DOI:
10.1039/D3LC00698K
(Paper)
Lab Chip, 2024,
24, 56-62
Grease the gears: how lubrication of syringe pumps impacts microfluidic flow precision†
Received
14th August 2023
, Accepted 10th November 2023
First published on 15th November 2023
Abstract
Pumps are indispensable for analytical applications and ensure controlled fluid movement. Syringe pumps are among today's most prevalent liquid delivery systems, especially for high-pressure, stable, low-flow-rate microfluidic applications. Due to moving mechanical parts of the assembly, regular maintenance is essential to ensure reliable operation and flow rates. However, lubrication of the mechanics is easily overlooked because the research focuses on novel analytical applications rather than on the maintenance of pumps. Here, we investigate the lubrication of the syringe pump guide rods with its effect on the flow rate stability after regular pump cleaning from contaminations. The guide rods of syringe pumps were thoroughly cleaned from any lubricant, and the flow rate for specified flowrates between 5 and 100 μL min−1 was measured, revealing tremendous flow rate fluctuations with a coefficient of variation (CV) value up to 0.34. In contrast, flow rate measurements of syringe pumps with lubricated guide rods show a five-fold smoother flow rate fluctuation depending on the specified flow rate with CV values below 0.07. These differences in flow rate's CV were most significant for pressure drops below 500 mbar, relevant for many lab-on-a-chip applications. In summary, we emphasize the awareness of lubricating moving parts of syringe pumps to achieve constant flow rates, minimize wear, and ensure the reliable operation of, for instance, accurate lab-on-a-chip workflows.
Introduction
To prepare this article, we asked many microfluidic community colleagues how they ensure their pumps' stable operation. Surprisingly, we learned that most laboratories consider their pumps as plug-and-play tools without an awareness of the maintenance efforts of the mechanics.
Fluid delivery systems are widely used in microfluidic systems with biological, chemical, or medical applications.1–6 Mainly, syringe pumps, pressure pumps, and peristaltic pumps are employed, besides niche applications for gravity-, osmotic-, surface tension-, electrokinetic-, and centrifugal-driven pumps.2,7–9 Flow fluctuations can be present in any fluidic system inherited from the fluid driving system, even when static conditions are imposed.
Peristaltic pumps exert a mechanical action on a flexible, liquid-carrying element. The incorporated progressive squeezing action drives the fluid by creating a pressure difference. Here, fluid flow pulsations are unavoidable due to the discontinuous compression of the flexible tubing. Thus, precise dosing is limited, making this type of pump primarily suitable for applications with high flow rates or fluid recirculation.7
In contrast, pressure pumps pressurize a fluid-containing reservoir with gas to establish a fluid flow in the microfluidic system. Due to the possibility of exact gas pressure control, very stable flow rates can be achieved in the nL min−1-range with even fL-dosing applications.10,11 However, the achieved flow highly depends on the fluidic resistance of the microfluidic system and, consequently, is directly dependent on the channel geometry and fluid viscosity. This generally excludes its use for applications demanding high pressures and insensitivity to mechanical disturbances.12
Today, syringe pumps are usually the most economical solution and, thus, widely used systems for academic laboratories with defined flow rates.13–16 For instance, a commercial system, such as the Pump 11 Pico Plus Elite from Harvard Apparatus, Holliston, MA, USA, provides a steady flow precision of 1.8 ± 0.08 μL min−1 with a theoretical minimal flow rate of 2.66 nL min−1 and sufficient pressure for typical nL-dosing applications.2,16,17 The motor drives the rotation of a drive screw, translated into a translational motion of the pusher block. Rods or other mechanical structures usually guide the pusher block linearly, picking up the torque. Thereby, the plunger of a mounted syringe is moved by the pusher block resulting in a fluid flow. Mainly, the steps of the motor limit the minimal dispensed volume of a syringe and guarantee a steady flow rate. Li et al. reported that minute fluctuations in the flow rate with frequencies in the 300–400 Hz regime could be traced back to the discrete steps taken by the driving stepper motor.1,18–20 Potentially, other mechanical syringe pump parts can also impede homogeneous fluid dispensing, but to the best of our knowledge, little of their influence is reported. Especially when cleaning a syringe pump thoroughly or just by frequent use, lubricants from moving parts will inevitably be removed and often not sufficiently reapplied. Such cleaning is, for instance, mandatory when removing pumps from a biosafety level 2 environment.
Here, we demonstrate the importance of lubricating moving parts of a syringe pump to achieve robust analytical results required for precise fluid control. In particular, we compare the fluctuations of flow rates of syringe pumps with and without lubricated guide rods. By exemplifying the forces and torques on the pusher block, we deduce that the canting and stuttering are sources of the fluctuations.
Experimental
Syringe pumps
A syringe pump (Fusion 4000, Chemyx Inc., Stafford, USA) with two parallel stainless steel guide rods and an eccentric drive screw, as shown in Fig. 1, was used for all investigations. The minimum flow rate specified by the manufacturer for the used 500 μL syringe is 19.57 nL min−1 at an accuracy of ±<0.35% and precision of ±<0.05%.21 The pusher block is aluminium and has brass sliding on the guide rods. In the case of the not-lubricated syringe pump, the guide rods were thoroughly cleaned from any lubricant and dirt with ethanol. However, little lubricant inevitably remained on the interior parts of the fit that could only be reached by completely dismantling the syringe pump. The guide rods were lubricated with non-resinous lubricant (CONTRAKOR A 100, Klüber Lubrication München SE & Co. KG, Munich, Germany) for subsequent experiments with the lubricated syringe pump. The lubricant had a kinematic viscosity of 480 mm2 s−1 at 50 °C, which is similar to honey at room temperature.22 Operating the syringe pump a few times back and forth over the maximum moving distance distributed the lubricant uniformly on the guide rods and allowed creeping into the fit. For more details, please see ESI† Fig. S1.
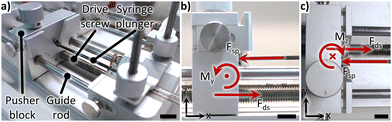 |
| Fig. 1 Guiding and driving parts of the syringe pump under test. a) Overview of the guide rods and drive screw configuration with a mounted syringe. Side view b) and top view c) of the pusher block with acting forces and moments when infusing. Fsp: force from the syringe plunger; Fds: force from the drive screw; M: resulting moment from forces. Scale bars equal 1 cm. | |
Syringes
500 μL and 2500 μL gas-tight glass syringes (1750 TLL and 1002 TLL, Hamilton Company Corp., Reno, USA) with a 3.26 mm and 7.28 mm inner diameter, respectively, PTFE (polytetrafluoroethylene) plunger tip, and Luer-lock connection were used to eliminate syringe deformations. Furthermore, two plastic syringes were utilized (Omnifix 3 mL, B. Braun Melsungen AG, Melsungen, Germany, and HSW HENKE-JECT 5 mL, Henke-Sass, Wolf GmbH, Tuttlingen, Germany) with 9.5 mm and 12.2 mm inner diameter measured with a hand-held calliper, respectively, Luer-slip connection, but different plunger tip designs. The Omnifix syringe has a rubber plunger tip that is more elastic than the solid, single-material HENKE-JECT plunger.
Setup
A matching dosing tip (Nordson Corp., Westlake, USA) with a stainless steel tip of 0.013″ inner and 0.025″ outer diameter was used to connect the used syringe and tubing. The 12 cm long PFA (perfluoroalkoxy alkane) tubing (IDEX Health & Science LLC, Oak Harbor, USA) with 0.020″ inner and 1/16″ outer diameter was pushed on the tip forming a tight connection. In contrast, the other end was connected flangeless to a 6 cm long FEP (fluorinated ethylene propylene) tubing (Fluigent S.A., Le Kremlin-Bicêtre, France) with 0.020″ inner and 1/32″ outer diameter. This thinner tubing was eventually connected to the flow sensor (Flow Unit M, Fluigent S.A.). At the outlet of the flow sensor, the same FEP tubing with a 4 cm length was connected and dipped into a water-pre-filled Eppendorf tube. Please note that the fluidic system had no elastic parts and was realized as rigid as possible to avoid any fluidic capacitance affecting transient phenomena and damping. The flow sensor was connected to its controller (Flow-EZ, Fluigent S.A.), facilitating a readout with a PC.
Flow rate measurements
A water-filled syringe was fixed tightly in the syringe pump and connected to the fluidic system. Special attention was given to a gas bubble-free filling of the whole system to avoid any fluidic capacitance. 5 s after starting the recording of the flow rate, the syringe pump was started manually. After 20 s of pumping time, the syringe pump is manually stopped, and for another 5 s, the flow rate is recorded to observe transient phenomena, if any. For the plastic syringes, the pumping time was 50 s. The set flow rates varied between 5–100 μL min−1. The recording was facilitated with a custom-written PC program (LabVIEW 2018, National Instruments Corp., Austin, USA) and a sample rate of 10 Hz. Quantitative flow rate analysis and the fast Fourier transformation (FFT) were conducted in OriginLab Pro 2023b (OriginLab Corp., Northampton, USA). Since we are not interested in flow rate fluctuations induced by the incremental steps of the driving stepper motor but in low-frequency effects, the sample rate of 10 Hz is sufficient for an FFT analysis with a bandwidth of 5 Hz limited by the Nyquist–Shannon sampling theorem. For comparison, with a step resolution s of our syringe pusher block of 0.012 μm per step, we would expect pulses with a frequency between 832–4992 Hz determined by fpulse = 4Qπ−1D−2s−1 where Q denotes the set flow rate and D the syringe's inner diameter.2,21
Fluidic resistance adjustments to mimic a typical microfluidic chip
To simulate microfluidic chips with high fluidic resistances, we connected to the flow sensor outlet PTFE tubing (RCT-ZS-DKA-SW, RCT Reichelt Chemietechnik GmbH, Heidelberg, Germany) with 300 μm inner and 800 μm outer diameter in different lengths (192 cm and 455 cm). Besides water with a dynamic viscosity of 1.00 mPa s, a 50w/% sucrose–water solution with a dynamic viscosity of 15.04 mPa s at 20 °C was used.23 Both tubing length and viscosity scale the fluidic resistance linearly according to the Hagen–Poiseuille equation. Here, the 2500 μL glass syringe was used, and the flow rate was constant for all conditions at 100 μL min−1.
Long-term test
To estimate the proper functionality period of a lubricated syringe, a long-term test was conducted. An initially well-lubricated syringe pump and the 500 μL syringe were used for cyclic infusion and withdrawal of 350 μL of water at a 100 μL min−1 flow rate. To test the deterioration of the lubrication at specific time points, the fluidic system was re-vented, and the flow rate was measured as described above.
Results and discussion
With our setup, we recorded flow rates for lubricated and not-lubricated syringe pump guide rods and compared them regarding flow rate fluctuation during continuous pumping. Additionally, transient phenomena were recorded when repetitively starting and stopping the syringe pump. The 500 μL glass syringe serves as reference to which the other syringes will be compared in the following.
Not-lubricated guide rods promote imprecise flow rates
Anomalous flow rate fluctuations with deviations up to 129% occurred depending on the flow rate, especially for fixed 15–100 μL min−1 flow rates (Fig. 2c)). At these experimental conditions, striking pulses towards higher and lower flow rates were measured; no steady flow rate condition was achieved during the 20 s pumping interval. Temporary drifts were observed above 10 μL min−1. The box plots of the recorded flow rates showed a distribution with broad whiskers at the 2.5–97.5 percentiles and CV values ranging from 0.05 to 0.34 (Fig. 2b)). Due to torque and high frictional forces, these heterogeneous flow rates must have directly resulted from the pusher block movement that was canting on the guide rods. Visualizing the force from the syringe plunger and the drive screw (Fig. 1b) and c)), resulting moments on the pusher block were induced in y- and z-direction. The magnitude of these moments could be determined by the cross-product of the force and position vector. Due to their point of attack, both forces contributed to the same torque direction in the respective y- and z-direction. Combined with the friction coefficient for brass on steel and some unavoidable play of the fit, canting of the pusher block and unsteady movement were promoted. Hence, reducing the torque of the pusher block or lowering the friction in the fit would redress canting and foster smooth movement. Since geometric modifications of the syringe pump were impossible, the guide rods were lubricated to reduce friction. In contrast, the flow rate at 5 μL min−1 held a constant level over the whole pumping time but only showed a small saw-tooth-like profile induced by the discrete steps of the pusher block. Only at such low flow rates the CV of the flow rate was 0.05 and comparable to operations with lubricated guide rods. With FFT, the anomalous flow rates can be further quantified with a broad range of frequencies from 5 to 100 μL min−1 (Fig. 2d)). Only discrete contributions at 1.32 Hz, 2.65 Hz, and 4.70 Hz are observed at 10 μL min−1, whereby the two lower frequencies are also present at 5 μL min−1.
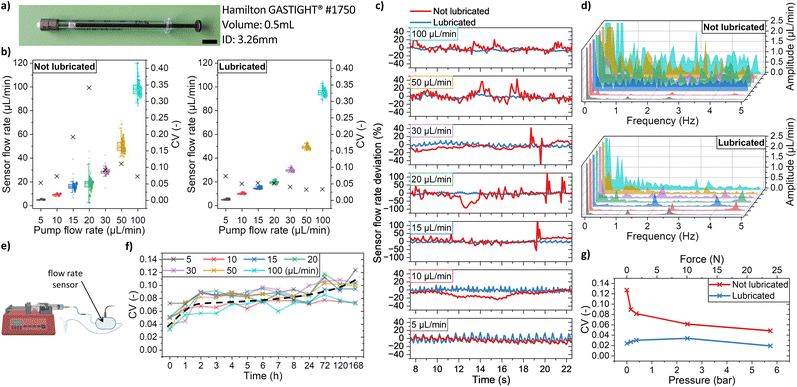 |
| Fig. 2 Quantitative analysis of the flow rate stability for lubricated and not-lubricated guide rods with a glass syringe and colour-coded flow rates ranging from 5 to 100 μL min−1. a) Shows the 500 μL glass syringe with a 3.26 mm inner diameter. The scale bar equals 1 cm. b) The flow profiles were evaluated between 7.5–22.5 s and plotted with whiskers at the 2.5 and 97.5 percentile of the data. The data's coefficient of variation (CV) is plotted with black crosses (x) on the right y-axis. Lubrication reduces the CV significantly. c) Comparison of the lubricated and not-lubricated flow profiles that are normalized to their respective specified flow rate. d) Shows the flow profiles between 7.5–22.5 s in the frequency domain by FFT for the not-lubricated and lubricated syringe pumps, respectively. e) Schematic of the measurement setup with adaptable tubing length between flow rate sensor and Eppendorf tube. f) The flow rate's CVs of initially well-lubricated guide rods increase over time, indicated by the dashed trend line. g) The pressure and force on the pusher block were varied, showing constantly higher CVs for the not-lubricated than the lubricated guide rods but converging for higher forces. Here, the 2500 μL glass syringe and a flow rate of 100 μL min−1 was used. | |
In the ESI† we show, that a dripping outlet, not immersed in a liquid, can create similar flow rate fluctuations (ESI† Fig. S6).
The advantage of lubricated guide rods
All set flow rates showed over the pumping time of 20 s a constant level with small fluctuations around a steady mean (Fig. 2c)). The impact of the lubrication is clearly observed with CV values around 0.05 for all flow rates but 0.07 for 5 μL min−1 (Fig. 2b)). Overall, canting of the pusher block was avoided since no disruptive flow rate peaks or significant deviations from the mean flow rate were observed. The lubrication of the guide rods reduced the friction substantially to facilitate the sliding of the pusher block. This is essential for steady flow rates and precise volume dosing with syringe pumps. Moreover, it contributes to less abrasion and minimized pump wear, besides assuring reliable functionality. However, significant components remain in the frequency domain for all flow rates (Fig. 2d)). The 5–10 μL min−1 flow rate peaks are the same as for the measurement without lubricated guide rods but slightly more pronounced (1.32 Hz, 2.65 Hz, and 4.70 Hz). Regarding the higher flow rates, most frequency components could be removed except for some remaining peaks, but the amplitude was reduced either way. This indicates that not all mechanical disturbances can be eliminated but minimized to some remaining vibrations.
Higher forces on the pusher block reduce CV
Higher fluidic resistances were induced by longer tubing and higher liquid viscosities to mimic a various microfluidic chips for different applications. With a constant flow rate, a constant pressure drop Δp of the system can be determined easily but needs to be related to the force on the syringe pump. Thereby, the force on the pusher block Fpb is the sum of (1) the syringe's frictional force to move the plunger in the barrel Fs and (2) the force exerted on the plunger tip by the pressure drop that scales linearly with its area: Fpb = Fs + 4−1πD2Δp, where D denotes the syringe's inner diameter. Hereby, Fs cannot be determined with this setup but is constant for a single syringe type and flow rate (here 100 μL min−1). In Fig. 2g), the CV is plotted for different pressure drops but constant flow rates. The CV is barely influenced by the pressure drop residing consistently below 0.04, in the lubricated case. In contrast, in the not-lubricated case, the CV falls exponentially with higher pressures and finally runs parallel to the lubricated case. Please note that the most considerable differences in CV are below 500 mbar, the pressure region where most microfluidic devices are operated especially when built from polydimethylsiloxane (PDMS). However, the constant CV offset of approx. 0.03 demonstrates that there is always an improvement in flow rate precision by lubricating the guide rods.
Syringe pump performance degrades already in the first hours
Fig. 2f) shows the long-term test of an initially well-lubricated syringe that was tested at time 0 h. After 1 h hour of constant use, the CV of the flow rate deteriorated but reached a plateau after 2 h. In this time, the lubricant is pushed to the sides; thus, only a thin film remains on the guide rods. In the following hours, the flow rate's CV worsened slightly but constantly. After 72 h of constant use, an increasing CV can be observed, assuming no sufficient lubrication anymore. Therefore, in the time scale of hundreds of hours, a significant deterioration of the flow rate precision is expected, together with considerable wear.
Plastic syringes dampen high-frequency fluctuations
In the not-lubricated case, plastic syringes do not exhibit as high flow rate's CV changes as glass syringes. Here, the maximal CV reached 0.10 at 30 μL min−1, whereas for the lubricated case, the CV was for all flow rates smaller than 0.03. In the frequency domain, the significant difference is at low frequencies below 1 Hz (Fig. 3d)). In this region, the amplitudes decrease when the guide rods are lubricated. In contrast, at frequencies above 1 Hz, there are no additional contributions for the not-lubricated syringe pump besides the unaffected distinct peaks. Plastic syringes, which are frequently found in clinical settings, are not as stiff as glass syringes. This flexibility translates into a fluidic capacitance that dampens flow rate changes. The striking peaks using the glass syringe in Fig. 2c) are prevented using the plastic syringe so that only low-frequency fluctuations appear (Fig. 3c)). Comparing the 5 mL syringe with a solid, single-material plunger (see ESI† Fig. S2) to the elastic plunger tip of the 3 mL syringe, the latter does not have better damping behaviour nor more precise flow rates.
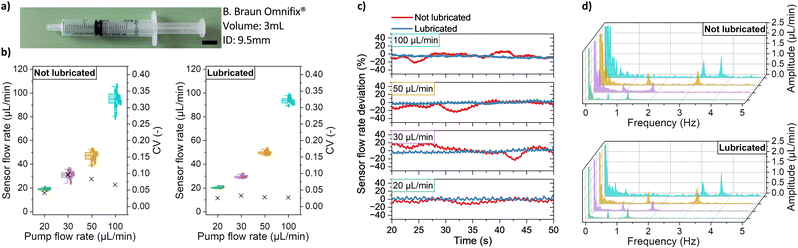 |
| Fig. 3 Quantitative analysis of the flow rate stability for lubricated and not-lubricated guide rods with a plastic syringe and colour-coded flow rates ranging from 20 to 100 μL min−1. a) Shows the 3 mL plastic syringe with a 9.5 mm inner diameter and an elastic rubber plunger tip. The scale bar equals 1 cm. b) The flow profiles were evaluated between 20–50 s and plotted with whiskers at the 2.5 and 97.5 percentile of the data. The data's coefficient of variation (CV) is plotted with black crosses (x) on the right y-axis. Lubrication reduces the CV significantly. c) Comparison of the lubricated and not-lubricated flow profiles that are normalized to their respective specified flow rate. d) Shows the flow profiles between 20–50 s in the frequency domain by FFT for the not-lubricated and lubricated syringe pumps, respectively. | |
Pusher block velocity affects fluctuation frequency
The force on the plunger scales linearly with the flow rate and the syringe's inner cross-sectional area (Fpb ∝ D2Q). If we assume that the force on the pusher block is the primary originator of high flow rate fluctuations and canting of the pusher block, the flow rate with the highest CV for the larger syringe must be less than for the smaller syringe (Fig. 2b)). However, increasing the syringe's inner diameter by approx. factor 2.23 to 7.28 mm (2500 μL syringe), the CV for flow rate fluctuations climaxes at 50 μL min−1 to 0.17 (Fig. 4b)), a higher flow rate than for the smaller syringe (500 μL) (Fig. 2b)). In the frequency domain (Fig. 4d)) the not lubricated 2500 μL syringe has frequency peaks at 1.06 Hz and 2.12 Hz for 20 μL min−1, 1.59 Hz and 3.18 Hz for 30 μL min−1, 2.65 Hz and 4.64 Hz for 50 μL min−1, and 4.64 Hz for 100 μL min−1. After lubrication, all peaks remain at their same frequencies but with a lower amplitude and at a 100 μL min−1 flow rate, an additional peak at 0.66 Hz emerges from the reduced background. Comparing the peak positions with their flow rates, higher flow rates result in higher peak frequencies, giving rise to an additional velocity dependence for flow rate fluctuations.
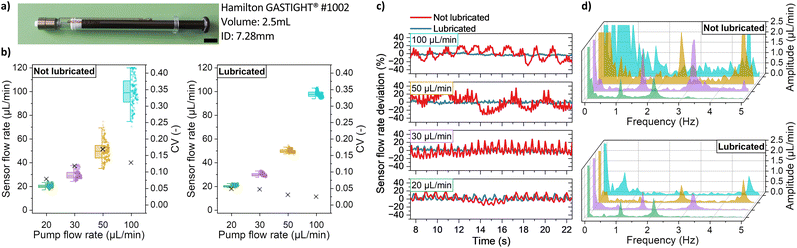 |
| Fig. 4 Quantitative analysis of the flow rate stability for lubricated and not-lubricated guide rods with a glass syringe and colour-coded flow rates ranging from 20 to 100 μL min−1. a) Shows the 2500 μL glass syringe with a 7.28 mm inner diameter. The scale bar equals 1 cm. b) The flow profiles were evaluated between 7.5–22.5 s and plotted with whiskers at the 2.5 and 97.5 percentile of the data. The data's coefficient of variation (CV) is plotted with black crosses (x) on the right y-axis. Lubrication reduces the CV significantly. c) Comparison of the lubricated and not-lubricated flow profiles that are normalized to their respective specified flow rate. d) Shows the flow profiles between 7.5–22.5 s in the frequency domain by FFT for the not-lubricated and lubricated syringe pumps, respectively. | |
Conversely to the force on the plunger, the velocity of the pusher block scales with the flow rate and the reciprocal of the syringe's inner diameter (vpb ∝ D−2Q). Here, we would expect for pronounced flow anomalies a higher flow rate for the larger 2500 μL syringe than for the smaller 500 μL syringe, matching our results. Coupling the syringe size dependence, force and velocity, and with the use of the continuity equation, the pusher block velocity vpb and force are correlated linearly: Fpb ∝ D4vpb, where D denotes the syringe's inner diameter. However, it cannot be derived clearly from our measurements how the pusher block's force and velocity are linked to flow rate fluctuations, but we observe that both have a combined contribution.
Nevertheless, independent of the syringe's inner diameter, lubrication minimizes the flow rate's CV, here for the larger 2500 μL syringe between 0.05–0.02 for flow rates from 20–100 μL min−1 (Fig. 4b)). Furthermore, withdrawing a liquid shows similar flow anomalies to these infusing results, indicating no directional dependence (see ESI† Fig. S3).
Conclusion
Lubrication of mechanical parts is not a novel idea, but it should be mentioned, as the researcher's focus is on the analytics rather than on the maintenance of the periphery. Syringe pumps are mainly used as plug-and-play tools, but for many high-precision applications the noise level of syringe pumps is a significant contributor to low experimental accuracy and may lead to false research results. Here, the flow rate stability of a commercial syringe pump was investigated concerning the lubrication of the moving parts after a typical cleaning cycle. The analysis revealed that in the tested flow regime of 5–100 μL min−1, the flow rate's CV without lubricated syringe parts could be 680% higher than the lubricated syringe. Striking pulses and unpredictable fluctuations result from the canting pusher block due to insufficient lubrication. This is especially relevant for lab-on-a-chip devices operating at pressures below 500 mbar where the differences in the flow rate's CV were largest. Furthermore, any fluidic capacitance, e.g. provided by plastic syringes, minimizes high-frequency flow rate fluctuations but may result in delayed response times of the fluidic system.
In conclusion, we encourage users of syringe pumps to regularly lubricate all moving parts to improve the experimental quality and reproducibility of microfluidic results. Furthermore, self-built and commercial syringe pumps should undergo a critical design assessment focusing on minimizing torques and play in fits. Despite the widespread designs for self-built syringe pumps employing affordable guide rods, it is advisable to implement low-tolerance linear axes, e.g., pre-stressed with dovetail guiding.
Author contributions
Conceptualization: M. L., O. H. investigation: M. L. formal analysis: M. L. methodology: M. L. funding acquisition: O. H. supervision: O. H. writing of the manuscript: M. L., O. H. All authors have read and approved the final version of the manuscript.
Conflicts of interest
All authors declare no conflict of interest.
Acknowledgements
This project is supported by the Federal Ministry for Economic Affairs and Climate Action (BMWK) on the basis of a decision by the German Bundestag (Grant No.: KK 5333701AD1).
References
- W. Zeng, I. Jacobi, D. J. Beck, S. Li and H. A. Stone, Lab Chip, 2015, 15, 1110 RSC.
- Z. Jiao, J. Zhao, Z. Chao, Z. You and J. Zhao, Microfluid. Nanofluid., 2019, 23, 26 CrossRef.
- A. J. deMello, Nature, 2006, 442, 394–402 CrossRef CAS PubMed.
- J. El-Ali, P. Sorger and K. Jensen, Nature, 2006, 442, 403–411 CrossRef CAS.
- D. B. Weibel and G. M. Whitesides, Curr. Opin. Chem. Biol., 2006, 10, 584–591 CrossRef CAS PubMed.
- T. A. Neff, J. E. Fischer, G. Schulz, O. Baenziger and M. Weiss, Intensive Care Med., 2001, 27, 287–291 CrossRef CAS.
- C. K. Byun, K. Abi-Samra, Y.-K. Cho and S. Takayama, Electrophoresis, 2014, 35, 245–257 CrossRef CAS.
- M. Hébert, W. Baxter, J. P. Huissoon and C. L. Ren, Microfluid. Nanofluid., 2020, 24, 90 CrossRef.
- N.-T. Nguyen, X. Huang and T. K. Chuan, J. Fluids Eng., 2002, 124, 384–392 CrossRef.
- C. Fütterer, N. Minc, V. Bormuth, J.-H. Codarbox, P. Laval, P. Rossier and J.-L. Viovy, Lab Chip, 2004, 4, 351–356 RSC.
- M. Leman, F. Abouakil, A. D. Griffiths and P. Tabeling, Lab Chip, 2015, 15, 753 RSC.
- D. J. Laser and J. G. Santiago, J. Micromech. Microeng., 2004, 14, R35–R64 CrossRef.
- W. Zeng, S. Li and H. Fu, Microfluid. Nanofluid., 2018, 22, 133 CrossRef.
- K. Loizou, V.-L. Wong and B. Hewakandamby, Inventions, 2018, 3, 54 CrossRef.
- K. Jiang, A. X. Lu, P. Dimitrakopoulos, D. L. DeVoe and S. R. Raghavan, J. Colloid Interface Sci., 2015, 448, 275–279 CrossRef CAS PubMed.
- S. G. K. Calhoun, K. K. Brower, V. C. Suja, G. Kim, N. Wang, A. L. McCully, H. Kusumaatmaja, G. G. Fuller and P. M. Fordyce, Lab Chip, 2022, 22, 2315 RSC.
- Harvard Apparatus Inc., Pump 11 Elite Series Syringe Pump User's Manual.
- Z. Li, S. Y. Mak, A. Sauret and H. C. Shum, Lab Chip, 2014, 14, 744 RSC.
- C. Kim, D. H. Hwang, S. Lee and S.-J. Kim, Microfluid. Nanofluid., 2016, 20, 4 CrossRef.
- M. E. Haque, A. Matin, X. Wang and M. Kersaudy-Kerhoas, Phys. Fluids, 2021, 33, 073317 CrossRef CAS.
- Chemyx Inc., Fusion 4000 & 6000 User Manual.
- Klüber Lubrication München SE & Co. KG, CONTRAKOR A 100 Product Information.
- V. R. N. Telis, J. Telis-Romero, H. B. Mazzotti and A. L. Gabas, Int. J. Food Prop., 2007, 10, 185–195 CrossRef CAS.
|
This journal is © The Royal Society of Chemistry 2024 |
Click here to see how this site uses Cookies. View our privacy policy here.