A new textiles economy: Redesigning fashion's future, 2017. https://www.ellenmacarthurfoundation.org/publications (accessed September 2024).
- Expert Network on Textile Recycling, Strategic Agenda on Textile Waste Management and Recycling. https://programme2014-20.interreg-central.eu/Content.Node/Strategic-Agenda.html (accessed September 2024).
-
Plastics Europe, Association of Plastics Manufacturers, The Circular Economy for Plastics - A European Overview, Brussels, 2022. https://plasticseurope.org/knowledge-hub/the-circular-economy-for-plastics-a-european-overview-2/ Search PubMed.
- G. Hole and A. S. Hole, Improving recycling of textiles based on lessons from policies for other recyclable materials: A minireview, Sustainable Prod. Consumption., 2020, 23, 42–51, DOI:10.1016/j.spc.2020.04.005.
- S. S. Muthu, Y. Li, J. Y. Hu and P. Y. Mok, Recyclability Potential Index (RPI): The Concept and Quantification of RPI for Textile Fibres, Ecol. Indic., 2012, 18, 58–62, DOI:10.1016/j.ecolind.2011.10.003.
- K. Ragaert, L. Delva and K. Van Geem, Mechanical and chemical recycling of solid plastic waste, Waste Manage., 2017, 69, 24–58, DOI:10.1016/j.wasman.2017.07.044.
- K. Cura, N. Rintala, T. Kamppuri, E. Saarimäki and P. Heikkilä, Textile Recognition and Sorting for Recycling at an Automated Line Using Near Infrared Spectroscopy, Recycling, 2021, 6, 11, DOI:10.3390/recycling6010011.
- D. Paraschiv, C. Tudor and R. Petrariu, The textile industry and sustainable development: a Holt–Winters forecasting investigation for the Eastern European area, Sustainability, 2015, 7, 1280–1291, DOI:10.3390/su7021280.
- L. Peng, D. Fu, H. Qi, C. Q. Lan, H. Yu and C. Ge, Micro- and nano-plastics in marine environment: Source, distribution and threats - A review, Sci. Total Environ., 2020, 698, 134254, DOI:10.1016/j.scitotenv.2019.134254.
- C. Jönsson, O. Levenstam Arturin, A. C. Hanning, R. Landin, E. Holmström and S. Roos, Microplastics Shedding from Textiles - Developing Analytical Method for Measurement of Shed Material Representing Release during Domestic Washing, Sustainability, 2018, 10, 2457–2474, DOI:10.3390/su10072457.
-
European Environment Agency, Microplastics from textiles: towards a circular economy for textiles in Europe, 2022. https://www.eea.europa.eu/publications/microplastics-from-textiles-towards-a Search PubMed.
-
OECD, Global Plastics Outlook: Policy Scenarios to 2060, OECD Publishing, Paris, 2022, DOI:10.1787/aa1edf33-en.
-
L. Wetterberg, J. Barrie and P. Schröder, The EU's Circular Economy transition for plastic and textiles: Opportunities and challenges for trade partners in emerging markets, Switch to Circular Economy Value Chains, 2022, https://www.switchtocircular.eu/publication/EU-circular-economy-policies-ChathamHouse-policy-paper?back Search PubMed.
- European Commission, A new Circular Economy Action Plan - For a cleaner and more competitive Europe, Brussels, COM(2020) 98 final, 2020, https://eur-lex.europa.eu/legal-content/EN/TXT/?uri=COM:2020:98:FIN Search PubMed.
-
European Commission, EU Strategy for Sustainable and Circular Textiles, Brussels, COM(2022) 141 final, 2022, https://eur-lex.europa.eu/legal-content/EN/TXT/?uri=COM:2022:141:FIN Search PubMed.
-
European Commission, A European Strategy for Plastics in a Circular Economy, Brussels, COM(2018) 28 final, 2018, https://eur-lex.europa.eu/legal-content/EN/TXT/?uri=COM:2018:28:FIN Search PubMed.
- Directive 2008/98/EC of the European Parliament and of the Council of 19 November 2008 on waste and repealing certain Directives, https://eur-lex.europa.eu/legal-content/EN/TXT/?uri=CELEX%3A02008L0098-20180705.
- Directive (EU) 2018/851 of the European Parliament and of the Council of 30 May 2018 amending Directive 2008/98/EC on waste, https://eur-lex.europa.eu/legal-content/EN/TXT/?uri=celex%3A32018L0851.
- European Environment Agency – European Topic Centre on Waste and Materials in a Green Economy, Textiles and the environment in a circular economy, Eionet Report – ETC/WMGE 2019/6, Mol, 2019. https://www.eionet.europa.eu/etcs/etc.-wmge/products/etc-wmge-reports/textiles-and-the-environment-in-a-circular-economy.
-
OECD, Towards a more resource-efficient and circular economy - The role of the G20, 2021, https://www.oecd.org/env/waste/latestdocuments (accessed September 2024) Search PubMed.
-
EURATEX - The European apparel and textile confederation, ReHubs A joint initiative for industrial upcycling of textile waste streams & circular materials, Brussels, 2020, https://euratex.eu/news/rehubs/ (accessed September 2024) Search PubMed.
- Ministero della Transizione Ecologica, Strategia nazionale per l'economia circolare, 2022, https://www.mase.gov.it/pagina/economia-circolare.
- Ministero della Transizione Ecologica, AVVISO M2C.1.1 I 1.2, Linea d'intervento D, “Infrastrutturazione della raccolta delle frazioni di tessili pre-consumo e post consumo, ammodernamento dell'impiantistica e realizzazione di nuovi impianti di riciclo delle frazioni tessili in ottica sistemica cd. “Textile Hubs”, https://www.mase.gov.it/pagina/pnrr-pubblicazione-decreti-economia-circolare, (accessed September 2024).
- Deutsche Gesellschaft für internationale Zusammenarbeit, Circular Economy in the Textile Sector, 2019, https://adelphi.de/en/publications/circular-economy-in-the-textile-sector.
-
D. Palm, M. Elander, D. Watson, N. Kiørboe, H. Salmenperä, H. Dahlbo, K. Moliis, K. A. Lyng, C. Valente, S. Gíslason, H. Tekie and T. Rydberg, Nordic Council of Ministers, Towards a Nordic textile strategy - Collection, sorting, reuse and recycling of textiles, Copenhagen, 2014, DOI:10.6027/TN2014-538.
-
https://www.ecap.eu.com
(accessed September 2024).
-
N. Šajn, Environmental impact of the textile and clothing industry, European Parliamentary Research Service, PE 633.143, 2019, https://www.europarl.europa.eu/thinktank/en/document/EPRS_BRI(2019)633143 Search PubMed.
-
A. R. Köhler, D. Watson, S. Trzepacz, C. Löw, R. Liu, J. Danneck, A. Konstantas, S. Donatello and G. Faraca, Circular economy perspectives in the EU Textile sector, Final report, European Commission - Joint Research Centre, 2021, https://publications.jrc.ec.europa.eu/repository/handle/JRC125110.
- G. M. Peters, G. Sandin and B. Spak, Environmental Prospects for Mixed Textile Recycling in Sweden, ACS Sustainable Chem. Eng., 2019, 7, 11682–11690, DOI:10.1021/acssuschemeng.9b01742.
- D. Damayanti, L. A. Wulandari, A. Bagaskoro, A. Rianjanu and H. S. Wu, Possibility Routes for Textile Recycling Technology, Polymers, 2021, 13, 3834–3863, DOI:10.3390/polym13213834.
- S. Bianchi, F. Bartoli, C. Bruni, C. Fernandez-Avila, L. Rodriguez-Turienzo, J. Mellado-Carretero, D. Spinelli and M. B. Coltelli, Opportunities and Limitations in Recycling Fossil Polymers from Textiles, Macromol., 2023, 3, 120–148, DOI:10.3390/macromol3020009.
- P. Harmsen, M. Scheffer and H. Bos, Textiles for Circular Fashion: The Logic behind Recycling Options, Sustainability, 2021, 13, 9714–9730, DOI:10.3390/su13179714.
- M. Ribul, A. Lanot, C. Tommencioni Pisapia, P. Purnell, S. J. McQueen-Mason and S. Baurley, Mechanical, chemical, biological: Moving towards closed-loop bio-based recycling in a circular economy of sustainable textiles, J. Cleaner Prod., 2021, 326, 129325, DOI:10.1016/j.jclepro.2021.129325.
- D. S. Stefan, M. Bosomoiu and M. Stefan, Methods for Natural and Synthetic Polymers Recovery from Textile Waste, Polymers, 2022, 14, 3939–3961, DOI:10.3390/polym14193939.
- R. B. Baloyi, O. J. Gbadeyan, B. Sithole and V. Chunilall, Recent advances in recycling technologies for waste textile fabrics: a review, Text. Res. J., 2024, 94, 508–529, DOI:10.1177/00405175231210239.
- L. Keßler, S. A. Matlin and K. Kümmerer, The contribution of material circularity to sustainability - Recycling and reuse of textiles, Curr. Opin. Green Sustainable Chem., 2021, 32, 100535, DOI:10.1016/j.cogsc.2021.100535.
- T. El Darai, A. Ter-Halle, M. Blanzat, G. Despras, V. Sartor, G. Bordeau, A. Lattes, S. Franceschi, S. Cassel, N. Chouini-Lalanne, E. Perez, C. Déjugnat and J. C. Garrigues, Chemical recycling of polyester textile wastes: shifting towards sustainability, Green Chem., 2024, 26, 6857–6885, 10.1039/d4gc00911h.
-
A. Merrington, Recycling of Plastics, in Applied Plastics Engineering Handbook, Elsevier, 2nd edn, 2017, ch. 9, pp. 167–189, DOI:10.1016/B978-0-323-39040-8.00009-2.
- P. K. Mishra, A. M. D. Izrayeel, B. K. Mahur, A. Ahuja and V. K. Rastogi, A comprehensive review on textile waste valorization techniques and their
applications, Environ. Sci. Pollut. Res., 2022, 29, 65962–65977, DOI:10.1007/s11356-022-22222-6.
- I. A. Ignatyev, W. Thielemans and B. Vander Beke, Recycling of Polymers: A Review, ChemSusChem, 2014, 7, 1579–1593, DOI:10.1002/cssc.201300898.
- Z. O. G. Schyns and M. P. Shaver, Mechanical Recycling of Packaging Plastics: A Review, Macromol. Rapid Commun., 2021, 42, 2000415, DOI:10.1002/marc.202000415.
- K. Hamad, M. Kaseem and F. Deri, Recycling of waste from polymer materials: An overview of the recent works, Polym. Degrad. Stab., 2013, 98, 2801–2812, DOI:10.1016/j.polymdegradstab.2013.09.025.
- T. Thiounn and R. C. Smith, Advances and approaches for chemical recycling of plastic waste, J. Polym. Sci., 2020, 58, 1347–1364, DOI:10.1002/pol.20190261.
- The European Chemicals Agency, Chemical Recycling of Polymeric Materials from Waste in the Circular Economy – Final Report, 2021, https://echa.europa.eu/-/reach-requirements-need-to-be-considered-in-chemical-recycling.
-
M. Schlummer, T. Fell, A. Mäurer and G. Altnau, The Role of Chemistry in Plastics Recycling, Kunststoffe International, 2020, vol. 5, https://en.kunststoffe.de/a/specialistarticle/the-role-of-chemistry-in-plastics-recycl-242578 Search PubMed.
- Circular Economy at BASF, BASF, 2022, https://www.basf.com/us/en/who-we-are/sustainability/we-drive-sustainable-solutions/circular-economy/mass-balance-approach/chemcycling/chemicalrecycling.html (accessed September 2024).
- H. Li,
et al., Expanding plastics recycling technologies: chemical aspects, technology status and challenges, Green Chem., 2022, 24, 8899–9002, 10.1039/d2gc02588d.
- S. M. Al-Salem, A. Antelava, A. Constantinou, G. Manos and A. Dutta, A review on thermal and catalytic pyrolysis of plastic solid waste (PSW), J. Environ. Manage., 2017, 197, 177–198, DOI:10.1016/j.jenvman.2017.03.084.
- S. Parrilla-Lahoz, M. C. Zambrano, V. Stolojan, R. Bance-Soualhi, J. J. Pawlak, R. A. Venditti, T. Ramirez Reina and M. S. Duyar, Charting a path to catalytic upcycling of plastic micro/nano fiber pollution from textiles to produce carbon nanomaterials and turquoise hydrogen, RSC Sustainability, 2023, 1, 1177–1183, 10.1039/d3su00095h.
- D. Munira, M. F. Irfanb and M. R. Usman, Hydrocracking of virgin and waste plastics: A detailed review, Renewable Sustainable Energy Rev., 2018, 90, 490–515, DOI:10.1016/j.rser.2018.03.034.
- D. P. Serrano, J. Aguado and J. M. Escola, Developing Advanced Catalysts for the Conversion of Polyolefinic Waste Plastics into Fuels and Chemicals, ACS Catal., 2012, 2, 1924–1941, DOI:10.1021/cs3003403.
- A. S. Burange, M. B. Gawande, F. L. Y. Lam, R. V. Jayaramd and R. Luque, Heterogeneously catalyzed strategies for the deconstruction of high density polyethylene: plastic waste valorisation to fuels, Green Chem., 2015, 17, 146–156, 10.1039/c4gc01760a.
- M. Hong and E. X. Y. Chen, Chemically recyclable polymers: a circular economy approach to sustainability, Green Chem., 2017, 19, 3692–3706, 10.1039/c7gc01496a.
-
J. Y. Q. Teoa and J. Y. C. Lim, Sustainable chemical recycling of plastic waste, in Circularity of Plastics, Elsevier, 2023, ch. 2, DOI:10.1016/B978-0-323-91198-6.00004-8.
- Refashion, Chemical Recycling of Textiles, June 2024, https://refashion.fr/pro/en/chemical-recycling-used-textiles-latest-developments.
- T. Uekert, A. Singh, J. S. DesVeaux, T. Ghosh, A. Bhatt, G. Yadav, S. Afzal, J. Walzberg, K. M. Knauer, S. R. Nicholson, G. T. Beckham and A. C. Carpenter, Technical, Economic, and Environmental Comparison of Closed Loop Recycling Technologies for Common Plastics, ACS Sustainable Chem. Eng., 2023, 11, 965–978, DOI:10.1021/acssuschemeng.2c05497.
- A. C. Fernandes, Reductive depolymerization as an efficient methodology for the conversion of plastic waste into value-added compounds, Green Chem., 2021, 23, 7330–7360, 10.1039/d1gc01634b.
- J. Sherwood, Closed-Loop Recycling of Polymers Using Solvents, Johnson Matthey Technol. Rev., 2020, 64, 4–15, DOI:10.1595/205651319X15574756736831.
- U. S. Chaudhari, D. G. Kulas, A. Peralta, T. Hossain, A. T. Johnson, D. S. Hartley, R. M. Handler, B. K. Reck, V. S. Thompson, D. W. Watkinsg and D. R. Shonnard, Solvent based dissolution-precipitation of waste polyethylene terephthalate: economic and environmental performance metrics, RSC Sustainability, 2023, 1, 1849–1860, 10.1039/d3su00231d.
- W. Kaminsky and F. Hartmann, New Pathways in Plastics Recycling, Angew. Chem., Int. Ed., 2000, 39, 331–333, DOI:10.1002/(SICI)1521-3773(20000117)39:2<331::AID-ANIE331>3.0.CO;2-H.
- D. V. A. Ceretti, M. Edeleva, L. Cardon and D. R. D'hooge, Molecular Pathways for Polymer Degradation during Conventional Processing, Additive Manufacturing, and Mechanical Recycling, Molecules, 2023, 28, 2344, DOI:10.3390/molecules28052344.
- S. Yue, P. Wang, B. Yu, T. Zhang, Z. Zhao, Y. Li and S. Zhan, From Plastic Waste to Treasure: Selective Upcycling through Catalytic Technologies, Adv. Energy Mater., 2023, 13, 2302008, DOI:10.1002/aenm.202302008.
- G. Xu and Q. Wang, Chemically recyclable polymer materials: polymerization and depolymerization cycles, Green Chem., 2022, 24, 2321–2346, 10.1039/d1gc03901f.
- A. J. Martín, C. Mondelli, S. D. Jaydev and J. Pérez-Ramírez, Catalytic processing of plastic waste on the rise, Chem, 2021, 7, 1–47, DOI:10.1016/j.chempr.2020.12.006.
- B. Dong, G. Xu, R. Yang, X. Guo and Q. Wang, Preparation of Block Copolymers by a Sequential Transesterification Strategy: A Feasible Route for Upcycling End-of-Life Polyester Plastics to Elastomers, Macromolecules, 2023, 56, 10143–10152, DOI:10.1021/acs.macromol.3c01773.
- R. Yang, G. Xu, B. Dong, H. Hou and Q. Wang, A “Polymer to Polymer” Chemical Recycling of PLA Plastics by the “DE–RE Polymerization” Strategy, Macromolecules, 2022, 55, 1726–1735, DOI:10.1021/acs.macromol.1c02085.
- T. Keijer, V. Bakker and J. C. Slootweg, Circular chemistry to enable a circular economy, Nat. Chem., 2019, 11, 190–195, DOI:10.1038/s41557-019-0226-9.
-
Quantis, Chemical Recycling: Greenhouse gas emission reduction potential of an emerging waste management route, European Chemical Industry Council (CEFIC), 2020, https://cefic.org/policy-matters/innovation/chemical-recycling/ (accessed September 2024) Search PubMed.
- A. E. Schwarz, T. N. Ligthart, D. Godoi Bizarro, P. De Wild, B. Vreugdenhil and T. van Harmelen, Plastic recycling in a circular economy; determining environmental performance through an LCA matrix model approach, Waste Manage., 2021, 121, 331–342, DOI:10.1016/j.wasman.2020.12.020.
-
McKinsey & Company, Scaling textile recycling in Europe – Turning waste into value, McKinsey Apparel, Fashion & Luxury Group, 2022, https://www.mckinsey.com/industries/retail/our-insights/scaling-textile-recycling-in-europe-turning-waste-into-value Search PubMed.
- B. D. Vogt, K. K. Stokes and S. K. Kumar, Why is Recycling of Postconsumer Plastics so Challenging?, ACS Appl. Polym. Mater., 2021, 3, 4325–4346, DOI:10.1021/acsapm.1c00648.
- Zero Waste Europe, Understanding the Environmental Impacts of Chemical Recycling - Ten concerns with existing life cycle assessments, December 2020, https://zerowasteeurope.eu/library/understanding-the-environmental-impacts-of-chemical-recycling-ten-concerns-with-existing-life-cycle-assessments/.
-
S. Hann and T. Connock, Chemical Recycling: State of Play, Eunomia Research & Consulting Ltd, 2020, https://www.eunomia.co.uk/reports-tools/final-report-chemical-recycling-state-of-play/ Search PubMed.
- I. Vollmer, M. J. F. Jenks, M. C. P. Roelands, R. J. White, T. van Harmelen, P. de Wild, G. P. van der Laan, F. Meirer, J. T. F. Keurentjes and B. M. Weckhuysen, Beyond Mechanical Recycling: Giving New Life to Plastic Waste, Angew. Chem., Int. Ed., 2020, 59, 15402–15423, DOI:10.1002/anie.201915651.
- Closed Loop Partners, Transitioning to a Circular System for Plastics, 2021, https://www.closedlooppartners.com/appendix-molecular-recycling-technologies/.
- J. P. Lange, Managing Plastic Waste-Sorting, Recycling, Disposal, and Product Redesign, ACS Sustainable Chem. Eng., 2021, 9, 15722–15738, DOI:10.1021/acssuschemeng.1c05013.
-
Valpak, TextileFlow: From Waste to Worth - An analysis of textile recycling opportunities in the UK, 2023, https://www.valpak.co.uk/knowledge-hub-post/textileflow-from-waste-to-worth/ Search PubMed.
- T. P. Haider, C. Völker, J. Kramm, K. Landfester and F. R. Wurm, Plastics of the Future? The Impact of Biodegradable Polymers on the Environment and on Society, Angew. Chem., Int. Ed., 2019, 58, 50–62, DOI:10.1002/anie.201805766.
- F. S. Dainton and K. J. Ivin, Reversibility of the propagation reaction in polymerization processes and its manifestation in the phenomenon of a ‘ceiling temperature, Nature, 1948, 162, 705–707, DOI:10.1038/162705a0.
- G. W. Coates and Y. D. Y. L. Getzler, Chemical recycling to monomer for an ideal, circular polymer economy, Nat. Rev. Mater., 2020, 5, 501–516, DOI:10.1038/s41578-020-0190-4.
- C. Shi, L. T. Reilly, V. S. P. Kumar, M. W. Coile, S. R. Nicholson, L. J. Broadbelt, G. T. Beckham and E. Y. X. Chen, Design principles for intrinsically circular polymers with tunable properties, Chem, 2021, 7, 2896–2912, DOI:10.1016/j.chempr.2021.10.004.
- S. T. Schwab, M. Baur, T. F. Nelson and S. Mecking, Synthesis and Deconstruction of Polyethylene-type Materials, Chem. Rev., 2024, 124, 2327–2351, DOI:10.1021/acs.chemrev.3c00587.
- C. Marquez, C. Martin, N. Linares and D. De Vos, Catalytic routes towards polystyrene recycling, Mater. Horiz., 2023, 10, 1625–1640, 10.1039/2mh01215d.
- X. Zhang, M. Fevre, G. O. Jones and R. M. Waymouth, Catalysis as an Enabling Science for Sustainable Polymers, Chem. Rev., 2018, 118, 839–885, DOI:10.1021/acs.chemrev.7b00329.
- M. Chu, Y. Liu, X. Lou, Q. Zhang and J. Chen, Rational Design of Chemical Catalysis for Plastic Recycling, ACS Catal., 2022, 12, 4659–4679, DOI:10.1021/acscatal.2c01286.
- L. D. Ellis, N. A. Rorrer, K. P. Sullivan, M. Otto, J. E. McGeehan, Y. Román-Leshkov, N. Wierckx and G. T. Beckham, Chemical and biological catalysis for plastics recycling and upcycling, Nat. Catal., 2021, 4, 539–556, DOI:10.1038/s41929-021-00648-4.
- J. C. Worch and A. P. Dove, 100th Anniversary of Macromolecular Science Viewpoint: Toward Catalytic Chemical Recycling of Waste (and Future) Plastics, ACS Macro Lett., 2020, 9, 1494–1506, DOI:10.1021/acsmacrolett.0c00582.
- F. Liguori, C. Moreno-Marrodan, W. Oberhauser, E. Passaglia and P. Barbaro, Hydrolytic depolymerisation of polyesters over heterogeneous ZnO catalyst, RSC Sustainability, 2023, 1, 1394–1403, 10.1039/d3su00089c.
- F. Pardal and G. Tersac, Kinetics of poly(ethylene terephthalate) glycolysis by diethylene glycol. Part II: Effect of temperature, catalyst and polymer morphology, Polym. Degrad. Stab., 2007, 92, 611–616, DOI:10.1016/j.polymdegradstab.2007.01.008.
- J. Chen, Z. Li, L. Jin, P. Ni, G. Liu, H. He, J. Zhang, J. Dong and R. Ruan, Catalytic hydrothermal depolymerization of nylon 6, J. Mater. Cycles Waste. Manage., 2010, 12, 321–325, DOI:10.1007/s10163-010-0304-y.
- X. Chen, L. Cheng, J. Gu, H. Yuan and Y. Chen, Chemical recycling of plastic wastes via homogeneous catalysis: A review, Chem. Eng. J., 2024, 479, 147853, DOI:10.1016/j.cej.2023.147853.
- F. Liguori, C. Moreno-Marrodán and P. Barbaro, Valorisation of plastic waste via metal-catalysed depolymerisation, Beilstein J. Org. Chem., 2021, 17, 589–621, DOI:10.3762/bjoc.17.53.
- A. K. Urbanek, A. M. Mirończuk, A. García-Martín, A. Saborido, I. de la Mata and M. Arroyo, Biochemical properties and biotechnological applications of microbial enzymes involved in the degradation of polyester-type plastics, Biochim. Biophys. Acta, Proteins Proteomics, 2020, 1868, 140315, DOI:10.1016/j.bbapap.2019.140315.
- I. Taniguchi, S. Yoshida, K. Hiraga, K. Miyamoto, Y. Kimura and K. Oda, Biodegradation of PET: Current Status and Application Aspects, ACS Catal., 2019, 9, 4089–4105, DOI:10.1021/acscatal.8b05171.
- C. Jehanno, M. M. Pérez-Madrigal, J. Demarteau, H. Sardon and A. P. Dove, Organocatalysis for depolymerisation, Polym. Chem., 2019, 10, 172–186, 10.1039/c8py01284a.
- S. S. Karim, S. Farrukh, T. Matsuura, M. Ahsan, A. Hussain, S. Shakir, L. F. Chuah, M. Hasan and A. Bokhari, Model analysis on effect of temperature on the solubility of recycling of Polyethylene Terephthalate (PET) plastic, Chemosphere, 2022, 307, 136050, DOI:10.1016/j.chemosphere.2022.136050.
-
Catalyst Separation, Recovery and Recycling; Chemistry and Process Design, ed. D. J. Cole-Hamilton and R. P. Tooze, Springer, Dordrecht, 2006 Search PubMed.
- S. Haase, P. Tolvanen and V. Russo, Process Intensification in Chemical Reaction Engineering, Processes, 2022, 10, 99–121, DOI:10.3390/pr10010099.
- T. Tan, W. Wang, K. Zhang, Z. Zhan, W. Deng, Q. Zhang and Y. Wang, Upcycling Plastic Wastes into Value-Added Products by Heterogeneous Catalysis, ChemSusChem, 2022, 15, e202200522, DOI:10.1002/cssc.202200522.
- S. Thiyagarajan, E. Maaskant-Reilink, T. A. Ewing, M. K. Julsing and J. van Haveren, Back-to-monomer recycling of polycondensation polymers: opportunities for chemicals and enzymes, RSC Adv., 2022, 12, 947–970, 10.1039/D1RA08217E.
- A. Tennakoon, X. Wu, M. Meirow, D. Howell, J. Willmon, J. Yu, J. V. Lamb, M. Delferro, E. Luijten, W. Huang and A. D. Sadow, Two Mesoporous Domains Are Better Than One for Catalytic Deconstruction of Polyolefins, J. Am. Chem. Soc., 2023, 145, 17936–17944, DOI:10.1021/jacs.3c05447.
- S. D. Jaydev, A. J. Martín, D. Garcia, K. Chikri and J. Pérez-Ramírez, Assessment of transport phenomena in catalyst effectiveness for chemical polyolefin recycling, Nat. Chem. Eng., 2024, 1, 565–575, DOI:10.1038/s44286-024-00108-3.
- K. V. Khopade, S. H. Chikkali and N. Barsu, Metal-catalyzed plastic depolymerization, Cell Rep. Phys. Sci., 2023, 4, 101341, DOI:10.1016/j.xcrp.2023.101341.
- L. O. Mark, M. C. Cendejas and I. Hermans, The Use of Heterogeneous Catalysis in the Chemical Valorization of Plastic Waste, ChemSusChem, 2020, 13, 5808–5836, DOI:10.1002/cssc.202001905.
- S. Ügdüler, K. M. Van Geem, R. Denolf, M. Roosen, N. Mys, K. Ragaert and S. De Meester, Towards closed-loop recycling of multilayer and coloured PET plastic waste by alkaline hydrolysis, Green Chem., 2020, 22, 5376–5394, 10.1039/d0gc00894j.
- S. K. Das, S. K. Eshkalak, A. Chinnappan, R. Ghosh, W. A. D. M. Jayathilaka, C. Baskar and S. Ramakrishna, Plastic Recycling of Polyethylene Terephthalate (PET) and Polyhydroxybutyrate (PHB) - a Comprehensive Review, Mater. Circ. Econ., 2021, 3, 9–31, DOI:10.1007/s42824-021-00025-3.
- Q. F. Yue, L. F. Xiao, M. L. Zhang and X. F. Bai, The glycolysis of poly(ethylene terephthalate) waste: Lewis acidic ionic liquids as high efficient catalysts, Polymers, 2013, 5, 1258–1271, DOI:10.3390/polym5041258.
- G. R. Lima, W. F. Monteiro, B. O. Toledo, R. A. Ligabue and R. M. C. Santana, Macromol. Symp., 2019, 383, 1800008, DOI:10.1002/masy.201800008.
- S. Westhues, J. Idel and J. Klankermayer, Molecular catalyst systems as key enablers for tailored polyesters and polycarbonate recycling concepts, Sci. Adv., 2018, 4, eaat9669, DOI:10.1126/sciadv.aat9669.
- S. Takebayashi and S. H. Bergens, Facile Bifunctional Addition of Lactones and Esters at Low Temperatures. The First Intermediates in Lactone/Ester Hydrogenations, Organometallics, 2009, 28, 2349–2351, DOI:10.1021/om900207.
-
Eunomia, PET market in Europe state of play, 2022, https://eunomia.eco/reports/pet-market-in-europe-state-of-play-2022/ (accessed February 2024) Search PubMed.
- M. Rabnawaz, I. Wyman, R. Auras and S. Cheng, A roadmap towards green packaging: the current status and future outlook for polyesters in the packaging industry, Green Chem., 2017, 19, 4737–4753, 10.1039/C7GC02521A.
- X. Qi, W. Yan, Z. Cao, M. Ding and Y. Yuan, Current Advances in the Biodegradation and Bioconversion of Polyethylene Terephthalate, Microorganisms, 2022, 10, 39–63, DOI:10.3390/microorganisms10010039.
- F. Kawai, The Current State of Research on PET Hydrolyzing Enzymes Available for Biorecycling, Catalysts, 2021, 11, 206–215, DOI:10.3390/catal11020206.
- D. Parida, A. Aerts, K. Vanbroekhoven, M. Van Dael, H. Mitta, L. Li, W. Eevers, K. M. Van Geem, E. Feghali and K. Elst, Monomer recycling of polyethylene terephthalate, polycarbonate and polyethers: Scalable processes to achieve high carbon circularity, Prog. Polym. Sci., 2024, 149, 101783, DOI:10.1016/j.progpolymsci.2023.101783.
- F. Cao, L. Wang, R. Zheng, L. Guo, Y. Chen and X. Qian, Research and progress of chemical depolymerization of waste PET and high-value application of its depolymerization products, RSC Adv., 2022, 12, 31564–31576, 10.1039/d2ra06499e.
- E. Barnard, J. J. R. Arias and W. Thielemans, Chemolytic depolymerisation of PET: a review, Green Chem., 2021, 23, 3765–3789, 10.1039/d1gc00887k.
- A. Bohre, P. R. Jadhao, K. Tripathi, K. K. Pant, B. Likozar and B. Saha, Chemical Recycling Processes of Waste Polyethylene Terephthalate Using Solid Catalysts, ChemSusChem, 2023, 16, e202300142, DOI:10.1002/cssc.202300142.
- J. Payne and M. D. Jones, The Chemical Recycling of Polyesters for a Circular Plastics Economy: Challenges and Emerging Opportunities, ChemSusChem, 2021, 14, 4041–4070, DOI:10.1002/cssc.202100400.
- M. Wang, Y. Li, L. Zheng, T. Hu, M. Yan and C. Wu, Recycling and depolymerisation of poly(ethylene terephthalate): a review, Polym. Chem., 2024, 15, 585–608, 10.1039/d3py01218b.
- M. Hofmann, J. Sundermeier, C. Alberti and S. Enthaler, Zinc(II) acetate Catalyzed Depolymerization of Poly(ethylene terephthalate), ChemistrySelect, 2020, 5, 10010–10014, DOI:10.1002/slct.202002260.
- H. Tang, N. Li, G. Li, A. Wang, Y. Cong, G. Xu, X. Wang and T. Zhang, Synthesis of gasoline and jet fuel range cycloalkanes and aromatics from poly(ethylene terephthalate) waste, Green Chem., 2019, 21, 2709–2719, 10.1039/c9gc00571d.
- R. A. F. Tomás, J. C. M. Bordado and J. F. P. Gomes, p-Xylene oxidation to terephthalic acid: a literature review oriented toward process optimization and development, Chem. Rev., 2013, 113, 7421–7469, DOI:10.1021/cr300298j.
-
https://www.statista.com/statistics/1244421/global-market-value-purified-terephthalic-acid/
(accessed September 2024).
- S. L. Loo, E. Yu and X. Hu, Tackling critical challenges in textile circularity: A review on strategies for recycling cellulose and polyester from blended fabrics, J. Environ. Chem. Eng., 2023, 11, 110482, DOI:10.1016/j.jece.2023.110482.
- M. Lykaki, Y. Q. Zhang, M. Markiewicz, S. Brandt, S. Kolbe, J. Schrick, M. Rabe and S. Stolte, The influence of textile finishing agents on the biodegradability of shed fibres, Green Chem., 2021, 23, 5212–5221, 10.1039/d1gc00883h.
- Regulation (EC) No 1907/2006 of the European Parliament and of the Council of 18 December 2006 concerning the Registration, Evaluation, Authorisation and Restriction of Chemicals (REACH), establishing a European Chemicals Agency, 2006.
- W. Li, Z. Wei, Z. Liu, Y. Du, J. Zheng, H. Wang and S. Zhang, Qualitative identification of waste textiles based on near-infrared spectroscopy and the back propagation artificial neural network, Text. Res. J., 2021, 91, 2459–2467, DOI:10.1177/00405175211007516.
- M. Wang, S. Shi, F. Li, W. Hou, H. Guo, S. Wang, H. Jia and J. Dai, Efficient recycling of polyester and microcrystalline cellulose through one-step extraction from waste polyester-cotton blended fabrics with deep eutectic solvents, Chem. Pap., 2022, 76, 5601–5612, DOI:10.1007/s11696-022-02246-5.
- G. Xia, W. Han, Z. Xu, J. Zhang, F. Kong, J. Zhang, X. Zhang and F. Jia, Complete recycling and valorization of waste textiles for value-added transparent films via an ionic liquid, J. Environ. Chem. Eng., 2021, 9, 106182, DOI:10.1016/j.jece.2021.106182.
- B. Mu and Y. Yang, Complete separation of colorants from polymeric materials for cost-effective recycling of waste textiles, Chem. Eng. J., 2022, 427, 131570, DOI:10.1016/j.cej.2021.131570.
- L. Rosson, X. Wang and N. Byrne, Investigating how the dye colour is impacted when chemically separating polyester-cotton blends, J. Text. Inst., 2024, 115, 656–666, DOI:10.1080/00405000.2023.2201977.
- H. J. Koo, G. S. Chang, S. H. Kim, W. G. Hahm and S. Y. Park, Effects of Recycling Processes on Physical, Mechanical and Degradation Properties of PET Yarns, Fibers Polym., 2013, 14, 2083–2087, DOI:10.1007/s12221-013-2083-2.
- Y. Li, H. Yi, M. Li, M. Ge and D. Yao, Synchronous degradation and decolorization of colored poly(ethylene terephthalate) fabrics for the synthesis of high purity terephthalic acid, J. Cleaner Prod., 2022, 366, 132985, DOI:10.1016/j.jclepro.2022.132985.
- S. R. Shukla, A. M. Harad and L. S. Jawale, Chemical recycling of PET waste into hydrophobic textile dyestuffs, Polym. Degrad. Stab., 2009, 94, 604–609, DOI:10.1016/j.polymdegradstab.2009.01.007.
- A. A. Barot and V. K. Sinha, Chemical scavenging of post-consumed clothes, Waste Manage., 2015, 46, 86–93, DOI:10.1016/j.wasman.2015.09.012.
- J. Lu, M. Li, Y. Li, X. Li, Q. Gao and M. Ge, Synthesis and sizing performances of water-soluble polyester based on bis(2-hydroxyethyl) terephthalate derived from depolymerized waste poly(ethylene terephthalate) fabrics, Text. Res. J., 2019, 89, 572–579, DOI:10.1177/0040517517750652.
- Z. Guo, M. Eriksson, H. de la Motte and E. Adolfsson, Circular recycling of polyester textile waste using a sustainable catalyst, J. Cleaner Prod., 2021, 283, 124579, DOI:10.1016/j.jclepro.2020.124579.
- V. Vinitha, M. Preeyanghaa, M. Anbarasu, B. Neppolian and V. Sivamurugan, Chemical recycling of polyester textile wastes using silver-doped zinc oxide nanoparticles: an economical solution for circular economy, Environ. Sci. Pollut. Res., 2023, 30, 75401–75416, DOI:10.1007/s11356-023-27567-0.
- M. Anbarasu, V. Vinitha, M. Preeyanghaa, B. Neppolian and V. Sivamurugan, Valorization of PES Textile Waste Through Glycolysis and Aminolysis Using Bimetallic ZnO and Carbon Nitride Nanocomposites, J. Cluster Sci., 2024, 35, 1105–1125, DOI:10.1007/s10876-023-02534-4.
- J. V. Valh, B. Vončina, A. Lobnik, L. F. Zemljič, L. Škodič and S. Vajnhandl, Conversion of polyethylene terephthalate to high-quality terephthalic acid by hydrothermal hydrolysis: the study of process parameters, Text. Res. J., 2020, 90, 1446–1461, DOI:10.1177/0040517519893714.
- A. Peterson, J. Wallinder, J. Bengtsson, A. Idström, M. Bialik, K. Jedvert and H. de la Motte, Chemical Recycling of a Textile Blend from Polyester and Viscose, Part I: Process Description, Characterization, and Utilization of the Recycled Cellulose, Sustainability, 2022, 14, 7272–7285, DOI:10.3390/su14127272.
- J. Bengtsson, A. Peterson, A. Idström, H. de la Motte and K. Jedvert, Chemical Recycling of a Textile Blend from Polyester and Viscose, Part II: Mechanism and Reactivity during Alkaline Hydrolysis of Textile Polyester, Sustainability, 2022, 14, 6911–6920, DOI:10.3390/su14116911.
- A. K. Nason, R. T. Jerozal, P. J. Milner and J. Suntivich, Reactive Crystallization via Metal–Organic-Framework Formation Enables Separation of Terephthalic Acid from Textile Impurities, ACS Sustainable Chem. Eng., 2023, 11, 18–22, DOI:10.1021/acssuschemeng.2c05496.
- S. Muangmeesri, K. R. Baddigam, K. Navare, V. Apostolopoulou-Kalkavoura, K. Witthayolankowit, H. Hakansson, A. P. Mathew, K. Van Acker and J. S. M. Samec, Recycling of Polyesters by Organocatalyzed Methanolysis Depolymerization: Environmental Sustainability Evaluated by Life Cycle Assessment, ACS Sustainable Chem. Eng., 2024, 12, 4114–4120, DOI:10.1021/acssuschemeng.3c07435.
-
P. Garcia-Gutierrez, A. M. Amadei, D. Klenert, S. Nessi, D. Tonini, D. Tosches, F. Ardente and H. Saveyn, Environmental and economic assessment of plastic waste recycling: A comparison of mechanical, physical, chemical recycling and energy recovery of plastic waste, Publications Office of the European Union, Luxembourg, 2023, JRC132067, DOI:10.2760/0472.
-
T. Duhoux, E. Maes, M. Hirschnitz-Garbers, K. Peeters, L. Asscherickx, M. Christis, B. Stubbe, P. Colignon, M. Hinzmann and A. Sachdeva, European Commission, Directorate-General for Internal Market, Industry, Entrepreneurship and SMEs, Study on the technical, regulatory, economic and environmental effectiveness of textile fibres recycling - Final Report, Brussels, 2021, https://data.europa.eu/doi/10.2873/828412.
- N. George and T. Kurian, Recent Developments in the Chemical Recycling of Postconsumer Poly(ethylene terephthalate) Waste, Ind. Eng. Chem. Res., 2014, 53, 14185–14198, DOI:10.1021/ie501995m.
- K. Hy. Paek and S. G. Im, Biodegradable Aromatic–Aliphatic Copolyesters Derived from Bis(2-Hydroxyethyl) Terephthalate for Sustainable Flexible Packaging Applications, ACS Appl. Polym. Mater., 2022, 4, 5298–5307, DOI:10.1021/acsapm.2c00212.
- N. J. Berger and C. Pfeifer, Comparing the financial costs and carbon neutrality of polyester fibres produced from 100% bio-based PET, 100% recycled PET, or in combination, Biomass Convers. Biorefin., 2024 DOI:10.1007/s13399-024-05362-2.
- M. Li, Y. Huang, T. Yu, S. Chen, A. Ju and M. Ge, Chemical recycling of waste poly(ethyleneterephthalate) fibers into azo disperse dyestuffs, RSC Adv., 2014, 4, 46476–46480, 10.1039/c4ra07608g.
- S. Lu, Y. Jing, B. Feng, Y. Guo, X. Liu and Y. Wang, H2-free Plastic Conversion: Converting PET back to BTX by Unlocking Hidden Hydrogen, ChemSusChem, 2021, 14, 4242–4250, DOI:10.1002/cssc.202100196.
- B. Stubbe, S. Van Vrekhem, S. Huysman, R. G. Tilkin, I. De Schrijver and M. Vanneste, White Paper on Textile Fibre Recycling Technologies, Sustainability, 2024, 16, 618–641, DOI:10.3390/su16020618.
- Greenblue, Chemical recycling, Making-Fiber-to Fiber Recycling a Reality for Polyester Textiles, https://greenblueorg.s3.amazonaws.com/smm/wp-content/uploads/2017/10/Chemical-RecyclingMaking-Fiber-to-Fiber-Recycling-a-Reality-for-Polyester-Textiles-1.pdf.
-
S. van Berkum, V. Philippi, A. A. Marcel, R. de Groot and T. Hooghoudt, (Ioniqa Technologies B.V.), WO2016/1051981A1, 2016.
-
M. V. Artigas, L. Mestrom, R. de Groot, V. Philippi, C. G. Sanchez and T. Hooghoudt, (Ioniqa Technologies B.V.), WO2014/209117A1, 2014.
-
https://ioniqa.com/applications/
(accessed March 2024).
-
https://www.jeplan.co.jp/en/technology/fashion/
(accessed September 2024).
-
S. Inada and K. Sato, (Aies Co., Ltd.), WO2001010812A1, 2001.
- Teijin Frontier Develops New Chemical Recycling Technology for Polyester Fibers, https://www2.teijin-frontier.com/english/news/post/120/ (accessed July 2024).
-
https://garbo.it/en/chempet/
.
-
G. Frangiacomo, G. Nipoti and G. Noja, (Garbo s.r.l.), WO2022/180563A1, 2022.
-
https://poseidonplastics.com/
(accessed March 2024).
-
M. Atkins, N. Curry and S. Evans, (Poseidon Plastics Limited), WO2022/17187A1, 2022.
-
M. Atkins and N. Curry, (Poseidon Plastics Limited), GB2598077A, 2022.
-
https://www.axens.net/markets/plastic-recycling
(accessed September 2024).
-
https://www.demeto.eu/
(accessed September 2024).
-
M. Parravicini, M. Crippa and M. V. Bertele, WO2013/014650A1, 2013.
-
https://gr3n-recycling.com/
(accessed September 2024).
-
F. G. Barla, T. Showalter, H. C. Su, J. Jones and I. Bobe, (Tyton Biosciences, LLC), US2020/0407530A1, 2020.
-
https://www.depoly.co/
(accessed March 2024).
-
https://mistrafuturefashion.com/rewind-recycles-cotton-polyester/
(accessed September 2024).
- A. Palme, A. Peterson, H. de la Motte, H. Theliander and H. Brelid, Development of an efficient route for combined recycling of PET and cotton from mixed fabrics, Textiles and Clothing Sustainability, 2017, 3, 4, DOI:10.1186/s40689-017-0026-9.
-
https://www.rittec.eu/solutions/revoltex-r.html#revoltexen
.
-
https://www.eastman.com/en/sustainability/environmental/
(accessed September 2024).
-
P. Granados, M. Russ, C. J. Pierce, R. Waymire and N. Brown, LCA summary report for Eastman methanolysis technology (North America), Eastman, Quantis, January 5, 2022, CIR-PRT-13360A DV14127.
-
https://www.loopindustries.com/en/technology
(accessed September 2024).
-
H. Essaddam and M. J. Hostetler, (Loop Industries, INC), WO2017/007965A1, 2017.
-
A. Walker, (Worn Again Footwearand Accessories Limited), WO2014/045062A1, 2013.
-
https://wornagain.co.uk/
(accessed June 2024).
- P. Patel, Shay Sethi talks about the future of fabric recycling, Chem. Eng. News, 2021, 99(9) Search PubMed , https://cen.acs.org/environment/recycling/Shay-Sethi-talks-future-fabric/99/i9.
-
https://ambercycle.com/technology
(accessed June 2024).
-
R. Speight, I. O'Hara, J. Z. Zhang, D. Moller, A. Jones and G. Ross, (Blocktexx Labs PTY LTD), WO2020/252523A1, 2020.
-
https://www.statista.com/statistics/1286414/global-polyamide-market-volume/
(accessed September 2024).
-
A. Carmichael, Man-Made Fibers Continue To Grow, 2015, https://www.textileworld.com/textileworld/fiber-world/2015/02/man-made-fibers-continue-to-grow/ (accessed August 2024) Search PubMed.
- Grand View Research. Global Nylon Market Size, Share & Trends Report, 2030, https://www.grandviewresearch.com/sector-report/nylon-industry-data-book (accessed September 2024).
- V. Hirschberg and D. Rodrigue, Recycling of polyamides: Processes and conditions, J. Polym. Sci., 2023, 61, 1937–1958, DOI:10.1002/pol.20230154.
- G. Tonsi, C. Maesani, S. Alini, M. A. Ortenzi and C. Pirola, Nylon Recycling Processes: a Brief Overview, Chem. Eng. Trans., 2023, 100, 727–732, DOI:10.3303/CET23100122.
- R. A. Clark and M. P. Shaver, Depolymerization within a Circular Plastics System, Chem. Rev., 2024, 124, 2617–2650, DOI:10.1021/acs.chemrev.3c00739.
- J. A. W. Harings, Y. S. Deshmukh, M. R. Hansen, R. Graf and S. Rastogi, Processing of Polyamides in the Presence of Water via Hydrophobic Hydration and Ionic Interactions, Macromolecules, 2012, 45, 5789–5797, DOI:10.1021/ma300459q.
- A. J. Minor, R. Goldhahn, L. Rihko-Struckmann and K. Sundmacher, Chemical Recycling Processes of Nylon 6 to Caprolactam: Review and Techno-Economic Assessment, Chem. Eng. J., 2023, 474, 145333, DOI:10.1016/j.cej.2023.145333.
- J. Chen, G. Liu, L. Jin, P. Ni, Z. Li, H. He, Y. Xu, J. Zhang and J. Dong, Catalytic hydrolysis of waste nylon 6 to produce ε-caprolactam in sub-critical water, J. Anal. Appl. Pyrolysis, 2010, 87, 50–55, DOI:10.1016/j.jaap.2009.10.004.
- U. Češarek, D. Pahovnik and E. Žagar, Chemical Recycling of Aliphatic Polyamides by Microwave-Assisted Hydrolysis for Efficient Monomer Recovery, ACS Sustainable Chem. Eng., 2020, 8, 16274–16282, DOI:10.1021/acssuschemeng.0c05706.
- C. Mihut, D. K. Captain, F. Gadala-Maria and M. D. Amiridis, Review: Recycling of nylon from carpet waste, Polym. Eng. Sci., 2001, 41, 1457–1470, DOI:10.1002/pen.10845.
- C. Gong, K. Zhang, C. Yang, J. Chen, S. Zhang and C. Yi, Simple process for separation and recycling of nylon 6 and polyurethane components from waste nylon6/polyurethane debris, Text. Res. J., 2021, 91, 18–27, DOI:10.1177/0040517520931893.
- B. Mu, Y. Shao, X. Yu, L. McBride, H. Hidalgo and Y. Yang, High-quality separation and recovery of nylon and dyes from waste carpet via non-destructive dissolution and controlled precipitation for sustainable recycling, Sep. Purif. Technol., 2024, 332, 125801, DOI:10.1016/j.seppur.2023.125801.
- S. L. Konopa, J. A. Mulholland, M. J. Realff and P. M. Lemieux, Emissions from Carpet Combustion in a Pilot-Scale Rotary Kiln: Comparison with Coal and Particle-Board Combustion, J. Air Waste Manage. Assoc., 2008, 58, 1070–1076, DOI:10.3155/1047-3289.58.8.1070.
- E. M. Zakharyana and A. L. Maksimov, Pyrolysis of Polyamide-Containing Materials. Process Features and Composition of Reaction Products, Russ. J. Appl. Chem., 2022, 95, 895–928, DOI:10.1134/S1070427222070011.
- M. Braun, A. B. Levy and S. Sifniades, Recycling Nylon 6 Carpet to Caprolactam, Polym.-Plast. Technol. Eng., 1999, 38, 471–484, DOI:10.1080/03602559909351594.
-
S. Sifniades, A. B. Levy and J. A. J. Hendrix, (AlliedSignal Inc.), US5932724, 1999.
- H. Hu, Q. Xu, L. Sun, R. Zhu, T. Gao, Y. He, B. Ma, J. Yu and X. Wang, Rapid Hydrolysis of Waste and Scrap PA6 Textiles to ε-Caprolactam, ACS Appl. Polym. Mater., 2023, 5, 751–763, DOI:10.1021/acsapm.2c01744.
- S. R. Shukla, A. M. Harad and D. Mahato, Depolymerization of Nylon 6 Waste Fibers, J. Appl. Polym. Sci., 2006, 100, 186–190, DOI:10.1002/app.22775.
- W. Wang, L. Meng, K. Leng and Y. Huang, Hydrolysis of waste monomer casting nylon catalyzed by solid acids, Polym. Degrad. Stab., 2017, 136, 112–120, DOI:10.1016/j.polymdegradstab.2016.12.017.
- H. Hu, R. Zhu, L. Sun, S. Gao, B. Ma, T. Gao, Y. He, J. Yu and X. Wang, Synchronous decolorization and depolymerization of colored waste and scrap PA6 textiles containing diverse dyes to recover regenerated ε-caprolactam, J. Anal. Appl. Pyrolysis, 2023, 176, 106240, DOI:10.1016/j.jaap.2023.106240.
- W. Yang, S. Jung, J. Lee, S. W. Lee, Y. T. Kim and E. E. Kwon, Selective recovery of caprolactam from the thermo-catalytic conversion of textile waste over γ-Al2O3 supported metal catalysts, Environ. Pollut., 2023, 329, 121684, DOI:10.1016/j.envpol.2023.121684.
- L. Wursthorn, K. Beckett, J. O. Rothbaum, R. M. Cywar, C. Lincoln, Y. Kratish and T. J. Marks, Selective Lanthanide-Organic Catalyzed Depolymerization of Nylon-6 to ε-Caprolactam, Angew. Chem., Int. Ed., 2023, 62, e202212543, DOI:10.1002/anie.202212543.
- L. Ye, X. Liu, K. B. Beckett, J. O. Rothbaum, C. Lincoln, L. J. Broadbelt, Y. Kratish and T. J. Marks, Catalyst metal-ligand design for rapid, selective, and solventless depolymerization of Nylon-6 plastics, Chem, 2024, 10, 172–189, DOI:10.1016/j.chempr.2023.10.022.
- C. Alberti, R. Figueira, M. Hofmann, S. Koschke and S. Enthaler, Chemical Recycling of End-of-Life Polyamide 6 via Ring Closing Depolymerization, ChemistrySelect, 2019, 4, 12638–12642, DOI:10.1002/slct.201903970.
- R. Coeck and D. E. De Vos, Effective and sustainable depolymerization of Nylon 66 – a transamidation for the complete recycling of polyamides, Chem. Commun., 2024, 60, 1444–1447, 10.1039/d3cc05462d.
- Y. Zhao, X. Zhou, L. Ye and S. C. E. Tsang, Nanostructured Nb2O5 catalysts, Nano Rev., 2012, 3, 17631, DOI:10.3402/nano.v3i0.17631.
- Aqualfil Sustainability Report 2023, https://www.econyl.com/download/ (accessed June 2024).
-
M. Bertolla, M. Cecchetto, A. Dal Moro, M. Modesti and S. Guerra, (Aquafil S.p.a)WO2023/084441A1, 2023.
-
A. Dal Moro, A. Drighi, M. Cecchetto, M. Bertolla, G. Mirri and S. Guerra, Aquafil S.p.a), WO2024/121765A1, 2024.
-
https://econyl.aquafil.com/sustainability/
(accessed August 2024).
-
https://www.asahi-kasei.com/news/2023/e230427.html
(accessed August 2024).
-
Market volume of polyurethane worldwide from 2015 to 2022, with a forecast for 2023 to 2030 (in million metric tons) (accessed September 2024). https://www.statista.com/statistics/720341/global-polyurethane-market-size-forecast/.
- A. Das and P. Mahanwar, A brief discussion on advances in polyurethane applications, Adv. Ind. Eng. Polym. Res., 2020, 3, 93–101, DOI:10.1016/j.aiepr.2020.07.002.
- K. M. Zia, H. N. Bhatti and I. A. Bhatti, Methods for polyurethane and polyurethane composites, recycling and recovery: A review, React. Funct. Polym., 2007, 67, 675–692, DOI:10.1016/j.reactfunctpolym.2007.05.004.
-
Statista, Production of elastane fibers worldwide from 2017 to 2022 (in million metric tons), Chart. December 1, 2023. (Accessed March 12024), https://www-statista-com./statistics/1260343/elastane-fiber-production-worldwide/ Search PubMed.
- E. Boschmeier, V. M. Archodoulaki, A. Schwaighofer, B. Lendl, W. Ipsmiller and A. Bartl, New separation process for elastane from polyester/elastane and polyamide/elastane textile waste, Resour., Conserv. Recycl., 2023, 198, 107215, DOI:10.1016/j.resconrec.2023.107215.
-
P. Harmsen and H. Bos, Textiles For Circular Fashion: Part 1: Fibre Resources and Recycling Options, Wageningen Food & Biobased Research, 2020, DOI:10.18174/517183.
- Covestro: a water-borne polyurethane dispersion
provides waterproof and breathable coating for outdoor textiles. https://solutions.covestro.com/en/highlights/articles/stories/2019/waterborne-waterproof-and-breathable-textile-coating-technology (accessed September 2024).
- K. Phan, S. Ügdüler, L. Harinck, R. Denolf, M. Roosen, G. O'Rourke, D. De Vos, V. Van Speybroeck, K. De Clerck and S. De Meester, Analysing the potential of the selective dissolution of elastane from mixed fiber textile waste, Resour., Conserv. Recycl., 2023, 191, 106903, DOI:10.1016/j.resconrec.2023.106903.
-
https://www.alcantara.com/the-material/
(accessed June 2024).
- C. Jönsson, R. Wei, A. Biundo, J. Landberg, L. Schwarz Bour, F. Pezzotti, A. Toca, L. M. Jacques, U. T. Bornscheuer and P. O. Syrén, Biocatalysis in the Recycling Landscape for Synthetic Polymers and Plastics towards Circular Textiles, ChemSusChem, 2021, 14, 4028–4040, DOI:10.1002/cssc.202002666.
- N. Malinverno, M. Schmutz, B. Nowack and C. Som, Identifying the needs for a circular workwear textile management - A material flow analysis of workwear textile waste within Swiss Companies, Resour., Conserv. Recycl., 2023, 189, 106728, DOI:10.1016/10.1016/j.resconrec.2022.106728.
-
Interreg North-West Europe, Fibersort, Manual Sort of Post-Consumer Textiles in North-West Europe, 2018, https://smartfibersorting.com/publications-and-reports/ (accessed June 2024) Search PubMed.
- A. Kemona and M. Piotrowska, Polyurethane Recycling and Disposal: Methods and Prospects, Polymers, 2020, 12, 1752–1773, DOI:10.3390/polym12081752.
- L. Vonbrül, M. Cordin, A. P. Manian, T. Bechtold and T. Pham, Solvent blends for selective elastane dissolution and recovery from mixed polyamide fabrics, Resour., Conserv. Recycl., 2024, 200, 107302, DOI:10.1016/j.resconrec.2023.107302.
-
O. Etemad-Parishanzadeh, T. Mayer-Gall, M. Hildebrandt, A. R. L. Jimenez, T. Engels, R. Wallmeier, D. Weißland, S. De Meester, R. De Bisschop, S. Ügdüler, K. Phan, N. De Coensel, I. De Schrijver and J. S. Gutmann, ReMixT – Separation and recycling of mixed textiles, 2023, DOI:10.13140/RG.2.2.25764.24961.
- S. Zhang, W. Xu, R. Du, W. An, X. Liu, S. Xu and Y. Z. Wang, Selective depolymerization of PET to monomers from its waste blends and composites at ambient temperature, Chem. Eng. J., 2023, 470, 144032, DOI:10.1016/j.cej.2023.144032.
- L. P. Fonseca, A. Duval, E. Luna, M. Ximenis, S. De Meester, L. Avérous and H. Sardon, Reducing the carbon footprint of polyurethanes by chemical and biological depolymerization: Fact or fiction?, Curr. Opin. Green Sustainable Chem., 2023, 41, 100802, DOI:10.1016/j.cogsc.2023.100802.
- M. Modesti and F. Simioni, Chemical recycling of reinforced polyurethane from the automotive industry, Polym. Eng. Sci., 1996, 36, 2173–2178, DOI:10.1002/pen.10614.
- V. Sendijarevic, Chemical recycling of mixed polyurethane foam stream recovered from shredder residue into polyurethane polyols, J. Cell. Plast., 2007, 43, 31–46, DOI:10.1177/0021955X07066107.
-
https://webgate.ec.europa.eu/life/publicWebsite/project/LIFE02-ENV-D-000398/large-scale-polyurethane-recycling
(accessed August 2024).
- European Diisocynate and Polyol Producers Association (ISOPA), Recycling and Recovery of Polyurethanes Chemical and feedstock recycling. https://www.isopa.org/wp-content/uploads/2022/09/chemical-and-feedstock-recycling.pdf (accessed July 2024).
- D. Simón, A. M. Borreguero, A. De Lucas and J. F. Rodríguez, Recycling of polyurethanes from laboratory to industry, a journey towards the sustainability, Waste Manage., 2018, 76, 147–171, DOI:10.1016/j.wasman.2018.03.041.
-
J. Datta and M. Włoch, Recycling of polyurethanes, in Polyurethane Polymers, Elsevier, 2017, pp. 323–358 Search PubMed.
- W. H. Xu, L. Chen, S. Zhang, R. C. Du, X. Liu, S. Xu and Y. Z. Wang, New insights into urethane alcoholysis enable chemical full recycling of blended fabric waste, Green Chem., 2023, 25, 245–255, 10.1039/d2gc03663k.
- L. Liu, Y. Wu and Z. Zhu, Internal structure and crystallinity investigation of segmented thermoplastic polyurethane elastomer degradation in supercritical methanol, Polym. Degrad. Stab., 2017, 140, 17–24, DOI:10.1016/j.polymdegradstab.2017.03.003.
- M. B. Johansen, B. S. Donslund, S. K. Kristensen, A. T. Lindhardt and T. Skrydstrup, tert-Amyl Alcohol-Mediated Deconstruction of Polyurethane for Polyol and Aniline Recovery, ACS Sustainable Chem. Eng., 2022, 10, 11191–11202, DOI:10.1021/acssuschemeng.2c02797.
- M. B. Johansen, B. S. Donslund, M. L. Henriksen, S. K. Kristensen and T. Skrydstrup, Selective chemical disassembly of elastane fibres and polyurethane coatings in textiles, Green Chem., 2023, 25, 10622–10629, 10.1039/d3gc02994h.
- I. Olazabal, A. González, S. Vallejos, I. Rivilla, C. Jehanno and H. Sardon, Upgrading polyurethanes into functional ureas through the asymmetric chemical deconstruction of carbamates, ACS Sustainable Chem. Eng., 2022, 11, 332–342, DOI:10.1021/acssuschemeng.2c05647.
- L. Villar, I. Schlapp-Hackl, P. B. Sánchez and M. Hummel, High-Quality Cellulosic Fibers Engineered from Cotton–Elastane Textile Waste, Biomacromolecules, 2024, 25, 1942–1949, DOI:10.1021/acs.biomac.3c01366.
- N. Gama, B. Godinho, G. Marques, R. Silva, A. Barros-Timmons and A. Ferreira, Recycling of polyurethane scraps via acidolysis, Chem. Eng. J., 2020, 395, 125102, DOI:10.1016/j.cej.2020.125102.
- Rampf group: recycling rPET & PU waste – with chemical solution from RAMPF, https://www.rampf-group.com/en/aktuelles/2023/recycling-rpet-pu-waste-with-chemical-solutions-from-rampf/ (accessed September 2024).
- Anace: Production of PUR recycling polyol, https://www.anace.eu/en/polyurethane-recycling (accessed September 2024).
- L. R. Mahoney, S. A. Weiner and F. C. Ferris, Hydrolysis of polyurethane foam waste, Environ. Sci. Technol., 1974, 8, 135–139, DOI:10.1021/es60087a010.
- J. L. Gerlock, J. Braslaw, L. R. Mahoney and F. C. Ferris, Reaction of polyurethane foam with dry steam: Kinetics and mechanism of reactions, J. Polym. Sci., Polym. Chem. Ed., 1980, 18, 541–557, DOI:10.1002/pol.1980.170180215.
- G. Rossignolo, G. Malucelli and A. Lorenzetti, Recycling of Polyurethanes: where we are and where we are going, Green Chem., 2024, 26, 1132–1152, 10.1039/d3gc02091f.
- A. Kumar, N. von Wolff, M. Rauch, Y. Q. Zou, G. Shmul, Y. Ben-David, G. Leitus, L. Avram and D. Milstein, J. Am. Chem. Soc., 2020, 142, 14267–14275, DOI:10.1021/jacs.0c05675.
- L. Gausas, B. S. Donslund, S. K. Kristensen and T. Skrydstrup, Evaluation of Manganese Catalysts for the Hydrogenative Deconstruction of Commercial and End–of–Life Polyurethane Samples, ChemSusChem, 2022, 15, e202101705, DOI:10.1002/cssc.202101705.
- W. Zhou, P. Neumann, M. Al Batal, F. Rominger, A. S. K. Hashmi and T. Schaub, Depolymerization of Technical–Grade Polyamide 66 and Polyurethane Materials through Hydrogenation, ChemSusChem, 2021, 14, 4176–4180, DOI:10.1002/cssc.202002465.
- R. Palucci Rosa, G. Rosace and V. Trovato, Recent Advancements in Acrylic Fabric Applications: A Comprehensive Review and Future Trends, Polymers, 2024, 16, 2111, DOI:10.3390/polym16152111.
- P. Bajaj and S. Kumari, Modification of Acrylic Fibers: An Overview, J. Macromol. Sci., Part C, 1987, 27, 181–217, DOI:10.1080/07366578708081915.
- R. Hong, L. Su and J. Wu, Cutinases catalyze polyacrylate hydrolysis and prevent their aggregation, Polym. Degrad. Stab., 2019, 159, 23–30, DOI:10.1016/j.polymdegradstab.2018.10.028.
- J. De Tommaso and J. L. Dubois, Risk Analysis on PMMA Recycling Economics, Polymers, 2021, 3, 2724, DOI:10.3390/polym13162724.
-
https://www.igtpan.com/Ingles/metodo_reciclagem.asp
(accessed September 2024).
- S. Kocak, C. Akduman, J. Yanik, E. Perrin, A. Kumbasar and A. Cay, Activated carbon fibers from recycled acrylic and cotton for carbon dioxide capture, Polym. Eng. Sci., 2024, 64, 1355–1364, DOI:10.1002/pen.26621.
- T. A. Adegbola, O. Agboola and O. S. I. Fayomi, Review of polyacrylonitrile blends and application in manufacturing technology: recycling and environmental impact, Results Eng., 2020, 7, 100144, DOI:10.1016/j.rineng.2020.100144.
- J. B. Young, R. W. Hughes, A. M. Tamura, L. S. Bailey, K. A. Stewart and B. S. Sumerlin, Bulk depolymerization of poly(methyl methacrylate) via chain-end initiation for catalyst-free reversion to monomer, Chem, 2023, 9, 1–14, DOI:10.1016/j.chempr.2023.07.004.
- M. R. Martinez, D. Schild, F. De Luca Bossa and K. Matyjaszewski, Depolymerization of Polymethacrylates by Iron ATRP, Macromolecules, 2022, 55, 10590–10599, DOI:10.1021/acs.macromol.2c01712.
- S. Nasimi, M. Baghdadi and M. Dorosti, Surface functionalization of recycled polyacrylonitrile fibers with ethylenediamine for highly effective adsorption of Hg(II) from contaminated waters, J. Environ. Manage., 2020, 270, 110883, DOI:10.1016/j.jenvman.2020.110883.
-
https://www.oekotest.de/kosmetik-wellness/Test-zeigt-Shein-Mode-teilweise-voller-giftiger-Chemikalien_14755_1.html
(accessed August 2024).
-
M. Kopp, M. Cobbing and V. Wohlgemuth, Self regulation: a fashion fairytale - Part 2: Evaluation of Detox Committed brands, 2021 - the ten-year milestone, Greenpeace e.V., 2021, https://www.greenpeace.de/sites/www.greenpeace.de/files/20211122-greenpeace-detox-fashion-fairytale-engl-pt2.pdf Search PubMed.
- S. Johnson, ‘It's like a death pit’: how Ghana became fast fashion's dumping ground, The Guardian, 5 Jun 2023, https://www.theguardian.com/global-development/2023/jun/05/yvette-yaa-konadu-tetteh-how-ghana-became-fast-fashions-dumping-ground.
-
M. Cobbing, S. Daaji, M. Kopp and V. Wohlgemuth, Poisoned Gifts – From donations to the dumpsite: textiles waste disguised as second-hand clothes exported to East Africa, https://www.greenpeace.org/international/publication/53355/.
-
https://www.reuters.com/sustainability/eu-wants-all-textile-waste-rules-place-by-2028-commissioner-2023-06-27/
(accessed August 2024).
- G7 Ministers of Climate, Energy and the Environment, G7 Climate, Energy and Environment Ministers’ Communiqué, Meeting 16th April 2023, Sapporo.
- Y. Jing, Y. Wang, S. Furukawa, J. Xia, C. Sun, M. J. Hglsey, H. Wang, Y. Guo, X. Liu and N. Yan, Towards the Circular Economy: Converting Aromatic Plastic Waste Back to Arenes over a Ru/Nb2O5 Catalyst, Angew. Chem., Int. Ed., 2021, 60, 5527–5535, DOI:10.1002/anie.202011063.
- J. Xu, K. Zhou, L. Qin, Z. Tan, S. Huang, P. Duan and S. Kang, One-Pot Tandem Alcoholysis-Hydrogenation of Polylactic Acid to 1,2-Propanediol, Polymers, 2023, 15, 413–424, DOI:10.3390/polym15020413.
- J. Walendziewski, Continuous flow cracking of waste plastics, Fuel Process. Technol., 2005, 86, 1265–1278, DOI:10.1016/j.fuproc.2004.12.004.
-
Sustainable Textile and Fashion Value Chains, ed. A. Matthes, K. Beyer, H. Cebulla, M. G. Arnold and A. Schumann, Springer Nature, Cham, Switzerland, 2021, https://link.springer.com/book/10.1007/978-3-030-22018-1 Search PubMed.
-
M. Hussain, S. H. Gillani and S. Uz Zaman, in Life Cycle Analysis of Textiles in Textile Engineering: An Introduction, ed. N. Yasir and S. Khubab, De Gruyter Oldenbourg, 2023, ch. 13, DOI:10.1515/9783110799415-013.
-
S. Trzepacz, D. Bekkevold Lingås, L. Asscherickx, K. Peeters, H. van Duijn and M. Akerboom, Norion Consult, LCA-based assessment of the management of European used textiles, 2023, https://euric.org/resource-hub/reports-studies/study-lca-based-assessment-of-the-management-of-european-used-textiles Search PubMed.
- S. S. Chopra, L. Dong, G. Kaur, C. Len and C. S. K. Lin, Sustainable process design for circular fashion: Advances in sustainable chemistry for textile waste Valorisation, Curr. Opin. Green Sustainable Chem., 2023, 39, 100747, DOI:10.1016/j.cogsc.2022.100747.
- S. Abagnato, L. Rigamonti and M. Grosso, Life cycle assessment applications to reuse, recycling and circular practices for textiles: A review, Waste Manage., 2024, 182, 74–90, DOI:10.1016/j.wasman.2024.04.016.
- A. C. Woolridge, G. D. Ward, P. S. Phillips, M. Collins and S. Gandy, Life cycle assessment for reuse/recycling of donated waste textiles compared to use of virgin material: An UK energy saving perspective, Resour., Conserv. Recycl., 2006, 46, 94–103, DOI:10.1016/j.resconrec.2005.06.006.
-
https://plasticsrecycling.org/apr-design-guide
(accessed September 2024).
- S. C. DeVito, On the design of safer chemicals: a path forward, Green Chem., 2016, 18, 4332–4347, 10.1039/c6gc00526h.
-
European Commission: Joint Research Centre and C. Caldeira, et al., Safe and sustainable by design chemicals and materials - Application of the SSbD framework to case studies, Publications Office of the European Union, Luxembourg, 2023, https://data.europa.eu/doi/10.2760/329423 Search PubMed.
- Regulation (EU) No 1007/2011 of the European Parliament and of the Council of 27 September 2011 on textile fibre names and related labelling and marking of the fibre composition of textile products and repealing Council Directive 73/44/EEC and Directives 96/73/EC and 2008/121/EC of the European Parliament and of the Council.
- European Commission, The European Green Deal, Brussels, 11.12.2019, COM(2019) 640 final, https://eur-lex.europa.eu/legal-content/EN/TXT/PDF/?uri=CELEX:52019DC0640.
- Target 12.5: “By 2030, substantially reduce waste generation through prevention, reduction, recycling and reuse”. https://sdgs.un.org/goals/goal12 (accessed September 2024).
- F. Rotondo, P. Perchinunno, S. L'Abbate and L. Mongelli, Ecological transition and sustainable development: integrated statistical indicators to support public policies, Sci. Rep., 2022, 12, 18513, DOI:10.1038/s41598-022-23085-0.
|
This journal is © The Royal Society of Chemistry 2024 |
Click here to see how this site uses Cookies. View our privacy policy here.